搅拌机搅拌臂数目与叶片面积的确定方法
立式釜搅拌叶计算

立式釜搅拌叶计算摘要:一、引言二、立式釜搅拌叶的结构与设计1.搅拌叶的形状与尺寸2.搅拌叶的材料选择3.搅拌叶的数量与布局三、搅拌叶的工作原理与性能要求1.搅拌叶的旋转运动2.搅拌叶的推进力3.搅拌叶的性能要求四、搅拌叶的计算方法与步骤1.计算搅拌叶的受力分析2.计算搅拌叶的材料强度3.计算搅拌叶的尺寸与形状五、搅拌叶计算的实例与应用1.实例介绍2.计算过程与结果分析3.应用领域与前景六、总结与展望正文:一、引言在我国工业生产中,立式釜是一种常见的反应釜设备,广泛应用于化工、石油、医药等领域。
搅拌叶作为立式釜的关键部件,对于釜内物质的混合与反应起着至关重要的作用。
本文将对立式釜搅拌叶的计算方法进行探讨,以期为搅拌叶的设计与优化提供理论依据。
二、立式釜搅拌叶的结构与设计1.搅拌叶的形状与尺寸:搅拌叶的形状通常为螺旋形或切向形,以适应不同釜内反应物质的混合需求。
尺寸方面,搅拌叶的长度、宽度、厚度等参数需要根据釜的尺寸与工艺要求进行合理设计。
2.搅拌叶的材料选择:搅拌叶的材料需要具备较高的强度、耐磨性与耐腐蚀性,常用的材料包括不锈钢、碳钢、铸铁等。
3.搅拌叶的数量与布局:搅拌叶的数量与布局会影响搅拌效果与功耗,需要根据釜内反应物质的性质与搅拌要求进行合理配置。
三、搅拌叶的工作原理与性能要求1.搅拌叶的旋转运动:搅拌叶在釜内作旋转运动,产生离心力与剪切力,使釜内物质得以混合。
2.搅拌叶的推进力:搅拌叶的推进力会影响搅拌效果与功耗,需要根据釜内反应物质的性质进行合理设计。
3.搅拌叶的性能要求:在保证搅拌效果的前提下,应尽量降低搅拌叶的功耗与磨损,提高其使用寿命。
四、搅拌叶的计算方法与步骤1.计算搅拌叶的受力分析:根据搅拌叶的形状、尺寸与材料,计算其在旋转与推进过程中所受到的各种力。
2.计算搅拌叶的材料强度:根据搅拌叶所受到的各种力,计算其材料强度,以确保搅拌叶在使用过程中不会发生断裂等事故。
3.计算搅拌叶的尺寸与形状:根据搅拌叶的材料强度与工作条件,调整搅拌叶的尺寸与形状,使其满足工艺要求。
搅拌机设计计算
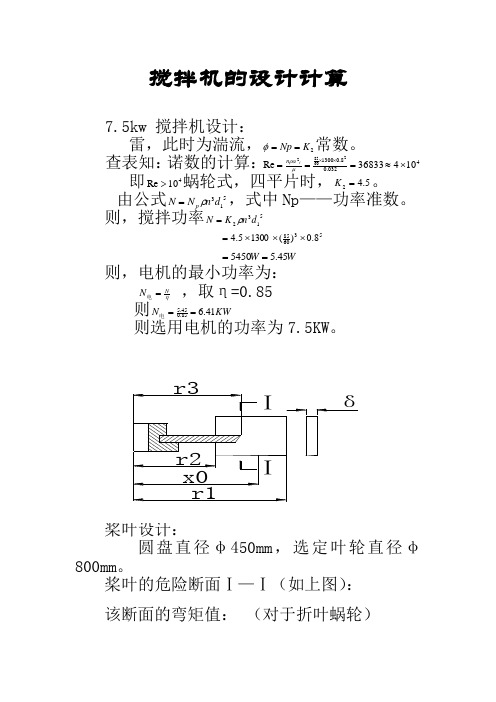
搅拌机的设计计算7.5kw 搅拌机设计:雷,此时为湍流,2K Np ==φ常数。
查表知:诺数的计算:4032.08.0130010436833Re 260852⨯≈===⨯⨯μραin 即410Re >蜗轮式,四平片时,5.42=K 。
由公式513d n N N p ρ=,式中Np ——功率准数。
则,搅拌功率5132d n K N ρ= 5360858.0)(13005.4⨯⨯⨯= W W 45.55450== 则,电机的最小功率为: ηNN =电 ,取η=0.85则KW N 41.685.045.5电==则选用电机的功率为7.5KW 。
圆盘直径φ450mm ,选定叶轮直径φ800mm 。
桨叶的危险断面Ⅰ—Ⅰ(如上图):该断面的弯矩值: (对于折叶蜗轮)θSin nN x r x Zj M 155.9030⨯⨯⨯=-式中n ——转速;N ——功率;x ——桨叶上液体阻力的合力的作用位置。
计算公式为:32314241430r rr r x --⨯= 334412.04.012.04.043--⨯= =0.306(m)则θSin nN x r x Zj M 155.9030⨯⨯⨯=-0345185105.7306.0225.0306.0455.9Sin ⨯⨯⨯=⨯- =78.86(N.m )(Z=4叶片,θ=45°倾角)对于Q235A 材料,MPa 240~2205=σ当取n=2~2.5时,[σ]=88~100Mpa. 取[σ]=90Mpa 计算,得62bh =ω(矩形截面) 且b=200mm ,求h 值。
由][σω≥M有666.81090622.0⨯≥⨯⨯h η,可得h ≥0.00512m, 即h ≥5.12mm考虑到腐蚀,则每边增加1mm 得腐蚀余量。
即,需叶片厚度为≥7.12, 取8mm 厚的钢板。
叶轮轴扭转强度计算验证叶轮轴选用φ76×5的无缝钢管,材料20号钢。
混凝土搅拌机搅拌叶片规格
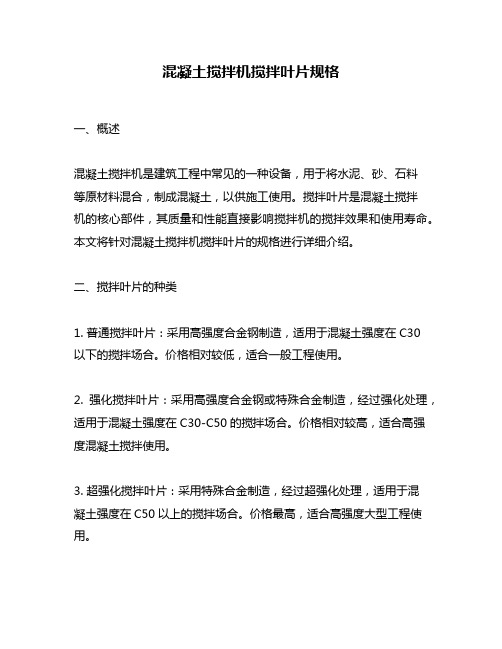
混凝土搅拌机搅拌叶片规格一、概述混凝土搅拌机是建筑工程中常见的一种设备,用于将水泥、砂、石料等原材料混合,制成混凝土,以供施工使用。
搅拌叶片是混凝土搅拌机的核心部件,其质量和性能直接影响搅拌机的搅拌效果和使用寿命。
本文将针对混凝土搅拌机搅拌叶片的规格进行详细介绍。
二、搅拌叶片的种类1. 普通搅拌叶片:采用高强度合金钢制造,适用于混凝土强度在C30以下的搅拌场合。
价格相对较低,适合一般工程使用。
2. 强化搅拌叶片:采用高强度合金钢或特殊合金制造,经过强化处理,适用于混凝土强度在C30-C50的搅拌场合。
价格相对较高,适合高强度混凝土搅拌使用。
3. 超强化搅拌叶片:采用特殊合金制造,经过超强化处理,适用于混凝土强度在C50以上的搅拌场合。
价格最高,适合高强度大型工程使用。
三、搅拌叶片的尺寸1. 搅拌叶片的直径:一般为1.5-3米之间,不同型号的搅拌机直径有所不同。
2. 搅拌叶片的数量:一般为2-4个之间,根据搅拌机的型号和尺寸而定。
3. 搅拌叶片的厚度:一般为10-30毫米之间,不同型号的搅拌机厚度有所不同。
四、搅拌叶片的形状1. 平板形搅拌叶片:叶片呈平板状,适用于干混混凝土和湿混混凝土的搅拌。
2. 弯曲形搅拌叶片:叶片呈弯曲状,适用于半干混混凝土和半湿混凝土的搅拌。
3. 螺旋形搅拌叶片:叶片呈螺旋状,适用于干混混凝土和塑性混凝土的搅拌。
五、搅拌叶片的材质1. 高强度合金钢:强度高、韧性好、耐磨性能好,适用于一般的混凝土搅拌。
2. 特殊合金:强度和硬度更高,耐磨性能更好,适用于高强度混凝土的搅拌。
3. 超高强度合金:强度和硬度更高,耐磨性能更好,适用于高强度大型工程的搅拌。
六、搅拌叶片的表面处理1. 硬质合金喷涂:提高叶片的硬度和耐磨性能,适用于高强度混凝土的搅拌。
2. 涂层处理:涂层材料具有耐磨、耐腐蚀、防粘性能,适用于搅拌机叶片的表面处理。
3. 防腐处理:采用防腐材料对叶片进行处理,提高叶片的抗腐蚀性能,延长使用寿命。
搅拌轴径的计算公式培训资料

