ATEX_VEGAMET_391_EN
Xtreme 104 900 MHz和2.4 GHz无线模组PC 104接口用户手册说明书

Xtreme/104 Radio Modems PC/104 Card Manual Xtreme/104 900 MHz and 2.4 GHz Radio ModemsPC/104 Interface User’s ManualContact Information:Connect Tech Inc.42 Arrow RoadGuelph, Ontario, Canada N1K 1S6Tel:519-836-1291 (International)800-426-8979 (Canada & USA)Fax: 519-836-4878Email:********************************************Web: CTIM-00032 Revision 0.01 March, 2007Xtreme/104 Radio Modem, Connect Tech Inc.One Year WarrantyConnect Tech Inc. provides a One-Year Warranty for all Xtreme/104 Radio Modem productsbuilt with Cirronet modules. Should this product, in Connect Tech Inc.'s opinion, fail to be ingood working order during the warranty period, Connect Tech Inc. will, at its option, repair orreplace this product at no charge, provided that the product has not been subjected to abuse,misuse, accident, disaster or non Connect Tech Inc. authorized modification or repair.You may obtain warranty service by delivering this product to an authorized Connect Tech Inc.business partner or to Connect Tech Inc. along with proof of purchase. Product returned toConnect Tech Inc. must be pre-authorized by Connect Tech Inc. with an RMA (Return MaterialAuthorization) number marked on the outside of the package and sent prepaid, insured andpackaged for safe shipment. Connect Tech Inc. will return this product by prepaid groundshipment service.Should the product prove to be irreparable, Connect Tech Inc. reserves the right to substitute anequivalent product if available.The above warranty is the only warranty authorized by Connect Tech Inc. for the Xtreme/104Radio Modems. Under no circumstances will Connect Tech Inc. be liable in any way for anydamages, including any lost profits, lost savings or other incidental or consequential damagesarising out of the use of, or inability to use, such product.Copyright NoticeThe information contained in this document is subject to change without notice. Connect TechInc. shall not be liable for errors contained herein or for incidental consequential damages inconnection with the furnishing, performance, or use of this material. This document containsproprietary information that is protected by copyright. All rights are reserved. No part of thisdocument may be photocopied, reproduced, or translated to another language without the priorwritten consent of Connect Tech, Inc.Copyright © 2007 by Connect Tech, Inc.Trademark AcknowledgmentConnect Tech Inc. acknowledges all trademarks, registered trademarks and/or copyrightsreferred to in this document as the property of their respective owners.Not listing all possible trademarks or copyright acknowledgments does not constitute a lack ofacknowledgment to the rightful owners of the trademarks and copyrights mentioned in thisdocument.2 Revision 0.01Xtreme/104 Radio Modem, Connect Tech Inc.Table of ContentsOne Year Warranty (2)Copyright Notice (2)Trademark Acknowledgment (2)Table of Contents (3)List of Figures (3)List of Tables (3)Customer Support Overview (4)Customer Support Overview (4)Contact Information (4)Introduction (5)Features (5)Radio Modem Modules (5)Xtreme/104 Base Card (5)Figure 1: Xtreme/104 Radio Modem Jumper Locations (6)Hardware Installation (6)Installing the PC/104 Radio Modem into your PC/104 Stack (6)Hardware Configuration (7)Memory Address and Interrupts Selection (7)I/O Address (7)IRQ Selection (8)IRQ Mode (8)Indicator LEDs (9)ACQ (DCD) (9)WAK (DTR) (9)Optional External LEDs (9)Operational Setup (10)Errata (11)List of FiguresFigure 1: Xtreme/104 Radio Modem Jumper Locations (6)List of TablesTable 1: Jumper J2-2 to J2-8 Functions (7)Table 2: J2 Jumpering Examples (8)Revision 0.01 3Xtreme/104 Radio Modem, Connect Tech Inc. Customer Support OverviewIf you experience difficulties after reading the manual and/or using the product, contact theConnect Tech reseller from which you purchased the product. In most cases the reseller can helpyou with product installation and difficulties.In the event that the reseller is unable to resolve your problem, our highly qualified support staffcan assist you. Our support section is available 24 hours a day, 7 days a week on our website at:/sub/support/support.asp. See the contact information section below formore information on how to contact us directly. Our technical support is always free. Contact InformationWe offer three ways for you to contact us:Email/InternetYou may contact us through the Internet. Our email and URL addresses on the Internet are:********************************************Note:Please go to the Download Zone or the Knowledge Database inthe Support Center on the Connect Tech website for productmanuals, installation guides, device driver software andtechnical tips.Submit your technical support questions to our customersupport engineers via the Support Center on the Connect Techwebsite.Telephone/FacsimileTechnical Support representatives are ready to answer your call Monday through Friday, from8:30 a.m. to 5:00 p.m. Eastern Standard Time. Our numbers for calls are:Telephone: 800-426-8979 (North America only)Telephone: 519-836-1291 (Live assistance available 8:30 a.m. to 5:00 p.m. EST, Monday toFriday)Facsimile: 519-836-4878 (on-line 24 hours)Mail/CourierYou may contact us by letter at:Connect Tech Inc.Technical Support42 Arrow RoadGuelph, OntarioCanada N1K 1S64 Revision 0.01Xtreme/104 Radio Modem, Connect Tech Inc.IntroductionConnect Tech’s PC/104 Radio Modems, available with Cirronet’s WIT910, WIT2450 orWIT2410 roaming transceiver modules, offer a conveinient, reliable method to introducewireless communications into your PC/104 application.Fully PC/104 2.5 compliant, this card installs into an available PC/104 position in your stack tocommunicate up to 20 miles away (“line of sight” only), depending on model and antennaconfiguration.FeaturesRadio Modem Modules•Frequency hopping spread spectrum technology•900 MHz or 2.4 GHz , incorporating Cirronet’s WIT910, WIT2410 or WIT2450 frequency hopping transceiver modules•Radio modem operating ranges of up to 20 miles (900 MHz model, with appropriate antennas in a “line of sight” implementation)•Low power consumption (can be powered via the PC/104 bus)•Store and forward repeating while operating as a node (WIT910)•License-free operation•Immunity to jamming and multipath fading, even in noisy environments•Available with roaming capability (2.4 GHz)•FCC certified•Data speeds between 86.4 Kbps (900 MHz) and 230.4 Kbps (2.4 GHz)•Point-to-point and point-to-multipoint network deployments•Operating temperature range of 0˚C to 70˚CXtreme/104 Base Card•Jumper selectable I/O addresses and interrupts•I/O address ranges from 0x000 to 0x7F0 (jumper selectable)•RTS/CTS hardware flow control•Jumper selectable IRQ interrupts 3, 4, 6, 7, 9, 10, 11, 12, 14, 15•Requires no additional drivers, appears as COM port to your operating systemRevision 0.01 5Xtreme/104 Radio Modem, Connect Tech Inc.6 Revision 0.01Figure 1: Xtreme/104 Radio Modem Jumper LocationsHardware InstallationInstalling the PC/104 Radio Modem into your PC/104 StackBefore you place your Xtreme/104 Radio Modem into your PC/104 stack, take a minute to ensure that your package includes the required components that should have shipped with your PC/104 Radio Modem.• One unit• One CD containing software and documentation • One cable (optional) • One antenna (optional)If any of these components is missing, contact Connect Tech (see Contact Details) or your reseller.This card can be installed into any PC/104 stack and is fully PC/104 2.5 compliant.Xtreme/104 Radio Modem, Connect Tech Inc.Revision 0.01 7Hardware ConfigurationMemory Address and Interrupts SelectionI/O AddressJ2 positions 2 through 8:Jumper block J2, positions 2 through 8, define the I/O Base Address setting for the UART. The board decodes 16 consecutive I/O addresses starting at the Base address. Each of the jumper positions corresponds to one bit of the I/O Address. If a jumper is installed (“On”), then the corresponding bit equals 1, otherwise that bit equals zero. (Please see Figure 1) for jumper locations.)Table 1: Jumper J2-2 to J2-8 FunctionsJ2 position Corresponding I/O Address Bit 2 I/O address bit 4 3 I/O address bit 5 4 I/O address bit 6 5 I/O address bit 7 6 I/O address bit 8 7 I/O address bit 9 8I/O address bit 10J2 position 1:Position J2-1 enables the control of the CFG (Configuration) signal on the Radio Modem. When the CFG signal is asserted, the Radio Modem is placed into its Configuration Mode. This is an alternate method of placing the Radio Modem in this state.When this position is not jumpered (“Off”):• The control of the Radio Modem CFG signal is disabled.When this position is jumpered (“On”):● The control of the Radio Modem CFG signal is enabled, and the operation of the CFGsignal is controlled by I/O writes to I/O Base Address + 0x08 [See Note 1 below].o Writing 0x00 disables the CFG mode, writing 0x01 enables the CFG mode. Onlybit-0 of the written byte has significance, all other bits are ignored. (The CFG mode is Disabled at power-up).Notes:[1] See Errata.[2] The lower 3 bits of the I/O address (A2, A1, A0), access theRegisters of the UART.[3] The Base I/O Address is always on a boundary of 16, [4] The total I/O setting range possible is 0x000 to 0x7F0. .[5] Settings below 0x100 should be used with caution, since theremay be conflicts with system devices.[6] Some systems may not support an I/O Base setting greaterthan 0x3F8.Xtreme/104 Radio Modem, Connect Tech Inc.8 Revision 0.01Table 2: J2 Jumpering ExamplesJ2 PositionsUART I/O AddressCFG I/O Address8 7 6 5 4 3 2 1Off On On Off Off Off Off Off 0x300 (01100000uuu) ---Off On On Off Off Off Off On 0x300 (01100000uuu) 0x308 (01100001xxx) [Note 1]Off On On Off Off Off On Off 0x310 (01100010uuu) ---Off On On Off Off Off On On 0x310 (01100010uuu) 0x318 (01100011xxx) [Note 1] On Off On Off On On Off On 0x560 (10101100uuu) 0x568 (10101101xxx) [Note 1]Off On On On On On On Off 0x3F0 (01111110uuu) ---Off On On On On On On On 0x3F0 (01111110uuu)0x3F8 (01111111xxx) [Note 1](Please see Figure 1 for jumper locations)Notes:[1] See Errata sectionIRQ SelectionThe IRQ number selection is controlled by jumper block J1. Jumpers 1 through 10 correspond to the IRQ numbers listed in Table 2 below. Only one jumper should be installed.Table 3: IRQ SelectionJ1 Position IRQ# 1 3 2 4 3 6 4 7 5 9 6 10 7 11 8 12 9 14 1015IRQ ModeJ2-9 (when jumpered or “On”) enables the IRQ to be shared with other cards/devices in the system.J2-10 (when jumpered or “On”) provides a 1K pull-down resistor on the selected IRQ signal. This is used in conjunction with the Shared IRQ mode. Only one 1K resistor is allowed in the system per Shared IRQ. Only one card in the system should provide this pull-down.Note:The IRQ Sharing mechanism is implemented as described in the PC/104 Bus Specification V2.5.(Please see Figure 1 for jumper locations.)Xtreme/104 Radio Modem, Connect Tech Inc.Revision 0.01 9Indicator LEDsThere are two red LEDs located on the PC/104 board. They serve to indicate whether the Xtreme/104 Radio Modem has aquired a lock (ACQ) and whether it is awake (WAK).ACQ (DCD)This LED indicates that the Xtreme/104 Radio Modem has acquired (ACQ) a lock with the hopping pattern. This applies to modems that are configured to be Remotes. A Base RadioModem would have this LED on at all times. The signal which drives this LED is also the DCD input on the serial port. When DCD is on, the Radio Modem has acquired the lock.WAK (DTR)This LED indicates that the Xtreme/104 Radio Modem is awake (WAK), or not sleeping. The serial port DTR signal is driving both this LED and the Sleep Signal of the Radio Modem. When DTR is on, the Radio Modem is awake.Optional External LEDsThe Xtreme/104 Radio Modem includes the option to connect the LED drivers to LEDs located external to board. Connector P4 provides this ability. (See Figure 2). The pinout for this connector is provided below.Table 4: Connector P4 Pinout for External LEDs PinFunction 1 ACQ 2 Gnd 3 WAK 4GndFigure 2: P4 Connector Option for External LEDsXtreme/104 Radio Modem, Connect Tech Inc.10 Revision 0.01Operational SetupA minimum operational setup for the Xtreme/104 Radio Modem card must include an antenna connected to the Radio Modem module at each end of the communications link.The following illustration demonstrates a typical lab or prototype setup using two possiblecable/antenna styles (only one antenna is needed at each end). The mounting surface for the antenna end of the patch cable could be the housing of the PC/104 stack or some other mounting surface. A metallic surface is preferred, but not necessary. In most situations a vertical orientation of the antenna works best, but this can be influenced by the environmental factors listed below.A field setup or a final application setup may vary greatly from application to application. Environmental factors play a big role in the effective deployment of wireless communication equipment. The following items need to be considered.• Desired range• Obstacles between the stations (hills, buildings, trees, etc) • RF power output settings of the modules • Attenuation of the interconnecting RF cables • RF gain of the antennas• Prevailing weather conditions• Multi-path (multiple RF pathways) effectsIn many circumstances experiments need to be conducted on the field setup to determine the effectiveness of the setup.Connect Tech’s partner, Cirronet, can offer application assistance with the choice of RF cabling and antennas and with the environmental considerations for a particular field installation. Contact Cirronet to ensure your unique application requirements are met.Xtreme/104 Radio Modem, Connect Tech Inc.ErrataCFG Mode OperationProblem DescriptionRevision “B” boards exhibit a problem when using the Radio Modem CFG Signal control feature (enabled with J2-position-1). When using an I/O address of Base+0x08, the data byte written also gets transmitted by the UART.Solution:The issue will be resolved in revision “C” of the board.Resolution:Instead of using an I/O address of Base+0x08, use Base+0x0F. The data value used will also bewritten into the UART Scratch-Pad register, but this does not affect the normal operation of theUART.Revision 0.01 11。
Omega Bio-tek Mag-Bind

1. Read the manufacturer’s instruction manual for the magnetic separation device, if provided.
3. Shake or vortex the Mag-Bind® Total Pure NGS to resuspend any particles that may have settled. Allow Mag-Bind® Total Pure NGS to come to room temperature before use.
2. Place the 96-well PCR plate on the bench and measure the volume of the PCR reaction. Determine the volume of Mag-Bind® Total Pure NGS that will be added to the reaction. If the reaction volume will exceed 200 µL transfer to a microtiter plate for processing. Note: PCR reactions >20 µL will need to be transferred to a processing plate.
magnetic bead volumes desired • Magnetic separation device (Recommend AlpAqua Cat# 001322). For elution volumes
Emotia Xtreme MX 用户手册说明书

• Genlock — Genlock capabilities allow for the integration of the scan converted images into a professional broadcast environment. Genlocking provides for seamless, vertical interval switching of these converted high resolution sources, and other video sources. Front panel access to horizontal phasing and subcarrier phasing control is provided for easy adjustment.
The Emotia Xtreme MX is housed in a rack-mountable metal enclosure and includes an internal 100-240 volt switch mode power supply.
An example of an Emotia Xtreme MX application with video input from a workstation is shown in the diagram below.
