微特迈WTM-G4L主板
工业微波开关电源.

WepeX Link
24V输入 RS485接口,支持数据上传 一拖18路电源,每个电源端口 就是其物理位置 五位拔码开关,单一RS485接 口支持32个中继板联机操作
WepeX 1600A: 风冷220V 输入,数字通讯,功率可调
WepeX 1280A:风冷, 220V输入,无数字接口,恒 定功率
传统变压器的可靠性问题
传统变压器在以下情况易烧坏:
➢ 电压过高或过低或者波动比较大 ➢ 元器件选的型号不匹配 ➢ 空间环境温度过高 ➢ 环境灰尘多覆盖变压器表面
一旦出现问题,体积 大,重量重,线路复 杂,故障定位和维修 非常困难
WepeX更耐用更易维护
WepeX的可靠性有如下优势:
➢ 对电网适应力强,能承受电压波动 ➢ 一体化设计,不存在元配件不兼容问题 ➢ 散热效率高,不外加风道时工作环境温度也可高达50度 ➢ 拥有铝制外壳保护,无视粉尘灰尘
1664.4 1272.9
0
170 180 190 200 210 220 230 240 264
输入电压(V)
工频变压 器
Wepex
➢ WepeX对电网适应性非常强,在165V~264V范围内稳定工 作;工频变压器工作范围较窄,仅在180V~240V范围内可工作
➢ WepeX在210V~264V区间,功率稳定性可做到+/-20W ; 工频变压器在 210V~264V区间,功率波动达到400W
传统电源方案问题:
➢ 效率低,耗电大 ➢ 电网适应性差(无法功率输出恒定)、兼容性差(无法自适应不同地区电网频率) ➢ 发热量过大,需油冷\风冷装置,成本高 ➢ 分体原件构成,需至少8根线材及接头,加工工时多,可生产性差,可靠性差,故障率高
麦格米特WepeX方案
TWN4 MultiTech 2 LEGIC M LF HF 用户手册.pdf_1697689493

TWN4 MULTITECH 2 LEGIC M LF HFUSER MANUALTABLE OF CONTENTS1INTRODUCTION (3)1.1ABOUT THIS MANUAL (3)1.2SCOPE OF DELIVERY (3)1.3ELATEC SUPPORT (3)2INTENDED USE (4)3SAFETY INFORMATION (5)4TECHNICAL DATA (7)4.1TECHNICAL SPECIFICATIONS (7)4.2FIRMWARE (7)4.3ANTENNAS (7)5MODE OF OPERATION (8)5.1OPERATING MODE (8)5.2POWER UP (8)5.3ENUMERATION (8)5.4INITIALIZATION (8)5.5NORMAL OPERATION (8)5.6DETECTION OF A TRANSPONDER (8)5.7SUSPEND MODE (9)6COMPLIANCE STATEMENTS (10)6.1EU (10)6.2FCC (10)6.3ISED CANADA (10)6.4RF EXPOSURE COMPLIANCE (11)6.5CHINA (PRC) / 中华人民共和国 (11)6.6UNITED KINGDOM (12)APPENDIX (13)A – RELEVANT DOCUMENTATION (13)B – TERMS AND ABBREVIATIONS (13)C – REVISION HISTORY (13)1INTRODUCTION1.1ABOUT THIS MANUALThis user manual is intended for the user and enables a safe and appropriate handling of the product. It gives a general overview, as well as important technical data and safety information about the product. Before using the product, the user should read and understand the content of this user manual.For the sake of better understanding and readability, this user manual might contain exemplary pictures, drawings and other illustrations. Depending on your product configuration, these pictures might differ from the actual design of your product.The original version of this user manual has been written in English. Wherever the user manual is available in another language, it is considered as a translation of the original document for information purposes only. In case of discrepancy, the original version in English will prevail.1.2SCOPE OF DELIVERYDepending on your product configuration, the product can be delivered alone or with different components and accessories, such as cables or wall holders, as part of a kit. For more information about the delivered components and accessories, refer to your delivery note, consult the ELATEC website or contact ELATEC.1.3ELATEC SUPPORTIn case of any technical questions or product malfunction, refer to the ELATEC website () or contact ELATEC technical support at***********************In case of questions regarding your product order, contact your Sales representative or ELATEC customer service at********************2INTENDED USEThe contactless RFID readers and modules of the ELATEC TWN4 MultiTech 2 LEGIC family are a direct enhancement of the TWN4 MultiTech LEGIC readers with the same form factors (PCB modules and desktop readers with housing). During the development of the TWN4 MultiTech 2 LEGIC family, special emphasis has been placed on optimizing the HF performance (13.56 MHz). Compared to the predecessor TWN4 MultiTech LEGIC, the read range could be increased by more than 50% for LEGIC transponders and even doubled for some HF transponders.TWN4 MultiTech 2 LEGIC M LF HF key features include a powerful SDK for writing apps that are executed directly on the module, the possibility to upgrade the firmware in the field and a direct chip-commands support. Additionally, the module can simultaneously read more than 60 RFID technologies from low (LF) and high frequency (HF) bands, including NFC. This gives the option to select as many of the technologies required instead of being forced to select just a few ones.The product is intended to be integrated into a host device.Any use other than the intended use described in this section, as well as any failure to comply with the safety information given in this document, is considered improper use. ELATEC excludes any liability in case of improper use or faulty product installation.3SAFETY INFORMATIONTransport and storage•Observe carefully the transport and storage conditions described on the product packaging or other relevant product documents(e.g. data sheet).Unpacking and installation•Before unpacking and installing the product, this user manual and all relevant installation instructions must be read and understood carefully.•The product might show sharp edges or corners and requires a particular attention during the unpacking and installation.Unpack the product carefully and do not touch any sharp edges or corners, or any sensitive components on the product.If necessary, wear safety gloves.•In case the product is equipped with a cable, do not twist or pull the cable.•The product is an electronic product whose installation requires specific skills and expertise.The installation of the product should be done by a trained and qualified personnel only.Handling•Depending on your product configuration, the product might be equipped with one or more light-emitting diodes (LED).Avoid direct eye contact with the blinking or steady light of the light-emitting diodes.•The product has been designed for a use under specific conditions, e.g. in a specific temperature range (refer to the product data sheet).Any use of the product under different conditions might damage the product or alter its reading performance.•The use of other RFID readers or reader modules in direct vicinity to the product, or in combination with the product might damage the product or alter its reading performance. In case of doubts, contact ELATEC for more information.•The user is liable for the use of spare parts or accessories other than the ones sold or recommended by ELATEC.ELATEC excludes any liability for damages or injuries resulting from the use of spare parts or accessories other than the ones sold or recommended by ELATEC.•In case the product is equipped with a cable, the cable may not be replaced or extended.ELATEC excludes any liability for damages or injuries resulting from the use of the product with a cable extension or a replaced cable.•Like most electronic devices, RFID systems generate electromagnetic waves that can vary in amplitude and frequency. It is generally known and accepted that some RFID devices might potentially interfere with personal medical devices, like pacemakers or hearing aids.TWN4 MultiTech 2 LEGIC M LF HF fulfills general radio and EMC requirements. However, users with a pacemaker or any other medical device should use TWN4 MultiTech 2 LEGIC M LF HF carefully and refer to the information given by the manufacturer of their medical devices before using TWN4 MultiTech 2 LEGIC M LF HF or any host device containing TWN4 MultiTech 2 LEGIC M LF HF.Maintenance and cleaning•Any repair or maintenance work should be done by a trained and qualified personnel only.Do not try to repair or carry out any maintenance work on the product by yourself.Do not allow any repair or maintenance work on the product by an unqualified or unauthorized third party.•The product does not need any special cleaning.Do not use any detergents or other cleaning agents on the product.Disposal•The product must be disposed of in accordance with the EU directive on waste electrical and electronic equipment (WEEE) or any applicable local regulations.Product modifications•The product has been designed, manufactured and certified as defined by ELATEC.Any product modification without prior written approval from ELATEC is prohibited and considered improper use of the product. Unauthorized product modifications may also result in the loss of product certifications.If you are unsure about any part of the safety information above, contact ELATEC support.Any failure to comply with the safety information given in this document is considered improper use. ELATEC excludes any liability in case of improper use or faulty product installation.4TECHNICAL DATA4.1TECHNICAL SPECIFICATIONSFREQUENCY 125 KHZ (LF) / 13.56 MHZ (HF) ANTENNA(S) IntegratedDIMENSIONS (L X W X H) Approx. 76 x 49 x 9 mm / 3.0 x 1.9 x 0.4 inchPOWER USB: 4.3 V - 5.5 VGeneric interface (X1): 3.3 V ± 5%RS-232: requires 5 V external power supplyPS2 classified power source according to IEC 62368-1, short-circuit current < 8 ACURRENT CONSUMPTION RF field on: 140 mA typicallyTEMPERATURE RANGE Operating: -25 °C up to +80 °C (-13 °F up to +176 °F) Storage: -40 °C up to +85 °C (-40 °F up to +185 °F)RELATIVE HUMIDITY 5% to 95% non-condensingREAD/WRITE DISTANCE LF and HF: Up to 100 mm / 4 inch, depending on environment and transponder WEIGHT Approx. 10 g / 0.35 oz (without cable)4.2FIRMWAREThe product is delivered ex-works with a specific firmware version. Refer to the label attached to the product to find the firmware version installed ex-works.4.3ANTENNASThe reader module is equipped with the following antennas:HF antenna (13.56 MHz)Dimensions: 42 x 47 mm / 1.65 x 1.85 inchNumber of turns: 3LF antenna (125 kHz)Diameter: 16 mm / 0.63 inchNumber of turns: 120For more information, refer to the related product data sheet or other technical documents.5MODE OF OPERATIONThe mode of operation described in the following chapter is based on a standard ELATEC RFID reader module equipped with two LEDs. Depending on your product (number of LEDs, installed firmware, etc.) and in case the product settings have been modified with the AppBlaster tool, the information below might differ from your product configuration when in operation. In particular, the color and sequence of the LEDs on your product might be different.5.1OPERATING MODEIn order to start operating TWN4 MultiTech 2 LEGIC M LF HF, it simply has to be connected directly to a host device.5.2POWER UPOnce TWN4 MultiTech 2 LEGIC M LF HF is connected to the host device, it detects the type of communications cable (e.g. USB or RS-232), with which it is connected to the host.In case of RS-232:• A version string is sent via RS-232 to the host device.• A 5 V external power supply is required and must meet the following conditions:o PS2 classified power source according to IEC 62368-1o Short-circuit current < 8 A5.3ENUMERATIONThis is only applicable for the USB version: Once the device has been powered up, it is waiting for completion of the enumeration by the USB host. As long as the device is not enumerated, it is entering a minimum power consumption mode, where both LEDs are turned off.5.4INITIALIZATIONAfter powering up and enumeration (in USB mode), the device is turning on the built-in transponder reader logic. The green LED is turned on permanently. Some RFID reader modules need some kind of initialization, which is performed in this step. After successful initialization, the device sounds a short sequence, which consists of a lower tone followed by a higher tone.5.5NORMAL OPERATIONAs soon as the reader module has completed the initialization, it is entering normal operation. During normal operation, the module is searching for a transponder continuously.5.6DETECTION OF A TRANSPONDERIf a transponder is detected by the reader module, following actions are performed:•Send the ID to the host. By default, the USB device sends by emulating keystrokes of a keyboard. An RS-232 device sends the ASCII code of an ID.•Sound a beep.•Turn off the green LED.•Blink the red LED for two seconds.•Turn on the green LED.Within the two seconds timeout, where the red LED is blinking, the transponder, which just has been recognized will not be accepted again. This prevents the reader module from sending identical IDs more than one time to the host.If during the two seconds timeout of the red LED a different transponder is detected, the complete sequence restarts immediately. 5.7SUSPEND MODEThe USB version of the reader module supports the USB suspend mode. If the USB host is signaling suspend via the USB bus, the reader module is turning off most of its power consuming peripherals. During this operation mode, no detection of transponders is possible and all LEDs are turned off. Once the host is resuming to normal operation mode, this is also signaled via the USB bus. Therefore, the reader module will resume to normal operation too.6COMPLIANCE STATEMENTS6.1EUHereby, ELATEC GmbH declares that TWN4 MultiTech 2 LEGIC M LF HF is in compliance with Directive 2014/53/EU. The full text of the EU declaration of conformity is available at the following internet address: /approvals6.2FCCFCC ID: WP5TWN4F22This device complies with Part 15 of the FCC Rules. Operation is subject to the following two conditions:(1) this device may not cause harmful interference, and(2) this device must accept any interference received, including interference that may cause undesired operation. (except receivers associated with operation of a licensed radio service and stand-alone devices).CautionThe Federal Communications Commission (FCC) warns the users that changes or modifications to the unit not expressly approved by the party responsible for compliance could void the user's authority to operate the equipment.FCC §15.105 (b)Note: This equipment has been tested and found to comply with the limits for a Class B digital device, pursuant to part 15 of the FCC Rules. These limits are designed to provide reasonable protection against harmful interference in a residential installation. This equipment generates, uses and can radiate radio frequency energy and, if not installed and used in accordance with the instructions, may cause harmful interference to radio communications. However, there is no guarantee that interference will not occur in a particular installation. If this equipment does cause harmful interference to radio or television reception, which can be determined by turning the equipment off and on, the user is encouraged to try to correct the interference by one or more of the following measures: •Reorient or relocate the receiving antenna.•Increase the separation between the equipment and receiver.•Connect the equipment into an outlet on a circuit different from that to which the receiver is connected.•Consult the dealer or an experienced radio/TV technician for help.6.3ISED CANADAIC: 7948A-TWN4F22This device contains licence-exempt transmitter(s)/receiver(s) that comply with Innovation, Science and Economic Development Canada’s licence-exempt RSS(s). Operation is subject to the following two conditions:1. This device may not cause interference.2. This device must accept any interference, including interference that may cause undesired operation of the device.L’émetteur/récepteur exempt de licence contenu dans le présent appareil est conforme aux CNR d’Innovation, Sciences et Développement économique Canada applicables aux appareils radio exempts de licence. L’exploitation est autorisée aux deux conditions suivantes:1. L’appareil ne doit pas produire de brouillage;2. L’appareil doit accepter tout brouillage radioélectrique subi, même si le brouillage est susceptible d’en compromettre le fonctionnement.6.4RF EXPOSURE COMPLIANCERF exposure statement (mobile and fixed devices)This device complies with the RF exposure requirements for mobile and fixed devices. However, the device shall be used in such a manner that the potential for human contact during normal operation is minimized.6.5CHINA (PRC) / 中华人民共和国Micropower scope of use declaration:TWN4 MultiTech 2 LEGIC M LF HF supports transmission frequencies of 13.56 MHz and 125 kHz. The user needs to adhere to the following specifications when using the product:(1) The specific provisions listed in the “catalog and the technical specifications for micropower short-range radio transmission equipment” as well as the usage scenarios for the antenna type used, the functions, and the customary use of the control system, regulation, and switches must be complied with;Transmission power:13.56 MHz: ≤ -9.06 dBμA/m(field strength at 10 meters, standard max value)125 kHz: ≤ -20.04 dBμA/m(field strength at 10 meters, standard max value)Antenna: built-in antenna (cannot be removed)Control system, regulation, and switches: The user cannot control, regulate, or switch over the radio transmission function of the antenna.(2) The unauthorized modification of usage scenarios or the conditions of use, expansion of the transmission frequency range, or increase of the transmission power (including installing additional transmission power amplifiers), as well as the unauthorized modification of the transmission antenna are not allowed;(3) The product may not interfere in any way with any legal radio transmitters (stations) and may not offer any shielding from harmful interference;(4) The product must be able to tolerate interference caused by industrial, scientific, and medical (ISM) devices which radiate high frequency energy or other legal interference from radio transmitters (stations);(5) Should the product cause harmful interference on other legal radio transmitters (stations), product use must be discontinued 微功率使用规范声明:TWN4 MultiTech 2 LEGIC M LF HF支持13.56MHz和125kHz发射频率,用户在使用过程中,需要遵守以下要求:(一)符合“微功率短距离无线电发射设备目录和技术要求”的具体条款和使用场景,采用的天线类型和性能,控制、调整及开关等使用方法;发射功率:13.56MHz:≤ -9.06dBμA/m(10米处场强,准峰值)125kHz:≤-20.04dBμA/m(10米处场强,准峰值)天线:内置天线(不可拆卸)控制、调整及开关:用户不能控制、调制及开关此无线电发射功能(二)不得擅自改变使用场景或使用条件、扩大发射频率范围、加大发射功率(包括额外加装射频功率放大器),不得擅自更改发射天线;(三)不得对其他合法的无线电台(站)产生有害干扰,也不得提出免受有害干扰保护;(四)应当承受辐射射频能量的工业、科学及医疗(ISM )应用设备的干扰或其他合法的无线电台(站)干扰;(五)如对其他合法的无线电台(站)产生有害干扰时,应立即停止使用,并采取措施消除干扰后方可继续使用;(六)在航空器内和依据法律法规、国家有关规定、标准划设的射电天文台、气象雷达站、卫星地球站(含测控、测距、接收、导航站)等军民用无线电台(站)、immediately and suitable measures must be taken prior to using the product again in order to eliminate said interference; (6) When using micropower devices inside of an aircraft or radiometric observatories, or when using such devices in meteorological radar stations, satellite ground stations (including measuring and control stations, distance measuring stations, receiving stations, or navigation stations), as well as in radio transmitters (stations) used by the military and electromagnetic environment protections zones at airports, all applicable provisions of the competent authorities as well as statutory provisions, national regulations, and national standards must be complied with;(7) Remote controls of any kind may not be used within 5000 meters of airport runways, measured from the middle of the runway;(8) Ambient conditions such as temperature and voltage when using micropower devices:operating voltage of TWN4 MultiTech 2 LEGIC M LF HF: 4.3 V – 5.5 V (charging via USB),operating temperature: -25 °C – +80 °C,storage temperature: -40 °C – +85 °C.The user must strictly adhere to these temperature and voltage specifications when using the product. 机场等的电磁环境保护区域内使用微功率设备,应当遵守电磁环境保护及相关行业主管部门的规定;(七)禁止在以机场跑道中心点为圆心、半径5000米的区域内使用各类模型遥控器;(八)微功率设备使用时温度和电压的环境条件。
