分割式热泵精馏的理论分析与实验探讨
探讨甲醇热泵精馏新工艺
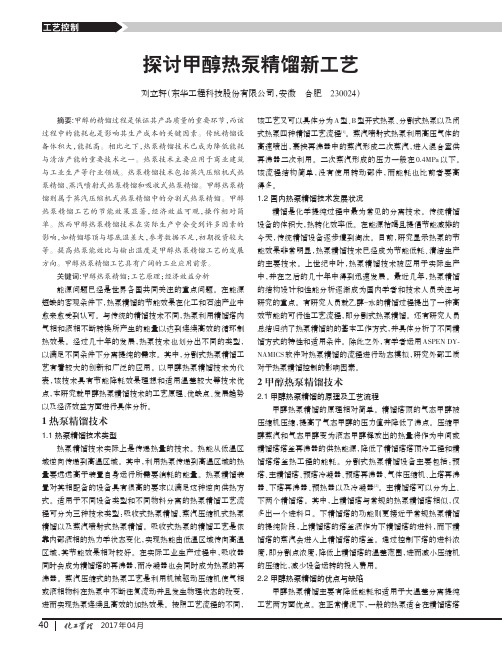
2017年04月探讨甲醇热泵精馏新工艺刘立轩(东华工程科技股份有限公司,安徽合肥230024)摘要:甲醇的精馏过程是保证其产品质量的重要环节,而该过程中的能耗也是影响其生产成本的关键因素。
传统精馏设备体积大,能耗高。
相比之下,热泵精馏技术已成为降低能耗与清洁产能的重要技术之一。
热泵技术主要应用于商业建筑与工业生产等行业领域。
热泵精馏技术包括蒸汽压缩机式热泵精馏、蒸汽喷射式热泵精馏和吸收式热泵精馏。
甲醇热泵精馏则属于蒸汽压缩机式热泵精馏中的分割式热泵精馏。
甲醇热泵精馏工艺的节能效果显著,经济效益可观,操作相对简单。
然而甲醇热泵精馏技术在实际生产中会受到许多因素的影响,如精馏塔顶与塔底温差大,参考数据不足,初期投资较大等。
提高热泵能效比与输出温度是甲醇热泵精馏工艺的发展方向。
甲醇热泵精馏工艺具有广阔的工业应用前景。
关键词:甲醇热泵精馏;工艺原理;经济效益分析能源问题已经是世界各国共同关注的重点问题。
在能源短缺的客观条件下,热泵精馏的节能效果在化工和石油产业中愈来愈受到认可。
与传统的精馏技术不同,热泵利用精馏塔内气相和液相不断转换所产生的能量以达到连续高效的循环制热效果。
经过几十年的发展,热泵技术也划分出不同的类型,以满足不同条件下分离提纯的需求。
其中,分割式热泵精馏工艺有着较大的创新和广泛的应用。
以甲醇热泵精馏技术为代表,该技术具有节能降耗效果理想和适用温差较大等技术优点,本研究就甲醇热泵精馏技术的工艺原理、优缺点、发展趋势以及经济效益方面进行具体分析。
1热泵精馏技术1.1热泵精馏技术类型热泵精馏技术实际上是传递热量的技术。
热能从低温区域逆向传递到高温区域。
其中,利用热泵传递到高温区域的热量要远远高于装置自身运行所需要消耗的能量。
热泵精馏装置对其相配备的设备具有很高的要求以满足这种逆向供热方式。
适用于不同设备类型和不同物料分离的热泵精馏工艺流程可分为三种技术类型:吸收式热泵精馏、蒸汽压缩机式热泵精馏以及蒸汽喷射式热泵精馏。
热泵精馏流程构建策略及应用研究

热泵精馏流程构建策略及应用研究热泵精馏是利用外部能源和热力作用,利用再循环升温,将混合溶液中的混合物分离出来的一种分离技术。
热泵精馏是在现代分离与精炼和反应的技术中,是由于其特定的优势而被广泛采用的一种技术。
热泵精馏技术在化学工业及石油、煤炭等行业中的应用日渐广泛,数量表现出显著的增长趋势,可以有效地提高精制系统的工艺性能,减少生产成本,是精制过程中重要的技术设备。
因此,热泵精馏是一种非常重要的技术,可以构建系统工艺,实现节能减排。
一般来说,热泵精馏系统由混合溶液泵、精馏塔、再循环热源、再循环驱动和再循环热源控制系统组成。
首先,混合液由混合溶液泵从精馏塔底层向顶层进行循环,使物料从塔底层到顶层形成自上而下的流动。
然后,再循环热源从热源器件中取出热量,将热量传递到混合液中,使混合物分离。
在再循环热源控制系统中,采用调节热源器件以控制混合液温度,实现热源驱动和控制,实现高效分离。
在构建热泵精馏系统的过程中,要考虑的因素很多,包括:热源温度、压力、体积等,热源介质种类、热源器件种类、热源驱动器件种类、热源驱动系统控制参数等。
热源驱动系统可以针对不同的物料进行定制化设计,以实现最佳的分离效果。
此外,为了实现热泵精馏系统的最佳性能,还需考虑到精馏塔的结构系数、质量流率、再循环量,以及热源系统内的物料冷却性能,系统中的气体种类等因素。
其中,精馏塔的结构系数可通过实验测定,再循环量可以通过热力学分析来确定,而物料冷却性能则可以通过流体力学分析来确定。
至于系统内的气体种类,需要考虑到物料的性质,以及操作及安全等因素,确定合理的搅拌方式和环境条件。
此外,热泵精馏技术的应用不仅仅局限于精馏,还可以用于各种分离与精炼、反应、传质、材料合成等工艺中。
例如,热泵精馏可以应用于收率高的反应工艺,如氧化、水解、脱氢、氯化等反应;也可以应用于有机结晶技术,涉及到溶剂蒸馏、溶剂分离、有机溶剂精馏等;另外,热泵精馏也可以应用于硅和稀土精炼技术、油井抽油技术、提纯金属材料合成技术等工艺中。
分割式酒精精馏热泵的研究

第31卷第8期 1997年8月 西 安 交 通 大 学 学 报JOURNAL OF XIøAN JIA OTONG U NIV ERSIT Y Vo l.31 №8 Aug.1997分割式酒精精馏热泵的研究李 珊 王 黎 胡袁春(西安交通大学,710049,西安)摘要 根据酒精-水相平衡的特点,设计出用于酒精精馏的分割式流程,使得原来因塔顶与塔底温差过大而不能应用的压缩式热泵得以应用.计算表明,此时的热力学效率比常规精馏提高82%.关键词 精馏 相平衡 分割式热泵中国图书资料分类法分类号 T K11.114目前,液体混合物的分离仍广泛采用精馏的方法.由于精馏过程是在塔底加热、塔顶取热、过程的不可逆性强和过程的热效率低(一般只有3%~5%,甚至只有千分之几),绝大部分热能被冷却水带走,变成无用的低位能排入环境.对酒精厂而言,精馏的能耗占生产总能耗的60%~70%.因此,降低精馏过程的能耗、提高其热力学效率,是酒精厂节能的重要内容[1~2].提高精馏热效率的方法多种多样,例如采取增设中间再沸器和冷凝器、多效精馏、热偶精馏或热泵精馏等,应该根据物料的具体性能因地制宜地选用、组合和配置.本文巧妙地利用酒精-水相平衡的特点,提出一种用分割式热泵进行酒精精馏的流程.并通过实例计算表明,此时可比常规酒精精馏的热效率提高82%,节能效果显著.1 分割式酒精-水热泵精馏流程的设计一般压缩式热泵精馏流程适用于塔顶与塔底的温差不超过10℃,温差过大则消耗压缩功太多.酒精-水精馏时塔顶、塔底温差高达21℃,一般压缩式热泵精馏流程(图1)不适用,而应设计新的流程.对酒精-水系统的相平衡关系进行分析可以看出(图2),当液相中乙醇含量小于0.4、相应的气相组成小于0.6时,溶液的相对挥发度较大.此时用不大的回流比和不多的塔板数即可达到分离酒精与水的目的.但当溶液组成大于0.4时,溶液的相对挥发度逐渐减小;当产品浓度接近恒沸点时,常规精馏为了保证产品质量,其回流比一般取3.5~4,理论板数精馏段为20~22块,提馏段为4~5块(实际生产中分别用到34~38块和8~10块),即需要用较大的回收到日期:1995-11-09. 李 珊:女,1937年2月生,化学工程学院化学工程系,副教授.图2 酒精-图水相平衡关系1 压缩式热泵精馏流程图3 分割式酒精精馏热泵原理图流比和较多的塔板数.针对上述图相特性,作者提出采用分割式热泵流程(图3)进行酒精精馏.其关键是将精馏装置分割为上、下两塔,使下塔出口的气相组成小于0.6,因而可以取较小的回流比和塔板数.如取回流比0.4~0.6时,下塔上升的蒸汽量仅为(1.4~1.6)D ,D 为馏出液量,单位是kmol /h .与此同时,上塔再沸器的釜液组成可以提高到0.25,相应沸点为82.3℃,则上塔的塔顶、塔底温差仅为3.9℃,符合采用压缩式热泵的有利范围.