新一代TMCP技术助力轧钢生产降本增效
TMCP_热机轧制_在中厚板工程中的应用_李伟

机前、机后或机架间的待温辊道一般采用在线型 式 ,也可采用离线型式 ,后者需增设钢材平移装置 ,且 辊道总数较多 ,故设备投资较多 ,且现场比较拥挤。 但
52
现 代 冶 金
第 38卷
它可缩短设备间距 ,主厂房长度可一定程度缩短。
一般为成品厚度的 1. 5~ 4. 0倍 ,成品阶段总压下率
一般不小于 60% ,终轧温度通常为小于 900℃。对于
4 热机轧制的工艺控制
某些特殊要求的产品 ,中间坯厚度还需增大 ,终轧温 度也要求适当降低。
热机轧制中 ,轧制时间与中间坯待温时间的配
锅炉板
20 g, 19 M ng
同上
一般 1. 3倍成品
厚度低强度等
1 200 级可常规轧制
9 40
生产
< 900
无要求
无要求
低强度等级可常规轧制生产 ,高强 度等 级一 般为铌 ( Nb)合 金钢 ,需 热机轧制 ( TM C P)生产。
压力 容器 钢板
16 MnR
同上
1 200
同上
桥梁板
16 M nq
图 1 各种轧制程序的模式图
2 热机轧制 ( TMCP)的金属学原理
钢材从奥氏体 (V)向铁素体 (T)的相变转化过程 中 ,其相变组织在大范围内变化 ,从而使强度和韧性 等性能变化较大。 钢材的强度因铁素体晶粒的微细 化而得到提高。 铁素体所特有的低温脆性也会因晶 粒的微细化得到改善。此外 ,显微组织微细化是同时 改善强度和低温韧性的唯一方法。
热轧板带钢新一代TMCP装备及工艺技术
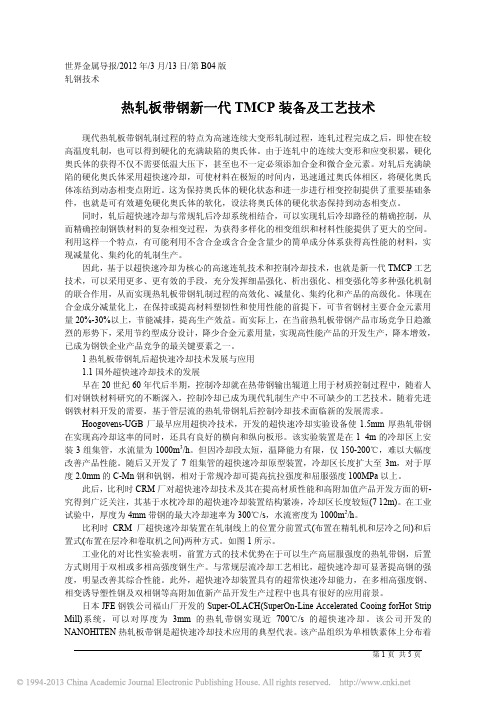
世界金属导报/2012年/3月/13日/第B04版轧钢技术热轧板带钢新一代TMCP装备及工艺技术现代热轧板带钢轧制过程的特点为高速连续大变形轧制过程,连轧过程完成之后,即使在较高温度轧制,也可以得到硬化的充满缺陷的奥氏体。
由于连轧中的连续大变形和应变积累,硬化奥氏体的获得不仅不需要低温大压下,甚至也不一定必须添加合金和微合金元素。
对轧后充满缺陷的硬化奥氏体采用超快速冷却,可使材料在极短的时间内,迅速通过奥氏体相区,将硬化奥氏体冻结到动态相变点附近。
这为保持奥氏体的硬化状态和进一步进行相变控制提供了重要基础条件,也就是可有效避免硬化奥氏体的软化,设法将奥氏体的硬化状态保持到动态相变点。
同时,轧后超快速冷却与常规轧后冷却系统相结合,可以实现轧后冷却路径的精确控制,从而精确控制钢铁材料的复杂相变过程,为获得多样化的相变组织和材料性能提供了更大的空间。
利用这样一个特点,有可能利用不含合金或含合金含量少的简单成分体系获得高性能的材料,实现减量化、集约化的轧制生产。
因此,基于以超快速冷却为核心的高速连轧技术和控制冷却技术,也就是新一代TMCP工艺技术,可以采用更多、更有效的手段,充分发挥细晶强化、析出强化、相变强化等多种强化机制的联合作用,从而实现热轧板带钢轧制过程的高效化、减量化、集约化和产品的高级化。
体现在合金成分减量化上,在保持或提高材料塑韧性和使用性能的前提下,可节省钢材主要合金元素用量20%-30%以上,节能减排,提高生产效益。
而实际上,在当前热轧板带钢产品市场竞争日趋激烈的形势下,采用节约型成分设计,降少合金元素用量,实现高性能产品的开发生产,降本增效,已成为钢铁企业产品竞争的最关键要素之一。
1热轧板带钢轧后超快速冷却技术发展与应用1.1国外超快速冷却技术的发展早在20世纪60年代后半期,控制冷却就在热带钢输出辊道上用于材质控制过程中,随着人们对钢铁材料研究的不断深入,控制冷却已成为现代轧制生产中不可缺少的工艺技术。
新一代TMCP技术控轧控冷

新一代TMCP技术
RAL.NEU
RAL
TMCP技术的发展和创新
• TMCP是20世纪最伟大的钢铁技术成果之一 • 开发引领未来社会发展和人类需求的新一代钢 铁材料 • 需要付出巨大的努力,充分利用新的科技成 果,站在巨人的肩膀上进行钢铁生产过程的脱 胎换骨的革命
RAL
TMCP技术的发展和创新
RAL
高速连轧的温度制度-“趁热打铁”
新一代的TMCP采用适宜的正常轧制温度 进行连续大变形,在轧制温度制度上不再坚持 “低温大压下”的原则。与“低温大压下”过程相 比,轧制负荷可大幅度降低,设备条件的限制 可放松。轧机建设不必追求高强化,大幅度降 低建设投资。
RAL
高速连轧的温度制度-“趁热打铁”
适宜的轧制温度,大大提高轧制的可操作 性,避免轧制工艺事故,例如卡钢、堆钢等, 同时也延长了轧辊、导卫等轧制工具的寿命。 提高产量、降低成本 对于一些原来需要在粗轧和精轧之间实施 待温的材料,可以直接轧制
RAL
“趁热打铁”及其优点
由于新一代的TMCP避免了“低温大压下”,使得传统的“趁 热打铁”的思想得以贯彻实行,这对于减轻生产设备负荷、确 保轧制过程稳定、改善加工过程的可操作性、提高材料的可加 工性、降低轧制能耗等具有十分重要的意义。由于可以少加或 者不加微合金元素和合金元素,所以可以节省大量的资源和能 源,实现减量化的轧制,降低钢材生产成本,这对于钢铁工业 的可持续发展和协调发展具有重要的作用。
RAL
TMCP特征
• 低温大压下——轧制负荷、生产率、设备投 资、轧制稳定性 • 微合金化——提高成本、焊接性能恶化、冶炼连铸-轧制工艺复杂、轧制负荷增大 • 水是最廉价的合金元素——高冷却速率的开发 利用、冷却路径的利用、冷却的均匀性
热轧钢铁材料新一代TMCP技术

世界金属导报/2012年/1月/10日/第B04版轧钢技术热轧钢铁材料新一代TMCP技术TMCP(Thermo-MechanicalControlled Processing),即控制轧制和控制冷却技术,是20世纪钢铁业最伟大的成就之一,也是目前钢铁材料轧制及产品工艺开发领域应用最为普遍的技术之一。
正是因为有了TMCP技术,钢铁工业才能源源不断地向社会提供越来越有用的钢铁材料,支撑着人类社会的发展和进步。
