大型铸钢轧辊轴心晶间裂纹形成的原因及防止措施
轧辊破坏常见原因分析及对策
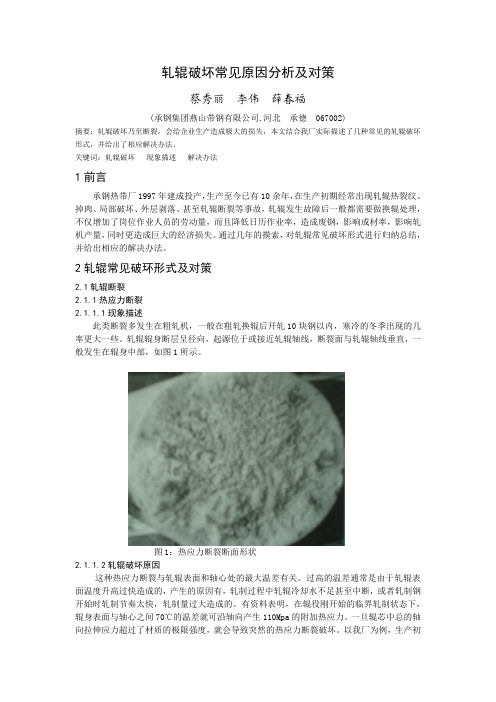
轧辊破坏常见原因分析及对策蔡秀丽李伟薛春福(承钢集团燕山带钢有限公司,河北承德 067002)摘要:轧辊破坏乃至断裂,会给企业生产造成极大的损失,本文结合我厂实际描述了几种常见的轧辊破坏形式,并给出了相应解决办法。
关键词:轧辊破坏现象描述解决办法1前言承钢热带厂1997年建成投产,生产至今已有10余年,在生产初期经常出现轧辊热裂纹、掉肉、局部破坏、外层剥落、甚至轧辊断裂等事故,轧辊发生故障后一般都需要做换辊处理,不仅增加了岗位作业人员的劳动量,而且降低日历作业率,造成废钢,影响成材率,影响轧机产量,同时更造成巨大的经济损失。
通过几年的摸索,对轧辊常见破坏形式进行归纳总结,并给出相应的解决办法。
2轧辊常见破环形式及对策2.1轧辊断裂2.1.1热应力断裂2.1.1.1现象描述此类断裂多发生在粗轧机,一般在粗轧换辊后开轧10块钢以内,寒冷的冬季出现的几率更大一些。
轧辊辊身断层呈径向,起源位于或接近轧辊轴线,断裂面与轧辊轴线垂直,一般发生在辊身中部,如图1所示。
图1:热应力断裂断面形状2.1.1.2轧辊破坏原因这种热应力断裂与轧辊表面和轴心处的最大温差有关。
过高的温差通常是由于轧辊表面温度升高过快造成的,产生的原因有,轧制过程中轧辊冷却水不足甚至中断,或者轧制钢开始时轧制节奏太快,轧制量过大造成的。
有资料表明,在辊役刚开始的临界轧制状态下,辊身表面与轴心之间70℃的温差就可沿轴向产生110Mpa的附加热应力。
一旦辊芯中总的轴向拉伸应力超过了材质的极限强度,就会导致突然的热应力断裂破坏。
以我厂为例,生产初期,有一次正值寒冬腊月,室外温度-20℃,厂房内温度较低,备辊正处在风口上,轧辊上线前没有预热,仅烫辊4块,在烫辊效果不好的前提下,温度较低的冷却水很快浇凉辊面,在轧制中与红钢接触,轧辊处于冷热交替中,内外表面温差大。
断辊后约10分钟,用手摸断辊边缘,触觉为凉辊,带钢轧制部位的轧辊表面微温,轧辊断口内触觉发凉。
锻钢轧辊缺陷产生的原因及对策

锻钢轧辊在轧制中出现问题的原因及对策目录页数1. 引言 42. 轧辊表面迹象A. 夹杂5~6B. 橘皮状轧辊表面7~8C. 辊印9~12D. 软点13~18E. 热裂纹i. 热轧机工作辊19ii. 冷轧机工作辊20~273. 剥落A. 表面迹像28~46B. 表皮下引发i. 与材质有关47~49ii. 接触应力a. 一般机理50~52b. 冷轧机工作辊53~61c. 热轧机工作辊62~64d. 支撑辊65~704. 辊颈断裂A. 表面迹像71~72i. 辊颈应力计算73~77B. 表皮下引发i. 轧辊设计或材料质量78~81C. 辊颈修复82~85D. 瞬时发生i. 深置缺陷86~87ii. 轧机过载88~905. 辊身断裂A. 疲劳--- 深置缺陷91~93B. 瞬时i. 轧机过载94~95ii. 深置缺陷96~976. 轧辊检测98A. 涡流探伤99~100B. 表面波超声波探伤101~105C. 着色渗入探伤106~108D. 刻蚀探伤109~111E. 磁粉探伤112~113F. 硬度检验114~1187. 轧辊处理和储存1198. 轧辊各部位的英文名称120~121引言在轧钢生产中的轧辊性能及质量直接影响轧机产量和产品质量。
因为轧辊采购费用在轧钢厂生产成本中占有较大比重,也是影响轧制成本的重要因素。
本书的目的是针对锻钢轧辊在轧制中可能出现的相关问题,并就问题的类型,特徵,样例(照片,图解),产生机理及预防措施等进行分析。
仅供有关人员参考。
锻造轧辊的无损探伤(NTD)对轧辊生产厂家和轧辊用户都非常重要。
轧辊生产厂家在轧辊热处理以及随后的精加工之前用NDT无损探伤,来确认轧辊的表面和内部是否合格。
轧辊用户(轧辊车间)利用NDT无损探伤确保研磨切削部分满足进一步使用之前的轧辊表面要求。
NDT 无损探伤以及其应用,可以作为最佳化轧辊维护过程的管理方法之一。
轧辊的处理和储存也是轧辊问题发生的因素。
轧辊铸造缺陷原因分析

3浇注外层时,开浇速度过慢,铁水在冷圈内腔同时达到一定厚度的时间拉长。
1涂料时冷圈的温度差、手法的不合理,冷圈与端盖间补砂太厚,造成涂料厚度差大,使得冷速不均
2外层离心浇注时,冷圈温度差大。
在地坑冷却过程中,有新浇注的轧辊放在已浇好的轧辊边上(太近),使得辊面冷速不均,有阴阳面或硬度落差大
1成分控制不严,硬度过高;
2离心机振动剧烈;
3原材料质量差。
14
结合不良
1离心机离心时间或停转到填芯间隔时间过
配料计算错误,少配或多配铁水。
8
球化不良
球化衰退
石墨漂浮
