模具设计作业
注塑模具设计作业指导书(注塑部)

注塑模具设计作业指导书(注塑部)1. 背景本指导书旨在为注塑部门的设计人员提供注塑模具设计作业的指导,以确保设计工作的高效性和质量。
注塑模具的设计是注塑工艺的关键环节,直接影响产品的质量和生产效率。
因此,设计人员需要掌握相关的专业知识和技能,并遵循一定的设计原则和标准。
2. 设计作业流程2.1 确定设计要求在开始设计作业之前,设计人员需要与产品设计部门和生产部门进行沟通,了解产品的要求和预期性能。
这些要求可能包括产品尺寸、材料要求、生产量要求等。
2.2 分析注塑工艺在确定设计要求后,设计人员需要对注塑工艺进行分析。
这包括注塑机的选择、模具结构的确定、注塑工艺参数的设定等。
设计人员应该具备一定的注塑工艺知识,以确保设计的可实施性和优化注塑过程。
2.3 模具设计在分析注塑工艺后,设计人员可以开始进行模具设计。
模具设计应包括以下几个方面:- 模具结构设计:根据产品的形状和尺寸要求,确定模具的结构,包括模具基板、模腔、模芯、冷却系统等。
- 模具材料选择:选择适合注塑工艺的模具材料,考虑材料的强度、耐磨性、耐腐蚀性等因素。
- 模具加工工艺:确定模具的加工工艺,包括数控加工、电火花等。
- 模具的标准部件选型:选择符合标准的模具部件,以提高模具的通用性和可靠性。
- 模具装配和调试:完成模具的装配和调试工作,确保模具运行稳定和正常。
2.4 模具验收完成模具设计后,设计人员需要与生产部门进行模具验收。
在模具验收过程中,需要检查模具的尺寸精度、操作性能、模具寿命等。
如果存在问题,设计人员需要及时进行调整和修改。
3. 设计原则和注意事项在进行注塑模具设计时,设计人员需要遵循以下原则和注意事项:- 合理性原则:设计应合理,确保产品质量和生产效率。
- 简化原则:模具结构应简化,以提高制造和维修的便利性。
- 可靠性原则:模具的结构应稳定可靠,能够经受长时间的注塑生产。
- 标准化原则:尽量使用标准模具部件,以提高模具的通用性和可靠性。
模具设计作业标准及规范

模具设计作业标准及规范二、2D模架设计1、产品的排位:影响排位的因素a产品的外形的结构b产品的进胶方式以及位置c不同产品的分型面形状d产品的大小e产品的材料属性A、有无客户的排位要求判定所给定的排位与模具结构方面有无冲突B、排位时要注意的事项:✧产品的排位基准(一般以产品的最大外形进行XY向分中,以前后模分型面的某点为Z向基准),✧产品的缩水中心(一般以排位基准进行缩水,而不以模具中心或其它坐标进行缩水处理)✧产品的缩水率及缩水方式(缩水率由产品的材料以及成形压力决定——此数据由客户提供,缩水方式要与3D缩水方式一致,如:3D的比例缩水——2D的“SCALE”,3D的XYZ向的不同缩水——2D的“块的三方向的不同比例”处理)✧镜像处理问题(前后模正视图必须要注意镜像处理的问题:使用的是产品的投影视图需镜像,使用的是模仁的投影视图就不需镜像处理,前后模侧视图则无需镜像处理)✧顶针,运水,镶件,螺丝以及抽芯机构的大概位置、位移,排位的梳密要有设计余地✧流道的距离问题(在其它因素的治约下要尽可能使流道越短越好)✧不同产品的排位要求分型面整齐,减少起伏多变的台阶2、模仁大小的定义:影响因素:a产品的排位b产品在分型方向的投影面积c型腔的结构d钢料物理属性——钢度和硬度e成型注射时的最大压力A、有无客户对模仁的要求B、确定模仁大小时应注意的事项✧确保型腔壁有足够的厚度,不致于在加工时变形、成型时钢料变形影响成型尺寸精度、飞边,成型压力过大致使模仁断裂等。
(一般的常规参考数据:投影面积在50* 50——型腔壁厚约为25mm100*100——型腔壁厚约为30mm150*150——型腔壁厚约为33mm200*200——型腔壁厚约为40mm250*250——型腔壁厚约为43mm300*300——型腔壁厚约为50mm350*350——型腔壁厚约为55mm具体参数待查)✧确保在后期设计中排位有足够的位置,不致于多方面发生干涉而无法处理(如:水路与模仁固定螺丝相干涉;钢料厚度方向在精框中没了管位限制,则可适当加厚钢料等)。
模具开发作业流程
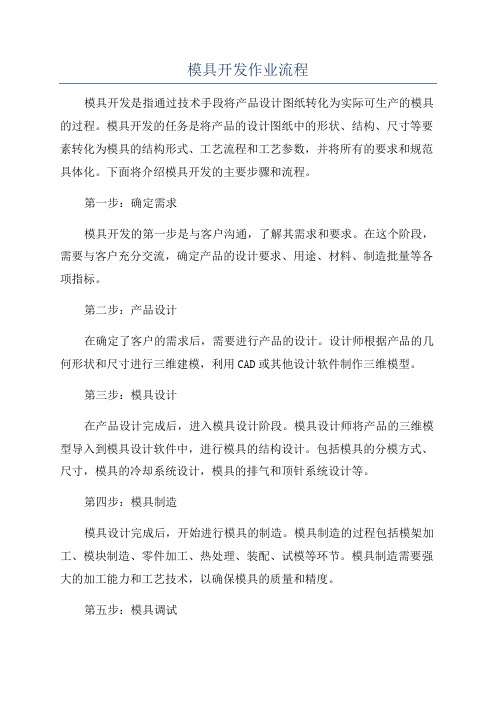
模具开发作业流程模具开发是指通过技术手段将产品设计图纸转化为实际可生产的模具的过程。
模具开发的任务是将产品的设计图纸中的形状、结构、尺寸等要素转化为模具的结构形式、工艺流程和工艺参数,并将所有的要求和规范具体化。
下面将介绍模具开发的主要步骤和流程。
第一步:确定需求模具开发的第一步是与客户沟通,了解其需求和要求。
在这个阶段,需要与客户充分交流,确定产品的设计要求、用途、材料、制造批量等各项指标。
第二步:产品设计在确定了客户的需求后,需要进行产品的设计。
设计师根据产品的几何形状和尺寸进行三维建模,利用CAD或其他设计软件制作三维模型。
