熔模铸造工艺卡
低压工艺卡

低压铸造工艺卡片
铝液温度
690-710℃
产品名称
TL5033
铸件毛重(Kg):9±0.2
机台型号:
铝液密度
≥2.60g/cm3
毛坯编号
ET44S
Sr含量:
见熔铝炉工艺指导书
冷却控制
工艺参数
压力控制
冷却时间
开始时间(S)
开通时间(S)
压力(bar)
控制项目
压力(mbar)
充型速率(mbar/S)
50±10
下模轮盘
280±10
40±10
4.5—6
模具烤模时间
45±10
下模大环
/
/
/
模具温度
轮盘
/
冷却风道基本位置图
轮缘
/
易出缺陷
1)轮辋易疏松
控制重点
1)严格按工艺参数进行
2)外观不能有碰伤、拉模、涂料脱落现象
编制
审核
批准
日期
分流锥风
160±20
80±20
4.5—6
升液
185
0.45
上模轮盘内环
80±20
170±20
4.5—6
充型Biblioteka 3400.06上模轮盘外环
130±20
70±20
4.5—6
420
0.06
增压
420
0.07
上模轮辐
/
/
/
750
0.72
保压
750
160±15
下模冒口
120±20
130±20
4.5—6
自然冷却时间
工艺卡片模板100例
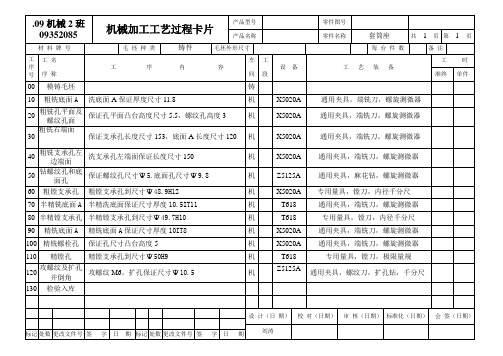
.09机械2班09352085 机械加工工艺过程卡片产品型号零件图号产品名称零件名称套筒座共 1 页第 1 页材料牌号毛坯种类铸件毛坯外形尺寸每台件数备注工序号工名序称工序内容车间工段设备工艺装备工时准终单件00 模铸毛坯铸10 粗铣底面A洗底面A保证厚度尺寸11.8 机X5020A 通用夹具,端铣刀,螺旋测微器20 粗铣孔平面及螺纹孔面保证孔平面凸台高度尺寸5.5,螺纹孔高度3 机X5020A 通用夹具,端铣刀,螺旋测微器30 粗铣右端面保证支承孔长度尺寸153,底面A长度尺寸120 机X5020A 通用夹具,端铣刀,螺旋测微器40 粗铣支承孔左边端面洗支承孔左端面保证长度尺寸150 机X5020A 通用夹具,端铣刀,螺旋测微器50 钻螺纹孔和底面孔保证螺纹孔尺寸ψ5.底面孔尺寸ψ9.8 机Z5125A 通用夹具,麻花钻,螺旋测微器60 粗镗支承孔粗镗支承孔到尺寸ψ48.9H12机X5020A 专用量具,镗刀,内径千分尺70 半精铣底面A半精洗底面保证尺寸厚度10.5IT11机T618 通用夹具,端铣刀,螺旋测微器80 半精镗支承孔半精镗支承孔到尺寸ψ49.7H10机T618专用量具,镗刀,内径千分尺90 精铣底面A精铣底面A保证尺寸厚度10IT8机X5020A 通用夹具,端铣刀,螺旋测微器100 精铣螺栓孔保证孔尺寸凸台高度5 机X5020A 通用夹具,端铣刀,螺旋测微器110 精镗孔精镗支承孔到尺寸ψ50H9机T618 专用量具,镗刀,极限量规120 攻螺纹及扩孔并倒角攻螺纹M6,扩孔保证尺寸ψ10.5机Z5125A通用夹具,螺纹刀,扩孔钻,千分尺130 检验入库设计(日期)校对(日期)审核(日期)标准化(日期)会签(日期)材料牌号毛坯种类毛坯外形尺寸每毛坯件数每台件数备注工序号工名序称工序内容车间工段设备工艺装备工时准终单件设计(日期)校对(日期)审核(日期)标准化(日期)会签(日期)材料牌号毛坯种类毛坯外形尺寸每毛坯件数每台件数备注工序号工名序称工序内容车间工段设备工艺装备工时准终单件设计(日期)校对(日期)审核(日期)标准化(日期)会签(日期)。