1铁水包内球化剂安放位置错误,或出铁时方法不当,没有选用合适的球化包;
2球化处理后到浇注间隔时间太长。
3出铁温度过高,Mg烧损严重,残Mg量少,我们采用高温熔炼低温浇注,及时球化,强化孕育
4出铁温度过低,覆盖剂(铁屑)易“结死”在包低,不起作用
2炉前成分没控制好,试样片白口判断不准确,配料错误;
3冷却过程中受外界影响使得冷速过快(高)或过慢(底)
2
R处夹渣、气孔等
1芯部出铁温度、浇注温度低;使得铁水流动性不好,夹渣物,氧化渣不易上浮。
2炉料、炉内、铁水包内的垃圾处理不干净(包括外层和芯部);
3铁水包没烘干,球化剂,孕育剂,覆盖剂等添加剂潮湿,覆盖的铁屑氧化严重或者里面垃圾太多,使得铁水铁水夹气夹渣严重。
9
辊面夹渣.、针孔
1外层出铁温度、浇注温度不合理;
2炉内、铁水包内的垃圾处理不干净;
3铁水包没烘干,铁水内夹气严重;
4孕育、球化处理后立刻浇注,作用不充分,铁水镇定时间太短;
5浇注外层时,开浇速度过慢,表层铁水凝固过快,垃圾不能及时往里浮出。
铸钢件不良发生原因与对策改善

2-1.尽可能只设置1个冒口,可避免2个熱节之间的裂纹产生
2-2.在冒口底部设置10mm高的凸台,也减少熱节间的裂纹产生
2-3.铸件外形尽量呈圆弧状,避免锐角存在减少裂纹发生
3.铸钢的熔点较高,钢液易氧化、钢水的流动性差、收缩大,残留应力高(体收缩率为10~14%,线收缩为1.8~2.8%)
1.首先考虑冒口切割的温度环境
1-1.铸件应在开箱或加热至200~250℃左右,再进行切割作业,要避免铸件常温状态下切割
如果只是割冒口处有裂纹,那就是铸件的温度过低下进行冒口切割
1-2.冒口切割以距离铸件5~10mm高度即可
1-3.冒口切割断后,冒口必须停放原处并以保温材料全周覆盖,避免温差过大促成缩裂
3-1采用合理的熔炼工艺和除气工艺去除金属液中的氧化夹杂和气体等,防止产生冷裂纹。
3-2.必要时,铸件在切割浇冒口后,还要进行一次时效热处理
2
铸件缩松
1.冒补缩的位置路径不佳
1-1.冒口原则上设置于厚薄连接部位上
1-2.在冒口底部增设补缩路径
1-3.对外形复杂补缩困难的铸件,也可上下型倒置并在上模砂芯头部位设置环状冒口补缩
2-7.堆焊作业必须每焊一层降温保温后再焊下一层,防止过热产生新的裂纹
2-8.焊补作业之前应对焊条进行预热
2.铸钢件生产技术比较难,厂家焊补现象十分普遍
2-1.铸钢件生产厂家必需建立焊补工艺流程管控
2-2.必需建制专业的焊补人员进行焊补作业
2-3.毛胚件与加工件应分开焊补,并对加工件及行必要的保护加工件
2-4.大型铸件焊补,需进行预热措施
2-5.单一条裂纹铸件可焊补;缩孔及多条或多处裂纹的铸件不可焊补
2-6.铸件较大巢孔必需以一层一层堆焊的方式进行焊补
引起轧辊发生垂直轧辊轴线断裂断面的主要原因_

引起轧辊发生垂直轧辊轴线断裂断面的主要原因1. 引言1.1 概述在轧钢过程中,轧辊是一种重要的工作部件,其质量和稳定性直接影响到整个轧制过程的效果和产品质量。
然而,在实际生产中,垂直轧辊轴线断裂断面问题时有发生,给生产运行带来了严重的影响和损失。
因此,了解引起这一问题的主要原因,并采取相应措施来预防和解决它们具有重要意义。
1.2 文章结构本文将从三个方面对垂直轧辊轴线断裂断面的主要原因进行探讨:轧辊质量问题、加工工艺问题以及动力系统问题。
每个方面将进一步细分为具体的子问题,并通过深入分析和研究来揭示这些子问题对垂直轧辊轴线断裂造成的影响。
1.3 目的本文旨在全面地研究并概述引起垂直轧辊轴线断裂断面的主要原因。
通过对这些原因进行深入剖析,我们可以更好地理解并找出有效的解决方案,从而提高生产过程中的效率和产品的质量。
给出相关的解决方案和改进建议有助于生产运行更加平稳和可靠地进行。
2. 垂直轧辊轴线断裂断面的主要原因垂直轧辊轴线断裂断面是钢铁工业中常见的问题之一,其主要原因可以归结为轧辊质量问题、加工工艺问题和动力系统问题。
2.1 轧辊质量问题轧辊质量问题是导致垂直轧辊轴线断裂断面的重要原因之一。
首先,材料的质量不合格会直接影响到轧辊的强度和韧性,在工作过程中容易出现疲劳破坏。
其次,热处理过程不当也可能使得轧辊内部存在残余应力或者晶粒生长异常,从而降低了其抗疲劳性能。
此外,加工精度不高也会导致负责分布不均匀以及表面误差增加,使得在工作过程中产生应力集中区域。
2.2 加工工艺问题加工工艺问题也是引起垂直轧辊轴线断裂断面的重要原因之一。
切割过程不正常会导致切口存在毛刺或者微裂纹等缺陷,这些缺陷在后续工作中会发展成裂纹,并最终导致轧辊断裂。
正火过程中温度和时间的控制不合理也会在轧辊内部形成大量的残余应力,使得轴线处于扭转应力状态,容易引发断裂。