无刷直流通道闸控制主板(一拖二)用户手册(V4.0)
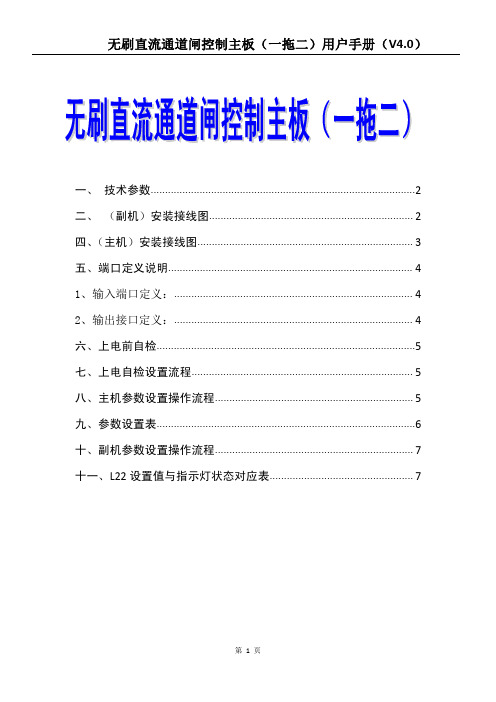
一、技术参数 (2)二、(副机)安装接线图 (2)四、(主机)安装接线图 (3)五、端口定义说明 (4)1、输入端口定义: (4)2、输出接口定义: (4)六、上电前自检 (5)七、上电自检设置流程 (5)八、主机参数设置操作流程 (5)九、参数设置表 (6)十、副机参数设置操作流程 (7)十一、L22设置值与指示灯状态对应表 (7)一、技术参数二、(副机)安装接线图四、(主机)安装接线图五、端口定义说明1、输入端口定义:K1:K1方向有效的刷卡(通行)信号输入接口K2:K2方向有效的刷卡(通行)信号输入接口报警:非法刷卡(通行)信号输入接口/或安全门联锁信号输入接口消防:消防信号输入接口红外1:为其中一个方向的入口红外传感器第一路输入接口红外2:为其中一个方向的入口红外传感器第二路输入接口红外3:为中间防夹红外传感器第一路输入接口红外4:为中间防夹红外传感器第二路输入接口红外5:为另一个方向的入口红外传感器第二路输入接口红外6:为另一个方向的入口红外传感器第一路输入接口※注:1、如需接8对红外,红外3和红外4接口各并接2对红外。
L-17参数选择还是选择6对红外模式。
2、红外3与红外4分别各接一路红外,效果更好。
如只想接一路红外,请将红外3与红外4短接后接一路红外,不短接将不能正常工作,请注意!!!2、输出接口定义:K1绿灯:顶盖灯K1方向绿灯控制端口(有12V输出)K2绿灯:顶盖灯K2方向绿灯控制端口(有12V输出)红灯:顶盖灯红灯控制端口(有12V输出)计数器1输出:K1方向进入通道过人后计数信号输出(无源触点)计数器2输出:K2方向进入通道过人后计数信号输出(无源触点)主副机通讯接口:TB1,TA1,两芯线同步主副板接线一致就好。
六、上电前自检道闸上电前,请务必检查好以下几项:1、供电电源为24V 10A 的直流电源。
2、所有外接线(电源线、电机线)等的极性、顺序是否正确,且连接牢固走线稳定。
Elatec TWN4 MultiTech M User Manual
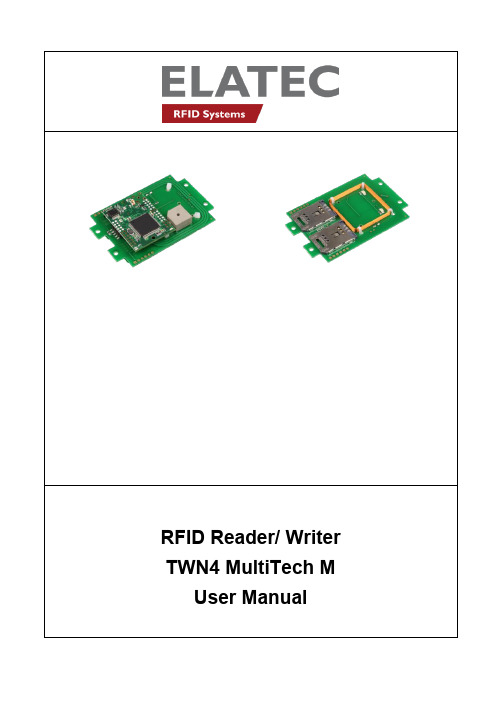
1. IntroductionThe transponder reader module TWN4 MultiTech M is a device for reading and writing RFID transponders. There are different versions of TWN4 devices available, which cover a large range of transponder types both in the frequency range of 125kHz and 13.56MHz.2. Getting Started2.1 Cable ConnectionIn order to start operating a TWN4 transponder reader, it simply has to be connected to a host.2.2 EnumerationOnce the device has been powered up, it is waiting for completion of the enumeration by the USB host. As long as the device is not enumerated, it is entering a minimum power consumption mode, where both LEDs are turned off.2.3 InitializationAfter powering up and enumeration, the device is turning on the built-in transponder reader logic. The green LED is turned on permanently. Some transponder readers need some kind of initialization, which is performed inthis step. After successful initialization, the device sounds a short sequence, which consists of a lower tone followed by a higher tone.2.4 Normal OperationAs soon as the device has completed the initialization, it is entering normal operation. During normal operation the device is searching for a transponder continuously.Detection of a TransponderIf a transponder is detected by the reader, following actions are performed ∙Send the ID to the host. By default, the USB device sends by emulating keystrokes of a keyboard.∙Sound a beep∙Turn off the green LED∙Blink the red LED for two seconds∙Turn on the green LEDWithin the two seconds timeout, where the red LED is blinking, the transponder, which just has been recognized will not be accepted again. This prevents the reader from sending identical IDs more than one time to the host.If during the two seconds timeout of the red LED a different transponder is detected, the complete sequence restarts immediately.Suspend ModeThe transponder reader supports the USB suspend mode. If the USB host is signaling suspend via the USB bus, the transponder reader is turning off most of its power consuming peripherals. During this operation mode, no detection of transponders is possible and all LEDs are turned off.Once the host is resuming to normal operation mode, this is also signaled via the USB bus. Therefore, the transponder reader will resume to normal operation, too.3. List of Antennas HF antennaLF antenna4. Compliance statementsFCC(RF module)Compliance statement:This device complies with Part 15 of the FCC Rules. Operation is subject to the following two conditions: (1) this device may not cause harmful interference, and (2) this device must accept any interference received, including interference that may cause undesired operation.Modification of equipment:The instruction manual of the host shall include the following statement: Changes or modifications made to this equipment not expressly approved by the party responsible for compliance may void the FCC authorization to operate this equipment.Information to the user:(The instruction manual of the host shall include the following statement) A compliance statement as applicable, e.g., for devices subject to part 15 of CFR 47 as specified in §15.19(a)(3), that the product complies with the rules; and the identification, by name, address and telephone number or Internet contact information, of the responsible party, as defined in §2.909. The responsible party for Supplier’s Declaration of Conformity must be located within the United States.Host devicesFCC notes for a host subject to verification or SDoC:For a host device assembled with the certified module and subject to 47 CFR Part 15 verification of class A digital devices, the following statements have to be included in the user manual and the host device has to be labelled as noted below. If the host device is subject to other authorization procedures or parts the appropriate requirements of these authorization procedures or parts apply.Important note:OEM integrator is still responsible for the FCC compliance requirements of the end product, which integrates this module. Appropriate measurements (e.g. 15B compliance) and if applicable additional equipment authorization of the host device to be addressed by the integrator/ manufacturerThe end device must be labeled with:Contains FCC ID: WP5TWN4F17Contains IC: 7948A-TWN4F17HVIN: EL20208Example for SDoC:The compliance information statement shall be included in the user's manual or as a separate sheet. In cases where the manual is provided only in a form other than paper, such as on a computer disk or over the Internet, the information required by this section may be included in the manual in that alternative form, provided the user can reasonably be expected to have the capability to access information in that form. The information may be provided electronically as permitted in §2.935.NOTE: The Commission does not have a required SDoC format. This is an example only and is provided to illustrate the type of information that may be supplied with the product at the time of marketing or importation for meeting the FCC SDoC requirement.For class B devices:FCC §15.105 (b):Note: This equipment has been tested and found to comply with the limits for a Class B digital device, pursuant to part 15 of the FCC Rules. These limits are designed to provide reasonable protection against harmful interference in a residential installation. This equipment generates, uses and can radiate radio frequency energy and, if not installed and used in accordance with the instructions, may cause harmful interference to radio communications. However, there is no guarantee that interference will not occur in a particular installation. If this equipment does cause harmful interference to radio or television reception, which can be determined by turning the equipment off and on, the user is encouraged to try to correct the interference by one or more of the following measures:- Reorient or relocate the receiving antenna.- Increase the separation between the equipment and receiver.- Connect the equipment into an outlet on a circuit different from that to which the Receiver is connected.- Consult the dealer or an experienced radio/TV technician for help.For class A devices:FCC §15.105 (b):NOTE: This equipment has been tested and found to comply with the limits for a Class A digital device, pursuant to part 15 of the FCC Rules. These limits are designed to provide reasonable protection against harmful interference when the equipment is operated in a commercial environment. This equipment generates, uses, and can radiate radio frequency energy and, if not installed and used in accordance with the instruction manual, may cause harmful interference to radio communications. Operation of this equipment in a residential area is likely to cause harmful interference in which case the user will be required to correct the interference at his own expense.CANADA:This device complies with Industry Canada’s license-exempt RSSs. Operation is subject to the following two conditions:(1) This device may not cause interference; and(2) This device must accept any interference, including interference that may cause undesired operation of the device.Le présent appareil est conforme aux CNR d’Industrie Canada applicables aux appareils radio exempts de l icence. L’exploitation est autorisée aux deux conditions suivantes:1) l’appareil ne doit pas produire de brouillage;2) l’utilisateur de l’appareil doit accepter tout brouillage radioélectrique subi, même si le brouillage est susceptible d’en compr omettre le fonctionnement. Special accessories:Where special accessories such as shielded cables and/or special connectors are required to comply with the emission limits, the instruction manual shall include appropriate instructions on the first page of the text describing the installation of the device.Simultaneous transmission:When the host product supports simultaneous-transmission operations the host manufacturer needs to check if there are additional RF exposure filing requirements due to the simultaneous transmissions. When additionalapplication filing for RF exposure compliance demonstration is not required (e. g. the RF module in combination with all simultaneously operating transmitters complies with the RFexposure simultaneous transmission SAR test exclusion requirements), the host manufacturer may do his own evaluation without any filing, using reasonable engineering judgment and testing for confirming compliance with out-of-band, restricted band, and spurious emission requirements in the simultaneous-transmission operating modes. If additional filing is required please contact the person at ELATEC GmbH responsible for certification of the RF module.5. Service AddressIn case of any technical questions, please contact: Elatec GmbHZeppelinstr. 182178 PuchheimGermanyPhone: +49 (0) 89 5529961 0Fax: +49 (0) 89 5529961 29Email: ********************6. TrademarksAll referenced brands, product names, service names and trademarks mentioned in this document are the property of their respective owners.。
CNC USB Controller Mk3 4 用户手册说明书
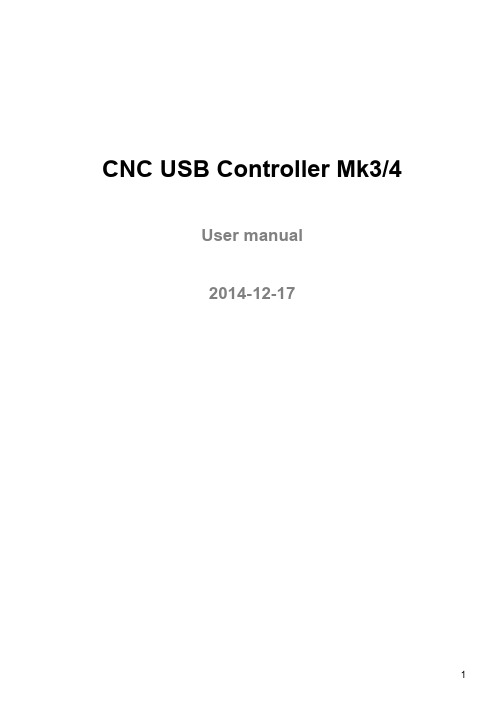
CNC USB Controller Mk3/4User manual2014-12-17DisclaimerCONTROLLER AND CONTROLLER SOFTWARE ARE PROVIDED TO YOU"AS IS,"WITHOUT WARRANTY.THERE IS NO WARRANTY FOR THE CONTROLLER AND CONTROLLER SOFTWARE,EITHER EXPRESSED OR IMPLIED,INCLUDING,BUT NOT LIMITED TO,THE IMPLIED WARRANTIES OF MERCHANTABILITY AND FITNESS FOR A PARTICULAR PURPOSE AND NONINFRINGEMENT OF THIRD PARTY RIGHTS. THE ENTIRE RISK AS TO THE QUALITY AND PERFORMANCE OF THE CONTROLLER OR CONTROLLER SOFTWARE IS WITH YOU. SHOULD THE CONTROLLER OR CONTROLLER SOFTWARE PROVE DEFECTIVE, YOU ASSUME THE COST OF ALL NECESSARY SERVICING, REPAIR OR CORRECTION.IN NO EVENT SHALL THE AUTHOR BE LIABLE TO YOU FOR DAMAGES,INCLUDING ANY GENERAL, SPECIAL, INCIDENTAL OR CONSEQUENTIAL DAMAGES ARISING OUT OF THE USE OR INABILITY TO USE THE CONTROLLER OR CONTROLLER SOFTWARE.1Introduction1.1OverviewThe PlanetCNC series of USB CNC motion controllers is link between a personal computer and motor drivers supporting step/direction control. PlanetCNC series of motion controllers are compatible with most motor drivers. The controllers use the USB port, available on all modern computers and laptops. They can serve as direct replacement or upgrade for many parallel port break-out boards.PlanetCNC controllers provide a complete, fully integrated software/hardware solution. Additional machine control software is NOT required. The USB CNC Controller software is a dedicated application, designed to fully exploit the features of the purpose-built hardware. It has many advanced features to assist day-to-day CNC machine operation.1.2Features and specifications:•USB (V2.x) from PC/Laptop running Windows XP, Vista, Windows 7, 8 or 8.1 (32 bit or 64bit)•motor driver connector pin-out is compatible with 10 pin open source interface (Linistepper, PICStep)•controller works with most step/dir stepper and servo motor drivers available on the market •buffered IO for maximum performance•advanced interpolation algorithms•start, stop, pause and resume execution of program on your machine•standard RS274/NGC G-code (EMC2 and LinuxCNC compatible)•advanced G-codes - G40, G41, G42 (Cutter Radius Compensation) supported•advanced G-codes - G43, G49 (Tool Length Offsets) supported•advanced G-codes - G54, G59.3 (Coordinate System Origins) supported•tested with SolidCAM, MasterCAM, ArtCAM, Vectric, CamBam, MeshCAM ... generated G-code •Profili 4-axes and 3-axes G-code supported•import toolpath from DXF files•import toolpath from PLT/HPGL files•import toolpath from image files•import toolpath from NC-Drill (Excellon) files•import toolpath from Gerber (RS-274X) files•toolpath simulation•automatic homing procedure•advanced toolchange procedures•automatic tool length measuring•export toolpath to G-code•export toolpath to DXF•SDK (software developers kit) is available•works on MacOS with virtual machine emulating WindowsMk3/4 - 4 axes USB CNC controller• 4 axes controller for stepper and servo motors•USB connection•110 kHz maximum step frequency•25 us minimum pulse width, 50% duty cycle at higher frequencies• 3 digital outputs on board• 3 PWM capable outputs with selectable frequency (10Hz to 500kHz)• 3 outputs with support for RC servo motors•jogging keyboard support with speed potentiometer, shift, step and spindle sync feature• 4 limit switches with shift feature• 4 digital inputs on board, filtered and protected•spindle encoder and index signal support for spindle synchronization•SD card support for running g-code without computer•control external devices with I2C and UART protocol•homing procedure•tool change procedure•tool length sensor support•sensor for capturing and measuring•digitizing probe support•H-bot kinematics support•transformation matrix•soft limits•slave axes•backlash compensation•API•screw terminal connectors for connecting motor drivers, inputs and outputs1.3System RequirementsMinimum system requirements:• 1 GHz or faster processor•512MB RAM•500 MB available hard disk space•Graphics with OpenGL support•USB 2.0 port•.NET Framework 3.5 SP1Recommended system requirements:• 2 GHz or faster processor•2GB RAM•500 MB available hard disk space•Graphics with OpenGL support•USB 2.0 port•.NET Framework 3.5 SP12Hardware2.1InstallationInstallation of PlanetCNC CNC USB Controller requires a USB equipped PC or laptop along with motor drivers appropriate to the motors in use. The USB CNC controller is compatible with the vast majority of motor drivers that use step/direction signals.Optional support hardware can be employed to customize installation to suit user requirement. Use of a screw terminal adapter makes connection to the type of drive in the image much easier. A DB25 adapter is available, for motor drivers requiring this form of input, with male or female DB25 