钢制安全壳
AP1000钢制安全壳封头板加热均匀性控制研究
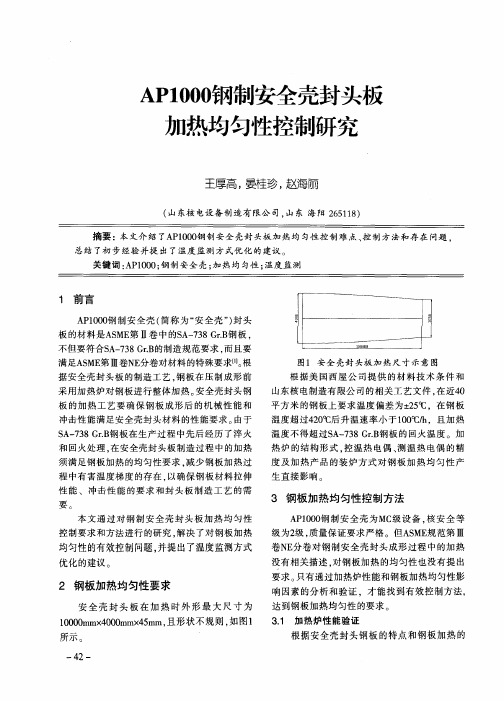
钢 板 表 面 的测 温 热 电偶 是钢 板 加 热 温 度 的 直接显 示部 件 , 只有 它们 的灵 敏度 、 安装 方式 、 布 置数量 和 安装位 置合 理 . 能客观 的反 映整 张 钢 才
1 底层 钢板 与燃 气 喷嘴之 间 的距离 ) 进 行 加 热 的安 全 壳 封 头 板 放 置 在加 热 喷 嘴 的上方 , 果底 层钢 板距 离燃 气 喷嘴 过 近 , 么 , 如 那 由于燃 气喷 嘴 喷出 的火焰 呈放 射 状 , 就易 于造 成 钢 板表 面温 度 的不均 匀 。根据 A ME S 规范 第 Ⅲ卷
工艺 , 加热 炉提 出 了 以下 基本 要求 : 对 1 )加热 炉应 满足 安全 壳 封头 钢板 加 热所 需
的尺寸、 有效 容 积 、 热功 率 、 热 速 度 、 温 精 加 加 控 2 钢板 层 间间距 和支 架形式 )
根 据加 热工 艺 和产能 要求 ,对 3 安全 壳封 层 头 钢板 进行 同时 加热 。 钢板 层 间间距 和支撑 支架
要。
度 及 加 热产 品 的装 炉 方 式对 钢 板加 热 均 匀 性 产
生直接 影 响 。
3 钢板加热均匀性控制方法
A 10 钢 制 安 全壳 为MC 设 备 。 安 全 等 P 00 级 核
本 文 通过 对 钢制 安 全 壳 封 头板 加 热 均 匀 性 控 制要求 和方 法进 行 的研 究 , 解决 了对 钢板 加 热
核电站钢制安全壳焊接质量控制
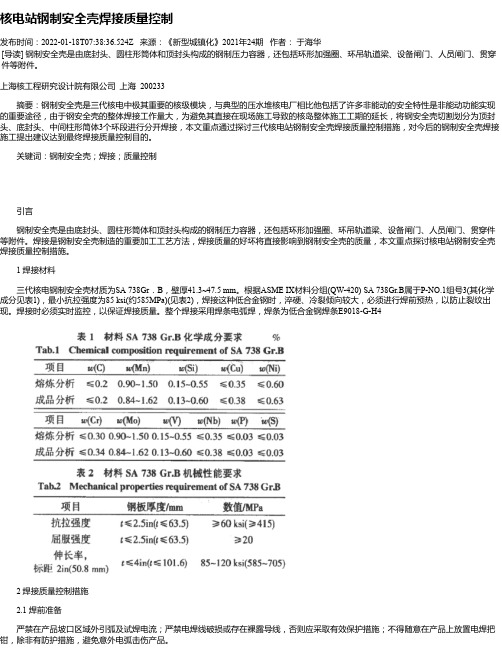
核电站钢制安全壳焊接质量控制发布时间:2022-01-18T07:38:36.524Z 来源:《新型城镇化》2021年24期作者:于海华[导读] 钢制安全壳是由底封头、圆柱形筒体和顶封头构成的钢制压力容器,还包括环形加强圈、环吊轨道梁、设备闸门、人员闸门、贯穿件等附件。
上海核工程研究设计院有限公司上海 200233摘要:钢制安全壳是三代核电中极其重要的核级模块,与典型的压水堆核电厂相比他包括了许多非能动的安全特性是非能动功能实现的重要途径,由于钢安全壳的整体焊接工作量大,为避免其直接在现场施工导致的核岛整体施工工期的延长,将钢安全壳切割划分为顶封头、底封头、中间柱形筒体3个环段进行分开焊接,本文重点通过探讨三代核电站钢制安全壳焊接质量控制措施,对今后的钢制安全壳焊接施工提出建议达到最终焊接质量控制目的。
关键词:钢制安全壳;焊接;质量控制引言钢制安全壳是由底封头、圆柱形筒体和顶封头构成的钢制压力容器,还包括环形加强圈、环吊轨道梁、设备闸门、人员闸门、贯穿件等附件。
焊接是钢制安全壳制造的重要加工工艺方法,焊接质量的好坏将直接影响到钢制安全壳的质量,本文重点探讨核电站钢制安全壳焊接质量控制措施。
1 焊接材料三代核电钢制安全壳材质为SA 738Gr.B,壁厚41.3~47.5 mm。
根据ASME IX材料分组(QW-420) SA 738Gr.B属于P-NO.1组号3(其化学成分见表1),最小抗拉强度为85 ksi(约585MPa)(见表2),焊接这种低合金钢时,淬硬、冷裂倾向较大,必须进行焊前预热,以防止裂纹出现。
焊接时必须实时监控,以保证焊接质量。
整个焊接采用焊条电弧焊,焊条为低合金钢焊条E9018-G-H42 焊接质量控制措施2.1 焊前准备严禁在产品坡口区域外引弧及试焊电流;严禁电焊线破损或存在裸露导线,否则应采取有效保护措施;不得随意在产品上放置电焊把钳,除非有防护措施,避免意外电弧击伤产品。
CAP1400钢制安全壳贯穿件套筒与插入板组件直接目视检验

CAP1400钢制安全壳贯穿件套筒与插入板组件直接目视检验摘要:CAP1400钢制安全壳是非能动冷却系统的一个重要组成部分,其贯穿件套筒与插入板组件的焊接为安全壳焊接过程中的难点之一。
通过对产品焊接前、中、后全过程进行直接目视检验,发现其存在的焊接质量问题并对其分析,找出解决问题的可行性措施,从而提高组件焊接质量。
