项目五螺纹的编程与加工
螺纹的编程及加工
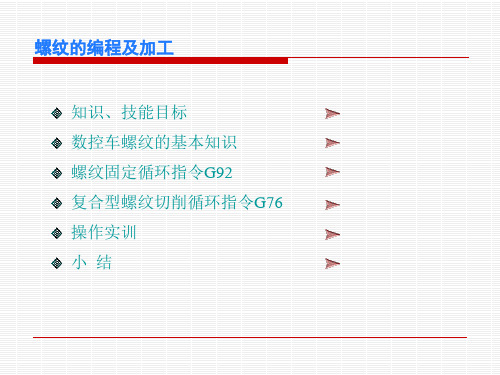
续 表
数控车床 程序卡 程序号 序号 N160 N170 N180 N190 N200 N210 N220 N230 N240 N250 N260 N270 N280 N290 N300
编程原点 零件名称 车床型号
续表 1 工件右端面与轴线交点 螺纹套 零件图号 图 7-11(b) CAK6150DJ O7002 程序 夹具名称 三爪卡盘 编程系统
d:精车余量,用半径编程指定,单位:微米,该参数为模态量; X(U)、Z(W):螺纹终点绝对坐标或增量坐标;
i:螺纹锥度值,用半径编程指定。如果i = 0则为直螺纹,可省略;
k:螺纹高度,用半径编程指定,单位:微米; d:第一次车削深度,用半径编程指定,单位:微米; L:螺纹的导程。
图7-8 螺纹切削多次循环示例
零件图工艺分析
数值计算 工件参考程序与加工操作过程
安全操作和注意事项
零件图工艺分析
(1)技术要求分析。如图7-11(b)所示,零件包括圆柱面、倒角、内螺纹和切断等加工。 零件材料为45#钢,无热处理和硬度要求。 (2)确定装夹方案、定位基准、加工起点、换刀点。由于毛坯为棒料,用三爪自定心卡盘 夹紧定位。由于工件较小,为了加工路径清晰,加工起点和换刀点可以设为同一点,放在Z向 距工件前端面200mm,X向距轴心线100mm的位置。 (3)制定加工方案,确定各刀具及切削用量。加工刀具的确定如表7-5所示,加工方案的制 定如表7-6所示。
建立工件坐标系 主轴正转,选择 1 号外圆刀 进给速度为 mm/r 快速定位至 38 直径,距端面正向 2 mm 刀具与端面对齐 加工端面 定位至 38 直径外,距端面正向 2 mm 粗车 30 外圆,留精加工余量 0.2mm 粗车倒角 返回刀具起始点,取消刀补,停主轴 程序暂停,检测工件 换转速,主轴正转,选镗孔刀 快速定位至(X14,Z2)位置 粗镗 M 20 孔,留精加工余量 0.2mm 返回刀具起始点,取消刀补,停主轴
数控车床编程与操作(五)_螺钉的加工

90°外圆车 刀(T01)
量具
夹具
游标卡尺 三爪卡盘
千分尺 三爪卡盘
游标卡尺 三爪卡盘
螺纹规 三爪卡盘
游标卡尺 三爪卡盘
游标卡尺 三爪卡盘
备注 自动 自动 自动 自动 自动 手动
任务二 工艺分析
工序示意图:
工序一
工序二
任务二 工艺分析
二、选择切削用量
在车削螺纹时,车床的主轴转速受到螺纹的螺距P(或导程)、 驱动电机的特性及螺纹插补运算速度等多种因素影响,所以对于 不同的数控系统,有不同的主轴转速选择范围。大多数经济型车 床数控系统车螺纹时推荐主轴转速如下:N≤1200/P-K (K为保 险系数,一般取80)。 单线螺纹的进给速度等于螺距,即F=P,单位为mm/r。 多线螺纹的进给速度等于导程,即F=S,单位为mm/r。 (S=P×n n为线数)
指令格式
带小数点的数,单位为s。如G04 X5.0表
G04 X__
示前面的程序执行完后,要经过5s的进给暂 停后,才能执行下面的程序段,采用P值表
G04 U__
示,P后面不允许用小数点,单位为ms,如
G04 P__
G04 P1000表示暂停1s。
3、螺纹的车削循环—G92指令
G92 X(U) __Z(W) __R__F__;
(2)螺纹小径的计算一般用公式d=D-1.3P(D为公称直径,d为 螺纹小径)
任务三 程序编制
2、螺纹轴向起点和终点尺寸的确定
