均匀设计试验方法的铝合金高速切削参数优化
7075铝合金切削参数优化试验研究
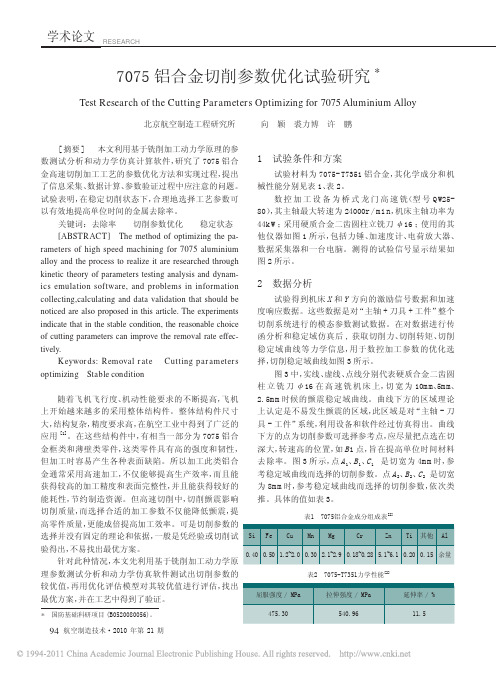
[摘要] 本文利用基于铣削加工动力学原理的参数测试分析和动力学仿真计算软件,研究了7075铝合金高速切削加工工艺的参数优化方法和实现过程,提出了信息采集、数据计算、参数验证过程中应注意的问题。
试验表明,在稳定切削状态下,合理地选择工艺参数可以有效地提高单位时间的金属去除率。
关键词: 去除率 切削参数优化 稳定状态 [ABSTRACT] The method of optimizing the pa-rameters of high speed machining for 7075 aluminium alloy and the process to realize it are researched through kinetic theory of parameters testing analysis and dynam-ics emulation software, and problems in information collecting,calculating and data validation that should be noticed are also proposed in this article. The experiments indicate that in the stable condition, the reasonable choice of cutting parameters can improve the removal rate effec-tively.Keywords: Removal rate Cutting parameters optimizing Stable condition随着飞机飞行度、机动性能要求的不断提高,飞机上开始越来越多的采用整体结构件。
整体结构件尺寸大,结构复杂,精度要求高,在航空工业中得到了广泛的应用[1]。
在这些结构件中,有相当一部分为7075铝合金框类和薄壁类零件,这类零件具有高的强度和韧性,但加工时容易产生各种表面缺陷。
铝合金的切削特性分析和工艺技术研究

表 1 铝合金切削性能
铝合金 合金含量 0% ~ 0.5% 铝铜合金 0.5% ~ 5.65% > 5.65% 铝镁合金 镁硅合金 铝硅合金 铝锰合金 铝锌合金 4% ~ 13% < 8% 9.5% ~ 11.5% 切削性能 不好 较好 良好 低劣 优良 优良 低劣 低劣 良好 加入适当 Cu,Mg,切削性改善 冷变形强化,切削性改善 LC4,LC5,LC6,ZL401,ZL402 ZL101,ZL103,ZL104,ZL105,ZL110 冷变形强化,切削性良好 改善措施 冷作处理后,切削性改善 代表合金 LD2 LD5-LD10D ZL202
铝合金本身的材料性能,引起工件在切削加工中出现粘 刀、变形、振动等问题。根据铝合金的切削性能,加工过程 中需合理选择刀具参数、切削参数等,设计恰当的工艺路线, 有效避免或减缓切削过程中的问题,确保工件切削质量。 2.1 刀具材料及刀具参数的选择 铝合金在切削过程中产生的切削力较小,可适于高速
表 2 切削铝合金的刀具材料
(1) 粘刀现象。 铝合金工件硬度小 (最高 120HB 左右) , 塑性较大,切削时工件变形大;切屑与前刀面的摩擦较大, 且接触面积也大;由摩擦和变形产生的热量,使工件表面 金属变软直至溶化。再者,铝合金切屑不容易断裂,热量 不能及时带走,加剧了工件材料的溶化。这样切屑滞留在 切削刃上,容易产生粘刀现象,从而进一步形成积屑瘤, 影响切削过程。ቤተ መጻሕፍቲ ባይዱ(2)切削变形。铝合金件的抗塑性变形能力差,在切 削力的作用下,工件表层容易产生塑性变形。在切削摩擦
钨钴类硬质合金刀具
超细晶粒硬质合金刀具 (聚晶)金刚石刀具 类金刚石碳涂层刀具 陶瓷刀具 聚晶立方氮化硼刀具
除刀具材料外,刀具的几何参数是影响加工质量的一 个重要因素。切削铝合金时,选用较大的刀具前角,一般 12°~ 18°。前角过大,切削刃和刀头强度降低,不利于 刀具散热,影响刀具寿命;前角过小,切屑变形增大,易 断屑,但切屑容易划伤工件已加工表面。粗加工时可适当 减小前角,精加工时可适当增大前角。刀具(副)后角有 利于减小(副)后刀面与工件的摩擦。由于铝合金弹性模 量小、易粘刀,切削摩擦严重,宜选择较大的后角。例如, 切削铸铝合金时,后角可取 12°。对于刃倾角的选择,冲 击较大的连续切削,取较大负值的刃倾角配合较大前角, 保证切削质量;精加工时宜取正刃倾角,防止切屑划伤已 加工表面。 切削时, 选用刀刃锋利的刀具, 前刀前研磨抛光, 选择尽可能小的刀尖圆弧半径,以防止积屑瘤和切削毛刺。 2.2 切削用量的选择 切削用量包括切削速度、进给量和背吃刀量三个切削 要素,表示切削过程中切削运动的大小以及刀具切入工件 的程度,直接影响到切削力、切削热、刀具寿命、工件表 面粗糙度等。对于铝合金这种适于高速切削又容易产生粘 刀、切削变形、振动等问题的材料,合理选择切削用量显 得尤为重要。一般情况下,粗加工时选用较大的切削深度 和进给量。例如,切削 2A12 时,速度可控制在 800r/min 左右;精加工时,切削深度 0.2 ~ 0.5mm,选择较高的切削 速度和较小的进给量。 2.3 切削液的合理选择 铝合金在高速切削下产生大量的切削热,极易使材料
铝合金高速切削有限元仿真及实验研究

铝合金高速切削有限元仿真及实验研究作者:汪健明刘康来源:《软件工程》2021年第12期摘要:为了研究不同切削参数对铝合金切削过程中切削力和切削温度的影响,以铝合金7075-T651为对象,采用仿真与实验验证结合的方法,利用金属有限元切削专用软件AdvantEdge建立了铝合金7075-T651的二维正交切削仿真模型,并进行合理的工件和刀具材料参数以及本构模型设置。
通过仿真分析,研究了切削力和切削温度与进给速度以及切削深度的关系,并通过实验进行验证。
仿真和实验结果表明:在一定范围内,随着进给速度和切削深度的增大,切削力和切削温度增大。
切削铝合金7075-T651时,应采用较小的切削深度和进给速度。
