冷拔钢管产品缺陷一览表
冷拔质量缺陷与解决办法

冷拔质量缺陷与解决办法划道和擦伤:划道和擦伤缺陷的特征是,在钢管的内外表面上呈现纵向宜线形的长短不一的划痕,多为沟状,但也可能是凸起的条纹。
产生划道和擦伤的主要原因是:在管料上有内划道在拔制时未能消除,钢管上残留着氧化铁皮,模具粘钢,模具强度和硬度不够或不均,模具出现碎裂和磨损,锤头不良,锤头过渡部分的尖锐梭角损伤了模具等。
为了防止产生划道和擦伤应该提高拔制前各准备工序的质量和使用强度及硬度高、光洁度好的模具1.表面铸造缺陷1 拉伤(1)特征:①沿开模方向铸件表面呈线条状的拉伤痕迹,有一定深度,严重时为整面拉伤;②金属与模具表面粘和,导致铸件表面缺料。
(2)产生原因:①模具型腔表面有损伤;②出模方向无斜度或斜度过小;③顶出不平衡;④模具松动:(3)处理方法:①修理模具表面损伤;(修理后光洁度一定要好)②修正斜度,提高模具表面光洁度;③调整顶杆,使顶出力平衡;④紧固模具;2.锤头原因;(1)产生原因:毛管上残存氧化皮(2)处理方法:锤头过度部分要圆滑无棱角。
2.打头不足原因:要求对φ60的无缝钢管进行打头时的推进翻转设计,要求要有动力系统有关参数选择和相关计算以及结构参数设计计算,才能减少缺陷,保持正常生产工艺。
3、冷拔钢管退火:常见的退火工艺有:再结晶退火,去应力退火,球化退火,完全退火等。
退火的目的:主要是降低金属材料的硬度,提高塑性,以利切削加工或压力加工,减少残余应力,提高组织和成分的均匀化,或为后道热处理作好组织准备等。
拔断出现拔断的主要原因是:中间退火不均,变形量不足。
润滑的质量不好,锤头不合乎要求,在锤头前的加热时产生了过热或过烧。
冷拔轴承钢管生产质量缺陷分析与预防

第14卷第3期重庆科技学院学报(自然科学版)2012年6月收稿日期:2011-11-07基金项目:重庆科技学院横向科研项目(1911-003)作者简介:任蜀焱(1973-),男,四川南部人,硕士,讲师,研究方向为材料加工。
采用管坯+加热+二辊斜轧穿孔+控冷+球化+多道次冷拔生产GCr15轴承钢管,常常会出现内外裂纹、离层、内折、外折、壁厚不均、不圆度过大、尺寸偏差过大、球化组织不合格、矫凹等缺陷。
依据钢管质量检验标准做好缺陷的预防工作,是提高冷拔轴承管质量和经济效益的关键。
1冷拔轴承管生产过程缺陷分析1.1圆管坯加热缺陷分析圆管坯加热要防止加热不均、过热、过烧、黑头、白头等缺陷。
如果测温设备不准确,操作工控温不严,造成钢温过高引起过热或过烧,排料长短不齐引起白头,均会使管坯塑性降低,出现穿孔破裂。
煤气质量差、二次风调节不当,产生炉气负压,引起炉门吸入冷空气圆钢黑头或表面严重氧化。
翻钢不及时、出钢过早,受料槽待穿时间过长产生阴阳面。
炉子加热能力小于穿孔能力,保温时间不足,穿孔过程管坯中心温度远低于表面温度时(硬心钢)都会造成穿孔毛管偏心、表面麻毛、内翘皮、离层等缺陷。
1.2穿孔缺陷分析穿孔要防止毛管出现裂纹、内折、外折、离层和壁厚不均等缺陷。
管坯在穿孔过程中受交变切应力和拉应力作用,管坯在接触顶头前,如果中心部分的金属在应力的作用下有微小的疏松,可以减小穿孔时的能量消耗,使穿孔过程易于进行。
但是,如果顶头前伸量不足,顶头前压下量过大,管坯中心产生了严重开裂形成了孔洞,则内表面金属被氧化,在继续穿孔变形中不能被焊合而造成裂纹及内折缺陷[1]。
穿孔过程管坯离层形成因素:除管坯加热温度过高外,斜轧穿孔使内外表面层金属沿横向产生附加剪切变形。
在穿孔准备区,外层金属沿横向流动的速度大于内层,使金属纤维歪扭。
在穿孔区,毛管外表面和内表面层金属有较大的变形,故其切向流动速度大于过渡层,使金属纤维弯曲成C 形。
减壁量越大,则弯曲程度越大,金属切向流动速度不一致引起各层金属间相互的附加横向剪切变形。
20#钢冷拔管表面缺陷分析及生产工艺改进研究

发现 /f 程度 的裂纹 、
沿 2中蓝 线 把 l#试 样 表 而 缺 陷 处纵 向 丌 瞎制 后检 验 ,发现 缺 陷深 约 0.83 Illnl,裂纹 侧 尤 I{』j
脱 碳 现 象 ,裂纹 有 沿 晶 或 穿 品 歼 裂 的 特 ,组 织 为铁素 体 +珠 光体 ,见冈 4、 5.
