模仿绘制-精馏塔DCS图
甲醇间歇精馏建模仿真

甲醇/水二元间歇精馏塔的建模与仿真间歇精馏过程是过程工业中的重要分离过程之一,由于间歇化工过程适合小批量、多品种和高附加值的精细化学品的生产,近年来其工艺研究和开发得到过程工业界的日益高度重视。
本文以一套甲醇与水二元间歇精馏塔试验装置为研究对象,应用动态物料平衡和相平衡等机理建模法,建立了固定回流比的间歇精馏工艺过程原理模型,以Matlab为平台,编写了模拟间歇精馏塔的一次开车过程,在不同回流比下,对每层塔板、冷凝器以及再沸器中甲醇的浓度的变化,以及第2、4层塔板和冷凝器、再沸器中的温度变化进行了仿真和模拟计算。
甲醇/水二元间歇精馏塔试验装置简介精馏实验前,原料一次性加入再沸器。
再沸器夹套通水蒸汽加热,水蒸气流量用一套流量控制器控制。
塔内共设有6块筛板式塔板。
塔顶甲醇蒸汽流经冷水冷凝器冷凝,部分回流。
工艺流程图如图1所示:图1甲醇/水二元间歇精馏塔实验装置工艺流程图动态数学模型的建立为了建立该甲醇/水二元间歇精馏塔的动态数学模型,做了以下主要假设:(1)塔内蒸汽流量V(mol/h)和回流量L(mol/h)保持恒定;无挟带和渗漏,冷凝器全冷凝。
(2)每块塔板上的滞留液量恒定(Mi,i=1,2,…,6);蒸汽滞液量可忽略。
(3)塔板为理想塔板,塔板效率恒定,气液相平衡,气相为理想气体。
(4)绝热操作,塔板和再沸器内气液相完全混合。
基于以上假设,该间歇精馏塔的再沸器、塔顶冷凝器和塔板1到塔板6的动态物料平衡方程如下:(1)(2)(3)(4)(5)(6)i=2,3,4,5(7) 式中,Ms为再沸器的滞留液量;Md为塔顶冷凝器的滞留液量;Xi(i=1,2,…,6,d,s)是塔板i(i=1,2,…,6)、再沸器和塔顶冷凝器的液相甲醇浓度(摩尔分数);Yi(i=1,2,…,6,s)是塔板i(i=1,2,…,6)和再沸器的气相甲醇浓度(摩尔分数)。
假定精馏塔中二元混合物的气相甲醇浓度Y和液相甲醇浓度X的关系,可以近似的以恒定的相对挥发度来表示,即:,j=1,2,…6,s (8)静态物料平衡方程和回流比计算式为:V=L+D (9)R=L/D (10) 式中,D为塔顶冷凝后收集的甲醇产品流量,mol/h;R为回流比。
精馏塔工作原理

精馏过程的主要设备有:精馏塔、再沸器、 冷凝器、回流罐和输送设备等。精馏塔以进料 板为界,上部为精馏段,下部为提留段。一定 温度和压力的料液进入精馏塔后,轻组分在精 馏段逐渐浓缩,离开塔顶后全部冷凝进入回流 罐,一部分作为塔顶产品(也叫馏出液),另 一部分被送入塔内作为回流液。回流液的目的 是补充塔板上的轻组分,使塔板上的液体组成
保持稳定,保证精馏操作连续稳定地进。而 重组分在提留段中浓缩后,一部分作为塔釜产 品(也叫残液),一部分则经再沸器加热后送 回塔中,为精馏操作提供一定量连续上升的蒸 气气流。
二、精馏塔动画演示
1.板式塔结构 2.板式塔工作原理 3.精馏塔实观 4.精馏塔剖面图 5.板式精馏塔
1.板式塔结构
2.板式塔工作原理
四、组态画面及设备
