Working and Manufacturing Procedures
工厂布局和物料路径(英文版)

工厂布局和物料路径(英文版)Factory Layout and Material FlowIntroductionFactory layout and material flow are crucial elements in the efficient operation of a manufacturing facility. They refer to the arrangement of machinery, equipment, and workspaces within a factory, as well as the movement of materials throughout the production process. A well-designed factory layout and material flow can enhance productivity, minimize production costs, and optimize the use of available space. This article will discuss the key considerations and strategies involved in designing an effective factory layout and material flow.Factory Layout ConsiderationsWhen designing a factory layout, several key considerations need to be taken into account:1. Production Process: The layout should support the most efficient production process flow. This involves identifying the sequence of operations and organizing the workstations accordingly. For example, if the production process involves multiple assembly steps, it would be ideal to arrange the workstations in a linear fashion, enabling materials to move seamlessly from one station to the next.2. Space Utilization: The layout should make efficient use of available space. This can be achieved through careful planning and utilization of vertical space. For instance, vertical storage systems and mezzanine floors can be used to maximize storage capacityand free up floor space for production activities.3. Safety Measures: Occupational safety is of utmost importance in any manufacturing facility. The layout should incorporate safety measures, such as clear walkways, safety barriers, and proper ventilation, to ensure a safe working environment.4. Flexibility: The factory layout should be flexible enough to accommodate changes in production demand or process modifications. This can be achieved by using modular or movable equipment and workstations, allowing for easy reconfiguration. Material Flow StrategiesEfficient material flow is essential for minimizing production downtime, reducing inventory levels, and optimizing overall production efficiency. Several strategies can be employed to achieve this:1. Lean Manufacturing: Adopting lean manufacturing principles can significantly improve material flow. This involves analyzing the value stream and eliminating waste, such as unnecessary movement and transportation of materials. Implementing tools and techniques like Just-in-Time (JIT) inventory management and Kanban systems can help streamline material flow.2. Single Piece Flow: Single piece flow, also known as one-piece flow, entails moving one item at a time through the production process. This strategy helps identify and resolve bottlenecks, reduces inventory levels, and improves overall production efficiency.3. Material Handling Equipment: The appropriate selection and use of material handling equipment can greatly enhance material flow. Forklifts, conveyors, automated guided vehicles (AGVs), and robotics can be used to transport materials efficiently between workstations.4. Kanban System: A Kanban system is a visual method used to control production and inventory levels. It involves using cards or containers to signal the need for a replenishment of materials. This ensures a smooth material flow and prevents overproduction or stockouts.ConclusionDesigning an effective factory layout and material flow involves careful consideration of production processes, space utilization, safety measures, and flexibility. Implementing strategies such as lean manufacturing, single piece flow, and the use of appropriate material handling equipment can greatly improve material flow and overall production efficiency. By investing time and effort into designing and optimizing these aspects, manufacturers can enhance productivity, reduce costs, and maintain a competitive edge in today's demanding market.Factory Layout Considerations:In addition to the considerations mentioned earlier, here are a few more factors to consider when designing a factory layout:5. Workstation Ergonomics: The layout should prioritize the ergonomics of workstations to ensure the comfort and safety of workers. This includes considering factors such as workstation height, accessibility of tools and equipment, and minimizingrepetitive or strenuous motions.6. Material Flow Analysis: A thorough analysis of the material flow is essential for designing an efficient layout. This involves identifying potential bottlenecks, congestion points, and unnecessary movements of materials. By optimizing the material flow, production efficiency can be improved, and waiting times can be minimized.7. Maintenance Access: The layout should provide easy access to machinery and equipment for maintenance purposes. This includes ensuring sufficient space for maintenance personnel to work comfortably and ensuring that equipment can be easily moved or replaced when necessary.8. Future Expansion: It is important to consider the possibility of future expansion when designing the factory layout. This can be done by leaving available space for future equipment, ensuring the layout can accommodate increased production capacity, and considering the impact on material flow when expanding the facility.Material Flow Strategies:Let's delve deeper into the strategies that can be employed to optimize material flow within a manufacturing facility:5. Value Stream Mapping: A value stream map is a visual tool that helps identify the steps and processes involved in delivering a product to the customer. By analyzing the value stream, inefficiencies and waste can be identified and targeted forimprovement, ultimately leading to a smoother material flow.6. Batch Size Reduction: Reducing batch sizes can help reduce lead time and inventory levels, and improve material flow. By producing smaller batches, companies can respond to changes in customer demand more effectively and minimize the need for excess inventory.7. Standardized Work: Implementing standardized work processes can help streamline material flow. By establishing standard operating procedures and work instructions, employees can perform tasks consistently and efficiently, reducing variability and delays in material handling.8. Cross-Training: Cross-training employees to perform multiple tasks can help reduce bottlenecks and ensure a smooth material flow. By having a workforce that is versatile and capable of performing various tasks, the dependence on specific individuals can be minimized.9. Visual Management: The use of visual management techniques, such as clear signage, labels, and color-coding, can greatly improve material flow. These visual cues help employees quickly identify and locate materials, reducing search times and errors. 10. Continuous Improvement: Continuous improvement methodologies, such as Kaizen and Six Sigma, can be applied to continuously optimize material flow. By regularly analyzing and improving processes, companies can identify and eliminate waste, improve cycle times, and enhance overall efficiency.Conclusion:In conclusion, designing an effective factory layout and optimizing material flow are crucial for maximizing productivity and minimizing costs. By considering factors such as production processes, space utilization, safety measures, and flexibility, companies can create a layout that supports efficient operations. Implementing strategies like lean manufacturing, single piece flow, and the use of appropriate material handling equipment can further enhance material flow. By continuously analyzing and improving material flow, companies can achieve higher efficiency levels, reduce lead times, and maintain a competitive edge in the market.。
生产流程的英文专业术语