关键词:贯穿件套筒与插入板组件;直接目视检验;焊接质量引言:CAP1400钢制安全壳(containment vessel,CV)由5个主要模块组成,底封头、筒体第一环、第二环、第三环和顶封头组成, 安全壳内部包含内、外环形加强圈,环吊梁,设备闸门,人员闸门,贯穿件和其他附件。
其中贯穿件套筒及插入板组件作为安全壳附件,作用是贯通安全壳筒体,便于安全壳内外通电缆、管道等。
CAP1400钢制安全壳贯穿件套筒和插入板组件的制造采用工厂化预制、现场拼装的模式,目视检验方法采用直接目视检验,贯穿到焊接作业的全过程,包括焊接前准备阶段的目视检验、焊接过程中的目视检验、焊接后表面质量缺陷检验三大方面。
1.检验要求检验技术执行ASME规范第Ⅲ卷NE5000和第Ⅴ卷的规定,验收标准执行SNG-NDE-V7-507/0《焊缝目视检测技术条件》;人员资质符合HAF602的要求;检验用设备均在标定合格有效期内;检验时能分辨出反射率为18%的中性灰度卡上0.8mm宽的黑线,应在大于1000lux的照度下进行观察,如果自然环境达不到要求必须借助一些照明设备达到要求,被检物与眼睛的距离小于600mm,视线与检测面的夹角大于30°。
2.焊接各环节直接目视检验要点及存在问题与解决措施2.1焊接前目视检验要点及存在问题与解决措施2.1.1焊接前先决条件检查组件焊接前,对先决条件进行确认,包括“人、机、料、法、环”等因素:所有从事对质量有影响的工作人员必须完成相应的培训并且考核合格的,NDE人员必须按照HAF602的要求取得相应的资质证书,从事此次焊接的焊工必须按照HAF603的要求完成相应的资格评定,并取得相应的资格证书。
核电钢制安全壳SA738 Gr.B搭接接头裂纹成因分析
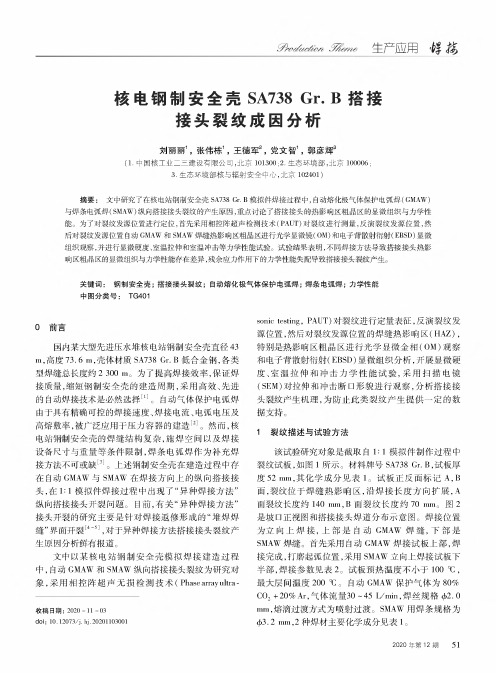
生产应用,殍核电钢制安全壳SA738 G'.B 搭接接头裂纹成因分析1,1,2,党文 1,3(1.中国核工业二三建设有限公司,北京101300 #2.生态环境部,北京100006 3.生态环境部核与辐射安全中心,北京102401)摘要:文中研究了在核电站钢制安全壳SA738 Gr.B 模拟件焊接过程中,自动熔化极气体保护电弧焊(GMAW )与焊条电弧焊(SMAW "纵向搭接接头裂纹的产生原因,重点 了搭接接头的 的显微组织 学性能。
为了对裂纹发源位置进行定位,首先采用相控阵超声检测技术! PAUT )对裂纹进行测量,反演裂纹发源位置,然对裂纹发源位置自动GMAW 和SMAW 焊进行光学显微镜(OM )和电子背(EBSD )显组织观察,并进行显 、室温拉伸和室温冲击 学% 结 ,不同焊接接接 影的显微组织 学 ,残余应作用下的力学 失接接 纹 %关键词:钢制安全壳;搭接接头裂纹;自动熔化极气体保护电弧焊;焊条电弧焊;力学性能中图分类号:TG4010 前言型先进压水堆核电站钢制径43叫 73.6 m , 质SA738 Gr. B 低合金,各类 型焊约2 300 m 。
为了 焊接 ,保证焊接质量,缩 制 的建造周期,采用 、先进的自动焊接 是必然选择[1]%自动气体保护电弧焊由于具 确可控的焊接、焊接电流、电弧电压及高熔敷率, 应用于压力容器的建造然而,核电 制的焊缝结构复杂,施焊空间以及焊接备尺寸量 件限制,焊 电弧焊作 充焊接 上述钢制 造过程中存自动GMAW 与SMAW 在焊接方向上的纵向搭接接 ,1:1模 件焊接过程中 了“异种焊接 ”向搭接接问题。
,“种焊接 ”接 的研究主要是针对焊接 形成的“堆焊焊”界面 [4'5],对于异种焊接接接 纹产生原因分析 报道。
文中以某核电站钢制模拟焊接建造过程中,自动GMAW 和SMAW 纵向搭接接 纹为研究对,用相控阵超声无损检(Phase array ultra -收稿日期:2020 -11 -03doi : 10.12073/j. hj. 202011030012020年第#期 51sonic testing ,PAUT )对裂纹进行疋量表征,反演裂纹发源位置,然后对裂纹发源位置的焊缝热影响区(HAZ ),特别是进行光学显微金相(OM )观察和电子背(EBSD )显 组织分析, 显度、室温拉伸和冲击力学 ,采用扫描电镜(SEM )对拉伸和冲击断口形貌进行观察,分析搭接接纹 机理, 类裂纹 定的数据 %1裂纹描述与试验方法该研究对象是截取自1:模拟件制作过程中裂纹试板,如图1所示。
安全壳介绍概述.