第三步:模具设计在产品设计完成后,进入模具设计阶段。
模具设计师将产品的三维模型导入到模具设计软件中,进行模具的结构设计。
包括模具的分模方式、尺寸,模具的冷却系统设计,模具的排气和顶针系统设计等。
第四步:模具制造模具设计完成后,开始进行模具的制造。
模具制造的过程包括模架加工、模块制造、零件加工、热处理、装配、试模等环节。
模具制造需要强大的加工能力和工艺技术,以确保模具的质量和精度。
第五步:模具调试模具制造完成后,需要进行模具的调试。
调试过程中,需要根据产品的要求进行调整和优化,确保产品质量稳定。
在试模过程中,发现存在问题需要及时进行修复和改进。
第六步:样品确认模具调试完成后,需要向客户提供样品,并与客户进行确认。
客户对样品进行测试和评估,确保产品符合其要求和预期。
第七步:模具生产样品确认后,模具进入正式生产阶段。
根据客户的订单要求,利用模具进行产品生产。
第八步:售后服务模具交付给客户后,需要进行售后服务。
定期回访客户,了解模具在生产过程中的使用情况和反馈,提供技术支持和售后服务。
总结:模具开发是一个复杂的过程,涉及到多个环节和技术知识。
通过以上的步骤,可以确保模具的质量和性能达到客户的要求,实现高效生产。
模具开发的每个环节都需要进行精心设计和制造,以确保模具的可靠性和稳定性。
精密五金模具设计作业标准-穿线孔

推行作業標准化,降低設計錯誤率﹐實現模具設計快速作業。
二.適用范圍
光寶沖模設計課。三.穿Fra bibliotek孔位置及尺寸要求
對于精度要求較高﹐考慮到需要使用線割加工的內孔﹐設計者必須參照以下原則畫出穿線孔(直徑Φ0.5mm,Φ1.0mm或Φ2.0mm,Φ3.0mm﹐圖層為該模板銑床層)。
1.異形孔大于等于6mm時﹐穿線孔直徑用Φ3.0mm。穿線孔離長邊4~~6mm(如圖A)﹐注意﹕刀口板折模孔穿線孔做在非刀口處離邊4mm,(如圖B)
5.一般圓孔設計者不需畫出穿線孔。
2.異形孔小于或等于6mm大于3mm時﹐穿線孔直徑用Φ1.0mm,穿線孔做中心
(如圖C)。
3.異形孔小于3mm﹐穿線孔直徑用Φ0.5mm(細孔放電),非刀口線割孔作外面離邊4mm或做在孔中心﹐(如圖D)﹐刀口線割孔做在孔中心(如圖C)。
4.共用板(零)件線孔一般做在對產品尺寸無直接影響的板(零)件上﹐例復合模公母模共用時做在公模上。
模具专项作业方案

一、项目背景随着我国制造业的快速发展,模具作为制造业的重要基础,其质量和效率对产品的生产成本和品质有着直接的影响。
为了提高模具生产效率、降低生产成本,确保产品质量,特制定本模具专项作业方案。
二、项目目标1. 提高模具设计、制造、检验、装配等环节的效率;2. 降低模具生产成本,提高模具质量;3. 培养一批高素质的模具技术人才;4. 优化模具生产流程,实现信息化管理。
三、项目内容1. 模具设计优化(1)采用先进的三维CAD/CAM软件,提高设计效率;(2)优化模具结构,减少加工难度,提高模具寿命;(3)进行模具结构分析,确保模具强度和刚度满足使用要求;(4)优化模具材料选择,降低成本,提高模具性能。
2. 模具制造(1)采用先进的数控加工设备,提高加工精度和效率;(2)优化模具加工工艺,减少加工余量,提高加工质量;(3)加强模具加工过程中的质量控制,确保模具尺寸精度和表面质量;(4)对模具加工人员进行技能培训,提高加工技能水平。
3. 模具检验(1)建立完善的模具检验制度,确保模具质量;(2)采用高精度的检测设备,提高检验精度;(3)加强检验人员培训,提高检验技能水平;(4)对不合格的模具进行返工处理,确保模具质量。
4. 模具装配(1)优化模具装配工艺,提高装配效率;(2)采用先进的装配工具,提高装配精度;(3)加强装配过程中的质量控制,确保模具装配质量;(4)对装配人员进行技能培训,提高装配技能水平。
5. 信息化管理(1)建立模具生产管理系统,实现模具生产过程的信息化;(2)利用网络技术,实现模具生产数据的实时共享;(3)优化模具生产流程,提高生产效率;(4)加强信息化设备投入,提高模具生产信息化水平。
四、项目实施计划1. 组织筹备阶段(1个月)(1)成立模具专项作业项目组,明确项目组成员职责;(2)制定项目实施方案,明确项目目标、内容、实施计划等;(3)收集相关技术资料,进行项目前期调研。
2. 实施阶段(3个月)(1)开展模具设计优化、制造、检验、装配等工作;(2)进行信息化管理系统的建设;(3)对项目组成员进行技能培训。
模具设计与制造大作业

模具设计与制造大作业文件排版存档编号:[UYTR-OUPT28-KBNTL98-UYNN208]模具设计与制造大作业机械0804 胡川红图示连接板冲裁零件,材料为10钢,厚度为2mm,该零件年产量20万件,冲压设备初选为250kN开式压力机,要求:1.冲裁件工艺性分析。
