FMEA失效模式与效果分析(ppt74页)(英文版)
FMEA失效模式和效果分析培训教材(英文版)
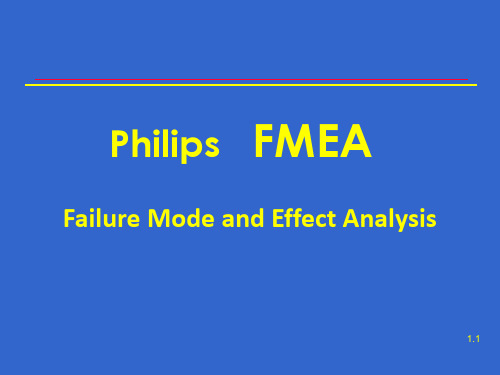
and unspoken.
1.20
Describe Function
Verb
Indicates action, occurrence, being
Generate Control Display
1.11
Generating FMEA’s
Who initiates?
When to discard?
How documented?
When completed?
Who prepares?
Failure MFoMdeEAasnd
Effect Analysis
Who updates?
Who is FMEAcustomer?
FMEA on L0 Schematics
(ftbo L0)
FMEA on L0 Board (ftbo L1)
FMEA on L1 Board (ftbo L2)
1.9
Benefits – Product-FMEA’s
Product Proces
❖ Assess failure mode effects on all customers.
• development
• production
• quality
• purchase
• testdept. 1.16
• ...
Product-FMEA – Scope
Once coreteam is established ...
❖ Create Blockdiagram ❖ Identify the boundery for Analysis ❖ Confirm composition of support
FMEA失效模式和效果分析培训教材
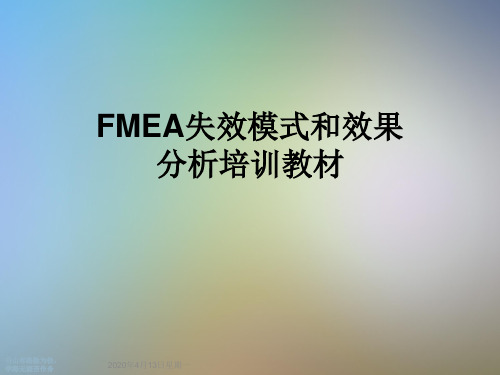
product/process and the effects of that failure 识别和评估一个产品或过程的潜在失效模式及其影响; 2. List down the actions which could eliminate or reduce the chance of the potential failure occurring 确定能排除或减少潜在失效发生的机率的措施; 3. Document all the elements for review and action 文件化整个过程。
•Taken from “The Certified Quality Engineer Handbook” ASQ
书山有路勤为径, 学海无涯苦作舟
Definition of FMEA FMEA定义 (II)
FMEA : Failure Mode and Effects Analysis FMEA:失效模式和效果分析
书山有路勤为径, 学海无涯苦作舟
Definition of FMEA FMEA定义
•An FMEA can be described as a systematic group of activities intended to : •FMEA 是一系列系统化的活动,其目的是 : 1. Identify and evaluate the potential failure modes of a
FMEA的失效模式、起源与小组成员PPT(84张)
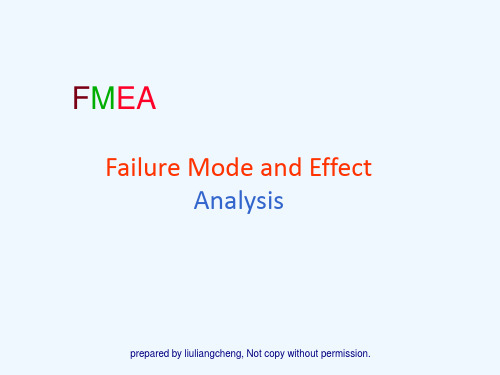
• 在产品寿命期内FMEA没有被重新评定和更新, 没有像动态工具一样被加工
• FMEA被认为太复杂或花费太多的时间
prepared by liuliangcheng, Not copy without permission.
FMEA 的起源
Introduction
prepared by liuliangcheng, Not copy without permission.
什么是 FMEA ?
FMEA 是先期质量策划中评价潜在失效模 式及其起因的一种工具
• 依照其发生在失效的风险优先排列并采取行 动排除或降低其发生的
• 为未来使用和持续改进提供文件化的预防经 验/方法
PFMEA 开始于基本的操作方法讨论完成时,完成时间早于生产 计划制定和生产批准之前
prepared by liuliangcheng, Not copy without permission.
FMEA 的关键术语
• 顾客输入 • 小组—小组的选择(横向功能小组) • 等级—等级的确定 • 风险评估 • 设计过程 • 生产过程
FMECA • Failure Mode Effects and Criticality Analysis
• 1950’s 起源于宇航和美国军方 • 对关注的问题加以分类和排列 • 将评定结果作为预防的目标
• 坚持安全的观点
prepared by liuliangcheng, Not copy without permission.