生产流程的英文专业术语Certainly, I will provide you with an English essay on the topic of "Technical Terminology in Production Processes" that meets your requirements.The production process is a complex and intricate series of steps that transform raw materials into finished products. Each stage of the production process involves specialized terminology that is essential for effective communication and understanding among industry professionals. These technical terms are crucial for describing the various components, equipment, and procedures involved in the manufacturing of goods.One of the fundamental concepts in production is the raw material. Raw materials are the unprocessed natural or synthetic substances that serve as the starting point for the manufacturing process. These materials can include metals, plastics, textiles, chemicals, and a wide range of other substances. The term "feedstock" is often used interchangeably with raw materials, referring to the input materials that are fed into the production system.The next step in the production process is the procurement of theseraw materials. Procurement involves the acquisition and delivery of the necessary raw materials to the manufacturing facility. This process may involve negotiating contracts with suppliers, arranging for transportation, and ensuring the timely delivery of the materials. The term "sourcing" is commonly used to describe the process of identifying and securing reliable suppliers of raw materials.Once the raw materials have been procured, they must be prepared for the manufacturing process. This preparation stage is known as preprocessing, and it may involve activities such as cutting, shaping, or mixing the materials to meet specific requirements. The term "pretreatment" is often used to describe the various processes that are performed on the raw materials before they enter the main production line.The actual manufacturing process is where the transformation of raw materials into finished products takes place. This stage is often referred to as the "production line" or the "assembly line," and it involves a series of carefully orchestrated steps. Each step in the production process is known as an "operation," and these operations may include activities such as molding, casting, welding, painting, or packaging.To ensure the efficient and consistent execution of these operations, manufacturers often employ various production control techniques.One such technique is known as "process control," which involves the monitoring and adjustment of process parameters to maintain the desired product quality and consistency. Another important concept in production control is "quality assurance," which encompasses the systematic procedures and activities that are implemented to ensure that the final product meets the required standards and specifications.In addition to the production process itself, there are also various supporting systems and infrastructure that are essential for the smooth operation of a manufacturing facility. One such system is the "material handling system," which is responsible for the movement and storage of raw materials, work-in-progress, and finished goods within the production environment. This system may include conveyors, cranes, forklifts, and other specialized equipment.Another important aspect of production is the maintenance of the manufacturing equipment and machinery. This is known as "preventive maintenance," and it involves the scheduled inspection, servicing, and repair of equipment to prevent breakdowns and ensure optimal performance. The term "predictive maintenance" is also used to describe the use of advanced monitoring and analysis techniques to predict and prevent equipment failures.Finally, the successful management of a production process requiresthe integration of various information systems and data-driven decision-making. This is where the concept of "production planning and control" comes into play. Production planning and control involves the use of sophisticated software and algorithms to optimize the production schedule, inventory management, and resource allocation based on real-time data and forecasting models.In conclusion, the technical terminology used in the production process is a critical component of effective communication and efficient manufacturing operations. From raw materials to production control, maintenance, and information systems, each stage of the production process is characterized by specialized terminology that is essential for industry professionals to understand and apply effectively.。
Unit_6_Manufacturing_Process_(1)

Unit 6 Manufacturing Process (1)生产过程(1)一、New words and expressions二、TranslationComputer-Aided Manufacturing计算机辅助制造1、The scientific study of metal-cutting and automation techniques is products of the twentieth century. 金属切削和自动化技术的科学研究时二十世纪的产物。
automation 自动化techniques 技术技巧手法Two pioneers of these techniques were Frederick Taylor and Henry Ford. Frederick Taylor和Henry Ford是这些技术的两个先驱。
pioneer 先驱开拓者先锋During the early 1900s, the improving U.S. standard of living brought a new high in personal wealth. 在十九世纪的早期,美国日益提高的生活水平将个人财富带到了一个新的高度。
improve改善改进提高standard 标准水平规范bring(brought)带来产生促进personal 个人wealth 财富The major result was the increased demand for durable goods. 这种现象主要影响就是对耐用消费品的需求的增长。
demand 需求需要durable耐用经久结实durablegood 耐用消费品This increased demand meant that manufacturing could not longer be treated as a blacksmith trade, and the use of scientific study was employed in manufacturing analysis. 日益增长的需求意味着制造业不再是简单的手工作坊式的行业,而应该在制造业中引入科学化的研究手段。
无菌工艺模拟试验指南 英语

无菌工艺模拟试验指南英语Aseptic Processing Simulation Test GuideAseptic processing is a critical aspect of pharmaceutical and medical device manufacturing, ensuring the sterility and safety of products. The implementation of a comprehensive aseptic processing simulation test is essential to validate the effectiveness of the aseptic techniques and procedures employed in the production environment. This guide provides a detailed overview of the key elements and considerations for conducting a successful aseptic processing simulation test.The primary objective of an aseptic processing simulation test is to assess the ability of the manufacturing personnel to maintain sterile conditions throughout the entire production process. This includes the proper gowning procedures, aseptic manipulations, equipment handling, and environmental monitoring. The simulation test should closely mimic the actual production process, allowing for the identification and resolution of any potential weaknesses or areas of improvement.One of the crucial components of the aseptic processing simulationtest is the selection of the appropriate microbiological media and challenge organisms. The media should be capable of supporting the growth of a wide range of microorganisms, including bacteria, yeasts, and molds. The challenge organisms should be representative of the potential contaminants that may be encountered in the production environment. Common examples include Bacillus subtilis, Staphylococcus aureus, and Candida albicans.The simulation test should be designed to evaluate the entire aseptic process, from the initial gowning and preparation of the work area to the final product handling and packaging. This includes the assessment of the following key elementsGowning ProceduresThe proper donning and doffing of the required personal protective equipment (PPE), such as sterile gowns, gloves, masks, and head coverings, is crucial to maintaining the sterile environment. The simulation test should assess the ability of the personnel to correctly don and remove the PPE without compromising the sterile integrity.Aseptic ManipulationsThe simulation test should evaluate the personnel's ability to perform aseptic manipulations, such as the transfer of materials, the handling of equipment, and the execution of critical process steps. This includes the assessment of hand-eye coordination, dexterity,and adherence to established aseptic techniques.Environmental MonitoringThe simulation test should incorporate environmental monitoring to assess the cleanliness of the work area and the effectiveness of the facility's air handling and filtration systems. This may include the use of settle plates, active air samplers, and surface monitoring techniques to detect the presence of viable microorganisms.Media Fill TestingMedia fill testing is a critical component of the aseptic processing simulation test. This involves the use of a sterile growth medium, such as soybean-casein digest medium (SCDM), to simulate the actual production process. The test assesses the ability of the personnel to maintain sterile conditions throughout the entire process, from the preparation of the growth medium to the final product filling or packaging.Incubation and EvaluationThe inoculated media fill samples should be incubated under appropriate conditions to allow for the growth of any potential contaminants. The samples are then evaluated for the presence of microbial growth, which can indicate a breach in the aseptic process.Data Analysis and ReportingThe results of the aseptic processing simulation test should be thoroughly analyzed and documented. This includes the evaluation of the environmental monitoring data, the media fill test results, and any observed deviations or issues during the simulation. The analysis should identify any areas of concern and provide recommendations for corrective actions or process improvements.The frequency and scope of the aseptic processing simulation test should be determined based on the complexity of the manufacturing process, the risk profile of the products, and the regulatory requirements. In general, the simulation test should be conducted at least annually, or more frequently if significant process changes or deviations occur.It is important to note that the aseptic processing simulation test is not a one-time event but rather a continuous process of evaluation and improvement. The results of the simulation test should be used to identify and address any weaknesses in the aseptic techniques and procedures, as well as to provide valuable feedback for the ongoing training and development of the manufacturing personnel.In conclusion, the aseptic processing simulation test is a critical component of ensuring the sterility and safety of pharmaceutical and medical products. By implementing a comprehensive simulation test, manufacturers can validate the effectiveness of their asepticprocesses, identify areas for improvement, and ultimately enhance the quality and reliability of their products.。
