advanced IC_Packaging_technology_overview
英语作文-集成电路设计行业的最新技术与应用案例分享

英语作文-集成电路设计行业的最新技术与应用案例分享In recent years, the field of integrated circuit (IC) design has witnessed remarkable advancements driven by cutting-edge technologies and innovative applications. This rapid evolution is not only shaping the future of electronics but also revolutionizing various industries reliant on semiconductor devices. In this article, we explore some of the latest trends and case studies that highlight the transformative impact of these advancements.One of the key areas experiencing significant breakthroughs is the development of System-on-Chip (SoC) designs. SoC integrates multiple functionalities previously handled by separate ICs into a single chip, enhancing efficiency, reducing power consumption, and minimizing physical footprint. This consolidation is pivotal in mobile devices, IoT applications, and automotive electronics, where compactness and energy efficiency are critical.Moreover, the rise of artificial intelligence (AI) and machine learning (ML) has spurred demand for specialized ICs optimized for neural network computations. Graphics Processing Units (GPUs) and Tensor Processing Units (TPUs) are prime examples of ICs tailored to accelerate complex AI algorithms, enabling advancements in autonomous vehicles, natural language processing, and computer vision.In parallel, the evolution of semiconductor manufacturing processes has been instrumental. The transition to smaller nodes, such as 7nm and beyond, enhances transistor density and performance while reducing power consumption. This trend not only supports the development of faster and more energy-efficient ICs but also enables the integration of advanced features like high-speed interfaces, secure hardware enclaves, and advanced signal processing capabilities.Furthermore, the proliferation of 5G technology has catalyzed innovations in RF (Radio Frequency) IC design. ICs capable of handling high-frequency signals withminimal latency are crucial for 5G infrastructure and mobile devices. These advancements are pivotal in enabling faster data rates, lower latency, and robust connectivity, thereby facilitating the widespread adoption of 5G across various sectors including telecommunications, healthcare, and smart cities.Another noteworthy trend is the growing emphasis on security in IC design. With the increasing connectivity of devices and the rise of cyber threats, there is a critical need for ICs that incorporate robust security features. Hardware-based security solutions such as Trusted Execution Environments (TEEs) and secure boot mechanisms are becoming standard in modern IC designs to safeguard sensitive data and protect against malicious attacks.Moreover, the convergence of IC design with advanced packaging technologies is opening new avenues for innovation. 3D IC integration and heterogeneous integration techniques enable the stacking of multiple IC layers or diverse technologies within a single package. This approach enhances performance, reduces interconnect lengths, and addresses thermal management challenges, thereby advancing the capabilities of ICs in high-performance computing, data centers, and edge computing applications.In conclusion, the field of integrated circuit design continues to evolve rapidly, driven by technological advancements and diverse applications. From SoC designs and AI-optimized ICs to advanced manufacturing processes and secure IoT solutions, each innovation contributes to pushing the boundaries of what is possible in electronics and beyond. As these trends unfold, they promise to reshape industries, enhance user experiences, and pave the way for a more connected and intelligent future.。
先进封装技术 advanced packaging technology-概述说明以及解释
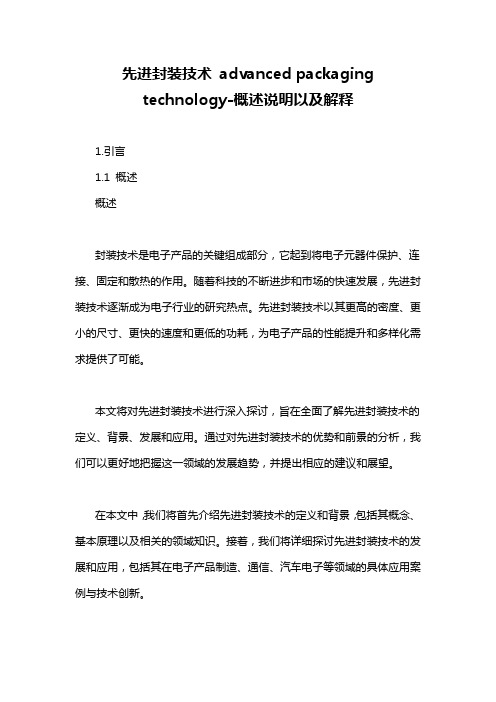
先进封装技术advanced packagingtechnology-概述说明以及解释1.引言1.1 概述概述封装技术是电子产品的关键组成部分,它起到将电子元器件保护、连接、固定和散热的作用。
随着科技的不断进步和市场的快速发展,先进封装技术逐渐成为电子行业的研究热点。
先进封装技术以其更高的密度、更小的尺寸、更快的速度和更低的功耗,为电子产品的性能提升和多样化需求提供了可能。
本文将对先进封装技术进行深入探讨,旨在全面了解先进封装技术的定义、背景、发展和应用。
通过对先进封装技术的优势和前景的分析,我们可以更好地把握这一领域的发展趋势,并提出相应的建议和展望。
在本文中,我们将首先介绍先进封装技术的定义和背景,包括其概念、基本原理以及相关的领域知识。
接着,我们将详细探讨先进封装技术的发展和应用,包括其在电子产品制造、通信、汽车电子等领域的具体应用案例与技术创新。
最后,我们将总结先进封装技术的优势和前景,并对其未来的发展进行展望。
通过本文的阐述,我们希望读者能够对先进封装技术有更深入的了解,并在相关领域的实践中能够运用到相关的知识和技术。
希望本文能够为读者提供有价值的信息,促进先进封装技术的快速发展和应用。
1.2 文章结构本文主要围绕先进封装技术展开,通过以下几个部分进行论述和分析。
首先,在引言部分我们将进行一系列的说明和介绍。
我们将从概述、文章结构和目的三个方面着手。
在概述中,我们将对先进封装技术进行简要的介绍和概括,为读者提供一个整体的了解。
在文章结构部分,我们将具体说明本文的组织结构,明确各个部分的内容和目的,使读者对整篇文章的逻辑有个清晰的认识。
在目的方面,我们将明确本文的目标和意义,阐述为什么研究和应用先进封装技术是重要的,以引起读者的兴趣和关注。
接下来,在正文部分我们将对先进封装技术进行更加深入的研究和探讨。
2.1节将着重阐述先进封装技术的定义和背景。
我们将解释先进封装技术的概念,并介绍其相关的背景知识,包括其发展历程和相关的研究领域。
英语作文-集成电路设计的发展趋势与应用领域解析

英语作文-集成电路设计的发展趋势与应用领域解析The Development Trends and Application Fields Analysis of Integrated Circuit Design。
Integrated circuit (IC) design has been experiencing rapid evolution, driven by technological advancements and the increasing demand for high-performance electronic devices across various industries. This article explores the current trends in IC design development and its applications.Firstly, the miniaturization of electronic components has been a significant trend in IC design. With the continuous advancement of semiconductor manufacturing processes, the size of transistors and other components on ICs has been shrinking, leading to the development of smaller and more power-efficient chips. This trend enables the integration of complex functionalities into a single chip, contributing to the development of compact and portable electronic devices such as smartphones, tablets, and wearable gadgets.Moreover, the growing demand for high-speed data processing and transmission has led to the emergence of advanced IC design techniques. For instance, the adoption of advanced packaging technologies such as system-on-chip (SoC) and system-in-package (SiP) allows for the integration of multiple functions and subsystems onto a single chip or package. This integration enhances the overall performance and efficiency of electronic systems, making them suitable for applications in telecommunications, networking, and data centers.Additionally, the increasing focus on energy efficiency and environmental sustainability has influenced IC design trends. Designers are incorporating power-saving features and optimizing circuit architectures to reduce energy consumption and heat dissipation in electronic devices. This trend is particularly important in the developmentof battery-powered devices and energy-efficient systems for IoT (Internet of Things) applications, where extended battery life and minimal environmental impact are critical considerations.Furthermore, the rise of artificial intelligence (AI) and machine learning (ML) technologies has reshaped the landscape of IC design. There is a growing demand for specialized ICs optimized for AI/ML workloads, such as neural network accelerators and inference engines. These specialized chips enable faster and more efficient execution of AI algorithms, facilitating the deployment of intelligent systems in various domains, including autonomous vehicles, robotics, healthcare, and cybersecurity.In conclusion, the field of integrated circuit design is experiencing continuous innovation and evolution, driven by advancements in technology and changing market demands. The trends discussed above highlight the ongoing efforts to develop smaller, faster, and more energy-efficient ICs for a wide range of applications. As technology continues to advance, we can expect further breakthroughs in IC design, enabling new capabilities and functionalities in electronic devices and systems.。
先进封装 名词

先进封装名词先进封装(Advanced Packaging)是一种半导体封装技术,用于将芯片或集成电路(IC)封装在一个外壳中,以提供保护、连接和散热等功能。
它是半导体制造过程中的关键环节之一,对于提高芯片性能、降低成本和实现小型化至关重要。
先进封装技术的发展是为了满足不断增长的芯片集成度和性能要求。
随着半导体工艺技术的演进,芯片的尺寸越来越小,引脚数量越来越多,同时对功耗、速度和可靠性的要求也越来越高。
传统的封装技术已经难以满足这些需求,因此需要采用更先进的封装技术。
先进封装技术包括以下几种主要类型:1. 系统级封装(System-in-Package,SiP):将多个芯片和其他组件集成在一个封装中,形成一个完整的系统。
这种封装方式可以减小尺寸、降低功耗并提高系统性能。
2. 晶圆级封装(Wafer-Level Packaging):在晶圆制造过程中进行封装,将芯片直接封装在晶圆上,而不是在单个芯片上进行封装。
这种方法可以提高生产效率和降低成本。
3. 三维封装(3D Packaging):采用多层堆叠技术,将芯片垂直堆叠在一起,以实现更高的集成度和性能。
这种封装方式可以减小芯片尺寸并提高信号传输速度。
4. 倒装芯片封装(Flip-Chip Packaging):将芯片的有源面朝下,通过焊点直接连接到封装基板上。
