转炉托圈层状撕裂的预防措施
转炉托圈装配的故障分析及处理

根据 上 面 所 述 , 理 这 一 故 障 的 关 键 是 制 止 销 子 继 续 处
外 窜 。 了有 空 问 处 理 故 障 , 为 在正 对 耳 轴 处 将 炉 子外 壳 割 开
一
个 大孔 。因 设 备 本 身 重 量 大 , 住 销 子 的 力 大 . 图将 销 卡 试
子 退 回销 孔 的 努 力 没 有 效 果 。 来 将 销 子 露 出 部 分 割 去 , 后 在
耳轴座端 面焊 一个直 径为  ̄2 8 0的 堵 板 , 住 销 子 , 板 除 封 堵
在 圆 周 上 跟 耳 轴 座 焊 死 外 , 在堵 板 径 向焊 8 卡板 , 再 个 以帮
助堵 板 受 力 , 止 销 子 外 窜 。 阻
4 2 销 子 强 度 校 核 .
前 面 己经 述 及 , 3个 骑 缝 圆 柱 销 不 仅 起 定 位 作 用 , 这 还
且过盈 量还 是较 大 的, 大过 盈量 为 0 12 最 . 3 mm, 小 过 盈 最
量为002 . 9mm 。这 个 过 盈 配 合 的 目的 不 仅 是 让 销 子 本 身 装 配 牢 固 , 时 也 靠 销 子涨 紧 , 传 动 耳 轴 与托 圈 耳 轴座 装配 同 使
的 轴 向 、 向 定 位 牢 固 。 销 修 周 从
图 3 销子外窜受力分析
1 传 动 耳 轴 ; 一销 子 ;一耳 轴座 ( 圈 ) 2 3 托
起 键 的 作 用 , 传 递 转 矩 , 将 其 长 度 割 去 一 段 , 须 校 核 即 现 必
于 上 下 位 置 , 图 3 见 。
托 圈 受 力 变 形 后 , 合 间 隙在 轴 线 上 下 方 的 间 隙 口方 配
一
1 — 5
转炉炉壳的变形分析及延长炉壳寿命的措施
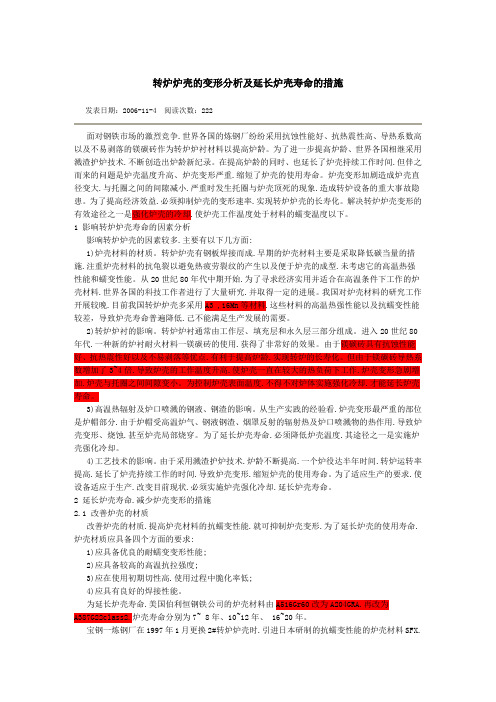
转炉炉壳的变形分析及延长炉壳寿命的措施发表日期:2006-11-4 阅读次数:222面对钢铁市场的激烈竞争.世界各国的炼钢厂纷纷采用抗蚀性能好、抗热震性高、导热系数高以及不易剥落的镁碳砖作为转炉炉衬材料以提高炉龄。
为了进一步提高炉龄、世界各国相继采用溅渣护炉技术.不断创造出炉龄新纪录。
在提高炉龄的同时、也延长了炉壳持续工作时间.但伴之而来的问题是炉壳温度升高、炉壳变形严重.缩短了炉壳的使用寿命。
炉壳变形加剧造成炉壳直径变大.与托圈之间的间隙减小.严重时发生托圈与炉壳顶死的现象.造成转炉设备的重大事故隐患。
为了提高经济效益.必须抑制炉壳的变形速率.实现转炉炉壳的长寿化。
解决转炉炉壳变形的有效途径之一是强化炉壳的冷却.使炉壳工作温度处于材料的蠕变温度以下。
1 影响转炉炉壳寿命的因素分析影响转炉炉壳的因素较多.主要有以下几方面:1)炉壳材料的材质。
转炉炉壳有钢板焊接而成.早期的炉壳材料主要是采取降低碳当量的措施.注重炉壳材料的抗龟裂以避免热疲劳裂纹的产生以及便于炉壳的成型.未考虑它的高温热强性能和蠕变性能。
从20世纪80年代中期开始.为了寻求经济实用并适合在高温条件下工作的炉壳材料.世界各国的科技工作者进行了大量研究.并取得一定的进展。
我国对炉壳材料的研究工作开展较晚.目前我国转炉炉壳多采用A3 ,16Mn等材料.这些材料的高温热强性能以及抗蠕变性能较差,导致炉壳寿命普遍降低.己不能满足生产发展的需要。
2)转炉炉衬的影响。
转炉炉衬通常由工作层、填充层和永久层三部分组成。
进入20世纪80年代.一种新的炉衬耐火材料一镁碳砖的使用.获得了非常好的效果。
由于镁碳砖具有抗蚀性能好、抗热震性好以及不易剥落等优点.有利于提高炉龄.实现转炉的长寿化。
但由于镁碳砖导热系数增加了3~4倍.导致炉壳的工作温度升高.使炉壳一直在较大的热负荷下工作.炉壳变形急剧增加.炉壳与托圈之间间隙变小。
为控制炉壳表面温度.不得不对炉体实施强化冷却.才能延长炉壳寿命。
钢结构层状撕裂的预防措施