其过程中:下塔由蒸汽加热(回流比取为0.4~0.6),使塔顶蒸汽气相的组成小于0.6后,进入上塔.上塔回流比及塔板数与常规塔相同,其塔顶蒸汽(组成接近恒沸点)进入压缩机增压并提高温度后去上塔再沸器作为热源.其冷凝液的一部分回流到上塔,另一部分作为产品导出.而上塔釜液经上塔再沸器后组成为0.25左右,引入下塔作为回流液.对于原料液的加入位置,应根据进料的组成具体计算确定(可能在上塔或下塔某处).2 精馏过程的热力学效率计算[3,4]精馏过程的热力学效率G 等于过程所需最小能耗E min 与过程实际有效能耗E 之比G =E min /E (1)94西安交通大学学报第31卷2.1 过程最小有效能耗E m in酒精精馏均为常压操作,此时可假定气相为理想状态.当取塔顶、塔底平均温度T 为计算温度时,可导出1km ol 进料(组成X F 1及X F 2)分离为塔顶产品(组成X D 1及X D 2)D 和残釜液量W ,单位为kmo l.塔釜残液(组成X W 1及X W 2)时所需的最小有效能E min 为E min =-R T {xF 1ln(C F 1x F 1)+x F 2ln(C F 2x F 2)-D [x D 1ln(C D 1x D 1)+x D 2ln(C D 2x D 2)]-W [x W 1ln(C W 1x W 1)+x W 2ln(C W 2x W 2)]}(2)式中 C 为物料活度系数;R 为通用气体系数,等于8.314J/mol õK.2.2 实际过程中的有效能E在实际精馏过程中,主要的能量输入是塔底再沸器的加热.从热力学的观点而言,相当用热泵使热能从环境温度T 0升至加热温度T s ;主要的能量输出使塔顶冷凝器冷却,相当于用热机使热能从冷凝温度T c 降至环境温度T 0.因此,过程中需要的有效能为E =Q D (T S -T 0)/T S -Q C (T C -T 0)/T C (3)式中 Q D 、Q C 为再沸器及冷凝器的热负荷原料液.E =Q D T 0(1/T C -1/T S )(4)3 分割式热泵精馏的热力学计算[3~4]3.1 下塔从下塔上升的蒸汽量为V 1=(1+R 1)D 单位:kmol/h(5)式中 R 1为下塔回流比,其优化值在0.4~0.6.下塔耗热量为Q 1=(1+R 1)Dr 单位:kJ/h (6)式中 r 为蒸汽的摩尔汽化潜热.由于V 1所含热量最终是在上塔冷凝器中被冷却水带走,因此过程所需的有效能E 1为E 1=Q 1T 0(1/T C -1/T S )(7)3.2 上塔上塔的能耗主要是压缩机耗功E 2E 2=P 1V 1k /(k -1)[(P 2/P 1)k -1/k -1](8)式中 P 1、V 1为压缩机入口气体的压力和体积;P 2/P 1为压缩比;P 2为压缩机出口压力;k 为酒精溶液在恒沸点下的绝热系数;k =1.14.3.3 系统热力学效率系统总能耗E =E 1+E 2(9)系统热力学效率G =E min /E (10)4 实 例某厂回收废酒精,进料量7m 3/h,X F 1=0.334,拟用0.3MPa 的蒸汽作热源,要求分离得到95第8期李 珊等:分割式酒精精馏热泵的研究酒精浓度X D1=0.836,塔釜残液组成X W1=0.003.试计算常规精馏与分割式热泵精馏的热力学效率.对于分割式热泵精馏塔,其进料位置由进料液的组成确定在上塔的塔底.原料液与从上塔最底层塔板上流下的液体混合后,送到上塔再沸器中,部分汽化的蒸汽返回上塔,液体流入下塔.在计算中,加热蒸汽T S=406K,恒沸点温度为351K,环境温度取T0=303K.计算结果如后文所述.4.1 常规精馏与分割式热泵精馏主要参数对比2种精馏流程的主要参数见表1.表1 常规精馏与分割式热泵精馏流程主要参数参 数 常规精馏分割式热泵精馏上塔下塔塔顶压力/M Pa0.10.1常压塔顶温度/℃78478.482.3塔底温度/℃约10082.3约100塔径/m221塔高/m30.825.413.1回流比 3.5 3.50.4实际塔板板数/块(取理论塔板数×2)382914再沸器热负荷/G Jõh-119.6 5.97再沸器面积/m211530614压缩机功/G Jõh-10.3234.2 分离所需最小有效能E min根据物料衡算的结果可求得计算E min所需数据,见表2.表2 计算E min所需的有关数据流量/kmolõh-1组成(摩尔分率)1组分2组分沸点温度/℃活度系数1组分2组分进料F=1X F1=0.334X F2=0.66681.3C F1=1.576C F2=1.458馏出液D=0.402X D1=0.830X D2=0.17078.3C D1=1.019C D2=2.056釜残液W=0.598X W1=0.003X W2=0.99799.0C W1=4.974C W2=0.975取T等于塔顶、塔底平均温度,T=362K.则将表2数据代入式(2)得E min=286J/m ol. 96西安交通大学学报第31卷4.3 2种精馏流程的热力学效率考虑到实际情况的多样性,此处均按理论有效能耗及功耗进行计算.4.3.1 常规精馏 将水的摩尔汽化潜热r w =40554J /m ol 及所取定的回流比R =3.5代入下式Q s =(R +1)Dr w =72268kJ.再根据常规精馏耗有效能E C =Q s T 0(1/T C -1/T S )=8451kJ 可得G C =E min E C = 3.4%4.3.2 分割式热泵精馏 下塔:取R 1=0.4,代入式(6)得热负荷Q 1=22483kJ,再由式(7)求得过程所需有效能E 1=2630kJ .上塔:进入压缩机的气体流量为(R 2-R 1)D =1.23mol /h ;塔顶蒸汽温度为78.4℃,塔釜为82.3℃,二者温差3.9℃.根据文献[1]的介绍,南京塔器厂曾对SDJ 塔的实际运行进行过测定,当塔板数为29块时,全塔压力降可达1.87m 水柱.为此,应适当加大压缩机的压缩比(取1.7),相应的酒精蒸汽饱和温度为90℃.将气体流量换算为压缩入口状态下的体积V =35.35m 3/h ,由式(8)求得压缩机作功E 2=1958kJ/h.代入式(9)、(10),则G S =E min /(E 1+E 2)=6.2%.4.3.3 2种流程热力学效率对比 由上可知,G S /G C =6.23.4×100%=182%,即分割式酒精精馏热泵的流程比常规酒精精馏流程的热力学效率提高了82%.5 结 论(1)化工精馏过程由于是塔底加热,塔顶取热,过程的不可逆性强,过程的热效率只有3%~5%,甚至更低.因而,因地制宜地采用多种方法(包括应用热泵精馏等)提高精馏过程的热效率,是降低相关化工行业的能耗、提高其竞争能力的重点课题之一,并有待进一步广泛研究.(2)本文提出了利用液体混合物,在相平衡关系中溶液相对挥发度的变化特点,巧妙地将精馏装置分割为上、下两塔,使上塔的塔顶、塔底温差变为3.9℃,因而可以应用压缩式热泵精馏流程.该思路可以推广到其他具有相近相平衡关系的双组分精馏过程中去,具有一定普遍意义.