这种封装方式可以提供更好的散热性能和更短的电路路径。
先进封装技术的发展推动了半导体行业的进步,使得芯片在更小的尺寸、更高的性能和更低的成本下实现更复杂的功能。
它对于手机、平板电脑、计算机、通信设备等各种电子产品的发展至关重要。
随着技术的不断创新,先进封装将继续在半导体领域发挥重要作用。
英语作文-集成电路设计行业中的行业热点与前沿技术
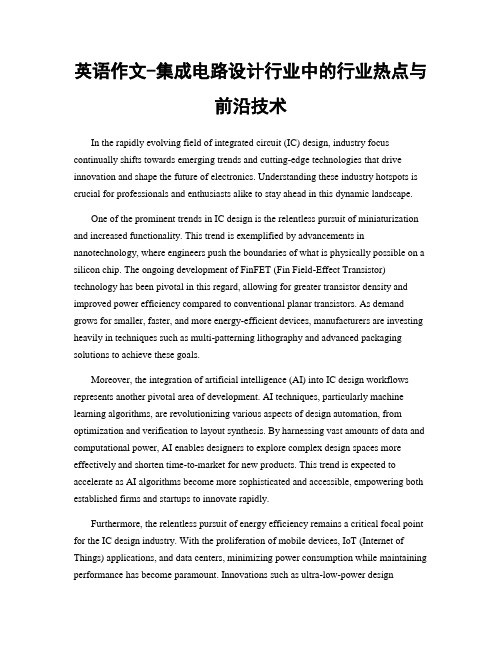
英语作文-集成电路设计行业中的行业热点与前沿技术In the rapidly evolving field of integrated circuit (IC) design, industry focus continually shifts towards emerging trends and cutting-edge technologies that drive innovation and shape the future of electronics. Understanding these industry hotspots is crucial for professionals and enthusiasts alike to stay ahead in this dynamic landscape.One of the prominent trends in IC design is the relentless pursuit of miniaturization and increased functionality. This trend is exemplified by advancements in nanotechnology, where engineers push the boundaries of what is physically possible on a silicon chip. The ongoing development of FinFET (Fin Field-Effect Transistor) technology has been pivotal in this regard, allowing for greater transistor density and improved power efficiency compared to conventional planar transistors. As demand grows for smaller, faster, and more energy-efficient devices, manufacturers are investing heavily in techniques such as multi-patterning lithography and advanced packaging solutions to achieve these goals.Moreover, the integration of artificial intelligence (AI) into IC design workflows represents another pivotal area of development. AI techniques, particularly machine learning algorithms, are revolutionizing various aspects of design automation, from optimization and verification to layout synthesis. By harnessing vast amounts of data and computational power, AI enables designers to explore complex design spaces more effectively and shorten time-to-market for new products. This trend is expected to accelerate as AI algorithms become more sophisticated and accessible, empowering both established firms and startups to innovate rapidly.Furthermore, the relentless pursuit of energy efficiency remains a critical focal point for the IC design industry. With the proliferation of mobile devices, IoT (Internet of Things) applications, and data centers, minimizing power consumption while maintaining performance has become paramount. Innovations such as ultra-low-power designtechniques, adaptive voltage scaling, and on-chip power management units are instrumental in meeting these challenges. Additionally, emerging technologies like silicon photonics offer promising avenues for reducing power consumption in high-speed interconnects, paving the way for future generations of energy-efficient computing systems.In parallel, the industry is witnessing significant advancements in specialized IC design for niche applications. Fields such as biomedical electronics, automotive electronics, and quantum computing demand tailored solutions that go beyond traditional CMOS (Complementary Metal-Oxide-Semiconductor) technologies. These specialized ICs often require stringent reliability, low noise, and high sensitivity, prompting innovations in materials, device architectures, and fabrication techniques. As these sectors expand, they drive cross-disciplinary collaborations and inspire novel approaches to IC design that cater to specific application requirements.Looking ahead, the convergence of these trends underscores a transformative era in IC design, characterized by unprecedented levels of integration, intelligence, and efficiency. As researchers and engineers continue to push boundaries, the industry's landscape will continue to evolve, fueled by innovations that redefine what is possible with semiconductor technology. Embracing these advancements and anticipating future developments will be essential for stakeholders seeking to navigate and capitalize on the opportunities presented by the dynamic field of integrated circuit design.。
英语作文-集成电路设计行业的智能化与数字化转型趋势

英语作文-集成电路设计行业的智能化与数字化转型趋势The semiconductor industry has been witnessing a remarkable transformation driven by the trends of intelligence and digitization. In particular, the field of integrated circuit (IC) design is experiencing a profound shift towards greater automation, intelligence, and digitalization. This transformation is not only reshaping the way ICs are designed but also revolutionizing the entire semiconductor ecosystem.One of the key drivers behind the trend of intelligence in IC design is the growing complexity of modern semiconductor devices. As technology nodes shrink and functionalities increase, traditional design methodologies are becoming inadequate to handle the intricacies involved. In response, design automation tools powered by artificial intelligence (AI) and machine learning (ML) algorithms are being increasingly deployed to streamline the design process. These tools can analyze vast amounts of data, identify patterns, and generate optimized designs with minimal human intervention. By leveraging AI and ML, designers can significantly reduce time-to-market and improve the overall quality and performance of ICs.Moreover, the digitization of IC design workflows is enabling greater collaboration and efficiency across the semiconductor industry. Cloud-based design platforms are becoming more prevalent, allowing geographically dispersed teams to collaborate seamlessly on design projects. This digital transformation also extends to simulation and verification, where advanced simulation tools and methodologies are being adopted to ensure the robustness and reliability of IC designs. Virtual prototyping, for instance, enables designers to simulate the behavior of complex ICs under various operating conditions, thereby reducing the need for physical prototypes and accelerating time-to-market.Furthermore, the integration of advanced manufacturing technologies such as 3D stacking and advanced packaging is driving the digitization of IC design. Thesetechnologies enable the integration of heterogeneous components within a single package, offering higher performance and greater energy efficiency. However, designing such complex systems requires sophisticated design tools capable of addressing multi-domain challenges, including thermal management, signal integrity, and power delivery. Digital twin technology, which creates a virtual replica of the physical system, is proving to be instrumental in optimizing the design of these integrated systems.In addition to enhancing design efficiency and productivity, the trend towards intelligence and digitization in IC design is also enabling new opportunities for innovation. For instance, the rise of edge computing and Internet of Things (IoT) devices is driving demand for ultra-low-power and high-performance ICs tailored for specific applications. Designers are leveraging AI-driven optimization techniques to design energy-efficient circuits capable of meeting stringent performance requirements. Similarly, the emergence of neuromorphic computing and quantum computing is pushing the boundaries of traditional IC design, necessitating new design methodologies and tools.In conclusion, the integration of intelligence and digitization is reshaping the landscape of IC design, driving greater efficiency, collaboration, and innovation. As the semiconductor industry continues to evolve, embracing these trends will be crucial for staying competitive in a rapidly changing market landscape. By leveraging advanced technologies and methodologies, IC designers can unlock new possibilities and accelerate the pace of innovation in semiconductor design.。
先进芯片封装知识介绍
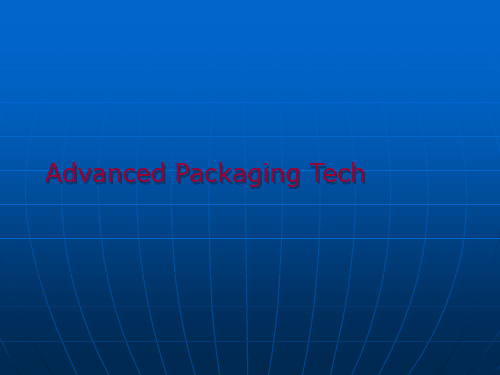
Bump
Bump Development
Bump Development
Bump Development
WLCSP
Process Flow of WLCSP
WLCSP
▼ Process Flow of WLCSP
Flip Chip Package
(PI)-EHS2-FCBGA
(Passive Integrated Exposed 2 pieces of Heat Sink Flip Chip BGA)
In some new 3D packages, through-silicon via replace edge wiring by creating vertical connections through the body of the chips. The resulting package has no added length or thickness.
In most 3D packages, the stacked chips are wired together along their edges. This edge wiring slightly increases the length and width of the package and usually requires an extra “interposer” layer between the chips.
