pu发泡工艺
PU发泡工艺介绍

A 5
聚氨酯分类
根据发泡方法分类,可以分为块泡,模塑和 喷涂聚氨酯泡沫:
分别应用: ➢ 块泡:复合泡沫、海绵。 ➢ 模塑:座椅,扶手,头枕。 ➢ 喷涂:冷库防水保温。
A 6
聚氨酯泡沫形成
➢反应方程式
A 7
聚氨酯泡沫形成
混合:
ISO与 POL混合,此过程在混合头上完成。
注释:以上是两个主要的反应,但实际还存在超过10个的副反应 存在,因此关键是控制好反应的平衡以获得所需要的结果。
A 19
聚氨酯化学:A料跟B料之比
➢ 根据A料与B料反应时的当量关系,可以计算出100克A料 需要多少克B料。
➢ 发泡指数INDEX:ISO实际用量/ISO理论用量*100; ➢ INDEX范围一般为60—110之间,INDEX较高时,产品比
乳白:
➢ 混合后泡沫并不是马上起发,而是经过一定时间的流动后, 泡沫才开始变白并开始迅速起发。
➢ 混合结束到起发(泡沫上升)之间的时间就是乳白时间。 ➢ 乳白时间越长则泡沫的流动性越好。 ➢ 乳白时间长有利于原料在模具中分布。
A 8
聚氨酯泡沫形成
上升:
涉及到泡沫填充能力和熟化速度。
拉丝:
涉及泡沫的凝胶程度。
氢氧化铝 ➢ 防老剂 ➢ 链增长剂:三乙醇胺(我们使用的) ➢ 颜料 ➢ 脱模剂
A 11
聚氨酯原材料-ISO部分
➢ TDI:甲苯二异腈酸酯
➢ MDI:多亚甲基多苯基多异腈酸酯
A 12
聚氨酯原材料-ISO部分
TDI(甲苯二异氰酸酯):主要有2,4-和2, 6-异构体。工业上主要有三种产品, T100,T80/20,T65/35
pu发泡工艺

发泡基本知识一、聚氨酯泡沫塑料的基本配方及各组分的作用原料名称白料主要作用聚醚、聚酯或其它多元醇主要反应原料水链增长剂、同时也是发生CO气泡原料来源2催化剂(胺或有机锡)催化发泡及凝胶反应泡沫稳定剂使泡沫稳定、控制孔的大小及结构阻燃剂提高阻燃性防老剂抗老化链增长剂改善和调节聚氨酯的性能发泡剂汽化后作为气泡来源并移去反应热,避免泡沫中心因高温而产生“烧焦”颜料制造色彩鲜艳的制品黑料多异氰酸酯主要反应原料二、目前常用发泡料的种类发泡料的种类划分主要是针对白料而言。
目前,白料主要有全氟系列、141b系列及环(/异)戊烷系列,历史上还曾经使用过减氟系列。
这些种类的划分是按照聚醚中混入的发泡剂的特性来分类的。
全氟系列对大气层的破坏最为严重,而环/异戊烷及环戊烷对环境的破坏几乎为零。
根据蒙特利尔协议,到2005年将全面停止全氟、减氟、141b的使用。
三、白料的预混目前使用的白料以前为自配,现改为组合料,由供应商直接提供。
组合料的预混流程如下:环戊烷组合料静态混合器过缸备用环异戊烷发泡剂预混的控制关键:温度、搅拌时间、配比环戊烷/组合料=11-14/100 ≥25min 22±5℃四、手工检测检测的目的是为了检测所配制的白料是否合格。
每缸必检并要求记录。
检测的内容包括:乳白时间、凝胶时间、失粘时间、密度及泡沫的外观。
具体操作方法:分别取一定量的黑白料并调节到要求的温度,按照要求的比例在台钻上搅拌一定的时间,用秒表记录三个反应时间,用排水法测试自由泡芯部密度。
参数: (黑料/白料) 25±2℃ 10s 12±2s/68±6s/95±20s 25±1 Kg/m3五、常见问题及处理1、反应时间太慢原因:组合料催化剂不够;处理:加大催化剂的用量;料温偏低;提高料温;黑料加多;使用合理比例;环境温度太低;适当控制环温;2、反应时间太快原因:组合料催化剂过多;处理:减少催化剂的用量;料温偏高;降低料温;黑料过少;使用合理比例;环境温度太高;适当控制环温;3、泡沫发不起原因:组合料出现问题;处理:停止使用;未加发泡剂;按照比例添加;未搅拌;按照规定时间搅拌均匀;4、泡孔粗大原因:组合料出现问题;处理:停止使用;六、安全注意事项环戊烷属于碳氢化合物,沸点49℃,是一种无色透明液体,不溶于水,溶于有机溶剂,蒸气比空气重,是一级易燃液体,闪点是-25℃,在空气中爆炸极限是~%(占空气中的体积的百分数),遇明火易爆炸。
聚氨酯发泡生产工艺

聚氨酯发泡生产工艺
聚氨酯发泡是一种广泛应用于建筑、汽车、航空航天、电子、家具等行业的发泡材料,其生产工艺大致可分为原材料准备、混合反应、模具注射和固化四个步骤。
首先,进行原材料准备。
聚氨酯发泡生产所需的原材料主要有聚醚、聚酯、催化剂、气体发生剂等。
