氧化异常解决方案
阳极氧化异常处理
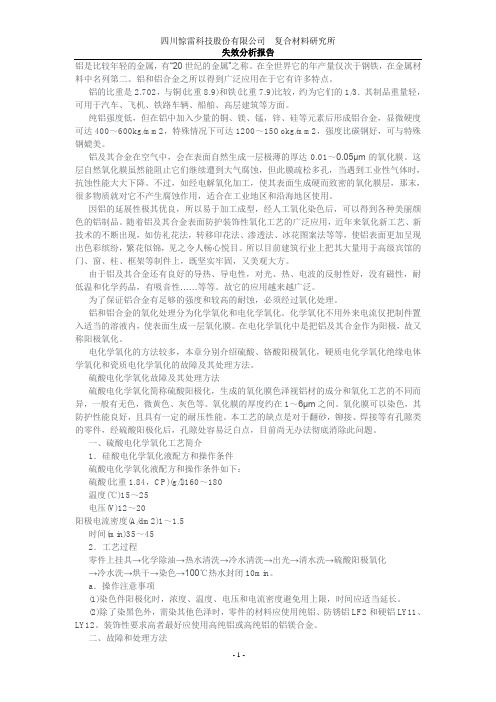
铝是比较年轻的金属,有“20世纪的金属”之称。
在全世界它的年产量仅次于钢铁,在金属材料中名列第二。
铝和铝合金之所以得到广泛应用在于它有许多特点。
铝的比重是2.702,与铜(比重8.9)和铁(比重7.9)比较,约为它们的1/3.其制品重量轻,可用于汽车、飞机、铁路车辆、船舶、高层建筑等方面。
纯铝强度低,但在铝中加入少量的铜、镁、锰,锌、硅等元素后形成铝合金,显微硬度可达400~600kg/mm2,特殊情况下可达1200~15Ookg/mm2,强度比碳钢好,可与特殊钢媲美。
铝及其合金在空气中,会在表面自然生成一层极薄的厚达0.01~0.05μm的氧化膜。
这层自然氧化膜虽然能阻止它们继续遭到大气腐蚀,但此膜疏松多孔,当遇到工业性气体时,抗蚀性能大大下降。
不过,如经电解氧化加工,使其表面生成硬而致密的氧化膜层,那末,很多物质就对它不产生腐蚀作用,适合在工业地区和沿海地区使用。
因铝的延展性极其优良,所以易于加工成型,经人工氧化染色后,可以得到各种美丽颜色的铝制品。
随着铝及其合金表面防护装饰性氧化工艺的广泛应用,近年来氧化新工艺、新技术的不断出现,如仿礼花法,转移印花法、渗透法、冰花图案法等等,使铝表面更加呈现出色彩缤纷,繁花似锦,见之令人畅心悦目。
所以目前建筑行业上把其大量用于高级宾馆的门、窗、柱、框架等制件上,既坚实牢固,又美观大方。
由于铝及其合金还有良好的导热、导电性,对光、热、电波的反射性好,没有磁性,耐低温和化学药品,有吸音性……等等。
故它的应用越来越广泛。
为了保证铝合金有足够的强度和较高的耐蚀,必须经过氧化处理。
铝和铝合金的氧化处理分为化学氧化和电化学氧化。
化学氧化不用外来电流仅把制件置入适当的溶液内,使表面生成一层氧化膜。
在电化学氧化中是把铝及其合金作为阳极,故又称阳极氧化。
电化学氧化的方法较多,本章分别介绍硫酸、铬酸阳极氧化,硬质电化学氧化绝缘电体学氧化和瓷质电化学氧化的故障及其处理方法。
硫酸电化学氧化故障及其处理方法硫酸电化学氧化简称硫酸阳极化,生成的氧化膜色泽视铝材的成分和氧化工艺的不同而异,一般有无色,微黄色、灰色等。
氧化岗位异常情况处置牌

氧化岗位异常、紧急情况处置方案序号异常、紧急情况应急处理措施1 停电1.本岗位操作工立即关闭发烟硫酸滴加阀门,停止向锅内滴加硫酸。
2.观察冷冻水是否正常,如无冷冻水立即关闭反应锅进出水冷却阀门。
3.立即向班长报告,始终观察温度计所显示温度并做好记录。
4.来电时确定冷冻水正常后,打开反应锅冷冻水进出水阀30分钟后,温度控制在工艺规定温度的下限,点动反应锅电机数次,待温度不再有上升趋势后,方可正常开启反应锅搅拌。
2 超温1.本岗位操作工立即关闭发烟硫酸滴加阀门,停止向锅内滴加发烟硫酸。
2.观察有无冷冻水,如有开大冷却水阀门降温,如无立即关闭冷冻水进出水阀门。
3.通知班长,始终观察温度计所显示温度并做好记录。
3 停水(冷冻盐水)1.本岗位操作工立即关闭发烟硫酸阀门,停止向锅内滴加硫酸。
2.通知班长,始终观察温度计所显示温度并做好记录。
4 设备、管道破裂1.立即关闭有关阀门,停止反应。
2.找到检修人员进行抢修。
3.安全转移事故容器内的物料。
4.立刻停止一切可以引起火源的活动。
5.撤离非必要人员。
5 发烟硫酸腐蚀性物质泄漏迅速撤离泄漏污染区人员至安全区,并立即隔离150m,严格限制出入。
建议应急处理人员戴正压式呼吸器,穿防自给酸碱工作服。
不要直接接触泄漏物。
尽可能切断泄漏源。
小量泄漏:将地面洒上苏打灰,然后用大量水冲洗,洗水稀释后放入废水系统。
大量泄漏:构筑围堤或挖坑收容。
在专家指导下清除。
6 火灾和爆炸事故1.爆炸事故:立即进行人员撤离。
并迅速上报。
2. 立即向上级报告。
3. 查明情况,向现场总指挥汇报撤离时现场的情况。
4. 确定警戒范围和危险区的隔离;5. 救生。
如果有人员被困,组成救人小组,携带救生器材迅速进入危险区域,应立即将被困人员解救出来;对救出人员进行登记、标识和现场急救。
6. 先打开与事故储罐或反应设备邻近储罐的冷却管线出水冷却,同时打开消防栓进行自救。
7. 关阀断源。
生产装置发生泄漏,应急队员积极配合事故,单位有关技术人员和业务技术熟练的工人在严密防护措施的前提下,断绝物料供应,切断事故源。
铝合金硬质阳极氧化常见缺陷的原因分析及措施
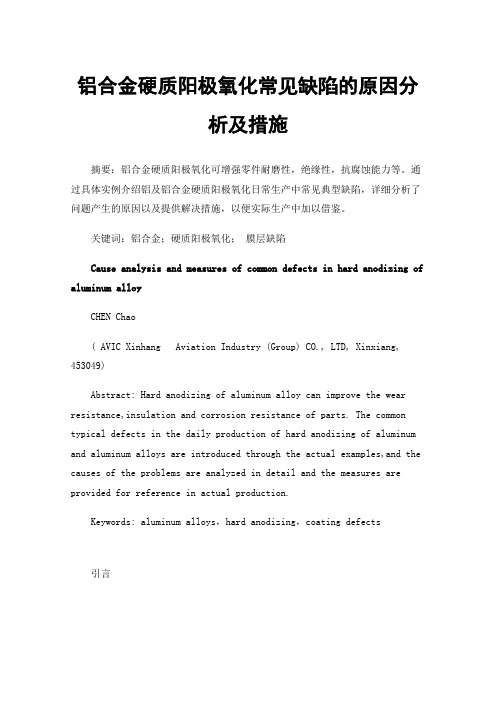
铝合金硬质阳极氧化常见缺陷的原因分析及措施摘要:铝合金硬质阳极氧化可增强零件耐磨性,绝缘性,抗腐蚀能力等。
通过具体实例介绍铝及铝合金硬质阳极氧化日常生产中常见典型缺陷,详细分析了问题产生的原因以及提供解决措施,以便实际生产中加以借鉴。
关键词:铝合金;硬质阳极氧化;膜层缺陷Cause analysis and measures of common defects in hard anodizing of aluminum alloyCHEN Chao( AVIC Xinhang Aviation Industry (Group) CO., LTD, Xinxiang, 453049)Abstract: Hard anodizing of aluminum alloy can improve the wear resistance,insulation and corrosion resistance of parts. The common typical defects in the daily production of hard anodizing of aluminum and aluminum alloys are introduced through the actual examples,and the causes of the problems are analyzed in detail and the measures are provided for reference in actual production.Keywords: aluminum alloys,hard anodizing,coating defects引言铝及铝合金具有比强度高,塑性好,导电,导热性能优异,以及优良的加工性能和耐蚀性能,是广泛应用于各种工业领域,特别是航空、航天工业中的有色金属材料[1]。