1.精馏塔单元仿DCS图 2.精馏塔单元仿现场图 3.精馏工艺流程 4.换热器 5.再沸器
1.精馏塔单元仿DCS图
2.精馏塔单元仿现场图
3.精馏工艺流程
4.换热器
感谢您的聆听 您的关注使我们更努力
此课件下载后可自行编辑修改 关注我 每天分享干货
19
作为回流液由调节器FC104控制流量(9664KG/H) 送回DA405第32层塔板;另一部分则作为产品,其 流量由调节器FC103控制(6707Kg/h)。回流罐的 液位由调节器LC103与FC103构成的串级控制回路 控制。DA405操作压力由调节器PC102分程控制为 5.0Kg/m2。同时调节器PC101将调节回流罐的气相 出料,保证系统的安全和稳定。
塔釜液体的一部分经再沸器EA408A/B回精馏 塔,另一部分由调节器FC102控制流量(7349Kg/h), 作为塔底采出产品。调节器LC101和FC102构成串 级控制回路,调节精馏塔的液位。再沸器用低压 蒸气加热,加热蒸气流量由调节器TC101控制, 其冷凝液送FA414。FA414的液位由调节器LC102 调节。
精馏操作及精馏DCS操作精讲
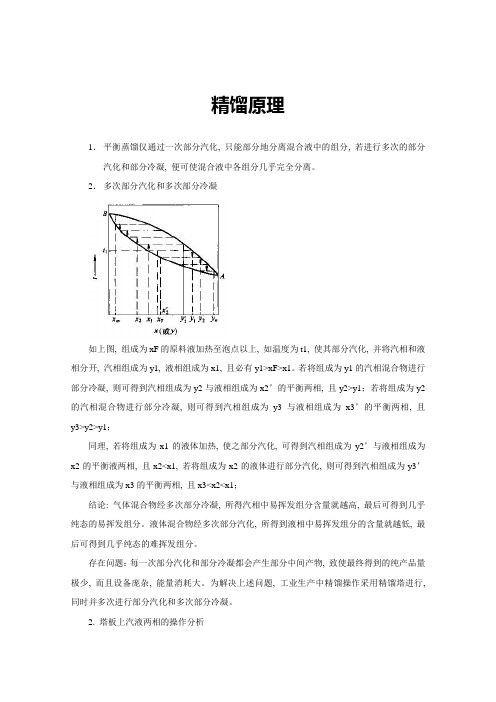
精馏原理1.平衡蒸馏仅通过一次部分汽化, 只能部分地分离混合液中的组分, 若进行多次的部分汽化和部分冷凝, 便可使混合液中各组分几乎完全分离。
2.多次部分汽化和多次部分冷凝如上图, 组成为xF的原料液加热至泡点以上, 如温度为t1, 使其部分汽化, 并将汽相和液相分开, 汽相组成为y1, 液相组成为x1, 且必有y1>xF>x1。
若将组成为y1的汽相混合物进行部分冷凝, 则可得到汽相组成为y2与液相组成为x2’的平衡两相, 且y2>y1;若将组成为y2的汽相混合物进行部分冷凝, 则可得到汽相组成为y3与液相组成为x3’的平衡两相, 且y3>y2>y1;同理, 若将组成为x1的液体加热, 使之部分汽化, 可得到汽相组成为y2’与液相组成为x2的平衡液两相, 且x2<x1, 若将组成为x2的液体进行部分汽化, 则可得到汽相组成为y3’与液相组成为x3的平衡两相, 且x3<x2<x1;结论: 气体混合物经多次部分冷凝, 所得汽相中易挥发组分含量就越高, 最后可得到几乎纯态的易挥发组分。
液体混合物经多次部分汽化, 所得到液相中易挥发组分的含量就越低, 最后可得到几乎纯态的难挥发组分。
存在问题:每一次部分汽化和部分冷凝都会产生部分中间产物, 致使最终得到的纯产品量极少, 而且设备庞杂, 能量消耗大。
为解决上述问题, 工业生产中精馏操作采用精馏塔进行, 同时并多次进行部分汽化和多次部分冷凝。
2. 塔板上汽液两相的操作分析图1为板式塔中任意第n块塔板的操作情况。
如原料液为双组分混合物, 下降液体来自第n-1块板, 其易挥发组分的浓度为xn-1, 温度为tn-1。
上升蒸气来自第n+1块板, 其易挥发组分的浓度为yn+1, 温度为tn+1。
当气液两相在第n块板上相遇时, tn+1>tn-1, 因而上升蒸气与下降液体必然发生热量交换, 蒸气放出热量, 自身发生部分冷凝, 而液体吸收热量, 自身发生部分气化。
