FMEA-800 rev 06 WKKT SAMPLE
FMEA手册
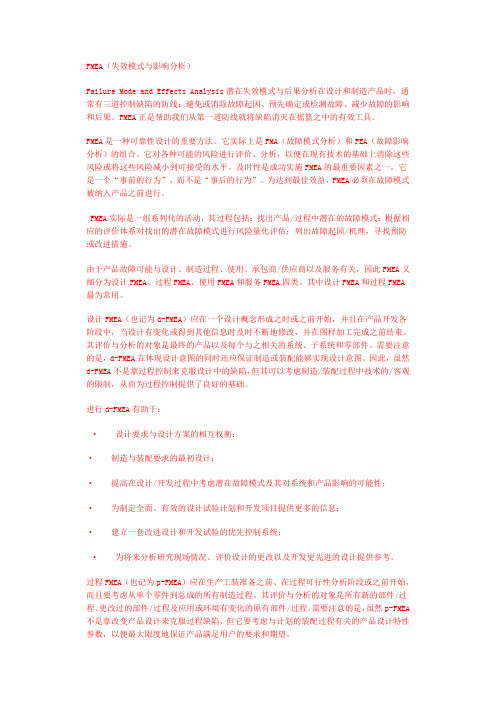
FMEA(失效模式与影响分析)Failure Mode and Effects Analysis潜在失效模式与后果分析在设计和制造产品时,通常有三道控制缺陷的防线:避免或消除故障起因、预先确定或检测故障、减少故障的影响和后果。
FMEA正是帮助我们从第一道防线就将缺陷消灭在摇篮之中的有效工具。
FMEA是一种可靠性设计的重要方法。
它实际上是FMA(故障模式分析)和FEA(故障影响分析)的组合。
它对各种可能的风险进行评价、分析,以便在现有技术的基础上消除这些风险或将这些风险减小到可接受的水平。
及时性是成功实施FMEA的最重要因素之一,它是一个“事前的行为”,而不是“事后的行为”。
为达到最佳效益,FMEA必须在故障模式被纳入产品之前进行。
FMEA实际是一组系列化的活动,其过程包括:找出产品/过程中潜在的故障模式;根据相应的评价体系对找出的潜在故障模式进行风险量化评估;列出故障起因/机理,寻找预防或改进措施。
由于产品故障可能与设计、制造过程、使用、承包商/供应商以及服务有关,因此FMEA又细分为设计FMEA、过程FMEA、使用FMEA和服务FMEA四类。
其中设计FMEA和过程FMEA 最为常用。
设计FMEA(也记为d-FMEA)应在一个设计概念形成之时或之前开始,并且在产品开发各阶段中,当设计有变化或得到其他信息时及时不断地修改,并在图样加工完成之前结束。
其评价与分析的对象是最终的产品以及每个与之相关的系统、子系统和零部件。
需要注意的是,d-FMEA在体现设计意图的同时还应保证制造或装配能够实现设计意图。
因此,虽然d-FMEA不是靠过程控制来克服设计中的缺陷,但其可以考虑制造/装配过程中技术的/客观的限制,从而为过程控制提供了良好的基础。
进行d-FMEA有助于:·设计要求与设计方案的相互权衡;·制造与装配要求的最初设计;·提高在设计/开发过程中考虑潜在故障模式及其对系统和产品影响的可能性;·为制定全面、有效的设计试验计划和开发项目提供更多的信息;·建立一套改进设计和开发试验的优先控制系统;·为将来分析研究现场情况、评价设计的更改以及开发更先进的设计提供参考。
2024年度FMEA培训教材ppt完整版

等级并制定应对措施,可提高系统或产品的可靠性和安全性。
2024/3/23
02 03
改进策略的制定
根据FMEA分析结果,针对高风险和中风险故障模式制定改进策略,包 括设计优化、工艺改进、材料替换等,以降低故障发生的可能性和影响 程度。
改进效果的跟踪
实施改进策略后,需对改进效果进行跟踪和评估,确保改进措施的有效 性。同时,将改进经验反馈到FMEA分析中,不断完善和优化分析过程 。
掌握了FMEA实施的基本技能
通过课程中的案例分析和实践操作,学员们表示已经掌握 了FMEA实施的基本技能,能够独立完成简单的FMEA分析 工作。
增强了团队协作和沟通能力
在课程中,学员们分组进行讨论和案例分析,不仅增强了 团队协作能力,还提高了沟通能力。
34
未来发展趋势预测
2024/3/23
01 02 03
23
05 FMEA在产品设 计阶段应用实践
2024/3/23
24
产品设计阶段FMEA实施流程
流程概述
01 明确FMEA在产品设计阶段的
目标和重要性,以及实施的基 本步骤。
团队组建与培训
02 组建专业的FMEA团队,并进
行必要的培训和技能提升。
功能分析与结构分解
03 对产品的功能进行详细分析,
并进行结构分解,以明确潜在 故障模式。
12
评估方法选择及实施流程
• 方法选择:根据失效模式的性质和影响程度选择合适的评 估方法,如风险矩阵、风险指数等。
2024/3/23
13
评估方法选择及实施流程
实施流程
1. 明确评估目标和范围
2. 收集相关数据和信息
2024/3/23
14
FMEA知识介绍

FMEA简介FMEA(Failure Mode and Effect Analysis,失效模式和效果分析)是一种用来确定潜在失效模式及其原因的分析方法。
具体来说,通过实行FMEA,可在产品设计或生产工艺真正实现之前发现产品的弱点,可在原形样机阶段或在大批量生产之前确定产品缺陷。
FMEA最早是由美国国家宇航局(NASA)形成的一套分析模式,FMEA是一种实用的解决问题的方法,可适用于许多工程领域,目前世界许多汽车生产商和电子制造服务商(EM S)都已经采用这种模式进行设计和生产过程的管理和监控。
FMEA简介FMEA有三种类型,分别是系统FMEA、设计FMEA和工艺FMEA,本文中主要讨论工艺FMEA。
1)确定产品需要涉及的技术、能够出现的问题,包括下述各个方面:需要设计的新系统、产品和工艺;对现有设计和工艺的改进;在新的应用中或新的环境下,对以前的设计和工艺的保留使用;形成FMEA团队。
理想的FMEA团队应包括设计、生产、组装、质量控制、可靠性、服务、采购、测试以及供货方等所有有关方面的代表。
2)记录FMEA的序号、日期和更改内容,保持FMEA始终是一个根据实际情况变化的实时现场记录,需要强调的是,FMEA文件必须包括创建和更新的日期。
3) 创建工艺流程图。
工艺流程图应按照事件的顺序和技术流程的要求而制定,实施FMEA需要工艺流程图,一般情况下工艺流程图不要轻易变动。
4)列出所有可能的失效模式、效果和原因、以及对于每一项操作的工艺控制手段:4.1 对于工艺流程中的每一项工艺,应确定可能发生的失效模式.如就表面贴装工艺(SMT)而言,涉及的问题可能包括,基于工程经验的焊球控制、焊膏控制、使用的阻焊剂 (soldermask)类型、元器件的焊盘图形设计等。