莫加 UC 系列产品说明书

Entry-level Arm-based 64-bit ComputersDual-core, 2-GB RAMCompact Dual-core, 2-GB RAM Built-in LTEValue-added Arm-based 64-bit ComputersQuad-core, 4-GB RAMQuad-core, 4-GB RAM5G/CAN/serial IsolationBuilt-in LTEMoxa Industrial LinuxMoxa's Debian-based industrial-grade stable Linux distribution for long-term projectsFeatures and Benefits5Debian-based distribution that can use all standard Debian packages5Developed as per IEC 62443-4-1 and compliant with IEC 62443-4-2 industrialcybersecurity standards (Moxa Industrial Linux 3 Secure)5Long-term support until 2027 for Moxa Industrial Linux 1 and 2031 for MoxaIndustrial Linux 35Wireless connection management utility with automatic network keep alive andfailover5Ready-to-use APIs and library to ease access to hardware and I/O interfaces5Crash-free robust file system5Over-the air (OTA) software updatesWireless-ready Arm-based 32-bit Computers Built-in cellular or Wi-Fi module, RF type approvals, and carrier approvalsBuilt-in LTE Cat.1Built-in LTECat.1 and Wi-FiBuilt-in LTECat.1 and Wi-FiBuilt-in LTECat.4 with Wi-Fi expansion1. Wireless module is built-in. Refer to the Wireless Connection and Expansion Modules section for details.2. Wireless module must be purchased separately. Refer to the Wireless Connection and Expansion Modules section for details.1 mPCIe for cellular/Wi-Fi1 mPCIe forcellular/Wi-Fi1 mPCIe forcellular/Wi-Fi1 mPCIe forcellular/Wi-Fi1 mPCIe for cellular 1mPCIe for Wi-Fi1 mPCIe forcellular/Wi-FiArm-based 32-bit Computers With Wireless Options Flexibility to add cellular or Wi-Fi capability when needed1. Wireless module must be purchased separately. Refer to the Wireless Connection and Expansion Modules section for details.1 LAN,1 serial2 LAN 2 LAN,2 serial2 LAN,2 serial2 LAN,4 serial2 LAN,4 serial2 LAN,1 serial2 LAN,2 serial3 LAN,8 serialStandard Arm-based 32-bit Computers Low power consumption and small form factorWireless Connectivity and Expansion Modules* Details of cellular and Wi-Fi support with a list of wireless accessory models* Antennas must be purchased separatelyLast updated: Aug. 15, 2023. All specifications are subject to change without notice.。
Eaton Memera全金属消费者单元和保护设备说明书

EatonMemera full metal consumer units and protective devices Consumer unit solutionsto meet the requirements of the18th edition wiring regulations2EATON Memera full metal consumer units and protective devices - August 2020Memera full metal consumer unitsand protective devicesBS7671:2018Tested to BS EN 61439-3Fully complies with BS7671:2018(IET wiring Regulations 18th Edition)Contents1. Product overview (3)2. Memera full metal consumer unit range (6)3. Circuit protection devices and accessories (7)4. Consumer unit accessory selection (8)5. T echnical data (9)1 Product overview100A type A RCCB’s• Three new versions of the Memera 10, 14 and16 way dual RCCB boards are now also availablepre fitted with 100A type A RCCB’s for usewhere the installation is required to have type ARCD protection.Memera full metal consumer unitsThe Eaton range of full metal consumer units provide asuite of products to meet the requirements of BS7671:201818th Edition IET wiring regulations.Todays 18th edition consumer units incorporate anenclosure manufactured from non-combustible material,i.e. a full metal enclosure.Eaton consumer unit features• Full compliance with BS EN 61439-3.• All metal enclosure to meet requirements of BS7671regulation 421.1.201.• Sturdy steel enclosure with ample cable entry knockoutsto accommodate cable entry from top, bottom or rearface of the enclosure.• Multiple large apertures in rear face of enclosure to allowflexible cable entry from the rear, with dual knockouts toaccommodate both round glands as well as trunking ontop/bottom faces.• “Snap - able” busbars enabling easy on-site configuration.• Dual RCCB units come with three Neutral bars asstandard for High Integrity configuration.• Comprehensive label kit to complete the installation.• Polyester powder coat paint finish which complieswith industry standards for low smoke density, flamepropagation and toxic fume emission. RAL 9010 (Purewhite).• Available in single rail and dual rail surface and flushmounting variants up to a maximum of 38 outgoing ways.Arc Fault Detection Device (AFDD) solutionsSurge Protection Device (SPD) solutions• A 280V 20kA 2 pole type 2 Surge Protection Device isalso available as a kit to enable an Eaton SPD to be fittedinto any consumer unit even when fitted with AFDD’s.Installation kits are detailed in section 5.Command and control devices• The full range of Eaton modular command and controldevices such as transformers, timers, contactors andrelays can be installed in any unused ways. For detailssee main Single phase product catalogue.• Bus bars and connection links are available to simplify theinstallation of Eaton’s AFDD’s within Memera consumerunits as detailed in section 5.• Additional accessory connection kits are also available toprovide internal connectivity for consumer units equippedwith AFDD’s as well as MCB’s, RCBO’s and SPD’s.3EATONMemera full metal consumer units and protective devices - August 20204.1Circuit Protection devicesThe Eaton Memera range of consumer units can be equipped with the standard range of EAD 6kA MCB’s with ratings up to 63A at 6KA in both B and C curve, along with a full range of single module 6kA RCBO’s rated up to 45A in B and C curve with both AC and A current type characteristics.A new addition to the circuit protection portfolio is Eaton’s range of AFDD’s rated up to 40A can now also be accommodated using the additional accessory kits detailed further in this guide.In addition to the protection devices above the wide range of Eaton DIN rail modular accessories including SPD’s, timers and contactors etc., can also be accommodated within the consumer unit enclosure due to the flexible nature of the design. Fitting of AFDD’s into consumer unitsIn order to comply with the requirements of BS7671 for the inclusion of AFDD’s when deemed necessary, Eaton can provide a range of AFDD installation accessory kits to simplify the fitting of these devices into our Memera metal consumer units along with other protective devices as required.The kits include a special 3-4 way AFDD 2 pole busbar kit as well as a number of other interconnection accessory kits that may be required depending upon the consumer unit configuration selected and the devices to be fitted.Full details can be found in section 4 & 5 of this brochure.Requirements for Surge Protection devicesBS7671: 2018 also now places a greater emphasis on Chapter 44 – Protection against voltage disturbances and electromagnetic disturbances.Such disturbances can be temporary as a result of system faults in the LV or HV supply network, or perhaps transient overvoltages of atmospheric origin or else due to switching.The need for the inclusion of a surge protection device in an installation is dependent upon the perceived risk to an installation. The regulations in BS7671 provide detailed guidance on the application of Surge Protection devices and the methodologies relating to risk management and assessment.To make it simple for Installers, Eaton has introduced an SPD kit which includes a standard 2 pole 2 module Type 2 SPD rated at 280 V 20kA complete with the necessary interconnections.Full details can be found in section 5 of this brochure.EAS2PT2SPD - SPD KitEAS2PT2SPD kit includes the SPD and the the 3 pre made connectionsrequired to facilitate the installation of the 2pole SPD into any standardIsolator controlled Memera Consumer unit.EarthNeutralLiveFor SPDoperatinginstructionsconsult literaturesupplied withSPCT2-280/25 EATON Memera full metal consumer units and protective devices - August 20202 Memera metal consumer unit rangeModules Eaton list numberIsolator controlled RCCB controlled Split load Dual RCD Dual tariff Dimensions (mm)Modules Eaton list numberIsolator controlled RCCB controlled Split load Dual RCD Dual tariff Cover dimensions (mm)Back boxdimensions (mm)Full metal consumer unit rangeSurface mountedFlush mounted6EATON Memera full metal consumer units and protective devices - August 20203 Consumer unit circuit protection Devices & AccessoriesEaton Memera MCB’sEaton arc fault detection devices - T ype AEaton Memera RCBO’sTrip curve BTrip curve BAC type trip curve BA type trip curve BConsumer unit SPD and AFDD accessory kitsTrip curve CTrip curve CAC type trip curve CA type trip curve Cote: N Also available as type AC and type A with short time delay.7EATON Memera full metal consumer units and protective devices - August 20208EATON Memera full metal consumer units and protective devices - August 20204 Consumer unit accessory selection tables5 T echnical dataFitting of Consumer unit SPD with and without AFDD’sEarthNeutralLiveFor SPD operating instructionsconsult literature supplied with SPCT2-280/2Neutral NeutralEarthEarthLiveLive EAS2PT2SPD - SPD KitExample EAS10S - EAS10F1615141312LN 11109876543L N 21P DRCD AFDD 3AFDD 2AFDD 1lx AFDD 3AFDD 2AFDD 1S P DS P D2625242322212019181716151413AFDD 7AFDD 6AFDD 5AFDD 4S P D14131211109876543L N 211817161514131211109876543L N 21AFDD 3AFDD 2AFDD 1S P D AFDD 4S P DAFDD 4AFDD 3AFDD 2AFDD 1xAFDD 3AFDD 2AFDD 1S P DS P D14131211109876543LN 211817161514131211109876543LN 211211109876543L N 21AFDD 1S P D xAFDD 3AFDD 2S P DAFDD 4AFDD 3AFDD 2AFDD 1AFDD 3AFDD 2AFDD 1S P D AFDD 4S P D AFDD 4AFDD 3AFDD 2AFDD 1EASAFDDBB3S P D14131211109876543LN 211817161514131211109876543L N 2188171615141312LN 11109876543L N 21EASAFDDBB3AFDD 3AFDD 2AFDD 1S P D AFDD 4S P D AFDD 4AFDD 3AFDD 2AFDD 1x AFDD 3AFDD 2AFDD 1S P D 1817161514131211109876543L N 213L N 211716151413S P DS P DS P DAFDD 4S P DAFDD 4AFDD 3AFDD 2AFDD 1AFDD 3AFDD 2AFDD 1S P DAFDD 4S P DAFDD 4AFDD 3AFDD 2AFDD 1xAFDD 3AFDD 2AFDD 1S P DEASSPCONSPD – SPD/AFDD KitEASRCDCONSPD – SPD/AFDD KitFor use with EAS18 - 20S/EAS18 - 20FFor use with EAS26S/EAS26Fand Split Load BoardsFitting instructions for SPD with AFDD to specific Memera boards see overleaf9EATON Memera full metal consumer units and protective devices - August 2020Fitting of consumer unit with AFDD’sEASSPCON - AFDD Single Pole T erminalEASAFDDBB3 - AFDD BusbarEASDPCON - AFDD Double Pole T erminalEASAFDDTB - AFDD Busbar Stab ShieldNeutralLive X3 AFFD’s - Busbar connected directly to isolatorORX4 AFFD’s - Busbar connected to isolator via cablesFacility to fit mcb’s withAFDD’s X6 AFFD’s - Busbar connected directly to isolatorShield all un-used AFDD busbar stabsNote: Unless otherwise specified, all internal cabling supplied in the consumer unit is left unmodofied.*2 - Remove x2 (blue) pre-installed isolator to neutral terminal block cables and x1 (brown) isolator to lower busbar cable181716151413121110987654321L N555121110987654321L N AFDD 5DD 6321L N321L N 2625242322212019181716151413EASAFDDBB3AFDD 1AFDD 1AFDD 2AFDD 1xAFDD 316151413121110L N 987654321LNAFDD 2AFDD 1x AFDD 3AFDD 4AFDD 3121110987654321L N1211109262524232216151413121110L N 987654321L N AFDD 8AFDD 7xAFDD 3AFDD 4AFDD 3AFDD 2AFDD 11413121110987654321L N26252423222625242322AFDD 3AFDD 2AFDD 1RCDAFDD 8AFDD 7AFDD 2AFDD 1x AFDD 3AFDD 4AFDD 3AFDD 2AFDD 11413121110987654321L N181716151413121110987654321L N121110987654321L NAFDD 4AFDD 3AFDD 2AFDD 1RCD AFDD 6AFDD 3AFDD 2AFDD 1AFDD 4AFDD 2AFDD 1AFDD 2AFDD 1xAFDD 3AFDD 4AFDD 3AFDD 4AFDD 3AFDD 2AFDD 11413121110987654321L N181716151413121110987654321L NAFDD 3AFDD 2AFDD 1AFDD 4AFDD 2AFDD 1AFDD 2AFDD 1x AFDD 3AFDD 4AFDD 3AFDD 4AFDD 3AFDD 2AFDD 1Isolator Controlled -Split Load1413121110987654321L N151413121110987654321L NAFDD 5AFDD 4AFDD 6AFDD 4AFDD 3AFDD 2AFDD 1AFDD 3AFDD 2AFDD 1AFDD 3AFDD 2AFDD 1AFDD 4AFDD 2AFDD 1AFDD 2AFDD 1x AFDD 3AFDD 4AFDD 3AFDD 4AFDD 3AFDD 2AFDD 1Isolator controlledSplit load10EATON Memera full metal consumer units and protective devices - August 2020Miniature circuit breakers (MCBs)Eaton’s range of 6kA high performance MCBs meet the latest UK and European standards IEC/EN 60898, with ratings up to 63A in both B & C curve characteristics. Features include:• Box clamp barrier to prevent incorrect cable insertion• Positive contact indication Residual current circuitbreakers - with overloadprotection (RCBOs)Eaton’s range of 6kA, 30mA highperformance compact RCBOs meetthe latest UK and European standardsIEC/EN 61009, combining ResidualCurrent Circuit Breaker protectionwith integral overload protection inone compact modular device. Ratingsavailable from 6A to 45A in both B &C curve characteristics.Features include:• Compact modular design, only102mm tall, giving enhanced wiringspace• Single module width with solidneutral• Box clamp barrier to preventincorrect cable insertion• Positive contact indication• Devices available as both AC and Acurrent typesArc Fault DetectionDevices (AFDD +)Eaton’s range of AFDD’s combine thefunctionality of an MCB, RCD andAFDD in one package designed inaccordance to IEC/EN 62606 & IEC/EN 61009. Ratings are available up to40A with B & C curve characteristicsand 10mA and 30mA sensitivity.Devices are available in current typesA, AC and short time delayed type A.Features include:• Variable installation of N on eitherleft or right• Tripped indication : MCB, RCCB orAFDD with LED indication of arcfaults• Permanent self monitoring includingover heating and over voltage• Rated breaking capacity up to 10kA(6kA above 25A)Consumer unitsThe 2019 Memera full metal consumer units range fully complies with BS EN 61439-3 and meetsthe requirements of BS7671:2018 clause 421.1.201 i.e. non-combustible enclosure.In accordance with BS7671, installation of these units should use proper materials and follow good workmanship and industry practices. The correct use of grommets, grommet strip or glands should be considered to minimise the risk of damage arising from mechanical stress or damage to wiring whereit enters the metal enclosure. In addition, the horizontal top surface of the consumer unit if readily accessible shall provide a degree of protection of at least IPXXD or IP4X. T erminal capacity and torque settingsNote: A ll terminals should be tightened to the recommended torque values below using an appropriate torque driver.• Device torque cable capacity• Isolator 2.5 – 5.0 Nm 2.5 – 50 mm2• RCCB 2.0 – 2.4 Nm 1.5 – 35 mm2• MCB 2.0 – 2.4 Nm 1 – 25 mm2• RCBO Line 2.0 – 2.5 Nm Load 1.2 -1.5 Nm 1 -16 mm2• AFDD - 2.0 – 2.4 Nm 1.5 – 25 mm2• SPD - 2.0 – 2.4 Nm 1.5 – 35 mm2• Neutral / Earth bars 2.0 Nm 1 -16 mm2• Other devices: see appropriate installation instructions11 EATON Memera full metal consumer units and protective devices - August 2020At Eaton, we’re energized by the challenge of powering a world that demands more. With over 100 years experience in electrical power management, we have the expertise to see beyond today. From ground breaking products to turnkey design and engineering services, critical industries around the globe count on Eaton. We power businesses with reliable, efficient and safe electrical power management solutions. Combined with our personal service, support and bold thinking, we are answering tomorrow’s needs today. Follow the charge with Eaton. Visit /uk.Eaton Electric Limited252 Bath RoadSloughSL1 4DXCustomer Support CentreTel: +44 (0)8700 545 333Fax: +44 (0)8700 540 333email:**********************© 2020 Eaton CorporationAll Rights ReservedPrinted in UKPublication No. BR012018ENEAN Code 9010August 2020。
NI 9220 16 AI, ±10 V, 16 Bit, 100 kS s ch Simultan
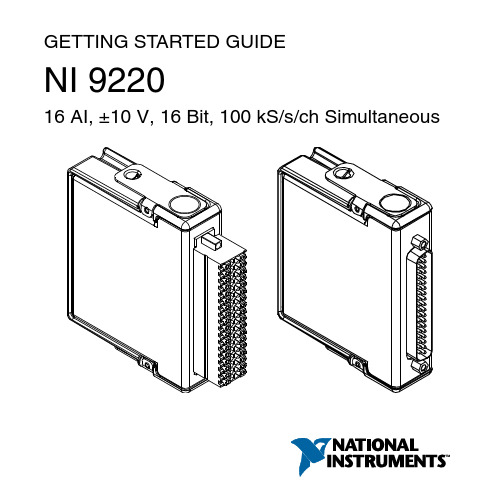
