溅镀系统
PVD(Sputter)介绍ppt

-
PVD(Sputter)介绍
1:PVD:即物理气相沉积(Physicql Vapor Deposition)的简称,包括真空蒸发镀膜,溅 射镀膜,离子束和离子助,外延膜沉积技术 等四大类. 2:PECVD:即等离子增强化学气相沉积
(Plasma-Enhanced Chmical vapor
-
PVD(Sputter)介绍
图2 Sputter溅镀模型
气体 固体
图3 Sputter溅镀后原子分子运动模型
-
图4 溅射原子弹性碰撞模型
PVD(Sputter)介绍
二、磁控溅镀相关知识: 1、物理依据:在磁感强度为B的磁场中,电荷
为q、运动速度为 v的带电粒子,所受的磁场力为F
称为洛仑兹力,F=qvXB 。如பைடு நூலகம்示
起辉时的发光过程解释如下: 当输入真空室的反应气体或溅镀气体被高速 旋转的电子碰撞后,气体与电子发生一系列 的解离、激发、附着等过程,由于部分电子 能量不足,便会把气体激发成亚稳态,
e + A → A* + e A* → A + hv (光子) 而亚稳态由于其外层电子的活跃性强,会回 到气体的稳定态,多余的能量就以光子的形 式释放出来。如图:
Deposition),其他还有LPCVD ,MOCVD, 等. APCVD
-
PVD(Sputter)介绍
一、Sputter(溅镀)定义及种类: 1、定义:所谓溅镀(Sputter)乃指物体以离子撞击时,被
溅射飞散出.具体过程:被电离之气体离子如Ar离子等受到阴 极加速快速与靶材表面撞击时,在靶材表面被电场所放出的 电子中和而呈中性,但仍保存其运动能量与植入靶材内部, 而靶材固体内部受此异离子植入而损伤其结晶,同时构成结 晶格的原子间相互重复碰撞,最终使表面的原子及分子被放 出至界外。如此原子大小的粒子从固体表面撞击分离而构成 离子,此称为溅镀(Sputter),又称电浆放电。如果将气体 加热至极高温或任其与高能量粒子相撞击,电子可由原分子 中释出,形成一带正负电粒子的集合体,称为电浆或等离子 体(Plasma);
溅镀的原理

3.2 当靶材变薄后,由于靶与透明片距离增加,所以成膜率将减少,请适时调整成膜率。
3.3 当仅溅镀一种材质的靶材时,请尽量降低透明片的温度以使溅镀粒子打到透明片上不致得到过多能量,因而破坏键结,又反弹回去(适用于CD、DVD)。但在镀多层膜时,镀第二层以上时即需提高温度以使溅镀面温度与尽量与溅镀粒子温度接近,增加界面间的平整性(适用于CD-RW、DVD-RAM)。
1、直流溅镀(DC Sputtering)原理:(适合导体材料的溅镀)
在真空溅镀舱中打入Ar,电极加数KV的直流电,因而产生辉光放电。辉光放电将产生Ar电浆,电浆中因阴极电位降而加速(阴极带负电荷),冲撞target表面,使target表面粒子溅射,溅射粒子沉积于substrate上,形成薄膜。
溅镀的原理 2007-01原理---转载整理
溅镀的原理:
