基于单片机控制的钻孔机构的设计
基于PLC的钻孔组合机床控制系统设计

基于PLC的钻孔组合机床控制系统设计摘要:钻孔组合机床是一种常用的加工设备,其控制系统对于机床的工作效率和加工质量有着重要的影响。
本文基于PLC(可编程逻辑控制器)技术,设计了一种钻孔组合机床控制系统,并对系统进行了仿真和实验验证。
实验结果表明,该控制系统能够稳定可靠地控制钻孔组合机床的工作,并且具有较高的精度和效率。
关键词:PLC;钻孔组合机床;控制系统;仿真;实验验证一、引言钻孔组合机床是一种常用的加工设备,广泛应用于各行各业。
传统的钻孔组合机床控制系统多采用电磁继电器和电路控制的方式,具有控制精度低、可靠性差等缺点。
而PLC技术具有编程灵活、控制精度高、可靠性好等优点,因此在钻孔组合机床控制系统中得到了广泛应用。
本文基于PLC技术,设计了一种钻孔组合机床控制系统,并对系统进行了仿真和实验验证。
二、PLC钻孔组合机床控制系统的设计1.控制系统硬件设计PLC钻孔组合机床控制系统的硬件部分包括PLC主控模块、人机界面模块、执行机构模块等。
PLC主控模块实现对整个控制系统各部分的控制指令的解码和执行;人机界面模块为操作员提供了直观的控制界面;执行机构模块负责实际的加工操作。
2.控制系统软件设计PLC钻孔组合机床控制系统的软件部分主要包括控制程序的编写和参数设置。
控制程序的编写是整个软件设计的核心,包括自动控制程序、手动控制程序、故障检测程序等。
参数设置是根据具体的机床和工件进行的,包括钻孔深度、钻孔速度等参数的设置。
三、PLC钻孔组合机床控制系统的仿真为了验证设计的控制系统的正确性和可行性,本文进行了系统的仿真。
仿真结果表明,控制系统能够稳定可靠地控制钻孔组合机床的工作,并且具有较高的精度和效率。
四、PLC钻孔组合机床控制系统的实验验证根据仿真结果,设计了实验验证方案,并进行了实验。
实验结果表明,控制系统能够稳定可靠地控制钻孔组合机床的工作,实现了钻孔深度和钻孔速度的准确控制。
五、总结通过本文的研究,基于PLC的钻孔组合机床控制系统设计得到了较好的结果。
基于PLC控制的数控钻孔机的设计与实现

基于PLC控制的数控钻孔机的设计与实现随着科技的进步和工业自动化水平的提高,数控(Numerical Control)钻孔机在工业生产中得到了广泛的应用。
数控钻孔机的设计与实现基于PLC(Programmable Logic Controller)控制,PLC控制具有可靠性高、灵活性强等优点。
本文将介绍基于PLC控制的数控钻孔机的设计与实现。
首先,在数控钻孔机的设计中,我们需要考虑到几个方面。
首先是机械部分的设计,包括钻头的选择、主轴的设计、夹持装置的设计等。
其次是电气部分的设计,主要包括电机的选择、传感器的选择、电气线路的设计等。
最后是PLC控制程序的编写,需要根据实际需求设计钻孔程序。
在机械部分的设计中,我们需要选择适合的钻头来满足不同的钻孔需求。
常见的钻头有立铣钻头、圆滚钻头等。
主轴的设计需要考虑到主轴的转速和稳定性,可以选择带有变频器的电机来调整主轴的转速。
夹持装置的设计需要满足钻孔材料的夹持需求,可以选择气动夹紧装置或电动夹紧装置。
在电气部分的设计中,我们需要选择适合的电机来驱动主轴。
根据钻孔材料的不同,可以选择不同功率的电机。
传感器的选择需要满足对材料位置和尺寸的检测需求,可以选择接近开关、压力传感器等传感器。
电气线路的设计需要根据实际需求进行布线,保证线路的安全稳定。
在PLC控制程序的编写中,我们需要根据实际需求设计钻孔程序。
首先,我们需要编写一个启动程序,通过点击按钮或接近开关来启动钻孔机的工作。
然后,我们需要编写一个控制程序,通过设定参数来控制钻孔机的运行。
控制程序可以设置钻孔深度、钻孔速度等参数。
最后,我们还需要编写一个停止程序,当钻孔完成或发生异常情况时,通过点击按钮或接近开关来停止钻孔机的工作。
总结起来,基于PLC控制的数控钻孔机的设计与实现需要考虑到机械部分的设计、电气部分的设计以及PLC控制程序的编写。
通过合理的设计和实施,可以实现数控钻孔机的自动化控制,提高生产效率,降低人工成本,提高产品质量。
中心孔打孔机的设计
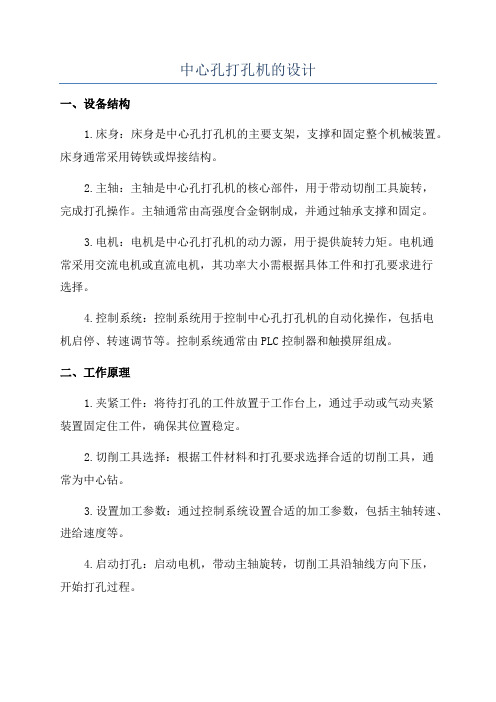
中心孔打孔机的设计一、设备结构1.床身:床身是中心孔打孔机的主要支架,支撑和固定整个机械装置。
床身通常采用铸铁或焊接结构。
2.主轴:主轴是中心孔打孔机的核心部件,用于带动切削工具旋转,完成打孔操作。
主轴通常由高强度合金钢制成,并通过轴承支撑和固定。
3.电机:电机是中心孔打孔机的动力源,用于提供旋转力矩。
电机通常采用交流电机或直流电机,其功率大小需根据具体工件和打孔要求进行选择。
4.控制系统:控制系统用于控制中心孔打孔机的自动化操作,包括电机启停、转速调节等。
控制系统通常由PLC控制器和触摸屏组成。
二、工作原理1.夹紧工件:将待打孔的工件放置于工作台上,通过手动或气动夹紧装置固定住工件,确保其位置稳定。
2.切削工具选择:根据工件材料和打孔要求选择合适的切削工具,通常为中心钻。
3.设置加工参数:通过控制系统设置合适的加工参数,包括主轴转速、进给速度等。
4.启动打孔:启动电机,带动主轴旋转,切削工具沿轴线方向下压,开始打孔过程。
5.打孔结束:达到打孔深度后,切削工具停止下压,主轴停止转动,完成打孔操作。
三、设计要点在中心孔打孔机的设计过程中,需要考虑以下几个要点:1.稳定性:床身的结构设计应确保机械装置的稳定性,以避免因振动而影响打孔精度。
2.定位准确性:工作台和夹具的设计应保证工件的定位准确,以确保打孔位置的精确性。
3.切削工具的选择和安装:切削工具的选用应根据材料和打孔要求进行选择,并正确安装在主轴上。
4.自动化控制:控制系统的设计应注重简洁、易操作,以实现自动化的打孔操作。
5.安全性:设计应考虑到操作人员的安全,并加装相应的安全装置,如防护罩、急停按钮等。
四、应用领域综上所述,中心孔打孔机的设计应注重稳定性、准确性、自动化控制和安全性,以满足不同行业对打孔加工的需求。
基于PLC控制的数控钻孔机的设计与实现

基于PLC控制的数控钻孔机的设计与实现数控钻孔机是一种通过计算机数控系统实现自动钻孔的设备,可以实现高精度、高效率的钻孔作业。
本文将基于PLC控制的数控钻孔机的设计与实现进行详细介绍。
1.设计概述数控钻孔机主要由机械部分和控制系统两部分组成。
机械部分主要包括电动机、传动装置和钻头等,控制系统则由PLC控制器和人机界面组成。
2.机械部分设计为了实现高精度的钻孔作业,机械部分需要具备较高的稳定性和刚度。
首先,选择质量较好的电动机,通过减速装置将电动机的转速转为稳定的钻头转速。
其次,使用高硬度的刀具材料,以保证钻头在高速转动时不会变形。
最后,选择高精度的导轨和滑块,确保钻孔机在运动过程中无偏差。
3.PLC控制系统设计PLC控制系统是数控钻孔机的核心部分,它通过计算机数控系统来实现自动化的钻孔操作。
首先,选择适合的PLC控制器,通常选择具有高速计算和多IO口的控制器。
其次,编写PLC程序,根据用户输入的坐标参数和钻头尺寸,计算出钻孔的位置和深度。
然后,通过控制器的输出口,控制电动机的转速和钻头的升降运动,实现自动化的钻孔操作。
最后,在控制界面上添加合适的控制按钮和显示界面,方便用户操作和监测钻孔过程。
4.人机界面设计为了方便操作和监测钻孔过程,需要设计一个直观清晰的人机界面。
在界面上添加坐标输入框和尺寸调节按钮,方便用户输入钻孔的坐标和尺寸参数。
同时,添加控制按钮和监测指示灯,方便用户启动和停止钻孔过程,并实时监测钻孔状态。
另外,在界面上添加错误提示功能,当出现异常情况时能及时提示用户,并采取相应的应对措施。
5.钻孔机的实现在完成设计后,将机械部分和控制系统进行组装和调试。
首先,根据设计要求,选择适合的材料和加工工艺,制作机械部分的各个零件。
然后,组装机械部分,确保各个部件的协调配合。
接下来,将PLC控制器和人机界面与机械部分进行连接,并进行电气布线和信号调试。
最后,进行整机调试和测试,检查钻孔机的各项指标是否符合设计要求。
基于PLC的钻孔加工过程自动化控制系统的设计
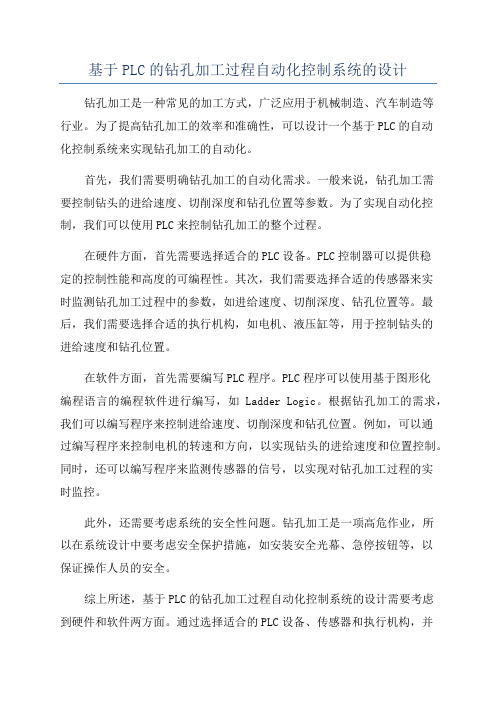
基于PLC的钻孔加工过程自动化控制系统的设计钻孔加工是一种常见的加工方式,广泛应用于机械制造、汽车制造等行业。
为了提高钻孔加工的效率和准确性,可以设计一个基于PLC的自动化控制系统来实现钻孔加工的自动化。
首先,我们需要明确钻孔加工的自动化需求。
一般来说,钻孔加工需要控制钻头的进给速度、切削深度和钻孔位置等参数。
