最新塑料模具工艺
塑料制品的模具设计与生产工艺
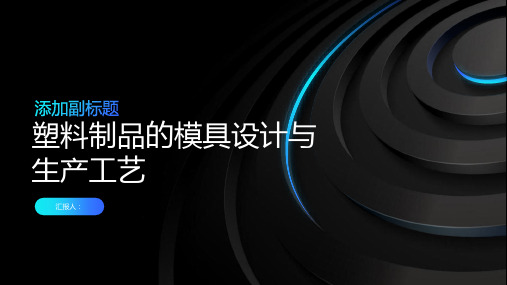
模具调试方法:检查模具闭合状态、调整模具间隙、测试模具成型效果
常见问题及解决方法:模具闭合不严、模具磨损、模具变形等
模具保养与维护:定期清洗模具、涂抹润滑剂、更换磨损部件等
制品质量检测与控制
检测方法:物理、化学、机械性能测试
检测设备:万能试验机、熔融指数仪、冲击试验机等
质量标准:符合相关行业标准和客户要求
智能化设计:利用AI技术进行模具设计,提高设计效率和质量
自动化生产:采用机器人和自动化设备进行模具生产,提高生产效率和精度
智能化监控:利用传感器和物联网技术对模具生产过程进行实时监控,提高生产安全和质量
自动化检测:采用自动化设备对模具进行检测,提高检测效率和准确性
环保与可持续发展要求
回收利用:提高塑料制品的回收利用率,减少环境污染
塑料制品的模具设计与生产工艺
汇报人:
目录
01
添加目录标题
02
塑料制品模具设计
03
塑料制品生产工艺
04
塑料制品模具设计实例分析
05
塑料制品生产工艺实例分析
06
塑料制品模具设计与生产工艺的未来发展
添加章节标题
塑料制品模具设计
设计原则与要求
满足产品性能要求:如尺寸精度、表面质量、力学性能等
考虑模具制造工艺:如模具材料、加工方法、热处理工艺等
模具材料选择:根据塑料制品的材质、形状和尺寸选择合适的模具材料
模具设计:根据塑料制品的尺寸和形状设计模具结构,包括型腔、型芯、冷却系统等
模具制造:采用数控机床、电火花、激光切割等工艺制造模具
塑料制品生产工艺
原材料准备
添加标题
添加标题
添加标题
添加标题
原料的干燥处理:去除原料中的水分和其他挥发性物质,保证制品的质量
塑料模具加工工艺流程
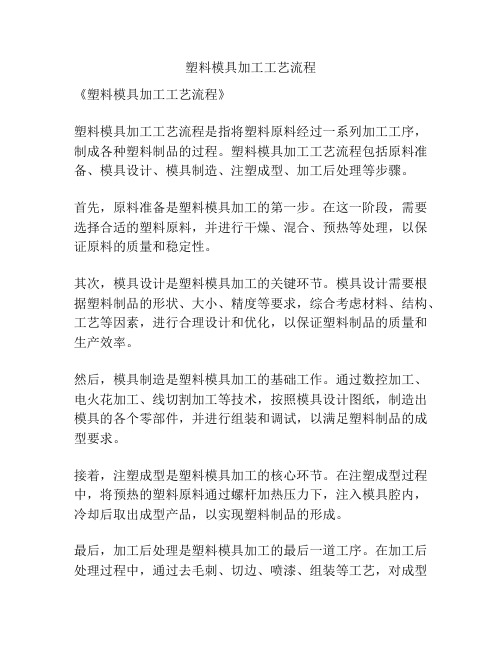
塑料模具加工工艺流程
《塑料模具加工工艺流程》
塑料模具加工工艺流程是指将塑料原料经过一系列加工工序,制成各种塑料制品的过程。
塑料模具加工工艺流程包括原料准备、模具设计、模具制造、注塑成型、加工后处理等步骤。
首先,原料准备是塑料模具加工的第一步。
在这一阶段,需要选择合适的塑料原料,并进行干燥、混合、预热等处理,以保证原料的质量和稳定性。
其次,模具设计是塑料模具加工的关键环节。
模具设计需要根据塑料制品的形状、大小、精度等要求,综合考虑材料、结构、工艺等因素,进行合理设计和优化,以保证塑料制品的质量和生产效率。
然后,模具制造是塑料模具加工的基础工作。
通过数控加工、电火花加工、线切割加工等技术,按照模具设计图纸,制造出模具的各个零部件,并进行组装和调试,以满足塑料制品的成型要求。
接着,注塑成型是塑料模具加工的核心环节。
在注塑成型过程中,将预热的塑料原料通过螺杆加热压力下,注入模具腔内,冷却后取出成型产品,以实现塑料制品的形成。
最后,加工后处理是塑料模具加工的最后一道工序。
在加工后处理过程中,通过去毛刺、切边、喷漆、组装等工艺,对成型
产品进行表面处理和组装,以提高产品的外观质量和性能。
综上所述,塑料模具加工工艺流程是一个复杂而严谨的过程,需要在设计、制造、成型和加工后处理等方面进行严格控制和协调,以保证塑料制品的质量和生产效率。
随着科技的不断进步,塑料模具加工工艺流程也在不断优化和完善,为塑料制品的生产和应用提供了更加全面的解决方案。
注塑模具的工艺流程

注塑模具的工艺流程注塑模具是塑料制品加工中常用的一种模具类型,它能够将塑料材料加工成各种形状的制品。
注塑模具的工艺流程主要包括模具设计、加工制造、组装调试和生产操作等几个步骤。
首先,注塑模具的工艺流程开始于模具设计。
根据客户的要求和产品设计图纸,模具设计师会根据产品的形状、尺寸、结构等要求,绘制出注塑模具的三维图。
设计图纸包括模具的总体结构、模腔的形状、冷却系统的布置、排气系统的设计等。
设计师还需要考虑模具的制造工艺,以确保模具加工的可靠性和可行性。
其次,注塑模具的工艺流程进入到加工制造阶段。
根据模具设计图纸,加工师傅们会根据材料的特性和加工工艺的要求选择合适的材料,进行模具的加工制造。
加工制造主要包括模架的制作、模腔和模芯的加工、冷却系统和排气系统的制作,以及一些特殊零部件的制作。
模具加工需要使用各种机械设备,如车床、铣床、磨床等,以确保模具的精度和质量。
当模具的加工制造完成后,注塑模具的工艺流程就进入到组装调试阶段。
组装师傅们会将模具的各个零部件进行组装,检查模具的各项功能是否正常。
同时,加工师傅们会进行模具的调试工作,以确保模具能够正常工作,产生良好的塑料制品。
调试过程中,会进行模具的开合顺畅程度、模腔的尺寸和表面光洁度、注塑机的参数设置等方面的调整,以达到预期的生产效果。
最后,注塑模具的工艺流程进入到生产操作阶段。
生产操作包括将模具安装到注塑机上,将塑料原料装入注塑机的料斗中,通过加热和注塑的方式,将塑料材料注入到模腔中,冷却成型后取出制品,然后进行加工和装配等后续工序。
生产操作需要操作工按照产品工艺要求和生产标准进行操作,确保生产出符合要求的塑料制品。
总之,注塑模具的工艺流程主要包括模具设计、加工制造、组装调试和生产操作等几个步骤。
