第2章 冲裁及冲裁模设计
合集下载
第2章 冲裁及冲裁模设计2[21页]
![第2章 冲裁及冲裁模设计2[21页]](https://img.taocdn.com/s3/m/99fa2c6e52ea551811a68741.png)
П形等制件
b
h
h
T形等制件
b
用于材质和厚度相
h
h
同,而形状不同或
相似的制件
b
用于小件、大批量
h
h
生产的圆形、方形、
矩形、六角形等制
件
§2-6 排样
二、 材料的利用率η
1.η0:在一个进料距离内,件面积与板料毛坯面积之比的百分率。
0
A0 A
•100%
A0 B0 L
100%
A0:件面积mm2 ;A:一个料距内毛坯面积mm2; L:进料距; 2.条、带、和板料的利用率η:
特点:η下降、件质量好、模具寿命 T 较高。
应用: 形状复杂件;精度要求高的排样。
2.少搭边排样:
(某一面无搭边) b图
η高于搭边,降低件质量.简化模具结构.降低T,降低F冲。
应用: 件某些尺寸要求不高的排样。
3.无搭边排样:
c图
η最高.降低件质量.简化模具结构.降低T,降低F冲。
应用: 对件形状要求严格,应用受限。
2. 阶梯冲裁
图2-10
•
多个凸模,高度成阶梯布置,设计注意平衡,金属流动方向。
•
阶梯高度 H:
•
1) t<3 H = t
图 2-10 b
2) t>3 H = t/2 取各层中F冲max 作为F冲 3. 加热冲裁(又称红冲)
•
温度↑,则τ↓,所以F冲下降。
•
加热后, τ值见 表 2-6
表2-6
• note: 冲压温度比加热温度低150 ~ 200℃左右.
t t
( a)斜刃冲裁
(b)阶梯冲裁
图2-10 斜刃与阶梯冲裁
落料 : 斜刃在凹模, 凸为平刃。
b
h
h
T形等制件
b
用于材质和厚度相
h
h
同,而形状不同或
相似的制件
b
用于小件、大批量
h
h
生产的圆形、方形、
矩形、六角形等制
件
§2-6 排样
二、 材料的利用率η
1.η0:在一个进料距离内,件面积与板料毛坯面积之比的百分率。
0
A0 A
•100%
A0 B0 L
100%
A0:件面积mm2 ;A:一个料距内毛坯面积mm2; L:进料距; 2.条、带、和板料的利用率η:
特点:η下降、件质量好、模具寿命 T 较高。
应用: 形状复杂件;精度要求高的排样。
2.少搭边排样:
(某一面无搭边) b图
η高于搭边,降低件质量.简化模具结构.降低T,降低F冲。
应用: 件某些尺寸要求不高的排样。
3.无搭边排样:
c图
η最高.降低件质量.简化模具结构.降低T,降低F冲。
应用: 对件形状要求严格,应用受限。
2. 阶梯冲裁
图2-10
•
多个凸模,高度成阶梯布置,设计注意平衡,金属流动方向。
•
阶梯高度 H:
•
1) t<3 H = t
图 2-10 b
2) t>3 H = t/2 取各层中F冲max 作为F冲 3. 加热冲裁(又称红冲)
•
温度↑,则τ↓,所以F冲下降。
•
加热后, τ值见 表 2-6
表2-6
• note: 冲压温度比加热温度低150 ~ 200℃左右.
t t
( a)斜刃冲裁
(b)阶梯冲裁
图2-10 斜刃与阶梯冲裁
落料 : 斜刃在凹模, 凸为平刃。
第2章6-7节(冲裁工艺及冲裁模设计)
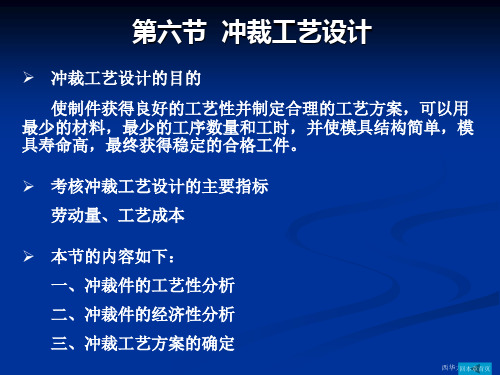
用途 薄件、平整要求高的零件、 薄件、平整要求高的零件、易分层的非金属件
西华大学 张晓洪
2、冲孔模 、
普通板坯冲孔模结构与落料模相似。 普通板坯冲孔模结构与落料模相似。 冲孔的多样性导致冲孔模有更多自己的特点。 冲孔的多样性导致冲孔模有更多自己的特点。
典型的冲孔模有: 典型的冲孔模有: (1)冲侧孔模 ) (2)单工序多凸模冲孔模 ) (3)导板式冲小孔模 )
西华大学 张晓洪
倒装复合模
冲制垫圈的复合冲裁模 适用条件 0.3mm以上低平直度要求件(刚性推件未压紧制件部分,卸 以上低平直度要求件(刚性推件未压紧制件部分, 以上低平直度要求件 料板也未压紧条料) 料板也未压紧条料) 特点 卸料板兼承料平面, 卸料板兼承料平面,冲前无法预压 凸凹模若直刃段长,则胀裂力大,须控制其最小壁厚 凸凹模若直刃段长,则胀裂力大, 条料废料部分: 条料废料部分:冲裁时有上下动作 改进 若上部改为弹性推件,则可加工 若上部改为弹性推件,则可加工0.3mm以下的冲件 以下的冲件
西华大学 张晓洪
… … …冲裁件的形状和尺寸 冲裁件的形状和尺寸
6、孔径不能太小; 、孔径不能太小; 自由凸模的最小尺寸 带护套凸模的最小尺寸 最小孔间距
西华大学 张晓洪
(二)冲裁件的尺寸精度和表面粗糙度要求
冲裁件的经济精度:一般不高于 冲裁件的经济精度:一般不高于IT11,冲孔比落料高一级 , 1、冲裁件外形与内孔尺寸公差表 、 2、冲裁件两孔孔心距公差表 、 3、冲裁件断面表面粗糙度表 、 4、冲裁件断面允许的毛刺高度表 、
第六节
冲裁工艺设计的目的
冲裁工艺设计
使制件获得良好的工艺性并制定合理的工艺方案, 使制件获得良好的工艺性并制定合理的工艺方案,可以用 最少的材料,最少的工序数量和工时,并使模具结构简单, 最少的材料,最少的工序数量和工时,并使模具结构简单,模 具寿命高,最终获得稳定的合格工件。 具寿命高,最终获得稳定的合格工件。 考核冲裁工艺设计的主要指标 劳动量、 劳动量、工艺成本 本节的内容如下: 本节的内容如下: 一、冲裁件的工艺性分析 二、冲裁件的经济性分析 三、冲裁工艺方案的确定
冲压模具设计——第二章

展。这就是塑性变形中的最小阻力定律。
弱区先变形,变形区为弱区
9
第三节 冲压变形理论基础
五、冲压材料及其冲压成形性能
1.冲压成形性能 材料的冲压成形性能:材料对各种冲压加工方法的适应能力。
冲压加工的依据。 成形极限高 材料的冲压性能好 成形质量好 便于冲压加工
成形极限高 冲压成形性能是一个综合性的概念
29
3、间隙对模具寿命的影响
模具寿命分为刃磨寿命和模具总寿命。 失效原因:磨损、变形、崩刃、折断和胀裂。
小间隙将使磨损增加,甚至使模具与材料之间产生粘 结现象,并引起崩刃、凹模胀裂、小凸模折断、凸凹 模相互啃刃等异常损坏。
为了延长模具寿命,在保证冲裁件质量的前提下
1)采用适当或较大的间隙值;
2)减缓间隙不均匀的影响; 3)采用小间隙时必须提高模具硬度与光洁度、精度; 4)改善润滑条件,减少磨损。
3
冲压变形理论基础
一、塑性变形的基本概念
变形:
弹性变形、塑性变形。
塑性:
表示材料塑性变形能力。它是指固体材料在外力作用下发 生永久变形而不破坏其完整性能力。
塑性指标:
衡量金属塑性高低的参数。常用塑性指标为延伸率δ和断
面收缩率ψ。
Lk L0 100 % L0
F0 Fk 100 % F0
成形质量好
10
第三节 冲压变形理论基础
五、冲压材料及其冲压成形性能(续)
2.冲压成形性能的试验方法 间接试验和直接试验
3.板料的机械性能与冲压成形性能的关系
板料的强度指标越高,产生相同变形量的力就越大; 塑性指标越高,成形时所能承受的极限变形量就越大; 刚度指标越高, 成形时抵抗失稳起皱的能力就越大。
c= (DA-dT)/2
弱区先变形,变形区为弱区
9
第三节 冲压变形理论基础
五、冲压材料及其冲压成形性能
1.冲压成形性能 材料的冲压成形性能:材料对各种冲压加工方法的适应能力。
冲压加工的依据。 成形极限高 材料的冲压性能好 成形质量好 便于冲压加工
成形极限高 冲压成形性能是一个综合性的概念
29
3、间隙对模具寿命的影响
模具寿命分为刃磨寿命和模具总寿命。 失效原因:磨损、变形、崩刃、折断和胀裂。
小间隙将使磨损增加,甚至使模具与材料之间产生粘 结现象,并引起崩刃、凹模胀裂、小凸模折断、凸凹 模相互啃刃等异常损坏。
为了延长模具寿命,在保证冲裁件质量的前提下