为了实现自动化控制,我们可以使用PLC来控制钻孔加工的整个过程。
在硬件方面,首先需要选择适合的PLC设备。
PLC控制器可以提供稳定的控制性能和高度的可编程性。
其次,我们需要选择合适的传感器来实时监测钻孔加工过程中的参数,如进给速度、切削深度、钻孔位置等。
最后,我们需要选择合适的执行机构,如电机、液压缸等,用于控制钻头的进给速度和钻孔位置。
在软件方面,首先需要编写PLC程序。
PLC程序可以使用基于图形化编程语言的编程软件进行编写,如Ladder Logic。
根据钻孔加工的需求,我们可以编写程序来控制进给速度、切削深度和钻孔位置。
例如,可以通过编写程序来控制电机的转速和方向,以实现钻头的进给速度和位置控制。
同时,还可以编写程序来监测传感器的信号,以实现对钻孔加工过程的实时监控。
此外,还需要考虑系统的安全性问题。
钻孔加工是一项高危作业,所以在系统设计中要考虑安全保护措施,如安装安全光幕、急停按钮等,以保证操作人员的安全。
综上所述,基于PLC的钻孔加工过程自动化控制系统的设计需要考虑到硬件和软件两方面。
通过选择适合的PLC设备、传感器和执行机构,并编写合适的PLC程序,可以实现对钻孔加工过程的自动化控制。
这样可以提高钻孔加工的效率和准确性,降低人工操作的工作强度,提高生产效益。
同时,还需要考虑系统的安全性问题,采取相应的安全保护措施,确保操作人员的安全。
基于PLC控制的数控钻孔机的设计与实现
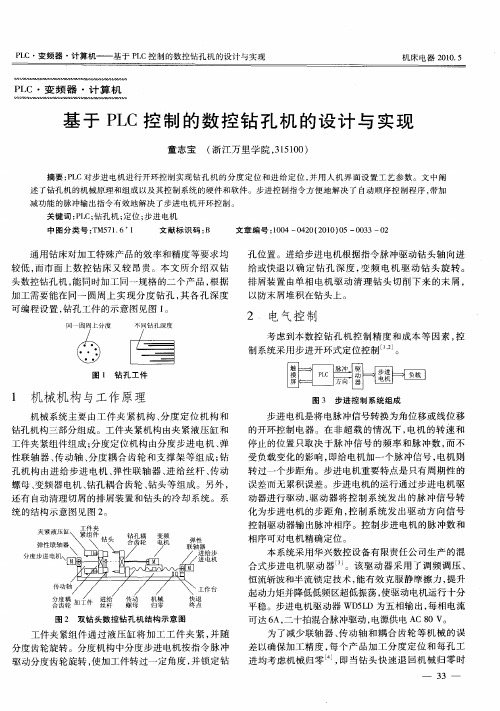
中 图分 类 号 : M 7 . 1 T 516 文献 标 识 码 : B 文章 编 号 : 0 0 2 ( 00 0 03 0 1 4— 40 2 1 )5— 0 3— 2 0
通用 钻床对加工特殊 产品 的效率 和精度等要 求均 较低 , 而市面上数 控 钻床 又较 昂贵。本文 所介 绍 双钻 头数控钻 孑 机 , 同时加 工同一规格 的二个产 品 , L 能 根据
图 2 双钻 头数 控 钻 孔机 结构 示 意 图
工件 夹紧组 件通 过液 压 缸将 加工 工件 夹 紧 , 随 并 分度齿轮旋转 。分度机构 中分度 步进 电机按 指令脉 冲 驱动分度齿 轮旋 转 , 使加工件转 过一定角度 , 并锁定 钻
可达 6 二十拍混合脉冲驱动 , A, 电源供 电 A 0V。 C8 为 了减少联轴 器 、 动轴 和耦 合齿 轮 等机 械 的误 传 差 以确保 加工精度 , 个产 品加 工分 度定 位和 每孔 工 每 进均 考虑机械归 零M , ] 即当钻头 快速 退 回机械 归零 时
应 考虑如下关系。
控制信号和电机脱 机控制信 号 、 变频器正 向启 动信号 、 工件夹紧电磁 阀控制信 号等 。变频器调节频率 以控制 钻头的转速 。触摸屏人机界面设置或修改工件加工技 术参数 , 并显示工作状况 。系统控制 电路见 图 4 。
凶
O Y 2
。ቤተ መጻሕፍቲ ባይዱ
奎
—
:
一
—
以防 末 屑 堆 积 在 钻 头 上 。
2 电气 控 制
考虑到本 数控钻 孔机 控制 精度 和成 本等 因素 , 控 制系统采用 步进开环式定位控 制 。
PLC控制的专用钻孔系统设计

PLC控制的专用钻孔系统设计PLC(可编程逻辑控制器)是一种用于控制工业自动化系统的计算机控制系统,它可以控制和监控各种工艺设备和机器。
钻孔系统是一种常见的工业设备,用于在不同材料上进行钻孔操作。
本文将介绍如何设计一个基于PLC控制的专用钻孔系统。
首先,设计钻孔系统时需要确定系统的功能需求。
主要功能包括控制钻头的进给速度和转速,控制钻孔深度和位置,实现自动钻孔和停止功能。
此外,钻孔系统还可以考虑添加自动刀具更换和质量检测等功能。
接下来,需要选择适用的PLC控制器和其他相关硬件设备。
根据钻孔系统的规模和要求,选择合适的PLC型号和扩展模块。
同时,选择合适的传感器和执行器,用于监测和控制钻孔系统的运行状态。
在进行系统设计时,需要根据功能需求和硬件设备的特性,编写PLC程序。
程序应考虑到钻孔的各种情况和特殊要求,例如不同材料的钻孔参数不同,需要根据材料类型和规格进行调整。
此外,还可以添加故障诊断和报警功能,以便及时发现和修复故障。
图形化编程软件是PLC编程的常用工具,它可以简化编程的过程,并提供友好的用户界面。
使用该软件,可以创建钻孔系统的控制界面,并实现直观的操作和监控功能。
同时,还可以通过通信接口与其他系统进行数据交换,如与上位机进行数据传输和与生产线进行协作。
在钻孔系统设计中,安全性是一个至关重要的因素。
系统应考虑到各种安全措施,包括紧急停止按钮、安全门和传感器等。
此外,还需要进行安全风险评估,并根据评估结果进行相应的控制和优化。
在设计完成后,需要进行系统的调试和测试。
通过模拟真实操作场景,测试PLC程序的功能和性能。
同时,还需要验证系统对各种输入条件的响应和处理能力,并进行必要的调整和改进。
最后,为了确保钻孔系统的可靠性和稳定性,需要进行预防性维护和定期检查。
定期检查系统的各个组件、传感器和执行器的工作状态,并及时更换损坏或老化的部件。
总之,基于PLC控制的专用钻孔系统设计需要综合考虑功能需求、硬件设备、编程软件和安全措施等因素。
基于PLC的钻孔加工过程自动化控制系统的设计
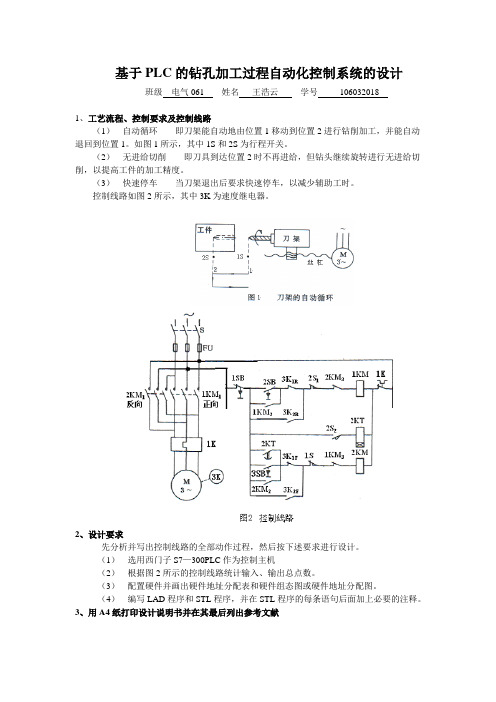
基于PLC的钻孔加工过程自动化控制系统的设计班级电气061 姓名王浩云学号1060320181、工艺流程、控制要求及控制线路(1)自动循环即刀架能自动地由位置1移动到位置2进行钻削加工,并能自动退回到位置1。
如图1所示,其中1S和2S为行程开关。
(2)无进给切削即刀具到达位置2时不再进给,但钻头继续旋转进行无进给切削,以提高工件的加工精度。
(3)快速停车当刀架退出后要求快速停车,以减少辅助工时。
控制线路如图2所示,其中3K为速度继电器。
2、设计要求先分析并写出控制线路的全部动作过程,然后按下述要求进行设计。
(1)选用西门子S7—300PLC作为控制主机(2)根据图2所示的控制线路统计输入、输出总点数。
(3)配置硬件并画出硬件地址分配表和硬件组态图或硬件地址分配图。
(4)编写LAD程序和STL程序,并在STL程序的每条语句后面加上必要的注释。
3、用A4纸打印设计说明书并在其最后列出参考文献设计步骤:1、根据上图分析过程:电机正转起动(进刀)→进刀按2SB→1KM吸合—→1KM1闭合→电机正转—→3K动作—→3K1F打开—→为反接制动作准备→1KM2闭合→自锁→3K2F闭合→→1KM3打开→反向闭锁进给电机正转(进刀)时的快速停车进给电机正转(进刀)时的快速停车可防止进刀过多,提高加工质量。
这种情况进给电机正转(进刀)是带负载运行(反转时不带负载),故本身断电停车就快,加上反接制动后,正向停车就更快。
其动作过程如下:→2S2闭合→2KT吸合→无进给切削计时开始撞压2S—→2S1打开→1KM释放—→1KM1打开→切断正转电源→1KM2打开→自锁解除→1KM3闭合—(3K2F早已闭合)→2KM吸合→①①—→2KM3打开→正向闭锁→2KM2闭合→因3K1F早已断开,无自锁作用→2KM1闭合→接通反转电源→电机反接制动(但仍正转)→电机转速迅速下降→当转速下降到约为零时(100转/分)→3K释放—→3K2F先断开→→3K1F后闭合—→2KM释放→2KM1打开→防止电机反转,同时反接制动结束→电机靠自由滑行减速到零→开始无进给切削→无进给切削时间到2KT闭合→进入进给电机的反转过程→退刀(2)进给电机反转(退刀)时的快速停车进给电机反转(退刀)时的快速停车可减少等待时间、提高辅助工时。
基于单片机控制的便携式电火花打孔机的设计