每个步骤都需要工艺师傅们的精心操作和合作配合,以确保最终生产出优质的塑料制品。
塑料模具加工工艺流程

塑料模具加工工艺流程塑料模具加工工艺流程是指将塑料原料通过一系列的加工工序和工艺参数控制,制作出所需的塑料模具产品的过程。
下面将介绍一般的塑料模具加工工艺流程。
首先,准备工作是非常重要的。
在制作模具之前,需要设计师根据产品的要求制作产品的三维模型,并进行质量验证。
然后,根据模型设计制作模具的结构,选择合适的材料。
第二步是制作模具的外形。
将设计好的模具结构在一块铁板上进行切割,然后用专用的数控切割机将模具的外轮廓进行切割。
切割好后,需要进行边角的磨光和倒角,以避免刃口对模具的损伤。
第三步是模具零件的加工。
根据模具的设计图纸,将不同零件进行加工。
一般采用的加工方式有铣削、钻孔、螺纹加工等。
这些零件通常是用工具机进行加工,以确保加工尺寸的精确度和质量。
第四步是模具的组装。
将加工好的模具零件组装在一起,并使用螺栓进行固定。
在组装过程中,需要仔细调整模具的位置和垂直度,以确保模具的正确定位和有效运行。
第五步是进行模具的热处理。
热处理是为了增加模具的硬度和耐用性。
常见的热处理方式是淬火和回火,通过控制热处理时间和温度,使模具达到理想的硬度和强度。
第六步是进行模具的试模。
即将模具安装在注塑机上,注射塑料原料,进行模具的试模。
通过试模可以检验模具的质量和性能,发现问题并进行调整和修正。
最后一步是进行模块的后处理。
包括抛光、喷漆和表面处理等。
抛光是为了提高模具的光滑度和亮度,以增加产品的表面质量。
喷漆是为了保护模具,增加其耐蚀性和美观性。
而表面处理可以根据不同的需求进行选择,如电镀、喷砂等。
总结起来,塑料模具加工工艺流程包括准备工作、外形制作、模具零件加工、组装、热处理、试模和后处理等步骤。
每个步骤都需要严格控制工艺参数,以确保模具的精确度和质量,从而制作出满足产品要求的塑料模具产品。
塑料制品模具的制造与加工工艺

塑料制品模具的制造与加工工艺模具技术是塑料制品生产中至关重要的环节之一,它直接影响着塑料制品的质量和效率。
本文将介绍塑料制品模具的制造与加工工艺,并详细阐述其中的关键步骤和注意事项。
一、模具的制造工艺1. 模具设计模具设计是模具制造的第一步,它要根据产品的要求确定模具的结构和尺寸。
设计时需考虑产品的材料、形状、尺寸等因素,并进行模具结构的合理布局。
模具设计需要使用CAD软件进行三维建模,确保模具的精度和稳定性。
2. 模具材料的选择模具材料的选择直接影响模具的质量和寿命。
目前常用的模具材料有钢材、铝合金等。
钢材具有高强度、高硬度和耐磨性好的特点,适合制造大型模具和复杂结构的模具。
铝合金则适合制造小型模具和简单结构的模具。
3. 模具加工模具加工包括粗加工和精加工两个阶段。
粗加工主要是对模具的整体加工和切割,如铣削、钻孔等。
精加工则是对模具的细节部分进行加工,如线切割、电火花等。
加工精度的控制对模具的质量至关重要,需要采取适当的加工工艺和加工设备。
4. 模具装配与调试模具加工完成后,需要进行模具的装配和调试,以确保各零部件的配合和动作正常。
装配时需注意各零部件之间的间隙和配合度,确保模具的运动平稳、无卡阻。
调试则是对模具的动作进行调整和测试,发现问题及时进行修正,保证模具的正常运行。
二、模具的加工工艺1. 材料预处理模具加工前需要对模具材料进行预处理,包括淬火、回火等热处理工艺,以提高模具的硬度和强度,增加其使用寿命。
2. 加工工艺选择模具加工可采用传统的机械加工工艺,也可以采用数控加工工艺。
数控加工具有高精度、高效率和自动化程度高的优点,适用于复杂结构和高精度要求的模具加工。
3. 加工步骤模具加工一般包括粗加工、精加工和热处理三个步骤。
粗加工主要是对模具的整体加工和切割,如铣削、钻孔等;精加工则是对模具的细节部分进行加工,如线切割、电火花等;热处理是对模具材料进行加热处理,提高其硬度和强度。
4. 加工质量控制模具的加工质量控制是确保模具精度和稳定性的重要环节。
塑料模具加工工艺流程

塑料模具加工工艺流程塑料模具加工工艺流程是指将塑料作为原料制作成模具的过程。
塑料模具加工工艺流程包括模具设计、模具制造、模具调试和模具使用等环节。
下面将详细介绍塑料模具加工工艺流程。
一、模具设计。
模具设计是塑料模具加工的第一步,它是塑料模具加工中最重要的环节。
模具设计是根据产品的形状和结构来确定模具的结构和尺寸。
模具设计的主要内容包括模具零件的设计、模具结构的设计和模具尺寸的设计等。
模具设计的目标是根据产品的需求来设计一个满足产品要求的模具。
在设计模具时,需要考虑到产品的形状、尺寸、精度和使用要求等方面的要求,同时还要考虑到模具的制造成本和使用成本等因素。
二、模具制造。
模具制造是根据模具设计图纸来制造模具的过程。
模具制造主要包括材料选择、模具加工、模具装配和模具调整等环节。
模具制造的第一步是材料选择,选择合适的模具材料非常重要。
常用的模具材料有钢铁、铝合金和塑料等。
材料选择要考虑到使用环境、成本和使用寿命等因素。
模具加工是根据模具设计图纸来进行的。
模具加工主要包括铣削、车削、磨削、打磨和组立等工艺。