此外,精加工磨削不足也可能使得表面存在凸起或者凹陷等缺陷,从而使得轧辊在工作过程中受到额外的摩擦和冲击。
热轧轧辊剥落或断裂的原因及预防方法探究
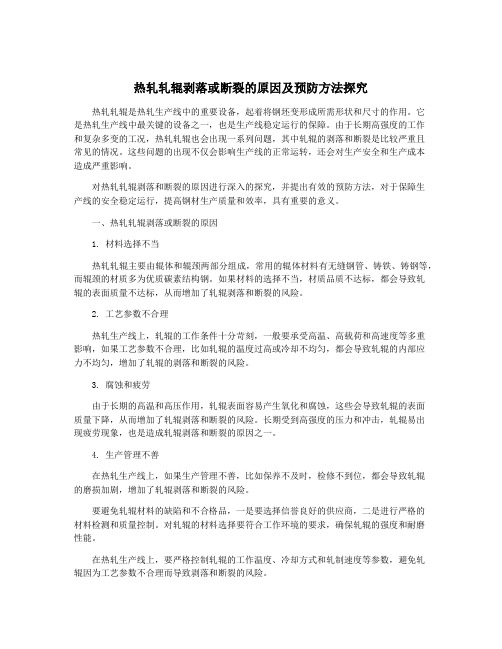
热轧轧辊剥落或断裂的原因及预防方法探究热轧轧辊是热轧生产线中的重要设备,起着将钢坯变形成所需形状和尺寸的作用。
它是热轧生产线中最关键的设备之一,也是生产线稳定运行的保障。
由于长期高强度的工作和复杂多变的工况,热轧轧辊也会出现一系列问题,其中轧辊的剥落和断裂是比较严重且常见的情况。
这些问题的出现不仅会影响生产线的正常运转,还会对生产安全和生产成本造成严重影响。
对热轧轧辊剥落和断裂的原因进行深入的探究,并提出有效的预防方法,对于保障生产线的安全稳定运行,提高钢材生产质量和效率,具有重要的意义。
一、热轧轧辊剥落或断裂的原因1. 材料选择不当热轧轧辊主要由辊体和辊颈两部分组成,常用的辊体材料有无缝钢管、铸铁、铸钢等,而辊颈的材质多为优质碳素结构钢。
如果材料的选择不当,材质品质不达标,都会导致轧辊的表面质量不达标,从而增加了轧辊剥落和断裂的风险。
2. 工艺参数不合理热轧生产线上,轧辊的工作条件十分苛刻,一般要承受高温、高载荷和高速度等多重影响,如果工艺参数不合理,比如轧辊的温度过高或冷却不均匀,都会导致轧辊的内部应力不均匀,增加了轧辊的剥落和断裂的风险。
3. 腐蚀和疲劳由于长期的高温和高压作用,轧辊表面容易产生氧化和腐蚀,这些会导致轧辊的表面质量下降,从而增加了轧辊剥落和断裂的风险。
长期受到高强度的压力和冲击,轧辊易出现疲劳现象,也是造成轧辊剥落和断裂的原因之一。
4. 生产管理不善在热轧生产线上,如果生产管理不善,比如保养不及时,检修不到位,都会导致轧辊的磨损加剧,增加了轧辊剥落和断裂的风险。
要避免轧辊材料的缺陷和不合格品,一是要选择信誉良好的供应商,二是进行严格的材料检测和质量控制。
对轧辊的材料选择要符合工作环境的要求,确保轧辊的强度和耐磨性能。
在热轧生产线上,要严格控制轧辊的工作温度、冷却方式和轧制速度等参数,避免轧辊因为工艺参数不合理而导致剥落和断裂的风险。
要对轧辊的表面进行防腐处理,避免氧化和腐蚀的发生;并对轧辊进行定期的疲劳检测和预防性维护,延长轧辊的使用寿命。
高铬铸铁离心轧辊裂纹和软点原因分析
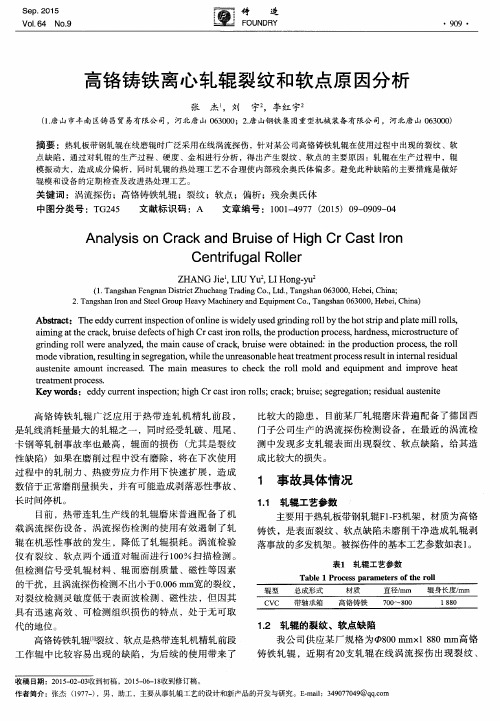
Vo 1 . 6 4 No . 9
・9 0 9・
高铬铸铁 离心轧辊裂 纹和 软点原 因分析
张 杰 ,刘 宇 ,李红 宇
( 1 . 唐 山市丰南区铸 昌贸易有 限公 司,河北唐 山 0 6 3 0 0 0 ;2 . 唐 山钢铁 集 团重型机械 装备有限公 司,河北唐 山 0 6 3 0 0 0 )
摘要 :热轧板带钢轧辊在线磨辊时广泛采用在线涡流探伤,针对某公司高铬铸铁轧辊在使用过程中出现的裂纹、软
点 缺陷 ,通过 对轧辊 的生产过程 、硬度 、金相进 行分析 ,得 出产生裂 纹 、软点 的主要 原 因:轧辊 在生产过程 中,辊 模振 动大 ,造成 成分偏析 ,同时轧辊 的热处理工 艺不合理使 内部残余 奥氏体偏 多。避免此种 缺陷的主要措施 是做好 辊模 和设 备 的定期检查 及改进热处理工艺 。
Ce n t r i f u g al Ro l l e r
ZHANG J i e , LI U Yu , LI Ho ng — y u 。 ( 1 . Ta n g s h a n F e n g n a n Di s t r i c t Z h u c h a n g T r a d i n g Co . , L t d . , Ta n g s h a n 0 6 3 0 0 0 , He b e i , C h i n a ;
g r i nd i n g r o l l we r e a na l y z e d ,t he ma i n c a us e o f c r a c k , br u i s e we r e o b t a i n e d :i n t he p r o d uc t i o n pr oc e s s , t h e r o l l mo d e vi br a t i o n . r e s ul t i ng i n s e g r e g a t i o n . wh i l e t he u n r e a s o na bl e h e a t t r e a t me n t p r oc e s s r e s u l t i n i n t e r na 1 r e s i d ua l
大型铸钢件热裂阻止措施研究
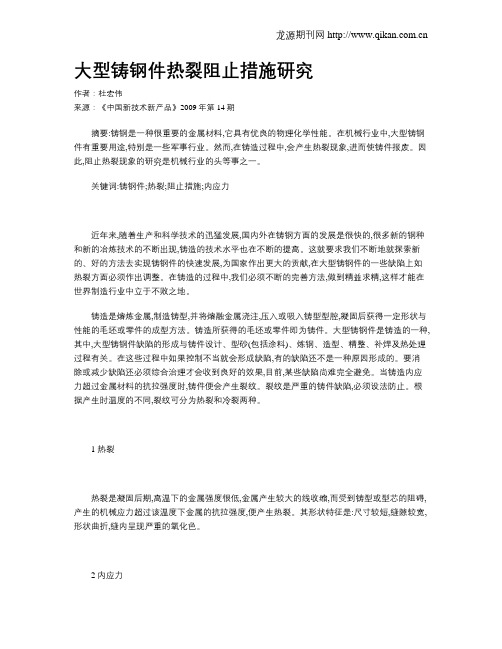