一起压板氧化造成越级跳闸事故分析及处理
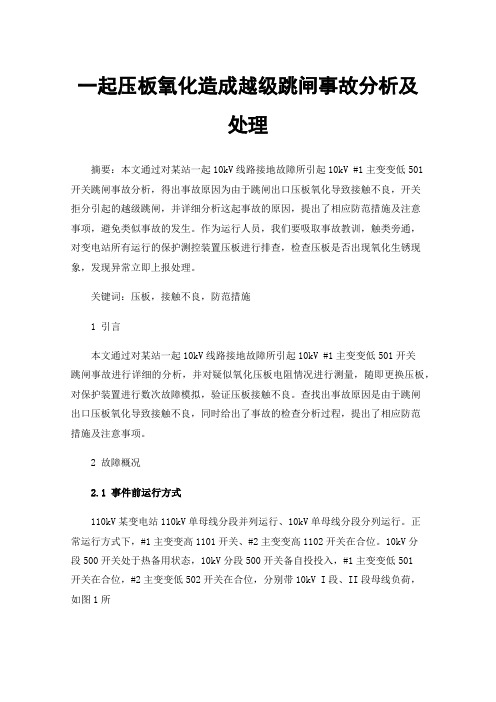
一起压板氧化造成越级跳闸事故分析及处理摘要:本文通过对某站一起10kV线路接地故障所引起10kV #1主变变低501开关跳闸事故分析,得出事故原因为由于跳闸出口压板氧化导致接触不良,开关拒分引起的越级跳闸,并详细分析这起事故的原因,提出了相应防范措施及注意事项,避免类似事故的发生。
作为运行人员,我们要吸取事故教训,触类旁通,对变电站所有运行的保护测控装置压板进行排查,检查压板是否出现氧化生锈现象,发现异常立即上报处理。
关键词:压板,接触不良,防范措施1 引言本文通过对某站一起10kV线路接地故障所引起10kV #1主变变低501开关跳闸事故进行详细的分析,并对疑似氧化压板电阻情况进行测量,随即更换压板,对保护装置进行数次故障模拟,验证压板接触不良。
查找出事故原因是由于跳闸出口压板氧化导致接触不良,同时给出了事故的检查分析过程,提出了相应防范措施及注意事项。
2 故障概况2.1 事件前运行方式110kV某变电站110kV单母线分段并列运行、10kV单母线分段分列运行。
正常运行方式下,#1主变变高1101开关、#2主变变高1102开关在合位。
10kV分段500开关处于热备用状态,10kV分段500开关备自投投入,#1主变变低501开关在合位,#2主变变低502开关在合位,分别带10kV I段、II段母线负荷,如图1所示。
图1 事件前运行方式2.2 事件经过2020年05月10日05时18分14秒,110kV某变电站10kV F10佰易线发生接地故障,零流故障二次电流8.121A(定值0.95A),10kV F10零流I段保护正确动作,但未跳开510开关;保护装置、站内监控后台均无510开关变位信息。
05时18分15秒#1站变兼接地变高零流1时限动作,故障电流1.35A(定值0.24A),闭锁备自投,持续2.891s后(定值2.5s),高零流2时限动作,故障电流1.32A,跳开#1主变变低501开关,10kV IM失压。
阳极氧化异常处理
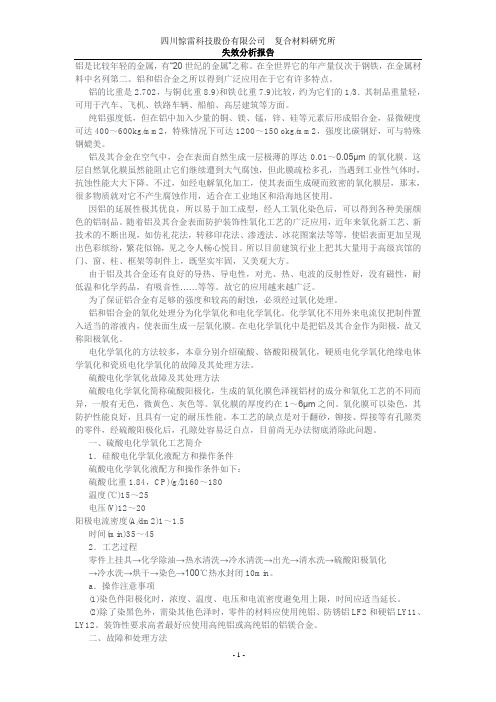
铝是比较年轻的金属,有“20世纪的金属”之称。
在全世界它的年产量仅次于钢铁,在金属材料中名列第二。
铝和铝合金之所以得到广泛应用在于它有许多特点。
铝的比重是2.702,与铜(比重8.9)和铁(比重7.9)比较,约为它们的1/3.其制品重量轻,可用于汽车、飞机、铁路车辆、船舶、高层建筑等方面。
纯铝强度低,但在铝中加入少量的铜、镁、锰,锌、硅等元素后形成铝合金,显微硬度可达400~600kg/mm2,特殊情况下可达1200~15Ookg/mm2,强度比碳钢好,可与特殊钢媲美。
铝及其合金在空气中,会在表面自然生成一层极薄的厚达0.01~0.05μm的氧化膜。
这层自然氧化膜虽然能阻止它们继续遭到大气腐蚀,但此膜疏松多孔,当遇到工业性气体时,抗蚀性能大大下降。
不过,如经电解氧化加工,使其表面生成硬而致密的氧化膜层,那末,很多物质就对它不产生腐蚀作用,适合在工业地区和沿海地区使用。
因铝的延展性极其优良,所以易于加工成型,经人工氧化染色后,可以得到各种美丽颜色的铝制品。
随着铝及其合金表面防护装饰性氧化工艺的广泛应用,近年来氧化新工艺、新技术的不断出现,如仿礼花法,转移印花法、渗透法、冰花图案法等等,使铝表面更加呈现出色彩缤纷,繁花似锦,见之令人畅心悦目。
所以目前建筑行业上把其大量用于高级宾馆的门、窗、柱、框架等制件上,既坚实牢固,又美观大方。
由于铝及其合金还有良好的导热、导电性,对光、热、电波的反射性好,没有磁性,耐低温和化学药品,有吸音性……等等。
故它的应用越来越广泛。
为了保证铝合金有足够的强度和较高的耐蚀,必须经过氧化处理。
铝和铝合金的氧化处理分为化学氧化和电化学氧化。
化学氧化不用外来电流仅把制件置入适当的溶液内,使表面生成一层氧化膜。
在电化学氧化中是把铝及其合金作为阳极,故又称阳极氧化。
电化学氧化的方法较多,本章分别介绍硫酸、铬酸阳极氧化,硬质电化学氧化绝缘电体学氧化和瓷质电化学氧化的故障及其处理方法。
硫酸电化学氧化故障及其处理方法硫酸电化学氧化简称硫酸阳极化,生成的氧化膜色泽视铝材的成分和氧化工艺的不同而异,一般有无色,微黄色、灰色等。
焊接异常处理方案

焊接异常处理方案在焊接过程中,经常会出现焊接异常的情况,例如出现焊缝间隙、氧化、裂纹和焊缝不牢等问题。
这些问题可能会导致焊接部件的性能下降或者完全失效。
因此,在焊接过程中,需要及时采取相应的处理方案来解决这些异常情况。
本文将介绍一些常见的焊接异常处理方案。
焊缝间隙焊缝间隙是指焊缝两侧的两个零件之间的间隙。
在操作不规范的情况下,该间隙可能会过大导致两个零件不能够完全焊接在一起,从而影响零件的整体性能。
解决方案如下:•调整焊接位置:在焊接过程中,如果发现焊缝间隙过大,可以尝试将焊接位置向间隙较小的方向移动,以此来减小焊缝间隙。
•加热零件:在焊接前,可以利用火炬或者加热板等工具对零件进行加热处理,以此来使零件变形,从而减小焊缝间隙的大小。
•采用填充金属:在焊接时,可以使用填充金属来填充焊缝间隙,以此来保证两个零件完全焊接在一起。
不过需要注意的是,填充金属的选择和加热温度需要根据具体情况进行调整。
氧化氧化是指焊件表面上出现的氧化物。
如果不及时去除氧化物,将会影响焊件的质量和性能。
