基于互联网的液压远程控制系统延时预测算法研究
%bd%91%e7%9a%84%e6%b6%b2%e5%8e%8b%e8%bf%9c%e7%a8%8b%e6%8e%a7%e5%88%b6%e7%b3%bb%e7%bb%9f%e5%bb%b6%e6%

图 ’ 采用补偿器前后系统的单位阶跃响应曲线 ./01’ 237P95<63/8<47=P8<=78937;768<348;=>=37? Q/3:
A<BQ/3:85368?P7<=A384=
R 延时预测算法
图 ,所 示 的 系 统 中!互 联 网 环 节 不 仅 导 致 信 息 传递延 时!而且 由 于 目 前 互 联 网 中 路 由 器 多 是 采 用 动态路由协议依据互联网负载状况选择信息的传递 路由 ) %S( 因此!互联网负载的实时变化!造成信息的 传 递路由 动态 变 化!从 而 导 致 信 息 传 递 延 时 具 有 不 确定性)研究表明!对于图 &所示的控制系统!如果 系统的补偿器使用的预测延时值不等于互联网的实 际 延 时 值 !即 存 在 延 时 补 偿 误 差 时 !补 偿 器 不 能 及 时 准 确地 补偿信 息 延 时!系 统 的 性 能 仍 然 不 能 得 到 改 善)图 +是延时补偿误差对系统性能的影响)曲线 T表示没有延时补偿误差时的系统单位阶跃响应) 曲 线 U 和 V 分 别 表 示 延 时 补 偿 误 差 为 WXWY=和
独 立 的 *具 有 相 同 概 率 分 布 *统 计 特 性 已 知 的 均 匀 分 布 ) %+( 对于图 ,所示的基于互联网的远程控制系统 而 言 !不 仅 存 在 信 息 的 传 输 延 时 问 题 !而 且 信 息 延 时 很难用确定的随机规律描述)
ห้องสมุดไป่ตู้
图 - 基于互联网的远程液压控制系统 ./01- 234563547893:737;768<348;=>=37? @A=7B8<C<374<73
字~声音~静 态 及 动 态 的 图 像 等 静 态 信 息E系 统 对 信 息的实时性要求不高F更具有实际意义的是如图 "
基于Internet的远程控制中网络延时的探讨
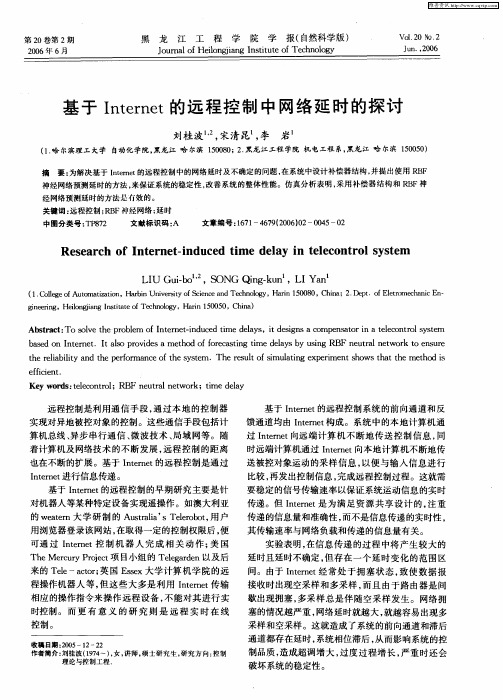
基 于 Itre 的远 程控 制 系统 的前 向通 道 和 反 nent
馈通道均由 It t ne 构成。系统中的本地计算机通 me 过 It nt ne e 向远端计算机不断地传送控制信 息, r 同 时远端计算机通过 It nt ne e 向本地计算机不断地传 r 送被控对象运动的采样信息 , 以便与输入信 息进行 比较 , 再发出控制信息 , 完成远程控制过程 。这就需
g er g eo gi gIsi t o eh o g , r 50 0 C i ) i ei ,H i nj n ntae f c n l y Hai 10 5 , h a n n l a t T o n n Ab ta t To s let ep o lm fI tm e— d c dtmed ly ,i d sg sac m p n ao ee n r l y tm sr c : ov h r be o n e ti u e i ea s t ein o e st ri atlc to se n n o s
J n ,0 6 u .2 0
基 于 Itre 的远 程控 制 中 网络 宋清 昆 , 一 李 岩
( . 尔滨理 工大学 自动化 学院, 1哈 黑龙江 哈 尔滨 10 8 ; . 50 0 2 黑龙江工程学院 机 电工程 系, 黑龙 江 哈 尔滨 10 5 ) 50 0
摘 要: 为解决基 于 It e 的远程控制 中的网络 延时及不确定的问题 , ne t n r 在系统中设计补偿器结构 , 并提出使用 R F B
神经网络预测延时 的方法 , 来保证系统的稳定性 , 改善系统 的整体性 能。仿 真分析 表明 , 用补偿 器结 构和 R F神 采 B
经 网络预测延时 的方 法是仃效的。 关键词 : 远程控制 ; 中图分类号 : 8 2 TP 7 神经网络 ; 时 延 文献标识码 : A 文章编 号:6 1 6 9 2 0 )2 0 5 2 1 7 —4 7 【0 6 0 —0 4 —0
基于Internet的实时控制系统研究综述
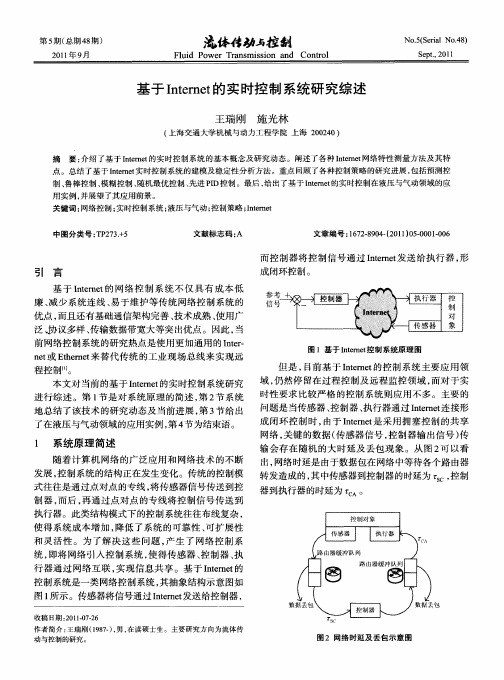
来对 网络时延进行建模及预测 , 随机过程建模简单 ,
象的网络控制系统设计 了一种通信协议并对系统进 参 数 可 在 线 估 计 。 文 献 [】 用 了 S 5采 MC(euni 行稳 定性 分 析 。 目前 , 缺乏 对 于不 确 定或 未完 全 建 Sq etl a 还 Mot C r ) n a o 算法计算 时延分 布密度 。文献[] e l 6采用 模 的对象 进行 稳定 性分 析 的方法 。
近 的文 献 『,31-2可 以看 出 L 技 术 已经成 为 了 9l,92] MI 网络 控制 系统 稳定 性分 析 的主要 数学 工具 。
Байду номын сангаас
22 系统 稳 定 性 分 析 方 法 .
MAD Mai m lw beDe yB ud , 大 允 许 B( xmu Al al l on s最 o a
l 系统原理简 述
网络 , 关键 的数据( 传感器信号 , 控制器输 出信号 ) 传
使得系统成本增加 , 降低 了系统 的可靠性 、 可扩展性 和 灵 活 性 。 为 了解 决 这 些 问 题 , 生 了 网络 控 制 系 产 统, 即将 网络引入控制系统 , 使得传感器 、 控制器 、 执
王瑞刚 施光林
( 上海交通大学机械与动力 工程学 院 上海 2 0 4 0 2 0) 摘 要: 介绍 了基 于 It t ne 的实时 控制系统 的基本 概念及研 究动态 。阐述 了各 种 Itme网络特性测 量方法及 其特 me ne t
点 。总结了基于 It n t ne e实时控制 系统 的建模及稳定性分 析方法 。重点 回顾 了各种控制策 略的研 究进展 , 括预测控 r 包
统 的模 型 也 存 在 较 大 的差 异 。一般 情 况 下 , 于 I— 基 n
《2024年基于AMESim的液压系统建模与仿真技术研究》范文
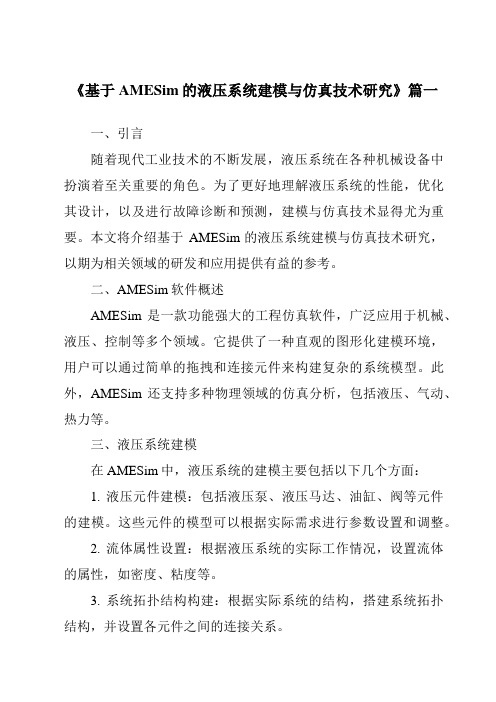
《基于AMESim的液压系统建模与仿真技术研究》篇一一、引言随着现代工业技术的不断发展,液压系统在各种机械设备中扮演着至关重要的角色。
为了更好地理解液压系统的性能,优化其设计,以及进行故障诊断和预测,建模与仿真技术显得尤为重要。
本文将介绍基于AMESim的液压系统建模与仿真技术研究,以期为相关领域的研发和应用提供有益的参考。
二、AMESim软件概述AMESim是一款功能强大的工程仿真软件,广泛应用于机械、液压、控制等多个领域。
它提供了一种直观的图形化建模环境,用户可以通过简单的拖拽和连接元件来构建复杂的系统模型。
此外,AMESim还支持多种物理领域的仿真分析,包括液压、气动、热力等。
三、液压系统建模在AMESim中,液压系统的建模主要包括以下几个方面:1. 液压元件建模:包括液压泵、液压马达、油缸、阀等元件的建模。
这些元件的模型可以根据实际需求进行参数设置和调整。
2. 流体属性设置:根据液压系统的实际工作情况,设置流体的属性,如密度、粘度等。
3. 系统拓扑结构构建:根据实际系统的结构,搭建系统拓扑结构,并设置各元件之间的连接关系。
4. 仿真参数设置:根据仿真需求,设置仿真时间、步长等参数。
四、液压系统仿真在完成液压系统的建模后,可以通过AMESim进行仿真分析。
仿真过程主要包括以下几个方面:1. 初始条件设置:设置系统的初始状态,如初始压力、流量等。
2. 仿真运行:根据设置的仿真时间和步长,运行仿真程序。
3. 结果分析:通过AMESim提供的可视化工具,分析仿真结果,如压力、流量、温度等参数的变化情况。
五、技术应用与优势基于AMESim的液压系统建模与仿真技术具有以下优势:1. 高效性:通过图形化建模环境,可以快速构建复杂的液压系统模型,提高建模效率。
2. 准确性:AMESim提供了丰富的物理模型和算法,可以准确模拟液压系统的实际工作情况。
3. 灵活性:用户可以根据实际需求,灵活地调整模型参数和仿真条件,以获得更符合实际的结果。
液压系统中的自适应控制算法研究
