氧化铝陶瓷的烧结
各类氧化物陶瓷烧结体积变化点

各类氧化物陶瓷烧结体积变化点一、概述氧化物陶瓷作为一种重要的结构材料,其烧结性能一直备受关注。
体积变化是认识氧化物陶瓷烧结行为的重要指标之一。
本文将对各类氧化物陶瓷在烧结过程中的体积变化点进行探讨。
二、硅酸盐陶瓷烧结体积变化点1. 石英陶瓷石英陶瓷在烧结过程中,通常在1200°C左右出现大小约0.2的体积收缩。
在1300°C左右会再次出现约0.5的体积收缩。
在1400°C以上,石英陶瓷的体积基本上稳定。
2. 镁铝硅酸盐陶瓷镁铝硅酸盐陶瓷在1000°C左右会出现约1的体积收缩。
在1100°C左右再度出现体积收缩,范围在0.5-1之间。
在1200°C以上,镁铝硅酸盐陶瓷的体积基本上保持稳定。
三、氧化物陶瓷烧结体积变化点1. 氧化铝陶瓷氧化铝陶瓷在1200°C左右会出现0.5-1的体积收缩。
在高温下,氧化铝陶瓷的体积基本上稳定,收缩的幅度不大。
2. 氧化锆陶瓷氧化锆陶瓷在1300°C左右会出现约0.5的体积收缩。
在1400°C以上,氧化锆陶瓷的体积基本上保持稳定。
四、复合氧化物陶瓷烧结体积变化点1. 氧化锆复合氧化钙陶瓷氧化锆复合氧化钙陶瓷在1300°C左右会出现约0.5的体积收缩。
在1400°C以上,氧化锆复合氧化钙陶瓷的体积基本上保持稳定。
2. 氧化锆复合氧化铝陶瓷氧化锆复合氧化铝陶瓷在1300°C左右会出现约1的体积收缩。
在1400°C以上,氧化锆复合氧化铝陶瓷的体积基本上保持稳定。
五、结论在烧结过程中,不同类型的氧化物陶瓷都会出现一定程度的体积收缩。
通过了解各类氧化物陶瓷在烧结过程中的体积变化点,可以更加深入地了解其烧结行为,为优化烧结工艺提供重要依据。
值得注意的是,以上数据仅供参考,实际应用中仍需根据具体情况进行调整。
希望本文对氧化物陶瓷烧结体积变化点的研究能够为相关领域的科研工作提供一定帮助。
氧化铝陶瓷的烧结方式
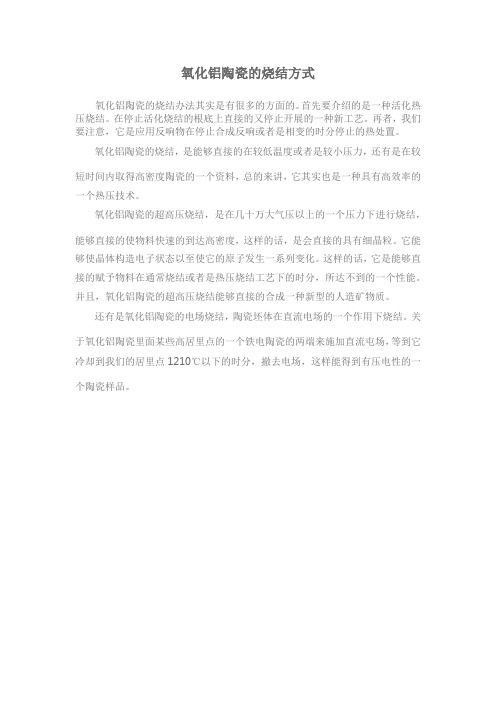
氧化铝陶瓷的烧结方式
氧化铝陶瓷的烧结办法其实是有很多的方面的。
首先要介绍的是一种活化热压烧结。
在停止活化烧结的根底上直接的又停止开展的一种新工艺。
再者,我们要注意,它是应用反响物在停止合成反响或者是相变的时分停止的热处置。
氧化铝陶瓷的烧结,是能够直接的在较低温度或者是较小压力,还有是在较短时间内取得高密度陶瓷的一个资料,总的来讲,它其实也是一种具有高效率的一个热压技术。
氧化铝陶瓷的超高压烧结,是在几十万大气压以上的一个压力下进行烧结,能够直接的使物料快速的到达高密度,这样的话,是会直接的具有细晶粒。
它能够使晶体构造电子状态以至使它的原子发生一系列变化。
这样的话,它是能够直接的赋予物料在通常烧结或者是热压烧结工艺下的时分,所达不到的一个性能。
并且,氧化铝陶瓷的超高压烧结能够直接的合成一种新型的人造矿物质。
还有是氧化铝陶瓷的电场烧结,陶瓷坯体在直流电场的一个作用下烧结。
关于氧化铝陶瓷里面某些高居里点的一个铁电陶瓷的两端来施加直流屯场,等到它冷却到我们的居里点1210℃以下的时分,撤去电场,这样能得到有压电性的一个陶瓷样品。
两步烧结

两步法烧结氧化铝陶瓷是Chen I-Wei首次试验发现,发表在Nature上,主要是用纳米粉烧结氧化镁陶瓷,通过两步法抑制晶粒长大,思想是:第一步在高温短时烧结氧化镁陶瓷,这时候要达到足够的致密度(大于90%),第二步低温长时间烧结(窗口温度),这时候晶粒几乎没有长大驱动力,但是气孔可以通过晶界扩散消除,晶界扩散需要很长的时间,最后得到晶粒细小的氧化镁陶瓷,他用的是10纳米的粉体,最终烧结的氧化镁陶瓷晶粒80纳米左右。
常规的工艺晶粒至少是微米级别的。
氧化铝陶瓷烧结动力学

如图2所示,假定颗粒是圆的,温度升高,颗粒界面相互融合,形成勃颈并不断扩大,颗粒径距缩短,气孔变小并逐渐排除,晶粒长大,体积收缩,最后形成致密体。从以上的分析可以看出,固相反应的关键是迁移,提高质点的迁移速度和效率,就能有效地促进烧结和致密过程;反之,就起阻碍作用。
3.2
3.2.1
氧化铝陶瓷烧结动力学
学号:************姓名:赵现堂
1.