connector.For maximum flexibility in controller layout, a ribbon cable and plug kit is available. This aids the construction of longer cables and ensures plug-in connections correspond to the USB CNC Controller pin outs.IMPORTANT:The controller should be powered with an external power supply.Mk3/4 - 4 Axis controller hardware requires 8 - 24V DC supply.Power supply should be at least 200mA.2.2Mk3/4 - 4 axis CNC USB controller description2.2.1Mk3/4 AXIS connectorEach connector controls one motor driver. Controller has 4 connectors for axes 1-4.Pins 2, 4, 6,7, 8 and 10 provide the ‘Ground’ or common side of connections.All signals are also available on screw type connector and 25 pin header.Axes are usually named like this: Axis 1=X, Axis 2=Y, Axis 3=Z...On some machines this can be different. For example foam cutter uses names such as Axis 1=A, Axis 2=Y, Axis 3=U, Axis 4=V. Lathes use Axis 1=Z, Axis 2=X. Configuration of axes, as well as their naming can be set in File/Settings/Axes.CONNECTOR PIN DESCRIPTION:+5V:+5V power. Motor drivers can take power for logic circuit or common anode connection from the USB controller.STEP:Provides a STEP signal of minimum 12 us pulse width to the motor driver.DIR:Provides DIR or DIRECTION signal to the motor driver.ENABLE:Provides an ENABLE signal for motor drivers. When the ENABLE signal is lost due to output command, E-Stop or limit switch activation, motor drivers will deactivate.A dedicated E-Stop switch connected to the CTRL or INPUT connector can control thesignal. It can also be operated by limit switch activation, software command or onshutdown of the control software.This arrangement provides a useful safety feature that can be user-configured to operateunder manual and/or computer control.GND:Ground connections.2.2.2Mk3/4 JOG connectorSwitched operation of JOG 1-8 controls manual jogging.Jogging keyboards can use a ‘SHIFT’ key, allowing Mk3/4 controller users to jog additional axes or toggle the option of jog ‘step’ mode. ‘SHIFT’ key function is defined in settings, as is the ‘step’ value for each key press.Jogging directions and axis assignment can be defined in 'settings'.CONNECTOR PIN DESCRIPTION:A typical use might be as below:JOG 1: Jog Axis 1 in negative direction.JOG 2: Jog Axis 1 in positive direction.JOG 3: Jog Axis 2 in negative direction.JOG 4: Jog Axis 2 in positive direction.JOG 5: Jog Axis 3 in negative direction.JOG 6: Jog Axis 3 in positive direction.JOG 7: Jog Axis 4 in negative direction.JOG 8: Jog Axis 4 in positive direction.SHIFT: Toggles 'step' jog mode or jogging for additional axes.ALT1:Selects different jog modeALT2:Selects different jog mode+3.3V: Power for jogging speed POTPOT:Jogging speed POTGND:Ground connections2.2.3Mk3/4 LIMIT connectorLIMIT 1-4 connects limit switches. It’s recommended that a 100nF capacitor is connecteddirectly across switch terminals. Switches are connected between LIMIT pin and GND pin.Mk3/4 controller requires 'Single Input' mode.SINGLE INPUT:Both axis limit switches are connected to one pin.Direction of travel determines if positive or negative switch is triggered.LIMIT 4: Axis 4 positive and negative limit.LIMIT 3: Axis 3 positive and negative limit.LIMIT 2: Axis 2 positive and negative limit.LIMIT 1: Axis 1 positive and negative limit.GND:GroundNOTE: If 'normally open' (NO) type switches are used, wiring must be done in parallel method, if'normally closed' (NC) type switches are used, wiring must be done in serial method.Software 'Invert' options allow use of ‘normally closed’ or ‘normally open’ switch hardware. This feature can be set in File/Settings/Limit/Invert2.2.4Mk3/4 CTRL connectorThis connector provides inputs for use of encoder devices and E-Stop.Spindle speed encoder for spindle synchronization can also be connected.GND pins provide ‘Ground’ or common connections.An E-Stop switch attached to this connector can be configured in software to activate/deactivate E-Stop.E-Stop switch hardware for use with this connector can be NC (Normally Closed) or NO (Normally Open). If NC is used, 'Invert' feature must be enabled in 'settings'. Locking switch is recommended.CONNECTOR PIN DESCRIPTION:E-STOP:E-StopIDX:Index signal for spindle synchronizationENC A:Encoder for spindle synchronizationENC B:Encoder for spindle synchronizationGND: GroundThis connector provides input for user-assigned functions. CONNECTOR PIN DESCRIPTION:IN4:Assignable input 4IN3:Assignable input 3IN2:Assignable input 2IN1:Assignable input 1GND:GroundThis connector provides 3 digital outputs for control of external devices.The optional ‘Output board’ links to the Mk3/4 controller using this connector. Output assignment is controlled in software.CONNECTOR PIN DESCRIPTION:OUT 6:Digital OutputOUT 2:Digital OutputOUT 1:Digital OutputGND:Ground connections+5V: +5V supply.OUT 1, 2 and 6 can generate PWM signal, RC servo signal or frequency modulation.2.2.7Mk3/4 26 pin headerPin 1:ENAPin 2:STEP 1Pin 3:DIR 1Pin 4:STEP 2Pin 5:DIR 2Pin 6:STEP 3Pin 7:DIR 3Pin 8:STEP 4Pin 9:DIR 4Pin 10:E-STOPPin 11:LIMIT 1Pin 12:LIMIT 2Pin 13:LIMIT 3Pin 14:OUT 6Pin 15:IN 1Pin 16:OUT 1Pin 17:OUT 2Pin 18:NCPins 19-25:GNDPin 26:NC/+5V2.2.8Mk3/4 SD&I2C connectorThis connector allows use of SD Card with PlanetCNC SD card adapter, I2C and UART protocol devices.DAT0: SD card signalCMD: SD card signalCLK:SD card signalTX: UART signalI2C CL: I2C signalI2C DA:I2C signalGND: Ground+3.3V: +3.3V supplyGND: Ground+5V: +5.0V supply2.2.9Mk3/4 USB connectorThe Mk3/4 USB CNC controller connects to computer via the USB port. The port uses the USB 2.x standard.2.2.10Mk3/4 Power terminalThe controller should be powered with an external power supply.Mk3/4 - 4 Axis controller hardware requires 8 - 24V DC supplyPower supply should be at least 200mA2.2.11Mk3/4 LED indicatorsThe user is provided with helpful feedback and live ‘status’ information via on-board LED indicators. There are four indicators.POWER: Lights when the controller is powered.DATA:Indicates controller functions.LINK:Indicates controller communication.STATUS: Blinks to indicate controller function is ‘good’.3Connection diagrams3.1Wiring of limit switchesMk3/4 controller has 4 designated limit switch inputs. This means that 'Single Input' method of wiring must be used.When 'Single input' method is used, both limit switches are connected to one limit pin.Mk3/4 has screw type connector already mounted on the board, which makes the connection even simpler.3.1.1'Single input' wiring methods:3.1.1.1Parallel wiring of NO type switches:Parallel wiring of NO type limit switches*:*On this picture only for axis one.3.1.1.2Serial wiring of NC type limit switches:Serial wiring of NC type limit switches*:*On this picture only for axis one.3.2Wiring inputs of Mk3/4 controllerMk3/4 has 4 assignable inputs. Bellow is wiring diagram of switch connected to Mk3/4's assignable input. Inputs function is assigned in settings.3.3Connecting motor driver to Mk3/4 controllerWiring diagrams for COMMON CATHODE and COMMON ANODE connection of motor driver:*STEP input on motor drivers can be also labeled as PUL or CLK.Picture bellow demonstrates the connection of 2.5A Motor driver to Mk3/4 controller and connection of stepper motor and power supply to 2.5A motor driver. Since this motor driver uses 10-pin header and ribbon cable, connection is pretty much trivial:Picture bellow demonstrates connection of motor driver to Mk3/4 controller and connection of controllers external power supply:3.4Shielded cablesWe always recommend the use of shielded cables for wiring. Whether you are connecting limit switches, input switches, output devices, motor drivers or motors etc... The shielded cables should be properly maintained and set with insulated ferrules or crimp terminals.Picture bellow demonstrates both ends of one shielded cable. Shield and GND are connected with ferrule only at that end of the cable which will be later connected to controllers input. Other end of the cable which will be connected to limit switch does not have shield and GND connected.Shield of the cable should be connected to GND only at the end which is connected to controllers input:Table of Contents1 Introduction (3)1.1 Overview (3)1.2 Features and specifications: (4)1.3 System Requirements (5)2 Hardware (6)2.1 Installation (6)2.2 Mk3/4 - 4 axis CNC USB controller description (7)2.2.1 Mk3/4 AXIS connector (8)2.2.2 Mk3/4 JOG connector (9)2.2.3 Mk3/4 LIMIT connector (10)2.2.4 Mk3/4 CTRL connector (11)2.2.5 Mk3/4 INPUT connector (12)2.2.6 Mk3/4 OUTPUT connector (13)2.2.7 Mk3/4 26 pin header (14)2.2.8 Mk3/4 SD&I2C connector (15)2.2.9 Mk3/4 USB connector (16)2.2.10 Mk3/4 Power terminal (16)2.2.11 Mk3/4 LED indicators (16)3 Connection diagrams (17)3.1 Wiring of limit switches (17)3.1.1 'Single input' wiring methods: (18)3.1.1.1 Parallel wiring of NO type switches: (18)3.1.1.2 Serial wiring of NC type limit switches: (20)3.2 Wiring inputs of Mk3/4 controller (21)3.3 Connecting motor driver to Mk3/4 controller (22)3.4 Shielded cables (25)。
广州唯创电子有限公司 WTN4 系列语音芯片说明书

广州唯创电子有限公司MP3录音模块WTN4系列语音芯片说明书3I/O Single-Chip Speech SynthesizerV1.052017-01-17Note:WAYTRONIC ELECTRONIC CO.,LTD.reserves the right to change this document without prior rmation provided by WAYTRONIC is believed to be accurate and reliable.However,WAYTRONIC makes no warranty for any errors which may appear in this document.Contact WAYTRONIC to obtain the latest version of device specifications before placing your orders.No responsibility is assumed by WAYTRONIC for any infringement of patent or other rights of third parties which may result from its use.In addition,WAYTRONIC products are not authorized for use as critical components in life support devices/systems or aviation devices/systems,where a malfunction or failure of the product may reasonably be expected to result in significant injury to the user, without the express written approval of WAYTRONIC.目录1、概述: (3)2、功能简述: (3)3、管脚描述: (4)3.1、WTN4045/WTN4065/WTN4105-8S管脚介绍 (4)3.2、WTN4165-8S管脚介绍 (4)3.3、极限参数: (5)3.4、直流特性: (5)4、一线串口通讯: (6)4.1、管脚分配: (6)4.2、一线语音地址对应关系: (6)4.3、一线语音及命令码对应表: (7)4.4、一线串口时序图: (7)4.5、一线串口程序范例: (8)5、两线串口通讯: (9)5.1、管脚分配: (9)5.2、语音地址对应关系: (9)5.3、语音及命令码对应表: (9)5.4、两线串口时序图: (10)5.5、两线串口程序范例: (10)6、数脉冲控制方式: (11)6.1、管脚分配: (11)6.2、语音地址对应关系: (11)6.3、数脉冲控制时序: (12)6.4、数脉冲程序范例: (12)7、应用电路: (13)7.1、WTN4045/065/105-8S一线串口控制应用电路 (13)7.2、WTN4045/065/105-8S两线串口控制应用电路 (14)7.3、WTN4045/065/105-8S数脉冲控制应用电路 (14)7.4、WTN4165-8S一线串口控制应用电路 (15)7.5、WTN4165-8S两线串口控制应用电路 (15)7.6、WTN4165-8S数脉冲控制应用电路 (16)8、管脚封装图: (16)9、版本记录 (17)1、概述WTN4系列语音芯片是广州唯创电子有限公司推出的一系列语音芯片,其性能优越,价格实惠。
悍马主板说明书
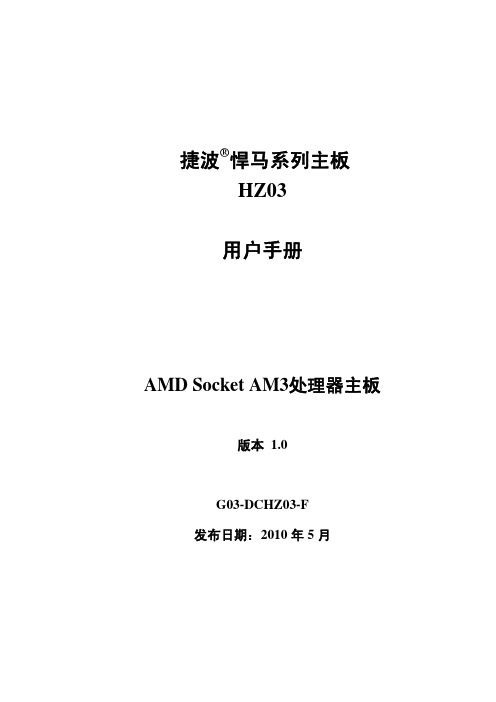
环境安全性须知 z 灰尘、潮湿以及剧烈的温度变化都会影响主板的使用寿命,请尽量避免在这些恶劣环
境地方放置和使用。 z 本产品的标准使用环境温度为 0 度~40 度 (数据来自于主芯片要求)。 z 一般情况下,当环境温度变化过大, 可能导致接插件 (CONNECTOR) 之间产生接触性
- II -
安全指导
1. 请仔细阅读这些安全指导。 2. 请保留这份用户手册以便日后参考。 3. 在您开始安装之前请将设备放置于稳定可靠的平台上面。 4. 在您将设备连接电源供应器之前请确保电源电压合乎标准。 5. 设备上所有的警告,警示您都应该注意。 6. 在安装附加的接口与模块之前请将设备与连接器间的连接断开。 7. 决不能让任何液体流入机箱的开口处,这样的行为有可能会引起火灾或电击。 8. 不正确的电池替换可能会引起爆炸.请使用制造厂商建议的电池类型作替换。 9. 如果发生下列情形,请专职的服务人员为您检查您的设备:
商标布告 (按字母表的顺序排列)
所有的品牌,产品,徽标,商标和公司名称都是属于商标或注册商标各自的拥有者。 AMD, Phenom™ II x 4;Phenom™ II x 3;Phenom™ II x2;Athlon II™ x4;Athlon II™ x3;Athlon II™ x2;Sempron™是AMD有限公司的注册商标。 AMI ® 是American Megatrend, Inc.的注册商标。 Kensington 和 MicroSaver 是Kensington 科技集团的注册商标。 Microsoft 是Microsoft有限公司的注册商标。 Netware® 是Novell, Inc的注册商标。 AMD, AMD徽标是AMD有限公司在美国和其它国家的注册商标。 PS/2 和 OS®/2 是International Business Machines有限公司的注册商标。 PCMCIA 和 CardBus 是个人电脑存储卡国际联合会的注册商标。 Windows® 98/2000/ /XP/Vista/7 是Microsoft有限公司的注册商标。
微特迈低功耗工控主板 WTM-T56N

微特迈AMD APU双屏显示主板/低功耗工控主板WTM-T56N为满足行业客户对低功耗主板显示性能不断提高需求,特别是对DVI,VGA接口独立双屏显示的特殊需要,微特迈科技量产了板载AMD Fusion APU G-T56N处理器的主板产品,竭力打造了一款接口更丰富,操作更简单,显示性能更强的嵌入式主板,WTM-T56N主板结构精致紧凑,简单实用,方便客户缩短开发周期,提升产品性能。
该主板采用AMD Brazos + Hudson E1 Chipset芯片组,支持AMD的新一代APU处理器AMD Fusion APU G-T56N双核处理器,双核心设计,1.65GHz主频,拥有2×512KB二级缓存,支持DDR3 1333MHz 内存,最高容量可达4GB,显卡GPU部分为RadeonHD6320,拥有80个流处理单元,核心频率为500MHz,能够轻松应对当今流行的DX11标准提供完整的支持,支持1080P高清流程播放大大提高了系统的整体性能。
超强的显卡性能,丰富的设备接口WTN-T56N板载AMD最新上市的AMD Fusion APU G-T56N处理器,集成AMD Radeon HD 6320显卡,APU将CPU和GPU进行专业的融合,对于数据处理将更快,显示性能更强。
强大的显卡性能支持了VGA、DVI、LVDS和HDMI四种显示接口,支持任意两个接口组成高清异步双显示画面。
主板采用ITX规格尺寸为170mm x170mm,应用DC电源12V供电,2个MINI PCI-E 接口,其中1个MINI PCI-E接口,支持WIFI 或3G网卡且主板提供SIM卡槽便于SIM卡位置固定,1个MINI PCI-E接口,支持MINI-SATA的固态硬盘,扩展1个PCI连接插槽、2个SATA接口,8个USB2.0接口、2个R232串口,1个音频插孔(可扩展2个)、1个千兆网口,1个GPIO接口。
WTM-T56N产品特点·板载AMD Fusion APU G-T56N处理器,集成AMD Radeon HD 6320显卡,显卡性能更强大,异步显示功能更理想。
MEMORY存储芯片MT48G4M32LFFC-10IT中文规格书
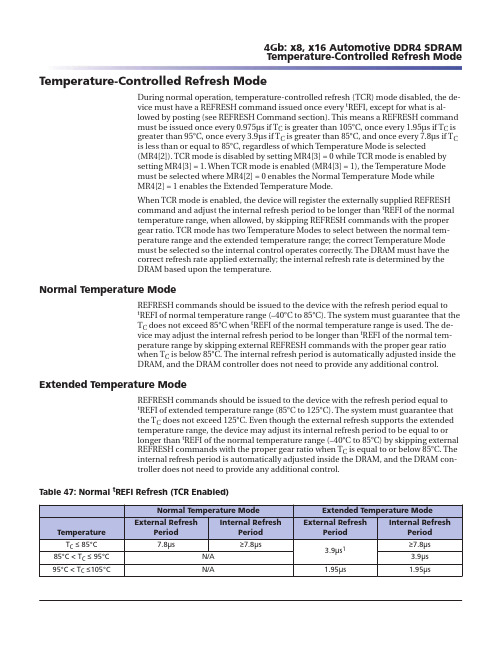
Temperature-Controlled Refresh ModeDuring normal operation, temperature-controlled refresh (TCR) mode disabled, the de-vice must have a REFRESH command issued once every t REFI, except for what is al-lowed by posting (see REFRESH Command section). This means a REFRESH commandmust be issued once every 0.975μs if T C is greater than 105°C, once every 1.95μs if T C isgreater than 95°C, once every 3.9μs if T C is greater than 85°C, and once every 7.8μs if T Cis less than or equal to 85°C, regardless of which Temperature Mode is selected(MR4[2]). TCR mode is disabled by setting MR4[3] = 0 while TCR mode is enabled bysetting MR4[3] = 1. When TCR mode is enabled (MR4[3] = 1), the Temperature Modemust be selected where MR4[2] = 0 enables the Normal Temperature Mode whileMR4[2] = 1 enables the Extended Temperature Mode.When TCR mode is enabled, the device will register the externally supplied REFRESHcommand and adjust the internal refresh period to be longer than t REFI of the normaltemperature range, when allowed, by skipping REFRESH commands with the propergear ratio. TCR mode has two Temperature Modes to select between the normal tem-perature range and the extended temperature range; the correct Temperature Modemust be selected so the internal control operates correctly. The DRAM must have thecorrect refresh rate applied externally; the internal refresh rate is determined by theDRAM based upon the temperature.Normal Temperature ModeREFRESH commands should be issued to the device with the refresh period equal tot REFI of normal temperature range (–40°C to 85°C). The system must guarantee that theT C does not exceed 85°C when t REFI of the normal temperature range is used. The de-vice may adjust the internal refresh period to be longer than t REFI of the normal tem-perature range by skipping external REFRESH commands with the proper gear ratiowhen T C is below 85°C. The internal refresh period is automatically adjusted inside theDRAM, and the DRAM controller does not need to provide any additional control. Extended Temperature ModeREFRESH commands should be issued to the device with the refresh period equal tot REFI of extended temperature range (85°C to 125°C). The system must guarantee thatthe T C does not exceed 125°C. Even though the external refresh supports the extendedtemperature range, the device may adjust its internal refresh period to be equal to orlonger than t REFI of the normal temperature range (–40°C to 85°C) by skipping externalREFRESH commands with the proper gear ratio when T C is equal to or below 85°C. Theinternal refresh period is automatically adjusted inside the DRAM, and the DRAM con-troller does not need to provide any additional control.Table 47: Normal t REFI Refresh (TCR Enabled)Fine Granularity Refresh ModeMode Register and Command Truth TableThe REFRESH cycle time (t RFC) and the average refresh interval (t REFI) can be pro-grammed by the MRS command. The appropriate setting in the mode register will set asingle set of REFRESH cycle times and average refresh interval for the device (fixedmode), or allow the dynamic selection of one of two sets of REFRESH cycle times andaverage refresh interval for the device (on-the-fly mode [OTF]). OTF mode must be ena-bled by MRS before any OTF REFRESH command can be issued.Table 48: MRS DefinitionThere are two types of OTF modes (1x/2x and 1x/4x modes) that are selectable by pro-gramming the appropriate values into the mode register. When either of the two OTFmodes is selected, the device evaluates the BG0 bit when a REFRESH command is is-sued, and depending on the status of BG0, it dynamically switches its internal refreshconfiguration between 1x and 2x (or 1x and 4x) modes, and then executes the corre-sponding REFRESH operation.Table 49: REFRESH Command Truth Tablet REFI and t RFC ParametersThe default refresh rate mode is fixed 1x mode where REFRESH commands should beissued with the normal rate; that is, t REFI1 = t REFI(base) (for T C≤ 85°C), and the dura-tion of each REFRESH command is the normal REFRESH cycle time (t RFC1). In 2xmode (either fixed 2x or OTF 2x mode), REFRESH commands should be issued to thedevice at the double frequency (t REFI2 = t REFI(base)/2) of the normal refresh rate. In 4xmode, the REFRESH command rate should be quadrupled (t REFI4 = t REFI(base)/4). PerFigure 84: TCR Mode Example1Controller85°C T C 95°C T C 85°C REFRESHExternal t REFI3.9μs Internal t REFI 3.9μs Internal t REFI 7.8μs REFRESH REFRESH REFRESH REFRESH REFRESH REFRESHREFRESH REFRESHREFRESH REFRESH REFRESH REFRESH REFRESH REFRESH REFRESH REFRESH REFRESH Note: 1.TCR enabled with Extended Temperature Mode selected.。