这些原材料需要严格按照配比准备,并且保持干燥和洁净。
其次,进行混合反应。
将事先准备好的聚醚、聚酯等原材料加入混合机中进行搅拌和混合。
加入的催化剂和气体发生剂可以控制发泡材料的反应速度和发泡性能。
然后,进行模具注射。
混合反应后的聚氨酯液体会在模具中注射,模具形状可以根据产品的要求进行设计和制造。
模具中的空腔会被聚氨酯液体填充,同时发生泡沫扩张,形成发泡材料的形状。
最后,进行固化。
注射完成后,发泡材料需要在模具中进行固化。
根据产品的要求,可以通过加热、冷却等方式对发泡材料进行固化,使其达到所需的硬度和强度。
在整个聚氨酯发泡的生产过程中,需要注意一些关键环节。
首先,原材料的选择和准备非常重要,不同的原材料和配比会对产品的质量产生影响。
其次,混合反应的时间和温度需要控制好,以保证反应的充分和均匀。
注射过程中,模具的设计和制造也需要精确,以确保产品形状的准确性和一致性。
最后,固
化的温度和时间也需要根据产品的要求进行调整,以获得最佳的固化效果。
总之,聚氨酯发泡生产工艺需要进行原材料准备、混合反应、模具注射和固化等步骤。
通过严格控制每个环节,可以获得高质量的发泡产品。
PU发泡工艺介绍
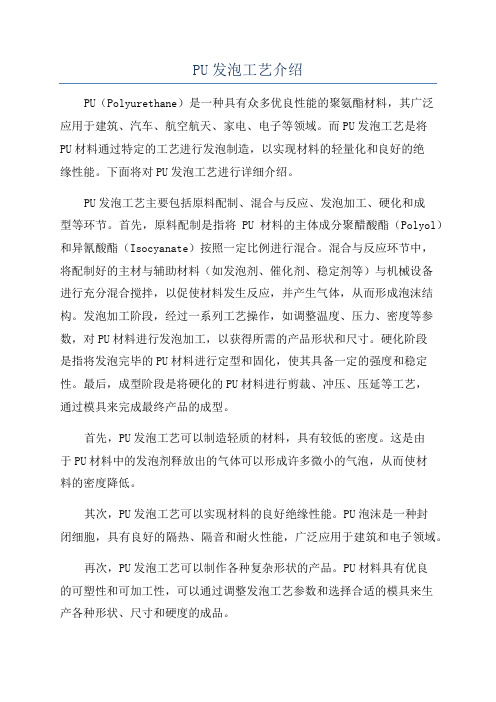
PU发泡工艺介绍PU(Polyurethane)是一种具有众多优良性能的聚氨酯材料,其广泛应用于建筑、汽车、航空航天、家电、电子等领域。
而PU发泡工艺是将PU材料通过特定的工艺进行发泡制造,以实现材料的轻量化和良好的绝缘性能。
下面将对PU发泡工艺进行详细介绍。
PU发泡工艺主要包括原料配制、混合与反应、发泡加工、硬化和成型等环节。
首先,原料配制是指将PU材料的主体成分聚醋酸酯(Polyol)和异氰酸酯(Isocyanate)按照一定比例进行混合。
混合与反应环节中,将配制好的主材与辅助材料(如发泡剂、催化剂、稳定剂等)与机械设备进行充分混合搅拌,以促使材料发生反应,并产生气体,从而形成泡沫结构。
发泡加工阶段,经过一系列工艺操作,如调整温度、压力、密度等参数,对PU材料进行发泡加工,以获得所需的产品形状和尺寸。
硬化阶段是指将发泡完毕的PU材料进行定型和固化,使其具备一定的强度和稳定性。
最后,成型阶段是将硬化的PU材料进行剪裁、冲压、压延等工艺,通过模具来完成最终产品的成型。
首先,PU发泡工艺可以制造轻质的材料,具有较低的密度。
这是由于PU材料中的发泡剂释放出的气体可以形成许多微小的气泡,从而使材料的密度降低。
其次,PU发泡工艺可以实现材料的良好绝缘性能。
PU泡沫是一种封闭细胞,具有良好的隔热、隔音和耐火性能,广泛应用于建筑和电子领域。
再次,PU发泡工艺可以制作各种复杂形状的产品。
PU材料具有优良的可塑性和可加工性,可以通过调整发泡工艺参数和选择合适的模具来生产各种形状、尺寸和硬度的成品。
此外,PU发泡工艺还具有可持续发展的优势。
PU材料可以通过循环利用和再生利用来降低对环境的影响。
同时,PU发泡工艺可以有效减少材料的使用量,从而实现资源节约。
在应用方面,PU发泡工艺广泛应用于建筑、汽车、航空航天、家电、电子等领域。
在建筑领域,PU发泡材料可用于墙体隔热、屋顶保温、地板隔音等。
在汽车行业,PU发泡材料可用于制造汽车座椅、车门内饰等零部件。
pu发泡工艺技术

pu发泡工艺技术PU发泡工艺技术是一种利用聚氨酯材料进行发泡制作的技术。
该技术可以使用于各种行业和领域,如建筑、汽车、家具、电子等。
在PU发泡工艺技术中,聚氨酯材料是通过化学反应组成的,形成一个具有轻质孔隙结构的发泡体。
PU发泡工艺技术主要包括材料准备、混合、注塑、发泡、固化等步骤。
首先,需要准备好聚氨酯材料,通常是由两种液体材料混合而成的。
然后,将这两种液体材料按一定比例混合,使其达到适合发泡的状态。
接下来,将混合的材料注入模具中。
模具可以根据需要制作成任何形状,以满足产品的要求。
在注塑过程中,材料开始发生变化,逐渐充满整个模具,并形成一个密闭的空腔。
在发泡阶段,注塑的材料会发生化学反应,产生气体,使整个空腔膨胀。
这样,PU发泡材料就形成了一个轻质、高强度的聚氨酯泡沫。
最后,通过固化工艺,使聚氨酯泡沫发泡体完全固化。
固化的时间和温度取决于具体的产品要求和材料性质。
完成固化后,就可以将PU发泡制品取出模具,得到成品。
PU发泡工艺技术具有许多优点。