精馏塔仿DCS图
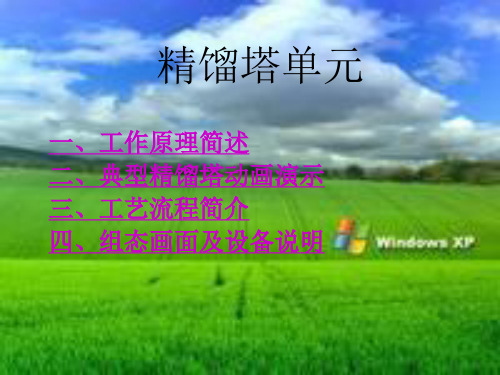
精馏塔单元一、工作原理简述二、典型精馏塔动画演示三、工艺流程简介四、组态画面及设备说明一、工作原理简述精馏是化工生产中分离互溶液体混合物的典型单元操作,其实质是多级蒸馏,即在一定压力下,利用互溶液体混合物各组分的沸点或饱和蒸汽压不同,使轻组分(沸点较低或饱和蒸汽压较高的组分)汽化,经多次部分液相汽化和部分气相冷凝,使气相中的轻组分和液相中的重组分浓度逐渐升高,从而实现分离。
精馏过程的主要设备有:精馏塔、再沸器、冷凝器、回流罐和输送设备等。
精馏塔以进料板为界,上部为精馏段,下部为提留段。
一定温度和压力的料液进入精馏塔后,轻组分在精馏段逐渐浓缩,离开塔顶后全部冷凝进入回流罐,一部分作为塔顶产品(也叫馏出液),另一部分被送入塔内作为回流液。
回流液的目的是补充塔板上的轻组分,使塔板上的液体组成保持稳定,保证精馏操作连续稳定地进行。
而重组分在提留段中浓缩后,一部分作为塔釜产品(也叫残液),一部分则经再沸器加热后送回塔中,为精馏操作提供一定量连续上升的蒸气气流。
二、精馏塔动画演示1.板式塔结构2.板式塔工作原理3.精馏塔实观4.精馏塔剖面图5.板式精馏塔1.板式塔结构2.板式塔工作原理3精馏塔实观4精馏塔剖面图5.板式精馏塔三、工艺流程简介本单元是一种加压精馏操作,原料液为脱丙烷塔塔釜的混合液,分离后馏出液为高纯度的C4产品,残液要是C5以上组分。
67.80C的原料液经流量调节器FIC101控制流量(14056Kg/h)后,从精馏塔DA405的第16块塔板(全塔共32块塔版)进料。
塔顶蒸气经全凝器EA419冷凝为液体后进入回流罐FA408;回流罐FA408的液体由泵GA412A/B抽出,一部分作为回流液由调节器FC104控制流量(9664KG/H)送回DA405第32层塔板;另一部分则作为产品,其流量由调节器FC103控制(6707Kg/h)。
回流罐的液位由调节器LC103与FC103构成的串级控制回路控制。
精馏塔dcs分散控制系统简介

精馏塔DCS分散控制系统简介一、分散控制系统功能与特点1.集散控制系统功能DCS,〔Distributed Control System〕分散控制系统的简称,国内一般习惯称之为集散控制系统,集散控制系统由计算机技术、信号处理技术、测量控制技术、通信网络技术和人机接口技术开展浸透产生。
其本质是利用计算机技术对消费过程进展集中监视、操作、管理和分散控制。
管理的集中性和控制的分散性构成了集散控制系统的主体。
2.集散控制系统特点〔1〕自主性。
系统上各工作站是通过网络接口连接起来,各工作站独立自主地完成分配给自己的规定任务,如数据采集、处理、计算、监视操作和控制等。
系统各工作站都采用最新技术的微计算机,存储容量易于扩大,配套软件功能齐全,是一个可以独立运行的高可靠性子系统,而且可以随着微处理器的开展而更新换代。
它的控制功能齐全,控制算法丰富,集反响控制、顺序控制和批量控制于一体,还可以实现模糊控制、优化控制等先进的控制算法。
