创致拼料工艺标准
石材加工工艺及技术标准
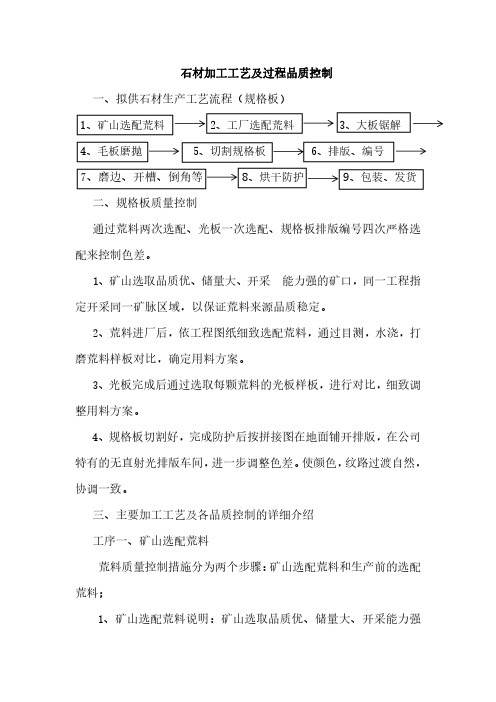
圆弧板的四个角。 以最大间隙的测量值表示圆弧板的角度公差。测量值精确到 0.05mm。 6.3.3 圆弧板 a 角 将圆弧靠模贴靠圆弧板装饰面并使其上的径向刻度线延长线与 圆弧板边线相交、将小平尺沿径向刻度线置于圆弧靠模上,测量圆弧 板侧面与小平尺间的夹角(见图 5)。
6.4 外观质量 6.4.1 花纹色调 将协议板与被检板材并列平放在地上距板材 1.5m 处站立目测。 6.4.2 缺陷 用游标卡尺测量缺陷的长度、宽度,测量值精确到 0.lmm。 6.5 镜向光泽度 采用 60°人射角,样品规格尺寸不小于 300mmX300mm,按 GB/T 13891 的规定试验。 6.6 干燥压缩强度 按 GB 9966.1 的规定试验, 干燥压缩强度值可取荒料的检测结果。
6.1.2 圆弧板规格尺寸 用游标卡尺或能满足测量精度要求的量器具测量圆弧板 的弦长、
高度及最小壁厚。在圆弧板的两端面处测量弦长(见图 1 )。在圆 弧板端面与侧面测量壁厚 (见图 1 ) ; 圆弧板高度测量部位如图 4 所 示。 分别用偏差的最大值和最小值表示弦长, 高度及壁厚的尺寸偏差。 测量值精确到 0.lmm 。
5 .2 .2 圆弧板壁厚最小值应不小于 18mm ,规格尺寸允许偏差应符 合表 2 的规定。圆弧板各部位名称及尺寸标注如图 1 所示。
表 2(mm) 亚光面和镜面板材 项目 优等品 品 弦长 0~-1.0 高度 5.2.3 -1.5 0~-1.0 0~-1.0 0~-1.5 0~ 0~-1.5 0~-2.0 0~-1.0 一等 合格品 优等品 一等品 合格品 粗面板材
的磨抛设备。该设备的先进性在于全数控操作,对毛板的平面度偏差 有修复作用,磨出的板面平整度偏差小于 0.2 ㎜;同品牌磨块采用佰 石特公司设备磨抛后,光泽度可达 80 多,要高出其他杂牌机器产品 起码 5 个光泽度以上,完全能满足招标方的要求;生产能里强大,每 台月产量达 10000 ㎡。石材荔枝面、火烧面加工采用全自动数控设备 操作,能够保证石材荔枝面、火烧面加工一致性,发挥石材完美的外 观效果。 工序五、切割规格板(红外线桥切机) 切割规格板工艺说明:在确定用料计划后,光板转入介板车间, 由红外线电子桥切机完成本道工序。该设备的先进性祥述如下:程序 控制自动进行刀, 有效解决因锯片磨损厚度发生变化而使切割尺寸偏 差加大,保证切割尺寸偏差小于 0.5 ㎜;工作台旋转 90 度,角度自 动调整,保证规格板切割长宽垂直,角度偏差小于 0.5 ㎜;每台月产 9000 ㎡规格板。 工序六、排版、编号 无直射光排版、编号工序说明:工程板完成切割后,为最大程度 的减少由于石材的天然属性而导致不可避免的色差, 通过此道工序来 进行有效控制。在“无直射光照排版理论”和超大规模的室内排版车 间,可将单个立面或整个大堂地面石材全部排版调色,经过大量实例 验证,效果非常明显,能达到色差控制的最理想效果。经过排版调整 后对每件规格板进行有序编号,货到工地后能直接按序安装,从而保 证工程整体装饰效果。
大理石、花岗石及碎拼大理石地面 施工工艺标准(711-1996)

大理石、花岗石及碎拼大理石地面施工工艺标准(711-1996)范围本工艺标准适用于民用建筑的大理石、花岗石和碎拼大理石地面面层(大理石板材不得用于室外地面面层)。
施工准备2.1 材料及主要机具;2.1.1 天然大理石、花岗石的品种、规格应符合设计要求,技术等级、光泽度、外观质量要求,应符合国家标准《天然大理石建筑板材》、《花岗石建筑板材》的规定,其允许偏差和外观要求见表7-12。
花岗石、大理石板材质量要求表7-12允许偏差 (mm)长度、宽度厚度平整度最大偏差值花岗石、大理石板材表面+0 ±2 要求光洁、明亮、色泽鲜-1 +1 明,无刀痕旋纹。
边角方-2 正,无据曲,缺角、掉边2.1.2 水泥:硅酸盐水泥、普通硅酸盐水泥或矿渣硅酸盐水泥,其标号不宜小于425号。
白水泥:白色硅酸盐水泥,其标号不小于425号。
2.1.3 砂:中砂或粗砂,其含泥量不应大于3%。
2.1.4 大理石碎块及色石渣:石渣颜色应符合设计要求。
应坚硬、洁净、无杂物,粒径宜为4~14mm。
大理石碎块不带夹角,薄厚应一致。
2.1.5 矿物颜料(擦缝用)、蜡、草酸。