首先,PU发泡材料具有优良的绝缘性能,可以在电子领域中广泛应用。
其次,由于聚氨酯材料的性质可调,可以制作出各种不同硬度、厚度和形状的产品。
另外,PU发泡材料重量轻、强度高,可以减少产品的重量和成本。
PU发泡工艺技术的应用范围很广。
在建筑领域,可以用来制作隔热材料、隔音材料和防水材料等。
在汽车领域,可以用于制作车座、车门和车顶等。
在家具领域,可以用于制作床垫、沙发和椅子等。
此外,PU发泡材料还可以用于制作包装材料、运动器材和医疗器械等。
总之,PU发泡工艺技术是一种十分重要且具有广泛应用的技术。
它通过化学反应和物理变化,将聚氨酯材料转化为轻质、高强度的泡沫制品。
这种技术不仅可以满足各种行业和领域的需求,同时也具有良好的环保性能。
随着科学技术的不断进步,PU发泡工艺技术将在更多领域中发挥作用,为人们的生活带来更多便利和舒适。
PU发泡工艺介绍解析

20
聚氨酯化学:A料跟B料之比
对于座椅泡沫而言(TDI系统及TDI&MDI系统)来说, 其对应关系为:
A料 P1:100
B料(软泡) 30-50
B料(硬泡)
根据实际羟值和水份计算,通常要 远高于软泡
21
聚醚组合料
2、新制的泡沫需在自然状态下熟化72小时方可取 样,取样应放在恒温恒湿内(GB/T2918规定的温 度是23±2℃,相对湿度50±5%)。
31
发泡测试标准
硬度:压陷硬度(ILD)、压缩硬度(CLD) 这两种测试方法的主要区别是泡沫塑料的加载面积,在ILD试验中
样件受压面积是323CM2,而CLD是将整个样件进行压缩。在此,我 们只讨论ILD试验方法。 在ILD试验中,试样大小是38*38*50mm,试验的压头直径200mm (压头底边有R=10的圆角),支撑板开有6mm的孔,孔间距20mm。 压头加压速度(100±20)mm/min,首先以5N的压力作为下压零点, 从零点开始下压试样厚度的70%,再以同样的速度卸荷,重复加压、 卸荷三次,作为预压,重复预压三次后立即以相同的速度压陷试样, 压头压入试样的厚度分别为25±1%、65±1%,到达变形量之后保持 30±1s记录相对压陷值,记下的值即为该压陷变量下的压陷硬度。
3
聚氨酯定义
➢主链上含有--NHCO-- 基团聚合物通称为聚 氨酯甲酸酯简称为聚氨酯。
➢简称PU。
4
聚氨酯分类
➢根据原料不同和配方的变化,分为软质、 半硬质和硬质泡沫。
软质:座椅,头枕,海绵… 半硬质:扶手,方向盘; 硬质:方向盘芯、冷库保温防水。
PU发泡工艺介绍

16
聚氨酯原材料-聚醚组合料
• 固含量: 固含量越高则泡沫产品硬度越高; • 粘度: 与固含量相关,固含量越高则粘度越高; 粘度越低则原料的流动性越好,加工性能 就越好; • 料比: 产品硬度,物理性能和开孔性的重要控制 点;
35
发泡测试标准
压缩永久变形:
在恒定的环境下,使泡沫材料试样在一定得时间内维持恒定 的变形,带试样回复一段时间后,观察变形对试样厚度的 影响。用试样的初始厚度与最终厚度之差与试样初始厚度 的比值表示泡沫塑料的永久压缩变形。 压缩永久变形=(试样初始厚度-试样最终厚度)/试样初始厚 度*100
36
发泡常用术语
另外65%ILD/25%ILD=压陷比,压陷比是衡量泡沫舒适度的指标。
32
发泡测试标准
拉伸强度是指拉伸试验至断裂时所施加的最 大拉伸应力,断裂伸长率是指试样至断裂 时标距内试样的伸长百分比。 拉伸强度=断裂时载荷/试样原始截面积 断裂伸长率=(断裂标距-原始标距)/原 始标距*100%。
33
发泡测试标准
1、快泡取自泡沫的中心,模塑泡沫的式样则取中心 部位或整体试验。 2、新制的泡沫需在自然状态下熟化72小时方可取 样,取样应放在恒温恒湿内(GB/T2918规定的温 度是23±2℃,相对湿度50±5%)。
31
发泡测试标准
硬度:压陷硬度(ILD)、压缩硬度(CLD) 这两种测试方法的主要区别是泡沫塑料的加载面积,在ILD试验中 样件受压面积是323CM2,而CLD是将整个样件进行压缩。在此,我 们只讨论ILD试验方法。 在ILD试验中,试样大小是38*38*50mm,试验的压头直径200mm (压头底边有R=10的圆角),支撑板开有6mm的孔,孔间距20mm。 压头加压速度(100±20)mm/min,首先以5N的压力作为下压零点, 从零点开始下压试样厚度的70%,再以同样的速度卸荷,重复加压、 卸荷三次,作为预压,重复预压三次后立即以相同的速度压陷试样, 压头压入试样的厚度分别为25±1%、65±1%,到达变形量之后保持 30±1s记录相对压陷值,记下的值即为该压陷变量下的压陷硬度。