在数控机床上车螺纹时,沿螺距方向的z向进给应和机床主轴的旋转 保持严格的速比关系,但在实际车削螺纹的开始时,伺服系统不可避 免地有一个加速的过程,结束也相应有一个减速的过程。在这两段时 间内,螺距得不到有效保证。为了避免在进给机构加速或减速过程中 切削,故在安排其工艺时要尽可能考虑合理的导入距离s1 和导出距 离s2,如图5-4所示。
螺纹的加工与编程
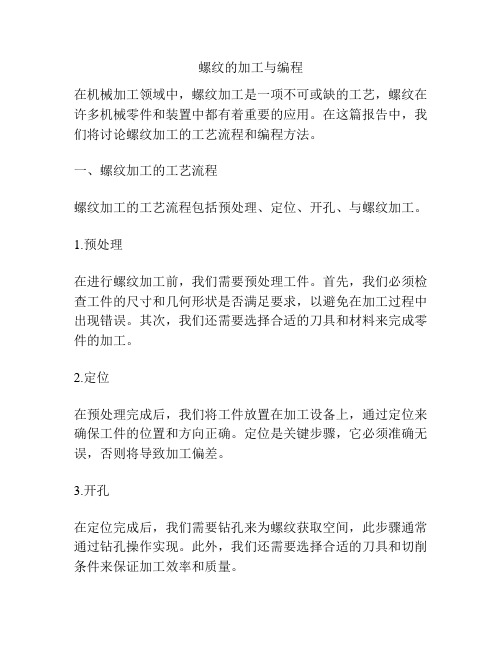
螺纹的加工与编程在机械加工领域中,螺纹加工是一项不可或缺的工艺,螺纹在许多机械零件和装置中都有着重要的应用。
在这篇报告中,我们将讨论螺纹加工的工艺流程和编程方法。
一、螺纹加工的工艺流程螺纹加工的工艺流程包括预处理、定位、开孔、与螺纹加工。
1.预处理在进行螺纹加工前,我们需要预处理工件。
首先,我们必须检查工件的尺寸和几何形状是否满足要求,以避免在加工过程中出现错误。
其次,我们还需要选择合适的刀具和材料来完成零件的加工。
2.定位在预处理完成后,我们将工件放置在加工设备上,通过定位来确保工件的位置和方向正确。
定位是关键步骤,它必须准确无误,否则将导致加工偏差。
3.开孔在定位完成后,我们需要钻孔来为螺纹获取空间,此步骤通常通过钻孔操作实现。
此外,我们还需要选择合适的刀具和切削条件来保证加工效率和质量。
4.螺纹加工在开孔完成后,我们才能进行螺纹加工,螺纹加工中最常用的方法是螺纹攻丝法,通过攻丝器将螺纹切削到孔中。
同时,我们需要选择正确的攻丝器、刀具和切削参数来确保加工质量。
二、螺纹加工的编程方法螺纹加工的编程方法通常有以下几种:1.手动编程这是一种较为基础的编程方法,操作人员通过手动输入加工程序代码,控制加工设备完成加工过程。
手动编程适用于简单的螺纹加工任务,但对于复杂、精密的加工任务则存在一定的误差风险。
2.自动编程自动编程采用计算机辅助制造(CAM)软件来自动生成加工程序。
操作人员只需要输入几何形状和加工标准等参数,CAM软件就可以自动计算出加工过程中要用到的切削路径、刀具类型和切削参数等信息。
3.机床编程机床编程利用数控加工设备自带的编程功能,将加工程序直接输入到设备中。
这种编程方法能够实现高效、自动化的加工过程,并在一定程度上增加了加工精度和稳定性。
三、螺纹加工的注意事项1.选择正确的切削条件在螺纹加工中,正确选择适合的切削条件对加工质量是至关重要的,可能会影响到螺纹质量和加工效率。
2.注意刀具的磨损情况刀具是直接参与螺纹加工的元器件,对螺纹质量有着非常重要的影响。
数控车床编程与操作 项目五 螺纹的编程与加工
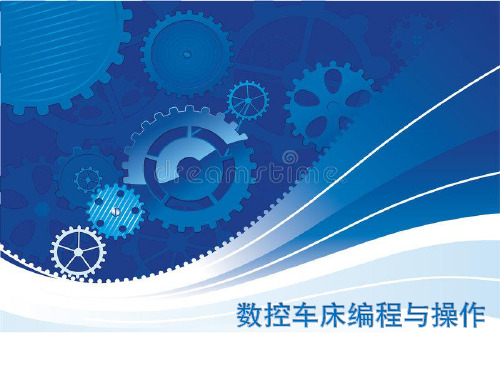
3、螺纹车刀装夹注意事项 (1) 螺纹车刀的刀尖角的对称中心线必须与工件的轴线垂直,否则, 加工的牙型会产生歪斜。 (2) 螺纹车刀的刀尖与数控车床的主轴轴线等高或略高0.1~0.2mm,防 止产生振动和“扎刀”。 (3) 螺纹车刀悬伸不宜过长,一般为刀体厚度的1.5倍。
二、程序编制
外轮廓及切槽加工程序略
N90 N100 N110 N120 N130 N140 N150 N160 N170 N180 N190 N200 N210 N220
量依次为1mm、0.6mm、0.25mm、0.1mm。
(2)螺纹加工起点和终点的位置 螺纹切削导入距离δ1≈(2~3)P=3~4.5(mm),取4mm。 导出距离δ2≈(1~2)P=1.5~3(mm),根据退刀槽宽取3mm。
任务一 常用螺纹切削指令
2、刀具及切削用量选择
数控车刀参数及切削用量表
刀具号 刀具名称
(3)螺纹总切深的计算 螺纹的总切深:h'≈1.3P。
任务一 常用螺纹切削指令