2.1.6 算机具;手推车、铁锹、靠尺、浆壶、水桶、喷壶、铁抹子、木抹子、墨斗、钢卷尺、尼龙线、橡皮锤(或木锤)、铁水平尺、弯角方尺、钢錾子、合金钢扁錾子、台钻、合金钢钻头、笤帚、砂轮锯、磨石机、钢丝刷。
2.2 作业条件:2.2.1 大理石、花岗石板块进场后,应侧立堆放在室内光面相对、背面垫松木条,并在板下加垫水方。
拆箱后详细核对品种、规格、数量等是否符合设计要求,有裂纹、缺棱、掉角、翘曲和表面有缺陷时,应予剔除。
2.2.2 搭设好加工棚,安装好台钻及砂轮锯,并接通水电源。
2.2.3 室内抹灰(包括立门口)、地面垫层、预埋在垫层内的电管及穿通地面的管线均已完成。
2.2.4 房间内四周墙上弹好+50cm水平线。
2.2.5 施工操作前应画出铺设大理石地面的施工大样图。
家具实木备料拼板工艺品质标准

4.9脚头上螺杆的位置不允许拼松软木质,以免预埋螺母吃力不足。
4.10粘结力测ห้องสมุดไป่ตู้:将板抬高至1M左右,平行自由下落,拼接处无脱胶现象即为合格。
4.11含油性实木需使用专用抗油性胶水。(如:泰柚木)
6.1.1.6虫蛀材须经杀虫处理。
6.1.1.7要根据涂饰要求选用不同等级的木材。
A.浅色透木纹类用A级材。
B.深色半透明类用B级材。
C.贴纸及不透明类用C级材。
6.2加工余量要求
6.1截锯:长度余量为5-20mm,出榫余量为5mm,不出榫余量为10mm,拼板余量为15-20mm。
6.3纵锯:宽、厚度余量为3-5mm,1m以下的短料余量为2-3mm,1m以上的长料余量为3-5mm,有弯翘变形的木材适当加宽加厚。
5.5定厚砂光后,必须是砂背面,不能砂正面,要求表面无崩烂、凹陷等现象。
5.6同一产品饰面木纹、颜色应相似,拼接木纹应对称,固定家具必须要对纹,同纹。
5.7拼大板或需加厚,再实木封边的部件,必须现将板材背面砂光定厚再冷压。
6、实木开料工艺标准:
6.1品质要求
6.1.1材质
6.1.1.1含水率为8-12%(特殊材质含水率可适当放宽),特殊情况根据客户所在地的木材年平均含水率而定。
4.5常规替代材料:胡桃木使用楸木、桦桃木(需要擦底色)
樱桃木使用桦桃木、赤杨,黄杨
实木椅类用橡胶木
橡木使用白栓木
4.6封边实木代替:奥古曼、椴木、赤杨、黄杨
4.7硬木类(水曲柳、桦木、橡胶木等)加压压力要求12-15kg/cm2,软木类(奥古曼、黄杨、赤杨等)加压压力要求8-12kg/ cm2加压3小时以上(25度以上)卸压8小时后才可进行二次深加工。
(完整版)下料工艺标准
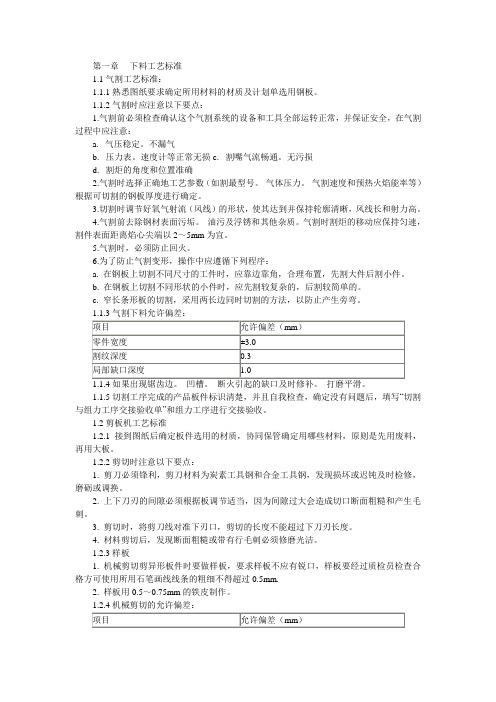
第一章下料工艺标准1.1气割工艺标准:1.1.1熟悉图纸要求确定所用材料的材质及计划单选用钢板。
1.1.2气割时应注意以下要点:1.气割前必须检查确认这个气割系统的设备和工具全部运转正常,并保证安全,在气割过程中应注意:a. 气压稳定。
不漏气b. 压力表。
速度计等正常无损c. 割嘴气流畅通。
无污损d. 割炬的角度和位置准确2.气割时选择正确地工艺参数(如割最型号。
气体压力。
气割速度和预热火焰能率等)根据可切割的钢板厚度进行确定。
3.切割时调节好氧气射流(风线)的形状,使其达到并保持轮廓清晰,风线长和射力高。
4.气割前去除钢材表面污垢。
油污及浮锈和其他杂质。
气割时割炬的移动应保持匀速,割件表面距离焰心尖端以2~5mm为宜。
5.气割时,必须防止回火。
6.为了防止气割变形,操作中应遵循下列程序:a. 在钢板上切割不同尺寸的工件时,应靠边靠角,合理布置,先割大件后割小件。
b. 在钢板上切割不同形状的小件时,应先割较复杂的,后割较简单的。
c. 窄长条形板的切割,采用两长边同时切割的方法,以防止产生旁弯。
1.1.3气割下料允许偏差:1.1.4如果出现锯齿边。
凹槽。
断火引起的缺口及时修补。
打磨平滑。
1.1.5切割工序完成的产品板件标识清楚,并且自我检查,确定没有问题后,填写“切割与组力工序交接验收单”和组力工序进行交接验收。
1.2剪板机工艺标准1.2.1接到图纸后确定板件选用的材质,协同保管确定用哪些材料,原则是先用废料,再用大板。
1.2.2剪切时注意以下要点:1. 剪刀必须锋利,剪刀材料为炭素工具钢和合金工具钢,发现损坏或迟钝及时检修,磨砺或调换。
2. 上下刀刃的间隙必须根据板调节适当,因为间隙过大会造成切口断面粗糙和产生毛刺。
3. 剪切时,将剪刀线对准下刃口,剪切的长度不能超过下刀刃长度。