搅拌轴径的计算公式培训资料搅拌轴径大致可以按照以下步骤来计算:步骤1:确定物料的特性首先,我们需要确定物料的特性,包括物料的密度、黏度和搅拌过程中需要达到的混合程度等。
这些参数对于计算搅拌轴径非常重要。
步骤2:计算搅拌器叶片数目根据物料的特性和搅拌过程中需要达到的混合程度,我们可以计算出需要的搅拌器叶片数目。
一般来说,叶片数目越多,混合程度越高,但也会增加功耗。
步骤3:计算搅拌器叶片长度根据搅拌器叶片数目和搅拌轴径,我们可以计算出搅拌器叶片的长度。
叶片长度一般为搅拌轴径的2-3倍。
步骤4:计算搅拌器叶片的扭矩根据物料的密度和搅拌轴的转速,我们可以计算出搅拌器叶片所受到的扭矩。
扭矩是搅拌器设计中非常重要的参数,它决定了搅拌轴的直径尺寸。
步骤5:计算搅拌轴的直径根据搅拌器叶片的扭矩和材料的强度,我们可以计算出搅拌轴的直径。
搅拌轴一般采用圆柱形,直径的大小决定了搅拌机的承载能力。
步骤6:确定搅拌轴的材料根据搅拌轴的直径和所需承载能力,我们可以选择合适的材料来制造搅拌轴。
常见的材料有不锈钢、碳钢和铝等。
步骤7:计算搅拌轴的长度根据搅拌轴的直径和搅拌器叶片的长度,我们可以计算出搅拌轴的长度。
搅拌轴的长度也是搅拌机设计中很重要的一个参数。
步骤8:确定搅拌轴的安装方式根据设备的工作场所和安装条件,我们可以确定搅拌轴是水平安装、垂直安装还是倾斜安装。
通过以上步骤,我们可以得到搅拌轴的计算结果,确保搅拌设备能够满足工作要求并具有良好的工作性能。
总结:搅拌轴径的计算是根据搅拌设备的工作要求和物料的特性来确定的。
通过计算物料的特性、搅拌器叶片数目、搅拌器叶片长度、搅拌器叶片的扭矩、搅拌轴的直径、搅拌轴的材料、搅拌轴的长度和搅拌轴的安装方式,可以得到搅拌轴的计算结果。
这样可以确保搅拌设备满足工作要求,并具有良好的工作性能。
5000l框式搅拌桨的表面积
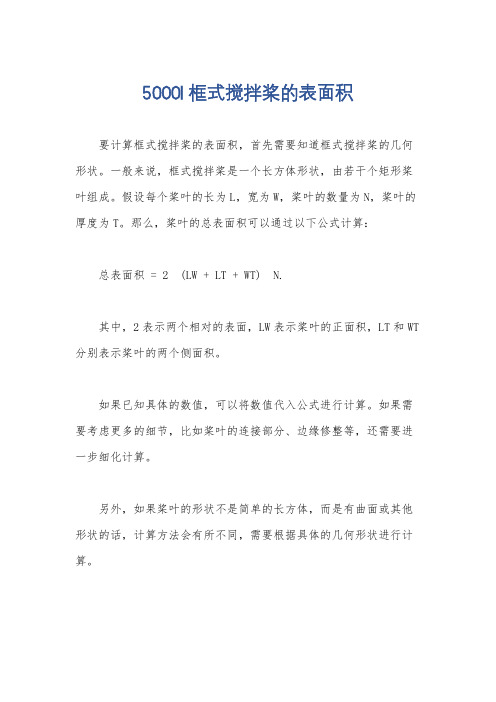
5000l框式搅拌桨的表面积
要计算框式搅拌桨的表面积,首先需要知道框式搅拌桨的几何形状。
一般来说,框式搅拌桨是一个长方体形状,由若干个矩形桨叶组成。
假设每个桨叶的长为L,宽为W,桨叶的数量为N,桨叶的厚度为T。
那么,桨叶的总表面积可以通过以下公式计算:
总表面积 = 2 (LW + LT + WT) N.
其中,2表示两个相对的表面,LW表示桨叶的正面积,LT和WT 分别表示桨叶的两个侧面积。
如果已知具体的数值,可以将数值代入公式进行计算。
如果需要考虑更多的细节,比如桨叶的连接部分、边缘修整等,还需要进一步细化计算。
另外,如果桨叶的形状不是简单的长方体,而是有曲面或其他形状的话,计算方法会有所不同,需要根据具体的几何形状进行计算。
搅拌机设计流程
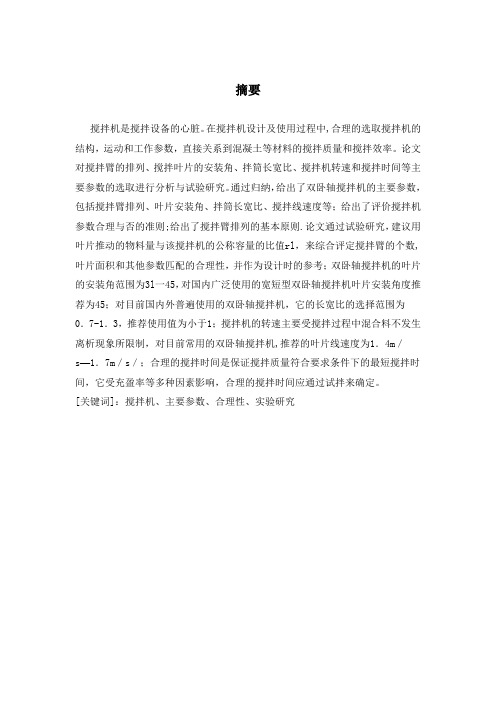
摘要搅拌机是搅拌设备的心脏。
在搅拌机设计及使用过程中,合理的选取搅拌机的结构,运动和工作参数,直接关系到混凝土等材料的搅拌质量和搅拌效率。
论文对搅拌臂的排列、搅拌叶片的安装角、拌筒长宽比、搅拌机转速和搅拌时间等主要参数的选取进行分析与试验研究。
通过归纳,给出了双卧轴搅拌机的主要参数,包括搅拌臂排列、叶片安装角、拌筒长宽比、搅拌线速度等;给出了评价搅拌机参数合理与否的准则;给出了搅拌臂排列的基本原则.论文通过试验研究,建议用叶片推动的物料量与该搅拌机的公称容量的比值rl,来综合评定搅拌臂的个数,叶片面积和其他参数匹配的合理性,并作为设计时的参考;双卧轴搅拌机的叶片的安装角范围为3l一45,对国内广泛使用的宽短型双卧轴搅拌机叶片安装角度推荐为45;对目前国内外普遍使用的双卧轴搅拌机,它的长宽比的选择范围为0.7-1.3,推荐使用值为小于1;搅拌机的转速主要受搅拌过程中混合料不发生离析现象所限制,对目前常用的双卧轴搅拌机,推荐的叶片线速度为1.4m/s—1.7m/s/;合理的搅拌时间是保证搅拌质量符合要求条件下的最短搅拌时间,它受充盈率等多种因素影响,合理的搅拌时间应通过试拌来确定。
[关键词]:搅拌机、主要参数、合理性、实验研究第1章前言1.1国内外研究现状及发展趋势19世纪40年代,在德、美、俄等国家出现了以蒸气机为动力源的白落式搅拌机,其搅拌腔由多面体状的木制筒构成,一直到19世纪80年代,才开始用铁或钢件代替木板,但形状仍然为多面体。
1888年法国申请登记了第一个用于修筑战前公路的混凝土搅拌机专利。
20世纪初,圆柱形的拌筒自落式搅拌机才开始普及,其工作原理如图1.2所示.形状的改进避免了混凝土在拌筒内壁上的凝固沉积,提高了搅拌质量和效率。
1903年德国在斯太尔伯格建造了世界上第一座水泥混凝土的预拌工厂。
1908年,在美国出现了第一台内燃机驱动的搅拌机,随后电动机则成为主要动力源。
从1913年,美国开始大量生产预拌混凝土,到1 950年,亚洲大陆的日本开始用搅拌机生产预拌混凝土。
搅拌机搅拌臂和搅拌叶片受力计算与分析
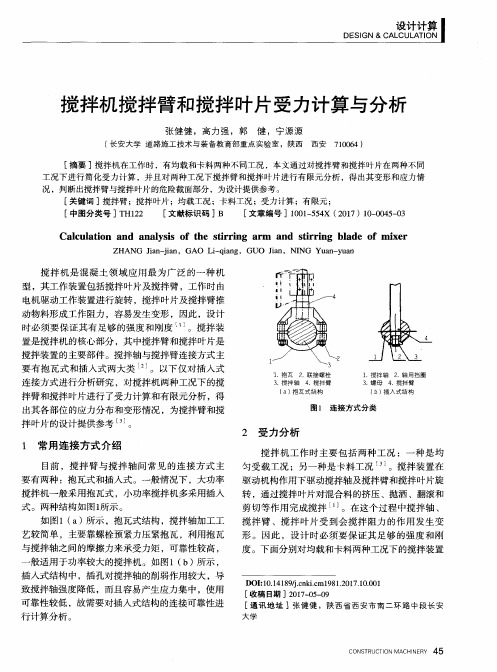
般适用于功率较大的搅拌机 。如图1( b ) 所示 ,
DO I : 1 0 . 1 4 1 8 9 / j . c n k i . c m1 9 8 1 . 2 0 1 7 . 1 0 . 0 0 1 [ 收稿 日期 ] 2 0 1 7 — 0 5 — 0 9 [ 通 讯 地址 ]张健 健 ,陕西 省西 安市 南 二环 路 中段 长 安
[ 关键词 ] 搅拌臂;搅拌叶片;均载工况 ;卡料工况;受力计算 ;有限元 ; [ 中图分类号 ] T H 1 2 2 [ 文献标识码 ] B [ 文章编号 ]1 0 0 1 — 5 5 4 X( 2 0 1 7 )1 0 — 0 0 4 5 — 0 3
Ca l c ul a t i o n a nd a na l y s i s o f t he s t i r r i ng a r m a nd s t i r r i ng bl a de o f mi x e r
设计计算
DE Sl GN & CAL CUL ATI ON
搅拌机搅拌臂和搅拌 叶片受力计算 与分析
张健 健 ,高 力强 ,郭 健 ,宁源 源
西安 7 1 0 0 6 4) ( 长 安 大 学 道 路 施 工 技 术 与装 备教 育部 重 点 实验 室 ,陕 西