1宏观检验
收 2支 20#铡 冷 拔 管 试样 宏 观 彤 貌 见 I 1,2支 铡僻 洲 J 寸均接 近 j l9 II11nX2.3 I11m规格 。 l#冷 拔 竹 缺 宏 观 彤 貌 2,缺 陷 有 多处 呈 串状 分 例 僻 In卜一侧 ,缺 彤貌 为“人”字 状 裂纹 ;2# 冷拔僻 Ifi 仃 ·处缺 陷 ,缺陷呈 J坑状 , 罔 3。
IlII t㈨ th 。I. rJ a(’(。Im lulation of’”0”,”I ” and ”Zn” elem ents is tbrm ed (1uring the processing an(1 lI1l Zn pliosphaling SOl[1liI… is
LISed in flit phosphaling treatlilell1.Tlle Itetk t was effectively elim inated and the pi’nduet quality WaS inlprove ̄l hy iinpi’(ivilig phosllhal—
僻 厂 4/-.i-产(I)30 nilnx2.5 IllIll 20#冷 拔 管 过程 ·I1.发 观 ,fr批 址 的 钢 篱 外 表 而 现 同 程 度 的 裂 纹 JJII I l 艺过 程 为 :(1)60 lllln网钢 加 热 到 1 000。C 进 行 穿孔 、冷 拔 、邀 火 、酸洗 、磷 化 处 理 等 ¨1 艺过 程 lIj-』 ̄ . IJ J 、.r符 合 求…,然 lnj 成 品检 验 ,{ 有 35支管
冷加工缺陷

冷轧时钢管的缺陷、产生原因及消除办法一、二辊式冷轧管机轧管缺陷二辊式冷轧管机轧管时最常出现的产品缺陷有:折叠,凹陷,过大的波纹,内表面上的凹陷和擦伤,直径和壁厚的超差以及壁厚不均,等。
1.1 折叠在机架的正行程中,金属进到了扎槽块之间的间隙中,在工作锥的侧表面上形成了耳子。
在机架的返行程时,这些耳子被轧槽块压到工作锥的表面中去。
所形成的缺陷就是折叠。
由于轧制时管料在一个轧制周期中要回转一次,所以折叠在管子表面呈螺旋分布。
轧槽块之间的间隙太大,间隙分布不均匀,孔型各部分的宽度不够,芯棒尺寸同孔型形状不相符合,送进量大小不均匀或者管料猛进以及管料停止回转等,这些原因都会促使在工作锥上形成侧面耳子和在管子表面上形成折叠。
如果轧槽块之间的间隙大大,应该重新调整间隙。
当孔型各个部分的宽度不够时,可以找出金属被孔型凸缘“啃掉”的地方,并用风动砂轮研磨孔型,加大孔型宽度较小部分的开口度。
芯棒尺寸同孔型形状不符会引起金属的集中压下而出现耳子。
为了消除这种现象,可换上芯棒圆锥母线斜度较大的芯棒。
在送进量大小不均匀或者在管料猛进的情况下,应该消除它们产生的原因。
如果管料停止了回转可调整一下前卡盘。
1.2 凹陷管子表面上的凹陷多发生在孔型的预精整段部分以及当机架返行程时管子不在芯棒上辊轧的情况下。
形成凹陷的原因是:轧槽块之间的间隙太大和孔型预精整部分侧壁的开口太陡,轧槽块在水平面内互相错开以及轧槽块表面上有缺陷等。
凹陷多半出现在轧制薄壁管时。
当轧槽块之间的间隙太大和孔型预精整部分侧壁开口太陡时,在机架的正行程中金属充满了孔型的侧壁开口部分并被孔型的凸缘切割,被切割部分的金属在返行程轧制时被压到管子的表面下而形成凹陷。
由于管子回转,管子表面上的凹陷一般呈螺旋分布。
当轧槽块两侧的间隙不等时,凹陷可能只出现在管子的一侧。
为了避免凹陷的产生必须减小出现凹陷处的轧槽块之间的间隙,同时研磨孔型预精整部分的侧壁开口,减小它的陡度。
(全)冷轧薄板质量缺陷图谱

粘结纹
表面质量缺陷
气泡
表面质量缺陷
1、定义与外观
气泡是指钢板表面无规律分布的、圆形的、大小不等的凸 包,其外缘比较圆滑,大多是鼓起的,也有不鼓起的,经酸洗 后表面发亮,其截面有分层并呈现凸起性空隙。
2、鉴别
很容易用肉眼判定。
表面质量缺陷
气泡
3、成因
(1)因铸坯存在较多的气泡等缺陷,虽经多道轧制没有 焊合,残留在钢带上。 (2)热轧时,铸坯在加热炉时间长,气泡暴露。
过酸洗
表面质量缺陷
氧化色
表面质量缺陷
1、定义与外观
钢带表面被氧化,其颜色由边部的深蓝色逐步过渡到浅 蓝色、淡黄色。
2、鉴别
很容易用肉眼判定
表面质量缺陷
氧化色
3、成因
(1)退火时,保护罩密封不严或漏气,发生化学反应;
(2)保护罩吊罩过早,高温出炉,钢卷边缘表面氧化;
(3)保护气体成份不纯;
(4)加热前予吹扫时间不足,炉内存在残氧,钢卷在氧化性气氛中退火。
4、消除及预防 (1)加强原料把关。
(2)减少轧制变形率。
孔洞
表面质量缺陷
粘结纹
表面质量缺陷
1、定义与外观