大型铸钢件热裂阻止措施研究作者:杜宏伟来源:《中国新技术新产品》2009年第14期摘要:铸钢是一种很重要的金属材料,它具有优良的物理化学性能。
在机械行业中,大型铸钢件有重要用途,特别是一些军事行业。
然而,在铸造过程中,会产生热裂现象,进而使铸件报废。
因此,阻止热裂现象的研究是机械行业的头等事之一。
关键词:铸钢件;热裂;阻止措施;内应力近年来,随着生产和科学技术的迅猛发展,国内外在铸钢方面的发展是很快的,很多新的钢种和新的冶炼技术的不断出现,铸造的技术水平也在不断的提高。
这就要求我们不断地就探索新的、好的方法去实现铸钢件的快速发展,为国家作出更大的贡献,在大型铸钢件的一些缺陷上如热裂方面必须作出调整。
在铸造的过程中,我们必须不断的完善方法,做到精益求精,这样才能在世界制造行业中立于不败之地。
铸造是熔炼金属,制造铸型,并将熔融金属浇注,压入或吸入铸型型腔,凝固后获得一定形状与性能的毛坯或零件的成型方法。
铸造所获得的毛坯或零件即为铸件。
大型铸钢件是铸造的一种,其中,大型铸钢件缺陷的形成与铸件设计、型砂(包括涂料)、炼钢、造型、精整、补焊及热处理过程有关。
在这些过程中如果控制不当就会形成缺陷,有的缺陷还不是一种原因形成的。
要消除或减少缺陷还必须综合治理才会收到良好的效果,目前,某些缺陷尚难完全避免。
当铸造内应力超过金属材料的抗拉强度时,铸件便会产生裂纹。
裂纹是严重的铸件缺陷,必须设法防止。
根据产生时温度的不同,裂纹可分为热裂和冷裂两种。
1 热裂热裂是凝固后期,高温下的金属强度很低,金属产生较大的线收缩,而受到铸型或型芯的阻碍,产生的机械应力超过该温度下金属的抗拉强度,便产生热裂。
其形状特征是:尺寸较短,缝隙较宽,形状曲折,缝内呈现严重的氧化色。
2 内应力铸造内应力主要是由于铸件在固态下的收缩受阻而引起的。
这些阻碍包括机械阻碍和热阻碍。
机械阻碍引起的内应力容易理解,如型芯、铸型或浇冒口等对铸件收缩的阻碍。
铸钢件裂纹的形成原因及预防方案
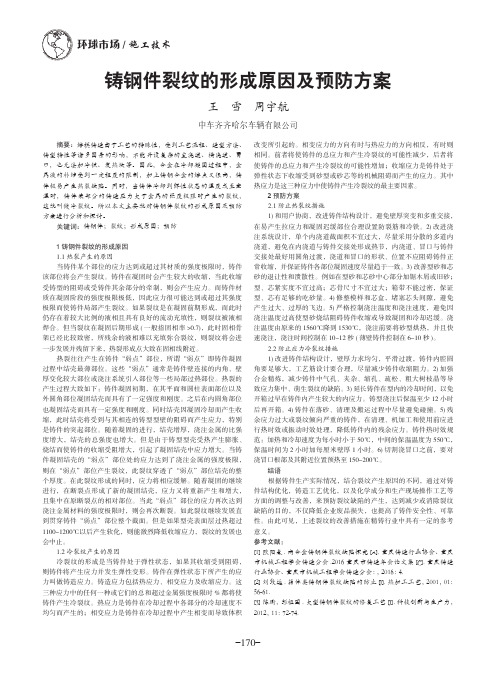
环球市场/施工技术-170-铸钢件裂纹的形成原因及预防方案王 雪 周宇航中车齐齐哈尔车辆有限公司摘要:熔模铸造由于工艺的特殊性,受到工艺流程、造型方法、铸型特性等诸多因素的影响,不能开设复杂的直浇道、横浇道、冒口,也无法加冷铁、发热块等。
因此,合金在冷却凝固过程中,金属液的补缩受到一定程度的限制,加上铸钢合金的熔点又很高,铸件极易产生热裂缺陷。
同时,当铸件冷却到弹性状态的温度或至室温时,铸件某部分的铸造应力大于金属的强度极限时产生的裂纹,这就叫做冷裂纹。
所以本文主要就对铸钢件裂纹的形成原因及预防方案进行分析和探讨。
关键词:铸钢件;裂纹;形成原因;预防1铸钢件裂纹的形成原因1.1热裂产生的原因当铸件某个部位的应力达到或超过其材质的强度极限时,铸件该部位将会产生裂纹。
铸件在凝固时会产生较大的收缩,当此收缩受铸型的阻碍或受铸件其余部分的牵制,则会产生应力。
而铸件材质在凝固阶段的强度极限极低,因此应力很可能达到或超过其强度极限而使铸件局部产生裂纹。
如果裂纹是在凝固前期形成,而此时仍存在着较大比例的液相且具有良好的流动充填性,则裂纹被液相焊合。
但当裂纹在凝固后期形成(一般指固相率>0.7),此时固相骨架已经比较致密,所残余的液相难以充填弥合裂纹,则裂纹将会进一步发展并残留下来,热裂形成点大致在固相线附近。
热裂往往产生在铸件“弱点”部位,所谓“弱点”即铸件凝固过程中结壳最薄部位。
这些“弱点”通常是铸件壁连接的内角、壁厚变化较大部位或浇注系统引入部位等一些局部过热部位。
热裂的产生过程大致如下:铸件凝固初期,在其平面和圆柱表面部位以及外圆角部位凝固结壳而具有了一定强度和刚度。
之后在内圆角部位也凝固结壳而具有一定强度和刚度。
同时结壳因凝固冷却而产生收缩,此时结壳将受到与其相连的铸型型壁的阻碍而产生应力,特别是铸件的突起部位。
随着凝固的进行,结壳增厚,浇注金属的比强度增大,结壳的总强度也增大。
但是由于铸型型壳受热产生膨胀、烧结而使铸件的收缩受阻增大,引起了凝固结壳中应力增大。
轧辊破坏常见原因分析及对策

轧辊破坏常见原因分析及对策蔡秀丽李伟薛春福(承钢集团燕山带钢有限公司,河北承德 067002)摘要:轧辊破坏乃至断裂,会给企业生产造成极大的损失,本文结合我厂实际描述了几种常见的轧辊破坏形式,并给出了相应解决办法。
关键词:轧辊破坏现象描述解决办法1前言承钢热带厂1997年建成投产,生产至今已有10余年,在生产初期经常出现轧辊热裂纹、掉肉、局部破坏、外层剥落、甚至轧辊断裂等事故,轧辊发生故障后一般都需要做换辊处理,不仅增加了岗位作业人员的劳动量,而且降低日历作业率,造成废钢,影响成材率,影响轧机产量,同时更造成巨大的经济损失。
