固体颗粒介质成形技术
柔性模具成形的6大关键技术,不是只能做飞机蒙皮零件
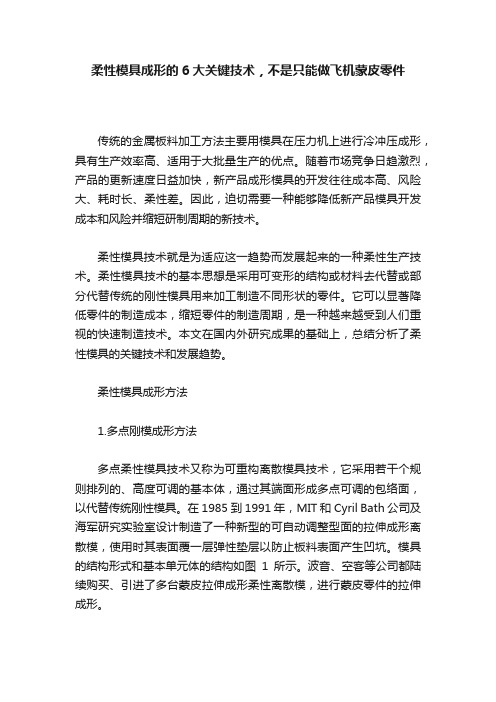
柔性模具成形的6大关键技术,不是只能做飞机蒙皮零件传统的金属板料加工方法主要用模具在压力机上进行冷冲压成形,具有生产效率高、适用于大批量生产的优点。
随着市场竞争日趋激烈,产品的更新速度日益加快,新产品成形模具的开发往往成本高、风险大、耗时长、柔性差。
因此,迫切需要一种能够降低新产品模具开发成本和风险并缩短研制周期的新技术。
柔性模具技术就是为适应这一趋势而发展起来的一种柔性生产技术。
柔性模具技术的基本思想是采用可变形的结构或材料去代替或部分代替传统的刚性模具用来加工制造不同形状的零件。
它可以显著降低零件的制造成本,缩短零件的制造周期,是一种越来越受到人们重视的快速制造技术。
本文在国内外研究成果的基础上,总结分析了柔性模具的关键技术和发展趋势。
柔性模具成形方法1.多点刚模成形方法多点柔性模具技术又称为可重构离散模具技术,它采用若干个规则排列的、高度可调的基本体,通过其端面形成多点可调的包络面,以代替传统刚性模具。
在1985到1991年,MIT和Cyril Bath公司及海军研究实验室设计制造了一种新型的可自动调整型面的拉伸成形离散模,使用时其表面覆一层弹性垫层以防止板料表面产生凹坑。
模具的结构形式和基本单元体的结构如图1所示。
波音、空客等公司都陆续购买、引进了多台蒙皮拉伸成形柔性离散模,进行蒙皮零件的拉伸成形。
国内北京航空制造工程研究所在现有柔性多点模具基础上,针对大型柔性多点模具,采用新型的调形驱动机构及伺服轴离合复用技术,实现与冲头驱动源分合,大大减少了驱动电机的数量,并开发出了具有价格竞争力的蒙皮拉伸成形多点模系统。
李明哲从90年代初期就开始进行离散模冲压技术的研究,开发了专用成形设备,取得了一系列的成果,在建筑结构件与装饰件、高速列车流线型车头覆盖件、船体外板及人脑颅骨修复体等产品的成形上发挥了重要作用。
图2(a)是利用片层式离散模进行的拉弯成形实验装置。
离散模应用拉弯成形时,由于型材拉弯零件截面复杂不同于板料拉形,因此需要模块化的结构。
塑料射出成形的原理

塑料射出成形的原理1.塑料熔融:将固体塑料颗粒加热至熔融状态,通常通过加热器加热塑料料筒中的原料。
在料筒中,螺杆将塑料推送到加热区域,并通过加热带将其熔化。
在被熔化的状态下,塑料经过混炼,确保其均匀性,以及与其他添加剂和颜料的混合。
2.射出注塑:将熔融态的塑料材料通过射出筒传送到射出嘴端,然后注射到模具的射出系统中。
射出系统通常由一个射出筒和一个射出嘴组成。
当塑料材料被注入到模具中时,射出嘴的阀门关闭以防止漏料。
3.压力和冷却:一旦塑料进入模具中,会施加一定压力以保持模具的形状。
这种压力通常由射出机的液压系统提供。
此外,模具内的冷却系统会通过冷却介质(如水)迅速降低塑料温度,促使其固化。
4.分离和排出:在塑料冷却和固化之后,模具会打开以分离成型件和废料。
成型件通常有一个喷嘴可以用来排出气体,是为了减少模具中的空气气体。
废料可以回收再利用,以减少浪费并提高效率。
1.高效生产:塑料射出成形是一种快速且连续的生产方法,可以在短时间内生产大量的塑料制品。
这是因为塑料射出成形每次只需要几秒钟至几分钟的周期时间。
2.复杂形状:塑料射出成形可以制造复杂的三维形状,具有细节丰富的内部空间和壁厚变化。
这是因为模具的设计可以根据需要进行定制,以实现所需的形状。
3.高精度:塑料射出成形具有高精度和重复性,可在0.001英寸的尺寸范围内制造产品。
这是因为模具的精确度高,并且注射过程经过精确控制。
4.多材料应用:塑料射出成形可以使用多种塑料材料进行生产,如聚丙烯、聚氨酯、聚碳酸酯等。
这使得塑料射出成形具有广泛的应用领域,在汽车、电子、医疗器械等行业得到广泛应用。
总结起来,塑料射出成形是一种通过将加热熔融态的塑料注入到模具中,通过压力冷却和固化成型的塑料加工方法。
它具有高效生产、制造复杂形状、高精度和适用于多材料的优势。