退火钢卷层间互相粘和在一起称粘结。粘合的形式有点状、 线状和块状粘结。粘结严重时,手摸有凸起感觉,多分布于带 钢的边部或中间。平整后为横向折印展平状或弓形。
2、鉴别
很容易用肉眼判定。
表面质量缺陷
(1)吹氩时间短,夹杂物未充分上浮;
(2)连铸时,保护渣带入钢中;
(3)中包液面低,钢渣卷入钢水中。 4、消除及预防
(1)严格执行操作规程,保证吹氩时间; (2)控制好连铸拉速; (3)保证中包液面。
表面夹杂
酸洗资料及冷拔常用缺陷

酸洗资料及冷拔常用缺陷冷拔钢管中常见的缺陷及其处理方法1、折迭:拔制后,钢管内外表面呈现直线或螺旋方向的折迭,局部或通长的出现在钢管上。
产生的原因:管料表面有折迭或平杂物,有严重擦伤和裂纹,管料磨修处有棱角或深宽比(H/b)不够。
预防和消除方法:严格按照规程要求对管料进行修磨。
不合格管料不投产,防患于未然。
严格把好穿孔热序的质量关。
2、尺寸超差(包括壁厚超差,壁厚不均,直径超差,椭圆)直径超过了标准的偏差范围,在同一截面上管壁一边薄,厚,直径不等,长短轴之差超出标准规定。
产生的原因:1、拔制模具选择不光,或蕊棒(内模)调整不当。
2、拔模内模设计制造不合理或磨损严重,或硬度不够造成变形磨损。
3、热处理时间长,温度高。
或热处理性能不均匀。
4、空拔时增减壁的规律控制不当,拔制表编制不合理。
5、钢管矫直时被压扁,工卡量具未校零,误差大。
预防和消除方法:1、正确设计制造和选配拔管模具。
2、正确执行热处理制度,均匀加热。
3、正确调整矫直机,经常校对拔管机各部件位置和量具。
4、正确合理编制拔制表,掌握不同钢种、不同规格钢管的增减壁规律。
5、椭圆度不出格,判为合格品,椭圆度出格可重新矫直,局部椭圆度出格可切除。
3、划道:钢管表面上呈现纵向直线形的划痕称为划道。
划道长短不一,宽穿窄不等,多为沟状,可见沟底。
产生的原因:1、拔模内表不光滑,有裂纹或结金属。
2、锤头过渡部分有棱角,磨损工具。
3欠酸洗或毛管上残存氧化铁皮。
4、在涂润滑油时,磷化、皂化工序操作不当。
5、内外模已损伤或磨损严重。
6、中间退火不均,变形量不足。
预防和消除方法:1、提高拔管模具的表面质量。
2、氧化皮要酸洗,冲洗干净,涂层要均匀牢固。
3、锤头过渡部分要圆滑无棱角。
4、勤检查模具和钢管表面,发现问题及时处理。
4、抖纹:钢管表面沿长度方向呈高低不平的环形波浪或波浪逐个相同排列,局部的或通长的出现在钢管内外表面上。
产生的原因:1、热处理后的性能不均,润滑不良,皂化不均。
冷拔管常见缺陷产生原因及预防和消除方法
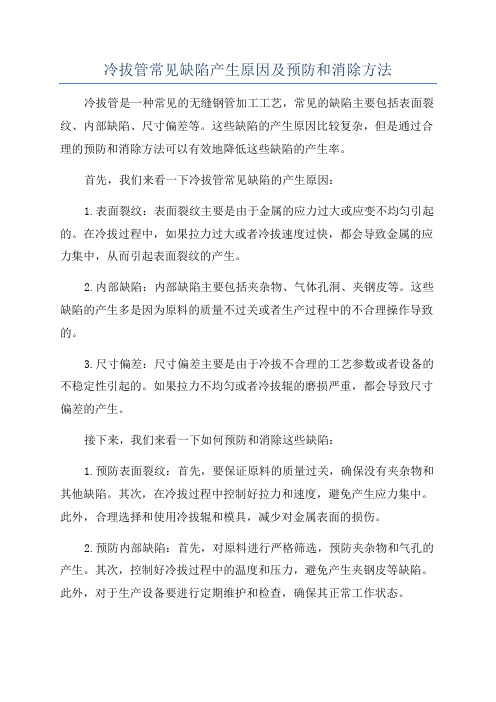
冷拔管常见缺陷产生原因及预防和消除方法冷拔管是一种常见的无缝钢管加工工艺,常见的缺陷主要包括表面裂纹、内部缺陷、尺寸偏差等。
这些缺陷的产生原因比较复杂,但是通过合理的预防和消除方法可以有效地降低这些缺陷的产生率。
首先,我们来看一下冷拔管常见缺陷的产生原因:1.表面裂纹:表面裂纹主要是由于金属的应力过大或应变不均匀引起的。
在冷拔过程中,如果拉力过大或者冷拔速度过快,都会导致金属的应力集中,从而引起表面裂纹的产生。
2.内部缺陷:内部缺陷主要包括夹杂物、气体孔洞、夹钢皮等。
这些缺陷的产生多是因为原料的质量不过关或者生产过程中的不合理操作导致的。
3.尺寸偏差:尺寸偏差主要是由于冷拔不合理的工艺参数或者设备的不稳定性引起的。
如果拉力不均匀或者冷拔辊的磨损严重,都会导致尺寸偏差的产生。
接下来,我们来看一下如何预防和消除这些缺陷:1.预防表面裂纹:首先,要保证原料的质量过关,确保没有夹杂物和其他缺陷。
其次,在冷拔过程中控制好拉力和速度,避免产生应力集中。
此外,合理选择和使用冷拔辊和模具,减少对金属表面的损伤。
2.预防内部缺陷:首先,对原料进行严格筛选,预防夹杂物和气孔的产生。
其次,控制好冷拔过程中的温度和压力,避免产生夹钢皮等缺陷。
此外,对于生产设备要进行定期维护和检查,确保其正常工作状态。
3.预防尺寸偏差:首先,要合理选择冷拔工艺参数,尽量保证拉力的均匀分布。
其次,定期检查和更换冷拔辊和模具,减少磨损对尺寸的影响。
此外,对于冷拔设备要进行定期维护和校准,确保其稳定性。
除了以上措施外,还可以通过加热退火、自动控制系统、成品质量检测等方法来预防和消除冷拔管的常见缺陷。
加热退火可以降低冷拔过程中的应力,提高内部结构的均匀性;自动控制系统可以实时监测冷拔过程中的各项参数,并进行调整;成品质量检测可以及时发现和修复缺陷,确保产品的合格率。
综上所述,冷拔管常见缺陷的产生原因比较复杂,但是通过合理的预防和消除方法可以有效地降低这些缺陷的产生率。
冷轧钢管产品缺陷一览表