关键词:AdvantEdge;铝合金7075-T651;切削力;切削温度中图分类号:TP319 文献标识码:AAbstract: In order to study the influence of different cutting parameters on cutting force and cutting temperature in cutting process of aluminum alloy, this research uses aluminum alloy 7075-T651 as the object, and takes the method of combining simulation and experimental verification as the research method. This paper proposes to use special software AdvantEdge of metal finite element cutting to establish two-dimensional orthogonal cutting simulation model of aluminum alloy 7075-T651. Reasonable workpieces, tool material parameters and constitutive model are set. Through simulation analysis, the relationship between cutting force and cutting temperature, feed speed and depth of cut are studied and verified by experiments. Simulation and experimental results show that within a certain range, with the increase of feed speed and cutting depth, cutting force and cutting temperature increase. When cutting aluminum alloy 7075-T651, smaller depth of cutting and feed rate should be used.Keywords: AdvantEdge; aluminum alloy 7075-T651; cutting force; cutting temperature1 引言(Introduction)由于鋁合金7075-T651具有高比强度和良好的热加工性能,以及高韧性和良好的耐腐蚀性,近年来在航空航天、模具加工、机械设备以及夹具中得到了越来越多的应用[1-2]。
铝合金高速数控铣削参数优化
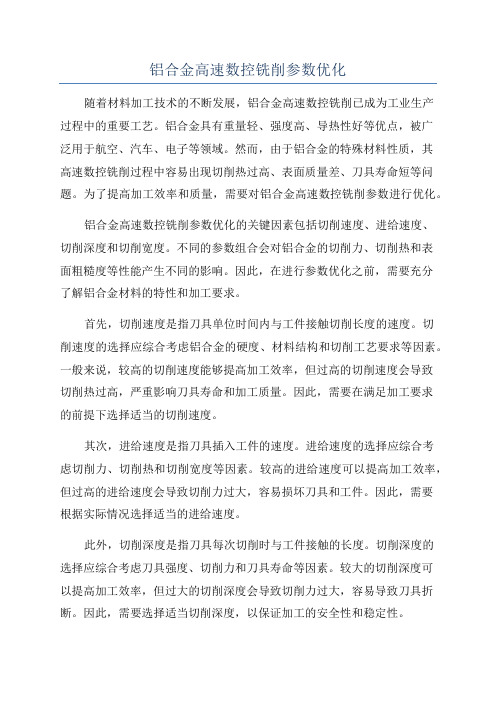
铝合金高速数控铣削参数优化随着材料加工技术的不断发展,铝合金高速数控铣削已成为工业生产过程中的重要工艺。
铝合金具有重量轻、强度高、导热性好等优点,被广泛用于航空、汽车、电子等领域。
然而,由于铝合金的特殊材料性质,其高速数控铣削过程中容易出现切削热过高、表面质量差、刀具寿命短等问题。
为了提高加工效率和质量,需要对铝合金高速数控铣削参数进行优化。
铝合金高速数控铣削参数优化的关键因素包括切削速度、进给速度、切削深度和切削宽度。
不同的参数组合会对铝合金的切削力、切削热和表面粗糙度等性能产生不同的影响。
因此,在进行参数优化之前,需要充分了解铝合金材料的特性和加工要求。
首先,切削速度是指刀具单位时间内与工件接触切削长度的速度。
切削速度的选择应综合考虑铝合金的硬度、材料结构和切削工艺要求等因素。
一般来说,较高的切削速度能够提高加工效率,但过高的切削速度会导致切削热过高,严重影响刀具寿命和加工质量。
因此,需要在满足加工要求的前提下选择适当的切削速度。
其次,进给速度是指刀具插入工件的速度。
进给速度的选择应综合考虑切削力、切削热和切削宽度等因素。
较高的进给速度可以提高加工效率,但过高的进给速度会导致切削力过大,容易损坏刀具和工件。
因此,需要根据实际情况选择适当的进给速度。
此外,切削深度是指刀具每次切削时与工件接触的长度。
切削深度的选择应综合考虑刀具强度、切削力和刀具寿命等因素。
较大的切削深度可以提高加工效率,但过大的切削深度会导致切削力过大,容易导致刀具折断。
因此,需要选择适当切削深度,以保证加工的安全性和稳定性。
最后,切削宽度是指切削刀具与工件之间的接触宽度。
切削宽度的选择应综合考虑切削力、表面粗糙度和刀具寿命等因素。
较大的切削宽度可以提高加工效率,但过大的切削宽度会导致切削力过大,降低表面质量。
因此,需要选择适当的切削宽度,以保证加工的质量和效率。
在铝合金高速数控铣削参数优化中,除了上述的关键因素外,还需要综合考虑刀具类型、冷却液使用和刀具磨损等因素。
高速铣削加工6061铝合金高速列车车体刀具涂层的优化
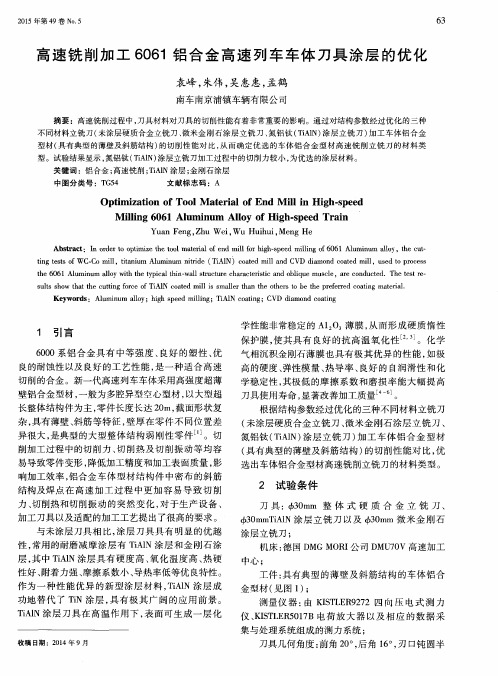
长整体结构件为主 , 零件长度长达 2 0 m, 截面形状复 杂, 具 有薄壁 、 斜 筋 等特 征 , 壁 厚 在 零 件不 同位 置 差 异很大, 是典 型 的大 型 整 体结 构 弱 刚 性 零件 J 。切
t i n g t e s t s o f WC — C o m i l l , t i t a n i u m A l u m i n u m n i t r i d e( T i A 1 N)c o a t e d m i l l a n d C V D d i a m o n d c o a t e d m i l l , u s e d t o p r o c e s s
1 引 言
6 0 0 0系 铝合 金 具 有 中等 强 度 、 良好 的塑 性 、 优 良的 耐蚀性 以及 良好 的工 艺 性 能 , 是 一种 适 合 高 速 切 削 的合金 。新 一代 高速列 车车 体采用 高 强度超 薄 壁 铝合 金 型材 , 一般 为多腔 异型 空心 型材 , 以大 型超
Yua n Fe n g, Zh u We i , Wu Hui h ui , Me n g He
Ab s t r a c t :I n o r d e r t o o p t i mi z e t h e t o o l ma t e r i a l o f e n d mi l l f o r h i g h — s p e e d mi l l i n g o f 6 0 6 1 A l u mi n u m a l l o y ,t h e c u t —
高速切削工艺参数优化技术取得重大突破
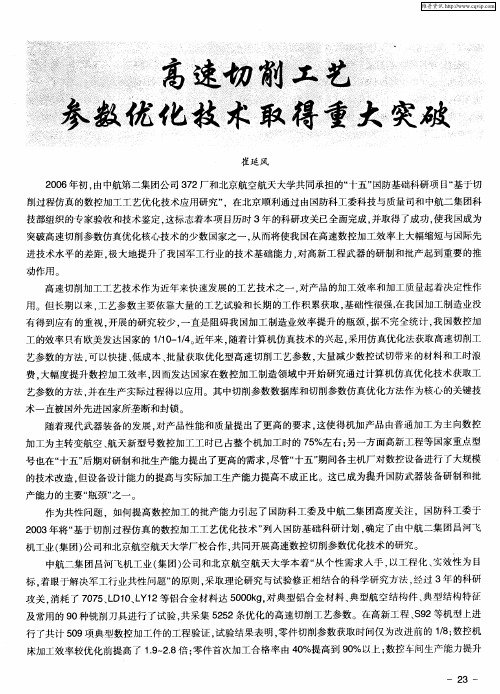
通过 该项 目的研究 , 成 了一套 基 于切 削过 程仿 真 的数 控加 工切 削参 数 优 化 的新 工具 , 索 出 了一条 工 厂 形 探
环境下基于动力学仿真和参数优化实现航空- 1性零件和高速加工过程切削参数优化 的新途径 :提出了一种 11 11 “ 基于特征、 面向网络 、 行进化” 自 的优化型切削参数数据获取的新方法和新机制 ; 建立了一 套铝合金特征结构和
维普资讯
。
l| -
} 。
礁 | | ≥ |
崔延风
2 0 年初 , 06 由中航第二集团公司 3 2 7 厂和北京航空航天大学共同承担的“ 十五” 国防基础科研项 目“ 基于切
削过程仿 真 的数控 加工 工艺 优化技 术应 用研究 ” ,在北 京顺 利通 过 由国防科 工委 科技 与质 量 司和 中航二 集 团科 技部组 织 的专家 验 收和技 术鉴 定 , 标志 着本项 目历 时 3年 的科 研攻关 已全 面完 成 , 取得 了成 功 , 我 国成为 这 并 使