典型的FMEAs
系统
设计
过程
部件 子系统 主系统
部件 子系统 主系统
人 机 料 法
FMEA失效模式和效果分析
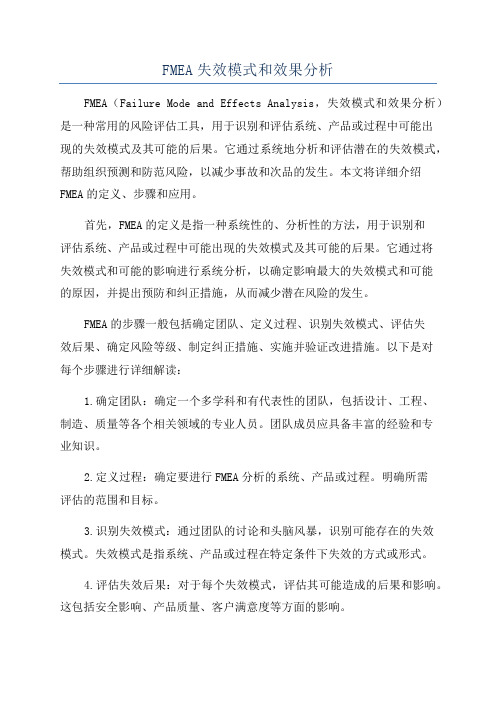
FMEA失效模式和效果分析FMEA(Failure Mode and Effects Analysis,失效模式和效果分析)是一种常用的风险评估工具,用于识别和评估系统、产品或过程中可能出现的失效模式及其可能的后果。
它通过系统地分析和评估潜在的失效模式,帮助组织预测和防范风险,以减少事故和次品的发生。
本文将详细介绍FMEA的定义、步骤和应用。
首先,FMEA的定义是指一种系统性的、分析性的方法,用于识别和评估系统、产品或过程中可能出现的失效模式及其可能的后果。
它通过将失效模式和可能的影响进行系统分析,以确定影响最大的失效模式和可能的原因,并提出预防和纠正措施,从而减少潜在风险的发生。
FMEA的步骤一般包括确定团队、定义过程、识别失效模式、评估失效后果、确定风险等级、制定纠正措施、实施并验证改进措施。
以下是对每个步骤进行详细解读:1.确定团队:确定一个多学科和有代表性的团队,包括设计、工程、制造、质量等各个相关领域的专业人员。
团队成员应具备丰富的经验和专业知识。
2.定义过程:确定要进行FMEA分析的系统、产品或过程。
明确所需评估的范围和目标。
3.识别失效模式:通过团队的讨论和头脑风暴,识别可能存在的失效模式。
失效模式是指系统、产品或过程在特定条件下失效的方式或形式。
4.评估失效后果:对于每个失效模式,评估其可能造成的后果和影响。
这包括安全影响、产品质量、客户满意度等方面的影响。
5.确定风险等级:根据失效模式的后果和可能性,评估其风险等级。
通常使用风险矩阵来划分风险等级,以帮助确定重要性和优先级。
6.制定纠正措施:针对高风险等级的失效模式,制定相应的纠正措施。
这包括预防措施来防止失效的发生,以及纠正措施来解决已经发生的失效。
7.实施并验证改进措施:根据纠正措施的计划,执行相应的改进措施,并进行验证和确认。
确保改进措施的有效性和可行性。
FMEA具有广泛的应用领域。
它可以用于设计过程中的设计FMEA,用于评估产品的可靠性和安全性;也可以用于制造过程中的制造FMEA,用于识别和评估可能导致产品质量问题的制造过程;同时,FMEA还可以用于服务过程中的服务FMEA,用于评估可能影响服务质量和客户满意度的过程。
FMEA潜在失效模式及后果分析(PPT 77张)
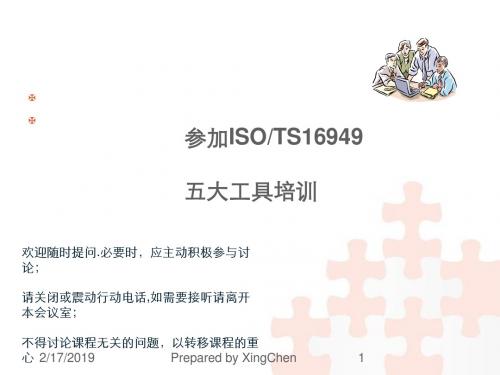
后果是 什么? 功能、特 性或要求 是什么?
有多 糟糕 ? 起因是 什么? 发生的频 率如何?
能做些什么? -设计更改 -过程更改 -特殊控制 -标准、程序或 指南的更改
会是什么问题? -无功能 -部分功能/功能 过强/功能降级 -功能间歇 -非预期功能
2/17/2019
怎样能得到 预防和探测? 该方法在 探测时 有多好?