(3)通过实例计算得知,酒精-水系统采用分割式热泵精馏装置时,其热力学效率比常规精馏装置提高82%,节能效果显著.参考文献1 许开天.酒精蒸馏技术.北京:轻工出版社,1990.387~3922 St andifo rd F C .Ener g y conserv atio n in alco hol pr oduct ion .New Y or k :CEP Jan ,1983.35~393 袁一.化工过程热力学分析法.北京:化学工业出版社,19854 骆赞椿.化工节能热力学原理.北京:化学工业出版社,1990(编辑 管咏梅)97第8期李 珊等:分割式酒精精馏热泵的研究98西安交通大学学报第31卷Research on Severance Type Heat Pump for Distilling AlcoholLi S han W ang L i H u Yuanchun(Xiøan J iaotong University,710049,Xiøan)Abstract T he com pression heat pum p used for distilling alcohol w as co nsidered inadequate in the past because of the rather big temper ature difference between the to p and the bottom of the tow er.In this paper,accor ding to the property of alco ho l-aquaphase balance,a sever-ance type flo w chart is designed w hich m akes application of the above-mentioned heat pum p po ssible.Proved by calculation,the therm odynam ic efficiency is increased by82%in this pr oject than conventional distilling process.Keywords distillation p hase balance sev erance typ e heat p ump(上接第92页)Study on the Measurement of Fracture Toughness J MC andFracture Criterion under Mixed ModeⅠ+ⅡLoadingSha J iangbo Deng Zengj ie Zhou H uij ui(Xiøan J iaotong University,710049,Xiøan)Abstract T he elastic-plastic fracture behavior and the measurem ent method of fr acture toughness J MC in Ly12and40CrN iM o under mixed m odeⅠ+Ⅱloading w ere studied w ith the finite element method and fracture test.The mix ed mode elastic-plastic fractur e criterion w as pro posed.The r esults sho w that1)Based o n the mixed mo de J R resistance curve,it is easy to im plm ent the m ethod of zero extension of crack tip stretch zone for measuring the fr actur e toughness J M C under m ixedⅠ+Ⅱmode lo ading,and the measurement result can meet eng ineer ing precisio n r eqairement;2)T he fracture toughness J M C of different m ix ed ra-tio s satisfies certain equation,fro m w hich the J MC w ith arbitrary mix ed ratio s can be obtained if JⅠc and JⅡc of the material ar e know n.Keywords mix ed mode f racture toughness f r acture criterion。
精馏节能技术

热泵精馏工艺分析化工行业就是能耗大户,其中精馏又就是能耗极高的单元操作,而传统的精馏方式热力学效率很低,能量浪费很大。
如何降低精馏塔的能耗,充分利用低温热源,已成为人们普遍关注的问题。
对此人们提出了许多节能措施,通过大量的理论分析、实验研究以及工业应用表明其中节能效果比较显著的就是热泵精馏技术。
热泵精馏就是把精馏塔塔顶蒸汽加压升温,使其用作塔底再沸器的热源,回收塔顶蒸汽的冷凝潜热。
热泵精馏在下述场合应用,有望取得良好效果:(1)塔顶与塔底温差较小,因为压缩机的功耗主要取决于温差,温差越大,压缩机的功耗越大。
据国外文献报导,只要塔顶与塔底温差小于36℃,就可以获得较好的经济效果。
(2)沸点相近组分的分离,按常规方法,蒸馏塔需要较多的塔盘及较大的回流比,才能得到合格的产品,而且加热用的蒸汽或冷却用的循环水都比较多。
若采用热泵技术一般可取得较明显的经济效益。
(3)工厂蒸汽供应不足或价格偏高,有必要减少蒸汽用量或取消再沸器时。
(4)冷却水不足或者冷却水温偏高、价格偏贵,需要采用制冷技术或其她方法解决冷却问题时。
(5)一般蒸馏塔塔顶温度在38~138℃之间,如果用热泵流程对缩短投资回收期有利就可以采用,但就是如果有较便宜的低压蒸汽与冷却介质来源,用热泵流程就不一定有利。
(6)蒸馏塔底再沸器温度在300℃以上,采用热泵流程往往就是不合适的。
以上只就是对一般情况而言,对于某个具体工艺过程,还要进行全面的经济技术评定之后才能确定。
根据热泵所消耗的外界能量不同,热泵精馏可分为蒸汽加压方式与吸收式两种类型1、蒸汽加压方式蒸汽加压方式热泵精馏有两种:蒸汽压缩机方式与蒸汽喷射式。
1、1蒸汽压缩机方式蒸汽压缩机方式又可分为间接式、塔顶气体直接压缩式、分割式与塔釜液体闪蒸再沸式流程。
1、1、1间接式当塔顶气体具有腐蚀性或塔顶气体为热敏性产品或塔顶产品不宜压缩时,可以采用间接式热泵精馏,见图1。
图1 间接式热泵精馏流程图它主要由精馏塔、压缩机、蒸发器、冷凝器及节流阀等组成。
热泵精馏与常规精馏的热力学分析比较
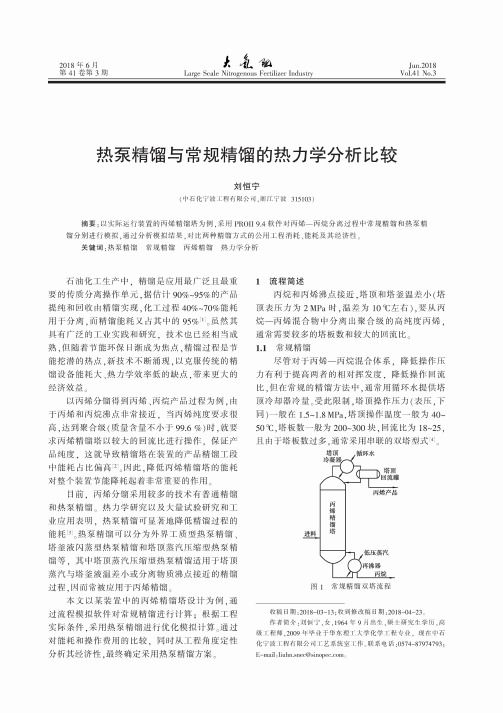