钢结构层状撕裂的预防措施(1)焊接接头坡口的设计焊接坡口的设计关系到拉伸应力场的强弱,是影响层状撕裂的关键因素。
从力学的观点分析:钢板一侧受力,产生层状撕裂的可能性远比两侧受力的机率小得多,截面积小的焊接坡口,产生层状撕裂的可能性远比截面积大的坡口小得多,焊缝少的焊接接头,产生层状撕裂厂的可能性比焊缝多的焊接接头要小得多,钢板内部的十字焊接接头,产生层状撕裂的可能性远比在钢板端部小得多。
在焊接接头和坡口的设计中,成功的因素完全服从于焊接应用技术理论,焊缝截面积的大小决定拉伸应力场的强弱,拉伸应力场的作用点会直接影响层状撕裂的产生。
这就是结构设计和深化设计所必须遵循的原则。
(2)抓好确认最佳焊接工艺关防止层状撕裂的产生,除正确的设计之外,必须有合理的焊接工艺作保证。
防止由冷裂纹引发的层状撕裂,可以采取防止冷裂纹相同的技术措施。
如适当预热、控制层间温度、后热消氢处理等,对防止层状撕裂均有一定作用。
但建筑钢结构有其特殊的地方,那就是构件的截面不同,防止层状撕裂的方法也不同。
A、深化设计时,严把设计关,特别是坡口设计和构件加工精度指标要严格控制,从根本上消除层状撕裂出现的必要条件。
B、优选钢材、焊材和供货商,在关键部位合理应用抗层状撕裂的优质Z向钢,并在加工前严格进行钢材Z向性能复检和UT探伤复查,从而保证接头抗层状撕裂能力,从材料品质上消除层状撕裂出现的必要条件。
C、厚板火焰切割前预热,火焰切割后切割断面检查。
提高坡口以及易产生层状撕裂面的加工精度,消除材料表面的微小应力集中点和硬化组织,从根本上杜决层状撕裂出现的充分条件。
预热最好采取远红外电加热装置以获得准确的预热温度,防止付加应力的产生。
层状撕裂的防止

层状撕裂的防止一概述厚度较大的钢板在轧制过程中存在各向异性。
经过轧制之后,钢板内部由硫、磷偏析产生的杂质和其它非金属夹杂物被压成薄片,出现分层(夹层)现象。
分层使钢板厚度方向受拉的性能恶化,并有可能在焊缝收缩或在拉力作用下出现层间撕裂。
层状撕裂主要发生在T形、十字形和角部接头中,这些部件约束程度大,使母材在厚度方向引起应变,由于延性有限无法调节,当钢板存在分层缺陷时,容易发生层间撕裂。
结构复杂,焊缝集中的节点,约束大,如刚接框架节点域中柱的翼缘板也可能产生层状撕裂。
二层状撕裂的起因由前述可知,层状撕裂主要由两个原因共同促成,即:①钢板存在分层缺陷;②在钢板分层处表面焊接和(或)其厚度方向有外拉力作用。
三防止层关撕裂的措施我国《建筑抗震设计规范》GB50011-2001和《高层民用钢结构技术规范》JBJ99-88等均有对焊接连接的节点,当钢板厚度大于50(或40)mm,并承受沿厚度方向的拉力作用时,应采用厚度方向性能钢板(抗层间撕裂的Z向钢板)的条款。
但是,Z向钢板目前产量较小,价格也比普通钢板高很多,而且采用质量好的钢板并不能消除焊缝收缩,也不一定能防止高约束节点处的层状撕裂,仅能减少层状撕裂的危险性。
因此,防止层状撕裂问题,必须从设计、制造工艺和检查等方面综合考虑。
要做到与焊接材料协调,可能产生层状撕裂的节点,设计时应考虑使其节点结构具有最大的柔性,避免高约束,使焊缝收缩应力最小。
具体措施如下:1.设计a. 在设计中不任意加大焊缝,在满足强度要求时应尽可能采用最小焊脚尺寸,在满足焊透深度要求时,应采用较小的焊接坡口角度和间隙;b. 避免焊接节点沿厚度方向受拉力作用;c. 相关节点采用高强度螺栓连接;d. 钢板厚度较大的角接接头焊缝,采用收缩时不易产生层状撕裂的构造(下图);T形接头采用对称(K形)坡口焊缝;e. 相关位置采用Z向钢板。
对受动力作用和大气环境恶劣的结构,如海上采油平台,其重要构件的钢板沿厚度方向所受拉力较大时,相应区域可采用Z向钢板;高层建筑钢结构刚性框架节点域由于焊缝集中,且约束程度大,梁端弯矩很大时可采用Z向钢;2 制造工艺a. 采用低氢型焊条,在满足设计强度要求时,选用屈服强度较低的焊条;b. 严格规定焊接顺序和焊接工艺,防止在约束状态下施焊,尽可能减小垂直于板面方向的约束;c. 适当提高预热温度施焊和进行必要的后热处理;d. 带有角部和T形接头的小组件在构件装配前全部焊好,构件最后装配只作对接焊接;e. 在容易发生层状撕裂的母材表面先用低氢型焊条堆置焊层;f. 采用“锤击”或其它特殊的工艺方法,减小母材厚度方向的应变。
钢结构层状撕裂的防止措施

钢结构层状撕裂的防止措施钢板的层状撕裂一般在板厚方向有较大拉应力时发生.在焊接节点中,焊缝冷却时,会产生收缩变形。
如果很薄或没有对变形的约束,钢板会发生变形从而释放了应力。
但如果钢板很厚或有加劲肋,相邻板件的约束,钢板受到约束不能自由变形,会在垂直于板面方向上产生很大的应力。
在约束很强的区域,由于焊缝收缩引起的局部应力可能数倍于材料的屈服极限,致使钢板产生层状撕裂.。
层状撕裂只可能发生在基材内,而且当它出现在接近焊缝的焊脚位置时,往往正好位于热影响区边缘,并且不会延伸至钢板表面.层状撕裂表面往往时纤维状的,发生在热影响区外并且具有阶梯行当纵向断面,纵向的尺寸往往数倍于横向尺寸。
这些特征可以容易将它与发生在热影响区内的由于氢引起的断裂区分开。
当有可能层状撕裂发生时,为防止钢板的层状撕裂,可采取一下措施:(1)改进节点的连接形式改进节点连接形式以减小局部区域内由于焊缝收缩而引起的应力集中,或避免使钢板在板垂直方向受拉。
(2)采用合理的焊缝形式及小焊脚焊缝焊缝的形式对基材变形有很大影响。
坡口焊缝的坡口越大,焊缝表面积也越大,将增加收缩应力。
单坡坡口焊缝会在整个连接厚度方向上产生不对称收缩应变而双坡焊缝会减少和平衡部分收缩变形,当板材厚度不大于19mm时,用双坡口代替单坡口并不能显著降低焊缝收缩变形。
随意用全熔透坡口焊代替角焊缝或在不需要熔透焊的连接中也要求采用全熔透焊,并不妥当,它会增加局部应力,容易导致层状撕裂。
(3)分段拼装在可行的情况下,应将一个大节点分成几个部分分别焊好后再拼装,并对各部分中焊缝的焊接次序进行仔细安排.此外,应尽可能减少定位焊点的尺寸及数量。
这些都将有利于节点焊缝去的收缩变形。
(4)谨慎布置加劲肋加劲肋会对焊缝变形产生约束.应按计算的要求设计加劲肋及其焊缝。
(5)选择屈服强度低的焊条只要能满足受力要求,应尽可能选择屈服强度低的焊条。
美国焊接学会的<<结构焊接规范>>和美国钢结构协会的<<建筑结构设计、制作、安装规程>>均指出:焊条、焊丝和焊剂应于基材"匹配"。
炼钢转炉喷溅事故的原因和预防措施