通过几年的摸索,对轧辊常见破坏形式进行归纳总结,并给出相应的解决办法。
2轧辊常见破环形式及对策2.1轧辊断裂2.1.1热应力断裂2.1.1.1现象描述此类断裂多发生在粗轧机,一般在粗轧换辊后开轧10块钢以内,寒冷的冬季出现的几率更大一些。
轧辊辊身断层呈径向,起源位于或接近轧辊轴线,断裂面与轧辊轴线垂直,一般发生在辊身中部,如图1所示。
图1:热应力断裂断面形状2.1.1.2轧辊破坏原因这种热应力断裂与轧辊表面和轴心处的最大温差有关。
过高的温差通常是由于轧辊表面温度升高过快造成的,产生的原因有,轧制过程中轧辊冷却水不足甚至中断,或者轧制钢开始时轧制节奏太快,轧制量过大造成的。
有资料表明,在辊役刚开始的临界轧制状态下,辊身表面与轴心之间70℃的温差就可沿轴向产生110Mpa的附加热应力。
一旦辊芯中总的轴向拉伸应力超过了材质的极限强度,就会导致突然的热应力断裂破坏。
以我厂为例,生产初期,有一次正值寒冬腊月,室外温度-20℃,厂房内温度较低,备辊正处在风口上,轧辊上线前没有预热,仅烫辊4块,在烫辊效果不好的前提下,温度较低的冷却水很快浇凉辊面,在轧制中与红钢接触,轧辊处于冷热交替中,内外表面温差大。
断辊后约10分钟,用手摸断辊边缘,触觉为凉辊,带钢轧制部位的轧辊表面微温,轧辊断口内触觉发凉。
热轧轧辊剥落或断裂的原因及预防方法探究

热轧轧辊剥落或断裂的原因及预防方法探究【摘要】热轧轧辊剥落或断裂是热轧生产中常见的问题,严重影响生产效率和产品质量。
本文从热轧轧辊剥落或断裂现象引起注意和研究目的和意义两个方面展开,然后深入探讨了造成这一问题的原因,包括金属材料的质量问题、外部环境因素和工艺参数设置不当等。
针对这些原因,提出了一些有效的预防方法,如加强材料检验、保持良好的生产环境和合理设置工艺参数。
在研究成果总结和未来研究展望两个方面进行总结,指出今后需要深入研究轧辊剥落或断裂的原因及预防方法,以提高热轧生产的效率和质量。
通过本文的研究,有望为解决热轧轧辊剥落或断裂问题提供一定的参考和借鉴。
【关键词】热轧轧辊、剥落、断裂、金属材料、质量问题、外部环境、工艺参数、预防方法、研究成果、展望。
1. 引言1.1 热轧轧辊剥落或断裂现象引起注意热轧轧辊剥落或断裂是热轧生产中常见的问题,一旦发生会给生产带来严重的影响。
轧辊是热轧生产中不可或缺的重要设备之一,承担着对金属带材进行塑性加工的重要任务。
由于受到多种因素的影响,轧辊往往会出现剥落或断裂的现象,如果不及时处理和预防,将导致生产事故的发生,影响生产效率和产品质量。
热轧轧辊剥落或断裂现象需要引起注意,因为其主要危害包括:一是轧辊剥落或断裂会导致生产线停机,给企业带来直接的经济损失;二是剥落或断裂的轧辊会造成产品表面质量不达标,影响产品的销售和企业的声誉;三是轧辊剥落或断裂会增加生产中的安全隐患,可能导致事故发生,影响员工的生命安全。
对热轧轧辊剥落或断裂现象引起足够的重视,研究其发生的原因以及预防方法,对于提高生产效率、保证产品质量和保障人员安全具有重要意义。
本文旨在探究热轧轧辊剥落或断裂的原因及预防方法,为热轧生产提供一定的参考和指导。
1.2 研究目的和意义研究的目的在于深入探究热轧轧辊剥落或断裂的原因,分析其中可能存在的金属材料质量问题、外部环境因素以及工艺参数设置不当等方面的因素。
通过研究分析,可以为预防热轧轧辊剥落或断裂提供理论依据和技术支持,提高轧辊的使用寿命和生产效率。
轧辊失效的原因及防治措施

轧辑失效的原因及防治措施轧辐的损坏形式多种多样,典型形式及失效原因如下:1、轧辑磨损分三类:机械磨损是由轧辐表面与轧件摩擦引起的;热磨损是由高温作用使其表层软化、熔化或蒸发引起的;腐蚀磨损是由轧辐表面水分的化学作用、电化学作用、氧化作用等引起表面材料损失和迁移。
2、轧辐裂纹轧制中发生堆钢、卡钢、追尾等事故,致使其局部温度急剧升高,产生的热应力和组织应力超过极限,形成热裂纹;轧制延伸形成舌头,其温度低于中部轧件,会产生热应力以及轧制应力突变,形成冲击裂纹;轧制中,由于氧化铁皮叠轧,导卫划痕等原因也会形成裂纹。
3、轧辐剥落裂纹的形成和扩展加快,到达一定长度和深度后,会导致剥落。
4、轧辑断裂1)辐轴铸造缺陷轧辐离心铸造中,因离心震动产生成分和组织层状偏析,形成裂纹迅速扩展,造成轧辐断裂。
2)轧辐组织缺陷化学成分不合格、冷却速度不当会导致成分偏析、渗碳体过高等缺陷,只是机械性能下降,最终导致断裂。
3)加工工艺轧辐在锻造时压力过小或变形不合理造成轧辐芯部未锻透,形成穿晶裂纹。
其防治措施为:1、轧辐选用耐磨又抗热裂纹的材质,采取相应的热处理及物流化学处理措施,使组织均化,表面耐磨性增加。