WTM-B75产品简介

深圳市微特迈科技有限公司WTM-B75产品简介WTM-B75 规格:处理器·Supports 2nd(3rd) Generation Intel® Core™ i7 / i5 / i3 in LGA1155 Package 芯片组·INTEL® B75显示接口·支持VGA1、VGA2 、HDMI、输出,·支持VGA1+VGA2,VGA1+HDMI, VGA2+HDMI,均可同步或异步双显示输出显示性能·视CPU而定内存·2*SO-DIMM,DDR3内存最大支持8GB电源·ATX存储·4* Serial II ATA接口,支持3Gb/s·1*MINI-SATA接口,6Gb/s网络·板载2*RTL 8111E 1000 LAN,支持网络唤醒,支持远程关机声音·瑞昱ALC662芯片,提供6声道输出LVDS ·NOGPIO ·8路输入输出看门狗·支持USB ·8*USB 2.0, 4*USB3.0背板接口·1*PS2 支持键盘鼠标·1*HDD LED+PW LED指示灯·1*HDMI·2*USB 3.0·2*VGA·2*RJ-45 1000M·4*USB 2.0·1*COM·1*Audio out·1*MIC内置接口·2*USB 2.0排针,支持4个USB 2.0·1*USB 3.0排针,支持2个USB 3.0·1*VGA1并行输出扩展排针·9*COM排针(COM2-COM9)·1*LPT排针·3*FAN 供电接口··1*PCI·1*MINI-SATA·4*SATA·1*前置音频排针·1*GPIOBIOS ·AMI 32M BIOS, ACPI supported,支持来电开机功能温度·工作:-20至+80摄氏度·仓储:在10~60摄氏度·湿度:10%~90%板型·MINI-ITX (180mm*180mm)Packing DetailWTM-B75 接口图WTM-B75正面图PS2接口支持键盘鼠标/2个USB 3.0/2个VGA输出/支持VGA1+VGA2,VGA1+HDMI,VGA2+HDMI,均可同步异步双显示输出双千兆网卡 2*RTL8111EL,后置电源POWER LED和HDD LEDATX 24pin+4pin 电源支持所有intel 1155 CPU,赛扬,i3,i5,i7,全固态电容,电感用料扎实讲究全铝合金散热片RS232 COM口 10个,Mini-SATA电子硬盘(M-SATA)接口,支持USB和Mini-pcie信号(选项)4个标准SATA硬盘接口SO-DIMM 支持204pin DDR3双通道内存1条PCI,可通过转接板支持到2个PCI支持GPIO,支持VGA的内置扩展排针,支持USB3.0的扩展排针。
Agilent Power PLCC-4 SMT LED 产品说明书
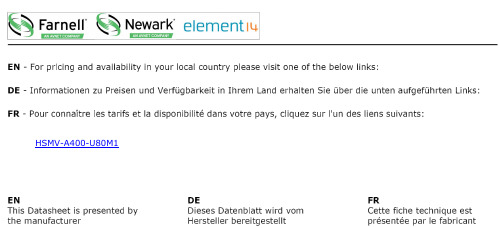
HSMV-A400-U80M1DescriptionAgilent Power PLCC-4 is an extension of our PLCC-2 SMT LEDs. The package can be driven at higher current due to its superior package design. The product is able to dissipate heat more efficiently compared to the conventional PLCC-2 SMT LEDs.In proportion to the increase in driving current, this family of LEDs is able to produce higher light output compared to the conventional PLCC-2 SMT LEDs.These SMT LEDs have higher reliability and better performance and are designed to work under a wide range of environmentalconditions. This higher reliability makes them suitable for use under harsh environment and conditions like automotive. In addition, they are also suitable to be used in electronic signs and signals.Agilent HSMx-A4xx-xxxxx SMT LED Surface Mount LED IndicatorData SheetCAUTION: HSMN-, HSMK-, HSMM-A40x-xxxxx LEDs are Class 2 ESD sensitive. Please observe appropriate precautions during handling and processing. Refer to Agilent Application Note AN-1142 for additional details.To facilitate easy pick and place assembly, the LEDs are packed in EIA-compliant tape and reel.Every reel will be shipped in single intensity and color bin (except for red color), to provide close uniformity.These LEDs are compatible with IR solder reflow process. Due to the high reliability feature of these products, they also can be mounted using through-the-wave soldering process.There are a variety of colors and various viewing angles (30°, 60°and 120°) available in these SMT LEDs. Ideally, the 30° parts are suitable for light piping where focused intensities are required.As for the 60° and 120°, they are most suitable for automotive interior and exterior lighting and electronic signs applications.Features•Industry standard PLCC-4•High reliability LED package •High brightness using AlInGaP and InGaN dice technologies •High optical efficiency•Higher ambient temperature at the same current possible compared to PLCC-2•Available in full selection of colors•Super wide viewing angle at 120˚•Available in 8mm carrier tape on 7-inch reel •Compatible with both IR and TTW soldering process Applications•Interior automotive– Instrument panel backlighting – Central console backlighting – Cabin backlighting– Navigation and audio system – Dome lighting– Push button backlighting •Exterior automotive – Turn signals – CHMSL– Rear combination lamp – Puddle light•Electronic signs and signals – Interior full color sign – Variable message sign•Office automation, home appli-ances, industrial equipment – Front panel backlighting – Push button backlighting – Display backlightingPackage DimensionsNOTE: ALL DIMENSIONS IN mm.Device Selection GuideColor Part Number Min. I v (mcd)Max. I v (mcd)Test Current (mA)Dice Technology Red HSMC-A400-S30M1160.0400.050AlInGaP HSMC-A401-T40M1250.0800.050AlInGaPHSMC-A401-T80M1310.01000.050AlInGaPHSMZ-A400-U80M1500.01600.050AlInGaPRed Orange HSMJ-A401-T40M1250.0800.050AlInGaP HSMJ-A401-U40M1400.01260.050AlInGaPHSMV-A400-U80M1500.01600.050AlInGaP Orange HSML-A401-U40M1400.01260.050AlInGaP Amber HSMA-A400-T35M1250.0630.050AlInGaP HSMA-A401-U45M1400.01260.050AlInGaPHSMU-A400-U85M1500.01600.050AlInGaP Emerald Green HSME-A401-P4PM140.0130.050AlInGaPGreen HSMM-A401-R7YM2120.0320.030InGaN HSMM-A401-S4YM2160.0500.030InGaNHSMM-A401-S7YM2200.0500.030InGaNHSMM-A400-T8YM2310.01000.030InGaNCyan HSMK-A401-R40M2100.0320.030InGaN HSMK-A400-T80M2310.01000.030InGaNBlue HSMN-A401-P4QM240.0130.030InGaN HSMN-A401-P7QM250.0130.030InGaNHSMN-A400-Q8QM280.0250.030InGaNNote:1. The luminous intensity, I v, is measured at the mechanical axis of the lamp package. The actual peak of the spatial radiation pattern may not be aligned.Part Numbering SystemHSM x1 – A x2 x3x4 – x5x6 x7 x8x9Packaging OptionColor Bin SelectionIntensity Bin SelectDevice Specific ConfigurationPackage TypeLED Chip ColorAbsolute Maximum Ratings (T A = 25°C)Parameters HSMC/J/L/A/E HSMZ/V/U HSMM/K/N DC Forward Current[1]70 mA[3,4]70 mA[3,4]30 mA Peak Forward Current [2]200 mA200 mA90 mA Power Dissipation180 mW240 mW114 mW Reverse Voltage 5 VJunction Temperature 110°COperating Temperature –40°C to +100°CStorage Temperature –40°C to +100°CNotes:1.Derate linearly as shown in figure 5.2.Duty factor = 10%, Frequency = 1 kHz.3.Drive current between 10 mA and 70 mA is recommended for best long-term performance.4.Operation at currents below 5 mA is not recommended.Optical Characteristics (T A = 25°C)PeakDominant LuminousLuminous Intensity/Wavelength Wavelength Viewing Angle Efficacy ηv [3]Total FluxPart λPEAK (nm)λD [1] (nm)2θ1/2[2] (Degrees)(lm/W)I v (mcd)/Φv (mlm)Color Number Typ.Typ.Typ.Typ.Typ.Red HSMC 6356261201500.45HSMZ 6396301201550.45Red Orange HSMJ 6216151202400.45HSMV 6236171202630.45Orange HSML 6096051203200.45Amber HSMA 5925901204800.45HSMU 5945921205000.45Yellow Green HSME 5765751205600.45Emerald Green HSME 5685671206100.45Green HSMM 5185251205000.45Cyan HSMK 5025051203000.45BlueHSMN468470120750.45Notes:1.The dominant wavelength, λD , is derived from the CIE Chromaticity Diagram and represents the color of the device.2.θ1/2 is the off-axis angle where the luminous intensity is 1/2 the peak intensity.3.Radiant intensity, I e in watts/steradian, may be calculated from the equation I e = I v /ηv , where I v is the luminous intensity in candelas and ηv is the luminous efficacy in lumens/watt.Electrical Characteristics (T A = 25°C)Forward VoltageReverse VoltageV F (Volts) @ I F = 50 mA V R @ 100 µA Part Number Typ.Max.Min.HSMC/J/L/A/E 2.2 2.55HSMZ/V/U2.83.45Forward VoltageReverse Voltage V F (Volts) @ I F = 30 mA V R @ 10 µA Part Number Typ.Max.Min.HSMM/K/N3.84.65Figure 1. Relative Intensity Vs. Wavelength.WAVELENGTH – nmR E L A T I V E I N T E N S I T Y1.00.803804805806807307806305304300.60.40.20.10.30.50.70.9Figure 2. Forward Current Vs. Forward Voltage.Figure 3. Relative Intensity Vs. Forward Current (AlInGaP).Figure 4. Relative Intensity Vs. Forward Current (InGaN).Figure 5a. Maximum Forward Current Vs.Ambient Temperature, Derated Based On T J max = 110°C (AlInGaP).Figure 6. Dominant Wavelength Vs. Forward Current – InGaN Devices.Figure 7. Radiation Pattern.40FORWARD CURRENT – mA 00.4 R E L A T I V E I N T E N S I T Y (N O R M A L I Z E D A T 50 m A )800.80.21.0200.61.2601030701.450CURRENT – mAD O M I N A N T W A VE L E N G T H – n mR E L A T I V E I N T E N S I T Y1.00ANGLE – DEGREES0.80.60.20.4-70-50-3030507090-90-10100.10.30.50.70.9M A X I M U M F O R W A R D C U R R E N T – m AAMBIENT TEMPERATURE – °C0M A X I M U M F O R W A R D C U R R E N T – m AAMBIENT TEMPERATURE – °C 2030151035525Figure 5b. Maximum Forward Current Vs.Ambient Temperature, Derated Based On T J max = 110°C (InGaN).FORWARD VOLTAGE – V 0207080 F O R W A R D C U R R E N T – m A1050406030020FORWARD CURRENT – mA0.4 R E L A T I V E L U M I N O U S I N T E N S I T Y (N O R M A L I Z E D A T 30 m A )350.80.21.0100.61.23051525Figure 9a. Recommended SnPb Reflow Soldering Profile.Figure 10. Recommended Wave Soldering Profile.Figure 8a. Recommended Soldering Pad Pattern.TIMET E M P E R A T U R EFigure 8b. Recommended Soldering Pad Pattern (TTW).300°C/W >16 mm 2350°C/W >12 mm2470°C/W >8 mm 2Figure 9b. Recommended Pb-free Reflow Soldering Profile.* THE TIME FROM 25 °C TO PEAK TEMPERATURE = 6 MINUTES MAX.BOTTOM SIDE OF PC BOARD TIME – SECONDST E M P E R A T U R E – °CTOP SIDE OF PC BOARDCONVEYOR SPEED = 1.83 M/MIN (6 FT/MIN)PREHEAT SETTING = 150°C (100°C PCB)SOLDER WAVE TEMPERATURE = 245°C AIR KNIFE AIR TEMPERATURE = 390°C AIR KNIFE DISTANCE = 1.91 mm (0.25 IN.)AIR KNIFE ANGLE = 40°SOLDER: SN63; FLUX: RMANOTE: ALLOW FOR BOARDS TO BE SUFFICIENTL Y COOLED BEFORE EXERTING MECHANICAL FORCE.DIMENSIONS IN mm (INCHES).SOLDER RESISTDIMENSIONS IN mm (INCHES).Figure 11. Tape Leader and Trailer Dimensions.USER FEED DIRECTIONFigure 13. Reeling Orientation.Storage Condition: 5 to 30°C @60% relative humidity max.Baking is required under the condition:a) the humidity indicator card color becoming pinkb) the pack has been opened for more than 4 weeksBaking recommended condition:60 ± 5°C for 20 hours.0.1VIEW B-BIntensity Bin Select (X5X6) Individual reel will contain parts from one half bin only.X5Min. Iv BinX60Full Distribution3 3 half bins starting from X514 4 half bins starting from X515 5 half bins starting from X517 3 half bins starting from X528 4 half bins starting from X529 5 half bins starting from X52Intensity Bin LimitsBin ID Min. (mcd)Max. (mcd) N128.5035.50N235.5045.00P145.0056.00P256.0071.50Q171.5090.00Q290.00112.50R1112.50140.00R2140.00180.00S1180.00224.00S2224.00285.00T1285.00355.00T2355.00450.00U1450.00560.00U2560.00715.00V1715.00900.00V2900.001125.00W11125.001400.00W21400.001800.00 Tolerance of each bin limit = ± 12%Color Bin Select (X7)Individual reel will contain parts fromone full bin only.X70Full DistributionZ A and B onlyY B and C onlyW C and D onlyV D and E onlyU E and F onlyT F and G onlyS G and H onlyQ A, B and C onlyP B, C and D onlyN C, D and E onlyM D, E and F onlyL E, F and G onlyK F, G and H only1A, B, C and D only2E, F, G and H only3B, C, D and E only4C, D, E and F only5A, B, C, D and E only6B, C, D, E and F onlyColor Bin LimitsBlue Min. (nm)Max. (nm)A460.0465.0B465.0470.0C470.0475.0D475.0480.0Cyan Min. (nm)Max. (nm)A490.0495.0B495.0500.0C500.0505.0D505.0510.0Green Min. (nm)Max. (nm)A515.0520.0B520.0525.0C525.0530.0D530.0535.0Color Bin LimitsEmeraldGreen Min. (nm)Max. (nm)A552.5555.5B555.5558.5C558.5561.5D561.5564.5YellowGreen Min. (nm)Max. (nm)E564.5567.5F567.5570.5G570.5573.5H573.5576.5Amber/Yellow Min. (nm)Max. (nm)A582.0584.5B584.5587.0C587.0589.5D589.5592.0E592.0594.5F594.5597.0Orange Min. (nm)Max. (nm)A597.0600.0B600.0603.0C603.0606.0D606.0609.0E609.0612.0RedOrange Min. (nm)Max. (nm)A611.0616.0B616.0620.0Red Min. (nm)Max. (nm)Full DistributionTolerance of each bin limit = ± 1 nmPackaging Option (X8X9)Test Package ReelOption Current Type SizeM150 mA Top Mount7 inchM230 mA Top Mount7 inchForward Voltage Bin TableFor HSMZ/V/U – A4xx-xxxxx only BIN MIN.MAX.VA 1.9 2.2VB 2.2 2.5VC 2.5 2.8VD 2.8 3.1VE 3.1 3.4 Tolerance of each bin limit = ± 0.05/semiconductors For product information and a complete list of distributors, please go to our web site.For technical assistance call:Americas/Canada: +1 (800) 235-0312 or (916) 788-6763Europe: +49 (0) 6441 92460China: 10800 650 0017Hong Kong: (+65) 6756 2394India, Australia, New Zealand: (+65) 6755 1939 Japan: (+81 3) 3335-8152 (Domestic/Interna-tional), or 0120-61-1280 (Domestic Only) Korea: (+65) 6755 1989Singapore, Malaysia, Vietnam, Thailand, Philippines, Indonesia: (+65) 6755 2044 Taiwan: (+65) 6755 1843Data subject to change.Copyright © 2004 Agilent Technologies, Inc. Obsoletes 5989-0663ENOctober 12, 20045989-1211ENHSMV-A400-U80M1。
微特迈WTM-I2主板

在市面上我们我们经常会看到很多多功能主板,像技嘉,华硕,华擎这些知名品牌的一线主板厂家都是专业做电脑主板的,在实现多功能多行业化应用上还是存在一定的差距。
当然能做到单一行列的领头羊也是不错的。
那么有没有实现多功能多行业为一体的主板呢?今天就专门为大家介绍一下WTM-I2,WTM-I2是微特迈简称(WTM)微了应征市面上实现多行业多功能主板缺陷而研发出的一种新型的微型主板,可以方便运用到各个行业很领域。
下面来看看具体的介绍!主要运用领域:电脑领域:现在很多人不仅仅追求的是大型的高性能主板,而是追求更加迷你系列主板,当然性能方面的要求也不会降低,WTM-I2实现了超级迷你微型主板的特征,它的体积只占市面上的主板三分之一,非常的迷你。
可以自由拓展配置工业工控领域:工业主板一般来说对功耗消耗非常的看重,而且对性能也非常的苛刻,WTM-I2实现了嵌入式多功能拓展特性,采用的是超级防水电容,超低功耗耗材,它的耗电量经过市场监测,仅仅是我们市场同领域主板的46%,要是按照工业用电的平均标准1.5元计算,一个企业拥有100台WTM-I2微型主板,一天按照10个小时工作耗电来计算,一台WTM-I2微型主板节约的成本大概为5.6毛左右,100台解决成本为560元,一年按照300的工作运行计算,可以为企业节约成本在168000元,这个足以支付80名普通员工一个月的开支,想想也比较乐观的。
游戏娱乐领域:游戏娱乐领域的主板主要是针对主板的拓展性能比较高,一般他们对显示画面效果和传输速率的要求比高,多款好的显卡,要想和一块好的主板完全搭配好必须要足够好的拓展性能,WTM-I2,不仅仅内部自带集成显卡,还能拓展外部显卡,采用双向双输入输入拓展,让游戏输出达到了一个巅峰。
商业领域:当然商业领域多主板的性能要求是最高的,必须保证主板能够高强度的工作,而且不出任何故障。
还需要求嵌入银行的各种系统。
但是微特卖WTM-i2却能很好的吻合,不管从拓展性,耗电量,程序嵌入式,等方面有很大的优势,关键在于它还有一个很重要的特征,那就是遇到故障的时候,会自动保存电脑数据,以免造成数据丢失,还保证来电自动开机,不误工作时间。
NUMAKER-HMI-MA35D1-S1用户手册说明书
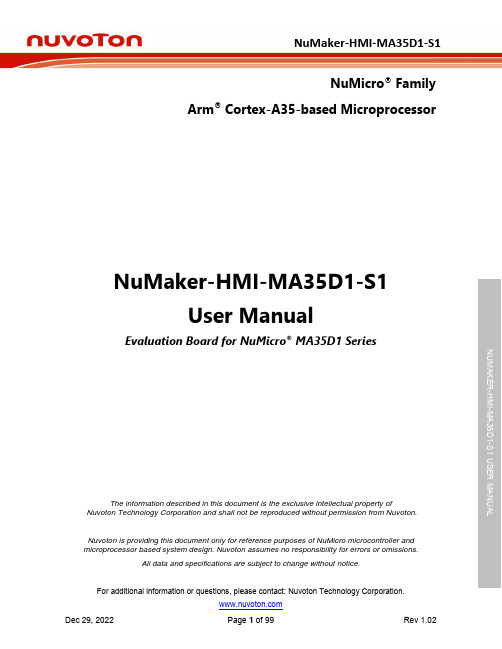
NuMicro® FamilyArm® Cortex-A35-based Microprocessor NuMaker-HMI-MA35D1-S1User ManualEvaluation Board for NuMicro® MA35D1 SeriesNUMAKER-HMI-MA35D1-S1 USER MANUAL M-m UThe information described in this document is the exclusive intellectual property ofNuvoton Technology Corporation and shall not be reproduced without permission from Nuvoton.Nuvoton is providing this document only for reference purposes of NuMicro microcontroller andmicroprocessor based system design. Nuvoton assumes no responsibility for errors or omissions.All data and specifications are subject to change without notice.For additional information or questions, please contact: Nuvoton Technology Corporation.Table of Contents1OVERVIEW (9)1.1NuMaker-SOM-MA35D16A81 Board (11)1.2NuMaker-BASE-MA35D1B1 Board (12)1.37’’ TFT LCD Daughter Board (13)1.4Board Part Number and Information (14)2FEATURES (15)2.1NuMaker-SOM-MA35D16A81 Features (15)2.2NuMaker-BASE-MA35D1B1 Features (15)2.37’’ TFT LCD Daughter Board Features (16)3HARDWARE CONFIGURATION (17)3.1NuMaker-SOM-MA35D16A81 Board (17)3.1.1Front View (17)3.1.2Rear View (17)3.1.3Power Input (17)3.1.4RTC Wake-up Control (18)3.1.5PMIC (18)3.1.6eMMC NAND Flash (19)3.1.7RGMII Gigabit PHY (20)NUMAKER-HMI-MA35D1-S1 USER MANUAL Maker Nu-mbed NUC472 User Manual3.1.8High Speed Connectors (21)3.2NuMaker-BASE-MA35D1B1 Board (26)3.2.1Front View (26)3.2.2Rear View (26)3.2.3Power and Ground (27)3.2.4High Speed Connectors (27)3.2.5QSPI Flash (31)3.2.6NAND Flash (32)3.2.7SD Card Slot (33)3.2.8HS USB2.0 Connectors (33)3.2.9Power-on Setting (33)3.2.10G igabit Ethernet Transformers and RJ45 Ports (36)3.2.11C MOS Sensor Capture Connectors (36)3.2.12E xternal Bus Interface (EBI) Connector (38)3.2.13E ADC Connector (40)3.2.14U ART (41)3.2.15R S485 (42)3.2.16C AN FD (42)3.2.17S WJ, SWD and ETM (43)3.2.18U SB Virtual COM (VCOM) Port (45)3.2.19R eset and RTC Wake-up Key Buttons (45)3.2.20T FT LCD Connector (45)3.2.21A udio Codec (48)3.2.22S IM Card Slot (49)3.2.23K ey Buttons, LEDs and Buzzer (49)3.2.24M EMS Digital Microphone (50)3.2.25M EMS G-Sensor (50)3.37’’ TFT LCD Daughter Board (51)3.3.1Front View (51)3.3.2Rear View (51)3.3.3Connectors (52)4QUICK START (53)4.1Hardware Setup and Power On (53)4.1.1Insert SD Card (53)4.1.2Configure Power-on Setting (53)4.1.3Power On the NuMaker-BASE-MA35D1B1 Board (54)4.1.4VCOM Port (Optional) (55)4.2Embedder Demos (56)4.2.1H.264 Video Playback (56)4.2.2ML People Counting (56)4.2.32D Accelerator (57)NUMAKER-HMI-MA35D1-S1 USER MANUAL M-m U4.2.4VoIP Demonstration (57)4.2.5Data Security (58)4.2.6Keyword Spotting by RTP M4 (58)5SUPPORTING RESOURCES (60)5.1Documents (60)5.2Software (60)6HARDWARE SCHEMATICS (62)6.1NuMaker-SOM-MA35D16A81 Schematics (62)6.1.1System Block (62)6.1.2PMIC, Crystal and Power Filter Schematic (63)6.1.3Power Group 0, 2, 4 and 5 Schematic (64)6.1.4Power Group 1 Schematic (65)6.1.5Power Group 3 (eMMC1_PJ) Schematic (66)6.1.6Power Group 6, 7, ADC and USB Schematic (67)6.1.7Power Group 8 (RGMII0_PE) Schematic (68)6.1.8Power Group 9 (RGMII1_PF) Schematic (69)6.1.9DDR PHY Schematic (70)6.1.10P CB Placement (71)6.2NuMaker-BASE-MA35D1B1 Schematics (73)6.2.1Power Schematic (73)6.2.2SOM Connectors Schematic (74)6.2.3Power-on Setting and NAND Flash Schematic (75)6.2.4SD0 Schematic (76)6.2.5QSPI0 Schematic (77)6.2.6EADC0 Schematic (78)6.2.7RGMII0_PE Schematic (79)6.2.8RGMII1_PF Schematic (80)6.2.9HSUSB 0/1 Schematic (81)6.2.10C CAP 0/1 Connector Schematic (82)6.2.11L CM Connector Schematic (83)6.2.12E BI Connector Schematic (84)6.2.13N AU88C22 Audio Codec Schematic (85)6.2.14S IM Card Schematic (86)6.2.15R S232 Schematic (87)6.2.16R S485 Schematic (88)6.2.17C AN FD Schematic (89)6.2.18K ey Buttons, LEDs and Buzzer Schematic (90)6.2.19S WJ, SWD and ETM Connectors Schematic (91)6.2.20N UC123 VCOM Schematic (92)6.2.21M EMS Digital Microphone Schematic (93)6.2.22M EMS G-Sensor Schematic (94)6.2.23P CB Placement (95)NUMAKER-HMI-MA35D1-S1 USER MANUAL Maker Nu-mbed NUC472 User Manual6.37’’ TFT LCD Daughter Board Schematic (97)7REVISION HISTORY (98)List of FiguresFigure 1-1 NuMaker-HMI-MA35D1-S1 Board from SOM Side (10)Figure 1-2 NuMaker-HMI-MA35D1-S1 Board from TFT LCD Side (10)Figure 1-3 NuMaker-SOM-MA35D16A81 Board (11)Figure 1-4 NuMaker-BASE-MA35D1B1 Board (12)Figure 1-5 7’’ TFT LCD Daughter Board (13)Figure 3-1 Front View of NuMaker-SOM-MA35D16A81 (17)Figure 3-2 Rear View of NuMaker-SOM-MA35D16A81 (17)Figure 3-3 Front View of NuMaker-BASE-MA35D1B1 (26)Figure 3-4 Rear View of NuMaker-BASE-MA35D1B1 (27)Figure 3-5 Front View of 7’’ TFT LCD Daughter Board (51)Figure 3-6 Rear View of 7’’ TFT LCD Daughter Board (52)Figure 4-1 SD0 Standard-SD Card Slot (CON4) (53)Figure 4-2 Power-on Setting DIP Switch (SW4) (53)Figure 4-3 Power Jack (CON1) and Slide Switch (SW1) (54)Figure 4-4 USB VCOM Port (CON21) (55)Figure 4-5 Main Screen of Demonstration (56)Figure 4-6 H.264 Video Playback Demonstration (56)Figure 4-7 ML People Counting Demonstration (57)NUMAKER-HMI-MA35D1-S1 USER MANUAL M-m U Figure 4-8 2D Accelerator Demonstration (57)Figure 4-9 VoIP Demonstration (58)Figure 4-10 Data Security Demonstration (58)Figure 4-11 Keyword Spotting by RTP M4 Demonstration (59)Figure 5-1 Nuvoton Website (60)Figure 5-2 MA35D1 GitHub Resources (61)Figure 6-1 System Block (62)Figure 6-2 PMIC, Crystal and Power Filter Schematic (63)Figure 6-3 Power Group 0, 2, 4 and 5 Schematic (64)Figure 6-4 Power Group 1 Schematic (65)Figure 6-5 Power Group 3 (eMMC1_PJ) Schematic (66)Figure 6-6 Power Group 6, 7, ADC and USB Schematic (67)Figure 6-7 Power Group 8 (RGMII0_PE) Schematic (68)Figure 6-8 Power Group 9 (RGMII1_PF) Schematic (69)Figure 6-9 DDR PHY Schematic (70)Figure 6-10 Front PCB Placement of NuMaker-SOM-MA35D16A81 Board (71)Figure 6-11 Rear PCB Placement of NuMaker-SOM-MA35D16A81 Board (72)Figure 6-12 Power Schematic (73)Figure 6-13 SOM Connectors Schematic (74)Figure 6-14 Power-on Setting and NAND Flash Schematic (75)Figure 6-15 SD0 Schematic (76)Figure 6-16 QSPI0 Schematic (77)Figure 6-17 EADC0 Schematic (78)Figure 6-18 RGMII0_PE Schematic (79)Figure 6-19 RGMII1_PF Schematic (80)Figure 6-20 HSUSB 0/1 Schematic (81)Figure 6-21 CCAP 0/1 Connectors Schematic (82)Figure 6-22 LCM Connector Schematic (83)Figure 6-23 EBI Connector Schematic (84)Figure 6-24 NAU88C22 Audio Codec Schematic (85)Figure 6-25 SIM Card Schematic (86)Figure 6-26 RS232 Schematic (87)Figure 6-27 RS485 Schematic (88)Figure 6-28 CAN FD Schematic (89)Figure 6-29 Key Buttons, LEDs and Buzzer Schematic (90)Figure 6-30 SWJ, SWD and ETM Connectors Schematic (91)Figure 6-31 NUC123 VCOM Schematic (92)Figure 6-32 MEMS Digital Microphone Schematic (93)NUMAKER-HMI-MA35D1-S1 USER MANUAL Maker Nu-mbed NUC472 User ManualFigure 6-33 MEMS G-Sensor Schematic (94)Figure 6-34 Front PCB Placement of NuMaker-BASE-MA35D1B1 Board (95)Figure 6-35 Rear PCB Placement of NuMaker-BASE-MA35D1B1 Board (96)Figure 6-36 7’’ TFT LCD Daughter Board Schematic (97)List of TablesTable 1-1 Board Part Number and Information (14)Table 3-1 RTC Power Control Pins of MA35D1 (18)Table 3-2 PMIC (U2) Output Voltage (19)Table 3-3 PMIC (U2) Control Pins (19)Table 3-4 eMMC1 NAND Flash Device (U3) Pin Function (20)Table 3-5 RGMII0 PHY (U4) Pin Funciton (20)Table 3-6 RGMII1 PHY (U5) Pin Funciton (21)Table 3-7 SOM Connector 1 (P1) Pin Function (23)Table 3-8 SOM Connector 2 (P2) Pin Function (25)Table 3-9 SOM Connector 1 (CON2) Pin Function (29)Table 3-10 SOM Connector 2 (CON3) Pin Function (31)Table 3-11 QSPI0 Flash (U8) Pin Function (32)Table 3-12 NAND Flash (U4) Pin Function (32)Table 3-13 SD0 Standard-SD Card Slot (CON4) Pin Function (33)Table 3-14 Secure Boot Options (34)Table 3-15 Booting Source QSPI0 and SD/eMMC IO Voltage Options (34)Table 3-16 Booting Source Options (34)Table 3-17 Page Size Options for NAND Flash Booting Source (34)NUMAKER-HMI-MA35D1-S1 USER MANUAL M-m U Table 3-18 ECC Options for NAND Flash Booting Source (35)Table 3-19 Options for SD Card 0/1 or eMMC 0/1 NAND Flash Device Booting Source (35)Table 3-20 4/8-bit Options for eMMC NAND Flash Device Booting Source (35)Table 3-21 1-bit Options for QSPI0 NAND/NOR Flash Booting Source (35)Table 3-22 Options for USBD or USBH Booting Source (36)Table 3-23 USBH Port 0/1 Options for USBH Booting Source (36)Table 3-24 Over-current High/Low-active Detect Options for USBH Booting Source (36)Table 3-25 CCAP0 Connector (CON7) Pin Function (37)Table 3-26 CCAP1 Connector (CON8) Pin Function (38)Table 3-27 EBI Connector (CON10) Pin Function (40)Table 3-28 EADC0 Connector (J6) Pin Function (41)Table 3-29 UART0 Port, Ground VSS and Tamper Pin Connector (J1) Pin Function (41)Table 3-30 UART11 (U21, CON13) Pin Function (41)Table 3-31 UART16 (U22, CON14) Pin Function (42)Table 3-32 UART12 (U23, CON15) Pin Function (42)Table 3-33 UART14 (U24, CON16) Pin Function (42)Table 3-34 CAN1 (U25, CON17) Pin Function (43)Table 3-35 CAN3 (U26, CON18) Pin Function (43)Table 3-36 SWJ Interface (CON19) Pin Function (44)Table 3-37 SWD Interface (J8) Pin Function (44)Table 3-38 ETM Interface (CON20) Pin Function (45)Table 3-39 NUC123 ICE Interface (J9) Pin Function (45)Table 3-40 LCM Connecor (CON9) Pin Function (48)Table 3-41 I2S0 (U18) Pin Function (48)Table 3-42 I2C2 (U18) Pin Function (48)Table 3-43 Audio Codec (U18) Control Pin Function (49)Table 3-44 SC0 SIM Card Connector (CON12) Pin Function (49)Table 3-45 Key Buttons (KEY_1, KEY_2, KEY_3) Pin Function (49)Table 3-46 LEDs (LEDG4, LEDR1) Pin Function (50)Table 3-47 MEMS Digital Mircrophone (U31) Pin Function (50)Table 3-48 MEMS G-Sensor (U32) Pin Function (50)Table 4-1 SD/eMMC Booting Source Configuration on Power-on Setting (54)Table 4-2 SD0 Booting Source Configuration on Power-on Setting (54)NUMAKER-HMI-MA35D1-S1 USER MANUAL Maker Nu-mbed NUC472 User Manual1 OVERVIEWThe NuMaker-HMI-MA35D1-S1 is an evaluation board for Nuvoton NuMicro MA35D1 series microprocessors, and consists of three parts: a NuMaker-SOM-MA35D16A81 SOM board, a NuMaker-BASE-MA35D1B1 base board and a 7” TFT-LCD daughter board. The SOM board integrates corecomponents to simplify the system design, based on MA35D16A887C (BGA312 package, and stackinga 256 MB DDR), PMIC power solution, a 16 GB eMMC Flash, and two Gigabit Ethernet PHY. TheNuMaker-HMI-MA35D1-S1 has rich peripherals such as 2 sets of Gigabit Ethernet, USB2.0 high-speedhost and device, 2 sets of CAN FD, and SPI, I2C, UART, RS-485 serial communication ports for usersto facilitate the evaluation in HMI and industrial control, home appliances, 2-wheel cluster, medicaldevice, new energy applications, ML (Machine Learning) or your creative applications.There are two evaluation boards for the MA35D1 series, NuMaker-HMI-MA35D1-S1 and NuMaker-IoT-MA35D1-A1, which are ideal for HMI and edge gateway applications, respectively. For more details onHMI applications, please refer to NuMaker-HMI-MA35D1-S1 User Manual. For more details on edgegateway applications, please refer to NuMaker-IoT-MA35D1-A1 User Manual.The NuMicro MA35D1 series is a heterogeneous multi-core microprocessor targeted to high-end edgeIIoT gateway. It is based on dual 64-bit Arm Cortex-A35 cores with speed up to 1 GHz, and one 180MHz Arm Cortex-M4 core. Based on the high-performance cores, the MA35D1 series facilities the tinyAI/ML for edge computing.The MA35D1 supports 16-bit DDR2 and DDR3/DDR3L SDRAM. For an easy system design andmanufacture, the MA35D1 series also offers LQFP and BGA packages stacked with the DDR2/DDR3LSDRAM and density up to 512 MB, which significantly reduces PCB layer, size and electromagneticinterference (EMI).The MA35D1 series is a trusted system for IoT products' security requirements. It includes severaladvanced security mechanisms such as Nuvoton Trusted Secure Island (TSI) an isolated securehardware unit, TrustZone, secure boot, tamper-detection, built-in cryptographic accelerators, and aTRNG, as well as Key Store and OTP memory. All the security operations are performed in the TSI toprotect sensitive and high-value data. The features also satisfy customers in IEC 62443 certificationNUMAKER-HMI-MA35D1-S1 USER MANUAL M-m U requirements.For high-end edge IIoT gateway requirements, the MA35D1 series provides multiple advanced and high-speed connection interfaces, such as Gigabit Ethernet, SDIO3.0, USB 2.0 HS, and CAN FD, for edgegateway and new energy applications.For HMI applications, the MA35D1 series provides a LCD display controller with the resolution up to1920x1080 at 60 FPS, a 2D graphic engine, a JPEG and a H.264 decoder integrated for better graphicalHMI effects and video playback.Figure 1-1 NuMaker-HMI-MA35D1-S1 Board from SOM SideFigure 1-2 NuMaker-HMI-MA35D1-S1 Board from TFT LCD Side1.1 NuMaker-SOM-MA35D16A81 BoardThe NuMaker-SOM-MA35D16A81 board contains an on-board target chip MA35D16A887C packagedin a MCP type with internal DDR3L 256 MB SDRAM, a PMIC device DA9062-3A to supply the powersto the target chip MA35D16A887C and dedicated peripherals on this SOM board, an eMMC NANDFlash memory device, two Gigabit Ethernet (RGMII) PHY devices, a battery input header and a PMICreset key button.Figure 1-3 NuMaker-SOM-MA35D16A81 BoardNUMAKER-HMI-MA35D1-S1 USER MANUAL M-m U1.2 NuMaker-BASE-MA35D1B1 BoardThe NuMaker-BASE-MA35D1B1 board contains rich peripherals, including two high speed connectorsto connect the NuMaker-SOM-MA35D16A81 board, serial SPI NAND and parallel NAND Flash memorydevices, a Standard-SD memory card slot, two Gigabit Ethernet transformers and RJ45 ports, two HighSpeed USB ports (Host/Device and Host), an audio codec with microphone and headset jack, a 24-bitRGB LCD with touch connector, an External Bus Interface (EBI) connector, two CMOS sensor inputconnectors, eight channels of ADC input, two RS232 COM ports, two RS485 connectors, two CAN FDconnectors, three user key buttons and two user LEDs.NUMAKER-HMI-MA35D1-S1 USER MANUAL Maker Nu-mbed NUC472 User ManualFigure 1-4 NuMaker-BASE-MA35D1B1 Board1.3 7’’ TFT LCD Daughter BoardThis daughter board contains a 7’’4-wire resistive touch TFT LCD panel with pixel resolution of1024x600. (TH0701024600NYR50L1 + AN-3748A)Figure 1-5 7’’ TFT LCD Daughter BoardNUMAKER-HMI-MA35D1-S1 USER MANUAL M-m U1.4 Board Part Number and InformationThe following table lists the part number of this evaluation board (EVB) based on the MA35D16A887C microprocessors, and the PCB names of three parts: NuMaker-SOM-MA35D16A81 SOM board, NuMaker-BASE-MA35D1B1 base board and 7” TFT-LCD daughter board.Part Number of EVB SOM Board BASE Board 7” TFT LCD Daughter BoardNuMaker-HMI-MA35D1-S1NuMaker-SOM-MA35D16A81 V2.xNuMaker-BASE-MA35D1B1 V2.xNuMaker TFT-LCD7 Table 1-1 Board Part Number and InformationNUMAKER-HMI-MA35D1-S1 USER MANUAL Maker Nu-mbed NUC472 User Manual2 FEATURES2.1 NuMaker-SOM-MA35D16A81 Features●Target Chip: MA35D16A887C (BGA 312-Ball) MCP package with DDR3L (256 MB), whichcan run up to 800 MHz●Power–DC 5V input from the NuMaker-BASE-MA35D1B1 board through the SOM high speedconnector–PMIC DA9062-3A:◆Four DC/DC: To supply 1.2V Core power, 1.2V CPU power, 1.35V DDR3L Memorypower and 3.3V I/O power◆Four LDO: To supply 3.0V RTC power, 1.8V I/O power, 2.5V PLL power and3.3V/1.8V eMMC NAND Flash power–Battery input header (J48): Independent DC 3.3V input to V BAT for RTC power (Optional)●Memory Devices–An on-board eMMC NAND Flash memory device (16 GB)●Two Gigabit Ethernet (RGMII) PHY devices●Two 120-pin high speed connectors to connect with NuMaker-BASE-MA35D1B1 board●One PMIC reset key button2.2 NuMaker-BASE-MA35D1B1 Features●Power:NUMAKER-HMI-MA35D1-S1 USER MANUAL M-m U –5V/2A Power Jack and Slide Switch●Debug/Trace:–UART0 debug port: USB Virtual COM (VCOM) port–Debug/Trace ports: SWJ (JTAG+SWD), ETM and SWD connectors●Memory Devices–An on-board Quad SPI NAND Flash device (512 MB)–An on-board NAND Flash device (1 GB)–Standard-SD (SD2.0) memory card slot●One power-on setting DIP-Switch for evaluation booting source selection●Two 120-pin high speed connectors to connect with NuMaker-SOM-MA35D16A81 board●Two sets of Gigabit Ethernet ports: Two Gigabit Ethernet transformer devices and two RJ45port connectors●Two sets of high speed USB ports: One Host/Device port and one Host port●Two camera capture (CMOS sensor) header connectors●One LCM connector to connect with 7’’ 1024x600 LCD da ughter board●One audio codec with microphone input and speaker output●One SIM card slot●One External Bus Interface (EBI) header connector●Two sets of UART transceivers and DB9 connectors●Two sets of RS485 transceivers and header connectors●Two sets of CAN FD transceivers and header connectors●One 8-channel ADC header connector●MEMS Mircrophone●MEMS G-Sensor●Three user key buttons●Two user LEDs●One set of buzzer pads2.3 7’’ TFT LCD Daughter Board Features●One LCD FPC connector to connect with 7’’ 1024x600 TFT LCD panel●One 4-wire resistive touch FPC connector●One connector to connect with NuMaker-BASE-MA35D1B1 board NUMAKER-HMI-MA35D1-S1 USER MANUAL Maker Nu-mbed NUC472 User ManualNUMAKER-HMI-MA35D1-S1 USER MANUALM-m U3HARDWARE CONFIGURATION3.1NuMaker-SOM-MA35D16A81 Board3.1.1Front ViewFigure 3-1 shows the main components and connectors from the front side of NuMaker-SOM-MA35D16A81 board. ●Target Chip (U1): MA35D16A887C (BGA312) MCP package with DDR3L (256MB).RGMII1 Gigabit PHY(U5, RTL8211FDI-CG)RGMII0Gigabit PHY(U4, RTL8211FDI-CG)Target Chip(U1, MA35D16A887C)eMMC NAND Flash (U3, THGBMJG7C2LBAU8)PMIC(U2, DA9062-3A)Battery Input(J48)PMIC Reset Key(SW1)Figure 3-1 Front View of NuMaker-SOM-MA35D16A813.1.2 Rear ViewFigure 3-2 shows the main components and connectors from the rear side of NuMaker-SOM-MA35D16A81 board.SOMHigh Speed Connector (P2, DF40C-120DP-0.4V (51))SOMHigh Speed Connector (P1, DF40C-120DP-0.4V (51))Figure 3-2 Rear View of NuMaker-SOM-MA35D16A813.1.3Power Input●5V Input (P2.1~6): DC 5V power input for the NuMaker-SOM-MA35D16A81 board that supplied from the base board through the pin 1 to pin 6 of SOM high speed connector P2.3.1.4 RTC Wake-up Control●Battery Input Connector (J48): DC 3V battery input connector to provide an additional optionalpower to keep the RTC power from the V BAT pin of MA35D1 when the system is power off.●RTC Wake-up Control Pins: The RTC_RPWR and RTC_nRWAKE pins of MA35D1 are the RTCwake-up control pins to control the related DC/DC power whether output voltages or not.Pin No. Pin Name of MA35D1 Function DescriptionU1.E7 RTC_RPWR*1RTC wake-up output pin for external DC/DC (forexample, the PMIC device DA9062-3A (U2) on thisNuMaker-SOM-MA35D16A81 board) enable pincontrol.U1.G5 RTC_nRWAKE*2*3RTC wake-up interrupt input with internal pull-high Note *1: This RTC_RPWR output pin of MA35D1 is not wired directly to the SYS_EN input pin (pin30) of PMIC device DA9062-3A (U2) on this NuMaker-SOM-MA35D16A81 board by default. (TheR89 resistor is NC, but R88 resistor is mounted on board by default)Note *2: This RTC_nRWAKE input pin is wired directly to the RTC Wakeup key button (SW3) onNuMaker-BASE-MA35D1B1 board and the R90 resistor is mounted on board by default.Note *3: This RTC_nRWAKE pin is internal pull-high. If user does not use the RTC wake-up interruptfunction, please pull this pin to low (the R90 is mounted on board by default). In this condition, useralso needs to disable the PWRST bit (RTC_PWRCTL[6]) of the RTC Power Control Register byclearing it for saving the RTC power consumption.Table 3-1 RTC Power Control Pins of MA35D13.1.5 PMIC NUMAKER-HMI-MA35D1-S1 USER MANUAL Maker Nu-mbed NUC472 User Manual●PMIC Reset Key Button (SW1): Press this key to pull the nRESETREQ (pin 16) of PMIC deviceDA9062-3A (U2) low to reset this PMIC device to supply the output voltages and control thenRESET signal following the default power-on sequence stored in the internal configuredinitialization.●PMIC (U2): After systerm power-on and pull the SYS_EN (pin 30) of the PMIC device DA9062-3A(U2) to high, the PMIC will follows the configured power-on sequence to supply all necessary anddifferent voltages to the target chip MA35D16A887C and dedicated peripherals on this NuMaker-SOM-MA35D16A81 board, and release the nRESET signal from low to high at the last onesequence step.U2.# Pin Name Output Voltage / MAX. CurrentU2.26 VBUCK1 DC 1.2V ~ 1.34V / 2.5AU2.27 VBUCK2 DC 1.2V / 2.5AU2.25 VBUCK3 DC 3.3V / 2AU2.24 VBUCK4*1DC 1.35V or 1.8V / 2AU2.1 VLDO1 DC 3V / 100mAU2.2 VLDO2 DC 1.8V / 300mAU2.9 VLDO3 DC 2.5V / 300mAU2.11 VLDO4*2DC 3.3V or 1.8V / 300mANote *1: The output voltage of VBUCK4 depends on the status of U2.28 pin and to supply the voltageto the internal DDR memory and DDR PHY of the target chip MA35D16A887C (MCP package withDDR3L SDRAM memory). By default, the U2.28 pin is pull-down to force VBUCK4 pin of PMIC tooutput 1.35V on this NuMaker-SOM-MA35D16A81 board.Note *2: No connection (NC) by default. For more detailed information about how to change the outputvoltage on VLDO4, please refer to the PMIC DA9062-3A Application Note on Nuvoton website.Table 3-2 PMIC (U2) Output VoltageU2.