热泵精馏与常规精馏的热力学分析比较刘恒宁(中石化宁波工程有限公司,浙江宁波315103'摘要:以实际运行装置的丙烯精馏塔为例,采用PROII 9.4软件对丙烯一丙烷分离过程中常规精馏和热泵精 馏分别,通过分析模拟结果,对比两种精馏方式的公用工程消耗、能耗及其经济性。
关键词:热精馏常规精馏精馏热力学分析石油化工生产中,精馏是应用最广泛且最重 要的传质分离操作单元,据估计90#〜95#的产品 提纯和回收由精馏实现,化工过程40#〜70#能耗 用于分离,而精馏能耗又占其中的95#[1]。
虽然其 具有广泛的工业实践和研究,技术也已经相当成 熟,但随着节能环保日渐成为焦点,精馏过程是节 能挖潜的热点,新技术不断涌现,以克服传统的精 馏设备能耗大、热力学效率低的点,大的经济效。
以分馏得到丙烯、丙烷产品过程为例,由于丙烯和 点常接近,当丙烯纯度要求很 高,达到聚 (质 于99.6#)时,要求 精馏以大的回操作,保 :品纯度,精馏 的产品精馏工中能耗占 高[2]。
,精馏的能耗节能降耗起着常重要的作用。
,分馏 用 的技术有 精馏 和热泵精馏。
热力学研究以及大量试验研究和工 业应用 ,热精馏精馏过程的能耗[3]。
热精馏以分为工质热泵精馏、热泵精馏和 热精馏 ,其中 热 精馏 用于分离物质点接近的精馏过程,而常应用于精馏。
以中的精 馏 设计为 ,过流程 常精馏计;据工程实 ,用热 精馏 化 计 。
过 能耗和 作 用的 ,工程 度分 其经 ,最 用热 精馏 。
1流程简述和丙烯沸点接近,塔顶和塔釜温差小(±荅顶表压力为2M Pa时,为10°C左右),要 f一 中分离 聚 的高 纯度 ,常需要 的和大的回。
1.1常精馏于丙烯一丙烷混合体系,降低操作压 力有于提高两者的相挥发度,作回流,但常的精馏方法中,通常用循环水提供塔 顶冷却器冷量。
受此限制,作力(,下)一般 1.5〜1.8MPa,作度一般为40〜50 C,塔板数一般为200-300块,回流比为18-25,且由于 过,通常采用串联的双 式[4]。
精馏实验原理和基本理论
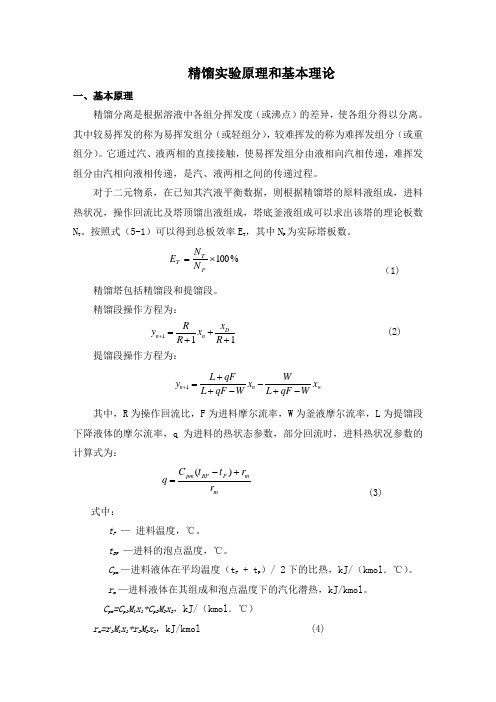
精馏实验原理和基本理论一、基本原理精馏分离是根据溶液中各组分挥发度(或沸点)的差异,使各组分得以分离。
其中较易挥发的称为易挥发组分(或轻组分),较难挥发的称为难挥发组分(或重组分)。
它通过汽、液两相的直接接触,使易挥发组分由液相向汽相传递,难挥发组分由汽相向液相传递,是汽、液两相之间的传递过程。
对于二元物系,在已知其汽液平衡数据,则根据精馏塔的原料液组成,进料热状况,操作回流比及塔顶馏出液组成,塔底釜液组成可以求出该塔的理论板数N T 。
按照式(5-1)可以得到总板效率ET,其中NP为实际塔板数。
%100⨯=PTT NNE(1) 精馏塔包括精馏段和提馏段。
精馏段操作方程为:111Dn nxRy xR R+=+++(2)提馏段操作方程为:1n n wL qF Wy x xL qF W L qF W++=-+-+-其中,R为操作回流比,F为进料摩尔流率,W为釜液摩尔流率,L为提馏段下降液体的摩尔流率,q为进料的热状态参数,部分回流时,进料热状况参数的计算式为:mm FBP pmrr ttCq+ -=)((3)式中:tF—进料温度,℃。
tBP—进料的泡点温度,℃。
C pm —进料液体在平均温度(tF+ tP)/ 2下的比热,kJ/(kmol.℃)。
rm—进料液体在其组成和泡点温度下的汽化潜热,kJ/kmol。
C pm =Cp1M1x1+Cp2M2x2,kJ/(kmol.℃)r m =r1M1x1+r2M2x2,kJ/kmol (4)式中:Cp1,C p2——分别为纯组份1和组份2在平均温度下的比热,kJ/(kg.℃)。
r1,r2——分别为纯组份1和组份2在泡点温度下的汽化潜热,kJ/kg。
M 1,M2——分别为纯组份1和组份2的摩尔质量,kg/kmol。
x1,x2——分别为纯组份1和组份2在进料中的摩尔分率。
二、全回流和最小理论板层数1. 全回流的概念若上升至塔顶的蒸汽经全凝器冷凝后,冷凝液全部回流到塔内,该回流方式称为全回流,全回流时的回流比为(5)在全回流下,精馏段操作线的斜率和截距分别为(6)(7)此时,在x–y图上,精馏段操作线及提馏段操作线与对角线重合,全塔无精馏段和提馏段之区分,两段的操作线合二为一,即(8)应予指出,在全回流操作下,塔顶产品D为零,一般和也均为零,即不向塔内进料,也不从塔内取出产品,装置的生产能力为零,因此对正常生产并无实际意义。
深入讲讲热泵精馏

深入讲讲热泵精馏热泵精馏技术的核心是逆向卡诺循环,即把工质通过加压升温,回收塔顶蒸汽的冷凝潜热,作为塔底再沸器的热源,以达到减少冷热公用工程用量的目的。
热泵精馏除开工阶段外,基本上不需向再沸器提供额外的热量。
自20世纪80年代末以来,热泵精馏在丙烯、丙烷、乙醇、醋酸甲酯等实际工业分离过程中取得了较好的节能效果。
热泵系统的工作原理热泵主要由压缩机、膨胀阀、蒸发器和冷凝器构成,热量通过这四个部件之间的循环来实现传递。
如上图所示,来自蒸发器的低温低压蒸气经压缩机升温升压,达到所需温度和压力的蒸气流经冷凝器,蒸气放出热量,降温冷凝成液相,经节流膨胀后压力继续下降。
低压液相工作介质流入蒸发器后,由于沸点很低,很容易吸收热量再蒸发,又形成低温低压蒸气。
如果把蒸发器放入低品位热源中吸收热量,则吸收了热量的蒸气再进入压缩机,如此循环,就能使低温热量不断流到温度较高的地方,实现热量的有效回收利用,其代价是不断给压缩机提供机械能或电能。
热泵精馏系统用“泵”(压缩机)把热量从低温处送到高温处,在该系统中压缩机消耗的能量是唯一由外界提供的能量,它比再沸器直接加热消耗的能量少得多,一般只相当于后者的20~40%,由此可见热泵节约能耗的作用。
热泵精馏的适用场合热泵精馏具有一定的应用范围,需要根据精馏塔工艺要求,通过准确的经济评比决定是否使用热泵精馏:⑴塔顶和塔底温差较小。
因为压缩机的功耗主要取决于温差,温差越大,压缩机的功耗越大。
据国外文献报导,只要塔顶和塔底温差小于36℃,就可以获得较好的经济效果;⑵塔顶温度低于环境温度又高于工质的蒸发温度,塔底温度低于工质冷凝温度的精馏塔;⑶工质蒸汽冷凝潜热较大的系统;⑷被分离物质沸点接近,相对挥发度较小,分离困难,按常规方法,蒸馏塔需要较多的塔盘及较大的回流比,才能得到合格的产品,而且加热用的蒸汽或冷却用的循环水都比较多。
若采用热泵技术一般可取得较明显的经济效益;⑸冷却水不足或冷却水温偏高、价格偏贵,低压运行时必须采用冷冻剂进行冷凝,为了使用冷却水或空气作为冷凝介质必须在较高压力下分离易挥发物质的场合;⑹工厂蒸汽供应不足或价格偏高,有必要减少蒸汽用量或取消再沸器时;⑺一般蒸馏塔塔顶温度在38~138℃之间,如果用热泵流程对缩短投资回收期有利就可以采用,但是如果有较便宜的低压蒸汽和冷却介质来源,用热泵流程就不一定有利;⑻蒸馏塔底再沸器温度在300℃以上,采用热泵流程往往是不合适的。
热泵精馏技术进展介绍

2 1 国内外热泵精馏技术 的研究 .