氧化铝陶瓷是一种用途广泛的陶瓷。因为其三大优越的性能:第一,硬度大。经中科院上海硅酸盐研究所测定,其洛氏硬度为HRA80-90,硬度仅次于金刚石,远远超过耐磨钢和不锈钢的耐磨性能;第二,耐磨性能极好。经中南大学粉末冶金研究所测定,其耐磨性相当于锰钢的266倍,高铬铸铁的171.5倍。根据某公司跟踪调查,在同等工况下,可至少延长设备使用寿命十倍以上;第三,重量轻。其密度为3.5g/cm3,仅为钢铁的一半,可大大减轻设备负荷。所以,在现代社会氧化铝陶瓷的应用已经越来越广泛,满足于日用和特殊性能的需要。氧化铝陶瓷由于强度高、耐高温、绝缘性好、耐腐蚀,其中氧化铝陶瓷以其优良的特性如耐酸碱性、耐磨性、耐电性、机械强度高等,在工业化生产中得到了广泛的应用。
深入研究氧化铝陶瓷的生产技术及其发展,服务于生产和社会需要就显得相当重要。在氧化的。坯体烧结后,制品的显微结构及其内在性能发生了根本的改变,很难通过其它办法进行补救。因此,深入研究氧化铝陶瓷的烧结技术及影响因素,合理选择理想的烧结制度确保产品的性能、分析烧结机理、研究添加剂工作机理等对氧化铝陶瓷生产极有帮助,为氧化铝陶瓷的更广泛应用提供理论依据。
2
注浆成型是氧化铝陶瓷使用最早的成型方法。由于采用石膏模、成本低且易于成型大尺寸、外形复杂的部件。注浆成型的关键是氧化铝浆料的制备。通常以水为熔剂介质,再加入解胶剂与粘结剂,充分研磨之后排气,然后倒注入石膏模内。由于石膏模毛细管对水分的吸附,浆料遂固化在模内。空心注浆时,在模壁吸附浆料达要求厚度时,还需将多余浆料倒出。为减少坯体收缩量、应尽量使用高浓度浆料。
氧化铝陶瓷基板生产工艺
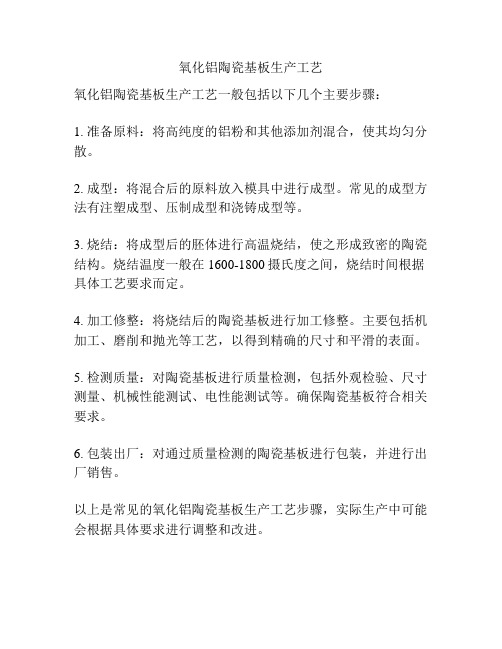
氧化铝陶瓷基板生产工艺
氧化铝陶瓷基板生产工艺一般包括以下几个主要步骤:
1. 准备原料:将高纯度的铝粉和其他添加剂混合,使其均匀分散。
2. 成型:将混合后的原料放入模具中进行成型。
常见的成型方法有注塑成型、压制成型和浇铸成型等。
3. 烧结:将成型后的胚体进行高温烧结,使之形成致密的陶瓷结构。
烧结温度一般在1600-1800摄氏度之间,烧结时间根据具体工艺要求而定。
4. 加工修整:将烧结后的陶瓷基板进行加工修整。
主要包括机加工、磨削和抛光等工艺,以得到精确的尺寸和平滑的表面。
5. 检测质量:对陶瓷基板进行质量检测,包括外观检验、尺寸测量、机械性能测试、电性能测试等。
确保陶瓷基板符合相关要求。
6. 包装出厂:对通过质量检测的陶瓷基板进行包装,并进行出厂销售。
以上是常见的氧化铝陶瓷基板生产工艺步骤,实际生产中可能会根据具体要求进行调整和改进。
三氧化二铝陶瓷标准
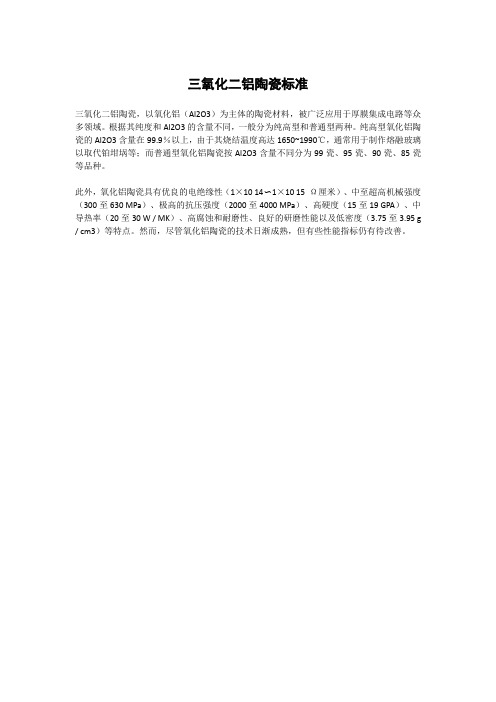
三氧化二铝陶瓷标准
三氧化二铝陶瓷,以氧化铝(Al2O3)为主体的陶瓷材料,被广泛应用于厚膜集成电路等众多领域。
根据其纯度和Al2O3的含量不同,一般分为纯高型和普通型两种。
纯高型氧化铝陶瓷的Al2O3含量在99.9%以上,由于其烧结温度高达1650~1990℃,通常用于制作熔融玻璃以取代铂坩埚等;而普通型氧化铝陶瓷按Al2O3含量不同分为99瓷、95瓷、90瓷、85瓷等品种。
此外,氧化铝陶瓷具有优良的电绝缘性(1×10 14〜1×10 15 Ω厘米)、中至超高机械强度(300至630 MPa)、极高的抗压强度(2000至4000 MPa)、高硬度(15至19 GPA)、中导热率(20至30 W / MK)、高腐蚀和耐磨性、良好的研磨性能以及低密度(3.75至3.95 g / cm3)等特点。
然而,尽管氧化铝陶瓷的技术日渐成熟,但有些性能指标仍有待改善。
96氧化铝陶瓷烧结温度

氧化铝陶瓷的烧结温度因具体类型和制造工艺的不同而有所差异。
对于Al2O3含量在99.9%以上的高纯型氧化铝陶瓷,其烧结温度可以高达1650℃以上。
然而,适当的提高烧结温度对氧化铝陶瓷的性能有积极的影响。
例如煅烧氧化铝粉末为主要原料,在1500℃、1550℃、1600℃等不同的温度下制备氧化铝陶瓷,结果表明:烧结温度对氧化铝陶瓷的体积收缩率、体积密度、吸水率和气孔率以及抗弯强度和维氏硬度都有显著影响。
值得注意的是,尽管氧化铝的熔点高达2000多度,使得氧化铝陶瓷的烧结温度普遍较高,但降低氧化铝陶瓷的烧结温度以缩短烧结周期、降低能耗、减少窑炉和窑具的损耗并降低生产成本一直是企业关注的重要问题。
为此,研究人员采取了诸如获得分散均匀、无团聚并具有良好烧结活性的超细粉体、添加适量的烧结助剂等途径来降低其烧结温度。
氧化铝烧结温度