1)采用适当或较大的间隙值;
2)减缓间隙不均匀的影响; 3)采用小间隙时必须提高模具硬度与光洁度、精度; 4)改善润滑条件,减少磨损。
3
冲压变形理论基础
一、塑性变形的基本概念
变形:
弹性变形、塑性变形。
塑性:
表示材料塑性变形能力。它是指固体材料在外力作用下发 生永久变形而不破坏其完整性能力。
塑性指标:
衡量金属塑性高低的参数。常用塑性指标为延伸率δ和断
面收缩率ψ。
Lk L0 100 % L0
F0 Fk 100 % F0
成形质量好
10
第三节 冲压变形理论基础
五、冲压材料及其冲压成形性能(续)
2.冲压成形性能的试验方法 间接试验和直接试验
3.板料的机械性能与冲压成形性能的关系
板料的强度指标越高,产生相同变形量的力就越大; 塑性指标越高,成形时所能承受的极限变形量就越大; 刚度指标越高, 成形时抵抗失稳起皱的能力就越大。
c= (DA-dT)/2
第二章 冲裁及冲裁模具 (1)[29页]
![第二章 冲裁及冲裁模具 (1)[29页]](https://img.taocdn.com/s3/m/f09037d8caaedd3383c4d3d4.png)
b
b
b
表2-7 常用的排样形式。
有搭边排样
少、无搭边排样
b
h
应用
圆形、方形、矩形 等制件
椭圆形、T形 、Γ 形及 S形
梯形、三角形、半 圆形、T形、Ш形、
П形等制件
b
h
h
T形等制件
b
用于材质和厚度相
h
h
同,而形状不同或
相似的制件
b
用于小件、大批量
h
h
生产的圆形、方形、
矩形、六角形等制
件
表2-1 凸模冲孔的最小尺寸 mm
因为弹性恢复而影响, 且对落料、冲孔不同。 Z小至一定限度,压缩弹复,落料件尺寸大于凹模尺寸,冲孔件<凸模直径 Z大至一定限度,拉伸弹复,落料件尺寸小于凹模尺寸,冲孔件>凸模直径 3、影响F冲,模具寿命T: 对F冲: Z增加,F冲小; 侧面μ小 且F卸 ,F推小。
3~4mm,在弯曲或拉深件上冲孔时应保证l≥R十0.5t,l1≥R1+0.5t (如
图2-4所示)。
5) 制件外形应避免有长悬臂或过窄的凹槽悬臂和凹槽的宽度要大于料厚的
1.5~2 倍。宽度b≥(1.5~2)t (见图2-3所示)。
名称
单 行 直 排
单 行 斜 排
直 对 排
斜 对 排
混 合 排
多 行 排
4.毛刺d:因为 Z,刃口处裂纹偏离刃口,凸模外侧,凹内。
材料分离时是被拉断而形成,高于板厚。Z合理,b很小。
§2-1 冲裁变形过程及断面特征 三、冲裁断面特征
(a) (b)
图2-2 冲裁断面 a-圆角带 b-光亮带 c-断裂面 d-毛刺
§2-2 冲裁件的工艺性
一、冲裁件的工艺性
第二章 冲裁工艺与模具设计
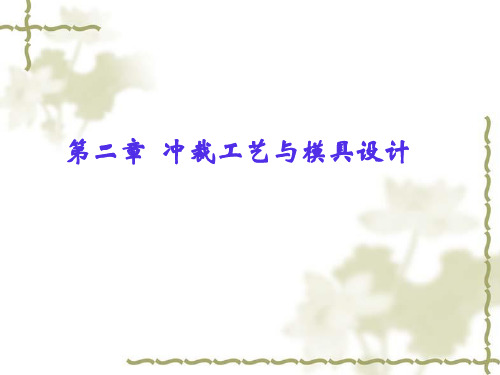
(1)材料的塑性要好,对硬质材料要尽量进行 退火,求得材质均一化;
(2)合理的模具间隙值,并使间隙均匀分布;
(3)保持模具刃口锋利 ,
(4)保持润滑。
2.2.1冲裁力的计算
计算冲裁力的目的是为了合理地选择压力机和设 计模具,压力机的吨位必须大于所计算的冲裁力, 以适应冲裁的要求。 (一)冲裁力的行程
采用刚性卸F料总 装 F置冲 和 F下卸 出 F料推方式的总冲压力为
采用弹性卸料F总装置F冲和上F出推 料方式的总冲压力为
F总 F冲 F卸 F顶
例2-1 计算冲裁图2-12所示零件所需的冲压力。材 料为Q235钢,料厚t=2mm,采用弹性卸料装置 和下出料方式,凹模刃口直壁高度h=6mm 解:冲裁力:由表查出 304 ~ 373MPa, 取 345MPa
这种模具的缺点是长凸模进入凹模较深,容易 磨损,修磨刃口也比较麻烦。
(二)斜刃口冲裁
在用平刃口模具冲裁时,整个刃口同时与冲裁 件周边接触,同时切断,所需冲裁力大。若采用斜 刃模具冲裁,也就是将凸模(或凹模)刃口做成有 一定倾斜角度的斜刃,如图2-11所示,冲裁时刃口 就不是同时切入,
而是逐步切入材料,
c 、将工件分解成若干直线段或弧度段,L1、
L2、…Ln,因冲裁力与轮廓线长度成正比关系,故 用轮廓线长度代替F。 d 、计算各基本线段的重心到Y轴的距离x1、 x2、…xn,到X轴的距离y1、y2、… yn,则根据力 矩原理可得压力中心的计算公式为
X0
l1x1 l2 x2 ln xn l1 l2 ln
(二)塑性变形阶段
凸模继续下降,压力增加,当材料内部应力达到 屈服点时,板料进入塑性变形阶段。
此时凸模开始挤入板料,并将下部材料挤入凹模 孔内,板料在凸、凹模刃口附近产生塑性剪切变 形,并在侧向挤压力作用下形成光亮的剪切断面。
(2)合理的模具间隙值,并使间隙均匀分布;
(3)保持模具刃口锋利 ,
(4)保持润滑。
2.2.1冲裁力的计算
计算冲裁力的目的是为了合理地选择压力机和设 计模具,压力机的吨位必须大于所计算的冲裁力, 以适应冲裁的要求。 (一)冲裁力的行程
采用刚性卸F料总 装 F置冲 和 F下卸 出 F料推方式的总冲压力为
采用弹性卸料F总装置F冲和上F出推 料方式的总冲压力为
F总 F冲 F卸 F顶
例2-1 计算冲裁图2-12所示零件所需的冲压力。材 料为Q235钢,料厚t=2mm,采用弹性卸料装置 和下出料方式,凹模刃口直壁高度h=6mm 解:冲裁力:由表查出 304 ~ 373MPa, 取 345MPa
这种模具的缺点是长凸模进入凹模较深,容易 磨损,修磨刃口也比较麻烦。
(二)斜刃口冲裁
在用平刃口模具冲裁时,整个刃口同时与冲裁 件周边接触,同时切断,所需冲裁力大。若采用斜 刃模具冲裁,也就是将凸模(或凹模)刃口做成有 一定倾斜角度的斜刃,如图2-11所示,冲裁时刃口 就不是同时切入,
而是逐步切入材料,
c 、将工件分解成若干直线段或弧度段,L1、
L2、…Ln,因冲裁力与轮廓线长度成正比关系,故 用轮廓线长度代替F。 d 、计算各基本线段的重心到Y轴的距离x1、 x2、…xn,到X轴的距离y1、y2、… yn,则根据力 矩原理可得压力中心的计算公式为
X0
l1x1 l2 x2 ln xn l1 l2 ln
(二)塑性变形阶段
凸模继续下降,压力增加,当材料内部应力达到 屈服点时,板料进入塑性变形阶段。
此时凸模开始挤入板料,并将下部材料挤入凹模 孔内,板料在凸、凹模刃口附近产生塑性剪切变 形,并在侧向挤压力作用下形成光亮的剪切断面。
冲裁及冲裁模设计
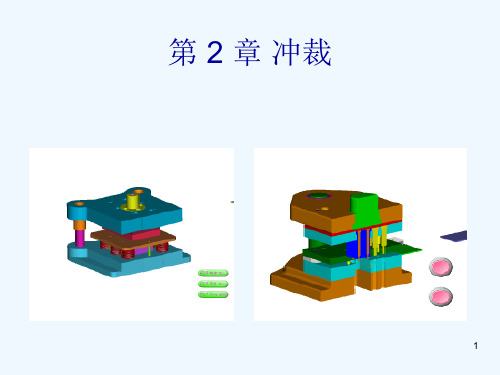
16
第 2 章 冲裁
2 -2 冲裁模具间隙
2.2.1 间隙对冲裁件质量的影响
冲裁件的质量:断面质量、尺寸精度 a 间隙对断面质量的影响 小间隙、合理间隙、大间隙情况下的剪切过程 断面特征值与间隙的关系图。
17
第 2 章 冲裁
2-2 冲裁模间隙
间隙对断面质量的影响
18
第 2 章 力、变形和冲裁件正常的断面状况 a)冲孔件 b)落料件
第 2 章 冲裁
2 -2 冲裁模具间隙
间隙的概念 模具凸凹模刃口缝隙间的距离。 单边间隙c、双边间隙z。 间隙对冲裁件的质量、模具寿命、冲裁力都有很大 的影响,是冲裁工艺和模具设计中的最重要的工艺参数。 2.2.1 间隙对冲裁件质量的影响 2.2.2 间隙对冲裁力的影响 2.2.3 间隙对模具寿命的影响 2.2.4 间隙的确定
12
第 2 章 冲裁
2-1 冲裁变形机理
2.1.5 断面特征
1)圆角带:冲裁过程中,纤维的弯曲与拉伸形成, 软材料圆角大。 2)光亮带:塑剪变形时,由于相对移动,凸凹模侧 压力将毛料压平形成的光亮垂直断面。
3)断裂带:刃口微裂纹受拉应力不断扩展形成的撕 裂面,导致断面粗糙并有斜度。 4)毛刺:由微裂纹位置与冲裁间隙等引起,是金属 拉断而形成的金属刺残留在冲裁件上
板 坯
F v 1
F v 2
F h 2
F h 2