模具加工的目标是按照设计图纸上的要求来制造模具。
模具装配是将加工好的模具零件进行组装成一个完整的模具。
模具装配要求装配精度高,零部件之间配合紧密。
模具调整是指在装配完成后,对模具进行调试和调整,使模具能够正常工作。
模具调试主要包括模具安装、模具调整和模具试运行等环节。
模具调试的目标是能够满足产品生产的需求。
三、模具使用。
模具使用是指将制作好的模具应用于产品生产的过程。
模具使用主要包括模具装夹、产品加工和质量控制等环节。
模具装夹是将模具安装到机床或注塑机上,使之能够进行产品加工。
模具装夹要求对模具进行准确、稳定和可靠的装夹。
产品加工是利用模具对原料进行加工,使之成为符合要求的产品。
产品加工要求模具加工精度高,加工效率高和加工质量高。
质量控制是对加工好的产品进行检验,以确保产品质量满足要求。
质量控制主要包括尺寸检验、外观检验和性能检验等环节。
塑料模压成型工艺与实例
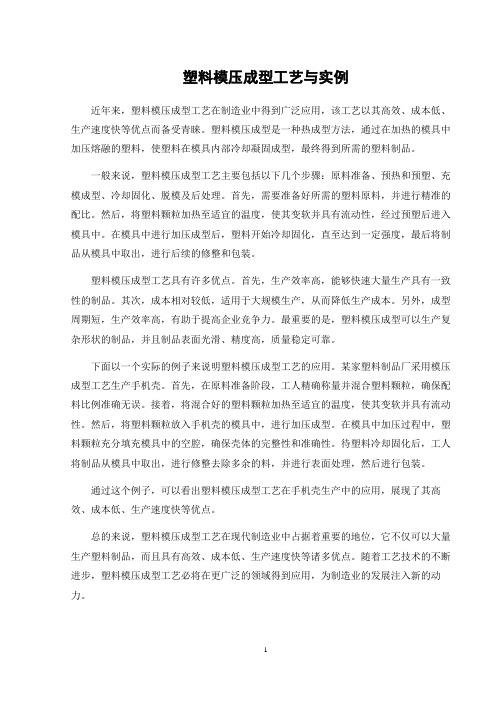
塑料模压成型工艺与实例近年来,塑料模压成型工艺在制造业中得到广泛应用,该工艺以其高效、成本低、生产速度快等优点而备受青睐。
塑料模压成型是一种热成型方法,通过在加热的模具中加压熔融的塑料,使塑料在模具内部冷却凝固成型,最终得到所需的塑料制品。
一般来说,塑料模压成型工艺主要包括以下几个步骤:原料准备、预热和预塑、充模成型、冷却固化、脱模及后处理。
首先,需要准备好所需的塑料原料,并进行精准的配比。
然后,将塑料颗粒加热至适宜的温度,使其变软并具有流动性,经过预塑后进入模具中。
在模具中进行加压成型后,塑料开始冷却固化,直至达到一定强度,最后将制品从模具中取出,进行后续的修整和包装。
塑料模压成型工艺具有许多优点。
首先,生产效率高,能够快速大量生产具有一致性的制品。
其次,成本相对较低,适用于大规模生产,从而降低生产成本。
另外,成型周期短,生产效率高,有助于提高企业竞争力。
最重要的是,塑料模压成型可以生产复杂形状的制品,并且制品表面光滑、精度高,质量稳定可靠。
下面以一个实际的例子来说明塑料模压成型工艺的应用。
某家塑料制品厂采用模压成型工艺生产手机壳。
首先,在原料准备阶段,工人精确称量并混合塑料颗粒,确保配料比例准确无误。
接着,将混合好的塑料颗粒加热至适宜的温度,使其变软并具有流动性。
然后,将塑料颗粒放入手机壳的模具中,进行加压成型。
在模具中加压过程中,塑料颗粒充分填充模具中的空腔,确保壳体的完整性和准确性。
待塑料冷却固化后,工人将制品从模具中取出,进行修整去除多余的料,并进行表面处理,然后进行包装。
通过这个例子,可以看出塑料模压成型工艺在手机壳生产中的应用,展现了其高效、成本低、生产速度快等优点。
总的来说,塑料模压成型工艺在现代制造业中占据着重要的地位,它不仅可以大量生产塑料制品,而且具有高效、成本低、生产速度快等诸多优点。
随着工艺技术的不断进步,塑料模压成型工艺必将在更广泛的领域得到应用,为制造业的发展注入新的动力。
塑胶模具制作流程

塑胶模具制作流程塑胶模具制作是一项复杂的工艺,需要经过多个步骤才能完成一个高质量的塑胶模具。
下面我将为大家介绍塑胶模具制作的详细流程。
首先,塑胶模具制作的第一步是设计。
设计师需要根据客户的要求和产品的需求,绘制出模具的结构图和尺寸。
设计图纸需要精确详细,确保模具制作的准确性和稳定性。
接下来是模具材料的准备。
根据设计图纸,选择合适的模具材料,通常包括金属材料和塑料材料。
金属材料通常用于制作模具的模具架和模具芯,而塑料材料则用于制作模具的外壳和一些细节部件。
选择合适的材料对于模具的质量和使用寿命至关重要。
第三步是加工制作。
根据设计图纸和模具材料,将金属材料进行切割、冲压、铣削等加工工艺,制作出模具的各个部件。
同时,塑料材料也需要经过注塑、挤压等工艺,制作出模具的外壳和细节部件。
加工制作需要严格按照设计要求进行,确保模具的精度和稳定性。
随后是组装调试。
将加工制作好的模具部件进行组装,进行调试和测试。
通过模具的组装调试,可以检验模具的使用效果和性能,发现并解决可能存在的问题,确保模具的正常使用。
最后是模具的使用和维护。
一旦模具制作完成并投入使用,需要定期进行维护保养,确保模具的正常使用和延长模具的使用寿命。
同时,根据不同的产品需求,可能需要对模具进行调整和改进,以满足不同产品的生产需求。
总的来说,塑胶模具制作是一个复杂而精细的工艺过程,需要设计、材料准备、加工制作、组装调试和使用维护等多个步骤的精心安排和协调。
只有每个步骤都做到位,才能制作出高质量的塑胶模具,满足不同产品的生产需求。
希望以上介绍对大家有所帮助,谢谢!。
塑料模具工艺流程

塑料模具工艺流程
《塑料模具工艺流程》
塑料模具工艺是一种用于制造塑料制品的加工方法,它涉及到许多复杂的步骤和工艺流程。
下面将简要介绍一下塑料模具工艺的流程。
首先,设计师需要根据客户的要求和产品的设计图纸来设计塑料模具。
设计师需要考虑到产品的尺寸、形状和结构,以及模具的生产工艺和制造成本等因素。
一旦模具设计完成,就可以开始制造模具。
模具制造通常包括铣削、电火花、磨削和装配等工序。
在铣削过程中,模具材料会被加工成设计所需的几何形状。