这种加工方法已经成为现代塑料制造业中不可或缺的一种技术。
四种典型的快速成型技术的成型原理
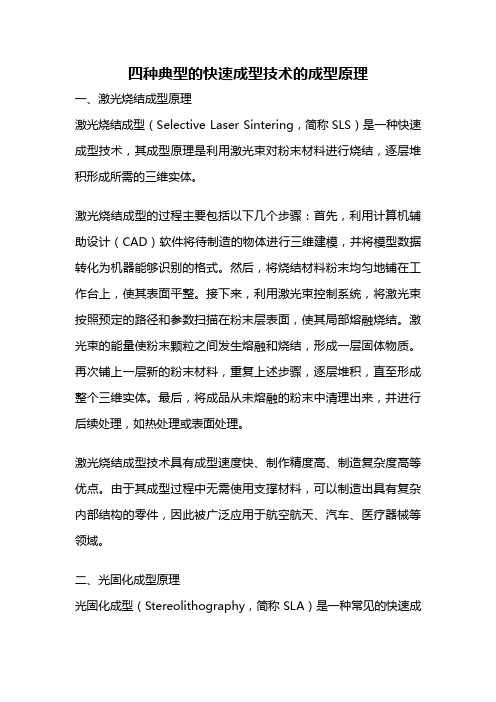
四种典型的快速成型技术的成型原理一、激光烧结成型原理激光烧结成型(Selective Laser Sintering,简称SLS)是一种快速成型技术,其成型原理是利用激光束对粉末材料进行烧结,逐层堆积形成所需的三维实体。
激光烧结成型的过程主要包括以下几个步骤:首先,利用计算机辅助设计(CAD)软件将待制造的物体进行三维建模,并将模型数据转化为机器能够识别的格式。
然后,将烧结材料粉末均匀地铺在工作台上,使其表面平整。
接下来,利用激光束控制系统,将激光束按照预定的路径和参数扫描在粉末层表面,使其局部熔融烧结。
激光束的能量使粉末颗粒之间发生熔融和烧结,形成一层固体物质。
再次铺上一层新的粉末材料,重复上述步骤,逐层堆积,直至形成整个三维实体。
最后,将成品从未熔融的粉末中清理出来,并进行后续处理,如热处理或表面处理。
激光烧结成型技术具有成型速度快、制作精度高、制造复杂度高等优点。
由于其成型过程中无需使用支撑材料,可以制造出具有复杂内部结构的零件,因此被广泛应用于航空航天、汽车、医疗器械等领域。
二、光固化成型原理光固化成型(Stereolithography,简称SLA)是一种常见的快速成型技术,其成型原理是利用紫外线激光束对光固化树脂进行逐层固化,最终形成所需的三维实体。
光固化成型的过程主要包括以下几个步骤:首先,利用计算机辅助设计(CAD)软件将待制造的物体进行三维建模,并将模型数据转化为机器能够识别的格式。
然后,将液态光固化树脂均匀地铺在工作台上。
接下来,利用紫外线激光束扫描器,将激光束按照预定的路径和参数照射在树脂表面,使其局部固化。
激光束的能量使树脂中的光敏物质发生聚合反应,从而使树脂由液态变为固态。
再次涂覆一层新的液态光固化树脂,重复上述步骤,逐层固化,最终形成整个三维实体。
最后,将成品从未固化的树脂中清洗出来,并进行后续处理,如烘干或光刻。
光固化成型技术具有成型速度快、制造精度高、制造复杂度高等优点。
SLS技术的成形工艺原理

SLS技术的成形工艺原理SLS(Selective Laser Sintering)即选择性激光烧结技术,是一种增材制造(Additive Manufacturing)的成形工艺。
它通过激光烧结聚合物或金属粉末,逐层堆叠形成三维实体物体。
以下是SLS技术的成形工艺原理的详细解释。
1.前期准备:在SLS技术开始之前,需要进行一系列的前期准备工作。
首先,设计师使用计算机辅助设计(CAD)软件创建三维模型。
然后,将模型转化为三维打印机可读取的STL文件格式。
接下来,将所需材料(聚合物或金属粉末)装载到SLS设备的粉末供料系统中,并确定打印参数,如温度、激光功率等。
2.激光扫描:SLS技术使用一束高能激光来瞄准并烧结粉末材料。
首先,工作台下降一层厚度,使其与打印平台上的一层粉末分离。
然后,激光器在工作区域内进行高速扫描,根据前期准备中的STL文件,将激光束逐点照射到工作区域粉末层上的目标位置。
3.材料烧结:当激光作用于目标位置时,粉末颗粒受热并瞬间熔化。
这种瞬时的高温使粉末材料粘结在一起形成固体结构。
这个过程被称为烧结。
烧结后,激光在目标位置上闪烁一段时间,使固体化的部分得到更充分的熔融。
4.补充粉末:完成激光扫描和烧结后,工作台再次下降一层厚度,以便为下一层打印粉末腾出空间。
然后,粉末供料系统启动,将新的一层粉末覆盖在上一层已烧结的部分上。
这个补充的粉末层将成为下一层产品的底部。
5.重复上述步骤:上述过程循环重复,直到打印的产品完全成型。
每次循环,工作台下降一个薄层的厚度,激光扫描并烧结新的一层粉末。
这个过程将逐渐堆叠形成一个完整的三维物体。
6.等待冷却与后处理:打印完成后,待打印物品冷却一段时间,以确保其达到足够的硬度和稳定性。
然后,将产品从打印平台上取下。