F v 2
凹 模
板坯受力简图 Diagram of sheet metal under load
10
第 2 章 冲裁
2-1 冲裁变形机理
2.1.3 裂纹的形成与发展 裂纹产生的条件:当变形区的应变达到极限塑性应变值时, 就产生微裂纹 裂纹扩展的方向:沿着最大剪切应变速度的方向扩展 裂纹的成长过程:裂纹首先在低应力区产生,由于变形过 程中最大剪切应变的速度方向发生变化,使得新的裂纹不断产 生,旧裂纹的扩展不断停止,然后在旧裂纹的前端附近重新产 生新的裂纹,不断产生的微裂纹的根部汇成了一条主裂纹 极限塑性应变值除和材质外,还和应力状态、变形历史(损 伤程度)有关。
第 2 章 冲裁
2 -2 冲裁模具间隙
2.2.1 间隙对冲裁件质量的影响
冲裁件的质量:断面质量、尺寸精度 a 间隙对断面质量的影响 小间隙、合理间隙、大间隙情况下的剪切过程 断面特征值与间隙的关系图。
17
第 2 章 冲裁
2-2 冲裁模间隙
间隙对断面质量的影响
18
第 2 章 力、变形和冲裁件正常的断面状况 a)冲孔件 b)落料件
第 2 章 冲裁
2 -2 冲裁模具间隙
间隙的概念 模具凸凹模刃口缝隙间的距离。 单边间隙c、双边间隙z。 间隙对冲裁件的质量、模具寿命、冲裁力都有很大 的影响,是冲裁工艺和模具设计中的最重要的工艺参数。 2.2.1 间隙对冲裁件质量的影响 2.2.2 间隙对冲裁力的影响 2.2.3 间隙对模具寿命的影响 2.2.4 间隙的确定
12
第 2 章 冲裁
2-1 冲裁变形机理
2.1.5 断面特征
1)圆角带:冲裁过程中,纤维的弯曲与拉伸形成, 软材料圆角大。 2)光亮带:塑剪变形时,由于相对移动,凸凹模侧 压力将毛料压平形成的光亮垂直断面。
3)断裂带:刃口微裂纹受拉应力不断扩展形成的撕 裂面,导致断面粗糙并有斜度。 4)毛刺:由微裂纹位置与冲裁间隙等引起,是金属 拉断而形成的金属刺残留在冲裁件上
板 坯
F v 1
F v 2
F h 2
F h 2
F v 2
凹 模
板坯受力简图 Diagram of sheet metal under load
10
第 2 章 冲裁
2-1 冲裁变形机理
2.1.3 裂纹的形成与发展 裂纹产生的条件:当变形区的应变达到极限塑性应变值时, 就产生微裂纹 裂纹扩展的方向:沿着最大剪切应变速度的方向扩展 裂纹的成长过程:裂纹首先在低应力区产生,由于变形过 程中最大剪切应变的速度方向发生变化,使得新的裂纹不断产 生,旧裂纹的扩展不断停止,然后在旧裂纹的前端附近重新产 生新的裂纹,不断产生的微裂纹的根部汇成了一条主裂纹 极限塑性应变值除和材质外,还和应力状态、变形历史(损 伤程度)有关。
模具第二章冲裁模

为了防止冲裁时凸模折断或压弯,冲孔的尺寸不能太小, 有关要求见下表 (一)
一般冲孔模可冲压的最小孔径值
(mm)
材料
钢г>700MPa 钢г=400~700MPa 钢г<400MPa 黄铜、铜 铝、锌 纸胶板、布胶板 硬纸、纸
d≥1.5t d≥1.3t
d≥t d≥0.9t d≥0.8t d≥0.7t d≥0.6t
凹
0
d x Z min
凹 0
式中:d凸、d凹——冲孔凸、凹模基本尺寸(mm); △——工件制造公差(mm); X——因数,见表2-13
冲孔时各部分尺寸公差的分配 位置如右图a)
(2)落料 设工件尺寸为D-△。
根据刃口尺寸计算原则,落料 时应首先确定凹模刃口尺寸。 由于基准件凹模的刃口尺寸在 磨损后会增大,因此应使凹模 的基本尺寸接近工件轮廓的最 小极限尺寸,再减小凸模尺寸 以保证最小合理间隙值Zmin。仍 然是凸模取负偏差,凹模取正偏 差。落料时各部分尺寸公差的 分配位置如右图b)
表2-3 冲裁件内外形所能达到的经济精度
基本尺寸/mm
材料厚度t/mm
≤3 1~2 2~3 3~5
≤3
3~6
6~10 10~18 18~500
IT12~IT13
IT14
IT12~IT13
IT14
--
IT14
IT11 IT11
IT12~IT13 IT12~IT13
表2-4 两孔中心距离公差
一般精度(模具)
1、尺寸计算原则(在决定模具刃口尺寸及制造公差时): 1)落料件的尺寸取决于凹件尺寸,冲孔件的尺寸取决于凸模
尺寸。因此,设计落料模时,以凹模为基准,间隙取在凸模上。 设计冲孔模时,以凸模为基准,间隙取在凹模上。
第二章 冲裁工艺与冲裁模设计

线表示冲压位置。
第二章 冲裁工艺与冲裁模设计
零件形状不同材料利用情况的对比
第二章 冲裁工艺与冲裁模设计
第二章 冲裁工艺与冲裁模设计
第六节 冲裁力和压力中心的计算
一、冲裁力的计算
冲裁力:冲裁过程中凸模对板料施加的压力。
用普通平刃口模具冲裁时,冲裁力F一般按下式计算:
F KLt b
注: F——冲裁力; L——冲裁周边长度; t——材料厚度; b——材料抗剪强度; K——系数。一般取K=1.3
三、压力机公称压力的确定
压力机的公称压力必须大于或等于各种冲压工艺力的总和Fz
采用弹性卸料装置和下出料方式的冲裁模时: FZ F FX FT
采用弹性卸料装置和上出料方式的冲裁模时:
FZ F FX FD
采用刚性卸料装置和下出料方式的冲裁模时: FZ F FT
第二章 冲裁工艺与冲裁模设计
第二章 冲裁工艺与冲裁模设计
一、材料的合理利用(续)
2.提高材料利用率的方法(续)
减少工艺废料的有力措施是:
设计合理的排样方案; 选择合适的板料规格和合理的裁板法 (减少料头、料尾和边余料); 利用废料作小零件(如表2.5.1中的混合排样)等。
利用结构废料的措施有:
当材料和厚度相同时,在尺寸允许的情况下,较小尺寸的冲 件可在较大尺寸冲件的废料中冲制出来。
第二章 冲裁工艺与冲裁模设计
内容简介: 冲裁是最基本的冲压工序。
在分析冲裁变形过程及冲裁件质量影响因素的基础上, 介绍冲裁工艺计算、工艺方案制定和冲裁模设计。涉及冲 裁变形过程分析、冲裁件质量及影响因素、间隙确定、刃 口尺寸计算原则和方法、排样设计、冲裁力与压力中心计 算、冲裁工艺性分析与工艺方案制定、冲裁典型结构、零 部件设计及模具标准应用、冲裁模设计方法与步骤等。
第2章 冲裁及冲裁模设计4[10页]
![第2章 冲裁及冲裁模设计4[10页]](https://img.taocdn.com/s3/m/5463590708a1284ac9504371.png)
静止件: 挡料销 9、 凹1、下模座8、卸料板2。
其他: 定位销、螺钉等。
• 工作过程: 条料沿导尺7送进,靠固定挡料销9定位;
•
ห้องสมุดไป่ตู้
运动件下移,凸模与凹模配合落料,
并推出凹模孔口内上次的落料件;
•
回程,运动件上移,卸料板2刮下卡在凸模上的条料。
图2-49 图2-50 图2-51
图2-49 无导向落料模 1-凹模;2-卸料板;3-凸模; 4-模柄;5-凸模固定板;
倒装复合模
图2-55 倒装垫圈复合冲裁模 1-凸模;2-凹模;3-上模固定板;4、16-垫板;5-上模座;6-模柄;7-推杆;8推块; 9-推销; 10-推件块;11、18-活动挡料销;12-固定挡料销;13-卸料板; 14-凸凹模;15-下模固定板;17-下模座;19-弹簧
图2-56 同时冲三个垫圈的复合模 1、2、8-凸凹模; 3-落料凹模; 4、6-顶件板; 5-连接销 ;7-冲孔凸模
图2-51 带弹顶器导柱导向的落料模
二 多工序模:
一次工作行程完成二道以上工序的模具。称~
• 特点: 生产率高;精度高;操作方便;安全;易自动化;减少模具数。
应用: 大批量;高精度件;复杂件。
1、复合模:
在冲床的一个工作行程中,在同一工位上完成两种或两种以上 复合模
冲压工序的模具。
特点:
生产效率高、冲裁件质量好、但模具制造困难。
适用于加工精度高、简单件。
连续模
2、连续模:
• 在冲床的一个工作行程中,完成数道工序,分布在坯料送进方向不同部位。
• 适用于加工精度要求不高、复杂件。
图2-52
图2-53
图2-54
图2-55
第二章冲裁工艺与冲裁模设计

2020/7/7
7.冲压设备选择 冲压设备选择关系到其合理使用、安全、产
品质量、模具寿命、生产效率及成本等。 设备类型的选择主要取决于冲压的工艺要求
和生产批量。设备选择主要包括设备类型和规格 两个方面。
设备规格主要取决于冲压力,变形功、模具 闭合高度和模板平面轮廓尺寸等。
2020/7/7
8.凸、凹模结构设计 根据冲件的形状和尺寸,冲模的加工以及装
(2)级进工艺
(3)复合工艺 即采用一副复合模一次冲裁完成。
2020/7/7
分析比较: (1)单工序工艺:模具结构简单,制造成本较 低,但制件内外形的位置精度难以得到保证,且 所占用设备及工人较多,生产效率低。
(2)级进工序工艺:制件内外形位置精度较易 得到保证,易于实现自动化生产,生产效率高, 但模具结构较复杂,制造成本较高。
冲压件上未注公差尺寸,要根据工件的公 差等级,进行公差标注。
标准步骤: 1.根据冲压件的公差等级与基本尺寸,查找冲压
基准件公差数值表,找到对应的公差,一般采 取单性偏差;
2020/7/7
2.判断该尺寸的偏差方向; 采用“入体原则”、可先画出该冲压件的假
想磨损图。所示工件的假想磨损图用双点划线画 出,再根据以下方法进行判断。如该尺寸磨损后 变小为负偏差;变大为正偏差;不变则为正负偏 差。
案例分析:电机定子 工序性质: 冲孔、落料
2020/7/7
案例分析:机芯自停杆 工序性质: 冲孔、落料
2020/7/7
案例分析:电位器接线片 工序性质: 落料
2020/7/7
(2)基本工序的数目 案例分析:
案例1为3个; 案例2和案例3为2个; 案例4为1个。
(3)基本工序的顺序 案例分析:
7.冲压设备选择 冲压设备选择关系到其合理使用、安全、产
品质量、模具寿命、生产效率及成本等。 设备类型的选择主要取决于冲压的工艺要求
和生产批量。设备选择主要包括设备类型和规格 两个方面。
设备规格主要取决于冲压力,变形功、模具 闭合高度和模板平面轮廓尺寸等。
2020/7/7
8.凸、凹模结构设计 根据冲件的形状和尺寸,冲模的加工以及装
(2)级进工艺
(3)复合工艺 即采用一副复合模一次冲裁完成。
2020/7/7
分析比较: (1)单工序工艺:模具结构简单,制造成本较 低,但制件内外形的位置精度难以得到保证,且 所占用设备及工人较多,生产效率低。
(2)级进工序工艺:制件内外形位置精度较易 得到保证,易于实现自动化生产,生产效率高, 但模具结构较复杂,制造成本较高。
冲压件上未注公差尺寸,要根据工件的公 差等级,进行公差标注。
标准步骤: 1.根据冲压件的公差等级与基本尺寸,查找冲压
基准件公差数值表,找到对应的公差,一般采 取单性偏差;
2020/7/7
2.判断该尺寸的偏差方向; 采用“入体原则”、可先画出该冲压件的假
想磨损图。所示工件的假想磨损图用双点划线画 出,再根据以下方法进行判断。如该尺寸磨损后 变小为负偏差;变大为正偏差;不变则为正负偏 差。
案例分析:电机定子 工序性质: 冲孔、落料
2020/7/7
案例分析:机芯自停杆 工序性质: 冲孔、落料
2020/7/7
案例分析:电位器接线片 工序性质: 落料
2020/7/7
(2)基本工序的数目 案例分析:
案例1为3个; 案例2和案例3为2个; 案例4为1个。
(3)基本工序的顺序 案例分析:
第二章 冲裁工艺及冲裁模设计

普通冲裁件的断面情况:
普通冲裁变形所得到的冲裁件端面常带有一定的锥度,并且 都有明显的区域特征,不同的是各区域的大小占整个断面的比例 不一样。 光亮带 产生于塑性变 圆角带
发生在弹性变形后 期和塑性变形初期, 由金属的弯曲和拉伸 而形成。其大小与材 质有关。
形阶段,断面主 要受剪应力和压 应力作用。断面 平整、光滑。通 常占整个区域的 1/2~1/3,与材质 有关。
第二章 冲裁工艺及冲裁模设计
普通冲裁原理
冲裁间隙 冲裁模刃口尺寸的计算(重点) 冲裁件的排样(重点) 冲压工艺力(重点) 压力中心的计算(重点) 冲裁件的工艺性 冲裁模的基本形式及特点 冲裁模主要零、部件结构和设计(重点) 冷冲模的设计程序(重点)
2.1 普通冲裁的基本原理
冲模刃口尺寸、制造公差的大小主要取决于 冲裁件的形状和精度。
刃口尺寸的计算方法
冲模刃口 尺寸公差带 分析图
1. 凸、凹模分开加工时的刃口计算
δd+δp≤Zmax-Zmin 运用该方法必须使模具的制造公差与间隙满足 或 δp= 0.4(Zmax-Zmin) δd= 0.6(Zmax-Zmin)
根据刃口尺寸的计算原则,分开加工时凸、凹模刃口尺寸 的计算公式如下:
推件力Pd: Pd = KdP
冲压工艺力的计算:
(它是选取压力机吨位的主要依据,具体计算要考虑模具的结构型式) 采用刚性卸料自然漏料方式:Pz≥P+Pt = P +nKtP 采用刚性打料、弹性卸料的倒装结构方式:Pz≥P + Px = P + KxP 采用弹性卸料和弹性顶料方式:Pz≥P + Px + Pd = P + KxP + KdP 采用弹性卸料自然漏料方式:Pz≥P + Px + Pd = P + KxP + nKdP (选择压力机时,压力机的公称压力N必须大于或等于Px)
第二章 冲裁工艺及冲裁模
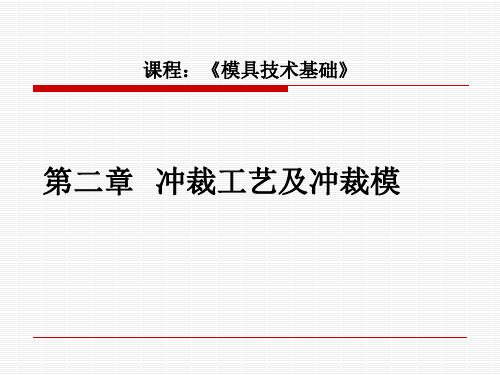
圆形凸模
第二章 冲裁工艺及冲裁模
非圆形凸模及其固定 冲小孔凸模及其导向结构
第二章 冲裁工艺及冲裁模
(4)凸模的长度 当采用固定卸料时(如图a):L=h1+h2+h3+h 当采用弹性卸料时(如图a):L=h1+h2+h4
2、凹模 定义:在冲压过程中,与凸模配合直接对冲制件进行分离或成形 的工作零件。
便于操作和实现生产自动化。 缺点:级进模轮廓尺寸较大,制造较复杂,成本较高。 适用:大批量生产小型冲压件。
第二章 冲裁工艺及冲裁模
第二章 冲裁工艺及冲裁模
第二章 冲裁工艺及冲裁模
第二章 冲裁工艺及冲裁模
第八节 冲裁模的部件和零件
第二章 冲裁工艺及冲裁模
一、工作零件 1、凸模 按整体结构分:整体式、护套式和镶拼式; 按截面形状分:圆形和非圆形; 按刃口形式分:平刃和斜刃。 凸模基本结构由两部分组成: 一是工作部分,用于成型冲件; 二是安装部分,用来使凸模正确固定在座上。 凸模的材料:形状简单寿命要求不高的凸模选用T8A、T10A等材料; 形状复杂且寿命要求较高凸模选用Cr12、Cr12MoV等制造 对于高寿命、高耐磨性的凸模选用硬质合金。 凸模的固定方法:
第二章 冲裁工艺及冲裁模
第四节 排样与搭边
一、排样 定义:排样指冲裁件在板料、条料或带料上的布置形式。 1、材料利用率 定义:在冲压生产中,材料利用率是指在一个进料距离内,冲裁件面积与板料
毛坯面积之比,用百分率表示。
A 100%
Bs
式中 ——材料利用率;
A——一个进料距离内冲裁件的实际面积,mm2; B——条料或带料宽度,mm; s——进料距离,mm。
第二章 冲裁工艺及冲裁模
模具设计与制造CAI-第二章冲裁模设计
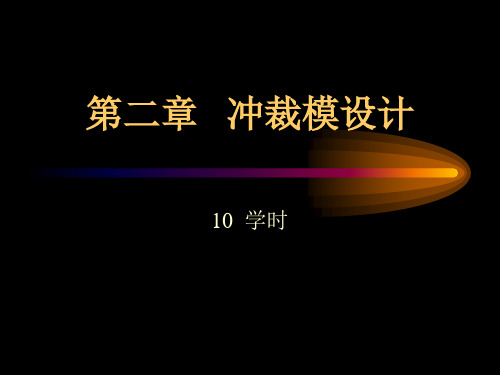
一般有以下四种方法:
• 模具制造精度要比零件精度高2~3级;
若冲裁件没有标注公差,对于非圆形件按国家标准 “非配合尺寸的公差数值”IT14精度处理,冲模则 按IT11精度制造。
• 凸、凹模制造公差(mm)分别按IT6、IT7制造;
• 按经验表格直接取,表2.14和2.15;
•
也可取
1 d4
。 (1 ~ 1) p 45
§2-2 冲裁间隙(p19) (p14)
• 冲裁间隙——指凸模与凹模刃口横向尺 寸的差值,在普通冲裁中均为正值,常 用Z表示.