4.2 对于每一种失效模式,应列出一种或多种可能的失效影响,例如,焊球可能要影响到产品长期的可靠性,因此在可能的影响方面应该注明。
4.3 对于每一种失效模式,应列出一种或多种可能的失效原因.例如,影响焊球的可能因素包括焊盘图形设计、焊膏湿度过大以及焊膏量控制等。
2024版FMEA培训资料最新版(ppt14)

验证预防措施有效性
在实施预防措施后,需要对措施的有 效性进行验证,确保措施能够真正降 低风险。
制定预防措施
根据潜在风险,制定相应的预防措施, 如改进设计、优化工艺、提高材料质 量等,以降低风险发生的概率。
纠正措施选择依据探讨
进行FMEA分析
对关键工序进行详细的故障模 式分析,找出潜在的故障模式、 原因及影响。
组建FMEA团队
包括生产、技术、质量等相关 部门人员,共同进行FMEA分 析。
收集数据
收集历史故障数据、生产数据、 设备维护数据等,为FMEA分 析提供基础。
制定预防措施
针对潜在的故障模式,制定相 应的预防措施,如设备维护计 划、操作规范等。
FMEA培训资料最 新版(ppt14)
contents
目录
• FMEA概述与基本原理 • FMEA实施流程与步骤 • 失效模式与影响分析(FM) • 风险控制措施制定与实施 • FMEA在产品设计阶段应用案例 • FMEA在生产过程监控中应用案例 • 总结回顾与展望未来发展趋势
01
FMEA概述与基本原 理
经济性影响
评估失效对经济方面的 影响程度,如可能导致 生产停顿、维修费用增
加等。
运行性影响
评估失效对设备运行的 影响程度,如可能导致 设备性能下降、运行不
稳定等。
环境性影响
评估失效对环境方面的 影响程度,如可能导致 环境污染、资源浪费等。
04
风险控制措施制定与 实施
预防措施设计思路分享
识别潜在风险
通过因果图的方式,将问题与其原因进行关联,有助于直观地发现问题的根本原因。
FMEA讲义课件
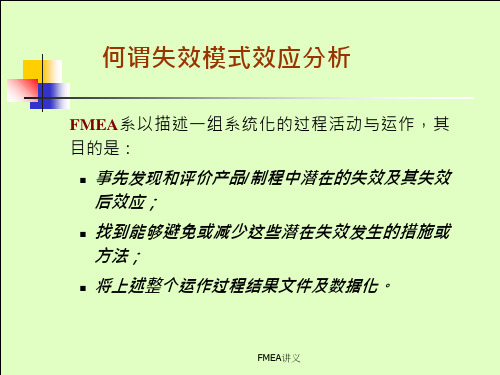
设计FMEA流程图
流 程
说 明
设计工程师应负责确认各项改正行动均经完成或均经通知负责人确实执行。
对RPN之项目应最优先采取必要措施,其目的在降低严重性、发生性及侦测性之分数。若不采有效之改正措施则制程FMEA之成效将受局限。
将风险领先指数做成柏拉图并决定建议之措施
将已采取之改正行动之内容及其完成日期填入记录,重新预估并记录改正后之严重性、发生性及侦测性之结果;计算新的RPN值。如果必要时,采取适当行动以降低RPN值。
9
很高
产品功能不能运作,丧失基本功能
8
高
产品功能能运作,但功能降低,顾客严重不满
7
中等
功能可运作,但舒适性及方便性降低,顾客使用时不满意
6
低
功能能运作,但舒适性及方便性降低,顾客使用时有些不满意
5
很低
如功能性、外观及结构等不合要求,大多数顾客注意到的了缺陷
4
微小
如功能性、外观等不合要求,一般顾客可注意到的缺陷
4
高
设计控制将会侦测出潜在原因/机制和随后的失效模式
3
非常高
设计控制有很高的机会侦测出潜在原因/机制和随后的失效模式
2
几乎肯定
设计控制几乎会侦测出潜在原因/机制和随后的失效模式
1
D-FMEA导入时机与展开
IN PUT
OUT PUT
产品主要功能
.
发生性系指预测该不良模式发生之频
度,不
良之
预防必须加以考虑
.
侦
测性系对该零件或装配件送交生产前,其可
能
存在之设计弱点是否能经设计
验证而查出之能
力
.
设计工程师应负责确认各项改正行动均经完成
2024年FMEA培训教材(多应用版)
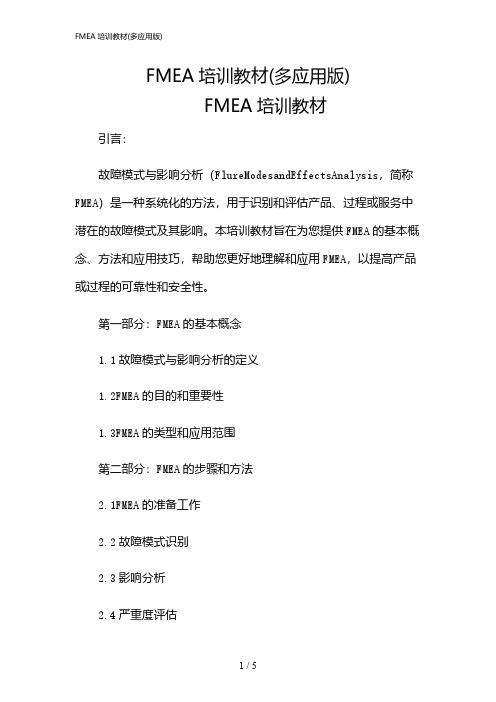
FMEA培训教材(多应用版)FMEA培训教材引言:故障模式与影响分析(FlureModesandEffectsAnalysis,简称FMEA)是一种系统化的方法,用于识别和评估产品、过程或服务中潜在的故障模式及其影响。
本培训教材旨在为您提供FMEA的基本概念、方法和应用技巧,帮助您更好地理解和应用FMEA,以提高产品或过程的可靠性和安全性。
第一部分:FMEA的基本概念1.1故障模式与影响分析的定义1.2FMEA的目的和重要性1.3FMEA的类型和应用范围第二部分:FMEA的步骤和方法2.1FMEA的准备工作2.2故障模式识别2.3影响分析2.4严重度评估2.5发生概率评估2.6检测难度评估2.7风险优先级评估2.8制定改进措施和行动计划第三部分:FMEA的实践应用3.1FMEA团队的组建和培训3.2FMEA实施过程中的常见问题及解决方法3.3FMEA报告的编制和评审3.4FMEA与其他质量管理工具的结合应用第四部分:FMEA的持续改进4.1FMEA的跟踪和监控4.2FMEA的回顾和更新4.3FMEA的最佳实践分享和推广结论:通过本培训教材的学习,您应该能够了解FMEA的基本概念、方法和应用技巧。
FMEA是一种重要的质量管理工具,可以帮助组织识别和评估潜在的故障模式及其影响,从而采取相应的改进措施,提高产品或过程的可靠性和安全性。
希望本教材能够为您在FMEA的实际应用中提供指导和支持。
注意事项:1.本教材的内容仅供参考,具体应用时需结合实际情况进行适当调整。
2.FMEA的实施需要团队合作和专业知识的支持,建议在实施前进行相关培训和能力提升。
3.FMEA是一种持续改进的过程,需要定期回顾和更新,以适应组织的发展和变化。
关键词:FMEA、故障模式、影响分析、风险管理、质量改进、可靠性、安全性重点关注的细节:FMEA的步骤和方法详细补充和说明:1.故障模式识别:故障模式是指产品、过程或服务中可能出现的问题或失效方式。