〔2〕协调性。
各工作站之间通过通信网络传送各种信息协调工作,以便完成控制系统的总体功能和优化处理,采用实时性、平安可靠的工业控制局部网络,使整个系统信息共享。
〔3〕可靠性。
高可靠性、高效率和高可用性是集散控制系统的生命力所在。
二、计算控制系统硬件构成硬件积木化、软件模块化、控制组态化和通信网络化。
1.现场控制站主要设备〔1〕机柜。
〔2〕电源。
〔3〕控制计算机。
一般由CPU、存储器、总线、输入/输出通道等根本局部组成。
2.操作站主要设备〔1〕操作台。
〔2〕主机设备。
〔3〕外存设备。
〔4〕显示设备。
〔5〕键盘。
三、集散控制系统软件技术1.控制软件现场控制站应具有数据采集、控制输出、自动控制和网络通信等功能。
要实现这些功能,现场控制站必须配置一个控制软件系统。
2.操作软件操作站要完成多种画面〔综观、分组、回路、趋势、报警、流程图、系统状态等〕的显示和操作、实时数据和历史数据的管理以及消费记录的打印输出,实现这些功能操作站必须配置实时多任务操作系统和数据库管理。
精馏塔物料平衡控制DCS系统设计
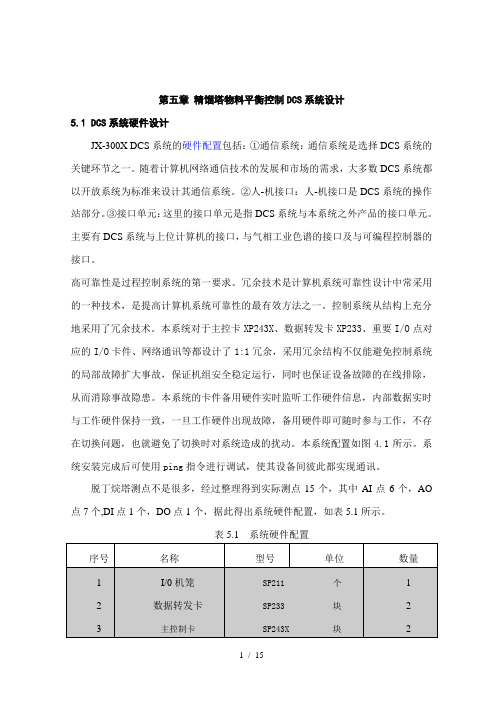
第五章精馏塔物料平衡控制DCS系统设计5.1 DCS系统硬件设计JX-300X DCS系统的硬件配置包括:①通信系统:通信系统是选择DCS系统的关键环节之一。
随着计算机网络通信技术的发展和市场的需求,大多数DCS系统都以开放系统为标准来设计其通信系统。
②人-机接口:人-机接口是DCS系统的操作站部分。
③接口单元:这里的接口单元是指DCS系统与本系统之外产品的接口单元。
主要有DCS系统与上位计算机的接口,与气相工业色谱的接口及与可编程控制器的接口。
高可靠性是过程控制系统的第一要求。
冗余技术是计算机系统可靠性设计中常采用的一种技术,是提高计算机系统可靠性的最有效方法之一。
控制系统从结构上充分地采用了冗余技术。
本系统对于主控卡XP243X、数据转发卡XP233、重要I/O点对应的I/O卡件、网络通讯等都设计了1:1冗余,采用冗余结构不仅能避免控制系统的局部故障扩大事故,保证机组安全稳定运行,同时也保证设备故障的在线排除,从而消除事故隐患。
本系统的卡件备用硬件实时监听工作硬件信息,内部数据实时与工作硬件保持一致,一旦工作硬件出现故障,备用硬件即可随时参与工作,不存在切换问题,也就避免了切换时对系统造成的扰动。
本系统配置如图4.1所示。
系统安装完成后可使用ping指令进行调试,使其设备间彼此都实现通讯。
脱丁烷塔测点不是很多,经过整理得到实际测点15个,其中AI点6个,AO 点7个,DI点1个,DO点1个,据此得出系统硬件配置,如表5.1所示。
表5.1 系统硬件配置5.2 DCS系统的组态设计5.2.1 I/O组态确定了系统的硬件配置,这样可以开始进行主机设置。
该系统测点较少,需要一个控制站,一个操作站、工程师站,分别命名为OS130、ES130。