1 TMCP工艺技术的发展及基本原理TMCP工艺的两个重要组成部分之一,控制轧制,在热轧钢铁材料领域很早就已根据经验予以实施,其核心思想是对奥氏体硬化状态的控制,即通过变形在奥氏体中积累大量的能量,力图在轧制过程中获得处于硬化状态的奥氏体,为后续的相变过程实现晶粒细化做准备。
在20世纪60年代至70年代,随着能源不断开发,对高性能管线钢的需求大幅增加。
为满足管线钢板的生产,控制轧制技术得到快速发展,并在当时的厚板轧制、船板生产等方面得到广泛应用。
为了突破控制轧制的限制,同时也是为了进一步强化钢材的性能,在控制轧制的基础上,又开发了控制冷却技术。
控制冷却的核心思想是对处于硬化状态的奥氏体相变过程进行控制,以进一步细化铁素体晶粒,甚至通过相变强化得到贝氏体等强化相。
相变组织比单纯控制轧制更加细微化,促使钢材获得更高的强度,同时又不降低其韧性,从而进一步改善材料的性能。
1980年,日本NKK福山制铁所首次为厚板生产线配置并使用了OLAC(On-Line Accelerated Cooling)系统。
此后基于对提高厚板性能及钢种开发的需要,重点发展了厚板的快速在线冷却技术,并相继开发出一系列快速冷却装置,投入厚板的开发生产及应用中。
控制冷却设备的普遍应用有力地推动了高强度板带材的开发和在提高材质性能方面技术的进步。
后来,人们将结合控制轧制和控制冷却的技术称为控轧控冷技术TMCP(Thermo-MechanicalControlled Processing)。
采用TMCP工艺开发低成本高强钢Q550
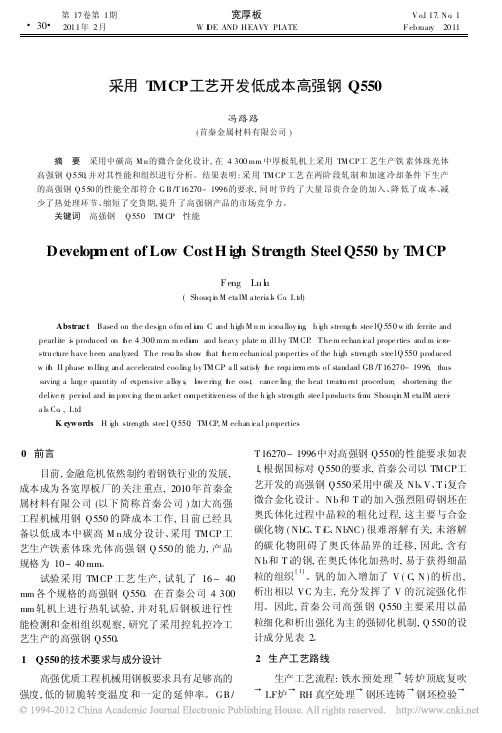
采用T MCP工艺开发低成本高强钢Q550冯路路(首秦金属材料有限公司)摘要采用中碳高M n的微合金化设计,在4300mm中厚板轧机上采用TM CP工艺生产铁素体珠光体高强钢Q550,并对其性能和组织进行分析。
结果表明:采用TM CP工艺在两阶段轧制和加速冷却条件下生产的高强钢Q550的性能全部符合G B/T16270-1996的要求,同时节约了大量昂贵合金的加入、降低了成本、减少了热处理环节、缩短了交货期,提升了高强钢产品的市场竞争力。
关键词高强钢Q550TM CP性能Develop m ent of Low CostH igh Stre ngth Steel Q550by T MCPFeng Lu l u(Shouq i n M eta lM a teria l s Co.L td)Abstrac t Based on the desi gn o fm ed i u m C and high M n m icroa lloy i ng,h i gh streng t h stee lQ550w ith ferrite and pearlite i s produced on t he4300mm m edi u m and heavy plate m ill by TM CP.T he m echan i ca l prope rties and m icro-struct ure have been ana lyzed.T he res u lts show t hat t he m echanical properti es o f the high strength stee lQ550produced w it h II phase ro lli ng and accelerated coo li ng by TM CP a ll satisf y t he requ irem ents o f standard GB/T16270-1996,thus saving a larg e quantity of expensive a lloy s,l owe ri ng t he cost,cance li ng the heat treat m ent procedure,shortening the deli ve ry per i od and i m prov i ng the m arke t competiti veness of the h i gh strength stee l products fro m Shouqi n M eta lM ater-i a ls Co.,L td.K eywords H i gh strength stee,l Q550,TM CP,M echan i ca l properties0前言目前,金融危机依然制约着钢铁行业的发展,成本成为各宽厚板厂的关注重点,2010年首秦金属材料有限公司(以下简称首秦公司)加大高强工程机械用钢Q550的降成本工作,目前已经具备以低成本中碳高M n成分设计、采用TMCP工艺生产铁素体珠光体高强钢Q550的能力,产品规格为10~40mm。
新一代tmcp工艺下热轧钢材显微组织的基本原理
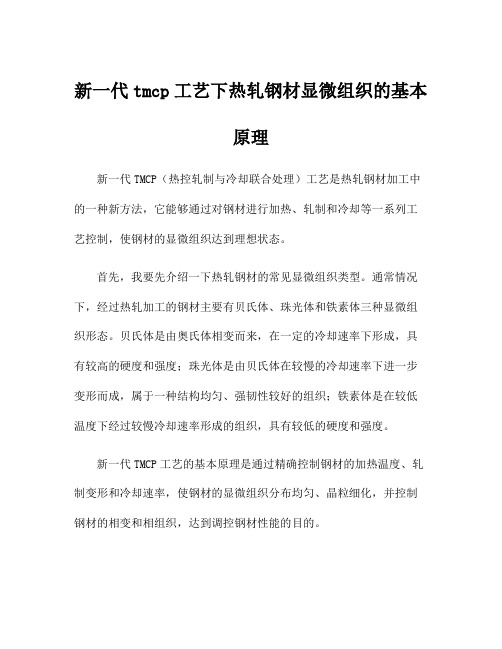
新一代tmcp工艺下热轧钢材显微组织的基本原理新一代TMCP(热控轧制与冷却联合处理)工艺是热轧钢材加工中的一种新方法,它能够通过对钢材进行加热、轧制和冷却等一系列工艺控制,使钢材的显微组织达到理想状态。
首先,我要先介绍一下热轧钢材的常见显微组织类型。
通常情况下,经过热轧加工的钢材主要有贝氏体、珠光体和铁素体三种显微组织形态。
贝氏体是由奥氏体相变而来,在一定的冷却速率下形成,具有较高的硬度和强度;珠光体是由贝氏体在较慢的冷却速率下进一步变形而成,属于一种结构均匀、强韧性较好的组织;铁素体是在较低温度下经过较慢冷却速率形成的组织,具有较低的硬度和强度。
新一代TMCP工艺的基本原理是通过精确控制钢材的加热温度、轧制变形和冷却速率,使钢材的显微组织分布均匀、晶粒细化,并控制钢材的相变和相组织,达到调控钢材性能的目的。