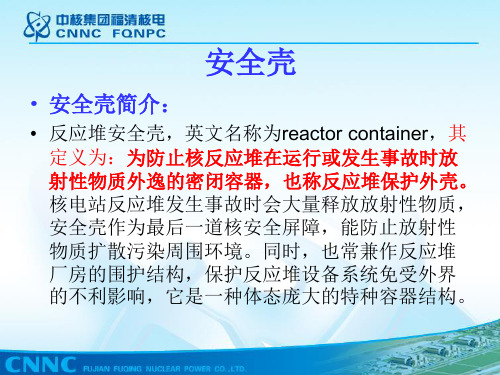
• 福建福清核电安全壳形式: • 安全壳多数为顶部为球型的圆柱体预应力钢筋混 凝土建筑物。内衬6mm的钢板密封层,目前国际 上主要的安全壳都属于这种结构。福建福清核电 厂的反应堆安全壳是一座由钢筋混凝土底板、立 式预应力混凝土筒壁和准球型预应力混凝土穹顶 三部分组成的封闭预应力混凝土结构。安全壳为 后张法施工的预应力钢筋混凝土结构,内侧有钢 衬里,形成一个圆柱状的密封空腔。安全壳内径 为37米,外径38.8米,筒身厚度为0.9米,筒身表 面为6mm厚的碳钢衬里,筒身部分由后张拉系统 用水平和垂直钢绞束产生预应力。标准段筒身高 度为45.75m,外圆周上均匀布置四个扶壁柱(扶 壁柱与筒身高度一致)。
• 在预应力安全壳中,事故压力荷载是由大量的双向预应力 钢束承受的,因此,安全壳结构不会出现脆性破坏,设计 压力也可不受限制,受力比较安全可靠。此外,不少的安 全壳还采用不灌浆无粘接的预应力配筋,便于对预应力钢 束作定期的检查和补张拉以及作必要的更换。因此自70年 代以后,在世界各国的轻水堆和重水堆核电站建设中普遍 采用。(80万千瓦核电站的预应力安全壳约需混凝土 14000米,预应力钢束近1000吨,施工期约需2~3年。)
• 安全壳的作用: • 安全壳是核电站的第三道安全屏障,在正常运行 时或失水事故(LOCA)造成的温度和压力下, 保证释放到环境的放射性物质在允许的限制内。 安全壳能够承受龙卷风、地震、海啸等自然灾害, 能承受外来飞击物的冲击,无论在以上各种恶劣 环境条件下,安全壳应具有良好的密封性和承受 失水事故压力的结构抗力。
• 安全壳的要求: • 根据《中华人民共和国核行业标准》EJ/T 926-95 规定,安全壳的设计必须满足强度和密封性的要 求:
• 安全壳的结构和类型: • 按照安全壳层数的区别,可分为单层安全壳和双 层安全壳。双层安全壳起密封作用的还是内层, 外层主要是防飞击物的撞击,保证反应堆堆芯的 安全。反应堆运行时安全壳内外层之间为负压, 即使内壳有泄漏时,放射性物质也不至于向外泄 漏。所以双层安全壳比单层更安全,缺点就是成 本相对较高。
钢制安全壳老化机理分析及AP1000防护措施初探

主 [ 3 1 。
1 引 言
p tc 、 ytr re 等 核 电厂也 曾发生过 安 全壳 a i O s ek rk eC 涂层 降质 . 部分 电厂 还伴 随有局 部 点腐蚀 等 老化 现象 。
腐 蚀 类 型对 钢 制 安全 壳 最 大 的危 害是 减 小 其 截 面面积 , 导致 其承 载力下 降 , 至发 生泄漏 。 甚 由于
材料 自身 的老化 ; 另一 类是 外部 环境 因素 对涂 层 的直 接破 坏作用 。 涂层 材料 在服役 期 间有可 能受 到高 温 、 氧化 、 辐照等 因素 的影 响 。 导致其 性 能逐 渐劣 化 。 此外 , 气 、 空 水及 其他 化学 物质对 涂层 的 侵蚀 , 以及 机械摩 擦或 碰撞 都有 可能 对涂 层造 成 直接 损害 。这两 类原 因都会 导致 涂层 产生 剥 落 、
部泄漏三种 , 中尤以壳体腐蚀最为常见。 其
21 壳体 腐蚀 .
