Kongsberg M3
Control4 CORE 1 家庭自动化控制器说明书

Control4 CORE 1 Controller Installation GuideSupported model• C4-CORE1 Control4 CORE 1 Hub & ControllerIntroductionDesigned for an exceptional family room entertainment experience, the Control4® CORE 1 Controller does more than automate the gear around your TV; it is the ideal smart home starter system with entertainment built in.The CORE 1 delivers a beautiful, intuitive, and responsive on-screen user interface with the ability to create and enhance the entertainment experience for any TV in the house. The CORE 1 can orchestrate a wide range of entertainment devices including Blu-ray players, satellite or cable boxes, game consoles, TVs, and virtually any product with infrared (IR) or serial (RS-232) control. It also features IP control for Apple TV, Roku, televisions, AVRs, or other network-connected devices, as well as secure wireless Zigbee control for lights, thermostats, smart locks, and more.For entertainment, the CORE 1 also includes a built-in music server that allows you to listen to your own music library, stream from a variety of leading music services, or from your AirPlay-enabled devices using Control4 ShairBridge technology.Box contentsThe following items are included in the CORE 1 controller box:• CORE 1 controller• AC power cord• IR emitters (2)• Rubber feet (2, pre-installed)• External antenna (1 for Zigbee)Accessories available for purchase• CORE 1 Wall-Mount Bracket (C4-CORE1-WM)• Control4 1U Rack-Mount Kit, Single/Dual Controller (C4-CORE1-RMK)• Control4 3-Meter Wireless Antenna Kit (C4-AK-3M)• Control4 Dual-Band Wi-Fi USB Adapter (C4-USBWIFI OR C4-USBWIFI-1)• Control4 3.5 mm to DB9 Serial Cable (C4-CBL3.5-DB9B) Requirements and specificationsWe recommend using Ethernet instead of Wi-Fi for the best networkThe Ethernet or Wi-Fi network should be installed before starting theThe CORE 1 requires OS 3.3 or newer.Composer Pro UserGuide (ctrl4.co/cpro-ug) for details.WarningsCaution! To reduce the risk of electrical shock, do not expose this apparatus torain or moisture.AVERTISSEMENT ! Pour réduire le risque de choc électrique, n’exposez pas cetappareil à la pluie ou à l’humidité.Caution! I n an over-current condition on USB, the software disables theoutput. If the attached USB device does not appear to power on, remove theUSB device from the controller.AVERTISSEMENT ! Dans une condition de surintensité sur USB ou sortie decontact le logiciel désactive sortie. Si le périphérique USB ou le capteurde contact connecté ne semble pas s’allumer, retirez le périphérique ducontrôleur.SpecificationsInputs / OutputsVideo out 1 video out—1 HDMIVideo HDMI 2.0a; 3840x2160 @ 60Hz; HDCP 2.2 and HDCP 1.4Audio out 2 audio out—1 HDMI and 1 digital coaxAudio playback formats AAC, AIFF, ALAC, FLAC, M4A, MP2, MP3, MP4/M4A, OggVorbis, PCM, WAV, WMAHigh-resolution audio playback Up to 192 kHz / 24 bitNetworkEthernet 2 10/100/1000BaseT compatible ports—1 PoE+ in and1 switch network portWi-Fi Optional Dual-Band Wi-Fi USB Adapter(2.4 GHz, 5 Ghz, 802.11ac/b/g/n/a)Zigbee Pro802.15.4Zigbee antenna External reverse SMA connectorUSB port 1 USB 3.0 port—500mAControlIR out 4 IR out—5V 27mA max outputIR capture 1 IR receiver—front, 20-60 KHzSerial out 2 serial out (shared with IR out 1 and 2)PowerPower requirements100-240 VAC, 60/50Hz or PoE+Power consumption Max: 18W, 61 BTUs/hourIdle: 9W, 30 BTUs/hourOtherOperating temperature32˚F ~ 104˚F (0˚C ~ 40˚C)Storage temperature4˚F ~ 158˚F (-20˚C ~ 70˚C)Dimensions (H × W × D) 1.16 × 7.67 × 5.2" (29.5 × 195 × 132 mm)Weight 1.5 lb (0.68 kg)Shipping weight 2.3 lb (1.04 kg)Additional resourcesThe following resources are available for more support.• Control4 CORE series help and information: ctrl4.co/core• Snap One Tech Community and Knowledgebase: •Control4 Technical Support:ctrl4.co/techsupport• Control4 website: 71231 Connect one of the included IR emitters to an IR OUT port on the controller.2 Place the stick-on emitter end onto the IR receiver on the Blu-ray player, TV, or othertarget device to emit IR signals from the controller to the target device.Setting up external storage devices (optional)You can store and access media from an external storage device, for example, a networkhard drive or USB memory device, by connecting the USB drive to the USB port andconfiguring or scanning the media in Composer Pro.We support only externally powered USB drives or solid state USB sticks.Composer Pro driver informationUse Auto Discovery and SDDP to add the driver to the Composer project. See theComposer Pro User Guide (ctrl4.co/cpro-ug) for details.OvrC setup and configurationOvrC gives you remote device management, real-time notifications, and intuitivecustomer management, right from your computer or mobile device. Setup isplug-and-play, with no port forwarding or DDNS address required.To add this device to your OvrC account:1 Connect CORE 1 controller to the Internet.2 Navigate to OvrC () and log in to your account.3 Add the device (MAC address and Service Tag numbers needed for authentication).Front viewA Activity LED—The Activity LED shows when the controller is streaming audio.B IR window—IR receiver for learning IR codes.C Caution LED—This LED shows solid red, then blinks blue during the boot process.The Caution LED blinks orange during the factory restore process. SeeD —The LED indicates that the controller has been identified in a Control4project and is communicating with Director.E Power LED—The blue LED indicates that AC power is present. The controller turns onimmediately after power is applied to it.Back viewPower port—AC power connector for an IEC 60320-C5 power cord.B IR OUT/SERIAL—3.5 mm jacks for up to four IR emitters or for a combination of IRemitters and serial devices. Ports 1 and 2 can be configured independently for serialcontrol (for controlling receivers or disc changers) or for IR control. See “Connectingthe IR ports/serial ports” in this document for more information.C USB—One port for an external USB drive (such as a USB stick formatted FAT32). See“Setting up external storage devices” in this document.D DIGITAL AUDIO—Outputs audio (AUDIO OUT) shared from other Control4 devices orfrom digital audio sources (local media or digital streaming services).E HDMI OUT—An HDMI port to display navigation menus. Also an audio out over HDMI.F ID button and RESET—ID button is pressed to identify the device in Composer Pro. TheID button on the CORE 1 is also an LED that displays feedback useful during a factoryrestore. The RESET pinhole is used to reset or factory restore the controller.G ENET OUT—RJ-45 jack for Ethernet out connection. Acts as a 2-port network switchwith ENET/POE+ IN jack.H ENET/POE+ IN—RJ-45 jack for a 10/100/1000BaseT Ethernet connection. Also canpower the controller with PoE+.I ZIGBEE—Antenna connector for the Zigbee radio.Installation instructionsTo install the controller:1 Ensure that the home network is in place before starting system setup. An Ethernetconnection to the local network is required for setup. The controller requires anetwork connection to use all of the features as designed. After initial configuration,Ethernet (recommended) or Wi-Fi (with an optional adapter) can be used toconnect the controller to web-based media databases, communicate with other IPdevices in the home, and access Control4 system updates.2 Mount the controller near the local devices you need to control. The controller canbe hidden behind a TV, mounted on a wall, installed in a rack, or placed on a shelf.The CORE 1 Rack Mount Kit is sold separately and is designed for easy installation ofup to two CORE 1 controllers side by side in a rack. The CORE 1 Wall-Mount Bracketis sold separately and designed for easy installation of the CORE 1 controller behinda TV or on the wall.3 Attach antenna to the ZIGBEE antenna connector.4 Connect the controller to the network.• Ethernet—To connect using an Ethernet connection, connect the network cableinto the controller’s RJ-45 port (labeled ENET/POE+ IN) and into the network porton the wall or at the network switch.• Wi-Fi—To connect using Wi-Fi, first connect the unit to Ethernet, connect theWi-Fi adapter to the USB port, and then use Composer Pro System Manager toreconfigure the unit for Wi-Fi.5 Connect system devices. Attach IR and serial devices as described in “Connectingthe IR ports/serial ports” and “Setting up IR emitters.”6 Set up any external storage devices as described in “Setting up external storagedevices” in this document. | 888.400.4070Copyright 2022, Snap One, LLC. All rights reserved. Snap One and its respective logos are registered trademarks or trademarks of Snap One, LLC (formerly known as Wirepath Home Systems, LLC), in the United States and/or other countries. 4Store, 4Sight, Control4, Control4 My Home, SnapAV, Mockupancy, NEEO, OvrC, Wirepath, and Wirepath ONE are also registered trademarks or trademarks of Snap One, LLC. Other names and brands may be claimed as the property of their respective owners. Snap One makes no claim that the information contained herein covers all installation scenarios and contingencies, or product use risks. Informationwithin this specification subject to change without notice.More helpFor the latest version of this document and to view additional materials, open the URL below or scan the QR code on a device that can view PDFs.Legal, Warranty, and Regulatory/Safety informationVisit /legal for details.MOST RECENT VERSIONctrl4.co/core1-ig200-00724-A 2022-05-31 DHATroubleshootingReset to factory settingsCaution! The factory restore process will remove the Composer project.To restore the controller to the factory default image:1 Insert one end of a paper clip into the small hole on the back of the controller labeled RESET .2 Press and hold the RESET button. The controller resets and the ID button changes to solid red.3 Hold the button until the ID flashes double orange. This should take five to seven seconds. The ID button flashes orange while the factory restore is running. When complete, the ID button turns off and the device power cycles one more time to complete the factory restore process.Note: During the reset process, the ID button provides the same feedback as the Caution LED on the front of the controller.Power cycle the controller1 Press and hold the ID button for five seconds. The controller turns off and back on.Reset the network settingsTo reset the controller network settings to the default:1 Disconnect power to the controller.2 While pressing and holding the ID button on the back of the controller, power on the controller.3 Hold the ID button until ID button turns solid orange and the Link and Power LEDs are solid blue, and then immediately release the button.Note: During the reset process, theID button provides the same feedback asthe Caution LED on the front of the controller.LED status informationActivityCautionLinkPowerMORE INFO ON CORE CONTROLLERSctrl4.co/core。