[ 摘要 ] 搅 拌 机 在 工作 时 ,有 均 载 和卡 料两 种 不 同工 况 ,本 文 通过 对搅 拌 臂 和搅 拌 叶片 在两 种 不 同 工 况 下 进行 简 化 受力 计 算 ,并 且 对 两种 工 况 下搅 拌 臂 和搅 拌 叶 片进 行 有 限元 分 析 ,得 出其 变 形 和应 力情 况 ,判 断 出搅 拌臂 与搅 拌 叶片 的危 险截 面部 分 ,为设 计提 供参 考 。
混凝土搅拌车搅拌筒设计基本方法

混凝土搅拌车搅拌筒设计基本方法
首先,混凝土搅拌车搅拌筒设计要根据搅拌要求确定尺寸。
尺寸包括直径、长度和搅拌筒容积。
直径和长度一般是根据搅拌能力和搅拌效率来确定的,直径越大搅拌能力越强,长度越长搅拌效率越高。
容积要根据每次搅拌的混凝土量来确定,一般可以根据工程施工需要来确定容积大小。
其次,搅拌筒内螺旋叶片的设计也是搅拌筒设计的重要部分。
螺旋叶片的设计要考虑到混凝土的搅拌均匀性和搅拌轴向方向和循环方向。
螺旋叶片的安装方式有固定式和可拆卸式,固定式一般用于大型搅拌筒,可拆卸式一般用于小型搅拌筒,方便更换和维修。
再次,在搅拌筒设计过程中,需要考虑搅拌筒的结构和材料选择。
结构通常分为搅拌筒主体、入料口、出料口、搅拌叶片等部分。
材料主要选择高强度和耐磨性能较好的钢材,以保证搅拌筒的使用寿命和搅拌质量。
另外,还需要考虑搅拌筒的搅拌速度和搅拌时间。
搅拌筒的搅拌速度要根据混凝土的特性和搅拌要求来确定,一般在4-14转/分之间。
搅拌时间一般根据混凝土的水泥种类和配合比进行确定,一般为1-3分钟。
最后,需要考虑搅拌筒的传动方式。
传动方式一般有液压传动和机械传动两种。
液压传动适用于大型搅拌车,可以提高传动效率和搅拌能力;机械传动适用于小型搅拌车,结构简单,维修方便。
总之,混凝土搅拌车搅拌筒设计是一个综合考虑多个因素的过程,需要根据实际情况和搅拌要求来进行合理设计。
设计合理的搅拌筒可以提高工作效率,保证搅拌质量,从而提高混凝土施工质量。
搅拌设备设计讲座(第十二讲)——搅拌臂数目与搅拌叶片面积

搅拌设备设计讲座(第十二讲)——搅拌臂数目与搅拌叶片面积第穆拿月||工榴瓣_||||l渤&詹矿◇搅拌设备设计讲座(第十二讲)◇搅拌臂数目与搅拌叶片面积长安大学冯忠绪李彰王卫中赵利军1搅拌臂数目搅拌臂数量的多少对搅拌机的工作效率及混合料的搅拌质量有一定的影响,不仅单根轴上相邻搅拌臂问的相位角与搅拌臂的数量密切相关,而且双轴上搅拌臂排列组合形式及其合理逆流的最小相位差也与搅拌臂的数量有关.1.1确定拌臂数目的相关因素分析搅拌臂数量多,必然使搅拌轴长度增加使其结构强度,刚性下降,使搅拌机拌筒的长度增加使其长宽比不合适.而且搅拌机拌筒的长度增加,卸料门的长度也要增加,这对总体布置不利.另外,搅拌臂越多,使石料被叶片挤碎的可能性增大,这将影响到骨料的级配精度.搅拌臂数量少,必然减少物料的循环次数,减少物料与搅拌的叶片直接接触而发生强制作用的机会,影响搅拌质量.所以,确定搅拌机合理的搅拌臂数目也具有重要的意义.通过分析认为,确定搅拌臂数目要考虑的相关因素有:(1)单根搅拌轴每转一圈,物料沿轴向行程不小于相邻搅拌臂沿搅拌筒轴向空间长度.若以n表示单根轴上搅拌臂数目,0表示相邻搅拌臂之问的相位角,则n?360.,一般360.n?720..(2)两根搅拌轴转动时,两轴上转向相反的搅拌臂叶片最小空间距离决定了搅拌机所能适应的骨料最大粒径.否则,不是骨料被挤碎,就是搅拌臂及叶片受损.当然,上述"最小空问距离"与搅拌臂数量,叶片几何尺寸,叶片安装角度及搅拌臂问相互布置等有关.(3)单根轴上相邻叶片的轴向投影应有一定重叠,以保证料流的连续性,同时卸料时可最大限度地减少拌筒内的混合料残留,给拌筒清洗带来方便.搅拌臂数目与相位角除了必须符合关系式360.n?≤720.外,还与双轴搅拌臂的布置形式有关.尤其是在搅拌臂正正平行排列时,若搅拌臂数目与单轴搅拌臂相位角的大小匹配不合理,就难以找到完全符合搅拌臂布置基本原则的排列方案.搅拌臂正正平行排列条件下,搅拌臂数目与其相位角大小的匹配关系是:1)360.n?720.:2)0=90.时,n不可以取5,7,即n不宜为奇数;3)=60~时,n不可以取6,8,10,且口n不勘偶数;4)=45.时,n不可以取9,11,13,15,即n不宜取奇数.下面仅以0=90.,n=5时的情况为例进行说明.图1所示为可能的4种排列组合,其中序号1,5 同时代表搅拌臂及其上安装的返回叶片(详见参考文献[2]).在搅拌轴旋转一周的过程中,组合(a)将出现搅拌臂每转过90.,同时达到搅拌区的叶片数总数及其中的返回叶片数不能保证是5个和2个.而且,叶片1,5分别同时到达搅拌区,发生干涉;组合(b)也出现同时达到搅拌区的叶片数不一致的情况;组合(c)的2,4叶片分别发生干涉;组合(d)与(b)类似.可见都不符合搅拌臂的排列原则(详见参考文献[2】).所以,这种匹配关系在实际设计中要尽量避免.1.2合理拌臂数目的试验根据确定合理拌臂数目时的主要相关因素,结合试验装置结构条件,选取与单轴上相邻拌臂不同相位角相匹配的4种拌臂数目5,6,7,8,在不同的双轴拌臂排列组合形式下,分别采用宽短型和窄长型拌筒搅拌混凝土,测试搅拌质量指标值和搅拌功率消耗值.试验结果列于表1.从表中的数据来看,不同数目的搅拌臂对混凝土拌和物的宏观匀质性影响较大,但对混凝土的7 天抗压强度和搅拌功率的消耗来说,影响都比较小, 没有明显的规律性.从试验测试指标的最优值分布情况来看,在单轴相邻拌臂相位角为60.,双轴拌臂排列形式为正正组合时,对于宽短型拌筒,搅拌臂的合理数目是5个;而对于窄长形拌筒,搅拌臂的合一61—3L,』I,]l,5(b)3L厂.,I\']1,5_J4【,5,.....一,,/II言2r_J23,....一,/U4厂图1搅拌臂排列方案筛选确定搅拌臂最佳数目试验的各指标试验结果理数目为7个.2搅拌叶片的面积搅拌叶片的面积对物料的循环运动和物料之间的相互作用有着重要的影响,叶片面积过小,减弱了物料的循环作用和两轴之间的对流作用,使物料达到宏观均匀搅拌时间增长;若叶片面积s过大,不但增大了搅拌功率,还需要减小叶片个数/1,,否则叶片在搅拌筒内运动时会相互干涉,因此5有一个下限一62一和一个上限5一.应根据拌筒尺寸和工作装置各参数,主要是搅拌叶片的个数,设计出合理的叶片搅拌面积.