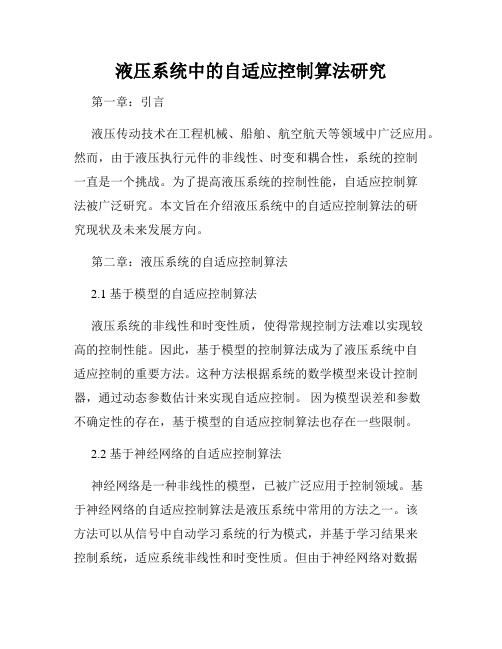
液压系统中的自适应控制算法研究第一章:引言液压传动技术在工程机械、船舶、航空航天等领域中广泛应用。
然而,由于液压执行元件的非线性、时变和耦合性,系统的控制一直是一个挑战。
为了提高液压系统的控制性能,自适应控制算法被广泛研究。
本文旨在介绍液压系统中的自适应控制算法的研究现状及未来发展方向。
第二章:液压系统的自适应控制算法2.1 基于模型的自适应控制算法液压系统的非线性和时变性质,使得常规控制方法难以实现较高的控制性能。
因此,基于模型的控制算法成为了液压系统中自适应控制的重要方法。
这种方法根据系统的数学模型来设计控制器,通过动态参数估计来实现自适应控制。
因为模型误差和参数不确定性的存在,基于模型的自适应控制算法也存在一些限制。
2.2 基于神经网络的自适应控制算法神经网络是一种非线性的模型,已被广泛应用于控制领域。
基于神经网络的自适应控制算法是液压系统中常用的方法之一。
该方法可以从信号中自动学习系统的行为模式,并基于学习结果来控制系统,适应系统非线性和时变性质。
但由于神经网络对数据量和训练参数的敏感性,需要针对具体系统设计合适的神经网络,并优化训练方法。
2.3 基于模糊逻辑的自适应控制算法模糊逻辑应用于自适应控制算法中,是一种基于经验或模糊规则的控制方法。
它可以从不同角度描述系统的特性,建立模糊规则库,使系统能够实现自适应性能。
这种方法已在某些液压系统中获得成功应用。
但由于模糊规则的模糊度较高,算法的可靠性和鲁棒性需要进一步研究。
第三章:自适应控制算法在液压系统中的应用3.1 活塞泵控制活塞泵控制作为液压系统中的基础控制,其控制效果直接影响整个液压系统的性能。
自适应控制算法在活塞泵控制中的应用已经得到广泛研究和应对,具有良好的控制效果。
3.2 液压伺服系统液压伺服系统是以液压缸为执行器的控制系统,现在已经被广泛应用于机床、成型机和机器人等领域。
对于液压伺服系统,高精度、快速、抗干扰是控制的核心问题。
自适应控制方法在液压伺服系统中的应用,可以提升系统的控制性能和鲁棒性。
基于改进PSO算法的液压调高系统神经网络预测控制
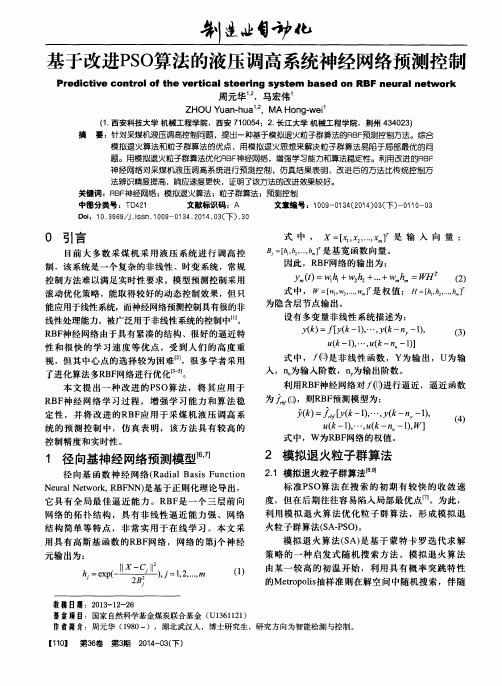
利用R B F 神经网络对 厂 ( 口 ) 进行逼近,逼近函数
为
.
,
( , ̄ q R B F 预测 模型 为 :
统 的预 测控 制 中 ,仿 真 表 明 ,该方 法具 有 较 高 的
控 制精 度 和实时 性 。
设 有 多变量 非线性 系统描述 为 :
. y ( ) =f [ y ( k —1 ) , …, y ( k 一 一 1 ) ,
u ( k 一1 ) , ・ 一 , u ( k 一, z 一 1 ) ]
f 3 、
视 ,但 其 中心 点 的选择 较 为 困
,很 多学 者 采用
式 中 ,/【 口 ) 是非 线 性 函数 ,Y为输 出 ,U为 输 入 ,n 为输入 阶数 ,n 为输 出阶数 。
了进化 算法 多R B F 网络 进行优 化 。 本 文提 出一 种 改 进 的P S O算 法 ,将 其 应 用 于 RB F 神 经 网 络 学 习过 程 ,增 强学 习能 力 和 算 法 稳
2 模拟退火粒 子群 算法
2 . 1 模拟退火粒子群算法【 8 I 9 ]
标准P S O算 法 在 搜 索 的初 期 有较 快 的 收 敛 速 度 ,但 在后 期往 往容 易 陷入 局部 最 优点 。为此 , 利 用模 拟 退 火 算法 优 化 粒 子 群 算 法 ,形 成 模 拟 退 火粒 子群 算法 ( S A- P S O ) 。 模 拟 退火 算 法 ( S A) 是 基 于 蒙 特 卡 罗 迭 代 求 解 策 略 的 一种 启发 式 随 机 搜 索 方 法 。模 拟 退 火 算 法 由某一 较 高 的初 温 开 始 ,利 用 具 有 概 率 突 跳 特 性 的Me t r o p o l i s 抽 样 准则 在 解 空 间 中随机 搜 索 ,伴 随
液压系统PID控制算法研究
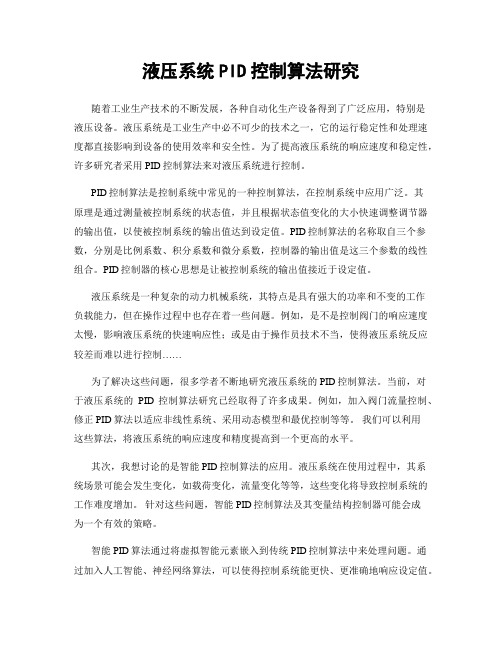
液压系统PID控制算法研究随着工业生产技术的不断发展,各种自动化生产设备得到了广泛应用,特别是液压设备。
液压系统是工业生产中必不可少的技术之一,它的运行稳定性和处理速度都直接影响到设备的使用效率和安全性。
为了提高液压系统的响应速度和稳定性,许多研究者采用PID控制算法来对液压系统进行控制。
PID控制算法是控制系统中常见的一种控制算法,在控制系统中应用广泛。
其原理是通过测量被控制系统的状态值,并且根据状态值变化的大小快速调整调节器的输出值,以使被控制系统的输出值达到设定值。
PID控制算法的名称取自三个参数,分别是比例系数、积分系数和微分系数,控制器的输出值是这三个参数的线性组合。
PID控制器的核心思想是让被控制系统的输出值接近于设定值。
液压系统是一种复杂的动力机械系统,其特点是具有强大的功率和不变的工作负载能力,但在操作过程中也存在着一些问题。
例如,是不是控制阀门的响应速度太慢,影响液压系统的快速响应性;或是由于操作员技术不当,使得液压系统反应较差而难以进行控制……为了解决这些问题,很多学者不断地研究液压系统的PID控制算法。
当前,对于液压系统的PID控制算法研究已经取得了许多成果。
例如,加入阀门流量控制、修正PID算法以适应非线性系统、采用动态模型和最优控制等等。
我们可以利用这些算法,将液压系统的响应速度和精度提高到一个更高的水平。
其次,我想讨论的是智能PID控制算法的应用。
液压系统在使用过程中,其系统场景可能会发生变化,如载荷变化,流量变化等等,这些变化将导致控制系统的工作难度增加。
针对这些问题,智能PID控制算法及其变量结构控制器可能会成为一个有效的策略。
智能PID算法通过将虚拟智能元素嵌入到传统PID控制算法中来处理问题。
通过加入人工智能、神经网络算法,可以使得控制系统能更快、更准确地响应设定值。
与传统PID控制算法不同,智能PID算法中的参数可以根据系统变化自动调整,从而保证了系统的稳定性。
人工智能在液压系统故障诊断中的应用研究

人工智能在液压系统故障诊断中的应用研究随着科技的迅猛发展,人工智能技术在诸多领域取得了重大突破,其中包括液压系统故障诊断。
液压系统广泛应用于工业自动化领域,是现代工程中不可或缺的一部分。
然而,液压系统在运行过程中会出现各种故障,这些故障对系统的正常运行产生了严重影响。
因此,开展人工智能在液压系统故障诊断中的应用研究,具有重要意义。
一、人工智能在液压系统故障诊断中的作用人工智能技术在液压系统故障诊断中发挥了重要的作用,主要体现在以下几个方面:1. 数据处理和分析:液压系统故障通常与传感器所采集到的数据有关,这些数据包括压力、温度、流量等信息。
人工智能技术可以对这些数据进行处理和分析,提取出有用的特征信息,并与故障模式关联起来,从而帮助工程师找出故障的根源。
2. 故障预测和预警:人工智能技术可以通过对历史数据的学习和分析,建立液压系统的健康预测模型。
当系统运行异常时,这些模型可以及时发出警报,提醒工程师注意可能的故障。
通过故障预测和预警,可以在故障发生前采取相应的维修和保养措施,提高系统的可靠性和可用性。
3. 专家系统辅助诊断:基于规则的专家系统是一种常用的液压系统故障诊断方法。
该系统通过事先定义的规则来识别故障,并给出相应的处理建议。
人工智能技术可以对这些规则进行优化和改进,提高系统的智能性和准确性。
此外,人工智能技术还可以结合机器学习算法,通过对大量故障样本的学习,建立更加精准和可靠的诊断模型。
二、人工智能在液压系统故障诊断中的应用案例1. 基于神经网络的故障诊断方法:神经网络是一种常用的人工智能算法,可以通过对大量数据的训练,建立复杂的非线性映射关系。
在液压系统故障诊断中,可以使用神经网络来建立故障诊断模型。
通过将系统传感器数据作为输入,将故障类型作为输出,通过对神经网络进行训练,可以实现对不同故障模式的准确识别和分类。
2. 基于遗传算法的优化方法:液压系统故障通常与参数调整有关,例如阀门的开度和油液流量。
基于智能控制的液压系统优化设计研究

基于智能控制的液压系统优化设计研究一、引言现代液压系统已经成为工业生产中重要的动力传递和控制手段。
随着技术的不断更新换代,液压系统的控制技术也经历了多年的发展。
智能控制是一种新兴的控制方式,液压系统的智能优化设计研究将为生产提供更有效的技术支持。