FMEA培训资料
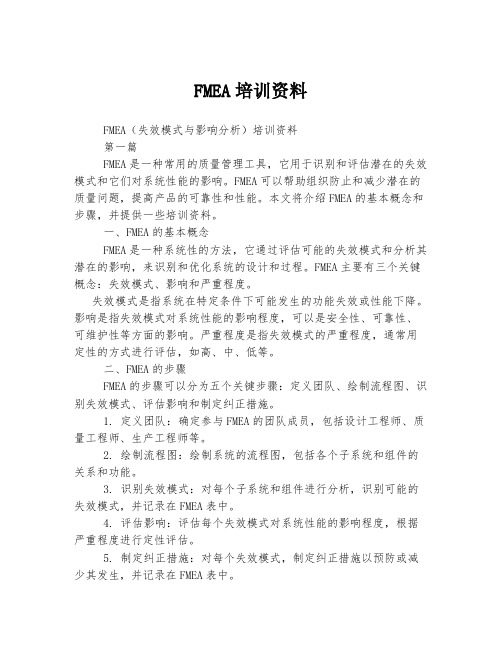
FMEA培训资料FMEA(失效模式与影响分析)培训资料第一篇FMEA是一种常用的质量管理工具,它用于识别和评估潜在的失效模式和它们对系统性能的影响。
FMEA可以帮助组织防止和减少潜在的质量问题,提高产品的可靠性和性能。
本文将介绍FMEA的基本概念和步骤,并提供一些培训资料。
一、FMEA的基本概念FMEA是一种系统性的方法,它通过评估可能的失效模式和分析其潜在的影响,来识别和优化系统的设计和过程。
FMEA主要有三个关键概念:失效模式、影响和严重程度。
失效模式是指系统在特定条件下可能发生的功能失效或性能下降。
影响是指失效模式对系统性能的影响程度,可以是安全性、可靠性、可维护性等方面的影响。
严重程度是指失效模式的严重程度,通常用定性的方式进行评估,如高、中、低等。
二、FMEA的步骤FMEA的步骤可以分为五个关键步骤:定义团队、绘制流程图、识别失效模式、评估影响和制定纠正措施。
1. 定义团队:确定参与FMEA的团队成员,包括设计工程师、质量工程师、生产工程师等。
2. 绘制流程图:绘制系统的流程图,包括各个子系统和组件的关系和功能。
3. 识别失效模式:对每个子系统和组件进行分析,识别可能的失效模式,并记录在FMEA表中。
4. 评估影响:评估每个失效模式对系统性能的影响程度,根据严重程度进行定性评估。
5. 制定纠正措施:对每个失效模式,制定纠正措施以预防或减少其发生,并记录在FMEA表中。
三、FMEA培训资料以下为FMEA培训资料的内容概要:1. FMEA概述:介绍FMEA的定义、目的和应用领域,以及FMEA 在质量管理中的作用。
2. FMEA步骤详解:详细介绍FMEA的五个步骤,并提供实例和案例分析。
3. FMEA表:介绍FMEA表的结构和内容,以及如何填写和使用FMEA表。
4. FMEA的应用:介绍FMEA在不同行业和领域的应用案例,如制造业、医疗行业等。
5. FMEA的优点和挑战:分析FMEA的优点和挑战,并提供解决方案和建议。
第四版FMEA手册解读
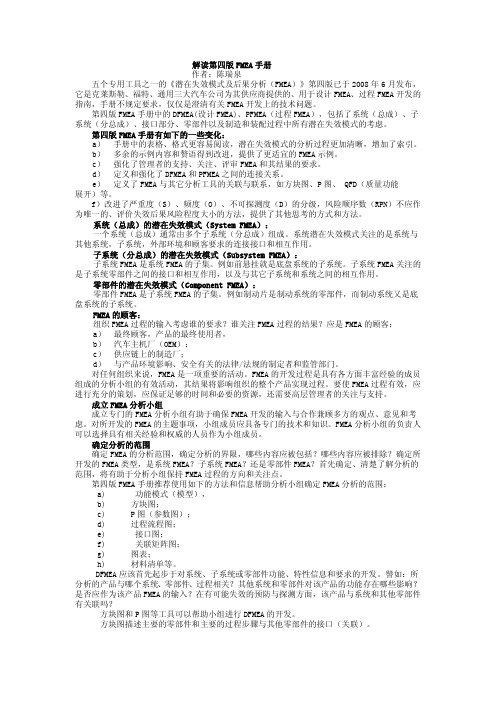
解读第四版FMEA手册作者:陈瑞泉五个专用工具之一的《潜在失效模式及后果分析(FMEA)》第四版已于2008年6月发布,它是克莱斯勒、福特、通用三大汽车公司为其供应商提供的、用于设计FMEA、过程FMEA开发的指南,手册不规定要求,仅仅是澄清有关FMEA开发上的技术问题。
第四版FMEA手册中的DFMEA(设计FMEA)、PFMEA(过程FMEA),包括了系统(总成)、子系统(分总成)、接口部分、零部件以及制造和装配过程中所有潜在失效模式的考虑。
第四版FMEA手册有如下的一些变化:a) 手册中的表格、格式更容易阅读,潜在失效模式的分析过程更加清晰,增加了索引。
b) 多余的示例内容和赘语得到改进,提供了更适宜的FMEA示例。
c) 强化了管理者的支持、关注、评审FMEA和其结果的要求。
d) 定义和强化了DFMEA和PFMEA之间的连接关系。
e) 定义了FMEA与其它分析工具的关联与联系,如方块图、P图、 QFD(质量功能展开)等。
f)改进了严重度(S)、频度(O)、不可探测度(D)的分级,风险顺序数(RPN)不应作为唯一的、评价失效后果风险程度大小的方法,提供了其他思考的方式和方法。
系统(总成)的潜在失效模式(System FMEA):一个系统(总成)通常由多个子系统(分总成)组成。
系统潜在失效模式关注的是系统与其他系统,子系统,外部环境和顾客要求的连接接口和相互作用。
子系统(分总成)的潜在失效模式(Subsystem FMEA):子系统FMEA是系统FMEA的子集。
例如前悬挂就是底盘系统的子系统。
子系统FMEA关注的是子系统零部件之间的接口和相互作用,以及与其它子系统和系统之间的相互作用。
零部件的潜在失效模式(Component FMEA):零部件FMEA是子系统FMEA的子集。
例如制动片是制动系统的零部件,而制动系统又是底盘系统的子系统。
FMEA的顾客:组织FMEA过程的输入考虑谁的要求?谁关注FMEA过程的结果?应是FMEA的顾客:a) 最终顾客,产品的最终使用者,b) 汽车主机厂(OEM);c) 供应链上的制造厂;d) 与产品环境影响、安全有关的法律/法规的制定者和监管部门。
FMEA的作业指导规范标准

1.0目的为了确定与设计和过程相关的潜在失效模式,评价潜在失效对顾客产生的后果,编制一个潜在失效模式的分级表,以便建立一个考虑预防/纠正措施的优选体系。
2.0围适用于XX电子客户要求的所有过程潜在失效模式与后果分析。
3.0定义3.1 FMEA:潜在失效模式与后果分析(Potential Failure Mode and Effects Analysis.)在产品的设计策划阶段对产品的各部份逐一进行分析,找出失效模式,分析可能产生的后果,鉴定失效的原因,评估其风险程度(RPN)从而采取相应的措施,减少失效的危害,提高产品/过程质量,确保顾客满意的一种系统化的管理方法。
包括设计FMEA(DFMEA)和过程FMEA (PFMEA)。
3.2 潜在失效模式:是指过程有可能不能满足过程功能/要求栏中所描述的过程和/或设计意图。
3.3 失效的潜在后果:是指失效模式对产品功能的影响,就如顾客的感受一样。
3.4 严重度(S):严重度是指失效模式发生时对产品的功能/产品的生产过程或顾客影响后果的严重程度的评价指标。