首先,新一代TMCP工艺中的热轧温度控制是非常关键的。
通过控制热轧温度可以实现钢材的相变和显微组织形态的控制。
一般来说,较高的热轧温度可以促使钢材中的贝氏体形成,而较低的热轧温度则有利于珠光体的形成。
因此,通过精确控制热轧温度可以实现贝氏体和珠光体的控制。
其次,新一代TMCP工艺中的轧制变形控制也是非常重要的。
通过控制轧制变形,可以实现钢材中晶粒的细化,从而提高钢材的强度和韧性。
一般来说,较大的轧制变形可以使钢材中的晶粒细化,形成更加各向均匀的组织结构。
因此,通过精确控制轧制变形可以实现晶粒细化的效果。
最后,新一代TMCP工艺中的冷却速率控制也是十分重要的。
通过控制冷却速率可以实现钢材中相变的控制。
一般来说,较快的冷却速率可以促使钢材中的贝氏体相变,而较慢的冷却速率则有利于珠光体和铁素体的形成。
因此,通过精确控制冷却速率可以实现相变的控制。
综上所述,新一代TMCP工艺通过精确控制钢材的加热温度、轧制变形和冷却速率,能够实现钢材显微组织的调控,从而提高钢材的强度和韧性。
在实际应用中,通过合理选择控制参数,可以得到理想的显微组织,满足不同工程要求。
以超快速冷却为核心的新一代TMCP技术
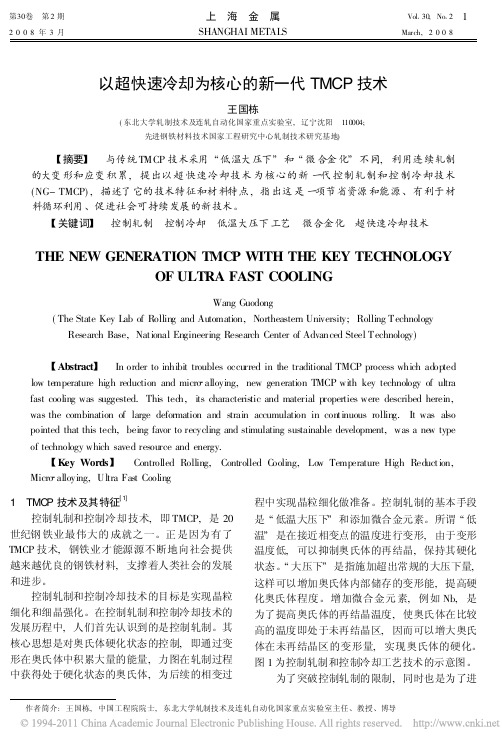
以超快速冷却为核心的新一代TMCP 技术王国栋(东北大学轧制技术及连轧自动化国家重点实验室,辽宁沈阳 110004;先进钢铁材料技术国家工程研究中心轧制技术研究基地)摘要 与传统TMCP 技术采用!低温大压下∀和!微合金化∀不同,利用连续轧制的大变形和应变积累,提出以超快速冷却技术为核心的新一代控制轧制和控制冷却技术(NG-TMCP),描述了它的技术特征和材料特点,指出这是一项节省资源和能源、有利于材料循环利用、促进社会可持续发展的新技术。
关键词 控制轧制 控制冷却 低温大压下工艺 微合金化 超快速冷却技术作者简介:王国栋,中国工程院院士,东北大学轧制技术及连轧自动化国家重点实验室主任、教授、博导THE NEW GENERATION TMCP WITH THE KEY TECHNOLOGYOF ULTRA FAST COOLINGWang Guodong(The State Key Lab of Rolling and Automation,Northeastern University;Rolling Technology Research Base,National Engineering Research Center of Advanced Steel Technology)Abstract In order to inhibit troubles occurred in the traditional TMCP process which adopted low te mperature high reduction and micro alloying,new generation TMCP with key technology of ultra fast cooling was suggested.This tec h,its characteristic and material properties were described herein,was the combination of large deformation and strain accumulation in continuous rolling.It was also pointed that this tech,being favor to recycling and stimulating sustainable development,was a ne w type of technology which saved resource and energy.Key Words Controlled Rolling,Controlled C ooling,Lo w Temperature High Reduction,Micro alloying,Ultra Fast Cooling1 TMC P 技术及其特征[1]控制轧制和控制冷却技术,即TMCP,是20世纪钢铁业最伟大的成就之一。
采用TMCP工艺开发低成本高强钢Q550
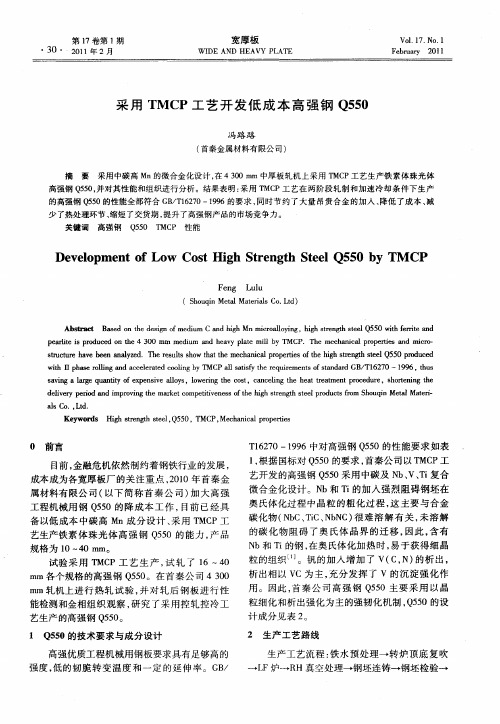
工程机械 用钢 Q 5 5 0的降 成 本 工作 , 目前 已经 具 备以低 成本 中碳 高 M n成 分设 计 、 用 T P工 采 MC 艺 生产铁素 体 珠 光 体 高强 钢 Q 5 5 0的能 力 , 品 产
规格 为 1 4 m。 O~ 0m
试验 采 用 T P工 艺 生 产 , 轧 了 1 MC 试 6~4 0 m m各 个规格 的高强钢 Q 5 。在首 秦公 司 43 0 50 0
第 1 第1 7卷 期
・
宽 厚 板
WI DE AND HEAVY pLATE
V0 . 7. 1 1 No. 1 Fe r a y 2 1 b u r 01
3 ・ 21 0 0 1年 2月
采用 T MC P工 艺 开 发 低 成 本 高 强 钢 Q 5 50
冯路路 ( 首秦金属材料有限公 司) 摘 要 采用中碳高 Mn的微合金化设计 , 430m 在 0 m中厚板轧机上采用 T P工艺 生产铁 素体珠 光体 MC
少 了热处 理 环 节 、 短 了 交货 期 , 升 了高 强 钢产 品的 市 场竞 争 力 。 缩 提 关键 词 高 强钢 Q 5 T C 性 能 50 M P
D v lp n fL w C s HihSrn t te 5 0b M C eeo me t o ot g te gh Sel 5 yT o Q P
as C . Ld l o , t.
