冷作模具的失效和预防
冷作模具热处理后变形与预防及工艺优化
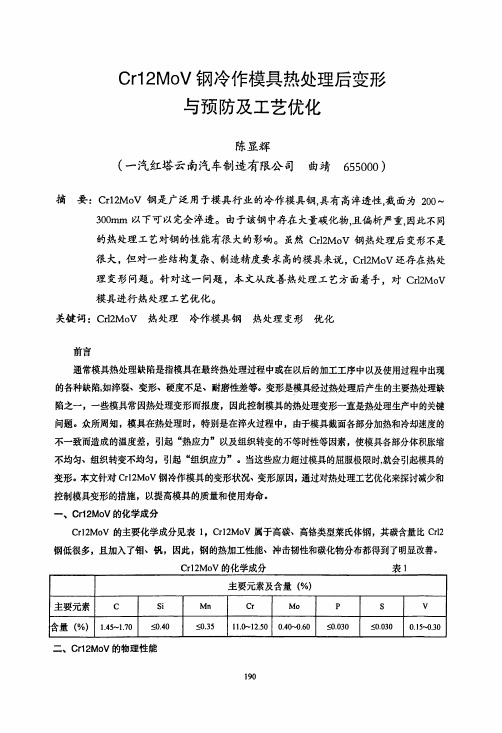
/、 Lj
o
,_、
(__)
o
邋 礴
遗
璃
时同(h)
时献Min)
图6
图7
小碳化物的完全溶解,另一方面促进了大碳化物尖角的局部溶解,使钢中的碳化物形态和分布 得到改善,从而减少了模具的变形。Crl2MoV高温调质工艺如图7所示。 (三)采用二次回火。淬火加热温度在1020~1050℃范围内,将回火温度由250℃提高到400"t2, 并进行二次回火,这样模具最终硬度可达到57~58HRC,不但可以减少了模具的变形,同时可以使
临界点 温度(℃)
Acl 810
表2 膨胀系数
A∞
1200
Arl 760
温度(℃) 膨胀系数
2啦!OO
10.9x10.6
2m400
11.4x10_6
2口击00
12.2x10.6
三、Orl2MoV钢经不同温度淬火后在不同温度回火后的硬度及其金相组织
(一)Crl2MoV钢经不同温度淬火和不同温度回火后的硬度见表3。根据实验数据绘制其关系
Crl
2MoV钢冷作模具热处理后变形 与预防及工艺优化
陈显辉
(一汽红塔云南汽车制造有限公司
曲靖655000)
摘要: Crl2MoV钢是广泛用于模具行业的冷作模具钢,具有高淬透性,截面为200—
300mm以下可以完全淬透。由于该钢中存在大量碳化物,且偏析严重,因此不同 的热处理工艺对钢的性能有很大的影响。虽然Cd2MoV钢热处理后变形不是 很大,但对一些结构复杂、制造精度要求高的模具来说,Crl2MoV还存在热处 理变形问题。针对这一问题,本文从改善热处理工艺方面着手,对Crl2MoV 模具进行热处理工艺优化o 关键词: Cd2MoV热处理冷作模具钢热处理变形优化
探讨分析模具钢的失效问题

探讨分析模具钢的失效问题
冷作模具主要完成金属或非金属材料的冷成形,包括冷冲压、冷挤压和冷镦模具等。
与热作模具相比,这类模具工作载荷大、尺寸精度、表面质量要求高、加工批量大,多数为最终产品。
为适应这种工况要求,多采用高碳或高合金钢制作冷作模具,工作硬度为
58-60HR
C。
通常选用的冷作模具钢要求有足够的强度(包括抗拉,抗压和抗弯强度),足够的韧度,足够的硬度和抗磨能力(特别是表面),足够的抗疲劳能力(特别是多冲疲劳性能);对于大载荷的冷挤压和冷镦锻体成型模具,因剧烈变形产生热量(约300℃),要求材料具有更高的抗变形和断裂能力。
冷作模具失效分析中的一些问题探讨
通过对国内冷镦、冷冲、冷挤压模具失效情况调查分析,冷作模具主要失效类型是过载失效和磨损失效,约占失效总数80%-90%。
冷镦模具以裂断或非正常磨损(局部脱落)为主,冷挤压模具以脆断或磨损失效为主,而冷冲模具以磨损失效为主。
高工作应力,大波动应力的冷挤压和冷镦模具出现脆性开裂失效比例明显高于低工作应力冷冲模。
实际上冷作模具失效原因很多,除此模具材料因素外,还与工作设备精度和状况,制品材质和表面质量,模具结构和加工精度,操作人员素质等多因素有关,其中一些随机因素给失效分析增加困难。
解析冷作模具裂纹形成原因
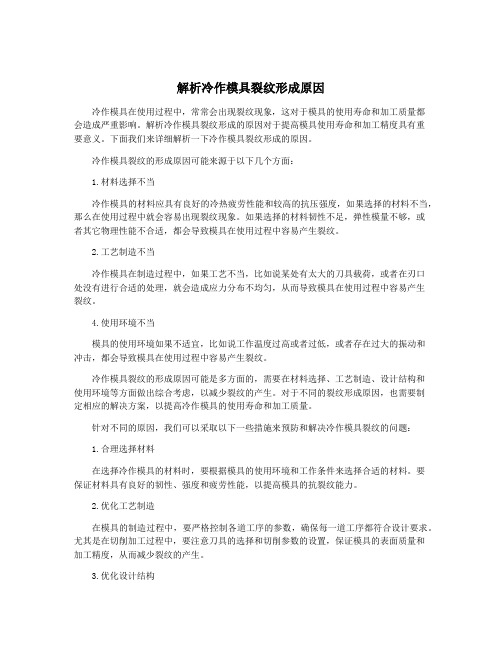
解析冷作模具裂纹形成原因冷作模具在使用过程中,常常会出现裂纹现象,这对于模具的使用寿命和加工质量都会造成严重影响。
解析冷作模具裂纹形成的原因对于提高模具使用寿命和加工精度具有重要意义。
下面我们来详细解析一下冷作模具裂纹形成的原因。
冷作模具裂纹的形成原因可能来源于以下几个方面:1.材料选择不当冷作模具的材料应具有良好的冷热疲劳性能和较高的抗压强度,如果选择的材料不当,那么在使用过程中就会容易出现裂纹现象。
如果选择的材料韧性不足,弹性模量不够,或者其它物理性能不合适,都会导致模具在使用过程中容易产生裂纹。
2.工艺制造不当冷作模具在制造过程中,如果工艺不当,比如说某处有太大的刀具载荷,或者在刃口处没有进行合适的处理,就会造成应力分布不均匀,从而导致模具在使用过程中容易产生裂纹。