三分仓容克式空预器说明书

一、空预器概述空气预热器是利用锅炉尾部烟气热量来加热燃烧所需要空气的一种热交换装置,由于它工作在烟气温度较低的区域,回收了烟气热量,降低了排烟温度,因而提高了锅炉效率。
同时由于燃烧空气温度的提高,有利于燃料着火和燃烧,减少了不完全燃烧损失1.1.1空气预热器的类型及特点空气预热器按传热方式分可以分为传热式和蓄热式(再生式)两种。
前者是将热量连续通过传热面由烟气传给空气,烟气和空气有各自的通道。
后者是烟气和空气交替地通过受热面,热量由烟气传给受热面金属,被金属积蓄起来,然后空气通过受热面,将热量传给空气,依靠这样连续不断地循环加热。
随着电厂锅炉蒸汽参数和机组容量的加大,管式空气预热器由于受热面的加大而使体积和高度增加,给锅炉布置带来影响。
因此现在大机组都采用结构紧凑、重量轻的回转式空气预热器。
管式空预器和回转式空预器两者相比较各有以下特点:1)回转式空气预热器由于其受热面密度高,因而结构紧凑,占地小,体积为同容量管式预热器的1/10;2)重量轻。
因管式预热器的管子壁厚1.5mm,而回转预热器的蓄热板厚度为0.5-1.25mm,布置相当紧凑,所以回转式预热器金属耗量约为同容量管式预热器的1/3;3)回转式预热器布置灵活方便,在锅炉本体更容易得到合理的布置;4)在相同的外界条件下,回转式空气预热器因受热面金属温度较高,低温腐蚀的危险较管式预热器轻些;5)回转式空气预热器的漏风量比较大,一般管式预热器不超过5%,而回转式预热器在状态好时为8%-10%,密封不良时可达20%-30%;6)回转空气预热器的结构比较复杂,制造工艺要求高,运行维护工作多,检修也较复杂。
回转式空气预热器有两种布置形式:垂直轴和水平轴布置。
垂直轴布置的空气预热器又可分为受热面转动和风罩转动。
通常使用的受热面转动的是容克式回转空气预热器,而风罩转动的是罗特缪勒(Rothemuhle)式回转预热器。
这两种预热器均被采用,但较多的是受热面转动的回转式空气预热器。
设置功能指南说明书

Flow MonitorOperation ManualPF3W3Safety InstructionsThese safety instructions are intended to prevent hazardous situations and/orequipment damage.These instructions indicate the level of potential hazard with the labels of"Caution", "Warning" or "Danger". They are all important notes for safety and mustbe followed in addition to International standards (ISO/IEC) and other safetyregulations.OperatorNOTEThe direct current power supply to be used should be UL approved as follows.Circuit (of class 2) which is of maximum 30 Vrms (42.4 V peak), with UL 1310class 2 power supply unit or UL 1585 class 2 transformer.The product is a approved product only if it has a mark on the body.UP buttonM3 x 8 L*: The panel mount adapter can be rotated through 90 degrees for mounting.*: The panel mount adapter should be fixed firmly with screws. Otherwise, fluids such as water mayenter. After contact with the panel, tighten screws by 1/4 to 1/2 turn.BackBe sure to select the correct sensor to be connected.Setting the ON and OFF points of the switch output.Switch operationWhen the flow exceeds the set value, theswitch will be turned ON.When the flow falls below the set value bywill be turned OFF.If the operation shown the right isacceptable, please keep this setting.Connecting and disconnecting of the sensor connector and powersupply/output connector•When connecting, insert the connectors straight into the body until it clicks.•To remove the connectors, push the lever downward with your thumb, and pullthe connectors out straight.WiringConnector connectionConnections should only be made with the power supply turned off.Use separate routes for the Flow monitor wiring and any power or high voltagewiring. Otherwise, malfunction may result due to noise.Ensure that the FG terminal is connected to ground when using a commerciallyavailable switch-mode power supply. When a switch-mode power supply isconnected to the product, switching noise will be superimposed and the productspecification can no longer be met. This can be prevented by inserting a noisefilter, such as a line noise filter and ferrite core, between the switch-mode powersupply and the product, or by using a series power supply instead of a switch-mode power supply.Sensor connectorPower supply/output connectorConnection of the sensor cable and connectorRefer to the product catalogue or SMC website(URL ) for more detailedinformation about type of sensor connector, applicablegauge of cable and connection method.1234DC(+): BrownN.C. / IN: White (unused / temp. sensor: 1 to 5 V)DC(-): BlueINPUT: Black (flow sensor: 1 to 5 V)COPY: GreyOUT2: WhiteOUT1: BlackDC(-): BlueDC(+): Brown[F 0] Selection of sensorBe sure to select the correct sensor to be connected before use.button.FrontMounting and InstallationInstallationMounting by panel mount adapterFix the panel mount adapter to the controller by the mounting screws M3 x 8 L(2 pcs.).Panel mount adapter (Part number: ZS-26-B)Front protective cover (Part number: ZS-26-01)Flow (Temperature) SettingMeasurement modeThe mode in which theflow is detected anddisplayed, and the switchfunction is operating.This is the basic operatingmode; other modes shouldbe selected for set-pointand other function settingchanges.Supply powerApprox. 3 seconds(the output remains offfor this period)orbutton is to increase and the4. Press the button to finish the setting.•Press theThe switch turns on within a set flow range (from P1L to P1H) during windowcomparator mode. Set P1L (switch lower limit) and P1H (switch upper limit) usingthe setting procedure above.When reversed output is selected, the main screen displays [n1L] and [n1H].To set accumulated output functions, refer to the product catalogue or SMCwebsite (URL ) for more detailed information.For models with 2 outputs, [P_2] or [n_2] will be displayed. Set as above.If the output to the fluid temperature is selected, [ tn] or [ tP] will be displayed.When the fluid temperature falls below the set value, the output turns ON.*: If a button operation is not performed for 30 seconds during the change of setting, the set value willstart flashing.button to confirm. Return to the function selection mode.[F 0] Sensor selection is completed.Refer to the product catalogue or SMC website(URL ) for more detailed information about panelcut-out dimensions and the thicknes of the panel.Notice when removing the productremoved from the panel after removing thetwo screws, and by disconnecting the hookson both sides.of thin card (as shown in the figure).Pull the panel mount adapter to the front, andremove the flow monitor.If the panel mount adapter is pulled forwardwith the hook caught, the product and theadapter may be damaged.<Operation>1. Press the2. [P_1] or [n_1] and the set valueare displayed alternately.Thank you for purchasing an SMC PF3W3 Series Flow Monitor.Please read this manual carefully before operating the product and make sure youunderstand its capabilities and limitations.Please keep this manual handy for future reference.To obtain more detailed information about operating this product,please refer to the SMC website (URL ) orcontact SMC directly.。
25000吨双壳散货船英文简要规格书
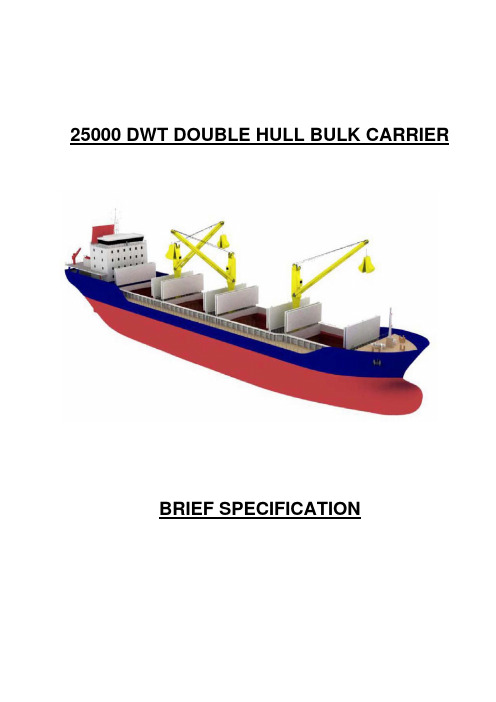
25000 DWT DOUBLE HULL BULK CARRIERBRIEF SPECIFICATION25000 DWT DOUBLE HULL BULK CARRIERGENERAL INFORMATION ABOUT THE VESSEL :The vessel is designed as 25000 DWT Double Hull Bulk Carrier with single screw CPP, four cargo holds and one uninterrupted main deck. The hull form will be of round bilge, bulbous bow, and transom stern to be of all welded steel construction.The engine room and accommodations are located at the aft part of the vessel. The vessel will have 4 Cargo Holds with folding type hydraulic hatch covers and 3 cargo cranes . 4 double bottom, 4 side, fore and aft peak ballast tanks which are separated by 6 watertight transverse bulkhead, passageway will positioning between aft and fore collision bulkheads on side ballast tanks and pipe tunnel will positioning in double bottom centerline.The vessel’s superstructure will have 5 decks and accommodation is designed for 22 people and a private room for the owner. The squared type construction funnel is located at the aft part of the superstructure.The vessel will be propelled with CPP with a diameter of 4200mm by Berg Propulsion and manoeuvring with streamline type semi spade rudder which is fabricated with rolled steel plate.The vessel shall comply with the following rules and regulations;1-Classification Society – BUREAU VERITAS2- Flag State3-International Rules And Regulations (SOLAS, MARPOL, IBC, ILO)The general layout of the vessel will be attached. (General ArrangementPlan)25000 DWT DOUBLE HULL BULK CARRIER1. VESSEL’S DATA :Type : 25000 DWT Bulk CarrierBuilder : Deniz Industry co. – Cicek Shipyard, Tuzla –Istanbul, TurkeyNavigation : Unrestricted – Worldwide including Panama andSuez ChannelsClass : BV HULL, MACHINERY, BULK CARRIER, CSR,BC-A, ESP, GRABLOADING, UNRESTICTEDNAVIGATION, NONHOMLOAD, HEAVY CARGO,+ AUT-UMS, CLEAN, MON SHAFT, IWS Main Data of Vessel :L OA: 159.2mL BP: 149.4 mB : 25.00 m -MOULDED-T : 9.7 m -DESIGN-DWT : 25000 DWTV : abt. 13 knots (@85% MCR)RANGE : abt 12000 nautical miles with 90% fuel Capacity Fuel Capacities :HFO : abt 875 m 3MDO : abt 205 m 325000 DWT DOUBLE HULL BULK CARRIERTypes Of Cargo and Hold Capacities :GRAIN BALEHold 1 : abt 6575 m3abt 6250 m3Hold 2 : abt 7785 m3abt 7500 m3Hold 3 : abt 7810 m3abt 7500 m3Hold 4 : abt 8325 m3abt 8200 m3TOTAL : abt 30495 m3abt 29450 m3Types Of Cargo :Dry bulk and break bulk cargoes such as grain, metal concentrates, iron ore, scrap metal, salt, sugar.General cargoes such as steel products including coil, forest products, packaged freight and palletized cargo.bagged cargoes.cement,BaggedLog, lumber, plywood.:LoadingStrenghtLocal strenght of cargo hold tank top and upper deck to be sufficient for following unit cargo load in metric tons.Loading on double bottom in holds : 20 t/m2Loading on main deck : 4 t/m225000 DWT DOUBLE HULL BULK CARRIERMachinery and Propeller Data :Maın Engine :Two stroke, low speedMAN B&W 8S35MC5920 kW OUTPUT5032 kW at 85% CMCR173 RPMFuel Consumption is 21.5 t/24hSpecific Fuel Consumption is less than 178 g/kWh at 85% CMCR The specific fuel consumption is related to test on Maker's station at ambient conditions as per ISO 3046/1-1986, low calorific value equal to 42707 kJ/kg and at 85% CMCR of ME.CPP Propeller :One propeller hub, type BCP with built in hydraulic cylinder in Cu-Ni-Al bronzeFour propeller blades in Cu-Ni-Al bronze with moderate skrew design machined polished and balanced.4200 mm diameter.Emergency / Harbour Dıesel Generator :Water cooled, four stroke diesel engine, turbo charged, inter cooled, cunter clockwise rotation MAN D 2866 LXE type generatorIso-rating acc. To IXCN : 313 kW at 1800 rpmNumber of cylinders : 6Cargo Cranes :3 (Three) sets SWL 35 t capacity, 4.0 – 24.0 m outreach Cargo Cranes withspare parts.25000 DWT DOUBLE HULL BULK CARRIERHatch Covers :4 (Four) Sets MCG high stowing Folding type operated by means of externalHydraulic cylinders. Weather Deck Hatch Covers with hydraulic system spare parts.The hatch covers are manually cleated and weatherthigt.The hatch covers are constructed with flat top plates and are of double skin.Opening/closing time for each pair is approximately 2,5/2,0 minutes excluding time.