炼钢转炉喷溅事故的原因和预防措施前言转炉是炼钢过程中的一种重要设备,主要用于高炉生铁除渣、除硫和合金化等工艺。
但在使用过程中,经常发生喷溅事故,给生产带来严重的威胁。
本文将从原因和预防措施两个方面来分析和探讨炼钢转炉喷溅事故。
喷溅事故的原因1. 转炉操作不规范炼钢转炉具有高温高压等特点,操作不规范会导致炉料溢出、热态反应失控等现象的发生。
比如说在加入炉料时没有及时开放炉门,炉料积压过多,导致热态反应失控,引起喷溅事故。
2. 转炉内壁破损炼钢转炉的内壁经常受到高温高压的冲击,长期使用后容易出现裂缝、缺陷等问题。
尤其在高炉煤气、生铁、镁砂等各种物料的强冲击下更容易造成内壁破损,从而引起钢水、炉料等的喷溅。
3. 炉料粒度不均炉料的粒度对喷溅事故的发生也有一定影响。
如果炉料的粒度不均匀,松紧程度不同,就会导致在加入新料时出现热态反应失控或部分炉料被抛出转炉的情况。
从而引起钢水、热风、渣等物料的喷溅。
喷溅事故的预防措施1. 做好安全防护在炼钢转炉使用过程中,必须严格执行操作规程和操作规范,保持注意力高度集中,特别是在加料、出钢水、冶炼合金等重要步骤时。
同时应做好防护措施,如安装可调式盖罩、定期检测转炉内壁等。
2. 均匀加料为防止粉尘喷溅,要求将物料加入转炉时应注意保持物料的均匀与抗溅性能。
机加工料和原料的混合、充堆、热敏年脆等理化状态的因素都会对加料的均匀性起到重要影响。
3. 定期检修定期检查和维护炼钢转炉的内壁和相关设备,以确保其完好无损,可正常运行。
同时,在检查转炉内壁之前,还应先通风、放空、冷却、卸料等步骤,确保操作人员的安全。
结论炼钢转炉是冶金生产线中重要的设备,发生喷溅事故有可能给生产带来不良影响。
为了保证炼钢生产的连续性和稳定性,必须制定出有效的技术维修方案和操作规程,以保证转炉的正常运转。
在生产中,我们还要加强对喷溅事故的风险评估和瓶颈监控,及时发现隐患并采取措施消除,以确保生产线的整体安全性和稳定性。
济钢120t转炉基础裂缝防治措施

( 济南钢铁集 团总公 司, 1 山东 济南 2 0 0 ; 山东省冶金工业总公司 , 5 1 12 山东 济南 2 0 1 ) 50 4
摘 要: 混凝土施工 出现裂缝 的主要原 因, 一是混凝土受力 ; 二是混凝土体 积变形 , 即混凝土在硬 化过程 中由于温度变 化而
的要求 , 以确保混 凝土浇 灌 连续进行 。同时 , 考虑在 混凝 土 中掺 加外加 剂 和混合 料 ,如 粉煤灰 和 高效减 水剂 等 , 以达到 改善 混 凝土 和 易性 , 低水 灰 比 , 降 减 少水泥用 量 , 降低水 化热 的 目的 。经 试配后 , 定的 确
( ) 骨料 : 2粗 采用 石灰 碎石 , 径 l~ 1 mm, 粒 6 3. 5 含
泥量 不大 于 l %。选用 粒径较 大 、 配 良好 的石子 配 级 置 的 混凝 土 , 和易 性较 好 , 压强 度 高 , 抗 同时可 减 少
凝土中, 温度裂缝 的概率远 大于 收缩裂缝 。 依据设 计理论 和 国家 现行施 工及验 收规 范的规
较 其它 工程上 的使用经验 , 确定采用 F C 5外加剂 , N一 掺量 为水 泥重量的 3 %~5 %。该 防冻 剂不含氯盐 , 对 钢筋无锈 蚀影响 , 掺人混凝土 中能明显提 高硬 化后 的 混凝士 性能 , 同时还具 有减水 、 降低水 化热峰值 、 对混
凝土收缩 有补偿 功能 , 可提高混凝 土的抗裂性 。
收 稿 日期 :0 6 2 l 2 0 一l一 2
施 工 ,所 以配 合 比设 计要 考虑 降低水 化热 温度 的原 则, 利用混 凝土 后期 (0 ) 度 , 6 d强 降低水 泥用量 , 要求
混 凝土和 易性好 , 于泵送 。 因此 , 利 混凝 土采用 现场 搅拌 ,混凝 土供应 能力 必须 满足现 场最 大浇灌 强度
转炉炼钢生产常见事故及应急预案