第36卷第4期2019年4月机㊀㊀电㊀㊀工㊀㊀程JournalofMechanical&ElectricalEngineeringVol.36No.4Apr.2019收稿日期:2018-09-05基金项目:国家自然科学基金资助项目(51665009)ꎻ广西高等教育本科教学改革工程重点项目(2016JGZ123)ꎻ国家级大学生创新项目(201710595028)作者简介:蒋志强(1997-)ꎬ男ꎬ湖南衡阳人ꎬ主要从事特种加工方面的研究ꎮE ̄mail:2511924763@qq.com通信联系人:陈虎城ꎬ男ꎬ博士研究生ꎬ讲师ꎮE ̄mail:qwtiger459@163.comDOI:10.3969/j.issn.1001-4551.2019.04.012基于单片机控制的便携式电火花打孔机的设计∗蒋志强ꎬ陈虎城∗ꎬ龙向前ꎬ来智浩ꎬ朱奋永ꎬ唐宇阳(桂林电子科技大学机电工程学院ꎬ广西桂林541004)摘要:针对现有的便携式电火花打孔机质量太大㊁加工效率低等问题ꎬ在分析总结了现有的便携式电火花打孔机研究现状的基础上ꎬ提出了一种滑块静止而导轨运动的执行机构设计方案ꎮ基于单片机ꎬ研究了直接利用RC比较电路以简化放电回路的方法ꎬ使用了千分表座作为便携式电火花打孔机的底座以调整打孔面ꎬ制作出的便携式电火花打孔机重量减轻至10kg以内ꎬ测得材料去除率达到了15mm3/min以上ꎬ且打孔面易于调整ꎮ设计结果表明:所优化的执行机构㊁放电回路㊁打孔面调整装置减轻了便携式电火花打孔机的重量ꎬ提高了加工效率ꎬ且工作稳定ꎮ关键词:单片机ꎻ电火花加工ꎻ便携式打孔机中图分类号:TH ̄39ꎻTG669㊀㊀㊀㊀文献标志码:A文章编号:1001-4551(2019)04-0402-05PortableEDMpunchingmachinebasedonsinglechipmicrocomputercontrolJIANGZhi ̄qiangꎬCHENHu ̄chengꎬLONGXiang ̄qianꎬLAIZhi ̄haoꎬZHUFen ̄yongꎬTANGYu ̄yang(SchoolofMechanical&ElectronicEngineeringꎬGuilinUniversityofElectronicTechnologyꎬGuilin541004ꎬChina)Abstract:AimingatweightandefficiencyproblemsofportableEDMdrillingmachineꎬtheresearchstatusofEDMdrillingmachinewerean ̄alyzedandsummarizedꎬadesignplanthatkeepthesliderstaytoletguidewaymovementwasputforward.Thewaythatsinglechipmicro ̄computerdirectlytaketheadvantagesofRCcomparisoncircuittosimplifydischargecircuitwasstudiedꎬmicrometerpedestalwasusedasabaseofportableEDMdrillingmachinetoadjusttheperforatedsurface.TheweightofportableEDMdrillingwasmadereducetolessthan10kgꎬtesteddatashowedthematerialremovalrateupto15mm3/minꎬandperforatedsurfaceeasytoadjust.TheresultsindicatethattheoptimizedactuatorꎬdischargecircuitandperforatedsurfaceadjustmentdevicereducetheweightofportableEDMdrillingmachineꎬimproveworkingefficiencyꎬtheworkisstable.Keywords:singlechipmicrocomputerꎻelectricaldischargemachining(EDM)ꎻpunchingmachine0㊀引㊀言电火花加工是一种特种加工方法ꎬ在我国已得到广泛的应用[1]ꎮ电火花加工方法是当前机械加工的重要方法之一ꎬ并有着其他加工方法无可替代的优点[2]ꎮ由于超硬材料加工㊁大型机床维护成本高ꎬ复杂形状零部件表面打孔 特别是狭小空间内的加工困难等问题ꎬ传统打孔方法无法实现或极为困难ꎬ便携式电火花加工设备便应运而生[3 ̄6]ꎮ林启明[1]㊁俞晓[7]㊁刘向前[8]㊁丁向阳[9]㊁刘晋春[10]㊁WANGXue ̄tao[11]等人ꎬ对便携式电火花打孔机进行了各自的研制ꎬ并形成了相应的产品ꎬ但整体设计思路仍拘泥于大型机床的微小化ꎬ对桌面式实验教学考虑不够ꎮ针对便携式电火花打孔机执行机构轻便和易于灵活安装的需求特点ꎬ本文将进行优化设计ꎮ1㊀系统结构与电路设计1.1㊀系统总体架构与设计思路系统要求便携且功能简单ꎬ在保证控制可靠性㊁稳定性下ꎬ采用ATmega16单片机进行控制ꎮ便携式电火花打孔机的机械结构部分和电路控制部分如下:(1)机械结构部分ꎮ包括机架㊁运动执行机构(滚动直线导轨以及滑动丝杆)㊁电极夹头㊁工作液系统和电气安装支架ꎻ(2)电路控制部分ꎮ包括RC电压比较电路㊁步进电机控制电路㊁按键输入电路㊁LED显示电路㊁电极限位置感应电路㊁单片机外围电路ꎮ根据整机的机械与电路设计ꎬ进行机械加工与装配和电路控制系统搭建ꎬ通过实物样机测试达到的设备性能参数ꎬ确定是否满足设计需求ꎮ1.2㊀机械结构设计电火花打孔机部分结构示意图如图1所示ꎮ图1㊀电火花打孔机机械部分结构示意图1-步进机电ꎻ2-下极限板金ꎻ3-极限开关ꎻ4-极限开关固定螺丝ꎻ5-极限开关固定座ꎻ6-副螺母ꎻ7-极限开关固定螺钉ꎻ8-主螺母ꎻ9-滑块ꎻ10-主轴拉杆ꎻ11-绝缘垫ꎻ12-绝缘套ꎻ13-主轴固定螺钉ꎻ14-直线导轨ꎻ15-上极限板金ꎻ16-钻夹由于本机行程小ꎬ构件尺寸较大ꎬ本研究采用滑块静止导轨运动的运动方式ꎻ又因为丝杆旋转体积小ꎬ机构简单ꎬ本研究选择采用螺母固定ꎬ丝杆与电机运动的方式ꎮ步进电机与丝杆之间通过联轴器相连ꎻ丝杆与滚动直线导轨通过螺纹相连ꎮ此外ꎬ因为滑轨运动ꎬ本研究将钻夹头安装在导轨上ꎬ并做好导轨与钻夹的绝缘处理ꎮ行程开关在这种构件大行程小的状态下ꎬ选择采用将其安装在滑块上ꎬ并采用限位片在导轨两端的方式实现限位ꎮ所以主螺母㊁消间隙螺母㊁弹簧㊁机架固定轴和机械限位开关全部要固定在滑块上ꎬ电机㊁丝杆㊁联轴器㊁极限片全部固定在导轨上ꎮ工作时ꎬ本研究将滚动直线导轨与关节型表座进行连接ꎬ通过表座实现空间任意角度的固定ꎬ利于打孔面的调整ꎬ只要有工作液浸泡则可工作ꎮ1.3㊀电路控制部分设计当电极与工件的距离大于基准距离时ꎬ电压比较电路的电路控制部分给出信号使步进电机旋转ꎬ向下进给ꎻ当电极与工件的距离小于基准距离时ꎬ电压比较电路不发出信号ꎬ电机停转ꎬ从而实现自动向下进给的功能ꎮ1.3.1㊀RC电路计算本机利用RC电路充电电压升高ꎬ击穿介质产生高温腐蚀金属材料的原理进行打孔ꎮRC脉冲放电过程如图2所示ꎮ图2㊀RC脉冲放电过程电压比较小时ꎬ击穿电压低ꎬ电容器释放能量很少ꎬ产生的温度较低ꎬ能量多集中在介质上ꎬ此时的放电频率很高ꎬ表面粗糙度良好ꎬ打孔效果很好ꎬ但是工作液因为节流作用压力非常大ꎬ刚度需求很高ꎬ且电源效率不高ꎮ当电压提升时ꎬ放电频率下降ꎬ电源效率提高ꎬ工作液压力下降ꎬ此时电源效率比较高ꎻ电压再加大时ꎬ频率低ꎬ而且工件的电解作用很大ꎬ电路效率降低了ꎮ所以电压需要在0~60V之间选择一个合适304 第4期蒋志强ꎬ等:基于单片机控制的便携式电火花打孔机的设计的值ꎮ进行电火花加工时ꎬ工具电极和工件分别接RC电源的两极ꎬ并浸入水中ꎮ控制工具电极向工件进给ꎬ当两电极间的间隙达到一定距离时ꎬ两电极上施加的电压将水击穿ꎬ产生火花放电ꎮ在放电的微细通道中瞬间集中大量的热能ꎬ温度剧增ꎬ工作液压力也有急剧变化ꎬ从而使这一 接触 点工作表面局部微量的金属材料立刻熔化㊁气化ꎬ并爆炸式地飞溅到工作液中ꎬ迅速冷凝ꎬ形成固体的金属微粒ꎬ被工作液带走ꎮ这时在工件表面上便留下一个微小的凹坑痕迹ꎬ放电短暂停歇ꎬ两电极间水恢复绝缘状态ꎮ紧接着ꎬRC充电ꎬ当电压又在两电极相对接近的另一点处击穿ꎬ产生火花放电ꎬ重复上述过程ꎮ这样ꎬ虽然每个脉冲放电蚀除的金属量极少ꎬ但因每秒有成千上万次脉冲放电作用ꎬ就能蚀除较多的金属ꎬ具有一定的生产率ꎮRC电路中R电阻用于充电限流ꎬ在本机中ꎬ这个电阻还可以在机器短路时保护电源ꎮ本机使用60Vꎬ10A电源ꎬ所以电阻应该大于6Ωꎮ功率大于600Wꎮ由于实际工作复杂ꎬ部分实际参数难以精确确定ꎬ也很难用模型直接估算ꎬ整机做出以后ꎬ直接通过调整不同阻值ꎬ对比试验打孔效果取得相应数据ꎮ本次通过测试确定ꎬ电压在40V时ꎬ效率比较高同时打孔质量可以保证ꎬ电容使用47μFꎬ电阻使用7Ω电阻ꎮ1.3.2㊀电压比较电路的设计电压比较器的功能:比较两个电压的大小(用输出电压的高或低电平ꎬ表示两个输入电压的大小关系)ꎮ当 + 输入端电压高于 - 输入端时ꎬ电压比较器输出为高电平ꎻ当 + 输入端电压低于 - 