以下是一些常见的氧化处理方案:•利用铜钱:利用铜钱对焊缝表面进行磨擦,以此来去掉氧化层。
不过需要注意的是,使用铜钱时需要避免磨损过度。
•使用金属刷:使用金属刷对焊缝表面进行刷洗,以此来去掉氧化层。
需要注意的是,使用金属刷时需要避免刷损过度。
•激光清洗:使用激光技术对焊缝表面进行清洗。
这种方式非常有效,但需要使用高端设备,且成本较高。
裂纹焊接时裂纹的出现是非常常见的。
如果不及时解决,较大的裂纹将会影响零件的整体性能和安全性。
以下是一些常用的裂纹处理方案:•热处理:对零件进行热处理,以此来去除焊接区域的应力,从而可以减少裂纹的出现。
•控制焊接速度:控制焊接速度,让焊接温度逐渐升高,逐渐冷却。
这种方式可以减少焊接产生的应力,从而减少裂纹的产生。
•选择适当的电流和电压:选择适当的电流和电压,可以减少焊接时的温度变化,从而减少裂纹的产生。
污水处理生化异常情况处理

污水处理生化异常情况处理引言概述:污水处理是保护环境和人类健康的重要环节。
然而,在实际运营中,污水处理厂常常会遇到生化异常情况,如氨氮过高、COD(化学需氧量)过高等问题。
本文将就污水处理生化异常情况的处理方法进行详细阐述。
正文内容:1. 氨氮过高的处理方法1.1 调整曝气量:适当增加曝气量能够提高氨氮的去除效果。
1.2 调整曝气时间:延长曝气时间可以增加氨氮的氧化反应时间。
1.3 添加硝化菌剂:通过添加硝化菌剂来增加污水中的硝化菌数量,加速氨氮的转化为硝态氮。
1.4 优化污水处理工艺:通过调整污水处理工艺,如增加好氧池的容积等,提高氨氮的处理效果。
1.5 加强污泥处理:合理处理好污泥,避免污泥中的氨氮再次释放到水体中。
2. COD过高的处理方法2.1 加强预处理:通过加强预处理工艺,如格栅、沉砂池等,去除大颗粒污染物,减少COD的负荷。
2.2 调整曝气量和曝气时间:适当增加曝气量和曝气时间,提高生化池内微生物的活性,加速COD的降解。
2.3 添加COD降解剂:添加COD降解剂,如硝化菌剂、好氧颗粒污泥等,促进COD的降解。
2.4 优化曝气方式:采用更加合理的曝气方式,如增加曝气孔、改变曝气方式等,提高氧气传递效率,促进COD的降解。
2.5 定期清理污泥:定期清理生化池中的污泥,避免污泥中COD的再次释放。
总结:在污水处理过程中,生化异常情况的处理至关重要。
针对氨氮过高和COD过高的情况,我们可以通过调整曝气量、曝气时间、添加适当的菌剂以及优化污水处理工艺等方式来提高处理效果。
同时,加强预处理和定期清理污泥也是有效的措施。
通过这些方法,我们可以更好地应对污水处理生化异常情况,保障环境和人类健康。
氨氧化率测定异常的原因及解决措施

(NH3)=
x 100
式 中 。(NH,)— —混合 气 中氨 的质量分数 ,% ; — — 滴定 消耗 的硫 酸标 准滴 定溶 液 的体
积 ,mL; C,— —硫 酸 标准滴 定 溶液 的浓 度 ,mol/L; — — 滴 定 消耗 的氢 氧化钠 标准 滴定 溶 液
1 试 验 部分
1.1 试 剂 与 仪 器 硫 酸 标 准 滴 定 溶 液 c (1/2 H:SO )
0.100 0 mol/L
氢 氧 化 钠 标 准 滴 定 溶 液 c (NaOH)
0.100 0 mol/L
[收稿 日期 ]2015-07—14 [作者简介]李常 山(1977一 ),男 ,甘肃 武威人 ,化工分析工 程师 ,质量工程师 ,长期从事化工分析工作 。
注 :混合 气 中 氨 含量 测 定 近 终 点 时 ,加 入 甲基 红 指 不 剂 均 出 现 褪 色现 象 。
由表 1可 知 :4台氧化 炉 的氨氧 化 率 测定 结 果 不 时出现 大 于 100% 的现 象 ,超 过 了理论 最 高 值 98.5% … ,存 在 明显 的误 差 。从 氨含 量 测 定 过 程 中近终 点 时 加 人 甲基 红 指 示 剂 出现 褪 色 现 象 ,推 断这 种异 常现 象并非 偶然 ,样 品 中可能存 在 氧化性 干扰 物质 ,或 者有 其他 因素对 测 定过 程 产 生 了影 响 。 2.2 混合 气温度 对氨 氧化 率测 定的影 响
的体 积 ,mL; c — — 氢 氧 化 钠 标 准 滴 定 溶 液 的 浓 度 ,
m ol/L;
17.O3— — NH3的摩 尔质 量 ,g/tool; m —— 试样 的质量 ,g。 1.3.2 转化气 中氧化 氮含 量 的计算 转化 气 中氧 化 氮 (以 NH 计 ) 的质 量 分 数 按下 式计 算 :
矿区生物接触氧化工艺的运行管理与异常对策

中遇接纳水质突发改变 、 活 性污泥膨 胀等 非正常 情 况束 手无 策 , 对 出水 水 质 的 评 价 只 局 限 于 人 体 感 观 。笔者 结 合 自身 专 业 特 点 , 经 过 总 结 多 年 来 的 实践 运行 经 验 , 在 华 晋 焦煤 有 限 责 任 公 司 内 部 形成了一套比较成熟的生物接触氧化工艺运行管
中图分类号: F 4 0 6 . 3 ; X 7 0 3
文献标志码 : B
文章编号 : 1 0 0 8 — 0 1 5 5 ( 2 0 1 7 ) 1 4 — 0 0 7 4 — 0 2