图1 三种 腐蚀 速 率模 型
. —
4 . 5—
骸电 工程与 技木 2 1 0 1年笫 4期
均匀 腐蚀 并 不 改 变材 料 的化 学成 分 以及 晶 体结构 , 只是 均匀 地 减小 构 件 的厚 度 , 因此 这 种
02 . %的碳 钢 暴 露 在 空气 中时 也可 以在表 面 形成
素及 材料 自身 性 质的原 因 ,有 可能 发 生腐 蚀 、 降
质 、 部 泄漏 等 老 化 现 象 . 致 安 全壳 的承 载 能 局 导 力 及 密封 性 降低 。 因此必 须 在安 全壳 服役 期 间开
核能工程中的安全壳设计与实践经验总结
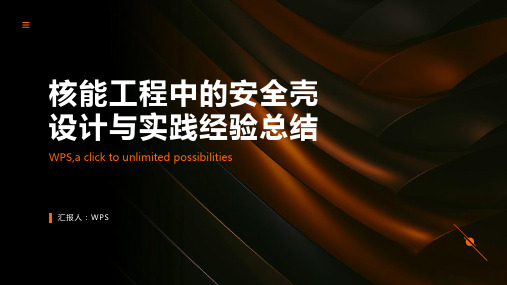
解决方案:采用先进的施工技术和设备,如盾 构机、顶管机等,提高施工效率和质量。
问题:安全壳施工过程中可能会遇到工期延误、 成本超支等问题。
问题:安全壳施工过程中可能会遇到环境污染、 辐射防护等问题。
解决方案:加强项目管理和成本控制,采用先 进的施工技术和设备,提高施工效率和质量, 确保工期和成本可控。
监测系统:安装辐 射监测系统,实时 监测安全壳内的辐 射水平
安全壳的防震与抗爆设计
防震设计:采用高强度钢 筋混凝土结构,提高抗震 能力
抗爆设计:采用双层安全 壳结构,内层为钢筋混凝 土,外层为钢结构
安全壳厚度:根据核反应 堆类型和规模,确定安全 壳厚度
安全壳密封性:采用密封 材料和密封技术,确保安 全壳密封性
安全壳技术的发展:新材料、新工 艺、新设计理念的应用
安全壳在核能工程中的地位:成为 核能工程中的核心组成部分
添加标题
添加标题
添加标题
添加标题
安全壳设计的优化:提高安全性、 可靠性、经济性
安全壳技术的推广:在全球范围内 推广应用,提高核能工程的安全性 和可靠性
安全壳与其他安全设施的协同发展策略
安全壳与其他安全设施的协同作用 安全壳与其他安全设施的协同设计 安全壳与其他安全设施的协同实践经验 安全壳与其他安全设施的协同发展趋势与展望
安全壳设计与建设的国际合作与交流
国际合作:各国在 安全壳设计与建设 方面的合作与交流
技术共享:各国在 安全壳设计与建设 方面的技术共享与 合作
经验交流:各国在 安全壳设计与建设 方面的经验交流与 合作
合作项目:各国在 安全壳设计与建设 方面的合作项目与 成果
感谢您的观看
汇报人:WPS
应急响应组织与协调机制
例析安全壳整体泄漏率试验

例析安全壳整体泄漏率试验1 概述安全壳作为核电站的第三道安全屏障,在正常运行时及失水事故(LOCA)造成的温度和压力下,均应保证具有规定的密封性。
在机组投入运行前,安全壳要承受一次被称为预运行的整体泄漏率试验(Integrated Leakage Rate Test,ILRT,又称为A类试验),主要目的是模拟设计基准事故下测量和计算安全壳的泄漏率,以确保安全壳的密封性符合法规要求。
目前国内运营核电厂安全壳均为预应力混凝土式结构,钢制安全壳也是首次运用,对该项试验的研究尚属起步阶段。
本文在初步介绍了试验要求、试验方法的基础上,分析了国内首次钢制安全壳整体泄漏率试验的特点,探讨了试验的难点和风险,以期为国内首次试验执行提供参考与指导。
2 AP1000整体泄漏率试验要求AP1000安全壳为钢制结构,除了在事故工况限制裂变产物的释放外,还与非能动安全壳冷却系统一起将壳内的热量传递给壳外最终热阱——大气。
AP1000安全壳参数如表1所示:2.1 试验准备ILRT试验时要向安全壳内充压到设计压力0.407MPa(表压,称为Pd),安全壳内许多仪器设备无法承受这个压力,需要进行技术处理,系统或设备需要隔离等,因此,执行该试验前需做大量的准备工作。
以下列出了一些重要准备工作:(1)设计基准事故后需暴露在大气环境下的工艺系统已按照要求排空并打开对空;(2)一回路主冷却剂系统液位应降到热段半管液位或更低;(3)安全壳内不能承受设计基准事故压力的物项已被移除或者隔离,如仪表盘等;(4)安全壳内已清除易燃易爆的物品,对已承压容器进行降压或者对空;(5)试验用仪器仪表已按照要求安装好;(6)所有安全壳隔离阀已处于关闭状态;(7)安全壳压力高触发的仪控逻辑控制已被闭锁;(8)已完成试验前的安全壳检查,对于发现的任何影响到安全壳结构完整性或者泄漏密封性的结构退化需在试验前进行修复和再确认。
