N300型客车后桥壳断裂的分析和改进
提高中型驱动后桥壳焊接接头疲劳寿命的方法

提高中型驱动后桥壳焊接接头疲劳寿命的方法说到中型驱动后桥壳焊接接头的疲劳寿命,哎呀,这可真是个让人头疼的话题!你要知道,那个后桥,简直就是整个车的命脉,稍微有个啥小问题,车子就能给你“开小差”,让你面临一些棘手的麻烦。
尤其是那些焊接接头,老是暴露在各种复杂的应力、温度和环境条件下,时间一长就容易疲劳,甚至断裂。
你想,这一旦出现问题,可不得了!车主或者工程师可真是要抓狂了。
别看这小小的焊接接头,它可不像我们想象的那么简单。
焊接工艺就像厨师做菜一样,不同的手法和材料,最后出来的味道差别大着呢。
最常见的做法是先选用好材料,确保焊接接头的质量过关。
俗话说,“工欲善其事,必先利其器”,用不好的焊材就像厨师拿个生锈的锅煮菜,怎么可能好吃?所以,选对了焊条、焊丝,材料强度也就有了保障。
焊接过程中可得保持温度稳定,温度一旦波动,焊接接头的性能可能就大打折扣,那可就麻烦了。
不过,别急,我们还可以从其他方面着手!像是优化焊接接头的形状和尺寸,真的比你想象的更重要。
有些焊接接头一开始就设计得不太理想,焊缝处可能会有尖锐的角落,或者焊接不均匀,稍微承受一下力量,就像爆米花一样,“噼里啪啦”地炸开了。
所以啊,设计时最好考虑到力学性能,避免那些不必要的应力集中区域。
就像我们平常走路,别让鞋子有凸起的地方,否则走着走着就容易崴脚,不小心就掉链子。
再聊聊一种常见的手段——预热。
这可是不少老司机的“秘密武器”!通过在焊接前加热焊接部位,能够有效减少焊接过程中的温差,避免裂纹的产生。
想象一下,如果你冰箱里的食物突然被拿到阳光下暴晒,温差太大岂不是炸开了?焊接也是一样的道理,温差大了,内部的应力积累就会导致疲劳,时间长了接头就容易崩溃。
此外,冷却速度的控制也是个技术活儿。
太快就容易形成脆性结构,太慢又会影响生产效率。
我们常说“急不得,来得快不一定好”。
控制好冷却速度,既能保证焊接接头的强度,又能提高焊接效率,一举两得,岂不美哉?说到这里,别以为这些都是纸上谈兵,光理论上做得再好,没有实际操作经验也不行。
汽车后桥壳开裂的分析与改进

科技与企业 221科技汽车后桥壳开裂的分析与改进【摘要】针对某汽车在丘陵地带矿区路上行驶过程中出现故后桥壳一侧弹簧座附近、近似垂直于轴向短焊缝末端开裂现象,通过桥壳断口形貌进行了宏微观观察,对桥壳基体进行了组织检查,确定了桥壳的开裂性质,分析了开裂的可能原因并提出改进方向。
【关键词】后桥壳;分析;开裂性质;改进随着汽车底盘技术日新月异的发展,汽车用高强度金属板材的应用与研究已经逐步引起了汽车制造厂商的重视,关于汽车桥壳强度的分析,有必要得到更深层次研究和开发。
1.概述某汽车在丘陵地带矿区路上行驶过程中出现故障,停车分解检查,发现后桥壳一侧弹簧座附近、近似垂直于轴向短焊缝末端开裂。
截止至发现后桥壳开裂时,汽车累计行驶路程为27662km。
故障发现前司机没有发现行车异常情况。
该桥壳为冲焊结构,首先经弯曲对接,然后用CO2气体保护焊焊接成型。
桥壳材料为A510L钢。
2.试验过程与结果2.1外观检查板桥外观及开裂位置均在桥壳的背面,位于弹簧座附近,与车辆的前进方向相反,沿桥壳周向分布;开裂区域未见异常损伤。
2.2断口宏观观察断口的整体形貌显示断口表面较为平整,有少量的塑性变形。
断口上可观察到较为明显的疲劳源区和疲劳弧线,裂纹扩展方向为沿桥壳周向,瞬断区出现了严重的磨损。
源区起源于焊缝区外表面一侧。
为进一步对断口进行观察,将断口放于体视显微镜下进行观察。
桥壳断口的宏观形貌分别见图1。
由图1可以看出,桥壳的源区起源于焊缝外表面一侧,为点源特征。
源区被少量油污覆盖,但仍能观察到明显的疲劳弧线,弧线大小间距不等。
疲劳扩展区所占面积较小,而在整个断口上瞬断区所占面积较大,瞬断区大部分区域都因磨损而呈现光亮。
2.3断口微观观察将断口经超声波清洗后放入扫描电镜下观察。
桥壳断口低倍形貌见图2a,源区的局部放大图见图2b。
从图中可以观察到明显的疲劳弧线。
源区旁边是焊缝区,该区域存在较为严重的磨损,应为桥壳开裂后形成,见图2c。
某型越野汽车尾梁结构失效分析及改进

10.16638/ki.1671-7988.2017.04.061某型越野汽车尾梁结构失效分析及改进叶智博,莫飞,钟瑞(陕西重型汽车有限公司,陕西西安710200)摘要:文章对某型越野汽车尾梁在使用中的开裂现象进行分析,根据使用工况,对模型进行力学分析,运用数学建模及有限元结构理论,对其进行计算与模拟分析,并提出改进结构,提高系统可靠度。
关键字:开裂;运动分析;有限元中图分类号:U467.3 文献标识码:A 文章编号:1671-7988 (2017)04-181-03Invalidation anasysis and optimization of the truck beamYe Zhibo, Mo Fei, Zhong Rui(Shaanxi Heavy Duty Automotive Co., Ltd, Shaanxi Xi'an 710200)Abstract: Craze of the beam was studied, the objective was to strong credibility by mechanics theory and Finite element. Keywords: craze; analysis; finite elementCLC NO.: U467.3 Document Code: A Article ID: 1671-7988 (2017)04-181-03引言我国重型舟桥系统用于江河、湖泊、等指定水域实施舟桥架设作业;提高应对突发事件及抗洪救灾时的紧急处置能力,争取救援时间,起到良好的军事、社会效益。
图1 尾梁总成加强角撑处脱焊2015年3月,售后市场反馈,服役的某重型舟桥系统底盘在高强度集中训练后,尾梁总成两侧加强角撑脱焊、开焊,存在安全隐患。
作为重型舟桥系统的承载、运输平台,出现此种故障失效,影响舟桥系统展开、撤收,需从根本上解决。
一种重卡管状横梁断裂的失效分析及改善方法