有得到应有 的重视 , 开展的研究较少, 一直是阻碍我 国加工制造业效率提升的瓶颈 , 据不完全统计 , 我国数控加 工的效率只有欧美发达 国家的 1 — /。 门0 1 近年来 , 4 随着计算机仿真技术的兴起 , 采用仿真优化法获取高速切削工 艺参数的方法 , 可以快捷 、 低成本 、 批量获取优化型高速切削工艺参数 , 大量减少数控试切带来的材料和工时浪 费, 大幅度提升数控加工效率 , 因而发达 国家在数控加工制造领域 中开始研究通过计算机仿真优化技术获取工 艺参数的方法, 并在生产实际过程得以应用。其中切削参数数据库和切削参数仿真优化方法作为核心的关键技
典型结构的切削参数数据库。 在仿真切削热 、 切削力 、 表面形貌 、 机床/ 刀具 工件模态 、 切削参数优化技术、 切削参 数数据库及工程应用研究 等多方面进行 了创新并形成 了自主知识产权。 目前各主机厂数控加工产值为数千万元 以 卜, 整个同防科技工业数控加工产值高达 1 亿元以上, 0 将数控加 工效率提高 1 倍将产生数亿元经济效益 . 而我圈数控效率与国外差距有数倍之多 , 以挖掘 的潜力很大, 可 优化切 削参数、 提高切削用量是最直接的解决方法 , 究和建立国防数控加工切削数据库将会产生巨大的经济效益和 研
高速切削参数优化加工技术的应用

高效数控加工 High-Effective NC Machining
高速铣削加工动力学仿真
高速切削加工要有高的主轴转 速,一般主轴转速在 10000~20000r/ min 以上的为高速切削;进给速度 很高,通常达 15~50m/min,最高可达 90m/min。
但是如果在加工中单纯地提高 机床的主轴转速和进给速度后,就会 带来铣切加工过程中刀具或工件的 振动,即颤振现象。颤振是金属切削 过程中刀具和工件之间产生的一种较 为强烈的自激振动现象。颤振的出现 会导致切削力峰值明显增加,使加工 表面粗糙度和尺寸精度明显下降,严 重时会使刀具破裂,主轴受损;此外通 常会对加工环境造成一定污染 [3]。
· 结构复杂,加工难度大。整体 壁板的底面为机翼理论外形,长桁沿 机翼型面法向分布,尤其是中外翼壁 板蒙皮是变厚度的。理论上外型面 与翼弦面不平行。长桁、肋等与壁板 底面呈变角状态。
A A
A
10800
B
B
B
A -A
(比例 3:1)
A向
B向
(比例 3:1)(比例 3:1)
B -B (比例 3:1)
80 606
高速切削加工技术是在机床结 构及材料、高速主轴系统、快速进给 系统、高性能 CNC 控制系统、机床设 计制造技术、高性能刀夹系统、高性 能刀具材料及刀具设计制造技术、高 效高精度测试技术、高速切削加工理
68 航空制造技术·2011 年第 23/24 期
论、高速切削加工工艺等诸多相关硬 件与软件技术均得到充分发展的基 础上综合而成的。它具有加工效率 高、切削力小、加工精度和表面质量 高等特点,已在航空、航天、汽车、模 具和精密机械等行业得到了广泛应 用,并取得了重大的经济效益。
· 材料去除率大。整体壁板的
铝合金的切削性能研究报告

铝合金的切削性能研究报告铝合金是一种常见的金属材料,广泛应用于航空航天、汽车制造、建筑工程等领域。
研究铝合金的切削性能对于提高加工效率、降低成本具有重要意义。
以下是关于铝合金切削性能的研究报告。
一、研究目的:分析不同切削参数对铝合金的切削性能的影响,为优化切削工艺提供科学依据。
二、试验材料:选取常见的铝合金材料,如铝-铜合金、铝-镁合金等作为试验材料。
三、试验方法:采用切削力实时监测系统,对不同切削参数下铝合金的切削力进行监测。
同时,通过测量切削力、切削温度、切削表面质量等指标来评估切削性能。
四、试验结果:根据实验数据分析,得出以下结论:1. 切削速度对切削力和切削温度有较大影响。
随着切削速度的增加,切削力和切削温度也随之增加。
但是当切削速度超过一定范围时,切削力和切削温度趋于稳定。
2. 切削深度对切削力和切削温度的影响相对较小。
在一定范围内增加切削深度,切削力和切削温度略微增加,但增长速率较慢。
3. 切削液对切削力和切削温度的影响较大。
使用合适的切削液可以降低切削力和切削温度,改善切削表面质量。
4. 刀具材料和几何参数对切削性能的影响需要进一步研究。
五、结论和建议:根据对铝合金的切削性能研究,可以得出以下结论和建议:1. 在切削过程中,合理控制切削速度,避免过高的切削速度导致切削力和切削温度过高。
2. 选择合适的切削液,减少切削力和切削温度,提高切削表面质量。
3. 进一步研究刀具材料和几何参数对切削性能的影响,优化切削过程。
总之,铝合金的切削性能研究对于提高加工效率、降低成本具有重要意义,通过合理控制切削参数和选择合适的切削液,可以优化切削工艺,提高铝合金的切削性能。
基于均匀设计法的精密车削参数优化
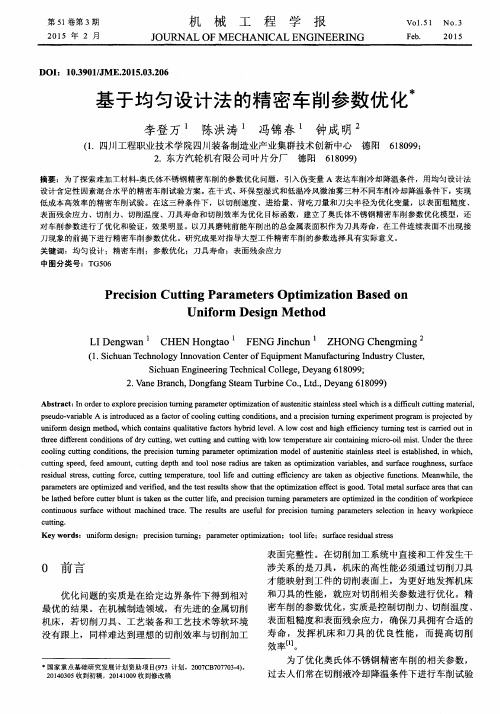
c o o l i n g c u t t i n g c o n d i t i o n s , t h e p r e c i s i o n t u r n i n g p a r a me t e r o p t i mi z a t i o n mo d e l o f a u s t e n i t i c s ai t n l e s s s t e e l i s e s t a b l i s h e d ,i n wh i c h , c u t i n g s p e e d , f e e d a mo nt u , c u t t i n g d e p h t a n d t o o l n o s e r a d i u s re a t a k e n a s o p t i mi z a t i o n v a r i a b l e s , nd a s u r f a c e r o u g h n e s s , s u r f a c e
( 1 . S i c h u a n T e c h n o l o g y I n n o v a t i o n C e n t e r o f E q u i p me n t Ma n u f a c t u r i n g I n d u s t r y C l u s t e r ,
Si c h ua n En gi ne e r i ng Te c hn i c a l Co l l e g e , De ya ng 6 1 8 09 9;
2 . V a n e B r a n c h , Do n g f a n g S t e a m T u r b i n e C o . , L t d . , D e y a n g 6 1 8 0 9 9 )
铝合金在高速切削加工中表面粗糙度的研究
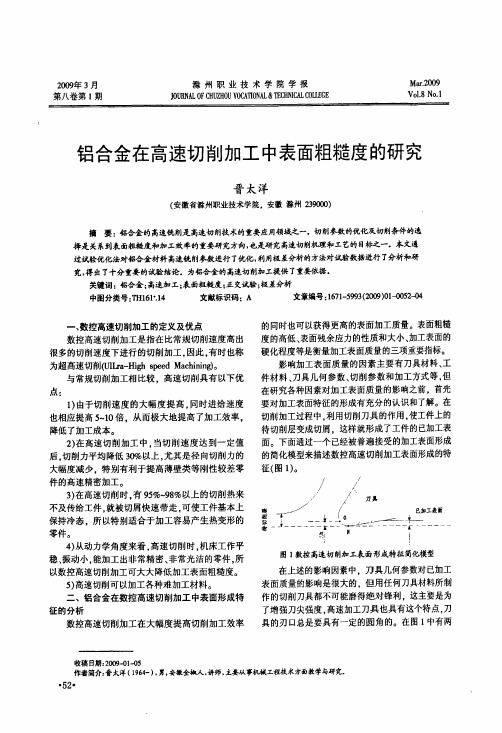
切削加 工过程中 ,利用Байду номын сангаас削 刀具的作用 ,使工件 上的
待切削层变成切屑,这样就形成了工件的已加工表
面。下面通过一个已经被普遍接受的加工表面形成
的简化模型来描述数控高速切削加工表面形成的特
征( 图1) 。
?