3.5 失效的潜在起因:是指失效是怎样发生的,并应依据可以纠正或可以控制的原则予以描述。
3.6 频度(O):指某一特定的起因/机理发生的可能性。
3.7 探测度(D):是指产品在投产之前,利用现行控制方法来探测失效的潜在起因/机理的能力评价指标。
4.0职责4.1DFMEA小组:负责组织编制设计FMEA。
4.2PFMEA小组:负责组织编制过程FMEA。
5.0过程FMEA的编制5.1 编制过程FMEA的时机5.1.1在可行性阶段或之前进行;5.1.2在生产用工装到位之前;5.1.3建立或修改PMP(质量管理计划)之前应进行。
5.2 编制过程FMEA的基本要求5.2.1负责的工程师要有一定的FMEA和团队工作推进经验。
5.2.2 过程FMEA假定所设计的产品能够满足设计要求。
5.2.3 过程FMEA不依靠改变产品设计来克服过程中的薄弱环节,但是它要考虑与计划的制造或装配过程有关的产品设计特性,以最大限度的保证产品能够满足顾客的要求和期望。
FMEA模板及介绍

Prepared by Justin Tao 32
2. 特性分类
按状态分: 产品特性和过程特性
按重要程度分: 1)关键特性: 与安全、法规有关的关键特性(特殊特性) 与功能、装配有关的关键特性(重要特性) 2)普通特性:除关键特性之外的所有特性
4. DFMEA潜在失效后果
潜在失效后果(设计) :
就是失效模式对功能的影响,就如顾客感受的一样。 要根据顾客可能发现或经历的情况来描述失效的后
果。 要清楚地说明该失效模式是否会影响到安全性,或
与法规不符。 不同级别的系统、子系统或零件之间存在着系统层
次上的关系。
Prepared by Justin Tao 19
工程的影响
采取可行的对策
Prepared by Justin Tao 11
5. FMEA分类
依据阶段不同可分为: DFMEA PFMEA
依据作用不同可分为: 系统FMEA 子系统FMEA 零件FMEA
Prepared by Justin Tao 12
二、FMEA关键术语理解
13
1. FMEA失效
SFMEA
来自SFMEA
生的原因
PFMEA 问题产生的原因来自 和DFMEA相同 详细的过程失效
DFMEA
的后果
模式产生的原因
Prepared by Justin Tao 39
3. FMEA的时间顺序
DFMEA PFMEA
概念 初始设计 设计完成 样件制造 设计/过程 生产开始 确认
DFMEA 开始早于过程,完成时间在早期的图样完成但任何工 具的制造开始之前 PFMEA 开始于基本的操作方法讨论完成时,完成时间早于生产 计划制定和生产批准之前
fmea手册

fmea手册新版FMEA终于正式发布了!关于新版FMEA正式版与草稿版的差异,后续黄老师将会每周撰写新文来给大家做解读及分享,敬请持续关注公众号(首页菜单的历史文章中有FMEA合集,大家可随时点击阅读旧文)。
为了方便部分已经懂了七步法的学员可以直接进行新版FMEA的使用,本篇特别将新版FMEA手册中的评分表整理出来,方便参考使用。
本篇文章建议收藏,后续可持续做为工具书随时参考使用。
关于打分说起FMEA,打分是所有FMEA制作者还有被审核者最大的痛呀。
什么情况下要打9分,什么情况下可以打1分。
45678中间怎么去做识别? 分数打太高了,客户要求做措施但是很难做。
分数打太低了,客户说你没正确识别风险。
风险分析其实FMEA的打分,一开始的立意是很好的。
是通过三个维度来帮助使用者,判断各种潜在失效模式的风险大小,并评估应该采取措施的优先顺序。
这个失效后果有多严重!?该失效发生的频度有多少!?失效能否被发现!?举例来说:一台车的安全气囊的弹出过程如果出问题了,那可是人命关天的事(前两年破产的某日本公司就是这部分出问题)。
如果只是外观上有小瑕疵,虽然也是问题,但严重度就明显不一样。
至于失效的发生,比如产品表面喷漆过程中因为空气中的微小粉尘附着,可能会导致产品表面出现小颗粒,这种发生的可能性会比较大(预防控制能力有限),可能需要在控制计划中加强检验。
如果是喷头堵塞造成问题,现行定期保养的预防措施已经足够,其发生的频度就低一点。
而一个失效的出现,如果通过设备进行防错,或是仪器精准测量,能有效识别失效模式的出现,防止不良品的流出,那探测度就很好。
如果没有好的工具或方法,只能靠人的感观去判断。
那问题产品探测不到的风险就很高了。
S O D 打分在官方出版的手册中,针对这三个分值,分别做了详细的定义。
从低风险到高风险,分别打上1-10分。
此次新版FMEA手册重新定义了打分的评级标准。
1.严重度(S):失效影响的严重度。
FMEA手册
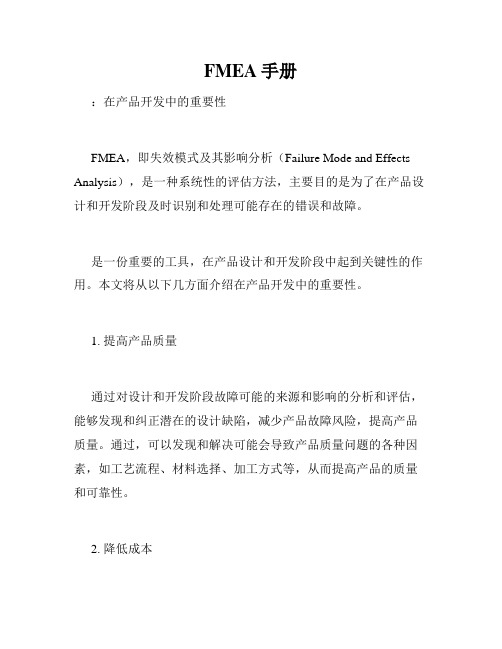
FMEA手册:在产品开发中的重要性FMEA,即失效模式及其影响分析(Failure Mode and Effects Analysis),是一种系统性的评估方法,主要目的是为了在产品设计和开发阶段及时识别和处理可能存在的错误和故障。
是一份重要的工具,在产品设计和开发阶段中起到关键性的作用。
本文将从以下几方面介绍在产品开发中的重要性。
1. 提高产品质量通过对设计和开发阶段故障可能的来源和影响的分析和评估,能够发现和纠正潜在的设计缺陷,减少产品故障风险,提高产品质量。
通过,可以发现和解决可能会导致产品质量问题的各种因素,如工艺流程、材料选择、加工方式等,从而提高产品的质量和可靠性。
2. 降低成本可以有效地减少产品开发和制造过程中的返工和修正,从而降低成本。
在设计和开发阶段发现和解决产品质量问题比在生产阶段进行修正更经济、有效。