收 稿 日期 :02— 4—1 21 0 3
作者简 介 : 剑波 (9 0 ) 男 , 谢 18 一 , 工程硕士 , 工程 师 , 主要从 事重卡动力系统 的产品开发和改进研究 。
6 8
四 川 兵 工 学 报
ht :/ c gjusr. o t / sb .o r v cm/ p e
—
96.
( 责任 编 辑
鲁
进)
( 接第 6 上 5页 )
对 于 主 轴 的 动 态 性 能 研 究 , 时 间 与 过 程 的 角 度 , 在 从 旨
为提高主轴运作 的高效性与准确性 提供依据 , 此可 以提高 如 加工精度 。动态 性能 包括 力学性 能 , 动频 率等 各种 性 能。 振 对机床主轴工作 状态下的动态性能 的评估 , 更好地把 握机 能 床 的工作性 能与机床 的发展 。
扩张应力 。② 应 力 腐 蚀 断裂 是 一 种 与 时间 有关 的滞 后 破 坏, 这和氢滞后开 裂 完全 类似 。③ 应 力 腐蚀 开裂 是 一种 低
应力脆性 断裂 。 该 管 状 梁 一 般 出现 断 裂 的部 位 在 发 动 机 着 力 点 上 , 接 焊
参 考文献 :
胡 玉梅 , 士 星 , 以轩 , , 动 机 悬 置 系统 优 化 方 法 张 向 等 发
直板 时热 影响区域较 大 , 使局 部材 质 的应力 发生 变化 , 因此
才 出 现 了 轴 向 方 向 的垂 直 断 裂 。
发生脆性断裂 的原 因是存 在和焊缝相 交 的构 造缝 隙 , 或 相 当于构造缝 隙的未透 焊缝 。构造焊缝 相当 于狭 长 的裂纹 , 造成 高度 的应力集 中 , 焊缝则造成高额 残余 拉应力并使 近旁
客车后钢板弹簧疲劳断裂原因的分析与改进措施
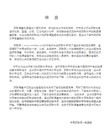
2)
簧片在断口处是否有附加应力产生除设计应力外,如果因某种原因有附加应力产生,使总应力加大也可能造成钢板弹簧片断裂,通过对断裂簧片断口处观察,发现此处在压延时造成了轻微急弯,使该片端部同上一片形成点接触,对这一点从试验后两片间的摩擦痕迹也证明了此点(如图)
摘 要:本文通过对BL客车后钢板弹簧断裂断口形状、设计应力、原材料及理化性能等方面的分析,找出造成钢板弹簧疲劳断裂的原因,提出了改进的措施,使该钢板弹簧的疲劳寿命达到日本五十铃公司标准的要求。
关键词:钢板弹簧;疲劳断裂;原因分析;改进措施
4 对钢板弹簧疲劳断裂原因分析
根据以上试验结果可以看出,疲劳断裂的簧片均在第7片且同在钢板弹簧的大卷耳端,且位置距钢板弹簧中心螺栓距离也差别不大(138、142、150),说明该钢板弹簧在此处存在规律性疲劳断裂源,而非偶然原因造成的,下面根据疲劳断裂试验结果及设计、生产过程对钢板弹簧疲劳断裂的原因进行分析。
......
I=7 σ1=37 σ2=41 σ3=44 σ4=47 σ5=17 σ6=2
......
注:I—片序 σ—应力 kg/mm2 各应力点为平均间隔(100mm)。
1 问题的提出
BL客车是对日本五十铃公司BE2ቤተ መጻሕፍቲ ባይዱ客车技术引进、吸收、消化后的一种轻型客车,该客车后悬挂弹性元件是一变刚度钢板弹簧,该种钢板弹簧的优点是在客车空载、满载状态下呈非线性状态,即悬挂在客车空载、满载状态下接近等频性,从而可以提高客车的平顺性,乘客乘坐舒适性,本文通过分析BL客车后钢板弹簧在设计、试制、试验过程中出现非正常疲劳断裂原因分析,提出了改进措施,使其达到了日本五十铃公司BE22客车后钢板弹簧疲劳寿命的标准要求。
汽车驱动桥壳性能仿真分析及其改进

术对某驱动桥壳体进行强度分析和刚度分析袁分析结果表明其最 大应力均在桥壳过渡区域袁但其未分析壳体的模态特性遥 文献[5]对 某扭转梁式后桥进行试验模态分析和有限元分析袁根据应变能较 大区域对关键部件进行了改进袁提升其模态性能袁但是其未考虑 后桥的强度性能和刚度性能遥 文献[6]对某驱动桥桥壳进行有限元 强度分析和自由模态分析袁分析结果表明该驱动桥壳的最大应力 和模态频率均能满足设计袁但是其过度简化了驱动桥壳有限元模 型袁为未考虑差速器和轮毂等遥 以上研究者未同时考察驱动桥的 强度特性尧刚度特性和模态特性袁有一定的局限性遥 为了更加精确 地分析并且验证某汽卡车驱动桥壳的性能袁现基于驱动桥壳原理
Performance Simulation Analysis and Optimization of a Truck Drive Axle
DING Wen-min
渊 Jiangling Motors Corporation Limited袁 Jiangxi Nanchang 330001袁 China冤
粤遭泽贼则葬糟贼:A iming at the problem of obtaining the strength袁 modal and stiffness performance of a truck driving axle袁 the finite element model of driving axle was established based on analysis principle model袁 the drive axle was constrained and loaded baed on actual conditions.The strength analysis results showed that the maximum stress of drive axle exceed the material yield in working condition of vertical jump袁 it located in the bridge shell and plate spring bearing weld joint袁 it didn爷t meet the design requirements. The maximum stress of drive axle was decreased and less than the material allowable stress by increasing the thickness of the drive axle housing and increasing the transition arc radius of the axle housing袁 so it meet the strength requirements.The modal analysis results showed that the first third restraint frequencies of the drive axle were greater than the engine idle frequency袁 the risk of resonance would be avoided袁 so it meet the modal requirements. The stiffness analysis results showed that the maximum vertical displacement per meter was less than the national standard袁 so it meet the stiffness requirements. The drive axle could meet the requirements of strength袁 modal and stiffness after optimization. Key Words院Driving Axle Housing曰 Simulation曰 Strength曰 Modal曰 Stiffness
某车型驱动桥后桥壳开裂分析

驱动 桥 后 桥 壳 是 汽 车重 要 的组 成 部 分 ,它 不 但 支 撑 着 汽 车 的 4 化学 元素 分析 去 除失效 件表 面保 护层 , 从失 效件 本体 上取 样进 行化 学元 素分 重量 , 将载荷传递给车轮 , 还 承受制动工况 、 驱动工况 、 横 向工况 、 纵 向工 况 及 上 下 跳 工况 产 生 的力 或 力矩 ,并 经悬 架 传 递 给 车 身 或 析 , 分析结 构如 表 1 :
图 1加 , 造成后桥壳出现破 观 察 断 口形 貌 , 发 现断 口表 面较 为平 整 , 有 少 量 的塑 形 变形 , 端 较恶劣 , 坏 。 口上 可观 察 到较 为 明 显 的疲 劳源 区 和疲 劳 弧线 , 裂 纹 扩 展方 向为 沿 综上 , 后桥壳工作过程受到较大的应力作用 , 在易于萌生裂纹 , 后 桥 壳周 向 , 瞬 断 区 出 现 了严 重 的磨 损 , 后 桥 壳 源 区起 源 于 焊 缝 区 工作 应力 较大 的焊 缝 区域产 生裂 纹 , 裂 纹产 生后 在 变化载 荷 的作用 外 表 面一 侧 。为 进 一 步对 断 口进 行 观察 , 将 断 口放 于 显 微镜 下 进 行 最 终导 致 桥壳疲 劳 开裂 。 观察 , 后 桥壳 源 区 起源 于焊 缝 外表 面一侧 , 为点 源特 征 , 源 区被少 量 下逐 渐扩 展 ,
表 1 车 架 。在 汽 车行 驶 过 程 中 , 由于 道 路 条件 的干 变 万 化 , 桥 壳 受 到 车 轮 与 地 面 间产 生 的 冲击 载 荷 影 响 , 可 能 引起 桥 壳 变 形 或 开裂 , 甚 至 兀素( % ) C J S s i M n P 断裂 , 因此 驱 动桥 后 桥 壳 应具 有 足 够 的强 度 和 刚度 。 同 时其 内部 装 要 求 ≤0 . 2 l l ≤0 . 0 3 5 ≤0 . 3 ≤1 . 5 ≤O . 0 3 5 有减速器 、 差速器 、 车轮 传 动 装 置 及 齿 轮 油 , 不 但 可 以保 护 上述 零 失效 件 0 . 1 6 l 0 . 0 0 6 0 . 1 1 l _ 1 8 O . 0 o 7 部 件 受 到 外 界 的破 坏 ,还 可 以通 过 内部 的 齿 轮 油 润滑 零 部 件 之 间 根据 分析 结果 可知 , 失效 后桥 壳所 用材 料化 学元 素满 足标 准要 的摩 擦 , 降 低零 部 件 摩 擦 产 生 的 温度 , 提 高 其 寿命 , 所 以合 理 的设 求 。 计制 造驱动桥后 桥壳是提高 汽车行驶稳定性 和操作 性的重要 措 5 分析 结论 施, 如 驱 动 桥 后桥 壳失 效 , 会 影 响整 车 操 稳 , 甚 至 发 生交 通 事 故 , 威 以上试 验 结果 表 明 , 后桥 壳开 裂断 口表 面可 见 明显 的疲劳 辉 胁生命。 纹, 疲 劳条 带特 征 , 表明此 开 裂为疲 劳 开裂 , 疲劳 源 区起 源 于焊 缝 , 某 款 车型 在 矿 区行 驶 过 程 中 , 驱动 桥 后 桥 壳 开 裂 , 对 失 效件 进 桥壳 在进 行气 体保 护焊 焊接 时 , 焊缝处 的金 属在 冷 却时会 收缩 , 往 行 分析 , 结 果如 下 : 往在 焊缝 内产 生较 大 的残余 应力 , 在较 大 的外力 作 用下容 易醒 焊缝
汽车后桥壳工艺分析及解决方案