输入端时ꎬ电压比较器输出为低电平ꎮ可工作在线性工作区和非线性工作区ꎮ工作在线性工作区时特点是虚短ꎬ虚断ꎻ工作在非线性工作区时特点是跳变ꎬ虚断ꎻ由于比较器的输出只有低电平和高电平两种状态ꎬ其中的集成运放常工作在非线性区ꎮ从电路结构上看ꎬ运放常处于开环状态ꎮ考虑到为了使比较器输出状态的转换更加快速ꎬ以提高响应速度ꎬ一般在电路中接入正反馈ꎮ该电路功能为将60V电源电压分压得到一基准比较电压ꎬ将电极与工件之间的电压与此电压相比较ꎬ然后输出信号ꎮ基准电压调节范围约为6V-50Vꎮ通过计算ꎬ电压比较电路的设计如图3所示ꎮ图3㊀电压比较电路1.3.3㊀步进电机控制电路步进电机控制电路的设计AVR单片机输出能力极强ꎬ所以直接将3个IO口与步进电机信号口相连ꎬ电路图如图4所示ꎮ图4㊀步进电机驱动器接口电路1.3.4㊀按键输入电路通常的按键分为独立式按键和矩阵式按键两种ꎬ独立式按键比较简单ꎬ并且与独立的输入线相连接ꎮ由于本机只有3个按键ꎬ占IO口非常少ꎬ直接使用独立式设计ꎮ将按键连接在IO口与VCCꎬ分别为S1向下㊁S2向上㊁S3工作3个按键ꎮ按键电路如图5所示ꎮ图5㊀按键电路1.3.5㊀电极极限位置感应电路电极限位感应电路与按键输入电路相同ꎬ如图5所示ꎮ机器有6个状态ꎬ分别为待机㊁工作状态㊁上升㊁下404 机㊀㊀电㊀㊀工㊀㊀程第36卷降㊁上极限触发和下极限触发ꎮ输入分别为3个功能按键ꎬ3个输入口ꎮ按键S3为workꎬ按下按键时ꎬ机器执行打孔功能ꎬ并进入工作状态ꎮ按键S2为upꎬ按下时会取消工作状态ꎬ并且上升ꎬ保持上升状态ꎬ松开时自动回到待机状态ꎮ按键S1为下降ꎬ按下时会取消工作状态ꎬ并且下降ꎬ保持下降状态ꎬ松开时自动回到待机状态ꎮ上极限触发时ꎬ机器进入上极限触发状态ꎬ此时只可转变到下降状态ꎬ当上极限触发信号消失时ꎬ机器自动复位到待机状态ꎻ下极限触发时ꎬ机器进入下极限触发状态ꎬ此时只可转变到上升状态ꎬ当下极限触发信号消失时ꎬ机器自动复位到待机状态ꎮ最后进行电压对比结果信号口ꎬ单片机由此确定是否需要进给ꎮ输出口分别为LED显示㊁步进电机控制ꎮ3个LED分别为:LED1ꎬLED2ꎬLED3ꎮLED1在工作状态点亮ꎬLED2在上升状态点亮ꎬLED3在下降状态点亮ꎮ步进电机控制口分别为脉冲信号和方向信号ꎬ一路接步进电机驱动器脉冲信号口ꎬ一路接步进电机驱动器方向信号口ꎮ整个电路控制系统的流程图如图6所示ꎮ图6㊀电路控制系统的流程图2㊀实验测试与结果通过实验设置相关的参数ꎬ电火花打孔机实物图如图7所示ꎮ图7㊀便携式电火花打孔机整机图1-表座ꎻ2-执行机ꎻ3-工作液ꎻ4-按键与指示灯ꎻ5-电流显示表ꎻ6-电压显示表实验测试数据如表1所示ꎮ表1㊀实验测试数据组别直径/mm深度/mm打穿时间/s材料去除率/(mm3 min-1)深径比电极工作液10.51180.652实心浸泡20.50.580.731实心浸泡3211512.560.5实心强制冲液421016811.212实心强制冲液5414815.70.25实心强制冲液64420814.491实心强制冲液7518713.530.2实心浸泡85437212.660.8实心浸泡981570.125空心浸泡10842410.5空心浸泡1191670.11空心浸泡㊀㊀机器打孔效果测试参数为:电压40Vꎬ电阻7Ωꎬ电容40μFꎻ工作液为自来水ꎻ电极均为黄铜圆形电极ꎮ在不同的深度㊁打孔直径㊁电极和工作液下ꎬ经过测试ꎬ得到的11项测试数据如表1所示ꎮ最小穿孔直径为0.5mmꎬ最大穿孔直径达到9mmꎬ材料去除率大于15mm3/minꎬ最大深径比为5ꎮ实验表明:该电火花打孔机在40V工作电压时ꎬ加工效率可达14.5mm3/minꎬ可以对各种金属进行打孔ꎻ底座为千分表ꎬ可以实现对一些特殊位置进行打孔ꎮ504第4期蒋志强ꎬ等:基于单片机控制的便携式电火花打孔机的设计便携式电火花打孔机对1.5mm厚白钢板(型号Q225)穿孔效果图如图8所示ꎮ图8㊀便携式电火花打孔机穿孔效果图3㊀结束语针对目前便携式电火花打孔机的现状ꎬ本文分别对执行机构㊁打孔面调整装置和放电回路等进行了优化ꎬ并制造出了基于单片机控制的电火花打孔机ꎮ测试结果表明:(1)该打孔机采用滑块静止导轨运动的运动模式ꎬ便携㊁工作稳定㊁执行效果好ꎻ(2)关节型千分表座作为打孔面调整装置ꎬ与安装滚动直线导轨上的执行机构直接相连ꎬ可实现空间任意角度的固定ꎬ有利于特殊位置打孔ꎻ(3)直接通过RC比较电路ꎬ简化了放电回路ꎬ可很好实现自动进给功能ꎬ材料去除率较高ꎬ可进一步降低生产成本ꎻ(4)设备尺寸小ꎬ实际工作电压只需40Vꎬ更便携㊁安全ꎬ可置于桌面直接用于教学演示ꎮ参考文献(References):[1]㊀林启明.新型便携式电火花穿孔机研制[J].机电工程技术ꎬ2011ꎬ40(8):93 ̄95ꎬ203[2]㊀张㊀昆.电火花加工技术在航天领域的典型应用及发展需求[C].特种加工技术智能化与精密化 第17届全国特种加工学术会议ꎬ北京:中国机械工程学会ꎬ2017.[3]㊀颜国正ꎬ赵国光ꎬ余承业.便携式电火花穿孔机性能研究[J].航空制造技术ꎬ1996(3):32 ̄34.[4]㊀第十三届中国国际模展评定评述专家组.第十三届中国国际模具技术和设备展览会现代模具制造技术及设备评述[J].模具工业ꎬ2010ꎬ36(11):1 ̄10.[5]㊀刘向前ꎬ刘永乐.便携式电火花机在风电制动钳通油孔加工中的应用[J].金属加工:冷加工ꎬ2014(7):71 ̄72.[6]㊀王㊀彤ꎬ张广志.电火花间隙放电状态检测方法综述[J].哈尔滨理工大学学报ꎬ2012ꎬ17(3):100 ̄104.[7]㊀俞㊀晓.便携式电火花取断丝锥机[P].中国:CN302527161Sꎬ2013.[8]㊀刘向前ꎬ张少波ꎬ丁向阳.Portableelectricsparkmachineguidingdevice[P].中国:CN203526739Uꎬ2014.[9]㊀丁向阳ꎬ张少波.Portabletypespark ̄erosiondrillingma ̄chine[P].中国:CN103878459Aꎬ2014.[10]㊀刘晋春ꎬ韦东波ꎬ自鹏翰ꎬ等.便携式㊁多功能㊁模块化㊁小型数控电火花加工机床系列的开发研制[J].电加工与模具ꎬ2015(6):55 ̄58.[11]㊀WANGXue ̄tao.DesignofportableEDMmachinetool[C].InternationalSymposiumonKnowledgeAcquisitionandModelingꎬNewYork:IEEEꎬ2015.[12]㊀邹㊀纯ꎬ祝锡晶ꎬ崔学良ꎬ等.工件超声振动对不同放电间隙电火花加工的影响[J].科学技术与工程ꎬ2018ꎬ18(1):222[编辑:周昱晨]本文引用格式:蒋志强ꎬ陈虎城ꎬ龙向前ꎬ等.基于单片机控制的便携式电火花打孔机的设计[J].机电工程ꎬ2019ꎬ36(4):402-406.JIANGZhi ̄qiangꎬCHENHu ̄chengꎬLONGXiang ̄qianꎬetal.PortableEDMpunchingmachinebasedonsinglechipmicrocomputercontrol[J].JournalofMe ̄chanical&ElectricalEngineeringꎬ2019ꎬ36(4):402-406.«机电工程»杂志:http://www.meem.com.cn604 机㊀㊀电㊀㊀工㊀㊀程第36卷。
基于双MCU的数控锁芯钻孔机床控制系统设计

19科技创新导报 Science and Technology Innovation Herald 技 术 创 新数控锁芯钻孔机床是一款专用的小型数控加工系统,其性能要求主要体现在加工精度和加工效率上,无需高端数控系统的复杂曲线计算能力和图形界面,因此,设计一个由低成本的单片机组成的控制系统即可满足系统要求。
本方案设计了一款基于双MCU组成的控制系统,具有成本低、体积小、实时性强,人机界面友好等特点,能够很好的满足系统的控制要求。
1 数控锁芯钻孔机床结构及工作原理本案机床设计为三轴双动力主轴结构,运动机构由X 、Y 轴控制的水平工作台和Z轴控制的垂直钻孔机构组成,X、Y、Z三轴由三只步进电机驱动,以实现三坐标精确定位控制。
水平工作台上X方向并列安装两组双工件气动夹具,一组夹具可同时安装两只锁芯,两组双工件气动夹具通过气动阀分别独控制各组的工件上料、加工锁定和下料;Z轴上安装两只高速变频动力主轴,驱动两只钻头,用于同时加工同组的两只锁芯。
通过控制X轴步进电机定位加工组坐标(X坐标),控制Y轴步进电机定位加工组的锁芯孔位坐标(Y坐标),控制Z轴步进电机进行设定深度的钻孔加工(Z坐标)。
机床通过对上述机构的协调控制,以一组加工一组上料的交替工作方式,一次同时加工两只锁芯,从而实现了机床高精度、高效率的锁芯钻孔加工要求(如图1)。
2 控制系统的硬件设计2.1控制系统方案由机床结构及其工作原理得知,本控制系统需要对X 、Y 、Z 轴上的三只步进电机、两只用于钻孔的高速主轴电机以及两组气动夹具进行有机联动控制。