2.选择模具的结构形式。
3.设计排样,画排样图。
4.进行必要的工艺计算。
冲压力、凸凹模间隙及尺寸等5.选择与确定模具的主要零部件的结构。
包括:定位、导向、卸料、支撑结构6.选择压力机,校核模具闭合高度及压力机有关参数。
7.绘制模具总图。
1.冲裁工艺分析冲裁件的工艺性是指冲裁件对冲裁工艺的适应性。
良好的冲裁工艺性是指能用普通冲裁方法,在模具寿命和生产效率较高、成本较低的条件下得到质量合格的冲裁件。
当然工艺性的好坏是相对的,它直接受到工厂的冲压技术水平和设备条件等因素的影响。
以上要求是确定冲压件的结构,形状,尺寸等对冲裁件工艺的实应性的主要因素。
根据这一要求对该零件进行工艺分析。
几何形状该冲裁件外形简单,形状规则,且成几何中心对称。
冲裁件的外形和内孔没有尖角。
冲孔的尺寸适宜。
冲孔的直径d 1.3t≥;==小于满足条件。
最小孔距、孔边距经应满足a2t≥,经计算零件的孔边距为5.75mm大于最小孔边距2t=2x2=4mm、孔距为40mm明显足够。
材料 10钢属于碳素钢,查附表可知其屈强比较小,延伸率较高,具有良好的冲压性能。
冲裁件的精度和断面粗糙度由于零件内外形尺寸均未注公差,属自由尺寸,可按IT14级确定工件尺寸公差,经查公差表得各尺寸公差分别为:零件的外形尺寸:00.5220- 00.4314-零件的空尺寸:0.3608.5+工艺性分析的结论:此零件适合冲裁2.模具结构形式的选择确定冲压工艺方案 确定方案就是确定冲压件的工艺路线,主要包括冲压工序数,工序的组合和顺序等。
确定合理的冲裁工艺方案应在不同的工艺分析进行全面的分析与研究,比较其综合的经济技术效果,选择一个合理的冲压工艺方案。
模具制作作业指导书
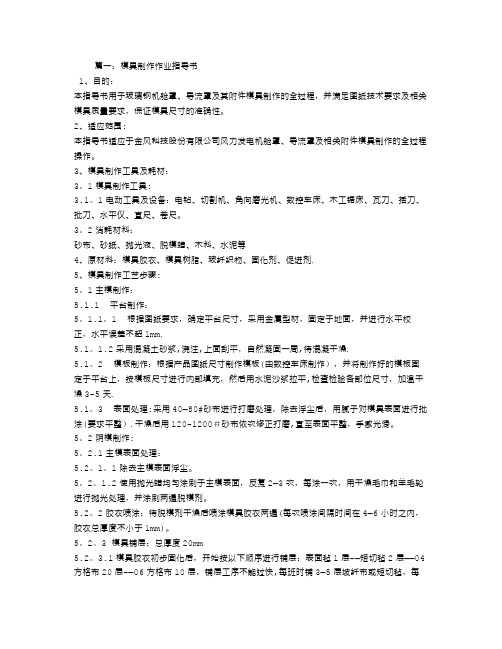
篇一:模具制作作业指导书1、目的:本指导书用于玻璃钢机舱罩、导流罩及其附件模具制作的全过程,并满足图纸技术要求及相关模具质量要求,保证模具尺寸的准确性。
2、适应范围:本指导书适应于金风科技股份有限公司风力发电机舱罩、导流罩及相关附件模具制作的全过程操作。
3、模具制作工具及耗材:3。
1模具制作工具:3.1。
1电动工具及设备:电钻、切割机、角向磨光机、数控车床、木工锯床、瓦刀、括刀、批刀、水平仪、直尺、卷尺。
3。
2消耗材料:砂布、砂纸、抛光液、脱模蜡、木料、水泥等4、原材料:模具胶衣、模具树脂、玻纤织物、固化剂、促进剂.5、模具制作工艺步骤:5。
1主模制作:5.1.1 平台制作:5。
1.1。
1 根据图纸要求,确定平台尺寸,采用金属型材,固定于地面,并进行水平校正,水平误差不超1mm.5.1。
1.2采用混凝土砂浆,浇注,上面刮平,自然凝固一周,待混凝干燥.5.1。
2 模板制作:根据产品图纸尺寸制作模板(由数控车床制作),并将制作好的模板固定于平台上,按模板尺寸进行内部填充,然后用水泥沙浆拉平,检查检验各部位尺寸,加温干燥3-5天.5.1。
3 表面处理:采用40—80#砂布进行打磨处理,除去浮尘后,用腻子对模具表面进行批涂(要求平整).干燥后用120-1200#砂布依次修正打磨,直至表面平整,手感光滑。
5。
2阴模制作:5。
2.1主模表面处理:5.2。
1。
1除去主模表面浮尘。
5。
2。
1.2使用抛光蜡均匀涂刷于主模表面,反复2—3次,每涂一次,用干燥毛巾和羊毛轮进行抛光处理,并涂刷两遍脱模剂。
5.2。
2胶衣喷涂:待脱模剂干燥后喷涂模具胶衣两遍(每次喷涂间隔时间在4—6小时之内,胶衣总厚度不小于1mm)。
5。
2。
3 模具铺层:总厚度20mm5.2。
3.1模具胶衣初步固化后,开始按以下顺序进行铺层:表面毡1层-—短切毡2层——04方格布20层-—06方格布10层,铺层工序不能过快,每班时铺3—5层坡纤布或短切毡,每铺一层玻纤织物涂一层胶,同时要用铁辊压平压实织物,排出气泡,使胶均匀,达到指定厚度后铺层结束。
模具制作作业指导书
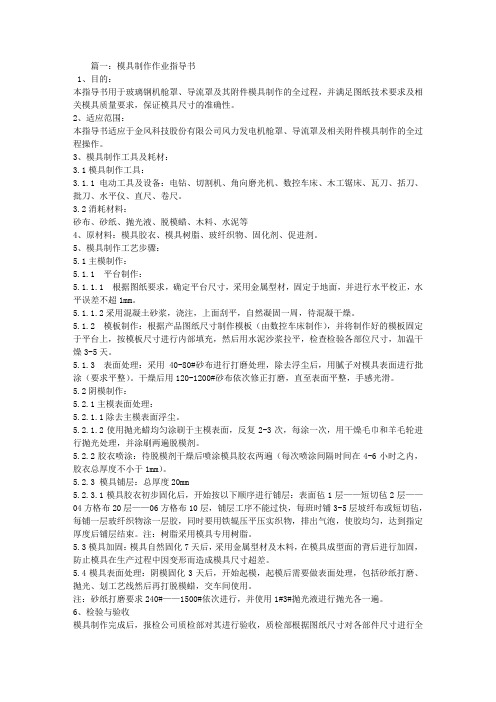
篇一:模具制作作业指导书1、目的:本指导书用于玻璃钢机舱罩、导流罩及其附件模具制作的全过程,并满足图纸技术要求及相关模具质量要求,保证模具尺寸的准确性。
2、适应范围:本指导书适应于金风科技股份有限公司风力发电机舱罩、导流罩及相关附件模具制作的全过程操作。
3、模具制作工具及耗材:3.1模具制作工具:3.1.1电动工具及设备:电钻、切割机、角向磨光机、数控车床、木工锯床、瓦刀、括刀、批刀、水平仪、直尺、卷尺。
3.2消耗材料:砂布、砂纸、抛光液、脱模蜡、木料、水泥等4、原材料:模具胶衣、模具树脂、玻纤织物、固化剂、促进剂。
5、模具制作工艺步骤:5.1主模制作:5.1.1 平台制作:5.1.1.1 根据图纸要求,确定平台尺寸,采用金属型材,固定于地面,并进行水平校正,水平误差不超1mm。