氧化铝烧结温度
氧化铝陶瓷以其优异的性能被广泛应用在电子电器、机械、化工、冶金和航空航天等行业,成为目前世界上用量最大的特种陶瓷材料之一。
但是由于氧化铝自身阳离子电荷多、半径小、离子键强等特点,导致其晶格能较大,扩散系数较低。
烧结工艺的介绍:
1、热压烧结:高温下对样品施加单向压力,促进陶瓷达到全致密。
对于纯氧化铝陶瓷,常规烧结需要1800℃以上的温度;而20MPa的热压烧结只需要1500℃。
2、热等静压烧结:对陶瓷坯体的各个方向同时施加压力的烧结,降低陶瓷的烧结温度,同时烧结得到的陶瓷结构均匀、性能好。
3、微波加热法烧结:利用微波与陶瓷间的相互作用,因为介电作用使陶瓷内部和表面同时烧结。
4、微波等离子体烧结:与常规烧结相比,在相同的条件下能够降低烧结温度200℃,并且烧结速度快、晶粒尺寸小、机械强度高。
5、放电等离子烧结:利用脉冲能、脉冲压力产生的瞬间高温场来实现陶瓷内部晶粒的自发发热从而使晶粒活化,由于这种烧结方法升温、降温快、保温时间短,抑制了晶粒的生长、缩短了陶瓷的制备周期、节约了能源。
氧化铝陶瓷制作工艺简介
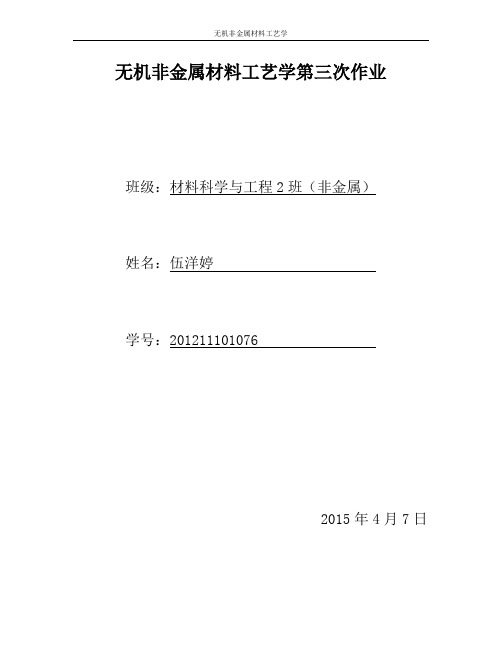
无机非金属材料工艺学无机非金属材料工艺学第三次作业班级:材料科学与工程2班(非金属)姓名:伍洋婷学号:2012111010762015年4月7日氧化铝陶瓷生产技术工艺简介氧化铝陶瓷的低温烧结技术氧化铝陶瓷是一种以Al2O3为主要原料,以刚玉(α—Al2O3)为主晶相的陶瓷材料。
一、通过提高Al2O3粉体的细度与活性降低瓷体烧结温度。
目前,制备超细活化易烧结Al2O3粉体的方法分为二大类,一类是机械法,另一类是化学法。
机械法是用机械外力作用使Al2O3粉体颗粒细化,常用的粉碎工艺有球磨粉碎、振磨粉碎、砂磨粉碎、气流粉碎等等。
通过机械粉碎方法来提高粉料的比表面积,尽管是有效的,但有一定限度,通常只能使粉料的平均粒径小至1μm左右或更细一点,而且有粒径分布范围较宽,容易带入杂质的缺点。
近年来,采用湿化学法制造超细高纯Al2O3粉体发展较快,其中较为成熟的是溶胶—凝胶法。
由于溶胶高度稳定,因而可将多种金属离子均匀、稳定地分布于胶体中,通过进一步脱水形成均匀的凝胶(无定形体),再经过合适的处理便可获得活性极高的超微粉混合氧化物或均一的固溶体。
目前此法大致有以下3种工艺流程。
(1)形成金属氧有机基络合物溶胶→水解并缩合成含羟基的三度空间高分子结构→溶胶蒸发脱水成凝胶→低温煅烧成活性氧化物粉料。
(2)含有不同金属离子的酸盐溶液和有机胶混合成溶液→溶胶蒸发脱水成凝胶→低温煅烧成粉体。
(3)含有不同金属离子的溶胶直接淬火、沉积或加热成凝胶→低温煅烧成粉体。
湿化学法制备的Al2O3粉体粒径可达到纳米级,粒径分布范围窄,化学纯度高,晶体缺陷多。
因此化学法粉体的表面能与活性比机械法粉体要高得多。
采用这种超细Al2O3粉体作原料不仅能明显降低氧化铝瓷的烧结温度(可降150℃—300℃),而且可以获得微晶高强的高铝瓷材料。
表二是日本住友化学有限公司生产的易烧结Al2O3粉料理化指标。
二、通过瓷料配方设计掺杂降低瓷体烧结温度氧化铝陶瓷的烧结温度主要由其化学组成中Al2O3的含量来决定,Al2O3含量越高,瓷料的烧结温度越高,除此之外,还与瓷料组成系统、各组成配比以及添加物种类有关。
氧化铝陶瓷的烧结工艺

氧化铝陶瓷的烧结工艺
氧化铝陶瓷的烧结工艺是指将氧化铝粉末经过加热处理使其颗粒之间形成结合,形成致密的陶瓷产品。
以下是一般的氧化铝陶瓷烧结工艺流程:
1. 原料准备:选择高纯度的氧化铝粉末作为原料,并根据产品要求加入适量的助烧剂和粘结剂。
2. 粉末制备:将原料粉末进行粉碎和混合,确保粉末颗粒的均匀分布。
3. 成型:将混合好的粉末通过压块机或注塑成型机进行成型,使其成为所需形状的陶瓷坯体。
4. 预烧:将成型后的陶瓷坯体进行预烧处理,通常在低温下进行,以去除一部分气体和挥发物,同时增强坯体的力学强度。
5. 烧结:将预烧后的陶瓷坯体进行高温烧结处理,通过控制温度、压力和烧结时间等参数,使粉末颗粒相互结合,形成致密的陶瓷体。
6. 表面处理:烧结后的陶瓷体可以通过机械加工、磨光、抛光等方法对其表面进行处理,以获得平滑的表面。
7. 检测:对成品进行质量检测,包括外观、尺寸、物理性能等方面的检测,确
保产品符合要求。
8. 包装:将合格的陶瓷产品进行包装,以便运输和储存。
以上是一般的氧化铝陶瓷烧结工艺流程,具体的烧结参数和工艺可以根据产品要求和生产设备的不同进行调整。
氧化铝陶瓷的烧结..