出于控制系统的成本和控制实时性要求考虑,本案控制系统采取双M C U 系统设计,M C U 1系统负责面板显示和按键处理,M C U 2系统负责加工数据处理和运动控制,M C U 1系统与MCU 2系统之间采用双向全双工串行通信方式实行数据交换,如图2所示。
设计M C U 1单独处理系统界面工作,可有效减轻M C U 2控制运算压力,同时其富裕的运算能力也可使界面设计得更友好。
基于单片机的智能钻床控制系统研制

第6期(总第151期)2008年12月机械工程与自动化M ECHAN I CAL EN G I N EER I N G & AU TOM A T I ON N o 16D ec 1文章编号:167226413(2008)0620134203基于单片机的智能钻床控制系统研制彭淑华,石剑锋(南通职业大学机械工程系,江苏 南通 226007)摘要:目前智能系统常采用PL C 来进行控制,成本较高。
通过对Z 5030A 钻床特点和控制要求进行分析,采用单片机来进行控制,设计了相关驱动接口电路和控制软件。
实际运行表明该系统取得了良好效果。
关键词:钻床;单片机;光电耦合中图分类号:T G 527 文献标识码:A收稿日期:2008204214;修回日期:2008206220作者简介:彭淑华(19662),女,江苏如皋人,高级工程师,本科。
0 引言利用简单立式钻床进行钻孔几乎遍及了整个机加工企业,它们多为继电器、接触器控制,其控制简单、造价低,但要人工辅助操作完成。
当工件要求钻孔较多、较复杂、孔距要求均匀分布时,很难达到要求,且劳动强度大,有一定的危险性。
目前钻床系统的自动化改造主要是采用PL C 控制系统,由于PL C 价格比较昂贵,增加了改造成本,制约了钻床自动化改造的规模。
本文采用51单片机作为控制系统,以Z 5030A 型钻床为平台进行改造,改造后实现了自动装夹、自动进给、自动加工等,可自动完成对一个工件的加工,提高了生产效率和产品质量。
1 机械控制系统调整首先在原钻床工作台上增加具有自动二维运动的钻夹台(夹持被加工件做轴向移动和绕轴转动),用2个步进电机分别驱动,这也就是工件准确定位系统。
此外,在夹具上增加一接近开关来检测夹具上是否有料;在夹紧V 形块下增加步进电机驱动的丝杠机构,并在V 形块内侧增加压力传感器以实现自动夹紧;还增加了钻头自动到上、下位和夹台到原点的距离可调整的接近开关。
钻头旋转及转速选择等仍由原有的电器和机械调节控制。
数控钻孔机控制系统设计

金华职业技术学院JINHUA COLLEGE OF VOCATION AND TECHNOLOGY毕业教学环节成果(2014届)题目数控钻孔机控制系统设计学院信息工程学院专业电气自动化技术班级自动化112学号201134010350201姓名指导教师2013年12月25日金华职业技术学院毕业教学成果目录摘要 (1)英文摘要 (1)引言 (2)1 数控钻孔机系统简介 (3)2硬件设计 (4)2.1 控制系统结构及工作原理 (4)2.2 主要器件选型 (5)2.3 PLC外围接线图 (6)2.4 控制系统设计原理图 (8)2.5 I/O口分配表 (8)3触摸屏界面设计 (9)4软件设计 (12)4.1 程序流程图 (12)4.2 控制程序的设计 (12)4.3 外围软件信号 (17)5参数整定 (17)5.1伺服电机定位参数设置 (17)5.2伺服系统内部参数设定 (19)6安装与调试 (20)6.1 控制系统接线图 (20)6.2模拟调试 (22)6.3 联机调试 (22)结论与谢辞 (22)参考文献 (23)附件1 (24)元器件清单 (24)附件2 (25)源程序 (25)附件3 (34)实物图 (34)数控钻孔机控制系统设计摘要:本文介绍了基于三菱Q系列PLC的数控钻孔机控制系统,该系统选用昆仑通态TPC7062KS嵌入版的触摸屏来实现人机交互,文中不但给出了数控钻孔机的基本架构,而且还简单分析了钻孔机控制系统的控制系统结构及工作原理与传感器的使用,以及介绍了PLC I/O口及钻孔机控制系统的布局图与接线图。
关键字PLC 钻孔机伺服控制Control system design of NC drilling machine(Information Engineering College of electrical automation technology Jin Ming) Abstract:This paper introduces the control system based on CNC drilling machine Mitsubishi Q series PLC, this system adopts KunLun on state of TPC7062KS embedded touch screen to realize man-machine interaction, this paper not only gives the basic architecture of the CNC drilling machine, but also a simple analysis of the use of drilling machine control system to control the system structure and the work principle and sensor, and introduced PLCI/O port and drilling machine control system layout and wiring diagram.Keywords: PLC drilling machine servo control引言数字控制(Numerical Control)是数字化信号对机床运动及其加工过程进行控制的一种方法,简称数控(NC)。
基于PLC三面钻孔控制设计

基于PLC的飞轮壳三面钻孔专用机床控制系统设计摘要:随着电子与信息技术的不断发展,给我国机床加工设备的现代化提供了强有力的技术支持。
用PLC模块、操作监控设备等组成电气控制系统,以实现编程输入、人机交互、自动化加工的控制方式,扩大加工能力,减少故障,提高效率,己成为企业进行技术改造的有效途径。
可编程序控制器(PLC)应用于三面钻孔专用机床电气控制系统的设计思想作了介绍。
对系统的硬件组成和软件设计作了较为详细的阐述。
通过上位计算机可对机床的现场状态实施监控和对工作参数进行调整,使系统工作在最佳状态。
设计了一套由PLC、多台电动机等主要设备构成的全自动三面钻孔机床控制系统,具有全自动运行及手动控制等功能。
系统有效地解决了传统机床中存在的问题,并具有多种辅助功能,增强了系统的可靠性。
在具体的设计中,首先介绍了三面钻孔机床控制系统的研究背景和意义,提出了三面钻孔机床控制系统的现状与发展前景,然后根据设计要求,提出了设计方案,并对控制原理进行分析,接着完成了系统硬件设计,在硬件设计中包括PLC的选型、主电路的设计和I/O接线图设计。
最后加上软件的设计使整个系统得以正常的运行。
控制器选择三菱公司的FX2N系列,其功能强大,编程简单,具有丰富的扩展模块,是目前市场上性价比比较高的可编程控制器。
此控制系统与传统的相比大大提高了加工的精确度和灵活度,使加工起来更加方便。