2/17/2019
Prepared by XingChen
10
2/17/2019
Prepared by XingChen
11
下图描述了进行 FMEA的顺序。这并不是简单地填写一下表
格,而是要理解FMEA的过程,以便消除风险并策划适宜的 控制方法以确保顾客满意。
2/17/2019
Prepared by XingChen
24
8)核心小组 列出有权确定和/或执行任务的责任部门的名称和个人的姓名(建议所 有参加人员的姓名、部门、电话、地址等都应记录在一张分发表上。) 9)项目/功能 填入被分析项目的名称和其他相关信息(如编号、零件级别等)。利 用工程图纸上标明的名称并指明设计水平。在初次发布(如在概念阶 段)前,应使用试验性编号。用尽可能简明的文字来说明被分析项目 满足设计意图的功能,包括该系统运行环境(规定温度、压力、湿度 范围、设计寿命)相关的信息(度量/测量变量)。如果该项目有多种 功能,且有不同的失效模式,应把所有的功能单独列出。
16
DFMEA考虑的内容:
设计 FMEA 针对设计意图并且 假定该设计将按此意图进行生 产/装配。 制造或装配过程中可能发生的 潜在失效模式和 / 或其原因 / 机 理不需、但也可能包括在设计 FMEA当中。 当这些未包含在设计 FMEA 当 中时,它们的识别、后果及控 制应包括在过程FMEA当中。
《MFMEA培训教材》PPT课件
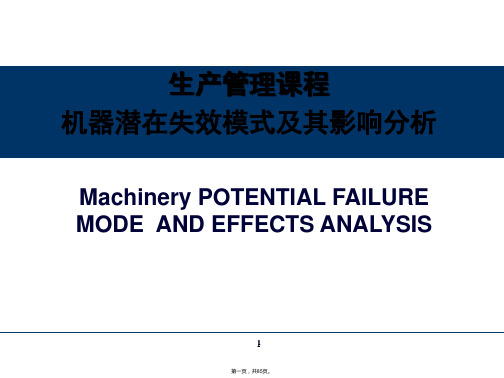
第十二页,共85页。
一个团队,应该是有思考性、自主性、合作性的组织。团队 的成员拥有共同的目标,是在一条船上共患难的水手!
对于团队,有个很新颖的解释:TEAM--Together Everybody can Achieve More! (只有在一起,每个人才能做到
更多!)
113
第十三页,共85页。
同角色的组合达至完美!
适合FMEA的小组成员:
-装配、制造人员(带来现场的经验) -设计人员(包括其它部件、子系统、系统和总成) -工艺人员(包括其它部件、子系统、系统和总成)
-可靠性分析/试验人员(带来失效的经验) -材料工程师(带来材料的要求) -质量工程师(带来质量控制的要求及相关的解决方案) -服务人员(带来客户处抱怨)
第三十一页,共85页。
8.核心小组
•列出所有被授权识别和执行任务的负责人姓名及所在部门(建议包含所有成 员的姓名,部门,电话号码,地址等)。
9a.子系统名称
输入对被分析的子系统名称的描述。
自动装货设备,锭子,水力的,电子的,工作站-5-左边。
设备等级术语
举例
•设备
转移生产线
•系统
设备工作站
•子系统
所有的MFMEA都关注设计。
MFMEA 作为专门的技术应用以识别并帮助最大程度地
减少潜在的隐患一直是非常重要的 !
8
第八页,共85页。
成功实施MFMEA项目的最重要因素之一是时间性。其含义是指 “事件发生前”的措施,而不是“事实出现后”的演练。为实现最大价 值,MFMEA必须在设备的失效模式被纳入到设备设计之前进行。事先 花时间很好地完成MFMEA分析,能够最容易、低成本地对设备进行更 改,从而最大程度地降低后期更改的危机。MFMEA能够减少或消除实 施可能会带来更大隐患的预防/纠正性更改的机会。
FMEA潜在的失效模式及后果分析
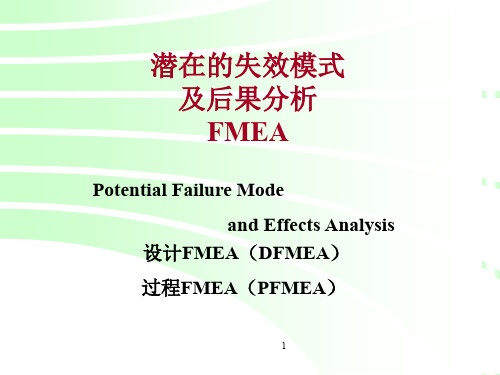
措施结果
项目 功能
潜在失 效模式
潜在失 效后果
严 重 度 S
级 别
潜在失 频 效起因/ 度
机理 O
现行设 计控制
预防
现行设 计控制
探测
探 测 度 D
R P N
建议措 施
责任及目 标完成日
期
采取的措 施
S
O
R DP
N
19
正表 DFMEA(设计)
项目/功能:
1、零部件、编号,修改状态 2、要满足设计意图的功能 3、工作环境
计、分析、试验、可 靠性、材料、质量、 服务、供方、以及高 一层和低一层总成、 系统、零部件设计人
• FMEA应成为促进不 同部门之间充分交换 意见的催化剂,从而 提高整个集体的工作 水平
• 可以邀请一位有 FMEA和团队工作推 进经验的推进员来协 助小组工作。
11
DFMEA是一份动态文件
• DFMEA要在一个设计概念最终 形成之时或之前开始
理效
的师是 一、负 种小责 分组设 析主计 技要的 术采工
用程
)Leabharlann 、9降低失效风险的方式
• 能客观评价设计,包括 功能要求及设计方案
• 为满足生产、装配、服 务和回收要求而评价初 步的设计
• 潜在失效对系统和车辆 运行产生影响在设计和 开发过程中得到考虑
• 为设计、开发、确认项 目的策划提供更多信息
4、其他方法
8
二、DFMEA简介
•
•
•
•
•
和维计体 文过过现 件程程了 化,中工
并正程 规常师 范的在 化思设
(
避 免 可 能 的 出 错