生物接触氧化法是当前给排水设 计中经常采 用 的技 术工 艺 。在 山西 地 区众 多 煤 矿 生活 污 水 处 理工 艺 中十 之 八 九 采 用 这一 工 艺 , 但 是 在 实 际 的 运行 管理 过 程 中 , 由 于煤 矿 自身 运 行 管 理 水 平 的 局限 性 , 对集 中 生 活 区 和 工 业 区 生 活 污 水 处 理 站 采用单一方法运行 , 导致生物接触氧化工艺 出现 各种 问题 , 甚至有人对工艺的先进性提 出了质疑 。 作者通过多年从事煤矿环保工 作的实践 , 经过 总 结多年来的实践运行经验 , 在华晋焦煤有限责 任 公司内部形成 了一套比较成熟的生物接触氧化工 艺运 行管 理 与异 常处理 对策 。 生物接触氧 化法是生物膜法 的形 式之一 , 生 物接触氧化工艺是在曝气 池中安装固定填料 , 正 常运行状态下, 填料表面附着了生物膜 , 填料空隙 中充满了活性污 泥。填料底部设 置有 曝气 管 , 含 有机物的污水在 曝气 管压缩 空气上 升 力的带 动 下, 水 中有机 物 与填料 表 面 充分 地 接 触 , 填料 表 面 生物膜和填料空隙中的活性污泥对原水 中有机物 质进行吸附、 降解 , 从而使污水得到净化 。生物接 触 氧 化法 与活 性污 泥法 的共 同 特 点是 污 水 充满 整 个 曝 气池 , 并 且都 需要 人 工 曝气 , 主 要 区别在 于 生 物接触氧化池比曝气 池增加 了填料 。生物接触氧 化 法 与生物 滤 池 的共 同点 是 生物 膜 附着 在 固定 的 滤 床 或填料 上 , 污水 通 过 流 动 与生 物 膜进 行 接 触 , 主 要 区别在 于 生物 滤 池 的滤床 较 生 物 接 触氧 化 法 的填料 密 实 , 更 容 易截 留水 中杂 质 。 因此 , 生 物 接 触 氧化 法有 活 性 污 泥 法 和 生 物 滤 池 的特 点 , 在 城 市 生 活污水 、 工 业 企 业 生 活 污 水 的处 理 工 艺 中 广 泛 采用 。 笔者所 在 的华晋 焦煤有限 责任 公 司沙 曲一 矿、 沙 曲选煤 厂 生 活 污 水 处 理 站都 采 用 了 生 物 接 触氧化工艺。虽然都采 用了接触氧化工艺 , 但由 于集 中生活区生活污水和工业区生活污水 中有机 物 的含 量差 别 很 大 , 日常 运 行 管 理 过 程 中 出 现 的 异常情况也不尽相同。由于现场操作工人运行技 术和 经验 不 足 , 运 行 过 程 控 制 只 局 限 于 简 单 的 开 泵和停泵, 运行操作及不规范 , 对工艺环节的运行 效果 无 法用 科学 的数 据 来 直 接反 映 。对 运 行 过程
电子元器件中的异常问题分析与解决方法

电子元器件中的异常问题分析与解决方法电子元器件是现代电子技术的重要组成部分,广泛应用于各种电子设备和系统中。
然而,在电子元器件制造和使用过程中,常常会出现各种异常问题,如焊接不良、静电击穿、氧化腐蚀等。
本文将从异常问题分析和解决方法两个方面介绍电子元器件中的一些常见异常问题和相应的解决方法。
一、异常问题分析1. 焊接不良焊接不良是电子元器件中常见的问题之一。
当焊接点接触不良或焊接质量不好时,会导致元器件性能下降或失效。
焊接不良的原因主要有以下几种:(1) 焊接温度不足,导致焊接点未能完全熔化和结合。
(2) 焊接时间太短,导致焊接点没有充分熔化和结合。
(3) 焊接点表面不干净,存在氧化物或污垢等,导致焊接不牢固。
(4) 焊接点设计不合理,焊接面积太小或焊接位置不当,容易出现焊接不良。
2. 静电击穿静电击穿是指电子元器件因受到静电场的影响而导致烧毁或失效的现象。
在现代电子制造过程中,静电击穿已成为电子元器件的重要故障之一。
静电击穿的原因主要有以下几种:(1) 电场强度过大,导致电子元器件内部断裂或击穿。
(2) 静电电荷在元器件表面聚集,导致表面受到静电击穿。
(3) 经过高速移动的物体会带电,当物体与元器件接触时,会将静电荷传递到元器件上,造成静电击穿。
3. 氧化腐蚀氧化腐蚀是电子元器件中的另一个常见问题。
当元器件表面被氧化或腐蚀时,会导致元器件性能下降或失效。
氧化腐蚀的原因主要有以下几种:(1) 暴露在潮湿环境中的元器件容易受到氧化腐蚀的影响。
(2) 暴露在酸性或碱性环境中的元器件容易受到化学腐蚀的影响。
(3) 元器件表面存在污垢或化学物质,容易引起氧化腐蚀。
二、解决方法1. 焊接不良的解决方法(1) 控制焊接温度,保证焊接点充分熔化和结合。
(2) 延长焊接时间,使焊接点有足够的时间熔化和结合。
(3) 在焊接前清洗焊接点表面,去除污垢和氧化物。
(4) 设计合理的焊接点,保证焊接面积充足且位置合理。
2. 静电击穿的解决方法(1) 安装静电保护设备,防止静电对元器件造成损害。
过氧化(二)苯甲酰-异常工况处置卡
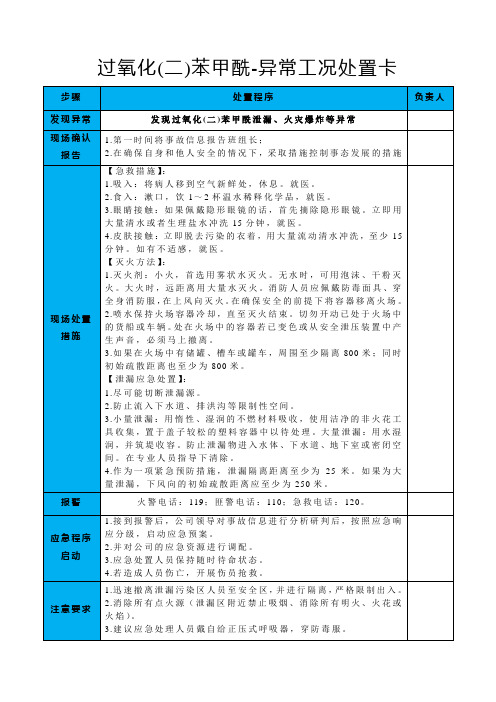
4.作为一项紧急预防措施,泄漏隔离距离至少为25米。如果为大量泄漏,下风向的初始疏散距离应至少为250米。
2.喷水保持火场容器冷却,直至灭火结束。切勿开动已处于火场中的货船或车辆。处在火场中的容器若已变色或从安全泄压装置中产生声音,必须马上撤离。
3.如果在火场中有储罐、槽车或罐车,周围至少隔离800米;同时初始疏散距离也至少为800米。
【泄漏应急处置】:
1.尽可能切断泄漏源。
2.防止流入下水道、排洪沟等限制性空间。
3.眼睛接触:如果佩戴隐形眼镜的话,首先摘除隐形眼镜。立即用大量清水或者生理盐水冲洗15分钟,就医。
4.皮肤接触:立即脱去污染的衣着,用大量流动清水冲洗,至少15分钟。如有不适感,就医。
【灭火方法】:
1.灭火剂:小火,首选用雾状水灭火。无水时,可用泡沫、干粉灭火。大火时,远距离用大量水灭火。消防人员应佩戴防毒面具、穿全身消防服,在上风向灭火。在确保安全的前提下将容器移离火场。
报警
火警电话:119;匪警电话:110;急救电话:120。
应急程序
启动
1.接到报警后,公司领导对事故信息进行分析研判后,按照应急响应分级,启动应急预案。
2.并对公司的应急资源进行调配。
3.应急处置人员保持随时待命状态。
4.若造成人员伤亡,开展伤员抢救。
注意要求
1.迅速撤离泄漏污染区人员至安全区,并进行隔离,严格限制出入。
过氧化(二)苯甲酰-异常工况处置卡
步骤
处置程序
负责人
橡胶过氧化处理

橡胶过氧化处理
处理橡胶过氧化的方法如下:
1. 橡胶表面清洗:使用肥皂水或专用的橡胶表面清洗剂来清洗橡胶制品,注意用湿布轻轻擦拭,不要使用过度力量,以免损坏橡胶表面。
2. 氧化表面研磨:对于已经出现氧化的橡胶制品,可以使用一些物理方法来清除。
其中比较常见的方法是采用研磨的方式。