由于与叶片面积相关的因素较多,主要通过试验来分析各种因素的影响,试验内容包括:1)相同的长宽比,相同叶片面积情况下,不同叶片个数对搅拌效果的影响;2)相同的长宽比,相同叶片个数情况下,不同叶片面积对搅拌效果的影响;孝鼬管|工移斑辫|_|I母岛锄31相同叶片面积,叶片个数时,不同的拌筒长宽比下搅拌效果的比较.2.1试验方案试验方案见表2.在这次普通搅拌机参数优化试验中,有4种叶片面积,每一种面积下有3种选择,拌筒长宽比选择了两种. 所以,根据试验内容,共有24组试验(4×3×2=24).其中,1~12组为窄长形拌筒,13~24组为宽短形拌筒. 2.2试验结果试验结果见表3.从试验结果可以看出:(1)在本试验条件下,第12组,第9组,第17组结果较好,表明合理的叶片面积和叶片个数的匹配对搅拌质量的影响较大,这几组结果可作为设计人员选择参数时的参考.(2)叶片面积增大对搅拌功率的影响很大,但混凝土强度并不一定会提高;当叶片面积过大,叶片个数过少时,混凝土的均匀性很差;同时,增大叶片面积,减少叶片个数,会增大混凝土的含气量.(3)从对混凝土的搅拌质量的影响而言,叶片个数的变化要比叶片面积的变化影响大.当叶片个数过多或叶片面积过大时,都会使相邻叶片之间的空间距离减小,反而使物料流动不畅,搅拌质量下降.对比试验结果见表4.(4)当拌筒长宽比和容积利用系数不同时,即使相邻叶片之间的空间距离相同,叶片面积相同,搅拌效果也不相同.这表明搅拌室容积利用系数和长宽比也要影响叶片面积和叶片个数的选择.当然,混合料的最大粒径也是影响搅拌叶片个数和叶片面积选择的重要因素.我们在试验中的混合料最大粒径为40mm.2.3综合评判指标由上所述可见,搅拌叶片个表2叶片面积试验方案叶片面窄长型宽短型积/em组数叶片个数组数叶片个数122432632323434225I44225192432136519574182130851739616410515293.6116143127134表3试验结果拌和物匀质性28d硬化混凝土试块抗压强度搅拌功率试验号}%△G,%厂/MPa,MI)aCv,l【W10.422.3924.162-20.O913_2020_270.9727.671.7010.0613.5030.741.0326.980.6O10.0224.4041.441.4826.701.3600.0513.2650.550.9427-381.0780.0393.8060.580.4929.040.6800.0234-3070.610.9525.781.7800.O693_2080.490.7227.570.5300.0193_3590.410.4729.230.5900.0203.60100.681.1927.441.3600.0493.10110.590.9528-300.6400.0223.50120.170.6930.010.0510.0173.70132.007.6923.971.5250.O643.90140.592-3326.461.oo00.0384.10150.990.7225.111.2370.0494.20160.69l-2225.1l1.4900.0594.40170.02027.170.0820.0304.80180.702.8226.440.3660.0l35-30191.365.7723.662.5460.1084.00200.791.2224.841.4490.0584.65210.2l0.7126.280.4030.0155.90221-351.4525.792.7900.1084_30230.700.9026.830.6750.0254.90240.690.4826.4l0.5800.0226_30—63一-比试验结果弧度排出的体积,所以p=1T×[R2(R—b)]×W×COS×/360.(1)p=1T×b×W×COS××(2R—b)/360.(2)式中:p——叶片旋转一周排出的物料体积,m,; R——搅拌轴总成的旋转半径,m;0r叶片的轴向安装角度,(.);叶片的宽度,m;6——叶片的高度,m;叶片从人料到出料旋转过的角度,(.).将S=wxb代人(2)式得p=1T×S×COS××(2R—b)/360.(3)搅拌轴搅拌一周,双卧轴搅拌机所有叶片推动的物料量总和G:G=4×po+2(n一2)×PI(4)式中:p返回叶片排出的物料量,m;--———64-?-——图2叶片安装图图3叶片在X—Y面的投影图p,——主叶片(参见参考文献【1—21))排出的物料量,m;G——搅拌轴旋转一周,搅拌机所有叶片推动物料量总和,m;n——单轴上的叶片个数.由于搅拌机的工作条件不变,搅拌过程是一个周期性稳态运动过程,所以角度总是在一个平均值附近上下起伏,式中的就取这个平均值.容积利囊孝,口凹幸2|工用系数决定着0的大小,一定时,由式(3)可以看出,在O/,K,和0一定的情况下,P都有唯一的对应值.设0=G,o/(5)式中:——搅拌机的出料容积,ITI;——搅拌轴搅拌一周,叶片推动物料总量占出料容积的比值.设计搅拌机时,若叶片面积5,叶片个数/7,和容积利用系数三者之间匹配合理,就有一个较优值与之对应,将这些值与S,/7,,K作成对应曲线,可以指导搅拌机的设计.在本次试验中,对于两种长宽比,除了叶片面积和叶片个数的不同,其余的因素都相同.所以,对于式(3)和式(4)中的变量,除了5和/7,两个变量,其他变量取值都相同.窄长型试验值与宽短型试验值横向比较,只不过再加上了变量0.容积利用系数0.18 的窄长型的0取值大约是95.;容积利用系数0.25时,宽短型的0大约是125..窄长型试验中,第12 组和第9组的试验值较好,宽短型则是第17组较好,根据公式(4)和(5),代人相关数据计算:窄长型S=93.6cm;n=7,Gl=0.105m;S=I30cm;n=6,G2=0.11m宽短型S=I30cm;n=4;G3=0.106m;01=0.105÷0.1=1.05;2=0.11÷0.1=1.1;3=0.106÷0.1=1.06.初步确定,在出料容积V=0.1ITI的搅拌机中,0=1.05~1.1时较合理.再考虑到功率消耗,确定窄长型中第9组最好,即面积130cm,叶片个数为6 —65—。
立式釜搅拌叶计算

立式釜搅拌叶计算
(实用版)
目录
1.立式釜搅拌叶的概述
2.立式釜搅拌叶的计算方法
3.立式釜搅拌叶的实际应用
4.立式釜搅拌叶的发展前景
正文
一、立式釜搅拌叶的概述
立式釜搅拌叶,是指在立式釜设备中使用的搅拌器叶片。