/
/ j
噬—/。/ /
/
,,、
‘ j 、 H“ 两翼
,j
厂
己加工 表面
蓁 一 二 … 一 二 二 ÷ =- 兰 ≥ 剁 : <皇 二 }… 一
一、 数控高 速切 削加工 的定 义及优 点 数控高速切削加工是指在比常规切削速度高出 很多 的切 削速度 下进 行的切 削加工 ,因 此。有 时也 称 为超高速切削( Ul ha—Hi gl l s peed Ma c hi ni ng) 。 与常规切削加工相比较。高速切削具有以下优 点: 1) 由于切削速度的大幅度提高,同时进给速度 也 相应 提高 5—1 0倍 。从 而极 大地 提高 了加 工效 率, 降低了加工成本。 2) 在高速切削加工中,当切削速度达到一定值 后, 切削 力平均 降低 30%以 上,尤 其是 径向切 削力 的 大幅度减少,特别有利于提高薄壁类等刚性较差零 件的高速精 密加工。 3) 在高速切削时,有95%~98%以上的切削热来 不及 传给 工件 。就被 切屑 快速 带走 。可使 工件 基本 上 保持冷态,所以特别适合于加工容易产生热变形的 零件。 4) 从动力学角度来看,高速切削时,机床工作平 稳、振动小, 能加工出非常精密、非常光 洁的零件,所 以数控高速切削加工可大大降低加工表面粗糙度。 5) 高速切削可以加工各种难加工材料。 二、铝合金在数控高速切削加工中表面形成特 征的分析 数控高速切削加工在大幅度提高切削加工效率
高速铣削加工6061铝合金高速列车车体工艺参数的优化
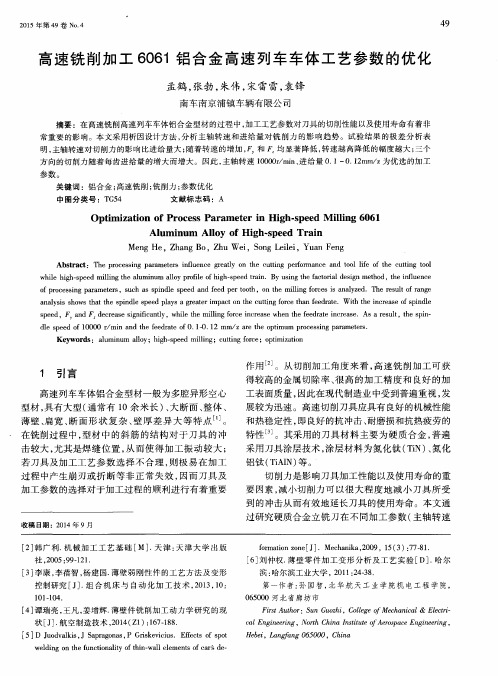
型材 , 具 有 大型 ( 通常 有 1 O余 米长 ) 、 大断面 、 整体 、 薄壁 、 扁宽 、 断面形状复 杂、 壁厚 差异大等特 点¨ J 。 在铣 削 过程 中 , 型材 中 的斜 筋 的 结 构 对 于 刀具 的 冲 击 较大 , 尤 其是 焊缝 位 置 , 从 而使 得 加 工 振 动 较 大 ;
d i e s p e e d o f 1 0 0 0 0 r / mi n a n d t h e f e e d r a t e o f 0 . 1 - 0. 1 2 mm/ z a r e t h e o p t i mu m p r o c e s s i n g p a r a me t e r s . Ke y wo r d s :a l u mi n u m a l l o y ;h i g h — s p e e d mi l l i n g;c u t t i n g f o r c e;o p t i mi z a t i o n
o f p r o c e s s i n g p a r a me t e r s ,s u c h a s s p i n d l e s p e e d a n d f e e d p e r t o o t h,o n t h e mi l l i n g f o r c e s i s a n a l y z e d .T h e r e s u l t o f r a n g e a n a l y s i s s h o ws t h a t t h e s p i n d l e s p e e d p l a y s a g r e a t e r i mp a c t o n t h e c u t t i n g f o r c e t h a n f e e d r a t e .W i t h t h e i n c r e a s e o f s p i n d l e s p e e d,Fy a n d d e c r e a s e s i g n i i f c a n t l y ,w h i l e t h e mi l l i n g f o r c e i n c r e a s e w h e n t h e f e e d r a t e i n c r e a s e .As a r e s u l t ,t h e s p i n —
采用试验设计法优化铝合金超精密车削加工参数
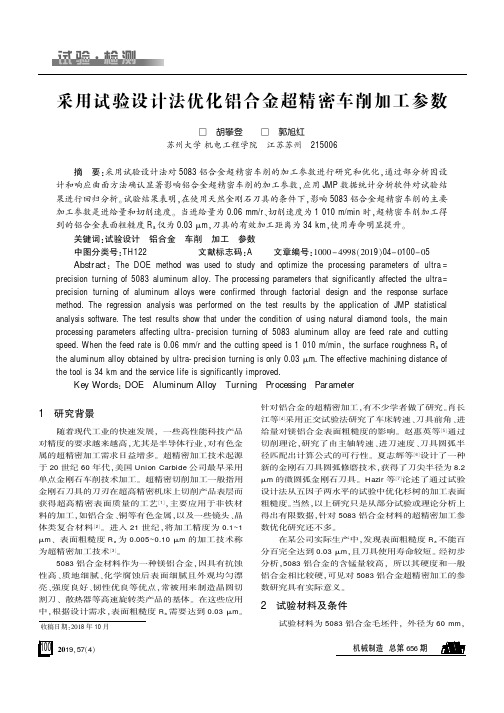
收稿日期:2018年10月1研究背景随着现代工业的快速发展,一些高性能科技产品对精度的要求越来越高,尤其是半导体行业,对有色金属的超精密加工需求日益增多。
超精密加工技术起源于20世纪60年代,美国Union Carbide 公司最早采用单点金刚石车削技术加工。
超精密切削加工一般指用金刚石刀具的刀刃在超高精密机床上切削产品表层而获得超高精密表面质量的工艺[1],主要应用于非铁材料的加工,如铝合金、铜等有色金属,以及一些镜头、晶体类复合材料[2]。
进入21世纪,将加工精度为0.1~1μm 、表面粗糙度R a 为0.005~0.10μm 的加工技术称为超精密加工技术[3]。
5083铝合金材料作为一种镁铝合金,因具有抗蚀性高、质地细腻、化学腐蚀后表面细腻且外观均匀漂亮、强度良好、韧性优良等优点,常被用来制造晶圆切割刀、散热器等高速旋转类产品的基体。
在这些应用中,根据设计需求,表面粗糙度R a 需要达到0.03μm 。
针对铝合金的超精密加工,有不少学者做了研究。
肖长江等[4]采用正交试验法研究了车床转速、刀具前角、进给量对镁铝合金表面粗糙度的影响。
赵惠英等[5]通过切削理论,研究了由主轴转速、进刀速度、刀具圆弧半径匹配出计算公式的可行性。
夏志辉等[6]设计了一种新的金刚石刀具圆弧修磨技术,获得了刀尖半径为8.2μm 的微圆弧金刚石刀具。
Hazir 等[7]论述了通过试验设计法从五因子两水平的试验中优化杉树的加工表面粗糙度。
当然,以上研究只是从部分试验或理论分析上得出有限数据,针对5083铝合金材料的超精密加工参数优化研究还不多。
在某公司实际生产中,发现表面粗糙度R a 不能百分百完全达到0.03μm ,且刀具使用寿命较短。
经初步分析,5083铝合金的含锰量较高,所以其硬度和一般铝合金相比较硬,可见对5083铝合金超精密加工的参数研究具有实际意义。
2试验材料及条件试验材料为5083铝合金毛坯件,外径为60mm ,采用试验设计法优化铝合金超精密车削加工参数□胡攀登□郭旭红苏州大学机电工程学院江苏苏州215006摘要:采用试验设计法对5083铝合金超精密车削的加工参数进行研究和优化,通过部分析因设计和响应曲面方法确认显著影响铝合金超精密车削的加工参数,应用JMP 数据统计分析软件对试验结果进行回归分析。