# Pin Name GPIO Function / Pin Nameof MA35D1U2.13 SDA PMIC_I2C0_SDA / PD6*1U2.14 SCL PMIC_I2C0_SCL / PD7*2U2.37 nIRQ PMIC_nIRQ / PA15*3U2.30 SYS_EN*4RTC_RPWR*5Note *1: This PD6 pin is dedicated as PMIC_I2C0_SDA function for controlling external PMIC bydefault.Note *2: This PD7 pin is dedicated as PMIC_I2C0_SCL function for controlling external PMIC bydefault.Note *3: This PA15 pin is dedicated as PMIC_nIRQ input function from external PMIC by default.Note *4: This SYS_EN input pin of PMIC device DA9062-3A (U2) is controlled by RTC_RPWR outputof MA35D1 by default. (The R89 resistor is mounted, but R88 resistor is NC by default)NUMAKER-HMI-MA35D1-S1 USER MANUAL M-m U Note *5: This RTC_RPWR output pin state of MA35D1 is controlled by RTC internal logic and theRTC_nRWAKE input pin state of the target chip MA35D16A887C. The RTC_nRWAKE input pin iscontrolled directly by the RTC Wake-up key (SW3) on NuMaker-BASE-MA35D1B1 board by default.(The R90 resistor is NC by default)Table 3-3 PMIC (U2) Control Pins3.1.6 eMMC NAND FlasheMMC1 NAND Flash Memory Device (U3): An on-board eMMC NAND Flash memory device (PTE7A0MI-16GI, 16 GB) for optional booting source. The booting source depends on the Power-on Setting by the status of DIP Switch (SW4) on the NuMaker-BASE-MA35D1B1 board.Function Name GPIO pin of MA35D1eMMC1_DAT4 PJ0eMMC1_DAT5 PJ1eMMC1_DAT6 PJ2eMMC1_DAT7 PJ3- PJ4*- PJ5*eMMC1_CMD PJ6eMMC1_CLK PJ7eMMC1_DAT0 PJ8eMMC1_DAT1 PJ9eMMC1_DAT2 PJ10eMMC1_DAT3 PJ11Note *: No connection (NC) by default.Table 3-4 eMMC1 NAND Flash Device (U3) Pin Function3.1.7 RGMII Gigabit PHY●RGMII0 Gigabit PHY (U4): The RGMII0 MAC of MA35D1 needs an external Gigabit PHY(RTL8211FDI) to transform signal and pass these 4-pair differential signals to the Ethernettransformer on NuMaker-BASE-MA35D1B1 board through the SOM high speed connector P1.Function Name GPIO pin of MA35D1RGMII0_MDC PE0RGMII0_MDIO PE1RGMII0_TXCTL PE2RGMII0_TXD0 PE3RGMII0_TXD1 PE4 NUMAKER-HMI-MA35D1-S1 USER MANUAL Maker Nu-mbed NUC472 User ManualRGMII0_RXCLK PE5RGMII0_RXCTL PE6RGMII0_RXD0 PE7RGMII0_RXD1 PE8RGMII0_RXD2 PE9RGMII0_RXD3 PE10RGMII0_TXCLK PE11RGMII0_TXD2 PE12RGMII0_TXD3 PE13Table 3-5 RGMII0 PHY (U4) Pin Funciton●RGMII1 Gigabit PHY (U5): The RGMII1 MAC of MA35D1 needs an external Gigabit PHY(RTL8211FDI) to transform signal and pass these 4-pair differential signals to the Ethernettransformer on NuMaker-BASE-MA35D1B1 board through the SOM high speed connector P1.Function Name GPIO pin of MA35D1RGMII1_MDC PF0RGMII1_MDIO PF1RGMII1_TXCTL PF2RGMII1_TXD0 PF3RGMII1_TXD1 PF4RGMII1_RXCLK PF5RGMII1_RXCTL PF6RGMII1_RXD0 PF7RGMII1_RXD1 PF8RGMII1_RXD2 PF9RGMII1_RXD3 PF10RGMII1_TXCLK PF11RGMII1_TXD2 PF12RGMII1_TXD3 PF13Table 3-6 RGMII1 PHY (U5) Pin Funciton3.1.8 High Speed ConnectorsSOM High Speed Connectors (P1 and P2): Two 120-pin high speed connectors (DF40C-120DP-0.4V (51)) to connect with the NuMaker-BASE-MA35D1B1 board.NUMAKER-HMI-MA35D1-S1 USER MANUAL M-m U Pin No. GPIO of MA35D1 or Function pin Pin No. GPIO of MA35D1 or Function pin1 PL42 nRESET3 PL54 RTC_nRWAKE5 PN146 VSS7 PD15 8 PN159 PN12 10 PK1511 PN13 12 PK1413 PN7 14 PK1315 PN6 16 PK1217 PN5 18 PL319 PN4 20 PL221 PN3 22 PL123 PN2 24 PL025 PN1 26 PJ1527 PN0 28 PJ1429 VSS 30 PJ1331 PN10 32 PJ1233 VSS 34 PL1535 PN11 36 PL1437 VSS 38 PL1339 PD9 40 PL1241 PD8 42 PL1143 PC4 44 PL1045 PC5 46 PD1447 PC0 48 PA1449 VSS50 PA1351 PC1 52 PA1253 VSS 54 PA1155 PC2 56 PA1057 PC3 58 PA9 NUMAKER-HMI-MA35D1-S1 USER MANUAL Maker Nu-mbed NUC472 User Manual59 PC7 60 PA861 PC6 62 PA763 VSS 64 PA665 E_MDIP0 66 PA567 E_MDIN0 68 PA469 VSS 70 PA371 E_MDIP1 72 PA273 E_MDIN1 74 PA175 VSS 76 PA077 E_MDIP2 78 PF1479 E_MDIN2 80 E_LED081 VSS 82 E_LED183 E_MDIP3 84 E_LED285 E_MDIN3 86 F_LED087 VSS 88 F_LED189 F_MDIP0 90 F_LED291 F_MDIN0 92 EADC0_CH793 VSS 94 EADC0_CH395 F_MDIP1 96 EADC0_CH697 F_MDIN1 98 EADC0_CH299 VSS 100 EADC0_CH5101 F_MDIP2 102 EADC0_CH1103 F_MDIN2 104 EADC0_CH4105 VSS 106 EADC0_CH0107 F_MDIP3 108 VSS109 F_MDIN3 110 HSUSB0_D+111 VSS 112 HSUSB0_D-113 PE15 114 VSS115 PE14 116 HSUSB1_D+117 HSUSB0_ID 118 HSUSB1_D-119 PF15 120 VSSNUMAKER-HMI-MA35D1-S1 USER MANUAL M-m U Table 3-7 SOM Connector 1 (P1) Pin FunctionPin No. GPIO of MA35D1 or Function pin Pin No. GPIO of MA35D1 or Function pin1 VDD5V2 VDD5V3 VDD5V4 VDD5V5 VDD5V6 VDD5V7 VSS 8 VSS9 PH3 10 PH411 PH2 12 PH513 PH1 14 PH615 PH0 16 PH717 PI15 18 PC1219 PI14 20 PC1321 PI13 22 PC1423 PI12 24 PC1525 PI11 26 PH1227 PI10 28 PH1329 PI9 30 PH1431 PI8 32 PH1533 PB15 34 VSS35 PB14 36 PG1037 PB13 38 VSS39 PB12 40 PG941 PB11 42 PG843 PB10 44 PK445 PB9 46 PK547 PB8 48 PK649 PK3 50 PK751 PK2 52 PM1553 PK1 54 PM1455 PK0 56 PM13 NUMAKER-HMI-MA35D1-S1 USER MANUAL Maker Nu-mbed NUC472 User Manual57 PI7 58 PM1259 PI6 60 VSS61 PI5 62 PL663 PI4 64 VSS65 PI3 66 PG1567 PI2 68 PG1469 PI1 70 PG1371 PI0 72 PG1273 PD13 74 PG1175 PD12 76 PG777 PD11 78 PG679 PD10 80 PG581 PL9 82 PG483 PL8 84 PG385 PL7 86 PG2。
REVAMP4120T 类电路驱动功耗大放大器说明书

REVAMP4120T Instruction manualREVAMP4120T3 REVAMP4120T manual4CLASS-D POWER AMPLIFIERIMPORTANT SAFETY INSTRUCTIONS1. R ead these instructions2. K eep these instructions3. P ay attention to all warnings4. F ollow all instructions5. T his professional device needs to be installed by qualified personnel only.6. D anger: Exposure to high sound levels may cause a permanent hearingloss. Individuals vary considerably to sound pressure level inducedhearing loss but nearly everyone will lose some hearing if exposed tohigh sound pressure levels for a sufficient amount of time. Thereforeit is recommended that all persons exposed to equipment capable ofproducing high sound pressure levels, such as this amplifier, be protectedby hearing protection while installing or operating this unit.7. M ake sure to only use power outlets conform to the power requirementslisted on the back of the unit.8. D o not connect the inputs / outputs of amplifiers or consoles to anyother voltage source, such as a battery, mains source, or power supply,regardless of whether the amplifier or console is turned on or off.9. D o not drive the inputs with a signal level higher than that required todrive equipment to full output.10. D o not run the output of any amplifier back into another input.11. T his unit has NOT been designed for use in mobile applications, suchas: mobile discobars, mobile PA systems, Live bands, audio rentalsystems, … Using it in such application will lead to product damages andsafety risks.12. D o not use this apparatus near water13. C lean only with dry cloth.14. D o not block any ventilation openings. Install in accordance with themanufacturer instructions.REVAMP4120T5 15. D o not install near any heat sources such as radiators, heat registers,stoves, or other apparatus (including amplifiers) that produce heat.16. D o not defeat the safety purpose of the polarized or grounding plug.Always use the device with a grounded mains power plug. If theprovided plug does not fit into your outlet, consult an electrician forreplacement of the obsolete outlet.17. P rotect the power cord from being walked on, pinched or damaged.Particularly at the plugs, connectors and at the point where they exitfrom the apparatus.18. O nly use attachments/accessories specified by the manufacturer.19. U nplug the apparatus during lightning storms or when unused for longperiods of time.20. U se only with the cart, stand, tripod, bracket, or table specified by themanufacturer, or sold with the apparatus. When a cart or rack is used,use caution when moving the cart/apparatus combination to avoid injuryfrom tip-over.21. R efer all servicing to qualified personnel. Servicing is required when theapparatus has been damaged in any way, such as power supply cordor plug is damaged, liquid has been spilled or objects have fallen intothe apparatus has been exposed to rain or moisture, does not operatenormally, or has been dropped.22. W ARNING: To reduce the risk of fire or electric shock, do not expose thisapparatus to rain or moisture. The apparatus shall not be exposed todripping or splashing and that objects filled with liquids, such as vases,shall not be placed on apparatus.23. W ARNING: The mains plug/appliance coupler is used as disconnectdevice, the disconnect device shall remain readily operable.6CLASS-D POWER AMPLIFIER24. T his lightning flash with arrowhead symbol within an equilateral triangleis intended to alert the user to the presence of non-insulated “dangerousvoltage” within the product’s enclosure that may be of sufficientmagnitude to constitute a risk of electric shock.- Warning: To reduce the risk of electric shock, do not remove cover (orback) as there are no user-serviceable parts inside. Refer servicing toqualified personnel.- The exclamation point within an equilateral triangle is intended toalert the user to the presence of important operating and maintenanceinstructions in the literature accompanying the appliance.25. P rotective earthing terminal. The apparatus should be connectedto a mains socket outlet with a protective earthing connection.26. Correct Disposal of this product. This marking indicates that thisproduct should not be disposed with other household wastesthroughout the EU. To prevent possible harm to the environment or human health from uncontrolled waste disposal, recycle it responsiblyto promote the sustainable reuse of material resources. To return yourused device, please use the return and collection systems or contact theretailer where the product was purchased. They can take this product forenvironmental safe recycling.27. N o naked flame sources, such as lighted candles, should be placed onthe apparatus.28. D o not install this equipment in a confined or building-in space suchas a book case or similar unit, and remain a well ventilation conditionsat open site. The ventilation should not be impeded by covering theventilation openings with items such as newspaper, table-cloths, curtainsetc.REVAMP4120T7 Features• 2 rack units high• High power Hypex® class-D power amplifier modules• Bridgeable 4 channel class-D amplifier• Output power: 4 x 120 W @ 100 V• Bridged output power: 2 x 240 W @ 100 V• High thermal efficiency• C onvectional cooling with temperature controlled cooling fan (normally off)• Integrated APC limiter/compressor• Soft start switching power supply unit• Toroidal 100 volt transformers• Switching mode power supply• Balanced euroblock inputs• Unbalanced inputs on RCA with pass through• Input level attenuators on all inputs• E uroblock speaker connectors with multiple taps: 35 volt, 50 volt, 70 volt, 100 volt and 4 ohm• E xtended speaker and amp protection circuits: over current protect, over temperature protect• Versatile LED status indicators• T his unit has NOT been designed for use in mobile applications, such as: mobile discobars, mobile PA systems, Live bands, audiorental systems, …• Removable rack-earsNote: the integrated APC limiter will automatically limit theincoming audio signal to avoid overloads. This feature can not be defeated and acts as a lifesaver for your valuable speakers.8CLASS-D POWER AMPLIFIER1. C hannel 2 overload led: when this led lights up, you areoverloading the input. Lower the input signal immediately to prevent the amplifier from shutting down.2. C hannel 2 unbalanced input and link cinch connector: connectthe line level input signal for channel 2 here. Line level is 0 dBV . Input and link connector are internally connected 1 on 1.3. C hannel 1 overload led: when this led lights up, you areoverloading the input. Lower the input signal immediately to prevent the amplifier from shutting down.ConnectionsOnly channel 1 and 2 are explained. Channel 3 and 4 are functionallyidentical to 1 and 2.126849573101112131514REVAMP4120T9 4. C hannel 1 unbalanced input and link cinch connector: connectthe line level input signal for channel 1 here. Line level is 0 dBV.Input and link connector are internally connected 1 on 1. Thisconnector is also used in bridge mode.5. C hannel 2 input gain setting: Adjust the input gain to theoutput level of your source. Make sure to avoid the clip ledlighting up at the strongest input peak level.6. Channel 2 balanced input on 3 pole euroblock connector.7. C hannel 1 input gain setting: Adjust the input gain to theoutput level of your source. Make sure to avoid the clip ledlighting up at the strongest input peak level.8. C hannel 1 balanced input on 3 pole euroblock connector: Thisconnector is used in bridge mode.9. H PF on/off dipswitch for channels 1 and 2: set to on position toenable the 250Hz highpass filter (ideal for using 100 volt hornspeakers)10. C hannel 2 output on euroblock: use the com (negative) incombination with one of the output options: low impedance (4ohms), 35 volt, 50 volt, 70 volt or 100 volt (positive). Never usemore than one output simultaneously.11. B ridge button: set to 2 channel for normal operation. Set tobridge mode for bridge mode operation.12. C hannel 1 output on euroblock: use the com (negative) incombination with one of the output options: low impedance (4ohms), 35 volt, 50 volt, 70 volt or 100 volt (positive). Never usemore than one output simultaneously.13. Fan area: keep free from dust and obstructions.10CLASS-D POWER AMPLIFIEROperation1. Removable rack ears for 19 rack mounting.2. Power switch.3. Power led.4. Channel 1 and 2 mute buttons and multifunctional led display.5. Channel 3 and 4 mute buttons and multifunctional led display.14. M ains voltage selector: set to 230 or 115 VAC according toyour local mains voltage.15. Mains voltage inlet:connect the mains power cord here.112345REVAMP4120T11• C lip – overload led indicates that the amplifier is overloaded or clipping: reduce the incoming signal immediately to avoidoverloads or clipping and eventually amplifier shutdown.• L imit – muted indicates that the internal limiter is active or that the channel is muted by pushing the mute button.• Signal -40dB indicates that a signal is present at the input• Mute button: push to mute/unmute the channel.• B ridged led (yellow) lights up when bridge mode is selected via the rear panel bridge pushbutton.12CLASS-D POWER AMPLIFIERIMPORTANTThis amplifier relies on convectional and active cooling. In normalsituations, overheating will not occur. The unit can be built in a 19inch rack system, but it is forbidden to block the ventilation holesprovided. Therefore, it is absolutely necessary to allow at leastone free rack space or 44 mm above and beneath the amplifier.Make sure the ambient temperature is between 0 and 35°C.Operating the unit beyond its normal limits will result in excessiveinternal temperature. Power amplifiers are hard workers, andtheir behaviour is similar to human beings. In extreme conditions,human beings are not able to perform efficiently. This also appliesto amplifiers. It is generally a bad idea to mount multiple heatgenerating units such as amplifiers in the same rack. If necessary,use an additional forced ventilation system in your mounting rack.The mains fuse is located inside the unit. When the fuse is broken,replace it with a fuse of the same current and voltage rating: 5AT/250V. For qualified personnel only!This unit has NOT been designed for use in mobile applications,such as: mobile discobars and DJ setups, mobile PA systems, Livebands, audio rental systems …Use it in fixed installations only.Before using the amplifier for the first time, check the impedanceof your 100 volt speaker lines using the Apart IMPMET: temporarilydisconnect the speaker line from the amplifier and measure the****************************************************value corresponds to 120 watts @ 100 volt.REVAMP4120T13 Technical specifications14CLASS-D POWER AMPLIFIER NotesdevelopedbyAudioprof nvIndustriepark Brechtsebaan 8 bus 12900 Schoten - BelgiumCompany names, product names and trademarks are property of theirrespective owners.Apart-Audio specifications are subject to change without notice.。
HR4988微特步进电机驱动芯片说明书
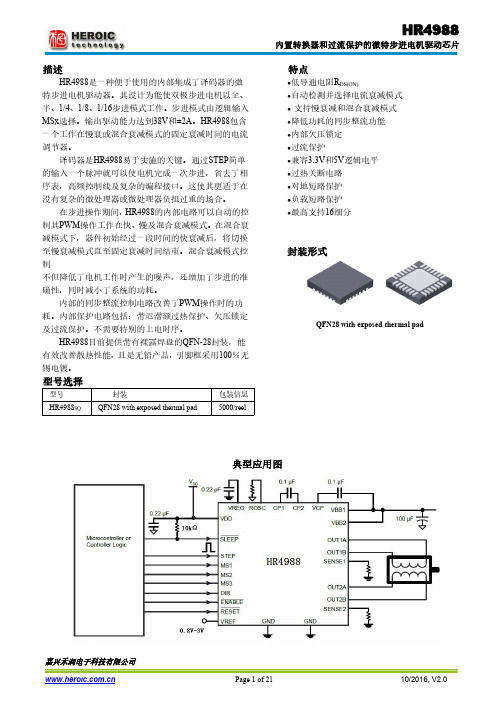
典型应用图描述HR4988是一种便于使用的内部集成了译码器的微特步进电机驱动器。
其设计为能使双极步进电机以全、半、1/4、1/8、1/16步进模式工作。
步进模式由逻辑输入MSx 选择。
输出驱动能力达到38V 和±2A 。
HR4988包含一个工作在慢衰或混合衰减模式的固定衰减时间的电流调节器。
译码器是HR4988易于实施的关键。
通过STEP 简单的输入一个脉冲就可以使电机完成一次步进,省去了相序表,高频控制线及复杂的编程接口。
这使其更适于在没有复杂的微处理器或微处理器负担过重的场合。
在步进操作期间,HR4988的内部电路可以自动的控制其PWM 操作工作在快、慢及混合衰减模式。
在混合衰减模式下,器件初始经过一段时间的快衰减后,将切换至慢衰减模式直至固定衰减时间结束。
混合衰减模式控制不但降低了电机工作时产生的噪声,还增加了步进的准确性,同时减小了系统的功耗。
内部的同步整流控制电路改善了PWM 操作时的功耗。
内部保护电路包括:带迟滞额过热保护、欠压锁定及过流保护。
不需要特别的上电时序。
HR4988目前提供带有裸露焊盘的QFN-28封装,能有效改善散热性能,且是无铅产品,引脚框采用100%无锡电镀。