转炉炼钢生产常见事故及应急预案转炉炼钢是钢铁生产中最重要的工艺之一,但同时也存在各种潜在的危险和风险,可能会导致生产事故的发生。
为此,制定和实施应急预案是非常重要的,以下是转炉炼钢生产常见事故及应急预案。
一、突然炸裂事故炉体结构松散,冷却水压力异常或内部炸药造成的爆炸等,这些原因会导致转炉出现突然炸裂事故。
应急预案:1. 事故发生后,立即通知安全、运行、设备等相关人员组织应急处置。
2. 在事故现场封锁周围地区,保护人员安全,并对现场进行处理。
3. 召开应急小组会议,指派专人负责事故调查和事故原因分析。
4. 根据事故原因,采取措施加强各项安全控制,以遏制类似事故再次发生。
二、熔渣的泄漏事故转炉炉口保护不力、熔渣清理不及时等原因,可能导致熔渣泄漏。
应急预案:1. 发现熔渣泄漏时,立即停炉。
2. 对泄漏的熔渣进行处理并清理现场。
3. 排查熔渣泄漏原因,并采取措施加强熔渣控制,4. 借鉴经验,改进工作流程,预防类似事故再次发生。
三、转炉过程中发生钢水喷溅事故转炉炉口开启不当、钢包压力不稳定或钢包温度偏高等原因,可能导致钢水喷溅。
应急预案:1. 发生钢水喷溅事故时,立即停炉断电。
2. 在现场封锁和警戒周围地区。
3. 确认现场安全后,进行喷溅钢水的清理工作。
4. 对事故原因进行调查和分析,并整改工作流程,加强安全管理。
四、炉蜗杆断裂事故转炉在卸载钢水过程中,由于操作不当、运行不正常等原因,可能会导致炉蜗杆断裂。
应急预案:1. 火速停机,拉开排放阀门,排出转炉内的钢水。
2. 对现场进行封锁,防止人员进入受伤。
3. 对断裂蜗杆进行处理。
4. 进行事故原因分析,制订相关的措施,加强安全工作。
五、产生废气冒烟事故转炉炉顶密封不良、油气回收装置故障等原因,可能导致强烈废气冒烟。
应急预案:1. 及时切断气路和电源,停机检查。
2. 紧急提升废气净化设施的效率,降低污染物排放。
3. 进行现场排查,确定废气冒烟的原因。
4. 根据事故原因制定措施,加强废气净化装置的维护管理。
转炉系统事故隐患预防措施和紧急处理程序
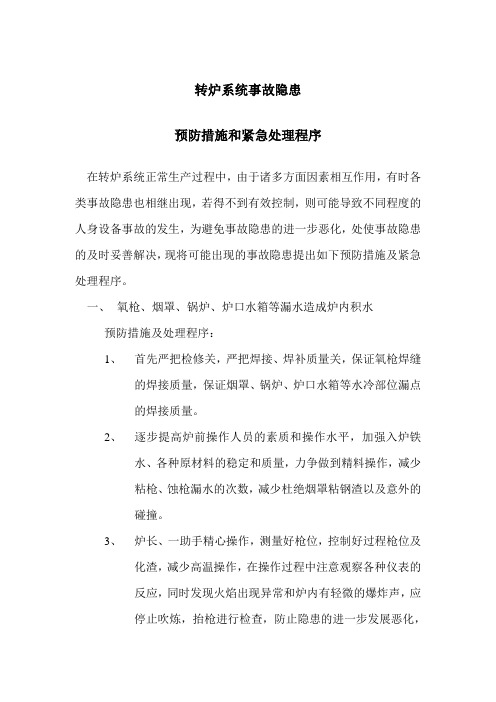
转炉系统事故隐患预防措施和紧急处理程序在转炉系统正常生产过程中,由于诸多方面因素相互作用,有时各类事故隐患也相继出现,若得不到有效控制,则可能导致不同程度的人身设备事故的发生,为避免事故隐患的进一步恶化,处使事故隐患的及时妥善解决,现将可能出现的事故隐患提出如下预防措施及紧急处理程序。
一、氧枪、烟罩、锅炉、炉口水箱等漏水造成炉内积水预防措施及处理程序:1、首先严把检修关,严把焊接、焊补质量关,保证氧枪焊缝的焊接质量,保证烟罩、锅炉、炉口水箱等水冷部位漏点的焊接质量。
2、逐步提高炉前操作人员的素质和操作水平,加强入炉铁水、各种原材料的稳定和质量,力争做到精料操作,减少粘枪、蚀枪漏水的次数,减少杜绝烟罩粘钢渣以及意外的碰撞。
3、炉长、一助手精心操作,测量好枪位,控制好过程枪位及化渣,减少高温操作,在操作过程中注意观察各种仪表的反应,同时发现火焰出现异常和炉内有轻微的爆炸声,应停止吹炼,抬枪进行检查,防止隐患的进一步发展恶化,初步检查由炉前段长组织人员进行确认。
4、若怀疑或确认炉内进水,应首先切断转炉氧枪、下料系统的所有电源,不准动炉,然后通知车间,由当班调度协调处理善后工作,包括判断漏水点关闭开关及停泵。
紧急处理程序:(1 )、炉内积水的确认,由当班段长,炼钢调度等人由氮封口进行确认,如炉内无水,可以继续生产。
如炉内存在积水要及时通知车间主任及至厂长到场具体处理炉内积水。
(2)、炉内积水的处理:由厂长、车间主任、安全科长再次组织人员进行确认,并估计积水量,可用铁丝或安全可靠的钢绳进行测量炉内积水液面,计算出炉内积水,可视炉内积水的多少,采取不同的处理方法。
(3)、准备动炉:确认炉内积水属实蒸发完,渣面全部变白或变红,无暗处,撤离炉子周围所有人员,在专人指挥下,由一助手操作,听从指挥人员指挥,缓慢动炉,正常后可视钢水凝固时间进行处理。
二、耳轴、烟罩及其他水冷部位漏水,造成渣道积水过多预防措施及处理程序:1、炉前除正常冶炼钢水外,要加强对各水冷部位的检查,发现漏水严重,应及时停炉检修,避免渣道内积水过多。
炼钢厂转炉托圈制作时焊接变形的预防及控制
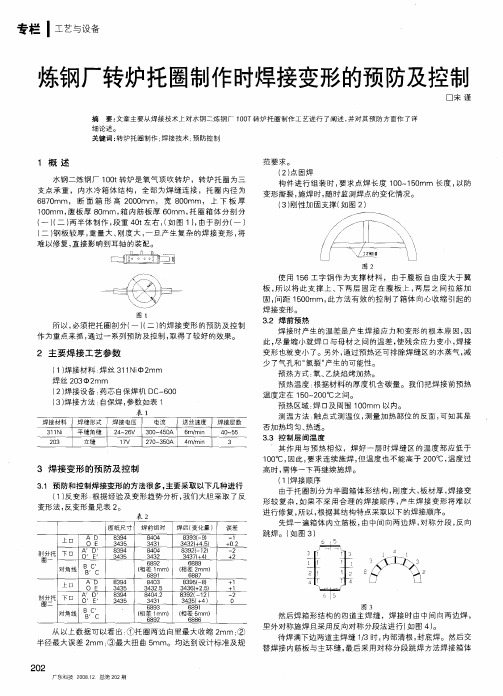
范要求。
( ) 固焊 2点
构 件进行组 装时 , 求点焊长度 1 O 10 要 0 ~ mm 长 度 , 防 5 以 变形撕裂 , 施焊 时, 随时监测焊点 的变化情况。
( 刚 性 加 固支 撑 ( 图 2) 3) 如
[ 差羔
图 2
使 用 1 6工 字钢作为支撑材 料 ,由于腹 板 自由度 大于翼 5 板 , 以将 此 支 撑 上 、 两 层 固定 在 腹 板 上 , 层 之 间 拉 筋 加 所 下 两
3 1 I 1平缝角缝 l 2~ 6 I 0— 5 A 1 6 ml 1N 4 2V 0 4 0 m, n 3
23 0 立缝 1 1v 7
否加 热 均 匀 、 透 。 热
33 控 制 层 间温 度 .
-= 谨防及 := 抹 =_ 币 = 3 焊 接变=I 控 制 形的预
焊后( 变化 量 )
8 9( ) 3 3一9
3 3 f ) 4 2+4 5
误 差
一1
+0 2
89 34
33 4 5
8O 44
3 31 4
剖 分 托 下 口 A D
圈一 0 E
B C
89 34
33 45
8O 44
33 42
69 82
3 3 +2 5 4 6( .)
+1
+1
剖 分 托 下 口 A D 圈 二 O E
B C
89 34 33 45
8 42 40 3 31 4 用 与 预 热 相 似 ,焊 好 一层 时 焊 缝 区 的 温 度 部 应 低 于 1 0C, 此 , 求 连 续 施 焊 , 温度 也 不 能 高 于 2 OC, 度 过 0。 因 要 但 0。 温
转炉爆炸事故及预防措施正式版