4.使用环境不当模具的使用环境如果不适宜,比如说工作温度过高或者过低,或者存在过大的振动和冲击,都会导致模具在使用过程中容易产生裂纹。
冷作模具裂纹的形成原因可能是多方面的,需要在材料选择、工艺制造、设计结构和使用环境等方面做出综合考虑,以减少裂纹的产生。
对于不同的裂纹形成原因,也需要制定相应的解决方案,以提高冷作模具的使用寿命和加工质量。
针对不同的原因,我们可以采取以下一些措施来预防和解决冷作模具裂纹的问题:1.合理选择材料在选择冷作模具的材料时,要根据模具的使用环境和工作条件来选择合适的材料。
要保证材料具有良好的韧性、强度和疲劳性能,以提高模具的抗裂纹能力。
2.优化工艺制造在模具的制造过程中,要严格控制各道工序的参数,确保每一道工序都符合设计要求。
尤其是在切削加工过程中,要注意刀具的选择和切削参数的设置,保证模具的表面质量和加工精度,从而减少裂纹的产生。
3.优化设计结构在模具的设计过程中,要注意减少应力集中部位,避免过大的锐角和槽口,设计合理的强化结构,从而提高模具的抗裂纹能力。
冷作模具失效分析及优化对策
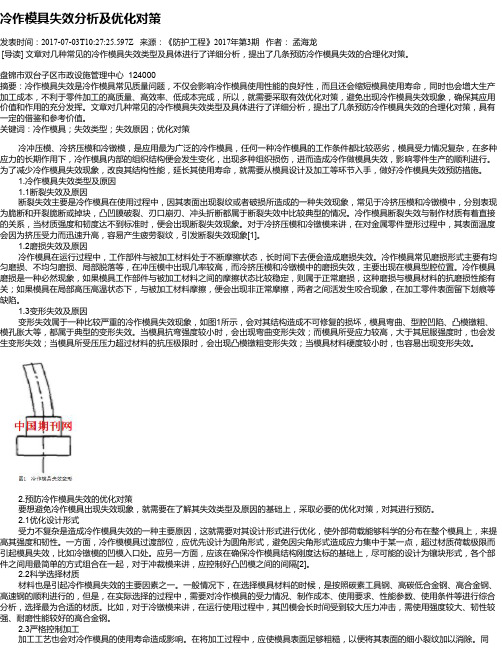
冷作模具失效分析及优化对策发表时间:2017-07-03T10:27:25.597Z 来源:《防护工程》2017年第3期作者:孟海龙[导读] 文章对几种常见的冷作模具失效类型及具体进行了详细分析,提出了几条预防冷作模具失效的合理化对策。
盘锦市双台子区市政设施管理中心 124000摘要:冷作模具失效是冷作模具常见质量问题,不仅会影响冷作模具使用性能的良好性,而且还会缩短模具使用寿命,同时也会增大生产加工成本,不利于零件加工的高质量、高效率、低成本完成,所以,就需要采取有效优化对策,避免出现冷作模具失效现象,确保其应用价值和作用的充分发挥。
文章对几种常见的冷作模具失效类型及具体进行了详细分析,提出了几条预防冷作模具失效的合理化对策,具有一定的借鉴和参考价值。
关键词:冷作模具;失效类型;失效原因;优化对策冷冲压模、冷挤压模和冷镦模,是应用最为广泛的冷作模具,任何一种冷作模具的工作条件都比较恶劣,模具受力情况复杂,在多种应力的长期作用下,冷作模具内部的组织结构便会发生变化,出现多种组织损伤,进而造成冷作做模具失效,影响零件生产的顺利进行。
为了减少冷作模具失效现象,改良其结构性能,延长其使用寿命,就需要从模具设计及加工等环节入手,做好冷作模具失效预防措施。
1.冷作模具失效类型及原因1.1断裂失效及原因断裂失效主要是冷作模具在使用过程中,因其表面出现裂纹或者破损所造成的一种失效现象,常见于冷挤压模和冷镦模中,分别表现为脆断和开裂脆断或掉块,凸凹膜破裂、刃口崩刃、冲头折断都属于断裂失效中比较典型的情况。
冷作模具断裂失效与制作材质有着直接的关系,当材质强度和韧度达不到标准时,便会出现断裂失效现象。
对于冷挤压模和冷镦模来讲,在对金属零件塑形过程中,其表面温度会因为挤压受力而迅速升高,容易产生疲劳裂纹,引发断裂失效现象[1]。
1.2磨损失效及原因冷作模具在运行过程中,工作部件与被加工材料处于不断摩擦状态,长时间下去便会造成磨损失效。
解析冷作模具裂纹形成原因
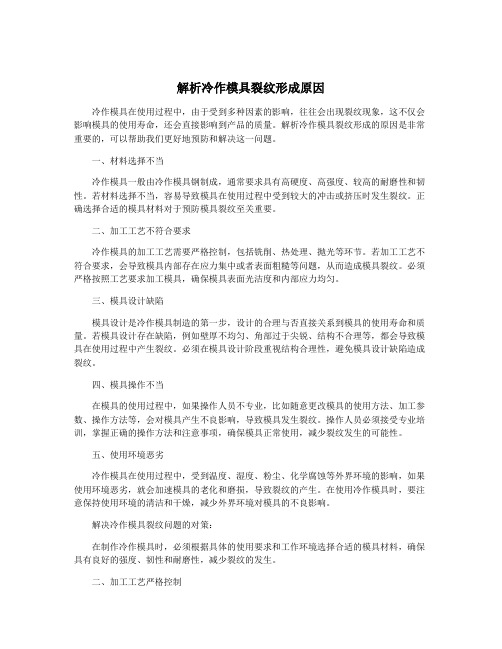
解析冷作模具裂纹形成原因冷作模具在使用过程中,由于受到多种因素的影响,往往会出现裂纹现象,这不仅会影响模具的使用寿命,还会直接影响到产品的质量。
解析冷作模具裂纹形成的原因是非常重要的,可以帮助我们更好地预防和解决这一问题。
一、材料选择不当冷作模具一般由冷作模具钢制成,通常要求具有高硬度、高强度、较高的耐磨性和韧性。
若材料选择不当,容易导致模具在使用过程中受到较大的冲击或挤压时发生裂纹。
正确选择合适的模具材料对于预防模具裂纹至关重要。
二、加工工艺不符合要求冷作模具的加工工艺需要严格控制,包括铣削、热处理、抛光等环节。