氧化铝陶瓷的烧结摘要:随着科学技术与制造技术日新月异的发展,氧化铝陶瓷在现代工业中得到了深入的发展和广泛的应用。
本文就氧化铝陶瓷的烧结展开论述。
主要涉及原料颗粒和烧结助剂两方面,以获得性能良好的陶瓷材料,对满足工业生产和社会需求有非常重要的意义。
关键词:氧化铝;原料颗粒;烧结助剂;1 引言在科学技术和物质文明高度发达的现代社会中,人类赖以制成各种工业产品的材料实在千差万别,但总体包括起来,无非金属、有机物及陶瓷三大类[1]。
氧化铝陶瓷是目前世界上生产量最大、应用面最广的陶瓷材料之一,具有机械强度高、电阻率高、电绝缘性好、硬度和熔点高、抗腐蚀性好、化学稳定性优良等性能,而且在一定条件下具有良好的光学性和离子导电性。
基于Al2O3陶瓷的一系列优良性能,其广泛应用于机械、电子电力、化工、医学、建筑以及其它的高科技领域[2]。
在氧化铝陶瓷的生产过程中, 无论是原料制备、成型、烧结还是冷加工, 每个环节都是不容忽视的。
目前氧化铝陶瓷制备主要采用烧结工艺[3],坯体烧结后,制品的显微结构及其内在性能发生了根本的改变,很难通过其它办法进行补救。
因此,深入研究氧化铝陶瓷的烧结技术及影响因素,合理选择理想的烧结制度确保产品的性能、分析烧结机理、研究添加剂工作机理等对氧化铝陶瓷生产极有帮助,为氧化铝陶瓷的更广泛应用提供理论依据,为服务生产和社会需要非常重要。
2 氧化铝陶瓷简介Al2O3是新型陶瓷制品中使用最为广泛的原料之一,具有一系列优良的性能[4]。
Al2O3陶瓷通常以配料或瓷体中的Al2O3的含量来分类,目前分为高纯型与普通型两种。
高纯型氧化铝陶瓷系Al2O3含量在99.9%以上的陶瓷材料。
由于其烧结温度高达1650℃~1990℃,透射波长为1μm~6μm,一般制成熔融玻璃以取代铂坩埚,利用其透光性及可耐碱金属腐蚀性用作钠灯管;在电子工业中可用作集成电路基板与高频绝缘材料。
普通型氧化铝陶瓷系Al2O3按含量不同分为99瓷、95瓷、90瓷、85瓷等品种,有时Al2O3含量在80%或75%者也划为普通氧化铝陶瓷系列。
氧化铝陶瓷烧结常见问题

氧化铝陶瓷烧结常见问题
氧化铝陶瓷烧结过程中可能会遇到的问题包括:
1. 烧结温度高:由于氧化铝的熔点高达2020℃,因此其烧结难度极大。
降低烧结温度是氧化铝陶瓷行业所关心和必需解决的问题。
2. 晶粒尺寸控制:烧结温度对晶粒生长的影响较大,而烧结时间与烧结压力的影响相对来说就比较小一些。
3. 颜色质量问题:在氧化铝陶瓷烧成后,可能会出现瓷件表面有斑点,如黑点、棕点、红点;瓷件表面产生斑块,如暗斑(阴斑),黑色云斑、亮斑等;瓷件有色差现象,如整体发黄或发灰等问题。
解决这些问题的方法包括采用热压烧结技术,即在烧结的同时施加一定的压力,使得原子的扩散速率增大,从而提高了烧结驱动力,使得烧结过程所需的时间大大减短。
此外,还可以通过获得分散均匀、无团聚,并具有良好烧结活性的超细粉体以降低陶瓷的烧结温度。
氧化铝低温 烧结综述 杨硕 139024199

安徽工业大学毕业设计实验综述论文题目:氧化铝低温烧结方法综述学院:材料学院专业:无机133班姓名:杨硕学号:139024199指导教师:二○一六年四月日氧化铝低温烧结方法综述摘要:本文就氧化铝低温烧结的研究成果做出大概的总结。
详细分析降低氧化铝烧结温度的三种主要手段(即:①加入烧结助剂;②烧结工艺;③提高氧化铝粉体活性)来具体讨论了氧化铝陶瓷低温烧结机制。
再根据之前实验提出的各种方法提出自己的实验方案,以达到对烧结温度的最大降低。
关键词:复合烧结助剂,溶胶凝胶法,液相烧结,CuO— TiO2。
氧化铝陶瓷是一种以Al2O3为主要原料,以刚玉为主晶相的陶瓷材料。
因其具有机械强度高、硬度大、高频介电损耗小、高温绝缘电阻高、耐化学腐蚀性和导热性良好等优良综合技术性能,以及原料来源广、价格相对便宜、加工制造技术较为成熟等优势,氧化铝陶瓷已被广泛应用于电子、电器、机械、化工、纺织、汽车、冶金和航天等行业,成为目前世界上用量最大的特种陶瓷材料之一。
然而,但其离子键较强,从而导致其质点扩散系数低、烧结温度较高。
(例如99氧化铝陶瓷的烧结温度可高达近1800℃)。
如此高的烧结温度将促使晶粒长大,残余气孔聚集长大,导致材料力学性能降低,同时也造成材料气密性差,且对窑炉耐火砖的损害较大。
因此,降低氧化铝陶瓷的烧结温度,降低能耗,缩短烧成周期,减少窑炉和窑具损耗,从而降低生产成本,一直是企业所关心和急需解决的重要课题。
本论文的写作来源以数据库论文为参照核心来延伸出自己的实验理论,并且总结得到更好的实验方法。
论文查找来源为,先登录安徽工业大学图书馆官网,在中文数据库中找到万方数据库,点击访问万方数据库官网,并且分别搜索“氧化铝的低温烧结”和“the low temperature sintering of Al2O3”得到论文目录,之后选取适合的文章下载阅览。
再进行总结延伸。
目前,对氧化铝陶瓷低温烧结技术的研究工作已很广泛和深入,从75 瓷到99 瓷都有系统的研究,业已取得显著成效。
氧化铝陶瓷烧结温度及时间

氧化铝陶瓷烧结温度及时间1. 烧结的基本概念说到烧结,咱们可以把它想象成一个大厨在烹饪美食,得把各种材料混合得当,火候掌握好,才能做出美味的佳肴。