在一些情况下,打印物可能需要进行一些后处理步骤,例如去除未粘结的粉末,热处理或表面处理。
总结:SLS技术利用激光烧结粉末材料来逐层堆叠形成三维实体物体。
热压烧结的成形原理及应用
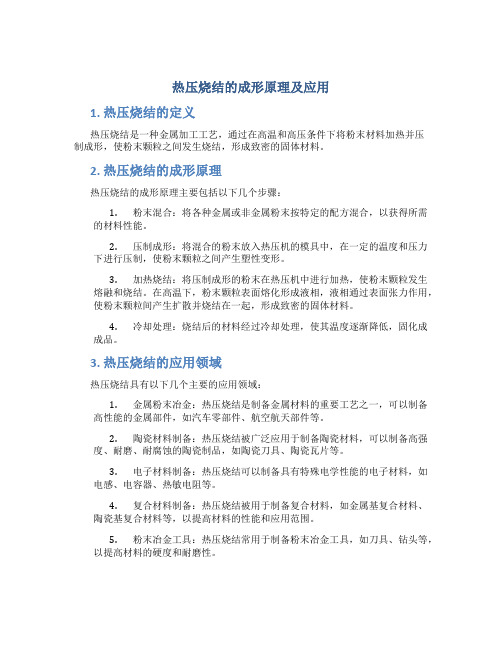
热压烧结的成形原理及应用1. 热压烧结的定义热压烧结是一种金属加工工艺,通过在高温和高压条件下将粉末材料加热并压制成形,使粉末颗粒之间发生烧结,形成致密的固体材料。
2. 热压烧结的成形原理热压烧结的成形原理主要包括以下几个步骤:1.粉末混合:将各种金属或非金属粉末按特定的配方混合,以获得所需的材料性能。
2.压制成形:将混合的粉末放入热压机的模具中,在一定的温度和压力下进行压制,使粉末颗粒之间产生塑性变形。
3.加热烧结:将压制成形的粉末在热压机中进行加热,使粉末颗粒发生熔融和烧结。
在高温下,粉末颗粒表面熔化形成液相,液相通过表面张力作用,使粉末颗粒间产生扩散并烧结在一起,形成致密的固体材料。
4.冷却处理:烧结后的材料经过冷却处理,使其温度逐渐降低,固化成成品。
3. 热压烧结的应用领域热压烧结具有以下几个主要的应用领域:1.金属粉末冶金:热压烧结是制备金属材料的重要工艺之一,可以制备高性能的金属部件,如汽车零部件、航空航天部件等。
2.陶瓷材料制备:热压烧结被广泛应用于制备陶瓷材料,可以制备高强度、耐磨、耐腐蚀的陶瓷制品,如陶瓷刀具、陶瓷瓦片等。
3.电子材料制备:热压烧结可以制备具有特殊电学性能的电子材料,如电感、电容器、热敏电阻等。
4.复合材料制备:热压烧结被用于制备复合材料,如金属基复合材料、陶瓷基复合材料等,以提高材料的性能和应用范围。
5.粉末冶金工具:热压烧结常用于制备粉末冶金工具,如刀具、钻头等,以提高材料的硬度和耐磨性。
4. 热压烧结的优势和局限性热压烧结具有以下几个优势:•可以制备复杂形状的零件:热压烧结可以利用模具制备各种形状的零件,可以满足各种特殊要求。
•可以制备高性能材料:热压烧结可以使粉末颗粒之间发生扩散和烧结,形成致密的固体材料,提高了材料的密度和性能。
•可以节约材料:热压烧结可以将废料、废渣等杂质重新利用,减少资源的浪费。
然而,热压烧结也存在一些局限性:•生产周期长:热压烧结的制备周期较长,需要经过多道工序,加工周期较长,不适合生产大批量产品。
特种陶瓷的成型方法

第三节 成型工艺
一、压力成型方法
所谓压力成型是用粉料,即以固体颗粒为原料在一定的 压力下进行成型的方法,也叫模压成型或干压成型。 为了减少摩擦和增加强度,粉料中可能含有少量液体、 粘结剂包裹在颗粒外面。粘结剂含量较低(一般为 7~ 8% )。
(一)干压成型
干压成型又称模压成型,是将粉料经过造粒、流动性好,颗粒级配 合适的粉料,装入模具内,通过压机的柱塞施以外加压力,使粉料压 成制一定形状的坯体的方法。 这是最常用的成型方法之一。由于粉末 颗粒之间,粉末与模冲、模壁之间的摩擦,使压制压力损失,造成压 坯密度分布的不均匀。单向压制时,密度沿高度方向降低。
条件下,快速充填到模具内,避免架桥和死角形成,对获得均匀坯体 尤为重要。 c.粘结剂和润滑剂:选择合适的润滑剂和粘结剂将有助于降低模壁与粉 体以及粉体之间的磨擦,从而使素坯密度保持均匀,也降低了模具的 磨损。 d.模具设计。很大程度上依赖于工程师们的经验,以及材料烧结收缩率, 选择合适的形状和公差,来保证成型工艺的质量和成品率。
第三节 成型工艺
(二) 挤压成型 挤压是利用液压机推动活塞,将已塑化的坯料从挤压
嘴挤出。由于挤压嘴的内型逐渐缩小,从而使活塞对泥团 产生很大的挤压力,使坯料致密并成型。
挤压被广泛用于生产砖、地砖、管子、棒以及具有等 截面的长形部件。截面形状非常复杂的部件也可采用挤压, 最具代表性的是大量用于汽车尾气排放的蜂窝陶瓷的生产, 目前国内制造陶瓷蜂窝体均采用此方法 。也可用于生产热 交换器的蜂窝结构。
(3)挤压法的优点: 污染小,操作易于自动化,可连续生产,效率高。
干式等静压制原理图
¾ 干压等静压成型的特点:
¾ 干式等静压更适合于生产形状简单的长形、壁薄、 管状制品。
sls技术的成型原理

SLS(Selective Laser Sintering)技术是一种增材制造(AM)技术,其成型原理基于激光束在粉末层上的选择性扫描和逐层烧结。
首先,SLS技术使用粉末材料作为原料,通常为金属粉末或塑料粉末。
在打印过程中,粉末被铺放在打印平台上,形成一层薄薄的粉末层。
接下来,激光束被投射到粉末层上。
激光束的功率密度和扫描速度可以根据需要进行调整,以控制烧结的深度和速度。
当激光束扫描到粉末层时,粉末颗粒之间的温度会迅速升高,达到熔点或软化点。
在激光束的作用下,粉末颗粒之间的连接形成烧结区域。
这些烧结区域会形成三维结构,并逐渐累积形成最终的打印对象。
在每一层烧结完成后,打印平台会下降一定距离,以便在下一层上铺设新的粉末层。
然后,新的激光束会再次扫描该层,进行下一层的烧结。
这个过程会重复进行,直到整个打印对象被制造完成。
需要注意的是,SLS技术的成型原理涉及到多个因素,如激光功率密度、扫描速度、粉末粒度、粉末成分等。
这些因素都会影响打印对象的精度、强度和表面质量。
因此,在实际应用中,需要根据具体需求和材料特性进行参数调整和优化。
此外,SLS技术还可以与其他增材制造技术结合使用,如SLA(光固化)、FDM(熔融沉积成型)等。
这些技术的结合可以进一步提高打印对象的精度、复杂性和功能性。
SLS成型技术工艺原理及应用

- 64 -工 业 技 术0 引言选择性激光烧结快速成形(Selective Laser Sintering Rapid Prototyping,SLS)技术材料选择广泛,正在迅速发展,并得到了越来越多的关注[1]。
SLS 技术与其他快速成型的制作过程相同,都采用离散堆叠成型原理,使用Nd:YAG 激光发射器作为光源,利用切片中的二维信息,通过计算机来控制激光束,调整合适的激光密度,全部烧结后,除去多余的粉末,进行一系列研磨处理后得到零件。
该技术将CAD 技术、数字控制加工、激光和材料技术相结合,缩短了产品设计制造周期,降低了开发成本,提高了产品竞争力。
由于SLS 工艺具有许多优点,例如粉末材料选择广泛,其制造工艺相对简单,具有无支撑结构以及零件直接烧结等特点,因此其发展最为迅速,已成为最成功和商业化的快速成型方法之一[2-3]。
1 SLS技术原理1.1 SLS技术的成形工艺原理图1是SLS 技术制造工艺的原理。
首先,建立CAD 模型,并转化为STL格式,利用分层软件对CAD 模型进行切片,获得各加工层的数据信息,在计算机的控制下,根据层面信息调整激光束进行扫描,使粉末烧结固化,重复该过程,直到得到三维实体[4]。
图1 SLS 技术的成形工艺原理1.2 SLS快速成形技术工艺流程SLS 快速成形技术工艺,具体流程如图2所示。
1.2.1建立CAD模型采用Pro/E,UG 等三维CAD 软件建立3D 实体模型,并以STL 格式输出。
图2 SLS 快速成形工艺流程图1.2.2 分层处理目前,SLS 所支持的文件格式为STL,采用分层软件在Z 方向进行分层处理,得到分层截面,并将该层面信息转化为激光扫描时的轨迹。
1.2.3 烧结成形扫描之前,先将成型缸下降一定厚度,然后使供粉缸升高一定的高度,铺粉辊从左边压到成型缸上。
激光扫描第1层横截面及轮廓信息,激光扫描的粉末会在高温下迅速熔化并相互黏接;烧结完第一层后,铺粉,进行第2层激光扫描,如此重复直到烧结完成。
第九章制粒第一节概述制粒(granulation)是把粉末、块状物

第九章制粒第一节概述制粒(granulation)是把粉末、块状物、溶液、熔融液等状态的物料进行处理、制成具有一定形态和大小的颗粒(粒子)的操作。
多数的固体剂型都要经过“制粒”过程。
制粒技术不仅应用于片剂、胶囊剂、颗粒剂等的制备过程,而且为了方便粉末的处理也经常需制成颗粒,再如供直接压片用的辅料也常需制成颗粒,以保证药品质量和生产的顺利进行。