王 樑
( 安阳工学院, 河南 安阳 %&&’’’ ) 摘 要: 通过对汽车后桥壳的工艺分析, 介绍了汽车焊接式后桥在组合机床上的常规工艺流程, 并针对用户 的一些特殊要求, 提出了解决方案, 总结出一条规范可靠的加工工艺方案。 关键词: ’&()#*’ +%*’,-)- &% .$" /*0 1"*0 +2’" *%3 4.- 5&’6.)&%()*+ ,-./0 ( )/1./0 2/34-4546 78 96:;/7<701,)/1./0 %&&’’’ ,=>*) !"#$%&’$ :9;?750; 4;6 ./.<13-3 78 46:;/7<701 87? 4;6 :.? ?6.? .@<6 ,./ -/4?7A5:4-7/ 47 4;6 :7/B6/4-7/.< 46:;/7<70-:.< C?7:633 87? D6<A-/0 4;6 :.? .@<6 7/ E7A5<.? E.:;-/6 477< -3 0-B6/F 9;6 C.C6? :7E63 5C 37E6 37<54-7/3 .::7?A-/0 47 4;6 536?3G 3C6:-8-: A6E./A3 ,./A 35E3 5C . 34./A.?A ./A ?6<-.H<6 46:;/7<70-:.< C<./F ()*+,%-#:=.?;I6.? )@<6 ;)/.<13-3 78 96:;/7<701;J7<54-7/ 随着我国汽车工业的不断发展, 组合机床在汽车 行业中的应用也越来越广, 产量也越来越大, 生产周期 要求越来越短。这就要求专机生产厂家, 对一些典型 的汽车零件的加工应有一套成熟的、 可靠的工艺方案, 以缩短设计周期, 为生产提供空间, 使企业跟上市场发 展的要求。 下面就近几年来的汽车后桥壳这一典型零件的专 机工艺方案加以介绍、 分析, 并希望与各位同行共同商 榷。 再次, 采用卧式单面移动工作台钻、 攻机床完成中 间琵琶孔端面上螺纹钻孔、 攻螺纹, 见图 K 。然后采用 卧式双面钻孔机床完成两端轴承孔端面上的螺纹底孔 加工, 见图 % 。 其次, 采用卧式双面精镗机床完成两端油封孔和 轴承孔的精加工, 见图 " 。
矿用汽车后桥壳断裂焊接工艺探讨与实践

1 3 0 3- 7矿 用汽 车后 桥断 裂的原 因及部 位分 析
11 后桥断裂的原因 .
() 1 工况条件差
歪矿 的采场路面质量极差 , 高低不平 , 而且急转弯 多 , 坡
1 一后桥壳 ; 半轴套管 2一
2 对后 桥断 裂焊修 的质量 要求
() 2 保证整个后桥的 同心度和直线 度 , 否则 就会影 响与 传动半轴 的配合精度 , 响传动 。 影 () 3 不允许改变后桥的结构尺 寸 , 因为后 桥还要与其 它 部件进行联接 , 如刹 车支座 、 悬挂缸支座等 。
3 采用的 工艺措 施
因为要进行焊接 的材质为 Z 3 , G 5 焊接性 能较差 , 而且还 要达到以上的质量要求 , 必须有新的工艺措施 才能保证 。 () 1 在断 口处 的半轴 套管 内镶 加强钢 套 , 如图 3所示 , 钢套的材质采用优质碳素结构 4 # , 与半 轴套管 的内壁 5钢 它 采用基孔制过盈配合 , 其过盈量为 00 3~ .8 m 用压力 .4 0 0 2 m, 机压装。镶加强钢套 的作用就在于支撑腔管 内壁 , 使之抗 弯 图 1 后桥壳与半轴套管整体结构 图 如图 1 图2所示 , 和 后桥壳 的两端都压装有细长 的半轴
( ) 口焊接后 的强度必须要高 于原强度 , 1断 因此必须 制 订新工艺才能达到此要求 , 并且在焊接处 以后不能再产生新
的裂纹。
度较大 , 因此行驶过程 中车辆颠簸较大 , 尤其是 在重 载急转 弯和上 、 下坡 时 , 产生巨大 的冲击 载荷 , 后桥 的冲击 较大 , 对
如后桥某部位一旦有微小裂纹, 就会出现裂纹迅速扩大的趋势。 () 2 结构方面的原因
桥壳后壳盖失效分析