聚氨酯发泡工艺流程

聚氨酯发泡工艺流程聚氨酯发泡是一种常用的制备泡沫材料的工艺,其在建筑、汽车、家具等领域有着广泛的应用。
在聚氨酯发泡的工艺流程中,需要经过原料准备、配料混合、发泡成型等多个环节。
下面将详细介绍聚氨酯发泡的工艺流程。
首先,原料准备是聚氨酯发泡工艺的第一步。
通常情况下,聚氨酯发泡所需的原料包括聚醚多元醇、异氰酸酯、催化剂、助剂等。
在进行原料准备时,需要确保原料的质量符合要求,同时要按照配方准确称量,以确保后续工艺的顺利进行。
接下来是配料混合环节。
在这一步中,需要将准备好的原料按照一定的配方比例进行混合。
通常情况下,聚醚多元醇、异氰酸酯等原料会在一定的温度下进行混合,同时加入催化剂、助剂等辅助材料。
混合的过程需要严格控制时间、温度和搅拌速度,以确保混合均匀,避免出现原料反应不完全的情况。
随后是发泡成型环节。
在这一步中,混合好的原料会被注入到模具中,然后在一定的温度和压力下进行发泡成型。
这一步的关键是控制发泡的时间和温度,以确保泡孔的均匀和稳定性。
同时,还需要根据产品的要求,控制模具的形状和尺寸,以确保最终产品的质量。
最后是固化和后处理环节。
在发泡成型后,产品需要在一定的时间内进行固化,以确保产品的力学性能和稳定性。
固化的时间和温度需要根据产品的具体要求进行控制。
同时,在固化后还需要进行一些后处理工艺,如修整、打磨、涂装等,以满足产品的外观和功能要求。
综上所述,聚氨酯发泡工艺流程包括原料准备、配料混合、发泡成型和固化后处理等多个环节。
在每个环节中,都需要严格控制工艺参数,以确保产品质量和生产效率。
同时,还需要根据产品的具体要求进行工艺调整,以满足不同客户的需求。
希望本文对聚氨酯发泡工艺流程有所帮助。
聚氨酯发泡工艺技术

聚氨酯发泡工艺技术聚氨酯(Polyurethane)是一种非常重要的聚合物材料,由于其低密度、良好的绝缘性能和抗冲击性,广泛用于建筑、汽车制造、家具等各个领域。
而聚氨酯发泡工艺技术作为聚氨酯制品的核心生产技术,对于产品的质量和性能起着至关重要的作用。
聚氨酯发泡工艺技术主要分为两类:化学发泡和物理发泡。
化学发泡主要通过在聚氨酯原料中加入发泡剂,然后在加热条件下发生化学反应来产生气体,使聚氨酯原料膨胀形成气泡结构,最后固化成弹性固体。
这种发泡工艺适用于制造软性的聚氨酯制品,如垫子、座椅和海绵等。
化学发泡的关键是选择合适的发泡剂和控制好热处理过程,以确保产品的质量和性能。
化学发泡工艺具有生产效率高、成本低的优点,是目前应用最广泛的聚氨酯发泡工艺之一。
物理发泡则是通过在聚氨酯原料中加入物理泡沫剂,然后通过机械方式形成气泡结构,最后固化成形。
这种发泡工艺适用于制造硬质的聚氨酯制品,如保温板、泡沫塑料和绝缘材料等。
物理发泡的关键是选择合适的泡沫剂和控制好发泡的机械参数,以确保产品的密度和结构均匀。
物理发泡工艺具有成型精度高、产品性能稳定的优点,但生产效率较低,成本较高。
不论是化学发泡还是物理发泡,聚氨酯发泡工艺技术都需要考虑以下几个关键因素:首先是选择合适的原料。
聚氨酯发泡材料通常由两种原料:聚氨酯预聚体和发泡剂组成。
在选择聚氨酯预聚体时,需要考虑预聚体的活性、分子量和端基类型等因素。
在选择发泡剂时,需要考虑发泡剂的稳定性、挥发性和气化速率等因素。
合理选择原料对产品的质量和性能有着直接的影响。
其次是控制好发泡参数。
发泡参数包括发泡剂的添加量、加热温度和时间等。
合理控制发泡参数可以确保聚氨酯材料膨胀形成均匀的气泡结构,从而提高产品的性能。
不同类型的聚氨酯制品需要根据其特定的要求来调整发泡参数,以满足产品的功能和应用需求。
最后是合理的快速固化。
聚氨酯发泡工艺中的固化过程对产品的质量和性能起着决定性的作用。
固化过程一般通过加热、冷却或添加固化剂来完成。
pu发泡工艺.docx

发泡基本知识一、聚氨酯泡沫塑料的基本配方及各组分的作用原料名称白料聚醚、聚酯或其它多元醇水催化剂(胺或有机锡)泡沫稳定剂阻燃剂防老剂链增长剂发泡剂颜料主要作用主要反应原料链增长剂、同时也是发生CO2气泡原料来源催化发泡及凝胶反应使泡沫稳定、控制孔的大小及结构提高阻燃性抗老化改善和调节聚氨酯的性能汽化后作为气泡来源并移去反应热,避免泡沫中心因高温而产生“烧焦”制造色彩鲜艳的制品黑料多异氰酸酯主要反应原料二、目前常用发泡料的种类发泡料的种类划分主要是针对白料而言。