GETTING STARTED GUIDENI 922016 AI, ±10 V, 16 Bit, 100 kS/s/ch SimultaneousThis document explains how to connect to the NI 9220. In this document, the NI 9220 with spring terminal and the NI 9220 with DSUB are referred to inclusively as the NI 9220.Note Before you begin, complete the software andhardware installation procedures in your chassisdocumentation.Note The guidelines in this document are specific tothe NI 9220. The other components in the system mightnot meet the same safety ratings. Refer to thedocumentation for each component in the system todetermine the safety and EMC ratings for the entiresystem.Caution Electrostatic Discharge (ESD) can damagethe NI 9220 with spring terminal. To prevent damage,use industry-standard ESD prevention measures duringinstallation, maintenance, and operation.Safety GuidelinesOperate the NI 9220 only as described in this document.2| | NI 9220 Getting Started GuideCaution Do not operate the NI 9220 in a manner notspecified in this document. Product misuse can result ina hazard. You can compromise the safety protectionbuilt into the product if the product is damaged in anyway. If the product is damaged, return it to NI forrepair.Hazardous Voltage This icon denotes a warningadvising you to take precautions to avoid electricalshock with the NI 9220 with spring terminal. Safety VoltagesConnect only voltages that are within the following limits:NI 9220 with Spring Terminal Isolation Voltages Channel-to-channel NoneChannel-to-earth groundContinuous250 Vrms,Measurement Category IIWithstand up to 4,000 m 3,000 Vrms, verified by a 5 s dielectric withstand testNI 9220 Getting Started Guide| © National Instruments| 3Measurement Category II is for measurements performed on circuits directly connected to the electrical distribution system. This category refers to local-level electrical distribution, such as that provided by a standard wall outlet, for example, 115 V for U.S. or 230 V for Europe.Caution Do not connect the NI 9220 with springterminal to signals or use for measurements withinMeasurement Categories III or IV.NI 9220 with DSUB Safety VoltagesChannel-to-COM±30 V maximumIsolationChannel-to-COM NoneChannel-to-earth groundContinuous60 VDC, MeasurementCategory IWithstand up to 2,000 m 1,000 Vrms, verified by a 5 s dielectric withstand testMeasurement Category I is for measurements performed on circuits not directly connected to the electrical distribution system 4| | NI 9220 Getting Started Guidereferred to as MAINS voltage. MAINS is a hazardous live electrical supply system that powers equipment. This category is for measurements of voltages from specially protected secondary circuits. Such voltage measurements include signal levels, special equipment, limited-energy parts of equipment, circuits powered by regulated low-voltage sources, and electronics.Caution Do not connect the NI 9220 with DSUB tosignals or use for measurements within MeasurementCategories II, III, or IV.Safety Guidelines for Hazardous VoltagesYou can connect hazardous voltages only to theNI 9220 with spring terminal. Do not connect hazardous voltages to the NI 9220 with DSUB.If hazardous voltages are connected to the device, take the following precautions. A hazardous voltage is a voltage greater than 42.4 Vpk voltage or 60 VDC to earth ground.Caution Ensure that hazardous voltage wiring isperformed only by qualified personnel adhering to localelectrical standards.NI 9220 Getting Started Guide| © National Instruments| 5Caution Do not mix hazardous voltage circuits andhuman-accessible circuits on the same module.Caution Ensure that devices and circuits connected tothe module are properly insulated from human contact.Caution When module terminals are hazardousvoltage LIVE (>42.4 Vpk/60 VDC), you must ensurethat devices and circuits connected to the module areproperly insulated from human contact. You must usethe NI 9940 connector backshell kit to ensure that theterminals are not accessible.Safety Guidelines for Hazardous LocationsThe NI 9220 is suitable for use in Class I, Division 2, Groups A, B, C, D, T4 hazardous locations; Class I, Zone 2, AEx nA IIC T4 and Ex nA IIC T4 hazardous locations; and nonhazardous locations only. Follow these guidelines if you are installing the NI 9220 in a potentially explosive environment. Not following these guidelines may result in serious injury or death.Caution Do not disconnect I/O-side wires orconnectors unless power has been switched off or thearea is known to be nonhazardous.6| | NI 9220 Getting Started GuideCaution Do not remove modules unless power hasbeen switched off or the area is known to benonhazardous.Caution Substitution of components may impairsuitability for Class I, Division 2.Caution For Division 2 and Zone 2 applications,install the system in an enclosure rated to at least IP54as defined by IEC/EN 60079-15.Caution For Division 2 and Zone 2 applications,connected signals must be within the following limits. Capacitance0.2 µF maximumSpecial Conditions for Hazardous Locations Use in Europe and InternationallyThe NI 9220 has been evaluated as Ex nA IIC T4 Gc equipment under DEMKO 12 ATEX 1202658X and is IECEx UL 14.0089X certified. Each NI 9220 is marked II 3G and is suitable for use in Zone 2 hazardous locations, in ambient temperatures of -40 °C ≤ Ta ≤ 70 °C. If you are using the NI 9220 in Gas Group IIC hazardous locations, you must use the device in an NI chassis thatNI 9220 Getting Started Guide| © National Instruments| 7has been evaluated as Ex nC IIC T4, Ex IIC T4, Ex nA IIC T4, or Ex nL IIC T4 equipment.Caution You must make sure that transientdisturbances do not exceed 140% of the rated voltage.Caution The system shall only be used in an area ofnot more than Pollution Degree 2, as defined inIEC/EN 60664-1.Caution The system shall be mounted in anATEX/IECEx-certified enclosure with a minimumingress protection rating of at least IP54 as defined inIEC/EN 60079-15.Caution The enclosure must have a door or coveraccessible only by the use of a tool.Electromagnetic Compatibility Guidelines This product was tested and complies with the regulatory requirements and limits for electromagnetic compatibility (EMC) stated in the product specifications. These requirements and limits provide reasonable protection against harmful interference 8| | NI 9220 Getting Started Guidewhen the product is operated in the intended operational electromagnetic environment.This product is intended for use in industrial locations. However, harmful interference may occur in some installations, when the product is connected to a peripheral device or test object, or if the product is used in residential or commercial areas. To minimize interference with radio and television reception and prevent unacceptable performance degradation, install and use this product in strict accordance with the instructions in the product documentation.Furthermore, any changes or modifications to the product not expressly approved by National Instruments could void your authority to operate it under your local regulatory rules.Caution To ensure the specified EMC performance ofthe NI 9220 with DSUB, the length of all I/O cablesmust be no longer than 30 m (100 ft).Caution To ensure the specified EMC performance,operate this product only with shielded cables andaccessories. Do not use unshielded cables oraccessories unless they are installed in a shieldedenclosure with properly designed and shielded input/NI 9220 Getting Started Guide| © National Instruments| 9output ports and connected to the product using ashielded cable. If unshielded cables or accessories arenot properly installed and shielded, the EMCspecifications for the product are no longer guaranteed. Special Conditions for Marine ApplicationsSome products are Lloyd’s Register (LR) Type Approved for marine (shipboard) applications. To verify Lloyd’s Register certification for a product, visit /certification and search for the LR certificate, or look for the Lloyd’s Register mark on the product.Caution In order to meet the EMC requirements formarine applications, install the product in a shieldedenclosure with shielded and/or filtered power andinput/output ports. In addition, take precautions whendesigning, selecting, and installing measurement probesand cables to ensure that the desired EMC performanceis attained.10| | NI 9220 Getting Started GuidePreparing the EnvironmentEnsure that the environment in which you are using the NI 9220 meets the following specifications.Operating temperature(IEC 60068-2-1, IEC 60068-2-2)-40 °C to 70 °COperating humidity (IEC 60068-2-78)10% RH to 90% RH, noncondensingPollution Degree2Maximum altitudeFor NI 9220 withspring terminal4,000 mFor NI 9220 withDSUB2,000 mIndoor use only.Note Refer to the device datasheet on /manualsfor complete specifications.NI 9220 Getting Started Guide| © National Instruments| 11NI 9220 Pinout12| | NI 9220 Getting Started GuideGrounded Differential ConnectionsNI 9220 Getting Started Guide| © National Instruments| 13Floating Differential ConnectionsConnect the negative lead to COM through a 1 MΩ resistor to keep the signal source within the common-mode voltage range. The NI 9220 does not read data accurately if the signal source is outside of the common-mode voltage range.14| | NI 9220 Getting Started GuideSingle-Ended ConnectionsConnect the ground signal to COM to keep the signal source within the common-mode voltage range.NI 9220 Connection Guidelines•Make sure that devices you connect to the NI 9220 are compatible with the module specifications.•You must use 2-wire ferrules to create a secure connection when connecting more than one wire to a single terminal on the NI 9220 with spring terminal.NI 9220 Getting Started Guide| © National Instruments| 15•For the NI 9220 with spring terminal, push the wire into the terminal when using a solid wire or a stranded wire with aferrule.•For the NI 9220 with spring terminal, open the terminal by pressing the push button when using stranded wire without a ferrule.High-Vibration Application ConnectionsIf your application is subject to high vibration, NI recommends that you use the NI 9940 backshell kit to protect connections to the NI 9220 with spring terminal.Overvoltage ProtectionThe NI 9220 provides overvoltage protection for each channel.Note Refer to the device datasheet on /manualsfor more information about overvoltage protection.16| | NI 9220 Getting Started GuideWhere to Go NextLocated at /manuals NI 9220 Getting Started Guide | © National Instruments | 17Worldwide Support and ServicesThe NI website is your complete resource for technical support. At /support, you have access to everything from troubleshooting and application development self-help resources to email and phone assistance from NI Application Engineers. Visit /services for NI Factory Installation Services, repairs, extended warranty, and other services.Visit /register to register your NI product. Product registration facilitates technical support and ensures that you receive important information updates from NI.A Declaration of Conformity (DoC) is our claim of compliance with the Council of the European Communities using the manufacturer’s declaration of conformity. This system affords the user protection for electromagnetic compatibility (EMC) and product safety. You can obtain the DoC for your product by visiting /certification. If your product supports calibration, you can obtain the calibration certificate for your product at /calibration.18| | NI 9220 Getting Started GuideNI corporate headquarters is located at11500 North Mopac Expressway, Austin, Texas, 78759-3504. NI also has offices located around the world. For telephone support in the United States, create your service request at /support or dial 1 866 ASK MYNI (275 6964). For telephone support outside the United States, visit the Worldwide Offices section of /niglobal to access the branch office websites, which provide up-to-date contact information, support phone numbers, email addresses, and current events.NI 9220 Getting Started Guide| © National Instruments| 19Refer to the NI Trademarks and Logo Guidelines at /trademarks for information on NI trademarks. Other product and company names mentioned herein are trademarks or trade names of their respective companies. For patents covering NI products/technology, refer to the appropriate location: Help»Patents in your software, the patents.txt file on your media, or the National Instruments Patent Notice at /patents. Y ou can find information about end-user license agreements (EULAs) and third-party legal notices in the readme file for your NI product. Refer to the Export Compliance Information at /legal/export-compliance for the NI global trade compliance policy and how to obtain relevant HTS codes, ECCNs, and other import/ export data. NI MAKES NO EXPRESS OR IMPLIED WARRANTIES AS TO THE ACCURACY OF THE INFORMATION CONTAINED HEREIN AND SHALL NOT BE LIABLE FOR ANY ERRORS. U.S. Government Customers: The data contained in this manual was developed at private expense and is subject to the applicable limited rights and restricted data rights as set forth in FAR 52.227-14, DFAR 252.227-7014, and DFAR 252.227-7015.© 2017 National Instruments. All rights reserved.378023A-01Jan17。
EFLOW用户指南 Release 12.3说明书

Path
:
Online
: True
RestartNeeded : False
2. Set execution policy and verify.
Set-ExecutionPolicy -ExecutionPolicy AllSigned -Force
Get-ExecutionPolicy AllSigned
5
EFLOW User's Guide, Release 12.3
3. Download and install EFLOW.
$msiPath = $([io.Path]::Combine($env:TEMP, 'AzureIoTEdge.msi')) $ProgressPreference = 'SilentlyContinue' Invoke-WebRequest "https:∕∕aka.ms∕AzEFLOWMSI_1_4_LTS_X64" -OutFile $msiPath
▶ The Windows host OS with virtualization enabled ▶ A Linux virtual machine ▶ IoT Edge Runtime ▶ IoT Edge Modules, or otherwise any docker-compatible containerized application (runs on
Agilent SureSelectXT Mouse All Exon Kit 数据手册

Introducing the SureSelect XT Mouse All Exon Kit — the fi rst NGS target enrichment system to cover the mouse exome. Mouse geneticists can now access the industry-leading SureSelect XT Target Enrichment System to generate mouse sequence data faster and more cost-effectively on the SOLiD, Illumina, and 454 NGS platforms.Developed in collaboration with leading mouse geneticists, the SureSelect XT Mouse All Exon Kit delivers a complete view of the mouse exome. The capture is 49.6 Mb and covers 221,784 exons within 24,306 genes. The content is based on the current UCSC mm9 mouse genome build and a BED fi le with exon and gene annotation is available on the Agilent eArray website.• C omplete Mouse exome coverage — 49.6 Mb capture spanning 221,784 exonsand 24,306 genes• E xcellent coverage uniformity, on-target specifi city, and SNP detection and accuracy• Fully optimized for SOLiD, Illumina, and 454 sequencingSureSelect XT Mouse All Exon KitAgilent SureSelect Target Enrichment System12%10%10%10%8%6%4%1%0%102030405060708090100110120130140150160170180190200Read Depth Distribution for SureSelect XT Mouse All Exon KitRead DepthC u m u l a t i v e R e a d s R e a d sFigure 1. Read depth distribution plot for C3H mouse genomic DNA enriched with the SureSelect XT Mouse All Exon Kit (49.6 Mb capture) and sequenced on an Illumina GAIIx. 5.2 Gb of sequence was obtained from a single 2x76bp lane and the percentage of on-target reads was 69 percent. 98 percent of bases were covered at 1X or greater and average read depth was 54X. 84 percent of targeted bases were covered at 20X or greater, enabling high-confi dence SNP calling at those loci.SureSelect XT Mouse All Exon Kit Specifi cationsSureSelect XT Mouse All Exon Kit – Ordering InformationMouse genome/ exome source content Total capture size Number of genes coveredNumber of exons Average exon size Median exons per geneAverage number of exons per geneMaximum exons in a geneUCSC mm9/ NCBI build 37 (July 2007)49.6 Mb24,306221,784182 bp58347/genomics/sureselectFor research use only. Not for use with diagnostics procedures.© Agilent Technologies, Inc., 2011 Published in USA, January 12, 2011Publication Number 5990-7235ENFigure 2. SNP data generated after enrichment with the SureSelect XT Mouse All Exon Kit and sequencing was highly sensitive and SNP calls were highly concordant with the Perlegen Mouse SNP data set. 165,249 SNPs from the Perlegen data set were assayed in gDNA samples from C3H and DBA mice, twowidely-used strains. NGS libraries for these strains were prepared and enriched using the SureSelect XT Mouse All Exon Kit and 5.2 Gb of sequence was generated on an Illumina GAIIx. Over 84 percent of the capture was sequenced at a depth of 20X or greater, enabling high-confi dence SNP calling. a) Sensitivity of SNPdetection relative to the Perlegen Mouse SNP dataset was very high with the SureSelect XTMouse All Exon Kit / Illumina GAIIx platform, with 99 percent ofreference SNPs detected for the C3H and DBA samples. Variant SNPs were also detected at high rates (99 percent) for both the C3H and DBA samples. b) Of the SNPs detected, concordance with the Perlegen Mouse SNP data set for both the C3H ad DBA samples was 98 percent for the variants and 95 percent overall.0%10%20%30%40%50%60%70%80%90%100%SNP Detection Sensitivity vs Perlegen Mouse DataSureSelect XT Mouse All Exon KitGT is RefGT is variant HOM0%10%20%30%40%50%60%70%80%90%100%SNP Concordance vs Perlegen Mouse DataSureSelect XT Mouse All Exon KitVariant ConcordanceOverall ConcordanceReactions/KitSureSelect XT MouseAll Exon KitIllumina Option CodeSOLiD Option CodeSureSelect Mouse All Exon KitRoche 454 OptionCode5G7550A 001002G7500A 00310G7550B 001002G7500B 00325G7550C 001002G7500C 00350G7550D 001002G7500D 003100G7550E 001002G7500E 003250G7550F 001002G7500F 003500G7550G 001002G7500G 0031000G7550H 001002G7500H 0032000G7550J 001002G7500J 0035000G7550K 001002G7500K 00310000G7550L001002G7500L003A BG7550 includes capture baits and all reagents for gDNA preparation, library preparation, and target enrichment.G7500 includes capture baits and reagents for target enrichment. The Roche Rapid Library Prep Kit (available from Roche) is also required.。
VEGAPULS60系列雷达物位计选型手册