转炉爆炸事故及预防措施正式版转炉是钢铁厂中的一种重要设备,用于冶炼炼钢。
然而,由于转炉操作不当或其他原因,转炉爆炸事故时有发生。
本文将介绍转炉爆炸事故的原因,以及可采取的预防措施。
1.炉温过高:转炉冶炼过程中,如果炉温过高,容易引发炉下破裂,导致爆炸事故。
2.操作不当:转炉工作人员在操作过程中,如未能正确设置指标、控制炉内气体比例等,都有可能引发事故。
3.液压故障:转炉的一些关键设备使用液压驱动,如果液压系统存在故障,比如泄漏、压力过高等,都有可能导致爆炸事故的发生。
为了预防并避免转炉爆炸事故的发生,可以采取以下措施:1.强化操作培训:转炉工作人员应接受专业的培训,掌握炉内温度、压力等指标的正确设置和控制方法,以及各种应急处理措施。
2.定期检测和维护:定期对转炉进行全面的检查,确保液压系统和其他关键设备的正常运行。
发现问题及时修复或更换故障部件。
3.设备更新升级:针对老化的设备,及时更新和升级,以提高设备的可靠性和安全性。
4.强化安全意识:转炉工作人员应加强安全意识,时刻关注炉内指标和设备运行情况,并及时报告异常情况。
5.设置安全保护装置:在转炉内设置温度、压力等安全保护装置,一旦达到危险限值,自动切断供气供电等功能,保证人员和设备的安全。
6.加强巡检和监控:加强对转炉操作过程的巡检和监控,及时发现并解决潜在的安全隐患。
7.做好应急准备:建立完善的应急预案和救护设施,培训相关人员熟悉预案,并定期组织演练。
总之,转炉爆炸事故的预防需要从多个方面入手,包括加强员工培训、设备维护、安全意识,以及设置安全保护装置等。
只有全面加强安全措施,才能在转炉冶炼过程中降低爆炸事故的风险,确保人员和设备的安全。
钢结构中厚板焊接层状撕裂 预防控制

166YAN JIUJIAN SHE钢结构中厚板焊接层状撕裂 预防控制Gang jie gou zhong hou ban han jie ceng zhuang si lie yu fang kong zhi尚亚杰中厚板焊接引起的分层撕裂是不同于热裂纹和冷裂纹的特殊裂纹。
它们通常发生在t 形接头、转角接头和十字接头热影响区的滚动区,或起源于根部裂纹。
其结果对结构件存在极大危害并且无法满足钢结构焊缝质量验收标准。
为了减少中厚板焊接中层状撕裂的发生,我们分析了产生这种现象的原因,进行合理的设计坡口,并消除了控制焊接应力产生的措施,并使用零件的整平消除压力并释放局部热量。
通过释放应力、焊接锤击和其他方法可以减少残余应力,从而提高焊接合格率。
一、层状撕裂产生的原因焊接和焊接后冷却过程中,或焊接后承受载荷时,可能发生层状撕裂。
导致分层撕裂的主要因素是材料因素,如低碳钢、低合金钢和高硫低合金钢。
钢的含碳量越高,钢结构越脆,分层撕裂越敏感。
焊缝中扩散氢含量能促进分层撕裂的扩展。
氢扩散在根部或热影响区剥落中起着间接但重要的作用。
二、防止措施某钢结构厂房项目钢柱采用Q235B 材质的原材,截面尺寸主要为日字柱1500*100*50mm、箱型柱1000*1000*50mm,在制造和安装过程中有许多角焊缝、T 形焊缝和坡口焊。
在其组合焊缝的热影响区将产生较大的焊接应力,可能出现阶梯式的应力开裂。
为了避免这种情况,在施工前根据项目情况制定以下预防措施:(1)严格控制钢中硫含量,在满足降低局部焊接变形引起应力集中的要求的同时,优化焊接节点的连接方式。
(2)采用合理的焊接方法和较小的焊脚焊缝,通常在焊缝基体范围内发生夹层撕裂,当夹层撕裂发生在焊接位置附近时,它通常位于热影响区的边缘,而不是待扩展的基体表面。
最好使用对称的码板或偏斜于角部接头处的侧板的码板,以使焊接收缩产生的拉应力与板厚方向成一定角度,特别是在特厚板的情况下,侧板码板表面的角度应超过板厚的中心,这样可以减少分层撕裂的趋势。
转炉托圈焊接工艺和控制措施的研究

转炉托圈焊接工艺和控制措施的研究【摘要】托圈是转炉的重要焊接部件,而倾翻主、从动端耳轴的焊接质量的优劣直接影响到设备的总体质量,同时也是设备制造中的关键所在。
在近期我公司为天津钢厂生产的100t混铁炉中,就涉及到托圈主、从动端耳轴的焊接问题,并列为技术攻关项目。
通过技术攻关,编制了合理的焊接工艺和制定了预防措施,并应用于实际生产操作中,把控制焊接裂纹和未熔合两大难题作为焊接重点加以解决,获得了良好的效果,一次通过无损检测验收。
【关键词】耳轴焊接;焊缝裂纹;未熔合;实施1、产品及施焊件的概况为天津钢厂生产的100t转炉,托圈部件重量为16000Kg,部件中心直径Ф4680mm,因加工设备能力限制,只能对各部件加工成品后焊接。
焊接要求变形控制极为严格,主、从动端耳轴焊后径向同轴度误差为Ф0.5mm,而其中的重要部件主、从动端耳轴直径Ф1160mm的焊接则是控制和攻关的难点。
此次生产的托圈,为首次全部采用CO2气体保护焊进行焊接。
其中:①主、从动端耳轴板为铸钢件,材质为ZG20MnMo,厚度为160mm,与直径Ф1160mm材质为37SiMn2MoV的耳轴进行焊接,焊接性能较差;②加工焊接的坡口为双U型坡口,就我厂目前的焊接设备只能采CO2气体保护焊进行焊接作业,存在焊接坡口熔合不良和易产生裂纹的倾向;③焊缝为封闭环型,焊缝长度为3650mm,存在焊接拘束应力大等不利因素。
2、对焊接裂纹、未融合的分析2.1材质分析与匹配选用焊接材料材质为ZG20MnMo的主、从动端耳轴板,与直径Ф1160mm材质为37SiMn2MoV的耳轴进行焊接,理论上对于屈服强度大于392Mpa的低合金钢,其中碳和合金元素含量较多,其强度和韧性高,焊接性较差,采用低匹配焊接材料以降低焊缝的淬硬倾向,降低裂纹产生的几率作为工艺的指导方针,故选用ER50-6Ф1.2mm焊接材料进行焊接。
2.2采取有效措施提高焊接组织性能焊接时主要存在淬硬倾向较大,易产生裂纹的问题。
炼钢厂转炉托圈裂纹产生原因分析及改造措施