目前,白料主要有全氟系列、141b 系列及环( / 异)戊烷系列,历史上还曾经使用过减氟系列。
这些种类的划分是按照聚醚中混入的发泡剂的特性来分类的。
全氟系列对大气层的破坏最为严重,而环 / 异戊烷及环戊烷对环境的破坏几乎为零。
根据蒙特利尔协议,到 2005 年将全面停止全氟、减氟、 141b 的使用。
三、白料的预混目前使用的白料以前为自配,现改为组合料,由供应商直接提供。
组合料的预混流程如下:环戊烷组合料静态混合器过缸备用环异戊烷发泡剂预混的控制关键:温度、搅拌时间、配比环戊烷 / 组合料= 11-14/100 ≥25min 22 ± 5℃四、手工检测检测的目的是为了检测所配制的白料是否合格。
每缸必检并要求记录。
检测的内容包括:乳白时间、凝胶时间、失粘时间、密度及泡沫的外观。
具体操作方法:分别取一定量的黑白料并调节到要求的温度,按照要求的比例在台钻上搅拌一定的时间,用秒表记录三个反应时间,用排水法测试自由泡芯部密度。
参数:( 黑料 / 白料 ) 25±2℃ 10s12±2s/68± 6s/95±20s25±1 Kg/m3五、常见问题及处理1、反应时间太慢原因:组合料催化剂不够;料温偏低;黑料加多;环境温度太低;处理:加大催化剂的用量;提高料温;使用合理比例;适当控制环温;2、反应时间太快原因:组合料催化剂过多;料温偏高;黑料过少;环境温度太高;处理:减少催化剂的用量;降低料温;使用合理比例;适当控制环温;3、泡沫发不起原因:组合料出现问题;未加发泡剂;未搅拌;处理:停止使用;按照比例添加;按照规定时间搅拌均匀;4、泡孔粗大原因:组合料出现问题;处理:停止使用;六、安全注意事项环戊烷属于碳氢化合物,沸点比空气重,是一级易燃液体,闪点是49℃,是一种无色透明液体,不溶于水,溶于有机溶剂,蒸气 -25 ℃,在空气中爆炸极限是~ %(占空气中的体积的百分数) ,遇明火易爆炸。
pu 发泡

pu 发泡1. 引言pu 发泡是一种常见的材料加工技术,通过将聚氨酯(polyurethane,简称PU)材料进行化学反应,使其在特定的条件下形成发泡结构。
PU 发泡具有轻质、隔热、吸音、抗压强度高等特点,在建筑、汽车、家具等领域得到广泛应用。
本文将介绍 pu 发泡的原理、工艺以及应用领域,帮助读者了解 pu 发泡技术的基本知识。
2. 原理PU 发泡的原理是通过在PU材料中加入发泡剂,并在一定的温度和压力条件下加热处理,使发泡剂放出气体,从而形成发泡结构。
发泡剂通常是含有低沸点液体的物质,加热后会蒸发产生气泡,使PU材料体积膨胀。
PU 发泡的原理可以总结为以下几个步骤:1.混合材料:将PU 原材料与发泡剂进行混合,通常还需要加入一些助剂来调节材料的性能。
2.加热处理:将混合材料放入加热设备中,在一定的温度和压力条件下进行加热处理,使发泡剂蒸发并形成气泡。
3.固化:在PU 发泡过程中,材料会逐渐固化,形成稳定的发泡结构。
3. 工艺PU 发泡的工艺包括材料准备、混合、加热、固化等步骤。
下面是一般的 pu 发泡工艺流程:1.材料准备:选择合适的PU原材料,包括聚酯酯等基材料,发泡剂,助剂等。
2.混合:将PU原材料与发泡剂、助剂等进行混合。
通常需要根据具体的要求进行配比,以获得适当的发泡效果。
3.加热处理:将混合后的材料放入加热设备中,控制温度和时间使发泡剂蒸发,形成气泡。
4.固化:在加热处理后,待材料中的气泡形成完整的发泡结构后,将材料进行冷却和固化。
5.后处理:根据具体的需求,对发泡材料进行切割、加工、涂层和表面处理等。
4. 应用领域PU 发泡材料具有许多优良的特性,使其在多个领域得到广泛应用。
以下是一些常见的应用领域:4.1 建筑领域PU 发泡材料在建筑领域广泛应用于隔热、隔音和抗震等方面。
例如,可以用于墙体、屋面和地板的保温材料,提供更好的能效和舒适性。
4.2 汽车领域PU 发泡材料在汽车制造中起到重要的作用。
PU发泡工艺介绍演示文稿

聚氨酯定义
➢主链上含有--NHCO-- 基团聚合物通称为聚 氨酯甲酸酯简称为聚氨酯。
➢简称PU。
聚氨酯分类