[ NOTE : ALL THIS INFORMATION IS GIVEN AS GUIDANCE BUT MAYBE CHANGED ACCORDING TO THE BUILDERS CHOICE ]25000 DWT DOUBLE HULL BULK CARRIER25000 DWT BULK CARRIER PREFERABLE MAKER’S LISTCOMPONENT MAKERMain Engine MAN B&W 8S35MC - 5920 KW 173 rpm Marine Genset 3PCS SH 17/28 HYUNDAI HIMSEN 540 KWMHC534F-1Alternator STAMFORDPropulsion Unit BERG PROPULSIONSteering Gear HATLAPAMain Engine Crane ON-ELCranes NMF G.m.b.HHatch Covers MacGREGORHigh Level Alarms ARISTONHEMPEL,AMERONPainting JOTUN,Emergency Generator LINDENBERGS-MAN,KANGRIMBoilersSeparators ALFA LAVALLife Boats NORWEGIAN EQUIPMENTMooring Winches YOO WON M-TECHAids FURUNONavigationCommunication Aids FURUNOEngine Pumps BOMBAS-ITURAir Compressors SPERREFresh Water Generator ALFA LAVALValves Remote Control EUROVALVE, KONGSBERGFire Detection System MARINLECAlarms and Monitoring PRAXIS, LINKSOCO2 Plant ALMAR25000 DWT DOUBLE HULL BULK CARRIERCOMPONENT MAKERFoam Plant ALMARPlate Type Heat Exchangers ALFA LAVALEquipment PERFECT-RINSEPUM-INOKSANGalleyLaundry Equipment ARCELIK, BEKO, BOSCHAir Conditioning HEINEN HOPMANOil Water Separator JOWA, GRS, CONFINWORDSewage Treatment System JOWA, GRSSea Chest Anti-Fouling System AQUAMARCATHELCOICCPSystem K.C.LTD,VIKKINGSCHLAUCHBOOT,LifeRafts DEUTSCHESONICSTyphoon KOCKUMSLights SEEMATZSearchFresh Water Distribution System JOWA, TEMAIncinerator TEAMTEC, GRS, JOWAKANGRIMEconomizers S-MAN,Module ALFA-LAVALBoosterWindlass Gear YOO WON M-TECHWipers WYNNWindows25000 DWT DOUBLE HULL BULK CARRIER。
世界经典船型

2011年世界经典船型(2012-06-08) 编辑发布:中国船舶在线阅读次数:9次日前《Marine Log》杂志又评选出一年一度的世界经典船型。
“节能”、“清洁船舶”、“环境友好”等越来越受重视,各国船舶设计所和运营集团不约而同地将环保作为民船的主要发展方向之一。
可以说环保已成为当前船舶设计的主流趋势。
而海工船方面则更强调功能上的创新和先进。
NO. 1––首艘LNG燃料成品油船“Bit Viking”号“Bit Viking”号成品油船在2011年度可以说十分抢眼,它是世界首艘由重燃油改装成LNG燃料的成品油船,也是除LNG船之外以LNG为动力的最大商船,船东为挪威Tarbit航运公司,运营商为挪威国家石油公司,主要在挪威海岸运营。
据瓦锡兰公司介绍说,该船为全球首艘将瓦锡兰46型发动机改装为瓦锡兰50DF型发动机运行的船,“Bit Viking”号因此成为世界上最环保的成品油轮之一。
瓦锡兰对“Bit Viking”号的整体改装包括气体燃料系统、管道系统、推进系统及相关控制系统,和其他相应的系统改装工作。
该船还采用了瓦锡兰新型LNG储存系统,甲板前部安装了2个500m3的LNG储罐,可使船舶在80%装载工况下自运行12天,并可切换至船用气体燃料。
“Bit Viking”号自2011年11月24日投入运营至今已取得了良好的表现,温室气体排放量减少了20%~25%,硫排放量为零,NOX减少了90%,颗粒物的排放减少了99%。
另外,改装后该船被挪威NOX排放基金项目所收取的NOX排放税显著减少。
NO. 2––肥大型、最少化压载水“Maersk Lima”号“Maersk Lima”号是马士基航运公司向韩国大宇造船海洋订购的一艘集装箱船。
该船拥有8个双层舱壁的货舱,以及18个40英尺的集装箱货位,16个货舱口。
“Maersk Lima”号拥有一个全焊接上甲板,带首舷弧、方尾,上层建筑设计在船尾,航行视野十分开阔。
豪顿华空预器基础知识简介
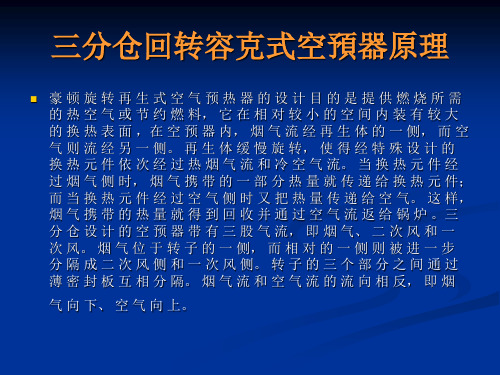
吹灰及消防系统
空預器采用蒸汽吹灰,每台空預器安装两台半伸缩式 吹灰器,一台位于烟气入口,另一台位于烟气出口 ,另外 还配备一套消防喷水设备,消防水的工作压力范围为 0.38~0.52MPa 。
吹灰蒸汽满足的条件:
入口法兰处压力:1.5 MPa; 吹灰喷嘴处压力:0.93 MPa 1.07 MPa; 吹灰喷嘴处温度:300 350 ℃
减速箱
FLENDER公司MOTOX齿轮减速箱ZF108-K4-160,速比14.63:1; FLENDER公司CAVEX蜗杆减速箱CDA 250,速比为9.25/1; FLENDER公司CAVEX蜗杆减速箱CDA 500,速比为13.33/1
联轴器
FLENDER公司BIPEX挠性联轴器BWN162。 驱动装置轴套锁紧盘: SD280-91,传递扭矩319000Nm
终级减速箱一侧装有扭矩臂,扭矩臂被固定在顶部结构上 的抗扭支座内,抗扭支座通过扭矩臂给驱动机构一个反作用扭 转力矩从而驱动转子顶部的驱动轴和转子一起旋转。驱动装置 扭矩臂沿垂直方向可以在抗扭支座内上下自由移动,以适应转 子与顶部结构的热态胀差。
驱动装置的驱动电机配有变频器,用以降低空预器启动时 的启动力矩,减轻启动时对减速箱的冲击作用,以实现“软启 动”。此外,通过变频控制,可以改变空预器的转速,用以满 足停炉时空预器在低速下对换热元件进行水冲洗的需要,两台 电机均能以正、反两个方向驱动空预器,只有在空预器不带负
换热元件
换热元件选型原则:
1. 传热效率高 2. 流通阻力低 3. 不易堵灰 4. 吹灰介质易穿透且能量损失小 5. 易清洗 6. 加工工艺性好 7. 使用寿命长
豪顿华预热器换热元件类型:
FNC 波型 (Flat Notched Crossed)
常用船舶设计软件对比

常用船舶设计软件对比目前,国际上常用的船舶设计软件有如下几种:TribonTribon 系统是由瑞典KCS(Kockums Computer System AB)公司设计开发的一套用于辅助船舶设计与建造计算机软件集成系统。
Tribon集CAD/CAM(计算机辅助设计与制造)与MIS(信息集成)于一体,并覆盖了船体、管子、电缆、舱室、涂装等各个专业的一个专家系统。
总体上Tribon系统可分为船体设计、舾装设计、系统管理及维护三大部分。
该软件是一个出色的集成系统,也是一个庞大的系统,它具有许多其他系统所不具备的优点。
Tribon推出的新版本较过去添加了很多新的功能,如在设备选择、合同设计等方面的功能。
我国使用该设计软件系统的公司有:广船国际股份有限公司、江南造船(集团)有限公司等。
对我国的用户来说,该软件存在的缺点有:数据开放性不够,数据库系统自成一套与常用的数据库缺少接口等。
TRIBON的第一个软件包是TRIBON Solution。
在2004 TRIBON Solution被AVEVA集团收购,M3是tribon的最新版本。
它包括初始设计模块,基本设计,船体建模,船舶配件模块,装配计划和工件准备模块。
运行于windows 系统,在造船工业排他性发展。
(注:言下之意是说tribon和其他程序的接口、兼容等方面过于保守)vantage marine是AVEVA基于已有着名的PDMS(工厂设计管理系统)发展的新产品。
vantage marine的意义在于它是PDMS配件模块和tribonM3船体和基本应用程序的联合产物。
NAPANAPA 公司首次在船舶设计软件中采用3D技术,并在船舶初步设计和基本设计阶段提出了3D NAPA船舶模型的概念,这一概念己得到广泛认同。
利用NAPA Steel设计师们可以在较短时间内迅速完成结构初步设计和重量、成本计算,生成可供送审的技术文件和图样,并根据需要生成结构有限元计算所需的网格模型。
Modicon M340自动化平台BMXP341000处理器模块说明书

DEL-BMXP341000i s c l a im e r : T h i s d o c u m e n t a t i o n i s n o t i n t e n d e d a s a s u b s t i t u t e f o r a n d i s n o t t o b e u s e d f o r d e t e r m i n i n g s u i t a b i l i t y o r r e l i a b i l i t y o f t h e s e p r o d u c t s f o r s p e c i f i c u s e r a p p l i c a t i o n sProduct datasheetCharacteristicsBMXP341000processor module M340 - max 512 discrete + 128analog I/O - ModbusMainRange of productModicon M340 automation platform Product or component type Processor module Number of racks 2Number of slots11Discrete I/O processor capacity 512 I/O single-rack configuration Analogue I/O processor capacity 128 I/O multi-rack configuration 66 I/O single-rack configuration Number of application specific channel 20MonitoringDiagnostic counters Modbus Event counters ModbusComplementaryControl channelsProgrammable loopsIntegrated connection typeUSB port 12 Mbit/sNon isolated serial link RJ45 character mode asynchronous in baseband RS232C full duplex 0.3...19.2 kbit/s 2 twisted shielded pairsNon isolated serial link RJ45 character mode asynchronous in baseband RS485 half duplex 0.3...19.2 kbit/s 1 twisted shielded pairNon isolated serial link RJ45 Modbus master/slave RTU/ASCII asynchronous in baseband RS232C half duplex 0.3...19.2 kbit/s 1 twisted shielded pairNon isolated serial link RJ45 Modbus master/slave RTU/ASCII asynchronous in baseband RS485half duplex 0.3...19.2 kbit/s 1 twisted shielded pair Communication module processor 2 Ethernet communication module 2 AS-Interface module Number of devices per segment 0...32 character mode 0...32 ModbusNumber of devices 2 point-to-point character mode 2 point-to-point ModbusBus length0...10 m serial link non isolated character mode segment 0...10 m serial link non isolated Modbus segment0...1000 m serial link isolated character mode segment 0...1000 m serial link isolated Modbus segment 0...15 m character mode point-to-point0...15 m Modbus point-to-pointTap links length0...15 m serial link non isolated character mode segment0...15 m serial link non isolated Modbus segment0...40 m serial link isolated character mode segment0...40 m serial link isolated Modbus segmentNumber of addresses0...248 character mode0...248 ModbusRequests 1 K data bytes per request character mode252 data bytes per RTU request Modbus504 data bytes per ASCII request ModbusControl parameter One CRC on each frame (RTU) ModbusOne LRC on each frame (ASCII) character modeOne LRC on each frame (ASCII) ModbusMemory description2048 kB internal RAM128 kB internal RAM for data1792 kB internal RAM for program constants and symbolsSupplied memory card (BMXRMS008MP) for backup of programs, constants, symbols and data Maximum size of object areas128 kB unlocated internal data16250 %Mi located internal bits32464 %MWi internal words located internal data32760 %KWi constant words located internal dataDefault size of object areas128 %KWi constant words located internal data256 %Mi located internal bits512 %MWi internal words located internal dataApplication structure 1 periodic fast task1 cyclic/periodic master taskNo auxiliary task32 event tasksExecution time per instruction0.18 µs Boolean0.26 µs double-length words0.38 µs single-length words1.74 µs floating pointsNumber of instructions per ms 4.2 Kinst/ms 65 % Boolean + 35 % fixed arithmetic5.4 Kinst/ms 100 % BooleanSystem overhead0.2 ms fast task1.05 ms master taskCurrent consumption72 mA 24 V DCSupply Internal power supply via rackMarking CEStatus LED 1 LED green processor running (RUN)1 LED red I/O module fault (I/O)1 LED red memory card fault (CARD ERR)1 LED red processor or system fault (ERR)1 LED yellow activity on Modbus (SER COM)Product weight0.2 kgEnvironmentAmbient air temperature for operation0...60 °CRelative humidity10...95 % without condensationIP degree of protection IP20Protective treatment TCStandards UL 508IEC 61131-2EN 61131-2CSA C22.2 No 213 Class I Division 2CSA C22.2 No 142Offer SustainabilitySustainable offer status Green Premium productRoHS (date code: YYWW)Compliant - since 0722 - Schneider Electric declaration of conformitySchneider Electric declaration of conformityREACh Reference contains SVHC above the threshold - Go to CaP for more detailsGo to CaP for more detailsProduct environmental profile AvailableProduct environmental Product end of life instructionsAvailableEnd of life manualContractual warrantyWarranty period18 monthsProduct datasheetDimensions DrawingsBMXP341000Modules Mounted on RacksDimensions(1)With removable terminal block (cage, screw or spring).(2)With FCN connector.DEL-BMXP341000。
欧洲汽车零部件公司及主营业务

加 麦格纳国际公司 Magna International Inc.
加 Martinrea International Inc. 瑞典 奥拓立夫公司 Autoliv Inc. 瑞典 普拉斯塔 Plastal Group 瑞典 斯凯孚公司汽车零件 SKF Automotive Division 瑞士 ABB 英国 GKN plc 吉凯恩公司 英国 TI汽车集团 英国 皮尔金顿集团公司 Pilkingtom Group Ltd.
国家 公司 德国 博世Bosch 德国 大陆Continental 德国 巴斯夫 德国 采埃福ZF 德国 蒂森克虏伯 Thyssen Krupp 德国 玛勒 Mahle GmbH 德国 本特勒汽车公司 Benteler Automobiltechnik GmbH 德国 海拉公司 Hella KGaA Hueek & Co 德国 贝洱公司 Behr GmbH & Co KG 德国 布鲁兹 Brose Fathrzeugteile 德国 威尔汉姆卡曼 Wilhelm Karmann GmbH 德国 皮尔伯格传动轴有限公司 Kolbenschmidt Pierburg AG 德国 弗瑞登伯格公司 Freudenberg 德国 埃贝施帕赫尔 J.Eberspaecher GmbH & Co. KG 德国 贝尔材料科学公司 Bayer Materical Science 德国 德克斯米尔公司 Draexlmaier Group 德国 莱尼 Leoni AG 德国 韦巴斯特 Webasto AG 德国 利奥波德Kostal有限公司 Leopold Kostal GmbHund Co.KG 德国 派格集团 Peguform GmbH 德国 考泰斯德事隆 Kautex Textron GmbH&Co. KG 德国 ZF Lenksysteme 德国 德国莱茵金属公司 Rheinmetall GmbH 德国 西门子西门子VDO Siemens VDO Automotive Corp.
