XHLWI0702结构件检验规程
建筑构件结构性能检验
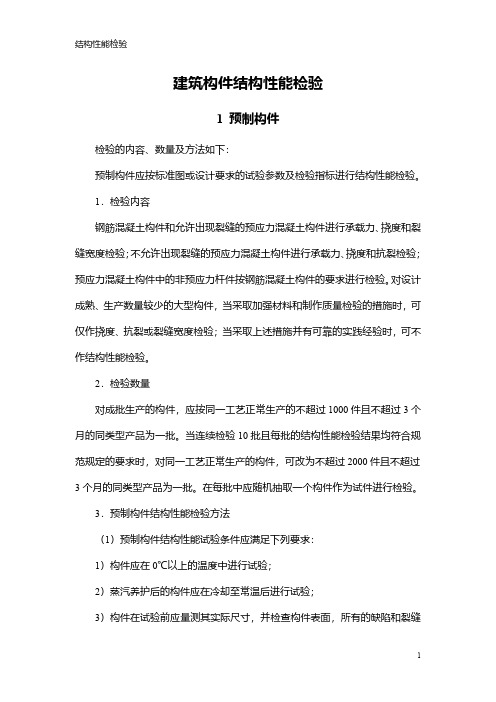
建筑构件结构性能检验1预制构件检验的内容、数量及方法如下:预制构件应按标准图或设计要求的试验参数及检验指标进行结构性能检验。
1.检验内容钢筋混凝土构件和允许出现裂缝的预应力混凝土构件进行承载力、挠度和裂缝宽度检验;不允许出现裂缝的预应力混凝土构件进行承载力、挠度和抗裂检验;预应力混凝土构件中的非预应力杆件按钢筋混凝土构件的要求进行检验。
对设计成熟、生产数量较少的大型构件,当采取加强材料和制作质量检验的措施时,可仅作挠度、抗裂或裂缝宽度检验;当采取上述措施并有可靠的实践经验时,可不作结构性能检验。
2.检验数量对成批生产的构件,应按同一工艺正常生产的不超过1000件且不超过3个月的同类型产品为一批。
当连续检验10批且每批的结构性能检验结果均符合规范规定的要求时,对同一工艺正常生产的构件,可改为不超过2000件且不超过3个月的同类型产品为一批。
在每批中应随机抽取一个构件作为试件进行检验。
3.预制构件结构性能检验方法(1)预制构件结构性能试验条件应满足下列要求:1)构件应在0℃以上的温度中进行试验;2)蒸汽养护后的构件应在冷却至常温后进行试验;3)构件在试验前应量测其实际尺寸,并检查构件表面,所有的缺陷和裂缝应在构件上标出;4)试验用的加荷设备及量测仪表应预先进行标定或校准。
(2)试验构件的支承方式应符合下列规定:1)板、梁和桁架等简支构件,试验时应一端采用铰支承,另一端采用滚动支承。
铰支承可采用角钢、半圆型钢或焊于钢板上的圆钢,滚动支承可采用圆钢;2)四边简支或四角简支的双向板,其支承方式应保证支承处构件能自由转动,支承面可以相对水平移动;3)当试验的构件承受较大集中力或支座反力时,应对支承部分进行局部受压承载力验算;4)构件与支承面应紧密接触;钢垫板与构件、钢垫板与支墩间,宜铺砂浆垫平;5)构件支承的中心线位置应符合标准图或设计的要求。
(3)试验构件的荷载布置应符合下列规定:1)构件的试验荷载布置应符合标准图或设计的要求;2)当试验荷载布置不能完全与标准图或设计的要求相符时,应按荷载效应等效的原则换算,即使控制截面上的内力值相等,但应考虑荷载布置改变后对构件其他部位的不利影响。
钢结构件制造检验规范(建筑类别)
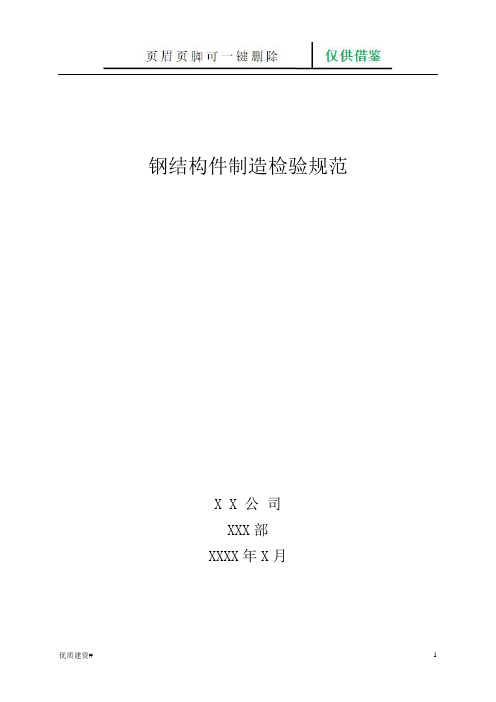
钢结构件制造检验规范X X 公司XXX部XXXX年X月钢结构件制造检验规范1主题内容与适用范围本规范规定了钢结构件产品生产全过程的质量检验要求。
本规范适用于各种牵引车、挂车、皮带运输机桁架、大漏斗、抓斗、装卸桥、起重机扒杆、灯塔以及船闸闸门等钢结构件的生产制造。
2材料结构材料承重结构的钢材,一般采用Q235-A、16Mn钢,其质量标准应符合现行《碳素结构钢》、《低合金结构钢》规定的要求。
钢材应有出厂合格证,如无合格证或标号不清者应进行复验,其结果应符合国家标准规范和设计文件的要求方可采用。
钢材表面锈蚀,、度点或划痕的深度不得大于该钢板负偏差的一半,不应有裂纹、分层等缺陷。
焊条、焊丝、焊剂2.2.1 用于焊接结构件的焊条、焊丝与焊剂应保证焊后不低于母材的机械性能。
2.2.2 焊条、焊丝与焊剂应有质量证明书,应符合设计文件的要求合国家标准的规范。
2.2.3 严禁使用药皮脱落或生锈的焊条、焊丝,以及受潮结块或熔烧过的焊剂。
3 放样、下料3.1 放样应根据工艺要求,预留焊接收缩余量及切割刨边和铣平等加工余量。
3.2 零件的切割线与号料线的允许偏差应符合下列规定:手工切割±2.0mm;自动、半自动切割±1.5mm;精密切割±1.0mm;3.3在下料划线前,应检查钢材变形程度,如有变形应矫正,方可下料划线。
3.4切割前,应将钢材表面切割区域内的蚀锈、油污等清除干净。
切割后,断口上不得有裂纹和大于1.0mm的缺棱,并应清除边缘上的熔瘤和飞溅物等。
3.5切割后切口与钢材表面不垂直度不大于钢板厚度的10%,且不大于2.0mm。
3.6机械剪切的零件,其剪切线与号料线的允差不得大于2.0mm,并应清除毛刺。
3.7机械剪切的型钢,其端部剪切斜度不得大于2.0mm,并应清除毛刺。
3.8已炔自动切口面光洁度等级分为:优级、一级、二级、三级、四级。
手工切割分为:一级、二级、三级,它们分别等于自动切割的二级、三级、四级(见表1)。
构建类零件质量检验指导书
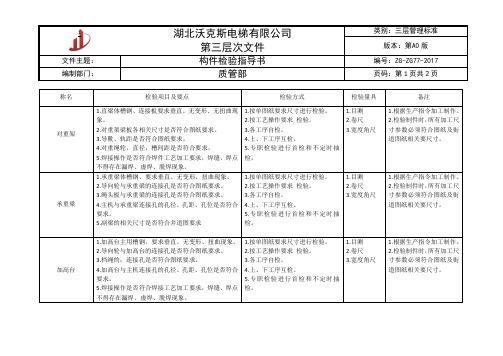
2.卷尺
3.宽度角尺
1.根据生产指令加工制作。
2.检验制件时,所有加工尺寸参数必须符合图纸及街道图纸相关要尺寸。
1.按单图纸要求尺寸进行检验。
2.按工艺操作要求检验。
3.各工序自检。
4.上、下工序互检。
5.专职检验进行首检和不定时抽检。
2.检验制件时,所有加工尺寸参数必须符合图纸及街道图纸相关要尺寸。
加高台
1.加高台主用槽钢、要求垂直。无变形、扭曲现象。
2.导向轮与加高台的连接孔是否符合图纸要求。
3.档绳的;连接孔是否符合图纸要求。
4.加高台与主机连接孔的孔径、孔距、孔位是否符合要求。
