在精密成形技术中的地位及发展现状
精密锻造成形技术的应用及其发展

精密锻造成形技术的应用及其发展导言精密锻造成形技术是一种宏观加工方法,它是通过锻造工艺将金属材料一步一步地用压力变形,最终实现工件的成形。
这种工艺有很多优点,如精度高、表面质量好、材料利用率高等。
在制造业中应用非常广泛,尤其在航空、航天、汽车等高端制造领域,成为生产高精度零部件的重要工艺之一。
本文将探讨精密锻造成形技术的应用以及其未来的发展趋势。
精密锻造成形技术的应用航空、航天领域精密锻造成形技术在航空、航天领域中的应用非常广泛,主要用于生产复杂的金属材料构件,如强制润滑轴承、涡轮叶片、变形块等。
这些零部件在飞行过程中需要经受住极端的温度、压力和负载等环境的考验,要求零部件精度高、重量轻,以确保飞行器的正确运行。
由于精密锻造成形技术具有加工精度高、表面质量好、强度高等优点,所以被广泛应用于飞行器的生产中。
汽车制造随着汽车行业的不断发展和普及,对汽车制造的要求也越来越高。
精密锻造成形技术在汽车制造中的应用越来越广泛,主要用于生产发动机、转向系统、悬挂系统等重要部件。
比起传统的铸造工艺,精密锻造成形技术可以生产出更加精密、高强度、轻量的零部件,使汽车性能更加卓越,受到了汽车制造企业的广泛认可。
其他领域除了航空、航天和汽车制造领域外,精密锻造成形技术还在其他领域得到了广泛的应用。
例如,在医疗设备制造中,精密锻造成形技术可以生产出高精度的医疗器械;在工业机器人设备制造中,精密锻造成形技术可以生产出高精度的零部件,提高了工业机器人的精度和稳定性。
精密锻造成形技术的未来发展随着经济的不断发展和工业技术的不断进步,精密锻造成形技术的应用将会更加广泛。
其中,主要有以下几个方面的发展趋势:数字化加工随着人工智能、云计算、大数据等新技术的出现和发展,数字化加工技术将逐渐取代传统的机械加工。
数字化加工具有高效、节能、精度高等优点,可以提高生产效率,降低生产成本。
精密锻造成形技术的数字化加工技术在未来将更加广泛应用,提高生产自动化水平,实现工艺的数字化控制。
精密和超精密加工现状与发展趋势.doc
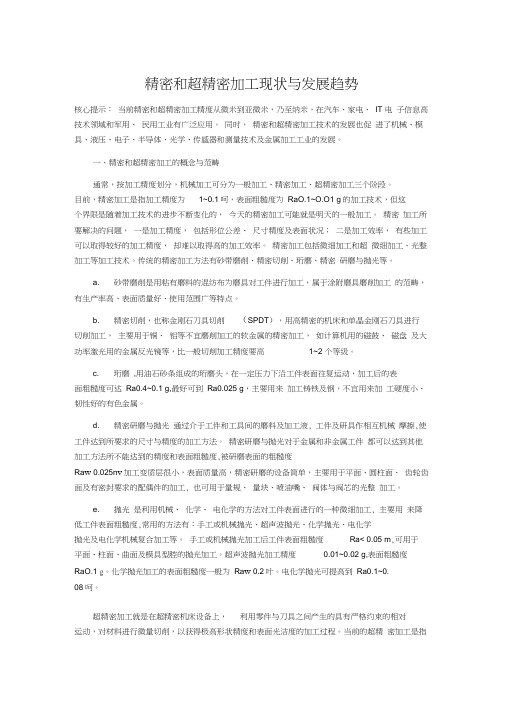
精密和超精密加工现状与发展趋势核心提示:当前精密和超精密加工精度从微米到亚微米,乃至纳米,在汽车、家电、IT 电子信息高技术领域和军用、民用工业有广泛应用。
同时,精密和超精密加工技术的发展也促进了机械、模具、液压、电子、半导体、光学、传感器和测量技术及金属加工工业的发展。
一、精密和超精密加工的概念与范畴通常,按加工精度划分,机械加工可分为一般加工、精密加工、超精密加工三个阶段。
目前,精密加工是指加工精度为1~0.1呵,表面粗糙度为RaO.1~O.O1 g的加工技术,但这个界限是随着加工技术的进步不断变化的,今天的精密加工可能就是明天的一般加工。
精密加工所要解决的问题,一是加工精度,包括形位公差、尺寸精度及表面状况;二是加工效率,有些加工可以取得较好的加工精度,却难以取得高的加工效率。
精密加工包括微细加工和超微细加工、光整加工等加工技术。
传统的精密加工方法有砂带磨削、精密切削、珩磨、精密研磨与抛光等。
a. 砂带磨削是用粘有磨料的混纺布为磨具对工件进行加工,属于涂附磨具磨削加工的范畴,有生产率高、表面质量好、使用范围广等特点。
b. 精密切削,也称金刚石刀具切削(SPDT),用高精密的机床和单晶金刚石刀具进行切削加工,主要用于铜、铝等不宜磨削加工的软金属的精密加工,如计算机用的磁鼓、磁盘及大功率激光用的金属反光镜等,比一般切削加工精度要高1~2 个等级。
c. 珩磨,用油石砂条组成的珩磨头,在一定压力下沿工件表面往复运动,加工后的表面粗糙度可达Ra0.4~0.1 g,最好可到Ra0.025 g,主要用来加工铸铁及钢,不宜用来加工硬度小、韧性好的有色金属。
d. 精密研磨与抛光通过介于工件和工具间的磨料及加工液, 工件及研具作相互机械摩擦,使工件达到所要求的尺寸与精度的加工方法。
精密研磨与抛光对于金属和非金属工件都可以达到其他加工方法所不能达到的精度和表面粗糙度,被研磨表面的粗糙度Ra w 0.025n v加工变质层很小,表面质量高,精密研磨的设备简单,主要用于平面、圆柱面、齿轮齿面及有密封要求的配偶件的加工, 也可用于量规、量块、喷油嘴、阀体与阀芯的光整加工。
精密锻造成形技术的应用及其发展通用版

安全管理编号:YTO-FS-PD832精密锻造成形技术的应用及其发展通用版In The Production, The Safety And Health Of Workers, The Production And Labor Process And The Various Measures T aken And All Activities Engaged In The Management, So That The Normal Production Activities.标准/ 权威/ 规范/ 实用Authoritative And Practical Standards精密锻造成形技术的应用及其发展通用版使用提示:本安全管理文件可用于在生产中,对保障劳动者的安全健康和生产、劳动过程的正常进行而采取的各种措施和从事的一切活动实施管理,包含对生产、财物、环境的保护,最终使生产活动正常进行。