热泵技术应用于精馏 生产中最早是 由2 0世纪
5 0年代 的 R bno oisn和 Gll d提 出 的 , iin la 随后 的半 个
世纪里该技术迅 速发展。0i i 1e a进行 了具有蒸汽 vr 再压缩式精馏塔技术的研究 , m s .G bi 研究 J e G eb a e
维秀等 学者归 纳 了热 泵 精馏 基 本 应 用 方 式 , 并根 据
热 泵技 术 在精 馏 过 程 中起 到 节 能 的作用 , 高 提 热 泵输 出温度 , 高热 泵 的能效 比 , 提 是热 泵技术 急需
攻 克 的难题 , 也是 热 泵 技 术 努力 的方 向。热泵 技 术
各 自特 点 、 详尽 分 析 了性 能 和应 用 条 件 的不 同。魏
W NGL —u n , H N ig—yn ,Q UR A i ja Z A G Yn i g I u—ce hn
( o eeo hmi l n ier g Q n doU i ri f c nea dT c nlg , ig a 1C l g f e c g e n , ig a nv s yo i c n eh o y Qn do l C aE n i e t Se o 2 6 4 ,C ia 2 S a g ogC l g f h m cl eh i a sT n zo 2 7 0 , hn ) 6 0 2 hn ; . h n dn o e eO e ia T c nc n , e gh u 7 5 0 C ia l C i
入混合 室 , 生成生产需 要 的中压蒸 汽 ( 一般 在 0 4 a .MP
以下 )供再 沸器 二 次使 用 , 流程 最 重要 的特 点 是 , 本 没有 转动部 件 , 构 简 单 , 对 蒸 气 压 有 一 定 的 要 结 仅
精馏酒精设备中废热的有效利用

精馏酒精设备中废热的有效利用摘要:随着酒精生产水平的提升,精馏酒精设备能耗损失随之增大,通过对精馏环节的余热进行回收处理,能够在顺利实现资源回收利用目标的基础上,更为高效的控制热能污染问题。
因此相关工作人员需要提高对精馏酒精设备余热利用的重视程度,及时采取热泵精馏技术展开废热回收处理,有助于进一步提升精馏余热的回收利用率。
本文首先分析酒精精馏工艺流程,其次探讨热泵精馏技术废热利用方式,以期对相关研究产生一定的参考价值。
关键词:精馏酒精设备;废热;有效利用引言:在酒精生产加工水平不断提高的背景下,设备能耗随之增大,为了将能耗变废为宝,回收利用精馏环节的余热,能够在顺利实现资源回收利用目标。
因此管理人员应该重点提升对废热利用的管理力度,加强对精馏酒精设备的余热管理,从而在余热实际利用率的基础上降低酒精生产能耗。
1酒精精馏工艺流程在精馏工序中,需要对发酵好的成熟醪液开展精馏处理,能够将乙醇浓度提高到95以上的状态,基于精馏分离理论,可以使用精馏塔对乙醇、水进行分离处理。
在醪液之中乙醇仅占据了10%,还存在一些固体杂质,在对乙醇进行精馏处理时,一般需要使用粗馏塔以及精馏塔开展分离处理。
2热泵精馏技术废热利用方式2.1热汽压缩式热泵精馏技术2.1.1A型开式热泵精馏技术这种热泵精馏技术的介质是塔顶气体,在热泵精馏处理时,塔顶气体需要先流经压缩机,压缩机能够对这些气体开展压缩处理工作,此时压缩压力会逐渐增大,气体温度随之增大,在气体压缩到界限值的时候,塔顶气体会渐渐进入到塔顶之中,然后再进入到再沸器内,历经冷凝处理、放热处理,酒精液体将会处于再次沸腾状态,部分冷凝液会进入塔顶位置进行回流[1]。
2.1.2B型开式热泵精馏技术这种热泵精馏技术采用的介质主要是塔釜液体,在热泵精馏处理时,应该及时对节流阀展开降压处理、降温处理,然后即可将塔釜液传送到塔顶区域的冷凝器之中,气体在展开冷凝处理时会释放很多热量,塔釜液体在历经气化处理时,会慢慢进入到压缩机中,此时压缩机能够对塔釜液体实施升压处理、升温处理,然后这些气体会渐渐返回塔釜之中,此时塔釜会释放很多热量,在完成冷凝处理之后将会产生很多液体。
热泵精馏流程构建策略及应用研究

热泵精馏流程构建策略及应用研究热泵精馏技术,也称为低温结晶法,是一种新兴分离工艺,它以低温温度低于蒸馏和精馏技术,可以较好地满足芳香族化合物在生物燃料制备及药物制备等领域的分离要求。
本文主要讨论了热泵精馏技术构建流程及其应用研究,旨在为热泵精馏技术的应用提供参考。
热泵精馏技术的主要构建流程是用溶剂和蒸馏方式实现分离和回收:首先,将原料混合物加入溶剂中,用蒸馏方式将混合物蒸馏出溶解性较高的组分;然后,用比例稀释处理,将溶解性较高的组分比例稀释,通过比例稀释操作,可以达到最优的回收效果;最后,将比例稀释的组分加入热泵进行精馏,此时,催化剂和杂质都会受到热泵抽气的影响,溶解度弱的组分会首先被抽出,而溶解度较强的组分则最后被抽出,以实现有效分离和纯化。
热泵精馏技术应用于许多领域,主要应用于生物燃料制备、药物制备和精细化学品生产等领域。
首先,在生物燃料制备中,热泵精馏技术可以有效地分离芳香族燃料原料,大大提高生物燃料的混合物组成和结构,控制生物燃料的性质,为生物燃料研发和制造提供便利;其次,在药物制备中,热泵精馏技术可以有效地回收有毒成分,从而减少有毒成分对人类身体的不良影响,可用于制备安全有效的药物;最后,在精细化学品生产中,热泵精馏技术可以有效地回收和净化废气,减少污染,为精细化学品生产提供可靠保障。
热泵精馏技术的构建流程及应用研究已取得了很大的进步,但仍有许多不足之处,如精馏过程中抽气流速过快,催化剂稳定性较差,流速控制不准确等。
应加强这些问题的研究,并努力提供更完善、更可行的解决方案,以推动热泵精馏技术应用的发展。