5.1.1.2采用混凝土砂浆,浇注,上面刮平,自然凝固一周,待混凝干燥。
5.1.2 模板制作:根据产品图纸尺寸制作模板(由数控车床制作),并将制作好的模板固定于平台上,按模板尺寸进行内部填充,然后用水泥沙浆拉平,检查检验各部位尺寸,加温干燥3-5天。
5.1.3 表面处理:采用40-80#砂布进行打磨处理,除去浮尘后,用腻子对模具表面进行批涂(要求平整)。
干燥后用120-1200#砂布依次修正打磨,直至表面平整,手感光滑。
5.2阴模制作:5.2.1主模表面处理:5.2.1.1除去主模表面浮尘。
5.2.1.2使用抛光蜡均匀涂刷于主模表面,反复2-3次,每涂一次,用干燥毛巾和羊毛轮进行抛光处理,并涂刷两遍脱模剂。
5.2.2胶衣喷涂:待脱模剂干燥后喷涂模具胶衣两遍(每次喷涂间隔时间在4-6小时之内,胶衣总厚度不小于1mm)。
5.2.3 模具铺层:总厚度20mm5.2.3.1模具胶衣初步固化后,开始按以下顺序进行铺层:表面毡1层——短切毡2层——04方格布20层——06方格布10层,铺层工序不能过快,每班时铺3-5层坡纤布或短切毡,每铺一层玻纤织物涂一层胶,同时要用铁辊压平压实织物,排出气泡,使胶均匀,达到指定厚度后铺层结束。
模具设计试产移转作业程序

模具设计试产移转作业程序1.准备工作:(1)设计部门的工程师应完成模具设计工作,并制定设计报告和设计图纸。
(2)准备试产材料和设备,确保试产过程中的材料和设备的供应。
2.设计评审:(1)将设计报告和设计图纸提交给工艺部门。
(2)工艺部门的工程师对设计进行评审,检查设计的合理性和生产的可行性,确保设计方案能够满足产品的质量要求和生产的效率要求。
3.工艺制定:(1)工艺部门根据设计评审结果,制定试产工艺方案。
(2)工艺部门将制定的试产工艺方案和设计图纸进行对比,确定是否需要对设计进行修改或调整。
4.工艺文件编制:(1)工艺部门将制定的试产工艺方案编制成工艺文件。
(2)工艺文件包括工艺路线、工艺参数、工艺操作规程等内容,确保试产过程中能够按照规定的工艺进行操作。
5.部门间协调:(1)设计部门和工艺部门进行沟通,确保设计方案和工艺方案的一致性。
(2)对于需要对设计进行修改或调整的情况,设计部门应根据工艺部门的要求进行相应的修改。
6.试产操作:(1)工艺部门按照制定的工艺方案,进行试产操作。
(2)工艺部门应记录试产过程中的关键参数和关键工艺,以便后续的生产过程参考。
7.试产评估:(1)工艺部门对试产效果进行评估,检查产品的质量和生产过程的效率。
(2)根据评估结果,对试产工艺方案进行修正和改进。
8.移交制造部门:(1)完成试产评估后,工艺部门将试产工艺方案和工艺文件移交给制造部门。
(2)制造部门根据工艺方案和工艺文件进行批量生产。
以上便是模具设计试产移转作业程序的一些步骤,通过严格的操作和评估,可以确保模具设计的试产工作能够成功移交给制造部门,实现产品的批量生产。
粉末冶金模具设计作业

中南大学粉末冶金研究院模具设计说明书班级:姓名:学号:指导老师:模具设计说明书一、工艺流程设计采用的零件材质为Fe-0.6C,压坯密度为6.4g/cm3,原料粉末的松装密度为2.5g/cm3,年产量为50万件。
用一般粉末冶金方法即可实现生产,其具体生产工艺流程如下:说明:由于零件为薄壁件,因此不予精整。
表面光洁度以及倒角要求由后续磨削加工达到。
二、压坯设计1.产品零件分析1)材质为铁基材料,非等高压坯,带一个外台阶和一个内台阶,共有3个螺栓孔。
2)为了简化模具结构,保证产品压坯顺利脱模,同时又由于螺栓孔不易在压制中成型,所以压坯设计中,该处设计为整体台阶,把螺栓孔除去,留在后续机加工中成形。
那么,该压坯大致为带一个外台阶和一个内台阶的压坯。
3)从零件精度分析,所给零件粗糙度要求为6.3及25较低,也无平行度、径向跳动、同轴度等形状精度的要求。
2. 压坯形状的设计:基本原则:尽可能使压坯形状与产品零件形状相同或相近——近净成形,同时考虑产品质量要求、压制成形过程要求及压模结构、零件强度等。
1)从裝粉和压制密度均匀性考虑:所给零件比较规则,无装粉困难。
2)从压坯脱模角度考虑:成品中没有不利于脱模的结构和因素。