文件下载后可定制修改,请根据实际需要进行调整和使用。
随着经济和科学技术的发展,常规的锻造技术已经不能满足发展的需求了。
精密锻造成形技术在航空航天、船舶、通用机械、汽车、兵器等领域的应用越来越广泛,越来越受到人们的关注。
本文将就精密锻造成形技术的种类进行介绍,并对其发展趋势进行阐述。
精密锻造成形技术,指的是在零件基本成形后,只需少许加工或无需加工就可以使用的零件成形技术,又称近净成形技术。
这种技术是以常规锻造成形技术为基础发展起来的,是由计算机信息技术、新能源、新材料等集成的一门应用技术。
现阶段,精密锻造成形技术主要用在精锻零件和精化毛坯等方面。
精密锻造成形技术的种类精密锻造成形技术,它的优势很明显,成本低、效率高、节能环保、精度高等。
这种成形工艺种类很多,按成形速度划分:高速精锻、一般精锻、慢速精锻成形等;以锻造过程中金属流动状况为标准划分:半闭、闭式、开式精锻成形工艺;按成形温度划分:超塑、室温、中温、高温精锻成形等;按成形技术分为:分流锻造、等温锻造、复动锻、复合成形、温精锻成形、热精锻成形和冷精锻成形等。
航空发动机涡轮叶片精密成形技术分析

航空发动机涡轮叶片精密成形技术分析【摘要】航空发动机涡轮叶片是航空发动机中至关重要的部件,对发动机的性能和效率起着关键作用。
涡轮叶片精密成形技术是一项关键技术,经历了多年的发展历程,逐步完善并应用于实际生产中。
本文从涡轮叶片的重要性入手,阐述了涡轮叶片精密成形技术的发展历程及关键步骤,探讨了该技术在航空领域的应用,并展望了未来的发展趋势。
通过本文的研究,有助于更深入地了解航空发动机涡轮叶片精密成形技术的重要性和发展现状,为相关领域的研究和应用提供参考和借鉴。
【关键词】航空发动机、涡轮叶片、精密成形技术、研究背景、研究意义、发展历程、关键步骤、应用、发展趋势、未来展望、总结1. 引言1.1 研究背景航空发动机涡轮叶片是航空发动机中的重要部件,直接影响着发动机的性能和效率。
随着航空业的发展和需求的提高,对于发动机的要求也越来越高,涡轮叶片的精密成形技术显得尤为重要。
在过去的几十年里,涡轮叶片的制造技术已经取得了长足的进步,包括材料的优化和加工工艺的改进。
随着飞行速度的提高和环保要求的增加,传统的涡轮叶片制造技术已经难以满足对高性能和高精度的要求。
研究涡轮叶片精密成形技术成为当前航空发动机领域的热点之一。
通过精密成形技术,可以实现涡轮叶片的高精度、高效率的制造,提高发动机的性能和可靠性。
涡轮叶片精密成形技术还可以减少材料浪费和能耗,降低制造成本,符合航空工业的可持续发展要求。
深入研究航空发动机涡轮叶片精密成形技术的背景意义重大,能够为航空领域的技术进步和发展提供重要支持和保障。
1.2 研究意义航空发动机涡轮叶片精密成形技术的研究意义在于提高航空发动机的性能和效率,进一步推动航空工业的发展。
随着航空业的快速发展,对涡轮叶片精密成形技术的要求也越来越高。
研究该技术能够提高航空发动机的性能和可靠性,减少能源消耗和碳排放,从而符合节能减排的国际趋势。
涡轮叶片是航空发动机的关键部件之一,其质量和制造工艺直接影响整个发动机的工作效率和安全性。
我国精密加工的现状及发展趋势

我国精密加工的现状及发展趋势内容摘要:近十年来,美国十分注重发展精密热加工和提高性能一体化技术。
如:铝锂合金粉制件精密热成形可使零件比刚度提高30%;碳化硅/铝复合材料可使零件的比刚度提高30%一75%;单晶叶片精铸可以提高涡轮温度55℃、节省燃料10%;快速凝固粉末层压式涡轮叶片,可使发动机涡轮温度提高220℃、油耗降低8.4%、飞机起飞质量降低7.4%,发动机推重比提高30%一50%。
发展精密热加工技术,并与提高零部件性能研究一体化,符合我国国防科技发展对关键基础加工技术研究所提出的要求。
正文:一、精密和超精密加工的概念与范畴通常,按加工精度划分,机械加工可分为一般加工、精密加工、超精密加工三个阶段。
目前,精密加工是指加工精度为1~0.1?;m,表面粗糙度为Ra0.1~0.01?;m的加工技术,但这个界限是随着加工技术的进步不断变化的,今天的精密加工可能就是明天的一般加工。
精密加工所要解决的问题,一是加工精度,包括形位公差、尺寸精度及表面状况;二是加工效率,有些加工可以取得较好的加工精度,却难以取得高的加工效率。
精密加工包括微细加工和超微细加工、光整加工等加工技术。
传统的精密加工方法有砂带磨削、精密切削、珩磨、精密研磨与抛光等。
a.砂带磨削是用粘有磨料的混纺布为磨具对工件进行加工,属于涂附磨具磨削加工的范畴,有生产率高、表面质量好、使用范围广等特点。
b.精密切削,也称金刚石刀具切削(SPDT),用高精密的机床和单晶金刚石刀具进行切削加工,主要用于铜、铝等不宜磨削加工的软金属的精密加工,如计算机用的磁鼓、磁盘及大功率激光用的金属反光镜等,比一般切削加工精度要高1~2个等级。
c.珩磨,用油石砂条组成的珩磨头,在一定压力下沿工件表面往复运动,加工后的表面粗糙度可达Ra0.4~0.1?;m,最好可到Ra0.025?;m,主要用来加工铸铁及钢,不宜用来加工硬度小、韧性好的有色金属。
d.精密研磨与抛光通过介于工件和工具间的磨料及加工液,工件及研具作相互机械摩擦,使工件达到所要求的尺寸与精度的加工方法。
精密加工技术的发展现状与应用
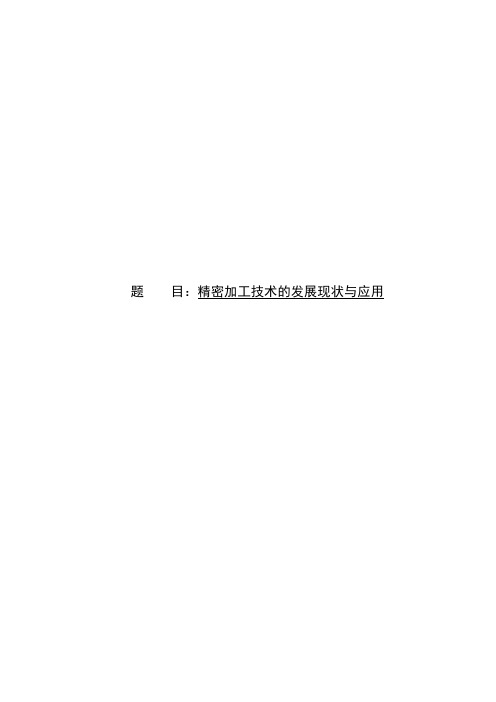