▼ PoP Core Technology
Low Loop Wire
PoP
Pin Gate Mold
电子封装技术发展现状及趋势

电子封装技术发展现状及趋势龙乐【摘要】The current IC wafer ling width characteristics is micronanoelectronic scale. The microminiaturization process of electronic products and electronic systems will depend on the advanced packaging technology .It has increasingly become a focus of the semiconductor industry. Novel packaging technology with larger market value around home and abroad in recent years are introduced. Basic structures and fabrication processes of some typical packaging are bescribed in detail. Furthermore, it is pointed out current status and development trend of packaging technology.In the recent years, endless varieties of packagings are proposed. It implements a new and higher level of packaging integration with higher assemble density, more strong features, better performance, smalles size, lower power consumption, faster speed, smaller delay, cost reduction,etc. Researches and process of packaging cannot be ignored. It has a great market potential and development in the days to come. Advanced packaging technology are forcing semiconductor industry access the More-than-Moore era .%现今集成电路晶圆的特征线宽进入微纳电子时代,而电子产品和电子系统的微小型化依赖先进电子封装技术的进步,封装技术已成为半导体行业关注的焦点之一。
ADVANCED PACKAGING
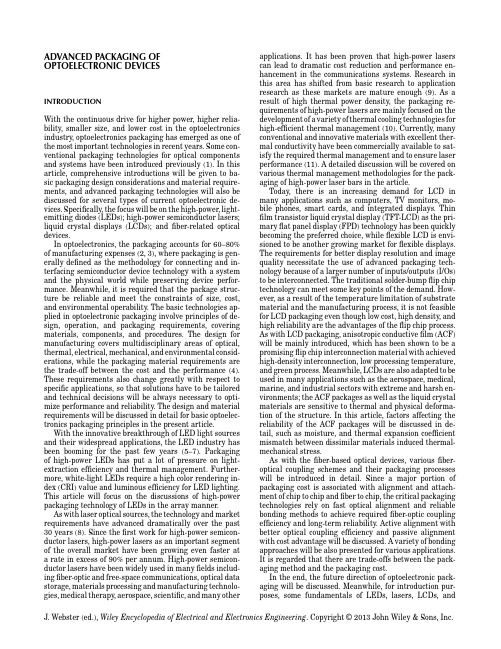
ADVANCED PACKAGING OF OPTOELECTRONIC DEVICESINTRODUCTIONWith the continuous drive for higher power,higher relia-bility,smaller size,and lower cost in the optoelectronics industry,optoelectronics packaging has emerged as one of the most important technologies in recent years.Some con-ventional packaging technologies for optical components and systems have been introduced previously(1).In this article,comprehensive introductions will be given to ba-sic packaging design considerations and material require-ments,and advanced packaging technologies will also be discussed for several types of current optoelectronic de-vices.Specifically,the focus will be on the high-power,light-emitting diodes(LEDs);high-power semiconductor lasers; liquid crystal displays(LCDs);andfiber-related optical devices.In optoelectronics,the packaging accounts for60–80% of manufacturing expenses(2,3),where packaging is gen-erally defined as the methodology for connecting and in-terfacing semiconductor device technology with a system and the physical world while preserving device perfor-mance.Meanwhile,it is required that the package struc-ture be reliable and meet the constraints of size,cost, and environmental operability.The basic technologies ap-plied in optoelectronic packaging involve principles of de-sign,operation,and packaging requirements,covering materials,components,and procedures.The design for manufacturing covers multidisciplinary areas of optical, thermal,electrical,mechanical,and environmental consid-erations,while the packaging material requirements are the trade-off between the cost and the performance(4). These requirements also change greatly with respect to specific applications,so that solutions have to be tailored and technical decisions will be always necessary to opti-mize performance and reliability.The design and material requirements will be discussed in detail for basic optoelec-tronics packaging principles in the present article.With the innovative breakthrough of LED light sources and their widespread applications,the LED industry has been booming for the past few years(5–7).Packaging of high-power LEDs has put a lot of pressure on light-extraction efficiency and thermal management.Further-more,white-light LEDs require a high color rendering in-dex(CRI)value and luminous efficiency for LED lighting. This article will focus on the discussions of high-power packaging technology of LEDs in the array manner.As with laser optical sources,the technology and market requirements have advanced dramatically over the past 30years(8).Since thefirst work for high-power semicon-ductor lasers,high-power lasers as an important segment of the overall market have been growing even faster at a rate in excess of90%per annum.High-power semicon-ductor lasers have been widely used in manyfields includ-ingfiber-optic and free-space communications,optical data storage,materials processing and manufacturing technolo-gies,medical therapy,aerospace,scientific,and many other applications.It has been proven that high-power lasers can lead to dramatic cost reduction and performance en-hancement in the communications systems.Research in this area has shifted from basic research to application research as these markets are mature enough(9).As a result of high thermal power density,the packaging re-quirements of high-power lasers are mainly focused on the development of a variety of thermal cooling technologies for high-efficient thermal management(10).Currently,many conventional and innovative materials with excellent ther-mal conductivity have been commercially available to sat-isfy the required thermal management and to ensure laser performance(11).A detailed discussion will be covered on various thermal management methodologies for the pack-aging of high-power laser bars in the article.Today,there is an increasing demand for LCD in many applications such as computers,TV monitors,mo-bile phones,smart cards,and integrated displays.Thin film transistor liquid crystal display(TFT-LCD)as the pri-maryflat panel display(FPD)technology has been quickly becoming the preferred choice,whileflexible LCD is envi-sioned to be another growing market forflexible displays. The requirements for better display resolution and image quality necessitate the use of advanced packaging tech-nology because of a larger number of inputs/outputs(I/Os) to be interconnected.The traditional solder-bumpflip chip technology can meet some key points of the demand.How-ever,as a result of the temperature limitation of substrate material and the manufacturing process,it is not feasible for LCD packaging even though low cost,high density,and high reliability are the advantages of theflip chip process. As with LCD packaging,anisotropic conductivefilm(ACF) will be mainly introduced,which has been shown to be a promisingflip chip interconnection material with achieved high-density interconnection,low processing temperature, and green process.Meanwhile,LCDs are also adapted to be used in many applications such as the aerospace,medical, marine,and industrial sectors with extreme and harsh en-vironments;the ACF packages as well as the liquid crystal materials are sensitive to thermal and physical deforma-tion of the structure.In this article,factors affecting the reliability of the ACF packages will be discussed in de-tail,such as moisture,and thermal expansion coefficient mismatch between dissimilar materials induced thermal-mechanical stress.As with thefiber-based optical devices,variousfiber-optical coupling schemes and their packaging processes will be introduced in detail.Since a major portion of packaging cost is associated with alignment and attach-ment of chip to chip andfiber to chip,the critical packaging technologies rely on fast optical alignment and reliable bonding methods to achieve requiredfiber-optic coupling efficiency and long-term reliability.Active alignment with better optical coupling efficiency and passive alignment with cost advantage will be discussed.A variety of bonding approaches will be also presented for various applications. It is regarded that there are trade-offs between the pack-aging method and the packaging cost.In the end,the future direction of optoelectronic pack-aging will be discussed.Meanwhile,for introduction pur-poses,some fundamentals of LEDs,lasers,LCDs,andJ.Webster(ed.),Wiley Encyclopedia of Electrical and Electronics Engineering.Copyright©2013John Wiley&Sons,Inc.2Advanced Packaging of Optoelectronic Devicesfiber-optic modules will be presented.Further details of optoelectronic device physics,optical sources,and common package platforms can be easily searched through the In-ternet,textbooks,and the literature.Interested readers are referred to some of these good literature to gain a more comprehensive understanding of optoelectronic technolo-gies for optoelectronic components and systems(12–15). PACKAGING DESIGNA major trend in optoelectronics packaging is for smaller, more efficient,and more cost-effective package designs that improve device manufacturability and reliability (16,17).For improved reliability,the packaging designer must consider the electrical,optical,mechanical,and ther-mal behavior of the package materials set under two sepa-rate temperature regimes:module assembly and in service. Additionally,the designer must understand the packaging design trade-offs that are required to meet customer cost and reliability needs.The designer must design a product that can be successfully manufactured while meeting cus-tomers’reliability requirements at a reasonable cost. Principle of PackagingPackaging in principle is a sequence of technologies that involve connecting,protecting,and manufacturing of de-vices to enable and maintain the device performance in use. Optoelectronics packaging is targeting the devices with optical and electrical characteristics.Its contents mainly involve the package design,materials selection,process development,and manufacturing,where the package de-signers need to consider a variety of optical,thermal,elec-trical,mechanical,and application environmental factors for manufacturability and reliability.Optical ConsiderationsThe wavelengths from optical sources of optoelectronic de-vices can vary largely ranging from a deep ultraviolet regime(200nm)to a far-infrared regime depending on the operation of devices.The spectrum can be generated in a single wavelength dominated by lasers or in a wide dis-tribution of multiwavelengths such as the white light of LEDs.One main task of optoelectronic packaging is to pro-vide the devices with optical interconnections between the chip and thefiber or to extract optical power from the chip to the desired position efficiently(18).It is necessary that a high chip-to-fiber coupling efficiency be realized to ensure that a sufficiently strong and effective optical signal is in-put into or output from the optoelectronic devices.Wave optics and ray optics modeling approaches are widely used for light transmission during optical design depending on the device geometrical dimensions(19).The optical design considerations in packaging mainly are trying to reach the goal of maximization of optical power transfer or output and minimization of reflection or coupling-induced optical loss(20).No matter what kind of optical coupling scheme is designed,optical packaging designers need to con-sider its manufacturability,which involves the sequential packaging process choice for the pick-and-place of each single part,the alignment and attachment steps among all parts,and the chip-to-waveguide optical power trans-fer efficiency.Obtaining a high coupling efficiency is also a difficult process and accounts for a big portion of pack-aging cost.Currently,coupling processes utilize both the active and passive alignment techniques.The active align-ment process can be performed under the operating con-ditions,while the passive alignment process is to be re-alized through a high tolerance of optical design mis-alignment.A typical passive alignment design of chip-to-fiber is the utilization of a silicon bench,where the fiber is placed in the V-groove of the silicon bench pre-cisely fabricated by the well-developed silicon