铝合金铸造壳体高速铣削参数优化研究
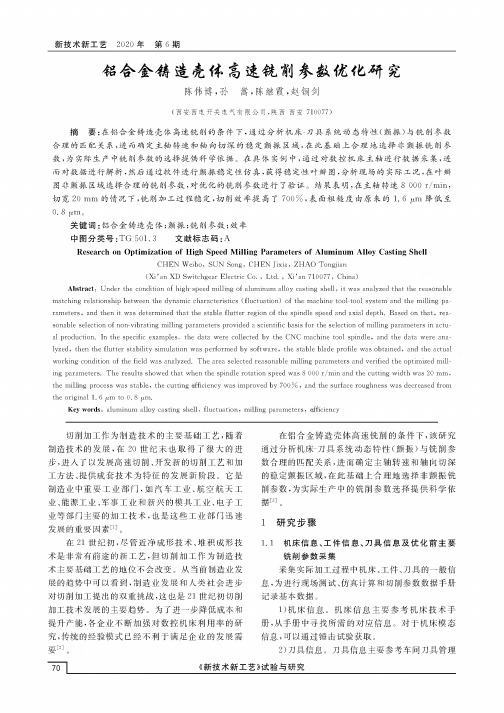
铝合金铸造壳体高速铣削参数优化研究陈伟博,孙嵩,陈继霞,赵铜剑(西安西电开关电气有限公司,陕西西安710077)摘要:在铝合金铸造壳体高速铳削的条件下,通过分析机床-刀具系统动态特性(颤振)与铳削参数合理的匹配关系,进而确定主轴转速和轴向切深的稳定颤振区域,在此基础上合理地选择非颤振铳削参数,为实际生产中铳削参数的选择提供科学依据。
在具体实例中,通过对数控机床主轴进行数据采集,进而对数据进行解析,然后通过软件进行颤振稳定性仿真,获得稳定性叶瓣图,分析现场的实际工况,在叶瓣图非颤振区域选择合理的铳削参数,对优化的铳削参数进行了验证。
结果表明,在主轴转速8000r/min,切宽20mm的情况下,铳削加工过程稳定,切削效率提高了700%,表面粗糙度由原来的1.6"m降低至0.8"m。
关键词:铝合金铸造壳体;颤振;铳削参数;效率中图分类号:TG501.3文献标志码:AResearch on Optimization of High Speed Milling Parameters of Aluminum Alloy Casting ShellCHEN Weibo,SUN Song,CHEN Jixia,ZHAO Tongjian(Xi'an XD Switchgear Electric Co.,Ltd.,Xi'an710077,China)Abstract:Under the condition of high-speed milling of aluminum alloy casting shell,it was analyzed that the reasonable matching;elationshipbetweenthedynamiccha;acte;istics(fluctuation)ofthe machine tool-tool system and the mi l ingpa-;amete;s andthenitwasdete;minedthatthestableflu t e;;egionofthespindlespeedandaxialdepth.Basedonthat;ea-sonable selection of non-vibrating milling parameters provided a scientific basis for the selection of milling parameters in actu-alproduction.IntheApecificexampleA thedata wereco l ectedbytheCNC machinetoolApindle andthedata wereana-lyzed,then the flutter stability simulation was performed by software ,the stable blade profile was obtained,and the actual workingconditionofthefieldwaAanalyzed.TheareaAelectedreaAonablemi l ingparameterAandverifiedtheoptimized mi l-ing parameters.The results showed that when the spindle rotation speed was8000r/min and the cutting width was20mm, Bhe mi l ingprocesswassBable Bhecu inge f iciencywasimprovedby700%andBhesurfaceroughnesswasdecreasedfrom Bheoriginal1.6"mBo0.8"m.Keywords:aluminuma l oycasingshe l flucBuaBion mi l ingparameBers e f iciency切削加工作为制造技术的主要基础工艺,随着制造技术的发展,在20世纪末也取得了很大的进步,进入了以发展高速切削、开发新的切削工艺和加工方法、提供成套技术为特征的发展新阶段。
高速铣削2A12铝合金的切削参数模糊推理
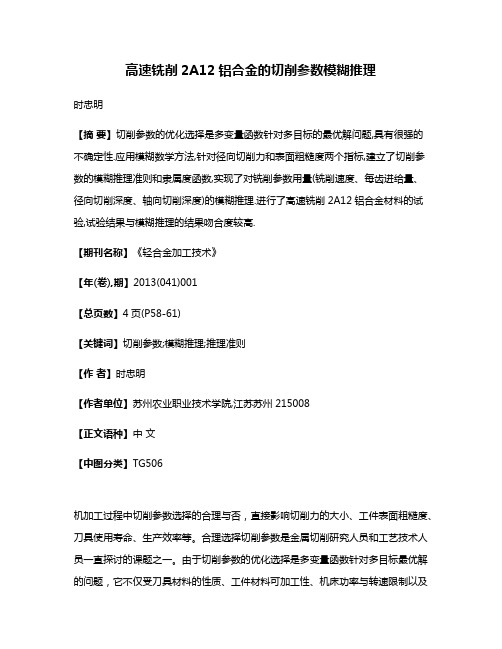
高速铣削2A12铝合金的切削参数模糊推理时忠明【摘要】切削参数的优化选择是多变量函数针对多目标的最优解问题,具有很强的不确定性.应用模糊数学方法,针对径向切削力和表面粗糙度两个指标,建立了切削参数的模糊推理准则和隶属度函数,实现了对铣削参数用量(铣削速度、每齿进给量、径向切削深度、轴向切削深度)的模糊推理.进行了高速铣削2A12铝合金材料的试验,试验结果与模糊推理的结果吻合度较高.【期刊名称】《轻合金加工技术》【年(卷),期】2013(041)001【总页数】4页(P58-61)【关键词】切削参数;模糊推理;推理准则【作者】时忠明【作者单位】苏州农业职业技术学院,江苏苏州215008【正文语种】中文【中图分类】TG506机加工过程中切削参数选择的合理与否,直接影响切削力的大小、工件表面粗糙度、刀具使用寿命、生产效率等。
合理选择切削参数是金属切削研究人员和工艺技术人员一直探讨的课题之一。
由于切削参数的优化选择是多变量函数针对多目标最优解的问题,它不仅受刀具材料的性质、工件材料可加工性、机床功率与转速限制以及工艺系统刚性等因素的影响,而且各影响因素之间又相互制约,因此很难建立准确的数学模型。
另外,依据切削用量手册选择参数的不确定性、实际加工环境的多变性等等原因决定了对切削参数选择的相对性,使得切削参数的选择具有模糊性[1-2],因此,对切削参数进行模糊优化具有很强的实际意义。
本文应用模糊数学方法,开展了切削参数影响切削力和表面粗糙度的模糊推理研究,并利用Mikron UCP 800DURO高速加工中心和相关仪器,进行了2A12铝合金的高速铣削加工试验,验证了推理准则的合理性。
1 模糊推理输入参数对输出指标的影响分析影响切削参数选择的因素应包括以下几个方面的指标:切削力、切削振动、加工精度、表面粗糙度等。