题目:精密加工技术的发展现状与应用内容摘要通过砂带研磨、精密切削、超精密磨削、珩磨、精密研磨、抛光等几种传统精密加工方法的论述对比,论述现有的传统精密加工方法;再通过对孔加工技术等技术的最新精密加工发展来论述目前国内精密加工发展趋势及前景;同时通过对美日欧等发达国家最新的精密加工技术发展情况来论述目前国外精密加工技术的发展方向及前景。
关键词:精加工;发展;应用内容摘要 (I)引言 (1)1 精密加工技术的发展现状 (1)1.1 砂带研磨 (1)1.2 精密切削 (1)1.3 超精密磨削 (2)1.4 珩磨 (3)1.5 精密研磨 (3)1.6 抛光 (3)2 国内精密加工技术发展趋势 (5)2.1 北京机床研究所 .............................................................. 错误!未定义书签。
2.2 航天航空工业部三零三部所 .......................................... 错误!未定义书签。
3.3 其他研究所 ...................................................................... 错误!未定义书签。
3.4 超精密加工技术发展趋势 .............................................. 错误!未定义书签。
3 国外精密加工技术发展前景 (8)3.1 美国 (8)3.1 欧洲 (8)3.2 日本 (8)4 研究和探讨 (9)4.1 精密加工技术 (9)4.2 开发精密的机械机构 (9)4.3 开发高精度的测试系统 (9)4.4 开发适用于精密加工并能取得高精度、高表面质量的新型材料 (10)5 结论 (11)参考文献 (12)为了满足现代先进制造与加工技术的需要,提高生产效率和改善零件的加工质量,精密加工技术和超精密加工技术已成为目前高科技技术领域的基础,超精密加工技术已成为社会生产发展的一个重大趋势。
航空发动机涡轮叶片精密成形技术及其发展趋势

航空发动机涡轮叶片精密成形技术及其发展趋势航空发动机涡轮叶片精密成形技术及其发展趋势导言航空发动机作为现代航空的重要组成部分,对于保障飞机的正常运行和飞行安全至关重要。
其中,涡轮叶片是发动机的核心组件之一,其性能直接关系到发动机的效率、燃料消耗和环境排放等方面。
为了满足航空工业对高性能发动机的需求,航空发动机涡轮叶片精密成形技术应运而生。
本文将以航空发动机涡轮叶片精密成形技术为主题,全面评估该技术的深度和广度,并探讨其未来发展趋势。
1. 理论基础(1)航空发动机涡轮叶片的作用和重要性航空发动机涡轮叶片是将高温高速气流能量转化为机械动力的关键部件。
其工作环境要求具备高强度、高稳定性和高耐腐蚀性能。
涡轮叶片的设计和制造过程相对复杂,对相关技术有着严苛的要求。
(2)精密成形技术的基本原理精密成形技术是通过对原材料进行精确控制和再塑性变形,实现对复杂几何形状部件的制造工艺。
其基本原理包括材料变形行为研究、成形工艺分析和模具设计等方面。
在航空发动机涡轮叶片制造中,精密成形技术可以实现对叶片外形的精确控制和优化。
2. 技术应用(1)常见的精密成形技术在航空发动机涡轮叶片精密成形中,常见的技术包括点焊成形、数控机床精密加工和电解成形等。
其中,点焊成形技术通过在叶片表面施加电脉冲,使其在高温高压气流冲击下形成预定形状。
数控机床精密加工技术则可以实现对叶片进行高精度的铣削和打磨。
电解成形技术则通过电解液和电极的作用,使叶片在电场和化学作用下形成所需形状。
(2)发展趋势随着航空工业的不断发展和对发动机性能的要求日益提高,航空发动机涡轮叶片精密成形技术也在不断创新和改进。
目前,有几个主要的发展趋势值得关注:-先进材料的应用。
随着复合材料和高温合金等新材料的发展和应用,航空发动机涡轮叶片的材料性能得到了显著提升。
这也为精密成形技术提供了更高的工艺要求和技术挑战。
-数字化制造的推广。
在涡轮叶片制造过程中,数字化制造技术的应用可以提高生产效率和产品质量,减少错误率和浪费。
精密微塑性成形技术的现状及发展趋势论文

精密微塑性成形技术的现状及发展趋势论文精密微塑性成形技术的现状及发展趋势论文引言微塑性成形技术主要是采用塑性变形的方式进行形成微型零件的工艺方法,在多种复杂形状微小零件作用下能够达到微米量级,所以在微型零件的制造上较为适用。
微塑性成形技术并非是传统塑性成形工艺的简单等比例缩小,其作为新的研究领域对实际的发展有着重要促进作用,故此加强这一领域的理论研究就有着实质性意义。
1 精密微塑性成形原理特征及方法分析1.1 精密微塑性成形原理特征分析科技的发展带来了生产的效率提升,在微塑性成形技术的发展过程中经历了不同时期的进步,传统的成形工艺按照比例微缩到微观领域在参数上的适应性就失去了。
而微塑性成形技术在现阶段已经成了多种学科交叉的边缘技术,实际成形中的润滑以及摩擦也与此同时发生了一些变化,所以宏观摩擦学当中的摩擦理论就不能有效适应。
但由于微小尺度下秒面积与体积的增大,所以在摩擦力就对成形造成的影响逐渐扩大,那么润滑就是比较关键的因素。
从实际的成形原理来看,在工件进行微缩化的过程中,此时在摩擦力上就会随之加大,压力的加大那么封闭润滑包中的润滑油压强也随之加大,这样就支持以及对成形的载荷实现了传递,进而对摩擦也减小了。