2.2 试验设备安全壳临时空气供给设备包:(1)至少包括3台空气压缩机,能提供0.689MPa(表压)的无油空气,流量10194m3/hr;(2)一组空气干燥器,总容量能处理上述流量的空气流;(3)空气过滤机组,总能力能处理上述流量的空气流。
CAP1000_核岛CV_底封头A_层钢筋模块化施工技术
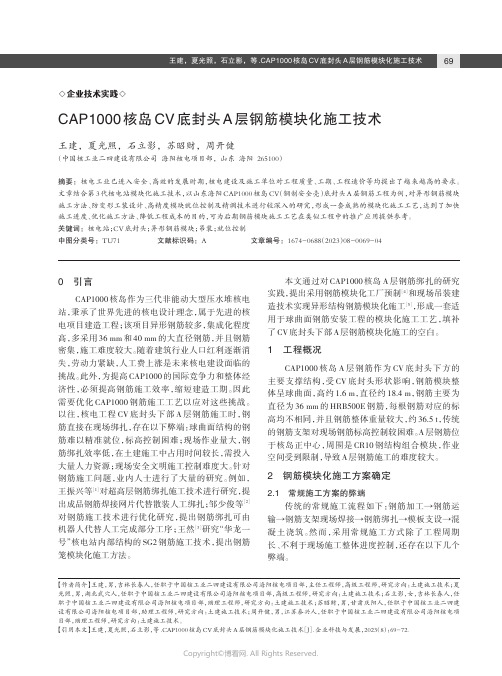
0引言CAP1000核岛作为三代非能动大型压水堆核电站,秉承了世界先进的核电设计理念,属于先进的核电项目建造工程;该项目异形钢筋较多,集成化程度高,多采用36mm 和40mm 的大直径钢筋,并且钢筋密集,施工难度较大。
随着建筑行业人口红利逐渐消失,劳动力紧缺,人工费上涨是未来核电建设面临的挑战。
此外,为提高CAP1000的国际竞争力和整体经济性,必须提高钢筋施工效率,缩短建造工期。
因此需要优化CAP1000钢筋施工工艺以应对这些挑战。
以往,核电工程CV 底封头下部A 层钢筋施工时,钢筋直接在现场绑扎,存在以下弊端:球曲面结构的钢筋难以精准就位,标高控制困难;现场作业量大,钢筋绑扎效率低,在土建施工中占用时间较长,需投入大量人力资源;现场安全文明施工控制难度大。
针对钢筋施工问题,业内人士进行了大量的研究。
例如,王振兴等[1]对超高层钢筋绑扎施工技术进行研究,提出成品钢筋焊接网片代替散装人工绑扎;邹少俊等[2]对钢筋施工技术进行优化研究,提出钢筋绑扎可由机器人代替人工完成部分工序;王然[3]研究“华龙一号”核电站内部结构的SG2钢筋施工技术,提出钢筋笼模块化施工方法。
本文通过对CAP1000核岛A 层钢筋绑扎的研究实践,提出采用钢筋模块化工厂预制[4]和现场吊装建造技术实现异形结构钢筋模块化施工[5],形成一套适用于球曲面钢筋安装工程的模块化施工工艺,填补了CV 底封头下部A 层钢筋模块化施工的空白。
1工程概况CAP1000核岛A 层钢筋作为CV 底封头下方的主要支撑结构,受CV 底封头形状影响,钢筋模块整体呈球曲面,高约1.6m ,直径约18.4m ,钢筋主要为直径为36mm 的HRB500E 钢筋,每根钢筋对应的标高均不相同,并且钢筋整体重量较大,约36.5t ,传统的钢筋支架对现场钢筋标高控制较困难。
A 层钢筋位于核岛正中心,周围是CR10钢结构组合模块,作业空间受到限制,导致A 层钢筋施工的难度较大。
核电站钢制安全壳SA-738 Gr.B的焊接工艺
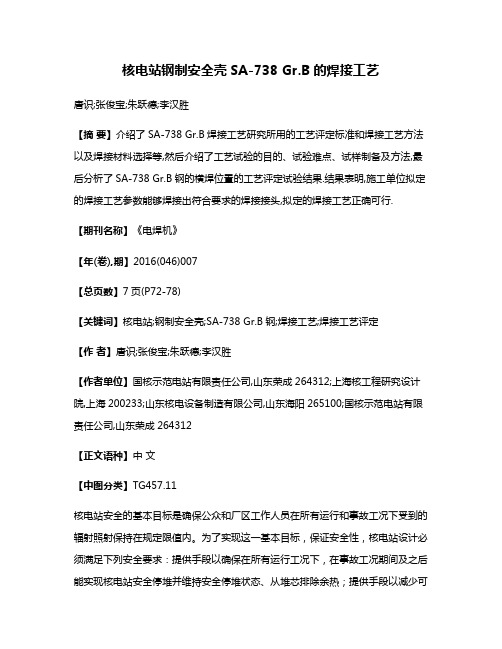
核电站钢制安全壳SA-738 Gr.B的焊接工艺唐识;张俊宝;朱跃德;李汉胜【摘要】介绍了SA-738 Gr.B焊接工艺研究所用的工艺评定标准和焊接工艺方法以及焊接材料选择等,然后介绍了工艺试验的目的、试验难点、试样制备及方法,最后分析了SA-738 Gr.B钢的横焊位置的工艺评定试验结果.结果表明,施工单位拟定的焊接工艺参数能够焊接出符合要求的焊接接头,拟定的焊接工艺正确可行.【期刊名称】《电焊机》【年(卷),期】2016(046)007【总页数】7页(P72-78)【关键词】核电站;钢制安全壳;SA-738 Gr.B钢;焊接工艺;焊接工艺评定【作者】唐识;张俊宝;朱跃德;李汉胜【作者单位】国核示范电站有限责任公司,山东荣成264312;上海核工程研究设计院,上海200233;山东核电设备制造有限公司,山东海阳265100;国核示范电站有限责任公司,山东荣成264312【正文语种】中文【中图分类】TG457.11核电站安全的基本目标是确保公众和厂区工作人员在所有运行和事故工况下受到的辐射照射保持在规定限值内。
为了实现这一基本目标,保证安全性,核电站设计必须满足下列安全要求:提供手段以确保在所有运行工况下,在事故工况期间及之后能实现核电站安全停堆并维持安全停堆状态、从堆芯排除余热;提供手段以减少可能的放射性物质释放,确保在运行工况期间和之后的任何释放不超过规定的限值,同时,确保在事故工况期间及之后的任何释放不超过可接受的限值。
为此,核电站设计中设置了三道反应堆安全屏障。