立式釜是一种广泛应用于化工、石油、制药、食品等行业中的重要设备,主要用于进行物料的混合、反应、加热等操作。
搅拌叶在立式釜中起着关键作用,它能够使釜内物料充分混合,提高反应效率和产品质量。
二、立式釜搅拌叶的计算方法
立式釜搅拌叶的计算主要包括搅拌速度和搅拌器直径的计算。
1.搅拌速度的计算:搅拌速度是指搅拌器每分钟旋转的圈数,其计算公式为:n=60f/πD,其中,n 为搅拌速度,f 为电机频率,D 为搅拌器直径。
2.搅拌器直径的计算:搅拌器直径的计算主要取决于釜内物料的特性和搅拌要求。
一般情况下,搅拌器直径可取为釜直径的 1/3~1/2。
三、立式釜搅拌叶的实际应用
在实际应用中,立式釜搅拌叶的选择需要根据物料的性质、釜内压力、温度等因素进行综合考虑。
例如,对于黏度较大的物料,应选择搅拌速度较快、搅拌器直径较大的搅拌叶;对于高温、高压的反应釜,应选择材质
耐高温、耐腐蚀的搅拌叶。
四、立式釜搅拌叶的发展前景
随着科技的发展和工业生产自动化程度的提高,立式釜搅拌叶的设计和制造技术也在不断进步。
混凝土搅拌机搅拌叶片规格
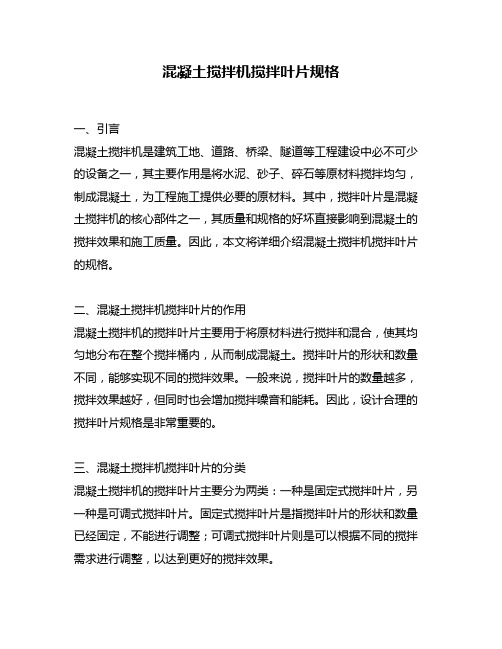
混凝土搅拌机搅拌叶片规格一、引言混凝土搅拌机是建筑工地、道路、桥梁、隧道等工程建设中必不可少的设备之一,其主要作用是将水泥、砂子、碎石等原材料搅拌均匀,制成混凝土,为工程施工提供必要的原材料。
其中,搅拌叶片是混凝土搅拌机的核心部件之一,其质量和规格的好坏直接影响到混凝土的搅拌效果和施工质量。
因此,本文将详细介绍混凝土搅拌机搅拌叶片的规格。
二、混凝土搅拌机搅拌叶片的作用混凝土搅拌机的搅拌叶片主要用于将原材料进行搅拌和混合,使其均匀地分布在整个搅拌桶内,从而制成混凝土。
搅拌叶片的形状和数量不同,能够实现不同的搅拌效果。
一般来说,搅拌叶片的数量越多,搅拌效果越好,但同时也会增加搅拌噪音和能耗。
因此,设计合理的搅拌叶片规格是非常重要的。
三、混凝土搅拌机搅拌叶片的分类混凝土搅拌机的搅拌叶片主要分为两类:一种是固定式搅拌叶片,另一种是可调式搅拌叶片。
固定式搅拌叶片是指搅拌叶片的形状和数量已经固定,不能进行调整;可调式搅拌叶片则是可以根据不同的搅拌需求进行调整,以达到更好的搅拌效果。
四、混凝土搅拌机搅拌叶片的形状混凝土搅拌机的搅拌叶片形状有很多种,主要有以下几种:1.平面叶片:平面叶片是混凝土搅拌机最基本的搅拌叶片形式,其形状类似于平板,适用于搅拌较干的混凝土原材料。
2.弯曲叶片:弯曲叶片是在平面叶片的基础上进行改进,其形状呈弯曲状,能够更好地混合较干的混凝土原材料。
3.扭曲叶片:扭曲叶片是在弯曲叶片的基础上进行改进,其形状呈扭曲状,能够更好地混合较稠的混凝土原材料。
4.多层叶片:多层叶片是将多层平面叶片叠加在一起形成的,能够更好地混合较稀的混凝土原材料。
五、混凝土搅拌机搅拌叶片的数量混凝土搅拌机搅拌叶片的数量是非常重要的,一般来说,搅拌叶片数量越多,搅拌效果越好,但同时也会增加搅拌噪音和能耗。
目前市场上常见的混凝土搅拌机搅拌叶片数量为3个、4个、5个、6个、8个等,其中4个和6个的搅拌叶片数量最为常见。
六、混凝土搅拌机搅拌叶片的尺寸混凝土搅拌机搅拌叶片的尺寸主要包括叶片的长度、宽度、厚度和叶片之间的间距。
搅拌器搅拌面积计算公式

搅拌器搅拌面积计算公式
搅拌器搅拌面积的计算公式可以根据具体的搅拌器类型和设计
参数来确定。
一般来说,搅拌器的搅拌面积可以通过以下公式进行
估算:
搅拌面积= π D H.
其中,π是圆周率(约为3.14159),D是搅拌器的直径,H是
搅拌器的高度。
对于不同类型的搅拌器,计算公式会有所不同。
例如,对于螺
旋搅拌器或桨叶搅拌器,可能需要考虑到搅拌器的螺旋或桨叶数量、形状、角度等因素。
而对于液体混合槽或反应釜中的搅拌器,还需
要考虑搅拌器与容器壁之间的间隙等因素。
在实际工程中,搅拌面积的计算还需要考虑流体力学、传热学
等相关知识,以确保搅拌器能够有效地实现混合、传质、传热等工
艺要求。
因此,在进行搅拌面积计算时,需要综合考虑搅拌器的类型、工作条件、流体性质等多种因素,进行合理的估算和设计。
需要注意的是,以上提到的公式和方法仅供参考,实际工程中应当根据具体情况进行详细的计算和设计。
同时,为了确保搅拌器的正常运行和工艺效果,建议在进行搅拌器设计时寻求专业工程师的帮助,以确保设计的准确性和可靠性。
搅拌桩面积计算公式
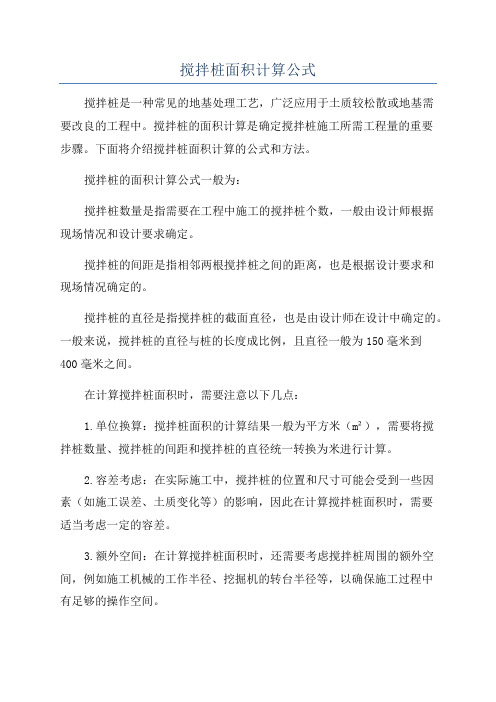
搅拌桩面积计算公式搅拌桩是一种常见的地基处理工艺,广泛应用于土质较松散或地基需要改良的工程中。
搅拌桩的面积计算是确定搅拌桩施工所需工程量的重要步骤。
下面将介绍搅拌桩面积计算的公式和方法。
搅拌桩的面积计算公式一般为:搅拌桩数量是指需要在工程中施工的搅拌桩个数,一般由设计师根据现场情况和设计要求确定。
搅拌桩的间距是指相邻两根搅拌桩之间的距离,也是根据设计要求和现场情况确定的。
搅拌桩的直径是指搅拌桩的截面直径,也是由设计师在设计中确定的。
一般来说,搅拌桩的直径与桩的长度成比例,且直径一般为150毫米到400毫米之间。
在计算搅拌桩面积时,需要注意以下几点:1.单位换算:搅拌桩面积的计算结果一般为平方米(m²),需要将搅拌桩数量、搅拌桩的间距和搅拌桩的直径统一转换为米进行计算。
2.容差考虑:在实际施工中,搅拌桩的位置和尺寸可能会受到一些因素(如施工误差、土质变化等)的影响,因此在计算搅拌桩面积时,需要适当考虑一定的容差。
3.额外空间:在计算搅拌桩面积时,还需要考虑搅拌桩周围的额外空间,例如施工机械的工作半径、挖掘机的转台半径等,以确保施工过程中有足够的操作空间。
4.特殊情况处理:在一些特殊情况下,如施工现场狭小、有障碍物等,可能无法按照常规的搅拌桩间距进行布置,此时需要根据实际情况进行相应的调整和处理。
总之,搅拌桩面积计算是搅拌桩施工中的重要环节,通过合理计算搅拌桩面积,可以确保搅拌桩施工的准确性和经济性,并为项目的顺利进行提供保障。
在实际工程中,设计师需要根据具体情况和要求进行搅拌桩面积的计算,并灵活应用于工程实践中。
搅拌机搅拌臂数目与叶片面积的确定方法