在工件的尺寸不断的微小化过程中,开口润滑包面积减少幅度不是很大,但在封闭润滑包的面积减少幅度就相对比较大,采用固体润滑剂的过程中由于不存在润滑剂溢出的状况所以就对摩擦系数的影响也较小。
1.2 精密微塑性成形方法分析微塑性成形工艺及方法的相关研究主要是在微冲压以及微体积成形方面,其中的微体积成形主要是进行的微连接器以及顶杆和叶片等微型的期间精密形成。
以螺钉为例,其最小的尺寸只有0.8 微米,而微成形胚料的最小直径是0.3 微米,在模压成形的微结构构建沟槽的最小宽度能够达到二百纳米。
另外在微冲压成形这一方法上最为重要的就是进行的薄板微深拉伸以及增量成形等方法。
微型器件的微塑性成形技术属于新兴的研究领域,在成形的方法上主要就是实现毫米级的微型器件精密微成形,在微塑性成形技术的不断发展下,这一技术会进一步的优化。
我国精密锻造成型技术及应用
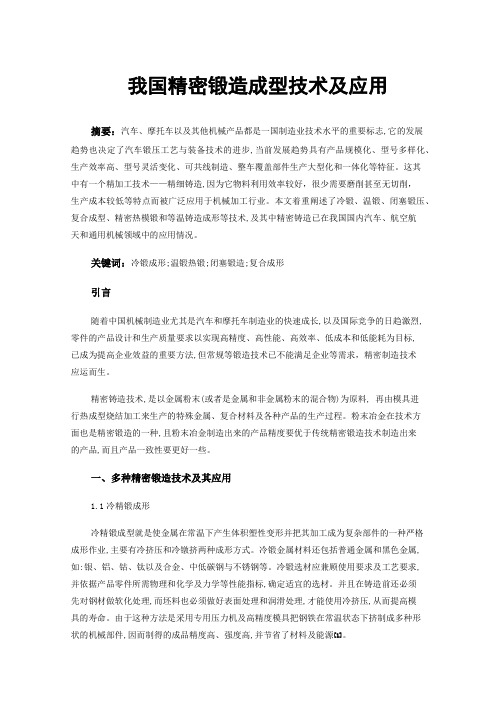
我国精密锻造成型技术及应用摘要:汽车、摩托车以及其他机械产品都是一国制造业技术水平的重要标志,它的发展趋势也决定了汽车锻压工艺与装备技术的进步,当前发展趋势具有产品规模化、型号多样化、生产效率高、型号灵活变化、可共线制造、整车覆盖部件生产大型化和一体化等特征。
这其中有一个精加工技术——精细铸造,因为它物料利用效率较好,很少需要磨削甚至无切削,生产成本较低等特点而被广泛应用于机械加工行业。
本文着重阐述了冷锻、温锻、闭塞锻压、复合成型、精密热模锻和等温铸造成形等技术,及其中精密铸造已在我国国内汽车、航空航天和通用机械领域中的应用情况。
关键词:冷锻成形;温锻热锻;闭塞锻造;复合成形引言随着中国机械制造业尤其是汽车和摩托车制造业的快速成长,以及国际竞争的日趋激烈,零件的产品设计和生产质量要求以实现高精度、高性能、高效率、低成本和低能耗为目标,已成为提高企业效益的重要方法,但常规等锻造技术已不能满足企业等需求,精密制造技术应运而生。
精密铸造技术,是以金属粉末(或者是金属和非金属粉末的混合物)为原料, 再由模具进行热成型烧结加工来生产的特殊金属、复合材料及各种产品的生产过程。
粉末冶金在技术方面也是精密锻造的一种,且粉末冶金制造出来的产品精度要优于传统精密锻造技术制造出来的产品,而且产品一致性要更好一些。
一、多种精密锻造技术及其应用1.1冷精锻成形冷精锻成型就是使金属在常温下产生体积塑性变形并把其加工成为复杂部件的一种严格成形作业,主要有冷挤压和冷镦挤两种成形方式。
冷锻金属材料还包括普通金属和黑色金属,如:银、铝、钴、钛以及合金、中低碳钢与不锈钢等。
冷锻选材应兼顾使用要求及工艺要求,并依据产品零件所需物理和化学及力学等性能指标,确定适宜的选材。
并且在铸造前还必须先对钢材做软化处理,而坯料也必须做好表面处理和润滑处理,才能使用冷挤压,从而提高模具的寿命。
由于这种方法是采用专用压力机及高精度模具把钢铁在常温状态下挤制成多种形状的机械部件,因而制得的成品精度高、强度高,并节省了材料及能源[1]。
精密和超精密加工现状与发展趋势.doc

精密和超精密加工现状与发展趋势核心提示:当前精密和超精密加工精度从微米到亚微米,乃至纳米,在汽车、家电、IT电子信息高技术领域和军用、民用工业有广泛应用。
同时,精密和超精密加工技术的发展也促进了机械、模具、液压、电子、半导体、光学、传感器和测量技术及金属加工工业的发展。
一、精密和超精密加工的概念与范畴通常,按加工精度划分,机械加工可分为一般加工、精密加工、超精密加工三个阶段。
目前,精密加工是指加工精度为1~0.1μm,表面粗糙度为Ra0.1~0.01μm的加工技术,但这个界限是随着加工技术的进步不断变化的,今天的精密加工可能就是明天的一般加工。
精密加工所要解决的问题,一是加工精度,包括形位公差、尺寸精度及表面状况;二是加工效率,有些加工可以取得较好的加工精度,却难以取得高的加工效率。
精密加工包括微细加工和超微细加工、光整加工等加工技术。
传统的精密加工方法有砂带磨削、精密切削、珩磨、精密研磨与抛光等。
a. 砂带磨削是用粘有磨料的混纺布为磨具对工件进行加工,属于涂附磨具磨削加工的范畴,有生产率高、表面质量好、使用范围广等特点。
b. 精密切削,也称金刚石刀具切削(SPDT),用高精密的机床和单晶金刚石刀具进行切削加工,主要用于铜、铝等不宜磨削加工的软金属的精密加工,如计算机用的磁鼓、磁盘及大功率激光用的金属反光镜等,比一般切削加工精度要高1~2个等级。
c. 珩磨,用油石砂条组成的珩磨头,在一定压力下沿工件表面往复运动,加工后的表面粗糙度可达Ra0.4~0.1μm,最好可到Ra0.025μm,主要用来加工铸铁及钢,不宜用来加工硬度小、韧性好的有色金属。
d. 精密研磨与抛光通过介于工件和工具间的磨料及加工液,工件及研具作相互机械摩擦,使工件达到所要求的尺寸与精度的加工方法。
精密研磨与抛光对于金属和非金属工件都可以达到其他加工方法所不能达到的精度和表面粗糙度,被研磨表面的粗糙度Ra≤0.025μm加工变质层很小,表面质量高,精密研磨的设备简单,主要用于平面、圆柱面、齿轮齿面及有密封要求的配偶件的加工,也可用于量规、量块、喷油嘴、阀体与阀芯的光整加工。
精密注塑成型技术最新发展动态

精密注塑成型技术最新发展动态精密注塑成型技术是塑料加工领域的一项关键技术,随着制造业的快速发展和市场需求的日益精细,其技术进步和创新步伐不断加速。