钢制安全壳是阻止放射性物质向环境逸散的最后一道屏障,钢制安全壳的质量将直接影响到核电站的核安全,焊接是钢制安全壳制造的重要加工工艺方法,焊接质量的好坏将直接影响到钢制安全壳的质量,焊接工艺评定是确保钢制安全壳焊接质量的前提。
1.1 标准选择要验证施工单位拟定的焊接工艺的正确性,评价施工单位能否焊接出符合标准要求的焊接接头,首先需要明确的是焊接工艺评定试验的标准。
碳当量对钢制安全壳附件板焊接质量的影响
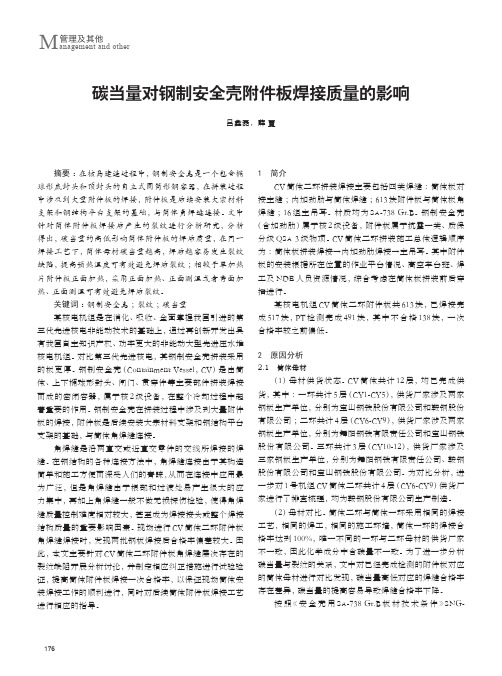
管理及其他M anagement and other碳当量对钢制安全壳附件板焊接质量的影响吕鑫磊,薛 覃摘要:在核岛建造过程中,钢制安全壳是一个包含椭球形底封头和顶封头的自立式圆筒形钢容器,在拼装过程中涉及到大量附件板的焊接,附件板是后续安装大宗材料支架和钢结构平台支架的基础,与筒体角焊缝连接。
文中针对筒体附件板焊接后产生的裂纹进行分析研究,分析得出,碳当量的高低影响筒体附件板的焊后质量,在同一焊接工艺下,筒体母材碳当量越高,焊后越容易发生裂纹缺陷,提高预热温度可有效避免焊后裂纹;相较于单加热片附件板正面加热,采用正面加热、正面测温或者背面加热、正面测温可有效避免焊后裂纹。
关键词:钢制安全壳;裂纹;碳当量某核电机组是在消化、吸收、全面掌握我国引进的第三代先进核电非能动技术的基础上,通过再创新开发出具有我国自主知识产权、功率更大的非能动大型先进压水堆核电机组。
对比第三代先进核电,其钢制安全壳拼装采用的板更厚。
钢制安全壳(Containment Vessel,CV)是由筒体、上下椭球形封头、闸门、贯穿件等主要部件拼装焊接而成的密闭容器,属于核2级设备,在整个冷却过程中起着重要的作用。
钢制安全壳在拼装过程中涉及到大量附件板的焊接,附件板是后续安装大宗材料支架和钢结构平台支架的基础,与筒体角焊缝连接。
角焊缝是沿两直交或近直交零件的交线所焊接的焊缝。
在钢结构的各种连接方法中,角焊缝连接由于其构造简单和施工方便而深受人们的青睐,从而在连接中应用最为广泛,但是角焊缝由于根部和过渡处易产生很大的应力集中,再加上角焊缝一般不做无损探伤检验,使得角焊缝质量控制难度相对较大,甚至成为焊接接头或整个焊接结构质量的重要影响因素。
现场进行CV筒体二环附件板角焊缝焊接时,发现两批钢板焊接后合格率偏差较大。
因此,本文主要针对CV筒体二环附件板角焊缝屡次存在的裂纹缺陷开展分析讨论,并制定相应纠正措施进行试验验证,提高筒体附件板焊接一次合格率,以保证现场筒体安装焊接工作的顺利进行,同时对后续筒体附件板焊接工艺进行相应的指导。
徐大堡核电工程CV筒体焊接总结

徐大堡核电工程CV筒体焊接总结摘要:本文介绍了徐大堡核电工程CV筒体的焊接工艺、焊接顺序、焊接施工过程控制要求、焊接施工难度及注意事项等,为后续AP1000堆型CV筒体焊接质量控制提供了一定经验。
关键词:CV筒体焊接质量控制注意事项1、工程概况徐大堡核电工程钢制安全壳(CV)拼装执行ASME标准2001版+2002补遗。
筒体板材质为SA-738Gr.B,内直径为39624mm,总高为42735mm,由11圈板组成,分三环拼装,三环分别为4圈+4圈+3圈,每圈由12块环板组成。
筒体与底封头/顶封头共同构成完整的钢制安全壳,形成核岛防泄漏的一道屏障。
目前施工区域为一环4圈环板的焊接施工。
其中底环板厚47.6mm,高3905mm,其余环板厚44.5mm,高3883mm。
2、焊接工艺介绍筒体焊接的焊接方法为焊条电弧焊(SMAW),焊材选择E9018-G-H4的焊条。
环缝12条(包括与封头相焊的两条环缝),约1495m、纵缝121条,约513m,均是双面坡口熔透焊缝。
根据ASME Ⅸ材料分组(QW-420)可知,SA-738 Gr.B属于P-NO.1组3,最小抗拉强度为85ksi(约585MPa),焊接这种碳钢时,淬硬、冷裂倾向较大,必须进行焊前预热,以防止裂纹出现。
焊接时须实时监控,以保证焊接质量。
3、焊接施工过程介绍3.1组对定位焊后间隙为0~5mm时,不作处理可正常焊接,对于间隙在5~10mm时,焊接时使用陶瓷衬垫或SA-738 Gr.B材料的衬垫。