零 部 件 的 设 计 思 想
fmea潜在失效模式分析中英文模版

FMEA编号N准备人Prep主要参加人Core Team: QA部QA Dept./模具部Tooling. Dept.; /工程部Eng.Dept.FMEA日期D潜在的失效模式及效应分析表POTENTIAL FAILURE MODE AND EFFECTS ANALYSI(PFMEA)项目名称 Item: 过程责任部门Process Responsibility: 车型年/车辆类关键日期Key Date:工FMEA编号N准备人Prep主要参加人Core Team: QA部QA Dept./模具部Tooling. Dept.; /工程部Eng.Dept.FMEA日期D 潜在的失效模式及效应分析表POTENTIAL FAILURE MODE AND EFFECTS ANALYSI(PFMEA)项目名称 Item: 过程责任部门Process Responsibility: 车型年/车辆类关键日期Key Date:FMEA编号N准备人Prep主要参加人Core Team: QA部QA Dept./模具部Tooling. Dept.; /工程部Eng.Dept.FMEA日期D 潜在的失效模式及效应分析表POTENTIAL FAILURE MODE AND EFFECTS ANALYSI(PFMEA)项目名称 Item: 过程责任部门Process Responsibility: 车型年/车辆类关键日期Key Date:FMEA编号N准备人Prep主要参加人Core Team: QA部QA Dept./模具部Tooling. Dept.; /工程部Eng.Dept.FMEA日期D 潜在的失效模式及效应分析表POTENTIAL FAILURE MODE AND EFFECTS ANALYSI(PFMEA)项目名称 Item: 过程责任部门Process Responsibility: 车型年/车辆类关键日期Key Date:工FMEA编号N准备人Prep主要参加人Core Team: QA部QA Dept./模具部Tooling. Dept.; /工程部Eng.Dept.FMEA日期D 潜在的失效模式及效应分析表POTENTIAL FAILURE MODE AND EFFECTS ANALYSI(PFMEA)项目名称 Item: 过程责任部门Process Responsibility: 车型年/车辆类关键日期Key Date:工FMEA编号N准备人Prep主要参加人Core Team: QA部QA Dept./模具部Tooling. Dept.; /工程部Eng.Dept.FMEA日期D 潜在的失效模式及效应分析表POTENTIAL FAILURE MODE AND EFFECTS ANALYSI(PFMEA)项目名称 Item: 过程责任部门Process Responsibility: 车型年/车辆类关键日期Key Date:工FMEA编号N准备人Prep主要参加人Core Team: QA部QA Dept./模具部Tooling. Dept.; /工程部Eng.Dept.FMEA日期D 潜在的失效模式及效应分析表POTENTIAL FAILURE MODE AND EFFECTS ANALYSI(PFMEA)项目名称 Item: 过程责任部门Process Responsibility: 车型年/车辆类关键日期Key Date:工FMEA编号N准备人Prep主要参加人Core Team: QA部QA Dept./模具部Tooling. Dept.; /工程部Eng.Dept.FMEA日期D 潜在的失效模式及效应分析表POTENTIAL FAILURE MODE AND EFFECTS ANALYSI(PFMEA)项目名称 Item: 过程责任部门Process Responsibility: 车型年/车辆类关键日期Key Date:工FMEA编号N准备人Prep主要参加人Core Team: QA部QA Dept./模具部Tooling. Dept.; /工程部Eng.Dept.FMEA日期D 潜在的失效模式及效应分析表POTENTIAL FAILURE MODE AND EFFECTS ANALYSI(PFMEA)项目名称 Item: 过程责任部门Process Responsibility: 车型年/车辆类关键日期Key Date:工FMEA编号N准备人Prep主要参加人Core Team: QA部QA Dept./模具部Tooling. Dept.; /工程部Eng.Dept.FMEA日期D 潜在的失效模式及效应分析表POTENTIAL FAILURE MODE AND EFFECTS ANALYSI(PFMEA)项目名称 Item: 过程责任部门Process