该技术在电子、汽车、医疗、包装等行业中扮演着至关重要的角色,对产品的尺寸精度、表面质量及功能性有着直接影响。
以下是精密注塑成型技术最新发展的六个主要动态:一、材料科技的进步随着新型高分子材料的不断涌现,如高性能工程塑料、生物基及可降解塑料,精密注塑成型技术得以拓展应用边界。
这些材料不仅具有优异的机械性能、耐热性、化学稳定性,还能够在微观层面上实现精确控制,满足复杂零件的成型需求。
例如,液晶聚合物(LCP)和聚醚醚酮(PEEK)在精密电子连接器中的应用,展现了超薄壁成型和高度尺寸稳定性的能力。
二、智能化与自动化技术的融合工业4.0浪潮下,精密注塑成型技术与智能制造深度结合,通过物联网(IoT)、大数据分析、(AI)等技术,实现了生产过程的全面数字化和智能化。
智能注塑机能够实时监控模具温度、注射压力、冷却速率等参数,自动调整工艺条件,保证成型过程的高度稳定性和重复性,显著提升产品合格率。
同时,自动化生产线的集成,如机器人取件、视觉检测系统的引入,进一步优化了生产效率和质量控制。
三、微注塑与纳米注塑技术的突破微注塑技术针对微型零件的生产,如微流控芯片、医疗器械微组件等,要求极高的精度和一致性。
新技术如微层叠注塑、激光辅助注塑等,能够在微米甚至纳米尺度上实现材料的精确沉积和结构成型,满足了精密医疗、光电子等行业的特殊需求。
纳米注塑则通过将纳米材料注入塑料基体中,改善材料的物理和化学性能,如提高强度、导电性或抗菌性,拓宽了精密注塑制品的功能性应用范围。
四、环保与可持续性的强化面对全球环保趋势,精密注塑行业也在积极应对,开发出更多环保解决方案。
这包括使用生物基或回收塑料原料,减少碳足迹;改进工艺流程,降低能耗与废弃物排放;以及开发易于回收或可降解的产品设计。
此外,轻量化设计也是提高材料利用率和减少资源消耗的重要方向,特别是在汽车和航空航天领域,通过精密注塑成型技术实现复杂结构件的轻量化,对提升能效和减少环境影响具有重要意义。
精密和超精密加工技术现状和发展趋势

精密和超精密加工技术现状和发展趋势1.引言国际上在超精密加工技术方面处于领先地位的国家有美国、德国和日本发达国家中,美国、日本、德国等在高技术领域(如国防工业、集成电路、信息技术产业等)之所以一直领先,与这些国家高度重视和发展精密、超精密制造技术有极其重要的关系。
由于加工技术水平的发展,精密和超精密加工划分的界限逐渐向前推移,但在具体数值上没有确切的定义。
被加工零件的尺寸精度在 1.0~0.1μm,表面粗糙度Ra在0.1~0.03μm之间的加工方法称为精密加工。
超精密加工当前是指被加工零件的尺寸精度高于0.1μm,表面粗糙度Ra小于0.025μm,以及所用机床定位精度的分辨率和重复性高于0.01μm的加工技术,亦称之为亚微米级加工技术,且正在向纳米级加工技术发展超精密加工技术主要包括:超精密加工的机理,超精密加工的设备制造技术,超精密加工工具及刃磨技术,超精密测量技术和误差补偿技术,超精密加工工作环境条件。
2.发展现状美国是开展研究最早的国家,也是迄今处于世界领先地位的国家。
早在50年代末,由于航天等尖端技术发展的需要,美国首先发展了金刚石刀具的超精密切削技术,并发展了相应的空气轴承主轴的超精密机床,用于加工激光核聚变反射镜、战术导弹及载人飞船用球面、非球面大型零件。
20世纪80年代后期,美国通过能源部“激光核聚变项目”和陆、海、空三军“先进制造技术开发计划”,对超精密金刚石切削机床的开发研究,投入了巨额资金和大量人力,实现了大型零件的微英寸超精密加工。
如美国劳伦斯利弗莫尔国家实验室已经研制出一台大型光学金刚石车床(Large Op tics Diam ond Turn ing Machine, LODTM ), 是一台最大加工直径为1.63m的立式车床,定位精度可达28nm,借助在线误差补偿能力,它已实现了距离超过1m而直线度误差只有±25nm 的加工。
在美国能源部支持下,LLI实验室和Y-12工厂合作,与1983年成功地研制出大型超精密金刚石车床(DTM—3型)。
精密与超精密加工技术现状和发展展望

精密与超精密加工技术现状和发展展望精密加工技术是一种在当今制造业中非常重要的技术,它的发展与制造业的发展息息相关。
精密加工技术是通过对材料进行高精度的加工来制造出各种精密零部件,这些精密零部件被广泛应用于汽车、航空航天、医疗器械、电子产品等各个领域。
现阶段,精密加工技术已经取得了很大的进步,各种高精度的加工设备和加工工艺层出不穷。
在这些技术发展的基础上,超精密加工技术应运而生。
超精密加工技术是一种相对于精密加工技术更加高端、更加精密的加工技术,它可以实现对材料的超高精度加工,甚至可以达到纳米级的精度。
这种技术对于一些特殊材料的加工非常重要,比如硬质合金、钢、陶瓷等材料。
超精密加工技术的发展展望是非常乐观的。
随着科学技术的不断进步,各种先进的加工设备和工艺将不断涌现。
在这种趋势下,超精密加工技术将会得到更加广泛的应用。
在汽车工业中,超精密加工技术可以用于制造高压油泵的零部件,提高汽车发动机燃油的利用率;在医疗器械领域,超精密加工技术可以用于制造各种医疗器械的零部件,提高医疗器械的精度和安全性。
在未来的发展中,我们还可以看到超精密加工技术将会在航空航天领域得到更广泛的应用。
超精密加工技术可以制造出更加轻巧和高强度的航空零部件,提高航空器的性能和安全性。