5.焊接操作是否符合焊接工艺加工要求,焊缝、焊点不得存在漏焊、虚焊、脱焊现象。
2.上导靴连接孔是否符合图纸要求。
3.轿顶轮间距连接孔是否符合图纸要求。
4.上梁与直梁连接孔的孔径、孔距、孔位是否符合要求。
5.焊接操作是否符合焊接工艺要求,焊缝、焊点不得存在漏焊、虚焊、脱焊现象。
1.按单图纸要求尺寸进行检验。
2.按工艺操作要求检验
3.各工序自检。
4.上、下工序互检。
5.专职检验进行首检和不定时抽检。
1.按单图纸要求尺寸进行检验。
2.按工艺操作要求检验。
3.各工序自检。
4.上、下工序互检。
5.专职检验进行首检和不定时抽检。
1.目测Biblioteka 2.卷尺3.宽度角尺1.根据生产指令加工制作。
2.检验制件时,所有加工尺寸参数必须符合图纸及街道图纸相关要尺寸。
称名
检验项目及要点
检验方式
检验量具
备注
称名
轿架
上梁
1.上梁体槽钢、连接板要求垂直、无变形、无扭曲现象。
混凝土预制构件结构性能检验作业指导书
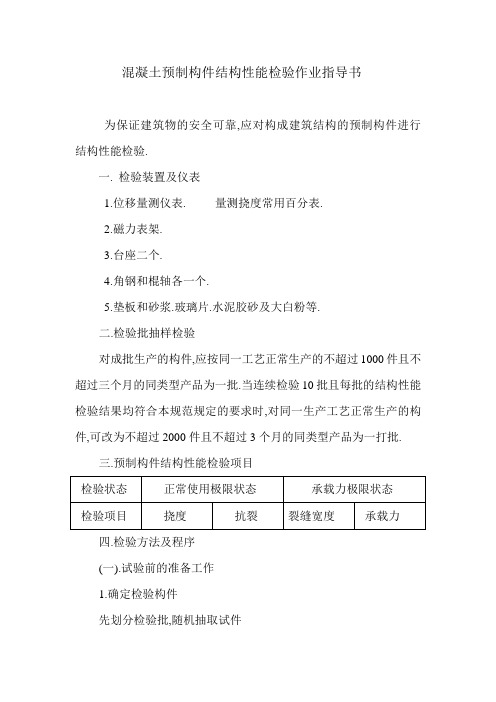
混凝土预制构件结构性能检验作业指导书为保证建筑物的安全可靠,应对构成建筑结构的预制构件进行结构性能检验.一. 检验装置及仪表1.位移量测仪表. 量测挠度常用百分表.2.磁力表架.3.台座二个.4.角钢和棍轴各一个.5.垫板和砂浆.玻璃片.水泥胶砂及大白粉等.二.检验批抽样检验对成批生产的构件,应按同一工艺正常生产的不超过1000件且不超过三个月的同类型产品为一批.当连续检验10批且每批的结构性能检验结果均符合本规范规定的要求时,对同一生产工艺正常生产的构件,可改为不超过2000件且不超过3个月的同类型产品为一打批.三.预制构件结构性能检验项目四.检验方法及程序(一).试验前的准备工作1.确定检验构件先划分检验批,随机抽取试件2.检查构件结构情况与图纸型号是否一致特别是钢丝规格.根数.几何尺寸与图纸设计的是否一致,生产日期是否到28d.3.对检验构件进行常规检查包括构件的几何尺寸(长.宽.高),主筋规格.数量,保护层厚度,混凝土强度(查强度试验日志).4.构件放线步骤为:(1)量取板两端中点连成轴线①;(2)量其中点作垂线②是为试件中线;(3)由中线向两侧量Lj/2(Lj为检验跨度)做出支座线③;(4)量取规定尺寸作均布加载区格线或集中加载线④(四区格均布荷载量Lj/4,三分点集中加载量Lj/6);(5)量后在支座线中点和跨中线两侧上玻璃片作为量测点⑤,整个放线工作完成。
5.构件就位6.支放百分表7.加载物的称重及分布8.均布荷载合理加载计算详见加载程序表9.预加载和仪表调零(二).构件加荷试验与检验1.人员安排一般由2~3个专职检验人员加上4~6个辅助人员组成。
2.分区格加载每个区格长度0.8~1.0m左右为宜,区格之间的间隙50~150mm.3.加载操作中的要求(1).每个区格一人负责加载,在主检人的指挥下各负其责互不干涉。
(2).加载时要轻拿轻放,均匀放置,避免冲击作用造成的瞬时超载。
(3).码放荷重块要摆放平稳.均匀.对称,以避免构件扭转和两挠度值相差过大。
结构件检验标准
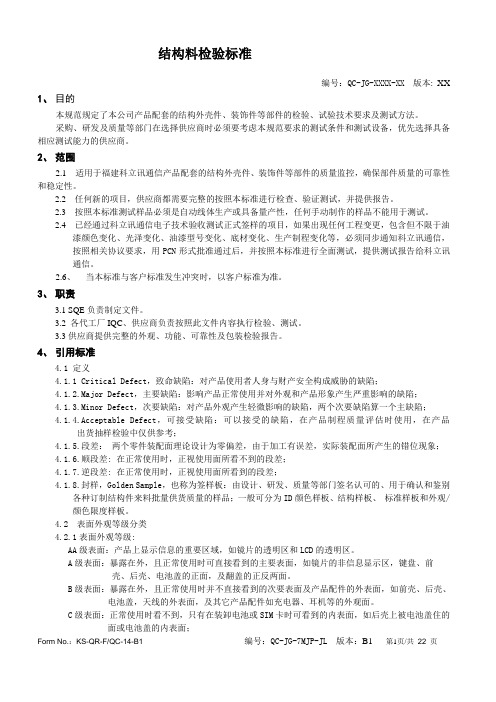
结构料检验标准编号:QC-JG-XXXX-XX 版本: XX 1、目的本规范规定了本公司产品配套的结构外壳件、装饰件等部件的检验、试验技术要求及测试方法。
采购、研发及质量等部门在选择供应商时必须要考虑本规范要求的测试条件和测试设备,优先选择具备相应测试能力的供应商。
2、范围2.1 适用于福建科立讯通信产品配套的结构外壳件、装饰件等部件的质量监控,确保部件质量的可靠性和稳定性。
2.2 任何新的项目,供应商都需要完整的按照本标准进行检查、验证测试,并提供报告。
2.3 按照本标准测试样品必须是自动线体生产或具备量产性,任何手动制作的样品不能用于测试。
2.4 已经通过科立讯通信电子技术验收测试正式签样的项目,如果出现任何工程变更,包含但不限于油漆颜色变化、光泽变化、油漆型号变化、底材变化、生产制程变化等,必须同步通知科立讯通信,按照相关协议要求,用PCN形式批准通过后,并按照本标准进行全面测试,提供测试报告给科立讯通信。
2.6、当本标准与客户标准发生冲突时,以客户标准为准。
3、职责3.1 SQE负责制定文件。
3.2 各代工厂IQC、供应商负责按照此文件内容执行检验、测试。
3.3供应商提供完整的外观、功能、可靠性及包装检验报告。
4、引用标准4.1 定义4.1.1 Critical Defect,致命缺陷:对产品使用者人身与财产安全构成威胁的缺陷;4.1.2.Major Defect,主要缺陷:影响产品正常使用并对外观和产品形象产生严重影响的缺陷;4.1.3.Minor Defect,次要缺陷:对产品外观产生轻微影响的缺陷,两个次要缺陷算一个主缺陷;4.1.4.Acceptable Defect,可接受缺陷:可以接受的缺陷,在产品制程质量评估时使用,在产品出货抽样检验中仅供参考;4.1.5.段差:两个零件装配面理论设计为零偏差,由于加工有误差,实际装配面所产生的错位现象;4.1.6.顺段差: 在正常使用时,正视使用面所看不到的段差;4.1.7.逆段差: 在正常使用时,正视使用面所看到的段差;4.1.8.封样,Golden Sample,也称为签样板:由设计、研发、质量等部门签名认可的、用于确认和鉴别各种订制结构件来料批量供货质量的样品;一般可分为ID颜色样板、结构样板、标准样板和外观/颜色限度样板。