4. 材料剪切后,发现断面粗糙或带有行毛刺必须修磨光洁。
1.2.3样板1. 机械剪切剪异形板件时要做样板,要求样板不应有锐口,样板要经过质检员检查合格方可使用所用石笔画线线条的粗细不得超过0.5mm.2. 样板用0.5~0.75mm的铁皮制作。
拼板工艺流程及基本要求
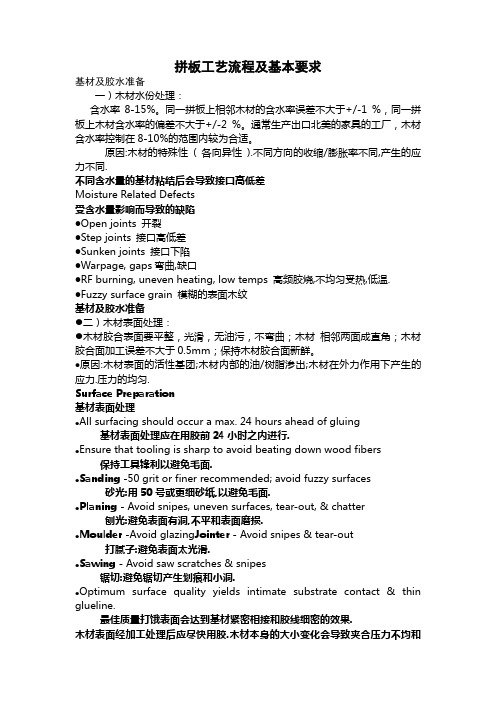
拼板工艺流程及基本要求基材及胶水准备一)木材水份处理:含水率8-15%。
同一拼板上相邻木材的含水率误差不大于+/-1 %,同一拼板上木材含水率的偏差不大于+/-2 %。
通常生产出口北美的家具的工厂,木材含水率控制在8-10%的范围内较为合适。
原因:木材的特殊性 ( 各向异性 ).不同方向的收缩/膨胀率不同,产生的应力不同.不同含水量的基材粘结后会导致接口高低差Moisture Related Defects受含水量影响而导致的缺陷●Open joints 开裂●Step joints 接口高低差●Sunken joints 接口下陷●Warpage, gaps弯曲,缺口●RF burning, uneven heating, low temps 高频胶烧,不均匀受热,低温.●Fuzzy surface grain 模糊的表面木纹基材及胶水准备●二)木材表面处理:●木材胶合表面要平整,光滑,无油污,不弯曲;木材相邻两面成直角;木材胶合面加工误差不大于0.5mm;保持木材胶合面新鲜。
●原因:木材表面的活性基团;木材内部的油/树脂渗出;木材在外力作用下产生的应力.压力的均匀.Surface Preparation基材表面处理●All surfacing should occur a max. 24 hours ahead of gluing基材表面处理应在用胶前24小时之内进行.●Ensure that tooling is sharp to avoid beating down wood fibers保持工具锋利以避免毛面.●Sanding -50 grit or finer recommended; avoid fuzzy surfaces砂光:用50号或更细砂纸,以避免毛面.●Planing - Avoid snipes, uneven surfaces, tear-out, & chatter刨光:避免表面有洞,不平和表面磨损.●Moulder -Avoid glazing Jointer - Avoid snipes & tear-out打腻子:避免表面太光滑.●Sawing - Avoid saw scratches & snipes锯切:避免锯切产生划痕和小洞.●Optimum surface quality yields intimate substrate contact & thin glueline.最佳质量打饿表面会达到基材紧密相接和胶线细密的效果.木材表面经加工处理后应尽快用胶.木材本身的大小变化会导致夹合压力不均和接口开裂.基材及胶水准备●三)胶水与固化剂的混合:●胶水与固化剂的混合比100:15(重量比)。
木工施工中的拼装要求和工艺标准
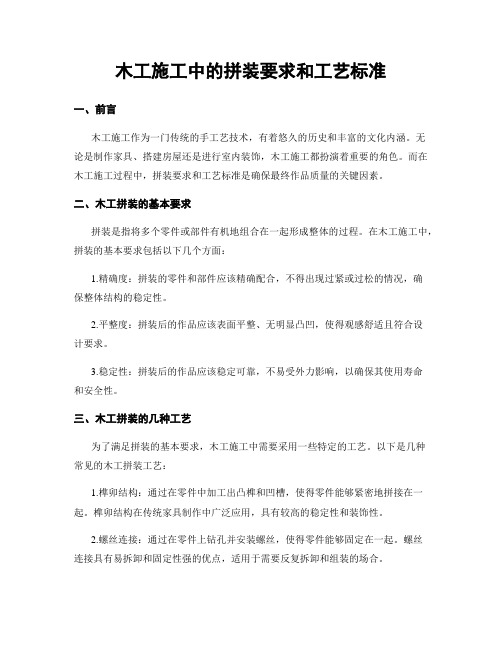
木工施工中的拼装要求和工艺标准一、前言木工施工作为一门传统的手工艺技术,有着悠久的历史和丰富的文化内涵。
无论是制作家具、搭建房屋还是进行室内装饰,木工施工都扮演着重要的角色。
而在木工施工过程中,拼装要求和工艺标准是确保最终作品质量的关键因素。
二、木工拼装的基本要求拼装是指将多个零件或部件有机地组合在一起形成整体的过程。
在木工施工中,拼装的基本要求包括以下几个方面:1.精确度:拼装的零件和部件应该精确配合,不得出现过紧或过松的情况,确保整体结构的稳定性。
2.平整度:拼装后的作品应该表面平整、无明显凸凹,使得观感舒适且符合设计要求。
3.稳定性:拼装后的作品应该稳定可靠,不易受外力影响,以确保其使用寿命和安全性。
三、木工拼装的几种工艺为了满足拼装的基本要求,木工施工中需要采用一些特定的工艺。
以下是几种常见的木工拼装工艺:1.榫卯结构:通过在零件中加工出凸榫和凹槽,使得零件能够紧密地拼接在一起。
榫卯结构在传统家具制作中广泛应用,具有较高的稳定性和装饰性。
2.螺丝连接:通过在零件上钻孔并安装螺丝,使得零件能够固定在一起。
螺丝连接具有易拆卸和固定性强的优点,适用于需要反复拆卸和组装的场合。