不断完善和推进控制技术,可以使液压系统在生产中更加精准、保证质量、稳定运行,有效提高生产效率。
二、智能控制在液压系统中的应用1. 智能控制的基本概念智能控制是基于先进的控制理论和计算机技术,将人的智力和经验融入到控制系统中,实现对被控对象的智能化控制。
智能控制技术涉及到模糊逻辑控制、神经网络控制、遗传算法控制和多模型自适应控制等。
2. 液压系统的智能控制概述液压系统智能控制技术的应用,可以使系统具有高灵敏度、高控制精度和控制速度、高可靠性以及高效率的特点。
液压系统智能控制方法包括模糊控制、神经网络控制、PID控制、H-infinity控制、自适应控制等。
3. 智能控制在液压系统中的优点智能控制技术实现了对液压系统中各种因素的自适应性调控,通过实时反馈、计算等手段实现控制策略的精细操控,有效提高了控制系统的响应速度和准确性。
智能控制技术还可以通过引入大量的实时监测和控制元素,来实现对系统的故障预测与诊断,进一步提高系统的可靠性和安全性。
三、液压系统智能化优化设计1. 调整控制参数液压系统智能化优化设计需要从控制参数出发,针对不同的液压系统特性进行不同的参数调整。
通过试验和理论计算相结合的方法,可以得出合适的参数组合。
液压系统可以使用自动控制方式,实现对各参数的实时控制。
2. 引入新的控制元素利用智能化的方法,可以在液压系统中引入新的控制元素,例如传感器和执行器。
传感器可以实时监测液压系统中各种参数的变化,执行器可以通过与各种控制模型相配合的方式实时调控系统的工作状态,进而实现对系统的智能化调节。
3. 优化流体控制液压系统智能优化设计中,应该注重流体控制这一方面。
液压伺服系统的控制算法与性能研究
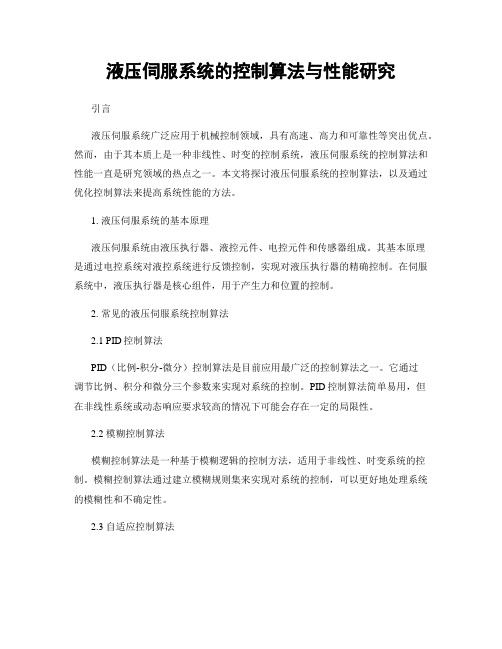
液压伺服系统的控制算法与性能研究引言液压伺服系统广泛应用于机械控制领域,具有高速、高力和可靠性等突出优点。
然而,由于其本质上是一种非线性、时变的控制系统,液压伺服系统的控制算法和性能一直是研究领域的热点之一。
本文将探讨液压伺服系统的控制算法,以及通过优化控制算法来提高系统性能的方法。
1. 液压伺服系统的基本原理液压伺服系统由液压执行器、液控元件、电控元件和传感器组成。
其基本原理是通过电控系统对液控系统进行反馈控制,实现对液压执行器的精确控制。
在伺服系统中,液压执行器是核心组件,用于产生力和位置的控制。
2. 常见的液压伺服系统控制算法2.1 PID控制算法PID(比例-积分-微分)控制算法是目前应用最广泛的控制算法之一。
它通过调节比例、积分和微分三个参数来实现对系统的控制。
PID控制算法简单易用,但在非线性系统或动态响应要求较高的情况下可能会存在一定的局限性。
2.2 模糊控制算法模糊控制算法是一种基于模糊逻辑的控制方法,适用于非线性、时变系统的控制。
模糊控制算法通过建立模糊规则集来实现对系统的控制,可以更好地处理系统的模糊性和不确定性。
2.3 自适应控制算法自适应控制算法是一种能够根据系统实时状态和参数变化进行调整的控制方法。
自适应控制算法通过反馈机制和参数估计来实现对系统的控制,可以提高系统的稳定性和鲁棒性。
3. 提高液压伺服系统性能的方法3.1 系统建模和参数辨识系统建模和参数辨识是提高液压伺服系统性能的关键步骤。
通过对系统进行建模和参数辨识,可以准确地描述系统的动态特性,为后续的控制算法设计和优化提供基础。
3.2 控制算法优化控制算法优化是提高液压伺服系统性能的有效途径。
基于建模和参数辨识的结果,可以通过优化控制算法来改善系统的动态性能。
常见的优化方法包括遗传算法、粒子群算法和模型预测控制等。
3.3 传感器和执行器的选型和优化传感器和执行器的选型和优化对液压伺服系统的性能影响巨大。
选择合适的传感器可以提高系统的测量精度和稳定性;优化执行器设计可以提高系统的输出能力和响应速度。
基于注意力机-多任务网络的液压系统多状态监测识别方法研究

第38卷第3期2021年3月机㊀㊀电㊀㊀工㊀㊀程JournalofMechanical&ElectricalEngineeringVol.38No.3Mar.2021收稿日期:2020-07-31基金项目:国家自然科学基金资助项目(5177050476)作者简介:黄鹏程(1994-)ꎬ男ꎬ广东梅州人ꎬ硕士研究生ꎬ主要从事机械状态检测及故障诊断方面的研究ꎮE ̄mail:895399270@qq.com通信联系人:李海艳ꎬ女ꎬ副教授ꎬ硕士生导师ꎮE ̄mail:Cathylhy@gdut.edu.cnDOI:10.3969/j.issn.1001-4551.2021.03.010基于注意力机 ̄多任务网络的液压系统多状态监测识别方法研究∗黄鹏程ꎬ李海艳∗ꎬ林景亮ꎬ梁桂铭(广东工业大学机电工程学院ꎬ广东广州510006)摘要:针对在复杂的多状态条件下ꎬ液压系统状态监测方法监测性能不高的问题ꎬ对多任务学习和注意力机制方法进行了研究ꎬ结合多任务与注意力机制ꎬ提出了一种基于注意力机多任务网络的液压系统监测方法ꎮ首先ꎬ利用注意力机制ꎬ根据不同传感器信号对任务贡献程度的大小ꎬ赋予了各个传感器不同的权重ꎻ其次ꎬ使用卷积网络(CNN)构建了自适应特征提取器ꎬ从赋予权重的多个传感器信号中提取了深度特征ꎻ最后ꎬ建立了多任务的特征共享诊断网络ꎬ实现了对液压系统多个状态的同时监测ꎮ研究结果表明:与以往的方法相比ꎬ所提出的方法监测性能更优ꎬ能更有效地对复杂的多状态条件下的液压系统的各种状态进行监测ꎬ且其平均精度达到99.3%ꎮ关键词:液压系统多状态监测ꎻ监测性能ꎻ注意力机ꎻ多任务网络中图分类号:TH137㊀㊀㊀㊀文献标识码:A文章编号:1001-4551(2021)03-0331-06Statemonitoringmethodofhydraulicsystembasedonattentionmachinemulti ̄tasknetworkHUANGPeng ̄chengꎬLIHai ̄yanꎬLINJing ̄liangꎬLIANGGui ̄ming(SchoolofMechanicalandElectricalEngineeringꎬGuangdongUniversityofTechnologyꎬGuangzhou510006ꎬChina)Abstract:Aimingatthepoormonitoringperformanceofthecurrenthydraulicsystemstatemonitoringmethodsundercomplexmulti ̄statecon ̄ditionsꎬthemulti ̄tasklearningandattentionmechanismmethodswerestudied.Combiningwiththemulti ̄taskandattentionmechanismꎬamulti ̄tasknetwork ̄basedmonitoringmethodforhydraulicsystemwasproposed.Firstlyꎬtheattentionmechanismwasusedtoassigndifferentweightstoeachsensoraccordingtothedegreeofcontributionofthesensorsignalstothetask.Secondlyꎬaconvolutionalnetwork(CNN)wasusedtoconstructanadaptivefeatureextractortoextractdepthfeaturesfrommultiplesensorsignalswithweights.Finallyꎬamulti ̄taskfeaturesharingdiagnosticnetworkwasestablishedtorealizesimultaneousmonitoringofmultiplestates.Theresultsindicatethatthepro ̄posedmethodissuperiortothepreviousmethodꎬandcaneffectivelymonitorthevariousstatesofthehydraulicsystemꎬwithanaverageac ̄curacyof99.3%.Keywords:statemonitoringofhydraulicsystemꎻmonitoringperformanceꎻattentionmachineꎻmulti ̄taskingnetwork0㊀引㊀言液压系统作为重要的传动系统ꎬ被广泛应用于工业领域[1ꎬ2]ꎮ因此ꎬ确保液压系统安全有效的运行非常重要ꎬ准确地估计液压系统状况可以避免突发状况ꎬ降低维护的成本ꎮ为了确保整个液压系统的正常运行ꎬ一种可靠㊁准确的液压系统状态监测方法是必不可少的ꎮ目前ꎬ已有的液压系统状态检测方法主要都是基于传统的机器学习的单一状态监测ꎮHELWIGN等人[3]先通过皮尔逊相关系数方法从原始传感器数据中提取特征ꎬ然后利用线性判别分析(LDA)将这些特征值转移到一个较低维的判别空间ꎬ从而对故障状态和严重程度进行了分类ꎮ考虑到使用单一分类器有时无法获得较高精度的缺点ꎬGUOP等人[4]提出了一种基于集成支持向量机的液压系统健康状态监测方法ꎬ该方法先从多传感器信号中提取统计特征来描述液压系统的健康状态特征ꎻ然后ꎬ利用皮尔逊相关系数对提取的特征进行了选择ꎻ最后ꎬ利用集成支持向量机和叠加方法实现了系统的健康状态识别ꎮ随着神经网络的发展ꎬ姜保军等人[5]把自编码器应用于液压系统监测ꎬ他们先用希尔伯特 ̄黄和小波变化对传感器信号进行了特征提取ꎬ然后利用堆栈稀疏自编码器来预测液压泵的状态ꎮ虽然上述方法取得了一定效果ꎬ但同时存在以下不足:(1)这些传统方法往往需要丰富的液压系统知识经验来选择特征提取和分类的方法ꎮ然而ꎬ液压系统在复杂的环境下工作ꎬ很难通过知识经验选取特征提取和分类方法ꎻ(2)对单一状态进行监测ꎬ分离了各个状态之间的相关性ꎬ丢失了各种状态之间潜在的相关特征[6]ꎮ对于液压系统中复杂的任务ꎬ其泛化力差ꎻ(3)在实际操作中ꎬ每个任务对各个传感器信号会有不同的依赖程度ꎬ而多个传感器信号笼统地直接输入ꎬ使得网络无法获取更为重要的信息ꎬ易出现网络信息过载的问题ꎬ降低了准确性ꎮ针对以上方法存在的问题ꎬ本文结合注意力机和多任务学习ꎬ提出一种基于注意力机的多任务网络的液压系统多状态监测方法ꎬ利用卷积网络(CNN)自动地从多个原始传感器信号中提取深度特征ꎬ并在网络中加入注意力机ꎬ然后建立多任务的特征共享诊断网络ꎬ实现对多个状态的同时监测ꎬ利用各状态之间的相关性ꎬ提取更泛化的特征ꎬ提高任务准确性ꎮ1㊀理论基础1.1㊀卷积神经网络卷积神经网路是一种典型的前馈神经网络ꎬ主要是由输入层㊁卷积层㊁池化层㊁全连接层和输出层组成ꎮ通过对输入层进行逐层卷积和池化ꎬ层层提取输入数据的特征ꎬ随着层数的加深ꎬ不断提取更加抽象的特征ꎬ最终得到具有平移旋转不变性的鲁棒特征ꎮ因其具有强大的非线性映射能力ꎬ近年来在图像识别[7]㊁语言识别[8]等方面被广泛应用ꎮ此处由于输入的特征是多变量时间序列ꎬ笔者使用一维卷积[9 ̄11]构建网络ꎮ卷积层通过用多个卷积核对前一层输出特征进行卷积操作ꎬ然后利用非线性激活函数构造出新的特征ꎬ其数学公式为:Xlj=fðiɪMjXl-1i wlij+blj()(1)式中:Mj 第l-1层第j个卷积区域ꎻw 卷积核的权重ꎻb 网络偏置ꎻXlj 第l层输出ꎻXl-1i 上一层的输入ꎻf () Relu非线性激活函数ꎮ池化层也叫下采样层ꎬ对上一层的卷积特征进行缩放映射ꎬ保留主要特征的同时减少参数和计算量ꎬ防止过拟合ꎬ提高模型泛化能力ꎮ常采用的是最大池化ꎬ即取局部的最大值ꎬ其数学公式为:Xdmꎬn=maxiɪRdmꎬnxi()(2)式中:xi 区域Rdmꎬn内神经元激活后的值ꎮ全连接层将前面卷积池化得到的高维数据铺平以作为输入ꎬ进行一些非线性变换ꎬ然后将结果输入到它后面的输出层softmax函数ꎮ全连接层数学表达式为:yl=gwlxl-1+bl()(3)式中:l 网络层的序号ꎻyl 全连接层的输出ꎻxl-1 平铺后的一维特征向量ꎻwl 权重系数ꎻg () softmax非线性激活函数ꎮSoftmax函数ꎬ将输出各值化作(0ꎬ1)之间ꎬ以便用于分类ꎮ其数学公式为:σzj()=ezjðKk=1ezk(4)式中:j 输出层第j个特征ꎻK 输出层特征总数ꎮ1.2㊀注意力机制2014年谷歌DeepMind[12]提出了注意力机(Atten ̄tion)ꎬ并将其应用于图像识别领域ꎬ解决了图片处理时计算量巨大的问题ꎮ同年ꎬBENGIOY[13]把注意力机应用于机器翻译ꎬ解决了机器翻译中不同长度的源语言对齐问题ꎮ上述两个注意力机应用均取得了不错的效果ꎬ随后注意力机在深度学习任务中蓬勃发展ꎮ深度学习中的注意力机从本质上讲是和人类视觉机制类似ꎬ核心233 机㊀㊀电㊀㊀工㊀㊀程第38卷任务都是用来捕获当前目标更为关键的信息ꎬ而忽视无关信息ꎮ采用注意力机通常有两个目的:(1)降低数据的维度ꎬ减少计算量ꎻ(2)选择输入数据中与当前输出更加相关的有用信息ꎬ提高输出的质量ꎮ常用的注意力机分为软注意力和硬注意力ꎮ其中ꎬ软注意力更关注区域或者通道ꎬ且因为注意力是确定性的ꎬ其可微分ꎬ可以通过反向传播来学习它的参数ꎻ而硬注意力更加关注点ꎬ且注意力是一个随机预测过程ꎬ动态变化ꎬ导致了其不可微分ꎮ由于软注意力是可微分的ꎬ可以利用反向传播进行训练ꎬ求它的参数ꎬ并方便地嵌入网络框架中ꎬ比较常用ꎮ因此ꎬ本文选择了软注意力机ꎬ其数学公式为:αi=pz=i|Xꎬq()=softmaxsxiꎬq()()=ðexpsxiꎬq()()ðNj=1expsxjꎬq()()(5)式中:αi 注意力分布ꎻsxiꎬq() 注意力打分模型ꎻq 和任务相关的查询向量ꎻX=[x1ꎬ ꎬxN] N组输入信息ꎻxi 第i个向量ꎮ通常ꎬ打分模型sxiꎬq()针对每个xi计算出一个sꎮ而打分的依据就是xi与注意力机所关注的对象的相关程度ꎻ它们越相关ꎬ所得元素分数值越大ꎮ利用softmax对上面的得分进行数值转换ꎬ一方面进行归一化ꎬ使得所有分数之和为1ꎻ另一方面也可以更加突出重要元素的权重ꎮ本文注意力机模型如图1所示ꎮ图1㊀注意力机模型图1中ꎬ用一个全连接层作为sxiꎬq()函数ꎬ来学习不同传感器特征与任务的相关程度ꎬ其中神经元数㊀为传感器个数ꎮ2 注意力机多任务网络本文的研究对象是液压系统的冷却器㊁阀门㊁内部泵及液压蓄能器状态ꎬ具有4个状态监测的任务ꎮ因此ꎬ本文使用多任务学习的方式来构建网络ꎮ多任务学习可以提取多个任务的共享特征ꎬ共享特征具有较强的抽象能力ꎬ可以适应多个不同但相关的任务ꎬ通常可以使网络获得更好的泛化力ꎻ且由于输入的是多个传感器信号ꎬ考虑到实际任务会对各个传感器信号有不同的依赖程度ꎬ笔者使用注意力机来赋予各传感器不同的关注程度ꎬ让网络关注更加有用的传感器信息ꎬ以减低对其他信息的关注度ꎬ提高网络的监测效率ꎮ结合注意力机与多任务网络ꎬ笔者构建注意力机多任务网络ꎬ如图2所示ꎮ图2中ꎬ网络由输入层㊁注意力层㊁特征提取层㊁多任务层构成ꎮ其总体状态监测步骤如下:(1)对多个传感器数据进行归一化处理ꎬ构建输入特征矩阵χꎻ(2)输入特征χ输入到注意力层ꎬ通过将注意力模型得到的特征权重α与输入特征χ做矩阵乘法ꎬ得到注意力特征χattꎻ(3)注意力特征χatt共享层ꎬ使用多个卷积层来提取4个任务的共享特征ꎻ(4)共享特征输入到任务层ꎬ共有4个任务ꎬ其损失函数为各个任务损失函数的线性加权ꎬ即联合损失函数ꎬ其数学表达式为:L=λ1L1+λ2L2+λ3L3+λ4L4(6)式中:L1 冷却器状态ꎻL2 阀门状态ꎻL3 内部泵状态ꎻL4 液压蓄能器状态ꎻλ1ꎬλ2ꎬλ3ꎬλ4 对应任务的权重ꎬ文中均取0.25ꎮ而Lt损失函数为交叉熵损失函数ꎬ其表达式为:Lt=-1NðNn=1ðKk=11yn=k{}logynkɡ()[](7)式中:N 样本数ꎻK 样本类别数ꎻyn 第n个样本真实类别ꎻynkɡ第n个样本对应的第k个输出神经元的激活值ꎻ1∗{} 指示性函数ꎻ(5)采用反向传播算法[14]对网络参数进行更新ꎮ333 第3期黄鹏程ꎬ等:基于注意力机 ̄多任务网络的液压系统多状态监测识别方法研究图2㊀注意力多任务网络㊀㊀本文利用深度学习框架pytorch构建模型ꎬ训练优化器为Adamꎬ批量为32ꎬ学习率初始设置为0.001ꎬ迭代次数为550ꎮ网络结构参数如表1所示ꎮ表1㊀网络结构参数层名参数特征维度Input(60ꎬ17)Attention(17ꎬ1)(60ꎬ17)Conv1d(17ꎬ50ꎬ10)(50ꎬ51)Conv1d(50ꎬ50ꎬ10)(50ꎬ42)Maxpooing(2ꎬ2)(50ꎬ21)Conv1d(50ꎬ100ꎬ10)(100ꎬ12)Conv1d(100ꎬ100ꎬ10)(100ꎬ3)Avgpooing(3ꎬ3)(100ꎬ1)FC_S(100ꎬ100)(100ꎬ1)FC1(100ꎬ3)(3ꎬ1)FC2(100ꎬ4)(4ꎬ1)FC3(100ꎬ3)(3ꎬ1)FC4(100ꎬ4)(4ꎬ1)㊀㊀表1中ꎬ根据一维卷积参考文献的网络结构ꎬ适当调整参数大小ꎬ构建网络共享层ꎬ并在共享层前面加入注意力模型ꎬ其参数为输入传感器的个数ꎻ在共享层后面加入多任务模型ꎬ其参数为各任务状态个数ꎬ构成整体网络结构ꎮ3㊀实验与分析3.1㊀数据描述此处采用UCI网站中的液压系统状态监测数据[15]进行实验ꎬ实验数据通过一个液压实验台获得ꎮ该试验台以60s为1周期进行恒定负载循环ꎬ通过测量压力㊁流量等17个传感器的值ꎬ来监测4个液压组件(冷却器㊁阀门㊁泵和蓄能器)的状态定量变化ꎻ共有2205组模拟数据ꎬ每个组包含了17个传感器数据和4个组件的运行状况ꎮ液压试验台使用的传感器如表2所示ꎮ表2㊀液压试验台使用的传感器传感器物理量单位采样频率/HzPS1 ̄PS6压力bar100EPS1电机功率W100FS1ꎬFS2体积流量1/min10TS1 ̄TS4温度ħ1VS1振动mm/s1CE冷却效率(虚拟)%1CP冷却功率(虚拟)kW1SE效率系数%1㊀㊀表2中ꎬCE㊁CP和SE是表示计算值的虚拟传感器ꎬ其余传感器是液压回路中的物理传感器ꎮ液压组件状态变量如表3所示ꎮ表3㊀液压组件状态变量组件变量(单位)值状态冷却器%100203全效率效率不足故障阀门%100908073最佳的切换行为小滞后重度滞后接近完全失效内部泵\012无泄漏弱泄漏严重泄漏液压蓄能器Pa13011510090最佳压力压力偏低压力过低故障㊀㊀表3中给出了4个液压组件所存在各种的状态ꎮ433 机㊀㊀电㊀㊀工㊀㊀程第38卷其中ꎬ冷却器与内部泵存在3种状态ꎬ阀门与液压蓄能器存在4种状态ꎮ3.2㊀数据处理由于传感器采样频率不一样ꎬ导致相同周期内不同传感器时序点个数不同ꎬ如压力传感器100Hzꎬ60s内有6000个时序点ꎬ而温度传感器1Hzꎬ60s内只有60个时序点ꎬ为了输入到网络中ꎬ需要对数据进行简单的平均处理ꎬ使得每个传感器时序点数均为60ꎮ处理后得到输入特征图如图3所示ꎮ图3㊀输入特征图图3中ꎬ输入特征图是由17个传感器堆叠构成的特征图ꎬ其维度为(17ꎬ60)ꎮ其中ꎬ行是每个传感器时序点数ꎬ列是传感器数ꎮ将2205组数据样本按照6:2:2比例ꎬ划分为训练集㊁验证集和测试集ꎮ在训练集上训练网络内部参数ꎬ通过验证集调节网络迭代次数㊁学习率等超参数ꎬ使训练集上得到的网络能在测试集上有更好的效果ꎮ3.3㊀评价指标为了量化网络诊断的性能ꎬ此处使用指标准确率ꎬ其计算公式为:acc(t)=1NðNn=1l(f(xn)=yn)(8)式中:acc(t) 第t个任务准确率ꎻN 样本数ꎻf(xn) 预测值ꎻyn 真实值ꎻ1∗{} 指示性函数ꎮ3.4㊀实验结果与分析为验证该方法的监测性能ꎬ此处在训练集与验证集以交叉验证的方式进行训练ꎬ最后在测试集上验证精度ꎻ并将其与现有的传统方法LDA㊁人工神经网络(ANN)㊁集成SVM进行对比ꎮ模型在训练过程中ꎬ由于权重的初始化是随机的ꎬ为了避免实验结果受到其影响ꎬ对训练数据重复做5次实验ꎬ然后取平均值ꎮ该方法与传统方法结果比较如表4所示ꎮ表4㊀与传统方法结果比较%组件LDAANN集成SVM注意力机+多任务冷却器100100100100阀门100100100100内部泵73.680.098.699.0液压蓄能器54.050.456.198.0平均81.982.688.799.3㊀㊀从表4中可以看出:本文提出的注意力多任务方法可以让液压系统状态获得更好的监测效果ꎻ它比最新的传统方法平均精度提高了10.6%ꎬ特别在液压蓄能器方面的提高了42.9%ꎮ为了验证多任务和注意力机的有效性ꎬ此处将该方法与有相同网络层的单任务CNN与多任务CNN进行了比较ꎬ其结果比较如表5所示ꎮ表5㊀与CNN方法结果比较%组件单任务CNN多任务CNN注意力机+多任务冷却器100100100阀门100100100内部泵99.098.099.0液压蓄能器89.197.098.0平均97.098.899.3㊀㊀从表5中可以看出:多任务CNN精度相比单任务平均精度提高1.8%ꎬ验证了多任务网络可以通过各个任务之间的相互辅助ꎬ有效地提取了各个任务之间潜在的特征ꎬ提高了监测的精度ꎻ而加入的注意力机ꎬ会根据各个传感器对任务的重要程度ꎬ给与相关的权重ꎬ缓解了网络的信息过载ꎬ使得内部泵和液压蓄能器任务精度均提高了1%ꎬ进一步提升了网络的监测精度(达到了99.3%)ꎮ各传感器权重分布如图4所示ꎮ图4㊀各传感器权重分布从图4可以看出:在没有使用注意力机之前的各个传感器的权重都是相等的ꎬ网络对每个传感器的侧533 第3期黄鹏程ꎬ等:基于注意力机 ̄多任务网络的液压系统多状态监测识别方法研究重程度都一样ꎻ使用了注意力机之后ꎬ各个传感器权重值发生了变化ꎬ网络对不同传感器侧重程度不同ꎬ有利于提取对网络更有用的传感器信息ꎮ4㊀结束语在复杂的多状态条件下ꎬ针对液压系统状态监测方法监测性能不高的问题ꎬ笔者提出一种基于注意力机的多任务网络的液压系统监测方法ꎮ相比以往的方法ꎬ该方法有以下优势: (1)直接把多传感器信号输入到CNNꎬ实现了端到端的预测ꎬ无需人工提取特征ꎬ降低了使用者的操作难度ꎻ(2)利用多任务网络ꎬ对多状态同时学习ꎬ有利于提取各状态之间存在的潜在特征ꎬ可以避免在单状态时ꎬ因为过度关注单个状态ꎬ而忽视了噪音及泛化性能ꎬ使得网络有更好的预测精度ꎻ(3)在网络中加入注意力机ꎬ给予了各个传感器一个权重ꎬ使得网络可以更多关注于对任务贡献大的输入变量ꎬ从而提取更相关的特征ꎬ缓解网络信息过载问题ꎬ进一步提升网络的预测精度ꎮ但是该方法依然存在不足之处:多任务网络各个任务的权重都是一样的ꎬ但是在实验中发现ꎬ对于冷却器状态ꎬ其收敛的速度快ꎬ很快达到了100%ꎻ而对于液压蓄能器状态ꎬ其收敛速度慢ꎬ精度提升相当慢ꎬ所以应该给予各个任务不同的权重比ꎬ来帮助网络更快收敛ꎮ所以ꎬ笔者下一步的研究重点是设计一个自适应的任务权重选择方法ꎬ以提高该方法的运行效率ꎮ参考文献(References):[1]㊀刘㊀志ꎬ纪爱敏ꎬ张㊀磊ꎬ等.剪叉式高空作业平台上车液压系统的稳定性研究[J].机电工程ꎬ2020ꎬ37(6):600 ̄606.[2]㊀HIGGSPAꎬPARKINRꎬJACKSONMꎬetal.Asurveyonconditionmonitoringsystemsinindustry[C].ProceedingsoftheASME7thBiennialConferenceonEngineeringSystemsDesignandAnalysis.England:ASMEꎬ2004. [3]㊀HELWIGNꎬPIGNANELLIEꎬSCHÜTZEA.Detectingandcompensatingsensorfaultsinahydraulicconditionmonito ̄ringsystem[C].AMAConferences2015.Nürnberg:AMAꎬ2015.[4]㊀GUOPꎬWUJꎬXUXꎬetal.Healthconditionmonitoringofhydraulicsystembasedonensemblesupportvectormachine[C].2019PrognosticsandSystemHealthManagementCon ̄ference.Qingdao:IEEEꎬ2019.[5]㊀姜保军ꎬ王帅杰ꎬ董绍江.基于深度学习的液压监测系统蓄能装置故障诊断[J].组合机床与自动化加工技术ꎬ2019(9):89 ̄92.[6]㊀张德明.连铸机液压系统油液状态监测实例分析[J].液压气动与密封ꎬ2020(3):74 ̄75.[7]㊀KRIZHEVSKYAꎬSUTSKEVERIꎬHINTONG.ImageNetclassificationwithdeepconvolutionalneuralnetworks[J].CommunicationsoftheACMꎬ2017ꎬ60(6):84 ̄90. [8]㊀SAINATHTNꎬKINGSBURYBꎬMOHAMEDARꎬetal.ImprovementstodeepconvolutionalneuralnetworksforLVCSR[C].2013IEEEWorkshoponAutomaticSpeechRecognitionandUnderstanding.Olomouc:IEEEꎬ2013. [9]㊀曲建岭ꎬ余㊀路ꎬ袁㊀涛ꎬ等.基于一维卷积神经网络的滚动轴承自适应故障诊断算法[J].仪器仪表学报ꎬ2018ꎬ39(7):134 ̄143.