因切削力会导致切削振动,从而引起精度下降和表面质量恶化,通过表面粗糙度指标也可以反映力和振动对加工过程的影响[3]。
均匀设计试验方法的铝合金高速切削参数优化
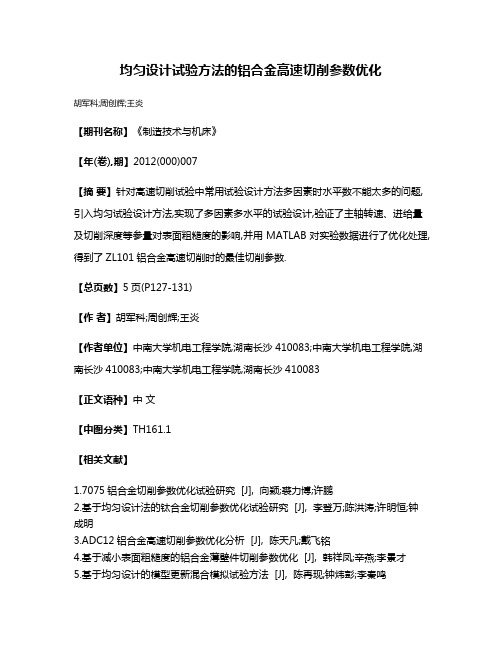
均匀设计试验方法的铝合金高速切削参数优化
胡军科;周创辉;王炎
【期刊名称】《制造技术与机床》
【年(卷),期】2012(000)007
【摘要】针对高速切削试验中常用试验设计方法多因素时水平数不能太多的问题,引入均匀试验设计方法,实现了多因素多水平的试验设计,验证了主轴转速、进给量及切削深度等参量对表面粗糙度的影响,并用MATLAB对实验数据进行了优化处理,得到了ZL101铝合金高速切削时的最佳切削参数.
【总页数】5页(P127-131)
【作者】胡军科;周创辉;王炎
【作者单位】中南大学机电工程学院,湖南长沙410083;中南大学机电工程学院,湖南长沙410083;中南大学机电工程学院,湖南长沙410083
【正文语种】中文
【中图分类】TH161.1
【相关文献】
1.7075铝合金切削参数优化试验研究 [J], 向颖;裘力博;许鹏
2.基于均匀设计法的钛合金切削参数优化试验研究 [J], 李登万;陈洪涛;许明恒;钟成明
3.ADC12铝合金高速切削参数优化分析 [J], 陈天凡;戴飞铭
4.基于减小表面粗糙度的铝合金薄壁件切削参数优化 [J], 韩祥凤;辛燕;李景才
5.基于均匀设计的模型更新混合模拟试验方法 [J], 陈再现;钟炜彭;李秦鸣
因版权原因,仅展示原文概要,查看原文内容请购买。
铝合金高速铣削中切削温度动态变化规律的试验研究
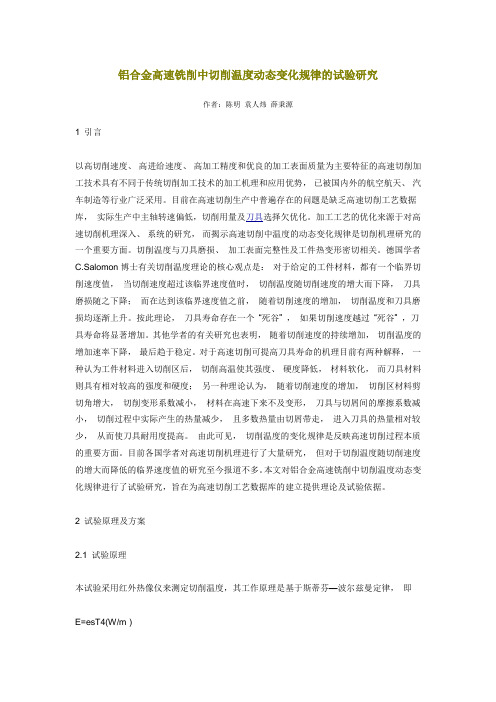
铝合金高速铣削中切削温度动态变化规律的试验研究作者:陈明袁人炜薛秉源1 引言以高切削速度、高进给速度、高加工精度和优良的加工表面质量为主要特征的高速切削加工技术具有不同于传统切削加工技术的加工机理和应用优势,已被国内外的航空航天、汽车制造等行业广泛采用。
目前在高速切削生产中普遍存在的问题是缺乏高速切削工艺数据库,实际生产中主轴转速偏低,切削用量及刀具选择欠优化。
加工工艺的优化来源于对高速切削机理深入、系统的研究,而揭示高速切削中温度的动态变化规律是切削机理研究的一个重要方面。
切削温度与刀具磨损、加工表面完整性及工件热变形密切相关。
德国学者C.Salomon博士有关切削温度理论的核心观点是:对于给定的工件材料,都有一个临界切削速度值,当切削速度超过该临界速度值时,切削温度随切削速度的增大而下降,刀具磨损随之下降;而在达到该临界速度值之前,随着切削速度的增加,切削温度和刀具磨损均逐渐上升。
按此理论,刀具寿命存在一个“死谷” ,如果切削速度越过“死谷” ,刀具寿命将显著增加。
其他学者的有关研究也表明,随着切削速度的持续增加,切削温度的增加速率下降,最后趋于稳定。
对于高速切削可提高刀具寿命的机理目前有两种解释,一种认为工件材料进入切削区后,切削高温使其强度、硬度降低,材料软化,而刀具材料则具有相对较高的强度和硬度;另一种理论认为,随着切削速度的增加,切削区材料剪切角增大,切削变形系数减小,材料在高速下来不及变形,刀具与切屑间的摩擦系数减小,切削过程中实际产生的热量减少,且多数热量由切屑带走,进入刀具的热量相对较少,从而使刀具耐用度提高。
由此可见,切削温度的变化规律是反映高速切削过程本质的重要方面。
目前各国学者对高速切削机理进行了大量研究,但对于切削温度随切削速度的增大而降低的临界速度值的研究至今报道不多。
本文对铝合金高速铣削中切削温度动态变化规律进行了试验研究,旨在为高速切削工艺数据库的建立提供理论及试验依据。
铝合金切削加工条件选择及其切削加工性能改善_熊建武

2.切削条件的选择 2.1 刀 具 几 何 参 数 的 选 择 铝 合 金 的 强 度 和 硬 度 比 铜 合 金 低 , 宜 选取更大的前角( γ0) 。粗车时取 γ0=200~250, 精车时取 γ0=250~300,
25 0.03~0.1 ≤0.5 30~40 乳液 或切
20 0.03~0.1 ≤0.5 ≤30 削液
3.铝合金切削加工性能的改善
所 选 用 的 铝 合 金 及 其 硬 度 对 刀 具 寿 命 有 重 要 影 响 。铝 合 金 中 添 加 的合金元素, 既可处于固溶状态, 也可作为弥散的质点而处于不溶解 状态。不溶解状态的组分一般要比铝的基体更硬, 这些硬的质点将造 成 刀 具 的 磨 损 。如 果 通 过 固 溶 处 理 及 快 速 淬 火 使 这 些 硬 的 质 点 来 不 及 析出, 可以减轻对刀具的研磨效应。然而, 如果这些组分由子固溶缓 慢, 固溶处理后淬火不良, 或是过度时效而导致硬的质点增大, 则将加 速刀具的磨损。
拱之间填充直径 25mm 石棉绳。 2.2.9 锅 炉 顶 盖 砖 与 炉 墙 、鼓 筒 、集 箱 连 接 处 均 应 留 设 膨 胀 缝 , 并
铝合金的切削加 工 包 括 车 、铣 、钻 、镗 、锯 等 , 其 中 车 、铣 切 削 加 工 应 用 最 广 。铝 合 金 的 切 削 加 工 性 与 铜 合 金 有 许 多 相 似 之 处 。由 于 铝 合 金强度和硬度相对较低, 塑性较小, 对刀具磨损小, 且热导率较高, 使 切削温度较低, 所以铝合金的切削加工性较好, 属于易加工材料, 适于 较高切削速度切削。但铝合金熔点较低, 温度升高后塑性增大, 在高温 高压作用下, 切屑界面摩擦力很大, 容易粘刀; 特别是退火状态的铝合 金, 不易获得低的表面粗糙度。
铝合金均匀化及加工技术
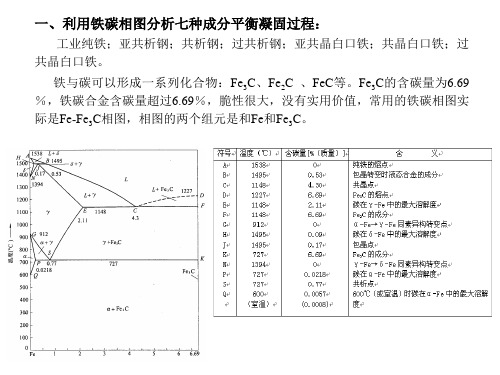
锻铝合金的应用:形状复杂的中等负荷零件,如压缩机叶片,飞机桨叶。
防锈铝合金的应用
飞机主起落架
飞机翼梁
压气机叶片
活塞(裙部为铝硅合金) 汽缸头(铝铜合金)
五、铝加工技术的发展趋势
1、铝合金材料发展趋向: 需发展高强、高韧、耐磨、耐蚀、耐疲劳、耐高温、耐辐射 、防火、防爆、易切削、易抛光、可表面处理、可焊接和超轻的新型铝合金,如Rm≥ 780MPa高强高韧合金,密度小于2.4t/m3的铝锂合金、粉末冶金和复合材料等。
含碳0.01%工业纯铁冷却曲线和结晶过程
共析钢冷却曲线和结晶过程
亚共析钢冷却曲线和结晶过程