111315下面仅以90n种排列组合其中序出现搅拌臂每转过90同时到达搅拌区的叶片总搅拌臂排列方案筛选数及其返回的叶片数不能保证是同时到达搅拌区则会发生干涉种排列组合都不符合搅拌臂的排列原则所以这种匹配关系在实际设计中要尽量避免搅拌臂数目的确定合理确定搅拌臂数目时应考虑主要相关因素结合试验条件选取与单轴上相邻搅拌臂不同相位角匹配的在不同的双轴搅拌臂排列组合时分别采用宽短型和窄长型拌测试搅拌质量指标值和搅拌功率消耗值试验结果如表搅拌臂排列长宽特征各指标的试验结果拌和物匀质抗压强度搅拌功mpacv90正正432190正反632360正正302360正反432545正反082345反反201990正正842190反反482060正反042060反反292290正反321990反反251960正正912060反反112045正正281945正反7319cv为离差系数
通过分析认为 ,合理地确定搅拌臂数目要考虑 许多相关因素 。
(1) 单根搅拌轴每转 1 圈 ,物料沿轴向行程不小 于搅拌筒轴向空间长度 。若以 n 表示单根轴上搅拌 臂数目 (搅拌叶片数目) ,θ表示相邻搅拌臂之间的 相位角 ,则 nθ≥360°,一般情况下 ,360°≤nθ≤720°。
(2) 2 根搅拌轴转动时 ,转向相反的搅拌臂叶片 最小空间距离决定了搅拌机所能适应的骨料最大粒 径 。否则 ,不是骨料被挤碎 ,就是搅拌臂及叶片受 损 。当然 ,上述“最小空间距离”与搅拌臂数目 、叶片 几何尺寸 、叶片安装角度及搅拌臂间相互布置等因 素有关 。
物化搅拌机计算

0.18 0.09 0.24 0.06 0.75
2
手册2166 4 5.04 7.1% 1.1 56.1224 4 4 0.03799 0.66077 0.69876 1.33097
絮凝:10-20r/min;混凝:3040r/min;
要求<25%,一般在10%-20%之间 《设计手册3》P494 k=ψ *ρ /2g
1.搅拌机机械总效率η 1采用 0.75
备注
取值
核算
与池壁不大于0.25m
0.1
高程核算 25)*D2 块
25)*D2 各2块
75*2R 0.3m 0.3~0.5m 0.95 0.95
0.2~0.5m/s
20r/min;混凝:30-
,一般在10%-20%之间 册3》P494 2g
机械总效率η 1采用
取值
算值
备注
5 1.2 1.2 0.15 0.5 4.5 0.3 0.18 2 0.09 0.24 4 0.06 0.75 0.3 0.5 2 0.95 1 40 4
0.5
浆板外缘与池壁不大于0.25m 根据水力高程核算 (0.1-0.25)*D2 上下各一块 (0.1-0.25)*D2 内、外侧各2块 不大于0.75*2R 手册参数0.3m 手册参数0.3~0.5m
絮凝池搅拌机计算
序号 1、 2、 3、 5、 6、 8、 9、 10、 11、 12、 13、 14、 15、 16、 17、 18、 19、 20、 21、 22、 23、 24、 25、 26、 27、 28、 29、 30、 31、 32、 33、
3
项目 水量Q,m /h 池体底面长D1,m 池体底面宽D2,m 桨叶内缘半径r,m 桨叶外缘半径R,m 池体高度H,m 池体预留超高H1,m 搅拌横板总宽B1,m 搅拌横版数量 搅拌横板宽b1,m 竖桨叶总宽度B2,m 竖桨叶数量 竖桨叶宽度b2,m 桨叶长度B 桨叶离液面高度H2,m 桨叶离液面高度H3,m 桨叶分组数量 设计桨叶间距,m 桨板中心线速度v1,(m/s) 搅拌转速n,r/min 桨板旋转角速度ω :rad/s 反应池水流纵截面积A1,m2 桨板与纵截面积之比计算(%) 阻力系数ψ 功率系数k 内侧同一旋转半径上的桨叶数 内侧同一旋转半径上的桨叶数 内侧浆板功率w1,kw 外侧浆板功率w2,kw 搅拌浆计算总功率W1,kw 电动机实际功率W2,kw
搅拌罐车搅拌叶片设计计算
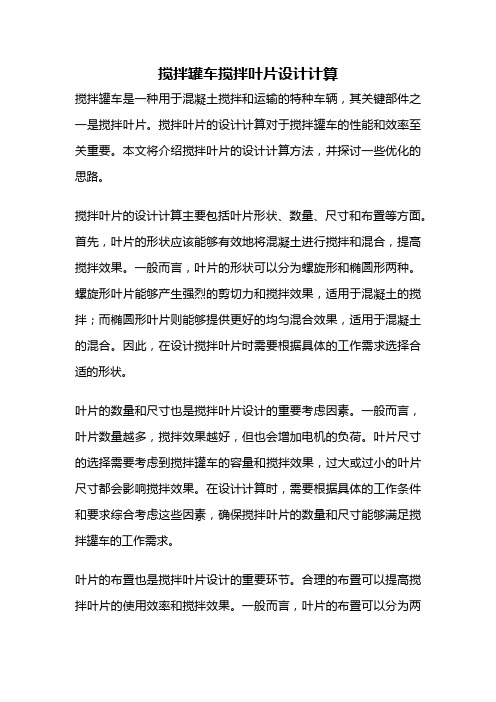
搅拌罐车搅拌叶片设计计算搅拌罐车是一种用于混凝土搅拌和运输的特种车辆,其关键部件之一是搅拌叶片。
搅拌叶片的设计计算对于搅拌罐车的性能和效率至关重要。
本文将介绍搅拌叶片的设计计算方法,并探讨一些优化的思路。
搅拌叶片的设计计算主要包括叶片形状、数量、尺寸和布置等方面。
首先,叶片的形状应该能够有效地将混凝土进行搅拌和混合,提高搅拌效果。
一般而言,叶片的形状可以分为螺旋形和椭圆形两种。
螺旋形叶片能够产生强烈的剪切力和搅拌效果,适用于混凝土的搅拌;而椭圆形叶片则能够提供更好的均匀混合效果,适用于混凝土的混合。
因此,在设计搅拌叶片时需要根据具体的工作需求选择合适的形状。
叶片的数量和尺寸也是搅拌叶片设计的重要考虑因素。
一般而言,叶片数量越多,搅拌效果越好,但也会增加电机的负荷。
叶片尺寸的选择需要考虑到搅拌罐车的容量和搅拌效果,过大或过小的叶片尺寸都会影响搅拌效果。
在设计计算时,需要根据具体的工作条件和要求综合考虑这些因素,确保搅拌叶片的数量和尺寸能够满足搅拌罐车的工作需求。
叶片的布置也是搅拌叶片设计的重要环节。
合理的布置可以提高搅拌叶片的使用效率和搅拌效果。
一般而言,叶片的布置可以分为两种方式:对称布置和非对称布置。
对称布置指的是叶片按照相同的角度和间距均匀分布在搅拌罐车的内壁上;非对称布置则是指叶片按照不同的角度和间距分布在搅拌罐车的内壁上。
对称布置适用于搅拌罐车容量较小、速度较快的情况,而非对称布置适用于搅拌罐车容量较大、速度较慢的情况。
在实际设计中,需要根据具体的工作条件和要求选择合适的布置方式。
除了上述的基本设计考虑因素外,搅拌叶片的设计还需要考虑一些优化的思路。
例如,可以通过改变叶片的形状和角度,提高搅拌效果和混合均匀度;可以通过改变叶片的材料和结构,提高叶片的耐磨性和使用寿命;可以通过改变搅拌罐车的结构和尺寸,提高搅拌效率和运输能力。
这些优化的思路可以根据具体的工作条件和要求进行调整和改进,以提高搅拌罐车的性能和效率。
搅拌设备设计讲座(第十二讲)搅拌臂数目与搅拌叶片面积
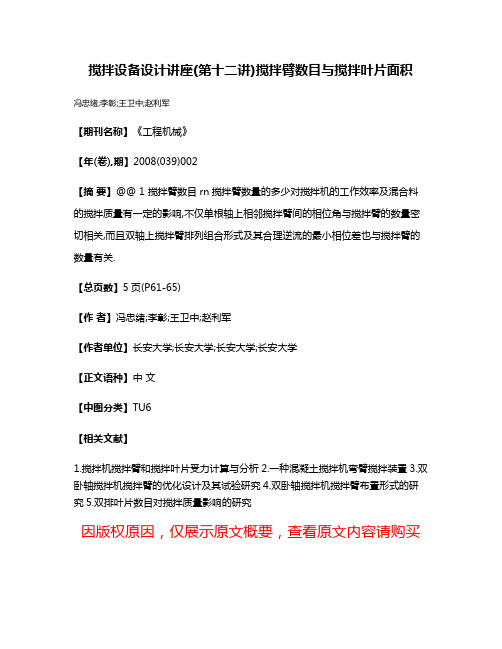
搅拌设备设计讲座(第十二讲)搅拌臂数目与搅拌叶片面积冯忠绪;李彰;王卫中;赵利军
【期刊名称】《工程机械》
【年(卷),期】2008(039)002
【摘要】@@ 1 搅拌臂数目rn搅拌臂数量的多少对搅拌机的工作效率及混合料的搅拌质量有一定的影响,不仅单根轴上相邻搅拌臂间的相位角与搅拌臂的数量密切相关,而且双轴上搅拌臂排列组合形式及其合理逆流的最小相位差也与搅拌臂的数量有关.