K y od H g r g t lQ 5 , M P M cai r e i ew rs ihs et s e,50 T C , ehnc po re tn h e l a pt s
பைடு நூலகம்
0 前 言
T67 12 0—19 9 6中对 高强钢 Q 5 5 0的性 能要求 如表 1根据 国标对 Q 5 , 5 0的要求 , 公司 以 T P工 首秦 MC
TMCP技术在Q460D钢板生产中的应用
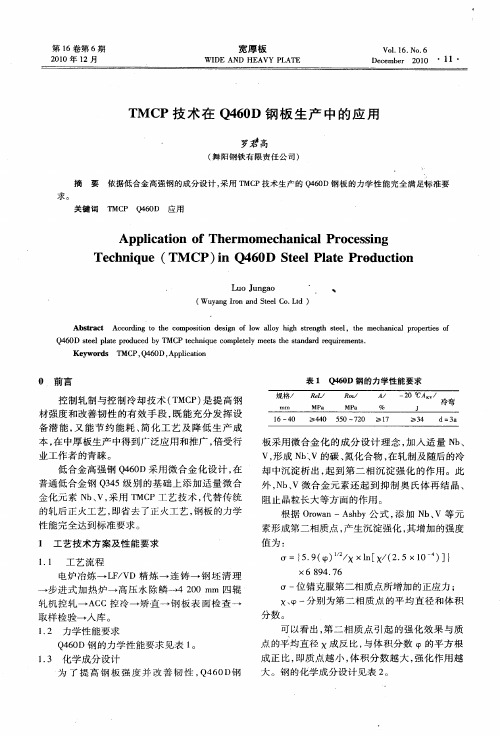
21 0 0年 l 2月
宽厚板
WI DE AND HEAVY LATE P
Vo _ 6. . l 1 No 6
D c mb r 2 0 e e e 01
・1 ・ I
T MC P技 术 在 Q4 0 钢 板 生 产 中 的 应 用 6D
罗君 高
( 阳钢 铁 有 限责 任 公 司 ) 舞
盯={. (p / n X ( . 59 ‘ ) X×I[/ 25×1 ) } 0 ]
×6 8 4. 6 9 7
一
电炉冶 炼一 L / D 精 炼一 连 铸 一 钢 坯 清 理 FV
一
步进 式 加 热 炉一 高 压 水 除 鳞 2 0 m 四辊 0 m 轧机控 轧 一 A c控 冷一 矫直 一 钢 板 表 面 检查 一 c 12 力 学性 能要求 . Q 6 D钢 的力学 性能要 求见 表 1 40 。
摘
求。
要
依 据 低 合 金 高强 钢 的成 分设 计 , 用 T P技术 生 产 的 Q 5 D钢 板 的 力学 性 能 完 全 满 足标 准 要 采 MC 40
T P Q 6 D 应 用 MC 4 0
关键词
App ia i n o e m o e h n c lPr c s i g l to fTh r c m c a i a o e sn
的轧后 正 火工艺 , 即省 去了正火工 艺 , 钢板 的力学
板采用 微合 金 化 的成 分 设 计 理 念 , 入适 量 N 、 加 b V, 形成 N \ b V的碳 、 氮化合 物 , 轧制及 随后 的冷 在 却 中沉 淀析 出 , 到 第二 相 沉 淀 强化 的作 用 。此 起 外 , b V微 合金元 素 还起 到 抑 制 奥 氏体 再 结 晶、 N 、
新一代TMCP技术的前景靓丽
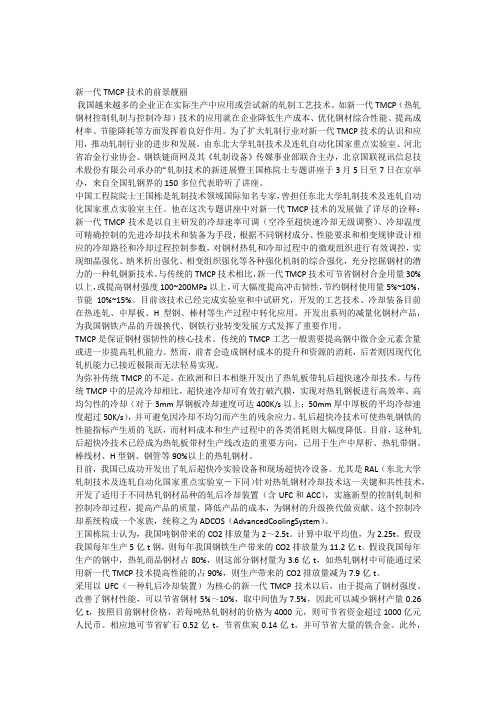
新一代TMCP技术的前景靓丽我国越来越多的企业正在实际生产中应用或尝试新的轧制工艺技术。
如新一代TMCP(热轧钢材控制轧制与控制冷却)技术的应用就在企业降低生产成本、优化钢材综合性能、提高成材率、节能降耗等方面发挥着良好作用。
为了扩大轧制行业对新一代TMCP技术的认识和应用,推动轧制行业的进步和发展,由东北大学轧制技术及连轧自动化国家重点实验室、河北省冶金行业协会、钢铁链商网及其《轧制设备》传媒事业部联合主办,北京国联视讯信息技术股份有限公司承办的“轧制技术的新进展暨王国栋院士专题讲座于3月5日至7日在京举办,来自全国轧钢界的150多位代表聆听了讲座。
中国工程院院士王国栋是轧制技术领域国际知名专家,曾担任东北大学轧制技术及连轧自动化国家重点实验室主任。
他在这次专题讲座中对新一代TMCP技术的发展做了详尽的诠释:新一代TMCP技术是以自主研发的冷却速率可调(空冷至超快速冷却无级调整)、冷却温度可精确控制的先进冷却技术和装备为手段,根据不同钢材成分、性能要求和相变规律设计相应的冷却路径和冷却过程控制参数,对钢材热轧和冷却过程中的微观组织进行有效调控,实现细晶强化、纳米析出强化、相变组织强化等各种强化机制的综合强化,充分挖掘钢材的潜力的一种轧钢新技术。
与传统的TMCP技术相比,新一代TMCP技术可节省钢材合金用量30%以上,或提高钢材强度100~200MPa以上,可大幅度提高冲击韧性,节约钢材使用量5%~10%,节能10%~15%。
目前该技术已经完成实验室和中试研究,开发的工艺技术、冷却装备目前在热连轧、中厚板、H型钢、棒材等生产过程中转化应用,开发出系列的减量化钢材产品,为我国钢铁产品的升级换代、钢铁行业转变发展方式发挥了重要作用。
TMCP是保证钢材强韧性的核心技术。
传统的TMCP工艺一般需要提高钢中微合金元素含量或进一步提高轧机能力。
然而,前者会造成钢材成本的提升和资源的消耗,后者则因现代化轧机能力已接近极限而无法轻易实现。
新一代TMCP技术的发展_王国栋
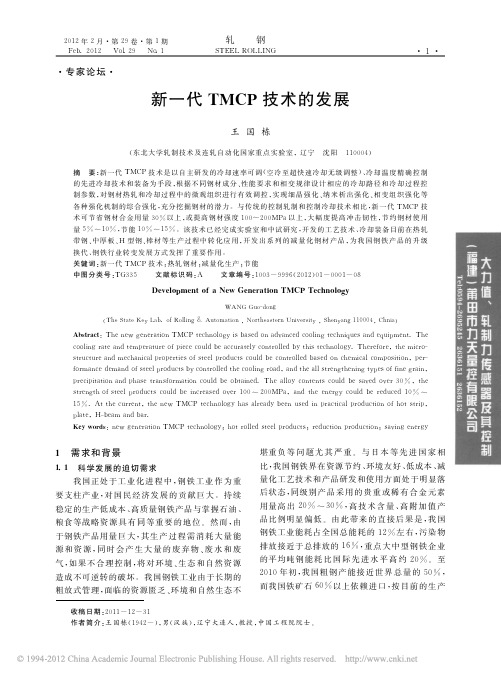
堪重负 等 问 题 尤 其 严 重 。 与 日 本 等 先 进 国 家 相 比, 我国钢铁界在资源节约 、 环境友好 、 低成本 、 减 量化工艺技术和产品研发和使用方面处于明显落 后状态 , 同级别产 品 采 用 的 贵 重 或 稀 有 合 金 元 素 用量高 出 2 高 技 术 含 量、 高附加值产 0% ~3 0% , 我国 品比例明显 偏 低 。 由 此 带 来 的 直 接 后 果 是 , 钢铁工业能耗占全国总 能 耗 的 1 污染物 2% 左 右 , 重点大中型钢铁企业 排放接近于总排放的 1 6% , 的平均吨 钢 能 耗 比 国 际 先 进 水 平 高 约 2 0% 。 至 我国 粗 钢 产 能 接 近 世 界 总 量 的 5 2 0 1 0 年初 , 0% , 而我国铁矿石 6 按目前的生产 0% 以上依 赖 进 口 ,