2 、螺纹起点和终点的确定 在安排其工艺时要尽可能考虑合理的导入距离δ1和导出距离δ2。
一般导入距离δ1取2~3P,对大螺距和高精度的螺纹则取较大值; 导出距离δ2一般取1~2P。若螺纹退尾处没有退刀槽时,其δ2=0。
任务一 常用螺纹切削指令
1.掌握G32、G34等螺纹切削指令的格式及其编程
知识目标 2.掌握普通三角螺纹的相关知识
3.掌握三角螺纹的尺寸控制及检测方法
技能目标
1.能够运用螺纹切削指令编程,并完成普通三角螺纹的加工 2.螺纹刀的正确装夹与使用
数控编程螺纹的加工

具体加工过程
• 编程时 控制螺纹两个方向(轴向和径向) 参数
• 轴向 • 需有开始的加速段和结束的减速段,否则
将乱牙 • 径向 • 根据牙深值确定每次切削的量(可查表)
趋势是先大后小
• 根据以上说明即可加工螺纹。
螺纹加工的调整
• 适配以能匹配相应内螺纹
螺纹的检测
螺纹加工
• 如何加工外螺纹 • 如何加工内、外螺纹 • 如何检测螺纹
螺纹的概述
• 螺纹的功能和分类 • 紧固,传动,密封 • 按形状分类:三角形,矩形,梯形,锯齿
形,特型等。
螺纹的形成
• 能否结合接触过的螺纹联接它的运动方式 得出螺旋运动是怎么形成的
• 螺旋运动由两个运动组成,可以看作是一 个点在圆柱面上,沿着轴线方向的移动和 绕着轴线方向的转到两个运纹矩形形 成矩形螺纹,其它形状就成了对应的螺纹。
• 左旋和右旋螺纹的形成
• 以上为定性描述,要得到准确的螺纹还需 对螺纹定量描述。
• 螺纹参数: 公称直径 : d 螺距:P
螺纹参数
• 牙型角:60° • 牙深:0.65P • 螺纹旋向:左 ,右(一般右旋)
• 线数:n(一般为单线)
• 简单方法能否和对应参数内螺纹旋合。
p
p
h
M10X1
牙深:0.65P
M10X1 牙深:0.65 直径值1.3
直径值1.3 1 0.2 0.1
Z 起始: 终点:
螺纹的加工
• 让机床实现螺旋运动即可加工螺纹 • 即工件旋转同时刀具沿轴向运动,此时刀
具相对工件在转动又沿着工件轴线移动形 成了螺旋运动,工件上面就可形成螺纹
• 把这个运动用指令表示出来就是加工螺纹 的指令G32和G92
项目五-螺纹类零件的数控车削加工解析PPT教学课件

2020/10/16
数控车床操作与加工 项目式教程5
任务5-1 圆柱螺纹类零件的数控车削加工
螺纹切削循环指令(G92) 格式:圆柱螺纹:G92 X(U)__ Z(W)__F__;
锥螺纹: G92 X(U)__ Z(W)__I__ F__; 其中X,Z(U,W)为螺纹切削终点坐标; I为螺纹的锥度,起点与终点的半径差(有正负之分)。加工圆柱螺 纹时,I=0。加工圆锥螺纹时,当X向切削起始点坐标小于切削终点坐标 时,I为负;反之为正。 例:如图所示的程序 ……; G00 X40.0 Z5.0; G92 X29.3 Z-42.0 F2.0;
2020/10/16
数控车床操作与加工 项目式教程10
任务5-1 圆柱螺纹类零件的数控车削加工
(4) 分层切削深度 如果螺纹牙型较深、螺距较大,可分几次进给,每次进给的 背吃刀量用螺纹深度减精加工背吃刀量所得的差按递减规律分配。 常用米制螺纹切削的进给次数与背吃刀量见表5-1,常用英制螺 纹切削的进给次数与背吃刀量见表5-1。
数控车床操作与加工 项目式教程3
任务5-1 圆柱螺纹类零件的数控车削加工
对于锥螺纹,如图5-2所示,角α在45°以下时,螺纹导程以Z轴方向指 定;角α在45°以上至90°时,螺纹导程以X轴方向指定;
图5-2 螺纹切削G32
螺纹切削应注意在两端设置足够的升速进刀段δ1和降速退刀段δ2。
2020/10/16