过共析钢冷却曲线和结晶过程
共晶铁冷却曲线和结晶过程
亚共晶铁冷却曲线和结晶过程
相图的应用: 1)在钢铁材料选用方面的应用;2)在铸造工艺方面的应用;3)在 热锻、热轧工艺方面的应用;4)在热处理工艺方面的应用。
无加工余量的精密模锻、多向模锻、等温模锻等新工艺将得到发展。由于铝合金 模锻件的品种多、批最小、模具成本昂贵,目前世界上有用预拉伸厚板数控加工的 方法代替大型模锻件的趋势。
6、质量检测与质量保证: 为保证产品质量,不仅要逐步建立各种质量保证体系(如ISO 9000等等),还
会不断研制开发各种先进的仪器仪表和测试手段保证产品的尺寸公差、形位精度、 化学成分、内部组织、力学性能和特种性能,表面质量达到技术标准的要求。
2、均匀化过程注意事项:
1)控制加热速度避免铸锭开裂; 2)保证不过烧的条件下,尽量提高温度; 3)使合金元素充分固溶的条件下,尽量缩短时间; 4)具体合金非平衡凝固产物的回溶和重熔的特点及其弥散相的形成特点。
铝合金热处理工艺优化方案

铝合金热处理工艺优化方案根据您提供的要求,我将为您撰写一篇深度文章,探讨铝合金热处理工艺的优化方案。
以下是我对这个主题的观点和理解。
铝合金热处理工艺是一项重要的制造工艺,用于改善铝合金材料的力学性能和耐热性。
通过控制材料的加热、保温和冷却过程,可以调整铝合金的晶体结构和性能,实现最佳的材料特性。
在热处理过程中,关键的工艺参数包括温度、时间和冷却速率。
要优化铝合金热处理工艺方案,首先需要评估材料的组成和性能需求。
不同类型的铝合金具有不同的组织结构和机械性能,因此需要针对具体材料确定最佳的热处理工艺。
同时,需要考虑到应用环境和使用要求,以确定适当的工艺参数。
以下是一些建议用于优化铝合金热处理工艺的方案。
首先,合理选择热处理温度。
热处理温度是影响铝合金组织转变和性能改善的重要参数。
过高的温度可能导致粗大晶粒和析出相过度生长,从而降低材料的强度和硬度。
相反,过低的温度可能无法完全改善材料的性能。
因此,需要通过实验和模拟计算确定最佳的热处理温度范围。
其次,确保适当的保温时间。
保温时间是指材料在热处理温度下保持稳定的时间。
保温时间过短可能导致热处理反应不完全,不同区域的组织结构差异较大。
相反,保温时间过长可能导致晶粒长大和析出相数量过多。
因此,需要根据材料的组织结构和性能需求,确定最佳的保温时间范围。
另外,冷却速率也是影响铝合金热处理效果的重要参数。
快速冷却可以减缓晶粒长大和相析出,从而获得细小的晶粒和均匀的组织结构。
低速冷却则可使相析出相对充分,提高材料的强度和硬度。
因此,在热处理工艺中,需要根据材料的组织结构和性能需求,选择适当的冷却速率。
除了上述的工艺参数,其它更加细致和复杂的调控方法也可以用于优化铝合金热处理工艺。
比如采用不同的热处理工艺序列,如固溶处理和时效处理的组合,可以显著改变材料的组织结构和性能。
此外,通过添加合适的合金元素和调整合金组成,也可以改善铝合金的热处理效果。
这些方法需要通过深入的研究和实验来确定最佳的工艺方案。
- 1、下载文档前请自行甄别文档内容的完整性,平台不提供额外的编辑、内容补充、找答案等附加服务。
- 2、"仅部分预览"的文档,不可在线预览部分如存在完整性等问题,可反馈申请退款(可完整预览的文档不适用该条件!)。
- 3、如文档侵犯您的权益,请联系客服反馈,我们会尽快为您处理(人工客服工作时间:9:00-18:30)。
2 2
。
铝合金高速切削加工中切削参数的选择是非常重 要的, 切削参数选择不合理不仅达不到所需的表面粗 糙度要求, 甚至还会由于过大的切削力和过高的切削 温度导致刀具和坯件的损坏。 由于切削过程是多变 量、 多水平的系统, 直接数学建模比较困难。现有的大 量数学模型都是将切削过程简单化、 理想化得出的结 论。实际生产中许多未知因素或环境变量都会对测量 结果产生影响, 因而理论值与实际加工结果有出入。 对切削参数的优化研究 ( 特别是实际生产中 ) 比较准 确的仍是用试验方法完成。 例如, 山东大学艾兴教授 的课题组
切削深度 a p / mm 0. 30 0. 55 0. 80 0. 25 0. 50 0. 75 0. 2 0. 45 0. 70 0. 15 0. 40 0. 65 0. 10 0. 35 0. 60
只需 15 次试验, 即可获得足够信息。 均匀设计的缺点是数据处理比较难 。但在计算机 技术高度发展的时代, 可以借助已开发出的处理软件 ( 如 DPS 等) 来完成数据处理。 本文基于 MATLAB 强 大的数据处理功能, 自编程序进行了数据处理。
方法” 的一个应用。 通过概率论的方法将设计点均匀 分布在试验范围内, 以便通过较少的试验获得最多的 信息。和正交试验设计相似, 均匀设计也是通过一套 精心设计的表来进行试验设计。 均匀设计因素的每个水平仅需做一次试验 , 因而 试验次数就等于水平数, 可以大大减少试验次数。 均 特别是因 匀实验设计更适合于多因素多水平的情况 , 。 素水平较多时更应当用均匀试验法 例如同样是一个 10 水平的试验项目, 若采用正交法则至少需要 100 次 试验, 而均匀设计只需要做 10 次试验即可, 与因素数 目没有关系。高速切削的切削参数取值范围较大, 例 如主轴转速可从 4 000 r / min 到 20 000 r / min, 因素的 否则信息不足, 难以较准确地表达在 水平数不能太少, 大范围内的因素与指标之间的关系。 综合考虑后, 取 水平数 q = 15 , 试验可控因素 4 个。多次单因素法显然
Parameters optimization of high speed machining aluminum alloy by uniform design method