控制冷却工艺一般需要提高钢中微合金元素含量 或进一步提 高 轧 机 能 力 。 然 而 , 前者会造成钢材 成本的提升和资 源 的 消 耗 , 后者则因现代化轧机 能力已接近 极 限 而 无 法 轻 易 实 现 。 另 外 , 长期以 来, 国内外普遍追 求 通 过 低 温 大 压 下 来 实 现 钢 材 对于普碳钢材而言 , 晶 的细晶强化 。 但实践证明 , 粒尺寸小到 2 尽管钢材的强度可有效 m 以下时 , μ 但其屈强比接近 1, 已经 失 去 工 程 材 料 的 应 提升 , 用价值 。 追求超细晶的生产工艺不仅会降低热轧 生产效率 、 增加事故发生率 , 而且会把过多的负担 转移到轧制过程 , 忽视了轧后冷却对钢材性能的 调控作用 。 此外 , 传统 TMC P 技术在提高热轧钢 会因低温轧制产生残余应力而 板强韧性的同时 , 带来板形不良和 剪 裁 瓢 曲 等 问 题 ; 生产高强钢厚 板时 , 除非提高钢 中 合 金 元 素 含 量 或 进 行 轧 后 热 否 则 已 无 法 突 破 强 度 和 厚 度 规 格 的 极 限。 处 理, 热轧钢铁 材 料 的 相 变 主 要 在 轧 后 冷 却 过 程 中 完 它 是 调 控 组 织 结 构、 最终控制性能的主要手 成, 段 。 因此 , 为实现资源节约型高性能钢材的生产 , 必须对轧后冷却 技 术 进 行 创 新 , 通过冷却路径和 冷却速率的优化 控 制 , 实现钢材组织和性能的调 控, 使成分简单的 钢 铁 材 料 能 够 具 备 满 足 多 样 化 要求的性能指标 。 为弥补传统控 制 冷 却 技 术 的 不 足 , 在欧洲和 日本相继 开 发 出 了 热 轧 板 带 轧 后 超 快 速 冷 却 技 术 。 传统的层流冷却和新一代的超快速冷却具有 即需要使用冷却水 , 利用冷却水来调 共同的特点 , 。但 节热轧 钢 材 的 冷 却 过 程 ( 材 料 的 相 变 过 程) 是, 与传统层流冷却相比 , 超快速冷却可有效打破 汽膜 , 实现对热轧钢板进行高效率 、 高均匀性的冷 / 却( 对于 3 mm 厚 钢 板 冷 却 速 率 可 达 4 0 0 K s以 / 上; 5 0 mm 厚 中 厚 板 的 平 均 冷 却 速 率 超 过 5 0 K ) , 并可 避 免 因 冷 却 不 均 匀 而 产 生 的 残 余 应 力 。 s 轧后超快冷技术使热轧钢板的性能指标有了质的 飞跃 , 而材料成本 和 生 产 过 程 中 的 各 类 消 耗 则 大 幅度降低 。 目前 , 轧后超快冷技术已经成为热轧 板带材生产线改 造 的 重 要 方 向 , 已用于生产中厚 板、 热轧 带 钢 、 棒 线 材、 钢管等9 H 型 钢、 0% 以 上 的热轧钢材 。 与 常 规 冷 却 方 式 相 比 , 超快冷不仅 且与常规 A 可以提高 冷 却 速 率 , C C 配合可实现 与性能要求相适应的多种冷却路径优化控制 。 但 是, 与对传统轧制技术的研究深度和广度相比 , 关 于超快速冷却条件下的各种物理冶金学规律尚未
无缝钢管生产中的控轧控冷技术

1) 在线常化工艺:需主要关注合理选择常化 链床长度、链床运行速度、冷却方式、增加水冷 环以及再加热炉的工艺参数设定等。
2)在线淬火(含在线固溶处理)工艺:需主要关 注冷却方式的选择,应尽量选择“内喷+外淋、钢 管夹持旋转”或“钢管旋转的同时浸入水槽、内 表面轴流喷水”的淬 火方式,后者还可变换为钢 管沿水槽轴向前进或水基液淬火。
/
虽然无缝钢管控轧控冷技术不能从变形温度、 变形量、变形道次、变形间隙时间、终轧温度以 及终轧后的冷却工艺等方面形成一套完整的控轧 控冷方案,但是目前无缝钢管的控轧控冷技术也 形成了包括在线常化、在线淬火和在线快速冷却 等多种工艺,呈多样化发展。
在线常化是一种热处理工艺,亦称在线正火, 是在热轧生产线上轧管工序之后,使钢管在奥氏 体相区内空冷或强制冷却后,得到均匀金相组织 的工艺。该工艺将热处理过程与轧制变形过程结 合在轧钢连续生产环节,其工艺特点既包含相变, 又包含轧制变形,因而属于现代轧制新工艺的一 种。通过在线常化工艺,既可以使钢材组织均匀, 晶粒细化,为进一步热处理做好准备,又可以改 善无缝钢管的综合力学性能。
无缝钢管生产中的控轧控冷技术
随着国家产业发展战略对资源节约和可持续 发展要求的提高,以及市场竞争的加剧,无缝钢 管生产企业越来越需要高性能、节约能源、成本 低的无缝钢管生产技术。因此,控制轧制和控制 冷却(简称控轧控冷,英文缩写TMCP)技术在无缝 钢管生产中越来越受重视。
控轧控冷技术作为一种降低合金消耗、减少 生产成本的有效手段,在热轧带钢、中厚板、棒 线材及H型钢工业生产中应用广泛。与板带的控轧 控冷技术相比,由于受钢管几何形状、轧制工艺、 轧制设备等因素的限制,无缝钢管在生产过程中 的可控、可变因素相对较少;因此,控轧控冷技术 在无缝钢管生产中的应用在一定程度上受到制约, 仍处于探索发展阶段。
论“TMCP技术”在轧钢生产中的意义作用

论“TMCP技术”在轧钢生产中的意义作用摘要本文结合作者几年来对相关课题的研究与在轧钢厂的相关实践经验,对“TMCP技术”的概念,产生背景,基本特点与技术优势(与其他轧钢强化工艺对比),发展现状进行了叙述,最后对于它在现代高性能热轧带钢生产中的意义与作用,提出了自己的看法。
关键词TMCP;控制轧制;控制冷却;热轧带钢1 TMCP技术概念近年来,随着社会发展与科学技术的进步,低合金高强度、高韧性并具有良好焊接性能的钢材已经在社会上得到了广泛的应用。
各行各业对热轧带钢的质量、品种、性能(强度、低温韧性及可焊性等)的要求也越来越高,而这些要求仅依靠传统的控制轧制工艺已经是无法满足了。
因此,不仅要用控轧工艺来控制奥氏体,而且要通过轧后冷却来控制相变本身,也就是利用轧后水冷进行控制冷却。
控制冷却成为继控制轧制之后中厚板生产史上的又一重大技术进步。
控轧与控冷技术相结合已成为宽厚板生产的主导工艺。
在国际上,将此工艺称为TMCP,全称(Thermomechanical Control Process),即:热机械控制工艺。