图1㊀后壳盖开裂失效件分析测量故障件板厚为2.7~2.8mm,符合材料拉伸范围要求理论最小允许厚度1.98mm)㊂材料成分见表1,符合标准要P Cr Ni Cuɤ0.035ɤ0.1ɤ0.25ɤ0.0.010.01860.00340.002是焊接时焊渣飞溅到后壳盖表面,会在金属表面产生类似焊接的金相组织,并有一定深度的热影响区,降低后壳盖的强E-mail:576857534@㊂图2㊀球状颗粒附着壳盖表面沿断口试样横截面切取磨制金相试样,经3%硝酸酒精溶液腐蚀㊁清洗㊁干燥后,宏观照片如图3所示,焊缝㊁薄板的位置特征清晰可见㊂置于莱卡DMI5000M 金相显微镜下观察,断口处金相组织为铁素体+珠光体组织,裂纹两侧未见偏析㊁杂质㊁脱碳等现象㊂同时在金相试样上进行洛氏硬度测试,经沃博特洛氏硬度计检测,故障件的洛氏硬度为52HRB ,故障件金相组织和硬度均正常㊂图3㊀裂纹附近金相组织将断口试样经超声波清洗干燥后,置于TESCAN 扫描电子显微镜下观察,起裂区在内侧,为多点起裂,如图4所示㊂图4㊀断口14倍SEM 照片㊀㊀在起裂区未见明显的冶金缺陷,其形貌为准解理+撕裂,如图5所示㊂图5㊀起裂区800倍SEM 照片扩展区形貌为准解理+贝壳纹,如图6所示,为典型的疲劳断口特征㊂图6㊀扩展区1500倍SEM 照片从对故障件的分析结果可以看出,后壳盖属于疲劳断裂,但故障件本身除焊渣飞溅到表面之外,其他方面未见明显的质量缺陷,这就需要从后壳盖的设计及使用环境去判断引起本次失效的原因[2]㊂3 失效原因分析3.1㊀壳盖材料机械性能根据标准GB /T228.1 2010进行材料拉伸试验[3],如图7所示,试样厚度3mm ,宽度30mm ,材料下屈服强度为175MPa ,抗拉强度290MPa ,符合原材料供应商技术协议中定义的要求㊂图7㊀材料拉伸试样3.2㊀CAE 分析根据现在发布的行业标准‘QC /T533 1999㊀汽车驱动桥台架试验方法“中驱动桥桥壳垂直弯曲疲劳试验的加载方法,建立CAE 分析模型(图8),得到桥壳后壳盖开裂区域应力为38MPa (图9),壳盖材料屈服强度为175MPa ㊂整车道路试验是按标准负荷加载的,没有发生超载情况,同时桥壳垂直弯曲疲劳台架试验已通过验证[4],且没有出现后壳盖失效故障㊂因此从CAE 分析及台架试验结果判断,后壳盖不可能在只承受垂向力作用下发生疲劳断裂㊂图8㊀CAE分析图9㊀后壳盖应力图3.3㊀路谱采集及台架对标基于故障件㊁原材料机械性能及常用工况CAE 分析结果均未发现异常,有必要对样件的使用环境进行路谱采集,以便进一步查找失效原因㊂应变片贴在后壳盖失效位置(图10),90ʎ为整车X 方向,0ʎ为Y 方向,45ʎ为Z 方向,在试验场地测试开裂位置处的应力应变㊂实测结果表明90ʎ方向(即整车X向)应力应变最大,最大值达到244MPa ,95%道路工况开裂位置应力值为103MPa (图11)㊂图10㊀开裂位置贴应变片图11㊀道路测试应力值根据路谱采集结果,欲在台架上模拟道路试验受力来复制整车上的故障模式㊂将装配主减速器壳体的桥壳总成样件,按主减速器壳体朝上的状态安装在试验台架上(图12),同时在开裂位置贴应变片以监控台架试验工况后壳盖受力与道路试验基本一致㊂共测试3台样件,均出现桥壳后壳盖开裂,开裂位置与道路试验一致㊂对台架试验开裂件进行检测,金相组织㊁材料成分等均正常㊂图12㊀台架试验装置3.4㊀焊接对材料性能的影响文中提到故障件表面有附着焊接时,飞溅到后壳盖表面的焊渣㊂在供应商现场抽取后壳盖表面附着焊渣的样件进行硬度梯度检测,判断焊缝热影响区范围以及焊渣的影响[5]㊂将样件磨制成金相试样(图13),分别进行硬度检测:(1)焊缝热影响区分析:沿图13箭头1方向进行硬度梯度检测,每隔0.5mm 取一个检测点,硬度曲线如图14所示㊂在焊缝区域任取一个点为测试起点(坐标位置0点),距离起点1mm 位置处为焊缝区域,该区域硬度最大为188HB ㊂从位置1mm 点开始,硬度快速下降㊂距起点位置1~2mm 区域为焊接热影响最大的区域,最低硬度为116HB ;距起点位置2~6mm 区域硬度逐步上升,位置6mm 点硬度152HB ,接近母材硬度(ȡ150HB ),焊缝热影响区域在1~6mm 范围㊂本次故障件开裂区域距离焊缝10mm ,因此焊缝热影响区对本次失效基本关联㊂图13㊀抽检试样图14㊀焊缝热影响区硬度梯度(2)焊渣的影响:沿图13箭头2方向进行硬度梯度检测,每隔0.2mm 取一个检测点,硬度曲线如图15所示㊂在焊渣区域任取1点为测试起点(坐标位置0点),距离起点0.2mm 位置处为焊渣区域,该区域硬度最大321HB ㊂从位置0.2mm 点开始,硬度快速下降㊂距起点位置0.2~0.4mm 区域为焊渣热影响最大的区域,最低硬度为137HB ;距起点位置0.4~0.6mm 区域硬度逐步上升,位置0.6mm 点硬度152HB ,接近母材硬度(ȡ150HB ),焊渣热影响区域在0.2~0.6mm 范围㊂从故障件分析来看裂纹有沿焊渣扩展趋势,焊渣对本次故障可能会有一定的影响,但不是关键影响因素㊂图15㊀焊渣热影响区硬度梯度通过以上分析,导致失效的主要原因是道路试验工况整车X 方向作用力大,后壳盖承载能力不足,需要对壳盖的材料进行重新选型㊂4㊀解决措施及验证根据路谱采集的结果,后壳盖材料选择热轧板SAPH440,屈服强度不小于305MPa ,抗拉强度不小于440MPa ㊂按照图12方式进行台架验证,完成80万次循环后,检查后壳盖是否开裂㊂原状态试样在完成80万次台架循环,后壳盖出现开裂;新材料试样,完成80万次循环,后壳盖未开裂,继续进行台架试验至185次循环,试样无裂纹,试验停止㊂台架试验寿命至少提升1.3倍以上,新状态样件也顺利通过整车道路试验考核㊂5㊀结束语综上所述,后壳盖失效是在整车X 向作用力下,后壳盖强度不足引起的㊂在实际工作中,后壳盖通常与桥壳壳体一起组成总成件,按行业标准‘QC /T533 1999㊀汽车驱动桥台架试验方法“中驱动桥桥壳垂直弯曲疲劳试验进行验证,往往忽略了来自整车X 方向作用力的台架验证㊂本文阐述的后壳盖开裂是典型的失效案例,通过道路试验路谱采集和台架试验对标分析,可建立适用企业设计研发用的台架验证标准,为今后零部件开发提供理论依据,在设计初期就考虑到类似风险并规避,提高开发效率㊂参考文献:[1]刘惟信.汽车车桥设计[M].北京:清华大学出版社,2004.[2]李亚江.焊接冶金学[M].北京:机械工业出版社,2007.[3]刘春廷.材料力学性能[M].北京:化学工业出版社.2009.[4]邓开豪.汽车桥壳焊缝漏油原因分析及改进措施[J].装备制造技术,2008(4):131-132.[5]李晓丽,王俊杰,路强.汽车驱动桥后盖焊缝㊁渗油漏油原因分析及改进措施[J].汽车实用技术,2015(7):110-111,116.。
微型汽车后桥桥壳强度及模态分析