供应商评审中英文对照
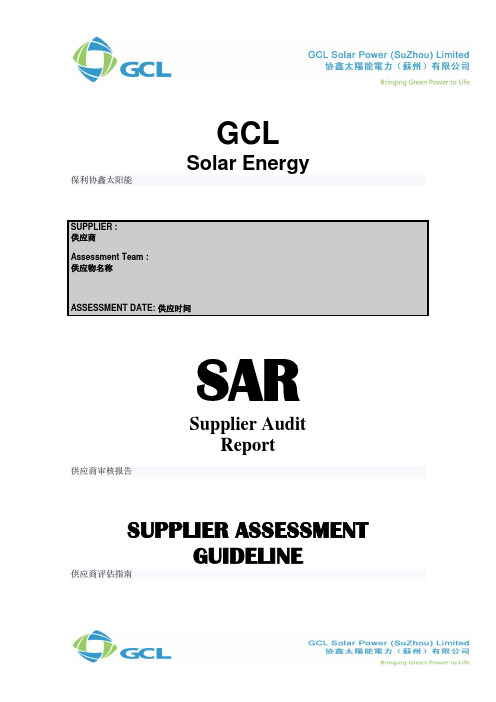
GCLSolar Energy保利协鑫太阳能SUPPLIER :供应商Assessment Team :供应物名称ASSESSMENT DATE: 供应时间SARSupplier AuditReport供应商审核报告SUPPLIER ASSESSMENTGUIDELINE供应商评估指南2010SUPPLIER ASSESSEMENTMANUFACTURING制造类供应商评估INTRODUCTION引言GCL Solar Energy is committed to product excellence in the markets we serve. We intend to continuously demonstrate this commitment by providing defect-free products on time and at competitive prices.协鑫光伏能源致力于对产品精益求精,在我们服务的市场,我们将不断证明这一承诺,并提供有竞争力的价格,无缺陷的产品。
This requires that we exercise every possible means to assure quality and consistent on-time delivery of purchased goods, which in-turn, contributes to continuous Quality improvement. Through the application of Statistical Process Control (SPC) combined with the cooperation and commitment of our Suppliers and Supply Chain Teams, GCL Solar Energy will drive continuous improvement both in Technical and Commercial aspects of business.这就要求我们千方百计保证质量和购进一致好的部件,不断提高服务质量。
生产加工流程英语

生产加工流程英语The production and processing workflow is a critical component of any manufacturing or industrial operation. It encompasses the series of steps and activities involved in transforming raw materials or components into a finished product that is ready for distribution and sale. This workflow is designed to optimize efficiency, minimize waste, and ensure the consistent quality of the final output.At the heart of the production and processing workflow is the manufacturing process. This process typically begins with the procurement of raw materials, which may include metals, plastics, chemicals, or other essential components. These raw materials are then transported to the production facility, where they undergo a series of transformative steps to become the desired product.One of the key stages in the production and processing workflow is the planning and scheduling of the manufacturing process. This involves carefully coordinating the various tasks and resources required to ensure that the production line runs smoothly and efficiently. This includes determining the optimal sequence ofoperations, allocating labor and equipment resources, and managing inventory levels to minimize disruptions and delays.Another critical aspect of the production and processing workflow is quality control. Throughout the manufacturing process, various quality checks and inspections are performed to ensure that the final product meets the established standards and specifications. This may involve visual inspections, dimensional measurements, material testing, and other quality assurance procedures. By implementing a robust quality control system, manufacturers can identify and address any issues or defects early in the production process, reducing the risk of costly rework or product recalls.The production and processing workflow also encompasses the packaging and labeling of the finished products. This step is crucial for protecting the product during transportation and storage, as well as providing important information to customers and end-users. Packaging can range from simple boxes or containers to more complex and specialized packaging solutions, depending on the nature of the product and the requirements of the target market.In addition to the manufacturing process itself, the production and processing workflow also involves the management of supporting activities and resources. This includes the procurement and management of raw materials, the maintenance and repair ofproduction equipment, the coordination of logistics and transportation, and the management of human resources, such as hiring, training, and scheduling of production personnel.One of the key trends in the modern production and processing workflow is the increasing adoption of automation and digital technologies. Advances in areas such as robotics, sensors, and data analytics are enabling manufacturers to automate various tasks and processes, improving efficiency, reducing errors, and enhancing overall productivity. Additionally, the use of digital technologies, such as enterprise resource planning (ERP) systems and manufacturing execution systems (MES), is helping to streamline the production and processing workflow, providing real-time visibility and control over the entire manufacturing process.Another important aspect of the production and processing workflow is sustainability and environmental responsibility. As concerns about climate change and resource scarcity continue to grow, manufacturers are increasingly focused on implementing more sustainable and eco-friendly practices throughout their production and processing workflows. This may involve the use of renewable energy sources, the implementation of waste reduction and recycling programs, and the adoption of more environmentally friendly raw materials and manufacturing processes.In conclusion, the production and processing workflow is a complex and multifaceted process that is critical to the success of any manufacturing or industrial operation. By carefully planning, managing, and optimizing this workflow, manufacturers can improve efficiency, enhance product quality, and reduce costs, ultimately delivering better value to their customers and stakeholders. As the industry continues to evolve, the production and processing workflow will need to adapt and incorporate new technologies and sustainable practices to remain competitive and responsive to the changing needs of the market.。
中国gmp附录 英文版

中国gmp附录英文版全文共四篇示例,供读者参考第一篇示例:中国GMP附录是China GMP的一部分,旨在规范并提高中国药品和医疗器械行业的生产质量和安全标准。
根据中国食品药品监督管理局的要求,药品和医疗器械生产企业必须遵守中国GMP的相关规定,并且定期接受监督检查以确保产品质量和安全性。
中国GMP附录的英文版提供了更多的参考资料和指导,以帮助企业更好地理解和实施中国GMP的要求。
该附录包括对一些特定事项的详细说明和解释,例如生产设备的选择和维护、人员培训和质量控制程序等。
中国GMP附录的英文版还包括对一些常见问题和挑战的解决方案,帮助企业更好地应对生产过程中可能出现的风险和问题。
附录中还包括了一些行业最佳实践和标准,以帮助企业提高其生产质量和效率。
在全球化的今天,遵守GMP标准已经成为药品和医疗器械企业的必然选择。
中国GMP附录的英文版为中国企业与国际接轨提供了重要的支持和指导,有助于他们在国际市场上取得更大的竞争优势。
The English version of China's GMP appendix also includes solutions to some common problems and challenges to help companies better address the risks and issues that may ariseduring the production process. In addition, the appendix includes some industry best practices and standards to help companies improve their production quality and efficiency.第二篇示例:中国GMP附录英文版Chinese Good Manufacturing Practice (GMP) AppendixIntroductionChina's pharmaceutical industry has been growing rapidly in recent years, with more and more companies entering the market. As a result, the need for stringent regulations to ensure the quality and safety of pharmaceutical products has become increasingly important. In response to this need, the Chinese government has issued the Chinese GMP, which outlines the requirements for the manufacturing of pharmaceutical products.Facility DesignEquipment ValidationProcess Controls第三篇示例:GMP是Good Manufacturing Practice的简称,是指良好生产规范。
Q1检查表介绍

Q1 2002 Site Assessment Evaluation Matrix Q1分数= Q1分数=
Capable Systems + Ongoing Performance PPM Performance –Production and/or service –Site PPM –Low-commodity PPM Delivery Performance –Production and/or service Field Service Actions Stop Shipment Violation of Trust 合格的体系 0~-250分 持续的业绩 PPM 业绩 ,+100~-250分 –生产件和/或售后服务件 –现场PPM –最低分值(>10%交货量)的产品 交货业绩 ,+100~-250分 –生产件和/或售后服务件 召回 0~-250分 停止发运 0~-250分 违背诚信原则 0~-250分 0~-250分
2
Q1 2002 Site Assessment Evaluation Matrix Q1 是什么? 是什么?