可以细化产品的开发和制造流程,从而清晰地了解每个步骤的影响,及时发现产品质量问题,减少不必要的消耗,降低成本。
3. 强化团队合作是一个团队合作的过程。
在的制定过程中,需要专业技术人员、工程师、生产制造人员,以及机构和客户代表等各方面参与讨论和分析。
这种跨部门的合作可以加强彼此之间的合作和沟通,更好地协调各方工作的重点和方向,提高解决问题的效率。
同时,也可以建立一种团队意识和责任感,让团队共同承担产品开发和生产的风险,从而建立一个良好的质量管理体系。
4. 提高客户满意度通过,可以更好地满足客户的需求和期望,提高客户满意度。
分析归纳了整个产品开发过程中存在的问题和缺陷,提出相应的改进措施,从而更好地满足客户的需求和期望。
通过这种方式,可以让客户得到高质量的产品和服务,并提高客户的信任和忠诚度。
总之,在产品开发和制造过程中起到至关重要的作用,可以帮助企业提高产品质量和可靠性,降低成本,加强团队合作,提高客户满意度,从而帮助企业赢得市场竞争优势。
FMEA(中文培训资料)

FMEA一、FMEA介绍1.预防胜于治病。
2.在事情开始阶段就有计划地把它做对,做好3.ECN和返工都没有增值的工作,而使成本增加4.失效模式和结果分析(FMEA)是一种用于研发和生产适应性分析过程中的一种统计分析工具5.它是一种能尽早发现潜在的失效模式的精确和系统的分析工具6.它能够用于元件级的分析(功能级、元件级等)7.使用这种工具可以使产品在设计初期就能较成熟8.因此,它是企业界一种重要的基准流程二、历史1.FMEA始用于飞机制造工业中,之后用航天工程中,也用于汽车制造企业中.现在在消费电子企业也广泛采用FMEA.2.这是一个对于每个元件的失效模式的分析,系统是由每一个元件构成的3.在消费电子企业中,预防失效是很重要的,可以缩短设计的导入时间、保证设计如期完成、使费用降为最低。
三、我们为什么要用FMEA1.这是在产品设计过程的每个阶段都要有的一个认证过程2.它可以检验试产后产品的成熟度3.为了生产能够顺利开始,它可以检验试产前后产品的可生产性4.它是通往6过程中的一个工具5.它可以帮助项目经理管理一个项目质量、速度、成本三方面的平衡6.它可以检验过程质量控制的有效性7.它可以检验产品的可靠性8.它可以检验由于来料质量引起的失效9.分析不良品报表(包括售后发现的不良)四、两种类型的FMEA―――设计FMEA、制程FMEA(1)、何谓设计FMEA1.利用一个完全装配好的样机,项目的主设计师要带领设计小组从各个角度观察产品的设计2.包括以下角度:电子、机械、开模过程、制作过程、线路图的设计等3.目的是利用经验在设计初期尽可能多地发现设计上的问题4.问题在设计阶段解决要比在生产阶段解决容易、廉价得多(2)、何谓制程FMEA1. 这是一种检验设计是否适合生产装配的方法,可以确定导致生产中失效的原因,可以给出失效模式发生时,判定其严重程度的标志。
2.制程FMEA可以使设计更成熟,更易于生产,减少潜在失效的数目五、设计FMEA小组的成员构成(专注于设计失效模式)1.由主设计师领导2.研发所的电子,机械和PCB设计师3.研发所的产品评估人员和样机设计师4.工程部的工业化领导者5.寻购部的寻购工程师6.重要元件的专家六、制程FMEA小组的成员构成(专注于制程失效)1.由工业化领导来领导2.研发所的电子,机械和PCB设计师3.工程部的电子,机械和制程工程师4.波峰焊和元件布局专家5.工业工程师和产品代表6.寻购部的寻购工程师7.售后的修理技术员七、对FMEA小组成员的基本技能要求设计准则方面的知识、PCB安装过程方面的知识、元件应用方面的知识、产品的了解、工厂的布置及所用设备方面的知识、知道怎样给违反准则的案例进行严重程度的打分八、进行FMEA所需的有关文档和资料波峰焊设计准则、回流焊工艺流程设计准则、组件的所有派生要求、光板、机芯板、装配完全的样机模型、PCB机械图、PCB元件料单、PCB元件布局、爆炸图九、典型的消费电子产品的里程碑介绍准备阶段概念确认阶段产品执行阶段过程确认阶段初步生产和批量生产注:VP:价值阐述;CS:概念开始;PRS:系列产品的研发开始阶段;DR:设计评审;IR:工业化评审;CR:商业化评审;MPR:量产评审。
FMEA第四版详解资料

44
DFMEA 的开发流程
d.严重度:一个给定失效模式的最严重的后果的评 价等级.
严重度是DFMEA范围内的一个相对级别. 推荐的DFMEA严重度的评价参见手册教材第37
页。
45
DFMEA 的开发流程
e 分类级别: 可以用A; 3.在产品设计发布之前,基本完成。 4.作为一种经验的累积,为将来的设计做准备。
24
设计和过程FMEA介绍
过程FMEA是一个动态的文件: 1.应在可行性论证阶段或之前开始; 2.在生产用工装到位之前起动; 3.考虑到从单个部件到总成的所有的制造操作; 包括工厂内所有可能影响制造和装配的操作过程,
DFMEA和PFMEA都旨在根据潜在失效模式后果 对“顾客”的后果的影响,并且开发潜在失效模式 的排序清单,从而为设计改进,开发和确认试验/分 析建立一套优先控制系统.
21
设计和过程FMEA 的介绍
DFMEA为将来分析研究现场情况, 评价设计的更 改及开发更先进的设计提供参考.
PFMEA为制造过程确定一个失效模式的分级表, 建立一个考虑预防/纠正措施的优先体系.
满意这一个过程的补充. 所有的FMEA都关注设计,无论是产品设计或者过程设计.
2
FMEA和TS16949标准的接口
小组讨论5分钟,请找出FMEA在TS16949标准中 的描述条款,回答以下的问题:
1)FMEA在什么阶段来做? 2)APQP中为什么需要FMEA的分析工具?