主要利用辉光放电(glow discharge)将氩气(Ar)离子撞击靶材(target)表面, 靶材的原子被弹出而堆积在基板(substrate)表面形成薄膜。溅镀薄膜的性质、均匀度都比蒸镀薄膜来的好,但是镀膜速度却比蒸镀慢很多。新型的溅镀设备几乎都使用强力磁铁将电子成螺旋状运动以加速靶材周围的氩气离子化,造成靶与氩气离子间的撞击机率增加, 提高溅镀速率。一般金属镀膜大都采用直流溅镀,而不导电的陶磁材料则使用RF交流溅镀,基本的原理是在真空中利用辉光放电(glow discharge)将氩气(Ar)离子撞击靶材(target)表面,电浆中的阳离子会加速冲向作为被溅镀材的负电极表面,这个冲击将使靶材的物质飞出而沉积在基板上形成薄膜。
一般来说,利用溅镀制程进行薄膜披覆有几项特点:
(1)金属、合金或绝缘物均可做成薄膜材料。(2)在适当的设定条件下可将多元复杂的靶材制作出同一组成的薄膜。(3)利用放电气氛中加入氧或其它的活性气体,可以制作靶材物质与气体分子的混合物或化合物。(4)靶材输入电流及溅射时间可以控制,容易得到高精度的膜厚。(5)较其它制程利于生产大面积的均一薄膜。
Sputter溅镀原理

Sputter磁控溅镀原理Sputter在辞典中意思为:(植物)溅散。
此之所谓溅镀乃指物体以离子撞击时,被溅射飞散出。
因被溅射飞散的物体附著于目标基板上而制成薄膜。
在日光灯的插座附近常见的变黑现象,即为身边最赏见之例,此乃因日光灯的电极被溅射出而附著于周围所形成。
溅镀现象,自19世纪被发现以来,就不受欢迎,特别在放电管领域中尤当防止。
近年来被引用于薄膜制作技术效效佳,将成为可用之物。
薄膜制作的应用研究,当初主要为Bell Lab.及Western Electric公司,于1963年制成全长10m左右的连续溅镀装置。
1966年由IBM公司发表高周波溅镀技术,使得绝缘物之薄膜亦可制作。
后经种种研究至今已达“不管基板的材料为何,皆可被覆盖任何材质之薄膜”目的境地。
而若要制作一薄膜,至少需要有装置薄膜的基板及保持真空状况的道具(内部机构)。
这种道具即为制作一空间,并使用真空泵将其内气体抽出的必要。
一、真空简介:所谓真空,依JIS(日本工业标准)定义如下:较大气压力低的压力气体充满的特定的空真空单位相关知识如下:二、Sputter(磁控溅镀)原理:1、Sputter溅镀定义:在一相对稳定真空状态下,阴阳极间产生辉光放电,极间气体分子被离子化而产生带电电荷,其中正离子受阴极之负电位加速运动而撞击阴极上之靶材,将其原子等粒子溅出,此溅出之原子则沉积于阳极之基板上而形成薄膜,此物理现象即称溅镀。
而透过激发、解离、离子化……等反应面产生的分子、原子、受激态物质、电子、正负离子、自由基、UV 光(紫外光)、可见光……等物质,而这些物质混合在一起的状态就称之为电浆(Plasma )。
下图为Sputter 溅镀模型(类似打台球模型):图一中的母球代表被电离后的气体分子,而红色各球则代表将被溅镀之靶材(Si 、ITO&Ti 等),图二则代表溅镀后被溅射出的原子、分子等的运动情形;即当被加速的离子与表面撞击后,通过能量与动量转移过程(如图三),低能离子碰撞靶时,不能从固体表面直接溅射出原子,而是把动量转移给被碰撞的原子,引起晶格点阵上原子的链锁式碰撞。