Responsibility: 车型年/车辆类关键日期Key Date:工FMEA编号N准备人Prep主要参加人Core Team: QA部QA Dept./模具部Tooling. Dept.; /工程部Eng.Dept.FMEA日期D 潜在的失效模式及效应分析表POTENTIAL FAILURE MODE AND EFFECTS ANALYSI(PFMEA)项目名称 Item: 过程责任部门Process Responsibility: 车型年/车辆类关键日期Key Date:工ALYSIS编号Number: 页码Page: 准备人Prepared By:日期Data(编制(orig):(修订REV):ALYSIS编号Number: 页码Page: 准备人Prepared By:日期Data(编制(orig):(修订REV):ALYSIS编号Number: 页码Page: 准备人Prepared By:日期Data(编制(orig):(修订REV):ALYSIS编号Number: 页码Page: 准备人Prepared By:日期Data(编制(orig):(修订REV):ALYSIS编号Number: 页码Page: 准备人Prepared By:日期Data(编制(orig):(修订REV):ALYSIS编号Number: 页码Page: 准备人Prepared By:日期Data(编制(orig):(修订REV):ALYSIS编号Number: 页码Page: 准备人Prepared By:日期Data(编制(orig):(修订REV):ALYSIS编号Number: 页码Page: 准备人Prepared By:日期Data(编制(orig):(修订REV):ALYSIS编号Number: 页码Page: 准备人Prepared By:日期Data(编制(orig):(修订REV):编号Number: 页码Page: 准备人Prepared By:日期Data(编制(orig):(修订REV): ALYSIS21 of 22ALYSIS编号Number: 页码Page:准备人Prepared By:日期Data(编制(orig):(修订REV):22 of 22。
FMEA失效模式效应分析的描述、类型及展开PPT(44张)

影响 设计 问题
制造 问题 影响
原因
现行控制 (DVP&R)
现行测试
原因
现行控制 20 (DVP&R)
结合DFMEA&PFMEA的实例讲解(附件1、2、3)
★ 建立FMEA活动小组; ★ DFMEA/PFMEA针对每个潜在失效模式及后果确定
潜在危害性(S、O、D); ☆ 列出每个原因的目前控制; ☆ RPN风险优先数量运算; ☆ 严重度、频度、不易探测度
☆一般常用的符号
开始和结束 活动说明 决策
过程流程的流向
9
1.3 例
流程 图
准备
接受文件
输入复印份数
开始
机器是否正 常运行?
否
纠正错误
是
是
装订
装订文件
否
重新开始
整理
复印文件的流程图
结束
10
1.3 因果分析
(其中采用方法之一 :鱼刺图又称特性要因图,石川图)
☆ 用图解法对影响过程或产品质量问题的各种因素 进行全面系统的观察和分析,找出其因果关系
FMEA
失效模式效应分析 Failure Mode & Effects Analysis
1
Unit1 失效模式效应分析(FMEA)的描述
1.1 什么是FMEA、起源、分类和实施原则 1.2 FMEA的要素及实施的前期准备 1.3 流程图与因果分析 1.4 系统与子系统
2
1.1 什么是FMEA?
失效模式效应分析 Failure Mode & Effects Analysis
☆ 使小组能集中于问题的实质,围绕问题产生集体 智慧和意见
☆ 集体智慧的火花集中于问题的原因而不是问题的 现状
F M E A失效模式和效果分析
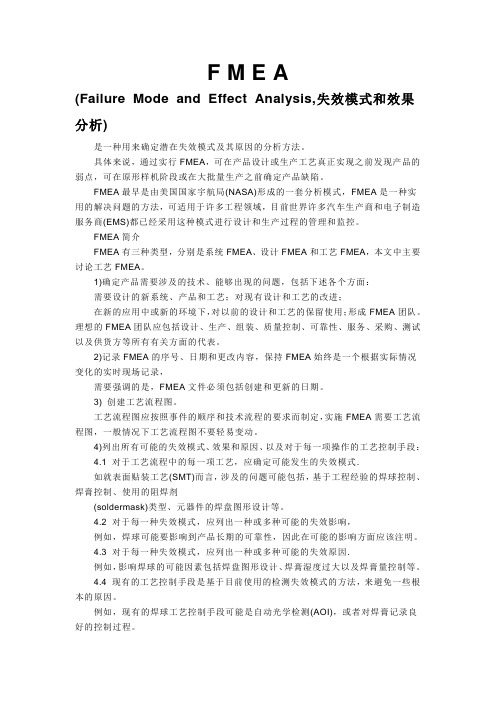
F M E A(Failure Mode and Effect Analysis,失效模式和效果分析)是一种用来确定潜在失效模式及其原因的分析方法。
具体来说,通过实行FMEA,可在产品设计或生产工艺真正实现之前发现产品的弱点,可在原形样机阶段或在大批量生产之前确定产品缺陷。
FMEA最早是由美国国家宇航局(NASA)形成的一套分析模式,FMEA是一种实用的解决问题的方法,可适用于许多工程领域,目前世界许多汽车生产商和电子制造服务商(EMS)都已经采用这种模式进行设计和生产过程的管理和监控。
FMEA简介FMEA有三种类型,分别是系统FMEA、设计FMEA和工艺FMEA,本文中主要讨论工艺FMEA。
1)确定产品需要涉及的技术、能够出现的问题,包括下述各个方面:需要设计的新系统、产品和工艺;对现有设计和工艺的改进;在新的应用中或新的环境下,对以前的设计和工艺的保留使用;形成FMEA团队。