3.胶水粘合:通过在零件表面涂抹胶水,然后将其拼接在一起,胶水会在干燥后形成强有力的粘合力。
胶水粘合在家具制作和建筑装饰中被广泛应用,能够提高结构稳定性和整体强度。
四、拼装要求与不同木材的特性不同种类的木材拥有不同的物理性质和机械性能,对于拼装要求也有一定的影响。
以下是几种常见木材的特性及其拼装要求:1.实木:实木具有天然的纹理和色泽,为家具制作提供了丰富的选择。
在拼装实木家具时,需要注意选择合适的面板厚度,确保拼接处的平整度和稳定性。
2.人造板:人造板由多层木片或木纤维板通过胶合剂粘合而成,具有均匀的结构和稳定的性能。
拼装人造板时,要注意控制胶合厚度和胶水使用量,以提高其耐用性和稳定性。
3.竹材:竹材纹理清晰、硬度较高,但横向抗弯能力相对较差。
家具实木备料拼板工艺品质标准

成品展示-1成品展示2
成品展示-3
拼板前涂胶
摆放
固定成型
3.4拼板前期准备:
断料(下料)
修边机
双面刨
4、品质工艺要求:
4.1按照生产技术部门指定的图纸规格尺寸、数量、质量要求,根据板材的长度、宽度及厚度合理搭配用材。
4.2面料选用树种统一、颜色接近、无虫眼、无死节、无油眼、无爆裂、无腐朽、无钝棱、无红、黑树芯的木材,含水率12%以下,按材质好坏。分为面料、垫料、填芯料及颜色要求的筛选。不符合用料要求及标准的材料不予加工。垫料选用不能做面料的材料,填芯料选用不能做垫料的材料。锯路要求平面、光滑、角度正常。
4.3拼板料的拼接面要求平整光滑、底面与拼接面要成直角,不允许有不同木材、颜色、木质、木纹方向的料拼成一个整体,相邻两块板料的湿度不超过2%。同一块拼板料中,料与料之间厚度差不得超过2MM,长度差不得超过3MM。
4.4拼缝线的宽度不允许超过0.2MM,涂胶量且要双面,涂抹均匀不得单面厚凃,以加压有均匀胶水刚挤出为宜。
4.8所有须经车枳和雕刻的台脚或立柱不允许拼松软木质,以免在车床因紧固松紧程度不同影响工艺线大小不一致或因木质松软无法加工。
4.9脚头上螺杆的位置不允许拼松软木质,以免预埋螺母吃力不足。
4.10粘结力测试:将板抬高至1M左右,平行自由下落,拼接处无脱胶现象即为合格。
4.11含油性实木需使用专用抗油性胶水。(如:泰柚木)
6.4带锯:按划线留2-3mm的加工余量。
6.3公差
6.3.1平压刨(单片锯):尺寸公差为0.5mm,工件宽度W<50mm,角度公差H≤0.15mm,工件宽度W<100mm,角度公差H≤0.3mm,工件宽度W<150mm,角度公差H≤0.5mm,工件宽度W<200mm,角度公差H≤0.6mm,(H为角尺长边靠拢工件后的间隙)。
家具车间备料工艺标准

家具车间备料工艺标准概述:就是运用家具备料所需要的机械设备和工具,在备料车间对家具毛料或素材进行一系列的加工操作,用来供应生产所需。
备料是家具生产的第一道工序,俗话说“万丈高,从地起”,备料工艺水平的高低,直接影响整个家具产品的质量。
工艺流程:备料包括选料、断料、开料(裁板/压板/贴皮/封边)、平刨、压刨、拼板、弯矩成型等工序。
质量要求:1、拼板时尽量将颜色相近的材料拼在一条拼缝上,保持板面颜色基本一致。
2、备料规格不能太大,更不能缩小,长度保持在1-1.5厘米,宽厚度保持在0.5-0.8厘米左右的砂光或精切余量。
3、所有材料必须保持方正、平直,杜绝拼缝空隙出现。
上胶水时必须将胶水均匀涂布在木材表面,不能过多或过少,以拼实后表面有芝麻大小胶粒溢出为宜,拼板必须保持一面平整,一头整齐,确保材料利用率。
4、锯裁后的板件必须与实际尺寸要求相符,大小头之差应小于2mm。
当板件长度L为:1000mm<L<2500mm 时,允许公差为2mm(极限偏差为土lmm)。
当板件长度L<1000mm时,允许加工公差为lmm(极限偏差为士0.5mm)。
5、截面应平整、与邻边垂直,不允许有波浪、发黑、毛刺、锯痕、崩边等现象。
6、冷压后部件表面应干净、平整,不可有明显的骨架印痕,弯曲变形,划痕及多余涂胶现象。
7、板芯条要紧密,表面平整,过渡自然无胶水污染。
8、热压贴皮拼花必须保证木纹走向与要求相符,粘贴必须牢固、平滑,不允许脱胶、离层、气泡、划花、折皱、烂纸、压痕及其它杂物等现象。
9、封边要保证严密、平整、胶合牢固、无脱胶、溢胶、漏封、叠封、撕裂和跑边现象;表面无划花、刮伤、碰伤、压痕、胶痕等缺陷;接口部位平顺,不能在显眼位置。