本文综述了热泵精馏技术的构建流程及其应用研究,根据热泵精馏技术的构建流程,可以按照溶剂和蒸馏方式来实现有效的分离和回收,而且可广泛应用于生物燃料制备、药物制备和精细化学品生产等领域,但存在一些技术难题,比如流速控制不准确,催化剂稳定性较差等,应加强上述问题的研究,以推动热泵精馏技术的发展。
热泵精馏流程构建策略及应用研究

热泵精馏流程构建策略及应用研究热泵精馏(thermally-assisted distillation)是一种技术,是借助外部热源使一种溶剂中的两种溶剂分离,以实现不相容液体之间精确,稳定和安全的分离精馏手段。
该技术可大大提高分子级分离的效率,以及温和复杂物质之间溶剂互换作用的效率,改变了传统精馏技术。
在进行热泵精馏反应过程之前,有几个重要的考虑因素,主要是围绕每次运行的流程结构,以实现最理想的分离操作和效果。
首先,热泵精馏流程的设计应建立在对系统结构及特性的全面理解的基础上。
比如进料的性质,反应过程中的变量,出口物的操作要求,溶剂的标准,废水的可回收或处理,设备和线路的应用等。
其次,设计师应根据实际情况确定最佳服务温度,确定热源和运行介质,如水、空气、油和蒸汽。
此外,热源温度必须与反应器温度同步,以确保系统的安全,以保证效率得到最佳改进,并确定最低回收费用。
热泵精馏流程中最重要的参数是热源温度、运行介质和进料温度。
此外,应考虑冷凝和板换的性能参数,如换热系统的冷凝温度,泵系统的压力、流速和气体配置,分線器及其他组件,及设备量等。
另外,应根据原材料以及最终产品特征,确定预防性维护程序,防止结垢、腐蚀和机械故障,以保证精馏效果的一致性。
最后,实验室分析的反映为最佳的回签。
实验室分析通常包括液体分析、化学测定、含气量检测和理化检测,以及包装质量检测,旨在根据用户的特定需求评估分离过程的质量和性能。
综上所述,热泵精馏流程的构建策略离不开对系统结构及特性的准确了解,根据实际情况确定最优服务温度,热源温度与反应器温度同步,确定热源和运行介质,充分考虑冷凝和板换的性能参数,及末端的实验室分析的准确性,以及预防性维护程序安全可靠。
这些都是热泵精馏系统高效运行的关键,具有极其重要的指导意义。
关于浅析萃取精馏技术的研究论文[5篇范文]
![关于浅析萃取精馏技术的研究论文[5篇范文]](https://img.taocdn.com/s3/m/a0e5becefbb069dc5022aaea998fcc22bcd143ee.png)
关于浅析萃取精馏技术的研究论文[5篇范文]第一篇:关于浅析萃取精馏技术的研究论文1、萃取精馏的原理在基本有机化工生产中,经常会遇到组分的相对挥发度比较接近,组分之间也存在形成共沸物的可能性。
若采用普通精馏的方法进行分离,将很困难,或者不可能。
对于这类物系,可以采用特殊精馏方法,向被分离物系中加入第三种组分,改变被分离组分的活度系数,增加组分之间的相对挥发度,达到分离的目的。
如果加入的溶剂与原系统中的一些轻组分形成最低共沸物,溶剂与轻组分将以共沸物形式从塔顶蒸出,塔底得到重组分,这种操作称为共沸精馏;如果加入的溶剂不与原系统中的任一组分形成共沸物,其沸点又较任一组分的沸点高,溶剂与重组分将随釜液离开精馏塔,塔顶得到轻组分,这种操作称为萃取精馏。
2、溶剂筛选原理由于萃取精馏混合物多为强非理想性的系统,所以工业生产中选择适宜溶剂时主要应考虑以下几点:(1)选择性:溶剂的加人要使待分离组分的相对挥发度提高显著,即要求溶剂具有较高的选择性,以提高溶剂的利用率;2)溶解性:要求溶剂与原有组分间有较大的相互溶解度,以防止液体在塔内产生分层现象,但具有高选择性的溶剂往往伴有不互溶性或较低的溶解性,因此需要通过权衡选取合适的溶剂,使其既具有较好的选择性,又具有较高的溶解性;(3)沸点:溶剂的沸点应高于原进料混合物的沸点,以防止形成溶剂与组分的共沸物。
但也不能过高,以避免造成溶剂回收塔釜温过高。
目前萃取精馏溶剂筛选的方法有实验法、数据库查询法、经验值方法、计算机辅助分子设计法用实验法筛选溶剂是目前应用最广的方法,可以取得很好的结果,但是实验耗费较大,实验周期较长。
实验法有直接法、沸点仪法、色谱法、气提法等。
实际应用过程中往往需要几种方法结合使用,以缩短接近目标溶剂的时间。
溶剂筛选的一般过程为:经验分析、理论指导与计算机辅助设计、实验验证等。
若文献资料和数据不全,则只有采取最基本的实验方法,或者采取颇具应用前景的计算机优化方法以寻求最佳溶剂。
精馏操作依据 以达到分离均相液体混合物

精馏操作依据以达到分离均相液体混合物一、概述精馏作为一种常见的分离技术,在化工生产、实验室研究以及日常生活中都有着广泛的应用。
通过精馏,可以有效地分离均相液体混合物中的成分,得到纯净的单一物质。
精馏的操作依据有着严谨的规范,掌握了这些操作依据,才能够实现分离的高效与准确。
二、精馏操作依据1. 蒸馏原理精馏的基本原理是利用混合物中成分的不同沸点来实现分离。
在精馏过程中,将混合物加热至液体汽化,然后采用冷凝器将汽化的混合物重新凝结成液体。
由于液体成分的沸点不同,不同的成分将会分别汽化和冷凝,从而实现分离。
正确把握不同成分的沸点是实施精馏操作的基础。
2. 设备选择在实施精馏操作时,需要选择合适的设备来确保操作的顺利进行。
冷凝器的选择要兼顾冷却效果和对混合物的适应性,以免造成混合物无法完全冷凝或者出现混合物反应性的问题。
3. 流体动力学精馏操作中,混合物的流体动力学是一个重要的考虑因素。
在操作时,要确保混合物在设备内能够顺利地进行汽化和冷凝,不出现液体的回流或者汽液两相的不稳定现象。
4. 控制器件在进行精馏操作时,需要配备合适的控制器件来确保操作的顺利进行。
恒温控制器可以控制精馏设备内的温度,确保混合物能够按照预定的温度进行汽化和冷凝。
5. 操作技能除了上述的操作依据外,实施精馏操作还需要具备一定的操作技能。
在加热混合物时需要掌握适当的加热速度和温度控制,以避免混合物的反应或过度汽化而导致分离效果的下降。