对于氧化铝陶瓷来说,烧结就是把氧化铝粉末经过高温加热,促使它们之间发生化学反应,最终形成坚硬、耐磨的陶瓷材料。
想象一下,你把一堆沙子放进烤箱,经过高温处理后,居然变成了坚硬的石头,这就是烧结的魔力!不过,烧结可不是随随便便就能搞定的,它对温度和时间可有着严格的要求。
1.1 烧结温度的重要性先说温度,这玩意儿可谓是烧结过程中的灵魂。
一般来说,氧化铝陶瓷的烧结温度通常在1500°C到1700°C之间。
哇,这可真是个高温啊!不过,要是温度过低,材料的密实度就会下降,像是刚出炉的面包发酵不够,软绵绵的没法吃;而温度过高,材料又可能会变形,成了一个四不像,既不像陶瓷,也不像什么其他的东西。
温度调得不好,结果就像打麻将,三缺一,心里急得不得了。
1.2 烧结时间的巧妙把控再说说时间,这也是个关键因素。
烧结时间通常在几小时到十几个小时不等,具体得看材料的种类和烧结温度。
时间太短,材料就像没熟的鸡蛋,心里不踏实;时间太长,又可能导致材料晶粒粗大,强度下降,变得脆弱得跟薄纸一样。
因此,掌握好这个时间,就像在跳舞,要把握住节奏,才能翩翩起舞,不至于踩到自己的脚。
2. 烧结过程中的注意事项当然,烧结可不仅仅是调温和把时间抓紧,过程中还有许多小细节要注意,就像做菜时那些“秘密调料”。
2.1 材料的选择首先,原材料的选择是个大问题。
氧化铝陶瓷的质量直接和原材料息息相关,选个劣质的材料,就像用廉价的调料,做出来的菜味道差得要命。
一般来说,优质的氧化铝粉末颗粒均匀、纯度高,这样烧结出来的陶瓷才会更结实、更耐磨。
说到底,选好材料,后面的事儿就简单多了,真是一步到位,事半功倍。
2.2 气氛的控制再者,烧结气氛也是不能忽视的。
一般来说,烧结可以在氧气、氮气或者真空环境下进行,不同的气氛会影响最终产品的性能。
氧化铝陶瓷的低温烧结技术

氧化铝陶瓷的低温烧结技术氧化铝陶瓷是一种以Al2O3为主要原料,以刚玉(α—Al2O3)为主晶相的陶瓷材料。
因其具有机械强度高、硬度大、高频介电损耗小、高温绝缘电阻高、耐化学腐蚀性和导热性良好等优良综合技术性能,以及原料来源广、价格相对便宜、加工制造技术较为成熟等优势,氧化铝陶瓷已被广泛应用于电子、电器、机械、化工、纺织、汽车、冶金和航空航天等行业,成为目前世界上用量最大的氧化物陶瓷材料。
然而,由于氧化铝熔点高达2050℃,导致氧化铝陶瓷的烧结温度普遍较高(参见表一中标准烧结温度),从而使得氧化铝陶瓷的制造需要使用高温发热体或高质量的燃料以及高级耐火材料作窑炉和窑具,这在一定程度上限制了它的生产和更广泛的应用。
因此,降低氧化铝陶瓷的烧结温度,降低能耗,缩短烧成周期,减少窑炉和窑具损耗,从而降低生产成本,一直是企业所关心和急需解决的重要课题。
目前,对氧化铝陶瓷低温烧结技术的研究工作已很广泛和深入,从75瓷到99瓷都有系统的研究,业已取得显著成效。
表一是已实现的各类氧化铝陶瓷低温烧结情况。
表中低温烧结氧化铝陶瓷的各项机电性能均达到了相应瓷种的国家标准,甚至中铝瓷在某些技术标准上超过高铝瓷的国标,如中科院上海硅酸盐研究所研制的1360℃烧成的85瓷,其抗弯强度超过99%Al2O3陶瓷的国标,各项电性能都优于95%Al2O3瓷的国标;Al2O3含量分别为90%和95%的低温烧结陶瓷,其机电性能都优于95瓷及99瓷的国标。
纵观当前各种氧化铝瓷的低温烧结技术,归纳起来,主要是从原料加工、配方设计和烧成工艺等三方面来采取措施,下面分别加以概述。
一、通过提高Al2O3粉体的细度与活性降低瓷体烧结温度。
与块状物相比,粉体具有很大的比表面积,这是外界对粉体做功的结果。
利用机械作用或化学作用来制备粉体时所消耗的机械能或化学能,部分将作为表面能而贮存在粉体中,此外,在粉体的制备过程中,又会引起粉粒表面及其内部出现各种晶格缺陷,使晶格活化。
萍乡75氧化铝烧结温度和时间
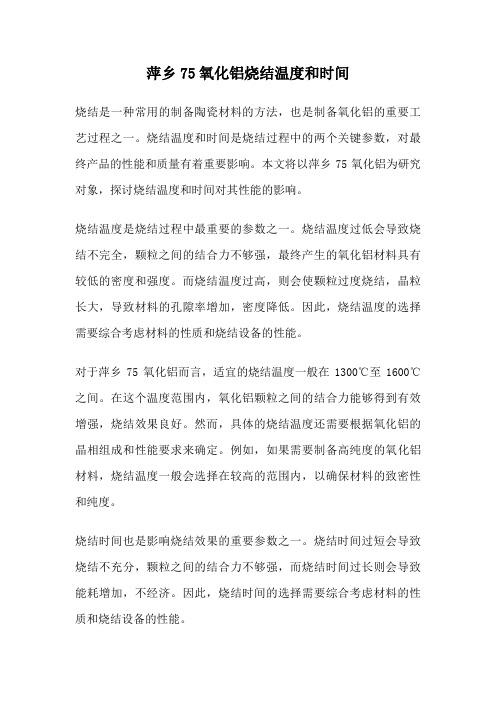
萍乡75氧化铝烧结温度和时间烧结是一种常用的制备陶瓷材料的方法,也是制备氧化铝的重要工艺过程之一。
烧结温度和时间是烧结过程中的两个关键参数,对最终产品的性能和质量有着重要影响。
本文将以萍乡75氧化铝为研究对象,探讨烧结温度和时间对其性能的影响。
烧结温度是烧结过程中最重要的参数之一。
烧结温度过低会导致烧结不完全,颗粒之间的结合力不够强,最终产生的氧化铝材料具有较低的密度和强度。
而烧结温度过高,则会使颗粒过度烧结,晶粒长大,导致材料的孔隙率增加,密度降低。
因此,烧结温度的选择需要综合考虑材料的性质和烧结设备的性能。
对于萍乡75氧化铝而言,适宜的烧结温度一般在1300℃至1600℃之间。
在这个温度范围内,氧化铝颗粒之间的结合力能够得到有效增强,烧结效果良好。
然而,具体的烧结温度还需要根据氧化铝的晶相组成和性能要求来确定。
例如,如果需要制备高纯度的氧化铝材料,烧结温度一般会选择在较高的范围内,以确保材料的致密性和纯度。
烧结时间也是影响烧结效果的重要参数之一。
烧结时间过短会导致烧结不充分,颗粒之间的结合力不够强,而烧结时间过长则会导致能耗增加,不经济。
因此,烧结时间的选择需要综合考虑材料的性质和烧结设备的性能。
对于萍乡75氧化铝而言,一般的烧结时间在2至4小时左右。
在这个时间范围内,氧化铝颗粒能够得到充分烧结,晶粒之间的结合力得到增强。