美国凯撒公司产品说明书:3380GFR钢制饮水源
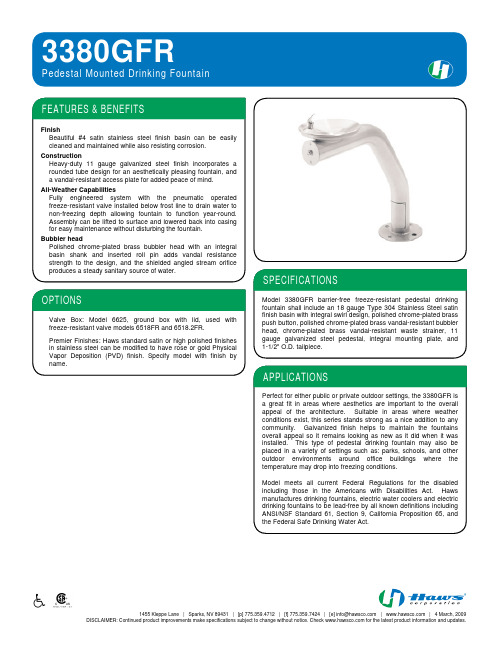
1455KleppeLane|Sparks,NV89431|[p]775.359.4712|[f]775.359.7424|[e]***************||4March,2009 DISCLAIMER: Continued product improvements make specifications subject to change without notice. Check for the latest product information and updates.12/06Model 3380FR/3380GFR/3380.6519FR Page 1 of 6No. 2077370(11) 1455KleppeLaneSparks, NV 89431-6467 (775) 359-4712 Fax (775) 359-7424HAWS AG Bachweg 3 CH-3401 Burgdorf SwitzerlandHaws Mfg. Pte Lt. 2A Sungei Kadet Drive Singapore 729554Avlis-Avenido Senador, Testonio Vilela 505 Jardim Aeroporto Itu, S.P. 13304-550 BrasilE-mail: *************** website: Model 3380FR/3380GFR/3380.6519FRDrinking FountainLIMITED WARRANTYHAWS® warrants that all of its products are guaranteed against defective material or poor workmanship for a period of one year from date of shipment. HAWS liability under this warranty shall be discharged by furnishing without charge F.O.B. HAWS Factory any goods, or part thereof, which shall appear to the Company upon inspection to be of defective material or not of first class workmanship, provided that claim is made in writing to company within a reasonable period after receipt of the product. Where claims for defects are made, the defective part or parts shall be delivered to the Company, prepaid, for inspection. HAWS will not be liable for the cost of repairs, alterations or replacements, or for any expense connected therewith made by the owner or his agents, except upon written authority from HAWS, Sparks, Nevada. HAWS will not be liable for any damages caused by defective materials or poor workmanship, except for replacements, as provided above. Buyer agrees that Haws has made no other warranties either expressed or implied in addition to those above stated, except that of title with respect to any of the products or equipment sold hereunder and that HAWS shall not be liable for general, special, or consequential damages claimed to arise under the contract of sale. The drinking fountain manufactured by HAWS is warranted to function if installation and maintenance instructions provided are adhered to. The units also must be used for the purpose for which they were intended.NO OTHER WARRANTIES EXPRESSED OR IMPLIED ARE AUTHORIZED, PROVIDED OR GIVEN BY HAWS.NOTE TO INSTALLER: Please leave this information with the Maintenance Department.SHOULD YOU EXPERIENCE DIFFICULTY WITH THE INSTALLATION OF THIS MODEL, PLEASE CALL:1-800-766-5612FOR PARTS CALL:1-800-758-9378(U.S.A. AND CANADA ONLY) MONDAY-THURSDAY: 6:00 A.M. – 4:00 P.M. PSTFRIDAY: 6:00 A.M –1:00 P.M. PSTRECOMMENDED TOOLS: Hack saw, pipe joint sealant, screwdriver, level, 12" adjustable wrench, 10" pipe wrench, 5/64“ hex key wrench, 9/16”, 1/2", 7/16” socket wrench or open end wrench.LOCATION OF UNIT: The Model 3380FR/3380GFR Drinking Fountain is a wheelchair accessible drinking water facility. The height dimensions shown, meet current ADA requirements. When installing this unit, local, state or federal codes should be adhered to. If height other than shown is required, then dimensions must be adjusted accordingly.SUPPLY LINE: The minimum recommended line size is 1/2“IPS. Flowing pressure is 30-90 psi (2-6 ATM) for Models 3121FR and 3121.6280FR.Flowing pressure for Model 3121.6519FR is 45-90 psi (3-6 ATM). Where sediment or mineral content is a problem, an inlet filter is recommended.PLUMBING CONNECTIONS: Supply inlet is 1/2" IPS male. Waste outlet is 1-1/2”O.D. tailpiece.MAINTENANCE: Refer to 6518FR or 6519FR Operation and Maintenance Sheet for additional information.INSTALLATION INSTRUCTIONS FOR 6519FR(SEE INSTALLATION DRAWING SHEET 2 OF 2)1. Cut fountain waste line (1-1/2” Tiger Flex) as required and use PVC primer and cementto attach 6519FR waste and air gap assembly. (NOTE: Locate assembly at lowestpossible point inside fountain).2. Attach 2” long piece of 1-1/2” Tiger Flex Hose (supplied) to bottom of 6519FR waste andair gap assembly tee. Next attach adaptor with tailpiece (supplied with fountain), usePVC primer and cement on these connections.TROUBLESHOOTING 3380FR/3380GFR W/6518FRPROBLEM REPAIR CHECKLIST1. Insufficient bubbler flow. a. Check that inlet screwdriver stop valve iswide open (customer supplied).b. Verify minimum 30 psi flowing supplypressure.c. Adjust valve to increase flow. See 6518FRmanual.TROUBLESHOOTING 3380.6519FRPROBLEM REPAIR CHECKLIST1. Insufficient bubbler flow. a. Check that inlet screwdriver stop valve iswide open (customer supplied).b. Verify minimum 45 psi flowing supplypressure.c. Adjust valve to increase flow. See 6519FRmanual.© 2006 Haws® Corporation – All Rights ReservedHAWS® and other trademarks used in these materials are the exclusive property of Haws Corporation.12/06 Model 3380FR/3380GFR/3380.6519FR Page 2 of 6。
Axis AXIS M3106-L Mk II 隐蔽式4MP视频监控与内置红外照明功能摄像机说明书

表数据AXIS M3106-L Mk II Network Camera隐蔽式4MP视频监控与内置红外照明功能AXIS M3106-L Mk II是一款价格实惠的隐蔽式迷你型固定半球摄像机,具备可抑制反光的平面设计。
通过使用WDR技术和红外照明,该款摄像机可提供紧凑型HDTV监控,即使在光照条件不佳或全黑环境下亦可如此。
智能设计可实现轻松重新喷涂外壳或使用可选的黑色附件外壳以使摄像机融入其环境中。
Axis Zipstream技术可降低带宽和存储要求。
提供多种附件以便灵活且易于安装。
>内置红外照明>四倍高清/4MP视频>宽动态范围(WDR)>Axis Zipstream技术>智能设计可实现便捷灵活安装AXIS M3106-L Mk II Network Camera 摄像机图像传感器1/3"逐行扫描RGB CMOS镜头M12支架、固定光圈、固定对焦2.4毫米,F2.2水平视野:130°垂直视野:73°日夜自动可拆卸式红外截止滤光片最低照度颜色:50IRE F2.2条件下为0.3lux黑/白:50IRE F2.2条件下为0.06lux在红外照明开启的情况下为0lux快门时间1/31500s至1/5s摄像机角度调整水平转动:±180°垂直转动:0°至60°(0°=透镜与摄像机底座呈直角)旋转:±95°可以调整朝向各个方向并能看到墙壁或天花板视频视频压缩H.264(MPEG-4Part10/AVC)Main和High ProfileH.265(MPEG-H Part2/HEVC)Main ProfileMotion JPEG分辨率2688x1520至320x240帧速率高达25/30fps,电源线频率为50/60Hz视频流提供多个可单独配置的H.264、H.265和Motion JPEG格式的视频流基于H.264和H.265格式的Axis Zipstream技术可控制的帧速和带宽VBR/MBR H.264/H.265多视点视频流全帧速下多达2个可独立裁剪的视点区域平移/倾斜/变焦数字PTZ图像设置压缩、颜色、亮度、锐度、对比度、白平衡、曝光控制、WDR:高达100dB,具体取决于场景。
巴克尔(Parker)空气准备系统产品目录说明书

Pneumatic Air Preparation Systems Optional Port Block Kits• To change port sizes Port Block Kits are available, they are attached to any unit utilizing the connecting kit.• Allows assemblies to be removed from a hard pipedsystem.Modular ManifoldP3Y Series Manifolds provide up to 4 extra outlet ports. They may be assembled at any position in a combination e.g. before the lubricator to provide oil free take off or at theend of a combination to provide extra outlet ports.Port sizesInlet port Top Bottom Front and Back 3/4"1/8”1”1/4”1"1/8”1”1/4”G1AccessoriesMaterial specificationsBody Aluminium Weight0.65 kg (1.43 lb)Material specificationsBody Aluminium Weight0.7 kg (1.5 lb)Dimensions mm (inches)Pneumatic Air Preparation SystemsSolenoid OperatorsSolenoid Operators - CNOMO MaterialsTechnical data -Solenoid operators, coil combinationsPilot ValveBody:Polyamide Armature tube:BrassPlunger & core:Corrosion resistant Cr-Ni steel Seals:Fluorocarbon Screws:Stainless steelCoilEncapsulation material:Thermoplastic as standard Duroplast for M12 connectionTransientsInterrupting the current through the solenoid coil producesmomentary voltage peaks which, under unfavorable conditions, can amount to several hundred times the rated operating voltage. Normally, these transients do not cause problems, but to achieve the Maximum life of relays in the circuit (and particularly of transistors, thyristors and integrated circuits) it is desirable to provide protection by means of voltage-dependent resistors (varistors). All connectors/cable plugs EN175301-803 with LED’s include this type of circuit protection.Solenoid Coils with M12 ConnectionSolenoid Coils with DIN A or Industrial B Connectionabove part numbers for spares. The operators are supplied with mounting screws and interface ‘O’ rings. Coils and connectors must be ordered separately.22mm x 30mm 30mm x 30mm Part number Spare Base Solenoid Pilot Operator CNOMO NCNC Normal Operator with 22 x 30 standard coilNC Normal Operator with 30 x 30 standard coil Working pressure 0 to 10 bar 0 to 10 bar Ambient temperature -10°C to 60°C *-10°C to 60°C *Power (DC) 4.8W 2.7W Power (AC)8.5VA 4.9VA Voltage tolerance +/-10%+/-10%Duty cycle 100%100%Insulation class FFElectric connection B Industrial DIN 43650A Protection IP65IP65Approval UL/CSAWorking mediaAll neutral media such as compressed air* Limited to 50°C if use with 100% duty cyclePneumatic Air Preparation SystemsSolenoid Nuts, Connectors & CablesSolenoid Connectors / Cable Plugs EN175301-803Part number 22mm Form B Part number 30mm Form A Solenoid coil dimensions mm (inches)Cable plug dimensions mm (inches)Electrical schematics22mm Form B industrial cable plugs22 x 30mm30 x 30mm30mm DIN 43650A cable plugs。
Parker Hannifin 全球空气准备系统P33系列用户说明说明书

Parker Hannifin Corporation Pneumatic Division Richland, Michigan/globalfrl16Catalog 0750-3 USGlobal Air Preparation SystemP33 SeriesFilter/Regulator + Lubricator Combinations, Poly bowl5 micron element, 8 bar (116 psig) regulator + gauge and wall mounting bracketsBall Valve + Filter/Regulator + Lubricator Combinations, Poly bowl5 micron element, 8 bar (116 psig) regulator + gauge and wall mounting bracketsPort size Flow Manual drainWeightAuto drain Weight1/2"43 dm 3/s 90 (scfm)P33CB94GEMNGLNW 1.84 kg (4.06 lbs)P33CB94GEANGLNW 1.84 kg (4.06 lbs)3/4"52 dm 3/s110 (scfm)P33CB96GEMNGLNW 1.84 kg (4.06 lbs)P33CB96GEANGLNW1.84 kg (4.06 lbs)Port size Flow Manual drainWeightAuto drain Weight1/2"43 dm 3/s90 (scfm)P33QB94GEMNGLNW 1.84 kg (4.06 lbs)P33QB94GEANGLNW 1.84 kg (4.06 lbs)3/4"52 dm 3/s110 (scfm)P33QB96GEMNGLNW 1.84 kg (4.06 lbs)P33QB96GEANGLNW1.84 kg (4.06 lbs)Port size Flow Manual drainWeightAuto drain Weight1/2"52 dm 3/s 110 (scfm)P33CA94GEMNGLNW 1.51 kg (3.33 lbs)P33CA94GEANGLNW 1.51 kg (3.33 lbs)3/4"71 dm 3/s150 (scfm)P33CA96GEMNGLNW 1.51 kg (3.33 lbs)P33CA96GEANGLNW1.51 kg (3.33 lbs)Port size Flow Manual drainWeightAuto drain Weight1/2"52 dm 3/s110 (scfm)P33QA94GEMNGLNW 1.51 kg (3.33 lbs)P33QA94GEANGLNW 1.51 kg (3.33 lbs)3/4"71 dm 3/s150 (scfm)P33QA96GEMNGLNW 1.51 kg (3.33 lbs)P33QA96GEANGLNW1.51 kg (3.33 lbs)Popular Combinations: Inlet pressure 10 bar (145 psig), Secondary pressure 6.3 bar (91.3 psig), 1 bar (14.5 psig) pressure drop.Filter coding(use with combo codes:B F G). For multiple filters, repeat as neededRegulator coding(use with combo code: B)Lubricator coding(use with combo codes: A B)Assembly configurationFilter / Regulator coding (use with codes: A M)Filter + Regulator + Lubricator Combinations, Poly bowl5 micron element, 8 bar (116 psig) regulator + gauge and wall mounting bracketsBall Valve + Filter + Regulator + Lubricator Combinations, Poly bowl5 micron element, 8 bar (116 psig) regulator + gauge and wall mounting brackets。
苏州贝宁格寇司德机械有限公司介绍企业发展分析报告模板
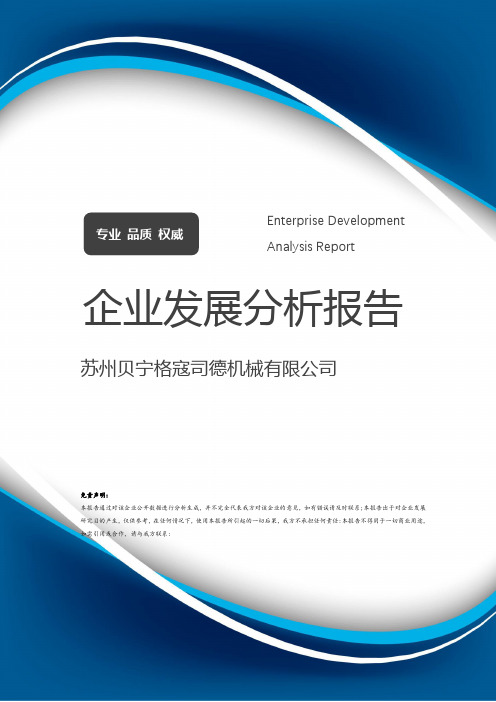
Enterprise Development专业品质权威Analysis Report企业发展分析报告苏州贝宁格寇司德机械有限公司免责声明:本报告通过对该企业公开数据进行分析生成,并不完全代表我方对该企业的意见,如有错误请及时联系;本报告出于对企业发展研究目的产生,仅供参考,在任何情况下,使用本报告所引起的一切后果,我方不承担任何责任:本报告不得用于一切商业用途,如需引用或合作,请与我方联系:苏州贝宁格寇司德机械有限公司1企业发展分析结果1.1 企业发展指数得分企业发展指数得分苏州贝宁格寇司德机械有限公司综合得分说明:企业发展指数根据企业规模、企业创新、企业风险、企业活力四个维度对企业发展情况进行评价。
该企业的综合评价得分需要您得到该公司授权后,我们将协助您分析给出。
1.2 企业画像类别内容行业空资质增值税一般纳税人产品服务机、后处理机、丝光机、水洗机、纺织烘干机、1.3 发展历程2工商2.1工商信息2.2工商变更2.3股东结构2.4主要人员2.5分支机构2.6对外投资2.7企业年报2.8股权出质2.9动产抵押2.10司法协助2.11清算2.12注销3投融资3.1融资历史3.2投资事件3.3核心团队3.4企业业务4企业信用4.1企业信用4.2行政许可-工商局4.3行政处罚-信用中国4.5税务评级4.6税务处罚4.7经营异常4.8经营异常-工商局4.9采购不良行为4.10产品抽查4.12欠税公告4.13环保处罚4.14被执行人5司法文书5.1法律诉讼(当事人)5.2法律诉讼(相关人)5.3开庭公告5.4被执行人5.5法院公告5.6破产暂无破产数据6企业资质6.1资质许可6.2人员资质6.3产品许可6.4特殊许可7知识产权7.1商标7.2专利7.3软件著作权7.4作品著作权7.5网站备案7.6应用APP7.7微信公众号8招标中标8.1政府招标8.2政府中标8.3央企招标8.4央企中标9标准9.1国家标准9.2行业标准9.3团体标准9.4地方标准10成果奖励10.1国家奖励10.2省部奖励10.3社会奖励10.4科技成果11 土地11.1大块土地出让11.2出让公告11.3土地抵押11.4地块公示11.5大企业购地11.6土地出租11.7土地结果11.8土地转让12基金12.1国家自然基金12.2国家自然基金成果12.3国家社科基金13招聘13.1招聘信息感谢阅读:感谢您耐心地阅读这份企业调查分析报告。
RJX汽油机说明书