[10]㊀BABUGSꎬZHAOPꎬLIXL.Deepconvolutionalneuralnetworkbasedregressionapproachforestimationofremai ̄ningusefullife[C].InInternationalConferenceonData ̄baseSystemsforAdvanceApplications.Online:DASFAAꎬ2016.[11]㊀杨兰柱ꎬ刘文广.改进的CNN网络在轴承故障诊断中的应用[J].机电工程技术ꎬ2020ꎬ49(8):11 ̄13.[12]㊀MNIHVꎬHEESSNꎬGRAVESA.Recurrentmodelsofvisualattention[EB/OL].(2014 ̄06 ̄24)[2020 ̄7 ̄30].https://arxiv.org/abs/1406.6247.[13]㊀BAHDANAUDꎬCHOKꎬBENGIOY.Neuralmachinetranslationbyjointlylearningtoalignandtranslate[EB/OL].(2014 ̄09 ̄01)[2020 ̄7 ̄30].https://arxiv.org/abs/1409.0473.[14]㊀RUMELHARTDEꎬHINTONGEꎬWILLIAMSRJ.Learningrepresentationsbyback ̄propagatingerrors[J].Natureꎬ1986ꎬ323(6088):533 ̄536.[15]㊀HELWIGNꎬPIGNANELLIEꎬSCHÜTZEA.Conditionmonitoringofacomplexhydraulicsystemusingmultivariatestatistics[C].Instrumentation&MeasurementTechnologyConference.IEEEꎬ2015.[编辑:雷㊀敏]本文引用格式:黄鹏程ꎬ李海艳ꎬ林景亮ꎬ等.基于注意力机 ̄多任务网络的液压系统多状态监测识别方法研究[J].机电工程ꎬ2021ꎬ38(3):331-336.HUANGPeng ̄chengꎬLIHai ̄yanꎬLINJing ̄liangꎬetal.Statemonitoringmethodofhydraulicsystembasedonattentionmachinemulti ̄tasknetwork[J].JournalofMechanical&ElectricalEngineeringꎬ2021ꎬ38(3):331-336.«机电工程»杂志:http://www.meem.com.cn 633 机㊀㊀电㊀㊀工㊀㊀程第38卷。
液压缸的动力学仿真与控制算法研究

液压缸的动力学仿真与控制算法研究液压缸作为现代工程领域广泛应用的一种执行元件,其动力学仿真与控制算法的研究对于提高液压系统的性能具有重要的意义。
一、液压缸的动力学仿真液压缸是一种将液压能转化为机械能的传动装置。
液压缸的动力学仿真研究通过模拟液压系统中液压缸的工作过程,可以分析液压缸的性能指标并进行优化设计。
液压缸的动力学仿真过程主要包括建立液压系统的数学模型、求解模型的运动方程以及模拟系统的动态响应等步骤。
在液压缸的动力学仿真中,首先需要确定液压系统的工作条件和参数,包括液压液的性质、液压缸的结构尺寸以及工作负荷等。
然后,可以利用理想气体定律、液力传动等基本原理建立液压系统的动力学模型。
通过求解模型的动态运动方程,可以得到液压缸的位置、速度、加速度等动态响应。
液压缸的动力学仿真可以帮助工程师更好地了解液压系统的工作原理和特性,提前发现系统中的问题并加以优化。
另外,通过仿真可以对液压缸的性能指标进行评估,如响应时间、精度和能耗等,为系统设计和控制算法提供参考。
二、液压缸的控制算法研究液压缸的控制算法研究是提高液压系统性能的关键。
液压系统的控制算法主要包括位置控制、速度控制和力控制等。
在液压缸控制算法研究中,主要考虑控制的精度、响应速度和稳定性等指标。
位置控制是液压系统最基本的控制方式之一,通过调节液压缸的工作位置来实现对执行元件的控制。
常用的位置控制算法有PID控制、模糊控制和神经网络控制等。
PID控制根据液压缸的位置误差和误差变化率进行控制,控制精度较高,但对系统参数变化较为敏感。
模糊控制基于模糊集合的概念,可以对参数变化和不确定性具有一定的鲁棒性。
神经网络控制利用神经网络模型的学习能力进行系统建模和控制,可以适应复杂系统的控制需求。
除了位置控制外,速度控制和力控制也是液压系统中常用的控制方式。
速度控制通过调节液压缸的工作速度控制执行元件的运动速度。
力控制则是根据负载情况调节液压缸的工作力来实现对执行元件的力控制。
基于BP网络规则PID控制的液压系统仿真与研究
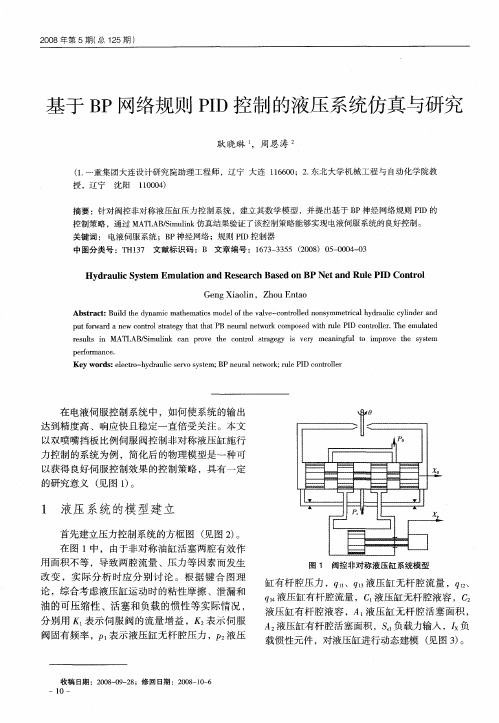
比较 困难 。PD参 数调整不 当 ,将会导致 系 I 统不停的振荡。为 了消除这一现象 ,就需要 对 PD算 法再 做 进 一 步 的改 进 。对 于 工业 上 I
许 多综 合 性 的 问题 ,在 多 数情 况 下 ,常 常难
以作出准确的描述和严格的分析 。而专家 系 统 对 上述 问题 就 可 以作 出较好 的 预测 ,并 找
在电液伺服控制系统 中,如何使 系统的输 出 达到 精度 高 、响应 快且 稳 定一 直 倍受 关 注 。本 文
以双 喷 嘴挡 板 比例 伺服 阀控 制非 对称 液 压 缸施 行
力控制的系统为例 ,简化后的物理模 型是一种可 以获 得 良好伺 服 控 制效 果 的 控制 策 略 ,具 有一 定 的研 究意 义 ( 图 1 。 见 )
中 图分 类 号 :T 3 文 献 标 识 码 :B 文 章 编 号 :17 — 3 5 (0 8 0 — 0 4 0 H17 6335 20) 500— 3
Hy r u i y t m u a i n a d Re e r h Ba e n BP Ne n l eP D n r l d a l S s e Em l to n s a c s d o ta d Ru I Co t o c
1 液压 系统 的模 型建 立
首先建 立 压力控 制 系统 的方框 图 ( 图 2 。 见 ) 在 图 1中 ,由于非 对 称油 缸 活塞 两 腔有 效 作
用面积不等 ,导致两腔流量、压力等 因素而发生
改 变 ,实 际分 析 时 应 分 别 讨 论 。根 据 键 合 图 理
图 1 阀控 非 对 称 液 压 缸 系 统模 型
1 一 0
《 一重技 术》
状 态 对应 于某 种 最 优控 制 规 律下 的 PD控 制器 参数 。 I
液压系统中的PID控制算法研究
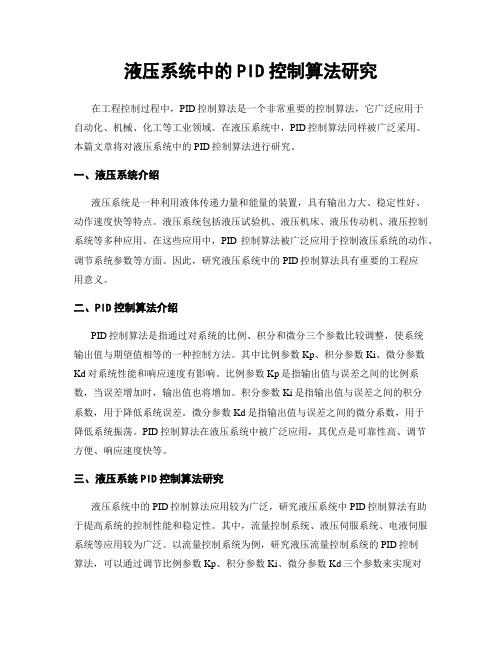
液压系统中的PID控制算法研究在工程控制过程中,PID控制算法是一个非常重要的控制算法,它广泛应用于自动化、机械、化工等工业领域。
在液压系统中,PID控制算法同样被广泛采用。
本篇文章将对液压系统中的PID控制算法进行研究。
一、液压系统介绍液压系统是一种利用液体传递力量和能量的装置,具有输出力大、稳定性好、动作速度快等特点。
液压系统包括液压试验机、液压机床、液压传动机、液压控制系统等多种应用。
在这些应用中,PID控制算法被广泛应用于控制液压系统的动作、调节系统参数等方面。
因此,研究液压系统中的PID控制算法具有重要的工程应用意义。
二、PID控制算法介绍PID控制算法是指通过对系统的比例、积分和微分三个参数比较调整,使系统输出值与期望值相等的一种控制方法。
其中比例参数Kp、积分参数Ki、微分参数Kd对系统性能和响应速度有影响。
比例参数Kp是指输出值与误差之间的比例系数,当误差增加时,输出值也将增加。
积分参数Ki是指输出值与误差之间的积分系数,用于降低系统误差。
微分参数Kd是指输出值与误差之间的微分系数,用于降低系统振荡。
PID控制算法在液压系统中被广泛应用,其优点是可靠性高、调节方便、响应速度快等。
三、液压系统PID控制算法研究液压系统中的PID控制算法应用较为广泛,研究液压系统中PID控制算法有助于提高系统的控制性能和稳定性。
其中,流量控制系统、液压伺服系统、电液伺服系统等应用较为广泛。
以流量控制系统为例,研究液压流量控制系统的PID控制算法,可以通过调节比例参数Kp、积分参数Ki、微分参数Kd三个参数来实现对系统的流量控制。