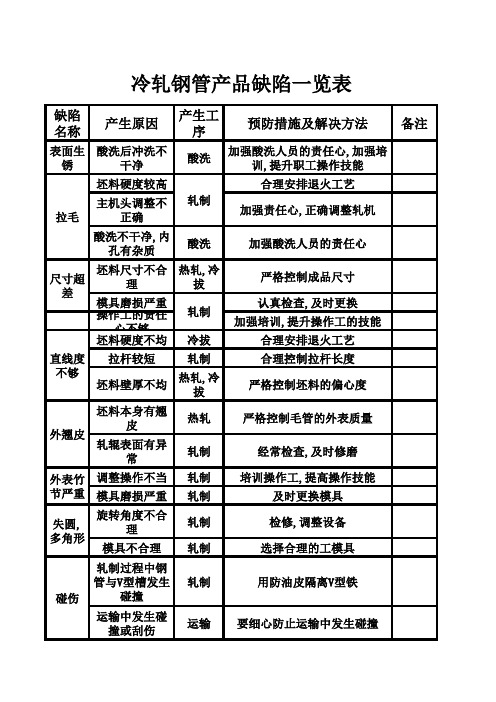
缺陷 名称
产生原因
产生工 序
预防措施及解决方法
表面生 酸洗后冲洗不
锈
干净
酸洗
加强酸洗人员的责任心,加强培 训,提升职工操作技能
拉毛
坯料硬度较高
主机头调整不 正确
轧制
合理安排退火工艺 加强责任心,正确调整轧机
酸洗不干净,内 孔有杂质
酸洗
加强酸洗人员的责任心
尺寸超 差
坯料尺寸不合 理
减壁量太大 轧制
螺旋(S 弯)
硬度不均
穿孔钢温不均 造成毛管有螺内外表面 不光
工模具磨损严 重
热轧,冷 拔
轧制
合理安排退火工艺 合理安排工艺,坯料保证尺寸
退火时不能有堆积现象
保证钢温,及时拔料
保证坯料质量 经常检查,及时更换
外表竹 调整操作不当 轧制 节严重 模具磨损严重 轧制
培训操作工,提高操作技能 及时更换模具
旋转角度不合
失圆,
理
多角形
模具不合理
轧制 轧制
检修,调整设备 选择合理的工模具
轧制过程中钢
管与V型槽发生
碰伤
碰撞
轧制
用防油皮隔离V型铁
运输中发生碰 撞或刮伤
运输
要细心防止运输中发生碰撞
备注
坯料硬度太高 冷拔 开裂
模具磨损严重 操作工的责任
心不够 坯料硬度不均
热轧,冷 拔
轧制
冷拔
严格控制成品尺寸
认真检查,及时更换 加强培训,提升操作工的技能
合理安排退火工艺
直线度 拉杆较短
轧制
不够
坯料壁厚不均
热轧,冷 拔
合理控制拉杆长度 严格控制坯料的偏心度
冷拔20钢管内表面缺陷分析

冷拔20钢管内表面缺陷分析武晶晶,李 荣,苏丽凤,张雪华(西部金属材料股份有限公司理化检验中心,陕西 西安 710016)摘 要:φ108xφ90冷拔精密无缝钢管在精加工过程中发现钢管内壁存在缺陷,宏观检查发现管内壁存在黑色凹坑,经过电镜分析和金相分析发现黑色凹坑为的冷拔过程中形成的。
关键词:20钢管;氧化膜;冷拔;中图分类号:TG356.11 文献标识码:A 文章编号:1002-5065(2016)19-0033-2Analysis of the surface defects in 20 steel pipe cold drawingWU Jing-jing,LI Rong,SU Li-feng,ZHANG Xue-hua(Western metal materials co., LTD., the physical and chemical inspection center,Xi'an 710016,China)Abstract: Phi phi 108 x 90 cold drawn precision seamless steel tube defects found in the finishing process of steel tube wall, macroscopic examination revealed tube wall is black pits, after electron microscopy (sem) analysis and metallographic analysis found black pits formed in the process of cold drawing.Keywords: 20 steel pipe; Oxide film; Cold drawn;1 情况简介一批φ108xφ90冷拔精密无缝钢管在精加工过程中发现钢管内壁存在缺陷,如图1所示,随后将存在缺陷的钢管截取成约40~70mm长度不等的样品进行检验,取其中的3个样品,样品的编号分别是1号、2号、3号,20 无缝钢管是适用于中压和低压锅炉的碳素结构钢无缝钢管,其使用GB 3087 - 2008《低中压锅炉用无缝钢管》中规定的材料牌号,是使用普通且用量很大的一种钢管材料,适用于制造各种低压和中压锅炉用的优质碳素结构钢无缝钢管。
不锈钢无缝管冷拔管主要缺陷原因分析

不锈钢无缝管冷拔管主要缺陷原因分析不锈钢无缝管冷拔管是制造工业中常用的一种管材,具有高强度、耐腐蚀、抗高温等优点。
然而,在生产过程中,不锈钢无缝管冷拔管也会出现一些缺陷,影响其质量和使用性能。
下面将对不锈钢无缝管冷拔管主要缺陷的原因进行分析。
1.冷拔裂纹冷拔裂纹是不锈钢无缝管冷拔管中常见的缺陷。
主要原因包括:(1)超过材料的塑性变形极限,导致材料发生微裂纹;(2)冷拔过程中,不锈钢管内外表面摩擦产生热量,使不锈钢管的表面温度升高,但内部温度较低,造成不均匀变形,引起裂纹;(3)冷拔过程中,不锈钢管的表面受到过大的切削力和压力,导致表面裂纹形成。
2.冷拔皮面凹陷冷拔皮面凹陷是因为不锈钢无缝管冷拔管的表面出现深度不均匀的凹陷。