3.压坯尺寸计算1)烧结压制中各参数选取如下:径向弹性后效:0.2%,轴向弹性后效:1.4%径向烧结收缩:0.5%,轴向烧结收缩:2%为满足表面粗糙度要求,在粗糙度要求为6.3的面预留0.05mm磨削加工余量2)压缩比:k=d压/d粉=6.4/2.5=2.563)压坯相对密度:d Fe=7.874g/cm3d C=2.25g/cm3则压坯理论密度dm=100/(99.4/7.874+0.6/2.25)=7.76g/cm3相对密度ρ=d压/dm=6.4/7.76=0.8254)轴向尺寸:压坯主体总高H1=10*(1-1.4%+2%)+0.05=10.11mm压坯台阶高度H2=5*(1-1.4%+2%)+0.05=5.08mm5)径向尺寸:长径D1=54*(1-0.2%+0.5%)=54.16mm短径D2=518(1-0.2%+0.5%)=51.15mm壁内径D3=28*(1-0.2%+0.5%)=28.08mm壁外径D4=35*(1-0.2%+0.5%)+2*0.05=35.21mm所设计压坯如图所示:三、压制方式1)零件高径比:H/D=10.11/54.162=0.187,零件总高径比很小,可考虑采用单向压制和非同时双向压制结合的压制方式。
模具设计与制作作业流程

模具设计与制作作业流程模具设计与制作作业流程是怎么样的?下面跟一起来瞧瞧吧!公司设计开发程序分为4个阶段:模具结构设计阶段模具制作阶段模具验收阶段模具移交阶段1.模具结构设计阶段(1)《模具开发申请单》经总经理批准后,研发部将申请单及相关技术文件及设计要求交模具部。
模具部经理对申请单、技术资料、相关要求进行确认。
(2)经模具部经理确认可行的,指定模具设计工程师进行模具设计。
模具设计工程师根据客户要求、产品图纸、设计要求设计模具结构。
并出具模具结构图。
(3)模具设计工程师设计出模具结构图后,交模具部经理审核。
经模具部经理审核的模具图纸,由模具设计工程师召集品管部、研发部进行模具结构评审。
评审的结果须形成《模具评审表》,对各部门在评审过程中提出的问题,模具部须制定出改善对策进行纠正,在现在技术能力、设备等因素无法解决的,则模具部经理报总工程师进行确认。
(4)模具评审须对以下内容进行评审:A.可维修性;B.可检测性;C.操作的简便性;D.操作的安全性;E.是否满足客户、设计的要求等。
2.模具制作阶段(1)模具组根据经评审及确认OK的模具图纸制作《模具制作进度表》,进度表包括以下内容:A.模具制作的各阶段。
B.各阶段的评审、验证和确认活动。
C.每个阶段的任务、责任人、进度要求。
D.物料采购的进度。
E.试样的进度。
F.其他必要的内容,如在本程序文件中没有确定的职责和权限以及接口管理的要求,都应在计划中确定下来。
(2)《模具制作进度表》经总工程师批准后,模具部交文控中心发行到责任部门、稽核中心、总经办。
在模具制作过程中,需对进度进行修改的,应按上述的要求重新审批后发放。
五金部做好各阶段的组织和协调工作。
除非有特别的规定,参与的各部门、人员之间以《内部联络单》的形式进行设计信息的沟通或以例会记录的形式进行沟通。
(3)模具组在进度表批准后的1日内对模具制作所需的物料状况进行确认,并制订《物料采购清单》交总工程师批准。
注塑模具设计作业流程规范

模具设计作业标准规范1﹑目的:确保模具设计规范化,统一化.能将设计意图正确的传达给制造部门.避免或减少失误。
2﹑范围:工程部设计课接收工程部产品组转交的图文件、样品等资料到图纸发行为止之阶段均属之。
3﹑权责:3.1 工程部设计课:负责模具开发设计及设计变更、2D/3D产品图面设计、3D建模、设计模具的组立图、3D拆模、绘制2D零件图、零件清单.3.2 模具课加工各组:加工各组的组长,在加工前需先审视加工图,若发现与原先检讨的不符合或有误,甚至不合理,需立即反应工程部设计课检讨查核后,方可继续加工。
4.作业内容4.1设计前置作业:4.1.1业务收到客人开模指令后。
开立【模具工令单】给总经理签核确认后,发给设计课开模。
模具设计课依据业务下达的工令单,开始模具设计作业4.1.2设计文员根据工令信息,将要开模的机种,品名,模号,穴数,模具大小及相应机台吨位,相关信息建立录入设计档案,以便后续查询。
4.1.2设计人员依据客人提供的产品图及相关工艺资料,做新产品开模检讨评估检讨,形成电子档的(DFM资料),内容包括如下:A开模穴数,材料,产品外观工艺要求B进浇口位置及数量C分模面位置D拔模分析E顶针位置F产品问题点设计做完DFM后,经过设计主管确认后,由设计主管将DFM电子档案发给客人讨论确认。
4.1.3治具模及自己试做模,由于是自行开模,不需要DFM给客人确认。
4.2设计作业4.2.1设计依据确认产品使用原料之收缩率范围,并参考类似产品实际收缩率后确定设计收4.2.2依据同客人检讨内容,参考相关技术数据,借鉴类似模具设计经验,进行模具组立图及模仁图设计绘制。
4.2.3客人对模具有专门要求的,按照客人要求设计制造。
如增加计数器,客人专用铭板, 客人指定的刻字内容,客人特定水嘴,客人指定刷特定颜色油漆等。
4.2.4设计人员完成模具组立图及零件图后,填写【新模设计检查表】复检一次设计图纸。
4.2.5模具图纸审核及发放4.2.5.1图档审核4.2.5.1.1模具组立图审核初审:设计师自身审核签名;复检:设计主管审核后签名 ;批准:总经理审核后签名;4.2.5.1.2散件图审核初审:设计师自身审核签名;复检:设计主管审核签名,文员复印下发;4.2.5.2图纸发放所有图纸在工程师签名后交工程文员加盖“受控”章后复印下发到模具课,模具课收到图纸后在【模具图纸移交单】签名确认收到。