其中,比例参数Kp是指输出流量与输入流量之间的比例系数,积分参数Ki是指与误差之间的积分系数,微分参数Kd用于降低系统振荡。
四、PID控制算法在液压系统中的应用PID控制算法在液压系统中有非常广泛的应用,包括流量控制系统、压力控制系统、位置控制系统等。
以液压伺服系统为例,其控制过程基于PID控制算法,通过对伺服阀口的控制来调节输出的位置和速度。
液压系统中的智能控制算法设计与优化

液压系统中的智能控制算法设计与优化液压技术作为一种传动和控制系统非常重要的工程技术,广泛应用于机械、航空、冶金等多个领域。
而液压系统的智能控制算法设计与优化是液压技术发展的重要方向之一。
本文就液压系统中的智能控制算法设计与优化进行探讨。
一、智能控制算法在液压系统中的应用液压系统中的智能控制算法,主要通过对传感器数据的采集和分析,以及对执行机构的控制,实现对液压系统的自动调节和优化。
智能控制算法的应用在于提高液压系统的工作效率,并保证系统的稳定性和安全性。
1.1 自适应控制算法自适应控制算法是指根据液压系统自身的动态特性和工作条件,通过实时调整控制参数以达到系统最佳控制效果的一种算法。
自适应控制算法主要通过反馈控制实现,当液压系统产生偏差时,自动调节控制参数,使系统回归到正常状态。
例如,在液压缸的控制中,通过对液压缸位置进行实时监测,根据监测结果动态调整液压缸的控制参数,使液压缸能够更加精确地完成工作任务。
1.2 模糊控制算法模糊控制算法是一种基于模糊逻辑的控制方法,它通过模糊推理和模糊规则来进行控制决策,达到控制系统的目标。
在液压系统中,模糊控制算法可以有效应对输入信号变化剧烈、系统模型复杂的问题。
例如,在液压泵控制中,通过将液压泵的输入信号和输出信号进行模糊化处理,建立模糊控制规则,从而实现对液压泵输出压力的精确控制。
1.3 神经网络控制算法神经网络控制算法是一种模仿人脑神经网络结构和功能的控制方法,它通过学习和自适应能力,实现对液压系统的智能控制。
神经网络控制算法通过训练网络模型,来自动调整液压系统的控制参数,从而实现对液压系统动态性能的优化。
例如,在液压系统的压力控制中,通过建立压力与控制开关状态的神经网络模型,实时调整控制开关状态,以达到对液压系统压力的精确控制。
二、智能控制算法设计与优化的挑战液压系统中的智能控制算法设计与优化面临着一些挑战。
2.1 系统建模复杂液压系统的动态性能受到众多因素影响,例如流体力学、机械结构、温度等。
基于互联网的远程控制中网络时延测试与研究
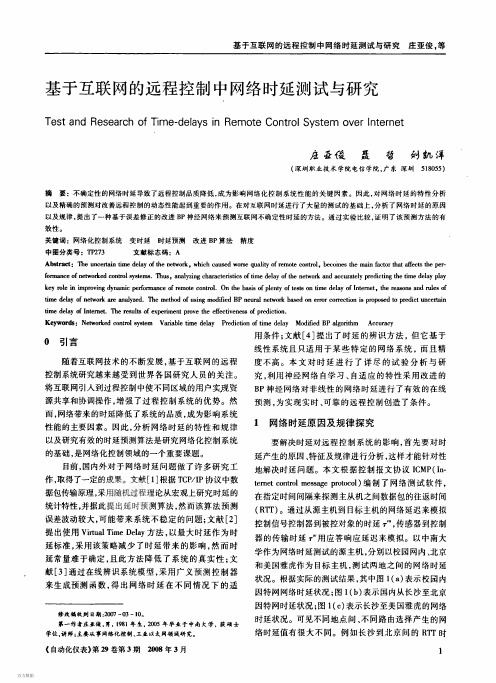
数据包1 个
( 校园网 T 分布 幼 RT
S IU 食 卜 气
数据包/ 个
桃 仍
5住 亩 』 气
()长沙到北京R 了 b l 分布
715 705 挑 哪
数据包/ 个
它随着负荷和网络阻塞程度的变化而变化. 由此可见, 数据包在通过网络进行传输的过程中, 由于在路由器中排队和转发, 从而产生时间延迟.数 据包的路由选择以及网络负载的变化, Ie e通 导致 n m t t 信时延成为一个随机变量. 从以上实验所得数据报得的网络回路时延分布可 以看出时延的不确定性, 然而, 在网络时延不确定性的 背后, 仍有一定的规律性.网络时延规律可归纳如下: ① 时延的幅值有界, 且在时延均值附近波动; 各 数据报得的时延在某一时间范围内总是在时延峰和时 延谷两幅值之间( 异常数据除外) . ② 在采样周期比较小, 网络流量正常的情况下, 时延的变化都比较有规律, 网络时延先达到某一峰值 再逐渐下降到某一谷值, 且变化在某一范围内, 故时延 的状况曲线呈现斜线. ③ 时延的幅值在同一区域, 某一时段, 网络负载
k li而p n dn 详 ra e r o cn . I b iOp n Otto t e e fle e t r nad 习s 盯me n 酬i y 而c rmn oe t ot O h a s l tfes ni dl g a o f c f me r n e l o s f e y s m 叮O n m t h e s n neo t .ea o s f t dl ont r , aa z . e e 记 O u鸣 m e B nu nt r b d n 二ro ln s r 关 d o r i u ea i e few k e y m a o nl e T m t f s 记近 d P er ew k a o e cr i ip p犯 tp d tn "i ydh h i l a o s e c e o o e cc n t e l o le e Te u oe伴r e p v t e cvnsop d tn i d a f n m . r l fx i n m eh f tee f r ii . me y t t h e t s s mt e e i s e co K y od:Nt r d otIy m V alt e e y Peii Ot e e M 访 d Pa ot e r w S e k cn s t o we o s e i r em a b i dl a r co fi dl dt n m a v d o e B l r m Acr y gh i ca u c
基于互联网的液压远程控制系统的协议选择和驱动方式研究
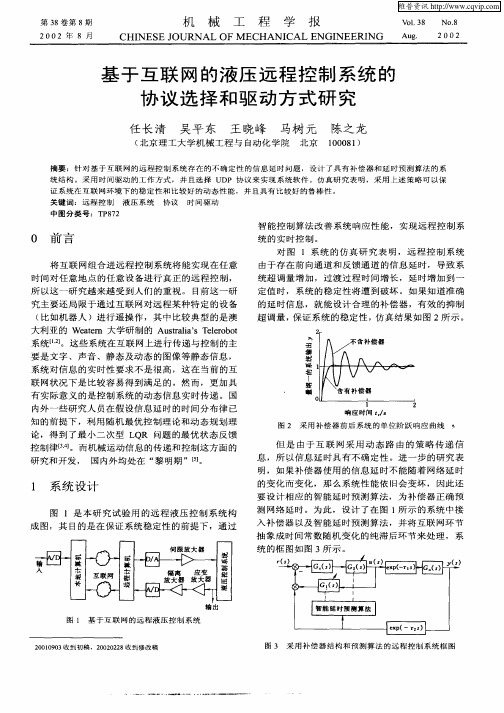
第 3 8卷 第 8期
2002 年 8 月
ห้องสมุดไป่ตู้
机
械
工
程
学
报
V. N. o3 18 o 8
Au . g 2002
CHI NESE OU RN AL J OF ECHAN I M CA L EN GI NEERI G N
联 网 状 况 下 是 比较 容 易得 到 满 足 的 。然 而 , 更 加 具 有 实 际 意 义 的是 控 制 系 统 的 动 态 信 息 实 时传 递 。 国
罚
球
一 一
害 f 骚 嘲
V V
、 含有补 偿器
1
一
2
内外 一 些研 究 人 员 在 假 设信 息 延 时 的时 间分 布 律 己
1 系 统 设 计
图 l 是 本 研 究 试 验 用 的 远 程 液 压 控 制 系 统 构 成 图 ,其 目的 是在 保 证 系 统 稳 定 性 的前 提 下 ,通 过
伺 服 放 大 器
输
入
隔 离 应 变 放 大 器 放 大 器 幽
纂
键
输 出
图 1 基 于 互 联 网 的 远 程 液 压 控 制 系 统
所 以这 一 研 究 越 来 越 受 到 人 们 的重 视 。 目前 这 一 研
究 主 要 还 局 限于 通 过 互 联 网 对 远 程 某 种 特 定 的 设 备 ( 比如 机 器 人 )进 行 遥 操 作 ,其 中 比较 典 型 的 是 澳 大利 亚 的 We tm 大 学研 制 的 Aut l ’ T l o o ae s ai s ee b t r a r
统 的实时控制 。 对 图 1 系 统 的 仿 真 研 究 表 明 , 远 程 控 制 系 统
基于神经网络的液压驱动系统建模与预测研究

基于神经网络的液压驱动系统建模与预测研究随着科技的不断进步和应用领域的不断扩大,液压驱动系统已经成为了现代工业中不可或缺的一个重要组成部分。
其中,神经网络技术的应用则为液压驱动系统的建模和预测提供了一种新的方法。
本文拟对基于神经网络的液压驱动系统建模和预测研究进行探讨,包括其应用的基本原理、建模方法和预测效果等。
一、神经网络技术在液压驱动系统中的应用神经网络技术是一种模仿人类神经系统信息处理机制的计算模型,它具有自适应性、非线性、并行处理等特点,可模拟并处理包括液压驱动系统在内的各种信息数据。
基于神经网络的液压驱动系统建模和预测研究则是运用神经网络的联想记忆和学习能力实现模型的输入输出关系。
具体而言,它可以将系统输入的状态量和控制信号作为输入变量,将系统输出量作为输出变量,采用反向传播算法进行模型训练和优化,从而实现模型的建立和预测。
二、基于神经网络的液压驱动系统建模方法在基于神经网络的液压驱动系统建模中,我们需要根据系统的特点和功能,选择合适的输入和输出量,确定神经网络的结构和拓扑,进行训练和测试等步骤。
常用的建模方法包括以下几种。
1. BP神经网络模型BP神经网络模型是一种单隐藏层前向反馈型神经网络,它采用反向传播算法对权值和偏置进行调整,以最小化模型输出与实际输出的均方误差。