主要原因包括:(1)冷拔过程中,不锈钢管内外表面存在不一致的形变应力,导致表面凹陷;(2)冷拔过程中,冷却不均匀,使得不锈钢管的表面有热量堆积,导致凹陷。
3.管道内部气泡管道内部气泡是不锈钢无缝管冷拔管中的一种重要缺陷。
主要原因包括:(1)冷拔过程中,由于变形应力大,会产生氧化皮,氧化皮与金属表面不牢固结合,形成空鼓;(2)冷拔过程中,冷却不均匀,导致管道内部产生凝结水,形成气泡。
4.脱漆脱漆是指不锈钢无缝管冷拔管表面的涂层脱落。
主要原因包括:(1)材料的涂层质量不达标,没有很好地附着在管道表面,容易脱落;(2)不锈钢管在运输和使用过程中受到外部力的作用,使得涂层剥落。
5.尺寸偏差尺寸偏差是指不锈钢无缝管冷拔管在制造过程中的尺寸不符合要求的缺陷。
主要原因包括:(1)冷拔过程中的冷变形过程无法完全控制,导致管道尺寸偏差;(2)生产设备的精度不高,也会导致不锈钢管尺寸的偏差;(3)材料的收缩因素未考虑充分,导致材料冷拔后的尺寸偏差。
综上所述,不锈钢无缝管冷拔管的主要缺陷原因包括冷拔裂纹、冷拔皮面凹陷、管道内部气泡、脱漆和尺寸偏差等。
在生产过程中,需要加强对每个环节的控制和管理,提高生产设备的精度,采取合理的工艺措施,以减少和防止缺陷的发生,提高不锈钢无缝管冷拔管的质量和使用性能。
不锈钢无缝管冷拔管主要缺陷原因分析
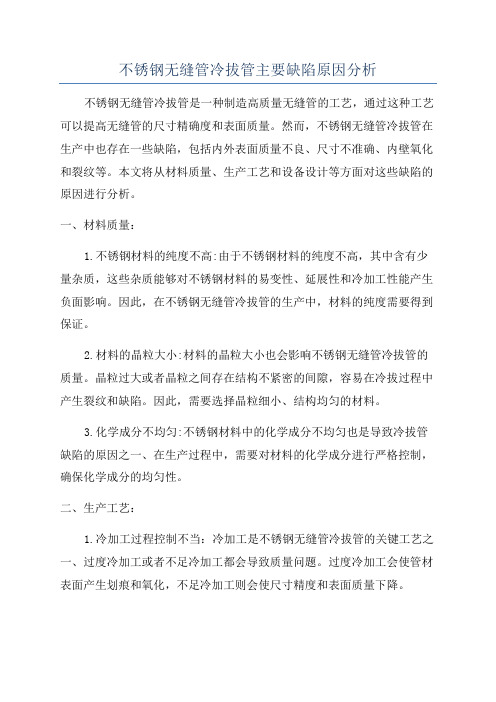
不锈钢无缝管冷拔管主要缺陷原因分析不锈钢无缝管冷拔管是一种制造高质量无缝管的工艺,通过这种工艺可以提高无缝管的尺寸精确度和表面质量。
然而,不锈钢无缝管冷拔管在生产中也存在一些缺陷,包括内外表面质量不良、尺寸不准确、内壁氧化和裂纹等。
本文将从材料质量、生产工艺和设备设计等方面对这些缺陷的原因进行分析。
一、材料质量:1.不锈钢材料的纯度不高:由于不锈钢材料的纯度不高,其中含有少量杂质,这些杂质能够对不锈钢材料的易变性、延展性和冷加工性能产生负面影响。
因此,在不锈钢无缝管冷拔管的生产中,材料的纯度需要得到保证。
2.材料的晶粒大小:材料的晶粒大小也会影响不锈钢无缝管冷拔管的质量。
晶粒过大或者晶粒之间存在结构不紧密的间隙,容易在冷拔过程中产生裂纹和缺陷。
因此,需要选择晶粒细小、结构均匀的材料。
3.化学成分不均匀:不锈钢材料中的化学成分不均匀也是导致冷拔管缺陷的原因之一、在生产过程中,需要对材料的化学成分进行严格控制,确保化学成分的均匀性。
二、生产工艺:1.冷加工过程控制不当:冷加工是不锈钢无缝管冷拔管的关键工艺之一、过度冷加工或者不足冷加工都会导致质量问题。
过度冷加工会使管材表面产生划痕和氧化,不足冷加工则会使尺寸精度和表面质量下降。
2.拔管速度不合适:拔管速度过快会导致管材表面粗糙,容易产生氧化和裂纹;拔管速度过慢会导致管材断裂。
因此,需要选择合适的拔管速度,以保证管材质量。
3.润滑剂选择不当:润滑剂对冷拔管的质量有很大影响。
润滑剂的选择不当会导致管材的内外表面质量下降,增加管材内壁氧化的风险。
三、设备设计:1.设备刚度不足:设备刚度不足会导致冷拔管过程中的振动和形变增大,容易产生缺陷。
因此,需要设计足够刚度的设备来保证冷拔管的质量。
2.设备寿命较短:设备的使用寿命较短也会导致冷拔管的质量问题。
设备经常需要修理和更换,容易产生停工和生产延误等问题。
综上所述,不锈钢无缝管冷拔管的主要缺陷主要是由材料质量、生产工艺和设备设计等因素引起的。
冷拔钢管折弯开裂原因

冷拔钢管折弯开裂原因
冷拔钢管在使用过程中出现折弯开裂的原因可能有多种,下面
我将从材料质量、生产工艺、使用环境等多个角度来分析可能的原因。
首先,从材料质量方面来看,冷拔钢管的原材料质量可能是导
致折弯开裂的一个重要因素。
如果原材料的质量不达标,可能会导
致冷拔钢管在加工过程中出现内部缺陷,如气孔、夹杂物等,从而
影响钢管的强度和韧性,使其容易发生折弯开裂的现象。
其次,生产工艺也是一个重要因素。
冷拔钢管的生产工艺包括
多道工序,如拉拔、冷拔、退火等。
如果在生产过程中工艺参数控
制不当,比如拉拔过程中的拉拔力、温度控制不准确,或者退火工
艺不合理等,都可能导致钢管内部组织结构不均匀,产生应力集中,从而引起折弯开裂。
另外,使用环境也是导致冷拔钢管折弯开裂的原因之一。
如果
在使用过程中,钢管承受了超出其承载能力的载荷,或者受到了较
大的冲击负荷,都可能导致钢管发生变形和开裂。
除此之外,还有一些其他因素可能会导致冷拔钢管折弯开裂,比如操作不当、贮存条件不佳等。
因此,在生产、使用过程中都需要严格控制各个环节,确保冷拔钢管的质量和稳定性。
综上所述,冷拔钢管折弯开裂的原因可能涉及材料质量、生产工艺、使用环境等多个方面,需要在生产、使用过程中加强质量管理和技术监控,以确保冷拔钢管的质量和安全可靠性。