anisotropic wet etching technique(21).It is also reported that a cost-effective optical PC board made of molded,poly-meric material with submicron mechanicalfiduciaries can enable passive,pick-and-place coupling of diverse op-tical components and single-modefibers with a small footprint(22).The active alignment method generally requires a long alignment time,even though an automated alignment pro-cess can be adopted to speed up the process.The active pro-cess can move the part to the optimal aligning position for required coupling efficiency,although it is not suitable for batch processes,and the cost is high because extra equip-ment and process time are required.On the other hand,the passive alignment process is suitable for batch processes with much reduced alignment time,and it is applicable to multiport chip-to-fiber array coupling(23,24).However, the coupling efficiency relies a lot on the design of optical coupling scheme tolerance(25).Another optical consideration in packaging is the post-attachment induced bonding shift,which can lead to the severe coupling loss.This issue can be overcome through proper bonding material and bonding process selection, which will be discussed in the following material require-ment section.Thermal ConsiderationsHeat dissipation,thermal stresses,and cost are key packaging design issues for virtually all optoelectronic de-vices,such as lasers,LEDs,photovoltaics,displays,pro-jectors,detectors,and sensors.Heat dissipation and ther-mal stresses affect both performance and reliability.In thermal considerations,one must consider the application and operation of the optoelectronic modules and devices when designing the package.Two types of device operat-ing modes can be identified:a)components and systems that are required to be reliable over multiple thermal cy-cles(on/off)and b)devices and systems that require highly efficient thermal dissipation to maintain a constant,uni-form,low-temperature value.For components and systems that are required to thermal cycle,the package material needs to have a high thermal conductivity value for effec-tive heat dissipation and a material coefficient-of-thermal-expansion(CTE)value that is compatible with that of the functional device to reduce mechanical stresses during op-eration.When the CTE values of package and device are compatible,stress compensation layers can be reduced in number or eliminated,thereby decreasing the assemblyAdvanced Packaging of Optoelectronic Devices3thermal resistance,enhancing device heat dissipation ca-pability,and improving assembly and operation reliabil-ity.Thermal mechanical stress analysis can be used to evaluate the design feasibility through standard modeling approaches(26).Traditional solutions to the combination of both require-ments for high thermal conductivity and compatible mate-rial CTE property have included the application of thermal stress compensation layers between the active component and the package material,where a very typical example is the utilization of an alumina substrate.However,these stress compensation layers usually have low thermal con-ductivity values and lead to increasing the thermal resis-tance of the assembly,which decreases the heat dissipation capability for the module or device.For example,copper has a high thermal conductivity for rapid heat dissipation; yet the CTE value(17ppm/◦C)is not compatible with ac-tive device materials such as silicon(4ppm/◦C)and gal-lium arsenide(7ppm/◦C).Therefore,the stress compensa-tion layers are necessary.In the end,using high thermal conductivity copper may not provide the thermal dissipa-tion performance required to meet overall design objectives as a result of introduced compensation layers.High-power devices impose more stringent require-ments on the thermal design considerations in optoelec-tronic packaging,which have triggered many thermal management solutions available to current high-power de-vices.For example,various specialized cooling methods are widely used in high-power laser packaging and high-power LED packaging.Furthermore,thermal management prob-lems are not unique to optical-related devices,and they are critical in many microelectronic devices,such as high-speed microprocessors.Interested readers may also refer to some good reviews for thermal management in microelec-tronics packaging.As the thermal behavior of the package is very dependent on the applied materials,more detailed discussions will be covered in the materials requirement section as followed in the later section.Electrical ConsiderationsOne main task of optoelectronic packaging is to provide the devices with electrical interconnections between the chip and the outer circuit to minimize the electro and elec-tromagnetic interference from each other and the outside (27).It is necessary that electrical interconnects ensure the effective electrical signals being input into or output from the optoelectronic devices.With the increasing de-mand for large-capacity and long-haul transmission in op-tical communication,optoelectronic devices and modules are continually developing toward higher speed besides the small size and low cost.For high-frequency optoelectronic devices,packaging has become the decisive factor in the final performance and cost effectiveness of the modules.To realize the high-speed operation of a device or module,a low-loss microwave driving circuit must be provided,in-cluding a microstrip,a coplanar waveguide(CPW),and other microwave components.A silicon bench that inte-grates a precise V-groove with the microwave circuit on the same silicon substrate will be an effective solution for op-toelectronic packaging,where the V-groove can be used for passive alignment of opticalfiber.At the same time,silicon substrate is a good thermal conductor for heat dissipation, and a microwave CPW integrated in a silicon bench can realize low microwave loss for the high-speed driving cir-cuit(28).For the electric design considerations in optoelec-tronic packaging,it is important to keep in mind that sig-nal lines are more sensitive to electrical disruption(such as noise,cross-talk,and leakage)than power or ground lines, where power and ground lines can be used to shield signal lines electrically(29).Interested readers may refer to some of the many good treatments outlined in the literature fo-cused on electronic packaging.Mechanical and Environmental ConsiderationsBesides thermal considerations,mechanical design will de-termine the performance and reliability of a package dur-ing testing and during exposure to its service environment (30).It is important to consider thermally induced me-chanical stresses from materials with different thermal expansion behaviors during the assembly operations such as brazing,soldering,welding,and epoxy joining.These thermally induced mechanical stresses increase the failure probability of the device as well as the failure probability of the package assembly that provides environmental protec-tion for the module.By choosing materials that have com-patible CTE,mechanical stresses are reduced and overall module reliability is improved.Environmental considerations mainly refer to the harsh environmental conditions such as high temperature,mois-turized,or erosional atmosphere.In these cases,the pack-age may require strong thermal-resistive and hematic packaging protection,which further put pressure on the materials selection,vacuum or hematic packaging process development,and thermo-mechanical stress tolerance. PACKAGING MATERIAL REQUIREMENTSPackaging materials selection has to meet the require-ments of packaging designs on the one hand,where overall optical,thermal,electrical,mechanical,and environmen-tal considerations set up designing criteria;on the other hand,the packaging process is defined once the materi-als are selected.There are also many potential payoffs for the optimal materials selection,such as higher power lev-els,reduced number of required devices,reduced thermal stresses and warpage,increased reliability,improved effi-ciency of alignment and performance,weight and size re-ductions,increased manufacturing yield,and cost reduc-tions.Therefore,packaging materials selection and their optimal combination is much more complex for engineers. In this discussion,the fundamentals of materials require-ments and a wide range of packaging materials such as polymer,metals,alloys,ceramics,and composites are pre-sented to illustrate the basic packaging principles in terms of their applications for optical,attachment,thermal man-agement,substrate,housing,and encapsulating functions. The status of advanced packaging material development is also presented for the packaging trend of ever growing high-power and high-reliability optoelectronics.4Advanced Packaging of Optoelectronic DevicesOptical MaterialsOptical grade epoxies can be described as clear,colorless, nonyellowing encapsulants,which are used in the packag-ing and assembly offiber optics,LEDs,and LCDs.A cur-rent trend in high brightness(HB)LED packaging mate-rials is the shift from organic polymers to silicones,which is in accordance with future packaging requirements(31). Silicone-based materials have attracted considerable at-tention from LED manufacturers for use as encapsulants and lenses for many next-generation LED device designs.A key factor for the preference of silicone materials over or-ganics in HB-LEDs is the stable thermo-optical property of silicones as compared with organic materials such as epoxy. Silicones are very stable when exposed to ultraviolet(UV) and blue light,even at high light intensities,high humid-ity,and high temperatures.On the other hand,organics are prone to yellowing when exposed to high thermalflux par-tially as a result of the heat generated within the system. This leads to photothermal-oxidative degradation of epox-ies,resulting in a decreased optical transmission.Surface mount technology(SMT)is another factor driving the use of silicones in LED packaging.Assembly of LEDs through SMT also requires that all the packaging materials are op-tically and mechanically stable after exposure to solder re-flow temperature of around260◦C,for short periods of time. Silicones can function in several roles that include protec-tive lenses,stress-relieving encapsulants,mechanical pro-tection,and light path materials.The key attributes of sil-icones that make them attractive materials for HB LEDs include their high transparency in the UV-visible region, controlled refractive index(RI),stable thermo-mechanical properties,and tunable hardness from soft gels to hard resins.Attachment MaterialsAs the last step in the packaging and assembly process, the primary function of attachment is tofixate a more or less precisely aligned position of an optical or nonoptical component within a device or system.Attachment can gen-erally be divided into the three branches,namely,form-fit, force-fit and material-fit,and material-fit can be further divided into intermediate bonding(with adhesive,solder, and composites)and direct bonding(direct interface acti-vation treatment or laser fusion).Although form-fit and force-fit usually serve for a mechanicalfixation of the com-ponent,a material-fit joint offers more possibilities to inte-grate functionality by choosing the proper joining media or bonding process.In the case of polymeric adhesives,they can be formulated to be precise index matching or highly transparent at a relatively lower temperature,sometimes also