微型汽车后桥桥壳强度及模态分析作者:赵慧真杨浩来源:《时代汽车》 2018年第7期赵慧真1 杨浩 21. 中原工学院信息商务学院河南省郑州市4500072. 郑州精益达汽车零部件有限公司河南省郑州市450001摘要:以国产某微型汽车后桥桥壳为研究对象,运用HYPERWORKS 前处理软件 Hypermesh 建立有限元模型,按照汽车行业标准给定的条件进行加载分析,计算桥壳的静载力学性能。
同时对桥壳进行动力学模态分析,综合评判结构强度设计的合理性,通过此分析方法大大缩短了产品设计及验证周期,对产品的设计和开发有一定的指导意义。
关键词:驱动桥桥壳;静强度;刚度;模态分析1 引言驱动桥桥壳是汽车底盘上主要承载构件之一,根据驱动桥的结构形式可以分为非断开式和断开式两种 [1] ,对于微型车后桥开发,不仅节约企业开发成本,而且便于大批量生产,一般都设计成非断开式的桥壳,本文也是对该种形式的桥壳进行研究。
驱动后桥的功能主要是传递来自传动轴的扭矩,通过主减速器进行减速增扭的目的,并且改变动力传动的方向,从而提供动力驱动车轮的前进。
而驱动桥桥壳作为后桥壳体支撑部件,主要功能是承受来自车身的垂向载荷,汽车前进、制动过程中的前后载荷,以及车辆转弯过程中地面对汽车的侧向载荷。
汽车行驶过程中频繁来自三个方向的综合载荷作用,使得桥壳设计必须承受恶劣的载荷冲击 [2-3] 。
设计时候考虑桥壳的强度、刚度等特性。
台架试验及路试是桥壳结构合理性的最终评价手段,但是桥壳样件的制作、模具开模都需要周期及金钱,台架试验成本高、路试试验周期长,不利于产品的快速开发及市场投放[4] 。
CAE分析技术基于单元网格的虚拟仿真技术,采用强度理论,能够对桥壳结构各位置进行应力及变形分析,利于后续的修改及优化工作,对强度及刚度的提升有至关重要的作用,为企业争取时间及节约了大量金钱。
本文在此基础上以国产某款微型汽车后桥桥壳为例,建立了驱动后桥桥壳的完整网格模型,参考汽车行业标准QC/T533-1999《汽车驱动桥台架试验方法》对桥壳垂向载荷工况进行分析,计算桥壳的垂向刚度及强度,评判结构是否满足强度及刚度要求。
汽车后桥半轴断裂失效分析
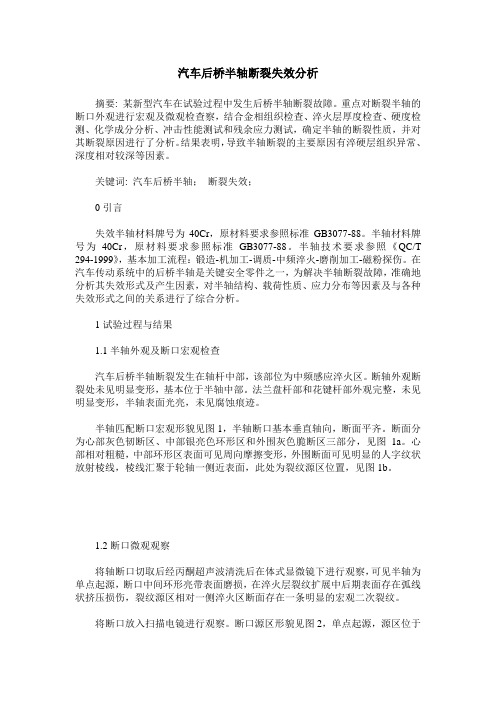
汽车后桥半轴断裂失效分析摘要: 某新型汽车在试验过程中发生后桥半轴断裂故障。
重点对断裂半轴的断口外观进行宏观及微观检查察,结合金相组织检查、淬火层厚度检查、硬度检测、化学成分分析、冲击性能测试和残余应力测试,确定半轴的断裂性质,并对其断裂原因进行了分析。
结果表明,导致半轴断裂的主要原因有淬硬层组织异常、深度相对较深等因素。
关键词: 汽车后桥半轴;断裂失效;0引言失效半轴材料牌号为40Cr,原材料要求参照标准GB3077-88。
半轴材料牌号为40Cr,原材料要求参照标准GB3077-88。
半轴技术要求参照《QC/T 294-1999》,基本加工流程:锻造-机加工-调质-中频淬火-磨削加工-磁粉探伤。
在汽车传动系统中的后桥半轴是关键安全零件之一,为解决半轴断裂故障,准确地分析其失效形式及产生因素,对半轴结构、载荷性质、应力分布等因素及与各种失效形式之间的关系进行了综合分析。
1试验过程与结果1.1半轴外观及断口宏观检查汽车后桥半轴断裂发生在轴杆中部,该部位为中频感应淬火区。
断轴外观断裂处未见明显变形,基本位于半轴中部。
法兰盘杆部和花键杆部外观完整,未见明显变形,半轴表面光亮,未见腐蚀痕迹。
半轴匹配断口宏观形貌见图1,半轴断口基本垂直轴向,断面平齐。
断面分为心部灰色韧断区、中部银亮色环形区和外围灰色脆断区三部分,见图1a。
心部相对粗糙,中部环形区表面可见周向摩擦变形,外围断面可见明显的人字纹状放射棱线,棱线汇聚于轮轴一侧近表面,此处为裂纹源区位置,见图1b。
1.2断口微观观察将轴断口切取后经丙酮超声波清洗后在体式显微镜下进行观察,可见半轴为单点起源,断口中间环形亮带表面磨损,在淬火层裂纹扩展中后期表面存在弧线状挤压损伤,裂纹源区相对一侧淬火区断面存在一条明显的宏观二次裂纹。
将断口放入扫描电镜进行观察。
断口源区形貌见图2,单点起源,源区位于半轴表面,源区未见材质缺陷,靠近源区为沿晶+韧窝断裂特征,扩展阶段以准解理+韧窝断裂特征为主。
矿用桥壳轴头环缝断裂情况分析

技术创新15矿用桥壳轴头环缝断裂精况分析◊山东蓬翔汽车有限公司鲍文勋王红强宋小会崔岩岩本文通过对市场返回的断裂桥壳进行分析,发现断裂与焊缝的根部熔透情况密切相关。
通过改进焊缝根部间隙设计及设备更新彻底解决了矿用桥壳断裂问题。
矿用车桥匹配矿用车,具备承载大,行驶路况差等特点,矿用车桥多采用铸钢本体,壁厚较厚,焊接性能相对较差。
矿用车桥的薄弱部位为桥壳本体与轴头对接焊缝,偶尔会出现开裂情况。
1断裂情况分析(1)断裂位置位于轴头环缝近中心位置(见图1)O图1断裂切片图2根部切片(2)裂纹源在轴头环缝坡口根部(靠近轴头侧根部未熔合)(见图2)o(3)断裂类型应该为根部未熔合形成尖锐缺口造成轴头环缝疲劳强度不足弓I起的断裂。
另外,轴头环缝根部没有和衬环熔合在一起,根部熔合线宽度为3mm(理论根部间隙4 mm,加丘求两侧熔深不小于1mm,根部舲駅度应大于6mm),证明焊缝根部的焊透、熔合IW况不是很好。
2根部未熔合、未焊透原因分析2.1操作者两侧轴头同时焊接,一名操作者难以保证时刻观察焊丝对中情况,存在偏弧造成未熔合的风险。
2.2设备设备比较老旧,不具备参数提前预设功能,打底、填充、盖面焊接参数难以调节,影响焊接质量。
2.3工件(1)本体为铸钢件,铸钢件的特点(含碳量高、铸态组织粗大、成分偏析不均匀、杂质含量较多、脱氧不完全、容易出现气孑歸松缺陷)造删®ft相对施%(2)壁厚超过30mm。
坡口根部间隙4mm,坡口角度30。
造成以下问题:一是焊枪受喷嘴限制难以深入焊缝坡口内部,容易造成焊接参数不稳定,气体保护效果变差,影响焊接质量;二是壁厚较厚,坡口角度过小,受电弧扩散角影响,焊接电弧难以达到焊缝根部,无法保证坡口根部母材的熔化,造成填充金属与根部母材假熔合,影响焊缝强度;三是焊缝深宽比大于1,铸钢件焊接杂质较多,容易出现结晶裂纹%(3)衬环与本体要求贴合紧密,最大间隙最好不超过1 mm,尤其是桥壳下方必须贴合紧密。
车后桥壳的分析研究1