超精密加工技术在电子产品领域也有很大的潜力,它可以制造出更小巧、更精密的电子元件,提高电子产品的性能和可靠性。
精密加工技术和超精密加工技术的发展是非常重要的。
它们直接关系到制造业的发展和产品的质量。
相信随着科学技术的不断进步,这些技术将会取得更大的突破,为各个领域带来更多的创新和发展。
精密与超精密加工技术的现状和发展展望精密加工技术是制造业中至关重要的一环,它的发展与制造业的发展密不可分。
精密加工技术通过对材料进行高精度的加工,制造出各种精密零部件,广泛应用于汽车、航空航天、医疗器械、电子产品等各个领域。
当前,精密加工技术已取得了长足的发展,各种高精度加工设备和工艺不断涌现。
关于模具制造技术的现状及发展的研究
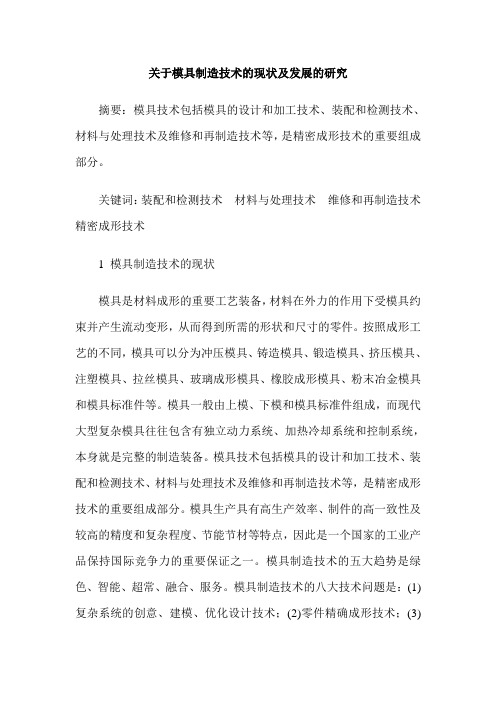
关于模具制造技术的现状及发展的研究摘要:模具技术包括模具的设计和加工技术、装配和检测技术、材料与处理技术及维修和再制造技术等,是精密成形技术的重要组成部分。
关键词:装配和检测技术材料与处理技术维修和再制造技术精密成形技术1 模具制造技术的现状模具是材料成形的重要工艺装备,材料在外力的作用下受模具约束并产生流动变形,从而得到所需的形状和尺寸的零件。
按照成形工艺的不同,模具可以分为冲压模具、铸造模具、锻造模具、挤压模具、注塑模具、拉丝模具、玻璃成形模具、橡胶成形模具、粉末冶金模具和模具标准件等。
模具一般由上模、下模和模具标准件组成,而现代大型复杂模具往往包含有独立动力系统、加热冷却系统和控制系统,本身就是完整的制造装备。
模具技术包括模具的设计和加工技术、装配和检测技术、材料与处理技术及维修和再制造技术等,是精密成形技术的重要组成部分。
模具生产具有高生产效率、制件的高一致性及较高的精度和复杂程度、节能节材等特点,因此是一个国家的工业产品保持国际竞争力的重要保证之一。
模具制造技术的五大趋势是绿色、智能、超常、融合、服务。
模具制造技术的八大技术问题是:(1)复杂系统的创意、建模、优化设计技术;(2)零件精确成形技术;(3)大型结构件成形技术;(4)高速精密加工技术;(5)微纳器件与系统;(6)智能制造装备;(7)智能化集成化传动技术;(8)数字化工厂。
机械工程11个技术领域是:(1)产品设计;(2)成形制造;(3)智能制造;(4)精密与微纳制造;(5)仿生制造;(6)再制造;(7)流体传动与控制;(8)齿轮;(9)轴承;(10)模具;(11)刀具。
2 模具制造技术的发展趋势是模具数字化设计制造技术2.1 概诉模具数字化设计制造技术的核心是CAD/CAM/CAE,应用模具数字化设计制造技术可以显著缩短模具开发周期,改善产品质量,降低产品成本,提高服务水平,即可以提高模具企业的TQCS水平。
对于推动模具行业的转型和提升模具工业的核心竞争力具有深远的意义。
航空发动机涡轮叶片精密成形技术分析

航空发动机涡轮叶片精密成形技术分析航空发动机涡轮叶片是发动机的关键部件,直接影响飞机的动力性能和燃油效率。
由于涡轮叶片受到高温、高速气流的作用,要求具有较高的耐热性和耐磨损性。
目前,随着航空工业的发展和技术进步,涡轮叶片的精密成形技术正在不断地得到改进和提高。
涡轮叶片的精密成形技术包括铸造、锻造和精密加工等多种工艺,并且国内外都在不断地进行技术创新和改进。
本文将重点分析涡轮叶片精密成形技术的发展现状和趋势,介绍其工艺流程和关键技术,以及面临的挑战和解决方案。
一、涡轮叶片精密成形技术发展现状涡轮叶片的精密成形技术经历了从传统手工制造到数控自动化生产的发展过程。
在20世纪初期,涡轮叶片的生产主要依靠手工锻造和加工,工艺简单,但精度和稳定性较低。
随着航空工业的发展和需求的增长,涡轮叶片的生产逐渐向自动化、数字化和精密化方向发展。
目前,国内外涡轮叶片的精密成形技术主要包括以下几种:1. 铸造技术:铸造是目前涡轮叶片生产的主流工艺之一。
通过模具和熔化金属的注入,可以实现复杂形状的叶片生产,具有成本低、生产效率高等优点。
但铸造工艺对原材料的要求较高,而且易产生气孔、夹渣等缺陷,影响叶片的性能和寿命。
2. 锻造技术:锻造是一种利用模具和高温高压使金属变形的工艺,可以实现叶片的精密成形。
锻造工艺具有成本低、材料利用率高等优点,但其工艺控制和模具设计较为复杂,难以实现复杂形状的叶片生产。
3. 精密加工技术:精密加工技术包括CNC加工、激光制造、电火花加工等,可以实现叶片的精确成形和表面处理。
这些技术在叶片成形的精度和表面质量上具有优势,但成本较高,适用于对叶片性能要求较高的航空发动机。
以上几种技术各有优劣,但目前主要的趋势是将这些技术进行有机结合,实现叶片生产的自动化、数字化和精密化。
涡轮叶片的精密成形技术涉及到多个关键工艺和技术,如材料选型、模具设计、热处理工艺、表面涂层等。
1. 材料选型:涡轮叶片所采用的材料通常为镍基合金或钛合金,具有高强度、高温性能和耐腐蚀性能。
精密制造发展现状

精密制造发展现状近年来,精密制造领域取得了长足的发展,其技术水平和产业规模均呈现出快速增长的趋势。
精密制造是一种将工艺精度提高到纳米或亚纳米级别的制造技术,主要应用于电子信息、光学仪器、航空航天等高科技领域。
目前,精密制造在我国的发展已经取得了显著的成就。
一方面,我国在高精密制造设备的研发和生产方面取得了重要突破。