熔模铸造工艺资料
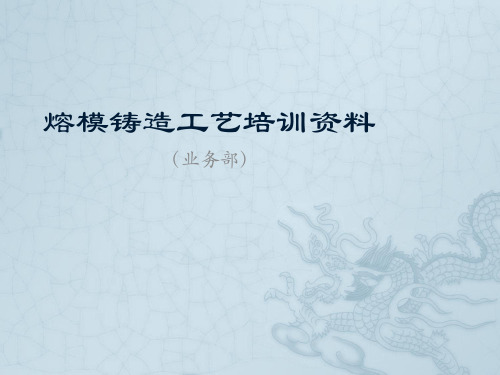
4、月产量:根据经验确定射蜡班产×3班×11个工位×30天×产品单重 5、面层:根据产品结构,及产品要求确定,一般复杂产品存在细的孔槽、产品单重大
以及产品表面质量要求较高时需加厚1-2层面层。 6、加厚层:根据产品最大尺寸及重量确定,一般最大尺寸超过150mm,重量超过2kg,
熔模铸造工艺培训资料
(业务部)
报价
报价
1、单重:客户提供单重或立体图的,若为毛坯单重可直接使用,若为加工单重则必须 加上加工量的重量,如没有提供则需根据图纸自己绘图计算。
2、合格率:主要考虑产品壁厚、结构、材质的影响,一般壁厚越小、结构越复杂、特 殊材质(高铬、高镍、铜合金、高温合金等)合格率低。
熔模铸件的尺寸精度高,表面粗糙度细。熔模铸件的尺寸精度可达到CT5~7级,表面粗糙度可 达到Ra(1.6~12.5)μm,因此可以减少铸件的切削加工量,甚至可以无须切削加工。
可以铸造薄壁铸件以及重量很小的铸件。最小壁厚可达0.5mm,重量可以小到几克。 可以铸造花纹精细的图案、文字、带有细槽和弯曲细孔的铸件。最小孔径可以小到0.5mm。 可以制造形状复杂的铸件。熔模铸件的外形和内腔形状几乎不受限制。 可以制造各种合金的铸件。如铝合金、镁合金、铜合金、不锈钢、镍铬合金、钴合金等。对于
制壳车间加快型壳表面的空气流动,从而增加型壳的干燥速度、减少干燥时间。但面层干燥速度不 可过快,干燥不可过度,防止出现龟裂。一般面层使用微风和不用吹风。 (3)环境湿度是影响型壳干燥的又一重要因素 在温度基本稳定的情况下,湿度大的车间,型壳水 分蒸发速度慢。当相对湿度大于80%时,型壳的干燥时间将大大加长。因而,制壳车间必须有除湿 机,严格控制车间的湿度。 面层涂挂区环境要求:温度25±2℃,干燥区环境要求:温度25±2℃,具体干燥时间应根据模壳实 际干燥情况而定。 型壳干燥程度的测量方法有:重量法、显色法、电阻法等。重量法因型壳外部砂粒容易脱落而不准 确;显色法是在涂料中加入显色剂,型壳干燥前后的颜色有明显区别,很容易根据颜色来判断型壳 是否干燥;电阻法的原理是利用型壳中水的高导电性,型壳的电阻和其含水量有关,当失水率达 70%以上时电阻值急剧增大,可以认为型壳的电阻增大到超过某一临界值时,型壳已干燥。 目前主要是靠经验,用手摸来感觉模壳是否干燥透或用小棒捅看是否有其强度
熔模铸造工艺流程
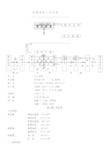
熔 模 铸 造 工 艺 流 程模料主要性能:灰 分 ≤0.025%铁含量 灰分的10% ≤0.0025% 熔 点 83℃-88℃(环球法)60℃±1℃ 针入度 100GM (25℃)3.5-5.0DMM450GM (25℃)14.0-18.0DMM收缩率 0.9%-1.1% 比 重 0.94-0.99g/cm 3 颜 色 新蜡——兰色、深黄色 旧蜡——绿色、棕色蜡(模)料处理工艺参数:除水桶 搅拌时温度 110-120℃ 搅拌时间 8-12小时 静置时温度 100-110℃ 静置时间 6-8小时 静置桶 静置温度 70-85℃ 静置时间 8-12小时 保温箱 温 度 48-52℃ 时 间 8-24小时 二、操作程序1、从脱蜡釜泄出的旧蜡用泵或手工送到除水桶中,先在105-110℃下置6-8小时沉淀,将水分泄掉。
2、蜡料在110-120℃下搅拌8-12小时,去除水份。