(一)制粒的目的(1)使粒子具有良好的流动性,在药物的输送、包装、充填等方面容易实现自动化、连续化、定量化;(2)防止由于粒度、密度的差异而引起的分离现象,有利于各种成分的均匀混合;(3)防止操作过程的粉尘飞扬及在器壁上的粘着,避免环境污染和原料的损失;(4)调整堆密度,改善溶解性能;(5)使压片过程中压力的传递均匀;(6)配方和操作适当时,可提高药效和药物的稳定性;(7)便于服用等。
颗粒有可能是中间体,如片剂生产过程中的制粒;也有可能是产品,如颗粒剂等。
制粒的目的不同,其要求有所不同或有所侧重。
如压片用颗粒,以改善流动性和压缩成形性为主要目的;而颗粒剂、胶囊剂的制粒过程以流动性好、防止粘着及飞扬、提高混合均匀性、改善外观等为主要目的。
近年来随着制药工业的发展,制粒技术也得到了很大的提高。
(二)制粒方法的分类在医药生产中广泛应用的制粒方法可分为三大类。
即湿法制粒、干法制粒、喷雾制粒。
(1)湿法制粒:在原材料粉末中加入粘合液,靠粘合液的架桥或粘结作用使粉末聚结在一起而制备颗粒的方法。
挤压制粒、转动制粒、流化床制粒、搅拌制粒等属于湿法制粒。
(2)干法制粒:在原料粉末中不加入任何液体,靠压缩力的作用使粒子间距离接近而产生结合力,按一定大小和形状直接压缩成所需颗粒,或先将粉末压缩成片状或板状物后,重新粉碎成所需大小的颗粒。
(3)喷雾制粒:将药物溶液或混悬液喷成雾状,在热风中迅速干燥而得球形颗粒的操作。
(三)粉粒间的结合力颗粒是由无数个粉粒(或结晶粒子)靠某种结合力结聚在一起形成的。
SLS技术的成形工艺原理

SLS技术的成形工艺原理SLS技术(Selective Laser Sintering)是一种基于激光能量照射塑料粉末,使其熔化并逐层固化成形的三维打印技术。
SLS技术采用粉末床层积法,能够制造出复杂的几何形状,并且不需要支撑结构,因此在工业领域有着广泛的应用。
其成形工艺原理主要包括粉末填充、激光照射和固化等过程。
首先,SLS技术的成形开始于粉末填充阶段。
在这个阶段,需要将塑料粉末均匀地喷散在建模区域的平面上。
通常情况下,建模区域的平面是由一层可移动的平台构成的。
通过粉末层的厚度控制,可以调整成品的质量和精度。
接下来,激光照射成为SLS成形过程的关键步骤。
激光器会发射一束高能量的激光束,可在建模区域上形成散焦的径向光斑。
这个焦点光斑极其精确,能够准确地照射到粉末层上的局部区域,并使其局部熔化。
而粉末层周围的区域并不受激光的照射,因此保持在原有的粉末状态。
当激光束照射到粉末层上时,粉末粒子的表面温度会迅速上升,超过其玻璃化温度。
玻璃化温度是粉末颗粒附近的温度,使得粉末颗粒变得粘稠,但是没有熔化。
这使得粘稠化的颗粒能够在创建一个连续的固态区域时保持在受激光区域内。
通过激光光斑的准确定位和时间控制,可以将多个固态区域连接起来,并形成一个完整的物体层。
当一层固态区域形成之后,建模区域平台会向下移动一层,重新装填新的粉末层。
再次进行激光照射和固化,新的固态区域就会与上一层进行连接。
通过不断重复这个过程,直到完成整个物体的打印。
在一次完整的打印过程中,由于激光束的径向散焦,可以同时打印多个物体或多个不同的部分。
这为提高生产效率提供了可能,可以在一次打印中完成多个物体的生产。
最后,打印完整后的物体需要进行后处理。
由于打印物体是由粉末层渲染出来的,还需要将多余的粉末清除出来,并进行喷砂、烧结等后处理工艺,以加强物体的强度和表面质量。
总结起来,SLS技术的成形工艺原理主要包括粉末填充、激光照射和固化,通过多次照射和固化形成连续的固态区域,最终构建出完整的三维打印物体。
干货制粒必读(详细的制粒技术及经验)
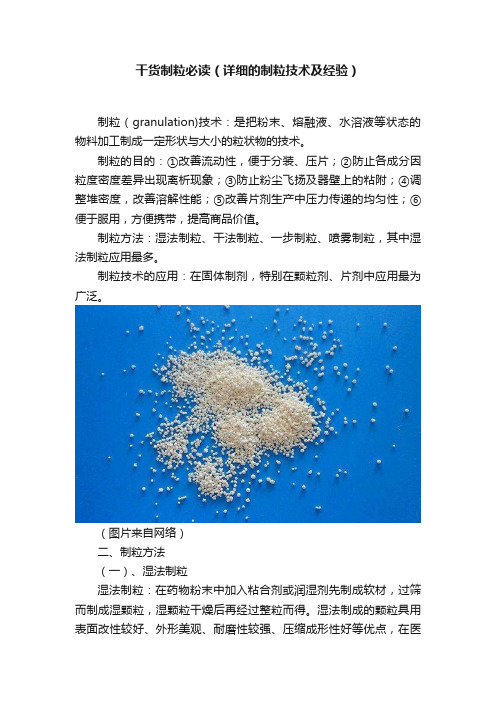
干货制粒必读(详细的制粒技术及经验)制粒(granulation)技术:是把粉末、熔融液、水溶液等状态的物料加工制成一定形状与大小的粒状物的技术。
制粒的目的:①改善流动性,便于分装、压片;②防止各成分因粒度密度差异出现离析现象;③防止粉尘飞扬及器壁上的粘附;④调整堆密度,改善溶解性能;⑤改善片剂生产中压力传递的均匀性;⑥便于服用,方便携带,提高商品价值。