注意事项:1、备料过程中的选料事关重大,要严格按设计要求使用相关材料,不得随意更改任何配件之材质。
材料的毛边,以及有撕裂、凹陷、压痕、虫孔、腐朽、斑点、节杷、变形等现象的尽量不予使用。
2、严格按订单要求成套生产(包括小配件)。
拼板胶工艺守则
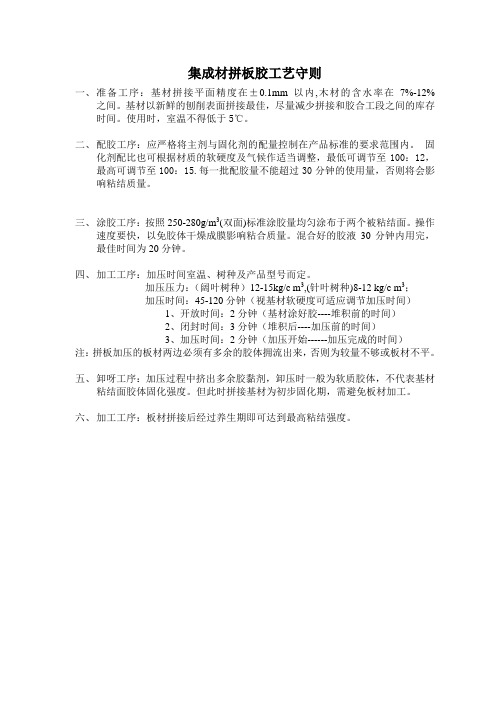
集成材拼板胶工艺守则
一、准备工序:基材拼接平面精度在±0.1mm以内,木材的含水率在7%-12%
之间。
基材以新鲜的刨削表面拼接最佳,尽量减少拼接和胶合工段之间的库存时间。
使用时,室温不得低于5℃。
二、配胶工序:应严格将主剂与固化剂的配量控制在产品标准的要求范围内。
固
化剂配比也可根据材质的软硬度及气候作适当调整,最低可调节至100:12,最高可调节至100:15.每一批配胶量不能超过30分钟的使用量,否则将会影响粘结质量。
三、涂胶工序:按照250-280g/m3(双面)标准涂胶量均匀涂布于两个被粘结面。
操作
速度要快,以免胶体干燥成膜影响粘合质量。
混合好的胶液30分钟内用完,最佳时间为20分钟。
四、加工工序:加压时间室温、树种及产品型号而定。
加压压力:(阔叶树种)12-15kg/c m3,(针叶树种)8-12 kg/c m3;
加压时间:45-120分钟(视基材软硬度可适应调节加压时间)
1、开放时间:2分钟(基材涂好胶----堆积前的时间)
2、闭封时间:3分钟(堆积后----加压前的时间)
3、加压时间:2分钟(加压开始------加压完成的时间)
注:拼板加压的板材两边必须有多余的胶体拥流出来,否则为较量不够或板材不平。
五、卸呀工序:加压过程中挤出多余胶黏剂,卸压时一般为软质胶体,不代表基材
粘结面胶体固化强度。
但此时拼接基材为初步固化期,需避免板材加工。
六、加工工序:板材拼接后经过养生期即可达到最高粘结强度。
实木家具拼板备料及拼板生产工艺

实木家具拼板备料及拼板生产工艺实木家具制造中的拼板备料工艺实木拼板是指用材性规格小的窄木条横向胶拼后上下两个面再砂光,然后再在上下两个面上压制花纹、材性较好的硬木刨切薄木单板而成的板材。
非直线造型配件使用拼板取料为可减少成型时切削量,提高木料的使用率,降低成本。
但有色差及胶合强度之问题。
白橡直拼板直拼板就是只有横向拼接,长度方向上是整料,直拼板制成,也是需经过干燥、选材、刨光、平整、侧拼宽度、砂光等重要步骤,利用10~12公分的长板材,应用特殊的木胶胶合成所需的宽度。
相较需耗费多年时间生长的大块实木,10~12公分的板材可拼接成所需要的宽度对于整块桌面的使用上来说,更广泛被运用。
指接板指接板由多块木板拼接而成,上下不再粘压夹板,由于竖向木板间采用锯齿状接口,类似两手手指交叉对接,故称指接板。
用于家具、厨具、衣柜等基础材料,指接板质量看芯材年轮,年轮较明显,年轮越大,说明树龄长,材质也就好。
指接板分为明齿和暗齿,暗齿最好,因为明齿在上漆后比较容易出现不平的现象,当然暗齿的加工难度要大些,木质越硬的板越好,因为它的变形要小得多,且花纹也会美观些。
拼板的种类【1】短拼板:【2】堆栈拼板【3】交错堆栈拼板注:取料排列方式取短料,有利于材料的利用率. 拼板取料注:1. 9mm=3mm(立轴成型) 3mm(带锯成型) 3mm(立轴成型)。
2.后脚料两端间距需以计算机制图仿真求其最小距离。
【1】加工规格:拼板最大宽度为930mm(拼板台面3'宽)。
南洋材(橡皮木)最大宽度,须依厂商提供规格而定。
2“厚拼板料宽度须在600mm以内,以避免重量太重,造成人员操作困难。
【2】加工余量: 长度:制长 20mm。
宽度:毛料宽 20mm。
锯路及两边余量:9mm。
两端切齐每端余量:10mm。
实木拼板制作工艺1、选料选料关系到后期板材的完美性,首先要尽量规避一些木料的缺陷地方,例如节疤、裂纹、凹口等。
然后注意所拼板的工艺要求,是否需要同色,要注意即使同一种材料颜色也可能会不一样。
(创新版)石料拼接工艺
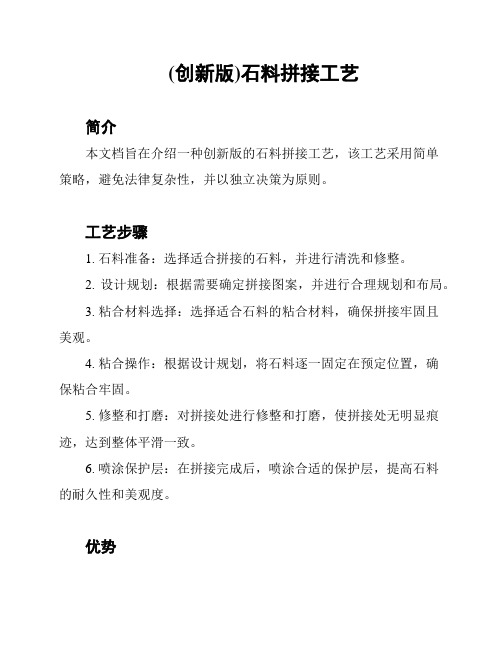
(创新版)石料拼接工艺
简介
本文档旨在介绍一种创新版的石料拼接工艺,该工艺采用简单
策略,避免法律复杂性,并以独立决策为原则。
工艺步骤
1. 石料准备:选择适合拼接的石料,并进行清洗和修整。
2. 设计规划:根据需要确定拼接图案,并进行合理规划和布局。
3. 粘合材料选择:选择适合石料的粘合材料,确保拼接牢固且
美观。