RadarContinuous level measurementOverview Page 16 VEGAPULS series 60 Page 18 Antenna cover Page 36AL-EN 11516Radar – VEGAPULSVEGAPULSNon-contact measurement under all process conditions Measuring principleExtremely short microwave impulses are emitted by the antenna system to the measured product, reflected by the product surface and received again by the antenna system. The time from emission to reception of the signals is proportional to the level in the vessel. A special time spreading procedure enables the reliable and precise measurement of the extremely short signal running times. The radar sensors are available indifferent C and K-band frequency ranges, this ensures the optimum solution for the different applications. The proven ECHOFOX signal processing analysis the reflections in the vessel based on long-standing experience and detects the level signal reliably. The adaptation to the respective application is really simple through the selection of the application parameters.ApplicationsLevel in liquidsTwo different emitting frequencies are available for these applications.The compact, high frequency K-band sensors VEGAPULS 61, 62 and 63 are particularly suitable for applications where high accuracy is required. Since even with small antenna sizes, an excellent signal focusing is reached, hence mounting on small mounting openingsis possible. The low frequency C-band sensors VEGAPULS 65 and 66can penetrate foam and strong condensation and are thus particularly suitable for arduous process conditions. Unaffected by steam, gas composition, pressure and temperature changes, radar sensors detect the product surface of different products reliably and ensure thus an optimum process.Level in bulk solidsThe high frequency sensors VEGAPULS 67 and 68 in K-bandtechnology are used for these applications. Thanks to the very good focusing of the signals, the level is detected reliably independent of silo installations or buildup on the vessel wall. A high sensitivity electronics optimized to the requirements of the bulk solids measurement, enables a reliable level measurement of different products up to a distance of 75 m. The measuring principle is unaffected by strong dust generation,filling noise, air turbulences by pneumatic filling and temperature fluctuations and ensures a reliable and maintenance-free operation of the systems. The application area covers applications in the food processing industry and the plastic processing up to the steel generati-on and mineral rock processing.AL-ENOverviewAL-EN117Radar – VEGAPULS18Radar – VEGAPULS WL611 Mounting strap2 Combi compression flangeYou will find further process fittings and options under /configurator .You will find further drawings and tables under /downloads.You will find mounting accessory, welded sockets and housing overviews in chapter "Accessory".AL-EN VEGAPULS WL 61Radar sensor for continuous level measurement of water and waste waterApplication areaThe VEGAPULS WL 61 is the ideal sensor for all applications in water and sewage water applications. It is particularly suitable for use in water processing, pump stations as well as overflow basins, for flow measurement in open flumes and gauge monitoring. The VEGAPULS WL 61 is an economical solution through versatile and simple mounting options. The flood-proof IP 68 housing ensures a maintenance-free permanent operation.Your benefit- Maintenance-free operation through non-contact measuring principle - High plant availability, because wear and maintenance-free- Exact measuring results independent of product, process and ambient conditionsTechnical data Measuring range: up to 15 m Process fitting: thread G1½ mounting strap compression flanges from DN 80, 3" Process temperature: -40 … +80 °C Process pressure: -1 … +2 bar (-100 … +200 kPa) Accuracy: +/- 2 mmApprovalXX without ....................................................................................................................................................................AX ATEX II 3G Ex nA IIC T6 Gc X ..............................................................................................................................CX ATEX II 1G, 1/2G, 2G Ex ia IIC T6 Ga, Ga/Gb, Gb ...............................................................................................Cable lengthfrom >6 m, per additional 100 mm cable of PURAL-EN119Radar – VEGAPULS WL61201 Version with encapsulated antenna system2 Version with plastic horn antenna3 Mounting strap4 Adapter flangeRadar – VEGAPULS 61You will find further process fittings and options under /configurator .You will find further drawings and tables under /downloads.You will find mounting accessory, welded sockets and housing overviews in chapter "Accessory".AL-EN VEGAPULS 61Radar sensor for continuous level measurement of liquidsApplication areaThe VEGAPULS 61 is a radar sensor for continuous level measurement of liquids under simple process conditions. The VEGAPULS 61 is an economical solution through its simple and versatile mounting possibilities. The encapsulated antenna system ensures a maintenance-free operation.Your benefit- Maintenance-free operation through non-contact measuring principle - High plant availability, because wear and maintenance-free - Exact measuring results independent of process conditionsTechnical data Measuring range: up to 35 m Process fitting: thread G1½, 1½ NPT mounting strap compression flanges from DN 80, 3" adapter flanges from DN 100, 4" Process temperature: -40 … +80 °C Process pressure: -1 … +3 bar (-100 … +300 kPa) Accuracy: +/- 2 mm SIL qualification: optionally up to SIL2ApprovalXX without ..................................................................................................................................................................... XM Ship approval ........................................................................................................................................................... CX ATEX II 1G, 1/2G, 2G Ex ia IIC T6 .......................................................................................................................... CA ATEX II 1G, 1/2G, 2G Ex ia IIC T6 + WHG ............................................................................................................. CM ATEX II 1G, 1/2G, 2G Ex ia IIC T6 + Ship approval ................................................................................................ CI IEC Ex ia IIC T6 ....................................................................................................................................................... DX ATEX II 1/2G, 2G Ex d ia IIC T5/T6 ........................................................................................................................AL-EN121Radar – VEGAPULS 6122Radar – VEGAPULS 621 Threaded version2 Threaded version withtemperature adapter up to +250 °C 3 Flange versionAntenna-øLength Beam angle40 mm 100 mm 20°48 mm 120 mm 15°75 mm 216 mm 10°95 mm430 mm 8°245 mm (parabolic)138 mm3°You will find further process fittings and options under /configurator .You will find further drawings and tables under /downloads.You will find mounting accessory, welded sockets and housing overviews in chapter "Accessory".AL-EN VEGAPULS 62Radar sensor for continuous level measurement of liquidsApplication areaThe VEGAPULS 62 is a universally implementable radar sensor for continuous level measurement of liquids. It is suitable for level measurement in storagecontainers, reactors and process vessels, even under difficult process conditions. With its various antenna versions and materials, VEGAPULS 62 is the optimal solution for almost all applications and processes. Its wide temperature and pressure range makes project planning simple.Your benefit- Maintenance-free operation through non-contact measuring principle - High plant availability, because wear and maintenance-free- Exact measuring results independent of pressure, temperature, gas and steamTechnical data Measuring range: up to 35 m Process fitting: thread from G1½, 1½ NPT flanges from DN 50, 2" Process temperature: -196 … +450 °C Process pressure: -1 … +160 bar (-100 … +16000 kPa) Measuring accuracy: +/- 2 mm SIL qualification: optionally up to SIL2ApprovalXX without .....................................................................................................................................................................XM Ship approval ..........................................................................................................................................................CX ATEX II 1G, 1/2G, 2G Ex ia IIC T6 .........................................................................................................................CA ATEX II 1G, 1/2G, 2G Ex ia IIC T6 + WHG ............................................................................................................CM ATEX II 1G, 1/2G, 2G Ex ia IIC T6 + Ship approval ...............................................................................................CI IEC Ex ia IIC T6 ......................................................................................................................................................DX ATEX II 1/2G, 2G Ex d ia IIC T5/T6 ........................................................................................................................DI IEC Ex d ia IIC T6 ...................................................................................................................................................CK IEC Ex ia IIC Ga,Ga/Gb,Gb + Ex t IIIC T...Da,Da/Db,Db .......................................................................................DK IEC Ex d IIC Ga/Gb,Gb + Ex t IIIC T... Da,Da/Db,Db .............................................................................................Length standpipe / Total length316L (200-5850 mm) per 100 mmAL-EN123Radar – VEGAPULS 6224Radar – VEGAPULS 631 Flange version DN 502 Flange version DN 803 Clamp version 2"You will find further process fittings and options under /configurator .You will find further drawings and tables under /downloads.You will find mounting accessory, welded sockets and housing overviews in chapter "Accessory".AL-EN VEGAPULS 63Radar sensor for continuous level measurement of liquidsApplication areaThe VEGAPULS 63 is a radar sensor for continuous level measurement ofaggressive liquids or with hygienic requirements. It is suitable for applications in storage tanks, process vessels, dosing vessels and reactors. The encapsulated antenna system of VEGAPULS 63 protects the VEGAPULS 63 against pollution and ensures a maintenance-free permanent operation. The front-flush mounting ensures an optimum cleanability even with high hygienic requirements.Your benefit- Maintenance-free operation through non-contact measuring principle - High plant availability, because wear and maintenance-free - Exact measuring results independent of process conditionsTechnical data Measuring range: up to 35 m Process fitting: hygienic fittings boltings flanges from DN 50, 2" Process temperature: -196 … +200 °C Process pressure: -1 … +16 bar (-100 … +1600 kPa) Accuracy: +/- 2 mm SIL qualification: optionally up to SIL21ApprovalXX without ......................................................................................................................................................................XM Ship approval ...........................................................................................................................................................CX ATEX II 1G, 1/2G, 2G Ex ia IIC T6 ...........................................................................................................................CA ATEX II 1G, 1/2G, 2G Ex ia IIC T6 + WHG .............................................................................................................CM ATEX II 1G, 1/2G, 2G Ex ia IIC T6 + Ship approval ................................................................................................CI IEC Ex ia IIC T6 .......................................................................................................................................................DX ATEX II 1/2G, 2G Ex d ia IIC T5/T6 .........................................................................................................................DI IEC Ex d ia IIC T6 ....................................................................................................................................................CK IEC Ex ia IIC Ga,Ga/Gb,Gb + Ex t IIIC T...Da,Da/Db,Db .........................................................................................DK IEC Ex d IIC Ga/Gb,Gb + Ex t IIIC T... Da,Da/Db,Db ..............................................................................................RX IEC Ex t IIIC T... Da,Da/Db,Db .................................................................................................................................1 Threaded version G1½2 Flange version DN 80You will find further process fittings and options under /configurator .You will find further drawings and tables under /downloads.You will find mounting accessory, welded sockets and housing overviews in chapter "Accessory".VEGAPULS 65Radar sensor for continuous level measurement of liquidsApplication areaThe VEGAPULS 65 is a radar sensor for continuous measurement of liquids under simple process conditions. It is particularly suitable for level measurement invessels with small process fittings and under simple process conditions. The slim rod antenna enables the installation in small vessel openings.Your benefit- Maintenance-free operation through non-contact measuring principle - High plant availability, because wear and maintenance-free - Reliable measurement independent of process conditionsTechnical data Measuring range: up to 35 m Process fitting: thread from G1½, 1½ NPT flanges from DN 50, 2" Process temperature: -40 … +150 °C Process pressure: -1 … +16 bar (-100 … +1600 kPa) Accuracy: +/- 8 mm SIL qualification: optionally up to SIL21ApprovalXX without ....................................................................................................................................................................XM Ship approval ..........................................................................................................................................................CX ATEX II 1G, 1/2G, 2G Ex ia IIC T6 .........................................................................................................................CA ATEX II 1G, 1/2G, 2G Ex ia IIC T6 + WHG ............................................................................................................CM ATEX II 1G, 1/2G, 2G Ex ia IIC T6 + Ship approval ...............................................................................................CI IEC Ex ia IIC T6 ......................................................................................................................................................DX ATEX II 1/2G, 2G Ex d ia IIC T5/T6 .......................................................................................................................1 Version with horn antenna ø 145 mm2 Version with standpipe antennaAntenna-øLength Beam angle75 mm 75 mm 38°96 mm 113 mm 30°145 mm 205 mm 20°195 mm 296 mm 17°240 mm380 mm14°You will find further process fittings and options under /configurator .You will find further drawings and tables under /downloads.You will find mounting accessory, welded sockets and housing overviews in chapter "Accessory".VEGAPULS 66Radar sensor for continuous level measurement of liquidsApplication areaThe VEGAPULS 66 is a sensor for continuous level measurement of liquids under arduous process conditions. It is suitable for applications in storage tanks, process vessels or standpipes. The VEGAPULS 66 can be used universally thanks to different antenna versions.Your benefit- Maintenance-free operation through non-contact measuring principle - High plant availability, because wear and maintenance-free - Reliable measurement independent of process conditionsTechnical data Measuring range: up to 35 m Process fitting: flanges from DN 50, 2" Process temperature: -60 … +400 °C Process pressure: -1 … +160 bar (-100 … +16000 kPa) Accuracy: +/- 8 mm SIL qualification: optionally up to SIL21ApprovalXX without .....................................................................................................................................................................XM Ship approval ..........................................................................................................................................................CX ATEX II 1G, 1/2G, 2G Ex ia IIC T6 .........................................................................................................................CA ATEX II 1G, 1/2G, 2G Ex ia IIC T6 + WHG ............................................................................................................CM ATEX II 1G, 1/2G, 2G Ex ia IIC T6 + Ship approval ...............................................................................................CI IEC Ex ia IIC T6 ......................................................................................................................................................DX ATEX II 1/2G, 2G Ex d ia IIC T5/T6 ........................................................................................................................DI IEC Ex d ia IIC T6 ...................................................................................................................................................CK IEC Ex ia IIC Ga,Ga/Gb,Gb + Ex t IIIC T...Da,Da/Db,Db ........................................................................................DK IEC Ex d IIC Ga/Gb,Gb + Ex t IIIC T... Da,Da/Db,Db .............................................................................................Length standpipe / Total length316L (500-5950 mm) per 100 mm1 Mounting strap2 Adapter flangeYou will find further process fittings and options under /configurator .You will find further drawings and tables under /downloads.You will find mounting accessory, welded sockets and housing overviews in chapter "Accessory".VEGAPULS 67Radar sensor for continuous level measurement of bulk solidsApplication areaThe VEGAPULS 67 is a sensor for continuous level measurement of bulk solids under simple process conditions. It is suitable for smaller silos and vessels. The VEGAPULS 67 is an economical solution through its versatile and simple mounting options. The encapsulated antenna system ensures maintenance-free permanent operation even with strong buildup.Your benefit- Maintenance-free operation through non-contact measuring principle - High plant availability, because wear and maintenance-free - Reliable measurement independent of vapour, dust and noiseTechnical data Measuring range: up to 15 m Process fitting: mounting strap compression flanges from DN 80, 3" Process temperature: -40 … +80 °C Process pressure: -1 … +2 bar (-100 … +200 kPa) Accuracy: +/- 2 mm SIL qualification: optionally up to SIL21ApprovalXX without .......................................................................................................................................................................RX ATEX II 1D, 1/2D, 2D Ex t IIIC T... Da, Da/Db, Db ....................................................................................................1 Threaded version with horn antenna2 Threaded version with horn antenna and with temperature adapter3 Version with horn antenna and swivelling holderAntenna-øLength Beam angle40 mm 100 mm 20°48 mm 120 mm 15°75 mm 216 mm 10°95 mm430 mm8°You will find further process fittings and options under /configurator .You will find further drawings and tables under /downloads.You will find mounting accessory, welded sockets and housing overviews in chapter "Accessory".VEGAPULS SR 68Radar sensor for continuous level measurement of bulk solidsApplication areaThe VEGAPULS SR 68 is a radar sensor for continuous measurement of bulk solids even under difficult process conditions. It is particularly suitable for level measurement in high silos and large bunkers. The VEGAPULS SR 68 is aneconomical solution thanks to the simple setup and the reliable, maintenance-free operation.Your benefit- Maintenance-free operation through non-contact measuring principle - High plant availability, because wear and maintenance-free - Reliable measurement independent of vapour, dust and noiseTechnical data Measuring range: up to 30 m Process fitting: thread from G1½, 1½ NPT flanges from DN 50, 2" Process temperature: -40 … +250 °C Process pressure: -1 … +100 bar (-100 … +10000 kPa) Accuracy: +/- 2 mm1ApprovalXX without .................................................................................................................................................................CX ATEX II 1G, 1/2G, 2G Ex ia IIC T5 ......................................................................................................................CK ATEX II 1, 1/2, 2G Ex ia IIC + II 1, 1/2, 2D Ex t IIIC ............................................................................................CI IEC Ex ia IIC T6 Ga, Ga/Gb, Gb .........................................................................................................................DX ATEX II 1/2G, 2G Ex d ia IIC T5/T6 ....................................................................................................................DI IEC Ex d ia IIC T6 ................................................................................................................................................CK IEC Ex ia IIC Ga,Ga/Gb,Gb + Ex t IIIC T...Da,Da/Db,Db ....................................................................................DK IEC Ex d IIC Ga/Gb,Gb + Ex t IIIC T... Da,Da/Db,Db .........................................................................................RX ATEX II 1D, 1/2D, 2D Ex t IIIC T... Da, Da/Db, Db .............................................................................................RX IEC Ex t IIIC T... Da,Da/Db,Db ............................................................................................................................1 Threaded version with horn antenna2 Threaded version with horn antenna and with temperature adapter3 Version with parabolic antenna and swivelling holderAntenna-øLength Beam angle40 mm 100 mm 20°48 mm 120 mm 15°75 mm 216 mm 10°95 mm430 mm 8°245 mm (parabolic)138 mm3°You will find further process fittings and options under /configurator .You will find further drawings and tables under /downloads.You will find mounting accessory, welded sockets and housing overviews in chapter "Accessory".VEGAPULS 68Radar sensor for continuous level measurement of bulk solidsApplication areaThe VEGAPULS 68 is a radar sensor for continuous measurement of bulk solids also under difficult process conditions and with large measuring ranges. The sensor is ideal for level measurement in high silos, large bunkers, stone crushers and in the furnace. The VEGAPULS 68 with different antenna versions and materials is the optimum solution for virtually all applications and processes. Through the wide temperature and pressure range, the sensor can be used universally and enables a simple planning.Your benefit- Maintenance-free operation through non-contact measuring principle - High plant availability, because wear and maintenance-free - Reliable measurement independent of vapour, dust and noiseTechnical data Measuring range: up to 75 m Process fitting: thread from G1½, 1½ NPT flanges from DN 50, 2" Process temperature: -196 … +450 °C Process pressure: -1 … +160 bar (-100 … +16000 kPa) Accuracy: +/- 2 mm SIL qualification: optionally up to SIL2ApprovalXX without ...................................................................................................................................................................... XM Ship approval ............................................................................................................................................................ CX ATEX II 1G, 1/2G, 2G Ex ia IIC T5 ........................................................................................................................... CM ATEX II 1G, 1/2G, 2G Ex ia IIC T5 + Ship approval ................................................................................................. CK ATEX II 1, 1/2, 2G Ex ia IIC + II 1, 1/2, 2D Ex t IIIC ................................................................................................. CI IEC Ex ia IIC T6 Ga, Ga/Gb, Gb .............................................................................................................................. DX ATEX II 1/2G, 2G Ex d ia IIC T5/T6 ......................................................................................................................... DI IEC Ex d ia IIC T6 ..................................................................................................................................................... CK IEC Ex ia IIC Ga,Ga/Gb,Gb + Ex t IIIC T...Da,Da/Db,Db ......................................................................................... DK IEC Ex d IIC Ga/Gb,Gb + Ex t IIIC T... Da,Da/Db,Db ............................................................................................... RX ATEX II 1D, 1/2D, 2D Ex t IIIC T... Da, Da/Db, Db ................................................................................................... RX IEC Ex t IIIC T... Da,Da/Db,Db .................................................................................................................................AL-EN135Radar – VEGAPULS 6836Radar – VEGAPULS Cover for antenna / Material / Temperature max.D Horn ø75 mm / PP / 80°C .............................................................................................................................F Horn ø75 mm / PTFE / 130°C ......................................................................................................................L Horn ø75 mm / PTFE textile for flange / 250°C ............................................................................................H Horn ø75 mm / PTFE textile with silicone ring / 200°C .................................................................................E Horn ø95 mm / PP / 80°C .............................................................................................................................G Horn ø95 mm / PTFE / 130°C ......................................................................................................................M Horn ø95 mm / PTFE textile for flange / 250°C ............................................................................................I Horn ø95 mm / PTFE textile with silicone ring / 200°C .................................................................................For flange / Material 33602 DN80 PN10-40, ANSI 3"150, JIS DN80 10K / EPDM .....................................................................................33750 DN100 PN10-16, ANSI 4"150 , JIS DN100 10K / EPDM ................................................................................33751 DN150 PN10-16, ANSI 6"150, JIS DN150 10K / EPDM .................................................................................AL-EN Antenna cover VEGAPULS 68 Antenna cover of plastic or flexible Gore ® diaphragm The antenna cover can be retrofitted and avoids dust layers in the antenna system. The necessary mounting material is included in the scope of delivery.Variable seal VEGAPULS 67 Variable seal for sensor inclination。
英飞凌TPM安全芯片率先通过全球TCG和CESG认证
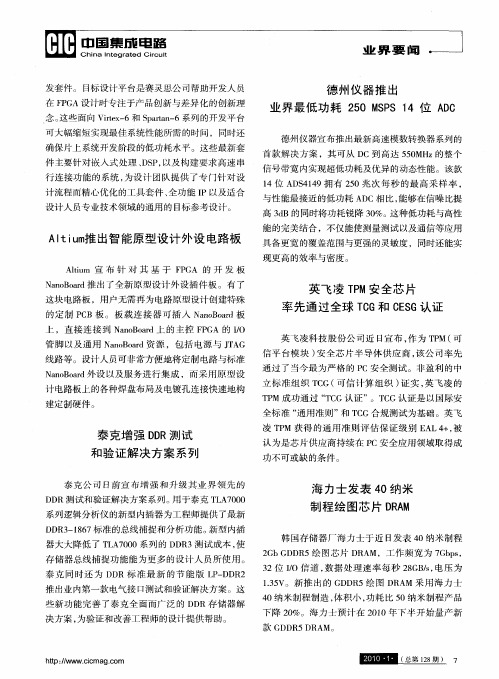
念。 这些 面 向 Vr x 6和 S atn 6系 列 的开发 平 台 ie一 t pr 一 a
德 州 仪 器 推 出
业 界 最低 功 耗 2 0 M P 4 位 A C 5 S S 1 D
上 ,直 接 连 接 到 N n B ad上 的 主 控 F G 的 I a o or PA / O
英 飞 凌 T M安 全芯 片 P
率 先通 过 全球 T G和 C S C E G认 证
英 飞 凌 科 技 股 份 公 司 近 日宣 布 , 为 T M( 作 P 可 信 平 台模 块 ) 全 芯 片 半 导 体供 应 商 , 公 司 率 先 安 该
3 2位 I / 道 , 据 处 理 速 率 每 秒 2 G /, O信 数 8 Bs 电压 为
15 . V。新 推 出 的 G D 5绘 图 D A 采 用 海 力 士 3 D R R M
4 米 制 程制 造 , 积小 , 耗 比 5 0纳 体 功 0纳米 制程 产 品
下 降 2 %。海力 士预 计 在 2 1 下 半 开始 量 产 新 0 0 0年
器 大大 降低 了 T A 0 0系 列 的 D R L 70 D 3测 试 成本 , 使
存储器总线捕捉功能能为更多 的设计人员所使用 。
泰克 同时还 为 D DR标 准 最 新 的节 能 版 L — D 2 P D R 推 出业 内第 一款 电气 接 口测试 和验 证 解决 方案 。这 些 新功 能 完 善 了泰克 全 面而 广泛 的 D R存 储 器解 D 决方 案 , 为验 证和 改善 工程 师 的设计 提 供 帮助 。
VEGAPULS67,68产品说明书新

1 测量原理及产品简介测量原理发射功率很低的极短的微波脉冲通过天线系统发射并接收。
雷达波以光速运行。
运行时间可以通过电子部件被转换成物位信号。
一种特殊的时间延伸方法可以确保极短时间内稳定和精确的测量。
即使存在虚假反射的时候,最新的微处理技术和独一无二的ECHOFOX-软件也可以准确地分析出物位回波。
通过输入容器尺寸,可以将上空距离值转换成与物位成正比的信号。
仪表可以空仓调试。
在固体测量中的应用对于这样的应用,可以使用K-频段的高频传感器。
由于信号的聚焦效果非常好,料仓内的安装物或仓壁的粘附物都不会影响测量。
高灵敏的电子部件使得物位测量更加精准,测量范围最大可达75米。
这种测量方法不受粉尘、入料噪音、气流或温度变化的影响。
应用领域包括:炼钢、采矿、食品、塑料加工等等。
输入参数测量过程连接和被测介质表面之间的举例。
基准面是法兰的密封面。
1 基准面2 测量参数,最大测量距离3 天线长度4 可用的测量范围2 仪表一览图VEGAPULS67VEGAPULS 68 VEGAPULS SR 68应用固体介质 固体介质,过程条件恶劣 固体介质,过程条件恶劣最大测量范围15米 75米 30米 天线/材料全部塑封的天线/PVDF 喇叭口天线、抛物线式天线/不锈钢316L 喇叭口天线/不锈钢316L 过程连接/材料龙门框或法兰/不锈钢304或聚丙烯 螺纹1½A ,符合DIN 3852-A 或法兰连接 螺纹1½A ,符合DIN 3852-A 或法兰连接 过程温度-40…+80°C -200…+450°C -20…+250°C 过程压力-1…+2bar/-100…+200kPa -1…+160bar/-100…+16000kPa -1…100 bar/-100…10000 kPa 测量偏差±2mm ±2mm ±2mm 频率范围K – 频段 K – 频段 K – 频段 信号输出 • 4…20mA/HART – 两线制• 4…20mA/HART – 四线制• Profibus PA• Foundation Fieldbus • 4…20mA/HART – 两线制 • 4…20mA/HART – 四线制 • Profibus PA • Foundation Fieldbus• 4…20mA/HART – 两线制 • 4…20mA/HART – 四线制 • Profibus PA • Foundation Fieldbus 显示/设定 • 调整显示模块PLICSCOM • 调试软件PACTware • 显示仪表VEGADIS61 • 显示仪表VEGADIS62 • 调整显示模块PLICSCOM• 调试软件PACTware• 显示仪表VEGADIS61• 显示仪表VEGADIS62• 调整显示模块PLICSCOM • 调试软件PACTware • 显示仪表VEGADIS61 • 显示仪表VEGADIS62 许可证 • ATEX 防爆许可证 • IEC 防爆许可证 • 船用许可证 • 溢出保护 • FM • CSA• ATEX 防爆许可证• IEC 防爆许可证• 船用许可证• 溢出保护• FM• CSA • ATEX 防爆许可证 • IEC 防爆许可证 • CSA3 仪表选型应用范围VEGAPULS 67VEGAPULS67适用于测量固体介质的物位。
Jumper R8 (D16 mode) Compatible Receiver instructi

Introduction:Thanks for choosing Jumper R8 full duplex telemetry receiver.Please read the instruction manual carefully and follow the instructions below to set up the device before using it.Overview:Specifications:Dimension: 35.8*23.7*12.6mm (L x W x H)Weight: <10gNumber of Channels: 16Ch (1~16ch from SBUS channel, 1~8ch from PWM channel) Operating Voltage Range: 3.5V~8.4VOperating Current: 70mA@5VOperating Range: Full rangeCompatibility: FrSky X-series module & radios in D16 modeFeatures:Telemetry TX/RX port enabled.( for PIX telemetry)Binding Procedure:Binding is the process of uniquely associating receiver to a transmitter/transmitter RF module .A transmitter internal or external RFmodule can be bound to multiple receivers (not to be used simultaneously).A receiver can only be bound to one RF module.Follow the steps below to finish the binding procedure.1.Put the transmitter/transmitter RF module into binding mode.For Jumper T16, Taranis X9D/X9D Plus/X9E and Taranis Q X7, turn on the radio, go to the MENU – MODEL SETUP – PAGE 2, choose Internal or External RF, and select BIND.2. Connect battery to the receiver while holding the F/S button on the receiver, the RED LED flashing indicates binding successfully.3. Reboot the receiver and go back to normal Mode of transmitter RF. Green LED constant on indicates linking normally. The receiver/transmitter module binding will not have to be repeated, unless one of the two is replaced.Note: After binding procedure is completed , power on the radio and the receiver and check if the receiver is really under control by linked transmitter.Range Check:A pre-flight range check should be done before each flying session. Reflections from nearby metal fences, concrete buildings or treescan cause loss of signal both during range check and during the flight. Under Range Check Mode, the RF power would be decreasedand Range distance to 1/30--1/10 that of Normal Model, about 30 meters.1. Place the model at least 60cm (two feet) above non-metal contaminated ground(e.g on a wooden bench). The receiver antennashould be in vertical position.2. For Jumper T16,Taranis X9D/X9D Plus/X9E and Taranis Q X7, turn on the radio and the receiver, go to : MODEL SETUP/Internal RF/Range.3. For transmitter RF module, please refer to its manual.Failsafe:Failsafe is a useful feature which is for a preset channel output position whenever control signal is lost for a period.Follow the steps to set Failsafe for channels necessary :Failsafe for receiver supporting D16 RF mode setting can be set via radio interface, which support no pulse, hold and customthree modes for each channel.For Jumper T16,Taranis X9D/X9D Plus/X9E and Taranis Q X7, turn on the radio, go to: MODEL SETUP/Internal RF/Failsafe.Note: Failsafe setting via transmitter for channel output position just for D16 RF mode, and Failsafe setting via transmitter has higher priority to setting via receiver. A reasonable Failsafe setting can decrease falling risk and damage.PIX telemetry:Much more operation and instruction please refer to radio manual.。
ProSoft Technology MVI56(E)-MNET添加指令安装指南说明书
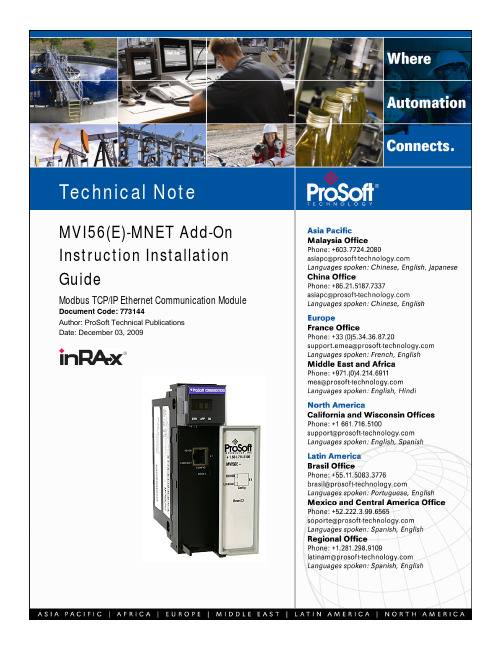
MVI56(E)-MNET Add-On Instruction Installation GuideModbus TCP/IP Ethernet Communication Module Document Code: 773144Author: ProSoft Technical PublicationsDate: December 03, 2009Document InformationAuthor ProSoft Technical PublicationsDescription Modbus TCP/IP Ethernet Communication ModuleDate December 03, 2009Revision 2.04.00Product Name MVI56(E)-MNETDocument Code773144ProSoft Technology5201 Truxtun Ave., 3rd FloorBakersfield, CA 93309+1 (661) 716-5100+1 (661) 716-5101 (Fax)Copyright © ProSoft Technology, Inc. 2009. All Rights Reserved.December 03, 2009ProSoft Technology ® ProLinx ®, inRAx ®, ProTalk®, and RadioLinx ® are Registered Trademarks of ProSoft Technology, Inc. All other brand or product names are or may be trademarks of, and are used to identify products and services of, their respective owners.How to contact us: Sales & SupportAll ProSoft Technology® products are backed with unlimited technical support. Contact our worldwide Technical Support team directly by phone or email:Asia Pacific+603.7724.2080,***********************************Languages spoken include: Chinese, Japanese, EnglishEurope – Middle East – Africa+33(0)5.34.36.87.20,***********************************Languages spoken include: French, English*****************************,fax to +33 (0) 5.61.78.40.52North America+1.661.716.5100,******************************Languages spoken include: English, Spanish*****************************,fax to +1 661.716.5101Latin America (Sales only)+1.281.298.9109,******************************Languages spoken include: Spanish, EnglishBrasil+55-11.5084.5178,******************************Languages spoken include: Portuguese, EnglishContentsDocument Information (2)ADD MODBUS TCP/IP ETHERNET COMMUNICATION TO CONTROLLOGIX WITH AN ADD-ON INSTRUCTION FOR RSLOGIX® 5000 VERSION 16 (4)Introduction (4)Instructions (5)Benefits (10)Add Modbus TCP/IP Ethernet Communication to ControlLogix with an Add-On Instruction for RSLogix® 5000 Version 16In This ChapterIntroduction (4)Instructions (5)Benefits (10)IntroductionBeginning with version 16 of RSLogix™ 5000 software, Rockwell Array Automation added an extremely helpful feature to make it easier that everto set up third party modules, custom code, or proprietary code. Theycalled this new feature an "Add-On Instruction" (AOI). This AOI featureallows third party vendors, panel builders, and system integrators to createladder logic code that can be protected for safety or security reasons andcan be locked to ensure that the code remains unchanged.ProSoft Technology®’s inRAx® Modbus TCP/IP Ethernet CommunicationModule for ControlLogix®, the MVI56(E)-MNET, is provided with an Add-On Instruction to allow easy integration of the module into new or existingRSLogix 5000 Version 16 and newer projects.ProSoft Technology® has enhanced the MVI56(E)-MNET module’s Add-On Instruction in a way that will significantly simplify installation.Now users can integrate the module into a new or existing project byimporting a single ladder logic import file, as opposed to importing multipleUser Defined Data Types and ladder logic rungs, one-by-one.The entire ladder logic required by the MVI56(E)-MNET is encapsulated inone, single Add-On Instruction. And, when the ladder logic .L5X file isimported, it automatically creates all the required User-Defined Data Types,Controller Tags, and the Add-On Instruction