制粒方法:湿法制粒、干法制粒、一步制粒、喷雾制粒,其中湿法制粒应用最多。
制粒技术的应用:在固体制剂,特别在颗粒剂、片剂中应用最为广泛。
(图片来自网络)二、制粒方法(一)、湿法制粒湿法制粒:在药物粉末中加入粘合剂或润湿剂先制成软材,过筛而制成湿颗粒,湿颗粒干燥后再经过整粒而得。
湿法制成的颗粒具用表面改性较好、外形美观、耐磨性较强、压缩成形性好等优点,在医药工业中应用最为广泛。
湿法制粒机理:首先是粘合剂中的液体将药物粉末表面润湿,使粉粒间产生粘着力,然后在液体架桥与外加机械力的作用下制成一定形状和大小的颗粒,经干燥后最终以固体桥的形式固结。
湿法制粒主要包括制软材、制湿颗粒、湿颗粒干燥及整粒等过程。
1、制软材:将按处方称量好的原辅料细粉混匀,加入适量的润湿剂或粘合剂混匀即成软材。
制软材应注意的问题(1)粘合剂的种类与用量要根据物料的性质而定;(2)加入粘合剂的浓度与搅拌时间,要根椐不同品种灵活掌握;(3)软材质量。
由于原辅料的差异,很难定出统一标准,一般凭经验掌握,用手捏紧能成团块,手指轻压又能散裂得开。
(4)湿搅时间的长短对颗粒的软材有很大关系,湿混合时间越长,则粘性越大,制成的颗粒就越硬。
2、制湿颗粒:使软材通过筛网而成颗粒。
颗粒由筛孔落下如成长条状时,表明软材过湿,湿合剂或润湿剂过多。
相反若软材通过筛孔后呈粉状,表明软材过干,应适当调整。
常用设备:摇摆式颗粒机、高速搅拌制粒机筛网:有尼龙丝、镀锌铁丝、不锈钢、板块四种筛网。
3、湿颗粒干燥:过筛制得的湿颗粒应立即干燥,以免结块或受压变形(可采用不锈钢盘将制好的湿颗粒摊开放置并不时翻动以解决湿颗粒存放结块及变形问题)。
MIM简介及基本流程
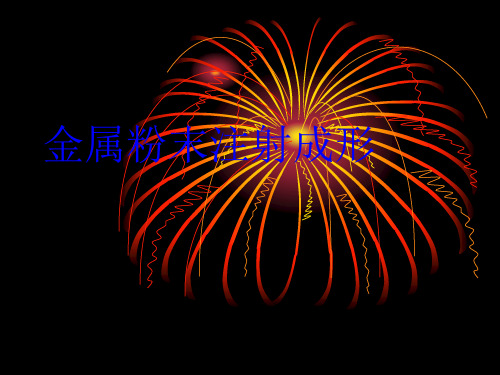
(5)成型周期
成型周期即完成一次注射成型制品所需的时间。包括: 1)注射加压时间(保压时间、注射时间); 2)冷却时间(模内冷却或固化时间); 3)其他时间(开模、取出制品、涂脱模剂、安放嵌件、闭模等 时间)。 成型周期是提高生产率的关键,在保证产品质量的前提下, 应尽量缩短成型周期。
制品后处理
作用 分类 提高制品的尺寸稳定性,消除内应力 热处理 调湿处理 (1)热处理 热处理的实质:迫使冻结的分子链松弛,凝固的大 分子链段转向无规位置,消除部分内应力,提高结晶度, 稳定结晶结构,提高弹性模量,降低断裂延伸率。 (2)调湿处理 将刚脱模的制品放入水中,与空气隔绝、防止氧化。 调湿条件:90~110℃ 4h
(4)注射速度及注射压力
注射压力大小与注射机种类、物料流动性、模具浇口尺寸、 产品厚度、模具温度及流程等因素有关。 一般注射压力略高于热塑性塑料的注射压力。 保压的作用:使制品冷却收缩时得以补料,尺寸准确,表 面光洁,有利于消除气泡。保压时间一般 0.3~2 分钟,特厚制 品可达5~10分钟。 注射速度与注射压力、温度、模口尺寸等因素有关。注射 速度慢不利于充模,生产效率低,注射速度过快易混入气泡。 需通过实际实验确定。
MIM和传统方法的比较: 压铸工艺用在铝和锌合金等熔点低、铸液流动性良好的材料。此工艺的产品因 材料的限制,其强度、耐磨性、耐蚀性均有限度。MIM工艺可以加工的原材料 则较多。注射成型工艺技术利用注射机注射成型产品毛坯,保证物料充分充满 模具型腔(金属液铸造充模较差),也就保证了零件高复杂结构的实现。 粉末锻造是一项重要的发展,已适用于连杆的量产制造。但是一般而言,锻造 过中热处理的成本和模具的寿命还是有问题,仍待进一步解决。 传统机械加工法,近年来靠自动化而提升了其加工能力,在效果和精度上 有极大的进步,但是基本的程序上仍脱不开逐步加工(车削、刨、铣、磨、钻孔、 抛光等)来完成零件形状的方式。机械加工方法的加工精度远优于其他加工方法, 但是因为材料的有效利用率低,且其形状的完成受限于设备与刀具,有些零件 无法用机械加工完成。相反,MIM可以有效利用材料,不受限制,对于小型、 高难度形状的精密零件的制造,MIM工艺比较机械加工而言,其成本较低且效 率高,具有很强的竞争力。 以往在传统加工技术中先作成个别元件再组合成组件的方式,在使用MIM 技术时可以考虑整合成完整的单一零件,大大减少步骤、简化加工程序。 MIM技术并非与传统加工方法竞争,而是弥补传统加工方法在技术上的不足 或无法制作的缺陷。MIM技术可以在传统加工方法制作的零件领域上发挥其特 长。MIM工艺在零部件制造方面所具有的技术优势可成型高度复杂的结构零件。