Version 2.0 Technical Data:Overall Length Overall Height Overall WideMain Rotor Diameter Tail Rotor Diameter Gear RatioGross Weight1340 mm430 mm210 mmca.1560 mmca.281 mm6.64:1:4.75000g - 5300gPLEASE READ AND UNDERSTAND THE INSTRUCTIONS THOROUGHLY BEFORE ASSEMBLYINTRODUCTIONPlease read this manual carefully. It is essential for the correct assembly of thecontrol of the model without warning and the possibility of serious accidents or injury.The fuel used in model helicopter engines is highly inflammable and poisonous to human beings. For your own safety and that of others, you should exercise care when handling and storing it. Always read the label on the container and please note the cautions below.1.Model helicopter fuel is highly inflammable. Do not smoke or light fires near your fuel.2.We recommend that you keep your fuel in metal cans or plastic bottles and to store it where there is no risk of fire.3.Please keep fuel away from the starter battery. It only needs one spark and…..!!!4.Wipe up spilt fuel immediately. Do not take any chances.5.Do not leave fuel in the sun or in you car on a hot day.6.Before refuelling, shut off the engine and wait until it cools down.7.Always drain the fuel tank of you helicopter at the end of a flying session. It is good practice.-GASSERTABLE OF CONTENTS1. Introducion2. Table of contents3. Additional Items Required4. Tools Required5. Assembly6. Servo Installation7. Servo Adjustment 8. Rotor Head Setup9. Final Servo and Radio Setup 10. Please read before flight 11. Spare Parts ListI1I2I3I4A1 - A33S1-S4S5-S6A24R1-R5Pf1SP1 - SP6This manual contains the detailed instructions to build and set up the . Please follow it to ensure that you achieve the best performance and mechanical integrity from your finished kit. For those of you who already have experience of model helicopters, we still suggest that you assemble and adjust your model according to theseinstructions for the best results. Please keep your copy of this manual in a safe place and refer to it when replacing spare parts or upgrading.Remove oil and grease. (This applies throughout the manual)Please refer to the list at the end of this instruction manual when you need spare parts.Regardless how tight the nuts, bolts and screws are tightened, they will still slowly come loose over a period of time due to vibration from the helicopter. Should this happen the helicopter will become out of control or severely damaged causing a very potential dangerouse situation.We strongly recommend that you apply threadlock to any nuts, bolts or screws that are indicated by these signs.with Alcohol (or similar) before you apply the threadlock.TO PREVENT LOOSE SCREWS AND BOLTSHOW TO USE THIS INSTRUCTION MANUALUse CA (Superglue or similar) at this pointCA-GASSERADDITIONAL ITEMS REQUIRED TO COMPLETE THEChoose a CCPM compatible PCM Radio System forHelicopters with a minimum of 6 channels.Gyro system with Heading HoldThree large and two small disks or arms are required26cc Engine included26cc Size MufflerUnleaded fuel (95-98oct):40:1 mix with OilFuel Pumb 12V Electric StarterStarter EXT90-ension Fuel Filter 690mm - 710mm Main Blades (for kits without Blades)-GASSERCDI Battery 4,8V-6V (6v recomended)Allen Drivers 1,5mm - 2mm - 3mm - 4mm Phillips Drivers Large,Middle, Small Nut Drivers 4,5mm - 5,5mm - 7mm Cutter Universal Pliers Scissors Sandpaper Ball Link Plier Metric Ruler Pitch Gauge Cyanoacrylate (CA/Superglue)Epoxy 30 Minutes GreaseBall Link Driver Universal RC Cross Wrench Ball Link ToolTOOLS REQUIRED (NOT INCLUDED)STEP 1-2B Tail Drive Pinion Gear Assembly (Belt Version)STEP 1-1 Clutch Bell / Starter Shaft BB Block AssemblyClutch Bell Assembly (14T Pinion)Starter Shaft BB BlockIMPORTANT:Sand the inside before glueing the clutch liner.Apply threadlock to the pinion gear and install in place until the threadlock has completely set.Bearing. Assemble it as shown in the diagramm below.With Flange facing downwardsTail Drive Pinion BB BlockTail Drive PinionM3 WasherM3x6 Socket Head BoltFront Tail Pulley USE THREADLOCKMagnet´s for Governor:Install them by using 30 minute EPOXY .Special Nut (Flange downwards)Clutch LinerWith Flange facing upwardsBrass SpacerUSE THREADLOCKE PO X YSTEP 1-2TT Tail Drive Pinion Gear Assembly (TT Version)Tail Drive PinionM3 Washer12mm PinOutput Shaft19T Delrin Bevel Gear5x7x1 Washer(if needed)TT Gear BoxView of the complete Assembly.Check that the gearmesh is correctly(if necesary add a 0.2mm Nylon Washer) andthe assembly rotated freely but withoutplay.USE THREADLOCKSTEP 1-3 Drive Gear AssemblyM3x8 Socket Head Bolt93T Helical Main Gear Tail Drive Gear HousingAutorotation Shaft IMPORTANT:Stepped side facing downward and entering completly insidethe bearing.View of complete AssemblyUSE THREADLOCKIMPORTANT: Start assembly with the OUTPUT SHAFT.Autorotacion UnitThis step is preassembled.PLEASE CHECK AND ADD THREAD LOCKAlignedSTEP 1-4 Fuel Tank AssemblyMain TankTank GrommetM5 Special Nut STEP 1-5 Swash Control Lever AssemblyM2x8 Socket Head BoltJointballControl LeverView of the completed AssemblyNOTE: Assembly 2 sets of this leverUSE THREADLOCKFuel ClunkSpecial Silicon Tube 77mmTank NipplePreasur Nipple4mm Ball ArmNick ArmSwash LeverView of the completed AssemblySTEP 1-7 Front Tail Arm AssemblyUSE THREADLOCKM2x10 Socket Head BoltM3x20 Socket Head BoltJoinballControl LeverWasher 3x5x1LeverblockView of the completed AssemblySTEP 1-8 Battery Tray AssemblyUSE THREADLOCKBattery TrayView of the completed Assembly from both sideSpecial Crossmember BATTERY TRAY inside the bag of the MAIN FRAMESTEP 1-9 Canopy Stands32mm CrossmemberM3x8 Socket Head BoltBreakoffView of the completed AssemblyBREAKOFF are inside the bag of the MAIN FRAMEUSE THREADLOCKMain Frame RightMain Frame LeftUSE THREADLOCK32mmCrossmember(Assembled in STEP 2-1)TOPFront Tailcontroll ArmView of the completed AssemblyM3x10 Socket Head Bolt with Finish Cap´sM4x10 Socket Head BoltMiddle Engine MountUSE THREADLOCK32mm Crossmember12mm SpacerCanopy MountM3x10 Socket Head BoltView of the completed AssemblyM3x10 Socket Head Bolt (Do NOT use Threadlock)M3x10 Socket Head Bolt M4x10 Socket Head BoltFrame StifferGyro MountGyro MountSwash GuideSTEP 2-6 Main Frame Assembly (TT+Belt)USE THREADLOCKCanopy MountCanopy StandoffM3x10 Socket Head BoltFront Tailrod SupportStarter ShaftAssembled in Step 1-2Hex Starter CopplerM4x4 Set ScrewFlange downwardsM3x10 Socket Head Bolt with FinishcapM3x10 Socket Head Bolt with FinishcapView of the completed AssemblySTEP 2-8 Fanshroud Cutting (TT+Belt)75mmNote:Cut the Fanshroud like shown with a Dremel or other cutting Tool.FANSHROUD IS DELIVERED FINISHED TO INSTALL3x16 Special Socket Head BoltFan ShroudView of the completed Assembly3x16 Special Socket Head BoltSTEP 2-10 Main Frame Assembly (TT+Belt)USE THREADLOCKMain ShaftMain Shaft CollarAutorotacion UnitView of the completed AssemblySTEP 2-11 CCPM Sytem Assembly (TT+Belt)M4x4 Set ScrewM4x4 Set ScrewM4 Lock NutM4 Lock NutWasher 4x6x1Nick LeverCCPM BallcrankSpacer 4x6x4Bearing F4x8x3Bearing F4x8x3CCPM BallcrankNick ArmView of the completed Assembly USE THREADLOCKSTEP 2-12 Main Tank InstallationTank RubberView of the completed AssemblyC AC ATank RubberNOTE:Use CA to fix the Tank Rubbersin the corners of the Main Frame.Main Tank AssemblySTEP 2-13 CDI Mounting PlateUSE THREADLOCKView of the completed AssemblyCDI Mounting PlateM3x14 Socket Head BoltLanding StrutLanding Skid Brace M3 Lock NutSkid HolderLanding StrutSTEP 2-14 Landing Skid AssemblyTo be used in backView of the completed AssemblyView of the completed AssemblyLanding SkidsNOTE:Place the complete assembly on a flat surface.Do NOT tighten the screws yetSTEP 2-15 Landing Gear AssemblySTEP 3 Engine Breakin InstructionsIMPORTANTProp MountM4x12Prop WasherM8x25Use the delivered Tool to block the Engine for tidening the engine nut.In order for the motor to do a proper running and break in follow the procedures . Proper needle settings, oil and oil ratio as well as properly filtered fuel must be used.Needle SettingsThe 26 motor is equipped with Walbro series carburetor. Low Speed Needle:1 and ½ turns openfrom full closed. Never operate at less than 1 and 3/8 turns open. It may be necessary to open this needle initially more than 1 and ½ turns open to get the motor rich enough for break in operation. This needle is very sensitive and very small adjustments are required.High Speed Needle:1 and ½ turns open from full closed. Never operate at less than 1 and 3/8 turns open. It may be necessary to open this needle initially more than 1 and ½ turns open to get the motor rich enough for break in operation. This needle is less sensitive than thelow needle and slightly larger adjustments can be made.Always run both needles as rich as possible for satisfactory results. During break in, the needles may both need to be opened slightly each flight as the motor breaks in.Always error to the rich side on both needles as being slightly too rich will not damage the motor, being too lean can cause motor damage.Run through the motor at least 5L of fuel. As longer the break in procedure as smoother the engine will run.Air FilterIt is recommended that an air filter be used on this motor. The stock filter will work adequately.To breakin the engine best to mount it outsideof the ing special designed Prop Mount (optinal) and a 16x10 Prop(not delivered).Fix the Prop as shown in the dia-gramm next.A correct done breakin of the engine will have a smooth running engine at the end.OPTIONAL (EG1000)STEP 3-1 CLUTCH/COOLING FAN ASSEMBLYDrive Nut( incl. with Engine)Cooling Fan HubUSE THREADLOCKNOTE:Assemble as shown in the diagram and securethe engine nut tightly and check that the Hub is correctly into the shaft. Use the delivered Crank LockTool.Take the Spark Plug out and replace it with the Tool. Check that the psiton is nearly at his highest point to avoid damage to the engine.ClutchM4x10 Socket Head BoltM2x8 Socket Head BoltM2,5x8 Socket Head BoltJointballCarbarmM2 NutM2,5 Lock NutCrankshaft Lock PinUse the delivered Tool to block the Engine for tidening the engine nut.View of the completed AssemblyUSE THREADLOCKSTEP 3-2 Engine Installation (TT+Belt Version)STEP 3-3 Engine Installation (TT+Belt Version)View of the completed AssemblyM5x55 Socket Head BoltM4 Lock Nut4x15x1,6 Washer2,5 mm BottomplateNOTE:Do NOT tiden the screws fully.Will be neededto adjust later to get correct gearmesh.M3x18 Socket Head BoltSTEP 3-4 ENGINE-PINION GEAR LINEOUT1.Push the engine so that the clutch is standing approx. 1mm out of the clutch bell. Look from the side and ensure that the clutch is level with theclutch bell. Check that the starter shaft rotate freely and smooth. Carefully tighten the four M3x10 Bolts so you do not disalign the engine. Check the correct alignment by turning the main gear and that the clutch is not touching the clutch bell and it runs smoothly. Now tighten the M4x35 screws and double check that the engine is still in correct alignmet.Unscrew one at a time the M3x10 bolts , apply threadlock then tighten them. This stop the clutch system moving position.2.IMPORTANT about GEAR MESH:In order to archive smooth operation of the main drive train, it is important that the correct gearmesh is obtained after assembly. Try to mesh the gears to get the minimum amount of backlash and the smoothest rotation. Remember that too little clearence and the train will be too stiff to work properly and too much clearance may result the teeth stripping off when under load.Tighten and threadlock the six M3x10 Socket Head Bolts and ensure the engine is in line.Tighten and threadlock the six M4x35 Socket Head Bolts and the two M3x10 Socket Head Bolts .Ensure the engine is in line.STEP 3-4/1 Fuel Line ConectionsNot ConectedUse a fuel line and take the final down to the bottomplate.STEP 4-1 SWASHPLATE ASSEMBLYSTEP 4-2 WASHOUT ASSEMBLYView of the completed AssemblyView of the completed AssemblyUSE THREADLOCKUSE THREADLOCKWashout BaseWashout ArmJointballM3x12 Socket Head BoltWasher 3x5x1Washout ArmSTEP 4-3 SWASHPLATE / WASHOUT INSTALLATIONSTEP 4-4 SEESAW INSTALLATIONTOPBOTTOMView of the completed AssemblyView of the completed AssemblyM3x10 Socket Head BoltRotor StopperCenterhubM4x6 Socket Head BoltM4x6 Socket Head BoltUSE THREADLOCKIMPORTANT:Do NOT over tighten the M4x6 Socket Head Bolt to fix the Seesaw.Hard type of thread lock is necessary.NOTE:Apply the threadlock inside the Seasaw.On this way the fix of the screws is enured.STEP 4-5 MAIN BLADE HOLDER ASSEMBLYSTEP 4-6 MIXER ARM ASSEMBLYView of the completed AssemblyView of the completed AssemblyMain Blade HolderM3x6 Socket Head BoltPitch ArmMixer ArmBall Arm 