3、将脱完水的蜡料送到70-85℃的静置桶中保温静置桶中保温静置8-12小时。
4、也可将少量新蜡加入静置桶中,静置后清洁的蜡料用手工灌到保温箱蜡缸中,保温温度48-52℃,保温时间8-24小时后用于制蜡模。
5、或把静置桶中的回收蜡料输入到气动蜡模压注机的蜡桶中,保温后压制浇道。
三、操用要点1、严格按回收工艺进行蜡料处理。
2、除水桶、静置桶均应及时排水、排污。
3、往蜡缸灌蜡时,蜡应慢没缸壁流入,防止蜡液中进入空气的灰尘。
4、蜡缸灌满后应及时盖住,避免灰尘等杂物落入。
5、经常检查每一个桶温,防止温度过高现象发生。
6、作业场地要保持清洁。
7、防止蜡液飞溅。
8、严禁焰火,慎防火灾。
压制蜡(熔)模一、工艺参数室温20-24℃压射蜡温50-55℃压射压力0.2-0.5Mpa 保压时间10-20S冷却水温度15±3℃二、操作程序1、从保温槽中取出蜡缸,装在双工位液压蜡模压注机上,使用前应去除蜡料中空气及硬蜡。
2、将模具放在压注机工作台面上定位,检查模具所有芯子位置是否正确,模具注蜡口与压注机射蜡嘴是否对正。
精密铸造工艺-熔模铸造
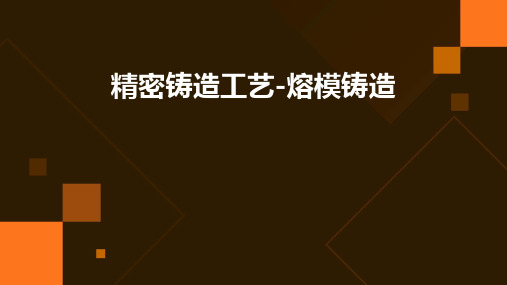
一定的强度
在搬运和组装过程中不易损坏。
易于脱壳
在铸件冷却后能够顺利脱去壳型,不 损伤铸件表面。
合金选择与性能要求
符合产品使用要求
良好的铸造性能
根据产品的使用环境和性能要求选择合适 的合金种类和牌号。
合金应具有较低的熔点和良好的流动性, 以便于充型和补缩。
安全操作规程及培训要求
制定安全操作规程
明确各工序的安全操作要求和注 意事项,确保操作人员严格遵守
。
应急预案与演练
对新员工和转岗员工进行安全培 训,提高员工的安全意识和操作
技能。
安全培训与教育
对涉及特种作业的员工,如电工 、焊工等,必须持证上岗,确保 操作安全。
特种作业人员持证上岗
制定针对熔模铸造过程中可能出现 的紧急情况的应急预案,并定期进 行演练,提高员工的应急处置能力。
加强人才培养
加强人才培养和引进,培养一支高素质、专业化的熔模铸造技术人才队伍,推动行业的技 术进步和可持续发展。例如,建立完善的人才培养和激励机制,吸引和留住优秀人才。
感谢您的观看
THANKS
蜡料选择与性能要求
低熔点和高流动性
确保蜡料在注射时能够充分填充模具,形成 精确的蜡模。
易于脱模
与模具材料之间有良好的分离性,降低脱模 难度。
稳定性好
在存放和使用过程中不易变质或产生缺陷。
对环境友好
无毒无害,符合环保要求。
壳型材料及其性能要求
高耐火度
能够承受高温金属液的冲刷而不破裂 或变形。
良好的透气性
较高的力学性能
良好的耐蚀性和耐磨性
合金应具有足够的强度、硬度和韧性等力 学性能,以满足产品的使用要求。
压铸工艺卡(800T)

数量
备注
配制比例 1:120
增压预热模数/模 慢速压力/bar 慢速流量/% 压射时间/s 开模时间/s 铝液温度/℃ 顶针前延时/s 顶针后延时/s 料柄厚度/mm
5±2 140±10
80±5 8±1 6±1 680±30 1±1 25±5 25±5
更改标记
处数 更改文件号 签名
日期
批准
版本号:A-0 ;
XX有限公司
新旧料比 7:3
铸件 (KG)
2.53
浇注 系统 (KG)
压力铸造工艺卡片
每模 腔数
1
每模重量 (KG)
编制 会签 审核
产品名称 产品图号 材料牌号
设备
工艺 装备
表单编号:
ADC12 设备名称 DCC800 压室直径 工艺装备名称
镶
图号
嵌
件
名称 涂 料
名称
牌号 9/bar
工 艺 规
锤头至模具行程 /mm
二快位置/mm
范 增压位置/mm
一快开度/%
二快开度/%
增压开度/%
重点自检内容:
15±5 130±5 110±5 620±5 400±5 450±5 60±5 60±5 40±5
客户代码 物料编码 工序号
设备编号
ф100 工艺装备编号
铸造工艺(附图)
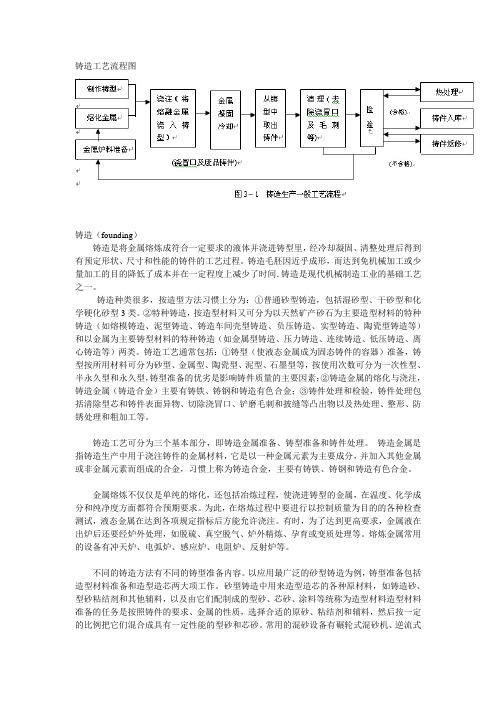
铸造工艺流程图铸造(founding)铸造是将金属熔炼成符合一定要求的液体并浇进铸型里,经冷却凝固、清整处理后得到有预定形状、尺寸和性能的铸件的工艺过程。
铸造毛胚因近乎成形,而达到免机械加工或少量加工的目的降低了成本并在一定程度上减少了时间.铸造是现代机械制造工业的基础工艺之一。
铸造种类很多,按造型方法习惯上分为:①普通砂型铸造,包括湿砂型、干砂型和化学硬化砂型3类。
②特种铸造,按造型材料又可分为以天然矿产砂石为主要造型材料的特种铸造(如熔模铸造、泥型铸造、铸造车间壳型铸造、负压铸造、实型铸造、陶瓷型铸造等)和以金属为主要铸型材料的特种铸造(如金属型铸造、压力铸造、连续铸造、低压铸造、离心铸造等)两类。
铸造工艺通常包括:①铸型(使液态金属成为固态铸件的容器)准备,铸型按所用材料可分为砂型、金属型、陶瓷型、泥型、石墨型等,按使用次数可分为一次性型、半永久型和永久型,铸型准备的优劣是影响铸件质量的主要因素;②铸造金属的熔化与浇注,铸造金属(铸造合金)主要有铸铁、铸钢和铸造有色合金;③铸件处理和检验,铸件处理包括清除型芯和铸件表面异物、切除浇冒口、铲磨毛刺和披缝等凸出物以及热处理、整形、防锈处理和粗加工等。
铸造工艺可分为三个基本部分,即铸造金属准备、铸型准备和铸件处理。
铸造金属是指铸造生产中用于浇注铸件的金属材料,它是以一种金属元素为主要成分,并加入其他金属或非金属元素而组成的合金,习惯上称为铸造合金,主要有铸铁、铸钢和铸造有色合金。
金属熔炼不仅仅是单纯的熔化,还包括冶炼过程,使浇进铸型的金属,在温度、化学成分和纯净度方面都符合预期要求。
为此,在熔炼过程中要进行以控制质量为目的的各种检查测试,液态金属在达到各项规定指标后方能允许浇注。
有时,为了达到更高要求,金属液在出炉后还要经炉外处理,如脱硫、真空脱气、炉外精炼、孕育或变质处理等。
熔炼金属常用的设备有冲天炉、电弧炉、感应炉、电阻炉、反射炉等。
不同的铸造方法有不同的铸型准备内容。
压铸工艺卡范例

客户 产品名称
后壳体
零(部)件号 文件版本号
材料 牌号
铸件毛重பைடு நூலகம்(kg)
7.8
模穴数 (pcs)
1
试模日期
设备
料管直径(mm)
¢110 每模周期(s)
工
1 机器检查、铝锭预热/溶解 2 架模、模具预热(模温机) 3 参数调整 4 吹气/喷涂 5 给料、压射
序
内
容
6
开模、顶出、取件、去浇口、自检
参数模具每调整一次需对相关项目进行检测取样送检品质部及时将检验情况反馈给现场压铸工程师配合生产直至质量达标目标良率96机器检查铝锭预热溶解架模模具预热模温机进入二次循环首检前15模产品强制报废吹气喷涂1射料最大位置7锤头追踪2增压开始位置选择8压射时间s3二快开始位置选择9射料慢速4一快开始位置选择10冷却时间s5储能压力bar11触发压力bar6铝液温度630650注
生产,直至质量达标(目标良率≥96%)