焊接坡口组对错边量的要求:焊接坡口尺寸公差应符合焊接工艺的要求,纵缝错边量≤3.2mm,环缝错边量≤5.6mm,并且定位焊完成以后必须重新检查定位的尺寸是否改变。
在纵缝、环缝允许的错边量范围内应修整成平滑过渡,在完工的焊接宽度范围内的斜度至少为3:1,必要时,在焊缝边缘的外侧堆焊附加焊缝金属。
焊件组对前应检查坡口面,以及其内外侧表面不小于25mm范围内无油、漆、垢、毛刺等,且不得有任何影响焊接质量的缺陷存在;定位焊用手工电弧焊在筒体内侧进行焊接。
核电站钢制安全壳底封头倒 装施工工法(2)
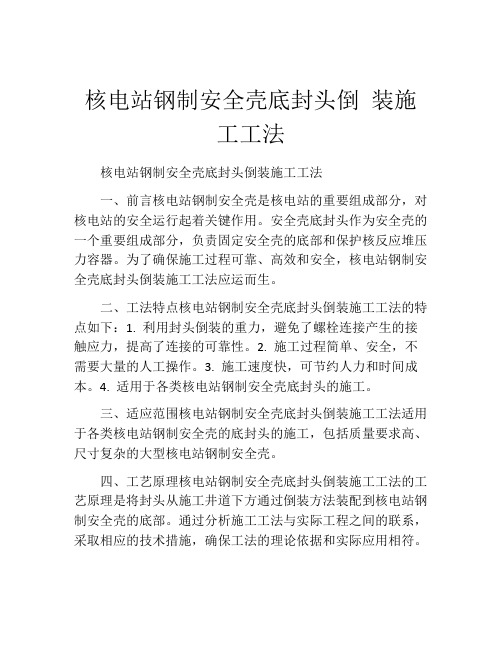
核电站钢制安全壳底封头倒装施工工法核电站钢制安全壳底封头倒装施工工法一、前言核电站钢制安全壳是核电站的重要组成部分,对核电站的安全运行起着关键作用。
安全壳底封头作为安全壳的一个重要组成部分,负责固定安全壳的底部和保护核反应堆压力容器。
为了确保施工过程可靠、高效和安全,核电站钢制安全壳底封头倒装施工工法应运而生。
二、工法特点核电站钢制安全壳底封头倒装施工工法的特点如下:1. 利用封头倒装的重力,避免了螺栓连接产生的接触应力,提高了连接的可靠性。
2. 施工过程简单、安全,不需要大量的人工操作。
3. 施工速度快,可节约人力和时间成本。
4. 适用于各类核电站钢制安全壳底封头的施工。
三、适应范围核电站钢制安全壳底封头倒装施工工法适用于各类核电站钢制安全壳的底封头的施工,包括质量要求高、尺寸复杂的大型核电站钢制安全壳。
四、工艺原理核电站钢制安全壳底封头倒装施工工法的工艺原理是将封头从施工井道下方通过倒装方法装配到核电站钢制安全壳的底部。
通过分析施工工法与实际工程之间的联系,采取相应的技术措施,确保工法的理论依据和实际应用相符。
五、施工工艺核电站钢制安全壳底封头倒装施工工法的施工工艺包括以下几个阶段:1. 准备阶段:确定施工方案,准备所需的施工材料和机具设备,搭建施工井道等。
2. 封头倒装准备阶段:将封头准备好,包括清洁、防锈和防腐等处理,检查尺寸和质量等。
3. 封头倒装阶段:通过起重设备将封头从施工井道下方提升到核电站钢制安全壳底部,并倒装到设计位置。
4. 封头定位和连接阶段:将封头定位到正确位置,通过螺栓连接和焊接等方法完成封头与核电站钢制安全壳的固定。
六、劳动组织核电站钢制安全壳底封头倒装施工工法的劳动组织包括工程师、技术人员、起重设备操作人员、焊工、质检人员等。
七、机具设备核电站钢制安全壳底封头倒装施工工法所需的机具设备包括吊车、吊具、支撑工具、焊接设备、检测设备等。
八、质量控制为了确保施工过程中的质量达到设计要求,应采取以下质量控制措施:1. 对封头进行质量检查,包括尺寸、表面质量以及防腐、防锈等处理。
CAP1400钢制安全壳筒体焊接质量控制
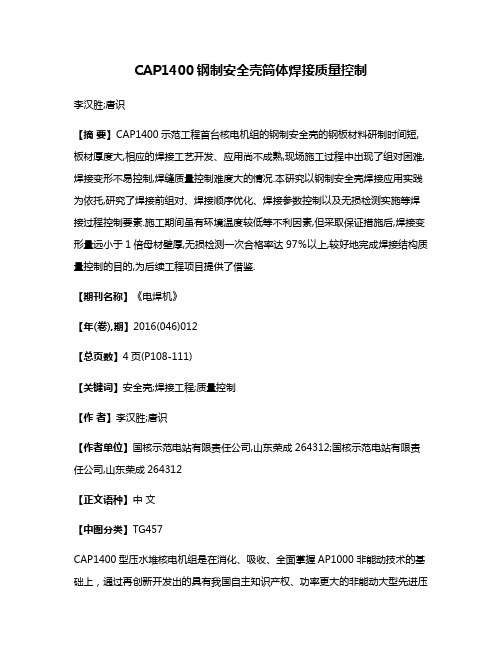
CAP1400钢制安全壳筒体焊接质量控制李汉胜;唐识【摘要】CAP1400示范工程首台核电机组的钢制安全壳的钢板材料研制时间短,板材厚度大,相应的焊接工艺开发、应用尚不成熟,现场施工过程中出现了组对困难,焊接变形不易控制,焊缝质量控制难度大的情况.本研究以钢制安全壳焊接应用实践为依托,研究了焊接前组对、焊接顺序优化、焊接参数控制以及无损检测实施等焊接过程控制要素.施工期间虽有环境温度较低等不利因素,但采取保证措施后,焊接变形量远小于1倍母材壁厚,无损检测一次合格率达97%以上,较好地完成焊接结构质量控制的目的,为后续工程项目提供了借鉴.【期刊名称】《电焊机》【年(卷),期】2016(046)012【总页数】4页(P108-111)【关键词】安全壳;焊接工程;质量控制【作者】李汉胜;唐识【作者单位】国核示范电站有限责任公司,山东荣成264312;国核示范电站有限责任公司,山东荣成264312【正文语种】中文【中图分类】TG457CAP1400型压水堆核电机组是在消化、吸收、全面掌握AP1000非能动技术的基础上,通过再创新开发出的具有我国自主知识产权、功率更大的非能动大型先进压水堆核电机组。
CAP系列大型钢制安全壳容器(简称CV)是隔离安全壳内、外部环境的边界,在事故工况下起限制裂变产物释放的作用,并且为安全壳冷却系统提供换热面,构成安全相关最终热阱,执行非常重要的安全功能[1]。