然而,具体的烧结时间还需要根据氧化铝的晶相组成和性能要求来确定。
如果需要制备具有特殊性能的氧化铝材料,例如高强度、高导热性等,可以适当延长烧结时间,以进一步改善材料的性能。
除了烧结温度和时间外,烧结过程中还有一些其他的影响因素需要考虑。
例如,烧结气氛、烧结速率、烧结压力等都会对最终产品的性能产生影响。
因此,在进行烧结实验或工业生产时,需要综合考虑这些因素,并进行合理的控制和调节。
萍乡75氧化铝的烧结温度和时间是影响最终产品性能的重要参数。
在制备过程中,需要根据材料的性质和要求,选择适宜的烧结温度和时间,以获得理想的烧结效果和材料性能。
氧化铝陶瓷的烧结
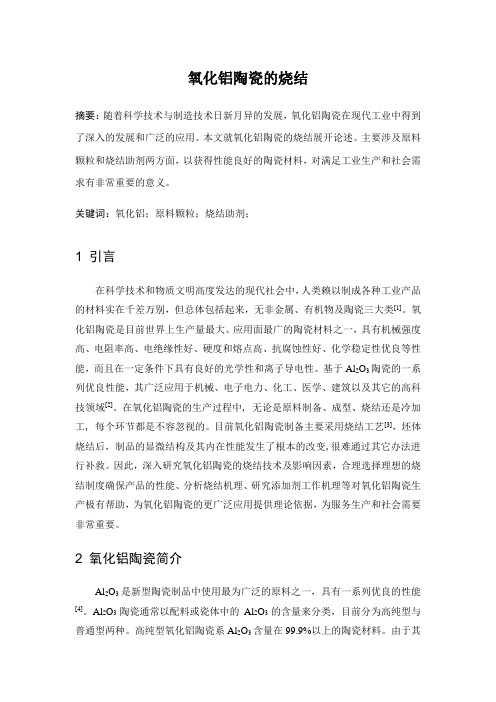
氧化铝陶瓷的烧结摘要:随着科学技术与制造技术日新月异的发展,氧化铝陶瓷在现代工业中得到了深入的发展和广泛的应用。
本文就氧化铝陶瓷的烧结展开论述。
主要涉及原料颗粒和烧结助剂两方面,以获得性能良好的陶瓷材料,对满足工业生产和社会需求有非常重要的意义。
关键词:氧化铝;原料颗粒;烧结助剂;1 引言在科学技术和物质文明高度发达的现代社会中,人类赖以制成各种工业产品的材料实在千差万别,但总体包括起来,无非金属、有机物及陶瓷三大类[1]。
氧化铝陶瓷是目前世界上生产量最大、应用面最广的陶瓷材料之一,具有机械强度高、电阻率高、电绝缘性好、硬度和熔点高、抗腐蚀性好、化学稳定性优良等性能,而且在一定条件下具有良好的光学性和离子导电性。
基于Al2O3陶瓷的一系列优良性能,其广泛应用于机械、电子电力、化工、医学、建筑以及其它的高科技领域[2]。
在氧化铝陶瓷的生产过程中, 无论是原料制备、成型、烧结还是冷加工, 每个环节都是不容忽视的。
目前氧化铝陶瓷制备主要采用烧结工艺[3],坯体烧结后,制品的显微结构及其内在性能发生了根本的改变,很难通过其它办法进行补救。
因此,深入研究氧化铝陶瓷的烧结技术及影响因素,合理选择理想的烧结制度确保产品的性能、分析烧结机理、研究添加剂工作机理等对氧化铝陶瓷生产极有帮助,为氧化铝陶瓷的更广泛应用提供理论依据,为服务生产和社会需要非常重要。
2 氧化铝陶瓷简介Al2O3是新型陶瓷制品中使用最为广泛的原料之一,具有一系列优良的性能[4]。
Al2O3陶瓷通常以配料或瓷体中的Al2O3的含量来分类,目前分为高纯型与普通型两种。
高纯型氧化铝陶瓷系Al2O3含量在99.9%以上的陶瓷材料。
由于其烧结温度高达1650℃~1990℃,透射波长为1μm~6μm,一般制成熔融玻璃以取代铂坩埚,利用其透光性及可耐碱金属腐蚀性用作钠灯管;在电子工业中可用作集成电路基板与高频绝缘材料。
普通型氧化铝陶瓷系Al2O3按含量不同分为99瓷、95瓷、90瓷、85瓷等品种,有时Al2O3含量在80%或75%者也划为普通氧化铝陶瓷系列。
氧化铝陶瓷干压坯体的烧结探讨.ppt

2.烧结曲线的实践探索
• 2. 1 瓷件开裂
观察图3实测曲线,看到200—700℃升温速率为7.17℃/min,700— 1349℃升温速率为9.27℃/min,曲线出现陡坡,即温度突升段。此段升温 速率按经验应在1—4℃/min为宜,可见此段温升严重过速。而此段正处窑 炉预热段,坯体水份蒸发有机物分解汽化的高速率阶段,所以坯体开裂的 原因即在于此段温升过速。鉴于此,我们根据窑炉情况,拟出了建议曲线 。曲线见图3。建议曲线主要是将入口至①热电偶处的曲线改为近似斜直 线,使升温变得均匀平缓。
今年初,某新建陶瓷企业出现了严重的瓷件阴斑情况。窑炉为推板窑。 肉眼观察到窑炉内灰蒙蒙,看不见光亮的烧成带。后加大烟囱抽力, 在烟道上加风扇抽风,炉内逐渐变得清亮。可以看到坯体释放的烟气 顺利地被烟囱抽出。瓷件阴斑逐渐变轻,大部分瓷件阴斑消失。说明 加大通风不仅保证了窑炉内完全的氧化气氛,防止有机物碳化,同时 将烟气排出,防止烟气中的有机物质的分解物、化合物在瓷件表面的 沉淀。
3.结论
• ①干压坯体由于含有1.5—4%的水分、有机物,所以在烧结的初始阶 段,升温速度要缓慢、平滑,要避免出现温度的突升段(点)。否则 急剧的水分蒸发和有机物分解形成的坯内高气压会使坯体发生开裂。 • ②干压坯体由于构成其的粉料很细,出现易烧结特性,所以要在较低 温度烧结;高温过烧,会使瓷件变坏。 • ③由于①所述同样的原因,干压坯体在水气蒸发有机物分解时所释放
前言
目前,陶瓷干压工艺发展出现突飞猛进局面 ,其推力在于:
• • • • • 热压铸工艺脱蜡过程空气污染被限制 热压铸工艺工序繁杂,用工多,招工难 原料造粒粉和模具制作已充分专业化市场化,质量在不断提高 干压工效高,用工少,污染少 干压成本相对降低,甚至还低于热压铸工艺
- 1、下载文档前请自行甄别文档内容的完整性,平台不提供额外的编辑、内容补充、找答案等附加服务。
- 2、"仅部分预览"的文档,不可在线预览部分如存在完整性等问题,可反馈申请退款(可完整预览的文档不适用该条件!)。
- 3、如文档侵犯您的权益,请联系客服反馈,我们会尽快为您处理(人工客服工作时间:9:00-18:30)。
氧化铝陶瓷的烧结摘要:随着科学技术与制造技术日新月异的发展,氧化铝陶瓷在现代工业中得到了深入的发展和广泛的应用。