Ford motor Company exclusive designation 它是福特汽车公司所特有的 Set of fundamental quality and manufacturing disciplines 基本的质量和制造规则(质量管理体系) Drives supplier’s continual improvement 帮助供应商不断持续改进 Put tools in place to maintain excellence 用一些工具维持优越表现 Improve each passing year 每年都得到提升 (Q1不是独立获得的--而是引导福特和供应商之间的关系)
gmp体系下药企物料供应商管理流程和要点
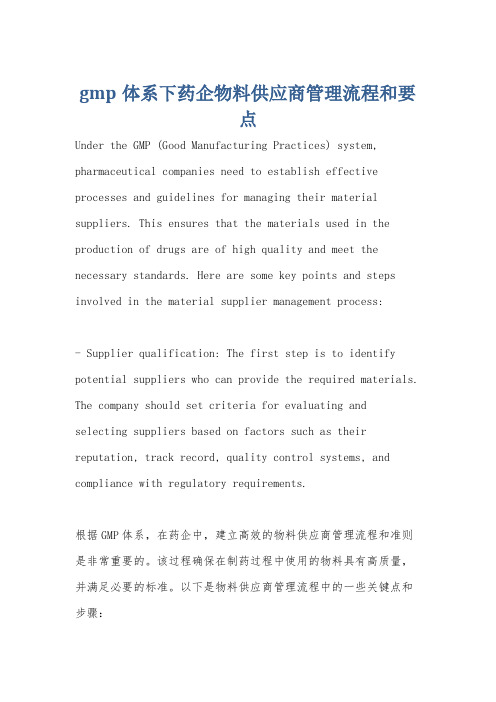
gmp体系下药企物料供应商管理流程和要点Under the GMP (Good Manufacturing Practices) system, pharmaceutical companies need to establish effective processes and guidelines for managing their material suppliers. This ensures that the materials used in the production of drugs are of high quality and meet the necessary standards. Here are some key points and steps involved in the material supplier management process:- Supplier qualification: The first step is to identify potential suppliers who can provide the required materials. The company should set criteria for evaluating andselecting suppliers based on factors such as their reputation, track record, quality control systems, and compliance with regulatory requirements.根据GMP体系,在药企中,建立高效的物料供应商管理流程和准则是非常重要的。
该过程确保在制药过程中使用的物料具有高质量,并满足必要的标准。
以下是物料供应商管理流程中的一些关键点和步骤:- 供应商资质:首先需要确定潜在供应商,他们可以提供所需的物料。
工序检验标准及流程

工序检验标准及流程In a manufacturing setting, process inspection standards and procedures are crucial for ensuring the quality and reliability of the end product. 工序检验标准和流程对于确保最终产品的质量和可靠性至关重要。
By establishing clear and comprehensive inspection standards and procedures, manufacturers can reduce the risk of defects and ensure that their products meet the necessary specifications. 通过建立清晰和全面的检验标准和流程,制造商可以减少缺陷的风险,并确保其产品符合必要的规格。
It also helps in maintaining consistency and efficiency in the production process. 这还有助于在生产过程中保持一致性和效率。
First and foremost, it is essential to develop a set of inspection standards that outline the specific criteria for evaluating the quality of a product at each stage of the manufacturing process. 首先,至关重要的是制定一套检验标准,详细说明在制造过程的每个阶段评估产品质量的具体标准。
These standards should be tailored to the unique requirements of the product and should be based on industry best practices and relevant regulatory requirements. 这些标准应根据产品的独特要求量身定制,并应基于行业最佳实践和相关的监管要求。
good manufacturing practices

Good Manufacturing PracticesIntroductionGood Manufacturing Practices (GMP) refer to a set of guidelines and regulations that ensure the consistent quality and safety of products during their manufacturing processes. GMP is crucial across various industries, such as pharmaceuticals, food and beverages, cosmetics, and medical devices. This article explores the importance of GMP and the key elements involved in its implementation.Advantages of Implementing GMPImplementing GMP provides several benefits for manufacturers, consumers, and regulatory authorities. Some of the key advantages include:1. Ensures Product QualityGMP ensures that products are manufactured consistently and meetspecific quality standards. By implementing GMP, manufacturers can minimize the risk of product defects, contamination, and deviations from desired specifications. This, in turn, increases customer satisfaction and brand reputation.2. Enhances Consumer SafetyOne of the primary objectives of GMP is to ensure consumer safety by preventing the presence of harmful substances or contaminants in products. GMP guidelines encompass rigorous quality control measures, sanitation practices, and documentation requirements. This ensures that products are safe for consumption or use by the end-users.3. Facilitates International TradeAdherence to GMP is vital for manufacturers engaged in international trade. Many countries and regulatory bodies require compliance with GMPguidelines for imported products. By implementing GMP, manufacturers can access global markets, establish trust with foreign consumers, and avoid trade barriers and restrictions.4. Reduces Manufacturing RisksGMP includes comprehensive risk management strategies, such as hazard analysis and critical control points (HACCP). These measures helpidentify and mitigate potential risks in the manufacturing process, ensuring that products are safe and of high quality. By minimizing risks, manufacturers can avoid costly product recalls, legal issues, and reputational damage.Key Elements of GMP ImplementationTo comply with GMP guidelines, manufacturers need to establish and maintain certain key elements. These elements include:1. Corrective and Preventive Actions (CAPA)CAPA is an essential component of GMP, focusing on identifying and rectifying deviations from established procedures. It involves investigating, documenting, and addressing any non-conformities to prevent their recurrence. CAPA processes help manufacturers continuously improve their operations and maintain compliance with GMP standards.2. Personnel Training and QualificationProper training and qualification of personnel are vital to ensure GMP compliance. Manufacturers must provide comprehensive training programsto employees, covering topics such as hygiene practices, product handling, quality control techniques, and regulatory requirements. Regular assessments and certifications can help validate employees’ competence and knowledge.3. Documentation and Record KeepingAccurate and thorough documentation is a fundamental aspect of GMP. Manufacturers must maintain comprehensive records regarding various aspects of their operations, including raw materials, manufacturing processes, equipment maintenance, inspections, and quality control tests. These records facilitate traceability, enable effective audits, and demonstrate compliance with GMP requirements.4. Quality Control and Quality AssuranceGMP emphasizes the importance of robust quality control and quality assurance systems. This involves testing and analyzing raw materials,in-process samples, and finished products to ensure they meet specified quality standards. Regular inspections, audits, and validationactivities help identify any deviations from established procedures and ensure ongoing compliance.5. Facility and Equipment MaintenanceMaintaining appropriate facilities and equipment is crucial for GMP compliance. Manufacturers must establish and adhere to maintenance schedules, calibration procedures, and cleaning protocols to ensure that production environments and equipment are in optimal condition. Regular inspections and preventive maintenance activities help minimize the risk of contamination or equipment failure.ConclusionGood Manufacturing Practices (GMP) form the foundation for ensuring product quality, consumer safety, and regulatory compliance across various industries. By implementing GMP guidelines, manufacturers can establish consistent manufacturing processes, mitigate risks, and maintain high-quality standards. Adherence to GMP principles not only benefits manufacturers but also enhances consumer confidence and facilitates international trade. Through the diligent implementation of key elements, such as CAPA, personnel training, documentation, quality control, and facility maintenance, manufacturers can achieve and sustain GMP compliance in their operations.。