而在电火花加工中,通过电火花放电来切割金属材料。
在磨削工序中,模具表面会被打磨成光滑的表面。
最后,所有的零部件将被装配起来,形成一个完整的模具。
一旦模具制造完成,就可以开始进行注塑生产。
在注塑生产中,首先需要将塑料颗粒加热到熔化状态,然后将熔化的塑料通过射出机射入模具腔内。
在模具腔内,熔化的塑料会被冷却并凝固成为产品的形状。
最后,模具打开,成品可以取出。
除了注塑生产,塑料模具还可以用于吹塑、挤出、压延等生产工艺中。
不同的生产工艺需要不同类型的模具,并且工艺流程也会有所不同。
总的来说,塑料模具工艺是一个复杂而系统的生产过程,需要设计、制造、调试和生产等多个环节的配合。
只有这些环节都能做得精益求精,才能生产出高质量的塑料制品。
塑料模具分类、特点及其成型工艺规程
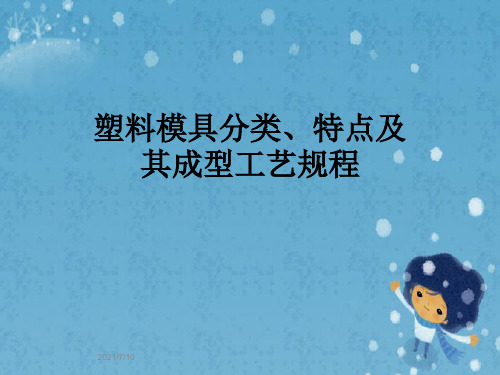
3.易产生应力集中,严格控制成型条件,塑件成型后退 火处理,消除内应力;塑件壁不宜厚,避免有尖角、缺 口和金属嵌件造成应力集中,脱模斜度宜取2℃ 。
2.塑件的尺寸精度分析
塑件外形尺寸: φ690-0.86 、 φ700-0.86 、 φ1270-1.28、 φ1290-1.28、φ1700-1.6 、 R50-0.24、 φ1370-1.28﹑30-0.2、 80-0.28﹑ 1330-1.28 内形尺寸:φ630+0.74、φ640+0.74、φ1140+1.14、φ1210+1.28、 R20+0.2、600+0.74、320+0.56、 300 +0.50、80+0.28、 φ1230+1.28、 φ1310+1.28、 φ1640+1.6 孔尺寸:φ100+0.32﹑ φ120+0.32、φ1370+1.28﹑φ1640+1.6﹑ φ4.50+0.24﹑ φ2.0+0.2、 φ50+0.24 孔心距尺寸:34±0.28﹑ φ96±0.50﹑ φ150±0.27
塑料模具分类、特点及 其成型工艺规程
2021/7/10
目录
1、塑料模具概念 2、塑料模具分类及特点 3、塑料模具结构 4、塑料模具材料 5、模塑成型工艺规程 6、塑料模塑成型及模具技术的发展动向
1、塑性模具概念
模具:——是指利用其本身特定形状去成型具有一 定形状和尺寸的制品的工具。
特点:
塑料注射(塑)模具
按成型过程中物理状态不同分 : 熔融成型
注射成型压机
塑胶模具制造流程
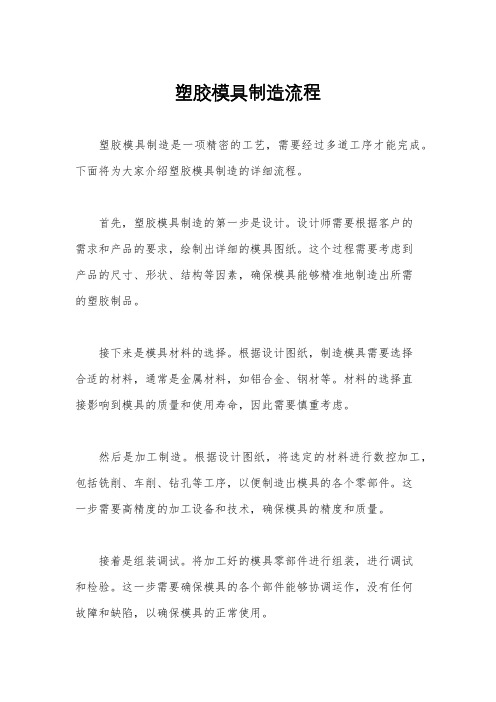
塑胶模具制造流程塑胶模具制造是一项精密的工艺,需要经过多道工序才能完成。
下面将为大家介绍塑胶模具制造的详细流程。
首先,塑胶模具制造的第一步是设计。
设计师需要根据客户的需求和产品的要求,绘制出详细的模具图纸。
这个过程需要考虑到产品的尺寸、形状、结构等因素,确保模具能够精准地制造出所需的塑胶制品。
接下来是模具材料的选择。
根据设计图纸,制造模具需要选择合适的材料,通常是金属材料,如铝合金、钢材等。
材料的选择直接影响到模具的质量和使用寿命,因此需要慎重考虑。
然后是加工制造。
根据设计图纸,将选定的材料进行数控加工,包括铣削、车削、钻孔等工序,以便制造出模具的各个零部件。
这一步需要高精度的加工设备和技术,确保模具的精度和质量。
接着是组装调试。
将加工好的模具零部件进行组装,进行调试和检验。
这一步需要确保模具的各个部件能够协调运作,没有任何故障和缺陷,以确保模具的正常使用。
最后是模具的表面处理。
经过组装调试的模具需要进行表面处理,以增加模具的硬度和耐磨性。
常见的表面处理方法包括热处理、镀硬铬、氮化等,以确保模具能够承受长时间的使用。
通过以上流程,一个完整的塑胶模具制造过程就完成了。
这个过程需要设计师、工程师、技术工人等多个环节的密切配合,以确保最终制造出的模具能够满足客户的需求和产品的要求。
塑胶模具制造是一项复杂而精密的工艺,需要高度的专业知识和技术。
只有经过严格的流程和质量控制,才能制造出高质量的塑胶模具,为客户提供优质的塑胶制品。
塑料模具加工工艺详述

塑料模具加工工艺详述塑料模具加工是将塑料原料加工成符合产品要求的生产工艺,它是制作塑料制品的重要步骤之一。
塑料模具的加工工艺对制品的加工效率、质量和成本有着重要的影响。
下面将详细介绍塑料模具加工的工艺流程与关键步骤。
1.设计模具:塑料模具的设计是非常关键的一步。
首先需要根据产品的形状和大小,确定模具的尺寸大小和结构,然后在CAD软件上进行绘制。
设计师需要考虑到产品的使用方式和材料特性,以及模具的操作性、维修性等方面,从而设计出一款结构合理、性能稳定的模具。
2.制造模具:制造模具是一个复杂的工艺,需要经过多个步骤。
首先,需要制作模具的基础部分,包括模板、腔体、芯棒、活动边、导柱、定位销等。
然后进行模具表面处理,通常采用电火花机加工、数控雕刻、高速雕铣等技术实现。
最后对模具进行组装和调试,确保其完好无损。
3.制作塑料制品:在制作模具之前,需要准备好塑料材料。
模具制作完成后,将塑料原料通过注塑机加热至熔融状态,然后注射进模具中。
在模具中冷却凝固后,就可以取出制品,进行喷漆、喷涂等后续处理。
这些处理方式不仅可以使产品更美观,还可以增加产品的耐用性和防腐性能。