冷拔工艺

四、冷拔钢管缺陷及分析
缺陷名称:折叠、裂缝(裂纹、发纹) 缺陷名称:折叠、裂缝(裂纹、发纹)、凹坑、尺寸超差、壁厚不均、 椭圆、划道(擦伤) 椭圆、划道(擦伤)、抖纹、纵向开裂、纵向凹折、翘皮、 夹杂、麻面(针孔) 夹杂、麻面(针孔)、矫痕、内外折等。
序 缺陷 号 名称
特征 产生原因 预防和消除方法
1 横裂 钢管表面 有连续或 断续的横 向破裂
酸洗时间过长引起氢脆 热处理不当, 热处理不当,加工应力未充分消除 拔制变形量过大 拔制速度过快, 拔制速度过快,产生热应力 空拔厚壁管内外变形不一致, 空拔厚壁管内外变形不一致,产生 附加应力
正确执行工艺制度, 正确执行工艺制度,按 操作规程作业 合理安排变形量 对厚壁管特别注意内外 性能均匀、要控制壁厚 不均
缺陷缺陷名称名称特征特征产生原因产生原因预防和消除方法预防和消除方法22钢管表面钢管表面呈直线形呈直线形划痕划痕拔模表面不光滑有裂纹或粘钢拔模表面不光滑有裂纹或粘钢锤头过渡区有棱角磨损工具锤头过渡区有棱角磨损工具欠酸洗或钢管表面残留有氧化皮欠酸洗或钢管表面残留有氧化皮润滑质量不高拔速过快润滑质量不高拔速过快热轧管料有青线拔后未能消除热轧管料有青线拔后未能消除模具硬度不够或已磨损模具硬度不够或已磨损变形量过大变形量过大热处理欠温或不均匀热处理欠温或不均匀提高模具的质量提高模具的质量氧化铁皮要洗干净氧化铁皮要洗干净涂层均匀牢固涂层均匀牢固锤头过渡区的质量锤头过渡区的质量勤检查模具和钢管表勤检查模具和钢管表面发现问题及时处面发现问题及时处理理33沿长度方沿长度方向出现高向出现高低不平的低不平的环形波浪环形波浪热处理后性能不均匀热处理后性能不均匀酸洗后冲洗不干净润滑不良酸洗后冲洗不干净润滑不良拔制时抖动拔制时抖动芯杆过细拔制时弹性变形引起芯杆过细拔制时弹性变形引起抖动抖动启动速度过快或链条振动启动速度过快或链条振动外模形状不合理入口锥角太大外模形状不合理入口锥角太大按规程进行热处理按规程进行热处理酸洗干净磷化润滑酸洗干净磷化润滑良好良好适当的拔制速度适当的拔制速度合理的道次变形量合理的道次变形量缺陷缺陷名称名称特征特征产生原因产生原因预防和消除方法预防和消除方法44在钢管纵在钢管纵向上管向上管壁厚向内壁厚向内呈条状凹呈条状凹空拔薄壁管时减径量过大空拔薄壁管时减径量过大钢管锤头部过渡太急钢管锤头部过渡太急合理分配减径量合理分配减径量锤头部应平缓无皱折锤头部应平缓无皱折管料修磨位置长宽比要管料修磨位置长宽比要合适合适55开裂开裂呈穿透管呈穿透管壁的纵向壁的纵向裂开裂开全长全长和局部和局部空拔管变形量过大空拔管变形量过大热处理不当加工硬化未全部热处理不当加工硬化未全部消除消除拔制后未及时热处理拔制后未及时热处理连拔道次多加工硬化严重连拔道次多加工硬化严重钢管本身塑性低钢管本身塑性低合理编排拔制表合理编排拔制表合金管和连拔管拔后及合金管和连拔管拔后及时热处理时热处理按工艺要求进行热处理按工艺要求进行热处理缺陷缺陷名称名称特征特征产生原因产生原因预防和消除方法预防和消除方法66表面成片表面成片的细点状的细点状凹坑凹坑过酸洗过酸洗氧化皮厚矫直量压入基体氧化皮厚矫直量压入基体钢管表面有油污加热时烧钢管表面有油污加热时烧酸洗后停放时间过
冷轧产品常见缺陷图谱与判断

冷轧产品常见缺陷图谱与判断目录结疤〔4〕表面夹杂〔5〕分层〔6〕氧化铁皮压入〔7〕辊印〔8〕压痕〔压印、压坑〕〔9〕扁卷 (10〕瓢曲 (11〕镰刀弯 (12〕折迭〔13〕边裂〔14〕气泡〔15〕折皱〔16〕刮伤〔17〕擦伤〔划伤、划痕〕〔18〕撞伤〔19〕切斜〔20〕欠酸洗〔21〕过酸洗〔22〕停车斑〔23〕浪形〔24〕氧化色〔25〕振动纹〔26〕平坦斑〔27〕粘结〔28〕塔形〔29〕溢出边〔30〕卷取擦伤〔31〕锈蚀〔32〕松卷〔33〕凸包〔起筋、隆起、鼓包〕〔34〕厚度不合〔35〕长度不合〔36〕平坦纹〔37〕孔洞〔38〕黄斑〔39〕黑斑〔40〕1.缺陷名称:结疤定义与外观:附着在钢带表面,形状不规那么翘起的金属薄片称结疤。
出现叶状、羽状、条状、鱼鳞状、舌端状等。
结疤分为两种,一种是与钢的本体相连结,并折合到板面上不易脱落叫闭口结疤;另一种是与钢的本体没有连结,但粘合在板面上,易于脱落,脱落后形成较光滑的凹坑称为开口结疤。
成因:●冷轧基板表面原有的结疤、翘皮等缺陷未挑出,经冷轧后残留在钢带表面上;●冷轧时钢板表面粘附异物,经轧制压入钢带表面。
危害:导致后续加工使用过程中显现金属剥离或产生孔洞。
预防及排除方法:加强冷轧基板的检查,检查判定:●用肉眼检查;●不承诺存在结疤缺陷,一样判利用品或以下等级,对局部结疤缺陷,承诺切除带有结疤部分带钢的方法清除。