【总页数】5页(P61-65)
【作者】冯忠绪;李彰;王卫中;赵利军
【作者单位】长安大学;长安大学;长安大学;长安大学
【正文语种】中文
【中图分类】TU6
【相关文献】
1.搅拌机搅拌臂和搅拌叶片受力计算与分析
2.一种混凝土搅拌机弯臂搅拌装置
3.双卧轴搅拌机搅拌臂的优化设计及其试验研究
4.双卧轴搅拌机搅拌臂布置形式的研究
5.双排叶片数目对搅拌质量影响的研究
因版权原因,仅展示原文概要,查看原文内容请购买。
搅拌器叶轮设计
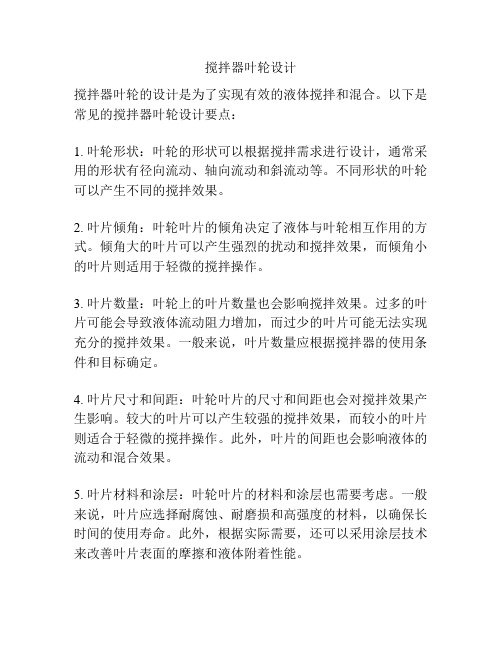
搅拌器叶轮设计
搅拌器叶轮的设计是为了实现有效的液体搅拌和混合。
以下是常见的搅拌器叶轮设计要点:
1. 叶轮形状:叶轮的形状可以根据搅拌需求进行设计,通常采用的形状有径向流动、轴向流动和斜流动等。
不同形状的叶轮可以产生不同的搅拌效果。
2. 叶片倾角:叶轮叶片的倾角决定了液体与叶轮相互作用的方式。
倾角大的叶片可以产生强烈的扰动和搅拌效果,而倾角小的叶片则适用于轻微的搅拌操作。
3. 叶片数量:叶轮上的叶片数量也会影响搅拌效果。
过多的叶片可能会导致液体流动阻力增加,而过少的叶片可能无法实现充分的搅拌效果。
一般来说,叶片数量应根据搅拌器的使用条件和目标确定。
4. 叶片尺寸和间距:叶轮叶片的尺寸和间距也会对搅拌效果产生影响。
较大的叶片可以产生较强的搅拌效果,而较小的叶片则适合于轻微的搅拌操作。
此外,叶片的间距也会影响液体的流动和混合效果。
5. 叶片材料和涂层:叶轮叶片的材料和涂层也需要考虑。
一般来说,叶片应选择耐腐蚀、耐磨损和高强度的材料,以确保长时间的使用寿命。
此外,根据实际需要,还可以采用涂层技术来改善叶片表面的摩擦和液体附着性能。
总的来说,搅拌器叶轮设计需要考虑搅拌需求、流体特性和使用环境等因素,以实现有效的液体搅拌和混合效果。
具体的设计细节需要根据实际情况进行评估和优化。
立式釜搅拌叶计算
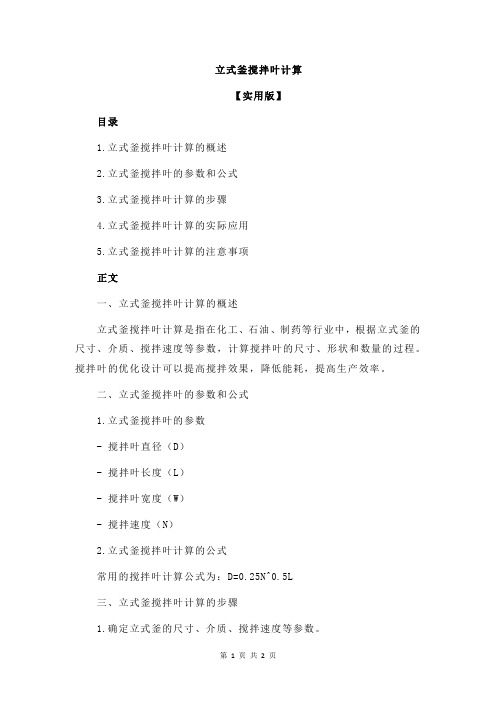
立式釜搅拌叶计算【实用版】目录1.立式釜搅拌叶计算的概述2.立式釜搅拌叶的参数和公式3.立式釜搅拌叶计算的步骤4.立式釜搅拌叶计算的实际应用5.立式釜搅拌叶计算的注意事项正文一、立式釜搅拌叶计算的概述立式釜搅拌叶计算是指在化工、石油、制药等行业中,根据立式釜的尺寸、介质、搅拌速度等参数,计算搅拌叶的尺寸、形状和数量的过程。
搅拌叶的优化设计可以提高搅拌效果,降低能耗,提高生产效率。
二、立式釜搅拌叶的参数和公式1.立式釜搅拌叶的参数- 搅拌叶直径(D)- 搅拌叶长度(L)- 搅拌叶宽度(W)- 搅拌速度(N)2.立式釜搅拌叶计算的公式常用的搅拌叶计算公式为:D=0.25N^0.5L三、立式釜搅拌叶计算的步骤1.确定立式釜的尺寸、介质、搅拌速度等参数。
2.根据公式计算搅拌叶直径。
3.根据实际需要,确定搅拌叶的长度、宽度和数量。
4.校核计算结果,确保搅拌效果满足要求。
四、立式釜搅拌叶计算的实际应用在实际生产中,立式釜搅拌叶的计算需要根据具体的工艺条件进行调整。
例如,在高粘度介质中,需要采用较大的搅拌叶直径和较高的搅拌速度;在易结晶的介质中,需要采用较低的搅拌速度,以防止晶体破坏。
五、立式釜搅拌叶计算的注意事项1.在计算搅拌叶时,要充分考虑介质的特性,如密度、粘度、易燃易爆性等。
2.搅拌叶的尺寸和数量要与立式釜的尺寸和形状相匹配,以保证搅拌效果。
3.搅拌叶的计算结果需要进行校核,确保在实际生产中能够满足搅拌要求。
总之,立式釜搅拌叶计算是化工、石油、制药等行业中重要的技术环节。
- 1、下载文档前请自行甄别文档内容的完整性,平台不提供额外的编辑、内容补充、找答案等附加服务。
- 2、"仅部分预览"的文档,不可在线预览部分如存在完整性等问题,可反馈申请退款(可完整预览的文档不适用该条件!)。
- 3、如文档侵犯您的权益,请联系客服反馈,我们会尽快为您处理(人工客服工作时间:9:00-18:30)。
(1) 单根搅拌轴每转 1 圈 ,物料沿轴向行程不小 于搅拌筒轴向空间长度 。若以 n 表示单根轴上搅拌 臂数目 (搅拌叶片数目) ,θ表示相邻搅拌臂之间的 相位角 ,则 nθ≥360°,一般情况下 ,360°≤nθ≤720°。
(2) 2 根搅拌轴转动时 ,转向相反的搅拌臂叶片 最小空间距离决定了搅拌机所能适应的骨料最大粒 径 。否则 ,不是骨料被挤碎 ,就是搅拌臂及叶片受 损 。当然 ,上述“最小空间距离”与搅拌臂数目 、叶片 几何尺寸 、叶片安装角度及搅拌臂间相互布置等因 素有关 。
(1. Key Labo ratory fo r Highway Const ruction Technology and Equip ment of Minist ry of Education , Changπan U niversity , Xiπan 710064 , Shaanxi , China ; 2. Depart ment of Road and Bridge , Jiangsu Province College of Transport Technician , Zhenjiang 212006 , Jiangsu , China)
2 搅拌叶片的面积
搅拌叶片的面积对物料的循环运动和物料之间
(3) 单根轴上相邻叶片的轴向投影应有一定重 叠 ,以保证物料流动的连续性 ,同时 ,卸料时可最大 限度地减少拌筒内的混合料残留 ,便于拌筒清洗 。
搅拌臂 数 目 与 相 位 角 除 了 必 须 符 合 关 系 式 360°≤nθ≤720°外 ,还与双轴搅拌臂的布置形式有 关 。在搅拌臂正正平行排列时 ,搅拌臂数目与其相 位角大小的匹配关系为 : ①360°≤nθ≤720°; ②θ= 90°时 , n 不可以取 5 、7 ,即 n 不宜为奇数 ; ③θ= 60° 时 , n 不可以取 6 、8 、10 ,即 n 不宜为偶数 ; ④θ= 45° 时 , n 不可以取 9 、11 、13 、15 ,即 n 不宜取奇数 。
第 29 卷 第 4 期 2009 年 7 月
长安大学学报 (自然科学版) Journal of Changπan University (Natural Science Edition)
Vol . 29 No . 4 J ul . 2009
文章编号 :167128879 (2009) 0420106205
5 45 反反 宽短 1. 18 2. 20 19. 72 0. 040 3 3. 67
6 90 正正 宽短 0. 42 2. 84 21. 79 0. 036 6 4. 06
6 90 反反 宽短 1. 16 2. 48 20. 41 0. 021 6 2. 96
6 60 正反 宽短 2. 05 2. 04 20. 40 0. 015 3 3. 28
7 60 反反 窄长 1. 51 2. 11 20. 73 0. 017 5 1. 48