1
100 顶针前进速度 80% 顶针前进延时 4s
铸
80
顶针后退速度
80% 顶针后退延时 25s
件 质
稀释倍数
送料设备
喷涂设备 喷涂时间
量
外观质量 符合制程检验标准
内在质量 符合探伤标准
离型 剂 离型剂
编制:
ELP-Z
1:90
质
量
离型剂压送机
气枪
>15S
审核:
符合制程检验标准 批准:
符合探伤标准
45%
8、压射时间(s)
13
530mm
65%
9、射料慢速
60%
480mm
45%
10、冷却时间(s)
铸造工艺卡

合金牌号
每车(或机)件数
每型件数
生产线
加工单位
型砂量/kg·型
更改根据
设计
校对
审核
检查科会签
厂批准
总厂批准
标记及数目
签名及日期
厂车间
铸件工艺卡(砂芯图)
第页
零件号
共页
零件名称
芯号
芯砂号
重量/kg·个
个/盒
个/件
名称
图号
数量
更改根据
设计
校对
审核
检查科会签
厂批准
总厂批准
标记及数目
签名及日期
厂车间
冷铁
材料
砂芯数量
下砂箱
数量
制芯
检查样板
砂芯编号
编号
用途
数量
制芯方法
涂料编号
涂料
次数
烘干前
烘干后
烘干温度
特殊操作说明:
浇口杯
内浇道
横浇道
直浇道
冒口
浇注温度
/℃
编号
数量
规格
数量
规格
数量
规格
数量
规格
浇注时间
/S
冷却时间/min
编制
校对
审核
批准
标记
处数Leabharlann 更改文件号签字日期
标记
处数
更改文件号
签字
日期
厂
造型工艺卡片
第页
零件简图:
每台件数
合金牌号
零件重量
铸件重量
浇冒口重量
没毛坯零件数
浇注后砂型重
名称
方法
使用设备
操作说明
落砂
铸造工艺卡片法兰盘
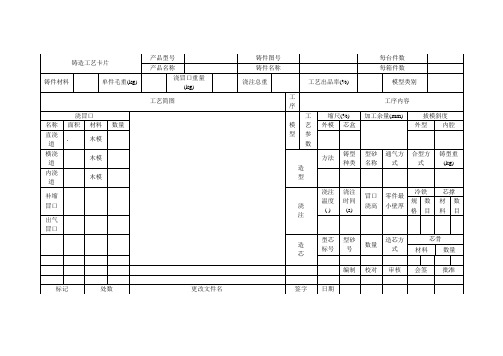
铸件名称
每箱件数
铸件材料
单件毛重(kg)
浇冒口重量(kg)
浇注总重
工艺出品率(%)
模型类别
工艺简图
工序
工序内容
浇冒口
模型
工艺参数
缩尺(%)
加工余量(mm)
拔模斜度
名称
面积
材料
数量
外模
芯盒
外型
内腔
直浇道
.
木模
横浇道
木模
造
型
方法
铸型
种类
型砂名称
通气方式
合型方式
铸型重(kg)
内浇道
木模
补缩冒口
浇
注
浇注温度( )
浇注时间(s)
冒口浇高
零件最小壁厚
冷铁
芯撑
规格
数目
材料
数目
出气冒口
造
芯
型芯标号
型砂号
数量
造芯方式
芯骨
材料
数量
编制
校对
审核
会签
批准
标记
处数
更改文件名
签字
日期
压铸工艺上卡

审核:
批准:
增压ACC
Mpa
料柄厚度
mm
喷雾时间
动:S静:s
持压时间
s
冷却时间
~s
吹气时间
动:s静:S
顶出行程
mm
脱模剂
稀释比例
射出状态
0→
低速区间(含一速)
高速区间
减速射出(FL)
增压启动(VP)
原点距离
前进停止
首
选
机
型
位置mm
0→→
速度m/s(圈)
→
~
代
用
机
型
位置mm
速度m/s(圈)
生产注意事项:
产品图片:
编号:
版本:
日期:
页次:
客户名称
产品名称
产品编号
模具编号
模具来源
产品材质
每模件数
镶件安装
每件净重
铸造重量
机器型号
代用型号
模具资料
压室类型
压室直径
mm
外型尺寸
高:宽:厚:mm
止口尺寸
φ×mm
冷却类型
产品壁厚
最小:最大:mm
复位类型
抽芯类型
内浇口面积
mm2
工
艺
参
数
浇铸温度
~℃
铸造压力
~Mpa
高速ACC
Mpa