结构检测规程
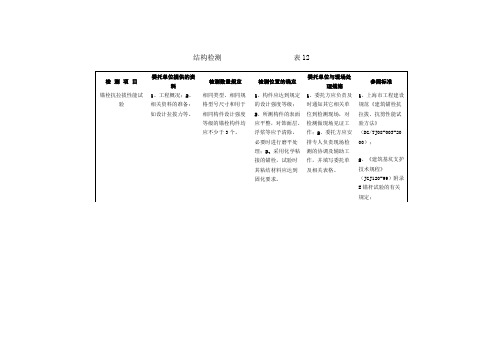
结构检测表12回弹法检测混凝土抗压强度1、工程概况;2、检测混凝土构件设计强度、浇注日期等1、单个检测:适用于单个结构或构件的检测;2、批量检测:适用于在相同的生产工艺条件下,混凝土强度等级相同,原材料、配合比、成型工艺、养护条件基本一致且龄期相近的同类结构或构件。
按批进行检测的构件,抽检数量不得少于同批构件总数的30%且构件数量不得少于10件;3、对某一方向尺寸小于4.5m且另一方向尺寸小于0.3m的构件,其测区数量可适当减少,但不应少于5个。
1、抽检构件时,应随机抽取并使所选构件具有代表性;2、每一构件测区数为10个,均匀分布于构件两个对称可测面上,在构件的重要部位及薄弱部位必须布置测区,并应避开预埋件;3、每一测区大小为20cm×20cm。
4、测区应选在使回弹仪处于水平方向检测混凝土浇注侧面,当不能满足这一要求时,可使回弹仪处于非水平方向检测混凝土浇注侧面、表面或底面;5、相邻两测区的间距应控制在2m以内,测区离构件端部或施工缝边缘的距离不宜大于0.5m,且不宜小于1、委托方应及时将检测事宜通知监理或甲方等相关单位代表,并要求其现场见证;2、在检测过程中,委托方应安排有关负责人员全程见证检测,并提供必要的协助。
3、委托方应对检测面即混凝土表面清洁、平整,不应留有疏松层、浮浆、油垢、涂层以及蜂窝、麻面,必要时可用砂轮清除疏松层和杂物,且不应有残留的粉末和碎屑。
1、《回弹法检测混凝土抗压强度技术规程》(JGJ/T 23—2001)。
0.2m。
结构抽芯现场检测1、工程概况;2、结构或构件类型、外形尺寸及数量;3、原设计采用的混凝土强度等级;4、成型日期、混凝土原材料情况;5、混凝土质量状况和施工中存在的问题;6、有关结构或构件设计图、竣工图等。
1、按单个构件检测时,每个构件的钻芯数量不应小于3个;对于较小构件可取2个;2、对构件的局部区域进行检测时,应由检测单位指定钻芯位置和数量。
1、结构或构件受力较小的部位;2、混凝土质量有代表性的部位;3、便于安放和操作钻芯机的部位;4、避开主筋、预埋件和其它管线的部位,也应尽量避开其它的钢筋的位置。
WI工序产品检验规程
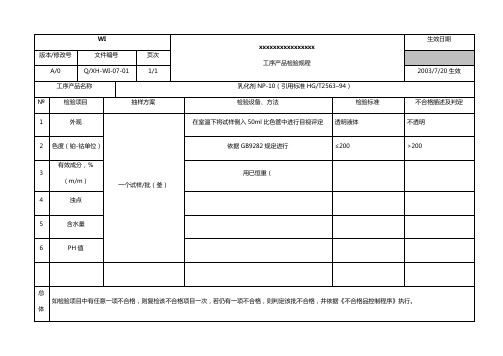
xxxxxxxxxxxxxxxx
工序产品检验规程
生效日期
版本/修改号
文件编号
页次
A/0
Q/XH-WI-07-01
1/1
2003/7/20生效
工序产品名称
乳化剂NP-10(引用标准HG/T2563–94)
№
检验项目
抽样方案
检验设备、方法
检验标准
不合格描述及判定
1
外观
一个试样/批(釜)
在室温下将试样倒入50ml比色管中进行目视评定
透明液体
不透明
2
色度(铂-钴单位)
依据GB9282规定进行
≤200
>200
3
有效成分,%(m/m)
用已恒重(
4
浊点
5
含水量
6
值
总体判定
如检验项目中有任意一项不合格,则复检该不合格项目一次,若仍有一项不合格,则判定该批不合格,并依据《不合格品控制程序》执行。
编制
年月日
审批
年月日
钢结构质量检查流程及规范要求

钢结构质量检查流程及规范要求一、依据标准《建筑工程施工质量验收统一规范》 GB50300—2001《钢结构工程施工质量验收规范》 GB50205—2001《钢结构工程质量检验评定标准》 GB50221—95《钢结构高强螺栓连接的设计施工及验收规程》 JGJ82二、检查准备(一)、钢结构设计图(二)、加工及安装图(三)、其他有关图纸及技术条件(四)、施工合同复印件(五)、劳务分包合同(六)、项目策划会交底记录三、流程及规范1、地脚螺栓基础检查重点检查地脚螺栓组群的间距、柱距、跨距是否满足结构安装要求,留存复验记录,基础的支撑面预留孔螺栓漏出的长度应重点检查其规范要求为:(一)基础标高误差在±5mm以内为合格。
(二)地脚螺栓中心偏移±5mm(含5mm)螺栓伸出支撑面长度偏差30mm(含30mm)螺纹外漏长度30mm(含30mm)。
检查方法:用水准仪、水平尺、钢尺现场实测。
2、主结构安装检查检查柱垂直度,梁起脊高度和平整度等,重点应为高强螺栓初拧、终拧的施工质量现场焊接质量均满足设计及规范要求。
(一)钢柱a、柱脚底座中线对定位中线的偏移±5mmb、柱脚标高允许偏差±5mmc、垂直度允许偏差单层柱H≤10m 偏差H/1000 且不大于10mmH>10m 偏差H/1000 且不大于25mm对高层最大不超过25mm(二) 钢梁a、钢梁的长度L/2500且不大于5mmb、焊接梁端部高度偏差:H≤800允许偏差:±2mmH>800 允许偏差:±3mm(包括吊车梁)c、梁的垂直度(梁高H) H/250 且不应大于15mmd、钢梁不允许有下挠,整体平面度≤20mm(三)高强螺栓a、要有合格的检测报告b、用手调试时应能自由进出c、紧固后用小锤敲打应无松动,另外用红蓝铅笔在螺栓和螺母头部划一直线,然后将螺母松动60°再紧固,检查扭力应在0.9T~1.1T之内(T为力矩)。