若加工工艺不符合要求,会导致模具内部存在应力集中或者表面粗糙等问题,从而造成模具裂纹。
必须严格按照工艺要求加工模具,确保模具表面光洁度和内部应力均匀。
三、模具设计缺陷模具设计是冷作模具制造的第一步,设计的合理与否直接关系到模具的使用寿命和质量。
若模具设计存在缺陷,例如壁厚不均匀、角部过于尖锐、结构不合理等,都会导致模具在使用过程中产生裂纹。
必须在模具设计阶段重视结构合理性,避免模具设计缺陷造成裂纹。
四、模具操作不当在模具的使用过程中,如果操作人员不专业,比如随意更改模具的使用方法、加工参数、操作方法等,会对模具产生不良影响,导致模具发生裂纹。
操作人员必须接受专业培训,掌握正确的操作方法和注意事项,确保模具正常使用,减少裂纹发生的可能性。
五、使用环境恶劣冷作模具在使用过程中,受到温度、湿度、粉尘、化学腐蚀等外界环境的影响,如果使用环境恶劣,就会加速模具的老化和磨损,导致裂纹的产生。
在使用冷作模具时,要注意保持使用环境的清洁和干燥,减少外界环境对模具的不良影响。
解决冷作模具裂纹问题的对策:在制作冷作模具时,必须根据具体的使用要求和工作环境选择合适的模具材料,确保具有良好的强度、韧性和耐磨性,减少裂纹的发生。
二、加工工艺严格控制严格按照工艺要求进行模具加工,包括铣削、热处理、抛光等环节,确保模具的表面光洁度和内部应力均匀分布,减少裂纹形成的可能性。
模具失效与防护前言及第一章

研究现状与问题
01
国内外学者对模具失效 进行了大量研究,但失 效原因复杂多样,仍存
在许多问题。
02
目前研究主要集中在单 一因素对模具失效的影 响,缺乏对多因素耦合
作用的深入研究。
03
模具材料、热处理、加 工工艺等对模具失效的 影响机制尚不明确,需
04
模具失效与防护案例分析
案例一:注塑模具失效分析
总结词
注塑模具在使用过程中,由于多种因素可能导致其失效,如温度控制不当、材料选择不当、模具设计不合理等。
详细描述
注塑模具失效通常表现为模具表面损伤、尺寸精度下降、塑料制品质量不稳定等。分析发现,模具温度过高或过 低、塑料材料收缩率不稳定、模具设计不合理等是主要原因。通过优化温度控制、选择合适的塑料材料和改进模 具设计,可以有效提高注塑模具的使用寿命。
集中等。
模具制造工艺问题
如热处理不当、加工精度不足等 ,影响模具的机械性能和使用寿
命。
使用和维护不当
如超负荷使用、润滑不足、清洁 维护不到位等,加速模具磨损和
损坏。
模具失效预防措施
合理选材和设计
根据使用条件和加工要求,选择合适 的模具材料和设计结构,以提高模具 的机械性能和使用寿命。
加强使用和维护保养
案例二:冲压模具失效分析
总结词
冲压模具在冲压过程中,由于反复承受高强度压力,容易出现磨损、开裂等现象,导致 其失效。
详细描述
冲压模具失效主要表现为刃口磨损、凸模断裂、凹模开裂等。分析发现,模具材料选择 不当、热处理工艺不合理、润滑剂使用不当等是主要原因。通过改进模具材料和热处理 工艺、合理使用润滑剂等措施,可以有效提高冲压模具的耐磨性和抗疲劳性能,延长其
冷作模具的常见失效形式及热处理质量检验
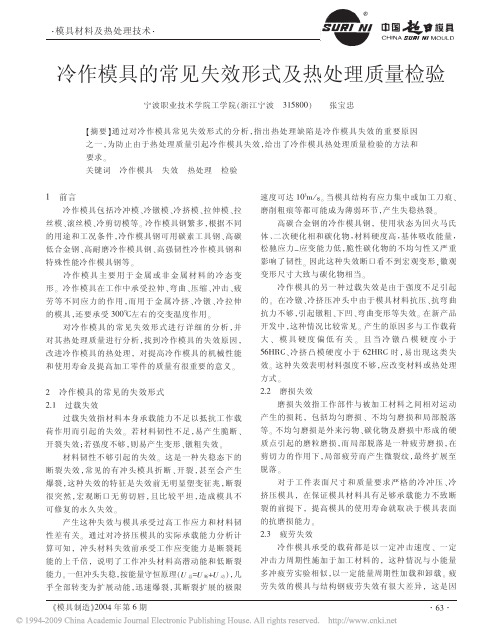
材料韧性不够引起的失效) 这是一种失稳态下的 断裂失效(常见的有冲头模具折断*开裂(甚至会产生 爆裂(这种失效的特征是失效前无明显塑变征兆(断裂 很突然(宏观断口无剪切唇(且比较平坦(造成模具不 可修复的永久失效)
产生这种失效与模具承受过高工作应力和材料韧 性差有关) 通过对冷挤压模具的实际承载能力分析计 算可知( 冲头材料失效前承受工作应变能力是断裂耗 能的上千倍( 说明了工作冲头材料高潜动能和低断裂 能力) 一但冲头失稳(按能量守恒原理$! 总+! 断,! 动%(几 乎全部转变为扩展动能(迅速爆裂(其断裂扩展的极限
冷作模具承受的载荷都是以一定冲击速度* 一定 冲击力周期性施加于加工材料的( 这种情况与小能量 多冲疲劳实验相似(以一定能量周期性加载和卸载) 疲 劳失效的模具与结构钢疲劳失效有很大差异( 这是因
!!"!