4.模具维护:模具加工完成后,需要对其进行定期的维护和保养。
在使用过程中,可能会出现模具损坏、生锈、损耗等情况,需要及时进行修复和更换。
模具的维护不仅可以延长模具的使用寿命,还可以保障制品的质量和效率。
综上所述,塑料模具加工是一个多个步骤组成的复杂工艺。
在该工艺过程中,设计、制造、加工和维护都是非常关键的一步。
只有通过精细的设计和严格的操作流程,才能生产出优质的塑料制品,提高生产效率和降低生产成本。
塑料模具零件的制造工艺与热处理工艺

塑料模具零件的制造工艺与热处理工艺塑料模具零件的制造工艺与热处理工艺塑料模具是塑料制品生产中不可或缺的工具,其质量对整个生产过程和产品品质都有着非常重要的影响。
与传统铸造模具相比,塑料模具更加复杂、精细,因此制造工艺和热处理工艺的要求也更高。
一、塑料模具制造工艺塑料模具的制造工艺可以分为以下几个步骤:1. 雕刻模具结构图因为塑料模具的结构比较复杂,一些细节部分比如内腔、冷却孔等需要精细地设计和制造。
因此在制造前需要通过CAD 软件等进行雕刻模具结构图,确定每个细节的尺寸和位置,保证最终模具的精度和质量。
2. 加工模具原材料模具原材料通常为铝合金、钢和钛合金等,这些材料的选择需要考虑到模具的型号和制造成本。
模具原材料加工过程通常包括铣削、钻孔、车削和磨削等环节,保证每个部分的尺寸和平整度。
3. EDM或线切割电火花放电加工和线切割是模具加工中不可缺少的环节。
通过EDM或线切割去除多余材料,保证模具内部空间和细节部分的精度和平整度。
4. 磨削磨削是模具加工的最后一道工序,通过对各个部分进行细致的磨削,保证模具的精度和表面质量。
磨削也可以消除电火花放电和线切割造成的毛边,减小模具表面的粗糙度。
5. 组装模具的组装包括将各个部件组合在一起,按照结构图进行拼装。
组装过程中需要特别注意细节部分的尺寸和细节精度,保证最终模具的质量和生产效率。
6. 测试和调试模具制造完成后需要进行测试和调试,调整模具内部结构和冷却系统的参数,检查模具是否合格。
二、塑料模具热处理工艺塑料模具的热处理对模具的精度和寿命有着重要的影响。
常见的热处理工艺包括以下几种:1. 固溶处理固溶处理是指将模具加热到一定温度下,使其内部组织发生相变,改善模具的机械性能和物理性能。
固溶处理的温度和时间一般由模具材料和加工工艺决定,需要严格控制,以避免过度固溶导致模具内部出现脆性断裂。
2. 淬火处理淬火处理是指将模具加热到一定温度,然后迅速进行冷却,使其内部组织发生相变。
塑料模具制造加工方法
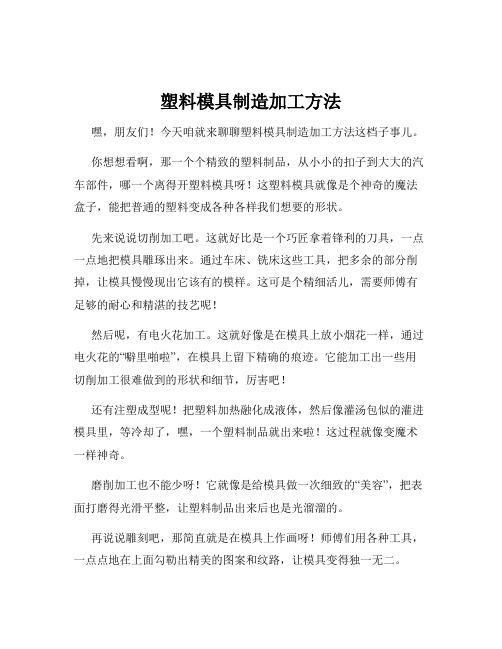
塑料模具制造加工方法嘿,朋友们!今天咱就来聊聊塑料模具制造加工方法这档子事儿。
你想想看啊,那一个个精致的塑料制品,从小小的扣子到大大的汽车部件,哪一个离得开塑料模具呀!这塑料模具就像是个神奇的魔法盒子,能把普通的塑料变成各种各样我们想要的形状。
先来说说切削加工吧。
这就好比是一个巧匠拿着锋利的刀具,一点一点地把模具雕琢出来。
通过车床、铣床这些工具,把多余的部分削掉,让模具慢慢现出它该有的模样。
这可是个精细活儿,需要师傅有足够的耐心和精湛的技艺呢!然后呢,有电火花加工。
这就好像是在模具上放小烟花一样,通过电火花的“噼里啪啦”,在模具上留下精确的痕迹。
它能加工出一些用切削加工很难做到的形状和细节,厉害吧!还有注塑成型呢!把塑料加热融化成液体,然后像灌汤包似的灌进模具里,等冷却了,嘿,一个塑料制品就出来啦!这过程就像变魔术一样神奇。
磨削加工也不能少呀!它就像是给模具做一次细致的“美容”,把表面打磨得光滑平整,让塑料制品出来后也是光溜溜的。
再说说雕刻吧,那简直就是在模具上作画呀!师傅们用各种工具,一点点地在上面勾勒出精美的图案和纹路,让模具变得独一无二。
在制造塑料模具的过程中,每一步都得小心翼翼的,就像走钢丝一样。
一个不小心,可能就会前功尽弃。
这可不是闹着玩的呀!咱再想想,如果没有这些加工方法,那我们的生活得失去多少精彩的塑料制品啊!那些漂亮的玩具、实用的工具、精美的装饰品,不都得大打折扣了吗?所以说,这些塑料模具制造加工方法可真是太重要啦!咱得感谢那些默默钻研和工作的模具制造师傅们,是他们用自己的智慧和汗水,让这些加工方法变得越来越精湛,让我们能享受到这么多好用又好看的塑料制品。
总之呢,塑料模具制造加工方法就是这么神奇又重要,它们让我们的生活变得更加丰富多彩。
大家说是不是呀!。
塑料模具加工工艺汇集

塑料模具加工工艺汇集塑料模具加工工艺汇集随着现代制造技术的不断发展,塑料模具加工工艺已经成为了工业生产中不可或缺的一部分。
塑料模具加工工艺主要是用于制造各种塑料制品的模具,这些模具包括塑料瓶、塑料盖子、塑料桶、塑料箱等各种塑料制品。
对于塑料模具加工工艺的掌握,不仅是提升工业生产效率的重要途径,也是为了符合环保和节能的要求。
塑料模具的加工过程主要包括图纸设计、加工设备准备、零件制作、装配调试、成品制造等环节。
在开始进行任何一项工艺之前,都必须进行精密的设计和制图工作。
设计师需要根据客户需求和所制造的产品特点进行制图,选择合适的塑料模型材料进行制作。