钢结构件检验规范

钢结构件检验规范钢结构件检验规范1目的通过对钢结构件的检验确保确保本公司生产的产品质量和安全性能要求。
2范围适用于本公司生产用的所有钢结构件的检验。
3检验规范3.1零件下料3.1.1钢材的平面度,直线度超差影响下料精度时,应进行预矫正。
3.1.2型钢、钢板下的零件,切割后未注公差尺寸的极限偏差应符合表1中的规定。
表1 单位:mm零件厚度=10 >10-20 >20-30 基本尺寸=1000 ±1.5 ±2.0 ±2.5>1000-2500 ±2.0 ±2.5 ±3.0>2500-4000 ±2.5 ±3.0 ±3.5>4000 ±3.0 ±3.5 ±4.03.1.3气割下料的零件,切口应光滑平整。
切割面与表面垂直度应不大于零件厚度的5%,且不得>2mm。
3.1.4气割下料的零件,切口边沿不允许有裂纹、熔渣及氧化铁。
其割痕深度应=1mm,局部深度应=2mm。
3.1.5型钢零件的切面割与表面的垂直度,以及切割之间的平行度,不得大于其尺寸偏差的1/2。
3.1.6剪切下料允许的尺寸偏差符合表2中的规定型钢全长扭曲度H>100 、t=1.5型钢全长扭曲度L>2000 t=0.6L/1000 且不大于3 注:表中§为材料厚度、L为长度、H为高度、t为公差值3.3弯曲及机械加工3.3.1零件弯曲成型在常温时,内侧弯曲半径应大于2倍板厚,弯曲后外侧不得有裂纹,热弯曲时,加热温度应控制在900—1000℃范围内。
3.3.2弯曲成型的零件,其形状尺寸应用样板检查,成形部位与样板之间的局部间隙不得大于2mm。
3.3.3零件边沿需要切削加工时,加工余量不应小于2 mm,加工表面粗糙度不应低于25um。
3.3.4焊缝坡口机械加工,也可用火焰切割,火焰切割的切口不得产生裂纹和大于1 mm 的缺棱。
金属结构件检验规范

金属结构件检验规范1.目的对外协、外购金属结构件质量进行有效控制,保证合格产品入库。
2.适用范围适用于外协、外购金属结构件,包括各模块的盒体体及配件的检验。
3.依据GB2828-87 逐批检查计数抽样程序及抽样表本公司制定的相关产品的设计文件及相关技术资料4.检验装备直尺游标卡尺放大镜万用表专用检具胶带5.环境要求常温检验室里进行6.主要内容6.1抽样方案6.1.1 对新供方产品或老供方提供的新产品(不包括先期提供的样品),前三批采用GB2828-87《逐批检查计数抽样程序及抽样表》中,检查水平IL=Ⅱ, AQL=0.4DE 的加严一次抽样方案。
6.1.2 连续三批加严检查合格后才可采用IL=Ⅱ的正常检查一次抽样方案;对于长期合格的产品,再按照GB2828-87要求实行转移规则。
6.1.3 对于采用以上抽样方案检验不合格的批次,但遇到特殊情况,如生产急需,暂时采用以下两种方法处理:1.针对有关键项目不合格的产品,可采用拣用的处理方法;2.而对于重要项目或一般项目不合格的产品,且不合格的程度不会对产品的最终质量形成影响,可采用让步放行的处理办法,但必须批准后实施。
6.2检验项目6.2.1 外观检验,包括对金属结构件的表面处理、外表光洁度、喷塑质量﹑丝印的颜色、字符的字体字号及各部件之间的配合所用的材质、几何形状的检验,属于重要检验项目。
6.2.2 电气性能检验,属于重要检验项目。
6.2.3 尺寸检验,包括金属结构件整体、各孔、内部铣槽等各部件尺寸的测量,属于重要检验项目。
6.2.4 装配检验,对于结构复杂的零件进行装配试验,属于重要检验项目。
检验项目中涉及到的具体指标见相关装配资料,如:外形尺寸,表面处理要求等等。
6.3 检验方法6.3.1 外观检验主要检验内容如下:(1)首先查看外协,外购金属结构件是否从各合格供应商处采购,其产品有无合格证或经检验合格的证明文件。
(2)目测检验表面处理、光洁度、喷塑质量,看喷塑颜色是否符合要求,表面有无划痕、气泡、表面漆膜是否均匀。
钢结构质量检查流程及规范要求
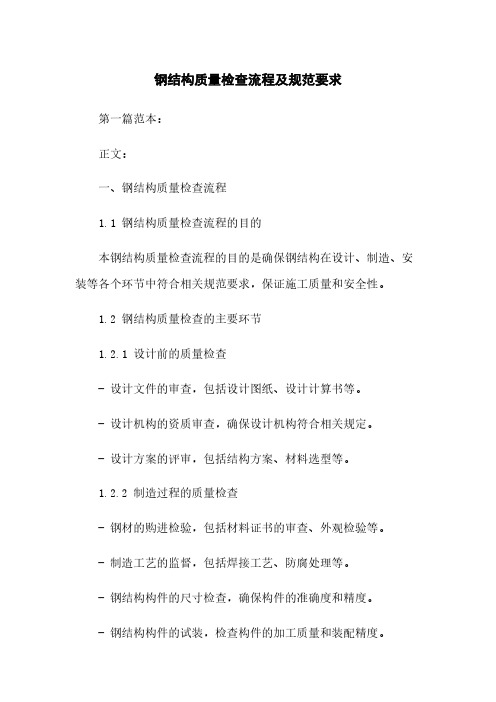
钢结构质量检查流程及规范要求第一篇范本:正文:一、钢结构质量检查流程1.1 钢结构质量检查流程的目的本钢结构质量检查流程的目的是确保钢结构在设计、制造、安装等各个环节中符合相关规范要求,保证施工质量和安全性。
1.2 钢结构质量检查的主要环节1.2.1 设计前的质量检查- 设计文件的审查,包括设计图纸、设计计算书等。
- 设计机构的资质审查,确保设计机构符合相关规定。
- 设计方案的评审,包括结构方案、材料选型等。
1.2.2 制造过程的质量检查- 钢材的购进检验,包括材料证书的审查、外观检验等。
- 制造工艺的监督,包括焊接工艺、防腐处理等。
- 钢结构构件的尺寸检查,确保构件的准确度和精度。
- 钢结构构件的试装,检查构件的加工质量和装配精度。
1.2.3 安装阶段的质量检查- 施工现场的检查与验收,包括施工人员的技术水平、安全措施等。