4mmNOTE: Assemble 2 sets of the Main Blade Holder. Detailed adjustments in Step 4-13.NOTE: Assemble 2 sets of this mixer armIMPORTANT:Mixer settings are explained in Step 4-13 more detailed.STEP 4-8 MAIN ROTOR HEAD ASSEMBLYView of the completed AssemblySpindleDamperSpindle CollarM5x12 Socket Head BoltThrust Bearingsmaller IDUSE THREADLOCKView of the completed Assembly4mm Flybar (550mm)Washer 3x5x2Ball Arm 9mmM3x16 Socket Head Bolt Assembled in Step 4-6Washer 3x5x1Flybar ArmRotorhead AssemblyM4x4 Set ScrewPhase RingSet Screw M3x4Jesus Bolt M4x8View of the completed AssemblyM3x14 Socket Head Bolt Link BUse four long links and STEP 4-10 CONTROL ROD INSTALLATIONUSE THREADLOCKSTEP 4-11 CONTROL ROD INSTALLATIONUSE THREADLOCKM2,5x12 Socket Head BoltLinkage Rod BLinkage Rod CLinkage Rod ASTEP 4-12 ROTOR HEAD SETUPNOTE:In this STEP will be explained one setup of the rotor head what is good point for 3D maneuvers. There are many other settings possible.Linkage rod sizes from the rotor head are changing depending on this settings.The size of the linkage rod is meassured from center to center of the hole (see STEP 4-10) .IMPORTANT: SECURE ALL JOINT BALLS AND SCREWS WITH THREADLOCKSTEP 4-12 MAIN ROTOR HEAD ASSEMBLYFlybar PaddleFlybar PaddleUSE THREADLOCKABEnsure the two M4x4 Sets Screws are on the D-Cut of the Flybar.Bh1Bh2Bh3Negative DeltaPositive DeltaSTEP 4-13 ROTOR HEAD SETUPMb1Mb2Mh1Mh2Mh3Mh1: LESS RESPONSIVE Mh2: RESPONSIVEMh3: VERY RESPONSIVE Mb1: RESPONSIVEMb2: VERY RESPONSIVEFor the linkage rod coming from the swashplate (left) using holes closer to the center make the head more active and away from center make the head more stable. For the linkage rod from the seesaw (right) using holes closer to the center make the head less active or more stable and away from center more active.In the diagrams below are explained the different settings posibilitys of this rotor head. There are many setups with different results. Adjust this settings on demand of you and your capability. Some of the settings can produce binding. Ensure that the ATV settings in the radio and linkage rod adjustments allowing no bindings. This is important to achive a good performance of the rotor head.S1S2S3S1: LESS RESPONSIVE S2: RESPONSIVES3: VERY RESPONSIVEOn the flybar carrier holes closer to the center pivot are more active and away from the center are more stable.STEP 5-1TT TAILCASE ASSEMBLY (TT Version)Pin 14mmTail Pulley 17TTail ShaftM3x4 Set ScrewTailcaseView of the completed AssemblyUSE THREADLOCKView of the completed AssemblyUSE THREADLOCKTail ShaftTail Input Shaft14mm Pin19T Delrin Bevel Gear19T Delrin Bevel Gear15,8mm Copper SpacerTT Tail CaseM3x4 Set ScrewIMPORTANT:Add 0,2mm Nylon washer to reach a PLAYLESS Gear mesh.Check that the two gears are perfectly aligned (shown in the picture on the right).Stay on the tight side of the gear mesh.A exesive play can strip the Delrin gear. Lub the Bevel Gears regulary.AlignedThis step is preassembled.PLEASE CHECK AND ADD THREAD LOCKView of the completed AssemblyWasher 3X5x2Tail Pitch Control LeverWasher 3X5x2M3x20 Socket Head BoltJointballM2x6 Socket Head BoltUSE THREADLOCKSTEP 5-2TT TAILCASE ASSEMBLY (TT Version)USE THREADLOCKWasher 3X5x2Tail Pitch Control LeverWasher 3X5x2M3x20 Socket Head BoltJointballM2x6 Socket Head Bolt Pitch BrigeSlider RingSliderView of the completed AssemblyWasher 3X5x1Washer 3X5x1Pitch Lever SupoortJointballM2x5 Socket Head BoltSTEP 5-3 TAILCASE ASSEMBLY (TT+Belt Version)STEP 5-4 TAILROTOR ASSEMBLY (TT+Belt Version)NOTE:Check that the Joint ball is working freely and smoothly in the tail pitch control lever.View of the completed AssemblyM2x10 Socket Head BoltTailhubTail GripM3 Lock NutView of the completed AssemblyUSE THREADLOCKIMPORTANT:Check the pre installed assemply and add red threadlock on the copper sleeve.JointballUSE THREADLOCK5x10x4 Bearing5x10x4 Bearing Dampner 5x7x1M3x20 Socket Head Bolt3x10x1,5 WasherSTEP 5-5 TAILCASE ASSEMBLY (TT+Belt)USE THREADLOCKM4x4 Set ScrewSTEP 5-5B TAILCASE ASSEMBLYView of the completed AssemblyUSE THREADLOCKS3M1800 Tail BeltSTEP 5-6TT Torque Tube ASSEMBLYUSE THREADLOCKTT Coppler with Oneway BearingTorque TubeView of the completed AssemblySTEP 5-6TT Torque Tube ASSEMBLYNote:Fix the Torque Tube Bearing Support with EPOXY .Take special Care that no EPOXY get inside the Bearing when assembly.Inner Bearing CaseBearingE PO X YOuter Bearing CaseRubber RingView of the completed AssemblySTEP 5-7 TAILCASE ASSEMBLY (Belt Version)USE THREADLOCKM3x6 Socket Head BoltFinish Cap Finish CapVertical FinTailboomAssembled in Step 5-6View of the completed AssemblySTEP 5-7TT TAILCASE ASSEMBLYUSE THREADLOCKM3x6 Socket Head BoltFinish CapFinish CapM3x10 Socket Head BoltTailboomAssembled in Step 5-6Torque Tube AssemblyNote:Add some grease on the Rubbers and inside of the Tailboom tointroduce the Torque Tube assembly easily.View of the completed AssemblySTEP 5-8 TAIL BOOM INSTALATION (Belt Version)Belt tension should be set so that hen pressing with you finger,the sides of the belt do not come in contact with each other. If unsure is always better to set the belt tension too tight rather than too loose.Tighten up the M3x40 after adjusting the tension.Front PulleyIN THE DIRECTION AS SHOWN.Check that the tail rotor is at 90 .ºNote:Check that the Oneway Bearing from the Coppler is flash with the Output shaft from the Front Tail Gear Case.correctly introduced.STEP 5-9 TAIL BRACE ASSEMBLY (TT+Belt Version)STEP 5-10 TAIL BRACE ASSEMBLY (TT+Belt Version)Metal EndMetal EndM3x12 Socket Head BoltFinish CapHorizontal FinUpper ClampLower ClampView of the completed AssemblySTEP 5-11 TAIL BRACE INSTALLATION (TT+Belt Version)STEP 5-12 TAIL CONTROL ROD ASSEMBLY (TT+Belt Version)32mm CrossmemberM3x10 Socket Head BoltUSE THREADLOCK12mm SpacerLong Link740mm Rod(Belt)Long LinkSTEP 6-1 SERVO INSTALLATION(Throttle Servo)STEP 6-2 SERVO INSTALLATION(CCPM)2,6x12 Selftapping Screws Washer 2,6x7x1Servo Mounting Plate (inside)2,6x12 Selftapping ScrewsServo Mounting Plate2,6x12 Selftapping ScrewsWasher 2,6x7x1Servo (from OUTSIDE)Servo (from INSIDE)Servo (from INSIDE)ENSURE ALL SERVOS ARE ON THEIR ANTI -VIBRACION MOUNTING RUBBERS AND NOT TO TIDE FIXED.STEP 6-3 SERVO INSTALLATION (CCPM Servo)STEP 6-4 SERVO INSTALLATION(Tail Servo)2,6x12 Selftapping ScrewsWasher 2,6x7x1Servo Mounting Plate(from inside)2,6x12 Selftapping ScrewsWasher 2,6x7x1Servo Mounting Plate(from inside)Servo(from OUTSIDE)Servo(from OUTSIDE)STEP 6-5 RECEIVER / GYRO / BATTERY INSTALLATION1.2.3.1.Install the Battery and Receiver2.3.Gyro Amp or Governor Amp Install the Gyro sensorInstall the Gyro Amp or Governor Amp.Install the the Switch harness Install the Carbsmart Amp or others.Mounting space for CDI and CDI BatteryNOTE:Before attaching any of the servo output arms, turn on your radio and check that all of the primary control functions and trims are set to neutral. Payspecial attention to the throttle/pitch channel where the stick has to be positioned manually unless your transmitter has a digital or graphical display of the output. If you have this feature, set the stick to give a read out of 50%. If you do not have this feature you will need to set the stick to the neutral position by eye. If you also have hovering pitch and throttle trim knobs, these should also be set to their mid positions to give equal amounts of +/- output. Once you have done this, all of the servos should be at their mid points and have equal amounts of rotation in both directions.Initial set up can now begin.Choose the thickest output arms/discs that you have, and that can accommodate the joint balls at a radius of 13.5mm each.For the left/right servos try the disc/arm on the output shaft until you find a position where a suitably spaced pair of holes sits closest to the centre line of the servo case. For the front servo, imagine a rectangle whose four corners sit on the four joint balls making up this linkage. The holes in the disc/arm should sit on the line that forms the short end of this rectangle. Please refer to the diagram again for clarification.If you cannot find an exact position use the one nearest and make minor adjustments with the appropriate sub trim and not the main trim.Remove the disc/arms one at a time and noting which side the joint balls fit, attach them as shown. Also note the use of spacers under the joint balls fitted to the left/right servo discs/arms.Cut off the excess material or unused arms as shown and refit the finished disk/arm in its original position. Fix securely with the screw that came with the servo.STEP 6-6 SERVO ARM PREPARATION AND INSTALLATION90º90ºM2x8 Socket Head BoltJointballM2 NutM2x8 Socket Head BoltJointballM2 NutRight ServoThrottle ServoIMPORTANT:Be sure that all arms are 90º and parallel to each other like shown in the diagrams above.1. Attach the jointball to the servo horns on the left,right,rear,throttle (ensure the carburator is at 50% opened, if not adjust the throttle arm on the carburator) and tail servo as shown in the diagram above.2. Mount the servo horns firmly with the screw included in the servo. Use threadlock on servos with metal gears to secure the screws.3. Be sure to connect the servos according your transmitter manual.4. Make sure all servo horns are positioned as shown above. If the servo horn is not parallel as shown, minor centering adjustments can be made using the radio´s subtrim.USE THREADLOCK90ºLeft ServoDepending on Servo Type installthe balls from INSIDE.Set Horn to be at full closed Carb and max open to full travel of servo17mm90ºNOTE: Assembly the linkage as shown belowCheck the correct side of the link with the logo.Measurments are from center hole to center hole.RJXHOBBY1. RIGHT SERVO2. LEFT SERVO3. REAR SERVO4. THROTTLE SERVO5. TAIL SERVO90ºUse two XL links and the 2,6x295mm RodSTEP 7-1 PHASE RING ADJUSTMENTCORRECTIN LINEINCORRECTOUT OF LINEINCORRECTOUT OF LINECENTER LINE OF THE HELICOPTERUSE THREADLOCKFixing pointSTEP 7-2 CANOPY ATTACHMENTRear Canopy MountFront Canopy MountSTEP 7-3 MAIN / TAIL BLADE INSTALLATIONM5x34 Socket Head BoltM5 Lock NutM3 Lock NutM3x20 Socket Head BoltWasher 3x10x1,595mm CF Tail BladesRudder and Throttle Servo Adjustments 1.Checking the servo rotation.With the radio transmitter and receiver switched on, move the rudder and throttle sticks, and check that each servo moves in the correct direction. If either servo moves in the wrong direction, it will be necessary to reset that servo using the appropriate reversing function on your transmitter. 2.Travel Adjust.Switch the transmitter and receiver on, then move the rudder and throttle sticks to their extremes and see if each servo moves to its full control position. If either servo moves too far and binds up it will be necessary to reduce the ATV for that channel, likewise if it does not move far enough you will have to increase it. For any given channel, the value in both directions should be equal. Do not exceed a maximum ATV difference of 10%. If the throttle ATV is unbalanced by more than this amount, then the servo sub trim or the positions of the arms on throttle servo and/or on the carburator will have to be repositioned. If the rudder ATV is unbalanced by more than 10% then the servo sub trim and/or tail pitch arm neutral setting should be re-checked and any necessary adjustments made.NOTE: Try to get the mechanical set up as close possible to the values given in this manual and you will find that final trimming will be so much easier. Using the transmitter to correct a poor mechanical set up will result in a model that is very difficult to trim and fly.3. Sub trim FunctionWhen the rudder stick and trim are in their mid position make sure that the servo horn and tail control rod are at 90º as shown next. If you cannot achieve the desired servo arm position use the sub trim function to make minor adjustments.NOTE: lt is necessary to keep the sub trim values as close to zero as possible to make final setting up simple.If you are not using a head locking gyro it will be necessary to adjust the revolution mixing to compensate for the torque changes of the engine during all flight conditions (except autorotation). We recommended that the initial Revo mix values be set to approximately 10% for hovering and 5% for stunt/aerobatic flight. Since there are many variables that can alter the values of the revolution mixing, it will be necessary to fine tune these according to your flying style. If you are using a dual function gyro ie one that can be switched between normal and head locking mode, then please refer to your gyro's instructions for more information.NOTE: The Revo mixing values must be set for a helicopter with aclockwise rotating head.Correct ATV Incorrect ATV100%100%100%50%0%0%90º90º。