使用砂纸或者钢丝刷等研磨工具,轻轻研磨橡胶表面,可以去除氧化的表面,让橡胶恢复光滑,但是需要注意不要把橡胶表面研磨太过,以免造成损伤。
3. 使用除氧化剂:如果橡胶表面氧化的比较严重,可以考虑使用除氧化剂。
常见的除氧化剂包括碱性溶液、氯化钠等。
使用除氧化剂需要注意安全,戴好防护手套,避免碰到皮肤或者口腔等敏感区域。
4. 使用橡胶表面保护剂:为了防止橡胶表面再次氧化,可以在清洗和处理后,使用橡胶表面保护剂进行涂抹,以保护橡胶表面不受到外界环境的影响。
此外,也可以尝试使用白醋、橄榄油、牙膏等其他去污剂进行清洁。
请注意,不同方法适用于不同程度和类型的氧化,选择合适的方法并根据说明正确操作才能达到最佳效果。
同时,储存橡胶制品时要注意避免阳光直射、高温高湿等条件对其影响。
定期清洗和保养橡胶制品表面,也能有效预防氧化问题的出现。
氧化车间产品异常判断

氧化车间产品异常判断氧化车间是一个重要的生产车间,主要负责氧化工艺的生产。
在氧化车间中,有时会发生产品异常的情况,这种情况需要及时判断并采取相应的措施。
首先,氧化车间产品异常的判断可以通过对原材料的检测来进行。
原材料是氧化工艺的重要组成部分,如果原材料出现质量问题,很可能导致产品异常。
因此,在收到原材料时,应该对其进行严格的检测,判断是否符合质量要求。
一旦发现原材料有问题,应立即联系供应商进行处理,并及时调整生产计划,避免继续生产出不合格产品。
其次,氧化车间产品异常的判断可以通过生产过程中的监控来进行。
在氧化工艺的生产过程中,应设置相应的监测系统,对关键参数进行实时监控。
如果某个参数偏离了标准范围,就需要及时判断是否会对产品质量造成影响。
在发现异常时,应立即停止生产,找出异常的原因,并采取相应的纠正措施。
可以通过分析监测数据,寻找生产过程中的问题,并针对性地进行改进,以确保产品质量的稳定性。
另外,氧化车间产品异常的判断还可以通过产品的检验来进行。
在生产过程中,要进行定期的抽样检验,对产品进行全面的检测。
通过检验结果的分析,可以得出产品质量的评价,判断是否存在异常。
如果发现产品不合格,就需要及时调查原因,确定异常产生的根本原因。
可以通过追溯技术,将异常产品的信息追溯到具体的生产批次,找出质量问题的来源。
在找到问题的根本原因后,可以对生产过程进行调整和改进,以提高产品质量的可靠性。
除了以上的方法,还可以通过与其他车间的沟通来判断产品异常。
氧化车间与其他车间之间存在着协同关系,产品在不同车间之间进行加工和转移。
如果其他车间反馈产品异常的情况,就需要及时判断是否是由氧化车间生产过程中的问题引起的。
可以对生产过程进行回顾,查找是否存在与其他车间之间的工艺和操作不一致的情况。
如果存在不一致,就需要及时调整,并与其他车间进行沟通,以确保产品的质量问题能够得到及时解决。
综上所述,氧化车间产品异常的判断是一个复杂而关键的过程,需要综合运用各种手段进行判断。
臭氧催化氧化系统效率异常偏低是什么原因导致的?

Guangzhou Sunny Environmental protection Technology Co.,LTD臭氧催化氧化系统效率异常偏低,是什么原因导致的?臭氧催化氧化技术是基于臭氧的高级氧化技术,它将臭氧的强氧化性和催化剂的吸附、催化特性结合起来,能较为有效地解决有机物降解不完全的问题。
在垃圾渗滤液处理、工业园区废水处理、纺织印染废水处理、炼油石化废水处理、制药废水处理、煤化工废水处理等废水处理领域都有很好的应用效果,确保出水稳定达标。
通过验证,臭氧催化氧化系统已经广泛应用在各类有毒高浓度有机废水中,但是臭氧催化氧化系统出现处理效率如果出现异常偏低,是什么原因导致的呢?有很多人首先会认为是臭氧催化剂的质量问题,想要更换催化剂,其实处理效率异常偏低的情况有很多种,当臭氧塔前端进入过多污泥、悬浮物时,时间久了,会导致催化剂表面被污泥附着,淤泥堆积减少了臭氧的接触面积等都会导致催化效率下降。
具体原因分析如下:1、前端沉淀池絮凝效果差由于pH、停留时间、PAC投加量、PAM投加量、进水水质波动将会直接影响絮凝效果,另外PAM 的适用性也是十分重要的,不同废水所适用的PAM各不相同,可用不同类型的PAM对废水进行反复小试试验,找到最佳类型的PAM。
2、反洗频率、反洗气量较低若反洗频率较低、反洗气量小也会导致悬浮物的累积,从而影响臭氧催化剂的效率。
3、投加填料时杂物掉入系统安装时不慎掉入的杂质,如臭氧催化剂的袋子等杂物进入也会影响催化剂的效率。
杂物、悬浮物影响的控制方法1、做小试/加过滤器①做不同的对比小试试验,找寻最佳pH、停留时间、PAC投加量、PAM投加量,一开始可以先给足停留时间然后慢慢缩减、PAC投加到溶液中产生大量明显肉眼可见的颗粒状悬浮物、PAM慢慢搅拌投加逐渐看到溶液中颗粒状悬浮物聚集在一块形成繁花后停止搅拌,沉淀的pH可先根据水中阳离子的完全沉淀pH进行试验。
Guangzhou Sunny Environmental protection Technology Co.,LTD②在臭氧前端可加设石英砂、精密过滤器,但当前端絮凝效果特别差时将会导致过滤器频繁堵塞。
氧化异常解决方案

2、碱槽浓度不均匀,槽底浓度比槽中以上要浓,造成产品底部有此现象。
2、产品材质疏松或碱蚀处理时间过长(返工品返工最为常见)。
1、降低碱蚀槽浓度。
2、碱蚀每挂前充分搅拌槽液,使槽液各部位均匀。
3、缩短处理时间,控制碱蚀量在4-6个丝内。
1、按量添加药品,不随意添加。
任何产品
不可修复
白点或黑点(水腐蚀造成)
1、产品表面呈现白色或黑色像花一样。
1、水中盐份或其它微量物质与铝材中的微量金属发生的化学反应(一般发生在咸潮期间)。
1、更换、清洗问题槽,采用过滤水生产,在清洗过程中不浸泡或不经过有隐患的水洗槽,
1、使用过滤水生产。
2、咸潮期间在生产每一种产品前先试样在各工序槽中浸泡查正待生产产品是否会有此现象再决定生产工艺。
2、碱蚀每挂前充分搅拌槽液,使槽液各部位均匀。