如结疤已脱落,那么比照压痕缺陷处理,假设深度没有超出相关标准规定,能够参照相应标准进行判定。
2.缺陷名称:表面夹杂定义与外观:冷轧基板皮下或表面非金属夹杂、夹渣在冷轧加工过程中破裂而暴露在钢带表面,一样呈点状、块状、线状或长条状无规律的分布在薄板的表面。
其颜色一样呈棕红色、黄褐色、灰白色或灰黑色。
成因:冷轧基板皮下夹杂轧后暴露或基板的表面原有夹杂轧后残留在带钢表面〔炼钢浇铸缘故〕。
危害:可能导致后续加工过程中产生孔洞、开裂、分层。
预防及排除方法:●严格遵守浇铸制度●加强冷轧基板表面质量检查。
冷加工缺陷

冷轧时钢管的缺陷、产生原因及消除办法一、二辊式冷轧管机轧管缺陷二辊式冷轧管机轧管时最常出现的产品缺陷有:折叠,凹陷,过大的波纹,内表面上的凹陷和擦伤,直径和壁厚的超差以及壁厚不均,等。
1.1 折叠在机架的正行程中,金属进到了扎槽块之间的间隙中,在工作锥的侧表面上形成了耳子。
在机架的返行程时,这些耳子被轧槽块压到工作锥的表面中去。
所形成的缺陷就是折叠。
由于轧制时管料在一个轧制周期中要回转一次,所以折叠在管子表面呈螺旋分布。
轧槽块之间的间隙太大,间隙分布不均匀,孔型各部分的宽度不够,芯棒尺寸同孔型形状不相符合,送进量大小不均匀或者管料猛进以及管料停止回转等,这些原因都会促使在工作锥上形成侧面耳子和在管子表面上形成折叠。
如果轧槽块之间的间隙大大,应该重新调整间隙。
当孔型各个部分的宽度不够时,可以找出金属被孔型凸缘“啃掉”的地方,并用风动砂轮研磨孔型,加大孔型宽度较小部分的开口度。
芯棒尺寸同孔型形状不符会引起金属的集中压下而出现耳子。
为了消除这种现象,可换上芯棒圆锥母线斜度较大的芯棒。
在送进量大小不均匀或者在管料猛进的情况下,应该消除它们产生的原因。
如果管料停止了回转可调整一下前卡盘。
1.2 凹陷管子表面上的凹陷多发生在孔型的预精整段部分以及当机架返行程时管子不在芯棒上辊轧的情况下。
形成凹陷的原因是:轧槽块之间的间隙太大和孔型预精整部分侧壁的开口太陡,轧槽块在水平面内互相错开以及轧槽块表面上有缺陷等。
凹陷多半出现在轧制薄壁管时。
当轧槽块之间的间隙太大和孔型预精整部分侧壁开口太陡时,在机架的正行程中金属充满了孔型的侧壁开口部分并被孔型的凸缘切割,被切割部分的金属在返行程轧制时被压到管子的表面下而形成凹陷。
由于管子回转,管子表面上的凹陷一般呈螺旋分布。
当轧槽块两侧的间隙不等时,凹陷可能只出现在管子的一侧。
为了避免凹陷的产生必须减小出现凹陷处的轧槽块之间的间隙,同时研磨孔型预精整部分的侧壁开口,减小它的陡度。
冷拔钢管表面质量缺陷
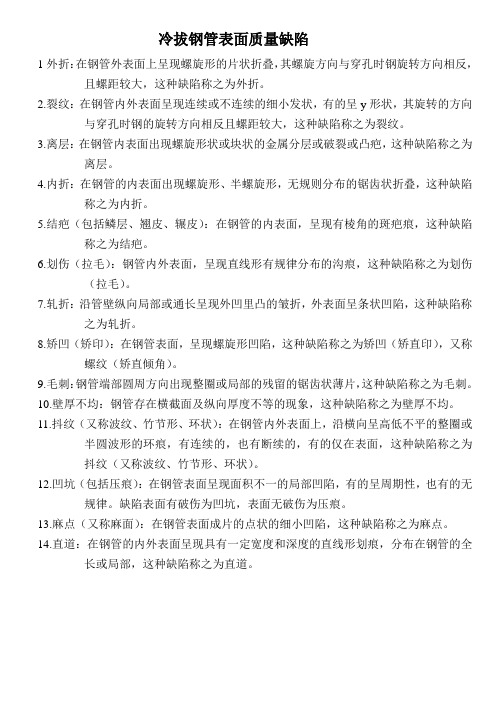
冷拔钢管表面质量缺陷1外折:在钢管外表面上呈现螺旋形的片状折叠,其螺旋方向与穿孔时钢旋转方向相反,且螺距较大,这种缺陷称之为外折。
2.裂纹:在钢管内外表面呈现连续或不连续的细小发状,有的呈y形状,其旋转的方向与穿孔时钢的旋转方向相反且螺距较大,这种缺陷称之为裂纹。
3.离层:在钢管内表面出现螺旋形状或块状的金属分层或破裂或凸疤,这种缺陷称之为离层。
4.内折:在钢管的内表面出现螺旋形、半螺旋形,无规则分布的锯齿状折叠,这种缺陷称之为内折。
5.结疤(包括鳞层、翘皮、辗皮):在钢管的内表面,呈现有棱角的斑疤痕,这种缺陷称之为结疤。
6.划伤(拉毛):钢管内外表面,呈现直线形有规律分布的沟痕,这种缺陷称之为划伤(拉毛)。
7.轧折:沿管壁纵向局部或通长呈现外凹里凸的皱折,外表面呈条状凹陷,这种缺陷称之为轧折。
8.矫凹(矫印):在钢管表面,呈现螺旋形凹陷,这种缺陷称之为矫凹(矫直印),又称螺纹(矫直倾角)。
9.毛刺:钢管端部圆周方向出现整圈或局部的残留的锯齿状薄片,这种缺陷称之为毛刺。
10.壁厚不均:钢管存在横截面及纵向厚度不等的现象,这种缺陷称之为壁厚不均。
11.抖纹(又称波纹、竹节形、环状):在钢管内外表面上,沿横向呈高低不平的整圈或半圆波形的环痕,有连续的,也有断续的,有的仅在表面,这种缺陷称之为抖纹(又称波纹、竹节形、环状)。
12.凹坑(包括压痕):在钢管表面呈现面积不一的局部凹陷,有的呈周期性,也有的无规律。
缺陷表面有破伤为凹坑,表面无破伤为压痕。
13.麻点(又称麻面):在钢管表面成片的点状的细小凹陷,这种缺陷称之为麻点。
14.直道:在钢管的内外表面呈现具有一定宽度和深度的直线形划痕,分布在钢管的全长或局部,这种缺陷称之为直道。
冷拔无缝钢管缺陷分类与产生原因基本知识

冷拔无缝钢管缺陷分类与产生原因基本知识一. 擦伤:特征:钢管表面呈现长短不一,方向不定的无规则的擦痕,一般呈直线形,均能看到其底。
产生原因:1)退火时操作不当;2)在吊运中划伤;3)在矫直过程中,钢管在套筒处擦伤。