粉末冶金 (1)
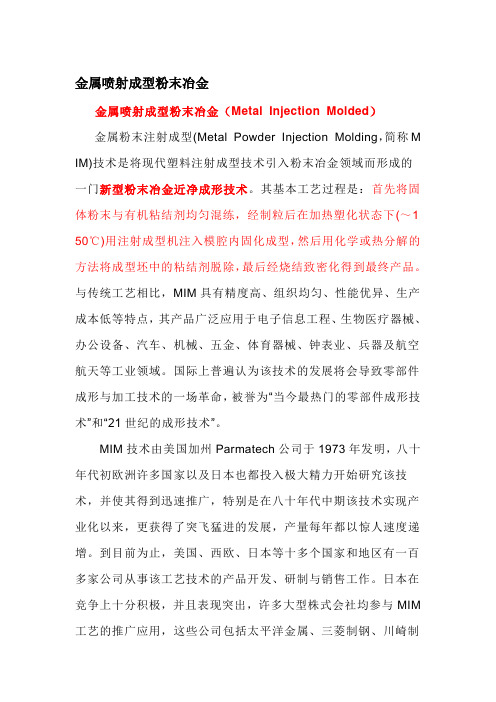
金属喷射成型粉末冶金金属喷射成型粉末冶金(Metal Injection Molded)金属粉末注射成型(Metal Powder Injection Molding,简称M IM)技术是将现代塑料注射成型技术引入粉末冶金领域而形成的一门新型粉末冶金近净成形技术。
其基本工艺过程是:首先将固体粉末与有机粘结剂均匀混练,经制粒后在加热塑化状态下(~1 50℃)用注射成型机注入模腔内固化成型,然后用化学或热分解的方法将成型坯中的粘结剂脱除,最后经烧结致密化得到最终产品。
与传统工艺相比,MIM具有精度高、组织均匀、性能优异、生产成本低等特点,其产品广泛应用于电子信息工程、生物医疗器械、办公设备、汽车、机械、五金、体育器械、钟表业、兵器及航空航天等工业领域。
国际上普遍认为该技术的发展将会导致零部件成形与加工技术的一场革命,被誉为“当今最热门的零部件成形技术”和“21世纪的成形技术”。
MIM技术由美国加州Parmatech公司于1973年发明,八十年代初欧洲许多国家以及日本也都投入极大精力开始研究该技术,并使其得到迅速推广,特别是在八十年代中期该技术实现产业化以来,更获得了突飞猛进的发展,产量每年都以惊人速度递增。
到目前为止,美国、西欧、日本等十多个国家和地区有一百多家公司从事该工艺技术的产品开发、研制与销售工作。
日本在竞争上十分积极,并且表现突出,许多大型株式会社均参与MIM 工艺的推广应用,这些公司包括太平洋金属、三菱制钢、川崎制铁、神户制钢、住友矿山、精工-爱普生、大同特殊钢等。
目前日本有四十多家专业从事MIM产业的公司,其MIM产品的销售总值早已超过欧洲并直追美国。
MIM技术已成为新型制造业中最为活跃的前沿技术领域,是世界冶金行业的开拓性技术,代表着粉末冶金技术发展的主方向。
金属粉末注射成型技术是塑料成型工艺学、高分子化学、粉末冶金工艺学和金属材料学等多学科渗透与交叉的产物,利用模具可注射成型坯件并通过烧结快速制造高密度、高精度、三维复杂形状的结构零件,能够快速、准确地将设计思想物化为具有一定结构、功能特性的制品,并可直接批量生产出零件,是制造技术行业一次新的变革。
制粒技术

制粒技术一、制粒技术概念制粒(granulation)技术:是把粉末、熔融液、水溶液等状态的物料加工制成一定形状与大小的粒状物的技术。
制粒的目的:①改善流动性,便于分装、压片;②防止各成分因粒度密度差异出现离析现象;③防止粉尘飞扬及器壁上的粘附;④调整堆密度,改善溶解性能;⑤改善片剂生产中压力传递的均匀性;⑥便于服用,方便携带,提高商品价值。
制粒方法:湿法制粒、干法制粒、一步制粒、喷雾制粒,其中湿法制粒应用最多。
制粒技术的应用:在固体制剂,特别在颗粒剂、片剂中应用最为广泛。
三、影响湿法制粒的因素1、原辅料性质(1)粉末细、质地疏松,干燥及粘性较差,在水中溶解度小;选用粘性较强的粘合剂,且粘合剂的用量要多些。
(2)在水中溶解度大,原辅料本身粘性较强;选用润湿剂或粘性较小的粘合剂,且粘合剂的用量相对要少些。
(3)对湿敏感,易水解;不能选用水作为粘合剂的溶剂,选用无水乙醇或其它有机溶媒作粘合剂的溶剂。
(4)对热敏感,易分解;尽量不选用水作为粘合剂的溶剂,选用一定溶度的乙醇作粘合剂的溶剂,以减少颗粒干燥的时间和降低干燥温度。
(5)对湿、热稳定;选用成本较低的水作为粘合剂的溶剂。
2、润湿剂和粘合剂润湿剂(moistening agents):使物料润湿以产生足够强度的粘性以利于制成颗粒的液体。