理想的FMEA团队应包括设计、生产、组装、质量控制、可靠性、服务、采购、测试以及供货方等所有有关方面的代表。
2)记录FMEA的序号、日期和更改内容,保持FMEA始终是一个根据实际情况变化的实时现场记录,需要强调的是,FMEA文件必须包括创建和更新的日期。
3) 创建工艺流程图。
工艺流程图应按照事件的顺序和技术流程的要求而制定,实施FMEA需要工艺流程图,一般情况下工艺流程图不要轻易变动。
4)列出所有可能的失效模式、效果和原因、以及对于每一项操作的工艺控制手段:4.1 对于工艺流程中的每一项工艺,应确定可能发生的失效模式.如就表面贴装工艺(SMT)而言,涉及的问题可能包括,基于工程经验的焊球控制、焊膏控制、使用的阻焊剂(soldermask)类型、元器件的焊盘图形设计等。
4.2 对于每一种失效模式,应列出一种或多种可能的失效影响,例如,焊球可能要影响到产品长期的可靠性,因此在可能的影响方面应该注明。
4.3 对于每一种失效模式,应列出一种或多种可能的失效原因.例如,影响焊球的可能因素包括焊盘图形设计、焊膏湿度过大以及焊膏量控制等。
失效模式与效应分析 (FMEA)

失效模式與效應分析 (FMEA)何謂「FMEA、FMECA」?FMECA 是兩種分析技術的總稱:1.FMEA﹝故障型式及其影響分析﹞2.CA﹝Criticality Analysis, 嚴重度分析﹞與失誤樹分析一樣,故障型式影響及嚴重度分析﹝failure modes, effects and criticality analysis, 簡稱 FMECA﹞,首先在美國國防科技中研究發展,且在國防部各機構中普遍應用﹝DOD, 1980﹞,後來漸應用於工業界。
在核能、化工、石化、海上鑽油等高風險工業中,自不例外。
工業界的設計工程師與可靠度﹝Reliability﹞工程師常運用 FMECA 以預測複雜的產品的可靠度,預估一件產品的零件在某特定的時間及情況下,如何失去其功能,故障的次數是多少,故障之後對其他零件或對整個系統會產生怎樣的影響等。
FMECA 的功用不止於可靠度一端,其分析所得的資料,尚可作下列用途:1.協助評估所設計的裝置,如複聯系統﹝Redundancy﹞、故障偵測,以及fail-safe 特性等。
2.對測試、採購﹝Procurement﹞、檢查、改善措施等提供先後順序的參考資料。
3.提供失誤隔絕﹝Fault isolation﹞及維護性﹝Maintainability﹞分析的參考資料。
4.提供系統安全分析﹝如失誤樹分析﹞所需的硬體資料。
FMECA 可在系統週期的任一階段中,依計劃內容之需要,以不同深淺程度實施,但在設計階段的初期,一旦所需的設備確定之後,即應實施。
FMECA 的對象是系統或子系統中的零組件,尤其對於複雜的系統中的設備零件,最能發揮其故障針砭的功效,此為其他系統安全分析技術不能望其項背之處。
但因其分析對象大多限於硬體,故對於人為因素和作業環境因素較少納入分析考慮範圍。
因此,如能將 FMECA 與失誤樹分析合併使用,必更能瞭解整個作業系統的危害,進而防範事故生。
摘於【環安 Q&A】。
过程失效模式及后果分析(PFMEA)(ppt)中英文

PPAP conditions apply 需提交PPAP actual failures occur 发生实际失效
PFMEA
何谓PFMEA 何时作PFMEA
何人作PFMEA
如何作PFMEA 16步工作步骤
Process FMEA 过程FMEA
PFMEA
Who performs a PFMEA? 由谁进行PFMEA?
A cross-functional team should be used 由跨部门小组进行
The leader should be the processresponsible engineer 小组组长应是过程设计责任工程师
PFMEA
Cross-Functional Team 跨部门小组
5-9 people from,5-9人,由从事如下工作的人员组成
Any DFMEA forms and supporting documents shoud be
brought to the PFMEA meetings
DFMEA表单和所有相关文件都应带入PFMEA It should be a natural part of concept development
PFMEA
Process FMEA 过程FMEA
PFMEA is focussed on the Product
PFMEA 关注对产品的影响
PFMEA is focussed on the PRODUCT. Namely, how the PROCESS can cause flaws or variation in the PRODUCT.