2、轧辑在上轧机前进行硬度、超声波等综合检验,确保其无裂纹等缺陷。
3、轧辐车削时,将残留氧化层及裂纹彻底清除,以减少轧辐表面裂纹及剥落产生。
4、合理安排换辐周期,选配轧辐,制定详细的轧辐车修方案,将车修量控制在要求范围内。
5、合理布置冷却水喷射范围和控制冷却水量,确保轧辐冷却温度控制在正常范围内。
6、加强设备点检,预防轧钢设备事故,减少导致卡钢、堆钢、追尾等事故发生。
严格控制轧制温度,杜绝低温钢通过轧机,避免轧制力过载。
轧辊破坏常见原因分析及对策.doc

CL0501-轧辊破坏常见原因分析及对策案例简要说明:依据国家职业标准和金属材料及热处理技术、材料成型与控制技术专业教学要求,归纳提炼出所包含的知识和技能点,弱化与教学目标无关的内容,使之与课程学习目标、学习内容一致,成为一个承载了教学目标所要求知识和技能的教学案例。
该案例是轧钢设备使用与维护事故案例,体现了轧辊材质及其力学性能等知识点和轧钢工、设备点检工的岗位操作技能,与本专业轧钢机械设备课程中轧辊部分、金属材料与热处理课程中金属材料的性能部分单元的教学目标对应。
轧辊破坏常见原因分析及对策天津冶金职业技术学院王磊该案例发生在承钢热带厂,该厂自1997年建成投产,生产至今已有10多年,在生产初期经常出现轧辊热裂纹、掉肉、局部破坏、外层剥落、甚至轧辊断裂等事故,轧辊发生故障后一般都需要做换辊处理,不仅增加了岗位作业人员的劳动量,而且降低日历作业率,造成废钢,影响成材率,影响轧机产量,同时更造成巨大的经济损失。
通过几年的摸索,对轧辊常见破坏形式进行归纳总结,并给出相应的解决办法。
该案例在教学过程中辅以图片等多媒体资源对学生进行讲解,让学生能够更好地掌握轧制过程中如何更好地延长轧辊的寿命。
1.背景介绍某厂自1997年建成投产,生产至今已有10多年,在生产初期经常出现轧辊热裂纹、掉肉、局部破坏、外层剥落、甚至轧辊断裂等事故,轧辊发生故障后一般都需要做换辊处理,不仅增加了岗位作业人员的劳动量,而且降低日历作业率,造成废钢,影响成材率,影响轧机产量,同时更造成巨大的经济损失。
通过几年的摸索,对轧辊常见破坏形式进行归纳总结,并给出相应的解决办法。
2.主要内容2.1.热应力断裂一、现象描述此类断裂多发生在粗轧机,一般在粗轧换辊后开轧10块钢以内,寒冷的冬季出现的几率更大一些。
轧辊辊身断层呈径向,起源位于或接近轧辊轴线,断裂面与轧辊轴线垂直,一般发生在辊身中部,如图1所示。
图1 热应力断裂断面形状二、轧辊破坏原因这种热应力断裂与轧辊表面和轴心处的最大温差有关。
分析铸钢件裂纹的成因与控制措施
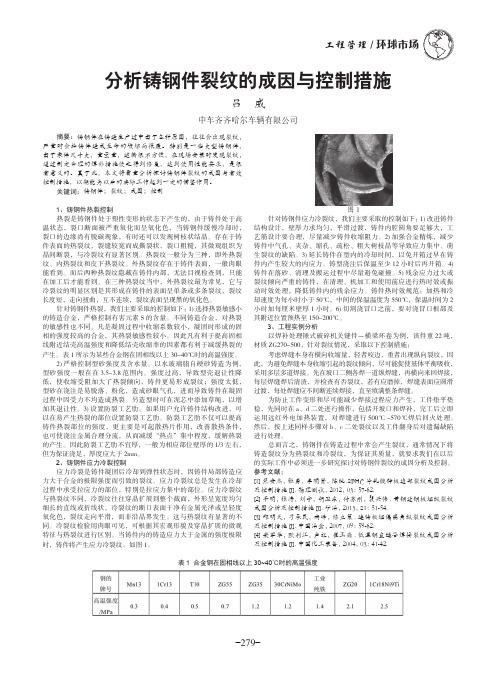
环球市场工程管理/-279-分析铸钢件裂纹的成因与控制措施吕 威中车齐齐哈尔车辆有限公司摘要:铸钢件在铸造生产过中由于各种原因,往往会出现裂纹,严重时会给铸件造成至命的破坏而报废。
特别是一些大型铸钢件,由于零件尺寸大,重量重,运输很不方便,在现场安装时发现裂纹,通过制定合理的焊补措施使之得到修复,达到使用性能要求,是很有意义的。
基于此,本文将着重分析探讨铸钢件裂纹的成因与有效控制措施,以期能为以后的实际工作起到一定的借鉴作用。
关键词:铸钢件;裂纹;成因;控制1、铸钢件热裂控制热裂是铸钢件处于塑性变形的状态下产生的,由于铸件处于高温状态,裂口断面被严重氧化而呈氧化色,当铸钢件缓慢冷却时,裂口的边缘尚有脱碳现象,有时还可以发现树枝状结晶。
存在于铸件表面的热裂纹,裂缝较宽而成撕裂状,裂口粗糙,其微观组织为晶间断裂,与冷裂纹有显著区别。
热裂纹一般分为三种,即外热裂纹、内热裂纹和皮下热裂纹。
外热裂纹存在于铸件表面,一般肉眼能看到。
而后两种热裂纹隐藏在铸件内部,无法目视检查到,只能在加工后才能看到。
在三种热裂纹当中,外热裂纹最为常见,它与冷裂纹的明显区别是其形成在铸件的表面呈单条或多条裂纹,裂纹长度短,走向扭曲,互不连续,裂纹表面呈现黑的氧化色。
针对铸钢件热裂,我们主要采取的控制如下:1)选择热裂敏感小的铸造合金,严格控制有害元素S 的含量。
不同铸造合金,对热裂的敏感性也不同。
凡是凝固过程中收缩系数较小,凝固时形成的固相的强度较高的合金,其热裂敏感性较小。
因此凡有利于提高固相线附近结壳高温强度和降低结壳收缩率的因素都有利于减缓热裂的产生。
表1所示为某些合金钢在固相线以上30~40℃时的高温强度。
2)严格控制型砂强度及含水量。
以水玻璃脂自硬砂铸造为例,型砂强度一般在在3.5-3.8范围内。
强度过高,导致型壳退让性降低,使收缩受阻加大了热裂倾向,铸件更易形成裂纹;强度太低,型砂在浇注是易脱落、粉化,造成砂眼气孔,进而导致铸件在凝固过程中因受力不均造成热裂。
铸件裂纹是怎么出现的?该怎么解决?看完终于明白了!