!!模具材料及热处理技术!
为脆性材料疲劳裂纹的产生周期占总寿命的绝大部 分$很多情况下产生与扩展无明显界限$似乎不存在稳 态扩展阶段% 疲劳失效实际上是应力应变下微裂纹的 产生过程$当产生约 "%&’’ 尺寸微裂纹$即可能发生瞬 间断裂% 实际应用中疲劳产生源有很多$其断口形状与 脆断极相似%
正火&退火零件的硬度用布氏试验机检查% 淬火工 件用洛氏硬度法检查% 表面硬化工件常用维氏硬度检 验法检查% 大型零件硬度测试$可用锤击式布氏&肖氏 或里氏硬度测试法检查%
冷作模具钢材主要磨损及失效

冷作模具钢材主要磨损及失效1.冷作模具的过载失效过载失效指模具钢材本身承载能力不足以抵抗工作载荷(包括约10%的随机波动载荷)作用引起的失效,包括模具钢材韧度不足和强度不足两类失效。
对模具钢材韧度不足出现的脆断失效应予以重视。
⑴模具钢材韧度不足失效。
此类失效前无宏观征兆和断裂突发性,是冷作模具失效中最危险的事故,此类失效增出现过人身事故,给生产安全和经济建设造成很大的损失。
这种失稳态下的断裂失效在冷挤压和冷镦模具中容易出现,如冲头折断、开裂、甚至发生爆裂,其特征是失效产生前无明显塑性变形,宏观断口无剪切唇,且比较平坦,造成模具不可修复的永久失效。
这种失效与模具钢材韧度不足、承受过高应力有关。
对冷挤压模具实际承载能力分析计算可知,冲头失效前承受的工作应变能力是模具钢材断裂消耗能的上千倍,说明了工作时冲头承受高潜在动能和低的断裂抗力。
根据能量守恒原理,冲头断裂势能大部分转变为扩展动能,其扩展的极限速度可达103m/s。
当模具结构存在应力集中,如六方冷镦冲头尾部过渡区r≤1mm时,应力集中系数Kt=2;冷挤压冲头台阶处r=3mm时,Kt=1.3;甚至机械加工刀痕、磨削粗痕迹等均可成为薄弱环节,产生失稳断裂。
高碳、高合金的冷作模具钢,使用状态为回火马氏体和二次析出相,含有较多一次剩余碳化物,材料硬度高,基体吸收能量、松弛应力——应变的能力低,一次碳化物的不均匀性分布又严重降低了材料韧度。
因此,这类失效断口看不到宏观变形,微观变形的尺寸大致与碳化物间距相当。
⑵强度不足失效。
在冷镦、冷挤压冲头中,材料抗压、弯曲抗力不足,易出现镦头下凹、弯曲变形失效。
在新产品开发中容易产生此类失效,这与工作载荷过大,模具硬度偏低有关。
实际经验表明,黑色金属冷镦冲头硬度小于HRC56、冷挤压冲头硬度小于HRC62时易出现这类失效,同时说明材料强度不足,塑性有余,有韧度潜力可以发挥。
解决此类模具早期失效的经验方法是脆断失效减硬度,变形失效增硬度。
谈模具失效的原因及其预防措施
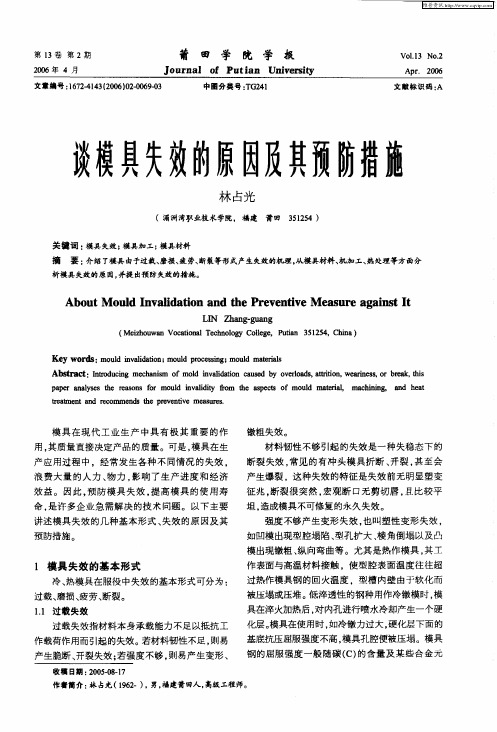
维普资讯
第 l 3卷 第 2期
2o O 6年 4 月
莆 田 学 院 学 报
J u n l f u i n nv ri o r a o P ta U ies y t
中圈分类号 : G 4 T 21
VO |3 l No 2 l . Ap . 2 0 r 06
析模具失效的原因, 并提出预防失效的措施。
Ab u o l n a i a i n a d t e P e e t e M e s r g i  ̄ I o tM u d I v l to n h r v n v a u e a a n d i t
L N Zh n -u n I a gg a g
模具在现 代工业生产 中具有极 其重要 的作 用, 其质量直接决定产品的质量。可是 , 模具在生 产应用过程中 ,经常发生各种不 同情况 的失效 。 浪费大量 的入力 、 力 , 物 影响了生产进度和 经济
效 益 。 因此 , 防 模 具 失 效 。 高 模 具 的使 用 寿 预 提
镦 粗失 效 。
( i owa o a oa T cn lg ol e P t n 5 24 h a) Me h u n V ct nl eh oo y C l g, u a 3 15 ,C i z i e i n