机械类外文文献翻译(中英文翻译)
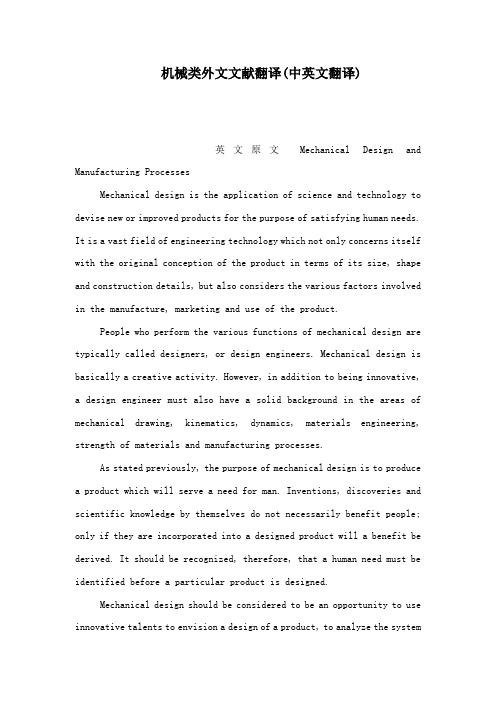
机械类外文文献翻译(中英文翻译)英文原文Mechanical Design and Manufacturing ProcessesMechanical design is the application of science and technology to devise new or improved products for the purpose of satisfying human needs. It is a vast field of engineering technology which not only concerns itself with the original conception of the product in terms of its size, shape and construction details, but also considers the various factors involved in the manufacture, marketing and use of the product.People who perform the various functions of mechanical design are typically called designers, or design engineers. Mechanical design is basically a creative activity. However, in addition to being innovative, a design engineer must also have a solid background in the areas of mechanical drawing, kinematics, dynamics, materials engineering, strength of materials and manufacturing processes.As stated previously, the purpose of mechanical design is to produce a product which will serve a need for man. Inventions, discoveries and scientific knowledge by themselves do not necessarily benefit people; only if they are incorporated into a designed product will a benefit be derived. It should be recognized, therefore, that a human need must be identified before a particular product is designed.Mechanical design should be considered to be an opportunity to use innovative talents to envision a design of a product, to analyze the systemand then make sound judgments on how the product is to be manufactured. It is important to understand the fundamentals of engineering rather than memorize mere facts and equations. There are no facts or equations which alone can be used to provide all the correct decisions required to produce a good design.On the other hand, any calculations made must be done with the utmost care and precision. For example, if a decimal point is misplaced, an otherwise acceptable design may not function.Good designs require trying new ideas and being willing to take a certain amount of risk, knowing that if the new idea does not work the existing method can be reinstated. Thus a designer must have patience, since there is no assurance of success for the time and effort expended. Creating a completely new design generally requires that many old and well-established methods be thrust aside. This is not easy since many people cling to familiar ideas, techniques and attitudes. A design engineer should constantly search for ways to improve an existing product and must decide what old, proven concepts should be used and what new, untried ideas should be incorporated.New designs generally have "bugs" or unforeseen problems which must be worked out before the superior characteristics of the new designs can be enjoyed. Thus there is a chance for a superior product, but only at higher risk. It should be emphasized that, if a design does not warrant radical new methods, such methods should not be applied merely for the sake of change.During the beginning stages of design, creativity should be allowedto flourish without a great number of constraints. Even though many impractical ideas may arise, it is usually easy to eliminate them in the early stages of design before firm details are required by manufacturing. In this way, innovative ideas are not inhibited. Quite often, more than one design is developed, up to the point where they can be compared against each other. It is entirely possible that the design which is ultimately accepted will use ideas existing in one of the rejected designs that did not show as much overall promise.Psychologists frequently talk about trying to fit people to the machines they operate. It is essentially the responsibility of the design engineer to strive to fit machines to people. This is not an easy task, since there is really no average person for which certain operating dimensions and procedures are optimum.Another important point which should be recognized is that a design engineer must be able to communicate ideas to other people if they are to be incorporated. Communicating the design to others is the final, vital step in the design process. Undoubtedly many great designs, inventions, and creative works have been lost to mankind simply because the originators were unable or unwilling to explain their accomplishments to others. Presentation is a selling job. The engineer, when presenting a new solution to administrative, management, or supervisory persons, is attempting to sell or to prove to them that this solution is a better one. Unless this can be done successfully, the time and effort spent on obtaining the solution have been largely wasted.Basically, there are only three means of communication available tous. These are the written, the oral, and the graphical forms. Therefore the successful engineer will be technically competent and versatile in all three forms of communication. A technically competent person who lacks ability in any one of these forms is severely handicapped. If ability in all three forms is lacking, no one will ever know how competent that person is!The competent engineer should not be afraid of the possibility of not succeeding in a presentation. In fact, occasional failure should be expected because failure or criticism seems to accompany every really creative idea. There is a great deal to be learned from a failure, and the greatest gains are obtained by those willing to risk defeat. In the final analysis, the real failure would lie in deciding not to make the presentation at all. To communicate effectively, the following questions must be answered:(1) Does the design really serve a human need?(2) Will it be competitive with existing products of rival companies?(3) Is it economical to produce?(4) Can it be readily maintained?