车后桥壳的分析研究江铃汽车公司技术中心蔡志武史英明2005-5-13e-works 本文针对某型车的引进吸收开发过程中,其海南路试发现后桥存在的局部强度不足的情况,用ANSYS有限元分析系统对其后桥壳进行了计算分析比较,并优化该产品的设计。
为了适应激烈的市场竞争,满足用户需求,企业需要开发出高品质、低价位的新产品。
为此,CAE技术在汽车产品开发过程中越来越多地得到开发人员的应用。
针对某型车的引进吸收开发过程中,其海南路试发现后桥存在的局部强度不足的情况,用ANSYS有限元分析系统对其后桥壳进行了计算分析比较,并优化该产品的设计。
随着汽车对安全、节能、环保的不断重视,汽车车后桥作为整车的一个关键部件,其产品的质量对整车的安全使用及整车性能的影响是非常大的,因而对汽车车后桥进行有效的优化设计计算是非常必要的。
本文介绍了有限元方法对某型车后桥壳的分析研究,建立了车后桥壳的有限元计算模型,并进行了多方案的模型计算分析比较,指出了其结构不足,提出了改进建议,为进一步优化设计提供了重要理论依据。
建立后桥壳的有限元模型根据该车后桥结构特点,传统的车桥有限元简化分析一般将重点集中于桥壳分析,该桥壳是钢板焊接式,由两根主桥壳对焊,中段两侧焊有四块三角形板,中间两端与桥后盖及主减速器壳连接固定。
一般其强度问题点发生的部位如图1。
图1 焊接桥壳常见的高应力响应部位本桥壳的G、H点即是平衡杆座板焊接位的应力集中问题,E点处在中间相对水平缓的过度部位,该处往往开大伞齿轮安装切槽或法篮螺孔,应力响应也较高,A、B点的高应力响应对应最大侧向载荷工作情况发生。
载荷与约束首先对后桥所受载荷进行分析,本分析考虑了两种工作载荷:一种桥负荷,分别作用在板簧支座与桥壳联接位;另一种载荷为平衡杆在车身发生倾斜等情况时产生的抗力。
图2 平衡杆模型与抗力图3 车身不发生倾斜时桥壳应力响应分布计算结果分析通过FEM对平衡杆模型有无作用力计算比较,得出:平衡杆支反力对桥壳体的影响主要体现在桥壳弯矩的加大。
客车后桥壳半轴套管失效分析
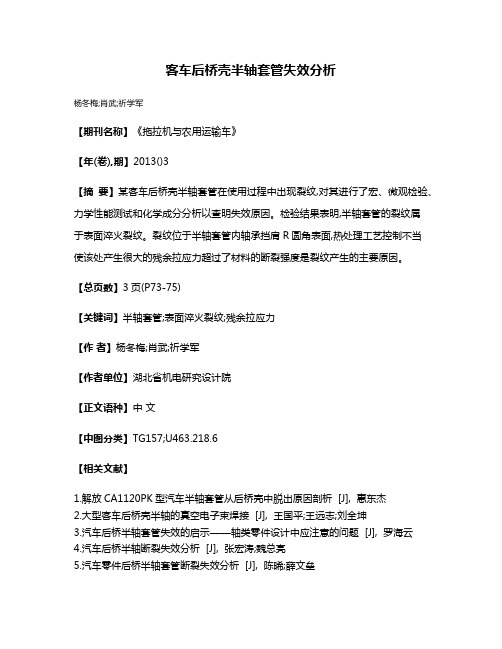
客车后桥壳半轴套管失效分析
杨冬梅;肖武;祈学军
【期刊名称】《拖拉机与农用运输车》
【年(卷),期】2013()3
【摘要】某客车后桥壳半轴套管在使用过程中出现裂纹,对其进行了宏、微观检验、力学性能测试和化学成分分析以查明失效原因。
检验结果表明,半轴套管的裂纹属
于表面淬火裂纹。
裂纹位于半轴套管内轴承挡肩R圆角表面,热处理工艺控制不当
使该处产生很大的残余拉应力超过了材料的断裂强度是裂纹产生的主要原因。
【总页数】3页(P73-75)
【关键词】半轴套管;表面淬火裂纹;残余拉应力
【作者】杨冬梅;肖武;祈学军
【作者单位】湖北省机电研究设计院
【正文语种】中文
【中图分类】TG157;U463.218.6
【相关文献】
1.解放CA1120PK型汽车半轴套管从后桥壳中脱出原因剖析 [J], 惠东杰
2.大型客车后桥壳半轴的真空电子束焊接 [J], 王国平;王远志;刘全坤
3.汽车后桥半轴套管失效的启示——轴类零件设计中应注意的问题 [J], 罗海云
4.汽车后桥半轴断裂失效分析 [J], 张宏涛;魏总亮
5.汽车零件后桥半轴套管断裂失效分析 [J], 陈晞;薛文垒
因版权原因,仅展示原文概要,查看原文内容请购买。
汽车差速器壳断裂失效分析

汽车差速器壳断裂失效分析黄平辉;余显忠;揭钢;万雄飞【摘要】针对某汽车驱动桥差速器壳体断裂情况,首先利用材料试验检验分析了该驱动桥差速器壳体所采用球墨铸铁材料的金相组织和铸造等级,然后根据<Q/T 543-1999汽车驱动桥台架试验评价指标>试验标准,采用有限元分析方法建立了该差速器壳体的有限元模型,利用有限元分析软件ABAQUS进行差速器壳体的静强度分析,得到了该差速器壳的应力分布情况和应力集中部位.通过与样件失效部位对比分析,确定了该差速器壳体断裂失效的原因,为改进设计提供了理论依据.【期刊名称】《汽车技术》【年(卷),期】2010(000)002【总页数】4页(P54-57)【关键词】差速器;壳体;失效;有限元【作者】黄平辉;余显忠;揭钢;万雄飞【作者单位】江西江铃底盘股份有限公司;江西江铃底盘股份有限公司;华中科技大学数字制造装备与技术国家重点实验室;江西江铃底盘股份有限公司;江西江铃底盘股份有限公司【正文语种】中文【中图分类】U463.218+.41 前言某装备差速器的样车在换挡循环专项试验进行到4 251 km及在进行发动机标定试验时,均发生了驱动桥差速器壳断裂失效现象。
因此,必须对差速器壳进行断裂失效模式分析、材料试验分析和力学性能分析,以改善汽车驱动桥差速器壳的设计。
本文针对驱动桥差速器壳断裂失效样件的失效模式以及差速器壳材料的金相组织和铸造等级等进行了分析。
采用有限元分析方法建立了差速器壳有限元模型,进行了工作状态下的静强度分析,得到了该差速器壳的应力分布情况和应力集中部位,通过与样件失效部位对比分析,确定了该差速器壳断裂失效的原因。
2 差速器壳断裂失效模式分析图1为差速器壳断裂失效断面照片。
从图1a的断裂失效断面可看出,差速器壳一字轴销孔的失效模式是由于差速器壳侧连接壳臂发生弯曲疲劳开裂后引起的断裂失效,因实际零件壳臂圆弧半径R=20 mm,所以初步判断开裂处圆角尺寸偏小。
后桥壳体断裂的原因

后桥壳体断裂的原因
解德金
【期刊名称】《农业科技与装备》
【年(卷),期】1998(000)004
【摘要】后桥壳体断裂的原因解德金吉林省伊通县农机推广站(130700一台改装的推土机正在推土,不知是什么原因连续脱轨,这次机手不愿再去卸掉履带板重新挂接,想采取前走后倒的方法复轨。
正往前走啃轨转向时,突然听到右侧后桥壳发出“咔咔”几声响声,机手急忙停车,下车...
【总页数】1页(P16-16)
【作者】解德金
【作者单位】吉林省伊通县农机推广站
【正文语种】中文
【中图分类】S232
【相关文献】
1.皮卡绕八字试验半浮式后桥半轴断裂原因分析 [J], 付荣鑫;吴国华
2.W4—60挖掘机后桥壳端部断裂的原因与修复 [J], 谭业发;陆明
3.半浮式后桥半轴断裂原因分析 [J], 姜致强;万熊飞;谢建林
4.东方红—75拖拉机后桥壳体损坏的原因及预防 [J], 张广成
5.重型载货汽车后桥主动锥齿轮断裂原因分析及改进措施 [J], 金荣植
因版权原因,仅展示原文概要,查看原文内容请购买。
某微卡后桥壳焊缝开裂问题处理