任务5-1 圆柱螺纹类零件的数控车削加工
5.1.1 基本螺纹切削G32 编程格式: G32 X(U) __Z(W) __ F __ ; 其中:X(U)、Z(W)——螺纹切削的终点坐标值,X省略时
为圆柱螺纹切削,Z省略时为端面螺纹切削,X、Z均不省略时 为锥螺纹切削;
螺纹加工数控编程
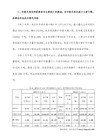
1、 G32用于公制螺纹加工、G33用于英制螺纹加工
2、 X(U)、 Z(W)为切削终点坐标、F 为螺纹导程
螺 纹 加 工 一 般 指 令
G32/G33与G01的区别是:通过脉冲编码器,能保证刀具在直线 移动时与主轴保持同步,即主轴旋转一周,刀具移动一个导程。
(二)应用类型 1、切削圆柱螺纹 G32/G33 Z(W)---F----
2、切削圆锥螺纹 G32/G33 X(U)---- Z(W)---3、切削端面螺纹 G32/G33 X(U)---- F----
F----
螺 纹 加 工 一 般 指 令
螺纹加工涉及6个方面的问题,编程时应多加注意:
1、主轴应指令恒转速(G97),螺纹加工中直径“X”是变化的
加 工 螺 纹 时 应 注 意 的 事 项
O0001 G50 X100. Z100. X59.1 G32 Z-53. F2 G97 M03 S600 G00 X62. T0101 Z5. G00 X62. Z5.
螺纹加工数控编程
螺纹加工指令
数控车床主要用于加工轴类、盘类等 回转体零件。机器中最常用的零件就是轴, 其作用是支撑零件、传递运动,如齿轮等, 齿轮一般通过螺纹实现轴向定位,所以螺 纹是轴类零件主要的组成面,掌握螺纹加 工的编程方法,对提高数控车削编程能力 意义重大。
本讲主要内容
一.螺纹概述 二.螺纹加工指令的格式 三.螺纹加工应注意的事项 四.螺纹加工举例 五.螺纹加工单一循环指令
加 工 螺 纹 时 应 注 意 的 事 项
径会变大Δ d ,加工内螺纹时直径会变小Δ d 。所以加工内螺纹时,孔径
应车到 d+Δ d ,加工外螺纹时,直径应车到 D-Δ d ,
• 常用螺纹切削的进给次数与背吃刀量 • (米制、双边) ( mm )
《数控车床编程与加工》实训教案

《数控车床编程与加工》实训教案一、教学目标1. 理解数控车床的基本原理和结构。
2. 掌握数控车床的编程方法和技巧。
3. 学会使用数控车床进行加工操作。
4. 能够根据加工要求编写合适的数控程序。
二、教学内容1. 数控车床概述:介绍数控车床的定义、特点、分类和发展趋势。
2. 数控车床编程基础:讲解数控编程的基本概念、方法和步骤。
3. 数控车床编程实例:通过具体实例讲解数控编程的技巧和注意事项。
4. 数控车床操作:介绍数控车床的操作界面、功能和操作方法。
5. 数控车床加工实践:进行实际操作,掌握数控车床的加工技能。
三、教学方法1. 讲授法:讲解数控车床的基本原理、编程方法和操作技巧。
2. 演示法:通过实际操作演示数控车床的编程和加工过程。
3. 实践法:学生亲自动手进行数控车床的操作和加工实践。
4. 讨论法:学生分组讨论,分享学习心得和经验。
四、教学资源1. 数控车床设备:提供足够的数控车床设备供学生实践操作。
2. 教学软件:使用数控车床仿真软件进行编程和操作练习。
3. 教学课件:制作详细的课件,辅助讲解和展示教学内容。
4. 参考资料:提供相关的书籍、论文和网络资源,供学生自主学习。
五、教学评价1. 平时成绩:考察学生的出勤、课堂表现和作业完成情况。
2. 实践操作考核:评估学生在数控车床上的操作技能和加工质量。
3. 编程能力考核:评估学生编写数控程序的能力和正确性。