本文就氧化铝陶瓷的烧结展开论述。
主要涉及原料颗粒和烧结助剂两方面,以获得性能良好的陶瓷材料,对满足工业生产和社会需求有非常重要的意义。
关键词:氧化铝;原料颗粒;烧结助剂;1 引言在科学技术和物质文明高度发达的现代社会中,人类赖以制成各种工业产品的材料实在千差万别,但总体包括起来,无非金属、有机物及陶瓷三大类[1]。
氧化铝陶瓷是目前世界上生产量最大、应用面最广的陶瓷材料之一,具有机械强度高、电阻率高、电绝缘性好、硬度和熔点高、抗腐蚀性好、化学稳定性优良等性能,而且在一定条件下具有良好的光学性和离子导电性。
基于Al2O3陶瓷的一系列优良性能,其广泛应用于机械、电子电力、化工、医学、建筑以及其它的高科技领域[2]。
在氧化铝陶瓷的生产过程中, 无论是原料制备、成型、烧结还是冷加工, 每个环节都是不容忽视的。
目前氧化铝陶瓷制备主要采用烧结工艺[3],坯体烧结后,制品的显微结构及其内在性能发生了根本的改变,很难通过其它办法进行补救。
因此,深入研究氧化铝陶瓷的烧结技术及影响因素,合理选择理想的烧结制度确保产品的性能、分析烧结机理、研究添加剂工作机理等对氧化铝陶瓷生产极有帮助,为氧化铝陶瓷的更广泛应用提供理论依据,为服务生产和社会需要非常重要。
2 氧化铝陶瓷简介Al2O3是新型陶瓷制品中使用最为广泛的原料之一,具有一系列优良的性能[4]。
Al2O3陶瓷通常以配料或瓷体中的Al2O3的含量来分类,目前分为高纯型与普通型两种。
高纯型氧化铝陶瓷系Al2O3含量在99.9%以上的陶瓷材料。
由于其烧结温度高达1650℃~1990℃,透射波长为1μm~6μm,一般制成熔融玻璃以取代铂坩埚,利用其透光性及可耐碱金属腐蚀性用作钠灯管;在电子工业中可用作集成电路基板与高频绝缘材料。
普通型氧化铝陶瓷系Al2O3按含量不同分为99瓷、95瓷、90瓷、85瓷等品种,有时Al2O3含量在80%或75%者也划为普通氧化铝陶瓷系列。
Al2O3陶瓷的机械强度极高,导热性能良好,绝缘强度、电阻率高,介质损耗低,其中99氧化铝瓷材料用于制作高温坩埚、耐火管及特殊耐磨材料,如陶瓷轴承、陶瓷密封件及水阀片等。
95氧化铝瓷主要用作耐腐蚀、耐磨部件,85瓷中由于常掺入部分滑石粉,提高了电性能与机械强度,可与钼、铌、钽等金属封接,有的用作电真空装置器件[5]。
Al2O3有许多同质异晶体,根据研究报道至少有10多种,说法不太一致。
这些变体中最常见的是α-Al2O3、β-Al2O3和γ-Al2O3三种,其余的主要是铝土矿热分解过程中的过渡相。
它们在1200℃以上几乎全部不可逆的转变为α-Al2O3[6]。
其晶体结构如图1所示,属三方柱状晶体,它是用途最广泛,原料最丰富,价格最低廉的一种高温结构陶瓷。
由于α-Al2O3具有熔点高,硬度大,耐化学腐蚀,优良的介电性,是氧化铝各种型态中最稳定的晶型,也是自然界中惟一存在的氧化铝的晶型,如天然刚玉、红宝石等。
用α-Al2O3为原料制备的氧化铝陶瓷材料,其机械性能、高温性能、介电性能及耐化学腐蚀性能都是非常优异的[7]。
图1 Al2O3的晶体结构3 氧化铝陶瓷的烧结烧结就是将粉末或者粉末压坯加热到低于其中基本成分的熔点温度,然后以一定的方法和速度冷却到室温的过程。
烧结的目的是使粉末颗粒之间发生粘结,烧结体的强度增加,把粉末颗粒的聚集体变为晶粒的聚集体,来获得所需的物理、机械性能的制品或材料[8]。
3.1 烧结理论简述当对固态素坯进行高温加热时,素坯中的颗粒发生物质迁移,达到某一温度后坯体发生收缩,出现晶粒长大,伴随气孔排除,最终在低于熔点的温度下,素坯变成致密的多晶陶瓷材料。
烧结而导致材料致密化的基本推动力是系统表面能的下降,因为素坯中粉末颗粒(通常为亚微米级甚至纳米级)具有较大的表面积,因而有较高的表面能。
任何系统都有向最低能量状态转化的趋势,因此表面能的降低,就可作为烧结的推动力。
陶瓷烧结依据是否产生液相分为固相烧结和液相烧结。
对于离子键结合的许多烧结活性好的的氧化物超细粉末,如Al2O3、ZrO2可实现固相烧结;但对于共价键为主的非氧化物陶瓷,如Si3N4,SiC,AlN,B4C等通常要加入适量的烧结助剂,通过形成液相来实现致密烧结。
液相烧结分为颗粒重排、溶解-沉淀和后期固体骨架聚合3个阶段。
初期的颗粒重排过程为液相填充气孔,液相量越多,相对密度越大。
溶解-沉淀过程小晶粒溶解于液相中并沉积到大颗粒表面,在此过程中如液相太多,则会出现晶粒异常长大或二次再结晶[9]。
氧化铝陶瓷烧结体的显微结构如图2所示。
图2 氧化铝陶瓷烧结体的显微结构烧结过程中通常发生三种主要变化:1)晶粒尺寸及密度的增大;2)气孔形状的变化;3)气孔尺寸和数量的变化,通常使气孔率减小。
对于致密陶瓷材料,相对密度一般可达到98%以上,而对于透明陶瓷要求烧结后陶瓷内部气孔率趋近于零[10]。
烧结可以分为初期、中期和后期三个阶段,如图3所示。
图3 烧结过程示意图烧结前成型体中颗粒堆积情况,有的接触,有的分开,空隙较多;初期(a →b ):只能使成型体中颗粒重排,空隙变形和缩小,总面积不减少,不能最终填满空隙;即:烧结随温度升高和时间延长,开始产生颗粒间键合和重排,颗粒靠拢,大空隙消失,气孔总体积减少,离子间以点接触为主,总面积未缩小;中期(b →c ):是最终排除气孔,使形成致密排列。