炼钢厂转炉托圈裂纹产生原因分析及改造措施转炉托圈是转炉极其重要的设备,起着转炉支撑、倾动的作用,托圈的状况是否正常直接关系到炼钢工序的进行和钢产量的实现。
生产实际中,经常会出现托圈在其耳轴座附近产生裂纹而发生漏水的问题,而当泄漏的冷却水遇到炉坑中高温的炉渣或者在出钢时流入到炉下钢水包中时,可能引起爆炸,存在巨大的安全隐患。
文章就此进行分析。
标签:炼钢厂;转炉托圈;裂纹;改造措施一、裂缝产生的原因分析转炉托圈产生裂纹与其结构、材料、载荷和使用温度有关。
包钢和攀钢的材料好于武钢,而炉壳温度高于武钢,且托圈无冷却;经过对比分析得出结论:托圈在长期过热的环境中使用,导致托圈材料因蠕变而降低承载能力;托圈自身的温度在冶炼过程有较大的变化。
托圈受热胀冷缩的影响,会产生较大的内应力,继而产生裂纹。
经过受力分析可知,裂纹的产生还有机械应力的原因,一是托圈受力不均,托圈在传动侧的一端不仅承受炉体的重量,而且还承受炉体转动的扭矩,在第三象限的靠近耳轴块处,托圈弯矩最大,所以裂缝发生在第三象限;二是在生产过程中,由于摇炉时炉体对托圈造成冲击,尤其出钢口常常撞击到其它的设备上,冲击力通过把持器作用在托圈上,更加大了托圈的应力。
综合以上分析,裂纹产生的主要原因是热应力和机械应力的联合作用,反复作用在危险点超过了强度极限。
热应力比机械应力的影响大得多。
考虑到裂纹仅仅是局部现象,只要不继续扩展就不致发生破坏。
因此在设计改造中采取以降低托圈的使用温度和消除冲击力为原则的改造措施,将原有的托圈修复后继续使用,从而降低投资费用。
基于此思想对现有托圈进行了增加水冷和增设缓冲器的技术改造。
二、改造措施(一)泄漏问题直接针对泄漏问题,即将常用于高压管道泄漏的带压堵漏技术应用到托圈漏水处理中。
具体实施过程如下:①将转炉摇炉停止在适合方便检修人员上下、施工的位置,停电,做好安全措施。
②排出托圈内部的冷却水,在转炉水旋接头处关闭托圈冷却水进回水阀门,在回水管放气阀上接胶管,将胶管引入下水道里,防止冷却水与炉坑中熔融钢渣接触发生爆炸。
层状撕裂产生机理影响因素及防治措施

层状撕裂产生机理影响因素及防治措施一.危害性层状撕裂大多发一在大厚度高强钢材的焊接结构中,这类结构常常用于海洋工程、核反应堆、潜艇建造等方面,在无损探伤的条件下,层状撕裂不易发现而造成潜在的危险,即使判明了接头中存在层状撕裂,几乎不能修复,经济损失极大。
二.特征及危害性是一种内部低温开裂,一般表面难以发现。
1、产生的部位和形状宏观形状:在外观上具有阶梯状的形式,由基本上平行于轧制方向表面的平台与大体上垂直于平台的剪切壁所组成。
微观形状:扫描电镜观察低倍下:断口表面呈典型的木纹状,是层层平台在不同高度分布的结果高倍下:在平台表面可以找到大量片状球状或长条状的非金属夹杂物,剪切壁成撕裂岭的形态.部位:母材或热影响区2、产生在厚板结构中十字接头,丁字接头,角接头,平台局部地区有硅酸盐或氧化物夹杂物种类依产生部位分第一类是在焊接热影响区焊趾或焊根冷裂纹诱发而形成层状措裂;第二类热影响区沿夹杂开裂;第三类远离热影响区母材中沿夹杂开裂MnS片状夹杂较多。
三、形成机理及影响因素(一)、层状撕裂的形成过程厚板结构中焊接时刚性拘束条件下,产生较大的Z向应力和应变,当应变达到超过材料的形变能力之后,夹杂物与金属基体之间弱结合面发生脱离,形成显微裂纹,裂纹尖端的缺口效应造成应力、应变的集中,迫使裂纹沿自身所处的平面扩展,把同一平面而相邻的一群夹杂物连成一平,形成所谓的“平面”。
与此同时相邻近的两个平台之间的裂纹尖端处,在应力应变影响下在剪切应力作用下发生剪切断裂,形成“剪切壁“,这些平台和剪切壁在一起,构成层状撕裂所持有的阶梯形状。
(二)、影响因素1、焊接应力厚板T字接头或角接头焊接时,焊缝收缩会在母材内厚度方向产生很大的收缩应力与应变。
在工向应力较大。
2、非金属夹杂物的层状构造由于钢材在热轧中产生流线带状组织片状硫化物、层状硅酸盐、氧化铝夹杂物大量成片密集同一平面,会使产生层状撕裂,急剧降低Z向塑性。
3、母材性能①热影响区产生淬硬组织、塑性下降②母才内部应变时效加热150~350℃出现应变时效,塑性、韧性下降4、氢的作用氢集聚发生在夹杂物和基体界面上的氢脆引起层状撕裂四、防止措施1、控制夹杂物冶炼降低杂质,脱S加Ti、Zr或稀土元素,促使夹杂物破碎、球化(成本高)2、改变接头形式、降低焊接应力接头形式在受力最小时即可防止层状撕裂,通过开坡口来减轻钢板Z向受承受的应力和应变。
浅谈焊接层状撕裂裂纹的成因和防治办法