图5.1 主机设置主机设置完成以后,可以进行控制站的I/O 组态,I/O 组态主要包括下面的一些内容:1. 数据转发卡设置2. I/O 卡件设置3. 信号点设置数据转发卡组态是对某一控制站内部的数据转发卡在SBUS-S2 网络上的地址以及卡件的冗余情况等参数进行组态。
精馏塔演示图

底产品罐 V13
釜排液前阀
V14 此段管路无 塔底产品冷却器水阀 离心泵 V15直排
回水
原料罐 倒料路径
水表
进水
中控教仪UTS-JL-2J精馏装置图(含减压系统)
产品冷却器
顶冷 V32 顶温
冷凝液温
回流温度
接真空
塔顶放空阀
V26
V50 外 回 流 L1 V52 V40 V49 产品罐
采 出 量 凝液罐
接真空
平衡管
V25 ▲不能以液位高 度判断产品量
凝液罐清空阀 采出泵 齿轮全开 装的高 度不一致 V29 真空缓冲罐 真空泵 A真空管路 蒸 气 量 V2
原料换热后出顶冷↓ 加料口 B接塔顶产品 罐
平衡管接塔顶
原料进顶冷↑
10板 产品罐 清空阀
TIC712 测温点
进料回流L3
蒸气量V1
产品出料 接软管 12板 V03 视镜 鼓泡 预热温 直接回水阀 底产品温度 排釜液流量 V10 V21 接真空
精馏塔操作仿真训练

技能训练二精馏塔操作仿真训练●训练目标能利用仿真系统操作精馏塔。
●训练准备熟悉工艺流程及原理。
本单元是一种加压精馏操作,原料液为脱丙烷塔塔釜的混合液,分离后馏出液为高纯度的C4产品,残液主要是C5以上组分。
67.8℃的原料液经流量调节器FICl01控制流量(14056kg/h)后,从精馏塔DA405的第16块塔板(全塔共32块塔板)进料。
塔顶蒸气经全凝器EA419冷凝为液体后进入回流罐FA408;回流罐FA408的液体由泵GA412A/B抽出,一部分作为回流液由调节器FCl04控制流量(9664kgm)送回DA405第32层塔板;另一部分则作为产品,其流量由调节器FCl03控制(6707kg/h)。
回流罐的液位由调节器LCl03与FCl03构成的串级控制回路控制。
DA405操作压力由调节器PCI02分程控制为5.0kg/m2,其分程动作如图3-34所示。
同时调节器PCI01将调节回流罐的气相出料,保证系统的安全和稳定。
图3-34调节阀PVl02分程动作示意图塔釜液体的一部分经再沸器EA408A/B回精馏塔,另一部分由调节器FCl02控制流量(7349kg/h),作为塔底采出产品。
调节器LCl01和FCl02构成串级控制回路,调节精馏塔的液位。
再沸器用低压蒸汽加热,加热蒸汽流量由调节器TCl01控制,其冷凝液送FA414。
FA414的液位由调节器LCl02调节。
其工艺流程如图3-35所示。
图3-58 精馏塔单元带控制点工艺流程图●训练步骤(要领)(一)冷态开车进料前确认装置冷态开工状态为精馏塔单元处于常温、常压、氮气吹扫完毕的氮封状态,所有阀门、机泵处于关停状态、所有调节器置于手动状态。
1.进料及排放不凝气(1)打开PVl01(开度>5%)排放塔内不凝气;(2)打开FVl01(开度>40%),向精馏塔进料;(3)进料后,塔内温度略升、压力升高;当压力升高至0.5atm(表)时(4)控制塔顶压力大于1.0atm(表),不超过4.25atm(表)。