HU Junke,ZHOU Chuanghui,WANG Yan ( Central South University,Changsha 410083 ,CHN) Abstract: Because the commonly used experimental design method of high speed cutting is not available to the case of multiple factors with many levels, this paper introduces the uniform design experimentation to achieve the experimental design of more factors and levels, verify the effects on the surface roughness by some parameters,such as spindle rotational speed,feed rate and cutting depth, then processes the experimental data by MATLAB , in order to get the optimal cutting parameters of ZL101 aluminum alloy in high - speed cutting. Keywords: Uniform Design; Aluminum Alloy; High -speed Cutting;Parameters Optimization 高速切削技术近 20 年来发展迅速, 主要在航空航 天、 模具和汽车工业等领域, 以加工铝合金和铸铁较 多。但在高速加工工艺参数选择方面, 目前还没有面 向生产的实用工艺参数可以参考, 其工艺规范还很不 完善, 对高速切削时的切削力、 切削温度、 刀具磨损与 刀具寿命、 加工表面质量与加工精度的变化规律还需 要更加深入地研究和探讨
[1-3 ]
常用试验方法有单因素试验法和正交试 验 法 2 种。当有多个可控因素时, 可针对不同因素多次使用 单因素试验, 但前提是各因素之间相互独立, 对试验结 同时各因素的水平不能太多, 果指标影响没有交叉性, 否则试验次数会很高, 而且常会得出错误的结论。 相 比多次单因素试验, 正交试验可大大减少试验次数, 还 能充分考虑到因素间的交互作用 。但正交试验法只适 应于水平不多的试验设计。 假设有 p 个因素, 每个因 素有 q 个水平, 用正交试验设计法安排试验, 则至少需 q 较大值时, q 会更大, 要 q 次试验, 对于大多数实际 上百次试验是很麻烦的。 生产问题而言, 针对以上 2 种试验方法的不足, 本文引入均匀试 验方法设计了多因素、 更多水平的试验方案, 以 ZL101 铸铝合金为样本, 研究高速切削时的主轴转速、 进给量 等切削参数对加工表面粗糙度及切削力的影响 。
[4-5 ]
1
均匀试验设计方法介绍
均匀试验设计是只考虑试验点在试验范围内均匀
45 钢进行了高速 分别对铝合金、 灰铸铁、
铣削加工试验, 研究了切削参数的匹配关系对表面粗 糙度的影响。
散布的一种试验设计法, 它由方开泰教授和数学家王 是数论方法中的“伪蒙特卡罗 元在 1978 年共同提出,
· 127 ·
均匀设计试验方法的铝合金高速切削参数优化
胡军科 周创辉 王 炎
( 中南大学机电工程学院, 湖南 长沙 410083 ) 摘 要:针对高速切削试验中常用试验设计方法多因素时水平数不能太多的问题 , 引入均匀试验设计方法, 实现了多因素多水平的试验设计 , 验证了主轴转速、 进给量及切削深度等参量对表面粗糙度的影响 , 并用 MATLAB 对实验数据进行了优化处理, 得到了 ZL101 铝合金高速切削时的最佳切削参数 。 关键词:均匀设计 铝合金 高速切削 优化 文献标识码:B 中图分类号:TH161. 1
试验安排
每齿进给量 f 齿 / ( mm / 齿) 0. 060 0. 025 0. 070 0. 035 0. 080 0. 045 0. 090 0. 055 0. 020 0. 065 0. 030 0. 075 0. 040 0. 085 0. 050 切削宽度 a e / mm 24 18 12 6 1 26 20 14 8 2 28 22 16 10 4
2 不实际, 正交法至少需要做 15 = 225 次试验, 试验次 数也太多了。均匀试验设计正好用来解决此类问题,
表1
试验 序号 1 2 3 4 5 6 7 8 9 10 11 12 13 14 15 主轴转速 n / ( r / min) 8 000 9 000 10 000 11 000 12 000 13 000 14 000 15 000 16 000 17 000 18 000 19 000 20 000 21 000 22 000
2
试验过程
试验指标应为表面粗糙度 R a 和 3 个方向的切削
Fy 、 F z 。根据工件加工工艺要求, 分力 F x 、 表面粗糙度 R 0. 8 m , 。 μ 即可 切削力越小越好 作为可控因 小于 a 素, 高速铣削参数主要包括机切削速度 v c 、 进给速度 vf 、 切削深度 a p 和切削宽度 a e 。 主轴转速 n 和每齿进 给量 f 齿 的调节更为直观, 因此用主轴转速 n 来替代切 用每齿进给量 f 齿 代替进给速度 v f 作为试验 削速度 v c , 因素。 试验在瑞士 Mikron 的 HSM600 数控五轴超高速 数 控 系 统 为 Heidenhain ITNC530 。 加工 中 心 上 进 行, 主轴最高转速 42 000 r / min, 最大进给速度 40 m / min, 定位精度 0. 008 mm, 重复定位精度 0. 005 mm。 根据 生产实际情况及厂家推荐试验中选取的转速为 8 000 ~ 22 000 r / min, 切削宽度为 1 ~ 28 mm, 径向切削深度 为 0. 1 ~ 0. 8 mm, 每齿进给量为 0. 02 ~ 0. 09 mm。 将 各因素 15 水平等分, 参照均匀试验设计表可得试验安 排方案如表 1 所示。 Fraisa 40 mm, 4 刃圆角铣 刀具: Mikron Grain, 刀, 螺旋角 45° 。 冷却方式: 油雾冷却。
表2
试验序号 1 2 3 4 5 6 7 8 9 10 11 12 13 14 15 n / ( r / min) 8 000 9 000 10 000 11 000 12 000 13 000 14 000 15 000 16 000 17 000 18 000 19 000 20 000 21 000 22 000 a p / mm 0. 30 0. 55 0. 80 0. 25 0. 50 0. 75 0. 2 0. 45 0. 70 0. 15 0. 40 0. 65 0. 10 0. 35 0. 60