熔模铸件生产工艺规程完整
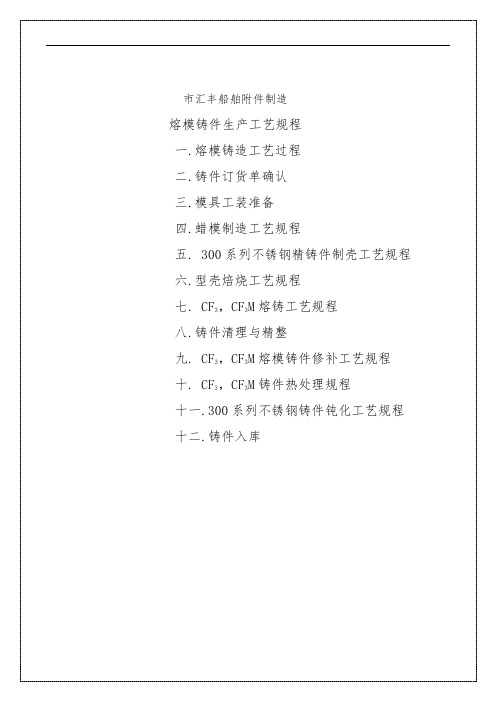
⑷浇注时钢水要对准浇口杯,既要快,又要稳,钢水浇至离浇口杯上部以下10mm即可,8大件铸件浇口杯浇浇后下沉后需要进行补浇,再后浇口杯上覆盖保温发热剂
⑸浇注后的模壳中铸件经冷却1小时后移出浇注场地准备下一炉的工作;
⑹做好过程记录。
(八).铸件清理与精整
⑴清砂、用震动脱壳机去除铸件表面型壳;
1室温度控制在15℃~30℃;
2焊接时,浇口棒下端流出15~20mm再焊接蜡形,上部蜡形距浇口杯顶端保持80mm~100mm。蜡形与蜡形之间间距15~30mm,视工件大小决定;
3焊接可用电烙铁,电炉加热焊刀等;
4焊刀温度不宜过高,一般为300℃左右;
5焊接时选用的浇口棒、冒口、浇口排列顺序均按焊接工艺卡执行;
⑻氩弧焊后进一步修磨,保证铸件表面无缺陷;
⑼经清理精整后逐只检收合格送下道热处理
(九).CF3,CF3M铸件热处理规程
1.恶劣工作条件用耐蚀铸钢的化学成分(%)[ASTM A744/A744M-2000]
钢号/元素
C≤
Si≤
Mn≤
P≤
S≤
Cr
Ni
Mo
相当于
CF3
0.03
2.0
1.5
0.04
0.04
17.0~21.0
6、成品的保管
经质检员按图纸要求检验合格的产品,又车间负责人填好入库单,入库单上必须写明产品的名称及数量交成品保管员,成品保管员接到入库单后必须认真负责进行清点核对,确认无误后才能入库、登帐,并放在指定位置,堆放整齐,不准乱堆。发货时,成品保管员要认真核对发货单位的产品名称、规格型号、发货数量,确认无误后才能发货并登帐。成品保管员每月要对库成品核对清查每个成品的库存量,并造册向厂部报告。
压铸工艺卡

名 称距 离速 度阀开度处数XX机械有限公司编制/日期会签/日期审核/日期批准/日期客户代码操作车间设备编号产能(件/班)页 码产品名称产品图号工序编号材料牌号表单编号/版本工艺路线熔炼→压铸→锯料头→打砂→去毛刺→抛丸→喷塑→机加一序→机加二序→机加三序→机加四序→超声波清洗→检验、包装→入库→发运铸造图示压铸机压铸机型号力劲900T 材料牌号LM6压室直径∅100压射位置下档模具模具编号法兰尺寸Φ200X20液压抽芯有顶杆先复位有涂料冲头油牌号/脱模剂牌号花野935冲头油类型颗粒脱模剂配比1:100镶嵌件/工艺活块名称活块材质H13图号数量1料柄厚度(mm )25±5顶回延时(s )4铝液温度/C°670±20压射时间(s )6模具温度/C°220±20冷却时间(s )取件方式自动熔炼温度/C°800±20喷雾方式自动新、旧料配比7:3顶出延时(s)310压机工作流程图快压流量2圈顶出时间(s )3增压流量7圈吹气时间(s )6热模时间10-15min增压预热模数10pcs产品要点常规要求快压压力(bar )140喷雾时间(s )8增压压力(bar )130冷模预热模数20pcs 1.操作人员上岗前必须穿戴好劳保用品;2.日期章按照周期更换并符合当前年月;3.产品各项尺寸检验符合检验规定;4.熔炼参数在控制范围内;(熔炼工艺点检记录表)5.压铸参数在控制范围内;(压铸工艺点检记录表)6.确保设备状态稳定;(设备点检记录表);7.作业按工艺流程模块化运作;(流程图);8.作业场地整洁,干净,安全;(5S 要求);参数压射0位快压启动点增压启动点料头保压点冲头跟踪位置0mm 340mm 关键点编号12345———压铸工艺参数增压选择420mm 480mm 550mm 0.5m/s2.5m/s 3m/s 3m/s 0.5m/s1.