electrically and thermally conducting.Metallic bond-ing materials(such as solder alloys)enable the conduc-tion of thermal and electrical energy at a relatively higher temperature.Conductive composite adhesives,where elec-trical conductive particles were added in polymeric adhe-sive,offer joining as well as the electrical interconnecting functions.However,any intermediate joining media may lead to failure of the joint absorbing energy in high-power applications as a result of thermal mechanical mismatch. In contrast,direct bonding in its various forms(plasma assisted and laser splicing/welding)can overcome this dis-advantage,but often it requires sophisticated alignment and bonding equipment for specific joining components. Through special process development,laser-based join-ing is under these circumstances the mostflexible joining technology comparable with intermediate ser-based joining technologies for optical assemblies overcome the limitations of standardfixation technologies such as adhesive or wafer level bonding.By applying the laser en-ergy locally and for a limited time,these technologies allow for higher stability of optical joints as well as for additional functionality.Working without intermediate layers,laser splicing creates highly stable transparent joints that are suitable for the transmission of high power,e.g.,infiber laser assemblies.In contrast,laser beam soldering of opti-cal components as an alternative with a metallic interme-diate layer is nontransparent,but it createsflexible and stress-compensating joints as well as thermal and electri-cal interconnects.In microelectronic packaging,adhesives have been widely known and have enjoyed great success in many low-cost bonding applications for die attachment,substrate at-tachment,surface-mounted device bonding,and hermetic lid sealing.As a low-cost bonding choice,polymeric ad-hesive materials are also widely used in optoelectronic packaging.In terms of epoxy-based adhesives,the ther-mal curing process is applied,while the UV curing process is necessary for acrylic-based adhesives.In optoelectronic packaging,components are usually packaged in hybrid technology;therefore,several microelectronic grade join-ing materials will be used.For example,many different classifications of epoxy resins have been used for joining, protecting,and sealing in LED and LCD.Silver-containing epoxy composites as die-attach materials for LEDs,LCDs, andfiber optics provide not only the electrical pathway, but also the heat-sinking for thermal dissipation improve-ment.Optical transparent adhesives are also required in the light pathway for light transmission as well as bonding purposes.Engineered RI-matched optical epoxies can min-imize the insertion loss for power transfer.Optically clear epoxy is used for the potting,molding,or encapsulation of the LED,and it is used for laminating and gluing the many glass layers used in the LCD sandwich.Material proper-ties such as glass transition temperature(Tg),outgassing, thermal conductivity,thermal resistance,viscoelasticity, hermeticity,strength,andfluorescence will be the focal considerations.Solders as the important joining material have been widely studied and applied in microelectronic packaging. In contrast,the successful commercialization of solders for microelectronic packages should be modified for optoelec-tronic packages because soldering technology needs tofit into the optical requirements of optoelectronic packaging mainly serving for optical alignment in addition to provid-ing electrical connections.In optoelectronic packaging,sol-der has also been used widely as a die-attach material,and its application range is being further expanded because of the development of theflip chip assembly.Flip chip sol-dering introduced by IBM as the controlled-collapse chip connection soldering technology has many advantages,in-cluding superior electrical performance,high reliability,Advanced Packaging of Optoelectronic Devices5reduced footprint,high I/O density,low cost,efficient heat conduction,batch assembly,and self-alignment during the chip jointing.It has been demonstrated that solder is use-ful in the formation of passive,precision alignments for optoelectronic packaging,which can be used to couple op-ticalfibers or waveguides to devices such as lasers and LEDs.The alignments can vary from sub-millimeter to millimeter levels for single-mode or multimodefiber appli-cations.In particular,batch assembly capability and the self-alignment mechanism are critical to precise optical alignments.In principle,as the temperature of the solder is raised above its melting point either by thermal heating or by laser beam soldering,the molten solder starts wetting the metal pad and moving the chip.The chip movement is driven by a surface tension force in an effort to minimize the surface area to reach the lowest total energy of the assembly.At thefinal position,the system will have the lowest total energy,and the position of the chip is locked by cooling the solder ing solder,hundreds or thou-sands of such alignments can be accomplished with a sin-gle batch reflow process,and the alignment time can be reduced by orders of magnitude.Although different soldering technologies have already been developed for various optoelectronic modules,most studies on solder-assembled optoelectronics modules have focused on how to obtain high alignment accuracy rather than on how to maintain the alignment obtained.In addi-tion,critical issues need to be addressed with an emphasis on solder materials,fluxless reflow,design,and reliabil-ity.Important solder properties are melting temperature, Young’s modulus,coefficient of thermal expansion,Poisson ratio,fatigue behavior,and creep rate.Indium-based sol-der has been used for prototyping,but it is not a good ma-terial for high-volume manufacturing because of its high cost,large creep rate,poor corrosion resistance,and high thermomigration rate.In addition,indium is a very effi-cient dopant and demands careful design and manufac-turing control to avoid problems caused by indium diffu-sion.PbSn-based solder is commonly used in electronic packaging.Its fatigue behavior is well accepted,but its creep may result in millimeter-level misalignment and de-grade the coupling performance.In addition,eutectic sol-der might form intermetallics with Au.The stoichiometric binary compound is generally very brittle.Early failure may result.Therefore,it may not be appropriated if the Au layer is more than0.25μm.AuSn solder is not subject to fatigue or creep rupture during thermal cycling because of its high strength;however,it may transfer the stress to the device and cause cracking in the die.To eliminate the contaminations of the soldering pro-cess to the optical components,such as the outgassing of the solder reflow process,thefluxless reflow process of sol-der is preferred in the soldering process for optoelectronic packaging.Different designs have demonstrated precision alignments,and the aligned structures are becoming more and more complex.It has been shown that thefinal align-ment accuracy for self-aligned soldering is strongly related to the solder bump parameters such as solder joint di-ameter and height and the number of joints.For solder self-alignment,these parameters can be designed for the optimum performance.Typically during metallization,Ti or Cr is used as the adhesion layer;Cu,Ni,or Pt is used as the barrier metal;and Au is coated to prevent surface oxidation.The length scales(diameter or width)of the sol-der bumps may vary from26to330mm and heights range from5to50mm.Solder failure mechanisms are driven by tempera-ture,moisture,and voltage.The thermal expansion mis-match between a chip and a substrate could result in stress/strain/fatigue damage of solder connections,optical devices,and layers of metallization or dielectrics.Moisture and voltage combined could result in corrosion or metal migration.Although a variety of mechanisms may result in cracked solder joints,the major cause of such damage is thermal stress and low-cycle,strain-controlled fatigue. Fortunately,for most optoelectronic modules,the assembly sizes are small and the thermal mismatch is much lower than that for microelectronics.Therefore,the reliability is-sue has not been a major issue at the moment.However,the chip size is getting larger and larger with high integration levels;therefore,the reliability assessment should be con-ducted rigorously.The long-term stability of the alignment accuracy depends heavily on the mechanical integrity of solder joints and their attaching layers.Higher mechanical integrity is required for solders during thermal reliability test and service;therefore,hard solder with higher melting temperature is preferred as well.Laser welding developed as an ultra-precision,ultra-fast,and reliable bonding technique is used in high-end optoelectronic packaging,such as pump lasers and dis-tributed feedback lasers for telecommunications.To exe-cute the laser welding bonding process,the material needs to possess the properties to absorb strongly the laser en-ergy while enduring the high-temperature melting without being vaporized(32,33).Currently,stainless steel,Invar, and Kovar are typical bonding materials tofit into the laser fusion process and form a strong joint.The process requires that the components be made of or coated with these ma-terials.A typical example is thefiber ferrule made of Invar or Kovar bonded to a U-typefixture on the optical bench to realizefiber-to-laser coupling.In this process,automated active alignment can be used and post-weld-shift can be applied when necessary(34).Thermal Management MaterialsThe need for improved thermal and packaging materials is well recognized for optoelectronic devices because ther-mal management and packaging materials have a great effect on both heat dissipation and thermal stresses,which further affect device performance and reliability.Thermal management materials are in great need in laser packages, LED packages and reflectors,LCDs,and many other op-toelectronic devices.Desired properties for most optoelec-tronic applications are the same:high thermal conductivity and low CTE.For cases where portability,shock loads,or both are important,low density is a requirement.Ideally, we want packaging materials having thermal conductivi-ties as high as possible and,to minimize thermal stresses, CTEs matching those of the semiconductors and ceramic substrates that are being packaged.Recently,increasing。
外贸英语翻译

To achieve rationalization of the package, you need from the following aspects of strengthening the management :
(1)广泛采用先进包装技术。 包装技术的改进是实现包装合理化的关键。 要推广诸如缓冲包装、防锈包装、防湿包装等包装方法,使用不同的包装技法,以适应不同商品的包装、装卸、储存、运输的要求。
商品包装可以分为生产领域的包装和流通领域的包装。 一般将生产领域的包装称为销售包装,或称为小包装、内包装;流通领域的包装则称为运输包装,或称为大包装、外包装。
Packaging canቤተ መጻሕፍቲ ባይዱbe divided into productive areas of the packaging and distribution of packaging. General Packaging production as the sales package, or in small packaging, packaging ; circulation of the package is known as transport packaging, or large packaging, packaging.
( 1 ) Extensive use of advanced packaging technology. Improvement of packaging technology is the key to achieve rationalization of the package. To promote, such as cushion packaging, preservation packaging, moisture - proof packaging and other packaging methods, using different packaging techniques to accommodate the different packaging, loading and unloading of goods, storage and transport requirements.