型号选择型号封装包装信息HR4988SQQFN28with exposed thermal pad5000/reel特点●低导通电阻R DS(ON)●自动检测并选择电流衰减模式●支持慢衰减和混合衰减模式●降低功耗的同步整流功能●内部欠压锁定●过流保护●兼容3.3V 和5V 逻辑电平●过热关断电路●对地短路保护●负载短路保护●最高支持16细分封装形式QFN28with exposed thermal pad功能模块图电路工作极限at Ta=25°CParameter Symbol Conditions Ratings UnitLoad Supply Voltage V BB40VOutput Current I OUT±2ALogic Input voltage V IN-0.3to5.5VLogic Supply voltage V DD-0.3to5.5VMotor Output Votage-2.0to37V Sense Voltage V SENSE-0.5to0.5VReference Voltage V REF 5.5V Operating Ambient Temperature T A Range S-20to85°C Maximum Junction T J(max)150°CStorage Temperature T stg-55to150°C推荐工作条件at Ta=25°CMin NOM Max UnitV负载供电电压VBB8-38V逻辑供电电压VCC3- 5.5输出电流设置IOUT02A推荐外围设置1、ROSC:必要时,根据自身电机和应用控制频率选择合适的ROSC对地电阻,选择电流上升慢衰,下降混合衰,使电机电流纹波最小。
Atmel SAM4L-EK用户指南说明书

APPLICATION NOTEAtmel AVR32850: ATSAM4L-EK User GuideAtmel SAM4L Features•ATSAM4L-EK kit•Board description•Using the demonstration firmwareIntroductionThe ATSAM4L-EK is a reference design and development system for the 32-bit ARM® Cortex TM -M4 ATSAM4LC4C microcontroller from Atmel® Corporation. The kit is equipped with a rich set of peripherals that make the ATSAM4L-EK a perfect evaluation platform. This guide shows the user how to quickly get started with this kit.1. SAM4L-EK Description1.1 SAM4L-EK board featuresMCU ATSAM4LC4C (256KB flash, 32KB RAM), powered in 3.3VClock 12MHz crystal32.768kHz crystalConnector 1x USB Micro AB for the main CPU ATSAM4LC4C1x USB Micro B for emdedded debugger Segger J-Link-OB1x Audio jack connector (3.5mm)1x Sensors Xplained board connector (2x 10-pin headers)1x RS485 header (3-pin)Board power supply 5V DC from ATSAM4LC4C USB5V DC from Segger J-Link-OB USB5V DC from a 2-pin headerBoard monitor Dedicated MCU for power measurement of the ATSAM4LC4C (VDDIN, VDDIO, VDDANA)1x OLED Display (128x64)5x LEDs1x joystick1x USART connected to the ATSAM4LC4C MCU1x TWI connected to the ATSAM4LC4C MCU4x40 segment LCD Connected to the ATSAM4LC4C LCD interfaceMemory 1x serial flash AT25DF641AUser interface for the ATSAM4LC4C 1x QTouch® button 1x QTouch slider1x RESET button1x push button (PB0) 1x LED (LED0)1x light sensor1.2 Board interface connectionThe following connections are supported by the board:•USB Micro B connector for the embedded debugger and serial debug COM port interface Segger J-Link OB (USB connector J1)•USB Micro AB connector for the ATSAM4LC4C USB interface (USB connector J305)•1x Wireless 10-pins interface (with support of both ATEXTBT and RF2xx interfaces) (10-pin headers J207)•1x audio jack connector•1x RS485 connector for industrial transmitter (RS485)•2-pin header for external power supply (5V DC)Figure 1-1. ATSAM4L-EK features overview.Segger J-Link OB USBconnector (J1)1x QTouch slider1x wirelessinterface (J207)1x audio jack1x segment LCD1x LEDATSAM4LC4C USB (J305) 2-pin header for external powersupply (5V)5x LEDs (board monitor)1x joystick (board monitor)1x sensor Xplained connectors(J4-J5)1x RESET push button1x user input push button (PB0)1x QTouch key (CS0)2. Board description 2.1 HardwareFigure 2-1.ATSAM4L-EK block diagram.ATSAM4LC4C DEBUGSWDUSARTSystemControllerUser I/OExternal MemoriesDebugger(Segger J-Link OB)WirelessSPI+IOSPICATBOsc32KHz12MHzSerialDataFlash®I/OUSBUSBSPIBoardMonitorTWI EICPB0ABDACPowerRS485InterfaceUSARTUSARTI/OSAM4L powerconsumptionLCD SegmentLCDSensorXplainedBoardAnalogJackPowerSupplyVDDIN VDDANA VDDIOQTouch2.2 Powering the boardThe ATSAM4L-EK offers three interfaces to power the board:•USB embedded debugger Segger J-Link OB (J1)•USB ATSAM4LC4C (J305)•External 5V (DC) source connected to the J303 2-pin headerTo select the USB or external power supply, a mechanical switch is used (SW300).The default kit configuration is using ATSAM4LC4C buck regulator configuration, where ATSAM4LC4C is powered at3.3V (VDDIN, VDDIO, VDDANA).Figure 2-2. Power supply sources.(J305) USB ATSAM4LC4C(J1) USB Segger J-Link OBPower supply LED regulator is used2.3 Buttons / LEDThe ATSAM4L-EK is equipped with one user push button and one LED. The push buttons consist of momentary push button switches mounted directly to the board. When any switch is pressed it will cause a low (zero) to appear at the associated input pin.Table 2-1. User I/O mapping.PC03 LED0PC10 Push button PB02.4 QTouchThe ATSAM4L-EK is equipped with one QTouch button and one QTouch slider using three channels.Table 2-2. QTouch I/O mapping.PB04 QTouch ButtonPB02 QTouch Slider Channel 0PA04 QTouch Slider Channel 1PA05 QTouch Slider Channel 2PB03 QTouch Discharge Pin2.5 RS485The ATSAM4L-EK is equipped with a RS485 interface. To enable the RS485 connector:•Close J200 and J203 jumpers•Open J600 and J601 jumpersTable 2-3. RS485 I/O mapping.PA06 USART_RTS J100.2 to J103.3PC08 USART_CTS J104.2 to J104.3PC02 USART_RXD Close J200 and J203PA07 USART_TXD Open J600 and J6012.6 Light Sensor (ADC)The ATSAM4L-EK is equipped with one light sensor connected to one of the ADC channel. To enable it, close the jumper J101.2 to J101.3.Table 2-4. Light sensor I/O mapping.PB05 ADC Channel Close J101.2 to J101.32.7 Serial FlashThe ATSAM4L-EK is equipped with one serial flash AT25DF641, connected through SPI.Table 2-5. Serial Flash I/O mapping.PC04 SPI_MISOPC05 SPI_MOSIPC06 SPI_SCKPC00 SPI_CS2.8 AudioThe ATSAM4L-EK is equipped with one audio amplifier. To enable it, close J105.2 to J105.3 jumper.Table 2-6. Audio I/O mapping.PC09 Audio ABDAC Channel 0 Close J105.2 to J105.3PC13 Audio ABDAC Channel 1 Close J105.2 to J105.32.9 SAM4LC4C USBThe ATSAM4L-EK is equipped with one USB connector for the SAM4LC4C USB.Table 2-7. USB I/O mapping.PA25 USB DMPA26 USB DPPB05 USB ID pin (GPIO) Close J101.1 to J101.2PC07 USB Over current Detected (GPIO) Close J103.1 to J103.2PC08 USB Over current Enabled (GPIO) Close J104.1 to J104.22.10 WirelessThe ATSAM4L-EK is equipped with one 10-pin Wireless extension connector, to connect other Atmel boards like ATEXTBT or AT86RF2xxx.Table 2-8. Wireless I/O mapping.PC04 SPI_MISOPC05 SPI_MOSIPC06 SPI_SCKPA02 SPI_CS2.11 Sensors Xplained connectionThe ATSAM4L-EK is equipped with one Sensor Xplained extension connector. To enable it, close J102.2 to J102.3jumpers.Table 2-9. Sensors Xplained I/O mapping.PC04 SPI_MISOPC05 SPI_MOSIPC06 SPI_SCKPC01 SPI_CS Close J102.2 to J102.32.12 Embedded DebuggerThe embedded debugger J-Link OB Module is provided by Segger, featuring:•1x JTAG interface to the ATSAM4LC4C•1x UART interface to the ATSAM4LC4C•1x USB interface for a PC hostThe USART connection between the ATSAM4LC4C and the J-Link OB Module is configured as follow:Table 2-10. Embedded Debugger I/O mapping.PC11 USART_RXPC12 USART_TX2.13 Custom Glass DisplayThis board is equipped with a 4x40 segment LCD, connected to the ATSAM4LC4C device through the LDCA controller.Figure 2-3. ATSAM4LC4C on-board custom glass display.2.14 Board MonitorThe board monitor features:•1x OLED Display (128x64)•5x LEDs•1x joystick•1x USART connected to the ATSAM4LC4C MCU•1x TWI connected to the ATSAM4LC4C MCUThe USART connection between ATSAM4L and the board monitor is configured as:Table 2-11. Board Monitor I/O mapping.PC02 USART_RX Close J600.1 to J600.2 PA07 USART_TX Close J601.1 to J601.23. Using the preloaded firmwareThe SAM4L-EK firmware demo features:•Low power architecture:•Display ATSAM4LC4C power consumption on the board monitor OLED display•Use of the sleep mode•Use of the power scaling mode (PS0 or PS1)•Segment LCD controller:•Text display text and text scrolling•Hardware automatic animations•Hardware touch (QTouch) support:•One capacitive button and one slider3.1 Power-on the board•Power the board through the USB connector J1. The board starts the embedded debugger J-Link-OB USB enumerations•If you do not have installer Atmel Studio 6, install the Segger J-Link OB driver availablehere: /jlink-software.html3.2 Running the Demonstration Firmware1.1.1 Mode 1: “startup, RUN mode” (after power-on reset)• ATSAM4LC4C is in active mode (12MHz on RC4M) with segment LCD and QTouch enabled. TheATSAM4LC4C starts with power scaling enabled (PS1)• ATSAM4LC4C displays on the segment LCD:• A scrolling text message “SAM4L-EK Demo” •Scrolling animation to show SAM4L is in active mode• ATSAM4LC4C sends trough the USART its internal status to the board monitor (power save mode, voltagescaling, CPU frequency and clock source)• The board monitor displays on the OLED display the power consumption, power save mode, power scalingmode, CPU frequency and clock source of ATSAM4LC4C• After 5 seconds, the demo moves to mode 2.Clock sourceStatusPowersave modeCPU frequencyVoltage scaling1.1.2 Mode 2 “RUN mode with all features”•The ATSAM4LC4C is in RUN mode. ATSAM4LC4C displays the voltage scaling mode (PS1 or PS0) on the segment LCD and its active mode (RUN)•Using QTouch capacitive button CS0 will change voltage scaling configuration (PS1 or PS0)•The ATSAM4LC4C sends its internal status trough USART to the board monitor (power save mode, voltage scaling, CPU frequency and clock source) each time it changes•Using PB0 button will disable QTouch and segment LCD, the demo move to mode 31.1.3 Mode 3 “RUN mode with no features”•The ATSAM4LC4C in active mode (12MHz on RC4M) with power scaling mode PS1. QTouch and LCD are disabled•The ATSAM4LC4C is executing the Fibonacci algorithm•Using PB0 button will enter the WAIT sleep mode and move the demo to mode 41uA10100uA1mARUN PS112MHzRC4M10100 uA/MHz1.20 mAOLED Display12MHzRC4M1.1.4 Mode 4 “WAIT mode”•The ATSAM4LC4C is in WAIT mode with power scaling mode PS1•The ATSAM4LC4C sends its new internal status through USART to the board monitor (power save mode, voltage scaling, CPU frequency and clock source). The Board monitors displays a splash screen indicating thenew sleep mode (WAIT here)•Using PB0 button will enter the RETENTION sleep mode and move the demo to mode 51.1.5 Mode 5 “RETENTION mode”•The ATSAM4LC4C in RET mode with power scaling configuration PS1•The ATSAM4LC4C sends its new internal status through USART to the board monitor (power save mode, voltage scaling, CPU frequency and clock source)•Using PB0 button will enter the BACK-UP sleep mode and move the demo to mode 61uA10100uA1mAWAIT PS112MHzRC4M102 uAOLED Display12MHzRC4M1.1.6 Mode 6 “BACKUP mode”• The ATSAM4LC4C is in backup mode with power scaling mode PS1• The ATSAM4LC4C sends its new internal status through USART to the board monitor (power save mode,voltage scaling, CPU frequency and clock source)• Using PB0 button will go back to mode 1 in RUN mode4. References and further information4.1 Device datasheetThe device datasheet contains block diagrams of the peripherals and details about implementing firmware for thedevice. It also contains the electrical specifications and expected characteristics of the device.The datasheet is available on / in the Datasheets section of the product page.4.2 Detailed hardware references (and associated errata)More detailed hardware information for this kit can be found in the file ATSAM4L-EK_Hardware-References.zipavailable on the Atmel web page dedicated to this kit: /The ATSAM4L family of devices is specified in the SAM4L Series datasheet. Always use this document as a reference throughout the development life cycle of an application destined to run on a SAM4L device.4.3 ToolsTo be able to develop applications for 32-bit ARM devices and build binaries for ARM targets and program a 32-bit ARM device, Atmel and its partners provide several tools supported on multiple host targets.•Atmel Studio 6 is the integrated development environment (IDE) for developing and debugging Atmel ARM Cortex-M and Atmel AVR® microcontroller (MCU) based applications. The Atmel Studio 6 IDE gives you aseamless and easy-to-use environment to write, build and debug your applications written in C/C++ orassembly code./microsite/atmel_studio6/default.aspx•IAR Embedded Workbench®: IAR™ Embedded Workbench with its optimizing C and C++ compiler provides full support and generates very compact and efficient code for ARM device./en/Products/IAR-Embedded-Workbench/ARM/5. Revision history42026A 09/2012 Initial document releaseAtmel Corporation 2325 Orchard Parkway San Jose, CA 95131 USATel: (+1)(408) 441-0311 Fax: (+1)(408) 487-2600 Atmel Asia LimitedUnit 01-5 & 16, 19FBEA Tower, Millennium City 5418 Kwun Tong RoadKwun Tong, KowloonHONG KONGTel: (+852) 2245-6100Fax: (+852) 2722-1369Atmel Munich GmbHBusiness CampusParkring 4D-85748 Garching b. MunichGERMANYTel: (+49) 89-31970-0Fax: (+49) 89-3194621Atmel Japan G.K.16F Shin-Osaki Kangyo Building1-6-4 OsakiShinagawa-ku, Tokyo 141-0032JAPANTel: (+81)(3) 6417-0300Fax:(+81)(3) 6417-0370© 2012 Atmel Corporation. All rights reserved. / Rev.: 42026A−SAM4L−09/2012Atmel®, Atmel logo and combinations thereof, AVR®, DataFlash®, Enabling Unlimited Possibilities®, QTouch®, and others are registered trademarks or trademarks of Atmel Corporation or its subsidiaries. ARM®, Cortex™ are registered trademarks or trademarks of ARM Ltd. Other terms and product names may be trademarks of others.Disclaimer: The information in this document is provided in connection with Atmel products. No license, express or implied, by estoppel or otherwise, to any intellectual property right is granted by this document or in connection with the sale of Atmel products. EXCEPT AS SET FORTH IN THE ATMEL TERMS AND CONDITIONS OF SALES LOCATED ON THE ATMEL WEBSITE, ATMEL ASSUMES NO LIABILITY WHATSOEVER AND DISCLAIMS ANY EXPRESS, IMPLIED OR STATUTORY WARRANTY RELATING TO ITS PRODUCTS INCLUDING, BUT NOT LIMITED TO, THE IMPLIED WARRANTY OF MERCHANTABILITY, FITNESS FOR A PARTICULAR PURPOSE, OR NON-INFRINGEMENT. IN NO EVENT SHALL ATMEL BE LIABLE FOR ANY DIRECT, INDIRECT, CONSEQUENTIAL, PUNITIVE, SPECIAL OR INCIDENTAL DAMAGES (INCLUDING, WITHOUT LIMITATION, DAMAGES FOR LOSS AND PROFITS, BUSINESS INTERRUPTION, OR LOSS OF。
SICK 加速器传感器 WTR、WLR 和 ZLM1 的产品说明说明书
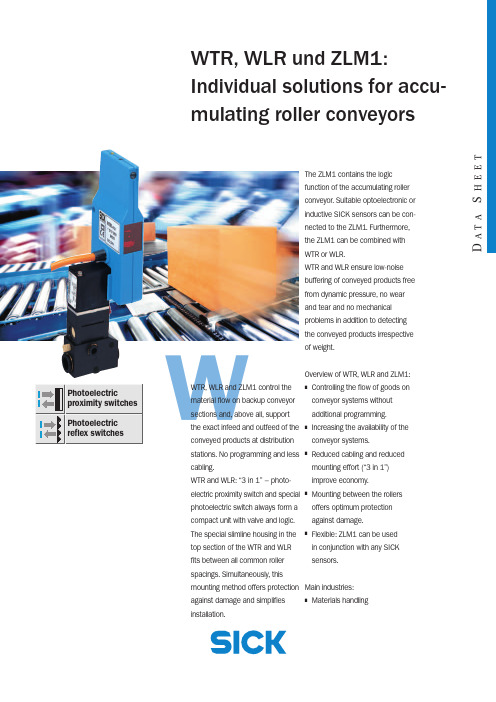
WWTR, WLR und ZLM1:Individual solutions for accu-mulating roller conveyorsWTR, WLR and ZLM1 control the material flow on backup conveyor sections and, above all, support the exact infeed and outfeed of the conveyed products at distribution stations. No programming and lesscabling. WTR and WLR: “3 in 1” – photo-electric proximity switch and special photoelectric switch always form a compact unit with valve and logic.The special slimline housing in the top section of the WTR and WLR fits between all common roller spacings. Simultaneously, thismounting method offers protection against damage and simplifiesinstallation.The ZLM1 contains the logic function of the accumulating roller conveyor. Suitable optoelectronic or inductive SICK sensors can be con-nected to the ZLM1. Furthermore,the ZLM1 can be combined with WTR or WLR.WTR and WLR ensure low-noise buffering of conveyed products free from dynamic pressure, no wear and tear and no mechanical problems in addition to detecting the conveyed products irrespectiveof weight.Overview of WTR, WLR and ZLM1:■Controlling the flow of goods on conveyor systems without additional programming.■Increasing the availability of the conveyor systems.■Reduced cabling and reduced mounting effort (“3 in 1”) improve economy.■Mounting between the rollers offers optimum protection against damage.