3、做好产品防护防止返工品返工时造成此现象。
壁厚较厚的产品
轻微的可打磨修复,严重的不可修复。
麻面
鱼鳞斑
1、整支产品麻面。
2、呈一条线状或局部麻面。
1.整支产品麻面有两个方面:第一、产品材质疏松;第二、碱槽烧碱与硝酸钠比例不平衡、或浓度太低或铝离子含量太高。
3、采用铝夹具上料。
1、产品素材在生产过程中,严禁接触水份、油类、腐蚀类气体或物体,员工操作时必须配带无含上续类物质的手套。产品成型后致氧化过程中的流程时间最好在10天内完成任务,储存环境必须干燥、阴凉。
任何产品
轻微可采用铝夹具上料方式返工,严重的返工不好。
电击烧伤
1、产品局部缺损。
2、夹具点处颜色发黑或烧穿。
3、封孔不良。
1、待温度恢复到20-23度再生产。
陶化后返锈异常报告总结

陶化后返锈异常报告总结陶化是一种将金属表面覆盖一层氧化膜的过程,这种氧化膜可以提高金属的耐腐蚀性能和美观度。
然而,在某些情况下,经过陶化处理的金属表面却出现了返锈现象,这是一种异常情况,需要及时进行分析和处理。
返锈异常报告的总结如下:一、异常情况描述在陶化后的金属表面出现了锈斑,这与陶化处理的初衷相悖。
锈斑的形成可能是由于陶化处理过程中出现了问题,导致金属表面的氧化膜受损或不均匀。
此外,可能还存在其他因素导致的返锈现象,需要进一步分析。
二、异常原因分析1. 陶化处理不当:陶化处理需要严格控制处理时间、温度和氧化剂浓度等参数,如果处理条件不当,就会导致氧化膜的形成不完整或不均匀,从而降低了金属的抗腐蚀性能。
2. 金属表面污染:在陶化处理前,金属表面可能存在污染物,如油脂、灰尘等,这些污染物会影响氧化膜的形成,使金属表面易于返锈。
3. 外界环境因素:陶化处理后的金属表面暴露在空气中,如果空气中存在高浓度的湿度、氧化性物质或化学污染物,都有可能导致金属表面返锈。
三、解决方案1. 优化陶化处理工艺:对陶化处理的时间、温度和氧化剂浓度等参数进行优化,确保氧化膜形成完整、均匀。
同时,加强对陶化处理设备的维护和保养,确保设备处于良好的工作状态。
2. 提高金属表面清洁度:在进行陶化处理前,对金属表面进行彻底的清洁,去除油脂、灰尘等污染物。
可以采用溶剂清洗、机械清洗或电化学清洗等方法,确保金属表面干净无污染。
3. 控制外界环境条件:对陶化处理后的金属制品进行包装或密封,减少其暴露在潮湿、氧化性物质或化学污染物的环境中的时间。
同时,可以采用防锈涂料等措施,增加金属表面的防护层。
四、预防措施1. 加强质量管理:建立健全的质量管理体系,严格按照工艺要求进行陶化处理,确保每一道工序符合标准。
同时,加强对原材料的检验和验收,确保原材料的质量符合要求。
2. 做好设备维护:定期对陶化处理设备进行检查、维护和保养,确保设备的正常运行。
晶圆背银氧化异常

晶圆背银氧化异常
晶圆背银氧化异常是指在晶圆制造过程中,晶圆背面的银氧化层出现异常情况。
银氧化层是一种常用的保护层,用于防止背面金属元件的氧化和腐蚀。
然而,有时候晶圆背银氧化异常可能会出现,给晶圆制造带来一些问题和困扰。
晶圆背银氧化异常可能由多种因素引起。
首先,制造过程中的温度和湿度控制不当可能导致银氧化层的形成不均匀或不完整。
其次,背面金属元件的材料和品质也会影响银氧化层的质量。
另外,制造过程中的化学物质的使用和处理也可能对银氧化层产生影响。
此外,设备的使用和维护不当也可能导致晶圆背银氧化异常。
晶圆背银氧化异常会给晶圆制造带来一系列的问题。
首先,不完整或不均匀的银氧化层可能会导致背面金属元件的腐蚀和损坏,进而影响晶圆的性能和可靠性。
其次,银氧化层异常可能会导致晶圆的表面粗糙度增加,影响后续工艺步骤的进行。
另外,银氧化层异常还可能导致晶圆的电性能发生变化,影响芯片的性能和稳定性。
为了解决晶圆背银氧化异常问题,制造过程中需要严格控制温度和湿度,确保银氧化层形成的均匀和完整。
此外,选择高品质的金属元件材料和化学物质,以及正确使用和维护设备,也是解决问题的关键。
同时,对晶圆背银氧化异常进行及时的检测和修复,可以减少对制造过程的影响,提高晶圆的质量和可靠性。
晶圆背银氧化异常是晶圆制造中常见的问题之一,可能会给制造过程和晶圆的性能带来一定的影响。
通过合理的制造控制和及时的检测修复,可以有效解决这一问题,提高晶圆的质量和可靠性。
金属氧化纠正措施

金属氧化纠正措施简介金属氧化是指金属表面与氧气发生氧化反应,形成氧化物的现象。
这种现象不仅影响了金属的外观美观度,还会降低金属的抗腐蚀性能和材料的强度。
因此,为了减少金属氧化对金属材料的影响,需要采取一系列的措施来进行纠正。
主要影响因素金属氧化的发生与以下几个因素密切相关:1.氧气浓度:氧气浓度是金属氧化的主要因素之一。
高氧气浓度会加速金属氧化的速度。
2.温度:金属氧化反应的速度与温度呈正相关关系。
较高的温度会促进金属与氧气的反应,从而加速金属氧化的进程。
3.金属种类:不同金属的氧化性能有所差异。
一些金属(如铜、银)容易被氧化,而一些金属(如铝、不锈钢)具有较好的抗氧化性能。
金属氧化纠正措施1. 表面涂层涂层是一种常见的金属氧化纠正措施。
通过在金属表面形成保护性涂层,可以有效隔绝氧气与金属的接触,从而延缓金属氧化的速度。
常见的涂层材料包括油漆、瓷釉、聚合物等。
涂层的选择应根据金属种类、使用环境和要求耐久性等因素进行合理选择。
2. 防腐蚀涂层防腐蚀涂层是一种特殊的涂层,主要用于金属在潮湿环境下的抗腐蚀保护。
这种涂层一般由氧化物、磷化物、硫化物等化合物组成,能够有效地隔离金属与腐蚀介质的接触,防止金属氧化和腐蚀。
3. 防氧化剂防氧化剂是一种能够与氧气反应形成保护性氧化物的物质。
通过添加防氧化剂,可以改变金属与氧气反应的方向,使金属表面氧化物层得以稳定而不继续增加。
常见的防氧化剂有氧化铝、氧化锌等。
4. 氧气排除排除金属周围环境中的氧气是一种有效的金属氧化纠正措施。
通常可以利用惰性气体(如氮气)将金属表面的氧气排除或稀释,使氧气浓度降低,从而减缓金属氧化的速度。