logic, all while adding thepreconfigured AOI instruction to the ladder rung.This new way of importing an AOI as a completed ladder rung enables quicker and easier integration of theMVI56(E)-MNET with fewer chances for human typographical errors and ladder coding or setup errors.Instructions1 Open the F ILE menu, and then choose N EW…2 Select your ControlLogix controller model.3 Select R EVISION 16.4 Enter a name for your controller, such as "My_Controller".5 Select your ControlLogix chassis type.6 Select S LOT 0for the controller.7 Add the MVI56(E)-MNET module to the project.In the C ONTROLLER O RGANIZATION window, select I/O C ONFIGURATION and click the right mouse button to open a shortcut menu. On the shortcut menu, choose N EW M ODULE...This action opens the S ELECT M ODULE dialog box.8 Select the 1756-M ODULE (G ENERIC 1756M ODULE)from the list and click OK.This action opens the N EW M ODULEdialog box.9 In the N EW M ODULE dialog box, enter the following values.Parameter ValueN AME Enter a module identification string. Example: Modbus TCP/IPEthernet.D ESCRIPTION Enter a description for the module. Example: Modbus TCP/IPEthernet Communication ModuleC OMM F ORMAT SelectD ATA-INT.S LOT Enter the slot number in the rack where the MVI56(E)-MNETmodule is located.I NPUT A SSEMBLY I NSTANCE 1I NPUT S IZE250O UTPUT A SSEMBLY I NSTANCE 2O UTPUT S IZE248C ONFIGURATION A SSEMBLY I NSTANCE 4C ONFIGURATION S IZE0Important: You must select the C OMM F ORMAT as D ATA -INT in the dialog box, otherwise the module will not communicate over the backplane of the ControlLogix rack.10 Click OK to continue.11 Edit the Module Properties. Select the R EQUESTED P ACKET I NTERVA l value for scanning the I/O on the module.This value represents the minimum frequency at which the module will handle scheduled events. This value should not be set to less than 1 millisecond. The default value is 5 milliseconds. Values between 1 and 10 milliseconds should work with most applications.12 Save the module.Click OK to close the dialog box. Notice that the module now appears in the C ONTROLLER O RGANIZATION window.13 In the C ONTROLLER O RGANIZATION window, expand the T ASKS folder and subfolder until you reach theM AIN P ROGRAM folder.14 In the M AIN P ROGRAM folder, double-click to open the M AIN R OUTINE ladder.15 Select an empty rung in the new routine, and then click the right mouse button to open a shortcut menu. On theshortcut menu, choose I MPORT R UNG…16 Navigate to the location on your PC where you saved the Add-On Instruction (for example, "My Documents" or"Desktop"). Select the MVI56(E)M ODBUS TCP/IP E THERNET_A DD O N_R UNG_<V ERSION #>.L5X fileThis action opens the I MPORT C ONFIGURATION dialog box, showing the controller tags that will be created.17 If you are using the module in a different slot (or remote rack), select the correct connection input and outputvariables that define the path to the module. If your module is located in Slot 1 of the local rack, this step is not required.18 Click OK to confirm the import. RSLogix will indicate that the import is in progress:When the import is completed, the new rung with the Add-On Instruction will be visible as shown in the following illustration.The procedure has also imported new User Defined Data Types, data objects and the Add-On instruction for your project.19 Save the application and then download the sample ladder logic into the processor.BenefitsThis process for importing the MVI56(E)-MNET Add-On Instruction into the RSLogix ladder logic file has replaced the practice of importing User Defined Data Types and multiple rungs of ladder in multiple ladder files.This enhancement allows you to easily integrate the module into a new or existing RSLogix project without manually copying over each file. Doing so practically eliminates human typographical errors. Additionally, errors that do occur are significantly easier to correct.。
AMD Athlon(TM) 64 and AMD Opteron(TM) Processors Thermal Design Guide

AMD Athlon™ 64 and AMD Opteron™ Processors Thermal Design GuidePublication # 26633 Rev: 3.03Issue Date: September 2003© 2002—2003 Advanced Micro Devices, Inc. All rights reserved.The contents of this document are provided in connection with AdvancedMicro Devices, Inc. (“AMD”) products. AMD makes no representations orwarranties with respect to the accuracy or completeness of the contents of thispublication and reserves the right to make changes to specifications andproduct descriptions at any time without notice. No license, whether express,implied, arising by estoppel, or otherwise, to any intellectual property rightsare granted by this publication. Except as set forth in AMD’s Standard Termsand Conditions of Sale, AMD assumes no liability whatsoever, and disclaimsany express or implied warranty, relating to its products including, but notlimited to, the implied warranty of merchantability, fitness for a particularpurpose, or infringement of any intellectual property right.AMD’s products are not designed, intended, authorized or warranted for use ascomponents in systems intended for surgical implant into the body, or in otherapplications intended to support or sustain life, or in any other application inwhich the failure of AMD’s product could create a situation where personalinjury, death, or severe property or environmental damage may occur. AMDreserves the right to discontinue or make changes to its products at any timewithout notice.TrademarksAMD, the AMD Arrow logo, AMD Athlon, AMD Opteron and combinations thereof, are trademarks of Advanced Micro Devices, Inc.Other product names used in this publication are for identification purposes only and may be trademarks of their respective companies.26633 Rev. 3.03 September 2003 AMD Athlon™ 64 and AMD Opteron™ Processors ThermalDesign GuideContentsRevision History (9)Chapter 1Introduction (11)1.1 Summary of Requirements (11)Chapter 2AMD Athlon™ 64 and AMD Opteron™ Processors ThermalRequirements (13)2.1 AMDAthlon™ 64, AMD Athlon 64 FX, and AMD Opteron™ ProcessorSpecifications (13)Description (14)2.2 Socket2.3 Motherboard Component Height Restrictions (16)2.4 Thermal Solution Design Requirements (18)2.5 Sample Heatsinks and Attachment Methods (19)2.5.1 Thermal Reference Design Solution 1 (19)2.5.2 Thermal Reference Design Solution 2 (22)2.6 Thermal Solution Design Considerations (25)2.6.1 Backplate Assembly (25)2.6.2 Spring Clip (25)2.6.3 Retention Frame (26)2.6.4 Heatsink (26)2.6.5 Fans (30)2.6.6 Thermal Interface Material (33)2.6.7 EMC Shield (33)Chapter 3Conclusion (35)A Appendix (37)Instrumentation (37)A.1 ThermocoupleA.1.1 Case Thermocouple Attachment (37)A.1.2 Heatsink Thermocouple Attachment (40)A.1.3 Ambient Thermocouple Attachment (40)A.2 Procedure for Clip Load Testing (41)A.2.1 Equipment (41)Contents 326633 Rev. 3.03 September 2003AMD Athlon™ 64 and AMD Opteron™ ProcessorsThermal Design GuideA.2.2 Procedure (45)A.3 Motherboard Component Keep-Out Areas and Height Restriction Drawings (47)A.4 Thermal Reference Design Solution Component Drawings (68)4 Contents26633 Rev. 3.03 September 2003 AMD Athlon™ 64 and AMD Opteron™ Processors ThermalDesign GuideList of FiguresFigure 1. 754-pin µPGA Socket Used for the AMD Athlon™ 64 Processor (14)Figure 2. 940 pin µPGA Socket Used for the AMD Opteron™ Processor (15)Figure 3. Motherboard Component Height Restrictions for the AMD Athlon 64 Processor Thermal Solution (16)Figure 4. Motherboard Component Height Restrictions for the AMD Opteron Processor Thermal Solution (17)Figure 5. AMD Athlon 64 and AMD Opteron Processors Thermal Reference Design Solution 1 (20)Figure 6. Thermal Reference Design Solution 1 Components Assembled for Shipment (21)Figure 7. View of an Installed Heatsink Utilizing the Thermal Reference Design Solution 1 (21)Figure 8. Exploded View of the Components Utilized in the AMD Athlon 64 andAMD Opteron Processors Thermal Reference Design Solution 2 (23)Figure 9. Thermal Reference Design Solution 2 Components Configured for Shipment (24)Figure 10. View of a Heatsink Installation Utilizing the Thermal Reference DesignSolution 2 (24)Figure 11. Example of a Low-Cost Heatsink Using Aluminum Extrusion Technology (27)Figure 12. High Performance Heatsink with Copper Slug Embedded in the Base (28)Figure 13. Required Exhaust Airflow Direction for Motherboard Voltage Regulator Cooling (29)Figure 14. Typical Temperature-Fan Speed Relation for Speed-Controlled Fan (31)Figure 15. Acoustic Noise from Sample Thermal Solutions with a 70x15 mm Fan (32)Figure 16. Diagonals Marked on Processor to Locate Center (37)Figure 17. Thermocouple Taped to Processor Lid (38)Figure 18. Thermocouple Attached to Processor with Strain Relief on Package and PCB (39)Figure 19. Heatsink with Thermocouple Relief Groove Machined into Base (39)Figure 20. Heatsink Thermocouple Relief Groove and Measurement Hole (40)Figure 21. An Entran ELW-D1 Load Cell (41)Figure 22. Load Cell Inserted into the Load Cell Fixture (42)Figure 23. Drawing of Load Cell Fixture for the Entran ELW-D1 Load Cell (43)Figure 24. Test Board with a Load Cell Fixture Installed in the Socket 754 (45)Figure 25. Heatsink Installation over the Load Cell Fixture (46)List of Figures 526633 Rev. 3.03 September 2003 AMD Athlon™ 64 and AMD Opteron™ ProcessorsThermal Design Guide6 List of Figures26633 Rev. 3.03 September 2003 AMD Athlon™ 64 and AMD Opteron™ Processors ThermalDesign GuideList of TablesTable 1. Mechanical and Thermal Specifications for the AMD Athlon™ 64 and AMD Opteron™ Processors (13)Table 2. Thermal Solution Design Requirements for the AMD Athlon 64 and AMD Opteron Processors (18)Table 3. Components for the AMD Athlon 64 and AMD Opteron Processors Thermal Reference Design Solution 1 (19)Table 4. Components for the AMD Athlon 64 and AMD Opteron Processors Thermal Reference Design Solution 2 (22)Table 5. Chemical Composition of SK7 Spring Steel (26)Table 6. Suggested Thermal Interface Materials (33)List of Tables 726633 Rev. 3.03 September 2003 AMD Athlon™ 64 and AMD Opteron™ ProcessorsThermal Design Guide8 List of Tables26633 Rev. 3.03 September 2003 AMD Athlon™ 64 and AMD Opteron™ ProcessorsThermal Design Guide Revision HistoryDate Rev DescriptionSeptember 2003 3.03 Revision 3.03 includes the addition of information for theAMD Opteron™ processor and the following changes:• In Chapter 2, added AMD Athlon™ 64 FX processorinformation in Section 2.1 on page 13, revised Table 1 on page13, added Figure 2 on page 15, revised Figure 3 on page 16,added Figure 4 on page 17, revised Table 2 on page 18,revised Table 3 on page 19, revised Table 4 on page 22,revised Section 2.6 on page 25, added Section 2.6.4.3,“Required Exhaust Airflow Direction,” on page 29, addedFigure 13 on page 29, revised Section 2.6.5 on page 30, addedFigure 14 on page 31, added Figure 15 on page 32, and revisedTable 6 on page 33.• In the Appendix , revised Socket 754 diagrams and addedSocket 940 diagrams to Section A.3 on page 47. Reviseddiagrams in Section A.4 on page 68.February 2003 3.02 Revised Figure 3, “Motherboard Component Height Restrictions forthe AMD Athlon™ 64 Processor Thermal Solution,” on page 16, andthe drawings in the Appendix, section A3, “Motherboard ComponentKeep-Out Areas and Height Restriction Drawings,” on pages 35–44. November 2002 3.01 Title changed to “AMD Athlon™ 64 Processor Thermal DesignGuide.”October 2002 3.00 Public release9Revision History26633 Rev. 3.03 September 2003 AMD Athlon™ 64 and AMD Opteron™ ProcessorsThermal Design Guide10Chapter 1 IntroductionThis document specifies performance requirements for the design of thermal and mechanical solutions for the AMD Athlon™ 64 and AMD Opteron™ processors, utilizing AMD64 architecture. Detailed drawings, descriptions, and design targets are provided to help manufacturers, suppliers, and engineers meet requirements for the AMD Athlon 64 and AMD Opteron processors.1.1 Summary of RequirementsTo allow optimal reliability of the AMD Opteron and AMD Athlon 64 processor-based systems, the thermal and cooling solution should dissipate heat from a processor operating at its maximum thermal power. The sections in this document specify required values for the thermal and mechanical parameters. This document provides two methods of creating a solution that satisfy the thermal and mechanical requirements for these processors. By setting a high-power target for the initial design, the thermal-design engineer may avoid redesign of the processor cooling solution for subsequent processors.Chapter 2 AMD Athlon ™ 64 and AMD Opteron ™Processors Thermal RequirementsThis chapter describes thermal solutions for the AMD Athlon™ 64, AMD Athlon 64 FX, and AMD Opteron™ processors.2.1 AMD Athlon ™ 64, AMD Athlon 64 FX, andAMD Opteron ™ Processor SpecificationsThe objective of thermal solutions, commonly referred to as heatsinks, is to maintain the processor temperature within specified limits. The main factors that must be considered during the design of a thermal solution are the thermal performance, physical mounting, acoustic noise, mass, reliability, and cost.This document presents the thermal and mechanical specifications, and heatsink requirements for the AMD Athlon 64, AMD Athlon 64 FX, and AMD Opteron processors. The thermal and mechanical specifications for the 940-pin AMD Athlon 64 FX processor are the same as those for the AMD Opteron processor. For the thermal and mechanical requirements for the AMD Athlon 64 FX processor, refer to the AMD Opteron processor information presented in this document.Table 1 lists the pertinent AMD Athlon 64 and AMD Opteron processor specifications for a thermal solution design.Table 1. Mechanical and Thermal Specifications for the AMD Athlon™ 64 andAMD Opteron™ Processors Symbol Description Maximum Value NotesT CASE Maximum case temperature 62–70°CCase temperature will be defined in the processor datasheetA CPU Processor contact area 1400 sq. mm Interfaces with heatsink Form factorProcessor form factorµPGAPGA Socket 754 form factor for AMD Athlon™ 64 processorForm factor Processor form factor µPGAPGA Socket 940 form factor for AMD Opteron™ processor2.2 Socket DescriptionFigure 1 shows a three-dimensional view of the Socket 754, which is a socket based on surface mount technology. The pin array is 29x29 on a 1.27 mm pitch with a 9x9 depopulation in the center. In addition, three pins are removed from the A1 corner of the package, and a single pin is removed from the other three corners. The electrical and mechanical connection to the motherboard is made with a small solder ball at each socket contact. This type of connection does not allow for a large mass, like a heatsink, to be attached to the socket. Therefore, independent support structures are required for mounting the heatsink.Figure 2 shows a three-dimensional view of the Socket 940, which is used for the AMD Opteron processor. As with the Socket 754, it has a 1.27 mm array pitch but has a 31x31 pin array with various pins removed from the package for keying and mechanical support.Figure 2. 