Ke r s mo l vl ao ; ud po es g mo l tr l y wo d : ud i ai t n mo l rcsi ; udmaeis n di n a
解析冷作模具裂纹形成原因
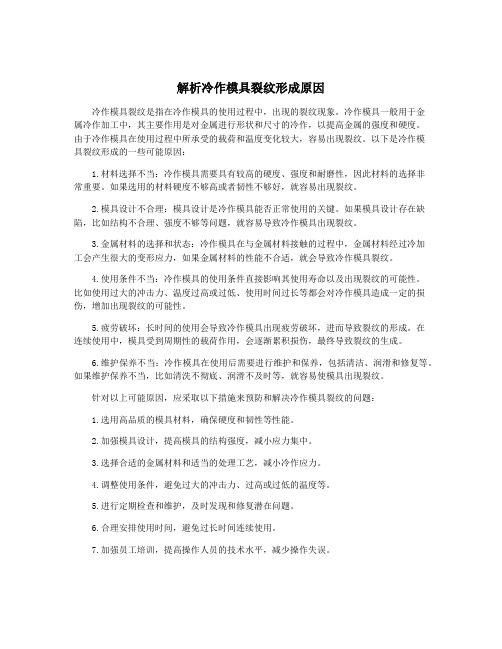
解析冷作模具裂纹形成原因冷作模具裂纹是指在冷作模具的使用过程中,出现的裂纹现象。
冷作模具一般用于金属冷作加工中,其主要作用是对金属进行形状和尺寸的冷作,以提高金属的强度和硬度。
由于冷作模具在使用过程中所承受的载荷和温度变化较大,容易出现裂纹。
以下是冷作模具裂纹形成的一些可能原因:1.材料选择不当:冷作模具需要具有较高的硬度、强度和耐磨性,因此材料的选择非常重要。
如果选用的材料硬度不够高或者韧性不够好,就容易出现裂纹。
2.模具设计不合理:模具设计是冷作模具能否正常使用的关键。
如果模具设计存在缺陷,比如结构不合理、强度不够等问题,就容易导致冷作模具出现裂纹。
3.金属材料的选择和状态:冷作模具在与金属材料接触的过程中,金属材料经过冷加工会产生很大的变形应力,如果金属材料的性能不合适,就会导致冷作模具裂纹。
4.使用条件不当:冷作模具的使用条件直接影响其使用寿命以及出现裂纹的可能性。
比如使用过大的冲击力、温度过高或过低、使用时间过长等都会对冷作模具造成一定的损伤,增加出现裂纹的可能性。
5.疲劳破坏:长时间的使用会导致冷作模具出现疲劳破坏,进而导致裂纹的形成。
在连续使用中,模具受到周期性的载荷作用,会逐渐累积损伤,最终导致裂纹的生成。
6.维护保养不当:冷作模具在使用后需要进行维护和保养,包括清洁、润滑和修复等。
如果维护保养不当,比如清洗不彻底、润滑不及时等,就容易使模具出现裂纹。
针对以上可能原因,应采取以下措施来预防和解决冷作模具裂纹的问题:1.选用高品质的模具材料,确保硬度和韧性等性能。
2.加强模具设计,提高模具的结构强度,减小应力集中。
3.选择合适的金属材料和适当的处理工艺,减小冷作应力。
4.调整使用条件,避免过大的冲击力、过高或过低的温度等。
5.进行定期检查和维护,及时发现和修复潜在问题。
6.合理安排使用时间,避免过长时间连续使用。
7.加强员工培训,提高操作人员的技术水平,减少操作失误。
冷作模具裂纹的形成原因复杂多样,需要结合具体情况进行综合分析和解决。
冷作模具的工作条件与失效形式 (1)

︼
5.几种典型冷作模具的工作条件与失效形式。
成功不是将来才有的,而是从决定去做的那一刻起,持续累积而成。
︻
模具
︼
冷作模具
热作模具
塑料模具
其他模具
成功不是将来才有的,而是从决定去做的那一刻起,持续累积而成。
︻
模具钢
模具材 料
其它材 料
︼
冷作模 具钢 热作模 具钢 塑料模 具钢 铸铁
有色金 属 及其合 金
硬质合 金
非金属 材料
成功不是将来才有的,而是从决定去做的那一刻起,持续累积而成。
︻
冷作模具
冷冲裁模 冷挤压模
拉深模
︼
冷镦模
冷弯曲模
成功不是将来才有的,而是从决定去做的那一刻起,持续累积而成。
︻
1、按工作条件模具可分为哪几类? 指在冷态下完成对金属或非金属材料塑性变形加工的 工具,包括:冷冲裁模具、冷拉深模具、弯曲模具、冷镦 模具、冷挤压模具、拉丝模具等,完成的工序有冲孔、落 料、挤压、冷镦、拉深、滚丝、拉丝、弯曲、成形等。
︻
1.分析图1-2所示的调整垫片的冷冲裁模具工作 条件与失效形式。
2.分析图1-4所示的冰箱门外壳的冷拉伸模具工 作条件与失效形式。
︼
成功不是将来才有的,而是从决定去做的那一刻起,持续累积而成。
︻
1.模具失效的定义及常见的失效形式。
2.产生模具失效的原因及预防措施。
3.模具寿命及其影响因素。
4.冷作模具的失效形式。
成功不是将来才有的,而是从决定去做的那一刻起,持续累积而成。
︻
2、什么叫模具失效?它可以分成几类?