5. 热处理热处理是一种通过加热金属以改变其组织结构和性能的方法。
在一些金属中,通过热处理可以形成一层致密的氧化层,从而提高金属的抗氧化性能。
热处理的温度和时间应根据金属的种类和要求进行合理选择。
6. 金属合金金属合金是由两种或多种金属组成的材料。
停采工作面采空区一氧化碳异常处理

停采工作面采空区一氧化碳异常处理摘要:针对土城矿13124停采工作面埋管抽放管内一氧化碳产生来源进行分析,介绍抑制一氧化碳气体采取的措施、治理过程及取得的效果。
关键词:一氧化碳;注氮防灭火;采空区注水;1 土城矿13124采面概况土城矿13124采煤工作面位于半坡采区一水平井筒东翼,西起1312运煤斜巷,东至F38断层。
走向长501m,倾斜长143m,距地表垂深为321m;煤层平均厚度2.96m,煤层平均倾角17°。
该工作面绝对瓦斯涌出量为49.12m3/min,相对瓦斯涌出量为16.59 m3/t;煤层具有爆炸性,煤层自燃发火等级为Ⅱ级。
采煤工作面为走向长臂后退式采煤,13124回风巷为13122采面运输巷留巷,在工作面回采至停采线位置准备回收期间,发现上隅角留管抽放管内有一氧化碳产生,且在24小时内由2ppm急剧上升至11ppm。
2 采面留管一氧化碳产生原因分析2.1 工作面推进速度慢且采空区遗煤量大采煤工作面接近末采期间受到F38断层的次生断层影响,煤层上移至工作面综采支架顶部,致使顶板破碎且采面支架前探梁附近瓦斯涌出异常等原因致使工作面推进速度慢,同时采煤工作面架子顶部存在大量遗煤堆积,且此段区域处在停采线往里50m范围,恰恰处在采煤工作面氧化带内,采空区及支架上方破碎的煤体有足够的时间聚热,氧化分解产生一氧化碳。
2.2 漏风自燃采面回风巷作为上部13122采面运输巷留巷,工作面回风巷采用沿空留巷技术,同时为降低沿空留巷恢复期间的瓦斯治理及管理难度,在留巷内每隔36m设置一个三通抽放上隅角瓦斯,无形中增加采空区氧化带长度。
3 采空区一氧化碳异常处理通过分析对采煤工作面断层情况及一氧化碳来源情况分析,认定主要一氧化碳来源主要为停采线往里40~70m段,且一氧化碳浓度急剧上升,必须立即进行处理。
3.1 切断采空区留管抽放回风巷留巷期间,每隔3m施工一道挡风墙,发现一氧化碳以后,迅速将抽放采空区的留管断掉,为了解决上隅角瓦斯超限,将断开的瓦斯管路抽放离上隅角最近的挡风墙“气室”,截留采空区瓦斯涌向采煤工作面,但此时瓦斯沿着采空区裂隙带涌向采面尾架前探梁处,又在此处增设瓦斯抽放管路。
- 1、下载文档前请自行甄别文档内容的完整性,平台不提供额外的编辑、内容补充、找答案等附加服务。
- 2、"仅部分预览"的文档,不可在线预览部分如存在完整性等问题,可反馈申请退款(可完整预览的文档不适用该条件!)。
- 3、如文档侵犯您的权益,请联系客服反馈,我们会尽快为您处理(人工客服工作时间:9:00-18:30)。
2、如是电流问题可一挂上适当的上少几层,不过最好是采用较好的氧化设备,从源头杜绝此现象;如是染色时间问题可适当稀释染料,使染色时间控制到30秒以上。
3、如是工艺问题,则要制定相关作业指导书,并严格按作业指导书操作。
2、模线为模具不光滑(模具长时间工作铝棒中含有的杂质粘附在工作带上造成)。
3、石墨线为产品挤压出后因出口处的石墨夹得太紧造成。
1、清洗水槽或过滤氧化槽。
2、过滤或更换染色槽。
3、使用过滤水或不含盐份(山泉水、井水)的水生产,缩短产品氧化后在水中停留(例全自动可改为半自动)的时间。
1、定期清洗水槽或过滤氧化槽。
2、定期过滤染色槽。
3、采用过滤水生产,发现有问题时及时更改生产方式。
任何产品
可返工
染色后表面出现针点状(有砂孔)小白点。
1、无规则分布表白斑,一般为产品停放时间过长,空气造成的腐蚀。
2、手印白斑为在挤压或后续加工在碱蚀之前的各工序中,员工未带手套或所带的手套已被液体或腐蚀性的物体所污染,污染物再接触产品表面加上停留时间超过3小时以上而形成的。
3、点状白斑一般为产品的一个面有此现象,不会大批量出现,此现象为产品在停放时被雨水淋湿或腐蚀性物品粘附在其表面。
异常问题原因分析、预防措施表
异常名称
异常现象描述
原因分析
纠正措施
预防措施
易发生的产品
能否修复
染色产品白点
染色后表面出现针点状(无砂孔)小白点或有黑色脏污抹去后露白。
1、产品在氧化后表面吸附有水中含有的脏污,或氧化槽中的脏物。
2、染色槽中有脏污吸附在产品上,阻隔染料的吸附。
3、咸潮期间水中盐份对氧化膜的影响。
2、封孔时间不够。
1、调整工艺致含量(热封孔):4—7g/L,(冷封孔)3-6g/L;温度:(热封孔)55-70℃、(冷封孔)常温;PH值:5-6。
2、封孔时间保持在8-10分钟。
1、每天定时检测、记录,保持在正常范围内。
任何产品
重新返封孔或返工。
油点
片状油污
1、表面有突出的小圆点,有些会有尾巴的现象。
1、产品素材在氧化前已腐蚀,碱蚀后有砂孔状现象。
2、产品在除油后在水槽中浸泡时间过长倒致产品腐蚀。
1、先机械打磨再采用高温、高浓度的碱液碱蚀。
2、在清洗后不要在水中停放,尤其在咸潮期间在水槽中停放时间不能超过一分钟。
3、采用铝夹具上料。
1、产品素材在生产过程中,严禁接触水份、油类、腐蚀类气体或物体,员工操作时必须配带无含上续类物质的手套。产品成型后致氧化过程中的流程时间最好在10天内完成任务,储存环境必须干燥、阴凉。
1、制定各产品工艺标准,并严格按工艺标准操作。
手动线生产的有颜色产品
可返工
如材料问题,亮哑品检出分开返工
线条
1、焊合线、表面一条或几条分布跨度均匀,颜色呈黑亮或黑色或凸线,整支贯通。
2、模线(机械纹)、一条或并列几条呈凹线,用指角刮会有手感的线条。
3、石墨线、并列几条无手感,颜色呈发亮的线条。
1、焊合线为挤压模具设计不合理或挤压工艺不合理造成。
1、排除除油问题,碱蚀槽浓度(一般为硝酸钠含量过高)过高。
2、碱槽浓度不均匀,槽底浓度比槽中以上要浓,造成产品底部有此现象。