关键词:可编程序控制器;钻孔;FX2N;监控Design of Control System for Flywheel Housing Three Drilling Special Machine Based on PLCAbstract :With the electronic and information technology continues to evolve,to the modernization of China's machine tool processing equipment provides a strong technical support. With the PLC module,operating monitoring equipment,electrical control system etc.,to achieve the programmed input,human-computer interaction,automated processing,control,expansion of processing capacity,reduce failures,improve the rate of technological transformation of enterprises has become an effective way.Programmable Logic Controller (PLC) used in Three Drilling Special Machine tool electrical control system design was introduced. The system's hardware and software design of more detail. Through the host computer can be implemented on the state of the machine on-site monitoring and adjustment of operating parameters, the system is in the best condition. Designed a set by the PLC,several motors and other major equipment consisting of reaming machine automatic Three Drilling control system with operation and manual control. System to effectively solve the problems of traditional machine tools,and has a variety of auxiliary functions,enhanced system reliability.In the specific design,first introduced the control system of triple-sided machine reaming the research background and significance of the proposed triple-sided reaming machine control system status and development prospects,and according to design requirements,proposed design,and analysis of control theory,and then completed the hardware design,hardware design,including the selection of PLC,the main circuit design,I / O wiring diagram design and selection of other necessary components. Last added software designed to make the whole system to normal operation. Controller selects Mitsubishi FX2N series,its powerful,simple programming,with extensive expansion modules,is currently on the market relatively high cost programmable controller. This control system has greatly enhanced compared to traditional processing accuracy and flexibility,so that processing more convenient.Key words:PLC; Reaming; FX2N;Monitor目录1.飞轮壳三面钻孔专用机床控制系统设计的概述 (1)1.1 三面钻孔机床控制系统在国民经济的地位 (1)1.2三面钻孔机床控制系统的国内外现状 (2)1.3三面钻孔机床控制系统设计的目的、内容、要求 (2)1.3.1设计目的 (2)1.3.2设计内容 (2)1.3.3设计要求 (3)2飞轮壳三面钻孔专用机床的工作原理及电气控制要求 (3)2.1飞轮壳三面钻孔专用机床的工作原理 (3)2.2电气控制要求分析 (5)2.3自动控制系统方案的确定 (5)2.3.1飞轮壳三面钻孔专用机床自动控制系统总体方案确定 (5)2.3.2液压站PLC控制系统 (6)2.3.3电动机PLC控制 (6)3 PLC控制系统硬件设计 (7)3.1 PLC介绍及选型 (7)3.1.1 PLC的介绍 (7)3.1.2 PLC的选型 (7)3.2 电源分配 (8)3.3 主电路设计 (9)3.4 PLC I/O接线图设计 (10)3.5 控制面板设计 (12)3.6 其他元器件的选择 (12)4 PLC控制系统软件设计 (14)4.1 I/O地址分配 (14)4.2梯形图的绘制以及分析 (18)5 PLC控制系统仿真实验 (35)6 PLC控制系统组态监控 (39)6.1组态软件简介 (39)6.2组态软件选择 (39)6.3组态的仿真实验 (39)7 结束语 (44)7.1总结 (44)7.2展望 (44)参考文献 (45)致谢 (46)附录 (47)附录1:电源分配图 (48)附录2:主电路图 (49)附录3:输入输出接线图 (51)附录4:输入输出接线图 (52)附录5:控制面板图 (47)盐城工学院本科生毕业设计说明书( 2012)基于PLC的飞轮壳三面钻孔专用机床控制系统设计1.飞轮壳三面钻孔专用机床控制系统设计的概述组合机床及其自动线在当今机械制造业中扮演着越来越重要的角色,其技术性能和综合自动化水平在很大程度上决定着相关部门的发展。
基于某PLC地两工位钻孔攻丝组合机床控制系统设计

基于PLC的两工位钻孔攻丝组合机床控制系统设计摘要随着机床行业和控制技术的不断发展与进步,根据生产的实际需要,机床的升级改造已成为一种新兴的行业。
通过对现有机床的全部或局部结构进行改造,来提高机床的各项技术指标,对于实现资源的合理利用和促进经济增长起到重要的作用。
本课题主要研究的是采用PLC控制两工位钻孔攻丝组合机床的动作。
两工位钻孔攻丝组合机床通电后能自动完成工件的钻孔和攻丝加工。
在传统的控制系统的设备中,通常采用的是继电器控制,这种控制系统可靠性低,而采用PLC进行控制改造后,系统可靠性明显提高。
本次设计的重点在于控制系统的硬件设计,根据工艺要求选择了控制系统所需要的电气元件,绘出电力拖动系统的主回路电路图、PLC的外部接线图。
论文根据机床的加工要求设计了PLC控制的程序,以及对机床的调试进行了简要的概括。
关键词: PLC控制程序设计调试组合机床The Design Of The Control System Of two worktables drilling tapping combination machine Based On ThePLCABSTRACTAlong with the development of machine tool industry and technology continues to progress according to the actual needs of the production machine ,upgrading has become a new growth industry based on the existing machine tools in whole or in part the structure upgrades to improve machine tool technology index. To achieve rational use of resources and promote economic growth plays an important role in.This topic main research is to use PLC to control two worktables drilling tapping modular machine tool operation. Two worktables drilling tapping modular machine tool by the system can automatically complete the workpiece. In the control system of the