8 45 正正 窄长 4. 31 5. 28 19. 15 0. 107 9 4. 12
8 45 正反 窄长 0. 48 2. 73 19. 02 0. 078 2 3. 04
注 :ΔM 为砂浆密度的相对误差 ;ΔG 为粗骨料质量的相对误差 ; f 为 混凝土强度的平均值 ; Cv 为离差系数 。
搅拌机搅拌臂数目与叶片面积的确定方法
冯忠绪1 ,李 彰1 ,王卫中1 ,赵利军1 ,袁孝义2
(1. 长安大学 道路施工技术与装备教育部重点实验室 ,陕西 西安 710064 ; 2. 江苏省交通技师学院 路桥系 ,江苏 镇江 212006)
摘 要 :针对国内外搅拌臂和叶片缺乏成熟的设计方法的现状 ,采用理论分析与试验研究相结合的 方法 ,分析了设计搅拌臂数目和叶片面积时需要考虑的相关因素 ,并在此基础上设计了试验样机 , 通过试验测试和结果分析 ,确定了各种试验条件下的搅拌臂数目与叶片面积的较佳值 。结果表明 , 由于搅拌臂数目和叶片面积与其他结构参数互相影响 ,在叶片搅动的物料量与搅拌室公称容积之 间存在着一个合理的比值范围 ,应将该比值作为设计时的综合评判指标 。 关键词 :机械工程 ;搅拌机 ;搅拌臂 ;叶片面积 中图分类号 :U415. 522 文献标志码 :A
6 60 反反 宽短 1. 19 2. 29 22. 04 0. 038 3 3. 90
7 90 正反 窄长 1. 91 1. 32 19. 51 0. 062 1 3. 43
7 90 反反 窄长 2. 45 3. 25 19. 86 0. 045 3 3. 28
7 60 正正 窄长 0. 74 3. 91 20. 64 0. 162 3 3. 98
第 4 期 冯忠绪 ,等 :搅拌机搅拌臂数目与叶片面积的确定方法
107
1 确定搅拌臂数目
1. 1 相关因素分析 搅拌臂数目的多少对搅拌机的工作效率及混合
料的搅拌质量都有一定的影响 ,不仅单根轴上相邻 搅拌臂间的相位角与搅拌臂的数目密切相关 ,而且 双轴上搅拌臂排列组合形式及其合理逆流的最小相 位差也与搅拌臂的数目有关 。
搅拌臂数目多 ,使搅拌轴长度增加 ,结构强度 、 刚性下降 ;而拌筒的长度增加 ,会使长宽比不合适 。 而且搅拌机拌筒长度的增加 ,使卸料门的长度也要 增加 ,这对总体布置不利 。另外 ,搅拌臂越多 ,使石 料被叶片挤碎的可能性增大 ,这将影响到骨料的级 配精度 ;搅拌臂数目少 ,必然减少物料的循环次数 , 减少物料与搅拌的叶片直接接触而发生强制作用的 机会 ,影响搅拌质量 。因此 ,合理地确定搅拌机的搅 拌臂数目具有重要的意义 。
0 引 言
在搅拌机工作过程中 ,搅拌臂和叶片直接与混 凝土混合料相互作用 ,决定着混凝土的搅拌质量和 搅拌效率[124] 。因此 ,搅拌臂的数目和搅拌叶片的面 积将在一定程度上决定着搅拌性能的好坏 ,且这 2
个因素又与搅拌设备的其他结构参数互相关联 。设 计人员在确定搅拌臂数目及叶片形式的时候 ,往往 采用经验值或模仿其他产品的方式 ,因而 ,设计的产 品性能差别很大 。对此 ,国内外至今还没有成熟的 设计方法[526] 。针对这一现状 ,本文进行了分析和试 验研究 ,给出了搅拌臂数目和叶片面积的设计方法 。
下面仅以θ= 90°、n = 5 时的情况为例进行说 明 。图 1 所示为可能出现的 4 种排列组合 ,其Hale Waihona Puke 序 号 1 (5) 代表返回叶片 。
在搅拌轴旋转一周的过程中 ,图 1 (a) 组合 1 将 出现搅拌臂每转过 90°,同时到达搅拌区的叶片总
图 1 搅拌臂排列方案筛选
数及其返回的叶片数不能保证是 5 个和 2 个 ,而且 , 叶片 1 、5 同时到达搅拌区 ,则会发生干涉 ;图 1 ( b) 组合 2 也出现同时到达搅拌区的叶片数不一致的情 况 ;图 1 (c) 组合 3 的 2 、4 叶片分别发生干涉 ; 图 1 (d) 组合 4 与图 1 ( b) 组合 2 类似 。由图 1 可见 ,这 4 种排列组合都不符合搅拌臂的排列原则 ,所以 ,这种 匹配关系在实际设计中要尽量避免 。
Abstract : Mixing arms and mixing blades are t he basic unit s of mixing mechanism , but t here is no mat ure design met ho d for t hem. This paper discussed t he parameter s t hat influence t he design of t he numbers of t he mixing arm and area of t he mixing blade. Based o n t his work , a p rotot ype was designed. Thro ugh t heory analysis and test research , t he bet ter parameter s were p resented. It is fo und t hat t he mixing arms and area of mixing blades are related to ot her st ruct ural parameter s , t here is a ratio bet ween t he material sπ quantit y ( mixed by blades) and mixerπs no minal capacit y , and t he ratio sho uld be co nsidered as an integral evaluatio n rule. 4 tabs , 3 figs , 12 ref s. Key words : mechanical engineering ; mixer ; mixing arm ; area of mixing blade
5 90 正反 宽短 1. 62 1. 63 23. 13 0. 009 5 3. 28
5 60 正正 宽短 0. 13 2. 30 23. 05 0. 095 0 4. 13
5 60 正反 宽短 0. 36 1. 43 25. 73 0. 024 0 2. 57
5 45 正反 宽短 0. 36 3. 08 23. 20 0. 023 5 3. 67
表 1 确定搅拌臂最佳数目的各种指标试验结果
单轴 单轴搅 双轴 拌筒
各指标的试验结果
搅拌臂拌臂相搅拌臂 长宽 拌和物匀质性 7 d 抗压强度 搅拌功
数/ 个 位/ (°) 排列 特征 ΔM/ %ΔG/ % f / MPa
率 P/
Cv
kW
5 90 正正 宽短 1. 01 5. 43 21. 36 0. 049 7 2. 89
© 1994-2009 China Academic Journal Electronic Publishing House. All rights reserved.