高精密加工设备、光刻机、电子束曝光设备等关键装备的性能和精度已经达到国际领先水平。
另一方面,我国的精密制造技术也在不断突破创新,例如光刻、纳米加工、微细加工等技术的研究和应用都取得了令人瞩目的成果。
在产业方面,我国的精密制造产业也呈现出快速发展的态势。
精密制造企业不断涌现,整个产业链的建设也日渐完善。
从原材料供应到设备研发,再到加工生产和产品销售,我国已经形成了一个较为完整的精密制造产业体系。
同时,我国的精密制造产品也逐渐扩大了在国际市场的份额,出口额和辐射带动就业等经济效益显著。
精密制造的发展已经成为推动我国制造业升级和高质量发展的重要力量。
通过提高产品质量和技术水平,精密制造不仅可以满足国内市场的需求,还能够扩大出口,提升国际竞争力。
此外,精密制造的发展还能推动相关产业发展,促进创新和创业,增加就业机会,推动经济社会的持续发展。
然而,精密制造仍面临一些挑战和问题。
首先,我国在核心关键技术上与国际先进水平仍存在差距,需要加大研发投入,加强国际合作,推动技术进步。
其次,精密制造行业与环境、安全等方面的协调还有待完善,需要建立健全的政策法规和标准体系。
同时,人才培养和引进也是精密制造发展的重要问题,需要加强人才队伍建设,提高全社会对精密制造人才的重视程度。
总之,精密制造作为一项关键的制造技术,在我国得到了快速发展。
其发展已经取得了显著成果,为我国的制造业升级和经济发展做出了重要贡献。
然而,精密制造仍面临一些挑战,需要进一步加大投入和改革创新,以提高我国精密制造的竞争力和核心技术水平。
精密加工制造技术的研究与发展

精密加工制造技术的研究与发展摘要:在现代工业制造中,精密加工制造技术是不可或缺的重要组成部分,涉及到诸如航空、航天、汽车、半导体等高科技领域,是现代工业制造的核心技术之一。
本文将从精密加工制造的定义入手,探讨其发展历程、选型原则、现状与趋势,并指出未来的确切发展方向。
一、精密加工制造技术的定义精密加工制造技术是指通过机械加工以及其他相关的技术手段,将材料的形状、尺寸和表面质量等方面达到高精度、高表面质量的制造技术。
其具有工业制造和制造技术的核心地位,也是工业制造中不可或缺的组成部分。
精密加工制造技术已经涉及到诸如航空、航天、汽车、半导体等高科技领域,在现代制造业中已经成为了重要的核心技术。
二、精密加工制造技术的发展历程自20世纪50年代起,精密加工制造技术便开始在各个行业领域中得到广泛的应用。
最初,精密加工制造技术主要是通过手工操作来完成的,对于材料的尺寸和表面质量控制的精确度较低。
随着科技水平的提高和机械设备的不断更新,精密加工制造技术也得到了快速的发展与改进。
各种精密加工制造的新技术和新工艺也越来越多地应用于工业制造中。
在当今的制造业中,我们已经可以看到高端机床,多轴机、数控加工设备、激光加工设备、电解加工设备等等,这些设备都是以精密加工制造技术为核心而诞生的。
三、精密加工制造技术的选型原则正确的加工选型是精密加工制造技术的成功应用的前提。
选择适合本次精密加工的机床、设备和工具材料等,是非常关键的。
一般来说,精密加工制造会依据材料的种类、制造工艺的要求来选择该精密加工技术的方法。
为了确保质量和生产效率,还需要在加工选型的过程中,充分考虑材料的硬度、表面欠损、精度要求以及加工工艺的适应性和经济性,并且需要定期地维护设备的表面质量,进行磨损情况的监测和判断,保证设备的加工质量。
四、精密加工制造技术的现状与趋势当今的精密加工制造技术已经非常成熟,其应用范围覆盖了汽车、航空、航天、半导体等多个领域。
精密模锻发展现状
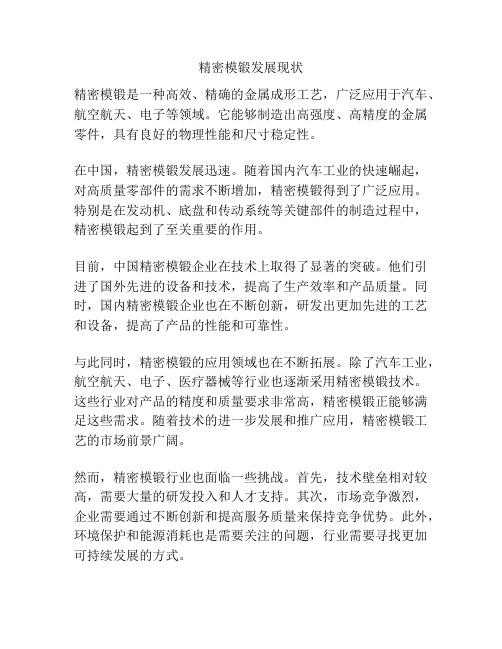
精密模锻发展现状
精密模锻是一种高效、精确的金属成形工艺,广泛应用于汽车、航空航天、电子等领域。
它能够制造出高强度、高精度的金属零件,具有良好的物理性能和尺寸稳定性。
在中国,精密模锻发展迅速。
随着国内汽车工业的快速崛起,对高质量零部件的需求不断增加,精密模锻得到了广泛应用。
特别是在发动机、底盘和传动系统等关键部件的制造过程中,精密模锻起到了至关重要的作用。
目前,中国精密模锻企业在技术上取得了显著的突破。
他们引进了国外先进的设备和技术,提高了生产效率和产品质量。
同时,国内精密模锻企业也在不断创新,研发出更加先进的工艺和设备,提高了产品的性能和可靠性。
与此同时,精密模锻的应用领域也在不断拓展。
除了汽车工业,航空航天、电子、医疗器械等行业也逐渐采用精密模锻技术。
这些行业对产品的精度和质量要求非常高,精密模锻正能够满足这些需求。
随着技术的进一步发展和推广应用,精密模锻工艺的市场前景广阔。
然而,精密模锻行业也面临一些挑战。
首先,技术壁垒相对较高,需要大量的研发投入和人才支持。
其次,市场竞争激烈,企业需要通过不断创新和提高服务质量来保持竞争优势。
此外,环境保护和能源消耗也是需要关注的问题,行业需要寻找更加可持续发展的方式。
总的来说,精密模锻在中国的发展前景非常广阔。
随着技术的进一步成熟和应用的扩大,精密模锻有望在更多领域得到应用,并为相关行业的发展提供支持。
TiAl合金精密成形技术发展现状及展望
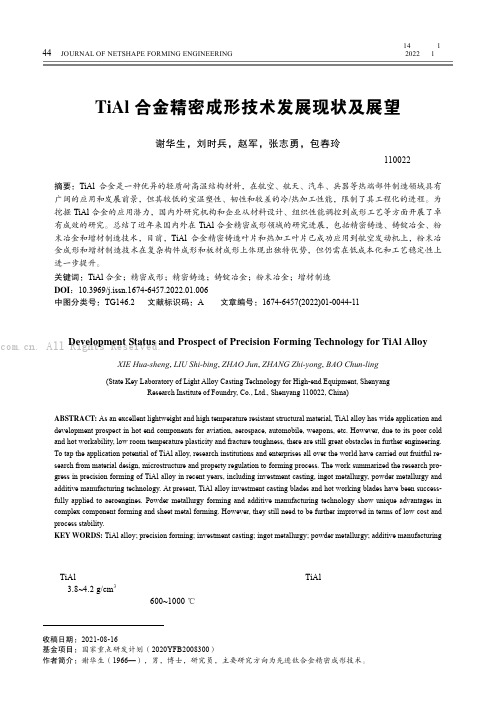