traditional is commonly used in the relay control, and this control system reliability is low, but when it is controlled by a PLC transformation, system reliability is obviously improved.The focus of this design is that the control system hardware design, according to the process requirements of electrical components control system requires the choice, Drawing the external wiring diagram of main circuit diagram and the PLC electric drive system. This paper designs a PLC control program according to the machine processing requirements, and commissioning of the machine are summarized.KEY WORDS:PLC control The program design debug Combinationmachine tools前言两工位钻孔攻丝组合机床主要用来给工件钻孔和攻丝的,是人类经济和社会发展的重要工具之一。
PLC下的矿井钻机控制系统设计-系统设计论文-设计论文

PLC下的矿井钻机控制系统设计-系统设计论文-设计论文——文章均为WORD文档,下载后可直接编辑使用亦可打印——摘要:为了适应煤矿装备的智能化、自动化潮流,以某型矿井钻机为研究对象,对矿井钻机主要结构进行分析,基于CAN总线、PLC 及PID设计了矿井钻机控制系统,并对控制程序进行研究。
结果表明,该系统能较好地实现对矿井钻机自动化和智能化控制,为矿井钻机及其他煤矿装备控制系统设计及智能化升级提供理论依据及技术参考。
关键词:矿井钻机;PLC;控制系统;设计1矿井钻机的结构组成矿井钻机主要用于煤矿井下钻探各种角度的煤层放水孔、瓦斯抽排放孔、地质孔、注浆灭火孔、地面钻探地质勘探孔及其他用途的各种工程孔。
本文研究的矿井钻机主要为煤矿井下全液压钻机,其主要结构如图1所示。
由图1可知,矿井钻机主要由钻具、机架、动力头、机座、操作台、泵站及轨道等部件组成,并包含液压系统及电控系统。
液压系统主要由齿轮液压泵、液压马达、防爆电机、节流阀、溢流阀、多路阀、油缸、油箱、压力表、过滤器、冷却器、液压油管、快速接头、液压卡盘、夹持器等主要零部件组成。
2矿井钻机控制系统总体设计根据矿井钻机结构,设计了矿井钻机控制系统,其结构框图如图2所示。
由图2可知,齿轮液压泵的实际压力决定了液压泵驱动电机的最大输出功率,且两者之间的关系基本呈现比例关系,液压泵压力越高,电机输出功率越大。
在矿井钻机控制系统中,PLC控制器通过J1939协议和通信规则,读取和获得液压泵驱动电机的实时工作状态,如电机输出功率、扭矩、转速、温度等关键参数,进而对电机转速进行精确控制。
液压泵驱动电机带反馈及对应的执行器。
控制系统直接与显示屏连通,可以实时地将关键参数可视化地显示出来。
矿井钻机控制系统的控制中心还可以读取和处理其他电控检测元件的数据,对其他电控执行元件进行控制,从而实现对矿井钻机的实时精确控制。
CAN是ISO国际标准化的串行通信协议。
在智能化、自动化设备行业中,对设备的舒适性、安全性、低功耗、方便性、低成本等方面的要求越来越高,多功能、智能化的各种电控系统层出不穷。
电路板数控钻孔机的研制

电路板数控钻孔机的研制刘建春(厦门理工学院)吴道坚摘要现在电路板一般采用专业软件如PROTEL进行辅助设计,印制电路板后一般需钻孔。
钻孔有的采用普通钻床手工钻孔,有的采用专用数控钻床加工,前者速度慢、精度差,后者成本太大。
本文介绍一种经济型的电路板数控钻孔机的研制,非常适合中小型企业厂家、学校及个人科研开发使用。
它是通过计算机把PROTEL产生的钻孔数据传送给单片机,然后利用单片机控制微型台式钻孔机的X、Y 轴的步进电机移动和Z轴电机的升降运动,实现电路板全自动数控钻。
实验表明,采用该设备可大大提高钻孔速度和精度。
随着我国电子工业的快速发展及集成电路的广泛应用,对印刷电路板的精度要求越来越高,传统的手工钻孔加工工艺已明显不能适应时代的要求。
虽然目前也有专门用来加工电路板的数控钻床,但它只适用于专门从事印刷电路板的大型厂家,而对于一些小批量生产的厂家和开发电路板的科研单位,花费几万、甚至几十万去购买这些设备是不经济的。
当然,也可以订做电路板,但存在批量少、价格贵、时间长等问题。
针对这一现状,我们研制出由单片机控制的集成电路板数控钻孔机。
该数控钻孔机具有体积小、功能强、成本低、精度高的特点。
本机主要供中小型企业、学校及个人科研开发使用。
本数控钻孔机的下位机控制系统采用A T89C51单片机控制,主要作用是存贮钻孔的数据,并控制相应孔的加工。
基于成本考虑,该系统采用开环控制系统。
以下分别介绍上位机程序设计、下位机控制系统的硬件电路设计和软件设计以及钻孔机的结构设计。
一、上位机控制系统设计在开发电路板数控钻孔机中,我们使用了Visual Basic 6.0在Windows98环境下开发上位机(PC机) 控制软件。
首先运行PROTEL软件,打开相应电路板的PCB图,产生的钻孔数据。
接着运行上位机控制软件,把PROTEL产生的钻孔数据(数控语言格式)转化为X坐标、Y坐标、孔径大小的格式,并把10进制的数据转为16进制的数据,然后通过RS-232C串行口以十六进制数形式传送到下位机。
专用钻床钻孔PLC设计

石家庄铁道大学四方学院集中实践报告书课题名称专用钻床钻孔PLC 设计 姓 名 ** 学 号 2012**** 系、 部电气工程系 专业班级方**** 指导教师李**2014年12月31日※※※※※※※※※ ※※ ※※※※※※※※※※※※※ 2012级 PLC 课程设计目录第1章设计目的 (1)第2章设计要求 (1)第3章I/O分配表和接线图 (1)3.1PLC选型 (1)3.2I/O分配表 (2)3.3I/O接线图 (2)第4章PLC程序设计 (3)4.1梯形图设计 (3)4.2指令语句表 (4)第5章设计总结 (4)参考文献 (5)第1章设计目的熟悉常用控制电器的结构原理、用途,达到正确使用和选用的目的。
掌握电气控制电路的基本环节,具备阅读和分析电气控制电路图的能力。
具备独立设计简单电气控制电路的能力。
熟悉掌握PLC的工作原理与系统构成、指令系统、编程方法及PLC控制系统的设计。
具备应用PLC实现电气控制自动化要求的设计、安装、调试、故障处理能力。
第2章设计要求1)初始状态时,大小钻头位置均在上限X3=1(大),X5=1(小);2)工件放好后,按下启动按钮X0=1,工件被加紧,Y0置1;3)当压力继电器X1=1时,大钻Y1、小钻Y3开始钻孔;4)当大小钻分别到达深度X2=1,X4=1时,大小钻开始上行,回到初始位置,此时,计数器C0加1;5)若没有钻完3对孔,则工件旋转120度Y5=1,旋转到位X6=1,又开始第二次钻孔;6)3对孔钻完,工件松开Y6=1,松开到位X7=1,系统返回初始状态。
请画出顺序功能图和梯形图。
第3章I/O分配表和接线图3.1plc选型三菱公司近年来推出的FX系列PLC有FX0、FX2、FX0S、FX0N、FX2C、FX1S、FX1N、FX2N、FX2NC等系列型号。
FX0S的功能简单实用,价格便宜,可用于小型开关量控制系统;FX0N可用于要求较高的中小型控制系统;FX2N的功能最强,可用于要求很高的系统。
- 1、下载文档前请自行甄别文档内容的完整性,平台不提供额外的编辑、内容补充、找答案等附加服务。
- 2、"仅部分预览"的文档,不可在线预览部分如存在完整性等问题,可反馈申请退款(可完整预览的文档不适用该条件!)。
- 3、如文档侵犯您的权益,请联系客服反馈,我们会尽快为您处理(人工客服工作时间:9:00-18:30)。
南通职业大学学报
!"#$%& ’"$(
,--. 年 %, 月 )*+$,--. /012’34 05 ’3’60’7 !083690’34 8044:7: 第!期 !!!!!!!!!!!!!!!!!!!!!!!!!!!!!!!!!!!!!!!!!!!!!!!!!!!!!!!!!!