接下来就是进行模具零件制作,主要有数控车加工、铣床加工、钳工车加工、电火花加工等。
这些制作工艺需要高精度、高速度、高效率的设备。
装配调试环节是整个工艺过程中最为重要的一步,只有在这一步的调试过程中,才能确保所制造的塑料模具符合要求、准确可靠。
在调试过程中,需要检查并调整塑料模具的各个部分的配合精度、磨合度和运行稳定性等参数。
这些参数决定了塑料模具在整个生产过程中的稳定性和使用寿命。
在成品制造环节中,需要将制作好的塑料模具配合塑料原料进行塑料制品的成型。
根据产品不同特点和成分,制造工艺也各不相同,常见的有注塑成型、吹塑成型、挤塑成型等。
无论是哪种成型方式,都需要进行各个生产参数的调整以达到最佳的成型效果。
总结来看,塑料模具加工工艺需要科学的设计和精密的制作工艺,以达到最好的制造效果。
在不断的探索和实践中,各种新的加工工艺相继涌现。
领先的加工技术可以大幅度提高制作效率和质量,降低生产成本,使得塑料模具加工工艺更具生产力,更符合节能环保的要求。
塑料模具的三种主要成型方法

塑料模具的三种主要成型方法
1,注射成型
塑料的注射成型又称注塑成型。
该方法采用注射成型机将粒状的塑料连续输入到注射成型机料筒中受热并逐渐熔融,使其呈黏性流动状态,由料简中的螺杆或柱塞推至料筒端部,通过料简端部的喷嘴将熔体注入闭合的模具中,充满后经过保压和冷却,使制品固化定型,然后开启模具取出制品。
注射成型主要用于热塑性塑料,现在也用于热固性塑料。
注射成型的生产是周期性的。
2,挤出成型
挤出成型又称挤塑成型。
该方法与注射成型的原理类似,将粒状塑料在挤出机的料简中完成加热和加压过程,熔体经过装在挤出机机头上的成型口模挤出,然后冷却定型,借助牵引装置拉出,成为具有一定横截面形状的连续制品,加管、板及异型材制品等。
挤出成型是热塑性塑料的主要成型方法之一。
除了成型加工外,该方法还用于塑料的混炼加工,如着色、填充、共混等皆可通过挤出造粒工序来完成。
3,中空成型
中空成型又称吹塑成型。
它是制造中空制品和管简形薄膜的方法。
该法先用挤出机或注射机挤出或注出管简状的熔融坏料,然后将此坏料放入吹塑模具内,向坯料内吹入压缩空气,使中空的坯料均匀膨胀直至紧贴模具内壁,冷却定型后开启模具取出中空制品。
在工业生产如瓶、桶一类的热塑性制品均可用此法制造。
若将从挤出机中连续不断挤出的熔融塑料管筒内走趁热通入压缩空气,把管筒胀大撑薄,然后冷却定型,可以得到管筒形薄膜。
深圳模具厂:。
塑胶模具制作工艺流程

模具制作工艺流程如下:审图—备料—加工—模架加工—模芯加工—电极加工—模具零件加工—检验—装配—飞模—试模—生产A:模架加工:1 打编号,2 A/B 板加工,3 面板加工,4 顶针固定板加工,5 底板加工B:模芯加工:1 飞边,2 粗磨,3 铣床加工,4 钳工加工,5CNC 粗加工,6 热处理,7 精磨,8CNC 精加工,9 电火花加工,10 省模C:模具零件加工:1 滑块加工,2 压紧块加工,3 分流锥浇口套加工,4 镶件加工模架加工细节1,打编号要统一,模芯也要打上编号,应与模架上编号一致并且方向一致,装配时对准即可不易出错。
2, A/B 板加工(即动定模框加工),a:A/B 板加工应保证模框的平行度和垂直度为0.02mm,b :铣床加工:螺丝孔,运水孔,顶针孔,机咀孔,倒角c:钳工加工:攻牙,修毛边。
3,面板加工:铣床加工镗机咀孔或加工料嘴孔。
4,顶针固定板加工:铣床加工:顶针板与B 板用回针连结,B 板面向上,由上而下钻顶针孔,顶针沉头需把顶针板反过来底部向上,校正,先用钻头粗加工,再用铣刀精加工到位,倒角。
5,底板加工:铣床加工:划线,校正,镗孔,倒角。
(注:有些模具需强拉强顶的要加做强拉强顶机构,如在顶针板上加钻螺丝孔)模芯加工细节1)粗加工飞六边:在铣床上加工,保证垂直度和平行度,留磨余量1.2mm2)粗磨:大水磨加工,先磨大面,用批司夹紧磨小面,保证垂直度和平行度在0.05mm,留余量双边0.6-0.8mm3)铣床加工:先将铣床机头校正,保证在0.02mm 之内,校正压紧工件,先加工螺丝孔,顶针孔,穿丝孔,镶针沉头开粗,机咀或料咀孔,分流锥孔倒角再做运水孔,铣R 角。
4)钳工加工:攻牙,打字码5) CNC 粗加工6)发外热处理HRC48-527)精磨;大水磨加工至比模框负0.04mm,保证平行度和垂直度在0.02mm 之内8) CNC 精加工9)电火花加工10)省模,保证光洁度,控制好型腔尺寸。
塑料制品注塑模具制造工艺流程
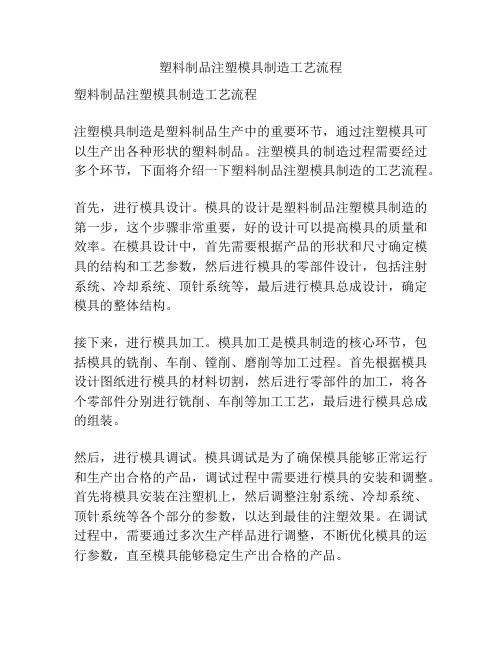
塑料制品注塑模具制造工艺流程塑料制品注塑模具制造工艺流程注塑模具制造是塑料制品生产中的重要环节,通过注塑模具可以生产出各种形状的塑料制品。
注塑模具的制造过程需要经过多个环节,下面将介绍一下塑料制品注塑模具制造的工艺流程。
首先,进行模具设计。
模具的设计是塑料制品注塑模具制造的第一步,这个步骤非常重要,好的设计可以提高模具的质量和效率。
在模具设计中,首先需要根据产品的形状和尺寸确定模具的结构和工艺参数,然后进行模具的零部件设计,包括注射系统、冷却系统、顶针系统等,最后进行模具总成设计,确定模具的整体结构。
接下来,进行模具加工。