模具因损伤积累至一定程度导致模具损坏而无法继续服役的现象 正常失效是指经过大量的生产使用,因摩擦而自然磨损或缓 慢地产生塑性变形及疲劳裂纹,达到正常使用寿命之后的失效属 于正常的现象。
防止模具异常的措施有哪些方法

防止模具异常的措施有哪些方法模具在工业生产中扮演着非常重要的角色,它们被广泛应用于塑料制品、金属铸造、玻璃制品等领域。
然而,模具在使用过程中往往会出现各种异常情况,例如磨损、变形、裂纹等,这些异常情况会导致产品质量下降,甚至影响生产进度。
因此,为了保证模具的正常使用,需要采取一系列的措施来预防模具异常的发生。
首先,要做好模具的日常维护保养工作。
模具在使用过程中会受到各种力的作用,容易出现磨损和变形。
因此,需要定期对模具进行检查和维护,及时发现并处理模具的异常情况。
维护工作主要包括清洁、润滑、紧固等,可以延长模具的使用寿命,减少异常情况的发生。
其次,要合理使用模具。
在生产过程中,要根据模具的设计要求和使用说明来合理使用模具,避免超负荷使用或者错误使用导致模具异常。
此外,还要注意产品的设计和材料选择,避免对模具造成过大的冲击和压力,减少模具的磨损和变形。
另外,要加强对模具的监控和检测。
在模具使用过程中,要定期对模具进行监控和检测,及时发现模具的异常情况。
可以通过观察模具的外观、测量模具的尺寸、使用仪器对模具的质量进行检测等方式来监控模具的状况,及时发现并处理异常情况。
此外,还可以通过改进模具的设计和制造工艺来预防模具异常的发生。
在模具的设计和制造过程中,可以采用先进的材料和工艺,提高模具的硬度和耐磨性,减少模具的变形和磨损。
此外,还可以优化模具的结构和工艺,减少模具的应力集中,提高模具的使用寿命。
最后,要加强对模具使用人员的培训和管理。
模具使用人员要具备一定的专业知识和技能,能够正确操作和维护模具,避免因操作不当导致模具异常。
因此,企业需要加强对模具使用人员的培训和管理,提高他们的技术水平和责任意识,减少模具异常的发生。
总之,预防模具异常的发生需要综合考虑模具的维护保养、合理使用、监控检测、设计制造和人员管理等因素。
只有通过多种措施的综合应用,才能有效预防模具异常的发生,保证模具的正常使用,提高生产效率和产品质量。
模具失效的原因及预防措施
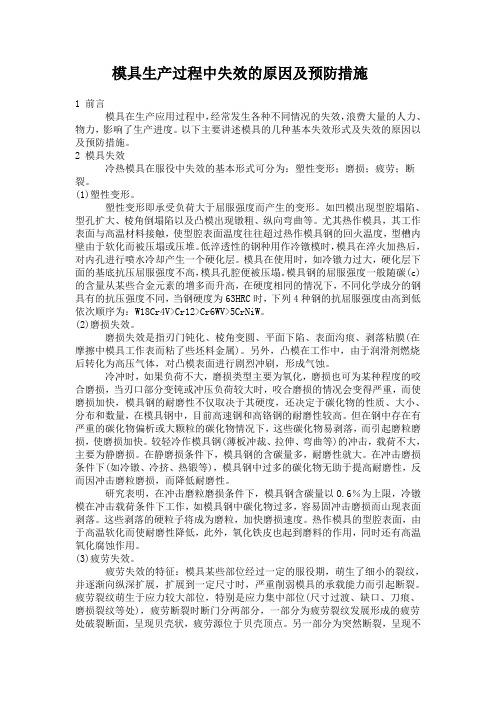
模具生产过程中失效的原因及预防措施1 前言模具在生产应用过程中,经常发生各种不同情况的失效,浪费大量的人力、物力,影响了生产进度。
以下主要讲述模具的几种基本失效形式及失效的原因以及预防措施。
2 模具失效冷热模具在服役中失效的基本形式可分为:塑性变形;磨损;疲劳;断裂。
(1)塑性变形。
塑性变形即承受负荷大于屈服强度而产生的变形。
如凹模出现型腔塌陷、型孔扩大、棱角倒塌陷以及凸模出现镦粗、纵向弯曲等。
尤其热作模具,其工作表面与高温材料接触,使型腔表面温度往往超过热作模具钢的回火温度,型槽内壁由于软化而被压塌或压堆。
低淬透性的钢种用作冷镦模时,模具在淬火加热后,对内孔进行喷水冷却产生一个硬化层。
模具在使用时,如冷镦力过大,硬化层下面的基底抗压屈服强度不高,模具孔腔便被压塌。
模具钢的屈服强度一般随碳(c)的含量从某些合金元素的增多而升高,在硬度相同的情况下,不同化学成分的钢具有的抗压强度不同,当钢硬度为63HRC时,下列4种钢的抗屈服强度由高到低依次顺序为:W18Cr4V>Cr12>Cr6WV>5CrNiW。
(2)磨损失效。
磨损失效是指刃门钝化、棱角变圆、平面下陷、表面沟痕、剥落粘膜(在摩擦中模具工作表而粘了些坯料金属)。
另外,凸模在工作中,由于润滑剂燃烧后转化为高压气体,对凸模表面进行剧烈冲刷,形成气蚀。
冷冲时,如果负荷不大,磨损类型主要为氧化,磨损也可为某种程度的咬合磨损,当刃口部分变钝或冲压负荷较大时,咬合磨损的情况会变得严重,而使磨损加快,模具钢的耐磨性不仅取决于其硬度,还决定于碳化物的性质、大小、分布和数量,在模具钢中,目前高速钢和高铬钢的耐磨性较高。
但在钢中存在有严重的碳化物偏析或大颗粒的碳化物情况下,这些碳化物易剥落,而引起磨粒磨损,使磨损加快。
较轻冷作模具钢(薄板冲裁、拉伸、弯曲等)的冲击,载荷不大,主要为静磨损。
在静磨损条件下,模具钢的含碳量多,耐磨性就大。
在冲击磨损条件下(如冷镦、冷挤、热锻等),模具钢中过多的碳化物无助于提高耐磨性,反而因冲击磨粒磨损,而降低耐磨性。
冷挤压模的工作条件及失效形式
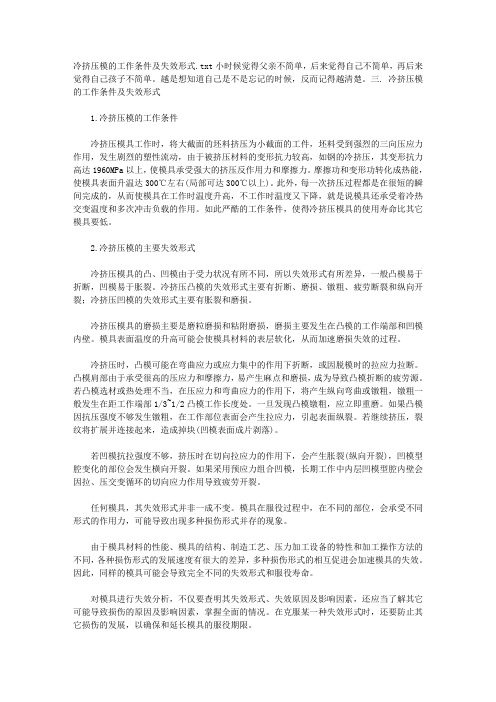
冷挤压模的工作条件及失效形式.txt小时候觉得父亲不简单,后来觉得自己不简单,再后来觉得自己孩子不简单。
越是想知道自己是不是忘记的时候,反而记得越清楚。