也就是在热轧过程中,在控制轧制温度、加热温度和压下量的控制轧制(Control Rolling)的基础上,再实施空冷或控制冷却及加速冷却(Accelerated Cooling)的技术总称。
2 TMCP技术产生背景60年代中期西方各国钢铁研究人员对控制轧制开始进行研究,政府也非常重视这方面的探索和开发。
60年代末到70年代初,世界上从事控制轧制机理研究的人越来越多,生产上的应用也日渐增多,70年代逐步开发出寒冷地带输油输气管线用X60,X65,X70等热轧板卷。
相关研究证明:应用控制轧制技术比用调质法、合金化及正火法能更好地降低碳当量,获得高塑性和焊接性,高强度同时又具有一定低温韧性的板带材,因此控制轧制技术得到了国际冶金界的极大重视。
但是,在控制轧制工艺中,一般要求保证较低的终轧温度或较大的变形量,从而会使轧机负荷大大增大,使机器的稳定性和安全性大大降低。
基于tmcp工艺的低成本q355b厚板开发
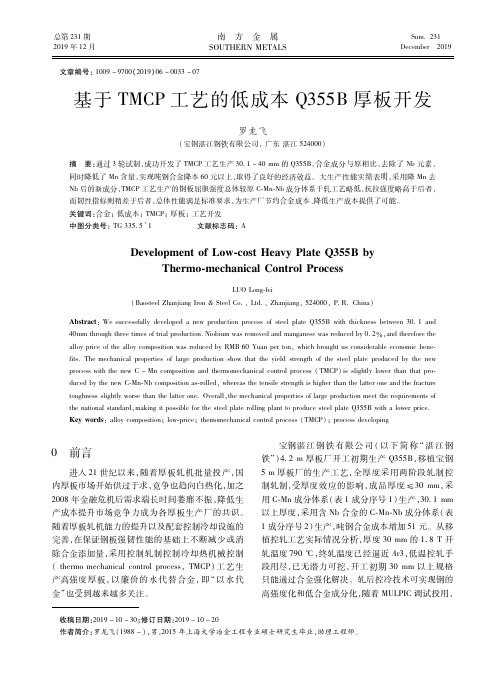
除合金添加量,采用控制轧制控制冷却热机械控制 轧温度790 ℃,终轧温度已经逼近Ar3,低温控轧手
( , )工艺生 thermo mechanical control process TMCP 段用尽,已无潜力可挖,开工初期30 mm 以上规格
产高强度厚板,以廉价的水代替合金,即“以水代 只能通过合金强化解决。轧后控冷技术可实现钢的
金”也受到越来越多关注。
高强度化和低合金成分化,随着MULPIC 调试投用,
收稿日期:2019 - 10 - 30;修订日期:2019 - 10 - 20 作者简介:罗龙飞(1988 - ),男,2015 年上海大学冶金工程专业硕士研究生毕业,助理工程师。
34
南 方 金 属
SOUTHERN METALS
总第 期 南方金属 231
Sum. 231
年 月 219 12
SOUTHERN METALS
December 2019
文章编号: ( )
1009 - 9700 2019 06 - 0033 - 07
fits. The mechanical properties of large production show that the yield strength of the steel plate produced by the new
( ) process with the new C - Mn composition and thermomechanical control process TMCP is slightly lower than that pro , duced by the new CMnNb composition asrolled whereas the tensile strength is higher than the latter one and the fracture , toughness slightly worse than the latter one. Overall the mechanical properties of large production meet the requirements of , the national standard making it possible for the steel plate rolling plant to produce steel plate Q355B with a lower price. : ; ; ( ); Key words alloy composition lowprice themomechanical control process TMCP process developing
东北大学01热轧钢铁材料新一代TMCP技术PPT

热轧钢铁材料新一代TMCP技术东北大学轧制技术及连轧自动化国家重点实验室2012年10月技术研发背景-钢铁工业面临的问题资源限制:铁矿石、合金依赖进口,年进口近7亿吨; 环境负荷:能耗高、CO 2/SO 2排放量同比高20%、污染严重;品种质量:产品档次低、同质化、无特色-严重供大于求;2011年:重点钢铁企业利润率仅2.4%,钢铁行业大面积亏损。
炼铁 炼钢 热轧 连铸 冷轧 热处理、涂镀使用热轧过程:大于95%以上钢材经历热加工,作用关键:成形、性能; TMCP (控制轧制与控制冷却):热加工过程的组织性能控制手段,对钢铁制造行业技术提升具有决定性影响;-20世纪最伟大的钢铁技术成果之一TMCP(控轧控冷):钢材热轧关键、共性技术TMCP制造技术的发展和创新1.二战后控制轧制作为提高材料强度的手段用于轧制工艺生产-低温轧制;2.1960年代,受能源需求影响,开发出控制轧制与Nb微合金化技术;3.1970年代,控制冷却技术得到进一步开发研究,用于热轧钢材生产;4.1980年代,开发出在线淬火技术,并用于实际生产;5.TMCP是20世纪最伟大的钢铁技术成果之一,支撑了钢铁材料的发展,对人类文明和社会发展作出了巨大贡献;6.关键在于创新——新一代的TMCP技术:作为材料物理冶金重要手段的TMCP技术,需要建立新的发展思路和开发框架。