▪ Z为冲裁工艺及模具设计中一个主要的工 艺参数
▪ 对于圆形凸、凹模:
Z=Dd-dp 叫双边间隙 Z/2叫单边间隙
▪ 合理的间隙对制件尺寸及其断面质量、 模具寿命、卸料力等均有影响,是非常
二、刃口尺寸确定的基本原则
• 落料时,首先确定凹模刃口公称尺寸, 可取凹模刃口的公称尺寸接近或等于工 件的最小极限尺寸,然后通过减少凸模 公称尺寸,以保证合理间隙。
• 冲孔时,首先确定凸模刃口公称尺 寸,可取凸模刃口的公称尺寸接近 或等于工件的最大极限尺寸,然后 通过增大凹模公称尺寸,以保证合 理间隙。
x :磨损系数。
磨损系数x的取值
• x·――磨损量,磨损系数x是为了使零件的实 际尺寸接近零件公差带的中间尺寸,可查表 (表2-17) 。
• 亦可按如下方法选取:
– 零件精度在IT10以上,取x=1 – 零件精度在IT11~IT13,取x=0.75 – 零件精度在IT14以下,取x=0.5
模具制造公差的确定
• 落料件(基准件为凹模,间隙取在凸模上):
– 凹模磨损后尺寸增加 A0
Ad ( A x)0a
– 凹模磨损后尺寸减小 B0
第2章 冲裁工艺与冲裁模

0 Dp ( Dd 2cmin )0 ( D x 2 c ) p max min p
1 1 1 1 Ld ( Lmin ) Td ( Lmin ) 2 2 2 8
0 绪论 一、冲压概念
2.凸模与凹模配合加工
配合加工法是指配做时,先制出一个基准件(如凹模),然后根据基准件 的实际尺寸,再按最小合理间隙Zmin配做另一件(如凸模)。
1.冲裁力的计算
平刃口冲裁模的冲裁力可按下式计算:
FP K PtL
式中,F—冲裁力,单位N; k—系数; L—冲裁件周边长度,单位㎜; t—板料厚度,单位㎜;τ b——材料抗剪强度,单位为MPa; 系数k是考虑到实际生产中各种因素对冲裁力的影响。 根据经验,一般取k=1.3。 抗剪强度τ 的数值,取决于材料的种类和状态,可在有关手册中查取。 一般取τ b=0.8σ b。 估算冲裁力公式: F=Ltσ
Ap A K T
0
p
0 绪论 一、冲压概念
② 凸模磨损后尺寸增大。
B p B K
Tp 0
③ 凸模磨损后尺寸没有变化。 (根据工件尺寸的标注形式不同其计算也各异) 工件尺寸为正偏差标注,如C+0Δ,可按下式计算。 T 即 C p C 0.5 2p 工件尺寸为负偏差标注,如,可按下式计算。 Tp C C 0 . 5 即 p 2 工件尺寸为对称偏差标注,如,可按下式计算。 即 C p C Tp 2 式中, Ap、Bp、Cp——凸模刃口尺寸; A、B、C——工件孔的基本尺寸。
0 绪论
2.2 冲裁件尺寸精度及结构工艺性
2.2.1 冲裁件尺寸精度和表面粗糙度
1、金属冲裁件的内、外形的经济精度不高于ITll级,如表2-1。 一般落料精度最好低于IT10级,冲孔精度最好低于IT9级。冲裁剪切 面的近似表面粗糙度值件见表2-2。 2、非金属冲裁件的内外形的经济精度为IT14、IT15级。 3、冲裁尺寸标注应符合冲压工艺要求。例如下图2-5所示的冲裁件, 其中图a的尺寸标注方法就不合理,因为,两孔中心距会随模具的磨 损而增大。如改为图b的标注方式,则两孔中心距与模具磨损无关。
1 1 1 1 Ld ( Lmin ) Td ( Lmin ) 2 2 2 8
0 绪论 一、冲压概念
2.凸模与凹模配合加工
配合加工法是指配做时,先制出一个基准件(如凹模),然后根据基准件 的实际尺寸,再按最小合理间隙Zmin配做另一件(如凸模)。
1.冲裁力的计算
平刃口冲裁模的冲裁力可按下式计算:
FP K PtL
式中,F—冲裁力,单位N; k—系数; L—冲裁件周边长度,单位㎜; t—板料厚度,单位㎜;τ b——材料抗剪强度,单位为MPa; 系数k是考虑到实际生产中各种因素对冲裁力的影响。 根据经验,一般取k=1.3。 抗剪强度τ 的数值,取决于材料的种类和状态,可在有关手册中查取。 一般取τ b=0.8σ b。 估算冲裁力公式: F=Ltσ
Ap A K T
0
p
0 绪论 一、冲压概念
② 凸模磨损后尺寸增大。
B p B K
Tp 0
③ 凸模磨损后尺寸没有变化。 (根据工件尺寸的标注形式不同其计算也各异) 工件尺寸为正偏差标注,如C+0Δ,可按下式计算。 T 即 C p C 0.5 2p 工件尺寸为负偏差标注,如,可按下式计算。 Tp C C 0 . 5 即 p 2 工件尺寸为对称偏差标注,如,可按下式计算。 即 C p C Tp 2 式中, Ap、Bp、Cp——凸模刃口尺寸; A、B、C——工件孔的基本尺寸。
0 绪论
2.2 冲裁件尺寸精度及结构工艺性
2.2.1 冲裁件尺寸精度和表面粗糙度
1、金属冲裁件的内、外形的经济精度不高于ITll级,如表2-1。 一般落料精度最好低于IT10级,冲孔精度最好低于IT9级。冲裁剪切 面的近似表面粗糙度值件见表2-2。 2、非金属冲裁件的内外形的经济精度为IT14、IT15级。 3、冲裁尺寸标注应符合冲压工艺要求。例如下图2-5所示的冲裁件, 其中图a的尺寸标注方法就不合理,因为,两孔中心距会随模具的磨 损而增大。如改为图b的标注方式,则两孔中心距与模具磨损无关。
第二章冲裁工艺与冲裁模
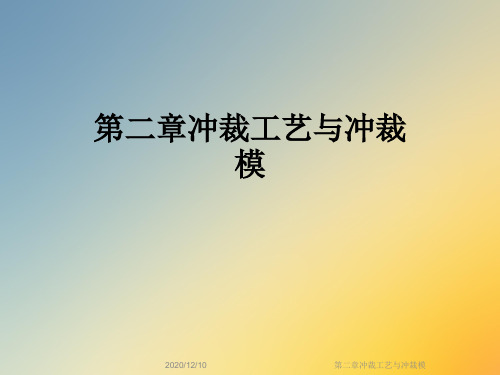
第二章冲裁工艺与冲裁模
凸模:
凹模:
式中: d—冲孔工件孔的基本尺寸,mm dp、dd—冲孔凸、凹模刃口尺寸,mm Δ—工件公差,mm —凸、凹模制造偏差(查表),mm X—磨损系数(查表)
第二章冲裁工艺与冲裁模
第二章冲裁工艺与冲裁模
②落料 设冲裁件的落料尺寸为
计算原则,计算公式为:
凹模:
,根据刃口尺寸
如不满足,则应提高模具制造精度,即减小 、 ⑤优点
凸、凹模具有互换性,制造周期短,便于批量生产。 ⑥缺点:模具制造公差小,模具制造困难,成本高。
第二章冲裁工艺与冲裁模
刃口尺寸计算注意点:
1.分清是冲孔还是落料 2.冲裁间隙Z的确定:与材料和料厚有关 3.冲裁件的尺寸标注是否标准
孔的标注: 落料的标注: 中心距标注:L
基准件刃口尺寸计算式:
A类尺寸:
B类尺寸:
C类尺寸:
C = C ±D ' 4 = C ±D 8
第二章冲裁工艺与冲裁模
A类尺寸:
B类尺寸:
C类尺寸: C = C ±D ' 4 = C ±D 8
式中: A、B、C—基准件基本尺寸, mm Amax—冲裁件A类尺寸最大极限值, mm B min—冲裁件B类尺寸最小极限值, mm δ—模具制造公差, mm
毛剌区:是由于冲裁间隙的存在 而产生,该区域一般不可避免。Байду номын сангаас
第二章冲裁工艺与冲裁模
注意事项
a、粗大毛刺的产生部位:
当凸模刃口磨钝时,落料件的上端会出现 粗大的毛刺; 当凹模刃口磨钝时,冲孔件的下端会出现 粗大的毛刺; 当凸、凹模刃口同时磨钝时,则冲裁件上、下端都会产生毛刺。
第二章冲裁工艺与冲裁模
凸模:
凹模:
式中: d—冲孔工件孔的基本尺寸,mm dp、dd—冲孔凸、凹模刃口尺寸,mm Δ—工件公差,mm —凸、凹模制造偏差(查表),mm X—磨损系数(查表)
第二章冲裁工艺与冲裁模
第二章冲裁工艺与冲裁模
②落料 设冲裁件的落料尺寸为
计算原则,计算公式为:
凹模:
,根据刃口尺寸
如不满足,则应提高模具制造精度,即减小 、 ⑤优点
凸、凹模具有互换性,制造周期短,便于批量生产。 ⑥缺点:模具制造公差小,模具制造困难,成本高。
第二章冲裁工艺与冲裁模
刃口尺寸计算注意点:
1.分清是冲孔还是落料 2.冲裁间隙Z的确定:与材料和料厚有关 3.冲裁件的尺寸标注是否标准
孔的标注: 落料的标注: 中心距标注:L
基准件刃口尺寸计算式:
A类尺寸:
B类尺寸:
C类尺寸:
C = C ±D ' 4 = C ±D 8
第二章冲裁工艺与冲裁模
A类尺寸:
B类尺寸:
C类尺寸: C = C ±D ' 4 = C ±D 8
式中: A、B、C—基准件基本尺寸, mm Amax—冲裁件A类尺寸最大极限值, mm B min—冲裁件B类尺寸最小极限值, mm δ—模具制造公差, mm
毛剌区:是由于冲裁间隙的存在 而产生,该区域一般不可避免。Байду номын сангаас
第二章冲裁工艺与冲裁模
注意事项
a、粗大毛刺的产生部位:
当凸模刃口磨钝时,落料件的上端会出现 粗大的毛刺; 当凹模刃口磨钝时,冲孔件的下端会出现 粗大的毛刺; 当凸、凹模刃口同时磨钝时,则冲裁件上、下端都会产生毛刺。
第二章冲裁工艺与冲裁模
第2章冲裁及冲裁模具设计

在四个特征区中,光亮带剪切面的质量最佳。各个部分,在整个断面上 所占的比例,随材料的性能、厚度、模具冲裁间隙、刃口状态及摩擦等条 件的不同而变化.