三. 冷挤压模的工作条件及失效形式1.冷挤压模的工作条件冷挤压模具工作时,将大截面的坯料挤压为小截面的工件,坯料受到强烈的三向压应力作用,发生剧烈的塑性流动,由于被挤压材料的变形抗力较高,如钢的冷挤压,其变形抗力高达1960MPa以上,使模具承受强大的挤压反作用力和摩擦力。
摩擦功和变形功转化成热能,使模具表面升温达300℃左右(局部可达300℃以上)。
此外,每一次挤压过程都是在很短的瞬间完成的,从而使模具在工作时温度升高,不工作时温度又下降,就是说模具还承受着冷热交变温度和多次冲击负载的作用。
如此严酷的工作条件,使得冷挤压模具的使用寿命比其它模具要低。
2.冷挤压模的主要失效形式冷挤压模具的凸、凹模由于受力状况有所不同,所以失效形式有所差异,一般凸模易于折断,凹模易于胀裂。
冷挤压凸模的失效形式主要有折断、磨损、镦粗、疲劳断裂和纵向开裂;冷挤压凹模的失效形式主要有胀裂和磨损。
冷挤压模具的磨损主要是磨粒磨损和粘附磨损,磨损主要发生在凸模的工作端部和凹模内壁。
模具表面温度的升高可能会使模具材料的表层软化,从而加速磨损失效的过程。
冷挤压时,凸模可能在弯曲应力或应力集中的作用下折断,或因脱模时的拉应力拉断。
凸模肩部由于承受很高的压应力和摩擦力,易产生麻点和磨损,成为导致凸模折断的疲劳源。
若凸模选材或热处理不当,在压应力和弯曲应力的作用下,将产生纵向弯曲或镦粗,镦粗一般发生在距工作端部1/3~1/2凸模工作长度处。
一旦发现凸模镦粗,应立即重磨。
如果凸模因抗压强度不够发生镦粗,在工作部位表面会产生拉应力,引起表面纵裂。
若继续挤压,裂纹将扩展并连接起来,造成掉块(凹模表面成片剥落)。
若凹模抗拉强度不够,挤压时在切向拉应力的作用下,会产生胀裂(纵向开裂),凹模型腔变化的部位会发生横向开裂。
冷作模具失效机理

冷作模具失效机理磨粒磨损当被加工材料很硬或者其中含有很硬的氧化物或碳化物颗粒时,这类磨损现象非常明显。
这些硬质颗粒擦伤模具表面。
当被加工材料是已热处理,陶瓷材料和木材时,明显出现磨粒磨损现象。
工具钢抵抗磨粒磨损所需具备的主要性能是:1 高硬度2 大量的碳化物3 碳化物的硬度很高4 大的碳化物颗粒粘着磨损引起粘着磨损的原因是模具表面与被加工材料间的局部点焊现象。
模具与被加工材料间的相对运动将引起焊点的再次撕开以及模具表面出现小碎片的脱落。
像这样持续的模具材料的损失最终导致了模具的明显磨损。
被撕落的模具表面碎片也会粘着在被加工材料上,其同样会造成模具表面的磨粒磨损。
粘着磨损也是崩角的起因。
在模具早期阶段的粘着磨损会逐渐被疲劳机理所替代,微裂纹萌生并且开始向深层扩展,最终会触发材料的大片剥落(崩角),甚至会导致一场灾难性的失效。
粘着磨损常在软而粘的金属被加工材料上出现,如铝、铜、不锈钢和低碳钢。
粘着磨损可以尝试让微焊及撕裂机理的困难发生而减少,工具钢抵抗粘着磨损所需具备的主要性能是:1 高硬度2 在模具与被加工材料间低的摩擦系数3 高延展性混合磨损应该注意:并不是所有的金属加工材料都只会引起纯粹的磨粒磨损或纯粹的粘着磨损。
有些材料会产生部分磨粒磨损和部分粘着磨损,这类磨损称之为混合磨损。
崩角崩角大部分是在模具早期使用时发生的现象。
是低周期疲劳机理中的一种。
在模具工作表面首先出现一些小裂纹,随着裂纹的逐渐长大最终导致材料成片崩出。
模具要获得好的抗崩角性能,最主要的是增加裂纹起始及扩展的阻力。
高延展性是工具钢获得优良抗崩角效果的性能要求。
塑性变形当工具钢所受应力超过其屈服强度时会发生塑性变形。
塑性变形会对模具工作面引起损害或使其形状发生变化。
高硬度是工具钢抗塑性变形的一种主要性能。
注意:在选择工具硬度时必须适当考虑其韧性要求。
破裂破裂时一种自发的失效机理,其通常会导致模具的更换。
裂纹不稳定的扩展是引起这类失效的原因。
冷挤压模具的失效分析

内容摘要自从我国加入WTO之后,模具产品已提升到技术装备总体水平至关重要的一个环节,其中,尤其是冷挤压模具,它是实现少、无切削加工的重要工艺装备,在现代生产加工中日益得到广泛的应用。
但在冷挤压加工时,常常遇到一些妨碍正常投产的重要问题,就是模具受到损坏,最终导致模具失效。
本文结合工厂实际的生产状况,对冷挤模具应用,冷挤模具的失效形式,以及对所产生的各种失效形式进行分析,而后找出解决的办法,提高生产效益,减少成本,使冷挤压得到广泛的应用。
关键词:冷挤压加工冷挤模具失效目录引言 (1)一、挤压的实质及方法分类 (2)(一)冷挤压加工的实质 (2)(二)冷挤压的方法分类 (2)二、冷挤压的特点 (2)(一)冷挤压的优点 (3)(二)冷挤压的缺点 (4)三、冷挤压的实现形式 (5)(一)冷挤压模具的构造及特点 (5)(二)对冷挤压模具的基本要求 (6)四、冷挤压模具的失效性 (6)(一)模具失效出现的过程 (6)(二)模具失效的形式 (7)五、冷挤模具的工作条件 (14)六、模具损坏的各种具体因素 (14)(一)模具材料的影响 (14)(二)模具结构的影响 (15)(三)模具制造工艺的影响 (16)七、模具工作条件和使用维护的影响 (17)(一)被加工材料的影响 (17)(二)润滑条件的影响 (18)参考文献 (19)致谢 (20)冷挤压模具的失效性分析冷挤压加工的发展在初期是极其缓慢的,长期以来一直局限于铅和锡等几种较软的金属材料。