外观:不允许有开裂或严重冷隔、拉模、缺料、变形等缺陷;2.气孔:按照ASTM-E505 5/8 3级执行;锯床剖切或X-ray 探伤;3.重量:毛坯重量3.16Kg±0.02Kg ,整模重量6.148Kg±0.02Kg4.拉模:检查孔内不允许严重拉模,注意喷雾位置;5.印痕:不允许有严重流痕或阶梯痕迹;6.合模:确保每次合模到位,每4小时全面清理1次模具分型面的杂物;7.产品整齐摆放在托盘上,层与层之间用隔板隔开;8.填写生产流程卡,标明生产信息;签名/日期异常处理管理流程更改标记更改内容样件试生产量产工艺参数异常停机报告压铸主管领班按要求执行压铸主管判定参数正确继续生产是否压铸工艺卡用木榔头把料柄(黄色标识)敲掉,内浇口残留要求凸出≥0.3mm ,凹进≤0.3mm,不允许缺料;敲完后注意查看是否严重变形,检查进料部位是否冲浇口严重。
压力铸造工艺卡(模版)
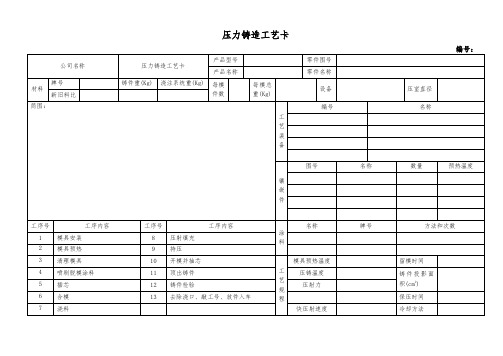
开模并抽芯
工艺规程
模具预热温度
留模时间
4
喷刷脱模涂料
11
顶出铸件
压铸温度
铸件投影面积(cm2)
5
插芯
12
铸件检验
压射力
6
合模
13
去除浇口、敲工号、放件入车
保压时间
7
浇料
快压射速度
冷却方法
压力铸造工艺卡
编号:
公司名称
压力铸造工艺卡
产品型号
零件图号
产品名称
零件名称
材料
牌号
铸件重(Kg)
浇注系统重(Kg)
每模件数
每模总重(Kg)
设备
压室直径
新旧料比
简图:
工艺装备
编号
名称
镶嵌件
图号
名内容
工序号
工序内容
涂料
名称
牌号
方法和次数
1
模具安装
8
压射填充
2
模具预热
9
持压
3
清理模具
熔模铸造工艺流程2

熔模铸造工艺流程重复多次模具制造制溶模及浇注系统模料处理模组焊接模组清洗上涂料及撒砂涂料制备型壳干燥(硬化)脱蜡型壳焙烧浇注熔炼切割浇口抛光或机加工钝化修整焊补热处理最后清砂喷丸或喷砂磨内浇口震动脱壳1模料制熔模用模料为日本牌号:K512模料模料主要性能:灰分≤0.025%铁含量灰分的10% ≤0.0025%熔点83℃-88℃(环球法)60℃±1℃针入度100GM(25℃)3.5-5.0DMM450GM(25℃)14.0-18.0DMM收缩率0.9%-1.1%比重0.94-0.99g/cm3颜色新蜡——兰色、深黄色旧蜡——绿色、棕色蜡(模)料处理工艺参数:除水桶搅拌时温度110-120℃搅拌时间8-12小时静置时温度100-110℃静置时间6-8小时静置桶静置温度70-85℃静置时间8-12小时保温箱温度48-52℃时间8-24小时二、操作程序1、从脱蜡釜泄出的旧蜡用泵或手工送到除水桶中,先在105-110℃下置6-8小时沉淀,将水分泄掉。
2、蜡料在110-120℃下搅拌8-12小时,去除水份。
3、将脱完水的蜡料送到70-85℃的静置桶中保温静置桶中保温静置8-12小时。
4、也可将少量新蜡加入静置桶中,静置后清洁的蜡料用手工灌到保温箱蜡缸中,保温温度48-52℃,保温时间8-24小时后用于制蜡模。
5、或把静置桶中的回收蜡料输入到气动蜡模压注机的蜡桶中,保温后压制浇道。
三、操用要点1、严格按回收工艺进行蜡料处理。
2、除水桶、静置桶均应及时排水、排污。
3、往蜡缸灌蜡时,蜡应慢没缸壁流入,防止蜡液中进入空气的灰尘。
4、蜡缸灌满后应及时盖住,避免灰尘等杂物落入。