模具设计与制造专业毕业大作业

模具设计与制造专业毕业大作业1.根据凹模零件图,编制零件机加工工艺路线和工艺卡片。
如图所示。
2.根据上模座零件图,编制零件机加工工艺路线和工艺卡片。
如图所示。
3.根据浇口套零件图,编制零件机加工工艺路线和工艺卡片。
如图3所示。
4.根据导套零件图,编制零件机加工工艺路线和工序卡片。
如图所示。
5.确定如图所示零件的数控铣削加工的工艺方案,并编制工艺卡片及数控加工程序。
6.塑料模具设计课题产品名称:三通管产品材料:PVC产品数量:大批量生产。
塑件尺寸:高100mm如图所示。
塑件重量:30克技术要求:按4级精度设计;塑件厚薄均匀,外侧表面光滑,不允许有浇口痕迹。
请按以下步骤进行设计(1)型腔布置、(2)确定分型面(3)选择设计浇注系统、(4)确定推出方式(5)模具结构形式及外形尺寸、(6)校核模具安装尺寸(7)计算成型零件尺寸、(8)绘制模具装配图。
完成时间:要求1~~2周时间内完成。
作业要求:交一份完整的设计说明书,一张模具装配图。
工件简图如图所示生产批量:大批量材料:20F料厚:0.8mm二、设计要求:1.冲压件的工艺分析根据工件图纸,认真分析该冲压件的形状、尺寸,精度要求和材料性能等因素是否符合冲压工艺的要求。
(5分)2.确定冲压件的最佳工艺方案通过对冲压件的工艺分析及必要的工艺计算,在分析冲压性质、冲压次数、冲压顺序和工序组合方式的基础上,提出各种可能的冲压工艺方案,并从多方面综合分析和比较,确定最佳工艺方案。
(10分)3.确定模具类型根据冲压件的生产批量,冲压件的形状,尺寸和精度等因素,确定模具的类型。
(5分)4.工艺尺寸计算(20分)1)排样设计与计算并画排样图2)冲压力、模具压力中心计算及压力设备的选择3)凸、凹模刃口尺寸的计算4)弹性元件的选取与计算5.选择与确定模具的主要零部件的结构、尺寸(20分)6.绘制模具总装图及零件图(40分)模具总装图中的非标准件,均需分别画出零件图。
7.编写技术文件作业要求:交一份完整的设计说明书,一张模具装配图。
东大17秋学期《冲压工艺与模具设计》在线作业3 免费答案
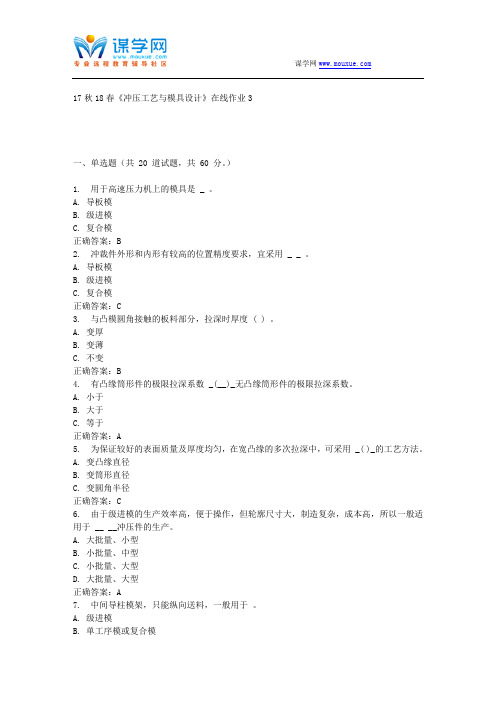
17秋18春《冲压工艺与模具设计》在线作业3一、单选题(共 20 道试题,共 60 分。
)1. 用于高速压力机上的模具是 _ 。
A. 导板模B. 级进模C. 复合模正确答案:B2. 冲裁件外形和内形有较高的位置精度要求,宜采用 _ _ 。
A. 导板模B. 级进模C. 复合模正确答案:C3. 与凸模圆角接触的板料部分,拉深时厚度 ( ) 。
A. 变厚B. 变薄C. 不变正确答案:B4. 有凸缘筒形件的极限拉深系数 _(__)_无凸缘筒形件的极限拉深系数。
A. 小于B. 大于C. 等于正确答案:A5. 为保证较好的表面质量及厚度均匀,在宽凸缘的多次拉深中,可采用 _( )_的工艺方法。
A. 变凸缘直径B. 变筒形直径C. 变圆角半径正确答案:C6. 由于级进模的生产效率高,便于操作,但轮廓尺寸大,制造复杂,成本高,所以一般适用于 __ __冲压件的生产。
A. 大批量、小型B. 小批量、中型C. 小批量、大型D. 大批量、大型正确答案:A7. 中间导柱模架,只能纵向送料,一般用于。
A. 级进模B. 单工序模或复合模C. 塑料模正确答案:B8. 凸模与凸模固定板之间采用 A 配合,装配后将凸模端面与固定板一起磨平。
A. H7/h6B. H7/r6C. H7/m6正确答案:A9. 需多次拉深的工件,在两次拉深间,许多情况下都不必进行 _(__)_。
从降低成本、提高生产率的角度出发,应尽量减少这个辅助工序。
A. 酸洗B. 热处理C. 去毛刺D. 润滑E. 校平正确答案:B10. 如果模具的压力中心不通过滑块的中心线,则冲压时滑块会承受偏心载荷,导致导轨和模具导向部分零件_ _ 。
A. 正常磨损B. 非正常磨损C. 初期磨损正确答案:B11. 冲制一工件,冲裁力为 F ,采用刚性卸料、下出件方式,则总压力为 _ _。
A. 冲裁力 + 卸料力B. 冲裁力 + 推料力C. 冲裁力 + 卸料力 + 推料力正确答案:B12. 拉深时,在板料的凸缘部分,因受 ( ) 作用而可能产生起皱现象。
东北大学《冲压工艺与模具设计》在线平时作业01

学期《冲压工艺与模具设计》在线平时作业1
为保证较好的表面质量及厚度均匀,在宽凸缘的多次拉深中,可采用 _( )_的工艺方法。
A:变凸缘直径
B:变筒形直径
C:变圆角半径
参考选项:C
当弯曲模间隙过大时,对U形弯曲件的不利影响是( ).