■Flexible: ZLM1 can be used in conjunction with any SICK sensors.Main industries:■Materials handlingDA T ASH E E T2S I C K 2009-04-08L o g i c f u n c t i o n s :– S i n g l e Fe e d – S i n g l e R e l e a s e – S l u g R e l e a s e – S l e e p m o d e – A w a k e m o d eWTR, WLR und ZLM1Valve type Conveyed product is not detected.Conveyed product is detected.De-ener-gised and closedValve energisedAir flows into the cylinderValve de-energisedCylinder is vented via valveDe-ener-gised and openValve energisedCylinder is vented via valve Valve de-energisedAir flows into the cylinderWTR, WLR, ZLM12009-04-08S I C K3WTR Photoelectric proximity switches for accumulation roller conveyors 4S I C K2009-04-08WTR, WLR and ZLM1: logic functions for accumulating roller conveyorsThe logic functions of the WTR, WLR and ZLM1 ensure a controlled flow of products, sothat the conveyed products are started at the defined segments within a conveyor belt.The logic functions autonomously control the accumulating roller conveyor and, in particular,support the exact infeed and outfeed of the conveyed products at the distribution stations.The conveyed goods pass through the feed area and will not be stopped until they reach the last WTRn of the WTR line.The conveyor section of the WTRn is occupied. The WTRn passes this informa-tion onto the WTRn-1, i.e. the next conveyed good is detected by WTRn-1 and stopped in the correspond-ing section n-1 etc.Basic function which occurs at any point on the conveyor system:An object on the roller conveyor is stopped when two successive sections are occupied. Even if the flow of the conveyed goods per hour is increased, it still remains controlled because a defined space between the goods is given.21The release of the con-veyed goods from the sec-tion of the WTRn is initiated by electrical control of the WTRn (+24 V at input “E” of the WTRn).The section of the WTRn starts and is not occupied any longer as soon as the WTRn does not see any object. The information will be passed onto the WTRn-1which in turn starts the cor-responding section etc. Inthis way, the objects are transported section by section.The manual release of the conveyed goods from the section of the WTRn has the same effect as the release by electrical control.21It is possible to increase the flow of goods by starting all sections within a WTR line at the same time. This will be initiated by activating the last WTRn (+24 V at input “VT”of the WTRn).S i n g l e Fe e dS i n g l e R e l e a s e – e l e c t r i c a l –S i n g l e R e l e a s e – m a n u a l –S l u g R e l e a s eWTR2009-04-08S I C K 5S l e e p m o d eA w a k e m o d eThe WTR2-P621S22 and the WLR2-P610S01 contain additional logic functions, usually,used in conjunction with motorised rollers.After the motorised rollers have been switched off by the sleep mode, the motorised rollersare successively re-energised with the wake-up mode.If the conveyed product has left the beam path of a WTR then, after 9 sec.approx., the connected motorised roller is switched off.1st option:At the beginning of the conveyor belt, the WTR1requires an external start signal (+24 V DC on input “E2”), so that the wake-up mode is activated and the motorised roller in the first segment is switched on .When the conveyed product has been moved into the WTR1’s beam path, then this informa-tion is passed on to the WTRn, so that the motorised roller in the segment (WTRn...) is switched on etc. .212nd option:When the conveyed prod-uct is placed onto any segment (WTRn...), then the associated motorisedroller in this segment is switched on. Simultane-ously, a signal is given to the WTRn-1 which switches the motorised roller on. When the con-veyed product has reached the beam path of the WTRn-1, a signal is given, in turn, to the WTRn which then switches the associated motorised roller on etc.WTR Photoelectric proximity switches for accumulation roller conveyors6S I C K 2009-04-08WTR1-P421, WTR1-P721, WTR1-P721 S09, WTR1-P721 S10 (picture on the left): Photoelectric proximity switch, solenoid valve and logic, single feedWTR1-P821 (picture on the left):Photoelectric proximity switch, solenoid valve and logic, block feed. WTR1-P421 S02 (picture on the right):Photoelectric proximity switch, solenoid valve and logic, single feed.Advantages of the SICK conceptIn general, a conveyor system is uniformly equipped with one single type of WTR. Depend-ing on the application T-pieces and other WTR types which should be adapted to the appli-cation may also be used.This simplifies procurement and installation, reduces stock of spare parts and prevents confusion of different types of unit.Standardisation within the conveyor systems is increased.WTR1-P421 S08, WTR2-P621:Photoelectric proximity switch, logic, cable for connecting solenoid valve or motor.WTR2-P621S22:Photoelectric proximity switch, logic specially for motorised rollers.WTR2-P521, WTR2-P511:Without logic and without solenoid valve.Accessories1.Bracket for mounting the WTR2.T-piece to be used for ■additional power supply to increase the maximum number of WTRs■interrogation of the status of a WTR or its corresponding conveyor section■interruption of the logic at any point and its reset3.Cable receptaclesWTRApplication examplesPossibilities of control and information interrogation of the WTR, WLR or ZLM1 forprocessing in an external control system (simplified description).Please contact us, especially for detection of critical objects, e.g. reflecting, irregular or verysmall surfaces. We recommend to carry out tests with the original conveyed goods.2009-04-08S I C K7WTR1 Photoelectric proximity switches for accumulation roller conveyors8S I C K2009-04-08Centre of transmitter’s optical axis Centre of receiver’s optical axis Cable with receptacle, 4-pin Solenoid valveMedia connector (2 x) l 8 x 1M12 plug, 4-pinMounting holes l 4.5LED signal strength indicator Scanning distance adjustment Control for timing element3 in 1: Photoelectric proximity switch, valve and logic form a compact unitBackground suppressionContinuously variable scanning distanceIntegrated logic for accumulatingroller conveyorsE M EM VT 2)VT Direction of transport198********)-P821: R 2)-P821: A VT1)Average service life 100,000 hat T A = +25 °C2)Limit values3)May not exceed or fall short ofV S tolerances4)Without load, without valve5)Don not bend cable below 0 °C6)Max. per power supply at 27.6 V DC7)Reference voltage 50 V DC8)A=Inputs/outputs reverse-polarityprotectedB=Outputs short-circuit protectedC=Interference pulse suppression9)Other valve types available on requestMedium: Compressed air or neutral gas-es (filtered) lubricated or unlubricated10)In combination with cylinders with smallair volume we recommend tests0 (mm) 200 400 600 800 1000(mm) 400 500 600 700 800 90010987654321%ofscanningdistanceWTR1 2009-04-08S I C K9WTR1/2 Photoelectric proximity switches for accumulation roller conveyors10S I C K2009-04-08Centre of transmitter’s optical axis Centre of receiver’s optical axis Cable with receptacle, 4-pin M12 plug, 4-pinCable without plug for motor or valve Mounting holes l 4.5Electrical connection via plug lugs (to DIN 43650 Form C)LED signal strength indicator Scanning distance adjustmentIntegrated logic for accumulating roller conveyors, especially for motorised rollersBackground suppressionContinuously variable scanning distanceConnection for motor or valveE M VTEM L+A M VT 2)9876543211)WTR2-P621S22: A 22)WTR2-P621S22: E 23)WTR1-P421S08:No cable to valve (plug-in)1)Average service life 100,000 hat T A = +25 °C2)Limit values without load, withoutsolenoid valve3)May not exceed or fall short ofV S tolerances4)Without load, without valve5)Do not bend cable below 0 °C6)Max. per individual feed at 27.6 V DCas well as dependent on the solenoidvalve (1W)/motor7)Reference voltage 50 V DC8)A=Inputs/outputs reverse-polarityprotectedB=Outputs short-circuit protectedC=Interference pulse suppression0 (mm) 200 400 600 800 1000(mm) 400 500 600 700 800 90010987654321%ofscanningdistanceWTR1/2 2009-04-08S I C K11WTR2 Photoelectric proximity switches for accumulation roller conveyors12S I C K 2009-04-08Centre of transmitter’s optical axis Centre of receiver’s optical axis M12 plug, 4-pinMounting holes l 4.5LED signal strength indicator Scanning distance adjustmentContinuously variable scanning distanceBackground suppressionL+NC M Q P6543211)Average service life 100,000 h at T A = +25 °C 2)Limit values3)May not exceed or fall short of V S tolerances4)Without load, without valve 5)Reference voltage 50 V DC6)A =Inputs/outputs reverse-polarityprotectedB =Outputs short-circuit protectedC =Interference pulse suppression0 (mm) 200 400 600 8001000(mm) 400500600700800900109876543210%of s c a nn i n g d i s t a n c eWTR22009-04-08S I C K 13WLR1 Special photoelectric reflex switch, red light for accumulation roller conveyors14S I C K2009-04-08Centre of transmitter’s optical axis Centre of receiver’s optical axis Cable with receptacle, 4-pin Solenoid valveMedia connector (2 x) ø 8 x 1M12 plug, 4-pinMounting holes ø 4.5Signal strength indicator Sensitivity control3 in 1: Special photoelectric reflex switch (FGS adjustable), valve and logic form a compact unitVery insensitive against mirroring,reflecting, shiny, depolarizeing surfacesIntegrated logic for accumulating roller conveyorsE ML+A M VTE M VT987654321WLR12009-04-08S I C K 151)Average service life 100,000 h, at T A = +25 °C 2)Limit values3)May not exceed or fall short of V S tolerances4)Without load, without valve 5)Do not bend cable below 0 °C 6)Max. per power supply at 27.6 V DC7)Reference voltage 50 V DC8)A = Inputs/outputs reverse-polarityprotectedB = Outputs short-circuit protectedC = Interference pulse suppression9)In relation with cylinder with small air volume we recommend tests– Diamond Grade reflective tape (prefabricated) should be installed at max. 1.5 m away from WLR – Align red light spot of WLR on the middle of the reflector, LED (8) ON– Turn sensitivity control (9) to the right until you’ve reach max., LED (8) OFF– Turn sensitivity control (9) back again to the left until LED (8) is constant luminously – WLR is adjustedWLR2 Special photoelectric reflex switch, red light for accumulation roller conveyors16S I C K2009-04-08Centre of transmitter’s optical axis Centre of receiver’s optical axis Cable with receptacle, 4-pin Plug M12, 4-pin Cable for motorMounting holes ø 4.5 mm LED signal strength indicator Scanning distance adjustmentSpecial photoelectric reflex switch (FGS adjustable)Very insensitive against mirroring,reflecting, shiny, depolarizeing surfacesIntegrated logic for accumulating roller conveyors, especially formotorised rollersE 1M A 2L+A 1M E 2E A A 1E 2M 87654321WLR22009-04-08S I C K 171)Average service life 100,000 h, at T A = +25 °C 2)Limit values3)May not exceed or fall short of V S tolerances4)Without load, without valve 5)Do not bend cable below 0 °C6)Max. per individual infeed at 27.6 V DC as well as dependent on the magnetic valve (1 W)/motor resp. separate power supply for motorised rollers 7)Reference voltage 50 V DC8)A = Inputs/outputs reverse-polarityprotectedB = Outputs short-circuit protectedC = Interference pulse suppression– Diamond Grade reflective tape (prefabricated) should be installed at max. 1.5 m away from WLR – Align red light spot of WLR on the middle of the reflector, LED (8) on– Turn sensitivity control (9) to the right until you’ve reach max., LED (8) off– Turn sensitivity control (9) back again to the left until LED (8) is constant luminously – WLR is adjustedZLM1-B Logic module with solenoid valve for accumulation roller conveyors18S I C K2009-04-08Cable with M12 socket, 4-pin Solenoid valveConnection for sensor, cable with M12socket, 4-pin or M8 socket, 4-pin M12 plug, 4-pinMedia connector (2 x) ø 8 mmLogic module with logic mode and solenoid valve for accumulation roller conveyorsConnection for different kinds of SICK sensors are possible Compatible with WTR1Adjustable release delay (ZLM1-B5612E41 only)E M L+A M VTE M VTDirection of transport21345543211)for ZLM1-B5612E41 = 93 mm2)ZLM1-B5612E41 with time controlZLM1-B2009-04-08S I C K 19Sensor output requirements PNP, reflex switch: light-switching;Proximity switch: dark-switching 5)PNP, inductive sensor: 5)1)Limit values, the device may connect only to protected extra low voltage 2)May not exceed or fall short of V S tolerances3)Without load, without valve, without sensor4)Do not bend cable below 0 °C5)Additional adapter is required to put pin 2 at the sensor onto pin 4 for the ZLM16)Max. per feed to 26.4 V DC as well as current consumption by the sensors7)A = Inputs/outputs reverse-polarityprotectedB = Outputs short-circuit protectedC = Interference pulse suppression8)Other valve types available on request 9)In combination with cylinders with small air volume we recommend testsSICK AG | Waldkirch | Germany | 2009-04-08 G O /G O P r i n t e d i n G e r m a n y (2009-04) S u b j e c t t o c h a n g e w i t h o u t n o t i c e T h e s p e c i f i e d p r o d u c t f e a t u r e s a n d t e c h n i c a l d a t a d o n o t r e p r e s e n t a n y g u a r a n t e e 01 A 4 4c i n t 32AustraliaPhone +61 3 9497 4100 1800 33 48 02 – tollfree ********************.au Belgium/Luxembourg Phone +32 (0)2 466 55 66E-Mail ************BrasilPhone +55 11 3215-4900E-Mail ************.br Ceská RepublikaPhone +420 2 57 91 18 50E-Mail ************ChinaPhone +852-2763 6966E-Mail ************.hk DanmarkPhone +45 45 82 64 00E-Mail ************DeutschlandPhone +49 211 5301-250E-Mail ************EspañaPhone +34 93 480 31 00E-Mail ************FrancePhone +33 1 64 62 35 00E-Mail ************Great BritainPhone +44 (0)1727 831121E-Mail ************.uk IndiaPhone +91–22–4033 8333*************************IsraelPhone +972-4-999-0590E-Mail *********************ItaliaPhone +39 02 27 43 41E-Mail ************JapanPhone +81 (0)3 3358 1341E-Mail ***************NederlandsPhone +31 (0)30 229 25 44E-Mail ************NorgePhone +47 67 81 50 00E-Mail ******************ÖsterreichPhone +43 (0)22 36 62 28 8-0E-Mail **************PolskaPhone +48 22 837 40 50E-Mail ************Republic of KoreaPhone +82-2 786 6321/4E-Mail ******************Republika SlowenijaPhone +386 (0)1-47 69 990E-Mail **************RomâniaPhone +40 356 171 120 ********************RussiaPhone +7 495 775 05 34E-Mail ***********************SchweizPhone +41 41 619 29 39E-Mail ***************SingaporePhone +65 6744 3732E-Mail *****************.sg SuomiPhone +358-9-25 15 800E-Mail ************SverigePhone +46 10 110 10 00E-Mail ************TaiwanPhone +886 2 2375-6288E-Mail *****************.net TürkiyePhone +90 216 587 74 00E-Mail *************.trUSA/Canada/MéxicoPhone +1(952) 941-6780 1 800-325-7425 – tollfree E-Mail ****************More representatives and agencies in all major industrial nations at 。
微特迈WTM-G4L主板

想在在市面上,像技嘉,威刚等主板在性能上已经算是做到比较领先的地位了,但是他们在行业性还有待完善,现在很多不同行业使用主板都有一个共同的呼吁,那就是是否有一阵套通用的主板,比如在游戏娱乐行业,KTV点歌系统,监控系统,银行领域,数字标牌领域,工业工控领域等事项同领域共享的一类主板,最新发现一款intel在大陆直接厂商微特迈联合多家知名主板厂家共同研发了一款新型主板,强悍的支持多领域功能,工业上使用无可挑剔!那就是WTM-G4L主板,WTM的主板特别WTM-G4L主板对于个人感觉像这样高性能强悍的主板,用于一般的电脑实在是浪费了,推荐用作工业工控行业的朋友使用,还有自带开发拓展功能,实在不错了。
废话不多说,直接进入正题!下面来欣赏一下他的强悍参数规格和靓照!版面概图Mini-itx主板WTM-G4L规格:处理器·Socket775,支持支持Intel Celeron 400、Pentium 4、Pentium 4 EE、Pentium D、Pentium EE、Celeron Dual-Core、Pentium Dual-Core、Core 2 Duo、Core 2 Quad、Core 2 Extreme芯片组·Intel® G41 + 82801GB显示接口·支持VGA·18至24位单双通道LVDS输出·支持VGA+LVDS,可同步或异步双显示输出显示性能·Intel Graphics Media Accelerator X4500,核心频率400MHz,集成350MHz RAMDAC;完整支持DirectX 10和Shader Model 4.0以及OpenGL 2.0,支持Intel Clear Video Technology(英特尔清晰视频技术)和高清视频硬件解码内存·1*DDR3 SDRAM内存槽,最大至4GB电源·ATX, 20pin+4pin存储·4* Serial II ATA接口,支持3Gb/s·1*40pin IDE支持DOM直接供电,无需接供电线缆网络·板载2*RTL 8111DL 1000 BaseT LAN,支持RTL和PXE无盘启动声音·瑞昱ALC662芯片,提供6声道输出LVDS ·LVDS支持18至24位单双通道LVDS输出GPIO ·8路输入输出USB ·8*USB 2.0背板接口·PS/2键盘鼠标·1*VGA·1*COM·1*LPT·2*RJ-45 1000M·4*USB 2.0·1*AUDIO/MIC内置接口·2*USB排针,支持4个USB·1*VGA输出扩展排针·1*DVI/HDMI输出扩展排针·1*COM1排针·1*COM2排针·3*FAN供电接口·1*LVDS接口·1*MINI-SATA接口·1*MINI-PCIE接口·1*电源输出4P·2*SATA·1*GPIO·1*SIM卡座BIOS ·AMI 8M BIOS, ACPI supported,支持来电开机功能温度·工作:0-60摄氏度·仓储:在-20~80摄氏度·湿度:10%~90%板型·MINI-ITX(170mm*170mm)重要部位图片展示:富士康脚座,支持全系列775 CPUDDR3代内存槽PCI槽COM3-6VGA COM LPT输出RTL8111DL双千兆网络接口VGA,USB1,COM2扩展排针1个IDE,4个SATA接口看到这么强悍的主板,不知道对大家有没有帮助,或者可以去微特迈官网了解一下具体的信息。
微特迈WTM-1714主板
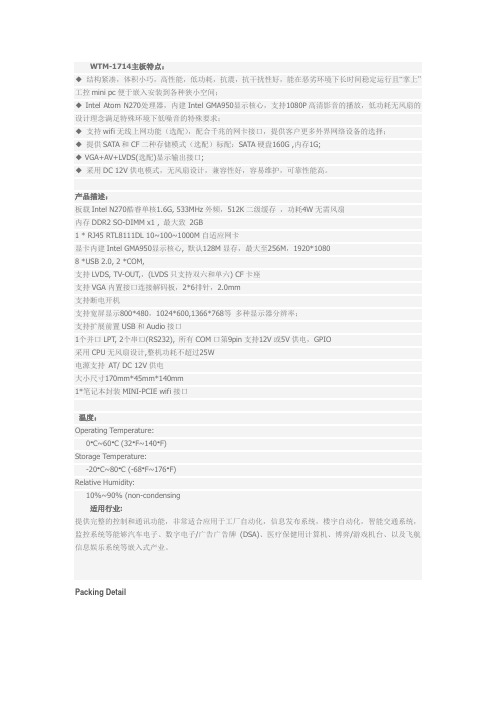
WTM-1714主板特点:◆结构紧凑,体积小巧,高性能,低功耗,抗震,抗干扰性好,能在恶劣环境下长时间稳定运行且“掌上”工控mini pc便于嵌入安装到各种狭小空间;◆ Intel Atom N270处理器,内建Intel GMA950显示核心,支持1080P高清影音的播放,低功耗无风扇的设计理念满足特殊环境下低噪音的特殊要求;◆支持wifi无线上网功能(选配),配合千兆的网卡接口,提供客户更多外界网络设备的选择;◆提供SATA和CF二种存储模式(选配)标配:SATA硬盘160G ,内存1G;◆ VGA+AV+LVDS(选配)显示输出接口;◆采用DC 12V供电模式,无风扇设计,兼容性好,容易维护,可靠性能高。
产品描述:板载Intel N270酷睿单核1.6G, 533MHz外频,512K二级缓存,功耗4W无需风扇内存DDR2 SO-DIMM x1 , 最大致2GB1 * RJ45 RTL8111DL 10~100~1000M自适应网卡显卡内建Intel GMA950显示核心, 默认128M显存,最大至256M,1920*10808 *USB 2.0, 2 *COM,支持LVDS, TV-OUT,,(LVDS只支持双六和单六) CF卡座支持VGA内置接口连接解码板,2*6排针,2.0mm支持断电开机支持宽屏显示800*480,1024*600,1366*768等多种显示器分辨率;支持扩展前置USB和Audio接口1个并口LPT, 2个串口(RS232), 所有COM口第9pin支持12V或5V供电,GPIO采用CPU无风扇设计,整机功耗不超过25W电源支持AT/ DC 12V供电大小尺寸170mm*45mm*140mm1*笔记本封装MINI-PCIE wifi接口温度:Operating Temperature:0°C~60°C (32°F~140°F)Storage Temperature:-20°C~80°C (-68°F~176°F)Relative Humidity:10%~90% (non-condensing适用行业:提供完整的控制和通讯功能,非常适合应用于工厂自动化,信息发布系统,楼宇自动化,智能交通系统,监控系统等能够汽车电子、数字电子/广告广告牌(DSA)、医疗保健用计算机、博弈/游戏机台、以及飞航信息娱乐系统等嵌入式产业。
- 1、下载文档前请自行甄别文档内容的完整性,平台不提供额外的编辑、内容补充、找答案等附加服务。
- 2、"仅部分预览"的文档,不可在线预览部分如存在完整性等问题,可反馈申请退款(可完整预览的文档不适用该条件!)。
- 3、如文档侵犯您的权益,请联系客服反馈,我们会尽快为您处理(人工客服工作时间:9:00-18:30)。
想在在市面上,像技嘉,威刚等主板在性能上已经算是做到比较领先的地位了,但是他们在行业性还有待完善,现在很多不同行业使用主板都有一个共同的呼吁,那就是是否有一阵套通用的主板,比如在游戏娱乐行业,KTV点歌系统,监控系统,银行领域,数字标牌领域,工业工控领域等事项同领域共享的一类主板,最新发现一款intel在大陆直接厂商微特迈联合多家知名主板厂家共同研发了一款新型主板,强悍的支持多领域功能,工业上使用无可挑剔!那就是WTM-G4L主板,WTM的主板特别WTM-G4L主板对于个人感觉像这样高性能强悍的主板,用于一般的电脑实在是浪费了,推荐用作工业工控行业的朋友使用,还有自带开发拓展功能,实在不错了。
废话不多说,直接进入正题!
下面来欣赏一下他的强悍参数规格和靓照!
版面概图
Mini-itx主板WTM-G4L规格:
处理器·Socket775,支持支持Intel Celeron 400、Pentium 4、Pentium 4 EE、Pentium D、Pentium EE、Celeron Dual-Core、Pentium Dual-Core、Core 2 Duo、Core 2 Quad、Core 2 Extreme
芯片组·Intel® G41 + 82801GB
显示接口·支持VGA
·18至24位单双通道LVDS输出
·支持VGA+LVDS,可同步或异步双显示输出
显示性能·Intel Graphics Media Accelerator X4500,核心频率400MHz,集成350MHz RAMDAC;完整支持DirectX 10和Shader Model 4.0以及OpenGL 2.0,支持Intel Clear Video Technology(英特尔清晰视频技术)和高清视频硬件解码
内存·1*DDR3 SDRAM内存槽,最大至4GB
电源·ATX, 20pin+4pin
存储·4* Serial II ATA接口,支持3Gb/s
·1*40pin IDE支持DOM直接供电,无需接供电线缆
网络·板载2*RTL 8111DL 1000 BaseT LAN,支持RTL和PXE无盘启动
声音·瑞昱ALC662芯片,提供6声道输出
LVDS ·LVDS支持18至24位单双通道LVDS输出
GPIO ·8路输入输出
USB ·8*USB 2.0
背板接口·PS/2键盘鼠标
·1*VGA
·1*COM
·1*LPT
·2*RJ-45 1000M
·4*USB 2.0
·1*AUDIO/MIC
内置接口·2*USB排针,支持4个USB
·1*VGA输出扩展排针
·1*DVI/HDMI输出扩展排针
·1*COM1排针
·1*COM2排针
·3*FAN供电接口
·1*LVDS接口
·1*MINI-SATA接口
·1*MINI-PCIE接口
·1*电源输出4P
·2*SATA
·1*GPIO
·1*SIM卡座
BIOS ·AMI 8M BIOS, ACPI supported,支持来电开机功能
温度·工作:0-60摄氏度·仓储:在-20~80摄氏度·湿度:10%~90%
板型·MINI-ITX(170mm*170mm)
重要部位图片展示:
富士康脚座,支持全系列775 CPU
DDR3代内存槽
PCI槽
COM3-6
VGA COM LPT输出
RTL8111DL双千兆网络接口
VGA,USB1,COM2扩展排针
1个IDE,4个SATA接口
看到这么强悍的主板,不知道对大家有没有帮助,或者可以去微特迈官网了解一下具体的信息。