英文缩写_全称

abbreviate from(来源)
Advanced Business Application Programming 高级商务应用程序 Activities Based Costing 基于成本的活动 Automatic insertion 自动 插入 Automated Inspection Technology 自动检查技 术 Accelerated life test 加速老化试 验 Approved Manufacturer Lists 批准的制 造商列表 Approved Manufacturers Parts Lists 批准的制造 商元件列表 Analysis of Variance 方差分析法 Automatic Optical Inspection 自动光学 检查 American Production and Inventory Control Society 美国产品和投资控制协会 Advanced Product Quality Planning and Control Plan 产品质量先期策划和控制计划 Advanced Planning System 高级计划 系统 As soon as possible Available to Promise Approved Vendor List 应商列表 Ball Grid Array 格阵列 Bill Of Materials 单 Bill of Material 单 Boards per hour 生产板数 Business Process Procedure 程 Bottom Side Quality Control Board System Test 统测试 Business Unit Co-ordinator 员 Business Unit Director Business Unit Manager Corrective Action Committee 委员会 Computer Aided Design 助设计 Computer Aided Engineering 助工程 Computer Aided Manufacture 助制造 Corrective action plan Corrective Action Report 报告 尽快 批准的供 球形栅 物料清 物料清 每小时 商务处理流 板子系 商务协调 商务总监 商务经理 纠正行动 计算机辅 计算机辅 计算机辅 矫正计划 纠正动作
英语作文-集成电路设计行业中的芯片封装与封装技术解析

英语作文-集成电路设计行业中的芯片封装与封装技术解析The chip packaging and packaging technology in the integrated circuit design industry play a crucial role in the overall performance and reliability of electronic devices. In this article, we will analyze the significance of chip packaging and explore the various packaging technologies used in the industry.Chip packaging is the process of enclosing the integrated circuit in a protective case and connecting it to the outside world through electrical contacts. The main function of chip packaging is to provide protection from mechanical and thermal stresses, as well as to provide electrical connections to the outside world. Additionally, chip packaging also affects the performance, power consumption, and overall cost of the integrated circuit.There are several key considerations in chip packaging, including size, thermal management, electrical performance, and cost. The size of the package is critical for portable electronic devices, where space is limited. Efficient thermal management is essential to ensure the reliability and longevity of the integrated circuit. Electrical performance, including signal integrity and power distribution, is also a major concern in chip packaging. Finally, the cost of the packaging must be optimized to meet the requirements of the target market.In the integrated circuit design industry, there are several packaging technologies that are commonly used to meet these requirements. One of the most widely used packaging technologies is the ball grid array (BGA), which provides a high density of interconnects and excellent thermal performance. Another popular packaging technology is the quad flat package (QFP), which is known for its ease of manufacturing and low cost. In addition, the chip scale package (CSP) has gained popularity for its small size and high performance.Furthermore, advanced packaging technologies such as system in package (SiP) and 3D packaging are becoming increasingly important in the industry. SiP integratesmultiple chips into a single package, offering improved performance and reduced form factor. 3D packaging, on the other hand, stacks multiple layers of integrated circuits, enabling higher integration density and improved electrical performance.In conclusion, chip packaging and packaging technology are essential aspects of the integrated circuit design industry. The choice of packaging technology has a significant impact on the performance, reliability, and cost of electronic devices. As the demand for smaller, faster, and more powerful electronic devices continues to grow, the development of advanced packaging technologies will play a crucial role in meeting these requirements. Therefore, it is important for designers and engineers to stay updated with the latest advancements in chip packaging and packaging technology to ensure the success of their integrated circuit designs.。
这200家公司,凭什么成为苹果供应商?
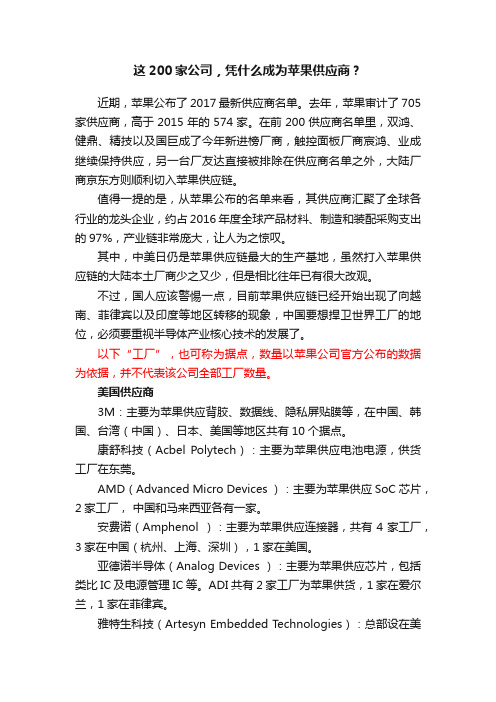
这200家公司,凭什么成为苹果供应商?近期,苹果公布了2017最新供应商名单。
去年,苹果审计了705家供应商,高于2015年的574家。
在前200供应商名单里,双鸿、健鼎、精技以及国巨成了今年新进榜厂商,触控面板厂商宸鸿、业成继续保持供应,另一台厂友达直接被排除在供应商名单之外,大陆厂商京东方则顺利切入苹果供应链。
值得一提的是,从苹果公布的名单来看,其供应商汇聚了全球各行业的龙头企业,约占2016年度全球产品材料、制造和装配采购支出的97%,产业链非常庞大,让人为之惊叹。
其中,中美日仍是苹果供应链最大的生产基地,虽然打入苹果供应链的大陆本土厂商少之又少,但是相比往年已有很大改观。
不过,国人应该警惕一点,目前苹果供应链已经开始出现了向越南、菲律宾以及印度等地区转移的现象,中国要想捍卫世界工厂的地位,必须要重视半导体产业核心技术的发展了。
以下“工厂”,也可称为据点,数量以苹果公司官方公布的数据为依据,并不代表该公司全部工厂数量。
美国供应商3M:主要为苹果供应背胶、数据线、隐私屏贴膜等,在中国、韩国、台湾(中国)、日本、美国等地区共有10个据点。
康舒科技(Acbel Polytech):主要为苹果供应电池电源,供货工厂在东莞。
AMD(Advanced Micro Devices ):主要为苹果供应SoC芯片,2家工厂,中国和马来西亚各有一家。
安费诺(Amphenol ):主要为苹果供应连接器,共有4家工厂,3家在中国(杭州、上海、深圳),1家在美国。
亚德诺半导体(Analog Devices ):主要为苹果供应芯片,包括类比IC及电源管理IC等。
ADI共有2家工厂为苹果供货,1家在爱尔兰,1家在菲律宾。
雅特生科技(Artesyn Embedded Technologies):总部设在美国,主要为苹果供应电源,为苹果供货的生产线,1家在菲律宾,1家在广东云浮。
博伊德(Boyd Die Cut ):为苹果提供散热器,1家供货工厂在苏州。
先进封装技术综述
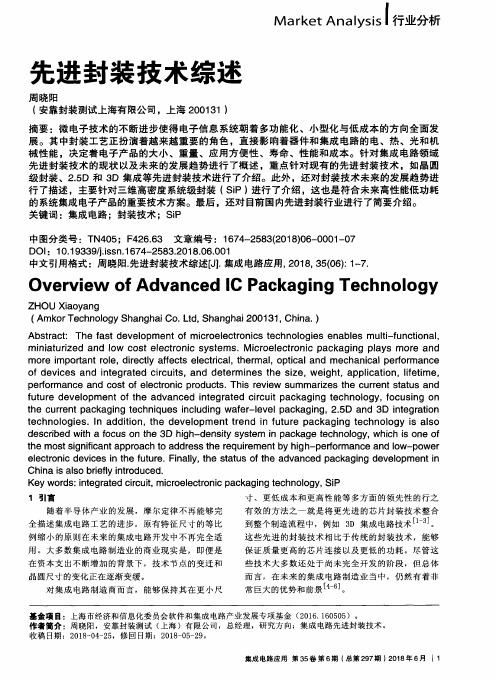
Overview of Advanced IC Packaging Technology
ZHOU Xiaoyang
(Amkor Technology Shanghai Co.Ltd,Shanghai 2001 31,China.)