A:弯裂
B:翘曲
C:回弹
D:畸变
参考选项:C
拉深过程中,坯料的凸缘部分为 ( )。
A:传力区
B:变形区
C:非变形区
参考选项:B
下面三种弹性压料装置中, __(__)_的压料效果最好。
A:弹簧式压料装置
B:橡胶式压料装置
C:气垫式压料装置
参考选项:C
对角导柱模架上、下模座,其工作平面的横向尺寸一般大于纵向尺寸,常用于_ _ 。
A:横向送料的级进模
B:纵向送料的单工序模或复合模
C:纵向送料的级进模
D:横向送料的单工序模或复合模
参考选项:A
对 T 形件,为提高材料的利用率,应采用。
A:多排
B:直对排
C:斜对排
参考选项:C
在合理的冲裁间隙范围内,适当取大间隙有利于( )
1。
- 1、下载文档前请自行甄别文档内容的完整性,平台不提供额外的编辑、内容补充、找答案等附加服务。
- 2、"仅部分预览"的文档,不可在线预览部分如存在完整性等问题,可反馈申请退款(可完整预览的文档不适用该条件!)。
- 3、如文档侵犯您的权益,请联系客服反馈,我们会尽快为您处理(人工客服工作时间:9:00-18:30)。
按国家职业定义,模具设计是:从事企业模具的数字化设计,包括型腔模与冷冲模,在传统模具设计的基础上,充分应用数字化设计工具,提高模具设计质量,缩短模具设计周期的人员。
连续冲模设计技术(讲义一)一. 前言:冲压模具依构造可分为单工程模、复合模、连续模三大类。
前两类需较多人力不符经济效益,连续模可大量生产效率高。
同样,设计一套高速精密连续冲模,也要对你所生产的产品(包含所有用冲压加工出来的产品,富士康集团主要有端子、电脑机壳以及连接器上用的小五金及目前的手机零件等等)。
设计连续冲模需注意各模组之间的间距、零件加工精度、组立精度、配合精度与干涉问题,以达到连续模自动化大量生产的目的。
二. 单元化设计之概念:冲压模具整体构造可分成二大部分:(1).共通部分(2).依制品而变动的部分。
共通部分可加以标准化或规格化,依制品而变动的部分是难以规格化。
三. 模板之构成及规格:1. 模板之构成冲压模具之构成将依模具种类及构成及相异,有顺配置型构造与逆配置型构造二大类。
前者是最常使用的构造,後者构造主要用於引伸成形模具或配合特殊模具。
从事的主要工作包括:(1)数字化制图——将三维产品及模具模型转换为常规加工中用的二维工程图;(2)模具的数字化设计——根据产品模型与设计意图,建立相关的模具三维实体模型;(3)模具的数字化分析仿真——根据产品成形工艺条件,进行模具零件的结构分析、热分析、疲劳分析和模具的运动分析;(4)产品成形过程模拟——注塑成形、冲压成形;(5)定制适合本公司模具设计标准件及标准设计过程;(6)模具生产管理。
2. 模具之规格(1).模具尺寸与锁紧螺丝模板之尺寸应大於工作区域,并选择标准模板尺寸。
模板锁紧螺丝之位置配置与模具种类及模板尺寸有关。
其中单工程模具最常使用锁紧螺丝配置於四边角,最标准形式工作区域可广大使用。
长形之模具及连续模具最常使用锁紧螺丝配置於四边角及中间位置。
(2).模板之厚度模板之厚度选择与模具之构造、冲压加工种类、冲压加工加工力、冲压加工精度等有绝对关系。
依据理论计算决定模具之厚度是困难的,一般上系由经验求得,设计使用的模板厚度种类宜尽量少,配合模具高度及夹紧高度加以标准化以便利采购及库存管理。
四. 模板之设计:连续模具之主要模板有冲头固定板、压料板、母模板等等,其构造设计依冲压制品之精度、生产数量、模具之加工设备与加工方法、模具之维护保养方式等有下列三种形式:(1)整块式,(2)轭式,(3)镶入式。
1. 整块式整块式模板亦称为一体构造型,其加工形状必须是封闭的。
整块式模板主要用於简单结构或精度不高的模具,其加工方式以切削加工为主(不需热处理),采用热处理之模板必须再施行线切割加工或放电加工及研磨加工。
模板尺寸长(连续模具)之场合将采用两块或多块一体型并用之。
2. 轭式轭式模板之中央部加工成凹沟状以组装块状品。
其构造依应用要求,凹沟部可以其他模板构成之。
此轭式模板构造之优点有:沟部加工容易,沟部宽度可调整之,加工精度良好等。
但刚性低是其缺点。
轭式模板之设计注意事项如下:(1).轭板构部与块状部品之嵌合采中间配合或轻配合方式,如采强压配合将使轭板发生变化。
(2).轭板兼俱块状部品之保持功能,为承受块状部品之侧压及面压,必须具有足够的刚性。
还有为使轭板沟部与块状部品得到密著组合,其沟部角隅作成逃隙加工,如轭板沟部角隅不能作成逃隙加工,则块状部品须作成逃隙加工。
(3).块状部品之分割应同时考虑其内部之形状,基准面必须明确化。
为使冲压加工时不产生变形,亦要注意各个块状部品之形状。
(4).轭板组入许多件块状部品时,由於各块状部品之加工累积误差使得节距产生变动,解决对策是中间块状部品设计成可调整方式。
(5).块状部品采并排组合之模具构造,由於冲切加工时块状部品将承受侧压使各块状部品间产生间隙或造成块状部品之倾斜。
此现象是冲压尺寸不良、冲屑阻塞等冲压不良之重要原因,因此必须有充分的对策。
(6).轭板内块状部品之固定方法,依其大小及形状有下列五种:A.以锁紧螺丝固定,B.以键固定,C.以揳形键固定,D.以肩部固定,E.以上压件(如导料板)压紧固定。
3. 镶入式模板中加工圆形或方形之凹部,将块状部品镶合嵌入於模板中,此种模板称为镶入式构造,此构造之加工累积公差少、刚性高,分解及组立时之精度再现性良好。
由於具有容易机械加工、加工精度由工作机械决定、最後调整之工程少等优点,镶入式模板构造已成为精密冲压模具之主流,但其缺点是需要高精度的孔穴加工机。
连续冲压模具采用此模板构造时,为使模板具有高刚性要求,乃设计空站。
镶入式模板构造之注意事项如下所述:(1).嵌入孔穴之加工:模板之嵌入孔穴加工使用立式铣床(或治具铣床)、综合加工机、治具镗床、治具磨床、线割放电加工机等。