4. 综合能力评价:综合考虑学生的理论知识和实践能力,给予全面评价。
六、教学安排1. 课时:共计32课时,包括16课时理论教学和16课时实践教学。
2. 教学计划:第1-8课时:数控车床概述和编程基础讲解。
第9-16课时:数控车床编程实例分析和实践操作。
第17-24课时:数控车床操作演示和练习。
第25-32课时:数控车床加工实践和综合训练。
七、教学过程1. 课堂讲解:通过PPT课件,讲解数控车床的基本原理、编程方法和操作技巧。
2. 实践操作:学生在数控车床上进行实际操作,教师现场指导并进行演示。
螺纹的编程与加工G92理论动画演示课件

问题一:G92指令参数设置错误
总结词
参数设置错误可能导致G92指令无法正确执行,影响螺纹加 工精度和稳定性。
详细描述
在使用G92指令时,需要正确设置螺纹的各项参数,如螺纹类型、 导程、起始角度等。如果参数设置不正确,可能导致螺纹加工失
败或精度不符合要求。
解决方案
在编程前仔细核对参数设置,确保各项参数与实际加工需求相符。 同时,参考机床操作手册或专业资料,了解G92指令的参数设置 要求和规范。
冷却与润滑
介绍切削液的使用,以及 如何保持刀具冷却和工件 润滑。
加工后处理与检测
1 2 3
刀具退回 刀具加工完成后,将其退回到初始位置。
工件检测 使用量具对工件进行检测,确保满足图纸要求。
后处理 根据需要,对工件进行清洗、去毛刺等后处理操 作。
案例一:简单螺纹的加工
Hale Waihona Puke 总结词G92指令在简单螺纹加工中的应用
详细描述
简单螺纹的加工通常采用G92指令,通过控制主轴的旋转和进给运动,实现螺纹的切削。在加工过程中,需要合 理选择刀具、切削参数和进给速度,以确保螺纹的精度和表面质量。
案例二:复杂螺纹的加工
总结词
G92指令在复杂螺纹加工中的应用
详细描述
对于复杂螺纹,如多线螺纹或异形螺纹,G92指令同样适用。在加工过程中,需要特别注意刀具的安 装角度、切削深度和切削顺序,以确保螺纹的形状和尺寸符合要求。此外,还需要根据实际情况调整 主轴转速和进给速度,以获得最佳的切削效果。
问题三:G92指令加工过程不稳定
总结词
加工过程不稳定可能影响G92指令的执行效果,降低螺纹加工精度和质量。
详细描述
在G92指令执行过程中,由于机床、刀具、工件等外部因素的影响,可能导致加工过程不稳定,如刀具振动、工件位 移等。这些不稳定因素可能对螺纹加工精度和表面质量造成影响。
五头螺纹编程实例
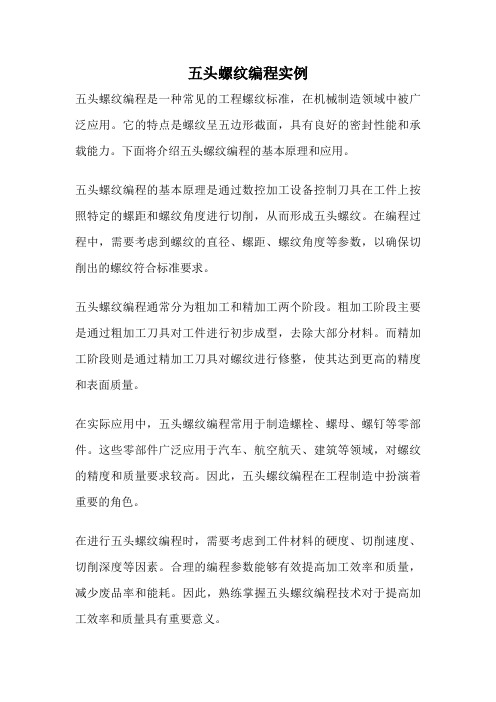
五头螺纹编程实例
五头螺纹编程是一种常见的工程螺纹标准,在机械制造领域中被广泛应用。
它的特点是螺纹呈五边形截面,具有良好的密封性能和承载能力。
下面将介绍五头螺纹编程的基本原理和应用。
五头螺纹编程的基本原理是通过数控加工设备控制刀具在工件上按照特定的螺距和螺纹角度进行切削,从而形成五头螺纹。
在编程过程中,需要考虑到螺纹的直径、螺距、螺纹角度等参数,以确保切削出的螺纹符合标准要求。
五头螺纹编程通常分为粗加工和精加工两个阶段。
粗加工阶段主要是通过粗加工刀具对工件进行初步成型,去除大部分材料。
而精加工阶段则是通过精加工刀具对螺纹进行修整,使其达到更高的精度和表面质量。
在实际应用中,五头螺纹编程常用于制造螺栓、螺母、螺钉等零部件。
这些零部件广泛应用于汽车、航空航天、建筑等领域,对螺纹的精度和质量要求较高。
因此,五头螺纹编程在工程制造中扮演着重要的角色。
在进行五头螺纹编程时,需要考虑到工件材料的硬度、切削速度、切削深度等因素。
合理的编程参数能够有效提高加工效率和质量,减少废品率和能耗。