5、经常检查每一个桶温,防止温度过高现象发生。
6、作业场地要保持清洁。
7、防止蜡液飞溅。
8、严禁焰火,慎防火灾。
压制蜡(熔)模2一、工艺参数室温20-24℃压射蜡温50-55℃压射压力0.2-0.5Mpa 保压时间10-20S冷却水温度15±3℃二、操作程序1、从保温槽中取出蜡缸,装在双工位液压蜡模压注机上,使用前应去除蜡料中空气及硬蜡。
管道铸造工艺卡
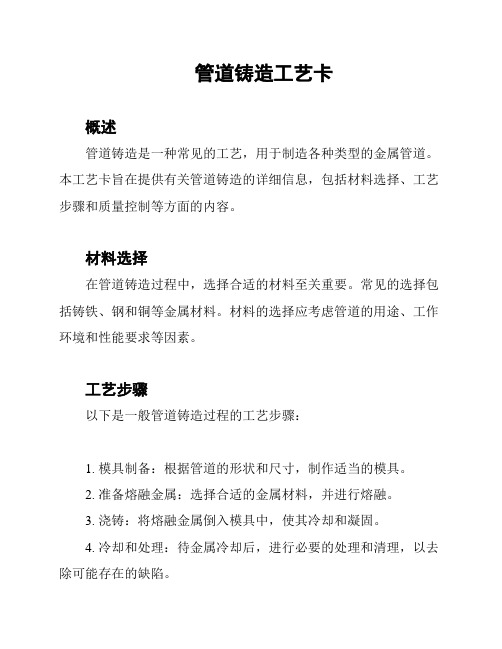
管道铸造工艺卡概述管道铸造是一种常见的工艺,用于制造各种类型的金属管道。
本工艺卡旨在提供有关管道铸造的详细信息,包括材料选择、工艺步骤和质量控制等方面的内容。
材料选择在管道铸造过程中,选择合适的材料至关重要。
常见的选择包括铸铁、钢和铜等金属材料。
材料的选择应考虑管道的用途、工作环境和性能要求等因素。
工艺步骤以下是一般管道铸造过程的工艺步骤:1. 模具制备:根据管道的形状和尺寸,制作适当的模具。
2. 准备熔融金属:选择合适的金属材料,并进行熔融。
3. 浇铸:将熔融金属倒入模具中,使其冷却和凝固。
4. 冷却和处理:待金属冷却后,进行必要的处理和清理,以去除可能存在的缺陷。
5. 检测和测试:对铸件进行非破坏性测试,如尺寸检测、X射线检测等,以确保质量符合要求。
6. 加工和装配:对铸件进行必要的加工和装配,以满足最终产品的要求。
7. 表面处理和涂层:为了提高铸件的耐腐蚀性和美观度,可以进行表面处理和涂层。
质量控制质量控制是管道铸造过程中至关重要的一环。
以下是一些常见的质量控制措施:- 模具检查:确保模具的尺寸和形状符合要求。
- 熔炼过程控制:控制熔炼温度和时间,以确保金属质量。
- 确保冷却时间充足:避免铸件内部存在缺陷。
- 检查和修复缺陷:对铸件进行全面检查,并及时修复可能存在的缺陷。
- 非破坏性测试:通过各种测试方法,如X射线检测和超声波检测,检查铸件的质量。
结论管道铸造是一项复杂的工艺,需要综合考虑材料选择、工艺步骤和质量控制等方面的因素。
本工艺卡提供了一份概述,旨在帮助人们更好地理解管道铸造过程,并为相关工作提供指导。
以上所述仅为一般性信息,具体工艺操作应根据实际情况进行调整和优化。
熔模铸造工艺卡

1
制造壳模
直浇道
1
Ø50
硅溶胶工艺:面层70-140目锆英砂,挂砂两遍;背层莫来石砂60目,挂2层;莫来石砂30目挂2层,最后封浆。
横浇道
2内浇道2Fra bibliotek阶梯式10*240
冒口
3
脱蜡
壳模焙烧
蒸汽压力
0.75MPa
入炉温度°C
保温温度°C
最高温度°C
保温时间h
蒸汽温度
170°C
室温
1200
1200
5
脱蜡时间
10min
设备及工艺装备
模具
1套
检验
按成品检验项目表
序号
工作内容
压蜡机、焙烧炉等设备
各1套
1
蜡模制造、蜡模组合、模壳制造
熔炼
2
合金熔炼、浇注
型壳温度°C
浇注温度°C
精炼温度°C
浇注至开箱时间h
3
铸件清壳,去浇冒口
300-400
1670-1690
2
4
热处理
清壳方法
水力清壳
5
切割方法
锯
更改
编制
质量会签
共1页
校核
审查
审定
第1页
标记
处数
文件号
签字
日期
标记
处数
文件号
签字
日期
标准检查
批准
XXXXX有限公司
熔模铸造工艺卡片
用户
产品代号
零件名称
零件代号
XXXXXX
壳体毛坯
XXXX
压制蜡模
材料
304L
蜡料
中温蜡
压蜡方法