CV由上下封头及中间筒体组成,属于ASME第Ⅲ分卷MC级部件。
CV筒体板材质为SA738Gr.B,筒体内径43 m,总高42.8 m,由11圈板组成,每圈由12块环板组成,总重约2 375 t;焊接方法为焊条电弧焊(SMAW),焊材选择E9018-G-H4焊条。
焊缝总长约1 867 m,其中纵焊缝132条、环焊缝10条,均是双面坡口熔透焊缝,其中纵缝及环缝坡口形式如图1所示。
由于焊缝自身的力学性能不均匀性、材料不均匀性以及焊缝设计、焊接质量控制等多种因素的影响,焊接接头容易发生缺陷[2],并在随后的电厂运行中,在应力、温度、辐照、氢吸附、腐蚀、振动和磨损等各种因素的作用下,引起接头材料性能的变化,甚至造成缺陷的萌生和扩展,成为核电厂部件、设备和系统的薄弱环节。
- 1、下载文档前请自行甄别文档内容的完整性,平台不提供额外的编辑、内容补充、找答案等附加服务。
- 2、"仅部分预览"的文档,不可在线预览部分如存在完整性等问题,可反馈申请退款(可完整预览的文档不适用该条件!)。
- 3、如文档侵犯您的权益,请联系客服反馈,我们会尽快为您处理(人工客服工作时间:9:00-18:30)。
此网站
2009年5月16日 星期六 首 页| 公司介绍| 新闻中心| 视频中心| 产品展示| 人力资源| 企业文化
公司简介
董事长致辞
董事会
监事会
总经理部成员
组织机构
公司新闻
行业动态
人力概况
他山之石
人才招聘
中国 ? 山东省海阳市临港产业区 邮编:265118
电话:0535-3305111 传真:0535-3305000
山东核电内容 关闭更易于访问的模式 山东核电设备制造有限公司
|
企业理念
党建工作
理论探索
精神文明
质量安全
当前位置: 山东核电设备制造有限公司 > Pages > itemdetails
我国三代核电钢制安全壳底封头首批钢板出厂
2009-5-15 14:30:10
--------------------------------------------------------------------------------
2007年11月30日,山东核电设备制造有限公司与美国西屋公司签署了三门核电站1号机组钢制安全壳(CV)采购框架协议,承担三门核电站1号机组CV制造和现场组拼装工作。目前,三门核电站现场CV拼装厂房已经满足使用条件,CV底封头拼装前的各项准备工作就绪。
三代核电AP1000是目前世界上相对最安全、技术最先进的核电技术,采用全新的非能动安全设计理念。其中,安全壳冷却系统作为一个非能动安全系统,用于发生LOCA事故或主蒸汽管道破裂事故后降低安全壳内的压力和温度,保证安全壳的结构完整性。钢制安全壳是这一系统的重要组成设备,属于ASME NE分卷MC级设备,不同于普通压力容器。另外,钢制安全壳还是反应堆厂房的一道重要安全屏障,它可以在反应堆冷却剂失水事故中包容从堆芯来的辐射。
山东核电设备制造有限公司经过大约10个月的摸索,通过对十几块钢板的几十次压制试验,目前已经掌握了整体模压一次成型技术,并形成了一套较完整的工艺参数。对这些试验板的预组装完成后,经过测量预组装后的各项技术参数,如错边量、间隙、半径和标高等都达到了设计技术要求。
据专家介绍,三代核电AP1000压水堆核电站钢制安全壳(CV)是反应堆厂房的内层屏蔽结构,是非能动安全系统中的重要设备之一。整个安全壳容器由中间的圆柱形筒体及上下两个椭圆型封头组成,最大直径39.624米,总高度65.633米,体积约70000立方米,总重量约3600吨。
2009年5月6日晚,由世界上首家AP1000专业化设备制造工厂——山东核电设备制造有限公司负责压制加工和运输的我国三代核电自主化依托项目三门核电站1号机组钢制安全壳(CV)底封头首批两张钢板,经国家核安全局和美国西屋公司严格审核并认可后,自山东省海阳市顺利出厂运往三门核电站工程现场。
三代核电AP1000钢制安全壳(CV)底封头钢板规格为10米×4米×44毫米,其典型特征是大尺寸、多曲率、高精度,采用整体模压一次成型技术,当前该技术尚属世界性难题。
山东核电设备制造有限公司
itemdetails