Abstract: The fast developm ent of m icrOeIectrOnics teChnOlOgies enables m uIti—functi0naI, m iniaturized and IOW cost electronic system s.M icroelectronic packaging plays m ore and m ore im po ̄ant role,directly affects electrical,therm al,opticaI and m echanical perform ance of devices and integrated circuits,and determ ines the size,weight,application,Iifetim e, perform ance and cost of electronic products.This review sum m arizes the current status and future developm ent of the advanced integrated Circuit packaging technology.focusing on the current packaging techniques including wafer-leveI packaging.2.5D and 3D integration teChnOlOgieS.In addition,the developm ent trend in future packaging technology iS also described with a focus on the 3D high—density system in package technology.which iS one of the m ost significant approach to address the requirement by hig h—perform ance and IOW—power electronic devices in the future.Finally.the status of the advanced packaging developm ent in C hina is also briefly introduced. Key words:integrated circuit,microelectronic packaging technology,SiP
先进封装 pi树脂应用场景
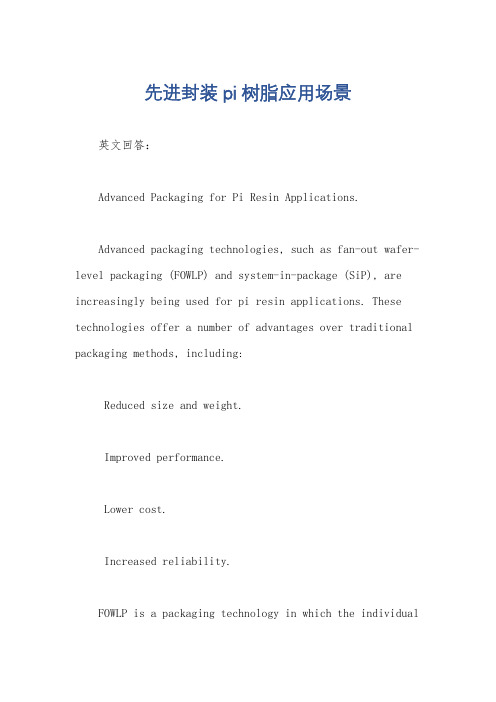
先进封装 pi树脂应用场景英文回答:Advanced Packaging for Pi Resin Applications.Advanced packaging technologies, such as fan-out wafer-level packaging (FOWLP) and system-in-package (SiP), are increasingly being used for pi resin applications. These technologies offer a number of advantages over traditional packaging methods, including:Reduced size and weight.Improved performance.Lower cost.Increased reliability.FOWLP is a packaging technology in which the individualdie are placed on a thin substrate and then interconnected using a fine-pitch copper trace. This technology allows for a significant reduction in size and weight compared to traditional packaging methods. FOWLP is also a very high-performance packaging technology, as it provides a very short electrical path between the die and the substrate. This results in improved electrical performance, including reduced inductance and capacitance.SiP is a packaging technology in which multiple die are integrated into a single package. This technology allowsfor the integration of a variety of functions into a single device, including analog, digital, and RF functions. SiP is a very cost-effective packaging technology, as it eliminates the need for multiple packages and interconnections. SiP is also a very reliable packaging technology, as it provides a high level of protection for the die.Pi resin is a type of polymer that is used in a variety of applications, including automotive, electronics, and medical. Pi resin is a very versatile material, as it canbe used in a variety of forms, including films, sheets, and moldings. Pi resin is also a very durable material, as itis resistant to heat, chemicals, and abrasion.The combination of advanced packaging technologies and pi resin offers a number of advantages for pi resin applications. These advantages include:Reduced size and weight.Improved performance.Lower cost.Increased reliability.Versatility.Advanced packaging technologies and pi resin are a good combination for a variety of applications. These technologies offer a number of advantages, including reduced size and weight, improved performance, lower cost,increased reliability, and versatility.中文回答:先进封装在 pi 树脂应用中的场景。
IEC_TC47
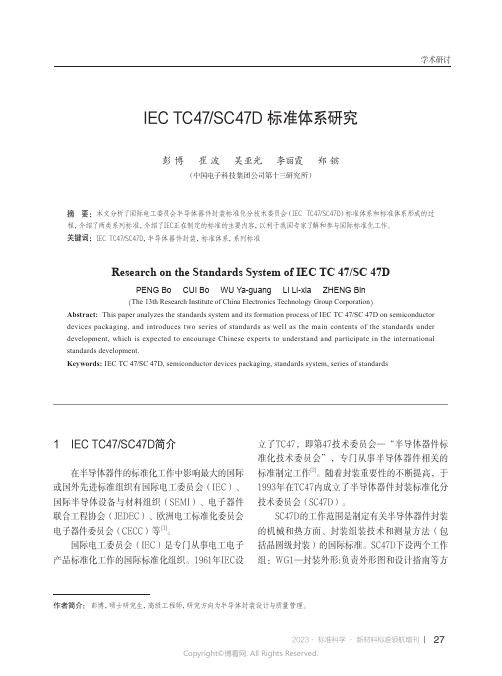
IEC TC47/SC47D 标准体系研究彭 博 崔 波 吴亚光 李丽霞 郑 镔(中国电子科技集团公司第十三研究所)摘 要:本文分析了国际电工委员会半导体器件封装标准化分技术委员会(IEC TC47/SC47D)标准体系和标准体系形成的过程,介绍了两类系列标准,介绍了IEC正在制定的标准的主要内容,以利于我国专家了解和参与国际标准化工作。
关键词:IEC TC47/SC47D,半导体器件封装,标准体系,系列标准Research on the Standards System of IEC TC 47/SC 47DPENG Bo CUI Bo WU Ya-guang LI Li-xia ZHENG Bin(The 13th Research Institute of China Electronics Technology Group Corporation)Abstract: This paper analyzes the standards system and its formation process of IEC TC 47/SC 47D on semiconductor devices packaging, and introduces two series of standards as well as the main contents of the standards under development, which is expected to encourage Chinese experts to understand and participate in the international standards development.Keywords: IEC TC 47/SC 47D, semiconductor devices packaging, standards system, series of standards1 IEC TC47/SC47D简介在半导体器件的标准化工作中影响最大的国际或国外先进标准组织有国际电工委员会(IEC)、国际半导体设备与材料组织(SEMI)、电子器件联合工程协会(JEDEC)、欧洲电工标准化委员会电子器件委员会(CECC)等 [1]。
中国芯片产业的崛起英语介绍
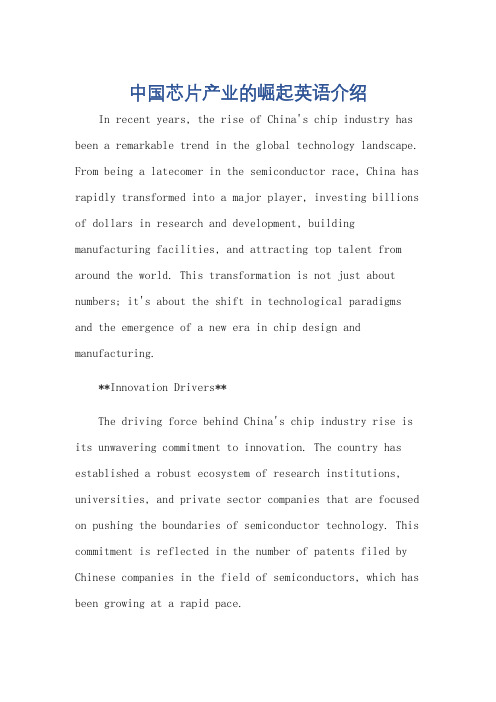
中国芯片产业的崛起英语介绍In recent years, the rise of China's chip industry has been a remarkable trend in the global technology landscape. From being a latecomer in the semiconductor race, China has rapidly transformed into a major player, investing billions of dollars in research and development, building manufacturing facilities, and attracting top talent from around the world. This transformation is not just about numbers; it's about the shift in technological paradigms and the emergence of a new era in chip design and manufacturing.**Innovation Drivers**The driving force behind China's chip industry rise is its unwavering commitment to innovation. The country has established a robust ecosystem of research institutions, universities, and private sector companies that are focused on pushing the boundaries of semiconductor technology. This commitment is reflected in the number of patents filed by Chinese companies in the field of semiconductors, which has been growing at a rapid pace.Moreover, China has been aggressive in attracting global talent, offering competitive salaries and research funds to top scientists and engineers. This strategy has been successful in bringing many of the world's brightest minds to China, who are now contributing to the country's chip industry in areas such as advanced packaging, chip design, and materials research.**Manufacturing Capabilities**Another key aspect of China's chip industry rise is its manufacturing capabilities. The country has invested heavily in building state-of-the-art chip fabs that can produce chips with advanced features and high yields. These fabs are not just located in traditional manufacturing hubs like Shanghai and Beijing but are also being set up in emerging tech cities like Chengdu and Wuhan.This widespread distribution of manufacturingfacilities ensures that China has the capacity to meet the growing demand for chips across various industries, from consumer electronics to automotive and healthcare. Additionally, China is also making strides in areas likewafer manufacturing and chip packaging, which are crucial for the production of advanced chips.**Challenges and Opportunities**However, the rise of China's chip industry is not without its challenges. One of the main obstacles is the dependence on foreign technology and equipment, as many of the key components and materials used in chip manufacturing are still imported from abroad. This dependence limits China's ability to fully control its chip supply chain and can pose significant risks in times of geopolitical tensions.To overcome these challenges, China is actively investing in research and development to develop its own technologies and materials. It is also promoting domestic production of key components and equipment to reduce its dependence on imports. These efforts are expected to payoff in the long run, making China's chip industry more resilient and competitive.Despite these challenges, the opportunities for China's chip industry are immense. The global demand for chips is growing rapidly, driven by the increasing digitization ofeconomies and the emergence of new applications like artificial intelligence, 5G, and the Internet of Things. By leveraging its manufacturing capabilities, research strength, and vast market, China has the potential to capture a significant share of this growing market.**Conclusion**In conclusion, the rise of China's chip industry represents a significant milestone in the global technology landscape. Through innovation, investment, and strategic planning, China has transformed itself into a major player in the semiconductor industry, challenging the established order. While there are still challenges to overcome, the opportunities for growth and development are immense. As we move into the future, it will be fascinating to watch how China's chip industry continues to evolve and shape the global technology landscape.**中国芯片产业的崛起:创新与挑战并存的新时代** 近年来,中国芯片产业的崛起已成为全球科技领域的一个显著趋势。