即:开始有明显传质过程,颗粒由点接触扩大到面接触,粒界面积增加,固气表面积相应减少,空隙仍连通;后期(c →d ):一般发生了相变,使物质密度进一步增加。
随传质继续,粒界进一步扩大,气孔逐渐缩小和变形,最终转变为孤立闭气孔,颗粒界开始移动,气孔逐渐迁移到粒界上最后消失,烧结体致密度增高。
根据singh 提出的烧结初期动力学过程,研究陶瓷系统的烧结激活能的大小: k t n L L g lg lg /l 0+=∆ (1))/exp(k RT Q A -= (2) 式中:ΔL/L为样品的线收缩率;t 为烧结时间(保温时间);n 为反应级数;K 为烧结速率常数;Q 为该组成的烧结激活能;T 为绝对温度;A 为与界面张力、扩散系数和颗粒半径相关的常数;R 为气体常数。
根据Kingery W D 最早提出的烧结模型,他将烧结的中后期分为颗粒的重排和溶解-沉淀两个过程,同时他提出的烧结中后期致密理论模型如下:313431100206t r RT V Dc L L LV -⎪⎪⎭⎫ ⎝⎛=∆κγδκ式中:△L/L0为样品烧结后的线收缩率;r 为颗粒直径;δ为液膜厚度;D 为扩散系数;k 1,k 2为比例系数;c 0为原始元素的浓度;γLV 为液-气表面能;R 为气体常数;T 为绝对温度;t 为烧结时间。
3.2 氧化铝陶瓷烧结工艺氧化铝陶瓷离子键较强,导致其质点的扩散系数低(Al 3+在1700℃时扩散系数仅为10-11cm 2·S -)、烧结温度高(99氧化铝的烧结温度高达1800℃)。
如此高的烧结温度使晶粒急剧生长,残余气孔聚集长大,从而导致材料的力学性能降低。
同时也使材料气密性变差,并加大对窑炉耐火砖的损害。
因此,降低氧化铝陶瓷的烧结温度是氧化铝陶瓷行业所关心和必需解决的问题[11]。
对于陶瓷材料,一般采用两种途径来降低其烧结温度一种途径是通过获得分散均匀、无团聚,并具有良好烧结活性的超细粉体以降低陶瓷的烧结温度;另一种降低陶瓷材料烧结温度的方法,是添加适量的烧结助剂。
3.2.1 细化原料颗粒采用晶粒小、比表面积大、表面活性高的单分散超细Al 2O 3粉料,由于颗粒间扩散距离短,仅需较低的烧结温度和烧结活化能,颗粒越细,就越容易烧结, 烧结温度也就越低。
粉体颗粒尺寸与烧结温度的关系如表1。
表1 粉体颗粒尺寸与烧结温度的关系(烧结扩散活化能 Q = 418KJ/mol )另外根据 Herring 规则,在相同的烧结温度下,具有不同颗粒尺寸(r 1,r 2)的粉料,烧结至相同的密度,各自所需的烧结时间t 1,t 2与颗粒尺寸的关系为:⎪⎪⎭⎫ ⎝⎛=2121r r n t t 4~3=n可见,颗粒越细,烧结时间越短。
粉体颗粒越细,缺陷越多,活性也越大,可促进烧结,制成的陶瓷强度也越高。
小颗粒还可以分散由刚玉和玻璃相线膨胀系数不同在晶界处造成的应力集中,减少开裂的危险性;细的晶粒还能妨碍微裂纹的发展,不易造成穿晶断裂,有利于提高断裂韧性;另外还可提高材料的耐磨性。
因此,降低Al2O3粉体粒度,对制备高性能的Al2O3制品具有重要意义。
目前,制备超细活化易烧结Al2O3粉体的方法分为两大类,一类是机械法,另一类是化学法。
机械法是用机械外力作用使Al2O3粉料颗粒细化,常用的粉碎工艺有球磨粉碎、振磨粉碎、砂磨粉碎、气流粉碎等,其中砂磨是制备超细陶瓷粉体的有效途径之一。
近年来,采用湿化学法制备超细高纯粉体技术得到较快发展,其中较为成熟的是溶胶-凝胶法,可以制备传统方法无法制备的材料。
溶胶高度稳定,可将多种金属离子均匀、稳定地分布于胶体中,通过进一步脱水形成均匀的凝胶(无定形体),再经过合适的处理便可获得活性极高的超微粉混合氧化物或均一的固溶体[12]。
3.2.2 添加烧结助剂添加剂就其作用来说,归纳起来可以分为两大类:一类是与Al2O3生成固溶体,一类是能生成液相。
第一类添加剂为变价氧化物,有TiO2、Cr2O3、Fe2O3与MnO2等。
由于其晶体结构和晶格常数与Al2O3相接近,因此,通常能与Al2O3生成固溶Al2O3晶格产生缺陷,活化晶格,促进烧结。
研究表明,这类添加剂促进烧结,具有如下的规律性:第一,凡是能与Al2O3形成有限固溶体的添加剂,比形成连续固溶体的作用大,这可能是形成有限固溶体的离子半径与Al3+离子半径相差较大,这样使晶格更易变形,从而促进烧结;第二,具有可变电价的添加剂,比不能变价的添加剂的作用大;第三,凡是阳离子的电子层结构为非惰性气体型,即阳离子电价高的添加剂作用较大。
第二类添加剂其作用是由于生成液相,降低烧成温度而促进Al2O3的烧结。
这一类添加剂有高岭土、SiO2、CaO、MgO等。
氧化铝原料或多或少地带入氧化钠、氧化硅等杂质。
为了降低氧化铝瓷的烧结温度,应引入某些氧化物或硅酸盐液相。
氧化物添加剂在烧结时易形成熔剂,促进烧结。
由于出现液相,即液相对固相的表面润湿力和表面张力,使固相粒子靠紧并填充气孔。
加入的细粒外加剂,可以均匀地被Al2O3吸附,降低表面能,因而能延缓Al2O3的晶粒长大。
比较传统的Al2O3烧结添加剂是MgO。
Al2O3与MgO生成二元、三元或更复杂的低熔物。
高纯Al2O3烧结过程中加入少量MgO(加入量为0.05~0.25wt%)可有效抑制晶粒过分长大。