4. 粘合操作:根据设计规划,将石料逐一固定在预定位置,确
保粘合牢固。
5. 修整和打磨:对拼接处进行修整和打磨,使拼接处无明显痕迹,达到整体平滑一致。
6. 喷涂保护层:在拼接完成后,喷涂合适的保护层,提高石料
的耐久性和美观度。
优势
1. 简单策略:该工艺采用简单的策略和操作步骤,易于研究和理解。
2. 无法律复杂性:该工艺避免了法律复杂性的问题,减少了法律风险。
3. 独立决策:本工艺要求独立决策,无需过多依赖外部帮助。
4. 美观耐用:采用本工艺拼接的石料经过修整和保护处理后,具有良好的美观度和耐久性。
注意事项
1. 安全第一:在进行石料拼接工艺时,务必注意安全,使用个人防护装备,并遵循相关安全操作规程。
2. 材料选用:选择适合的石料和粘合材料,避免不匹配或不合适的情况。
3. 规划设计:在拼接前确保进行合理规划和设计,避免出现拼接位置错误或图案不合适的情况。
以上是关于(创新版)石料拼接工艺的简要概述,请根据需要细化每个步骤,并注意相关的良好实践和注意事项。
请注意,本文档所提供的内容无法直接确认引用,切勿将其作为法律依据使用。
木工车间各工序质量标准

木工车间各工序质量标准目的:加强员工责任心、提高工作效率、保证产品质量。
原则:本标准规定了实木零件或木材加工过程的材质要求和质量标准。
开料质量要求断料要求避开大死节、芯材、开裂、黑水纹、蛀虫、腐朽、断料长度按规定尺寸公差在5MM-10MM以内,零件横切面的垂直公差控制在3MM以内。
主要控制点:表面质量、长度、厚度尺寸。
平刨质量要求1、零件加工时必须顺木纹纹理方向刨,不出现逆纹深针孔和粗毛刺现象。
2、边面角度成90度直角。
3、刨削完的边面必须平整,无凹凸,跳刀,波浪现象。
主要控制点:表面质量,角度,尺寸,刨削面区分。
压刨质量要求1、零件加工时必须顺木纹纹理加工,一次刨削质量控制在2MM内。
2、实木零件角度公差为±1度。
3、实木零件变形公差长度500MM内控制在0.5MM内,500-1000MM控制在1MM 内,1000以上控制在1.5MM内。
4、实木零件尺寸公差宽厚控制在±0.8MM内。
主要控制点:表面质量,崩烂,跳刀,角度,深孔毛刺,变形等。
拼板质量要求1、使用指定胶水,不得随意用其它胶水替代。
2、对色时,必须以相同或相近颜色,相同木质,相同木纹方向的板件拼成一整体,任意相邻配件板件之间的含水率差不得超过3度。
3、拼板线的大小控制在0.3MM以内,胶水必须均匀分布。
4、拼板件卸下后,在常温下必须堆放24小时后才能进入下一道工序。
单边锯质量要求1、零件的实度尺寸公差控制在0.3MM。
2、需经拼板的零件纵部面的平整度控制在0.2MM内。
3、纵剖面不得出现有明显锯痕。
4、纵剖实木板材时,其翘曲度不得超过5MM。
带锯质量要求1、以模具划线为标准,弯形加工时锯线划线距离控制在线外3-5MM左右(注:实模大5MM)。
2、锯切瑞头余量保留3-5MM。
出榫质量要求1、零件加工时榫头长度公差控制在(0-0.5MM)内。
2、加工面端有榫的须以加工好一端榫肩为基础,加工另一端榫,才能保证内空。
3、加工零件的榫头内空尺寸控制在±0.5MM内。
摊的成型工艺要求制品规格一致,保护均匀,完整无损
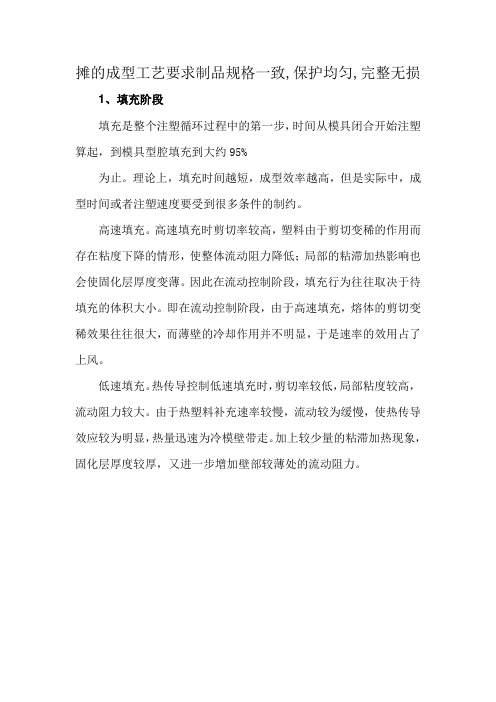
摊的成型工艺要求制品规格一致,保护均匀,完整无损1、填充阶段填充是整个注塑循环过程中的第一步,时间从模具闭合开始注塑算起,到模具型腔填充到大约95%为止。
理论上,填充时间越短,成型效率越高,但是实际中,成型时间或者注塑速度要受到很多条件的制约。
高速填充。
高速填充时剪切率较高,塑料由于剪切变稀的作用而存在粘度下降的情形,使整体流动阻力降低;局部的粘滞加热影响也会使固化层厚度变薄。
因此在流动控制阶段,填充行为往往取决于待填充的体积大小。
即在流动控制阶段,由于高速填充,熔体的剪切变稀效果往往很大,而薄壁的冷却作用并不明显,于是速率的效用占了上风。
低速填充。
热传导控制低速填充时,剪切率较低,局部粘度较高,流动阻力较大。
由于热塑料补充速率较慢,流动较为缓慢,使热传导效应较为明显,热量迅速为冷模壁带走。
加上较少量的粘滞加热现象,固化层厚度较厚,又进一步增加壁部较薄处的流动阻力。
由于喷泉流动的原因,在流动波前面的塑料高分子链排向几乎平行流动波前。
因此两股塑料熔胶在交汇时,接触面的高分子链互相平行;加上两股熔胶性质各异(在模腔中滞留时间不同,温度、压力也不同),造成熔胶交汇区域在微观上结构强度较差。