- 钢结构的安装质量监督,包括构件的拼装、安全连接等。
- 焊接质量的检查,包括焊缝的外观、尺寸检测等。
- 环境监测,包括施工现场的温度、湿度等。
1.3 钢结构质量检查的结果处理根据钢结构质量检查的结果,根据不同问题的严重性和影响,采取相应的处理措施,比如整改、返工、重做等。
二、钢结构质量检查规范要求2.1 钢结构质量检查标准- 国家标准:按照国家相关标准进行质量检查,如《钢结构工程施工质量验收规范》等。
- 行业标准:按照行业协会制定的标准进行质量检查,如《钢结构制作与安装质量控制规范》等。
2.2 钢结构质量检查要求- 构件尺寸偏差要求:按照设计要求进行检查,确保构件尺寸与设计要求的偏差在允许范围内。
- 焊接质量要求:按照相关标准对焊缝的质量进行检查,包括焊缝的外观、强度等。
- 强度和稳定性要求:按照设计要求,对钢结构的强度和稳定性进行检查。
附件:相关标准文件、设计文件、检查记录等。
法律名词及注释:- 《钢结构工程施工质量验收规范》:国家钢结构工程施工质量验收的标准文件。
- 《钢结构制作与安装质量控制规范》:行业标准,针对钢结构制作与安装过程的质量控制要求。
建筑结构材料质量检测技术规程

建筑结构材料质量检测技术规程一、引言建筑结构材料质量检测是建筑工程中不可或缺的环节,其质量直接关系到建筑工程的安全和稳定性。
本技术规程旨在规范建筑结构材料的质量检测方法,确保建筑工程的安全和可靠性。
二、检测对象建筑结构材料包括水泥、混凝土、钢筋、砖块、玻璃等。
三、检测方法1. 水泥(1)外观检查:检查水泥的色泽、细度、密度、含水量等,确保水泥符合要求。
(2)强度检测:混合水泥和标准砂浆按比例制成试块,经过一定时间的养护后进行强度测试,测试结果应符合规定要求。
2. 混凝土(1)配合比检测:检查混凝土配合比是否符合设计要求。
(2)骨料检测:检查混凝土骨料的种类、质量、含水量等,确保符合要求。
(3)强度检测:制成试块,经养护后进行强度测试,测试结果应符合规定要求。
(4)密度检测:测量混凝土的实际密度,确保符合要求。
3. 钢筋(1)外观检查:检查钢筋的表面是否有裂纹、锈蚀等缺陷。
(2)尺寸检测:测量钢筋的直径、长度和弯曲度等,确保符合要求。
(3)拉伸试验:制成试片进行拉伸试验,测试结果应符合规定要求。
4. 砖块(1)外观检查:检查砖块的外观是否平整,有无破损、裂缝等缺陷。
(2)尺寸检测:测量砖块的长度、宽度、厚度等尺寸,确保符合要求。
(3)强度检测:制成试块进行强度测试,测试结果应符合规定要求。
5. 玻璃(1)外观检查:检查玻璃表面是否平整,有无划痕、损伤等缺陷。
(2)尺寸检测:测量玻璃的长度、宽度、厚度等尺寸,确保符合要求。
(3)强度检测:制成试片进行强度测试,测试结果应符合规定要求。
四、检测仪器1. 水泥:砂浆试验机、水泥标准细度仪等。
2. 混凝土:混凝土试验机、骨料筛选机等。
3. 钢筋:金相显微镜、拉力试验机等。
4. 砖块:砖块试验机、砖块尺寸测量仪等。
5. 玻璃:玻璃强度测试仪、玻璃尺寸测量仪等。
五、检测标准建筑结构材料的检测应符合国家和行业标准,如《水泥标准》、《混凝土标准》、《钢筋质量检验标准》等。
钢结构件制造检验规范
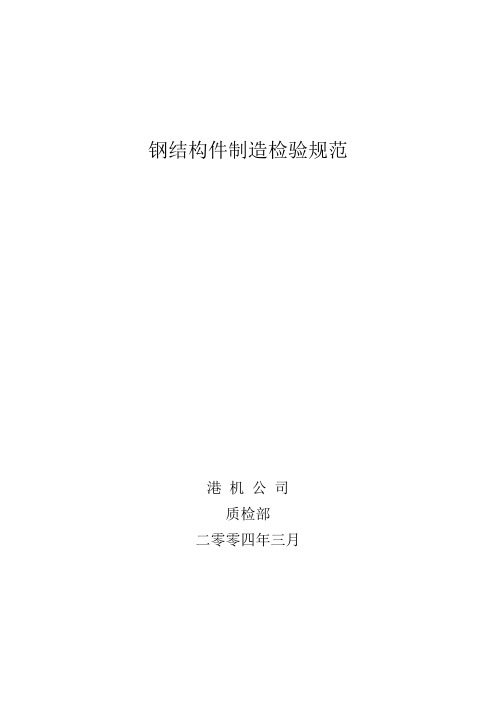
钢结构件制造检验规范港机公司质检部二零零四年三月钢结构件制造检验规范1主题内容与适用范围本规范规定了钢结构件产品生产全过程的质量检验要求。
本规范适用于各种牵引车、挂车、皮带运输机桁架、大漏斗、抓斗、装卸桥、起重机扒杆、灯塔以及船闸闸门等钢结构件的生产制造。
2材料2.1结构材料2.1.1承重结构的钢材,一般采用Q235-A、16Mn钢,其质量标准应符合现行《碳素结构钢》、《低合金结构钢》规定的要求。
2.1.2钢材应有出厂合格证,如无合格证或标号不清者应进行复验,其结果应符合国家标准规范和设计文件的要求方可采用。
2.1.3钢材表面锈蚀,、度点或划痕的深度不得大于该钢板负偏差的一半,不应有裂纹、分层等缺陷。
2.2焊条、焊丝、焊剂2.2.1 用于焊接结构件的焊条、焊丝与焊剂应保证焊后不低于母材的机械性能。
2.2.2 焊条、焊丝与焊剂应有质量证明书,应符合设计文件的要求合国家标准的规范。
2.2.3 严禁使用药皮脱落或生锈的焊条、焊丝,以及受潮结块或熔烧过的焊剂。
3 放样、下料3.1 放样应根据工艺要求,预留焊接收缩余量及切割刨边和铣平等加工余量。
3.2 零件的切割线与号料线的允许偏差应符合下列规定:手工切割±2.0mm;自动、半自动切割±1.5mm;精密切割±1.0mm;3.3在下料划线前,应检查钢材变形程度,如有变形应矫正,方可下料划线。
3.4切割前,应将钢材表面切割区域内的蚀锈、油污等清除干净。
切割后,断口上不得有裂纹和大于1.0mm的缺棱,并应清除边缘上的熔瘤和飞溅物等。
3.5切割后切口与钢材表面不垂直度不大于钢板厚度的10%,且不大于2.0mm。
3.6机械剪切的零件,其剪切线与号料线的允差不得大于2.0mm,并应清除毛刺。
3.7机械剪切的型钢,其端部剪切斜度不得大于2.0mm,并应清除毛刺。