精 密 成 形 工 程第14卷 第1期 44 JOURNAL OF NETSHAPE FORMING ENGINEERING2022年1月收稿日期:2021-08-16基金项目:国家重点研发计划(2020YFB2008300)作者简介:谢华生(1966—),男,博士,研究员,主要研究方向为先进钛合金精密成形技术。
TiAl 合金精密成形技术发展现状及展望谢华生,刘时兵,赵军,张志勇,包春玲(沈阳铸造研究所有限公司 高端装备轻合金铸造技术国家重点实验室,沈阳 110022) 摘要:TiAl 合金是一种优异的轻质耐高温结构材料,在航空、航天、汽车、兵器等热端部件制造领域具有广阔的应用和发展前景,但其较低的室温塑性、韧性和较差的冷/热加工性能,限制了其工程化的进程。
为挖掘TiAl 合金的应用潜力,国内外研究机构和企业从材料设计、组织性能调控到成形工艺等方面开展了卓有成效的研究。
总结了近年来国内外在TiAl 合金精密成形领域的研究进展,包括精密铸造、铸锭冶金、粉末冶金和增材制造技术,目前,TiAl 合金精密铸造叶片和热加工叶片已成功应用到航空发动机上,粉末冶金成形和增材制造技术在复杂构件成形和板材成形上体现出独特优势,但仍需在低成本化和工艺稳定性上进一步提升。
关键词:TiAl 合金;精密成形;精密铸造;铸锭冶金;粉末冶金;增材制造 DOI :10.3969/j.issn.1674-6457.2022.01.006中图分类号:TG146.2 文献标识码:A 文章编号:1674-6457(2022)01-0044-11Development Status and Prospect of Precision Forming Technology for TiAl Alloy XIE Hua-sheng , LIU Shi-bing , ZHAO Jun , ZHANG Zhi-yong , BAO Chun-ling(State Key Laboratory of Light Alloy Casting Technology for High-end Equipment, ShenyangResearch Institute of Foundry, Co., Ltd., Shenyang 110022, China)ABSTRACT: As an excellent lightweight and high temperature resistant structural material, TiAl alloy has wide application and development prospect in hot end components for aviation, aerospace, automobile, weapons, etc. However, due to its poor cold and hot workability, low room temperature plasticity and fracture toughness, there are still great obstacles in further engineering. To tap the application potential of TiAl alloy, research institutions and enterprises all over the world have carried out fruitful re-search from material design, microstructure and property regulation to forming process. The work summarized the research pro-gress in precision forming of TiAl alloy in recent years, including investment casting, ingot metallurgy, powder metallurgy and additive manufacturing technology. At present, TiAl alloy investment casting blades and hot working blades have been success-fully applied to aeroengines. Powder metallurgy forming and additive manufacturing technology show unique advantages in complex component forming and sheet metal forming. However, they still need to be further improved in terms of low cost and process stability.KEY WORDS: TiAl alloy; precision forming; investment casting; ingot metallurgy; powder metallurgy; additive manufacturingTiAl 合金是一种新型的耐高温结构材料,具有低密度(3.8~4.2 g/cm 3)、高比强、高比刚、优异的高温抗蠕变和抗氧化等性能,在600~1000 ℃温度下应用极具竞争力。