13
第二章 冲裁及冲裁模设计
2.1冲裁变形分析
2.1.4 冲裁件断面质量及影响因素
2.材料的性能对断面质量的影响
对于塑性较好的材料,冲裁时裂纹出现得较迟,因而材料 剪切的深度较大。所以得到的光亮带所占比例大,圆角和穹 弯较大,断裂带较窄。
板料的应力达到屈服极限,板料开始
断裂分离阶段
已成形的裂纹沿最大剪应变速度方向
向材料内延伸,呈楔形状发展。
8
第二章 冲裁及冲裁模设计
2.1冲裁变形分析
9
第二章 冲裁及冲裁模设计
2.1冲裁变形分析
2.1.3 冲裁力——凸模行程曲线(如图2.1.4)
图 2.1.4 冲裁力与凸模行程曲线
10
第二章 冲裁及冲裁模设计
尺寸精度:指冲裁件的实际尺寸与基本尺寸的差值,差值 越小则精度越高。
影响冲裁件尺寸精度的主要因素:间隙、材料、工件形状 和尺寸。
当模具制造精度确定后: 间隙较大时,拉伸作用增大,落料件尺寸小于凹模尺寸, 冲孔件孔径尺寸大于凸模孔径尺寸; 间隙较小时,挤压力大,落料件尺寸将会增大,冲孔件孔 径尺寸将会变小。
19
第二章 冲裁及冲裁模设计
2.2 冲裁间隙
20
第二章 冲裁及冲裁模设计
2.2 冲裁间隙
图2.2.1中曲线与δ=0的横轴交点表明制件尺寸与模具尺 寸完全一样。
当间隙较小时,由于材料受凸 、凹模挤压力大,故冲裁完 后,材料的弹性恢复使落料件尺寸增大,冲孔孔径变小。尺 寸变化量的大小与材料性质、厚度、轧制方向等因素有关。 材料性质直接决定了材料在冲裁过程中的弹性变形量。软钢 的弹性变形量较小,冲裁后的弹性恢复也就小;硬钢的 弹性 恢复量较大。上述因素的影响是在一定的模具制造精度这个 前提下讨论的。若模具刃口制造精度低,则冲裁件的 制造精 度也就无法保证。因此, 凸、凹模刃口的制造公差一定要按 工件的尺寸要求来决定。
13
第二章 冲裁及冲裁模设计
2.1冲裁变形分析
2.1.4 冲裁件断面质量及影响因素
2.材料的性能对断面质量的影响
对于塑性较好的材料,冲裁时裂纹出现得较迟,因而材料 剪切的深度较大。所以得到的光亮带所占比例大,圆角和穹 弯较大,断裂带较窄。
板料的应力达到屈服极限,板料开始
断裂分离阶段
已成形的裂纹沿最大剪应变速度方向
向材料内延伸,呈楔形状发展。
8
第二章 冲裁及冲裁模设计
2.1冲裁变形分析
9
第二章 冲裁及冲裁模设计
2.1冲裁变形分析
2.1.3 冲裁力——凸模行程曲线(如图2.1.4)
图 2.1.4 冲裁力与凸模行程曲线
10
第二章 冲裁及冲裁模设计
尺寸精度:指冲裁件的实际尺寸与基本尺寸的差值,差值 越小则精度越高。
影响冲裁件尺寸精度的主要因素:间隙、材料、工件形状 和尺寸。
当模具制造精度确定后: 间隙较大时,拉伸作用增大,落料件尺寸小于凹模尺寸, 冲孔件孔径尺寸大于凸模孔径尺寸; 间隙较小时,挤压力大,落料件尺寸将会增大,冲孔件孔 径尺寸将会变小。
19
第二章 冲裁及冲裁模设计
2.2 冲裁间隙
20
第二章 冲裁及冲裁模设计
2.2 冲裁间隙
图2.2.1中曲线与δ=0的横轴交点表明制件尺寸与模具尺 寸完全一样。
当间隙较小时,由于材料受凸 、凹模挤压力大,故冲裁完 后,材料的弹性恢复使落料件尺寸增大,冲孔孔径变小。尺 寸变化量的大小与材料性质、厚度、轧制方向等因素有关。 材料性质直接决定了材料在冲裁过程中的弹性变形量。软钢 的弹性变形量较小,冲裁后的弹性恢复也就小;硬钢的 弹性 恢复量较大。上述因素的影响是在一定的模具制造精度这个 前提下讨论的。若模具刃口制造精度低,则冲裁件的 制造精 度也就无法保证。因此, 凸、凹模刃口的制造公差一定要按 工件的尺寸要求来决定。
精选第二章冲裁工艺与冲裁模设计

40~50
L凹或D凹 工作台孔径
40~50
(1~1.5)H 凹 50~70
(10)冲裁模装配图绘制 (11)非标零件图绘制
2.3 冲裁工艺性分析
2.3.1 冲裁变形特征
a)弹性变形阶段
b)塑性变形阶段
c)断裂分离阶段 凸、凹模间隙正常且无弹压时,金属材料的冲裁变形过程
普通冲裁零件断面
冲裁件断面示意图
1)应避免冲裁件上有过长的悬臂和狭槽。
最小宽度:b>2t
冲裁件悬臂与窄槽尺寸
2)冲裁件的孔与边缘间、孔与孔之间的距离b1、b2不 能太小。
一般取b1>1.5t, b2>2t
1.5t
最小孔边距离
3)冲裁件的外形或内孔的转角处,应避免有锐角的 清角,应采用圆弧过渡。 4)冲孔的尺寸不能太小。
(2)冲裁件的尺寸精度和粗糙度 普通冲裁件 1)尺寸精度一般在IT10~IT11级以下 2)粗糙度低于Ra=6.3μm 3)冲孔精度比落料精度高一级
般为Ⅲ类断面,由表2-18可查得Z=(14%~18%)t,即 Z=0.049~0.063mm。
3)录音机机芯暂停杆展开件冲裁间隙 录音机机芯暂停杆对冲裁断面质量要求较高,一般
为Ⅲ类断面,由表2-18可查得Z=(14%~18%)t,即 Z=0.112~0.144mm。
2.6.2 凸、凹模刃口尺寸计算的原则 ①落料尺寸取决于凹模尺寸,冲孔尺寸取决于凸模尺寸。
电机转子
电机定子
电机转子与电机定子套排(级进工序)
录音机机芯暂停杆展开件
录音机机芯暂停杆展开件
2.5.2 搭边值的确定 搭边:指排样时制件与制件之间、制件与条(板)料边 缘之间的余料。
搭边的作用 1)搭边能够补偿定位误差,保证冲出合格的制件; 2)保证条料具有一定的刚性,便于送料; 3)起到保护模具的作用,以免模具过早地磨损而报废。
第二章冲裁工艺与模具设计

2)斜排:适用于椭圆形、T形、Г形、S形零件。
3)直对排:适用于梯形、三角形、半圆形、T形、Π形、 Ш形零件。
4)斜对排:适用于椭圆形、T形、Г形、S形零件。
5)组合排:适用于材料与厚度相同的两种以上零件。
6)多行排:适用于大批量生产中尺寸不大的圆形、六角 形、方形、矩形零件。
7)交叉排:适用于C形、Π形、Ш形等零件。
3)采用侧刃:B=(L+1.5b+nF) –Δ
式中: L——制件垂直于送料方向的基本尺寸; n——侧刃数; F——侧刃裁切宽度; Δ——条料的宽度公差; b——侧面搭边值。
(2)材料利用率的计算 一般常用的计算方法是:一个进距内的实际面积与 所需板料面积之比的百分率,一般用η表示:
S S 100% 100% S0 A B
(4)典型案例分析 1)垫圈:
(4)典型案例分析 2)电机转子:
(4)典型案例分析 2)电机定子:
2)电机转子: 制件结构复杂,形状对称,无悬臂狭槽,孔边距较大; 转子轴孔Φ10的公差为0.027mm(IT8级);
外圆Φ47.2的公差为0.05mm(IT9级); 毛刺高度应小于0.05mm; 材料为电工硅钢,材料具有一定的脆性。
式中: A—在送料方向,排样图中相邻两个制件对应点的距离(mm); B—条料宽度(mm); S—一个进距内之间的实际面积(mm); S0 —一个进距内所需毛坯面积(mm)。
(3)典型案例冲裁材料利用率计算(见表2-17)
2.6 冲裁模刃口尺寸计算
2.6.1 冲裁间隙 冲裁间隙是指冲裁模凸模与凹模刃口间缝隙的距离。
1)应避免冲裁件上有过长的悬臂和狭槽。
最小宽度:b>2t
冲裁件悬臂与窄槽尺寸
- 1、下载文档前请自行甄别文档内容的完整性,平台不提供额外的编辑、内容补充、找答案等附加服务。
- 2、"仅部分预览"的文档,不可在线预览部分如存在完整性等问题,可反馈申请退款(可完整预览的文档不适用该条件!)。
- 3、如文档侵犯您的权益,请联系客服反馈,我们会尽快为您处理(人工客服工作时间:9:00-18:30)。
第二章 冲裁及冲裁模设计
§2-1 冲裁变形过程及其断面特征 §2-2 冲裁间隙 §2-3 凸模、凹模的刃口尺寸计算 §2-4 冲裁力 §2-5 排样与搭边 §2-6 冲裁件的工艺性 §2-8 冲裁模的基本类型及典型模具 §2-9 冲裁模的零部件设计 §2-10 冲裁模设计要点
3/31/2011
1
第二章 冲裁及冲裁模设计
3/31/2011
19
2.凹模设计
(1)直壁型(柱形孔)孔口: (2)锥孔型孔口: (3)凹模外形尺寸的确定: ↓表2-9 凹模厚度:H = k· b ↑工件最大外形尺寸 凹模壁厚:C=(1.5~2.0)H (≥30~40) (4)固定方式: (5)技术要求:材料:T10A、Cr6WV、9Mn2V Cr12 硬度:HRc58~62 粗糙度:Ra0.8~0.4
定义:指凸模与凹模之间的直径之差(即双面间隙,用Z表示。单边间隙,用Z/2表示。)。 一.间隙对冲裁件断面质量的影响: 过大:制件锥度过大、断裂带过宽。 过小:两个光亮带、上有毛刺。 二.间隙对冲裁件尺寸精度的影响: 过大:以拉伸变形为主,弹性恢复后,冲孔孔扩大、落料料缩小。 过小:以压缩变形为主,弹性恢复后,冲孔孔缩小、落料料扩大。 三.间隙对模具寿命的影响: 过小:凸模与凹模之间磨损严重,降低模具寿命。 四.间隙对冲裁力的影响: 间隙大:冲裁力减小。 但是,当间隙增至材料厚度的5%~20%时,冲裁力不再明显降低。 另外,间隙大:卸料力也减小。 五.间隙值的确定: 合理间隙值与材料性质和厚度等因素有关。 h 1.理论计算法: Z = 2 (t − h0 )tg β = 2 t 1 − 0 tg β