减量化成分设计、工艺过程友好、减量化工艺、发挥冷却系统潜力总体思路:理论创新实现工艺、装备、产品的系统创新 创新的工艺:基于超快速冷却的新一代TMCP工艺——全新的热轧工艺理论、全新的产品强化机制等理论体系的完整建立 创新的装备:超快速冷却系统开发——高冷速、高冷却均匀性的水冷机理研究;高性能超快冷喷嘴系统结构开发、超快冷装备开发与集成——与轧线控制系统无缝衔接、高精度自动化控制系统开发创新的产品:减量化热轧钢铁材料产品工艺,产品升级换代——“成分节约型、工艺减量化”、低成本高性能热轧钢铁材料产品时间温度奥氏体中析出粒子 20-30nm铁素体中析出粒子小于10nm形变诱导析出TMCP: 低温大压下NG-TMCP 控制终轧温度析出 铁素体相变 传统 T M C P 新一代TMCPUFC :抑制析出温度时间离线工艺在线工艺UFC: 抑制相变控制轧制UFC :抑制晶粒长大; 细化晶粒尺寸; 避免低温大压下温度奥氏体再结晶· · · · · ·· · · · · · · · · · · · · · · 轧后立即超快冷动态相变点关键点:控制轧制与UFC 最佳匹配,超快冷抑制晶粒长大关键装备技术:热轧钢铁材料超快速冷却技术原理层流冷却:冷却效率低:膜态沸腾为主冷却均匀性差:过渡沸腾、残留水的无序流动超快速冷却核心技术-超快速冷却机理措施:采用带压力斜喷方式 有效打破钢板与水之间的汽膜 新水直接接触钢板实现核沸腾残水形成有序壁面射流,减少膜态/过渡沸腾超快速冷却关键技术-大型喷嘴结构开发1. 基于有限元流体模拟分析;2. 超快冷大型喷嘴系统结构开发:具有多重阻尼系统的大型整体式超宽狭缝式喷嘴多重阻尼系统长寿命周期高密快冷喷嘴装备核心技术:热轧钢铁材料超快速冷却喷水系统技术自主开发的系列超快速冷却装备-ADCOS中厚板超快冷装备热轧带钢超快冷装备H型钢超快冷装备棒材超快冷装备助力我国钢铁行业发展转型,节能减排,绿色发展!国家发改委:《产业结构调整指导目录(2011年版本》;“钢铁、有色、石化行业低碳技术创新及产业 化示范工程”;国家工信部:《产业关键共性技术发展指南(2011年)》;《“十二五”产业技术创新规划》;《钢铁工业“十二五”发展规划》;国家科技部:《中国科学技术发展报告(2010)》;“十二五”科技支撑计划项目“钢铁行业绿色制造关键技术集成应用示范”中国钢铁工业协会、中国金属学会:列为钢铁行业重点推广技术技术推广与应用-列入国家及行业重要发展政策指南热轧钢铁材料新一代TMCP工艺技术Thanks for your attention!。
热机轧制(TMCP)实验方案+(1)+(1)

小棒线热机轧制(TMCP)实验方案一、实验目的1、改善轴承钢组织形态,降低退火消耗;2、降低Cr、CrMo钢硬度;3、细化晶粒、提高钢的强韧性;4、冷镦钢热机轧制作为技术储备的工艺研究。
二、实验钢种45、40Cr、20-42CrMoA、GCr15三、化学成分及相关数据根据经验公式计算出相关钢种的奥氏体转变临界温度。
相关论文用公式:Ac1 = 723 - 26Si + 20Cr + 8W +16MO + 55V - 14Cu - 18Ni - 12Mn Ac3 = 910 - 320 C - 14Ni - 12Cu -10Mn + 5Cr + 7W + 14MO + 5V +18Si国内常用公式:Ac1=723-14Mn%+22Si%-14.4Ni%+23.3Cr%Ac3 =854-180C%-14Mn%+44Si%-17.8Ni%-1.7Cr%四、实验方案及过程控制参数1、试验材料的确定2、由技术中心与精棒分厂根据生产计划确定实验钢种及规格,进行热机轧制试验,待参数调整达到设定值后,在4支坯所产材中间倍尺上取样4 X400MM;,此规格热机轧制结束,水箱下线,产材取试料后的钢材与未进行热机轧制钢材一起正常上交,不进行单独标识及管理,同时取随后生产的同炉号未进行热机轧制钢材试料4 X400MM交由技术中心检验;2、加热温度控制实验钢种在实验过程中加热温度按相应加热工艺的下限控制,以获得细小而均匀的奥氏体晶粒,不允许高温长时间加热;3、控轧温度及控冷温度的确定4、不同规格各道次变形率5、水箱参数的设定使用CCT-OFFLINE ,试轧前依据控轧控冷温度确定水箱参数。
根据轧制过程中实际测定温度参数对水箱参数进行调整,直至达到试验方案要求温度。
6、注意事项由于二段穿水,冷却强度大,钢材出2#水箱后表面温度低,易造成热检无信号,需对热检进行签定,必要时更换可进行低温检测热检。
五、检验项目(试验钢与对比钢)1、GCr15检验组织中珠光体片层间距,晶粒度及网状情况;2、40Cr/35-42CrMo检验组织、晶粒度、机械性能及硬度;3、45/20CrMnTi/20-30CrMo检验组织、晶粒度及机械性能。
TMCP工艺的发展
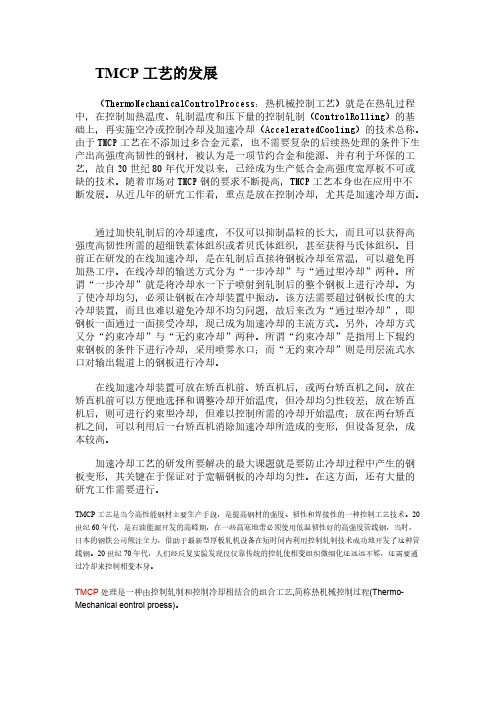
TMCP工艺的发展(ThermoMechanicalControlProcess:热机械控制工艺)就是在热轧过程中,在控制加热温度、轧制温度和压下量的控制轧制(ControlRolling)的基础上,再实施空冷或控制冷却及加速冷却(AcceleratedCooling)的技术总称。
由于TMCP工艺在不添加过多合金元素,也不需要复杂的后续热处理的条件下生产出高强度高韧性的钢材,被认为是一项节约合金和能源、并有利于环保的工艺,故自20世纪80年代开发以来,已经成为生产低合金高强度宽厚板不可或缺的技术。
随着市场对TMCP钢的要求不断提高,TMCP工艺本身也在应用中不断发展。
从近几年的研究工作看,重点是放在控制冷却,尤其是加速冷却方面。
通过加快轧制后的冷却速度,不仅可以抑制晶粒的长大,而且可以获得高强度高韧性所需的超细铁素体组织或者贝氏体组织,甚至获得马氏体组织。
目前正在研发的在线加速冷却,是在轧制后直接将钢板冷却至常温,可以避免再加热工序。
在线冷却的输送方式分为“一步冷却”与“通过型冷却”两种。
所谓“一步冷却”就是将冷却水一下子喷射到轧制后的整个钢板上进行冷却。
为了使冷却均匀,必须让钢板在冷却装置中振动。
该方法需要超过钢板长度的大冷却装置,而且也难以避免冷却不均匀问题,故后来改为“通过型冷却”,即钢板一面通过一面接受冷却,现已成为加速冷却的主流方式。
另外,冷却方式又分“约束冷却”与“无约束冷却”两种。
所谓“约束冷却”是指用上下辊约束钢板的条件下进行冷却,采用喷雾水口;而“无约束冷却”则是用层流式水口对输出辊道上的钢板进行冷却。