某微卡后桥壳焊缝开裂问题处理
张翠
【期刊名称】《汽车零部件》
【年(卷),期】2022()4
【摘要】桥壳是安装主减速器、差速器、半轴、轮毂和悬架的基础件,起着支承并保护主减速器、差速器和半轴的作用。
文中针对桥壳半轴套管焊缝开裂问题,对故障问题从整车承载、使用路况、样件失效模式等方面进行了全面系统排查;对故障件进行了深入分析,并通过故障再现确认了故障原因;最后提出了整改措施并通过效果验证。
结果表明:熔深率均可达到100%,整改后的样件满足整车使用需求,从而解决了环焊缝开裂问题。
【总页数】4页(P82-85)
【作者】张翠
【作者单位】安徽江淮汽车集团股份有限公司商用车研究院
【正文语种】中文
【中图分类】TH163
【相关文献】
1.汽车后桥壳开裂的分析与改进
2.基于CAE分析的微卡后桥主减壳优化设计
3.某车型驱动桥后桥壳开裂分析
4.905AK后桥焊缝开裂原因和解决方法
5.座圈与炉壳间焊缝开裂原因分析及处理对策
因版权原因,仅展示原文概要,查看原文内容请购买。
汽车后桥故障的诊断及排除2例

汽车后桥故障的诊断及排除2例
刘宏;郭秀波
【期刊名称】《农机使用与维修》
【年(卷),期】2005(000)002
【摘要】1.后半轴断裂 (1)汽车行驶时后半轴易断,且易断半轴的那一侧轮胎有锯齿形磨损。
【总页数】2页(P38-39)
【作者】刘宏;郭秀波
【作者单位】黑龙江省拜泉县农机技术推广中心;黑龙江省桦南县农业机械化学校【正文语种】中文
【中图分类】S229.1
【相关文献】
1.东风EQ1118GA汽车后桥油封损坏和齿油变质故障排除一例 [J], 程卫星
2.帕杰罗汽车后桥冒白烟故障排除1例 [J], 史宣琳
3.汽车后桥故障问题的辨识及有效排除方法研究 [J], 石涛
4.汽车后桥故障的诊断及排除 [J], 刘宏;高雪梅
5.诊断Windows Server 2003中IPsec问题的9种方法 IPsec的故障排除一般就是验证过程的故障排除 [J], Orin;Thomas;徐瑾(译)
因版权原因,仅展示原文概要,查看原文内容请购买。
铁路客车车辆导流罩支架焊缝断裂失效分析
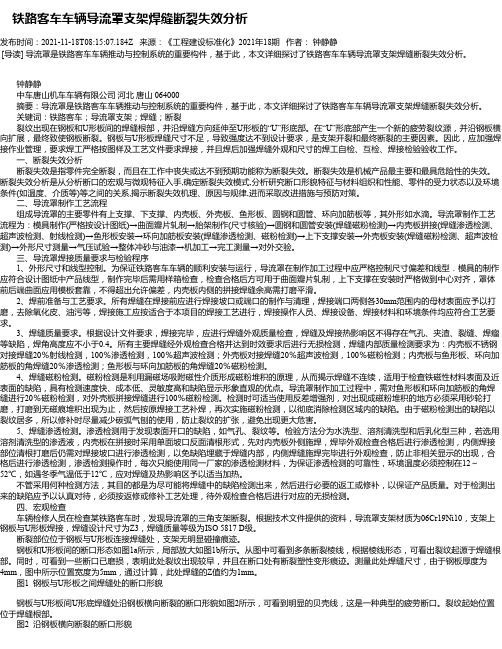
铁路客车车辆导流罩支架焊缝断裂失效分析发布时间:2021-11-18T08:15:07.184Z 来源:《工程建设标准化》2021年18期作者:钟静静[导读] 导流罩是铁路客车车辆推动与控制系统的重要构件,基于此,本文详细探讨了铁路客车车辆导流罩支架焊缝断裂失效分析。
钟静静中车唐山机车车辆有限公司河北唐山 064000摘要:导流罩是铁路客车车辆推动与控制系统的重要构件,基于此,本文详细探讨了铁路客车车辆导流罩支架焊缝断裂失效分析。
关键词:铁路客车;导流罩支架;焊缝;断裂裂纹出现在钢板和U形板间的焊缝根部,并沿焊缝方向延伸至U形板的“U”形底部。
在“U”形底部产生一个新的疲劳裂纹源,并沿钢板横向扩展,最终致使钢板断裂。
钢板与U形板焊缝尺寸不足,导致强度达不到设计要求,是支架开裂和最终断裂的主要因素。
因此,应加强焊接作业管理,要求焊工严格按图样及工艺文件要求焊接,并且焊后加强焊缝外观和尺寸的焊工自检、互检、焊接检验验收工作。
一、断裂失效分析断裂失效是指零件完全断裂,而且在工作中丧失或达不到预期功能称为断裂失效。
断裂失效是机械产品最主要和最具危险性的失效。
断裂失效分析是从分析断口的宏观与微观特征入手,确定断裂失效模式,分析研究断口形貌特征与材料组织和性能、零件的受力状态以及环境条件(如温度、介质等)等之间的关系,揭示断裂失效机理、原因与规律,进而采取改进措施与预防对策。
二、导流罩制作工艺流程组成导流罩的主要零件有上支撑、下支撑、内壳板、外壳板、鱼形板、圆钢和圆管、环向加筋板等,其外形如水滴。
导流罩制作工艺流程为:模具制作(严格按设计图纸)→曲面瓣片轧制→胎架制作(尺寸核验)→圆钢和圆管安装(焊缝磁粉检测)→内壳板拼接(焊缝渗透检测、超声波检测、射线检测)→鱼形板安装→环向加筋板安装(焊缝渗透检测、磁粉检测)→上下支撑安装→外壳板安装(焊缝磁粉检测、超声波检测)→外形尺寸测量→气压试验→整体冲砂与油漆→机加工→完工测量→对外交验。
- 1、下载文档前请自行甄别文档内容的完整性,平台不提供额外的编辑、内容补充、找答案等附加服务。
- 2、"仅部分预览"的文档,不可在线预览部分如存在完整性等问题,可反馈申请退款(可完整预览的文档不适用该条件!)。
- 3、如文档侵犯您的权益,请联系客服反馈,我们会尽快为您处理(人工客服工作时间:9:00-18:30)。
图 4 最大动载应力分析:180 MP a 图 5 最大牵引力应力分析:120 MP a
收稿日期:2009- 07- 25 作者简介: 韦 波(1976—),男,广西柳州人,工程师,主要负责传动系统及零部件设计。
140
《装备制造技术》2009 年第 10 期
2 改进方案
2.1 增焊加强板的方案 后桥包增加开焊接坡口的工艺更改,要求供应商新增相
!!!!!!!!!!!!!!!!!!!!!!!!!!!!!!!!!!!!!!!!!!!!!!!
(上接第 120 页)
Dis cus s ia n On Us ing Concurre nt Engine e r In The De ve lopme nt P roce s s Of La rge S ta mping Of Ca rs
(3)加强板焊缝与桥壳纵焊缝距离为 15 mm,考虑桥壳纵 焊缝为受应力较大区域,加强板焊缝在焊接加工时,必须与之 保持一定距离,不能对纵焊缝造成损坏。
3 结束语
经过海南试验场可靠性道路试验验证,加强板焊接改进 方案的样件,能满足 26 000 km 坏路里程的要求(公司试验要 求),证明该方案有效并可行地解决了 N300 型客车桥壳断裂 的问题。
桥包开坡口焊接之后的切片结构(切片照片见图 9)。
15
R8
图 10 加强板(每桥壳增加 2 件,左右各 1 件) 2.2 后桥壳焊接部位漏油的分析
加强板采用材料为 SAPH370,t = 2。加强板上和桥壳轴 管以及桥包的贴合部位应与相应部位相切,以保证焊接时两 者不产生离空,保证焊缝质量;同时根据桥壳应力的分析(图 4、图 5、图 6),得知:加强板所焊接到桥壳上的位置,均是桥壳 应力较大的部位,桥壳母材对焊接的伤害敏感性很强,如焊接 工艺参数不当,将会导致桥壳的焊接部位出现裂纹最终出现 漏油(后桥齿轮油渗漏)。采用加强板方案的后桥壳,在随后的 海南可靠性路试中,多次出现漏油的质量问题,桥壳漏油照片 如图 11。
参考文献: [1] 《汽车工程手册》编辑委员会. 汽车工程手册 设计篇[M]. 北京:人
民交通出版社,2001.
An Ana lys is a nd Improve me nt of Re a r Axle Ca s e Fra cture in N300 Ve hicle
WEI Bo (Technical Development Center, SAIC- GM- Wuling Automobile Co., Ltd., Liuzhou Gunagxi 545007,China)
图 1 后桥壳断裂照片
1 原因分析
图 2 断口照片
足使用要求的。 (4)桥壳与轴管的连接部位强度分析。发生断裂的桥壳与