模具加工是模具制造的核心环节,包括模具的铣削、车削、镗削、磨削等加工过程。
首先根据模具设计图纸进行模具的材料切割,然后进行零部件的加工,将各个零部件分别进行铣削、车削等加工工艺,最后进行模具总成的组装。
然后,进行模具调试。
模具调试是为了确保模具能够正常运行和生产出合格的产品,调试过程中需要进行模具的安装和调整。
首先将模具安装在注塑机上,然后调整注射系统、冷却系统、顶针系统等各个部分的参数,以达到最佳的注塑效果。
在调试过程中,需要通过多次生产样品进行调整,不断优化模具的运行参数,直至模具能够稳定生产出合格的产品。
最后,进行模具保养和维修。
模具的保养和维修是模具制造的最后一环,也是一个重要的环节。
模具在生产过程中会受到磨损和损坏,因此需要定期进行保养和维修。
模具保养包括清洗模具、润滑模具、更换损坏零部件等,以保证模具的正常运行。
而当模具出现损坏时,需要进行维修,包括修补模具表面、更换受损部件等。
综上所述,塑料制品注塑模具制造的工艺流程包括模具设计、模具加工、模具调试以及模具保养和维修等多个环节。
每个环节都非常重要,需要精细操作和严格把控。
只有在每个环节都做好的情况下,才能生产出质量合格的塑料制品。
同时,注塑模具制造也需要不断创新和改进,以适应不同产品的需要。
在注塑模具制造工艺流程之外,还有一些相关的内容需要考虑和涉及。
- 1、下载文档前请自行甄别文档内容的完整性,平台不提供额外的编辑、内容补充、找答案等附加服务。
- 2、"仅部分预览"的文档,不可在线预览部分如存在完整性等问题,可反馈申请退款(可完整预览的文档不适用该条件!)。
- 3、如文档侵犯您的权益,请联系客服反馈,我们会尽快为您处理(人工客服工作时间:9:00-18:30)。
塑料模具工艺
常见透明塑料的性能及注塑工艺
--------------------------------------------------------------------------------
发表时间:2009-02-04 19:49 来源: 作者: 点击:次由于塑料具有重量轻、韧性好、成型易、成本低等优点,因此在现代工业和日用产品中,越来越多用塑料代替玻璃,特别应用于光学仪器和包装工业方面,发展尤为迅速。
但是由于要求其透明性要好,耐磨性要高,抗冲击韧件要好,因此对塑料的成份,注塑整个过程的工艺、设备、模具等,都要做大量工作,以保证这些用于代替玻璃的塑料(以下简称透明塑料),表面质量良好,从而达到使用的要求。
目前市场上一般使用的透明塑料有聚甲基丙烯酸甲酯(PMMA,即俗称压克力或有机玻璃,)、聚碳酸酯(PC)、聚对苯二甲酸乙二醇脂(PET)、透明尼龙、丙烯睛一苯乙烯共聚物(AS)、聚砜(PSF)等,其中我们接触得最多的是PMMA、PC和PET三种塑料,下面就以这三种塑料为例,讨论透明塑料的特性和注塑工艺。
一、透明塑料的性能
透明塑料首先必须有高透明度,其次要有一定的强度和耐磨性,能抗冲击,耐热性要好,耐化学性要优,吸水率要小,只有这样才能在使用中,能满足透明度的要求而长久不变,下面列出表l,比较一下 PMMA、PC和PET的性能。
表1:透明塑料性能比较
性能密度
(g/am2) 抗拉强度
(MPa) 缺口冲击
(J/m2) 透明度
(%) 变形温度
(℃) 允许含水量收缩率耐磨性抗化学性
PMMA 1.18 75 1200 92 95 0.04 0.5 差良
PC 1.20 66 1900 90 137 0.02 0.6 中良
PET 1.37 165 1030 86 120 0.03 2 良优
注:(1)因品种繁多,这只是取平均值,实际不同品种数据有异。
(2)PET数据(机械方面)为经拉伸后的数据。
从表1数据可知PC是较理想的选择,但主于其原料价贵和注塑工艺较难,所以仍以选用PMMA为主,(对一般要求的制品),而RET由于要经过拉伸才能得到好的机械性能,所以多在包装、容器中使用。
二、透明塑料注塑过程中应注意的共同问题
透明塑料由于透光率要高,必然要求塑料制品表面质量要求严格,不能有任何斑纹、气孔、泛白、雾晕、黑点、变色、光泽不佳等缺陷,因而在整个注塑过程对原料、设备、模具、甚至产品的设计,都要十分注意和提出严格甚至特殊的要求。
其次由于透明塑料多为熔点高、流动性差,因此为保证产品的表面质量,往往要在较高温度、注射压力、注射速度等工艺参数作细微调整,使注塑料时既能充满模,又不会产生内应力而引起产品变形和开裂。
下面就其在原料准备、对设备和模具要求、注塑工艺和产品的原料处理几方面,谈谈应注意的事项。
(一)原料的准备与干燥由于在塑料中含有任何一点杂质,都可能影响产品的透明度,因此和储存、运输、加料过程中,必须注意密封,保证原料干净。
特别是原料中含有水分,加热后会引起原料变质,所以一定要干燥,并在
注塑时,加料必须使用干燥料斗。
还要注意一点的是干燥过程中,输入的空气最好应经过滤、除湿,以便保证不会污染原料。
其干燥工艺如表2。
表2:透明塑料的干燥工艺:
工艺干燥温度(℃)干燥时间(h)料层厚度(mm)备注
PMMA 70~80 2~4 30~40 采用热风循环干燥
PC 120~130 大于6 小于30 采用热风循环干燥