KONGSBERG GT402 海洋应用压力传感器说明书
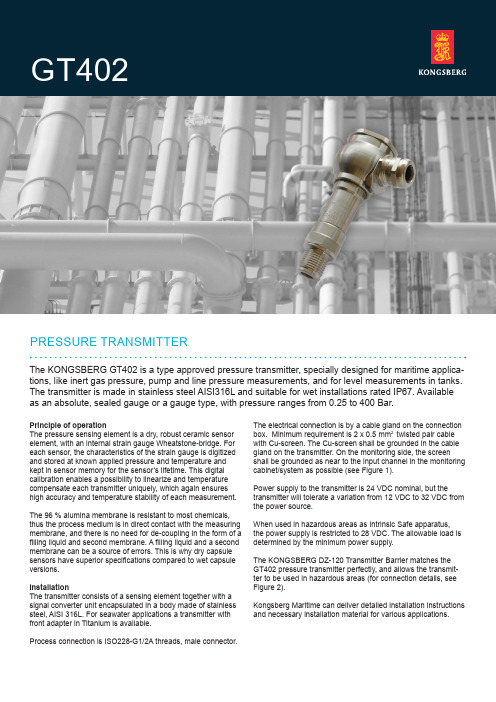
The KONGSBERG GT402 is a type approved pressure transmitter, specially designed for maritime applica-tions, like inert gas pressure, pump and line pressure measurements, and for level measurements in tanks. The transmitter is made in stainless steel AISI316L and suitable for wet installations rated IP67. Available as an absolute, sealed gauge or a gauge type, with pressure ranges from 0.25 to 400 Bar.PRESSURE TRANSMITTERPrinciple of operationThe pressure sensing element is a dry, robust ceramic sensor element, with an internal strain gauge Wheatstone-bridge. For each sensor, the characteristics of the strain gauge is digitized and stored at known applied pressure and temperature and kept in sensor memory for the sensor’s lifetime. This digital calibration enables a possibility to linearize and temperature compensate each transmitter uniquely, which again ensures high accuracy and temperature stability of each measurement.The 96 % alumina membrane is resistant to most chemicals, thus the process medium is in direct contact with the measuring membrane, and there is no need for de-coupling in the form of a filling liquid and second membrane. A filling liquid and a second membrane can be a source of errors. This is why dry capsule sensors have superior specifications compared to wet capsule versions.InstallationThe transmitter consists of a sensing element together with a signal converter unit encapsulated in a body made of stainless steel, AISI 316L. For seawater applications a transmitter with front adapter in Titanium is available.Process connection is ISO228-G1/2A threads, male connector.The electrical connection is by a cable gland on the connection box. Minimum requirement is 2 x 0.5 mm 2 twisted pair cable with Cu-screen. The Cu-screen shall be grounded in the cable gland on the transmitter. On the monitoring side, the screen shall be grounded as near to the input channel in the monitoring cabinet/system as possible (see Figure 1).Power supply to the transmitter is 24 VDC nominal, but thetransmitter will tolerate a variation from 12 VDC to 32 VDC from the power source.When used in hazardous areas as Intrinsic Safe apparatus, the power supply is restricted to 28 VDC. The allowable load is determined by the minimum power supply.The KONGSBERG DZ-120 Transmitter Barrier matches the GT402 pressure transmitter perfectly, and allows the transmit-ter to be used in hazardous areas (for connection details, see Figure 2).Kongsberg Maritime can deliver detailed installation instructions and necessary installation material for various applications.DRAWINGS AND INSTALLATIONFigure 1: Electrical and mechanical installation of GT402Figure 2: Connection diagram for Ex-area installationsORDER CODEThe system must be depressurized before assembly of the pressure transmitters.Compliance with the Essential Health and Safety Requirements has been assured by compliance with:CENELEC EN 60079-0 : 2012 and CENELEC EN 60079-11 : 2012• The stated input values Ui, Ii and Pi are to be regarded as individual maximum values. It is a precondition that the diode safety barrier in the supply circuit has a linear resistive output characteristic.• When installing titanium sensors, special caution must be taken to avoid ignition hazard due to impact or friction.For details about safe installation and various solutions for different applications, see the GT400 Series Pressure Sensor Applica -tions Guidelines369048.SPECIAL CONDITIONS FOR SAFE USEMeasuring range: 0.25 to 400 barAccuracy*: See order code Temperature drift: See order codeLong term drift: < 0.3 % /year (% of nom. range)Output signal: 4 to 20 mA / HART Output current:3.8 mA < Io < 21.6 mA Output current at fault: Io ≤ 3.6 mAPower supply: 24 VDC (12 to 32 VDC depending on load resistance)Load resistance: 0 to 1150 ohm dependingon power supplyEx classification: Ex certification: NEMKO 02ATEX119X IECEx NEM 12.0008XEnvironmental standards: IACS E10 CISPR 22Operating temperature: - 45 °C to + 85 °C Storage temperature: - 50 °C to + 100 °C Materials Body: AISI 316 / Titanium gr.2Membrane: 96 % alumina ceramics Gasket:See order keyProtection grade: IP 56 (gauge transmitter) IP 66/67 (abs. transmitter)Weight: 0.4 kgCable gland:M20, M20+ or M25Safety dataMax. input voltage: Ui = 28 VDC Max. input power: Pi = 0.85 W Max. input current: Ii = 150 mA Max. internal capacitance: Ci = 30 nF Max. internal inductance: Li = NegligibleType approvals: MR (EU mutual recognition), NK, CCS, ABS * Including non-linearity, hysteresis and repeatibility at 22 ˚C. ** FRO = Full Range OutputSpecifications subject to change without any further notice.TECHNICAL SPECIFICATIONSFEATURES• Accuracy 0.25 % of FRO**• Temperature drift < 0.005 % of FRO**/˚C • Pressure ranges from 0.25 to 400 Bar • HART compatible• Membrane made of 96 % alumina ceramics • Body of AISI 316 L or titanium •Rugged constructionP -G T 402/C E R e v . TE-mailsales:*********************.comE-mailsupport:************************Figure 3: Dimensional sketch of GT402。
KONGSBERG GLA-300 P Radar Tank Gauge产品说明书

The KONGSBERG GLA-300/P Radar Tank Gauge (RTG) is part of the GL-300 Tank Monitoring System. Together with the GC-300 Cargo Temperature Unit (CTU) and the GLK-300 Signal Processing Unit (SPU), the RTG introduces modern and flexible arrangements for simpler installation. The radar technology pro -vides accurate measurement regardless of the atmospheric conditions inside the tank. The tank pressure transmitter is fully integrated regarding mechanics, electronics and cabling.RADAR TANK GAUGE FOR OIL, PRODUCT AND CHEMICAL TANKERSPrinciple of operationThe RTG employs the Frequency Modulated Continuous Wave (FMCW) principle with dual sweep technology to eliminate Doppler-effect caused by cargo movement. The distance (i.e. ullage) is derived from the time delay of the reflected signal. The electronic unit in the RTG includes a patented signal detec-tion method that ensures optimum performance.A frequency sweeping microwave signal is emitted by the RTG, and by aid of the offset parabolic antenna directed vertically down the tank. The high frequency combined with the antenna design gives a very narrow beam width of ±3 °.The GLA-300/P is designed with an offset parabolic antenna and a small feeder. The antenna and feeder are designed with an angle that will avvoid any condensate or pollution to stick to the antenna surface.The radar is connected to a dedicated GLK-300 SPU by a RS-485 communication link (2-pair cable).Tank pressure transmitterThe GT406 tank pressure transmitter is fully integrated in the RTG. The transmitter comes pre-installed from the factory.The pressure transmitter is built around a dry, robust ceramic measurement capsule with internal capacitive sensing and with a ratiometric output.The pressure transmitter is connected to the GLK-300 SPU by a HART bus link (1-pair cable).Tank installationThe RTG adapts to a gauge socket with a minimum inner diam-eter of 200 mm (larger sockets can be used). The gauge socket shall be welded to the top of the tank, preferably as close to the centre of gravity of the tank as possible.The RTG housing includes a cable gland for connection to the GC-300 Cargo Temperature Unit (1-pair cable).Radar Tank Gauge Measuring range: 0 to 50 meter RMS accuracy*: 2 mmFrequency: K-band (24 GHz)Beam width: ± 3 °Material:AISI 316L and PTFETank Pressure Transmitter Measuring range: 0.8 to 1.8 bar Accuracy: ±1.0 % of FRO** Temperature drift: < 0.014 % of FRO**/ ˚C Long term drift: < 0.3 % /year (% of nominal range) Material: AISI 316 and Titanium Common specification Cable specification: 3 x twisted pair common screen Operating temperature: -45 ˚C to +80 ˚C Protection grade: IP66/67Weight: 12 kgEx-classification:Ex ia IIC T4 Ga Ex-certification: IECEx SIR 14.0025XSIRA 14ATEX2056XEnvironmental standards: IACS E10 CISPR 22Safety data (power)Max. input voltage: Ui = 14,3 VDC Max. input power: Pi = 2,1 W Max. input current: Ii = 360 mA Max. internal capacitance: Ci = 75 nF Max. internal inductance: Li = negligible Type approvals:ABS, BV, CCS, DNV-GL, KRS,LRS, NK, Rina, RMRS* RMS sensor accuracy at controlled environment ** FRO = Full Range OutputSpecifications subject to change without any further notice.TECHNICAL SPECIFICATIONSFEATURES• Applicable for oil, product and chemical tankers • Radar RMS accuracy 2 mm• Half power beam width 1 6 ° (±3 °)• Measuring range 0 to 50 m• Operating temperature -45 to +80 °C • Ingress protection IP 66/67• Intrinsically safe Ex ia IIC T4 Ga • Stainless steel AISI 316L•Integrated tank pressure transmitterP -G L A 300/C E R e v . FE-mailsales:*********************.com E-mailsupport:************************1For details about free space requirements, ref. Installation Manual.RTG unit housingGauge socket(yard supply)Figure 2: GLA-300/P on a Ø200 mm socket. In-spection hatch mounted on the gauge socket.Figure 1: Dimensional drawing GLA-300/PORDER CODE。
KONGSBERG NASAMS空气防御系统产品介绍说明书
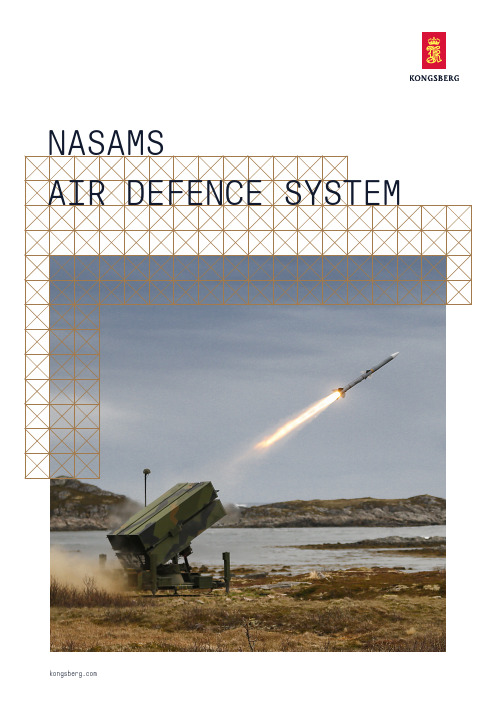
NASAMSAIR DEFENCE SYSTEMKONGSBERG is an international corporation with strong Norwegian roots. Collaboration with our customers, partners and suppliers, and a commitment to understand the context where our technology is applied, are important driving forces behind the corporation’s international development and growth.KONGSBERG contributes to improved safety, security and performance in demanding and complex missions. We achieve this through an in-depth knowledge of our customer’s objectives and the needs of the operator, and by meeting their challenges with the right systems, services andtechnological solutions.NASAMSAIR DEFENCE SYSTEMNASAMS (Norwegian Advanced Surface-to-Air Missile System) is the world’s first operational Network Centric Short to Medium Range Ground Based Air Defence System.Unique featuresNASAMS features net centric architecture, multiple simultaneous engagements and Beyond Visual Range (BVR) capabilities, closely integrated and adapted to a country’s adjacent weapons and command and control systems. The NASAMS network expands the defended area and enhances the total fighting capability of the armed forces.NASAMS has since the introduction in Norway been on a path of continuous evolution. The current NASAMS customer base consists of twelve (12) countries, including five NATO and/or EU members.A total of fifteen (15) nations have acquired the KONGSBERG command and control solution adapted to their requirements.The most recent capabilities, demonstrating NASAMS path of evolution, are the AMRAAM Extended Range missile (AMRAAM ER) and the AIM-9X-2. AMRAAM ER significantly extends the engagement volume of NASAMS, while the AIM-9X-2 is optimized for shorter ranges. Adding multiple missiles proves the flexibility of the architecture and the ability to introduce new capabilities to counter current and future threats. The SystemA standard NASAMS unit has a modular design comprising of a command post; the FDC, an active 3D radar AN/MPQ-64F1 Sentinel, a passive electro- optical and infrared sensor and a number of missile canister launchers with AMRAAM missiles. Normally, a number of NASAMS fire units are netted together in a uniquely designed ”hard-real-time” communication network to ensure minimum latency over large distances for maximum system performance utilizing the unique capabilities of the AMRAAM missile.Flexible mission configurationNASAMS is by nature a highly mobile system designed with focus on operational