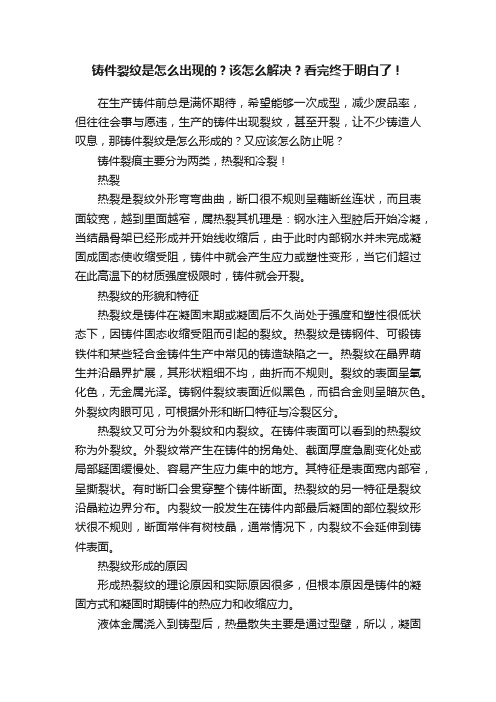
铸件裂纹是怎么出现的?该怎么解决?看完终于明白了!在生产铸件前总是满怀期待,希望能够一次成型,减少废品率,但往往会事与愿违,生产的铸件出现裂纹,甚至开裂,让不少铸造人叹息,那铸件裂纹是怎么形成的?又应该怎么防止呢?铸件裂痕主要分为两类,热裂和冷裂!热裂热裂是裂纹外形弯弯曲曲,断口很不规则呈藕断丝连状,而且表面较宽,越到里面越窄,属热裂其机理是:钢水注入型腔后开始冷凝,当结晶骨架已经形成并开始线收缩后,由于此时内部钢水并未完成凝固成固态使收缩受阻,铸件中就会产生应力或塑性变形,当它们超过在此高温下的材质强度极限时,铸件就会开裂。
热裂纹的形貌和特征热裂纹是铸件在凝固末期或凝固后不久尚处于强度和塑性很低状态下,因铸件固态收缩受阻而引起的裂纹。
热裂纹是铸钢件、可锻铸铁件和某些轻合金铸件生产中常见的铸造缺陷之一。
热裂纹在晶界萌生并沿晶界扩展,其形状粗细不均,曲折而不规则。
裂纹的表面呈氧化色,无金属光泽。
铸钢件裂纹表面近似黑色,而铝合金则呈暗灰色。
外裂纹肉眼可见,可根据外形和断口特征与冷裂区分。
热裂纹又可分为外裂纹和内裂纹。
在铸件表面可以看到的热裂纹称为外裂纹。
外裂纹常产生在铸件的拐角处、截面厚度急剧变化处或局部疑固缓慢处、容易产生应力集中的地方。
其特征是表面宽内部窄,呈撕裂状。
有时断口会贯穿整个铸件断面。
热裂纹的另一特征是裂纹沿晶粒边界分布。
内裂纹一般发生在铸件内部最后凝固的部位裂纹形状很不规则,断面常伴有树枝晶,通常情况下,内裂纹不会延伸到铸件表面。
热裂纹形成的原因形成热裂纹的理论原因和实际原因很多,但根本原因是铸件的凝固方式和凝固时期铸件的热应力和收缩应力。
液体金属浇入到铸型后,热量散失主要是通过型壁,所以,凝固总是从铸件表面开始。
当凝固后期出现大量的枝晶并搭接成完整的骨架时,固态收缩开始产生。
但此时枝晶之间还存在一层尚未凝固舶液体金属薄膜(液膜),如果铸件收缩不受任何阻碍,那么枝晶骨架可以自由收缩,不受力的作用。
双曲线轧辊断裂原因分析
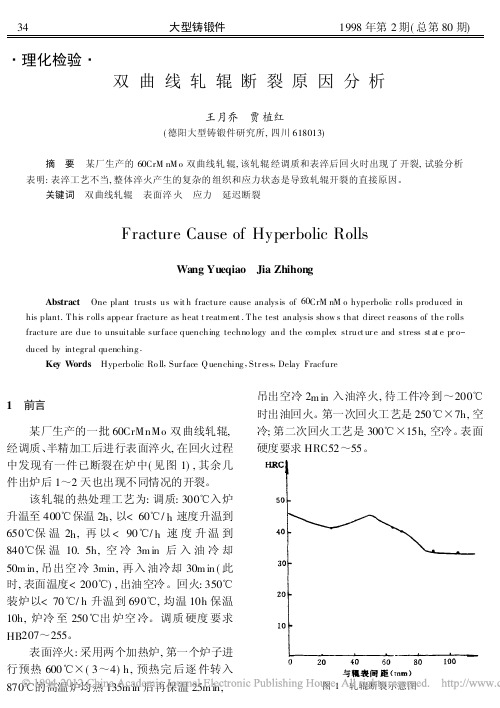
吊出空冷 2m in 入油淬火, 待工件冷到~200℃ 时出油回火。第一次回火工艺是 250℃×7h, 空 冷; 第二次回火工艺是 300℃×15h, 空冷。表面 硬度要求 HRC52~55。
关键词 双曲线轧辊 表面淬 火 应力 延迟断裂
Fracture Cause of Hyperbolic Rolls
Wang Yueqiao Jia Zhihong
Abstract One plant trusts us wit h fracture cause analysis of 60CrM nM o hyperbolic r olls produced in his plant. T his r olls appear fracture as heat t reatment . T he test analysis show s that direct r easons of the r olls fracture are due to unsuitable sur face quenching techno logy and the co mplex struct ur e and stress st at e pr oduced by integr al quenching .