3.8已炔自动切口面光洁度等级分为:优级、一级、二级、三级、四级。
手工切割分为:一级、二级、三级,它们分别等于自动切割的二级、三级、四级(见表1)。
结构件通用检验规范

大唐联仪科技有限公司质量体系文件结构件通用检验规范(V 1.0)责任人:吴志雄审核:张钢批准:范炬2013 -11 –8发布2013 –11-9 实施大唐联仪科技有限公司发布目录1 范围 (3)2 规范性引用文件 (3)3 检验依据 (3)4 术语与定义 (3)4.1缺陷定义 (3)4.2表面等级定义 (4)5 检验 (5)5.1 检验环境 (6)5.2检验方式 (6)5.3 检验程序 (6)5.4检验内容及方法 (6)5.4.1文件齐套性检验 (6)5.4.2 形状尺寸检验 (7)5.4.3焊接工艺检验 (8)5.4.4装配性能检验 (9)5.4.5外观检验 (9)1 范围本规程规定了结构件产品的通用检验要求和检验方法。
本规程适用于指导各种结构件产品的检验,包括结构零件、结构部件及其他由结构件和非混合组装而成的产品。
本规程适用于各个阶段对于结构件产品实施的检验,包括来料检验、工序检验、整机检验。
本文档为通用文件,当某一或者某些结构件产品有独立成文的检验规范或质量要求时,应以其独立成文的检验规范和质量要求为标准。
2 规范性引用文件下列文件对于本文件的引用是必不可少的,凡是注明日期的标准文件,仅注日期的版本适用于本文件,凡是不注明日期的引用文件,其最新版本(包括所有的修改单)适用于本文件。
GB/T 1.1-2009 标准化工作指导第1部分:标准的结构和编写GB/T 1804-2000 一般公差未注公差的线性和角度尺寸的公差GB/T 1184-96 形状和位置公差未注公差值GB/T 9286-1998 色漆和清漆漆膜的划格试验GB/2828.1-2003 计数抽样检验程序第1部分:按接收质量限(AQL)检索的逐批检验抽样计划3 检验依据本文档为通用文件,当某一或者某些结构件产品有独立成文的检验规范或质量要求时,应按照独立成文的检验规范和质量要求进行合格与否的判定。
DTM 0.006.211 JG 结构件通用检验规范DTM 0.006.215 JG 面板检验规范结构件外检检验标准9.184 术语与定义4.1缺陷定义致命缺陷(CR):有可能危及顾客生命财产安全的缺陷重缺陷(MA):对产品装配或产品使用性能会造成较大影响的缺陷,如:重要尺寸的超差,重要技术要求的不满足,外观件的表面缺陷等。
07WI工序产品检验规程

xxxxxxxxxxxxxxxx
工序产品检验规程
生效日期
版本/修改号
文件编号
页次
A/0
Q/XH-WI-07-01
1/ 1
2003/7/20生效
工序产品名称
乳化剂NP-10(引用标准HG/T2563–94)
№
检验项目
抽样方案
检验设备、方法
检验标准
不合格描述及判定
1
外观
一个试样/批(釜)
在室温下将试样倒入50ml比色管中进行目视评定
透明液体
不透明
2
色度(铂-钴单位)
依据GB9282规定进行
≤200
>200
3
有效成分,%(m/m)
用已恒重(
4
浊点
5
含水量
6
PH值
总体判定
如检验项目中有任意一项不合格,则复检该不合格项目一次,若仍有一项不合格,则判定该批不合格,并依据《不合格品控制程序》执行。
编制
年月 日
审批
年月 日
07WI工序产品检验规程(竖)
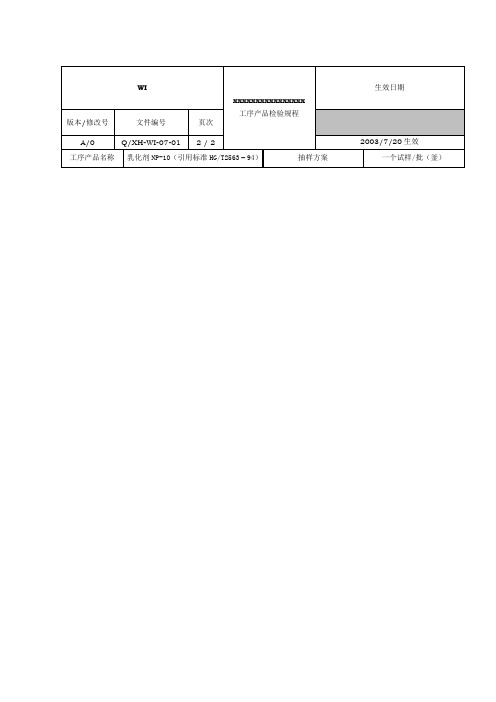
式中:V0-空白试验时耗用氢氧化钠标准溶液的体积,mL;
V1-试样耗用氢氧化钠标准滴定溶液的体积,mL;
N-氢氧化钠标准滴定溶液的浓度,N;
m-试样的质量,g;
X-试样的酸值,mgKOH/g。
检验标准:40-60
不合格描述:<40或>60
5、含水量(%,m/m)
检验方法:称取试样4-6g,(精确至0.001g),置于100ml容量瓶中,加入无水甲醇并稀释至刻度,剧烈振摇使样品中的水溶解,静置,使不溶盐沉淀至瓶底。
2/2
2003/7/20生效
工序产品名称
乳化剂T-85(引用标准Q/320682RSZ09-2003)
抽样方案
一个试样/批(釜)
1、外观
检验方法:在室温下将试样倒入50ml比色管中进行目测评定
检验标准:棕褐色粘稠油状物
不合格描述:与标准色有明显偏差
2、酸值:mgKOH/g
检验方法:称取约10g试样于锥形瓶中(称准至0.004g),加100ml中性乙醇,并摇动使之完全溶解,加10滴酚酞指示剂),用0.1N氢氧化钾溶液滴定至中点。
x=
式中:x-酸值,mgkOH/g;
m-试样的质量,g;
v-所用标准溶液体积,ml;
N-所用标准溶液的当量浓度,N。
检验标准:≤2.1
不合格描述及判定:>2.1
3、皂化值,mgkOH/g
检验方法:称取试样约3g(精确至0.0001g)于磨口锥形瓶中,用移液管吸取25ml约0.5mol/L氢氧化钾乙醇溶液置于已装有称量试样的锥形瓶中,接上回流冷凝管,于恒温控制水管中温和地煮沸回流60min,然后用10mL95%乙醇冲洗冷凝管的内壁和塞的下部。取出锥形瓶,加入12滴酚酞指示剂,以0.5N盐酸标准溶液滴定至粉红色刚好褪去,加热至沸,如溶液又出现红色,再滴定至粉红色刚好裉去。并进行空白试验。