溅射镀膜机原理
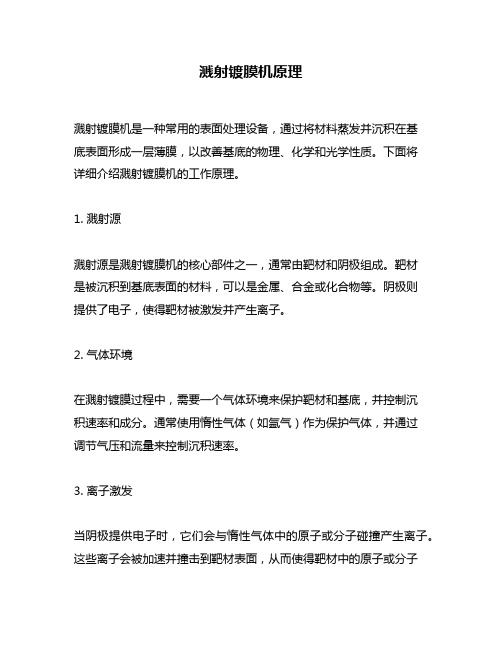
溅射镀膜机原理
溅射镀膜机是一种常用的表面处理设备,通过将材料蒸发并沉积在基
底表面形成一层薄膜,以改善基底的物理、化学和光学性质。
下面将
详细介绍溅射镀膜机的工作原理。
1. 溅射源
溅射源是溅射镀膜机的核心部件之一,通常由靶材和阴极组成。
靶材
是被沉积到基底表面的材料,可以是金属、合金或化合物等。
阴极则
提供了电子,使得靶材被激发并产生离子。
2. 气体环境
在溅射镀膜过程中,需要一个气体环境来保护靶材和基底,并控制沉
积速率和成分。
通常使用惰性气体(如氩气)作为保护气体,并通过
调节气压和流量来控制沉积速率。
3. 离子激发
当阴极提供电子时,它们会与惰性气体中的原子或分子碰撞产生离子。
这些离子会被加速并撞击到靶材表面,从而使得靶材中的原子或分子
被激发并蒸发。
4. 沉积过程
靶材蒸发的原子或分子会向基底表面沉积,并形成一层薄膜。
沉积速率可以通过调节气压、流量和离子能量等参数来控制。
同时,可以通过更换不同的靶材来改变沉积膜的成分和性质。
5. 监测和控制
在溅射镀膜过程中,需要对沉积速率、厚度和成分进行实时监测和控制。
通常使用压电晶体振荡器(Quartz Crystal Microbalance)来测量沉积速率和厚度,并使用光谱仪等设备来检测沉积膜的成分。
总之,溅射镀膜机是一种利用离子激发将靶材原子或分子沉积到基底表面形成一层薄膜的设备。
它具有高精度、高效率、可重复性好等优点,在电子、光学、太阳能等领域得到广泛应用。
溅镀原理
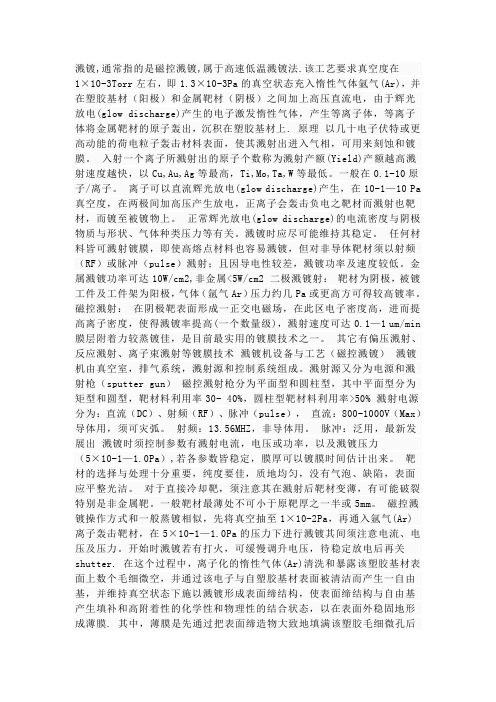
溅镀,通常指的是磁控溅镀,属于高速低温溅镀法.该工艺要求真空度在1×10-3Torr左右,即1.3×10-3Pa的真空状态充入惰性气体氩气(Ar),并在塑胶基材(阳极)和金属靶材(阴极)之间加上高压直流电,由于辉光放电(glow discharge)产生的电子激发惰性气体,产生等离子体,等离子体将金属靶材的原子轰出,沉积在塑胶基材上. 原理以几十电子伏特或更高动能的荷电粒子轰击材料表面,使其溅射出进入气相,可用来刻蚀和镀膜。
入射一个离子所溅射出的原子个数称为溅射产额(Yield)产额越高溅射速度越快,以Cu,Au,Ag等最高,Ti,Mo,Ta,W等最低。
一般在0.1-10原子/离子。
离子可以直流辉光放电(glow discharge)产生,在10-1—10 Pa 真空度,在两极间加高压产生放电,正离子会轰击负电之靶材而溅射也靶材,而镀至被镀物上。
正常辉光放电(glow discharge)的电流密度与阴极物质与形状、气体种类压力等有关。
溅镀时应尽可能维持其稳定。
任何材料皆可溅射镀膜,即使高熔点材料也容易溅镀,但对非导体靶材须以射频(RF)或脉冲(pulse)溅射;且因导电性较差,溅镀功率及速度较低。