评定断辊表面 至心部的非金 属夹杂物级 别, 心部夹杂物最高为: 脆性夹杂 1. 0 级, 塑性 夹杂物 2. 5 级, 总和 3. 5 级。
图 2 轧辊中部的横向低倍组织 图 3 轧辊低倍试片上的硬度分布
36
a
b
c 图 4 断辊显微组织 ×1000 a- 表面 b- 二分之一半径 c- 中心
铸钢件裂纹缺陷及预防措施
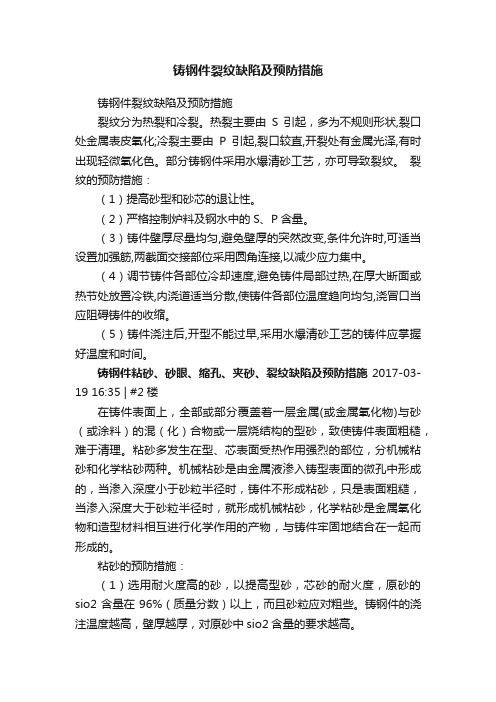
铸钢件裂纹缺陷及预防措施铸钢件裂纹缺陷及预防措施裂纹分为热裂和冷裂。
热裂主要由S引起,多为不规则形状,裂口处金属表皮氧化;冷裂主要由P引起,裂口较直,开裂处有金属光泽,有时出现轻微氧化色。
部分铸钢件采用水爆清砂工艺,亦可导致裂纹。
裂纹的预防措施:(1)提高砂型和砂芯的退让性。
(2)严格控制炉料及钢水中的S、P含量。
(3)铸件壁厚尽量均匀,避免壁厚的突然改变,条件允许时,可适当设置加强筋,两截面交接部位采用圆角连接,以减少应力集中。
(4)调节铸件各部位冷却速度,避免铸件局部过热,在厚大断面或热节处放置冷铁,内浇道适当分散,使铸件各部位温度趋向均匀,浇冒口当应阻碍铸件的收缩。
(5)铸件浇注后,开型不能过早,采用水爆清砂工艺的铸件应掌握好温度和时间。
铸钢件粘砂、砂眼、缩孔、夹砂、裂纹缺陷及预防措施2017-03-19 16:35 | #2楼在铸件表面上,全部或部分覆盖着一层金属(或金属氧化物)与砂(或涂料)的混(化)合物或一层烧结构的型砂,致使铸件表面粗糙,难于清理。
粘砂多发生在型、芯表面受热作用强烈的部位,分机械粘砂和化学粘砂两种。
机械粘砂是由金属液渗入铸型表面的微孔中形成的,当渗入深度小于砂粒半径时,铸件不形成粘砂,只是表面粗糙,当渗入深度大于砂粒半径时,就形成机械粘砂,化学粘砂是金属氧化物和造型材料相互进行化学作用的产物,与铸件牢固地结合在一起而形成的。
粘砂的预防措施:(1)选用耐火度高的砂,以提高型砂,芯砂的耐火度,原砂的sio2含量在96%(质量分数)以上,而且砂粒应对粗些。
铸钢件的浇注温度越高,壁厚越厚,对原砂中sio2含量的要求越高。
(2)适当降低浇注温度和提高浇注速度,减轻金属液对砂型的热力学和物理化学作用。
(3)砂型紧实度要高(通常大于85)且均匀,减少砂粒间隙;型、芯修补到位,不能有局部疏松。
(4)采用在高温下不开裂、不烧结成熔洞的涂料铸钢件砂眼缺陷及预防措施砂眼缺陷处内部或表面有充塞着型(芯)砂的小孔,砂眼是一种常见的铸造缺陷,往往导致铸件报废。
大型锻件粗晶缺陷的成因及控制措施

本文源自:中国无损检测论坛
金属材料的晶粒大小不是一成不变的,一般情况下,随着晶粒细化,钢的屈服强度、疲劳强度提高,同时具有很高的塑性和冲击韧性。
但发生粗晶时,锻材的塑性性能便会明显下降,影响了材料使用寿命。
粗晶影响因素:
1.变形温度
加热条件下,原子的活动能力增加,随着加热温度升高,原子的扩散能力增加,晶粒长大趋势加剧,细晶粒极易变为粗晶粒。
加热温度越高,粗晶越严重。
2、保温时间
高温保温时间越长,粗晶现象越严重,但较加热温度影响小。
3、变形程度
粗晶可以通过热变形消除,原始加热温度越高,所需变形程度越大。
预防粗晶应采取的措施:
1、锻造前加热温度应严格控制在平衡图固相线(AE)以下150-250℃。
保温时间不宜过长,要根据锭型确定合理的保温时间。
2、锻造变形可以打碎粗大的奥氏体晶粒,细化组织,消除粗晶。
3、锻造过程中应尽量避免出现锻件上只加热而不变形部分。
4、在决定最后一次的加热温度时,要根据剩余变形量决定,以免由于终锻温度过高,引起晶粒粗大,变形程度过小,锻造变形力传递不到锻件中心。
在锻造变形时,应避免小压下量变形工艺。
本文摘自: 中国无损检测论坛() 详细出处请参考:/forum.php?mod=viewthread&tid=669&extra=page%3D4。
锻造裂纹的原因分析及预防措施

应力状态如图示防止裂纹再次产 Nhomakorabea的措施从冶炼的角度讲,应从提高钢锭头尾部的冶金质量, 即提高钢的纯净度和细化晶粒、均匀结晶组织的角 度出发,改善冶炼条件,提高头尾部的可锻性;
从锻压方面讲,应从应力状态和减小锤击力出发, 即避免产生轴心径向拉应力和减小变形程度的方面 做文章,避免裂纹的产生。打击辊颈时,送进量应 限制在坯料直径的0.5~0.8倍之间,避免拔长辊颈时 出现径向展宽现象,既提高了拔长效率,又避免轴 心的径向拉应力。另外,限制锤的打击力,尽可能 在两吨锤上成形,并选择合适的压下量,以减轻心 部的变形程度。两方面入手,以避免裂纹的产生。
锻造裂纹的原因分析及预防措施
φ288mm冷轧辊尾部锻造裂纹
锻件成形及缺陷位置示意图
该件产品用1.75吨钢锭出3件产品,成形情况 及缺陷出现位置如图示
头 1
尾
2
3
裂纹形成原因分析
首先我们看缺陷产生的部位,在钢锭的头尾端。而 钢锭锭身却很少出现缺陷,钢锭的头尾部的冶金质 量不如锭身也是我们的共识,这应是裂纹产生的本 质上的原因。
说明
以上观点仅为个人看法。
其次,辊身与辊颈的台阶差较大。辊身的直径为 288mm,裂纹端辊颈才100mm,台阶差188。变形 过程中有两方面问题要说,一方面下圆弧砧的圆弧 大,击打辊颈时,近似于平砧,即料侧面未受力。 砧宽为250mm,若送进量过大,对于辊颈而言,轴 向拔长就变成了径向展宽,即应力状态为轴心径向 拉应力(如下图示),容易产生轴心纵向裂纹;另 一方面,因辊身与辊颈的台阶差大,操作时可能重 锤打击,造成心部变形量过大。头尾料差的塑性与 低的强度加之径向拉应力和重锤就可能导致裂纹的 产生,这应是裂纹产生的外因。