(5) Will it sell and make a profit?Only time will provide the true answers to the preceding questions, but the product should be designed, manufactured and marketed only with initial affirmative answers. The design engineer also must communicate the finalized design to manufacturing through the use of detail and assembly drawings.Quite often, a problem will occur during the manufacturing cycle [3].It may be that a change is required in the dimensioning or tolerancing of a part so that it can be more readily produced. This fails in the category of engineering changes which must be approved by the design engineer so that the product function will not be adversely affected. In other cases, a deficiency in the design may appear during assembly or testing just prior to shipping. These realities simply bear out the fact that design is a living process. There is always a better way to do it and the designer should constantly strive towards finding that better way.Designing starts with a need, real or imagined. Existing apparatus may need improvements in durability, efficiently, weight, speed, or cost. New apparatus may be needed to perform a function previously done by men, such as computation, assembly, or servicing. With the objective wholly or partly defined, the next step in design is the conception of mechanisms and their arrangements that will perform the needed functions.For this, freehand sketching is of great value, not only as a record of one's thoughts and as an aid in discussion with others, but particularly for communication with one's own mind, as a stimulant for creative ideas.When the general shape and a few dimensions of the several components become apparent, analysis can begin in earnest. The analysis will have as its objective satisfactory or superior performance, plus safety and durability with minimum weight, and a competitive east. Optimum proportions and dimensions will be sought for each critically loaded section, together with a balance between the strength of the several components. Materials and their treatment will be chosen. These important objectives can be attained only by analysis based upon the principles ofmechanics, such as those of statics for reaction forces and for the optimumutilization of friction; of dynamics for inertia, acceleration, and energy; of elasticity and strength of materials for stress。
good manufacturing practice

good manufacturing practiceGood Manufacturing Practice(GMP) is a set of guidelines covering the manufacturing and quality control of varioustypes of products. These guidelines are designed to provide assurance that products intended for human or animal use meet safety, efficacy and quality standards. GMP compliance is an ongoing commitment by companies to ensure that their products are consistently produced in accordance with these guidelines.GMP compliance involves documenting and implementingprocesses to control all aspects of production, from raw materials to finished products. This includes documenting processes such as material testing, production and quality control procedures, validation and verification activities, tracking of products and personnel qualifications. GMP also includes ensuring that personnel have adequate training and experience in the field in which they are working, that the necessary equipment is in good condition, and thatappropriate records and documents are kept properly.GMP compliance also entails investing in quality assurance systems such as extensive laboratory testing of raw materials and finished products, process and product validation, risk analysis, environmental monitoring and supplierqualifications. It also requires close communication between departments throughout the entire production process.GMP compliance is essential to ensure the safety and quality of products. Good manufacturing practices are designed to eliminate problems before they occur, and to detect and correct them if they do occur. Companies that comply with GMP can demonstrate their commitment to safety and quality, and improve public confidence in their products. GMP compliance also helps to ensure that any claims made about the product are supported by evidence.Finally, GMP compliance helps to reduce wastage and costs, as well as helping to increase customer satisfaction. By investing in GMP compliance, organizations can therefore minimize the likelihood of recalls or product failures, while improving customer loyalty and satisfaction. Familiarizing yourself with good manufacturing practice can thus help your business or organization make better decisions about product quality, safety and compliance.。
高频制管机生产线操作流程注意事项
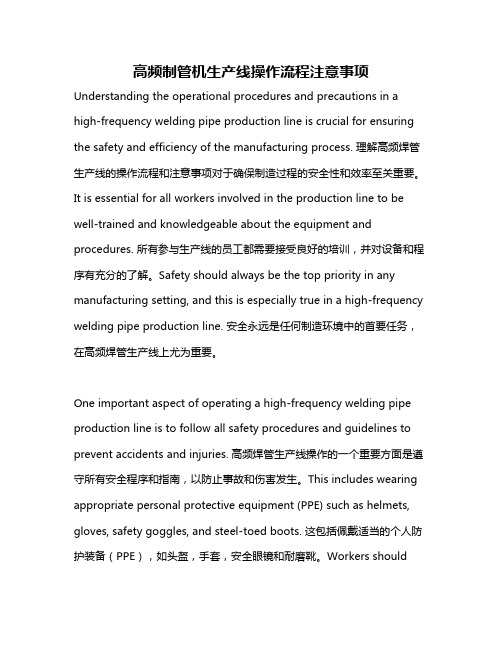
高频制管机生产线操作流程注意事项Understanding the operational procedures and precautions in a high-frequency welding pipe production line is crucial for ensuring the safety and efficiency of the manufacturing process. 理解高频焊管生产线的操作流程和注意事项对于确保制造过程的安全性和效率至关重要。
It is essential for all workers involved in the production line to be well-trained and knowledgeable about the equipment and procedures. 所有参与生产线的员工都需要接受良好的培训,并对设备和程序有充分的了解。
Safety should always be the top priority in any manufacturing setting, and this is especially true in a high-frequency welding pipe production line. 安全永远是任何制造环境中的首要任务,在高频焊管生产线上尤为重要。
One important aspect of operating a high-frequency welding pipe production line is to follow all safety procedures and guidelines to prevent accidents and injuries. 高频焊管生产线操作的一个重要方面是遵守所有安全程序和指南,以防止事故和伤害发生。
This includes wearing appropriate personal protective equipment (PPE) such as helmets, gloves, safety goggles, and steel-toed boots. 这包括佩戴适当的个人防护装备(PPE),如头盔,手套,安全眼镜和耐磨靴。
标准化生产流程英文缩写
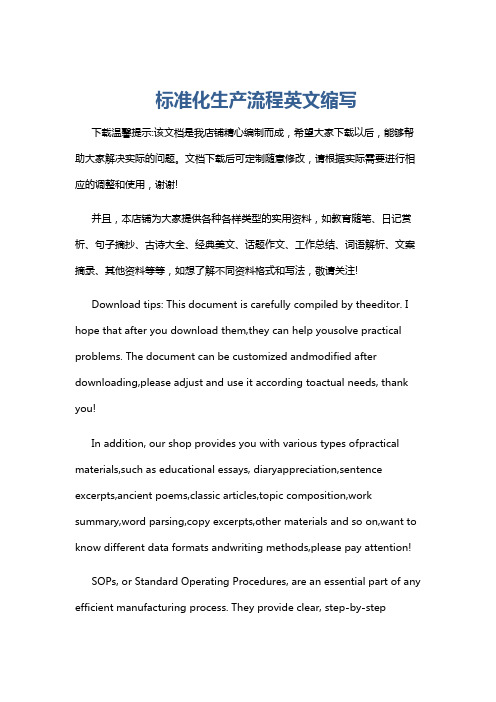
标准化生产流程英文缩写下载温馨提示:该文档是我店铺精心编制而成,希望大家下载以后,能够帮助大家解决实际的问题。
文档下载后可定制随意修改,请根据实际需要进行相应的调整和使用,谢谢!并且,本店铺为大家提供各种各样类型的实用资料,如教育随笔、日记赏析、句子摘抄、古诗大全、经典美文、话题作文、工作总结、词语解析、文案摘录、其他资料等等,如想了解不同资料格式和写法,敬请关注!Download tips: This document is carefully compiled by theeditor. I hope that after you download them,they can help yousolve practical problems. The document can be customized andmodified after downloading,please adjust and use it according toactual needs, thank you!In addition, our shop provides you with various types ofpractical materials,such as educational essays, diaryappreciation,sentence excerpts,ancient poems,classic articles,topic composition,work summary,word parsing,copy excerpts,other materials and so on,want to know different data formats andwriting methods,please pay attention!SOPs, or Standard Operating Procedures, are an essential part of any efficient manufacturing process. They provide clear, step-by-stepinstructions for every task, ensuring consistency and reducing the risk of errors.By defining the "who, what, when, where, and how" of each process, SOPs help streamline operations and improve quality. They eliminate guesswork and ensure that everyone is working from the same set of instructions.SOPs can also help improve safety by identifying potential hazards and outlining proper safety procedures. This can reduce the risk of accidents and injuries, creating a safer work environment.In addition to improving efficiency, quality, and safety, SOPs can also help reduce costs. By eliminating waste and rework, they can help manufacturers save money and improve their bottom line.Finally, SOPs are an essential tool for continuous improvement. By documenting processes, they make it easier to identify areas for improvement and implement changes that can lead to even greater efficiency and productivity.。