金属溅镀功率可达10W/cm2,非金属<5W/cm2 二极溅镀射:靶材为阴极,被镀工件及工件架为阳极,气体(氩气Ar)压力约几Pa或更高方可得较高镀率。
磁控溅射:在阴极靶表面形成一正交电磁场,在此区电子密度高,进而提高离子密度,使得溅镀率提高(一个数量级),溅射速度可达0.1—1 um/min 膜层附着力较蒸镀佳,是目前最实用的镀膜技术之一。
其它有偏压溅射、反应溅射、离子束溅射等镀膜技术溅镀机设备与工艺(磁控溅镀)溅镀机由真空室,排气系统,溅射源和控制系统组成。
溅射源又分为电源和溅射枪(sputter gun)磁控溅射枪分为平面型和圆柱型,其中平面型分为矩型和圆型,靶材料利用率30- 40%,圆柱型靶材料利用率>50% 溅射电源分为:直流(DC)、射频(RF)、脉冲(pulse),直流:800-1000V(Max)导体用,须可灾弧。
PVD(Sputter)介绍
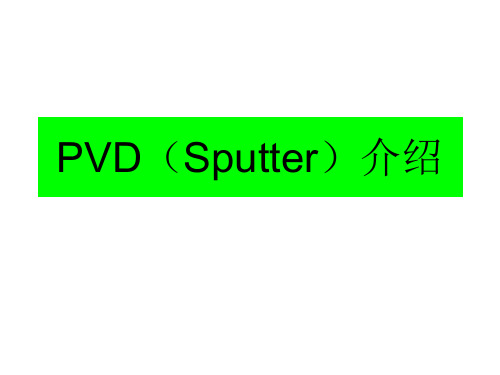
PVD(Sputter)介绍
3、Sputter Coating成膜过程:溅射过程 是以动量传递的离子轰击为基础的动力学过 程。具有高能量的入射离子与靶原子产生碰 撞,通过能量传递,使靶原子获得一定动能 之后脱离靶材表面飞溅出来。 从溅射靶中出来的沉积粒子入射基体表 面之后,在基体表面上形成吸附原子后,它 便失去了在表面法线方向的动能,只具有与 表面水平方向相平行运动的动能。依靠这种 动能,吸附原子在表面上作不同方向的表面 扩散运动.在表面扩散过程中,单个吸附原子 间相互碰撞形成原子对之后才能产生凝结。 经过吸附、凝结、表面扩散迁移、碰撞结合 形成稳定晶核。然后再通过吸附使晶核长大 成小岛,岛长大后互相联结聚结,最后形成 连续状薄膜。
PVD(Sputter)介绍
2、电浆放电系统种类:电浆放电系统可分为以下几种— —热电阻式、电子束式、直流溅射、射频溅射、离子溅射、 镭射剥镀、分子束磊晶系统、冷阴极电弧电浆沉积; 3、溅镀的模型:图2中的母球代表被电离后的气体分子, 而红色各球则代表将被溅镀之靶材(Si、ITO&Ti等),图3则 代表溅镀后被溅射出的原子、分子等的运动情形;即当被加 速的离子与表面撞击后,通过能量与动量转移过程(如图4), 低能离子碰撞靶时,不能从固体表面直接溅射出原子,而是 把动量转移给被碰撞的原子,引起晶格点阵上原子的链锁式 碰撞。这种碰撞将沿着晶体点阵的各个方向进行。同时,碰 撞因在原子最紧密排列的点阵方向上最为有效,结果晶体表 面的原子从邻近原子那里得到愈来愈大的能量,如果这个能 量大于原子的结合能,原子就从固体表面从各个方向溅射出 来;
PVD(Sputter)介绍
PVD(Sputter)介绍
1:PVD:即物理气相沉积(Physicql Vapor Deposition)的简称,包括真空蒸发镀膜,溅 射镀膜,离子束和离子助,外延膜沉积技术 等四大类. 2:PECVD:即等离子增强化学气相沉积 (Plasma-Enhanced Chmical vapor Deposition),其他还有LPCVD ,MOCVD, 等. APCVD