结构件检验标准

材质
依设计要求或承认样品确认材质:
A.材质与设计要求或样品一致。
B.未特别指定,不允许定掺对水口料。
C.生产厂家须能够提供材质证明。
相关
文件
样品
文件
B
3
颜色
依色板、色卡或颜色限度样板,目视比对:
A.颜色不可有明显的差异,当出现颜色差异时要以颜色限度样品为准进行限收(当五金件为内置组装件时,色差可接受,基色须符合要求)
L≤3、N≦2、D≤10
0.08<W≦0.10
W≤0.1mm、L≤5mm
N≤3、D≧10mm
可接收
异色点、点状杂质、撞伤、凹凸状
不允许
0.10<Φ≦0.20
N≦1
0.15<Φ≦0.25
N≦1
D≤0.5mm、N≤2个
D≧10mm
可接收
同色点、点状杂质、撞伤、凹凸状
不允许
0.15<Φ≦0.25
N≦1个
0.20<Φ≦0.30
在选定的待测表面作百格(1mm*1mm),即在待测表面用百格刀,横竖两个方向各划一刀
第三步:贴3M胶
取全新的3M胶带约50mm长,紧贴于百格区域,用手指将胶带压平,注意不可有气泡,需压净其中的气泡
第四步:拉起3M胶
用手抓住胶带一端,在垂直方向(90°)迅速拉下胶纸,同一位置操作2次,然后观察表面处理(喷油)脱落情况
色卡
目视
B
4
表面
处理
确认表面处理方式与要求是否一致(与规格、样板核对一致):
A.一般表面处理分:无表面处理(素材)、喷油、丝印、电镀、氧化、阳极、研磨、晒文等,其表面处理方式要求与设计及样板核对一致。
目视
结构件检验规范

凹坑
不允许
D≤0.30mm(S≤0.07mm2) , N≤2 且DS≥15mm
D≤0.60mm (S≤0.28 mm2) , N≤2且DS≥15mm
颗粒
D≤0.20mm(S≤0.05mm2) , N≤2 且DS≥15mm(喷漆件允收、电镀件不允许)
22
雕刻
图标正确,无锯齿状,线条粗细与样品对比偏差10%;
图标位置偏差±0.30mm(在透光区域内),无雕刻不良现象。
备注:
1)直径小于0.10mm且间距大于15mm的点缺陷可忽略不计。
2)点缺陷包括异色点、杂质、多胶点、气泡等所有呈现点形状的缺陷,摸上去有手感的颗粒按异色点计算。
序号
不良项目
I测量面
D≤0.60mm (S≤0.28 mm2) , N≤2且DS≥15mm
凹坑
D≤0.20mm(S≤0.05mm2) , N≤2 且DS≥15mm(显示窗区域不允许有凹坑)
D≤0.30mm(S≤0.07mm2) , N≤2 且DS≥15mm
D≤0.60mm (S≤0.28 mm2) , N≤2且DS≥15mm
11
顶白/顶凸
不允许
不允许
允许
12
注塑不饱和
不允许
不允许
不允许
13
银条/流纹/烧焦等
不允许
不允许
允许
14
暗斑
不允许
不允许
允许
15
水口
不允许
不允许
不影响装配时允许
16
多料
不允许
17
字符阴影、发白
不允许
18
漏光
- 1、下载文档前请自行甄别文档内容的完整性,平台不提供额外的编辑、内容补充、找答案等附加服务。
- 2、"仅部分预览"的文档,不可在线预览部分如存在完整性等问题,可反馈申请退款(可完整预览的文档不适用该条件!)。
- 3、如文档侵犯您的权益,请联系客服反馈,我们会尽快为您处理(人工客服工作时间:9:00-18:30)。
受控状态:文件编号:ZX/WI-08-01 发放编号:版本:B
结构件检验规程
编制\日期:
批准\日期:
实施\日期:
1 范围
本标准规定了结构件通用检验规程的内容与要求。
本标准适用于本公司自制的结构件检验
2 规范性引用文件
下列文件中的条款通过本标准的引用而成为本标准的条款。
凡是注日期的引用文件,其随后所有的修改单(不包括勘误的内容)或修订版均不适用于本标准。
凡是不注日期的引用文件,其最新版本适用于本标准。
GB/T 3323-1987 钢熔化焊对接接头射线照相和质量分级’
GB/T 11345-1989 钢焊缝手工超声波探伤方法和探伤结果分级
JB/ 重型机械通用技术条件焊接件
XHL/WI08-02 自制件通用检验规程
XHL/WI08-03 涂装通用检验规程
3 内容与要求
检验程序和一般检验要求
结构件的检验程序和一般检验要求应符合XHL/WI08-02《自制件通用检验规程》的规定
下料检验
3.2.1 检验方式
下料检验方式为首检+抽检。
3.2.2切割下料
3.2.2.1 尺寸偏差按JB/《重型机械通用技术条件焊接件》标准的C级精度验收,且不大予3mm。
3.2.2.2 切割面相对板面的垂直度公差按JB/《重型机械通用技术条件焊接件》标准的G级精
度验收,且不大于1.5mm。
,::
3.2.2.3切割面粗糙度不大于Ra50,局部塌陷不大于1mm
3.2.2.4切割产生的氧化物应清理干净。
3.2.3剪切下料
3.2.3.1板料和型材长度偏差按JB/《重型机械通用技术条件焊接件》标准的C级精度检验,
不大于3mm。
3.2.3.2型材端面垂直度公差按JB/T 《重型机械通用技术条件焊接件》标准的F级精度验收,
且不大于1.5mm。
3.2.4刨边
3.2.