因此,熟练掌握五头螺纹编程技术对于提高加工效率和质量具有重要意义。
总的来说,五头螺纹编程是一项重要的机械加工技术,在工程制造领域中有着广泛的应用前景。
通过合理的编程和加工操作,能够实现对螺纹的高效加工,满足不同行业对于螺纹零部件的需求。
希望通过本文的介绍,读者能够更加深入了解五头螺纹编程的原理和应用,为工程制造领域的发展贡献自己的力量。
- 1、下载文档前请自行甄别文档内容的完整性,平台不提供额外的编辑、内容补充、找答案等附加服务。
- 2、"仅部分预览"的文档,不可在线预览部分如存在完整性等问题,可反馈申请退款(可完整预览的文档不适用该条件!)。
- 3、如文档侵犯您的权益,请联系客服反馈,我们会尽快为您处理(人工客服工作时间:9:00-18:30)。
例:用螺纹切削复合循环G76代码编图5.12程序,加工螺纹 为M68×6。 程序如下: G50 X100 Z50;(设置浮动坐标系) M3 S300;(启动主轴,指定转速) G00 X80 Z10;(快速定位到加工起点) G76 P011060 Q0.1 R0.2;(进行螺纹切削) G76 X60.64 Z-62 P3.68 Q1.8 F6.0; G00 X100 Z50;(返回程序起点) M5 S0;(停主轴) M30;(程序结束)
二、螺纹编程与加工练习 在螺纹开始及结束部分,一般由于升降速的原因,会出现 导程不正确部分,考虑此因素影响,指令螺纹长度是应比实 际需要的螺纹长度要长些,一般情况下,升速长度>1.3mm, 如图5.5所示: 例3.3:加工如图5.5所示零件螺 纹导程1mm,切深1.3mm(直径 值,分两次切入)。 N0050 G01 U-1 F100 N0060 G33 W-24 P1 N0070 G0 U2 N0080 W24 N0090 G1 U-2.2 F100 N0100 G33 W-54 P1 N0110 G0 U6 N0120 W24
r:螺纹倒角量。 a:刀尖的角度 d:精加工余量 i:螺纹部分的半径差,单位: mm,i=0 为切削直螺纹; k:螺纹牙高(X 轴方向的距离用 半径值指令),单位: mm;
图 5.10
△d:第一次切削深度,半径值, 单位: mm。 F:螺纹导程,单位:mm; I:每英寸牙数。
说明: ● 用P、Q、R指定的数据,根据有无地址X(U),Z(W)来区别。 ● 循环动作由地址X(U),Z(W)指定的G76代码进行。 ● 循环加工中,刀具为单侧刃加工,刀尖的负载可以减轻. ● 第一次切入量为△d,第N次为△D× N ,每次切削量是一定的
图 5.8
例: 加工图 5.90 N0040 N0050 N0060
G00 X52 Z0 M03 S80 G92 X48.6 Z-30 P3 R-3 X47.6 X47 X46.75
注:执行完上述程序段后刀具停留在A点。
任务四 螺纹切削复合循环G76
例: 编制如图示零件的加工程序:用螺纹切削复合循环G76指令编 程,加工螺纹ZM60×2,其中括弧内尺寸根据标准得到。 O3344 N1 T0101 N2 G00 X100 Z100 N3 M03 S400 N4 G00 X90 Z4 N5 G80 X61.125 Z-30 I-1.063 F80 N6 G00 X100 Z100 M05 N7 T0202 N8 M03 S300 N9 G00 X90 Z4 N10 G76 C2 R-3 E1.3 A60 X58.15 Z-24 I-0.875 K1.299 U0.1 V0.1 Q0.9 F2 N11 G00 X100 Z100 N12 M05 N13 M30