在光线下将零件摆放适当的角度用肉眼观察,可以发现有明显的接合线产生,这就是熔接痕的形成机理。
熔接痕不仅影响塑件外观,同时由于微观结构的松散,易造成应力集中,从而使得该部分的强度降低而发生断裂。
一般而言,在高温区产生熔接的熔接痕强度较佳,因为高温情形下,高分子链活动性较佳,可以互相穿透缠绕,此外高温度区域两股熔体的温度较为接近,熔体的热性质几乎相同,增加了熔接区域的强度;反之在低温区域,熔接强度较差。
2、保压阶段保压阶段的作用是持续施加压力,压实熔体,增加塑料密度(增密),以补偿塑料的收缩行为。
在保压过程中,由于模腔中已经填满塑料,背压较高。
在保压压实过程中,注塑机螺杆仅能慢慢地向前作微小移动,塑料的流动速度也较为缓慢,这时的流动称作保压流动。
QDZQ1214板材、型材拼接工艺守则
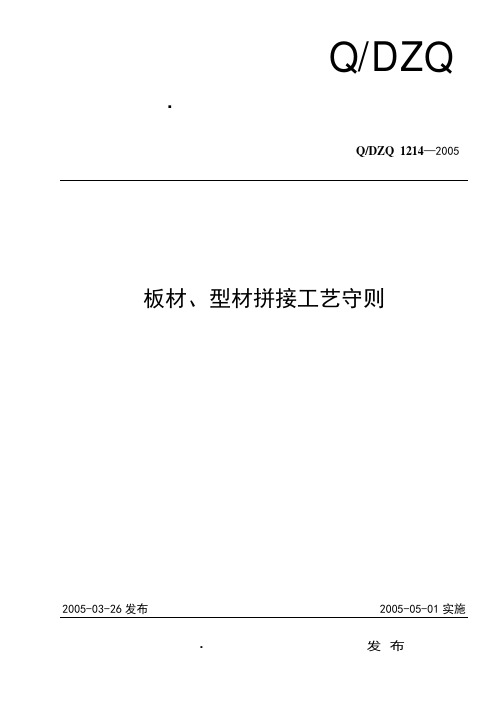
焊缝)。
9
不允许
δ且≤0.5mm,每米焊 ≤ 1mm, 每 米 焊 缝 不
缝不得超过一处
得超过一处
焊瘤
506
不允许
8
续表A1
Q/DZQ 1214-2005
GB6417
缺陷分级
缺陷名称
代号
Ⅰ
Ⅱ 402
焊缝厚度
为准)
不允许
不加垫单面焊缝允许 值 ≤ 15% δ 且 ≤ 1.5mm 每 100mm 焊 缝 内 缺 陷 总长≤25mm
( 指 不 足 ) 511
不允许
1mm, 每 100mm 焊 缝 内 2mm,每100mm焊缝内
设计要求
缺陷总长≤25mm
缺陷总长≤25mm
根部收缩
515 5013
不允许
≤0.2+0.02δ, 且≤0.5mm
≤0.2+0.02δ, 且≤1mm
≤0.2+0.04δ, 且≤2mm
≤0.05δ且≤0.5mm,
5.1.2 起重机轨道用型材超过供货长度的,可以焊接接长。轨道的最小拼接长度不应 小于 1m,且应位于轨道端部。 5.1.3 起重机轨道在距主梁跨度中心左右各 2.5m 范围内不得有拼接焊缝。
6 接头型式与要求
6.1 坡口型式 6.1.1 板材拼接接头坡口型式推荐如下(工艺另有规定的除外):
δ≤6mm: 不开坡口,采用I型焊缝,间隙0~1mm(δ为板材厚度)。 6mm<δ≤12mm: 开60°(单边30°)Y型坡口,间隙1mm,钝边2mm,背面清根后 焊接(采用埋弧焊时不开坡口)。 12mm<δ≤25mm: 开60°(单边30°)Y型坡口,间隙1~2mm,钝边2mm(采用手 工电弧焊及CO2气体保护焊)或5mm(采用埋弧焊),背面清根后焊接。
最新材料拼接工艺守则2901-1C
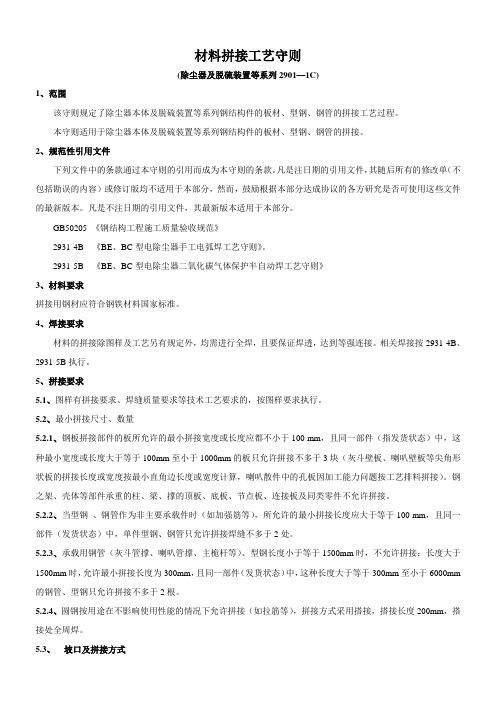
材料拼接工艺守则(除尘器及脱硫装置等系列2901—1C)1、范围该守则规定了除尘器本体及脱硫装置等系列钢结构件的板材、型钢、钢管的拼接工艺过程。
本守则适用于除尘器本体及脱硫装置等系列钢结构件的板材、型钢、钢管的拼接。
2、规范性引用文件下列文件中的条款通过本守则的引用而成为本守则的条款。
凡是注日期的引用文件,其随后所有的修改单(不包括勘误的内容)或修订版均不适用于本部分,然而,鼓励根据本部分达成协议的各方研究是否可使用这些文件的最新版本。
凡是不注日期的引用文件,其最新版本适用于本部分。
GB50205 《钢结构工程施工质量验收规范》2931-4B 《BE、BC型电除尘器手工电弧焊工艺守则》。
2931-5B 《BE、BC型电除尘器二氧化碳气体保护半自动焊工艺守则》3、材料要求拼接用钢材应符合钢铁材料国家标准。
4、焊接要求材料的拼接除图样及工艺另有规定外,均需进行全焊,且要保证焊透,达到等强连接。
相关焊接按2931-4B、2931-5B执行。
5、拼接要求5.1、图样有拼接要求、焊缝质量要求等技术工艺要求的,按图样要求执行。
5.2、最小拼接尺寸、数量5.2.1、钢板拼接部件的板所允许的最小拼接宽度或长度应都不小于100 mm,且同一部件(指发货状态)中,这种最小宽度或长度大于等于100mm至小于1000mm的板只允许拼接不多于3块(灰斗壁板、喇叭壁板等尖角形状板的拼接长度或宽度按最小直角边长度或宽度计算,喇叭散件中的孔板因加工能力问题按工艺排料拼接)。
钢之架、壳体等部件承重的柱、梁、撑的顶板、底板、节点板、连接板及同类零件不允许拼接。