溅镀机介绍
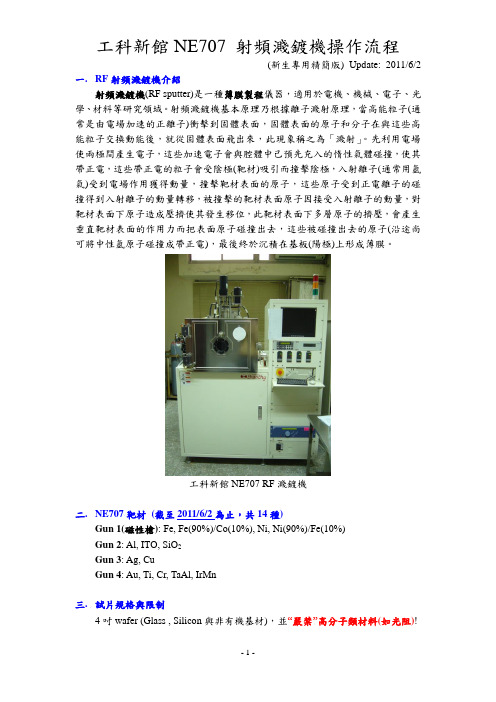
一.RF射頻濺鍍機介紹射頻濺鍍機(RF sputter)是一種薄膜製程儀器,適用於電機、機械、電子、光學、材料等研究領域。
射頻濺鍍機基本原理乃根據離子濺射原理,當高能粒子(通常是由電場加速的正離子)衝擊到固體表面,固體表面的原子和分子在與這些高能粒子交換動能後,就從固體表面飛出來,此現象稱之為「濺射」。
先利用電場使兩極間產生電子,這些加速電子會與腔體中己預先充入的惰性氣體碰撞,使其帶正電,這些帶正電的粒子會受陰極(靶材)吸引而撞擊陰極,入射離子(通常用氬氣)受到電場作用獲得動量,撞擊靶材表面的原子,這些原子受到正電離子的碰撞得到入射離子的動量轉移,被撞擊的靶材表面原子因接受入射離子的動量,對靶材表面下原子造成壓擠使其發生移位,此靶材表面下多層原子的擠壓,會產生垂直靶材表面的作用力而把表面原子碰撞出去,這些被碰撞出去的原子(沿途尚可將中性氬原子碰撞成帶正電),最後終於沉積在基板(陽極)上形成薄膜。
工科新館NE707 RF濺鍍機二.NE707靶材(截至2011/6/2為止,共14種)Gun 1(磁性槍): Fe, Fe(90%)/Co(10%), Ni, Ni(90%)/Fe(10%)Gun 2: Al, ITO, SiO2Gun 3: Ag, CuGun 4: Au, Ti, Cr, TaAl, IrMn三.試片規格與限制4吋wafer (Glass , Silicon與非有機基材),並“嚴禁”高分子類材料(如光阻)!四.濺鍍機操作步驟與注意事項:1.訓練並考核通過,並取得門禁許可與濺鍍機專用帳號/密碼。
PS.實驗室網頁下載並填寫“考核表”,依表上規定進行訓練與考核。
合格使用者聯絡資訊張貼於NE707門上。
2.預約時段→閱讀並遵守黑板上張貼最新公告→留意白板上靶材更換狀況。
3.填寫使用紀錄簿,點選電腦桌面捷徑軟體,登入帳號/密碼。
4.檢查機台狀況(全亮綠燈!)。
5.確定Gun與靶材位置對位(歸零)。
溅镀讲解
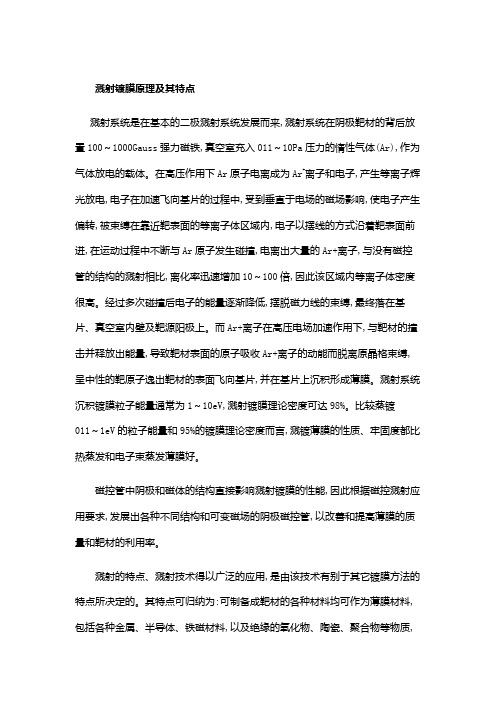
溅射镀膜原理及其特点溅射系统是在基本的二极溅射系统发展而来,溅射系统在阴极靶材的背后放置100~1000Gauss强力磁铁,真空室充入011~10Pa压力的惰性气体(Ar),作为气体放电的载体。
在高压作用下Ar原子电离成为Ar+离子和电子,产生等离子辉光放电,电子在加速飞向基片的过程中,受到垂直于电场的磁场影响,使电子产生偏转,被束缚在靠近靶表面的等离子体区域内,电子以摆线的方式沿着靶表面前进,在运动过程中不断与Ar原子发生碰撞,电离出大量的Ar+离子,与没有磁控管的结构的溅射相比,离化率迅速增加10~100倍,因此该区域内等离子体密度很高。
经过多次碰撞后电子的能量逐渐降低,摆脱磁力线的束缚,最终落在基片、真空室内壁及靶源阳极上。
而Ar+离子在高压电场加速作用下,与靶材的撞击并释放出能量,导致靶材表面的原子吸收Ar+离子的动能而脱离原晶格束缚,呈中性的靶原子逸出靶材的表面飞向基片,并在基片上沉积形成薄膜。