4.1 粗糙度不低于Ra25;
3.2.
4.2 尺寸公差不大于Lmm;
3.2.
4.3刨边直线度≤2/1000,且不大于2眦:
3.2.
4.4相邻边夹角偏差不大于±30′
焊前检验
3.3.1 焊前检验方式为抽检
3.3.2焊前检验包括确认构件材质、焊丝、焊条是否符合设计和工艺要求;焊缝部位应无氧化皮、
污、油漆、飞溅物、毛刺和影响焊接的镀层;坡口符合图纸和工艺要求,定位焊点应避开应力集中区域且不应有烧穿、裂纹、未焊透点、气孔等缺陷。
焊接过程检验
3.4.1 焊接过程检验方式为首检+抽检。
3.4.2焊接过程检验内容为焊接工艺规范、焊接顺序、焊缝装配尺寸、夹具夹紧情况、焊接设备
运行情况等应符合图纸、工艺、标准和相关技术文件的要求;焊接形式和焊缝尺寸应符合图纸要求。
焊缝质量检验
3.5.1 检验标准
焊缝按GB/T 3323-198'7《钢熔化焊对接接头射线照相和质量分级》和GB/T 9《钢焊缝手工超声波探伤方法和探伤结果分级》进行分级:焊缝的等级要求由设计提出,未提出者视为Ⅳ级焊缝。
3.5.2检验方式
焊缝质量检验方式按表l执行
表1 焊缝质量检验方式
3.5.3焊缝外观及外形尺寸检验
3.5.3.1 焊缝的外观质量要求表面无焊渣、飞溅、裂纹、焊瘤、焊丝头,其余要求见表2.
后进行检验。
3.5.3.3外观检验一般目测,必要是采取放大镜或磁粉探伤,渗透探伤等方法辅助判断。
3.5.3.4 对接焊缝和角焊缝的外形尺寸要求见表3和表4。
3.5.3.5 点焊点直径允许为2
1+-mm ;
焊点相对于焊缝中心偏移量不大于2mm ;点焊焊点间距允许差为5±。
3.5.3.6 搭接焊缝焊角高允差为5.1±mm ,且小于达接板材厚度。
3.5.3.7 断续焊缝间距允差为5±mm 。
表3 对接焊缝外形尺寸的允许值
项目 接头尺寸
Ⅰ、Ⅱ级焊缝 Ⅲ级焊缝 Ⅳ级焊缝 焊缝余高h
h ≤1mm+0.05c h ≤1mm+0.15c 允许局部超差 h ≤1mm+0.25c 允许局部超差 焊缝宽度c 的偏
差
0~1mm+0.1c
0~1mm+0.15c
0~1mm+0.2c
错边量e
e <δ且≤2mm
e <δ且≤2mm e <δ且≤3mm
表4 角焊缝外形尺寸允许值
项目
接头型式 Ⅰ级 Ⅱ级
Ⅲ级
焊缝余高的上偏
差a-b
≤1mm+且局部最大凸起≤1.5mm
≤1mm+且局部最大凸起≤2mm
≤1mm+且局部最大凸起≤2.5mm
焊缝余高的下偏
差b-a
不允许
≤0.3mm+且局部最大不超过≤1mm ≤0.3mm+且局部最大不超过≤2mm
注:k 为焊高设计值
3.5.4 焊缝内部质量的检验
3.5.
4.1对结焊缝内在质量按GB/T3323-1987《钢焊融化焊对接接头射线照相和质量分级》进行检验,其它接头形式按GB/T11345-1989《钢焊缝手工超声波探伤方法和探伤结果分级》进行检验。
3.5.
4.2 当结构件限制不便于检验时,内部缺陷可用在相同条件下制备的试件上取样进行探伤检验,式样的数量和取样标准由工艺确定。
3.
5.4.3 不允许过烧。
3.5.5 密封性能检验
有密封性能要求的焊缝,工作压力小于300KPa 时用煤油试验检测其密封性;工作压力大于300kpa 时用不小于工作压力倍的水压实验,保压时间不小于5min ,不应有渗漏。
结构件外观检验
结构件外观要求表面无毛刺、飞溅、飞边、焊渣、锈蚀、油污等,锐边倒钝(t 为板厚),
氧割边粗糙度不大于Ra50。
焊接结构未注公差
3.7.1 各种门、窗、护板、盖板、油标、油箱等,呈对称安装的对称度应不大于3mm;与相邻件间隙不均匀值应不大于2mm,与机体面贴合间隙应不大于3mm;对角线差值应不大于4mm。
3.7.2 焊接结构件未注公差应符合表5-表9之规定。
3.7.3 结构件油漆检验按Q/QKAM《涂装通用检验规程》之规定执行。
表5 焊接结构尺寸与形位公差(形位公差指:直线度、平行度、平面度、垂直度)等级应用范
表6焊接结构件尺寸偏差和形位公差数值
表7焊接结构件角度偏差
L 公称尺寸
Δα、e 允许角度偏差
图1
表8焊前弯曲成型的筒体允许差
外径直径偏差ΔDH
圆度允差A-B
弯角C 筒体壁厚
≤30 >30
DH≤300 ±1 2 1 2 300<DH≤500 ±3 5 3 3 500<DH≤1000 ±58 5 3 1000<DH≤1500 ±711 7 4 1500<DH≤2000 ±914 9 4 2000<DH≤2500 ±1117 11 5 2500<DH≤3000 ±1320 13 5 DH>3000 ±1523 15 6
注:参数A、B、C、DH、ΔDH见图2
图2
表9焊前管子的弯曲半径、圆度允差及允差的波纹深度
允差名称
管子外径示意图
30 38 51 60 70 83 102 108 125 150 200
弯曲半径R的允差
75=R<125±2±2±3±3±4
160=R<300 ±1±1±2±2±3
400=R<500 ±5±5±5±5±5±5 500=R<1000 ±4±4±4±4±4±4 R>1000 ±3±3±3±3±3±3
在弯曲半径处的圆度允差a 或b
R=75 R=100 R=125
R=160 R=200 R=300 R=400 R=500 R=600 R=700
弯曲处的波纹深度a
编制/日期审核/日期。