嵌入孔穴之加工基准,使用线割放电加工机时,为提高其加工精度乃进行二次或以上之线割加工。
(2).嵌入件之固定方法:嵌入件固定方法之决定因素有不变动其加工的精度、组立及分解之容易性、调整之可能性等。
嵌入件之固定方法有下列四种:A.以螺丝固定,B.以肩部固定,C.以趾块固定,D.其上部以板件压紧。
母模板之嵌入件固定方法亦有采用压入配合,此时应避免因加工热膨胀而产生的松弛结果,使用圆形模套嵌入件加工不规则孔穴时应设计回转防止方法。
(3).嵌入件组立及分解之考量:嵌入件及其孔穴加工精度要求高以进行组立作业。
为得到即使有稍微的尺寸误差亦能於组立时加以调整,宜事先考虑解决对策,嵌入件加工之具体考虑事项有下列五项:A.设有压入导入部,B.以隔片调整嵌入件之压入状态及正确位置,C嵌入件底面设有压出用孔穴,D.以螺丝锁紧时宜采用同一尺寸之螺丝,以利锁固及松开,E.为防止组立方向之失误,应设计防呆倒角加工。
连续冲模设计技术(讲义二)五. 单元化之设计:1. 模具对准单元模具对准单元亦称为模具刃件之对合引导装置。
为确实保持上模与下模之对准及缩短其准备时间,依制品精度及生产数量等条件要求,模具对准单元主要有下列五种:(1).无导引型:模具安装於冲床时直接进行其刃件之对合作业,不使用引导装置。
(2).外导引型:此种装置是最标准的构造,导引装置装设於上模座及下模座,不通过各模板,一般称为模座型。
(3).外导引与内导引并用型(一):此种装置是连续模具最常使用之构造,冲头固定板及压料板间装设内导引装置。
冲头与母模之对合利用固定销及外导引装置。
内导引装置之另一作用是防止压料板倾斜及保护细小冲头。
(4).外导引与内导引并用型(二):此种装置是高精密度高速连续模具之使用构造,内导引装置贯穿冲头固定板、压料板及母模固定板等等。
内导引装置本身亦有模具刃件对合及保护细小冲头作用。
外导引装置之主要作用是模具分解及安装于冲床时能得到滑顺目的。
(5).内导引型:此构造不使用外导引装置,内导引装置贯穿冲头固定板、压料板及母模固定板等等,正确地保持各块板之位置关系性以保护冲头。
2. 导注及导套单元模具之导引方式及配件有导注及导套单元之种类有两种:(A).外导引型(模座型或称主导引),(B).内导引型(或称辅助引)。
另行配合精密模具之要求,使用外导引与内导引并用型之需求性高。
(1).外导引型:一般上使用於不要求高精密度之模具,大多与模座构成一单元贩卖之,主要作用是模具安装於冲床时之刃件对合,几乎没有冲压加工中之动态精度保持效果。
(2).内导引型:由於模具加工机之进展,最近急速普及。
主要作用除了模具安装於冲床时之刃件对合外,亦有冲压加工中之动态精度保持效果。
(3).外导引与内导引并用型:一副模具同时使用外导引与内导引装置。
3. 冲头与母模单元(圆形)(1).冲头单元:圆形冲头单元依其形状(肩部型及平直型)、长度、维修之方便性,使用冲头单元宜与压料板导套单元配合。
(2).母模单元:圆形母模单元亦称为母模导套单元,其形式有整块式及分开式,依生产数量、使用寿命及制品或冲屑之处理性,母模单元之组合系列有:(A).使用模板直接加工母模形状,(B).具有二段斜角之逃隙部,(C).是否要使用背板,(D).不规则母模形状必须有回转防止设计。
4. 压料螺栓与弹簧单元(1).压料螺栓单元:压料板螺栓之种类有:(A).外螺丝型,(B).套筒型,(C).内螺丝型。
为保持压料板於指定位置平行状态,压料螺栓之停止方法(肩部接触部位):(A).模座凹穴承受面,(B).冲头固定板顶面,(C).冲头背板顶面。
(2).压料弹簧单元:可动式压料板压料弹簧单元可大致分为:(A).单独使用型,(B).与压料螺栓并用型选择压料弹簧单元时最好考虑下列要点再决定之:(A).确保弹簧之自由长度及必要的压缩量(压缩量大之弹簧宜置于压料板凹穴)。
(B).初期的弹簧压缩量(预压缩量) 或荷重之调整有无必要。
(C).考量模具组立或维护保养之容易性。
(D).考量与冲头或压料螺栓长度之关系。
(E).考量安全性(防止弹簧断裂时之飞出)。
5. 导引销单元(料条送料方向之定位)(1)..导引销单元:导引销之主要作用是连续冲压加工时得到正确的送料节距。
冲压模具用导引单元有间接型(导引销单独使用) 及直接型(导引销装设於冲头内部) 两种形式。
(2).导引销之组装方式与冲孔冲头有相同(装设於冲头固定板)。
利用弹簧将其受制於冲头固定板。
(3).导引销另外装设於压料板之形式,由于要求导引销突出於压料板之量达到一定及防止模具上升时之容易带上被加工材料,压料板之刚性及导引形式有必要注意之。
(4).导引销单元有直接型,其装设於冲头内,主要用于外形冲切(下料加工) 或引伸工程之切边加工,其位置定位系利用制品之孔及引伸部内径。
6. 导料单元(1).外形冲切(下料加工) 或连续冲压加工时,为使被加工材料之宽度方向受到导引及得到正确的送料节距,乃使用导料单元。
(2).料条宽度方向之导引装置,导引方式有:(A).固定板导引销型,(B).可动导引销型,(C).板隧道导引型(单块板),(D).板导引型(两块构成),(E).升料销导引型(有可动式、固定式及两者并用之。
(3).起始停止之导引装置,其形式有:(1).滑块式,(2).可动销式等两种,主要作用是材料置于模具之最初起始位置定位。
(4).送料停止装置,可正确地决定出送料节距,主要用於人手送料之场合,其形式有:(A).固定式停止销,(B).可动式停止销,(C).边切停止方式,(D).挂钩停止机构,(E).自动停止机构。
(5).侧推式导料机构,冲压加工时材料被压向一方,可防止材料因料条宽度与导料件宽度差所产生的蛇行现象。
(6).胚料位置定位导料机构,其形式有:(A).固定销导料型(利用胚料之外形),(B).固定销导料型(利用胚料之孔穴),(C).导料板(大件部品用),(D).导料板(一体形),(E).导料板(分割形)。