3
什么是FMEA
FMEA的开发涉及整个APQP过程的多方论证活 动,
范围应该涵盖公司一级多个层级的供应商的 FMEA;
是工程技术评审的一部分; 是产品和过程设计例行批准和审定的一部分。
《2024年基于FMEA和FTA的医用蒸汽灭菌器可靠性分析》范文

《基于FMEA和FTA的医用蒸汽灭菌器可靠性分析》篇一一、引言随着医疗技术的不断进步,医用蒸汽灭菌器作为医疗器械消毒的重要设备,其可靠性及安全性显得尤为重要。
本文旨在通过运用故障模式与影响分析(FMEA)及故障树分析(FTA)两种方法,对医用蒸汽灭菌器的可靠性进行深入研究与分析,以期提高其产品质量和用户体验。
二、FMEA在医用蒸汽灭菌器可靠性分析中的应用1. FMEA概述FMEA是一种预防性的质量工具,通过对产品或系统的潜在故障模式进行识别、评估和优先处理,以达到提高产品可靠性和减少风险的目的。
2. FMEA实施步骤(1)确定分析系统:明确分析对象为医用蒸汽灭菌器。
(2)识别潜在故障模式:从设备运行、加热系统、控制系统、安全保护系统等方面识别可能的故障模式。
(3)评估影响:对每种潜在故障模式的影响进行评估,包括设备性能、患者安全、操作人员安全等方面。
(4)确定风险优先级:根据故障影响和发生概率确定风险优先级,为后续的改进提供依据。
3. FMEA在医用蒸汽灭菌器可靠性分析中的应用效果通过FMEA分析,可以提前发现医用蒸汽灭菌器的潜在故障模式,预测其可能产生的影响,并采取相应的预防措施,从而提高设备的可靠性。
三、FTA在医用蒸汽灭菌器可靠性分析中的应用1. FTA概述FTA是一种通过逻辑推理和演绎法来分析复杂系统或设备发生故障原因的方法。
它通过对故障事件进行分析,找出导致该事件发生的原因及影响因素,从而达到优化系统的目的。
2. FTA实施步骤(1)确定顶事件:将医用蒸汽灭菌器整体故障作为顶事件。
(2)分析中间事件及门关系:从顶事件开始,逐步分析导致其发生的中间事件及各事件之间的逻辑关系。
(3)确定基本事件:找出导致中间事件发生的基本原因或影响因素。
(4)制定纠正措施:针对基本事件制定相应的纠正措施,以降低或消除故障发生的可能性。
3. FTA在医用蒸汽灭菌器可靠性分析中的应用效果通过FTA分析,可以深入了解医用蒸汽灭菌器整体故障的原因及影响因素,找出关键环节和薄弱点,为制定针对性的改进措施提供依据。
FMEA参数
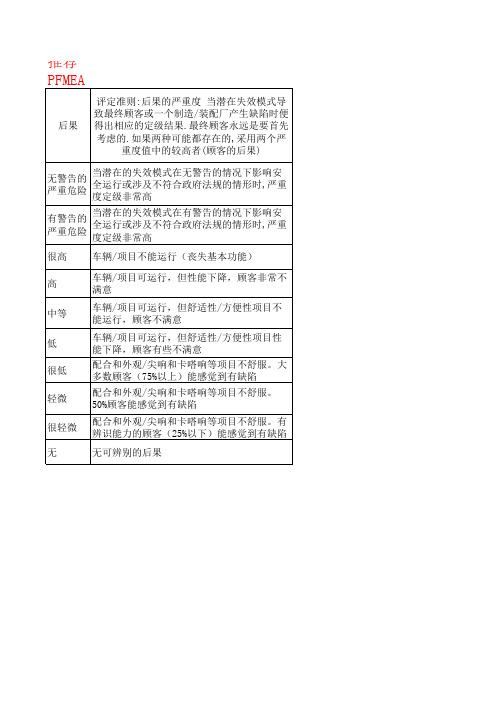
推荐PFMEA频度评价准
评定准则:后果的严重度 当潜在失效模式导致最终 顾客或一个制造/装配厂产生缺陷时便得出相应的 定级结果.最终顾客永远是要首先考虑的.如果两种 可能都存在的,采用两个严重度值中的较高者(制造 /装配后果) 或可能在无警告的情况下对(机器或总成)操作者造 成危害 或可能在有警告的情况下对(机器或总成)操作者造 成危害 或100%的产品可能需要报废,或项目需在返修部门 返修1个小时以上 或产品需要分检,一部分需要报废,或项目需在返修 部门返修时间在0.5-1小时之间 或一部分需要报废,不需分检或项目需在返修部门 返修时间少于0.5小时 100%的产品可能需要返工或项目在线下返修,不需 送往返修部门处理 或产品需要分检,无需要报废,但部分产品需返工 或部分产品需要返工,无需要报废,在产线上其他工 位返工 或部分产品需要返工,无报废,在产线上其他工位返 工 或对操作或操作者而言有轻微的不方便或无影响 严重度 失效发生可能性
9 8 7 6 5 4 3 2 1
A 防错
B 量具
C 人工检查
推荐PFMEA严重评价准则
后果 评定准则:后果的严重度 当潜在失效模式导 致最终顾客或一个制造/装配厂产生缺陷时便 得出相应的定级结果.最终顾客永远是要首先 考虑的.如果两种可能都存在的,采用两个严 重度值中的较高者(顾客的后果)
当潜在的失效模式在无警告的情况下影响安 无警告的 全运行或涉及不符合政府法规的情形时,严重 严重危险 度定级非常高 当潜在的失效模式在有警告的情况下影响安 有警告的 全运行或涉及不符合政府法规的情形时,严重 严重危险 度定级非常高 很高 高 中等 低 很低 轻微 很轻微 无 车辆/项目不能运行(丧失基本功能) 车辆/项目可运行,但性能下降,顾客非常不 满意 车辆/项目可运行,但舒适性/方便性项目不 能运行,顾客不满意 车辆/项目可运行,但舒适性/方便性项目性 能下降,顾客有些不满意 配合和外观/尖响和卡嗒响等项目不舒服。大 多数顾客(75%以上)能感觉到有缺陷 配合和外观/尖响和卡嗒响等项目不舒服。 50%顾客能感觉到有缺陷 配合和外观/尖响和卡嗒响等项目不舒服。有 辨识能力的顾客(25%以下)能感觉到有缺陷 无可辨别的后果
- 1、下载文档前请自行甄别文档内容的完整性,平台不提供额外的编辑、内容补充、找答案等附加服务。
- 2、"仅部分预览"的文档,不可在线预览部分如存在完整性等问题,可反馈申请退款(可完整预览的文档不适用该条件!)。
- 3、如文档侵犯您的权益,请联系客服反馈,我们会尽快为您处理(人工客服工作时间:9:00-18:30)。
FMEAFMEA No.控制计划编号FMEA0800-0001Model No.型号0800-02/03-00Original Date日期(原始)16/5/2000Revision No. 修订编号06Total Pages总页数7Revision Date日期(修订)08/09/2003Revision History修订记录Rev. 修订Effective Date生效日期Revision Detail修订内容Prepared by制作者Signed by审批Date日期00 16/05/2000 New release 800 core team01 01/06/2001 Changed contents in page 7, 8, 11, 12 & 13 800 core team02 17/01/2002 FMEA0800-0002 incorporated into FMEA0800-0001, andFMEA0800-0002 canceled correspondently800 core team03 15/08/2002 Changed format per the new edition of FMEA Manual, and changedFMEA per the meeting and training of APQP Team800 core team04 11/04/2003 Flux residue added as a “Potential Cause / Mechanism of Failure” of“Solder Ball / Solder Particle”, A120 / A145;RPN changed and a “Recommended Action” added for A220;The Recommended