在线加速冷却装置可放在矫直机前、矫直机后,或两台矫直机之间。
放在矫直机前可以方便地选择和调整冷却开始温度,但冷却均匀性较差;放在矫直机后,则可进行约束型冷却,但难以控制所需的冷却开始温度;放在两台矫直机之间,可以利用后一台矫直机消除加速冷却所造成的变形,但设备复杂,成本较高。
加速冷却工艺的研发所要解决的最大课题就是要防止冷却过程中产生的钢板变形,其关键在于保证对于宽幅钢板的冷却均匀性。
- 1、下载文档前请自行甄别文档内容的完整性,平台不提供额外的编辑、内容补充、找答案等附加服务。
- 2、"仅部分预览"的文档,不可在线预览部分如存在完整性等问题,可反馈申请退款(可完整预览的文档不适用该条件!)。
- 3、如文档侵犯您的权益,请联系客服反馈,我们会尽快为您处理(人工客服工作时间:9:00-18:30)。
中国冶金报/2012年/3月/29日/第B02版
装备・技术
新一代TMCP技术助力轧钢生产降本增效
夏杰生
我国越来越多的钢铁企业在实际生产中应用或尝试新的轧制工艺技术。
如新一代TMCP(热轧钢材控制轧制与控制冷却)技术在助力企业降低生产成本、优化钢材综合性能、提高成材率、节能降耗等方面发挥着良好作用。
为了扩大轧制行业对新一代TMCP技术的认识和应用,推动轧制行业的进步和发展,由东北大学轧制技术及连轧自动化国家重点实验室、河北省冶金行业协会、钢铁链商网及其《轧制设备》传媒事业部联合主办,北京国联视讯信息技术股份有限公司承办的轧制技术的新进展暨王国栋院士专题讲座于3月5日至7日在京举办,来自全国轧钢界的150多位代表聆听了讲座。
产减量化钢材推动升级换代
中国工程院院士王国栋是轧制技术领域国际知名专家,现任东北大学轧制技术及连轧自动化国家重点实验室(RAL)学委会副主任。
他在这次专题讲座中对新一代TMCP技术的发展作了详尽的诠释。
新一代TMCP技术是以自主研发的冷却速率可调(空冷至超快速冷却无级调整)、冷却温度可精确控制的先进冷却技术和装备为手段,根据不同钢材成分、性能要求和相变规律设计相应的冷却路径和冷却过程控制参数,对钢材热轧和冷却过程中的微观组织进行有效调控,实现细晶强化、纳米析出强化、相变组织强化等各种强化机制的综合强化,充分挖掘钢材潜力的一种轧钢新技术。
与传统的TMCP技术相比,新一代TMCP技术可节省钢材合金用量30%以上,或提高钢材强度100MPa~200MPa以上,可大幅度提高冲击韧性,节约钢材使用量5%~10%,节能10%~15%。
目前该技术已经完成实验室和中试研究,开发的工艺技术、冷却装备目前在热连轧、中厚板、H 型钢、棒材等生产过程中转化应用,开发出系列的减量化钢材产品,在助力我国钢铁产品的升级换代、钢铁行业转变发展方式等方面发挥了重要作用。
提升轧机能力优化性能指标
TMCP是保证钢材强韧性的核心技术。
传统的TMCP工艺一般需要提高钢中微合金元素含量或进一步增强轧机能力。
然而,前者会造成钢材成本的提升和资源的消耗,后者则因现代化轧机能力已接近极限而无法轻易实现。
为弥补传统TMCP的不足,在欧洲和日本相继开发出了热轧板带轧后超快速冷却技术。
与传统TMCP中的层流冷却相比,超快速冷却可有效打破汽膜,实现对热轧钢板进行高效率、高均匀性的冷却(对于3mm厚钢板冷却速度可达400K/s以上;50mm厚中厚板的平均冷却速度超过50K/s),并可避免因冷却不均匀而产生的残余应力。
轧后超快冷技术可使热轧钢铁的性能指标产生质的飞跃,而材料成本和生产过程中的各类消耗则大幅度降低。
目前,这种轧后超快冷技术已经成为热轧板带材生产线改造的重要方向,已用于生产中厚板、热轧带钢、棒线材、H型钢、钢管等90%以上的热轧钢材。
目前,我国已成功开发出轧后超快冷实验设备和现场超快冷设备,并开发适用于不同热轧钢材品种的轧后冷却装置(含UFC和ACC),实施新型的控制轧制和控制冷却过程,有助于提高产品的质量、降低产品的成本。
这些控制冷却系统构成一个家族,统称之为ADCOS(Advanced Cooling System)。
减少能源消耗实现低碳生产
王国栋认为,我国吨钢带来的CO2排放量为2吨~2.5吨。
计算中取平均值,为2.25吨。
假设我国每年生产5亿吨钢,则每年我国钢铁生产带来的CO2排放量为11.2亿吨。
假设我国每年生产的钢中,热轧商品钢材占80%,则这部分钢材量为3.6亿吨。
如热轧钢材中通过采用新一代TMCP技术提高性能的产能占90%,则生产带来的CO2排放量有望减为7.9亿吨。
采用以UFC(一种轧后冷却装置)为核心的新一代TMCP技术以后,由于提高了钢材强度、改善了钢材性能,可以节省钢材5%~10%,取中间值为7.5%,因此可以减少钢材产量0.26亿吨。
按照目前钢材价格计算,若每吨热轧钢材的价格为4000元,则可节省资金超过1000亿元,相应地可节省矿石0.52亿吨,节省焦炭0.14亿吨,并可节省大量的铁合金。
此外,节省钢材可以减少碳排放量为0.47亿吨,减少排放量占我国钢铁行业总排放量的比例为7.6%。
进入21世纪,开发绿色钢铁工艺技术已经成为钢铁工业发展的主流。
新一代TMCP技术作为绿色钢铁工艺技术的代表,已获得国家和政府部门的高度重视,得到了大力支持。
该技术已被列入2011年7月发布的《产业关键共性技术发展指南(2011年)》中。
同时,在去年国家发展改革委施行的《产业结构调整指导目录(2011年本)》中,“在线热处理、在线性能控制、在线强制冷却的新一代热机械控制加工(TMCP)工艺技术应用”也被列为钢铁行业鼓励类技术之一。
据了解,新一代TMCP技术已在一些大中型钢铁企业中落户。
例如鞍钢新一代TMCP技术创新及产业化示范工程已被列入国家发改委钢铁、有色、石化行业低碳技术创新及产业化示范工程。
该工程依托鞍钢4300mm中厚板生产线和2150mm热连轧生产线,进行新一代TMCP技术的研发工作。