浅谈焊接层状撕裂裂纹的成因和防治办法摘要:随着钢铁、石油化工、造船、轨道交通和电力等工业的发展,在焊接结构方面都趋向大型化、大容量和高参数的方向发展,有的还在低温、深冷、腐蚀介质等环境下工作。
因此,各种低合金高强钢,中、高合金钢、超强钢,以及各种合金材料的应用日益广泛。
但是随着这些钢种和合金的应用,在焊接生产上带来许多新的问题,其中较为普遍而又十份严重的就是焊接裂纹。
焊接过程中所产生的裂纹有多种多样,就目前的研究,按产生裂纹的本质来分,大体上可分为以下五大类:热裂纹、再热裂纹、冷裂纹、层状撕裂、应力腐蚀裂纹等,其中层状撕裂裂纹的危害性更为严重,由于层状撕裂在外观上没有任何迹象,无损检测手段又较难发现,即使能判断结构中又层状撕裂也很难修复,造成巨大经济损失,特别严重的是层状撕裂引起的事故往往是灾难性的。
如何防止层状撕裂的发生,是焊接应用中的一项重要课题。
关键词:焊接裂纹层状撕裂层状撕裂是一种内部的低温开裂。
仅限于厚板的母材金属或焊缝热影响区,多发生于“L”、“T”、“+”型接头中。
其定义为轧制的厚钢板沿厚度方向塑性不足以承受该方向上的焊接收缩应变而发生于母材的一种阶梯状冷裂纹。
一般是由于厚钢板在轧制过程中,把钢内的一些非金属夹杂物轧成平行于轧制方向的带状夹杂物,这些夹杂物引起了钢板在力学性能上的各向导性。
防治层状撕裂在选材上可以选用精练钢,即选用z向性能高的钢板,也可以改善接头设计形式,避免单侧焊缝、或在承受z向应力的一侧开出坡口。
1、层状撕裂的特点层状撕裂与冷裂不同,它的产生与钢种强度级别无关,主要与钢中的夹杂量和分布形态有关。
一般轧制的厚钢板,如低碳钢、低合金高强钢,甚至铝合金的板材中也会出现层状撕裂。
根据层状撕裂产生的位置大体可以分为三类:第一类是在焊接热影响区焊趾或焊根冷裂纹诱发而形成的层状撕裂。
第二类是焊接热影响区沿夹杂开裂,是工程上最常见的层状撕裂。
第三类远离热影响区母材中沿夹杂开裂,一般多出现在有较多MnS的片状夹杂的厚板结构中。
转炉托圈主副挡座检查及处理方法探究

转炉托圈主副挡座检查及处理方法探究摘要转炉炉壳与托圈之间的连接部分称为转炉炉体支撑装置,目前国内外应用比较广泛的是三点下吊挂支撑方式。
转炉整套支撑装置由两部分组成:一部分是拖圈下方连接炉壳的3组吊挂支撑装置,三组之间彼此相隔120°,吊挂支撑装置的主要功能是将炉壳悬挂支撑在拖圈上,吊挂结构可以适应炉壳的热变形导致与拖圈相对位置的微量变化。
另一部分是位于托圈上下定位炉壳的4组辅助防倾挡座组,挡座可以对炉壳与拖圈定位进行限制定位,挡座定位通过控制导向间隙适应炉壳径向和轴向热胀冷缩的变化,同时防止摇炉过程中出现冲击。
此种结构既能有效地在360°范围内支撑炉壳,又可适应炉壳的热膨胀,形成完整的炉体支撑连接系统。
关键字转炉托圈挡座检查处理Research on Inspection and Treatment Method of Main and AuxiliaryBlocks of Converter Support RingZhang Xuejun(Rizhao Iron and Steel Co., Ltd., Lanshan District, Rizhao City,Shandong 276806)Abstract The connecting part between the converter shell and the trunnion ring is called the converter body support device. At present, the three-point hanging support method is widely used at home and abroad. Converter furnace body complete supporting device consists of two parts: one part is 3 sets of upside down hanging support devices connected to the furnace shell under the drag ring. The three sets are separated by 120° from each other. The main function of the hanging support device The furnace shell is suspended and supported on the drag ring, and the hanging structure can adapt to the slight change ofthe relative position of the furnace shell caused by the thermal deformation of the furnace shell. The other part is the 4 sets of auxiliary anti-tilt block seat groups located on the upper and lower sides of the tru Changes in expansion and contraction, while preventing shocks during shaking. This structure can not only effectively support the furnace shell within 360°, but also adapt to the thermal expansion of the furnace shell to form a complete furnace body supporting connection system.Keywords Converter Truss ring Retaining seat Inspection of deal wit引言炉体支撑装置工作在高温、重载和频繁冲击的工况下,因此支撑装置是转炉设备的关键,也是易于发生失效故障的节点。
浅谈转炉托圈焊接修复技术分析