若制件没有标注公差,则: 对于非圆形工件,工件按IT14级精度、模具按IT11级精度处理; 对于圆形工件,由于加工方法比较成熟,模具按IT6~IT7级精度处理。 当凸模、凹模分开加工时,须满足:δ凸+δ凹≤Zmax-Zmin
3/31/2011
6
二.刃口尺寸的计算方法:
1.凸模、凹模可分开加工(完全互换): 对于简单形状,如圆形、正方形等形状的工件,可分开加工,且分别标注公差。 1)冲孔:根据上述计算原则,应先确定凸模的尺寸。 由于凸模磨损后尺寸变小,所以凸模尺寸应尽量取工件尺寸的上限,即 考虑制造精度的影响,取 式中x为磨损系数,与制造精度有关,即 工件精度在IT10级以上,x=1.0 工件精度在IT11~IT13级,x=0.75 工件精度在IT14级以下,x=0.5 由于基本尺寸已经偏上限,所以凸模的上偏差应为零,即 凹模的刃口尺寸为凸模的刃口尺寸加上最小间隙Zmin, 以保证凹模磨损后间隙仍在合理范围之内(凹模磨损后尺寸变大),即 由于基本尺寸已经偏下限,所以凹模的下偏差应为零,即
(2)弹压卸料:工件预先被压紧,冲裁过程平稳, 制件尺寸精度高、平整度高。 适用于板料较薄,制件表面平整度要求较高的场合。 分类:(a)橡胶类: (b)弹簧类:
设计时注意:
a. 弹簧或橡胶有疲劳寿命 b. 橡胶最大压缩量40% c. 预压量10~15% e. 若橡胶处于封闭的内腔, 3/31/2011 须有足够的径向空间 f. 橡胶注意防油
t
2.经验确定法: 表2-1:间隙较小,精度高,用于仪器仪表行业。 表2-2:间隙较大,精度一般,用于机电行业中结构件。 3/31/2011
4
表2-1:间隙较 小,精度高,用 于仪器仪表行业。
表2-2:间隙较大, 精度一般,用于机 电行业中结构件。
3/31/2011
5
§2-3 凸模、凹模的刃口尺寸计算:
一.冲裁件的精度等级: 经济精度:IT11~IT 12 最高精度:IT8~IT 10 冲孔可高一些(凸模精度可高一些) 断面粗糙度:Ra12.5~50 最高可达:Ra6.3 二.冲裁件的结构工艺性
1.形状应简单对称,最好采用圆形、矩形等规则形状; 2.凸出的悬臂和凹槽部分宽度不宜太小; 3.内、外转角处,应避免尖角出现,应以圆角过度; 4.冲孔时,孔的直径不宜太小,否则凸模的强度不易保证; 5 5.冲裁件的孔与孔之间、孔与边缘之间距离不宜过小; 6.弯曲件或拉深件上冲孔时,其孔边与制件直壁之间的距离 不宜过小。
Ai = ( A − x∆ )
1 + ∆ 4
1)B类尺寸:凹模磨损后尺寸变小, 先将尺寸化为B+Δ(工件最大尺寸)的形式: 凹模尺寸为:
Bi = ( B + x∆ ) − 1 ∆
4
1)C类尺寸:凹模磨损后尺寸不变, 先将尺寸化为A±Δ/2(工件中心尺寸)的形式: 1 凹模尺寸为: C =C± ∆
i
8
一.刃口尺寸计算的原则:
1.落料:制件尺寸为锥面大端尺寸,其尺寸等于凹模的刃口尺寸; 故,应先确定凹模的刃口尺寸; 凸模的刃口尺寸为凹模的刃口尺寸减去最小间隙Zmin, 以保证凸模磨损后间隙仍在合理范围之内。 2.冲孔:孔的尺寸为锥面小端尺寸,其尺寸等于凸模的刃口尺寸; 故,应先确定凸模的刃口尺寸; 凹模的刃口尺寸为凸模的刃口尺寸加上最小间隙Zmin, 以保证凹模磨损后间隙仍在合理范围之内。 3.凸模、凹模的制造公差: 过高:增加了加工成本,造成产品市场竞争力降低。 过低:难以保证制件的质量。 模具精度与工件精度之间的关系:
3.条料的送进导向方式与零件:
保证条料有正确的送进方向,以保证沿边宽度要求。 无侧压:导向槽,宽度要有公差要求(间隙配合)图2-33 有侧压:工件靠一边送进。图2-34
3/31/2011
22
三.卸料与出件(顶件、推件)装置:
1.卸料装置
(1)固定卸料:适用于板料较厚、较硬, 制件表面平整度要求不高的场合。 优点:a. 卸料力大; b. 冲裁在全封闭的状态下进行,操作安全 c. 结构简单、体积小; d. 便于连续冲压; 缺点:条料未被预先压住, 工件易弯曲、弓背,制件精度低。 分类:导向类: 不导向:
3/31/2011
13
§2-8 冲裁模的基本类型及典型模具:
一.冲裁模的分类
1.按工序性质分类 落料模、冲孔模、切断模、切口模┅ ┅ 2.按工序组合程度分类 (1)单工序模(简单模):在一付模具上只完成一道工序; (2)级进模(跳步模):在不同的位置上完成两道以上工序; (3)复合模:在同一位置上完成两道以上工序;
一.冲裁力的计算:
F = KLt τ
可取 二.卸料力、推件力和顶件力的计算: 推件力:
τ = 0.8σ b
F1 = nK1 F
F2 = K 2 F
F3 = K 3 F
顶件力:
脱料力: 表2-5 :
3/31/2011
10
§2-5 排样与搭边
一.排样:
冲裁件在板料上的布置方式叫排样。 材料利用率:
:
K=
工件的总面积 × 100% 毛坯(板料)的总面积
3/31/2011
11
二.搭边:
排样时,制件与制件或制件与边沿之间的余料叫搭边。 搭边并不是越小越好。 搭边值过大:材料利用率低,造成浪费。 搭边值过小:容易出残缺废品,或搭边被拉断,造成模具刃口损坏。 搭边值的选取:表2-7
3/31/2011
12
§2-6 冲裁件的工艺性:
§2-1 冲裁变形过程及其断面特征:
一.冲裁变形过程:
1.弹性变形阶段:由加压接触开始,至材料屈服前。 2.塑性变形阶段:由材料屈服开始,至产生裂纹前。 3.断裂分离阶段:由产生裂纹开始,至上下裂纹重合。 4.推出阶段)
3/31/2011 2
二.冲裁件及其断面特征:
1.圆角带:
特点:如钝圆加工后一般。 产生机理:塑性变形开始时,金属纤维发生弯曲形成圆角。
3/31/2011
24
3. 模柄:
(a)带凸沿模柄:适用于大型模具 (b)压入式模柄:H7/m6、H7/n6 (c)旋入式模柄:定位精度差、应有骑缝螺钉(防松) (d)浮动式模柄:避免过定位。
二.典型冲裁模的结构分析:
1.单工序模(简单模): (1)无导向单工序模:靠滑块与机床导轨导向,可靠性差,难以保证间隙均匀,制件精度低。
3/31/2011
14
(2)导板式导向: 导向精度低,但结构简单。
(3)导柱式导向: 导向精度高,但结构复杂, 模具轮廓尺寸大,成本高。
3/31/2011
15
2.级进模(跳步模):
e− d D =C− 2 2
挡料销位置: e = C − D + d + 0.1 2 2
↑作为条料前推后拉的余量
3/31/2011
21
2.侧刃定距:
特点:适用于薄壁工件,但用料增加,造成浪费。 三种形状: a.长方形:在步距衔接处容易产生毛刺,影响定位精度。 b.成形侧刃:毛刺位于凹进处,不影响定位精度。 c.尖角侧刃:可设在排样的空挡处,避免浪费材料, 但送料后必须向后拉一下,否则定位不准。
3/31/2011
上述公式中模具公差取工件公差的1/4,磨损系数x为: 工件精度在IT10级以上,x=0.9~1.0 工件精度在IT11~IT13级,x=0.7~0.9 工件精度在IT14级以下,x=0.5~0.7 上述制件的冲孔时,应先制造凸模。由于A类尺寸变小, B类尺寸变大,方法相应改变。
9
§2-4 冲裁力:
2. 凸模与凹模的配作(配合加工):
对于复杂形状的工件,先按照制件尺寸加工出凸模 与凹模中的一件(落料时加工凹模;冲孔时加工凸模), 然后按照间隙要求加工另一件,另一件凸模或凹模 只需标注基本尺寸和间隙。 上述制件的落料,应先制造凹模。 1)A类尺寸:凹模磨损后尺寸变大, 先将尺寸化为A-Δ(工件最小尺寸)的形式: 凹模尺寸为:
(1)有固定挡料销及导正钉的级进模:
3/31/2011
优点:定位精度高,定位可靠。 缺点:导向孔直径不能太小,工件料厚不能太薄。
16
(2)采用侧刃定距的级进模:
3/31/2011
§2-1 冲裁变形过程及其断面特征 §2-2 冲裁间隙 §2-3 凸模、凹模的刃口尺寸计算 §2-4 冲裁力 §2-5 排样与搭边 §2-6 冲裁件的工艺性 §2-8 冲裁模的基本类型及典型模具 §2-9 冲裁模的零部件设计 §2-10 冲裁模设计要点
3/31/2011
1
第二章 冲裁及冲裁模设计
3/31/2011
19
2.凹模设计
(1)直壁型(柱形孔)孔口: (2)锥孔型孔口: (3)凹模外形尺寸的确定: ↓表2-9 凹模厚度:H = k· b ↑工件最大外形尺寸 凹模壁厚:C=(1.5~2.0)H (≥30~40) (4)固定方式: (5)技术要求:材料:T10A、Cr6WV、9Mn2V Cr12 硬度:HRc58~62 粗糙度:Ra0.8~0.4