flexibility for protection of Air Bases, Sea Ports, Populated Areas, other High Value Assets and mobile Army Forces. NASAMS has proven interoperability with Higher Echelon Units (HEU) and longer range systems, such as Patriot. The modular design permits mission oriented task force organization of NASAMS, allowing the operators to maximize the effect of the components and tailor the system to the task.Continued active missionNASAMS has been protecting Washington DC 24/7 since 2005 demonstrating extreme reliability and with very high availability.N A SAM S is de signed foroperations in artic, sub tropicand desert conditions.NASAMSExtreme Performance for Extreme ConditionsKONGSBERG/Raytheon offers a fielded and proven NASAMS system with capability to protect several areas and high-value assets separated by large distances.NASAMS is on a path of continuous evolution.VALUE OF NASAMSUnprecedented fire power, low manning requirements, redundancy and flexibility are typical NASAMS characteristics enabled by the relatively small and agile components comprising the system. The NASAMS’ ability to protect static and mobile assets, opens for a range of roles and missions.Dual use AMRAAM MissileNASAMS employs the Raytheon AMRAAM as the basic missile, identical to the AMRAAMs used on fighter aircraft. The dual-use concept has operational advantages and reduces logistics cost.Defends a large geographical areaThe radar and launcher elements can be deployed over a large area separated by more than 20 kilometres from the FDC, providing an extended coverage with few elements. Dispersed elements increase its survivability against enemy air and ground attacks.NASAMS is designed to evolve with the development of technology and can integrate with or utilize future technology when available. This can be future active or passive radars and sensors, Sense & Warn capability, and a wide range of effectors (e.g. longer and shorter range missiles, C-RAM, etc.). The evolution is enabled by the open architecture in the FDC.The FDC is a true Multi Domain Command & Control component and can, pending on desired configuration, support a wide range of missions; GBAD, Army counter fire operations, coastal defence, air surveillance, airspace management and others.EVOLUTION40AMRAAM User nationsNASAMS FEATURESStatus of NASAMSIn production and in operational use. Selected by 12 customers.NASAMS Tests & Tactical firings 228 ( > 91 % success)AMRAAM Dual use(without any modification)Fighter Aircraft and NASAMS AMRAAM Combat kills > 13Target setsUAVs, Helicopters, Cruise Missiles, UCAVs, Aircraft NASAMS ArchitectureOpen SW & HW architecture, COTS, Network Centric Simultaneous multiple engagements 72Mission of Reference > 140 000 hours demonstrated(continuous operations (24/7), ongoing mission)TransportabilityAir (C-130 and helicopter), Sea and Land Data links (implemented and in use)Link 16, JRE, Link 11, Link 11B, LLAPI, ATDL-1Mission Planning ToolEmbedded and stand alone (PC)The KONGSBERG FDC command post and networking technology are selected by several nations globally. Experience and practical knowledge from these programs are embedded in NASAMS and ensures proven interoperability with a nation’s higher echelon and allied NATO/EU forces. NASAMS is in operational use in Norway, Spain, USA, the Netherlands, Finland, Oman, Lithuania, Indonesia and one undisclosed customer. The system is in production for Australia, Qatar and Hungary. NASAMS is in use with both Armies and Air Forces around the world. In addi-tion Poland, Greece and Turkey operate the KONGSBERG Command and Control solution for various weapon systems.AN INTERNATIONAL SYSTEM12NASAMS User nations15Air Defence C2 user nationsKONGSBERG DEFENCE & AEROSPACE AS Kirkegaardsveien 45PO Box 1003N-3601 KongsbergNorway+47 32 28 82 00************************。
博斯自由空间模型32SE表面掩膜环境扬音器安装指南说明书
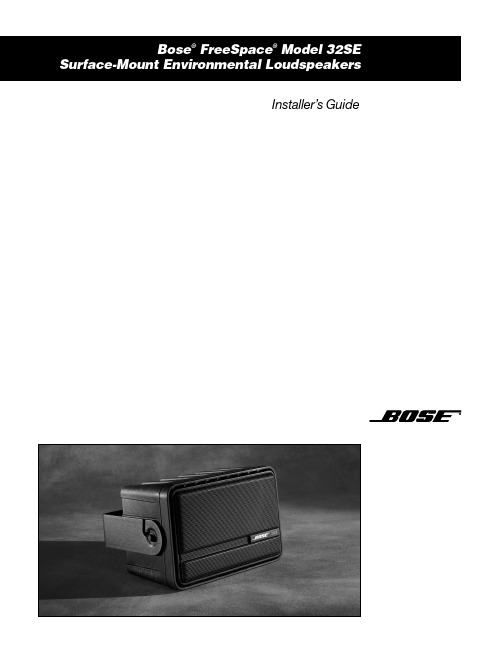
Installer’s GuideSafety reminders1.1Read and keep all safety and operating instructions for futurereference.1.2For your safety, follow all cautions and warnings in the operatinginstructions and on the speakers.1.3Follow the instructions in this guide carefully when installing thisproduct.1.4Do not install the loudspeakers near excessive heat sources.This includes installations near or above radiators, ranges, grills,fryers, stoves, or other appliances.1.5Always route cables so heavy or sharp objects cannot pinch orcut them.1.6Check local codes for use of safety cables. The loudspeakerhas threaded inserts and 1/4-20 screws (1/4-inch diameter with20 threads per inch, U.S. terminology) are provided forattaching the safety cables.1.7Service by a qualified service person if:A.The loudspeaker cone is visibly damaged;B.The loudspeakers do not operate normally even though theinstructions in this guide have been followed;C.The loudspeakers exhibit a distinct change in performance.Nic MerksVice President EuropeManufacturer’s authorized EU representative21.0Package contents2.0Steps for loudspeaker installationFor 70V and 100V versions of the Model 32SE loudspeakers,remove the rear cover.2.1Changing the tap on 70V and 100VversionsBoth the 70V and 100V versions are set at the factory to the maxi-mum of 32W. For lower output volume, change that setting to 16W,8W, 4W, 2W or 1W. To do that, remove the spade connector fromthe 32W spade and reinsert it into the preferred spade.34 2.2Connecting the wires This process varies according to the version of loudspeaker you are using.2.2.1T o the 4 ohm version Caution: Install the 4 ohm Model 32SE loudspeaker in compliance with local building and electrical codes. In the U.S., this version is designed for installation using Class 2 wiring methods in accordance with Articles 640 and 725 of NFPA 70, National Electrical Code.Guidelines for Class 2 wiring methods are usually appropriate for nonhazardous live circuits and wiring methods in many other coun-tries.2.2.2T o the 70V or 100V versions Caution: Install the loudspeakers in compliance with local building and electrical codes. In the U.S., this version is designed for installa-tion using Class 1, 2, or 3 wiring methods in accordance with Articles 640 and 725 of NFPA 70, National Electrical Code. Guide-lines for Class 2 wiring methods are usually appropriate for nonhaz-5EnglishOptional use of quick-connect terminals on 70V and 100V versionsReattach the cover to protect wire termination. Dress the wirescarefully to prevent the cover from pinching them.Alternative wire treatment•Simple wiring • Daisy chaining•Sealed rear housing*• Daisy-chaining and sealed rear*Use supplied liquid-tight**Dealer must supply additional fitting fitting. Or, if local codes allow it,route both wires through onefitting.6 2.3Mounting the bracket Choose a position and mounting method consistent with local building codes and regulations. Use two screws per bracket.• Wall-mount option • Ceiling-mount • Mounting footprint2.4Attaching and adjusting the speaker Partially insert the screws into the speaker.After adjusting the speaker angle, use a wrench to tighten themounting screws firmly, securing the bracket.6.9"3.0 Loudspeaker specificationsFrequency Range90Hz to 16kHz (±3 dB)Model 32SE VersionsActive Equalization• 70V (1W, 2W, 4W, 8W, 16W, 32W taps)• 100V (1W, 2W, 4W, 8W, 16W, 32W taps)Passive Equalization• 4Ω, 32W, no transformerSensitivityActive Equalization86dB-SPL @ 1W, 1m (pink noise)Passive Equalization86dB-SPL @ 1W, 1m (pink noise)Maximum Acoustic Output101dB-SPL @ 1m (pink noise)101dB-SPL @ 1m (IEC noise)Dispersion (-6dB point, average, 1-4kHz)132o conicalLong-T erm Power Handling32W continuousMechanical SpecificationsDimensions: 6"H x 9"W x 5.6"D (15.2 cmH x 22.9 cmW x14.1 cmD)Weight: 5 lb (2.3 kg)Connectors: 70V/100V, screw terminals; 4Ω hex-nut post terminalsMounting Hardware Included: Quick install U-bracket and hardwareAdditional Mounting Points: T wo (2) 1/4-20 inserts, 0.7" on bottom7Limited Warranty Bose® ProductWhat is covered:All parts defective in material and workmanship.For how long:Five years from the purchase date.What we will do:We will, at our sole option, repair or replace any defective parts free of charge. What we will not do:Pay shipping or transportation charges from you to us.What you must do:1.Return product personally with proof of purchase from an authorized Bosedealer to your authorized Bose dealer, or2.Return product personally with proof of purchase from an authorized Bosedealer to the nearest Bose Service Agency, or3.Return product personally with proof of purchase from an authorized Bosedealer directly to the Bose organization in your country. If you elect to returnthe product directly to a Bose organization,a)Contact the Bose organization in your country for specific return andshipping instructions;b)Properly pack the product in the original carton for shipping. If youneed a new carton, contact the Bose organization in your country for anew carton available at a nominal charge;c)Label and ship, freight prepaid, to the address provided by the Boseorganization in your country, andd)Place any necessary return authorization number prominently on theoutside of the carton. (Cartons not bearing a return authorizationnumber, where required, will be refused.)Other conditions:This warranty is fully transferable provided that the current owner furnishes the original proof-of-purchase from an authorized Bose dealer. The provisions of this warranty are in lieu of any other written warranty, whether express or implied, written or oral, including any warranty of merchantability or fitness for a particular purpose. Bose’s maximum liability shall not exceed the actual purchase price paid by you for the product. In no event shall Bose be liable for special, incidental, consequential or indirect damages. This warranty does not cover a defect that has resulted from improper or unreasonable use or maintenance, accident, improper packing, or unauthorized tampering, alteration or modification as determined solely by us. This warranty is void if the label bearing the serial number has been removed or defaced. Other law rights:This warranty gives you specific legal rights, and you may also have other rights which vary from country to country or state to state. Some places do not allow limitations on implied warranties or the exclusion or limitation of incidental or consequential damages, so the above limitations or exclusions may not apply to you.Please keep this warranty information for your personal records.Bose Corporation thanks you for your recent Bose product purchase. For your benefit, we recommend that you record your serial number(s), found on theproduct(s), and other purchase information below and keep it with your personal records along with proof-of-purchase. If necessary, this information will allow us to89©2000 Bose Corporation The Mountain Framingham, MA01701-9168 USA English。
- 1、下载文档前请自行甄别文档内容的完整性,平台不提供额外的编辑、内容补充、找答案等附加服务。
- 2、"仅部分预览"的文档,不可在线预览部分如存在完整性等问题,可反馈申请退款(可完整预览的文档不适用该条件!)。
- 3、如文档侵犯您的权益,请联系客服反馈,我们会尽快为您处理(人工客服工作时间:9:00-18:30)。
接口参数 通讯:以太网 数据速率:
10/100/1000Mbps 输入电压:11—36VDC 功耗:22W O/S:Windows 7 Pro, XP 环境适应性 工作温度:-2°-+38° 存放温度:-40°-+55°
物理参数 尺寸: 直径:185mm 长度:126mm 空气中重量:7kg 水中重量:3.9kg 耐压:4000m 接口品牌:Impulse 接口型号:
电站(eIQ 模式)
提供水平大角度视野,能实现实 时动态目标物的跟踪
垂向波束角可调,更加适应障碍 物的避碰
突堤转角
桥梁的剖面图
通用性 M3 的软件没有繁琐的参数
设置,用户可以根据不同的 应用选择相应的模式。M3 水 平视野高达 120°,探测距 离达到 100m。垂直波束角可 以在 30°的范围内根据具 体应用而调节。
视野 eIQ 模式 140°水平
视野 耐压 4000m
声纳参数 量程:0.2—100m 距离分辨率:1cm 频率:500kHz 带宽:100kHz 脉冲类型:CW,LFM 模式:导航模式/eIQ 导航模式 水平视野:120° 垂直视野:3°—30° 波束数:256 方位分辨率:1.8° 更新率:40Hz eIQ 模式(图像增强模式) 水平视野:140° 垂直视野:30° 波束数:216 方位分辨率:0.8° 更新率:10Hz
MSSJ-10-FCR 材料 钛合金 316 不锈钢 氨纶
上海地海仪器有限公司
电话:021-54970635/6/7
传真:021-54970091
地址:上海市徐汇区漕溪路 251 弄望族城 5 号楼 601C
网址:
地海科技有限公司(香港) 电话:(852)-26352127 传真:(852)-26351672 地址:香港沙田安心街 19 号汇贸中心 10 楼 19 室 E-Mail: janson@
应用 ROV 导航 水下监测 水下检测
ቤተ መጻሕፍቲ ባይዱ
安装 紧凑的声纳头可以非
常方便的集成到绝大多数 ROV 上(从工作级到观察级 ROV)
使用标准的以太网数 数据传输。
优势 视野广阔 轻巧方便 多功能 实时成像
特征 0.2—100m 量程 厘米级分辨率 单个波束 0.8° 导航模式 120°水平
M3 ROV 成像声纳—4000m 耐压
概述 Kongsberg Mesotech Ltd. M3 是多功能的多波束成像声纳。 M3 提供高分辨率及易于分辨的 影像。能探测 100 米以外的小型 目标物,水平视野 120°,使得 操作员可以实时看到水下情况。
具备更快的成像速度并且接近单 波束声纳的成像质量