940-pin µPGA Socket Used for the AMD Opteron™ Processor2.3 Motherboard Component Height RestrictionsThe mounting solution for the heatsink requires attachment to the motherboard. As such, this solution calls for a standard motherboard keepout region and mounting holes for the processor. An overview of the motherboard component restrictions for the AMD Athlon 64 is shown in Figure 3.A complete detailed set of drawings is shown in Appendix A.3 on page 47. Thermal-solution designers must adhere to these geometric restrictions to be compatible with the motherboards designed for the AMD Athlon 64 processor. Similarly, overview of the motherboard component restrictions for the AMD Opteron is shown in Figure 4 on page 17.Figure 3. Motherboard Component Height Restrictions for the AMD Athlon™ 64 Processor Thermal SolutionFigure 4. Motherboard Component Height Restrictions for the AMD Opteron™ Processor Thermal Solution2.4 Thermal Solution Design RequirementsTo maintain the case temperature of the processor below the maximum specification, certain heatsink design parameters must be considered. Table 2 provides the design-target specifications that must be met for the AMD Athlon 64 and AMD Opteron processors to operate reliably.Table 2. Thermal Solution Design Requirements for the AMD Athlon™ 64 and AMD Opteron™ ProcessorsSymbol Description Minimum Maximum Notes L Length of heatsink 77 mm 77 mm Measurements are forthe entire assembly,including attached fan.W Width of heatsink 68 mm 68 mmH Height of heatsink 60 mmθCA Case-to-ambientthermal resistance0.28°C/WmHSMass of heatsink 450 gFCLIPClip force 60 lb 90 lbTA Local ambienttemperature nearprocessor42°C32 dbA The preferred level is tohave no annoying tones.LPA Sound pressuremeasured 1 mfrom fan 38 dbA Maximum level is atroom temperature withno annoying tones2.5 Sample Heatsinks and Attachment MethodsThe following sections provide two possible thermal design solutions and the specifics on their attachment to the motherboard.2.5.1 Thermal Reference Design Solution 1Table 3 lists the parts that comprise the thermal reference design solution 1 for theAMD Opteron and AMD Athlon 64 processors. The heatsink installers do not have to assembleeach individual component. The heatsink suppliers package the parts with some of the components already assembled. The logical breakdown consists of the components that reside on the topside ofthe motherboard, the heatsink, and the components that reside on the bottom side of the motherboard, the backplate. An exploded view showing the components used in the thermal reference design solution 1 is shown in Figure 5 on page 20.Due to the high load required to attach the heatsink to the processor, a backplate is used on the backside of the motherboard to minimize possible warping of the motherboard due to clip forceson the heatsink. Figure 6 on page 21 shows the assembly components grouped for shipment andhow they are used during the final assembly of the system.When developing the thermal reference design solution 1, AMD took into consideration the manufacturing and assembly ease of the solution. The thermal reference design solution 1 requiresa screwdriver to install the heatsink. The mechanical advantage of the screw is that it applies alarge force to the clip. Minimizing installation fatigue was a significant factor in selecting the useof screws in this thermal solution. During installation each screw is driven until it bottoms out onthe retention frame. This may require a torque of 6 to 12 in-lbs. Figure 7 on page 21 shows a heatsink installed according to the thermal reference design solution 1.Table 3. Components for the AMD Athlon™ 64 and AMD Opteron™ Processors Thermal Reference Design Solution 1Part Description Material QuantityHeatsink Aluminum 1 Fan Plastic 1 Mounting frame Lexan, 20% glass filled 1Spring clip SK7 heat treated spring steel 16-32x1” pan head screw Stainless steel 2Backplate Low carbon steel, anti-corrosive finish 1GK-17 1 Insulator FormexEMC shield Stainless steel 1Figure 5. AMD Athlon™ 64 and AMD Opteron™ Processors Thermal Reference Design Solution 1Figure 6. Thermal Reference Design Solution 1 Components Assembled for Shipment Figure 7. View of an Installed Heatsink Utilizing the Thermal Reference Design Solution 12.5.2 Thermal Reference Design Solution 2Table 4 lists the parts used in the thermal reference design solution 2 for the AMD Athlon 64 andAMD Opteron processors. An exploded view of the components used for this thermal solution isshown in Figure 8 on page 23. The components are shipped as subassemblies so the heatsinkinstaller does not have to assemble each individual component. The retention frame and backplateare shipped pre-installed on the motherboard as shown in Figure 9 on page 24. The heatsink unithas the components assembled so the installer can remove it from the packaging, remove anythermal interface material protection, hook the clip onto the retention frame, and then actuate thecam. For the thermal reference design solution 2, the installer needs no tools for the heatsinkinstallation process. Figure 10 on page 24 shows an installed heatsink utilizing the thermalreference design solution 2.Table 4. Components for the AMD Athlon™ 64 and AMD Opteron™ Processors ThermalReference Design Solution 2Part Description Material QuantityComponents Installed by OEM, System Integrator, or End UserHeatsink Aluminum 1 Fan Plastic 1 Spring clip SK7 heat treated spring steel 1Camshaft Lexan, 20 % glass filled 1Cam spacer Lexan, 20 % glass filled 1EMC shield Stainless steel 1Components Assembled on the MotherboardRetention frame Lexan, 20% glass filled 1Backplate Low carbon steel, anti-corrosive finish 1Insulator FormexGK-17 16-32x 0.75” pan head screw Stainless steel 2Figure 8. Exploded View of the Components Utilized in the AMD Athlon™ 64 and AMD Opteron™ Processors Thermal Reference Design Solution 2Figure 9. Thermal Reference Design Solution 2 Components Configured for Shipment Figure 10. View of a Heatsink Installation Utilizing the Thermal Reference Design Solution 22.6 Thermal Solution Design ConsiderationsThe two thermal reference design solutions shown in Figure 5 on page 20 and Figure 8 on page 23 contain several components that have specific functions. A complete set of drawings is shown in Appendix A.4 beginning on page 68. Because the µPGA processors have features that are significantly different from the previous generation of processors, some background is given in the following sections on the various aspects of the mechanical requirements for the thermal solution. Also, additional design considerations and requirements are given for improved thermal and acoustic performance.2.6.1 Backplate AssemblyThe backplate assembly is designed to prevent excessive motherboard warpage in the area near the processor. Without using a backplate, the warpage could cause serious damage to electrical connections of the processor socket and integrated circuit packages surrounding the processor. The reference backplate is made from cold rolled steel and incorporates three stiffening ribs to meet stiffness requirements. The center rib is partially cut away by a square hole located in the center of the backplate. This region is for decoupling the capacitors on the backside of the motherboard. It is important to not cut entirely through the center rib, as that action would compromise the stiffness of the reference backplate. The size of the square hole differs according to the type of processor. The AMD Athlon 64 processor version has a 20 mm square hole while the AMD Opteron processor version has a 26 mm square hole. Using a 26-mm hole on both AMD Athlon 64 and AMD Opteron processors is being investigated, and the results will be included in an update of this document.There are two PEM standoffs used in the plate. The standoffs serve multiple purposes, mainly as attachment points for the retention frame screws and for aligning the backplate easily and properly to the motherboard. The retention frame is made to slide over the standoffs and allow the screws to be installed with a minimum chance of cross threading.The insulator also serves multiple purposes. The primary function of the insulator is to prevent the backplate from shorting to the motherboard. Additionally, a pressure-sensitive adhesive in the insulator keeps the backplate in place against the motherboard during assembly. The insulator is thick enough to prevent any significant capacitive coupling between the motherboard and backplate.2.6.2 Spring ClipThe spring clips used for both thermal reference design solutions were designed to apply 75 lbs of force to the heatsink. This force is necessary to prevent a large-mass heatsink from lifting off the package during a shock or vibration-induced event. Any lifting of the heatsink away from the processor could result in damage to the processor pins, the socket contacts, or the socket solder ball joints. This spring force is greater than required in previous generations of AMD processors. Maintaining the spring force is important for the life of the processor and for repeated installations and upgrades of the processor.The reference spring clip material is the heat-treatable spring steel, SK7. AMD strongly recommends using SK7 or an equivalent material for the spring clip. The clip should be plated after heat treatment for cosmetic and anti-corrosive reasons. Table 5 gives the chemical composition of SK7. The heat treatment used should bring the ultimate strength of the material to a minimum of 1,300 Mega-Pascals (Mpa) or 189 Kilo-pounds per square inch (Ksi) and a yield strength to 940 MPa (or 136 Ksi).Other materials commonly used for heatsink spring clips have been shown to yield under the high load of the initial spring clip deflection, become deformed, and can no longer apply the same load. Table 5. Chemical Composition of SK7 Spring SteelComposition Percentage of the ElementC 0.60–0.700.35Si MaximumMn 0.80–0.90P Maximum0.0300.030S MaximumBalanceFe Remaining2.6.3 Retention FrameThe retention frame serves multiple purposes. During installation, the retention frame provides a stop for the spring clip ends used in the thermal reference design solution 1. The retention frame also aligns the heatsink and provides a stop for the heatsink in case of a large shock-force event. The retention frame serves to hold the solution 1 heatsink assembly together as a single unit for shipping and assembly, and aligns and helps to retain the EMC shield.The retention frame serves the same function for the thermal reference design solution 2, but it is implemented in a different way. The retention frame and backplate are joined to the motherboard by the motherboard manufacturers. Two screws securely hold the backplate and retention frame together. The six mounting tabs on the retention frame serve as an attachment point for the heatsink spring clip. The thermal reference design solution 2 utilizes only two of the mounting tabs, but the flexibility of the design is increased with the additional mounting tabs.2.6.4 HeatsinkThe footprint of the reference design heatsink is 77x68 mm. The highest-power processors may require solutions incorporating copper in the base of the heatsink to dissipate heat, taller fins and greater fin density to increase surface area, and higher flow fans to increase cooling capacity. Because the processor mounting surface extends above the surface of the cam box on the socket, the heatsink bottom must be flat. The heatsink must have a flat surface of at least 40x40 mm centered over the processor as specified in the reference design drawing.2.6.4.1 Low-Cost Heatsink ExampleBased on the thermal performance requirements of a particular processor, a low-cost heatsink may be appropriate for an application. An example of a low-cost heatsink utilizing extruded aluminum stock is shown in Figure 11.Figure 11. Example of a Low-Cost Heatsink Using Aluminum Extrusion Technology2.6.4.2 High Performance Heatsink ExampleWhen a high performance heatsink is needed to meet thermal or acoustic requirements, other manufacturing technologies can be used. These technologies combine high-density fin pitches with thin fins. They may also incorporate copper into the heatsinks. Copper and aluminum are commonly used together in the same heatsink. Figure 12 shows an example of a heatsink that would perform better than the low-cost extrusion heatsink The heatsink shown in Figure 12 is based on high-aspect ratio extrusion manufacturing technology. An example of a high performance heatsink using a high-density fin technology is shown in Section A.4 on page 64. Figure 12. High Performance Heatsink with Copper Slug Embedded in the Base2.6.4.3 Required Exhaust Airflow DirectionThe current that a motherboard must supply to the AMD Athlon 64 and AMD Opteron processors has increased during the development of these processors. The increase in current requires that air exhausting from the heatsink be directed across the motherboard processor voltage regulator. Motherboard suppliers have designed their motherboards to have voltage regulators located along the long side of the heatsink. Therefore, heatsinks should be designed to have aiflow exit the long side of the heatsink as shown in Figure 13. Alternatively, airflow may exit the heatsink on all sides.Figure 13. Required Exhaust Airflow Direction for Motherboard Voltage Regulator Cooling2.6.5 FansImprovements in fan technology have increased the range of flow capacity available to thermal solution designers. However, increased flow may often occur at the expense of causing increased acoustic noise. Larger fans can move more air at lower rotational speeds than smaller fans. The recent increase in availability of 70-mm body fans allows them to be used for high-volume thermal solutions. AMD recommends using 70-mm body fans for the AMD Athlon 64 and AMD Opteron and processors.Because the thermal solutions are used on a variety of motherboard designs with the fan power connector in different locations, AMD recommends a minimum fan power cable length of 200 mm. This length should allow the thermal solution to be mounted in any orientation while maintaining the ability to power the fan.Because the thermal solution must meet the processor thermal requirements at elevated ambient temperatures, a single fan speed solution results in a high fan speed to meet these requirements.Acoustic noise is a concern for both system builders and AMD. Systems with high levels of acoustic noise can generate customer complaints and can influence the acceptance of a product. Therefore, AMD recommends using fans that have speed control implemented on the fan.Usually, a thermistor is used to sense the airflow temperature at the fan to determine the fan speed.A fan with variable speed capability can meet the thermal requirement at multiple ambient conditions.The significant temperatures for the AMD Athlon 64 and AMD Opteron processor systems are 32°C and 42°C. These temperatures correspond to room temperatures of 25°C and 35°C, respectively, with an additional 7°C allowed for the temperature rise from the system external temperature to the system internal temperature at the processor location.At 25°C (normal room temperature), the thermal solution has an additional 10°C added to to the system thermal budget. The required thermal resistance increases, for example, from 0.31°C/W to 0.40°C/W. While the fan speed and heatsink performance are closely coupled, the fan speed can be significantly reduced with the additional 10°C in the thermal budget.Preliminary Information26633 Rev. 3.03 September 2003AMD Athlon™ 64 and AMD Opteron™ Processors Thermal Design GuideFigure 14 shows a typical fan speed curve. The actual fan speed can depend on the heatsink, but the speed versus temperature ramping should be implemented as shown in the figure.Figure 14. Typical Temperature-Fan Speed Relation for Speed-Controlled FanChapter 2AMD Athlon™ 64 and AMD Opteron™ Processors Thermal Requirements31。
Dell EMC PowerEdge T40 小型企业服务器说明书

© 2019 Dell Inc. o sus filiales.Invierta de forma inteligente para su pequeña empresaEl servidor confiable Dell EMC PowerEdge T40 y el equipo de soporte de Dell EMC simplificarán los retos diarios de su pequeña empresa.• Elija un servidor de calidad diseñado para superar los retos de las pequeñas empresas.• Disfrute del soporte confiable de Dell EMC con una garantía de hardware estándar de un año al siguiente día laboral o seleccione una garantía estándar de hasta cinco años.• Controle sus datos y el acceso estos in situ.• Administre los gastos al evitar los costos desconocidos de procesamiento y almacenamiento de la nube pública.• Confíe en la cadena de suministro garantizada de Dell EMC.Apoye eficientemente a su pequeña empresa con características fundamentalesDell EMC PowerEdge T40 soporta eficientemente sus operaciones empresariales diarias, lo que le permite concentrarse en su empresa. T40 es fácil de administrar, lo que le permite liberar tiempo para dedicar a las prioridades de trabajo.• Trabaje de manera más eficiente con un rendimiento mejoradogracias a una velocidad de transferencia de datos un 25 % másrápida, una velocidad de CPU más eficiente y una velocidadturbo un 27 % más elevada con el procesador Intel ® Xeon ®E-2224G.1• Comparta más contenido con los miembros del equipo y losclientes con un aumento del 50 % en el almacenamiento dedatos in situ.2• Coloque su torre en un lugar conveniente gracias a un diseñoun 23 % más pequeño.3• Consolide, almacene y comparta archivos in situ fácilmente.El PowerEdge T40 es el servidor básico confiable, eficiente y fundamental para apoyar su empresa en crecimiento.PowerEdge T40• 27 % más elevada • de datos •POWEREDGE T40El componente básico confiable para su pequeña empresa1I nformación basada en análisis internos de Dell EMC en los que se comparan el número de velocidad máxima de la memoria (MT/s), la velocidad de cálculo de la CPU y la velocidad de cálculo de la CPU turbo del modelo T40 con el modelo anterior. Abril del 20192 Información basada en análisis internos de Dell EMC en los que se compara el espacio de almacenamiento máximo del modelo T40 con la generación anterior. Abril del 20193 Información basada en análisis internos de Dell EMC en los que se compara el tamaño (L) del modelo T40 con la generación anterior. Abril del 2019* Están disponibles discos duros adicionales junto con el portaunidades y el cable asociados. Consulte a su representante de ventas en caso de que desee realizar solicitudes adicionales. Obtenga más información en /PowerEdgeServicios recomendadosProSupport Plus para los sistemas críticos o ProSupport para el soporte de hardware y software integral para la solución PowerEdge. También hay ofertas de consultoría e implementación disponibles. Comuníquese con un representante de Dell EMC hoy mismo para obtener más información.La disponibilidad y los términos de Dell EMC Services varían según la región. Para obtener más información, visite /ServiceDescriptions. Soluciones tecnológicas integralesAproveche las soluciones de negocio y de TI para reducir la complejidad de TI, disminuir los costos y eliminar las ineficiencias. Puede confiar en las soluciones integrales de Dell para aprovechar al máximo el rendimiento y el tiempo de actividad. Los servicios y las soluciones empresariales de Dell, reconocido como líder en servidores, almacenamiento y redes, brindan innovación a cualquier escala. Además, si no quiere gastar dinero o si desea aumentar la eficiencia operativa, Dell Financial Services™ cuenta con una amplia variedad de opciones para que la adquisición de tecnología sea fácil y asequible. Para obtener más información, comuníquese con su representante de ventas de Dell*.© 2019 Dell Inc. o sus filiales. Todos los derechos reservados. Dell, EMC y otras marcas comerciales son propiedad de Dell Inc. o sus filiales. Otras marcas comercialespueden ser marcas comerciales de sus respectivos propietarios. Este documento solo tiene fines informativos. Dell se reserva el derecho de realizar cambios a cualquierproducto que aparece aquí sin previo aviso. El contenido se proporciona tal como está y sin garantías explícitas ni implícitas de ningún tipo. * Dell Financial Services L.L.C.o su filial o entidad designada (“DFS”) ofrecen y gestionan el leasing y el financiamiento para los clientes que cumplen con los requisitos. Las ofertas pueden no estardisponibles o pueden variar en determinados países. Donde se encuentran disponibles, las ofertas pueden modificarse sin previo aviso y están sujetas a la disponibilidaddel producto, aprobación crediticia, ejecución de la documentación proporcionada y aceptada por DFS, y pueden estar sujetas a un monto mínimo de transacción. Lasofertas no se encuentran disponibles para uso personal, familiar o doméstico.Copyright © 21 de abril de 2020, Dell Inc. o sus filiales. Todos los derechos reservados.。