定义:指凸模与凹模之间的直径之差(即双面间隙,用Z表示。单边间隙,用Z/2表示。)。 一.间隙对冲裁件断面质量的影响: 过大:制件锥度过大、断裂带过宽。 过小:两个光亮带、上有毛刺。 二.间隙对冲裁件尺寸精度的影响: 过大:以拉伸变形为主,弹性恢复后,冲孔孔扩大、落料料缩小。 过小:以压缩变形为主,弹性恢复后,冲孔孔缩小、落料料扩大。 三.间隙对模具寿命的影响: 过小:凸模与凹模之间磨损严重,降低模具寿命。 四.间隙对冲裁力的影响: 间隙大:冲裁力减小。 但是,当间隙增至材料厚度的5%~20%时,冲裁力不再明显降低。 另外,间隙大:卸料力也减小。 五.间隙值的确定: 合理间隙值与材料性质和厚度等因素有关。 h 1.理论计算法: Z = 2 (t − h0 )tg β = 2 t 1 − 0 tg β
若制件没有标注公差,则: 对于非圆形工件,工件按IT14级精度、模具按IT11级精度处理; 对于圆形工件,由于加工方法比较成熟,模具按IT6~IT7级精度处理。 当凸模、凹模分开加工时,须满足:δ凸+δ凹≤Zmax-Zmin
3/31/2011
6
二.刃口尺寸的计算方法:
1.凸模、凹模可分开加工(完全互换): 对于简单形状,如圆形、正方形等形状的工件,可分开加工,且分别标注公差。 1)冲孔:根据上述计算原则,应先确定凸模的尺寸。 由于凸模磨损后尺寸变小,所以凸模尺寸应尽量取工件尺寸的上限,即 考虑制造精度的影响,取 式中x为磨损系数,与制造精度有关,即 工件精度在IT10级以上,x=1.0 工件精度在IT11~IT13级,x=0.75 工件精度在IT14级以下,x=0.5 由于基本尺寸已经偏上限,所以凸模的上偏差应为零,即 凹模的刃口尺寸为凸模的刃口尺寸加上最小间隙Zmin, 以保证凹模磨损后间隙仍在合理范围之内(凹模磨损后尺寸变大),即 由于基本尺寸已经偏下限,所以凹模的下偏差应为零,即
(2)弹压卸料:工件预先被压紧,冲裁过程平稳, 制件尺寸精度高、平整度高。 适用于板料较薄,制件表面平整度要求较高的场合。 分类:(a)橡胶类: (b)弹簧类:
设计时注意:
a. 弹簧或橡胶有疲劳寿命 b. 橡胶最大压缩量40% c. 预压量10~15% e. 若橡胶处于封闭的内腔, 3/31/2011 须有足够的径向空间 f. 橡胶注意防油
t
2.经验确定法: 表2-1:间隙较小,精度高,用于仪器仪表行业。 表2-2:间隙较大,精度一般,用于机电行业中结构件。 3/31/2011
4
表2-1:间隙较 小,精度高,用 于仪器仪表行业。
表2-2:间隙较大, 精度一般,用于机 电行业中结构件。
3/31/2011
5
§2-3 凸模、凹模的刃口尺寸计算:
一.冲裁件的精度等级: 经济精度:IT11~IT 12 最高精度:IT8~IT 10 冲孔可高一些(凸模精度可高一些) 断面粗糙度:Ra12.5~50 最高可达:Ra6.3 二.冲裁件的结构工艺性
1.形状应简单对称,最好采用圆形、矩形等规则形状; 2.凸出的悬臂和凹槽部分宽度不宜太小; 3.内、外转角处,应避免尖角出现,应以圆角过度; 4.冲孔时,孔的直径不宜太小,否则凸模的强度不易保证; 5 5.冲裁件的孔与孔之间、孔与边缘之间距离不宜过小; 6.弯曲件或拉深件上冲孔时,其孔边与制件直壁之间的距离 不宜过小。
Ai = ( A − x∆ )
1 + ∆ 4
1)B类尺寸:凹模磨损后尺寸变小, 先将尺寸化为B+Δ(工件最大尺寸)的形式: 凹模尺寸为:
Bi = ( B + x∆ ) − 1 ∆
4
1)C类尺寸:凹模磨损后尺寸不变, 先将尺寸化为A±Δ/2(工件中心尺寸)的形式: 1 凹模尺寸为: C =C± ∆
i
8
一.刃口尺寸计算的原则:
1.落料:制件尺寸为锥面大端尺寸,其尺寸等于凹模的刃口尺寸; 故,应先确定凹模的刃口尺寸; 凸模的刃口尺寸为凹模的刃口尺寸减去最小间隙Zmin, 以保证凸模磨损后间隙仍在合理范围之内。 2.冲孔:孔的尺寸为锥面小端尺寸,其尺寸等于凸模的刃口尺寸; 故,应先确定凸模的刃口尺寸; 凹模的刃口尺寸为凸模的刃口尺寸加上最小间隙Zmin, 以保证凹模磨损后间隙仍在合理范围之内。 3.凸模、凹模的制造公差: 过高:增加了加工成本,造成产品市场竞争力降低。 过低:难以保证制件的质量。 模具精度与工件精度之间的关系:
3.条料的送进导向方式与零件:
保证条料有正确的送进方向,以保证沿边宽度要求。 无侧压:导向槽,宽度要有公差要求(间隙配合)图2-33 有侧压:工件靠一边送进。图2-34
3/31/2011
22
三.卸料与出件(顶件、推件)装置:
1.卸料装置
(1)固定卸料:适用于板料较厚、较硬, 制件表面平整度要求不高的场合。 优点:a. 卸料力大; b. 冲裁在全封闭的状态下进行,操作安全 c. 结构简单、体积小; d. 便于连续冲压; 缺点:条料未被预先压住, 工件易弯曲、弓背,制件精度低。 分类:导向类: 不导向:
3/31/2011
13
§2-8 冲裁模的基本类型及典型模具:
一.冲裁模的分类
1.按工序性质分类 落料模、冲孔模、切断模、切口模┅ ┅ 2.按工序组合程度分类 (1)单工序模(简单模):在一付模具上只完成一道工序; (2)级进模(跳步模):在不同的位置上完成两道以上工序; (3)复合模:在同一位置上完成两道以上工序;
一.冲裁力的计算:
F = KLt τ
可取 二.卸料力、推件力和顶件力的计算: 推件力:
τ = 0.8σ b
F1 = nK1 F
F2 = K 2 F
F3 = K 3 F
顶件力:
脱料力: 表2-5 :
3/31/2011
10
§2-5 排样与搭边
一.排样:
冲裁件在板料上的布置方式叫排样。 材料利用率:
:
K=
工件的总面积 × 100% 毛坯(板料)的总面积
3/31/2011
11
二.搭边:
排样时,制件与制件或制件与边沿之间的余料叫搭边。 搭边并不是越小越好。 搭边值过大:材料利用率低,造成浪费。 搭边值过小:容易出残缺废品,或搭边被拉断,造成模具刃口损坏。 搭边值的选取:表2-7
3/31/2011
12
§2-6 冲裁件的工艺性:
§2-1 冲裁变形过程及其断面特征:
一.冲裁变形过程:
1.弹性变形阶段:由加压接触开始,至材料屈服前。 2.塑性变形阶段:由材料屈服开始,至产生裂纹前。 3.断裂分离阶段:由产生裂纹开始,至上下裂纹重合。 4.推出阶段)
3/31/2011 2
二.冲裁件及其断面特征:
1.圆角带:
特点:如钝圆加工后一般。 产生机理:塑性变形开始时,金属纤维发生弯曲形成圆角。
3/31/2011
24
3. 模柄:
(a)带凸沿模柄:适用于大型模具 (b)压入式模柄:H7/m6、H7/n6 (c)旋入式模柄:定位精度差、应有骑缝螺钉(防松) (d)浮动式模柄:避免过定位。
二.典型冲裁模的结构分析:
1.单工序模(简单模): (1)无导向单工序模:靠滑块与机床导轨导向,可靠性差,难以保证间隙均匀,制件精度低。
3/31/2011
14
(2)导板式导向: 导向精度低,但结构简单。
(3)导柱式导向: 导向精度高,但结构复杂, 模具轮廓尺寸大,成本高。
3/31/2011
15
2.级进模(跳步模):
e− d D =C− 2 2
挡料销位置: e = C − D + d + 0.1 2 2
↑作为条料前推后拉的余量
3/31/2011
21
2.侧刃定距:
特点:适用于薄壁工件,但用料增加,造成浪费。 三种形状: a.长方形:在步距衔接处容易产生毛刺,影响定位精度。 b.成形侧刃:毛刺位于凹进处,不影响定位精度。 c.尖角侧刃:可设在排样的空挡处,避免浪费材料, 但送料后必须向后拉一下,否则定位不准。
3/31/2011
上述公式中模具公差取工件公差的1/4,磨损系数x为: 工件精度在IT10级以上,x=0.9~1.0 工件精度在IT11~IT13级,x=0.7~0.9 工件精度在IT14级以下,x=0.5~0.7 上述制件的冲孔时,应先制造凸模。由于A类尺寸变小, B类尺寸变大,方法相应改变。
9
§2-4 冲裁力:
2. 凸模与凹模的配作(配合加工):
对于复杂形状的工件,先按照制件尺寸加工出凸模 与凹模中的一件(落料时加工凹模;冲孔时加工凸模), 然后按照间隙要求加工另一件,另一件凸模或凹模 只需标注基本尺寸和间隙。 上述制件的落料,应先制造凹模。 1)A类尺寸:凹模磨损后尺寸变大, 先将尺寸化为A-Δ(工件最小尺寸)的形式: 凹模尺寸为:
(1)有固定挡料销及导正钉的级进模:
3/31/2011
优点:定位精度高,定位可靠。 缺点:导向孔直径不能太小,工件料厚不能太薄。
16
(2)采用侧刃定距的级进模:
3/31/2011