Action for A250 in the last revision completed,the Present Process Control and the RPN value changedaccordingly;A120,Nozzel clean cycle changed;A220 Screw driver changed;A250 Add electronical balance to prevent missing packing material.0800 core team05 21/05/2003 Adding models 0800 core team06 08/09/2003 Changed Core Team member and added A220 middle frameprinting (such as IP30);0805 apart from 0800 (Delete 0805 ModelNo)0800 core team页码2之7项目:0800-02 / 03-00 SMC 制程责任:MFG3 填表人:ST Yim产品生产年份:2000年5月主要日期:2000年11月FMEA 日期(原始)25/11/1999(修订)08/09/2003核心小组:流程功能要求潜在失效模式潜在失效效应严重度等级潜在失效原因/机制发生度现行流程管制预防措施现有流程管制检查方法难检度风险优先值建议措施责任及目标完成时间行动结果采取的措施严重度发生度难检度风险优先值AS5胶水印刷(胶水能准确地转移到PCB上)印刷模糊胶水拖尾粘力不够易漏件5 印刷机工作参数设定不良4 1. SMT技术员/IPQC每班作业前检查机器参数;2. QA每小时每台机检查2块板;3.IPQC每小时每台机检查2块板1 205 印刷网底积聚残余胶渣3 1 每班作业前洗网2 作业中每印5-10次后抹网底1. IPQC每班检查印刷网;2.IPQC每小时每台机检查2块板;3. QA每小时每台机检查2块板1 15少胶/无胶 6 印刷网孔堵塞 4 作业中定期用风枪清理网孔胶渣1. IPQC每班检查印刷网;2.IPQC每小时每台机检查2块板;3. QA每小时每台机检查2块板2 48A10SMT安装(元件能准确地安装到PCB指定的位置上) 元件偏位料竖、可靠性不良7 机器参数设定不准确2 调校机器/Model;首件检查1. IPQC每小时每台机检查2块板;2. QA每小时每台机检查1块板3 42错料功能不良7 Feeder上错料 2 按Feeder List上料 1. IPQC每小时每台机检查2块板;2. QA每小时每台机检查1块板;3. IPQC每次开机,换料或转型号时对料检查2 28错向功能不良7 安装程序设定不良或来料与原安装程序不同2 1. IPQC每小时每台机检查2块板;2. QA每小时每台机检查1块板3 42AS15胶水固化(元件与PCB充分粘合)漏件影响功能7 炉温设定不良导致粘力不够2 1. IPQC每小时每台机检查2块板;2. QA每小时每台机检查2块板;3.QA每天每型号检查三块板的推力;4IPQC、QA每班检查一次炉温1 14页码3之7项目:0800-02 / 03-00 插机—包装出货制程责任:MFG1 and IE 填表人:HL Cho产品生产年份:2000年5月主要日期:2000年11月FMEA 日期(原始)25/11/1999(修订)08/09/2003 核心小组:Tony Kwok, Chao Lau, ST Yim, Yin Hung,YK Cheung, YM Kong, HL Cho, YC Li,William Wan, Matsumoto , YS Wong , Micheal Woo ,流程功能要求潜在失效模式潜在失效效应严重度等级潜在失效原因/机制发生度现有流程管制预防措施现有流程管制检查方法难检度风险优先值建议措施责任及目标完成时间行动结果采取的措施严重度发生度难检度风险优先值A100零件成型(尺寸符合要求,没有破损)零件破损功能不良7机架调校不良2技术员试加工,确定机架良好员工自检3427机架零件磨损2定期维修更换员工自检335加工尺寸不符规格插机困难5机架调校不良3试加工确认员工自检345A110插机(元件种类、方向、高度正确,后焊焊盘贴好阻焊胶纸)插错料,插错方向功能不良或降低可靠性7操作错误及拿错近似的料3同一人盡量避免插近似的料QA首件检查;员工自检242坏料与好料混合使用坏料导致功能不良7坏料沒分开2用专门的坏料盒装坏料QA首件检查;员工自检342后焊焊盘无阻焊胶纸焊盘上锡从而影响后焊操作正常进行6漏貼胶紙3员工自检236元件高度不对外观不良或降低可靠性7操作错误3员工自检242A120波峰焊接/ A145二次波峰焊接少锡,无锡功能不良或降低可靠性6喷头堵塞造成松香不均2每4小吋锡炉工清洗喷头,定期保养QA每小时抽查三块板;员工自检448(焊点符合IPC 要求,没有锡珠、锡碎等,元件没有损坏)7大,小锡波不均或高度不够2锡炉工及IFE检查并调校马达参数QA每小时抽查三块板;员工自检342多锡,短路外观不良功能坏机7松香比重不适2IFE两小时测一次QA每小时抽查三块板;IFE检查1次/2小时并记录报表4487预热温度超出范围.2锡炉工自检,IFE每天作温度profile并调校锡炉参数QA每小时抽查三块板;IFE检查1次/2小时并记录报表3427锡炉杂质 1 锡炉工两小时清一次炉QA每小时抽查三块板3 21页码4之7项目:0800-02 / 03-00 插机—包装出货制程责任:MFG1 and IE 填表人:HL Cho产品生产年份:2000年5月主要日期:2000年11月FMEA 日期(原始)25/11/1999(修订)08/09/2003 核心小组:Tony Kwok, Chao Lau, ST Yim, Yin Hung,YK Cheung, YM Kong, HL Cho, YC Li,William Wan, Matsumoto , YS Wong , Micheal Woo ,流程功能要求潜在失效模式潜在失效效应严重度等级潜在失效原因/机制发生度现有流程管制预防措施现有流程管制检查方法难检度风险优先值建议措施责任及目标完成时间行动结果采取的措施严重度发生度难检度风险优先值锡珠,锡碎降低可靠性5PCB板受潮1QA每小时抽查三块板5255 板面余有松香 2 板底间隙贴胶纸,过炉加松香罩QA每小时抽查三块板3 306锡炉杂质 3 锡炉工两小时请一次炉QA每小时抽查三块板354元件损坏功能不良或降低可靠性7大,小锡波温度过高2IFE每天作温度profile并调校锡炉参数QA每小时抽查三块板;IFE检查1次/2小时并记录报表342A130收板(完全清除档块等)没有完全清除档块,胶纸,牙签等装配,外观不良5作业错误3员工自检345A140剪脚(元件肚子长度合适,不能造成裂锡)剪脚过短或过长影响装配或降低6不掌握剪脚高度3员工自检;QC100%目视检查336裂锡断路或降低可靠性7剪钳钝化或剪脚时刀峰不平行PCBA板且用力不均匀;(剪脚过程中抖动或翻转手腕)2二次波峰焊接及定时更換剪钳员工自检刀锋状况;QC100%目视检查342A150板面执锡/ A160板底执锡(焊点符合IPC 要求,不能造成元件损坏)板面尚有锡珠、连锡、少锡、无锡等功能坏机6执锡遗漏3分区执锡減少遺漏员工自检;QC100%目视检查236元件损坏功能坏机6烙铁溫度太高3每天检查烙铁溫度354A170清洗(不能留有锡珠、锡碎等)板底,板面余有锡珠,锡碎锡渣功能不良6作业错误3QC100%目视检查354页码5之7项目:0800-02 / 03-00 插机—包装出货制程责任:MFG1 and IE 填表人:HL Cho产品生产年份:2000年5月主要日期:2000年11月FMEA 日期(原始)25/11/1999(修订)08/09/2003 核心小组:Tony Kwok, Chao Lau, ST Yim, Yin Hung,YK Cheung, YM Kong, HL Cho, YC Li,William Wan, Matsumoto , YS Wong , Micheal Woo ,流程功能要求潜在失效模式潜在失效效应严重度等级潜在失效原因/机制发生度现有流程管制预防措施现有流程管制检查方法难检度风险优先值建议措施责任及目标完成时间行动结果采取的措施严重度发生度难检度风险优先值A180后焊LED高度不符规格外观不良5装配不良3机架定位 1 QA每天每个型号抽检三块板; 2 QC100%目视检查345热敏电阻高度不符规格性能精度不良6装配错误3机架定位同上354(LED和热敏电阻的高度符合要求,锡点符合IPC要求)焊点不良(拉尖, 连锡,锡空等)降低可靠性6不按以下焊锡方法:1,烙铁头预热焊盘;2,锡线靠近焊盘使之熔化;3,锡线离开后再将烙铁拿开.3 1 QA按MIL-STD-105E抽检2 QC100%目视检查354A190除锡珠(不能有残留的锡珠)PCBA板残留锡珠降低可靠性6吸嘴损坏3员工自检3546锡珠太少,容易看漏3IPQC用10X或以上放大镜全检354A210连接主板与电源板/打热熔胶(不能有锡珠、锡碎,热熔胶结合紧密)焊点间存有锡珠,锡碎电气短路、功能失效7锡线含松香过多2使用990014锡线,焊完后用洗机水擦净焊点员工自检3427不按以下执锡方法:1,烙铁头预热焊盘;2,锡线靠近焊盘使之熔化;3,锡线离开后再将烙铁拿开2生产主管、组长巡拉检查228热熔胶松脱FFC线焊接处断开引起功能失效7热熔胶枪出胶不均2维修或更换胶枪QC100%目视检查;100%功能测试342A220组装螺丝金属碎短路引起功能失效7螺丝之间碰撞造成2清洗QC100%目视检查342(端子及其它地方不能留有7打螺丝时,螺丝同电批嘴磨擦造成1底壳打端子螺丝时改用手批QC100%目视检查321页码6之7项目:0800-02 / 03-00 插机—包装出货制程责任:MFG1 and IE 填表人:HL Cho产品生产年份:2000年5月主要日期:2000年11月FMEA 日期(原始)25/11/1999(修订)08/09/2003 核心小组:Tony Kwok, Chao Lau, ST Yim, Yin Hung,YK Cheung, YM Kong, HL Cho, YC Li,William Wan, Matsumoto , YS Wong , Micheal Woo ,流程功能要求潜在失效模式潜在失效效应严重度等级潜在失效原因/机制发生度现有流程管制预防措施现有流程管制检查方法难检度风险优先值建议措施责任及目标完成时间行动结果采取的措施严重度发生度难检度风险优先值金属碎,外壳来料良好)壳发白,裂纹降低产品寿命6螺丝批钮力太大3生产部及IFE检查IFE每天检查螺丝批扭力3546塑胶壳来料材质差3QC100%目视检查;IQC按MIL-STD-105E检查354端子堵塞影响产品的使用性7端子螺丝来料不良2QC全检;IQC按MIL-STD-105E检查;端子测试342绝缘性能不够影响最终用户的安全1来料性能不合格 1 100%Hi-Po测试;IQC按MIL-STD-105E检查来料1 10温度精确度不够影响最终客户满意度7 ◇热敏电阻精度不够1 100%温度测试;IQC按MIL-STD-105E检查来料1 7中壳丝印标识(如IP30等)漏及丝印不良影响最终客户使用 6 ◇中壳来料不良 2 员工自检QC全检;IQC按MIL-STD-105E检查1 12A230盖印(字迹清晰)字迹残缺不清影响外观5印章损坏3更换员工自检345A250包装(无错件、少件)少放或错放物品附件(螺丝,说明书等)影响产品的使用;6员工操作失误 2 1 螺丝,说明书等附件先由操作员按要求配套放好,再进行包装2每种型号做Sample;3.用电子磅称重量,并和标准重量QA按MIL-STD-105E抽检336页码7之7项目:0800-02 / 03-00 插机—包装出货制程责任:MFG1 and IE 填表人:HL Cho产品生产年份:2000年5月主要日期:2000年11月FMEA 日期(原始)25/11/1999(修订)08/09/2003 核心小组:Tony Kwok, Chao Lau, ST Yim, Yin Hung,YK Cheung, YM Kong, HL Cho, YC Li,William Wan, Matsumoto , YS Wong , Micheal Woo ,流程功能要求潜在失效模式潜在失效效应严重度等级潜在失效原因/机制发生度现有流程管制预防措施现有流程管制检查方法难检度风险优先值建议措施责任及目标完成时间行动结果采取的措施严重度发生度难检度风险优先值相比较.页码8之7项目:0800-02 / 03-00 Storage and Handling 制程责任:IE 填表人:HL Cho产品生产年份:2000年5月主要日期:2000年11月FMEA 日期(原始)25/11/1999(修订)08/09/2003 核心小组:Tony Kwok, Chao Lau, ST Yim, Yin Hung,YK Cheung, YM Kong, HL Cho, YC Li,William Wan, Matsumoto , YS Wong , Micheal Woo ,流程功能要求潜在失效模式潜在失效效应严重度等级潜在失效原因/机制发生度现有流程管制预防措施现有流程0管制检查方法难检度风险优先值建议措施责任及目标完成时间行动结果采取的措施严重度发生度难检度风险优先值贮存(来料)来料变质影响产品外观或功能6 超过贮存期 2 1 先入先出系统2 控制仓存量半年进行一次仓存期检查3 366 贮存温度或湿度过高2 配备温、湿度调节系统及温、湿度仪每天检查温湿度1 12贮存(成品)产品变质功能或外观不良7 超过贮存期 2 每三个月进行一次仓存期检查3 42搬运破坏IC等部件的功能功能不良7 静电带或静电台坏,失去释放静电的作用2 每天检查静电带,每三个月检查静电台2 28。