➢根据原料不同和配方的变化,分为软质、 半硬质和硬质泡沫。
软质:座椅,头枕,海绵… 半硬质:扶手,方向盘; 硬质:方向盘芯、冷库保温防水。
➢根据多元醇品种分类,分为聚酯型、聚醚 型;我们主要是使用聚醚型。
氢氧化铝 ➢ 防老剂 ➢ 链增长剂:三乙醇胺(我们使用的) ➢ 颜料 ➢ 脱模剂
聚氨酯原材料-ISO部分
➢ TDI:甲苯二异腈酸酯
➢ MDI:多亚甲基多苯基多异腈酸酯
聚氨酯原材料-ISO部分
TDI(甲苯二异氰酸酯):主要有2,4-和2, 6-异构体。工业上主要有三种产品, T100,T80/20,T65/35
聚氨酯化学:A料跟B料之比
➢ 根据A料与B料反应时的当量关系,可以计算出100克A料 需要多少克B料。
➢ 发泡指数INDEX:ISO实际用量/ISO理论用量*100; ➢ INDEX范围一般为60—110之间,INDEX较高时,产品比
较硬;
➢ 其中TDI理想的范围是90-105; ➢ MDI系统理想的范围是85-95。
PU发泡工艺介绍演示文稿
课程目标
• 介绍聚氨酯发泡工艺基础原理 • 发泡设备、模具的基础知识 • 工业生产安全防范
课 程 目录
• 聚氨酯的发展史 • 聚氨酯的分类 • 原料的介绍 • 聚氨酯的发泡原理 • 影响发泡的因素 • 配方制作基本要素 • 脱模剂原理及选择 • 发泡设备简单介绍
• 发泡模具简单介绍 • 生产工艺流程解析 • 常见问题分解 • 工业生产安全防范 • 聚氨酯发展趋势 • 知识要点回顾 • 持续改进(发泡工艺) • 经验分享
pu发泡工艺专业资料

发泡基本知识一、聚氨酯泡沫塑料的基本配方及各组分的作用原料名称白料重要作用聚醚、聚酯或其它多元醇重要反映原料气泡原料来源水链增长剂、同时也是发生CO2催化剂(胺或有机锡)催化发泡及凝胶反映泡沫稳定剂使泡沫稳定、控制孔的大小及结构阻燃剂提高阻燃性防老剂抗老化链增长剂改善和调节聚氨酯的性能发泡剂汽化后作为气泡来源并移去反映热,避免泡沫中心因高温而产生“烧焦”颜料制造色彩鲜艳的制品黑料多异氰酸酯重要反映原料二、目前常用发泡料的种类发泡料的种类划分重要是针对白料而言。
目前,白料重要有全氟系列、141b系列及环(/异)戊烷系列,历史上还曾经使用过减氟系列。
这些种类的划分是按照聚醚中混入的发泡剂的特性来分类的。
全氟系列对大气层的破坏最为严重,而环/异戊烷及环戊烷对环境的破坏几乎为零。
根据蒙特利尔协议,到2023年将全面停止全氟、减氟、141b的使用。
三、白料的预混目前使用的白料以前为自配,现改为组合料,由供应商直接提供。
组合料的预混流程如下:环戊烷组合料静态混合器过缸备用环异戊烷发泡剂预混的控制关键:温度、搅拌时间、配比环戊烷/组合料=11-14/100 ≥25min 22±5℃四、手工检测检测的目的是为了检测所配制的白料是否合格。
每缸必检并规定记录。
检测的内容涉及:乳白时间、凝胶时间、失粘时间、密度及泡沫的外观。
具体操作方法:分别取一定量的黑白料并调节到规定的温度,按照规定的比例在台钻上搅拌一定的时间,用秒表记录三个反映时间,用排水法测试自由泡芯部密度。
参数: 1.15(黑料/白料) 25±2℃ 10s 12±2s/68±6s/95±20s 25±1 Kg/m3五、常见问题及解决1、反映时间太慢因素:组合料催化剂不够;解决:加大催化剂的用量;料温偏低;提高料温;黑料加多;使用合理比例;环境温度太低;适当控制环温;2、反映时间太快因素:组合料催化剂过多;解决:减少催化剂的用量;料温偏高;减少料温;黑料过少;使用合理比例;环境温度太高;适当控制环温;3、泡沫发不起因素:组合料出现问题;解决:停止使用;未加发泡剂;按照比例添加;未搅拌;按照规定期间搅拌均匀;4、泡孔粗大因素:组合料出现问题;解决:停止使用;六、安全注意事项环戊烷属于碳氢化合物,沸点49℃,是一种无色透明液体,不溶于水,溶于有机溶剂,蒸气比空气重,是一级易燃液体,闪点是-25℃,在空气中爆炸极限是1.5~8.7%(占空气中的体积的百分数),遇明火易爆炸。
- 1、下载文档前请自行甄别文档内容的完整性,平台不提供额外的编辑、内容补充、找答案等附加服务。
- 2、"仅部分预览"的文档,不可在线预览部分如存在完整性等问题,可反馈申请退款(可完整预览的文档不适用该条件!)。
- 3、如文档侵犯您的权益,请联系客服反馈,我们会尽快为您处理(人工客服工作时间:9:00-18:30)。