PET 140~180 3~4 采用连续干燥加料装置为佳
(二)机筒、螺杆及其附件的清洁
为防止原料污染和在螺杆及附件凹陷处存有旧料或杂质,特别热稳定性差的树脂存在,因此在使用前、停机后都应用螺杆清洗剂清洗干净各件,使其不得粘有杂质,当没有螺杆清洗剂时,可用PE、PS等树脂清洗螺杆。
当临时停机时,为防止原料在高温下停留时间长,引起解降,应将干燥机和机筒温度降低,如 PC、PMMA等机筒温度都要降至 160℃以下。
(料斗温度对于 PC应降至100℃以下)
(三)在模具设计上应注意的问题(包括产品的设计)
为了防止出现回流动不畅,或冷却不均造成塑料成型不良,产生表面缺陷和变质,一般在模具设计时,应注意以下几点。
a)壁厚应尽量均匀一致,脱模斜度要足够大;
b)过渡部分应逐步。
圆滑过渡,防止有尖角。
锐边产生,特别是PC产品一定不要有缺口;
c)浇口。
流道尽可能宽大、粗短,且应根据收缩冷凝过程设置浇口位置,必要时应加冷料井;
d)模具表面应光洁,粗糙度低(最好低于0.8);
e)排气孔。
槽必须足够,以及时排出空气和熔体中的气体;
f)除 PET外,壁厚不要太薄,一般不得小于lmm。
(四)注塑工艺方面应注意的问题(包括注塑机的要求)
为了减少内应力和表面质量缺陷,在注塑工艺方面应注意以下几方面的问题。
a)应选用专用螺杆、带单独温控射咀的注塑机;
b)注射温度在塑料树脂不分解的前提下,宜用较高注射湿度;
c)注射压力:一般较高,以克服熔料粘度大的缺陷,但压力太高会产生内应力造成脱模因难和变形;
d)注射速度:在满足充模的情况下,一般宜低,最好能采用慢-快-慢多级注射;
e)保压时间和成型周期:在满足产品充模,不产生凹陷、气泡的情况下;宜尽量短,以尽量减低熔料在机筒停留时间;
f)螺杆转速和背压:在满足塑化质量的前提下,应尽量低,防止产生解降的可能;
g)模具温度:制品的冷却好坏,对质量影响极大,所以模温一定要能精确控制其过程,有可能的话,模温宜高一些好。
(五)其他方面的问题
由于为要防上表面质量恶化,一般注塑时尽量少用脱模剂;当用回用料时不得大20%。
对于除PET外,制品都应进行后处理,以消除内应力,PMMA应在70-80T热风循环干燥4小时; PC应在清洁空气、甘油。
液体石腊等加热 110-135℃,时间按产品而定,最高需要10多小时。
而PET必须经过双向拉伸的工序,才能得到良好机械性能。
三、透明塑料的注塑成型工艺
(一)透明塑料的工艺特性:除了以上的共同问题,透明塑料亦各有一些工艺特性,现分述如下:
1、PMMA 的工艺特性
PMMA粘度大,流动性稍差,因此必须高料温、高注射压力注塑才行,其中注射温度的影响大于注射压力,但注射压力提高,有利于改善产品的收缩率。
注射温度范围较宽,熔融温度为 160℃,而分解温度达270℃,因此料温调节范围宽,工艺性较好。
故改善流动性,可从注射温度着手。
冲击性差,耐磨性不好,易划花,易脆裂,故应提高模温,改善冷凝过程,去克服这些缺陷。
2、PC的工艺特性
PC粘度大,融料温度高,流动性差,回此必须以较高温度注塑(270-320T之间),相对来说料温调节范围较窄,工艺性不如PMMA。
注射压力对流动性影响较小,但因粘度大,仍要较大注射压力,相应为了防止内应力产生,保压时间要尽量短。
收缩率大,尺寸稳定,但产品内应力大,易开裂,所以宜用提高温度而不是压力去改善流动性,并且从提高模具温度,改善模具结构和后处理去减少开裂的可能。
当注射速度低时,浇口处易生波纹等缺陷,放射咀温度要单独控制,模具温度要高,流道、浇口阻力要小。
3、PET的工艺特性
PET成型温度高,且料温调节范围窄(260-300℃),但熔化后,流动性好,故工艺性差,且往往在射咀中要加防延流装置。
机械强度及性能注射后不高,必须通过拉伸工序和改性才能改善性能。
模具温度准确控制,是防止翘曲。
变形的重要因素,因此建议采用热流道模具。
模具温度高,否则会引起表面光泽差和脱模困难。
四、透明塑料件的缺陷
由于篇幅关系,这里只讨论影响产品透明度的缺陷,其他缺陷请参考产品说明书或其他资料。
其缺陷大概有以下几项:
透明产品的缺陷和克服方法:
(一)银纹:由充模和冷凝过程中,内应力各向异性影响,垂直方向产生的应力,使树脂发生流动上取向,而和非流动取向产生折光率不同而生闪光丝纹,当其扩展后,可能使产品出现裂纹。
除了在注塑工艺和模具上注意外(见表,最好产品作退火处理。
如pc料可加热到160℃以上保持3~5分钟,再自然冷却即可。
(二)气泡:主于树脂内的水气和其他气体排不出去,(在模具冷凝过程中)或因充模不足,冷凝表面又过快冷凝而形成“真空泡”。
其克服方法见表。
(三)表面光泽差:主于模具粗糙度大,另一方面冷凝过早,使树脂不能复印模具表面的状态,所有这些都使其表面产牛微小凹凸不平,而使产品失去光泽。
其克服方法见表。
(四)震纹:是指从直浇口为中心形成的密集波纹,其原因因熔体粘度过大,前端料已在型腔冷凝,后来料又冲破此冷凝面,而使表面出现震纹。
其克服方法见表。
(五)泛白。
雾晕:主要由于在空气中灰尘落入原料之中或原料含水量太大而引起的。
其克服方法见表。
(六)白烟。
黑点:主要由于塑料在机筒内,因局部过热而使机筒树脂产生分解或变质而形成的。