二.划道(又称拉丝、拉毛、直道包括青线)特征:钢管内外表面上呈现纵向直线形的长短不一划道,外为沟状,可见底,表面有损伤内划道,表面无损伤直线。
产生原因:1)毛管上划道;2)毛管上残存有氧化铁皮;3)润滑剂涂层不良,引起摩擦力增加,致使模具发热焊接金属;4)内外模具硬度不够或不均,光洁度差;5)锤头不良,过渡部分产生尖锐的棱角,模具磨损,造成划道。
三.抖纹:特征:在钢管内外表面上,沿长度方向呈高低不平的整圈或半圈波形的环痕,逐个相间排列,有连续的,也有断续的。
一般由拉拔动时抖动(称“打机枪”)所造成。
产生原因:1)酸洗过程未冲净,润滑不良,涂层不均;2)退火性能不均匀,抗拉强度过大,含碳量较高的热轧钢管冷却速度过大,造成钢质较硬,加工硬化;3)管子过大,头部无空隙,皂化不良;4)芯棒细,拔制时芯棒产生弹性变形,引起抖动; 5)拉拔时启动速度过快,或开拉时链条振动;6)配模不合理,入口锥角太大,管与模孔接触面积小,或模具定径位置不当,拔制时变形不稳,定面抖动。
四.凹坑(包括压痕):特征:钢管表面呈面积不一的局部凹陷,有的呈周期性,也有的无规律。
缺陷表面有破伤为凹坑,表面无破伤的为压痕。
产生原因:1)由于氧化铁皮或其他质硬的污物粘附在钢管表面,在拔制或矫直中压入钢管表面后剥落而留下压痕;2)矫直辊粘附了异物,在矫直过程中钢管表面压成凹坑;3)原先存在于钢管表面的翘皮剥落。
五.麻点:特征:钢管表面成片的点状细小凹坑。
产生原因:1)酸洗时产生点状腐蚀;2)退火后氧化铁皮过厚矫直后压入了钢管表面;3)钢管保存不好产生锈蚀;4)氧化皮未清洗干净,拉拔压入管面,产生麻点;5)管面有油污,退火时局部烧成麻面。
冷弯型钢产品缺陷及存在原因

冷弯型钢的产品缺陷及产生原因:
一、冷弯型钢成品焊缝开裂或破裂
产生原因:
1、生产过程中原料厚度宽度不稳定,产生漏焊或假焊。
2、焊接时挤压力度不够,焊缝融合不良。
二、产品弯曲度不符合标准
产生原因:
1、钢管壁厚不均(原料厚度不均匀或由生产所产生);
2、轧辊直径的不同导致钢管变形不均,产生弯曲。
三、产品尺寸波动较大
产生原因:
1、在调节轧辊时操作不当;
2、扎实速度过快,导致尺寸波动较大。
四、产品截面毛刺现象严重,产生老鼠尾巴,
产生原因:
1、剪切刀刃变钝,使间隙过大容易残留;锯片迟钝,或安装不当也会导致毛刺的产生;
2、焊管时焊缝处有挤出的多余金属。
焊接制度不规范会让剪切时更容易留下毛刺。
五、焊缝表面不平整,凹凸明显
产生原因:
1、焊缝外凸,焊缝刨削深度偏深,导致平面度降低。
2、焊缝内凹,焊缝刨削深度较浅。
六、方管或矩形管R角不均匀
产生原因:
生产操作不当导致R角不均匀。
R1=5
R2=7 R3=14.5
R4=9.5
七、管身存在接焊现象
八、端口锯切不整齐,倾斜或凹凸不平。
产生原因:
在生产过程中,原料是以卷状进行开卷轧制,每卷原料无接口,为了能够连续生产,需将两卷原料首末相焊接。
产生原因:
在剪切时产生剪切变形使得端口不齐。
- 1、下载文档前请自行甄别文档内容的完整性,平台不提供额外的编辑、内容补充、找答案等附加服务。
- 2、"仅部分预览"的文档,不可在线预览部分如存在完整性等问题,可反馈申请退款(可完整预览的文档不适用该条件!)。
- 3、如文档侵犯您的权益,请联系客服反馈,我们会尽快为您处理(人工客服工作时间:9:00-18:30)。
冷拔钢管产品缺缺陷名称
产生原因产生工序酸洗不清、润滑不好酸洗内模磨损、粘钢拉拔
打头肩部有棱角打头
矫直辊角度不正确
压下量过大
矫直辊磨损严重
坯料本身壁厚不均热轧穿孔
模具失圆拔制线和钢管轴线不
一致
生产工艺不当拉拔偷减道次
退火不当、不及时退火机械性能不达标热处理不当,退火温度过高或过低,保温时间不定
退火过酸酸洗
氧化皮在矫直后压入钢管表面
矫直,退火打头、退火温度过高打头,退火翘皮
热轧毛管本身有翘皮热轧抖纹钢管润滑不够酸洗
直道矫痕壁厚不均开裂麻点矫直拉拔拉拔
配模错误模具磨损严重老头管
管头尾切不净切管切管工责任心不够切管拉车衬内模过后拉拔
成品长度达
不到要求拉拔尺寸超差
产品缺陷一览表
预防措施及解决方法备注加强酸洗管理,保证酸洗质量
经常检查模具,及时更换
打头时要保证肩部圆滑
认真调整矫直机,经常检查、修磨辊面
严格按工艺要求控制壁厚
经常检查模具,及时更换
调整拔管机
合理安排工艺,严格按工艺生产
严格执行热处理工艺制度
严格执行热处理工艺制度
控制酸洗温度和时间
减少氧化铁皮的厚度
控制打头退火温度,不得过烧
投料时加强检查,及时修磨
掌握好酸洗磷化皂化时间和成分调整
加强责任心,认真检查模具,及时更换
加强切管工的责任心
加强切管工的责任心,提高自身的水平
保证衬芯到位。