发泡基本知识一、聚氨酯泡沫塑料的基本配方及各组分的作用原料名称白料主要作用聚醚、聚酯或其它多元醇主要反应原料水链增长剂、同时也是发生CO气泡原料来源2催化剂(胺或有机锡)催化发泡及凝胶反应泡沫稳定剂使泡沫稳定、控制孔的大小及结构阻燃剂提高阻燃性防老剂抗老化链增长剂改善和调节聚氨酯的性能发泡剂汽化后作为气泡来源并移去反应热,避免泡沫中心因高温而产生“烧焦”颜料制造色彩鲜艳的制品黑料多异氰酸酯主要反应原料二、目前常用发泡料的种类发泡料的种类划分主要是针对白料而言。
目前,白料主要有全氟系列、141b系列及环(/异)戊烷系列,历史上还曾经使用过减氟系列。
这些种类的划分是按照聚醚中混入的发泡剂的特性来分类的。
全氟系列对大气层的破坏最为严重,而环/异戊烷及环戊烷对环境的破坏几乎为零。
根据蒙特利尔协议,到2005年将全面停止全氟、减氟、141b的使用。
三、白料的预混目前使用的白料以前为自配,现改为组合料,由供应商直接提供。
组合料的预混流程如下:环戊烷组合料静态混合器过缸备用环异戊烷发泡剂预混的控制关键:温度、搅拌时间、配比环戊烷/组合料=11-14/100 ≥25min 22±5℃四、手工检测检测的目的是为了检测所配制的白料是否合格。
每缸必检并要求记录。
检测的内容包括:乳白时间、凝胶时间、失粘时间、密度及泡沫的外观。
具体操作方法:分别取一定量的黑白料并调节到要求的温度,按照要求的比例在台钻上搅拌一定的时间,用秒表记录三个反应时间,用排水法测试自由泡芯部密度。
参数: 1.15(黑料/白料) 25±2℃ 10s 12±2s/68±6s/95±20s 25±1 Kg/m3五、常见问题及处理1、反应时间太慢原因:组合料催化剂不够;处理:加大催化剂的用量;料温偏低;提高料温;黑料加多;使用合理比例;环境温度太低;适当控制环温;2、反应时间太快原因:组合料催化剂过多;处理:减少催化剂的用量;料温偏高;降低料温;黑料过少;使用合理比例;环境温度太高;适当控制环温;3、泡沫发不起原因:组合料出现问题;处理:停止使用;未加发泡剂;按照比例添加;未搅拌;按照规定时间搅拌均匀;4、泡孔粗大原因:组合料出现问题;处理:停止使用;六、安全注意事项环戊烷属于碳氢化合物,沸点49℃,是一种无色透明液体,不溶于水,溶于有机溶剂,蒸气比空气重,是一级易燃液体,闪点是-25℃,在空气中爆炸极限是1.5~8.7%(占空气中的体积的百分数),遇明火易爆炸。
1、环戊烷产生爆炸的必备条件:1)有环戊烷气体存在。
它来源于泄漏的容器、管道和机械设施以及发泡时原料的挥发。
2)环戊烷气体与空气混合浓度达到爆炸极限。
3)有明火产生。
包括电气打火,电势差放电起火,静电摩擦起火及人为造成明火等。
因此,在运输、储存、使用三个环节上,要采用必要的安全装置和严格的防范措施。
2、产生爆炸危险的控制:1)有环戊烷的地方,尽可能避免有空气存在。
措施:a.对储料罐采用氮气加压;b.箱体在充注前通入氮气排除空气。
2)尽可能避免环戊烷气体的产生或将其浓度控制在爆炸极限以下(一般控制在40%以下)。
措施:a.采用密封可靠的贮存、供料和配料系统,并把前二者置于工作厂区之外;b.向电气柜内通入净化干燥的氮气,尽可能带走存留的环戊烷;c.隔离环戊烷发泡工作区,并在其内(发泡设备、夹具周围)安装抽风设施。
3、注意事项:1)进入预混站包括环异戊烷地下储罐区,禁带火种、关闭通讯工具;2)作业时,穿棉质衣服,穿戴防护服;3)严禁敲击,使用铜质工具;4)处理含有环异戊烷发泡剂组合料时做好安全接地,使用气动工具;5)作业场所注意抽风;6)发泡料严禁直接排放到下水道,注意用木糠或沙粒吸收;7)溅到皮肤上立即用大量水冲洗;8)黑白料严禁相混和;9)严禁在黑料里混入水分,特别是密闭的黑料容器中。
箱体发泡一、箱体发泡原理白料预装箱现场黑/白储罐高压发泡机枪头模具箱体半成品黑料加热、熟化发泡料灌注方式:背部闭模灌注二、箱发泡控制参数1、烘道预热温度及时间 60±10℃ 30±10s2、模具温度 45±5℃3、原料温度环戊烷 25±2℃4、原料比例环戊烷 I/P=1.15±2%5、灌注压力 I、P 14±2Mpa6、枪样密度 23-26 Kg/m37、原料流量 500-1000 g/s(一旦设定不能随意更改)8、灌注量根据标准密度设定,具体见工艺通知单。
9、熟化时间根据泡层厚度、箱体结构、发泡料种类确定,具体见工艺通知单。