6. 安全保障精馏操作涉及能源的使用和高温高压环境,因此在实施操作时要做好安全防护措施,确保操作人员和设备的安全。
三、总结精馏作为一种重要的分离技术,操作依据的掌握对于实现分离效果至关重要。
通过对精馏操作依据的充分理解和实践,可以确保分离的高效、准确地进行,从而得到所需的单一物质。
在实施精馏操作时,要注意安全和环保,做好相关防护措施,才能够确保操作的顺利进行。
掌握精馏操作依据是进行分离操作的基础,也是科学实验和工业生产中不可或缺的重要技能。
热泵在精馏节能中的作用
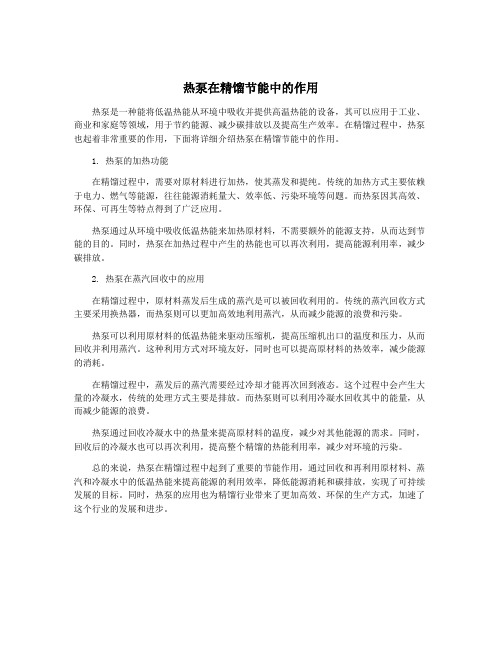
热泵在精馏节能中的作用热泵是一种能将低温热能从环境中吸收并提供高温热能的设备,其可以应用于工业、商业和家庭等领域,用于节约能源、减少碳排放以及提高生产效率。
在精馏过程中,热泵也起着非常重要的作用,下面将详细介绍热泵在精馏节能中的作用。
1. 热泵的加热功能在精馏过程中,需要对原材料进行加热,使其蒸发和提纯。
传统的加热方式主要依赖于电力、燃气等能源,往往能源消耗量大、效率低、污染环境等问题。
而热泵因其高效、环保、可再生等特点得到了广泛应用。
热泵通过从环境中吸收低温热能来加热原材料,不需要额外的能源支持,从而达到节能的目的。
同时,热泵在加热过程中产生的热能也可以再次利用,提高能源利用率,减少碳排放。
2. 热泵在蒸汽回收中的应用在精馏过程中,原材料蒸发后生成的蒸汽是可以被回收利用的。
传统的蒸汽回收方式主要采用换热器,而热泵则可以更加高效地利用蒸汽,从而减少能源的浪费和污染。
热泵可以利用原材料的低温热能来驱动压缩机,提高压缩机出口的温度和压力,从而回收并利用蒸汽。
这种利用方式对环境友好,同时也可以提高原材料的热效率,减少能源的消耗。
在精馏过程中,蒸发后的蒸汽需要经过冷却才能再次回到液态。
这个过程中会产生大量的冷凝水,传统的处理方式主要是排放。
而热泵则可以利用冷凝水回收其中的能量,从而减少能源的浪费。
热泵通过回收冷凝水中的热量来提高原材料的温度,减少对其他能源的需求。
同时,回收后的冷凝水也可以再次利用,提高整个精馏的热能利用率,减少对环境的污染。
总的来说,热泵在精馏过程中起到了重要的节能作用,通过回收和再利用原材料、蒸汽和冷凝水中的低温热能来提高能源的利用效率,降低能源消耗和碳排放,实现了可持续发展的目标。
同时,热泵的应用也为精馏行业带来了更加高效、环保的生产方式,加速了这个行业的发展和进步。
热泵精馏的原理范文

热泵精馏的原理范文热泵精馏是一种通过低温热泵技术实现精馏过程能量回收与能效提升的方法。
其原理可分为热泵作用、精馏过程与能量回收三个方面。
1.热泵作用:热泵是一种能够将低温热量提取并通过能量转换提升至高温热量的机械装置。
按照热力学定律,热量自然会从高温向低温传递,使得高温物体的温度降低。
而热泵技术通过采用特定的工质来完成这种热量的逆向转移,即将低温热量从环境中提取并通过能量转换将其提升至更高温度的热量。
2.精馏过程:精馏是一种通过温度差异使液体混合物中的组分根据其挥发性差异蒸发和冷凝的分离过程。
在传统的精馏过程中,通常需要将混合物加热至较高温度,使得其中挥发性较高的组分蒸发,然后通过冷凝使其重新凝结,并分离出纯净的组分。
这一过程需要耗费大量的热量。
而在热泵精馏中,通过热泵技术,可以实现在较低温度下将混合物的一部分蒸发出来,然后通过热泵将蒸汽中的热量提取出来,再将其重新压缩提高温度,然后与其他部分混合物进行进一步的分离。
这样可以实现在低温下进行精馏过程,从而减少能耗,提高能效。
3.能量回收:在传统的精馏过程中,蒸发产生的蒸汽通常直接排放或冷凝成液体。
而在热泵精馏中,通过热泵技术,可以将部分蒸汽中的热量提取出来,并再度利用。
具体而言,热泵精馏中一部分蒸汽经过压缩,其温度和压力都得到提高。
这部分蒸汽中的热量通过传热器(换热器)与混合物中的低温部分进行热交换,从而使混合物再度升温,实现部分分离。
与此同时,压缩后的蒸汽中的热量也可以通过与进一步的冷却介质(如水)进行热交换,从而使其温度降低,使其冷凝成液体。
这样,可以将蒸汽中的热量回收利用,实现能量的有效循环。
总结起来,热泵精馏通过低温热泵技术在低温条件下进行精馏过程,实现了能量回收与能效提升。
它不仅节约了能源,减少了环境污染,降低了生产成本,还可以提高产品的纯度和质量,具有广阔的应用前景。
热泵精馏的原理
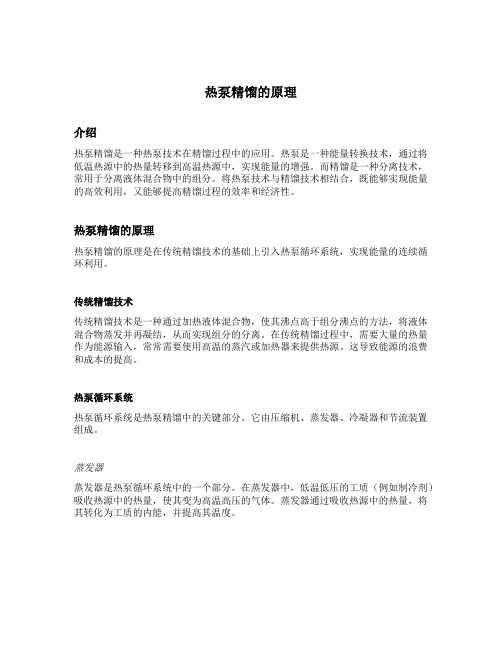
热泵精馏的原理介绍热泵精馏是一种热泵技术在精馏过程中的应用。
热泵是一种能量转换技术,通过将低温热源中的热量转移到高温热源中,实现能量的增强。
而精馏是一种分离技术,常用于分离液体混合物中的组分。
将热泵技术与精馏技术相结合,既能够实现能量的高效利用,又能够提高精馏过程的效率和经济性。
热泵精馏的原理热泵精馏的原理是在传统精馏技术的基础上引入热泵循环系统,实现能量的连续循环利用。
传统精馏技术传统精馏技术是一种通过加热液体混合物,使其沸点高于组分沸点的方法,将液体混合物蒸发并再凝结,从而实现组分的分离。
在传统精馏过程中,需要大量的热量作为能源输入,常常需要使用高温的蒸汽或加热器来提供热源。
这导致能源的浪费和成本的提高。
热泵循环系统热泵循环系统是热泵精馏中的关键部分。
它由压缩机、蒸发器、冷凝器和节流装置组成。
蒸发器蒸发器是热泵循环系统中的一个部分。
在蒸发器中,低温低压的工质(例如制冷剂)吸收热源中的热量,使其变为高温高压的气体。
蒸发器通过吸收热源中的热量,将其转化为工质的内能,并提高其温度。
压缩机是热泵循环系统中的另一个关键部分。
蒸发器中的高温高压气体被压缩机吸入,压缩机对气体进行压缩,提高其压力和温度。
压缩机将气体的内能增加,并将其进一步升温。