18世纪末,法国人首先成功地冷挤压出铅棒。
直到19世纪20世纪初,才开始应用于锌,锡,纯铜,无氧铜及黄铜等,如冷挤压生产锡制牙膏管,英国于1886年开始运用于冷挤压加工,某一工厂先从加工软金属开始,后来逐步实现冷挤压比较坚硬的有色金属,如锌,铝,铜极其合金。
1903年美国运用冷挤压制成薄壁黄铜管,随后,又采用预制成杯形坯料,然后再用正挤压的方法,成功地制成深孔杯形件,第一次世界大战期间,美国军火商采用这种挤压方法大批量生产黄铜弹壳,第一次世界大战后,德国用冷挤压方法可成批生产纯铝和纯锌电容器外壳等各种有色金属器件。
- 1、下载文档前请自行甄别文档内容的完整性,平台不提供额外的编辑、内容补充、找答案等附加服务。
- 2、"仅部分预览"的文档,不可在线预览部分如存在完整性等问题,可反馈申请退款(可完整预览的文档不适用该条件!)。
- 3、如文档侵犯您的权益,请联系客服反馈,我们会尽快为您处理(人工客服工作时间:9:00-18:30)。
冷作模具的失效和预防
冷作模具质量的好坏将直接影响其制品的质量, 模具的寿命又决定着零件的生产成本及经济效益,而影响冷作模具的因素很多。
所以, 冷作模具的失效形式也是各种各样。
根据实际生产经验,针对冷作模具的几种基本失效形式,提出有效的预防措施。
对于早期失效的模具,主要表现有如下三种失效类型:⑴断裂失效:包括塑性断裂失效、疲劳断裂失效、蠕变断裂失效、低应力脆性失效等。
⑵变形失效:包括过量的弹性和塑性变形失效。
⑶表面损坏失效:包括磨损失效、腐蚀失效、表面疲劳(点蚀或剥落)失效等。
苛刻的工作条件,使得冷作模具的使用寿命比其它模具要短许多。
因此,为了延长冷作模具的使用寿命,降低成本,提高经济效益,需要查明模具失效的根本原因,并采取有效的措施加以解决。
1.断裂。
这是冷作模具最常见的一种损坏形式,主要是因为载荷超过模具材料的强度极限或模具产生应力集中所造成的。
例如:凸模折断、凹模及紧固圈开裂、顶杆断裂、镶块疲劳开裂等。
2.变形。
由于冷作成形时作用的工作模具上的载荷非常大,直接承受压力作用的工作模具,将会产生一定的弹性变形或塑性变形,使得模具无法使用而报废。
例如:凹模型腔的弹性膨胀,凸模的镦粗、弯曲,顶料杆的镦粗,垫块的中心压塌等等变形。
3.磨损。
由于毛坯润滑、软化处理、模具热处理强度等方面的原因,使得冷作模具与其它模具一样,常发生型腔表面早期磨损损环失效。
如韧带工作面表面粘金属、点蚀、剥落或尺寸急剧变化等。
当模具零件产生上述这些缺陷时,就不能成形出合格的紧固件产品,势必会影响企业的生产计划。
预防措施
为了防止模具早期失效,有效的延长模具的使用寿命,主要从以下几方面采取相应的预防措施。
一、模具材料。
由于冷作模具承受单位挤压力较大,所以应选择强度高、韧性好、耐磨性好的高性能模具材料;由于凸模的工作条件比凹模更易受偏心力的作用,所以,凸模材料的耐磨性应该选得比凹模材料更高些。
二、热处理。
模具热处理包括:冷作模具胚料锻造后的及时回火以细化晶粒,粗加工后的回火以消除应力,电火花、线切割后的去应力低温回火。
经验表明,直径≤80mm的模具,宜采用棒料直接机加工,无需再锻造,因为锻造不当反而会造成过烧、粗晶、偏析等缺陷。
模具淬火和回火时还应注意加热速度、保温时间、淬火温度、冷却速度、回火次数、表面硬度等。
模具淬火加热时温度过高,容易造成模具的过热、过烧,冲击韧性下降,导致早期断裂。
如果淬火温度过低,会降低模具的硬度、耐磨性及疲劳抗力,容易造成模具的塑性变形、磨损失效。
淬火加热时还要注意采取保护措施,防止表面氧化和脱碳,脱碳将造成淬火软点和软区,降低模具的耐磨性、疲劳强度,影响其使用寿命。
淬火冷却速度过快和游温过低,模具容易产生淬火裂纹。
如果回火温度太低,而且不够充分,将无法消除淬火过程中的残余应力,使模具的韧性降低,容易发生早期断裂。
三、模具设计冷作模具的结构必须有足够的强度、刚度、可靠性和良好的的导向性,但模具的结构形式不合理将会直接影响模具的使用寿命。
模具工作部分应设计为足够大的圆角半径,避免尖角过渡产生应力集中,韧带的宽度应根据金属流动情况合理设计,以最大限度地减小摩擦力,一般在1.5-3.5之间。
四、模具加工。
在摸具切削加工过程中,应采取以下措施;提高表面粗糙度,磨削形成的微裂纹痕迹,过渡部分要平滑,不能有机加工刀痕及微小缺陷,防止使用过程中出现应力集中导致裂纹产生。
资料整理——东莞市美坚扣件(螺丝)有限公司。