FUJITSU LIMITED PRIMERGY TX150 S4 BIOS Update tool

********************************************************************************* For PRIMERGY TX150 S4 **** BIOS Update tools V1.0L10 *********************************************************************************FUJITSU LIMITED--------------------------------------------------------------------------This manual explains the BIOS Update tools for PRIMERGY TX150 S4.The manual consists of the following:[Contents]1. Before Using this Software2. Applicable Models3. Revision History (Revised Items)4. How to use5. Trademarks and Copyrights---------------------------------------------------------------------------1. Before Using this SoftwarePlease observe the following terms of use of this software.If you do not agree to the terms of use of this software,please do not use this software.Terms of Use1) This software shall be used only for the applicable model specified below.2) This software shall not be redistributed.3) This software shall not be modified, reverse engineered, or disassembled.4) Any copyright information about this software shall not be modified.5) Fujitsu assumes no responsibility for any damage that may occur as a result of using this software.---------------------------------------------------------------------------2. Applicable ModelsPRIMERGY TX150 S4---------------------------------------------------------------------------3. Revision History (Revised Items)V1.0L10(1) First edition released---------------------------------------------------------------------------4.How to use1) Expand the downloaded TX150103.EXE module, which is in self expand format.2) The following files are expanded:[Installation Procedure]TX150-S4-UpdateNote.pdf[Installation Data kit]make.batmakefpd.batTX153DK1.EXETX153DK2.EXE3) Please execute make.bat file for making Utilities.4) For details on using the Installation Kit, read the expanded installation note(TX150-S4-UpdateNote.pdf).Use a PDF file viewer to read the PDF file.---------------------------------------------------------------------------5. Trademarks and CopyrightsAny other trademarks are those of their respective owners.All Rights Reserved, Copyright© FUJITSU LIMITED 2006。
VEGAPS60雷达物位选型手册

1 测量原理及产品简介测量原理发射能量很低的极短的微波脉冲通过天线系统发射并接收。
雷达波以光速运行。
运行时间可以通过电子部件背转换成物位信号。
一种特殊的时间延伸方法可以确保极短时间内稳定和精确的测量。
雷达传感器的发射功率非常小,分C频段和K频段。
即使在存在虚假反射的时候,最新的微处理技术和独一无二的ECHOFOX-软件也可以准确地分析出物位回波。
仪表可以空仓调试。
液体测量应用对于这种应用,可以提供两种不同的发射频率。
一体式的高频传感器(K频段)适用于高精度测量。
开口尺寸小的喇叭口天线聚焦效果更好。
低频传感器(C频段),适用于泡沫、冷凝水等困难的测量条件。
测量不受蒸汽、混合气体、压力和温度变化的影响。
输入端参数测量参数是过程连接和被测介质表面之间的距离。
根据传感器类型不同,基准面可以是六角螺母的密封面或法兰的下边缘。
1 基准面2 测量参数,最大测量范围3 天线长度4 可用的测量范围2 仪表类型一览表VEGAPULS61VEGAPULS62 VEGAPULS63VEGAPULS65VEGAPULS62VEGAPULS WL 613 仪表选型应用范围VEGAPULS 61适用于测量小容器内的液体,几乎可以用于各个工业领域。
塑封的天线非常适用于测量小容器内的腐蚀性液体。
塑料天线还特别适用于测量开口渠的流量或河流的水面。
VEGAPULS 62适用于在恶劣的过程条件下测量储罐或过程容器中的液体。
可以用于化工行业、石化行业或环保和循环行业等等。
喇叭口型天线特别适用于测量储罐或过程容器内的介质,比如:溶剂、碳氢化合物、动力燃料等。
抛物线式天线适于在测量范围较大的条件下测量介电常数小的介质。
VEGAPULS 63适用于腐蚀性液体测量或特殊的卫生要求。
特别适用于化工行业、食品行业和制药行业等。
VEGAPULS 65适用于在一般测量条件下,测量液体。
可以用于较小的过程连接。
VEGAPULS 66适用于在复杂的测量条件下测量液体。
Error catch RAM for memory tester has SDRAM memory
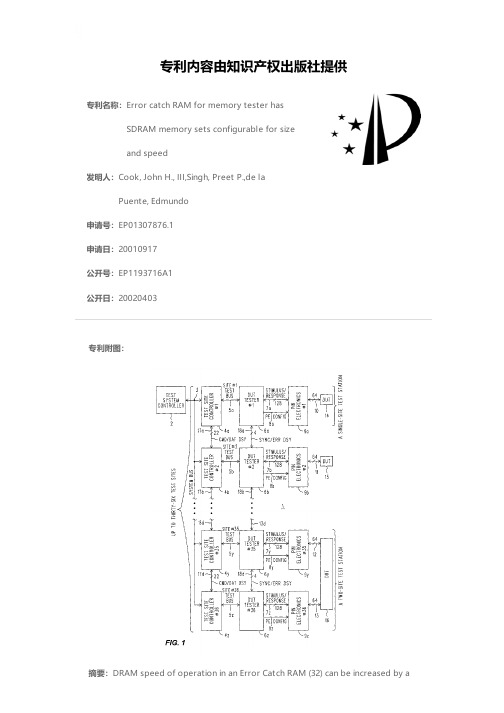
专利名称:Error catch RAM for memory tester hasSDRAM memory sets configurable for sizeand speed发明人:Cook, John H., III,Singh, Preet P.,de laPuente, Edmundo申请号:EP01307876.1申请日:20010917公开号:EP1193716A1公开日:20020403专利内容由知识产权出版社提供专利附图:摘要:DRAM speed of operation in an Error Catch RAM (32) can be increased by acombination of interleaving signals for different Banks (113-116) of memory in a Group (88) thereof and multiplexing between those Groups of Banks. A three-way multiplexing between three Groups of four Banks each, combined with a flexible four-fold interleaving scheme for signals to a Group produces an increase in speed approaching a factor of twelve, while requiring only three memory busses. Each of the twelve Banks represents the entire available address space, and any individual write cycle might access any one of the twelve Banks. A utility mechanism (146) composes results for all twelve Banks during a read cycle at an address into a unified result. There is a mechanism to track of the integrity of the composed results, as further write operations can produce the need for another composing step. There are four Memory Sets, two are "internal" SRAM's (75, 76) and two are "external" DRAM's (73,74). The SRAM's are integral parts of VLSI circuits, while the DRAM's are individual packaged parts adjacent that VLSI. The amount of DRAM is optional. For DRAM memory sets the multiplexing and interleaving mode allows full random access at speeds of up to 100 MHz. For speeds will not exceed 33 MHz, the DRAM's can be configured to provide three times the depth in return for the lower speed by removing the multiplexing between Groups in favor of just interleaving upon one larger Group; Bank enable bits that were used as part of the multiplexing can now be used as regular address bits to increase the size of the address space of the one Group that remains. If the testing to the DUT fits the "linear" mode of access, a twelve-fold increase in memory depth is available, even when the DUT is tested at the highest speed the tester can operate at. This eliminates the interleaving scheme in favor of addressing within a single Bank at a time. Another reconfiguration is to combine the external memory sets into one memory set that has twice the depth of either uncombined set, regardless of other (i.e., the speed related) modes of operation.申请人:Agilent Technologies, Inc.地址:395 Page Mill Road Palo Alto, CA 94306 US国籍:US代理机构:Jackson, Richard Eric 更多信息请下载全文后查看。
雷达料位计VEGAPULS67[1][1].68
![雷达料位计VEGAPULS67[1][1].68](https://img.taocdn.com/s3/m/25ed42c20c22590102029dea.png)
实用的仪表类型 对于不同的被测介质的特性和安装条件,需要相匹配的 传感器。因此 VEGAPULS67 和 68 既有螺纹连接,又有 法兰连接,同时还可以通过万向节安装。VEGAPULS68 还可以选择一体式的冷却空气连接。通过使用温度适配 器介质温度可达 200°C。VEGAPULS67 和 68 安装十分 简便,测量现场不需要其他附加工作。
对于防爆型应用,必须注意相关的接线说明。
4.3 屏蔽电缆和接地 4…20mA / HART 屏蔽电缆应该两端接地。 为了达到电位平衡,在分析处理仪表一边必须连接一个 陶瓷电容(比如:1nF,1500V)。
Profibus PA / Foundation Fieldbus FF 对于带电位补偿的系统,供电仪表、接线盒以及传感器 的屏蔽电缆直接连接接地电位。 对于不带电位补偿的系统,只有供电仪表和传感器的屏 蔽线可以直接连接接地电位,接线盒或,T 型连接器不可 以。
• 1 个 M20x1.5 电缆入口(电缆直径 5…9mm),一个盲堵 M20x1.5,插头 M12x1 用于连接 VEGADIS61(可选)
或 • 一个锁紧帽½NPT,一个盲堵½NPT,插头 M12x1 用于连接
VEGADIS61(可选) • 一个插头取决于仪表类型, 一个盲堵 M20x1.5,插头 M12x1
数字型输出信号,符合 Foundation Fieldbus 协议 符合 IEC 1158-2
初始数值 次级数值 1 次级数值 2 温度值 10mA+/- 0.5mA
过程连接到介质表面的距离 15 米
过程连接到介质表面的距离 70 米
最大 1mm 15mm
最大 1mm 15mm
天津天威有限公司
天津天威有限公司
- 1、下载文档前请自行甄别文档内容的完整性,平台不提供额外的编辑、内容补充、找答案等附加服务。
- 2、"仅部分预览"的文档,不可在线预览部分如存在完整性等问题,可反馈申请退款(可完整预览的文档不适用该条件!)。
- 3、如文档侵犯您的权益,请联系客服反馈,我们会尽快为您处理(人工客服工作时间:9:00-18:30)。
S afety instructionsVEGAMET MET391.C****TÜV09ATEX555127II(1)G[E x ia G a]IIC,II(1)D[E x ia D a]IIICI(M1)[E x ia M a]I004440324C ontentsEG-K onformitätserklärung4EC declaration of conformity4 Déclaration CE de conformité4 1A rea of applicability5 2G eneral information53T echnical data53.1A pplication conditions7 4I nstallation7P lease note:T hese safety instructions are part of the following documentation:l36032-VEGAMET391E xl40325-EC type approval certificate TÜV09ATEX5551272VEGAMET MET391.C****40324-EN-110531DE S icherheitshinweise f ür den E insatz in explosionsgefährdeten B ereichen ,verf ügbar in den S prachen deutsch ,englisch ,franz ösisch und spanisch .EN S afety instructions for the use in hazardous areas are available in G erman ,E nglish ,F rench and S panish language .FR C onsignes de sécuritépour l 'utilisation en atmosphère explosible ,disponibles dans les langues allemande ,anglaise ,française et espagnole .ES I nstrucciones de seguridad para el empleo en áreas con riesgo de explosi ón ,disponible en los siguientes idiomas alemán ,ingles ,francés y espa ñol .CZ P okud nastanou pot íže p ři čten íbezpečnostn ích upozorněn ív oti štěn ých jazyc ích ,poskytneme .V ám na základěžádosti k dispozici kopii v jazyce V a šízemě.DA H vis D e har svært ved at forståsikkerhedsforskrifterne påde trykte sprog ,kan .D e fåen kopi påD eres sprog ,hvis D e ønsker det .ELΕάνδυσκολεύεστεναδιαβάσετετιςυποδείξειςασφαλείαςστιςγλώσσεςπουήδηέχουντυπωθεί,τότεσεπερίπτωσηζήτησηςμπορούμεναθέσουμεστηδιάθεσήσαςένααντίγραφοαυτώνστηγλώσσατηςχώραςσας.ET K ui teil on raskusi tr ükitud keeltes ohutusn õuete lugemisega ,siis saadame me teie järelepärimise peale nende koopia teie riigi keeles .FI L aitteen mukana on erikielisiäturvallisuusohjeita .V oit tilata meiltääidinkieliset turvallisuu -sohjeet ,jos et selviämukana olevilla kielillä.HUH a a biztonági el őírásokat a kinyomtatott nyelveken nem tudja megfelel ően elolvasni ,akkor lépjen vel ünk kapcsolatba :azonnal a rendelkezésére bocsátunk egy példányt az Ön országában használt nyelven .IT S e le N ormative di sicurezza sono stampate in una lingua di di fficile comprensione ,potete richiederne una copia nella lingua del vostro paese .LT J ei J ums sunku suprasti saugos nuorod ųtekstąpateiktomis kalbomis ,kreipkit ės įmus ir mes J ums duosime kopijąJ ūs ųšalies kalba .LV J a J ums ir problēmas dro šības noteikumus las īt nodrukātajās valodās ,tad mēs J ums sniegsim pēc piepras ījuma kopiju J ūsu valsts valodā.MT F ’kaz li jkollok xi di ffikulta `biex tifhem listruzzjonijiet ta ’sigurta `kif ipprovduti ,infurmana u ahna nibghatulek kopja billingwa tieghek .NL A ls u moeilijkheden mocht hebben met het lezen van de veiligheidsinstructies in de afgedrukte talen ,sturen wij u op aanvraag graag een kopie toe in uw eigen taal .PL W przypadku trudno ści odczytania przepis ów bezpiecze ństwa pracy w wydrukowanych j ęzykach ,ch ętnie udost ępnimy P a ństwu kopi ęw j ęzyku obowiązującym w danym kraju .PT C aso tenha di ficuldade de ler as instruções de segurança no idioma ,no elas foram impressas ,poderásolicitar junto a n ós uma c ópia em seu idioma .SK P okia ľnastan úproblémy pri čítan íbezpečnostn ých pokynov vo vydan ých jazykoch ,poskytneme V ám na základe žiadosti k dispoz ícii k ópiu v jazyku V a šej krajiny .SL K adar se pojavijo te žave pri branju varnostnih navodil v izdanih jezikih ,vam bomo na osnovi zahtevka dali na razpolago kopijo v jeziku va še dr žave .SVO m du har problem att läsa säkerhetsanvisningarna påde här tryckta språken ,ställer vi gärna påbegäran en kopia påditt språk till f örfogande .VEGAMET MET 391.C ****340324-E N -110531EG-K onformitätserklärungEC declaration of conformityDéclaration CE de conformitéVEGA G rieshaber KGA m H ohenstein11377761S chiltachD eutschlanderklärt in alleiniger V erantwortung,dass das P roduktdeclare under our sole responsibility that our productdéclare sous sa seule responsabilitéque le produitVEGAMET MET391.C****auf das sich diese E rklärung bezieht,mit den folgenden N ormenübereinstimmtto which this declaration relates is in conformity with the following standards auquel se réfère cette déclaration est conforme aux normesEN60079-0:2009EN60079-11:2007EN60079-26:2007EN61241-11:2006EN61326-1:2006E mission:C lass B,I mmission:I ndustrialareaEN61010-1:2001gemäßden B estimmungen der R ichtlinienfollowing the provision of D irectivesconformément aux dispositions des D irectives94/9/EG2006/95/EG2004/108/EGEG B aumusterprüfbescheinigung N ummer TÜV09ATEX555127EC-T ype E xaminiation C ertificate N umber1.supplementN uméro du certificat d'examen CE de typeB enannte S telle/K ennnummer TÜV N ordC ert./0044N otified B ody/I tdentification numberO rganisme notifié/N uméro d'identificationS chiltach,15.04.11ppa.J.F ehrenbachE ntwicklungsleitungD evelopment M anagementD irecteur du service recherche et développement i.V.F rühaufL eiter Z ertifizierungC ertification M anagerD irecteur du service de certification4VEGAMET MET391.C****40324-EN-1105311A rea of applicabilityT hese safety instructions apply to the signal conditioning instruments VEGAMET MET 391.C ****according to EC type approval certi ficate T ÜV 09ATEX 55512with the 1.supplement (certi ficate number on the type label )and to all instruments with the number of the safety instruction (40324)on the type label .2G eneral informationT he VEGAMET 391signal conditioning instruments are accessory electrical devices used to process intrinsically safe 4…20m A /HART signals as well as to supply intrinsically safe sensors with power .T hey are also used to galvanically isolate intrinsically safe circuits from non -intrinsically safe circuits .I f the VEGAMET 391is used for power supply of intrinsically safe sensors that are installed and operated in hazardous areas ,the general E x mounting instructions EN 60079-14as well as these safety instructions have to be observed .T he operating instructions as well as the corresponding valid E x installation regulations or standards for electrical equipment must be observed .T he installation of explosion -endangered systems must always be carried out by quali fied personnel .3T echnical dataT he VEGAMET MET 391.C ****include non -intrinsically safe circuits and one intrinsically safe circuit .N on -intrinsically safe circuitsV oltage supply :(connections KI 3[25,26])U =20…72V AC U =20…253V DC U m =253V AC R elay outputs-R elay output 1:(connections KI 3[31,32,33])M aximum values :250V AC ,3A ,500VA 60V DC ,1A ,54W-R elay output 2:(connections KI 3[34,35,36])-R elay output 3:(connections KI 2[13,14,15])-R elay output 4:(connections KI 2[16,17,18])-R elay output 5:(connections KI 2[19,20,21])-R elay output 6:(connections KI 2[22,23,24])C urrent output :(connections KI 3[28,29])0/4…20m A U m =253VVEGAMET MET 391.C ****540324-E N -110531C ommunication circuits-RS232connection:(socket on the lower part of the housing)F or connection to an RS232interface Um=50V-E thernet connection:(socket on the lower part of the housing)F or connection to an E thernet interface Um=50V-USB connection:(socket on the lower part of the housing)F or connection to a USB interface Um=16VD igital inputs-D igital input1:(connections KI1[8,12])M aximum values:L ow-L evel:U=-3…+5V DCH igh-L evel:U=11…+30V DCU m=36V-D igital input2:(connections KI1[9,12])-D igital input3:(connections KI1[10,12])-D igital input4:(connections KI1[11,12])I ntrinsically safe circuitS ignal circuit and power supply:(connec-tions KI1[1,2])I gnition protection type intrinsic safety E x ia IIC,E x ia IIBM aximum values:Uo=24.2VIo=110m APo=662m WC haracteristics:linearEffective internal capacity Ci=0and inductance L i=0 T he permissible values for the external capacities Co and inductances L o which result from the combina-tion of C o and L o,can be found in the following chart.F or gas group IIE x ia IIC E x ia IIBP ermissible external inductance Lo0.2m H0.5m H0.5m H1m HP ermissible external capacitance Co110n F82n F540n F460n F F or gas group IE x ia IP ermissible external inductance Lo0.5m H10m HP ermissible external capacitance Co1000n F930n FW ith additionally connected VEGACONNECT(PTB07ATEX2013X):connections KI1[3,4])6VEGAMET MET391.C****40324-EN-110531S ignal circuit and power supply :(connec -tions KI 1[1,2])I gnition protection type intrinsic safety E x ia IIC ,E x ia IIBM aximum values :U o =24.2V I o =113m A P o =667m WC haracteristics :linearE ffective internal capacity C i =0and inductance L i =0T he permissible values for the external capacities C o and inductances L o which result from the combina -tion of C o and L o ,can be found in the following chart .F or gas group IIE x ia IICE x ia IIBP ermissible external inductance L o 0.2m H 0.5m H 0.5m H 1m H P ermissible external capacitance C o110n F81n F540n F460n FF or gas group IE x ia IP ermissible external inductance L o 0.5m H 10m H P ermissible external capacitance C o1000n F930n FT he intrinsically safe signal circuit and power supply is separated from the non -intrinsically safe circuits up to a peak value of the nominal voltage of 375V .3.1A pplication conditionsA mbient conditions A mbient temperature-20…+60°C (-4…+140°F )4I nstallationI f the signal conditioning instruments VEGAMET MET 391.C ****are not set up in dry and clean environments ,they must be mounted in a housing with the required protection rating .T he signal conditioning instruments VEGAMET MET 391.C ****must be operated outside hazardous areas .T he separating wall must be installed before setup .I f the intrinsically safe circuit is fed into explosive areas of zone 0/1or 20/21,please make sure that the instruments connected to these circuits meet the requirements of category 1G /2G or category 1D /2D and are appropriately certi fied .VEGAMET MET 391.C ****740324-E N -110531VEGA G rieshaber KGA m H ohenstein11377761S chiltachG ermanyP hone+49783650-0F ax+49783650-201E-mail:info@©VEGA G rieshaber KG,S chiltach/G ermany2011S ubject to change without prior notice40324-EN-110531。