2、产品材质疏松或碱蚀处理时间过长(返工品返工最为常见)。
1、降低碱蚀槽浓度。
2、碱蚀每挂前充分搅拌槽液,使槽液各部位均匀。
3、缩短处理时间,控制碱蚀量在4-6个丝内。
1、按量添加药品,不随意添加。
3、化抛时间过长。
1、搅拌槽液后温度控制在100-120度。
2、添加适当比例的磷酸。
3、减少化抛时间。
1、在生产过程中多搅拌槽液,温度控制在100-120度以内。
2、检查每挂产品化抛后的效果,发现异常或有潜在的问题时及时调整作业方法或调整槽液。
化抛产品
不可直接修复,一般需打磨
异常名称
异常现象描述
原因分析
2、表面无氧化膜,没有耐磨性。
1、夹具(夹具太小或未脱膜、上料方法不对、橡皮接得太松或断掉等)与产品接触不良松动,造成产品不导电或电流密度过小。
2、氧化时间或其它氧化工艺不够。
3、如是整一小挂为挂钩与铜杆接触不良,如是一大挂为铜杆与导电座接触不良。
1、选用较好的夹具和正确的上料方法,增加夹具与产品的接触,保证产品在氧化时不会松动。
4、有规则分布白斑为操作过程中隔产品所使用的隔条含有污染物。
1、先机械打磨再(或)采用高温、高浓度的碱液碱蚀。
2、适当提高除油槽中的浓度和温度。
1、产品素材在生产过程中,严禁接触水份、油类、腐蚀类气体或物体,员工操作时必须配带无含上续类物质的手套。产品成型后致氧化过程中的流程时间最好在10天内完成任务,储存环境必须干燥、阴凉。
2、增大接触面或将电流适当调低后将产品入槽待整挂产品已全部导电后慢慢将电流调致正常位置。
1、制定作业指导书,加强员工培训,按作业要求操作。
2、对氧化面积比较大的产品,在工程设计时就应先考虑采取适当的夹具。
皇冠产品
大面积铝板产品
轻微可打磨修复,严重的不可修复。
导电不良
氧化后不导电
1、白色产品氧化后表面呈五颜六色,有颜色产品表面颜色明显比正常色浅。
纠正措施
预防措施
易发生的产品
能否修复
水印
1、表面呈现一块一块亮哑不均像波浪形的现象。
1、片碱偏少,硝酸钠浓度太高出槽后产品表面活性成分太少。
2、片碱,硝酸钠浓度过高,浓度、温度高反应剧裂,造成产品出槽即风干,导致产品出槽后在空气中局部腐蚀。
1、添加烧碱5g/L,增加槽液的活性成分。
2、降低槽液的浓度。
3、染色槽PH超标或染色槽打气时产生的泡沫影响。
1、加多清洗次数,如水槽较脏时更换清水;对较难中和的产品(如6061系列)在中和槽中可适当添加硝酸或铬酸。
2、在不影响表面效果下,出氧化槽后在第四个水槽可适当的浸泡,让酸液渗出。
3、调整PH到正常值,染色时不打气或打小一点气且及时打捞液面上的泡沫。
1、定期清洗或更换水槽和中和槽。
1、按化验室提供的数据,控制好各工艺槽的工艺参数。
可返工处理
酸、碱水印
1、氧化膜表面有块状退色或哑白色现象
1、在前处理时酸、碱水粘附在铜杆上未清洗干净,造成产品在氧化后酸碱水滴到产品腐蚀氧化膜形成。
2、在生产线出线下铜杆或下料,松捆绑在挂框上的橡皮时,橡皮将酸、碱水弹到产品上。
1、前处理时,将铜杆上的酸、碱清洗干净。
任何产品
轻微可采用铝夹具上料方式返工,严重的返工不好。
黑或烧穿。
1、氧化时产品与氧化槽中的阴极板(也有可能为掉落在槽中的产品)接触,产生短路,造成电流上升产品接触部位温度升高而溶解。
2、夹具与产品导电点接触面积太小电流过大而造成局部烧伤。
1、调整上料夹具或在放产品进氧化槽时不要碰到阴极板上,及时打捞掉落在槽中的产品。
2、定期(2h/次)检测染色槽内的PH值,有偏差时及时调整。
任何产品
可返工
异常名称
异常现象描述
原因分析
纠正措施
预防措施
易发生的产品
能否修复
封孔不良
1、封孔后两支产品以2Kg的力相互磨擦容易磨花。
2、用干净的赤手抓产品表面,有粘手的感觉。
3、哑光产品表面光光滑但有白雾。
1、封孔工艺未达标(如封孔剂含量、槽液温度、PH值)。
1、上料时把产品上有凹槽的一方或死角向上。
2、针对上料时无法解决的产品,在生产过程时必须将死角内的空气全部排出才能通电氧化。
皇冠产品
机加工较复杂产品
未造成腐蚀的可返工,已造成腐蚀的不可修复。
有颜色产品花脸
颜色不均匀、像流水状
1、前处理水洗或中和时不彻底,未清洗干净。
2、氧化后水洗不彻底,氧化膜表面酸性溶液未清洗干净。
2、表面有突出的呈片状的起堆现象。
1、原材料表面有固化油污,脱脂时无法分解。
2、表面颗粒状小点较多是由于脱脂后清洗不够。
3、脱脂槽或碱蚀槽表面浮油太多,产品进入或掉出时粘附在产品表面。
4、脱脂时间或槽内温度不够。
1、发现产品表面有固化油污时用煤油或天那水浸泡使油污松化后用碎布擦掉小面积油污即用砂纸去除。
2.呈一条线状或局部麻面同上面第二点原因。
3、鱼鳞斑一般发生在壁厚较厚的产品或实心棒加工或未人工时效的产品上,某些特殊材质也有可能发生,壁厚在1.5mm内产品正常不会发生此现象.
1、如是材质问题,可适当提高碱槽的浓度和温度,减少碱蚀时间进行处理;如是槽液问题可按比例适当添加药品或更换部分槽液。
2、如是鱼鳞斑无较好的处理方案,不过可采取同材质麻面的方法进行处理;如还不行在颜色限度的允许下可采用直接除油氧化或哑光氧化。
2、在生产线出线松橡皮时,应在最后一个水槽上松下,并将铜杆上的水珠用干抹布抹干净。
3、在烤干时将产品和橡皮彻底烤干,在下料下橡皮时,动作慢点不要松下一边后让其另一边弹下来。
1、培训、提醒。
自动线横串有颜色产品
可返工处理
哑光产品白雾
产品表面用手抹后有手印
1、氧化槽温度过高。
2、哑光槽内浓度配比不均匀或超过使用期。
1、槽液问题在本厂生产过程中应不定时搅拌槽液,采用量少次多的方法补充槽液浓度的损耗。
2、如看到厚度超2mm的制品,应先试样后再选择合适的工艺生产。
1、壁厚较厚的产品
2、一挂料挂得很密的产品。
轻微的调整槽液后可返工;严重的(也可打磨再碱蚀)先试样确认会不会产生鸡皮后再确定。
异常名称
异常现象描述
原因分析
3、封孔不良。
1、待温度恢复到20-23度再生产。
2、调整槽液或更换槽液。