轴管的连接部位(B 处,见图 3)桥管外径 D = 73.5 mm,桥管内 径 D = 63.5mm,抗弯系数 Ww =17 255.7 mm3;抗扭系数 Wn = 34511.3 mm3,则该部位相关应力比 A 处要小,那么 B 处的强 度设计也是满足使用要求的。 1.1.2 CAE 应力分析
Equipment Manufactring Technology No.10,2009
N300 型客车后桥壳断裂的分析和改进
韦波
(上汽通用五菱汽车股份有限公司 技术中心,广西 柳州 545007)
摘要:针对 N300 客车在海南汽车试验场可靠性道路试验中桥壳断裂的问题,应用理论计算和 CAE 分析软件对桥壳强度进行了分 析,并对桥壳样件进行焊接工艺检查和分析,明确了断裂原因和提出改进方案,说明了实施改进方案的相关要求。 关键词:后桥壳;断裂;分析;改进
(1)加强板 R4 mm 的圆角区域,不进行焊接,焊缝从离开 圆角 14 mm 处再开始起焊,考虑避免圆角处焊接应力集中;
(2)加强板起到连接桥包和轴管的作用,加强板焊缝和桥 包与轴管的环焊缝共同承受桥壳轴向的拉应力影响,考虑尽
量减少焊接对桥壳和轴管母材的损坏,经过焊接工艺验证后, 加强板焊缝宽度确定为 3 mm,且分三段与桥壳相连;
142
前后 4 处 (左右对称)
图 12 加强板焊接原方案
135
141
Equipment Manufactring Technology No.10,2009
3 18 135(前后 2 处)
3 2×20(20) 135(前后 2 处)
45° 15°
15
6.3
14
40
纵焊缝
图 13 加强板焊接改进方案 2.3 焊接方案的工艺要求
1.2 制造工艺分析 对失效件断口进行查看和分析,并将断口切开抛光后在
显微镜下观察焊缝熔合结构和位置,最终确认为在桥壳油箱 与轴管接合处的桥包(见图 7)没有熔透,导致耐久性能达不到 实际坏路里程要求而出现断裂失效,具体分析如下:
后桥壳
桥包
套管
环焊处
桥包
套管
桥包Leabharlann 套管单 V 形波口
嵌套
V 形波口
A
B
图 7 制造工艺分析示意图
参照《汽车工程手册·设计篇》相关章节内容,进行桥壳设 计强度校核,校核部位在桥壳截面最小处(如 A 处,见图 3)。
A
B
图 3 桥壳校核部位示意图
(1)A 处尺寸。桥管外径 D = 65mm,桥管内径 D = 55mm, 抗弯系数 Ww=13 133.7 mm3;抗扭系数 Wn = 26 267.3 mm3;
Abs tract:Static strength of the rear axle case was calculated and examined by using the CAE software, and the welding procedure of case sample was confirmed and analyzed. So an improved solution of reinforced bracket and some requirements of that was proposed. Key words :rear axle case;fracture;analysis;improve
图 11 焊缝处出现漏油 针对上述问题,从焊接工艺等方面进行分析,制订和更改 了加强板焊接到桥壳上的位置参数和焊接参数,参数更改前 后的对比见图 12 和图 13。
C 40
R4
45
C
130
图 8 桥包未焊透,形 成的小缝隙空间
图 9 桥包焊透,没有小缝隙空间
4×18 135
前后两处
(左右对称)
4×25
图 7 中 A 状态为与断裂的后桥壳对应的实际结构,由于 桥包(油箱)处端口没有打磨倒角(即开焊接坡口),最终形成 的焊接熔池金属不能完全贯穿整个桥包板厚,故导致存在有 小间隙空间(缝隙),这些缝隙将成为耐久试验过程中应力集 中的疲劳源(如图 8);在可靠性路试过程中,缝隙受到应力的 不断作用,将逐渐扩大成为裂纹,最终导致桥壳断裂。
(2)计算结果数据。最大牵引力时的应力(合成应力) σaq = 118.3MPa;最大制动时的应力(合成应力) σaz = 85.7MPa;最大 动载应力(动载应力) σd = 173.4 MPa(动载系数 δ = 2.5)。
(3)桥壳轴管设计强度分析。桥壳轴管材料为 20#,其材 料强度 σs = 245 MPa;由此安全系数计算为 1.41;根据《重型 汽车结构现代设计》 中,桥壳安全系数推荐值:当 σs / σb = 0.4~0.6 时,n = 1.2~1.5;当 σs / σb >0.6 时,n = 1.4~1.8(现 材料 20# 钢,σs / σb = 0.628),可见 N300 的桥壳强度设计是满
中图分类号:U463.218+.5
文献标识码:B
文章编号:1672-545X(2009)10-0140-03
N300 型客车 OTS 阶段样车在海南汽车试验场进行的 26 000 km 耐久性道路试验中,曾数次出现后桥壳断裂的问 题。断裂的具体位置,均出现在桥壳油箱与轴管接合的焊缝 处,整个焊缝处被撕裂,半轴轴管与桥壳(油箱壳)完全分离, 试验车辆不能行驶,故障情况如图 1、图 2 所示。
B 状态为开坡口的设计,桥包开了焊接坡口(倒角),坡口 有利于提高桥包板厚方向的焊透程度,使焊缝贯穿整个板厚 区域。采用该设计的桥壳样件已顺利通过海南可靠性路试 (26 000 km 全坏路),未出现断裂的试验故障反馈,证明桥包 开焊接坡口的设计,能提高桥壳环焊缝的焊接质量,并满足车 辆实际使用要求的。
为验证理论强度计算的正确性,采用 CAE 分析软件对整 个桥壳进行分析,根据 CAE 分析的结果,与上述理论强度计 算结果符合;各工况下桥壳出现最大应力位置都不是油箱与 轴管接合处,这就排除了由于设计强度不足导致桥壳与轴管 结合处断裂的可能性。
CAE 分析具体数据如下(图 4~图 6)。
1.1 设计分析 1.1.1 理论强度计算
关设备,并对桥壳焊接工艺路线进行调整。考虑到目前暂不具 体相关条件,不能立刻实施工艺更改;经过讨论和研究后,决 定 N300 后桥壳改进的方案(提高桥壳强度)不采用桥包增开 焊接坡口的方案;根据实际经验,采用在桥壳油箱(桥包)与轴 管接合焊缝处的下方,增焊加强板的方案(详见图 10)。
图 6 最大制动时应力分析 81 MP a
LIU Guo- lin (Technology Center of Shanghai General Motors Wuling ,Liuzhou Guangxi 545007,China)
Abs tract: Strengths and weakness of using concurrent engineering (CE) and sequential engineering (SE) in the development process of large stamping parts for cars are compared, and the application and benefit of concurrent engineering in the development process of large stamping parts for cars is discussed in the article. Key words : concurrent engineering ; cars ; stamping parts ; application