基于DCS的精馏塔工艺流程

第一章绪论1.1 课题研究的目的和意义随着现代化工的飞速发展,生产规模的不断扩大,工艺过程越趋复杂,对工艺流程前后工序相互关联紧密,充分利用能源等提出的要求,DCS控制系统已发展为过程控制的主流。
它在工业过程控制领域发挥了越来越重要的作用,广发应用于各种行业的生产过程中。
生产设备自动化程度的提高有利于降低工厂生产成本,促进生产线的柔性化和集成化,有利于提高产品的质量,产量以及产品的竞争力。
从某种意义上说,DCS控制技术为我们创造了不可忽视的经济效益和社会效益。
精馏塔作为石油化工生产过程的一个十分重要的环节,对其实现科学的控制直接决定着产品的质量、产量和能耗。
这也是工业自动化领域里的一个长期的研究课题。
1.2本课题的主要研究内容本课题的主要内容是根据精馏塔的工艺流程,控制系统要求等,分析影响精馏塔控制的主要参数,提出合理的控制方案并绘出其相应的控制流程图,最后,应用JX-300XP DCS控制系统实现精馏塔的过程监视,数据收集,数据处理,数据存储,报警和登陆,过程控制等功能。
第二章工艺过程分析2.1精馏系统工艺过程分析2.1.1工艺流程简介本设计流程是利用精馏方法,在精馏塔中将乙醇从塔釜混合物中分离出来。
精馏是将液体混合物部分气化,利用其中各组分相对挥发度的不同,通过液相和气相间的质量传递来实现对混合物的分离。
本装置中将由于乙醇的沸点较低,易挥发,故采用加热精馏,经气化的乙醇蒸汽经冷凝,可得到较高纯度的乙醇。
原料(乙醇和水及少量杂的混合物)经进料管由精馏塔进料板处流入塔内,开始精馏操作;当釜中的料液建立起适当液位时,再沸器进行加热,使之部分气化返回塔内。
气相沿塔上升直至塔顶,由塔顶冷凝器将其进行全部或部分冷凝。
将塔顶蒸汽凝液部分作为塔顶产品取出,称为馏出物。
另一部分凝液作为回流返回塔顶。
回流液从塔顶沿塔流下,在下降过程中与来自塔顶的上升蒸汽多次逆向接触和分离。
当流至塔底时,被再沸器加热部分气化,其气相返回塔内作为气相回流,而其液相则作为塔底产品采出。
采用CHEMCAD进行精馏塔模拟和设计
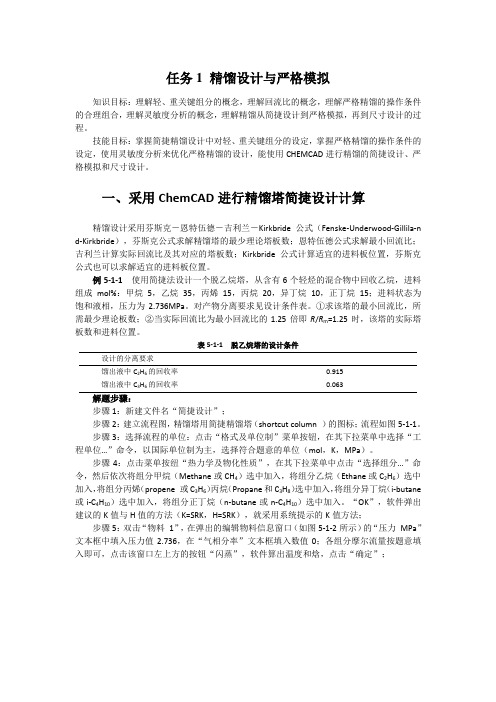
任务1 精馏设计与严格模拟知识目标:理解轻、重关键组分的概念,理解回流比的概念,理解严格精馏的操作条件的合理组合,理解灵敏度分析的概念,理解精馏从简捷设计到严格模拟,再到尺寸设计的过程。
技能目标:掌握简捷精馏设计中对轻、重关键组分的设定,掌握严格精馏的操作条件的设定,使用灵敏度分析来优化严格精馏的设计,能使用CHEMCAD进行精馏的简捷设计、严格模拟和尺寸设计。
一、采用ChemCAD进行精馏塔简捷设计计算精馏设计采用芬斯克-恩特伍德-吉利兰-Kirkbride公式(Fenske-Underwood-Gillila-n d-Kirkbride),芬斯克公式求解精馏塔的最少理论塔板数;恩特伍德公式求解最小回流比;吉利兰计算实际回流比及其对应的塔板数;Kirkbride公式计算适宜的进料板位置,芬斯克公式也可以求解适宜的进料板位置。