5.2.2、当型钢、钢管作为非主要承载件时(如加强筋等),所允许的最小拼接长度应大于等于100 mm,且同一部件(发货状态)中,单件型钢、钢管只允许拼接焊缝不多于2处。
5.2.3、承载用钢管(灰斗管撑、喇叭管撑、主桅杆等)、型钢长度小于等于1500mm时,不允许拼接;长度大于1500mm时,允许最小拼接长度为300mm,且同一部件(发货状态)中,这种长度大于等于300mm至小于6000mm 的钢管、型钢只允许拼接不多于2根。
- 1、下载文档前请自行甄别文档内容的完整性,平台不提供额外的编辑、内容补充、找答案等附加服务。
- 2、"仅部分预览"的文档,不可在线预览部分如存在完整性等问题,可反馈申请退款(可完整预览的文档不适用该条件!)。
- 3、如文档侵犯您的权益,请联系客服反馈,我们会尽快为您处理(人工客服工作时间:9:00-18:30)。
斜顶头拼料工艺:
1,加工方向:拼料是从顶部往下铣削加工的,底部要有装夹螺丝,加工方向尽 量少,以减少加工量为原则 20mm 斜孔摆正加工 (目的:减少工 件校表分中和装 夹次数)
装夹螺丝:1, 底部没有足够空 间需加厚底部 20mm
装夹螺丝:2, 底部有足够空间, 直接攻牙
斜顶头拼料工艺:
2,方位基准:拼料要有基准符号D或倒C角,单个斜顶头要有基准符号D
方斜顶杆拼料工艺: 4,拼料间隙:0.3~0.5mm
整体式斜顶拼料工艺
1,加工方向:减少加工量为原则,省料省线割方向刀数,常用中间贴合开料再做 2,方位基准:拼料要有基准符号D或倒C角,单个斜顶要有基准符号D 3,线割区域:需上粉色区分,供CNC编程参考用,不然加工内容可能重复或遗漏 4,拼料间隙:两侧并排的入0.3~0.5mm,背靠背贴合的中间贴紧,上下面放0.25余量 磨光 5,拼料图:要有边界实体(方料),同类拼料放在一个文件中,如斜顶头放在 CZ0174-4000,斜顶杆放在CZ0174-4100,以此类推,可按照我司编码规则
需有X,Y,Z三个方向 的平位基准面
斜顶头拼料工艺: 3,线割区域:需上粉色区分,供CNC编程参考用,不然加工内容可能重复或遗漏
斜顶拼料工艺: 4,拼料间隙:按刀具的R十倍计算,比如R3只能加工30的深度,间隙为刀具直径再加 0.5防弹刀余量放
72mm
16.5 加工深度72除以球刀的半径的十倍后约为7.2,用 R8即可加工出来,间隙=直径16+0.5余量
斜顶头拼料工艺
1,加工方向:拼料是从顶部往下铣削加工的,底部要有装夹螺丝,加工方向尽 量少,以减少加工量为原则 2,方位基准:拼料要有基准符号D或倒C角,单个斜顶头要有基准符号D 3,线割区域:需上粉色区分,供CNC编程参考用,不然加工内容可能重复或遗漏 4,拼料间隙:按刀具的R十倍计算,比如R3只能加工30的深度,间隙为刀具直径再加 0.5防弹刀余量放 5,拼料图:要有边界实体(方料),同类拼料放在一个文件中,如斜顶头放在 CZ0174-4000,斜顶杆放在CZ0174-4100,以此类推,可按照我司编码规则 6,单件重量超过一公斤的不用拼
整体式斜顶拼料工艺
1,加工方向:减少加工量为原则,省料省线割方向刀数,常用中间贴紧线割开料再做后 续工序
背靠背贴合的中间贴紧,上下面放0.25余量磨光 斜顶侧面与拼料面贴紧,可以少割一刀
整体式斜顶拼料工艺
2,方位基准:拼料要有基准符号D或倒C角,单个斜顶要有基准符号D
整体式斜顶拼料工艺
3,线割区域:需上粉色区分,供CNC编程参考用,不然加工内容可能重复或遗漏
整体式斜顶拼料工艺
4,拼料间隙: A,两侧并排的放0.3~0.5mm
B,背靠背贴合的中间贴紧,上下面放0.25余量磨光
整体式斜顶拼料工艺
5,拼料图:要有边界实体(方料),同类拼料放在一个文件中,如斜顶头放在 CZ0174-4000,斜顶杆放在CZ0174-4100,以此类推,可按照我司编码规则
模仁挤紧块拼料工艺
1,拼料图:要有边界实体(方料),同类拼料放在一个文件中,如挤紧块放在 CZ0174-5000,以此类推,可按照我司编码规则 2,背靠背中间割开,一分为二,两侧面留余量0.25单边
镶件拼料工艺
1,拼料图:要有边界实体(方料),同类拼料放在一个文件中,如后模镶件放在 CZ0174-2100,以此类推,可按照我司编码规则 2,背靠背中间割开,一分为:要有边界实体(方料),同类拼料放在一个文件中,如滑块放在CZ01743000,以此类推,可按照我司编码规则 2,并排中间割开,一分为二,T槽可不留余量
3,背靠背一分为二,中间留0.5MM