FMEA失效模式及后果分析

跟踪 •评审 •确认 •控制计划
20
DFMEA 简介
• 由“设计主管工程师/小组”采用的一种分析技 术 • 以其最严密的形式总結了设计一个零部件、子系 统或系统时,工程师/小组的设计思想 • 在最大范围內保证已充份的考虑到并指明潜在失 效模式及与其相关的后果起因/机理
• 在任何设计过程中正常经历的思维过程是一致的, 并使之规范化
采取的 措施
不 易 R 严 频 重 探 .P 度 测 . 度 数 数 度 N 数
功能 、特 征或 要求
后果 是什 么
有多 糟糕
会有什么问题 •无功能 •部分功能 •功能过强 •功能降级 •功能间歇 •非预期功能 起因 是什 么
发生 频率 如何 怎样 预防 和探 测
能做些什么 •设计更改 •过程更改 •特殊控制 •采用新程序 或指南的更 改 该方法在 探测时有 多好
很少
少 中等 中上
设计控制有很少的机会能找出潜在的起因/机理及后续的失效模式
设计控制有较少的机会能找出潜在的起因/机理及后续的失效模式 设计控制有中等的机会能找出潜在的起因/机理及后续的失效模式 设计控制有中上多的机会能找出潜在的起因/机理及后续的失效模式
76Βιβλιοθήκη 5 4多很多 几乎肯 定
设计控制有较多的机会能找出潜在的起因/机理及后续的失效模式
失效
在規定条件 下, 产品参 数值不能维 持在規定的 上下限之间
5
FMEA 的起源
FMECA
•Failure Mode Effects and Criticality Analysis
•1950’s 起源于宇航和美国军方
•对关注的问题加以分类和排列
•将评定结果作为预防的目标
•坚持安全的观点
失效模式与效应分析在护理风险PPT课件(精选)

失效模式与效应分析在护理风险PPT课件(精选)失效模式与效应分析在护理风险PPT课件(精选)失效模式与效应分析(Failure Mode and Effects Analysis, FMEA)是一种用于识别和评估系统、设备或过程中潜在失效的方法。
在护理领域中,FMEA被广泛应用于识别护理过程中潜在的风险和错误,以便采取相应措施预防风险事件的发生。
本PPT课件将介绍失效模式与效应分析在护理风险管理中的应用,并提供一些精选案例。
第一部分:什么是失效模式与效应分析(FMEA)失效模式与效应分析是一种结构化的方法,用于识别和评估潜在失效对系统或过程的影响。
该方法通过系统性分析可能的失效模式,评估其严重性以及对其他环节的影响,从而确定采取的控制措施和风险管理策略。
FMEA通常由跨专业的团队共同进行,以获得全面准确的分析结果。
第二部分:FMEA在护理风险管理中的应用2.1 护理风险管理的背景和意义护理风险管理是为了提供安全有效的护理而采取的一系列策略和措施。
在日常护理实践中,存在着各种风险和误差,例如药物错误、手术事故、设备故障等。
通过采用FMEA方法,护理团队可以识别和分析这些潜在的失效模式,制定相应的预防措施,降低患者遭受伤害的风险。
2.2 FMEA的基本步骤(1)确定目标:明确进行FMEA的目的和范围。
(2)建立团队:组建跨专业的团队,包括护士、医生、护理管理人员等。
(3)流程分析:详细描述护理过程中的每个步骤和环节。
(4)识别失效模式:分析每个步骤中可能发生的失效模式。
(5)评估严重性与频率:评估每个失效模式的严重性和发生频率。
(6)确定控制措施:制定相应的控制措施,包括预防和纠正措施。
(7)执行措施:在实际护理过程中执行制定的措施,并追踪效果。
(8)持续改进:根据实际效果,对措施进行评估和改进。
第三部分:护理风险管理中的FMEA案例3.1 药物错误防范以护理过程中的药物错误为例,通过FMEA的方法,可以识别出引发药物错误的失效模式,如医嘱错误、药物相互作用等。
失效模式与效应分析(failure modes and effects analysis,FMEA)
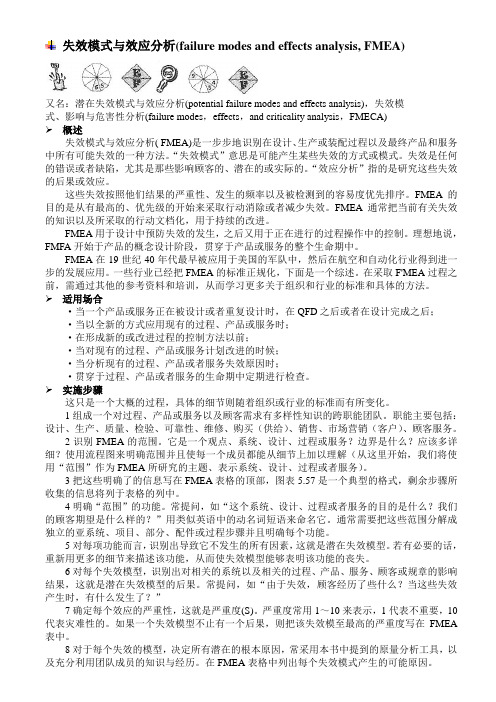
失效模式与效应分析(failure modes and effects analysis, FMEA)又名:潜在失效模式与效应分析(potential failure modes and effects analysis),失效模式、影响与危害性分析(failure modes,effects,and criticality analysis,FMECA)概述失效模式与效应分析( FMEA)是一步步地识别在设计、生产或装配过程以及最终产品和服务中所有可能失效的一种方法。
“失效模式”意思是可能产生某些失效的方式或模式。
失效是任何的错误或者缺陷,尤其是那些影响顾客的、潜在的或实际的。
“效应分析”指的是研究这些失效的后果或效应。
这些失效按照他们结果的严重性、发生的频率以及被检测到的容易度优先排序。
FMEA的目的是从有最高的、优先级的开始来采取行动消除或者减少失效。
FMEA通常把当前有关失效的知识以及所采取的行动文档化,用于持续的改进。
FMEA用于设计中预防失效的发生,之后又用于正在进行的过程操作中的控制。
理想地说,FMFA开始于产品的概念设计阶段,贯穿于产品或服务的整个生命期中。
FMEA在19世纪40年代最早被应用于美国的军队中,然后在航空和自动化行业得到进一步的发展应用。
一些行业已经把FMEA的标准正规化,下面是一个综述。
在采取F'MEA过程之前,需通过其他的参考资料和培训,从而学习更多关于组织和行业的标准和具体的方法。
适用场合·当一个产品或服务正在被设计或者重复设计时,在QFD之后或者在设计完成之后;·当以全新的方式应用现有的过程、产品或服务时;·在形成新的或改进过程的控制方法以前;·当对现有的过程、产品或服务计划改进的时候;·当分析现有的过程、产品或者服务失效原因时;·贯穿于过程、产品或者服务的生命期中定期进行检查。