● 考虑各地址的符号,有四种加工图形,也可以加工内螺纹。在图2-50所示的螺纹切削中
,只有B, C间用F指令的进给速度,其他为快速进给。 循环中,增量的符号按下列方法决定: U:由轨迹 A 到 C 方向决定; W:由轨迹 C 到 D 的方向决定; R(I):由轨迹 A 到 C 的方向决定; P(K):为正; Q(△D):为正。 ● 关于切螺纹的注意事项,与G32切螺纹相同。 ● 螺纹倒角量的指定,对G92螺纹切削循环也有效。 ● m,r,a同用地址p一次指定。
例题
车M24×2的细牙螺纹,求中径d2、小径d1、和牙型高度h1 的基本尺寸。 解: 已知d=24,P=2,根据公式: d2=D2=d-0.6495P=24-0.6495×2=22.7(mm) h1=0.5413P=24-1.0825×2=21.83(mm) d1=D1=d-1.0825P=0.5413×2=1.08(mm) 二、螺纹车刀 螺纹车刀的选择主要考虑刀具,形状和几何角度等三个方面。 高速钢车刀用于加工塑性(钢件)材料的螺纹工件;白钢刀刃磨 螺的纹车刀,适用于加工大螺距的螺纹和精密丝等工件;硬质 合金螺纹车刀适用于加工脆性材料(铸铁)和高速切削塑性工 件。
G92 螺纹循环的执行过程,如图5.6所示:
如图5.6
1、X轴从A点快速进给到B点。 2、X、Z轴螺纹切削到C点。(包括螺纹退尾) 3、X轴快速退到D点。 4、Z轴快速退回A点。(起始点) 5、若多头螺纹,重复1~4的过程进行多头螺纹的切削。 一般螺纹切削都需要多次进刀,此时只需修改进刀终点的X坐标值 (或相对于起点的增量值)。螺纹循环结束后,坐标位置回到起 点。
(二) 三角螺纹的尺寸计算 普通螺纹是我国应用最广泛的一种三角螺纹,牙形角为 60°,它分为粗牙普通螺纹和细牙普通螺纹。 粗牙普通螺纹代号标记用字母“M”及公称直径表示,如 M24、M30等。细牙普通螺纹代号标记用字母“M”及公称 直径×螺距表示,如M14×1、M30×2等。 普通螺纹的基本牙型如图。该牙型具有螺纹的基本尺寸。普 通螺纹(新国标GB196-86)的基本尺寸计算如下: 1.螺纹的公称直径是指大径的基本尺寸:d=D=公称直径 2.中径(d2、D2) d2=D2=d-0.6495P 3.牙型高度(h1 ) h1=0.5413P 4.螺纹小径(d1、D1) d1=D1=d-1.0825P
一、螺纹切削复合循环G76
指令格式:G76 P(m)(r)(a) Q(△dmin) R(d); G76 X(U)Z(W)R(i) P(k) Q(△d) F(I) ; 指令功能:系统根据指令地址所给的数据自动计算并进行多 次螺纹切削循环螺纹加工完成,指令轨 迹如图 5.10 所示。 X、Z:螺纹终点(螺纹底部)坐标值,单位:mm; U、W:螺纹终点相对加工起点的坐标值,单位:mm; m:最后精加工的重复次数 1~99,此指定值是模态的,在 下次指定前均有效。
任务二 螺纹车削指令G33
一、螺纹切削G32 指令格式:G00 X Z G32 X(U) Z(W) F(I) 其中:G00 X Z ——定位 X(U)、Z(W)——螺纹终点的绝对或相对坐标。(省略X 时为直螺纹) F——公制螺纹导程。 单位:mm 范围:0.001~500mm I——英制螺纹导程。 单位:牙/英寸 范围:0.06~25400 牙/英寸
G32指令可以加工公、英制等螺距的直螺纹、锥螺纹、内螺 纹、外螺纹等常用螺纹。当G32指令中X(U)坐标值非零时 表示加工锥螺纹。在主轴正转情况下,正方向切削为右旋螺 纹。负方向切削为左旋螺纹,主轴反转时则相反,如图5.4所 示:
一般加工螺纹时从粗车到精车同一轨迹要进行多次螺纹切削 ,因为螺纹切削开始是从检测到主轴编码器的第一转信号后 才开始的,因此进行多次螺纹切削零件圆周上的切削点仍是 相同的,但必须保证主轴转速不变,当主轴转速发生变化时 螺纹会产生少许误差。螺纹加工需要与主轴速度相适应。主 轴转速过高会因系统响应不上使螺纹乱牙。推荐主轴转速应 满足下试: N×R≤3000 其中:N——主轴转速 单位:转/分 最高转速小于2000转/分 R——螺纹导程 单位:mm 英制螺纹时将其换算 成公制计算。
项目五 螺纹的编程与加工
任务一 螺纹车削基础知识
一、螺纹切削参数 (一)螺纹基本术语及定义 1.螺旋线:螺旋线是指沿着圆柱表面运动质点的轨迹,该点 的轴向位移与相应的角位移成定比。 2.螺纹在圆柱表面上,沿着螺旋线所形成的,具有相同剖面 的连续凸起和沟槽称为螺纹。 3.螺纹的牙型、牙型角和牙型高度 螺纹牙型是指通过螺纹轴线剖面上的螺纹轮廓形状。 牙型角是指在螺纹牙型上,相邻两牙侧间的夹角。 牙型高度是指在螺纹牙型上,牙顶到牙底之间,垂直于螺纹 轴线方向的距离。
图 5.5
任务三 螺纹切削循环G92
一、螺纹切削循环G92 指令格式:G00 X Z G92 X(U) Z(W) F(I) J K L 其中:G00 X Z —定位 X(U)、Z(W)—螺纹终点的坐标位置 F—公制螺纹螺距。 范围:0.0025-100mm I—英制螺纹导程。 范围:100-0.25牙/英寸 J—螺纹退尾时X轴方向的移动距离。当K≠0时省略I则默认 I=2×K即45°方向退尾,J为半径值。 K—螺纹退尾时退尾起点距终点在Z方向的距离。 R—螺纹起点与螺纹终点的直径之差(螺纹锥度,省略R为直 螺纹)。 L—多头螺纹的螺纹头数(省略L为单头螺纹)。
4.螺距 螺距是指相邻两牙在中径线上对应两点间的轴向距离。 5.螺纹直径 (1)公称直径代表螺纹尺寸的直径,指螺纹大径的基本尺 寸。 (2)大径(d、D) 指与外螺纹牙顶或内螺纹牙底相重合的 假想圆柱面的直径,外螺纹大径用d表示,内螺纹大径用D表 示。 (3)小径(d1、D1)指与外螺纹牙底或内螺纹牙顶相重合 的假想圆柱面的直径,外螺纹小径用d1表示,内螺纹小径用 D1表示。 (4)中径(d2、D2)指一个假想圆柱(中径圆柱)的直径 ,该圆柱的母线通过牙型上沟槽和凸起宽度相等的地方。
G92加工的几种方式如图5.7
如图5.7
二、螺纹编程加工实例 例: 加工图 5.8所示的米制圆柱螺纹。 N0010 G0 X22 Z2 N0020 M03 S80 N0030 G92 X18.9 Z-50 R2.5 N0040 X18.2 N0050 X17.5 N0050 X17.3 注:执行完上述程序段 后刀具停留在A点。
车刀的几何角度有三个(1)刀尖角ε应等于牙型角,车削普通三 角形螺纹是60°;(2)前角Υ一般为0°~15°,螺纹车刀的径向前 角对牙形角有很大的影响,对精度高的螺纹径向前角可适当取 小一些(约0°~5°);(3)后角α一般为5°~10°,因螺纹升角的影 响,两后角大小应该磨成不同,进刀方向一面应稍大一些.但对 大直径,小螺距的三角形螺纹,这种影响可忽略不计。刃磨车 刀时要根据粗,精车的要求,刃磨出合理的前,后角.粗车刀前角 大,后角小,精车刀则相反。车刀的左右刀刃必须是直线,无崩 刃.刀尖角的刃磨比较困难,为保证磨出准确的刀尖角,在刃磨 时用螺纹角度样板测量刀尖角。测量时,把刀尖角与样板贴合 ,对准光源,仔细观察两边贴合的间隙,并以此为依据进行修磨 。另外车刀磨损过大时会引起切削力增大,顶弯工件,出现啃 刀现象,此时应对车刀加以修磨。