例5-1-1使用简捷法设计一个脱乙烷塔,从含有6个轻烃的混合物中回收乙烷,进料组成mol%:甲烷5,乙烷35,丙烯15,丙烷20,异丁烷10,正丁烷15;进料状态为饱和液相,压力为2.736MPa。
对产物分离要求见设计条件表。
①求该塔的最小回流比,所需最少理论板数;②当实际回流比为最小回流比的1.25倍即R/R m=1.25时,该塔的实际塔板数和进料位置。
表5-1-1 脱乙烷塔的设计条件设计的分离要求馏出液中C2H6的回收率馏出液中C3H6的回收率0.915 0.063解题步骤:步骤1:新建文件名“简捷设计”;步骤2:建立流程图,精馏塔用简捷精馏塔(shortcut column )的图标;流程如图5-1-1。
步骤3:选择流程的单位:点击“格式及单位制”菜单按钮,在其下拉菜单中选择“工程单位…”命令,以国际单位制为主,选择符合题意的单位(mol,K,MPa)。
步骤4:点击菜单按纽“热力学及物化性质”,在其下拉菜单中点击“选择组分…”命令,然后依次将组分甲烷(Methane或CH4)选中加入,将组分乙烷(Ethane或C2H6)选中加入,将组分丙烯(propene 或C3H6)丙烷(Propane和C3H8)选中加入,将组分异丁烷(i-butane 或i-C4H10)选中加入,将组分正丁烷(n-butane或n-C4H10)选中加入。
精馏塔工作原理PPT课件

2.板式塔工作原理
7
3 精 馏 塔 实 观
8
4 精 馏 塔 剖 面 图
9
5.板式精馏塔
10
2019/10/24
11
三、工艺流程简介
本单元是一种加压精馏操作,原料液为脱 丙烷塔塔釜的混合液,分离后馏出液为高纯度 的C4产品,残液要是C5以上组分。
67.80C的原料液经流量调节器FIC101控制 流量(14056Kg/h)后,从精馏塔DA405的第
液位由调节器LC103与FC103构成的串级控制回 路
控制。DA405操作压力由调节器PC102分程控制
为
13
塔釜液体的一部分经再沸器EA408A/B回精 馏
塔,另一部分由调节器FC102控制流量 (7349Kg/h),
作为塔底采出产品。调节器LC101和FC102构成 串
级控制回路,调节精馏塔的液位。再沸器用低压
3
保持稳定,保证精馏操作连续稳定地进行。而 重组分在提留段中浓缩后,一部分作为塔釜产 品(也叫残液),一部分则经再沸器加热后送 回塔中,为精馏操作提供一定量连续上升的蒸 气气流。
4
二、精馏塔动画演示
1.板式塔结构 2.板式塔工作原理 3.精馏塔实观 4.精馏塔剖面图 5.板式精馏塔
5
1.板式塔结构
蒸气加热,加热蒸气流量由调节器TC101控制,
其冷凝液送FA414。FA414的液位由调节器
LC102
14
四、组态画面及设备
1.精馏塔单元仿DCS图 2.精馏塔单元仿现场图 3.精馏工艺流程 4.换热器 5.再沸器
15
1.精馏塔单元仿DCS图
16
2.精馏塔单元仿现场图
17
3.精馏工艺流程
精馏示意图

q值
q>1
q线斜率 q/q1 +
饱和液体
气液混合 物
IF=IL
IL<IF<IV
q=1
0 < q <1
无穷大