在液压驱动系统建模中,BP神经网络模型可以将输入量和输出量之间的非线性映射转化为线性模型,从而实现输入输出关系的预测。
2. RBF神经网络模型RBF神经网络模型是基于径向基函数的一种神经网络模型,它将输出变量分解为多个径向基函数和线性组合项,从而实现输入输出的非线性映射。
在液压驱动系统建模中,RBF神经网络模型可以通过不同的径向基函数来表示不同的输入输出分布,从而提高模型的准确度和泛化能力。
3. Elman神经网络模型Elman神经网络模型是一种基于时间序列信息反馈的神经网络模型,它利用隐藏层状态变量来存储和反馈历史时刻的输入信息,从而实现对时序性信息的建模和预测。
控制系统中时间延迟影响的方法研究

控制系统中时间延迟影响的方法研究控制系统中时间延迟是指信号在传输过程中由于一些物理原因而引起的一定的时间延迟。
这种时间延迟会对系统的稳定性和性能产生不良的影响。
因此,控制系统中时间延迟影响的方法研究至关重要。
一、引言控制系统中时间延迟是一个常见的问题。
在自动控制、信号处理和通信系统等领域中,时间延迟是无法避免的。
时间延迟会导致系统的性能下降,降低系统的稳定性和可靠性。
所以,控制系统中时间延迟的研究是非常重要的。
二、控制系统中时间延迟的来源时间延迟的来源很多,例如:1. 传输线路的长度控制信号在传输过程中需要经过一定的距离,传输线路的长度就是一个重要的因素。
传输线路越长,信号传输的时间延迟也就越大。
2. 信号处理时间当控制信号需要进行处理时,信号处理时间也会对时间延迟产生影响。
例如,计算机的处理速度就会影响自动控制系统的响应速度。
3. 信号传输介质的特性信号传输介质的特性也会对时间延迟产生影响。
例如,光纤传输速度比电缆传输速度快,因此在使用光纤传输控制信号时,响应速度会更快。
三、控制系统中时间延迟的影响时间延迟会对控制系统的稳定性、精度和鲁棒性产生不良影响。
具体表现在以下几个方面:1. 系统的稳定性时间延迟会改变控制系统的时间响应特性,导致系统不稳定。
例如,在控制电机的运动时,如果控制信号的响应速度较慢,电机就会出现不稳定运动。
2. 系统的精度时间延迟会导致控制系统输出的结果与期望结果之间存在误差。
这会导致控制系统的精度下降,影响系统的性能。
3. 系统的鲁棒性时间延迟会使控制系统对外部干扰更加敏感,从而增加了系统的鲁棒性问题。
例如,在控制机器人时,时间延迟会导致机器人无法快速响应外部干扰,从而影响系统的鲁棒性。
四、控制系统中时间延迟的解决方法针对控制系统中时间延迟的影响,需要采用一系列的方法进行解决。
1. 建立数学模型为了更好地了解时间延迟对控制系统的影响,需要先建立一个合理的数学模型,分析控制算法和控制系统的特性。
- 1、下载文档前请自行甄别文档内容的完整性,平台不提供额外的编辑、内容补充、找答案等附加服务。
- 2、"仅部分预览"的文档,不可在线预览部分如存在完整性等问题,可反馈申请退款(可完整预览的文档不适用该条件!)。
- 3、如文档侵犯您的权益,请联系客服反馈,我们会尽快为您处理(人工客服工作时间:9:00-18:30)。
F b 2 0 e . 02
文章■号 :0 10 4 (0 2 0 —080 10 —8 8 2 0 )10 8 —5
基于互联 网的液压远程控制系统 延时预测算法研究
任长 清 , 吴平 东 , 王 晓 峰 , 马 树 元 , 陈 之 龙
( 北京理工大学 机械工程与 自动化学院 , 北京 10 8 ) 0 0 1
REN a g q n Ch n — ig, W U n — o g, Pig d n W ANG a —e g, Xio f n M A h — u n. CHEN h —o g S uy a Z iln
( c o l f c a i l n ie H ga d A t main B in n t ueo T c n lg , e ig 0 0 1 C i ) S h o Me h n a E g e n n u o t , e igIsi t f e h o o y B in 1 0 8 , hn o c n o j t j a
v l e me h d a e ma e u e o n o d r t e p t e s s e h v n e f r n e wh n t a u t o r d s f i r e o k e h y t m a e a f e p r o ma c e h i e
Wetm 大学 研制 的 Aut l ’Te rbt系统 [. ae sr is l oo aa e J ] 这些 系 统在 互 联 网上 进行 传 递 与控 制 的主 要 是 文 字 、 音 、 态 及动 态的 图像 等静 态 信 息 , 声 静 系统对 信 息 的实 时性 要 求 不高.更 具 有 实际意 义 的是 如 图 1
c a g o tme ea i u c ran Th smu a in h ws h t o h n e f i d ly s n e t i . e i lt s o t a c mp n ao s n f rc s o e s t r a d o ea t a i me i a e efci e b t o k e h y t m t be a d t i i t e s se o e s o ta d rt h tc r fetv o h t e p t e s se sa l n o l t h y tm v r h o n m
维普资讯
第2卷 2
第1 期
北 京 理 工 大 学 学 报
J u n l f ej g L si t o e h oo y o r a o in q t u f c n lg 02
中圈分娄号 : P 82 T 7
文献 标识码 : A
A u y o h r c s ih e i f H y a lc St d n t e Fo e a tAr t m tc o dr u i Te e o r lS se s d on l t r t l c nt o y t m Ba e n e ne
■
蔓 ;为了解决 不确定性变化 的网络 延时对基 于互联 网的液压远 程控制系统性能的 影响. 在系统 中设计 了补偿
器结构 解决 网络 延时问题 , 同时采用 延时预测算 法解决 网络延时不确 定性 变化的问题 . 以改善 系统的动态性 瞻和 保持 系统 的稳定性.仿真研究表明 , 采用补偿器结构和 延时预测算法能 够在 保证系统稳定性的 同时有 效地 降低系 统的超调量 , 短系统的过渡过程. 缩 关■调 : 互联 阿}液压远程控制 系统 f 补偿器 f 预测算法
s o t n t e s s e ’ t a se t b h v o . h re h y t m s r n in e a ir
Ke r s n e n t y r u i ee o to y tm }c m p n a o ;f rc s rt me i ywo d It r e ;h d a l tlc n r ls s e l c o e s t r o e a ta ih tc
Ab ta t sr c :A o c mp n a o sd sg e na h d a l ee o to y tm a e n I t r e n o d r e s t ri e in d i y r u i tlc n r ls s e b sd o n en ti r e c t mp o et es s e p ro ma c fet d b n e n tid c dtmed ly n b t o wa d lo o i r v h y tm e fr n ea c e yi tr e-n u e i ea si oh f r r o p a d fe b c o p Fo e a t a ih ei u h a h e s n r l—a l t o n h v r g — n e d a k lo . rc s rt m t s c st e r a o —u et be me h d a c d t e a e a e
所示的控制 系统动态信息的实时传递 , 即机械运动
出
目前 , 于互联 网 的远程 控 制 系统 研 究越 来 越 基 受 到世 界各 国研 究人 员 的重 视 , 但主 要 还 是局 限 于
通过互联网对远程某种特定的设备 ( 比如机器人) 进 行 遥 控 操 作 , 中 比 较 典 型 的 是 澳 大 利 亚 的 其