实施步骤这只是一个大概的过程,具体的细节则随着组织或行业的标准而有所变化。
fmea失效模式分析范文英文版
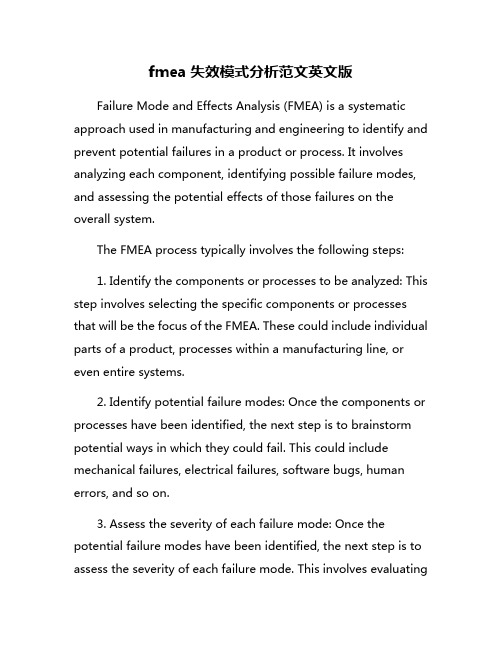
fmea失效模式分析范文英文版Failure Mode and Effects Analysis (FMEA) is a systematic approach used in manufacturing and engineering to identify and prevent potential failures in a product or process. It involves analyzing each component, identifying possible failure modes, and assessing the potential effects of those failures on the overall system.The FMEA process typically involves the following steps:1. Identify the components or processes to be analyzed: This step involves selecting the specific components or processes that will be the focus of the FMEA. These could include individual parts of a product, processes within a manufacturing line, or even entire systems.2. Identify potential failure modes: Once the components or processes have been identified, the next step is to brainstorm potential ways in which they could fail. This could include mechanical failures, electrical failures, software bugs, human errors, and so on.3. Assess the severity of each failure mode: Once the potential failure modes have been identified, the next step is to assess the severity of each failure mode. This involves evaluatingthe potential impact of each failure on the overall system, including safety, cost, and performance implications.4. Determine the likelihood of each failure mode occurring: In this step, the team assesses the likelihood of each failure mode occurring. This could be based on historical data, industry standards, or expert judgment.5. Evaluate the ability to detect each failure mode: Finally, the team assesses the ability to detect each failure mode before it causes harm. This could involve implementing quality control measures, adding redundancy, or improving monitoring systems.By going through this process for each component or process, teams can identify the most critical failure modes and prioritize their efforts on preventing those failures from occurring. This can lead to improved product quality, increased reliability, and a reduction in unexpected downtime.In conclusion, FMEA is a powerful tool for identifying potential failures in products and processes and taking proactive measures to prevent them from occurring. By systematically analyzing each component and assessing the potential failure modes and effects, organizations can improve their products and processes and ultimately provide better value to their customers.。