–
0
饱和蒸汽
IF=IV
q=0
精馏
5
双组分连续精馏塔的计算
– 不同q值对 操作线的影 响
q值不同改变的 是提馏段的操作线 方程。当进料组成、 回流比及分离要求 一定时,q值的减少 使提馏段操作线越 来越靠近平衡线。
由于提馏段下降 液体量L’不易确定,所 以提馏段操作线的实际 应用价值不大。但提馏 段操作线一定通过C点 (xW,xW)(间接蒸汽 加热方式)
c
d
xW
xD
精馏
4
双组分连续精馏塔的计算 – 不同 q值对应的 q线方 程
f q=1 0 < q <1
q=0 q<0 q>1
e
xF
进料状况
冷液体
进料的焓 IF IF<IL
q<0
q>1
f 0 < q <1
q=0
q=1
e
xW
精馏
xF
xD
6
双组分连续精馏塔的计算
图解法
1
逐板法原理
4 5
2
3
xW
精馏
xF
xD
7
双组分连续精馏塔的计算
图解法(续)
1
实际图解过程
4
2
3
5
xW
精馏
xF
xD
y n1 L D xn xD L D L D
L 令 R ( 回流比) D
精馏塔的动态模拟

精馏塔的动态模拟目录一、数学建模二、分析与讨论三、优化四、程序清单(1)分析和讨论(2)分析和讨论(3)最优化部分前言化学工业中,精馏过程是能量消耗最大的单元操作之一,自从发生了世界性的能源问题以来,精馏过程的节能问题已广泛引起了人们的重视。
近年来,已经开发了多种精馏节能的工艺流程,如多效精馏.热泵精馏、热偶精馏等。
多效精馏作为一种精馏节能新工艺近几年来其理论研究不断深入,在工业生产中的应用日益广泛。
工业上普遍存在非稳定状态或动态的精馏过程.实际的生产过程不可避免地受到各种人为或非人为因素的扰动,使一些操作参数和过程变量随时间发生变化,因此对于连续精馏过程的动态特性的研究和模拟具有重要的实际意义.研究精馏塔的动态特性时通常使用数学模拟方法,这首先需要建立1个模型精馏塔,然后对模型塔中的各个塔板作非稳态物料衡算、热量衡算等,得到动态精馏过程的数学模型,在一定的初始条件下经过求解,可得到操作条件发生扰动时各个精馏过程参数随时间变化的历程,即动态响应.若精馏系统内无约束某些参数变化速度和变化范围的控制器,其动态响应称为开环响应,否则为闭环响应.反应精馏技术将反应与分离过程在一个塔内实现, 相对传统的先反应后分离过程具有转化率高、选择性好、操作易、投资省等一系列优点, 但反应精馏过程需同时遵循质量作用定律和精馏分离原理, 其过程影响因素复杂. 自20 世纪70 年代以来, 有关反应精馏的研究重点从工艺转向数学模拟. 现已开发有灵活可靠的过程模拟计算软件. 另一方面, 自20 世纪70 年代末催化精馏技术成功地应用于甲基叔丁基醚(M TBE) 生产以后, 该技术的应用受到了学者们的关注.一、精馏塔数学模型的建立:根据对过程系统中状态变量分布特征的不同描述方法,一般可以把数学模型分为集中参数模型,分布参数模型和多级集中参数模型。
本次大作业利用多级集中参数模型对精馏塔动态特性进行分析和模拟。
对于控制的动态数学模型,我们希望用最简单的形式,最大限度地概括出过程的特性。