IC封装基板设计及APD软件简介

I NVENTIVECONFIDENTIAL Ming@IC封装基板设计及APD软件简介Agenda芯片封装设计的背景简介IC基板设计的概念和常用软件常见的BGA封装的结构和特点Cadence APD软件的简介封装基板设计的一般流程封装设计中的一些注意点芯片封装设计的背景•集成电路(IC )产业主要包括三个环节:–IC 设计–晶圆制造–封装和测试•封装包括IC 晶片的粘结固定、电路连线、结构密封、与电路板接合、与系统组合。
•封装的一般功能和作用:–传递电子电路信号–提供散热途径–承载与结构保护电子封装制程的层次(Level )•第一层:–将IC 晶片粘结于构装壳体中并完成其中的电路连线与密封保护之制程。
又称模组(module )或者晶片层次封装。
我们通常说的IC 封装指这个层次。
•第二层:–指第一层完成之后的元件组合成一电路卡(Card )的制程。
•第三层:–将数个电路板组合于一主机板(Board )上成为一次系统的制程。
•第四层:–将数个次系统组合成一完整的电子产品(Gate )的制程。
IC 封装的大致流程•晶片粘结:将IC 晶片固定于构装机板或者引脚架的承载座上的制程;•连线:打线接合(Wire Bonding )、卷带自动接合(Tape Automated Bonding ,TAB )、倒装接合(Flip Chip );•封胶(Molding ):将IC 晶粒及焊线保护住,不受外界温湿度影响,并使形状固定符合规范。
•电镀(Solder Plating ):为了使成品能够焊接在电路板上,并防止氧化,外脚需要做锡铅电镀。
•引脚成型(Forming ):依产品类型及顾客要求,将外脚切割或弯曲成型。
以符合标准尺寸规范之形状。
全球较知名的封装厂•日月光(ASE ,台湾)•安可(Amkor ,美国)•矽品(SPIL ,台湾)•乐依文(ASAT ,香港)•金朋(Chip PAC ,美国)•阿法泰克(Alphatec ,泰国)•ST Assembly Testing Services(新加坡)•华泰(OSE ,台湾)•安南(Anan ,韩国)IC 基板和封装产业的关系•由于IC 性能需求的提高,很多封装已经不需要导线架封装;•将近48%的封装采用到IC 基板;•随着高阶封装的比例不断上升,IC 基板和封装产业的关系愈加密切;•当前主要的IC 基板设计为BGA 、CSP 、Flip Chip 等类型;•目前IC 基板的产值占IC 封装产值的2成左右;•2003年全球IC 基板市场为37亿美元,2004年大概为50亿美元。
封装工艺 英语
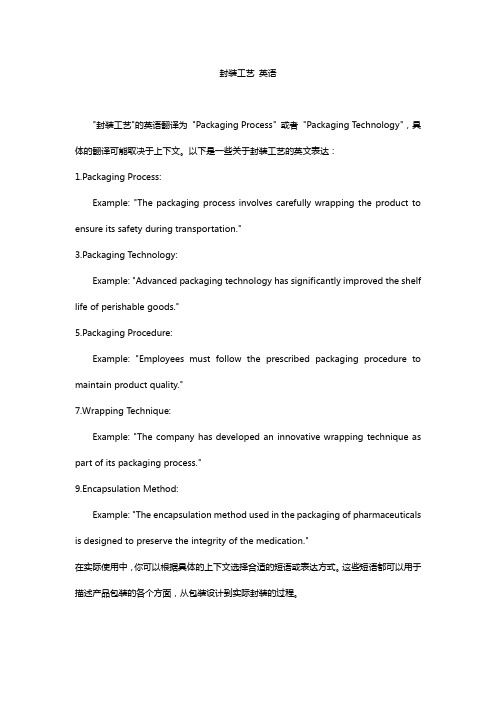
封装工艺英语"封装工艺"的英语翻译为"Packaging Process" 或者"Packaging Technology",具体的翻译可能取决于上下文。
以下是一些关于封装工艺的英文表达:1.Packaging Process:Example: "The packaging process involves carefully wrapping the product to ensure its safety during transportation."3.Packaging Technology:Example: "Advanced packaging technology has significantly improved the shelf life of perishable goods."5.Packaging Procedure:Example: "Employees must follow the prescribed packaging procedure to maintain product quality."7.Wrapping Technique:Example: "The company has developed an innovative wrapping technique as part of its packaging process."9.Encapsulation Method:Example: "The encapsulation method used in the packaging of pharmaceuticals is designed to preserve the integrity of the medication."在实际使用中,你可以根据具体的上下文选择合适的短语或表达方式。
- 1、下载文档前请自行甄别文档内容的完整性,平台不提供额外的编辑、内容补充、找答案等附加服务。
- 2、"仅部分预览"的文档,不可在线预览部分如存在完整性等问题,可反馈申请退款(可完整预览的文档不适用该条件!)。
- 3、如文档侵犯您的权益,请联系客服反馈,我们会尽快为您处理(人工客服工作时间:9:00-18:30)。
• ALL Use mechanical based tools for design (AutoCAD)
– NOT a Good Fit For APD – 75% of IC’s are in Lead Frame Packages
IC Package Types Continued…
• BGA- Ball Grid Array
• Build-up is Less Expensive Than LTCC. However, LTCC Exhibits Better Die Shrink Support with Same Build-Up Arrangement (a 3/2/3 process)
• Die Cost (size) Drives Use of Flip-Chip, Build-Up Process
• Used in Lead Frame, PGA and BGA packaging
• Over 80% of Packages are Wirebonded
• Epoxy Glue to Attach Chip • Typically Gold Wire
– Also Copper, Aluminum
Advantages of Flip-Chip
• Reduced Signal Inductance
– Shorter Interconnect Lengths
• Use Power More Efficiently
– Power Directly at the Core
• Higher Interconnect Density
– Under-fill epoxy is used to secure the attachment and absorb stress
– The chip is then “flipped” face down onto the package carrier using a reflow process – Bump sizes range from 90-125 microns in diameter – Also known as C4 (Controlled Collapsible Chip Connection)
– Flex Tape and Wirebond also possible
• Common for Wireless Handsets and Handheld Electronics . • Stacked die support (S-CSP- Stacked CSP) • Laminate and Ceramic Substrates
IC Package Types (Lead Frame)
• PQFP- Plastic Quad Flat Pack
– Up to 304 pins (500 micron pitch) – Inexpensive (~ a penny per pin) – Hermetic (Good for Harsh Environments) – Smaller ASICs and lower performance, lower pin count Microprocessors.
• Based on High Density, Micro Via Organic Substrate
– Also Referred To As Sequential Build-up
– Requires Flip-Chip Escape Route Patterns
– Typical Package Assembly Based on a 2layer Core and Build-Up From Each Side of Core – i.e. 3/2/3 process equals 3 build-up layers from each core side
• High Pin Count ASICs and Microprocessors • Typical Package is CBGA or TBGA (> 600 pins) • Tape Carrier Package Used for < 600 pins
Flip-Chip…The Build-Up Process
2layer core
Flip-Chip…The Build-Up Process
• Layer to Layer Connections Typically Use:
– Micro-Vias of 100um or Less
– Special Patterns (Stagger, Staircase, etc.) – Core Vias Larger Than Micro Vias – Lines and Spaces < 35um
– PBGA (Plastic BGA)
– Routable Laminate Substrate (Many Layers) – High Pin Count (Over 2000 pins)
– ASICs, DSPs, PC Chipsets
– Wirebond, TAB or Flip-Chip (Build-Up) attach – Build-Up Technology Requires Special Via Structures – Can support Via in Balls (uncommon)
– Usually Flip-Chip and SiP (MCM) – Supports Smaller Feature Sizes (Interconnect Density) – Supports Via in Ball – Support for Die Cavities – More Expensive, Reliability Questions
• Supports Smaller On-chip Pin Size and Pitch • Supports up to 850 Pins
• Better Electrical Performance than Wirebonds
• Area TAB for Flip-Chip
Flip-Chip (C4) Attachment
• TSOP- Thin Small Outline Package (TQFP- Thin QFP)
– Very Low Profile
– Common for Memory – Can Support Stacked Die – Can Support Flip chip
• PLCC, SOIC, MLF, DIP, SIP, etc– Smaller Pin Count (4-84 pins)
• Two methods of “Bumping” the Chip:
– RDL- Re-Distribution Layer
– Direct Bumping (UBM)
More Flip-Chip…
• Stud Bumping
– Direct Gold Bump Placed on Die Bond Pad – Supports Tighter Pin Pitch
• Use of Mesh Planes for Fabrication Yields
– IBM
Unique uvia Patterns Core via vs. uvia
CSP- Chip Scale Packaging
• Definition: A Package is Considered CSP when it is Less than 20% Larger than the Die. • Usually Flip-Chip Attachment
– Invented by IBM
Flip-Chip Continued
• Flip-Chip is NOT:
– A Specific Substrate Material like LTCC or FR4
– A Specific Package like SOIC
– A Specific Package Type like QFP, BGA or PGA
Advanced IC Packaging A Technology Overvik C. Moll
A Chip is Useless w/out a Package
• Delivers power to the Chip • Transfers information into and out of the Chip to the PCB • Draws heat away from the Chip • Protects the Chip from outside elements
– More Routable Area
• Smaller Package Size
– Chip Scale Packaging (CSP)
• I/O Not Controlling Core Size
– Area Array Placement – Possible Die Shrink
More about Flip-Chip
– Wire length- typ. 1-5 mm – Wire diam.- typ 25-35 µm
– Inexpensive, Reliable
TAB (Tape Automated Bonding)
• Interconnect Patterned On Tape
• Stronger Lead Bonding Strength
BGA Continued…
• BGA- Ball Grid Array
– TBGA (Tape BGA)