发动机止推片工艺流程

发动机止推片工艺流程As we delve into the manufacturing process of engine thrust blocks, it is important to understand the intricate steps and procedures involved in creating this crucial component. Engine thrust blocks play a vital role in the functionality and performance of the engine, providing support and stability to the various components within the engine system. These components must be manufactured with precision and accuracy to ensure optimal performance and efficiency.随着我们深入研究发动机止推片的制造过程,了解创造这个关键部件所涉及的复杂步骤和程序是很重要的。
发动机止推片在发动机的功能和性能中起着至关重要的作用,为发动机系统内的各个部件提供支撑和稳定。
这些组件必须精确制造,以确保最佳性能和效率。
The production of engine thrust blocks involves various stages, starting from the design phase to the final assembly of the component. The first step is to create a detailed design of the thrust block, specifying the dimensions, material specifications, and manufacturing processes required. This design is crucial as it servesas a blueprint for the entire manufacturing process, guiding the engineers and technicians in producing the component accurately.发动机止推片的生产涉及各个阶段,从设计阶段开始到最终组件的总装。
工艺工程师岗位职责
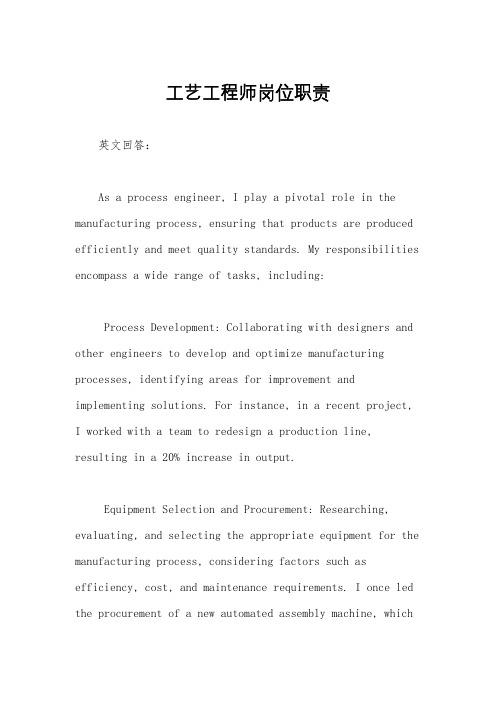
工艺工程师岗位职责英文回答:As a process engineer, I play a pivotal role in the manufacturing process, ensuring that products are produced efficiently and meet quality standards. My responsibilities encompass a wide range of tasks, including:Process Development: Collaborating with designers and other engineers to develop and optimize manufacturing processes, identifying areas for improvement and implementing solutions. For instance, in a recent project, I worked with a team to redesign a production line, resulting in a 20% increase in output.Equipment Selection and Procurement: Researching, evaluating, and selecting the appropriate equipment for the manufacturing process, considering factors such as efficiency, cost, and maintenance requirements. I once led the procurement of a new automated assembly machine, whichsignificantly reduced labor costs and improved product quality.Process Monitoring and Control: Establishing and maintaining procedures to monitor and control the manufacturing process, using statistical techniques and data analysis to identify and resolve issues. Recently, I implemented a real-time monitoring system that detected and corrected deviations in the production process, minimizing downtime and reducing scrap.Process Documentation and Training: Creating and maintaining documentation for manufacturing processes, including standard operating procedures, process maps, and training materials. For example, I developed a comprehensive training program for new operators, ensuring they fully understood the process and safety protocols.Collaboration and Communication: Working closely with other departments, such as production, quality control, and maintenance, to ensure seamless coordination and resolve cross-functional issues. I regularly attend team meetingsand participate in problem-solving sessions to share knowledge and contribute to continuous improvement initiatives.Continuous Improvement: Regularly evaluating and improving manufacturing processes, using lean principlesand industry best practices to enhance efficiency, reduce costs, and improve product quality. I recently implementeda kaizen event that identified and eliminated several bottlenecks in the production process, leading to a 15% increase in productivity.Safety Compliance: Ensuring compliance with all applicable safety regulations and standards, conductingrisk assessments, and implementing safety protocols to protect personnel and equipment. I spearheaded the development of a safety training program for all employees, resulting in a significant reduction in workplace accidents.Problem Solving and Decision Making: Analyzing and solving technical problems that arise during the manufacturing process, using logical thinking andanalytical skills to develop and implement solutions. For instance, I resolved a persistent quality issue byidentifying and correcting a faulty component in the assembly process.My role as a process engineer is both challenging and rewarding, as I am constantly learning and adapting to the evolving needs of the manufacturing industry. By leveraging my technical expertise and passion for continuous improvement, I strive to optimize processes, ensure product quality, and contribute to the overall success of the organization.中文回答:作为一名工艺工程师,我在制造工艺中发挥着至关重要的作用,确保产品以高效的方式生产,并达到质量标准。
精品GOOD MANUFACTURING PRACTICES
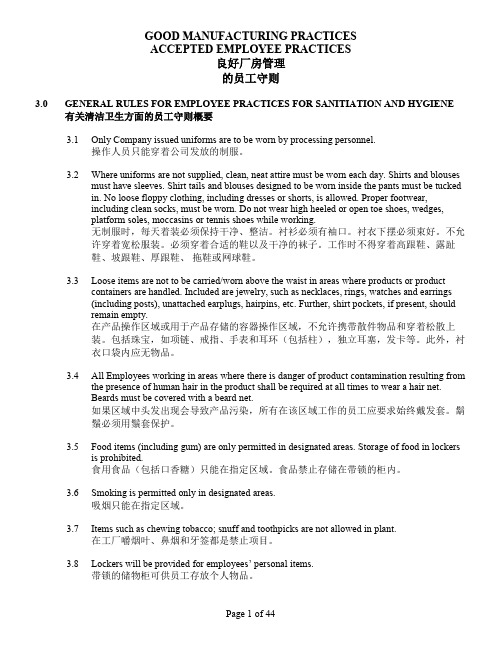
GOOD MANUFACTURING PRACTICESACCEPTED EMPLOYEE PRACTICES良好厂房管理的员工守则3.0GENERAL RULES FOR EMPLOYEE PRACTICES FOR SANITIATION AND HYGIENE有关清洁卫生方面的员工守则概要3.1Only Company issued uniforms are to be worn by processing personnel.操作人员只能穿着公司发放的制服。
3.2Where uniforms are not supplied, clean, neat attire must be worn each day. Shirts and blousesmust have sleeves. Shirt tails and blouses designed to be worn inside the pants must be tuckedin. No loose floppy clothing, including dresses or shorts, is allowed. Proper footwear,including clean socks, must be worn. Do not wear high heeled or open toe shoes, wedges,platform soles, moccasins or tennis shoes while working.无制服时,每天着装必须保持干净、整洁。
衬衫必须有袖口。
衬衣下摆必须束好。
不允许穿着宽松服装。
必须穿着合适的鞋以及干净的袜子。
工作时不得穿着高跟鞋、露趾鞋、坡跟鞋、厚跟鞋、拖鞋或网球鞋。
3.3Loose items are not to be carried/worn above the waist in areas where products or productcontainers are handled. Included are jewelry, such as necklaces, rings, watches and earrings(including posts), unattached earplugs, hairpins, etc. Further, shirt pockets, if present, shouldremain empty.在产品操作区域或用于产品存储的容器操作区域,不允许携带散件物品和穿着松散上装。
Manufacturing Process Control
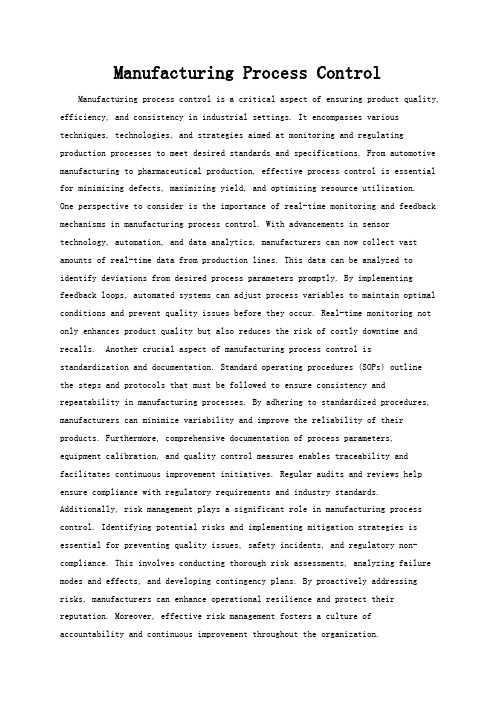