浅谈转炉托圈焊接修复技术分析摘要:对转炉托圈采用圆板按照托圈表面形状进行加工处理,带有一定弧度与托圈表面紧密接触,在进行焊接修复。
转炉是靠托圈支托,旋转的托圈承受巨大的载荷,是一个刚性很大的焊接结构件。
在生产过程中耳轴侧主焊缝附近的工艺孔焊缝均容易出现不同程度的裂纹,漏水频繁,补焊起不到根本的作用,严重影响生产节奏,并给转炉本体带来设备隐患。
现在需要采用圆板按照托圈表面形状进行加工处理,带有一定弧度与托圈表面紧密接触,在进行焊接修复及防止裂纹。
关键词:裂纹熔化极氩弧焊应力集中一、托圈焊接性能分析炼钢转炉托圈是材料为16MnR、腹板厚为70mm、翼板厚为100mm的大厚板压力容器类箱体形结构。
由于受结构的影响只能采用横焊位置焊接。
对于这种大型,超厚度的压力容器类焊件,受焊接设备能力的限制,只能采用手弧焊。
在焊接过程中,若采用不加热的方法焊接,焊后经超声波探伤发现焊缝根部裂纹严重,且在翼板的焊缝附近呈层状撕裂微裂纹等缺陷。
转炉托圈板材16MnR的碳当量为0. 39% ~0. 49%。
随着碳当量的增加,淬硬倾向即冷裂和热裂倾向增大,焊接性渐变差。
尤其是工件刚性较大,当焊接材料选择不当,工艺过程控制不好或多层焊,焊第1道焊缝时,由于母材金属熔合到焊缝中比例大,焊缝金属和热影响区会出现高硬度的马氏体组织,导致在焊缝金属及热影响区产生裂纹。
此外,由于含碳量高,气孔敏感性也增大,钢材厚度增加,散热加快,冷却速度增大,导致裂纹敏感性增加。
二、存在问题及分析停炉检查发现出现耳轴侧主焊缝附近的工艺孔焊缝均出现不同程度的裂纹,且裂纹有向托圈母材延伸的趋势。
对炼钢的安全构成严重威胁。
如图1所示图1托圈上工艺孔焊缝裂纹现在贴方板较贴圆板更容易造成应力集中而出现裂纹,在焊接前也没有打破口焊实,托圈焊后没有采用热处理,局部热处理工件拘束度大散热较快不能达到预期效果,残余应力未完全释放,残存在焊缝及热影响区中造成应力严重集中。
- 1、下载文档前请自行甄别文档内容的完整性,平台不提供额外的编辑、内容补充、找答案等附加服务。
- 2、"仅部分预览"的文档,不可在线预览部分如存在完整性等问题,可反馈申请退款(可完整预览的文档不适用该条件!)。
- 3、如文档侵犯您的权益,请联系客服反馈,我们会尽快为您处理(人工客服工作时间:9:00-18:30)。
1 情 况 介 绍
11 托圈 结构 .
裂 ( 图1。裂纹率按长度计算达一半 。位置在 见 ) 盖板 厚度 中心 ,在深 度方 向走势 趋 向焊 缝根部 。
托 圈材 质 为 1Mn 。由盖板 、腹板 和 筋板 组 6 钢
成箱 形结 构 。按 图 纸要 求 。对 盖 板 与腹 板形 成 的 4 角 接 形 式 主 焊 缝 进行 超 声 波 探 伤 检 验 .达 到 条 Ⅱ级合 格 。
. 焊 工对 称爬 坡 施 焊 。即外 圆 弧侧 两 条焊 缝 由 22 结构 形式影 响 盖板 厚度 大 .采用 现 状 的接 头形 式 极易 引 发 两 端 向 中间焊 ,内 圆弧 侧 两条 焊 缝 由 中间 向两 端 施 焊 。 首先 焊 外 圆弧 侧 两 条 焊 缝 两层 ( 道) 3 。然 层状 撕裂 。 . 后 托 圈 翻转 1 0 ,焊 内 圆弧侧 两 条 焊缝 至 坡 深 度 23 焊接 应力及 淬硬 性的影 响 8。 在 焊缝 填 满 或 将 要 填 满 时 产 生 了层 状 撕 裂 . l ;再 将外 圆弧 焊缝 填满 。最 后将 内圆弧侧 焊 缝 / 3 填满。
体方法 。
关键词 :闭式 回路 ;液压系统 ;安装与调试
中 图 分 类号 :T 5 2 2 文 献标 识 码 :B 文 章 编 号 :17 - 3 5 (0 6 6 0 5 - 2 G 0. 3 6 3 35 20 )0- 0 5 0
在众 多 的工 程 机 械 中 ,特 别 是 进 口设 备 中 ,
的要 点做 一简 ห้องสมุดไป่ตู้介 绍 。
正 确布置 软 管 ,避 免 软管 的扭转 、憋劲 、擦 伤 和磕 碰 。机械 运 动 时 ,相对 于软管 应有 足 够 的 安 全距 离 。以免 划 伤 软管 表 面 ,造成 不 必要 的泄
这 说 明 随着 焊 缝 金 属 的增 加 ,焊 接 应 力 也 增 加 ,
托圈按要求超声波探伤合格后 .进炉消除应 致使盖板撕裂。 由于焊接 时环境温度降低 。焊缝冷却速度加 力 热处理 。
收 稿 日期 :2 0 — 7 1 ; 修 回 日期 :20 — 8 1 060—0 060—5
工 程 机械 液压 系 统 中得 到 了广 泛 的应 用 ,但 与开 会污染系统 ,并可能造成系统故障。应对面积较
式 回路相 比 。闭 式 回路 的 安装 与 调试 都 有较 高 的 大的结合面进行必要的刮研 ;加橡胶 、聚乙烯和 难度和技术要求 .下面对闭式回路的安装 、调试 紫铜 等 密封垫 。
一
8 — 5
维普资讯
20 0 6年第 6期 ( 1 4期 ) 总 1
浅谈 闭式液压系统的安装与调试
王 宁 .窭连友
(. 1 中国第一 重型机械 ( 集团)有限责任公 司表处管线分厂工程师 ,黑龙江 富拉尔基 1 14 ) 602
摘 要:阐述闭式液压系统 的安装与调试过程 ,介绍提高泵和马达等液压件 的使用效率和使用期限的具
12 焊 接 工 艺 .
外 圆弧侧
图 1
( 内圆弧侧 b )
2 层状撕裂原 因
2 1 化学 成分影 响 .
采用碱性焊条焊接 。使用前烘焙并放人保温
筒 内随用 随取 。
托 圈 盖板 撕 裂 后 。对 盖 板 进 行 了化 学 分 析 , 焊接采用直流反接 。打底焊用细焊条 。其余 大于 0 2 . 。按 照I 0 I 钢 材层 状 撕 裂 W将 用 粗焊 条 。焊接 电流 :用细 焊条 为 10 10A。粗 结果 表 明 ,S 2~ 8 敏感 性 评 定 级别 规 定 ,其 钢 材 为 C ,即 只能 用 级 焊条 为1 0 2 0A。 8— 2 于z 向拘束应力小 的结构 。而托圈结构 的拘束应 焊 前 托 圈采 用 煤 气 预 热 , 温 度 10 10o 。 0 — 5 = 【 由于 托 圈为 圆弧 形且 较 长 .故 自制 了一 个预 热 环 力较大 。若没有工艺保证措施 ,则很容易诱发层 进 行预 热 。 状撕 裂 。
维普资讯
《 重技 术》 一
转炉托圈层状撕裂 的预防措施
粱振 久
(. 1 一重集 团公 司金属结构分厂工程师 ,黑龙 江 富拉尔基 1 14 ) 60 2 摘要 :针对转 炉托 圈焊接时产生层状撕裂的问题 ,从产品结构 、焊接工艺等方面人手 。分析了撕裂原 因,并制定了相应 的工艺措施 ,避免 了层状撕裂产生。 关键词 :托圈 ;盖板 ;转炉 ;层状撕裂 ;焊接工艺
路 系统 和元 器件 承 受横 向作 用 力 及 内部应 力 ,一
采 用 液压 传动 和全 液 压 驱 动十 分普 遍 。液压 闭式 定要注意保护管路系统 。 禁 止使用 麻 线 、胶 粘 剂作 为 密封 材 料 ,否则 回路 能耗 低 、结 构 紧凑并 容 易 实 现无 级 变速 ,在
中 图分 类 号 :T 4 71 文 献 标 识 码 :B 文章 编 号 :17 — 35 (0 6 6 0 5 - 2 G5. 6 3 3 5 20 )0 — 0 4 0
我 厂为 某炼 钢 厂焊 制 转 炉托 圈备件 时 。托 圈 盖 板 产 生 了严 重 的层 状 撕 裂 ,因 而影 响 了 生 产 。
13 层状 撕裂 的产 生 .
采 用上 述焊 接 工 艺将 外 圆弧 侧 两条 焊缝 全 部
为 消除 层状 撕裂 ,保证 生 产 正常 进 行 ,我们 从 产 填 满后 。焊接 内 圆弧 侧两 焊 缝 至母 材 表面 .托 圈
品结构 、焊 接 工艺 等方 面 分析 引 发 层状 撕 裂 的原 盖 板 外 圆 弧 侧 产 生 严 重 层 状 撕 裂 。 约几 小 时 后 因 。并 采取 了相 应 的工 艺 保证 措 施 ,消除 了产 品 ( 已停 止焊 接 、加热 )盖 板 内 圆弧 侧也 产生 层 状撕 层状撕 裂 问题 的发生 。