开工时通过枪头小样监控参数的合理及泡料的反应性三、箱发泡自检要求1、发泡工艺参数:同上2、导热系数:环戊烷≤0.0220W/M.K 每月拆箱送检。
3、首检及记录:外观及尺寸检验,包括包装件的配合检验。
4、箱体外观:侧板、后板、内胆无凹花、划花;箱体框条与左右侧板离缝≤0.5mm;箱体框条与内胆的离缝≤0.5mm;箱体框条45度接缝缝隙正面≤0.3mm,背面≤0.5mm;侧板正面不平度≤3mm;无空泡、无纤维状、无离泡、无变形。
5、箱体尺寸:正面对角≤3mm;顶部对角≤2mm;正面宽度上及中±0.8mm、下±1mm四、常见问题及处理1、漏泡原因:发泡剂含量偏大处理:减少发泡剂的用量;预热烘道温度及模温超高;降低预热烘道温度及模温;料温偏高;降低料温;料比偏小;调整到合理的黑白料比;内胆密封不到位;加强密封;2、金属板离泡原因:料温、预热烘道温度及模温过低;处理:提高相应温度;料比过高;降低料比;熟化时间过短;延长熟化时间;组合料粘性偏低;提高温度或停用。
3、蒸发器离泡原因:蒸发器胶面存在问题;处理:挑选或停用;内胆存在油污、灰尘;清洁;内胆过薄;控制吸塑、贴铝箔、降低温度;压接未到位;改善压接质量;发泡模配胆未到位;重新配胆调模;4、内胆变形原因:模温及预热烘道温度过高;处理:降低温度;内胆过薄;控制吸塑、贴铝箔、降低温度;重新配胆调模;模内有杂物;清理模具;5、箱体凹花原因:预装箱外表面碰凹、划花;处理:加强流转过程保护;流水线粘附异物引起;清理流水线;发泡模未清理干净;清模;6、箱体假满原因:灌注过程中急停;处理:排出故障;发泡参数设定不准;重新调整;组合料问题;停用;门体发泡一、门体发泡原理白料预装门现场储罐高压发泡机枪头模具门体半成品黑料加热、熟化发泡料灌注方式:开模灌注二、门发泡控制参数1、模具温度 40±5℃2、原料温度环戊烷 25±2℃3、原料比例环戊烷 I/P=1.18-1.204、灌注压力 14±2Mpa5、枪样密度 23-26 Kg/m36、原料流量 500-1000 g/s(一旦设定不能随意更改)7、灌注量根据标准密度设定,具体见工艺通知单。
8、熟化时间或周期循环时间根据泡层厚度、门体结构、发泡料种类确定,具体见工艺通知单。
开工时通过枪头小样监控参数的合理及泡料的反应性三、门发泡自检要求1、发泡工艺参数:同上2、导热系数:环戊烷≤0.022W/M.K 每月拆门送检。
3、首检及记录:外观及尺寸检验,包括包装件的配合检验。
4、门体外观:门面板无凹花、划花、变形;定位板无白口、开裂、压伤、划花;门胆无变形;门体无假满;定位板与面板离缝≤0.2mm,R位离缝≤0.5mm;5、门体尺寸:正面对角≤2mm;正面宽度上下±1mm、高±0.8mm;四角不平度≤0.6mm;四、常见问题及处理1、漏泡原因:发泡剂含量偏大处理:减少发泡剂的用量;模温超高;降低模温;料温偏高;降低料温;料比偏小;调整到合理的黑白料比;门体密封不到位;加强密封;2、门面板离泡原因:料温、模温过低;处理:提高相应温度;料比过高;降低料比;熟化时间过短;延长熟化时间;3、门胆变形原因:模温过高;处理:降低温度;内胆过薄;控制吸塑、贴铝箔、降低温度;重新配胆调模;模内有杂物;清理模具;4、门体凹花原因:预装门外表面碰凹、划花;处理:加强流转过程保护;发泡模未清理干净;清模;5、门体假满原因:灌注过程中急停;处理:排出故障;发泡参数设定不准;重新调整;组合料问题;停用;发泡设备的调控1、温度的调控主要通过对设备上相应的温控表或电脑设定值的改变来进行。
2、料比的调控主要通过调节黑白料计量泵的流量来进行,但应与枪头两料的压力调节相适应。
3、压力的调控主要调节枪头上两料的节流阀的大小来进行。
4、枪头及计量泵精度的调控主要通过周期性对设备进行校正,并配合相关软件参数的修正来进行。
具体做法是通过实测黑白料的单位时间重量并将其与显示结果作比对,找出正负误差,然后调整相关脉冲数的大小,使实测与显示相近。
机械部分的损坏应及时进行更换。
泡沫物理性能1、导热系数(平均温度10℃、W/m.K):环戊烷发泡≤0.0222、10%压缩强度(平行方向、MPa):环戊烷发泡≥0.155(垂直方向、MPa):环戊烷发泡≥0.113、线性尺寸稳定性(-20℃、48h、%):≤0.64、密度范围(Kg/m3):环戊烷发泡 32-39。