Manufacturing Process Control Manufacturing process control is a critical aspect of ensuring product quality, efficiency, and consistency in industrial settings. It encompasses various techniques, technologies, and strategies aimed at monitoring and regulating production processes to meet desired standards and specifications. From automotive manufacturing to pharmaceutical production, effective process control is essential for minimizing defects, maximizing yield, and optimizing resource utilization. One perspective to consider is the importance of real-time monitoring and feedback mechanisms in manufacturing process control. With advancements in sensor technology, automation, and data analytics, manufacturers can now collect vast amounts of real-time data from production lines. This data can be analyzed to identify deviations from desired process parameters promptly. By implementing feedback loops, automated systems can adjust process variables to maintain optimal conditions and prevent quality issues before they occur. Real-time monitoring not only enhances product quality but also reduces the risk of costly downtime and recalls. Another crucial aspect of manufacturing process control is standardization and documentation. Standard operating procedures (SOPs) outlinethe steps and protocols that must be followed to ensure consistency and repeatability in manufacturing processes. By adhering to standardized procedures, manufacturers can minimize variability and improve the reliability of their products. Furthermore, comprehensive documentation of process parameters, equipment calibration, and quality control measures enables traceability and facilitates continuous improvement initiatives. Regular audits and reviews help ensure compliance with regulatory requirements and industry standards. Additionally, risk management plays a significant role in manufacturing process control. Identifying potential risks and implementing mitigation strategies is essential for preventing quality issues, safety incidents, and regulatory non-compliance. This involves conducting thorough risk assessments, analyzing failure modes and effects, and developing contingency plans. By proactively addressing risks, manufacturers can enhance operational resilience and protect their reputation. Moreover, effective risk management fosters a culture ofaccountability and continuous improvement throughout the organization.Furthermore, the integration of advanced technologies such as artificial intelligence (AI) and machine learning (ML) is revolutionizing manufacturing process control. AI-driven algorithms can analyze complex data patterns and optimize process parameters in real time, leading to enhanced efficiency and productivity. ML models can predict equipment failures and quality defects, enabling proactive maintenance and quality assurance measures. Additionally, robotics and automation technologies are increasingly being utilized to streamline production processes and minimize human error. By embracing digital transformation, manufacturers can stay competitive in today's fast-paced market environment. Another perspective to consider is the importance of employee training and engagement in manufacturing process control. Human factors play a critical role in ensuring the effectiveness of process control measures. Well-trained employees understand the importance of adhering to procedures, monitoring process parameters, and responding to deviations promptly. Moreover, fostering a culture of continuous learning and improvement empowers employees to contribute ideas for enhancing process efficiency and quality. By investing in training and development programs, manufacturers can cultivate a skilled workforce capable of driving operational excellence. Lastly, collaboration and communication across functional teams are essential for successful manufacturing process control. Cross-functional collaboration ensures alignment between departments such as engineering, production, quality assurance, and supply chain management. By sharing information and insights, teams can identify areas for improvement, address issues proactively, and drive collective decision-making. Furthermore, effective communication channels enable rapid response to changing market conditions, customer feedback, and regulatory requirements. By fostering a collaborative work environment, manufacturers can adapt quickly to evolving challenges and opportunities. In conclusion, manufacturing process control is a multifaceted discipline that requires a holistic approach encompassing technology, standardization, risk management, employee engagement, and collaboration. By leveraging real-time monitoring, standard operating procedures, risk management practices, advanced technologies, employee training, and collaboration, manufacturers can achieve superior product quality, operational efficiency, and customer satisfaction.Continuous improvement and adaptation to changing market dynamics are key to sustaining competitiveness in the manufacturing industry.。
- 1、下载文档前请自行甄别文档内容的完整性,平台不提供额外的编辑、内容补充、找答案等附加服务。
- 2、"仅部分预览"的文档,不可在线预览部分如存在完整性等问题,可反馈申请退款(可完整预览的文档不适用该条件!)。
- 3、如文档侵犯您的权益,请联系客服反馈,我们会尽快为您处理(人工客服工作时间:9:00-18:30)。
equipment
Working and Manufacturing Procedures
管道组对 Pipe fit-up
尺寸检验 Dimension inspection
预热 Preheat
焊接 Welding
焊后热处理 PWNT
无损检测 NDT
Working and Manufacturing Procedures
Organization Chart for AL Heracles
Click for Detail
Working and Manufacturing Procedures
WPS PQR
Working and Manufacturing Procedures
焊接 Welding
Working and Manufacturing Procedures
焊缝外观和尺寸检验 Dimension and Visual inspection
无损检测 NDT
焊后热 处理
PWNT
试压 Pressur
e test
管道整体检验 Pipe final inspection
喷砂底漆 sandblast , primer
coating
供应商审核 Audit suppliers
材料计划 Purchase order
材料下料/标识移植 Cutting the pipe material / Marking Transplantation
材料/设备接收 Materials and Equipments receive
Working and Manufacturing Procedures
1. Marking 2. Cleanliness 3. Painting & Blasting 4. Hydrostatic Test 5. Packing
Working and Manufacturing Procedures
position
无损检测 NDT
焊缝外观和尺寸检验 Dimension and Visual
inspection
管道整体检验 Pipe final inspection
试压 Pressure test
管道组件复位 Reset piping and
components
பைடு நூலகம்
Working and Manufacturing Procedures
coating
材料下料/标识移植 Cutting the pipe material / Marking Transplantation
材料/设备检验 Check material and
equipment
管道组对 Pipe fit-up
尺寸检验 Dimension inspection
预热 Preheat
管道整体安装就位 Install the pipe into the
position
管道整体检验 Pipe final inspection
管道组件复位 Reset piping and
components
焊缝外观及尺寸检验 Dimension and Visual
inspection
试压 Pressure test
材料/设备接收 Materials and Equipments receive
材料/设备检验 Check material and
equipment
管道组对 Pipe fit-up
尺寸检验 Dimension inspection
焊接 Welding
管道整体安装就位 Install the pipe into the
Manufacturing Process Plan For S.S.
图纸审核 Review drawings
喷砂底漆 sandblast , primer
coating
供应商审核 Audit suppliers
材料计划 Purchase order
材料下料/标识移植 Cutting the pipe material / Marking Transplantation
Manufacturing Process Plan For C.S.
图纸审核 Review drawings
供应商审核 Audit suppliers
材料计划 Purchase order
材料/设备接收 materials and equipments
receive
喷砂底漆 Sandblast; primer
管道整体安装就位 Install the pipe into the
position
管道组件复位 Reset piping and
components
Working and Manufacturing Procedures
Manufacturing Process Plan For A.S.
图纸审核 Review drawings
Find Your Partner Among the Best