* 结束语
本系统不但可用于控制钻孔机床,而且可用 于冲床及电焊机等要求确定位置的场合。
,!- 查纯古 . 微机控制定位钻孔装置 ,6-. 电气自动化 2(77"2 8(9. ,*- 黄 一 夫 . 微 型 计 算 机 控 制 技 术 ,/-. 北 京 + 机 械 工 业 出 版 社 2 (77"+47$5".
474
步进电机驱动电路 单片机根据加工程序发出控制步进电机的进
%;! 输出动力头步进电机的控制命令,当动力头
到达切削面时, 再启动切削电机进行切削工作。 当 动力头完成钻孔程序并复位后,立即通过收信电 单片机接收后 路向 %(0 输入步进电机进给信号, 继续执行下一个孔位的进给命令。当控制 9 向和
收稿日期: "##$%&#%&$
-./(0$" 内 部 的 内 存 用 以 存 放 系 统 监 控 程
序。打孔次数显示采用三位七段发光二极管显示 。选用 0736 显示驱动器 70&!!(( 作为 器 (59:) 显示接口, 显示方式为硬件动态扫描式。7-8)(#
作者简介: 唐德礼 ’&(!)% *, 男, 副教授, 从事自控和单片机的教学及研究。
将 /, 1 现行励磁状 态字拼成一字输出
化、 / 向、 1 向和 % 向步进电机状态初始化、由程 序定义的各标志寄存器单元与计数单元的初始 化。程序框图如图 ! 所示。
&"’’ 初始化
$#"#$
加工处理程序*,+ 加工处理程序自动完成各钻孔工位进给及动
图!
转显示 初始化程序框图
力头进给系统的控制。加工处理程序的算法采用 逐点比较直线插补法, 按照插补法计算要求, 每条 加工指令应包括以下内容: / 轴坐标值、 1 轴坐标 值、 总步数 4、 进给速度选择 (% 步进电机) 和加工 结束指令等。由于 / 向、 1 向和 % 向的步进电机 运动皆为直线,因此每条加工指令由 ! 个字节组 成, 第 " 个字节为 / 轴坐标值; 第 $ 个字节为 1 轴坐标值; 第 , 个字节为总步数 4; 第 ! 个字节为 (全 ") 。当单片机检测到全 “"” 时结束本次加 556 工。 每一个加工点都要按此要求编程序, 然后将其 写入 789 中, 在加工时调用。加工处理程序如图 由 $ 号键启动。 ’ 所示, $#"#, 点动处理程序 本系统用点动程序来解决拖板进给的点动操 作, 以便于校机和定位。 用 !, ’, -, . 号键来分别定 义 /, 0/, 1, 01 方向的点动进给按钮。点动程序 由 " 号键启动。
*:
> 向步进电机
图& 拖板 切削动力头 动力头进给方向
8 向步进电机
8 进给方向 > 进给方向
系统机械结构图
&
系统硬件设计
+&,
狗电路” 等组成。
单片机控制系统的原理图如图 " 所示。 整 个 系 统 硬 件 电 路 由 单 片 机 -./(0$" 及 并 行 1 2 3 芯 片 /&$$、 键 盘 接 口 芯 片 4!56&)!、 显示 接口芯片 70&!!(( 及 7-8)(# 电压监控、 “看 门
给命令,由 .4##( 的 %(":%(# 口及 %;":%;! 输 出,经接口电路和驱动电路加到步进电机的各相 绕组。 步进电机采用三相六拍工作方式, 其各绕组 与 .4##%( 口的对应关系是:
%(" !9(, %(4 !9;, %(! !9$, %;" !<(, %;4 !<;, %;! !<$, %(6 !=(, %(1 !=;, %(# ! =$ 其中 9(、 9;、 9$ 分别是 9 向步进电机的 (、 ;、 $ 相绕组, =(、 =;、 =$ 分别是 = 向步进电机的 (、 ;、 $ 相绕组, <(、 <;、 <$ 是 < 向步进电机的 (、 ;、 $ 相绕组,单片机的控制程序要保证各相绕组 的供电顺序是: ( !(; !; !;$ !$ !$( !(777。 61
=
驱动
接口
%(, 8+ %(4 ’8 %(! $A %(6 B/,@ %(1 (2A %(# +" %(5 %(0 +0 %$" %$4 %$! %;" %;4 %;!
驱动 驱动
接口 接口
<
驱动
接口
E#> 84 %AB 8!
地
8A3A) %A, ’&! 系统硬件框图
4 ,3$ ! 6
第!期
唐德礼: 基于单片机控制的钻孔机构的设计
"#$
动力头进给系统 当工件进给到加工工位后,在钻孔切削程序
初始化程序
的控制下, 动力头完成打孔任务。 根据加工工艺要 求, 动力头的进给程序如下: 当动力头系统收到单片机发出的钻孔信号 后,先启动 % 向动力头步进电机和切削电机, 然 后快进到工作钻孔面。 当刀具接触到加工面时, 动 力头减速为慢速进给切削。 当切削深度到位后, 再 以慢速退出加工工件。 当刀具脱离工件后, 立即快 速退至原始位置,切削电机停止,并发出复位信 号,等待下一个钻孔信号。切削电机的驱动由
==
南 通 职 业 大 学 学 报
!""# 年 E#> 8
向 电 机 向 电 机 切 削 电 机 向 电 机
9
.4##(
驱动 接口
4号 !号 6号 1号 #号 5号 0号 .号 8+ %671 ’8 %!70 %!7" (2A +" +0 %67" %674 %67# + $2G AD ().C$#! 8A3A) BD)" %47" @$411CC 4H !H 6H ( 6 4F! . 0123451 1 # 5 4" 44 4! 46
转相应的程序 图, 主程序框图 显示 键盘扫描
:
有键按下吗?
1
查键值表
&"’’ 的 () 口组成的逻辑电路完成。
$
系统软件设计
*$+
系统软件采用模块化结构, 便于编程、 调试、 修改和扩展。整个程序由主程序和四个专用程序 组成。 这四个专用程序是: 初始化程序、 点动程序、 加工处理程序和回零处理程序。后三个程序分别 由 ", $, , 号键启动,用程序定义 !, ’, -, . 四个键 分别为 /, 0/, 1, 01 向的进给按钮, & 号键为打孔 数设置按钮。
$#"#! 回零处理程序
回零处理程序的任务是保证拖板在任何位置
,’
南 通 职 业 大 学 学 报
!""# 年
启动
加工孔数显示
取操作码
循环?
’
循环加工子程序
)
回零?
’
调回零子程序
)
打孔?
’
发孔打信号
打孔结束?
)
加工孔数减 (
) $% 向步进? ) &% 向步进? ) $’ 向步进? ) &’ 向步进? )
= 向步进电机带动拖板到达第二个加工孔位后,
再重复上述控制过程,直到把所有的孔加工完成 为止。9 向和 = 向步进电机通过驱动电路和接口 电路与 .4##%( 口连接, 置为输出方式。< 向步进 电 机 通 过 驱 动 电 路 和 接 口 电 路 与 .4## 的 %; 口 连接, 也置为输出方式。 动力头进给控制的应答信 号 通 过 接 口 电 路 与 .4## 的 %(5 和 %(0 口 相 连 接, 置为位控制方式。
!"#"$%&’ () *%+,,+-. /$&’+-" 0$#"1 ($ 2+-.," 3’+4 5%(&"##(%
$% &’ ()*+, -()./012)31 45 6+)71043,78 639,3))0,39: ;<,=/3 $)7<3,7/ >381,1?1): ;<,=/3: @?A), BBCDDDE 67#8%$&89 $<) F)8,93 /3F 0)/+,G/1,43 45 F0,++,39 2/7<,3) A/8)F 43 1<) 7<,. 45 2,704*742.?1)0 743104++)0 /0) .0)8)31)F ,3 1<,8 ./.)0: </0FH/0) /3F 8451H/0) /0) /+84 9,I)3J :"; <(%1#9 / 7<,. 45 2,704*742.?1)0K F0,++,39 2/7<,3)K .0490/2 743104+K 81)..)0
各相的接口电路采用光电耦合方式,驱动电路采 用晶体管放大电路。 各相的供电电压为 1" > 直流 电源。 系统的工作过程如下: 加工工件的各钻孔位置和钻孔的过程通过编 程输入到单片机内部 ?2(3*8,@ 中,在程序的 控制下,单片机通过 .4## 接口输出控制信号, 经 接口电路和驱动电路控制 9 向和 = 向步进电机, 带动拖扳步进到各加工位置。同时发出钻孔应答 信号从 .4## 的 %(5 输出,经接口电路和驱动电 路控制动力头进行钻孔工作。 这时单片机从 %;":