溅射系统沉积镀膜粒子能量通常为1~10eV,溅射镀膜理论密度可达98%。
比较蒸镀011~1eV的粒子能量和95%的镀膜理论密度而言,溅镀薄膜的性质、牢固度都比热蒸发和电子束蒸发薄膜好。
磁控管中阴极和磁体的结构直接影响溅射镀膜的性能,因此根据磁控溅射应用要求,发展出各种不同结构和可变磁场的阴极磁控管,以改善和提高薄膜的质量和靶材的利用率。
溅射的特点、溅射技术得以广泛的应用,是由该技术有别于其它镀膜方法的特点所决定的。
其特点可归纳为:可制备成靶材的各种材料均可作为薄膜材料,包括各种金属、半导体、铁磁材料,以及绝缘的氧化物、陶瓷、聚合物等物质,尤其适合高熔点和低蒸汽压的材料沉积镀膜;在适当条件下多元靶材共溅射方式,可沉积所需组分的混合物、化合物薄膜;在溅射的放电气氛中加入氧、氮或其它活性气体,可沉积形成靶材物质与气体分子的化合物薄膜;控制真空室中的气压、溅射功率,基本上可获得稳定的沉积速率,通过精确地控制溅射镀膜时间,容易获得均匀的高精度的膜厚,且重复性好;溅射粒子几乎不受重力影响,靶材与基片位置可自由安排;基片与膜的附着强度是一般蒸镀膜的10倍以上,且由于溅射粒子带有高能量,在成膜面会继续表面扩散而得到硬且致密的薄膜,同时高能量使基片只要较低的温度即可得到结晶膜;薄膜形成初期成核密度高,故可生产厚度10nm以下的极薄连续膜。
- 1、下载文档前请自行甄别文档内容的完整性,平台不提供额外的编辑、内容补充、找答案等附加服务。
- 2、"仅部分预览"的文档,不可在线预览部分如存在完整性等问题,可反馈申请退款(可完整预览的文档不适用该条件!)。
- 3、如文档侵犯您的权益,请联系客服反馈,我们会尽快为您处理(人工客服工作时间:9:00-18:30)。
濺鍍系統
原理:
主要利用輝光放電(glow discharge)將氬氣(Ar)離子撞擊靶材(target)表面,靶材的原子被彈出而堆積在基板表面形成薄膜。濺鍍薄膜的性質、均勻度都比蒸鍍薄膜來的好,但是鍍膜速度卻比蒸鍍慢很多。若靶材為金屬,則使用DC(直流)電場即可;若為非金屬,則因靶材表面會累積正電荷,導致往後之正離子與之相斥而無法繼續吸引正離子,使得濺鍍無法進行,所以,改為RF電場(因場的振盪頻率變化太快,使得正離子跟不上變化,而讓RF in的地方呈現陰極效應)即可解決問題。
6.濺射粒子幾不受重力影響,靶材與基板位置可自由安排。
7.基板與膜的附著強度是一般蒸鍍膜的10倍以上,且由於濺射粒子帶有高能量,在成膜面會繼續表面擴散而得到硬且緻密的薄膜,同時此高能量使基板只要較低的溫度即可得到結晶膜。
8.薄膜形成初期成核密度高,可生產10nm以下的極薄連續膜。
9.靶材的壽命長,可長時間自動化連續生產。
一般來說,利用濺鍍製程進行薄膜披覆有幾項特點:
1.金屬、合金或絕緣物雜的靶材製作出同一組成的薄膜。
3.利用放電氣氛中加入氧或其他的活性氣體,可以製作靶材物質與氣體分子的混合物或化合物。
4.靶材輸入電流及濺射時間可以控制,容易得到高精度的膜厚。
5.較其他製程利於生產大面積的均一薄膜。