冷凝器冷凝器是热泵循环系统中的一个组成部分。
在冷凝器中,高温高压气体通过散热的方式,将其热量传递给冷源,使其逐渐冷却并凝结为液体。
冷凝器通过散热的方式,将气体的热量转移给冷源,并使其冷却。
节流装置节流装置是热泵循环系统中的最后一个部分。
它用于降低气体的压力,使其重新变为低温低压的工质,循环继续。
热泵精馏的原理热泵精馏通过将热泵循环系统与传统精馏技术相结合,实现能量的连续循环利用,并提高精馏过程的效率和经济性。
在热泵精馏中,蒸发器用来吸收热源中的热量,并将其转化为工质的内能,并提高其温度。
压缩机将高温高压气体吸入,并对其进行压缩,提高其压力和温度。
冷凝器通过散热的方式,将高温高压气体的热量转移给冷凝器,并将其冷却成为液体。
热泵精馏热力学

热泵精馏热力学
热泵精馏是一种利用热泵技术实现精馏过程的方法。
在传统的精馏过程中,需要消耗大量的热能,而热泵精馏则可以通过回收废热来提供所需的热能,从而实现能量的节约和效率的提高。
热泵精馏的基本原理是利用热泵循环中的低温热源和高温热源,将低温热源的热能转移到高温热源上,以实现对精馏过程的热能供应。
通常情况下,热泵精馏使用的热源可以是工业过程中的废热或环境中的低温热能,如地热、太阳能等。
在热泵精馏中,通过将低温热源的热能吸收到热泵系统中,通过压缩和膨胀过程将热能提升到高温热源的温度水平,然后将高温热源的热能释放给精馏过程。
这样就能够实现对精馏过程中所需热能的供应,从而降低了外部能源的需求。
热泵精馏相对于传统精馏方法的优势在于能够充分利用废热或低温热能,提高能源利用效率,降低能源消耗和碳排放。
然而,热泵精馏的实际应用还面临一些挑战,包括技术成本、系统复杂性和可行性等方面的考虑。
总的来说,热泵精馏是一种利用热泵技术实现精馏过程的能源节约方法,可以通过回收废热或利用低温热能来提供精馏过程所需的热能,从而实现能源的高效利用。
基于分割式热泵的2-甲氧基乙醇-水精馏工艺模拟
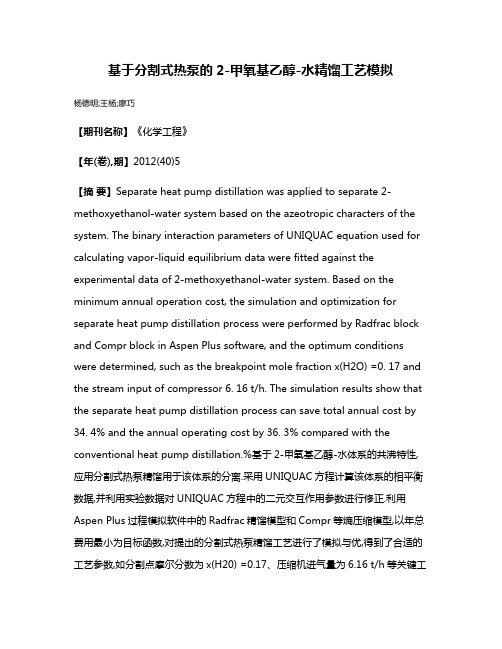
基于分割式热泵的2-甲氧基乙醇-水精馏工艺模拟杨德明;王杨;廖巧【期刊名称】《化学工程》【年(卷),期】2012(40)5【摘要】Separate heat pump distillation was applied to separate 2-methoxyethanol-water system based on the azeotropic characters of the system. The binary interaction parameters of UNIQUAC equation used for calculating vapor-liquid equilibrium data were fitted against the experimental data of 2-methoxyethanol-water system. Based on the minimum annual operation cost, the simulation and optimization for separate heat pump distillation process were performed by Radfrac block and Compr block in Aspen Plus software, and the optimum conditions were determined, such as the breakpoint mole fraction x(H2O) =0. 17 and the stream input of compressor 6. 16 t/h. The simulation results show that the separate heat pump distillation process can save total annual cost by 34. 4% and the annual operating cost by 36. 3% compared with the conventional heat pump distillation.%基于2-甲氧基乙醇-水体系的共沸特性,应用分割式热泵精馏用于该体系的分离.采用UNIQUAC方程计算该体系的相平衡数据,并利用实验数据对UNIQUAC方程中的二元交互作用参数进行修正.利用Aspen Plus过程模拟软件中的Radfrac精馏模型和Compr等熵压缩模型,以年总费用最小为目标函数,对提出的分割式热泵精馏工艺进行了模拟与优,得到了合适的工艺参数,如分割点摩尔分数为x(H20) =0.17、压缩机进气量为6.16 t/h等关键工艺变量.模拟结果表明,与常规热泵精馏工艺相比,分割式热泵精馏工艺的年总费用可节约34.4%,操作费用可节约36.3%.【总页数】5页(P1-5)【作者】杨德明;王杨;廖巧【作者单位】常州大学石油化工学院,江苏常州213164;常州大学石油化工学院,江苏常州213164;常州大学石油化工学院,江苏常州213164【正文语种】中文【中图分类】TQ028【相关文献】1.热泵自夹带共沸精馏分离乙醇-甲苯-水三元共沸混合物 [J], 吕新宇;赵磊;汪文丞;单俊;邱滔2.分割式热泵精馏的研究及其分割点的确定 [J], 朱平;冯霄3.基于MVR热泵精馏的粗甘油脱水提纯工艺模拟研究 [J], 阮宗琳;杨秀娜;姜阳;齐慧敏4.基于中间再沸器的氯化苄热泵精馏工艺模拟 [J], 丁良辉;陈俊明;李乾军;刘从容;薛云波5.水-乙醇-环己醇三元体系精馏分离工艺模拟及优化 [J], 司美玉;陈艳丽;芦亚宁;倪怀兰;林枫因版权原因,仅展示原文概要,查看原文内容请购买。