润湿剂本身无粘性或粘性不强,但可润湿物料并诱发物料本身的粘性,使之能聚结成软材并制成颗粒。
如:蒸馏水、乙醇。
粘合剂(adhesives):能使无粘性或粘性较小的物料聚集粘结成颗粒或压缩成型的具粘性的固体粉末或粘稠液体。
如聚维酮(PVP)、羟丙甲纤维素(HPMC)、羧甲纤维素钠(CMC-Na)、糖浆等。
(1)种类①蒸馏水:水本身无粘性,当物料中含有遇水能产生粘性的成分时,用蒸馏水润湿即可诱发其粘性而制成适宜的颗粒。
但用水作润湿剂时,由于物料往往对水的吸收较快,较易发生湿润不均匀的现象,且干燥温度较高,故不耐热、遇水易变质或易溶于水的药物不宜采用。
粉末注射成形技术

粉末注射成形技术粉末注射成形技术是一种常用的材料成型方法,适用于一系列粉末材料,如金属、陶瓷、塑料等。
它通过将粉末材料加热并注射到模具中,然后通过压力和温度控制来形成固体零件。
本文将介绍粉末注射成形技术的原理、过程、优势以及应用领域。
1.材料准备:选择合适的粉末材料,并进行预处理,如筛选、控制颗粒大小和形状等。
2.混合:将粉末材料与添加剂混合,以改善其流动性、可压性和烧结性能。
3.注射:将混合物注入到注射机中,然后通过高压将其注射到设定的模具腔中。
4.压实:在注射后,使用压力机对材料进行压缩和固化,以增加材料的密度和强度。
5.烧结:将压实后的材料置于高温环境中,进行烧结以使粉末颗粒结合成为坚固的零件。
1.复杂形状:粉末注射成形技术可以制造复杂形状的部件,例如内腔、薄壁结构和三维曲面,相比于传统的成形方法更加灵活。
2.高精度:通过控制材料的流动性和压实过程,可以实现高精度、高质量零件的制造。
3.材料选择:粉末注射成形技术适用于多种材料,包括金属、陶瓷、塑料等,可以根据不同应用的需要选择合适的材料。
4.节约材料:由于粉末材料可以重复使用,粉末注射成形技术可以节约材料成本并减少废料的产生。
1.汽车行业:粉末注射成形技术可用于制造发动机零件、传动系统、刹车系统、底盘部件等,提高零件的耐磨性和耐腐蚀性。
2.航空航天行业:粉末注射成形技术可制造导弹部件、发动机零件、航空航天设备等,提高材料的强度和抗腐蚀性。
3.医疗器械:粉末注射成形技术可用于制造金属和陶瓷假体、植入物以及手术器械等,提供个性化和高精度的解决方案。
4.电子行业:粉末注射成形技术可制造电子器件、散热器、天线等,提高元器件的稳定性和可靠性。
总之,粉末注射成形技术是一种广泛应用于材料成型的先进技术,具有高精度、高强度和多材料选择等优势。
随着技术的不断发展,相信粉末注射成形技术将在更多领域展现其巨大潜力。
固体颗粒介质成形技术
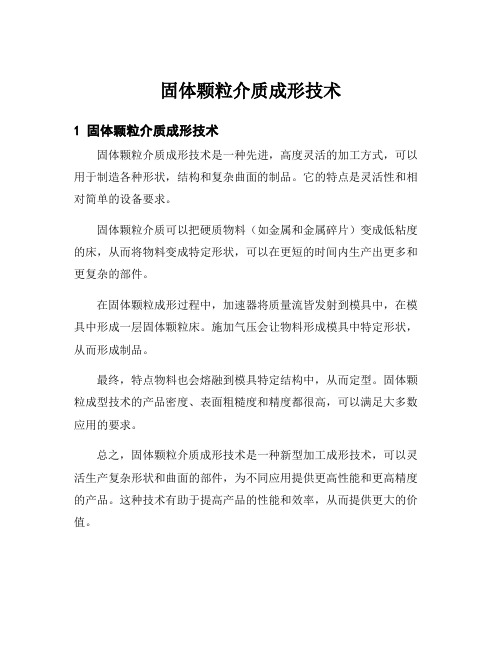
固体颗粒介质成形技术
1 固体颗粒介质成形技术
固体颗粒介质成形技术是一种先进,高度灵活的加工方式,可以用于制造各种形状,结构和复杂曲面的制品。
它的特点是灵活性和相对简单的设备要求。
固体颗粒介质可以把硬质物料(如金属和金属碎片)变成低粘度的床,从而将物料变成特定形状,可以在更短的时间内生产出更多和更复杂的部件。
在固体颗粒成形过程中,加速器将质量流皆发射到模具中,在模具中形成一层固体颗粒床。
施加气压会让物料形成模具中特定形状,从而形成制品。
最终,特点物料也会熔融到模具特定结构中,从而定型。
固体颗粒成型技术的产品密度、表面粗糙度和精度都很高,可以满足大多数应用的要求。
总之,固体颗粒介质成形技术是一种新型加工成形技术,可以灵活生产复杂形状和曲面的部件,为不同应用提供更高性能和更高精度的产品。
这种技术有助于提高产品的性能和效率,从而提供更大的价值。
干粉造粒工艺流程

干粉造粒工艺流程一、概述干粉造粒是一种常见的固体物料处理技术,广泛应用于化工、冶金、农药、医药等行业。
它将粉状物料通过造粒机械加工,使其颗粒化,并赋予一定的物理和化学性质,以满足不同工艺和产品要求。
二、干粉造粒的基本原理干粉造粒是通过机械力和压力作用下的颗粒形成过程,可以分为以下几个基本步骤:1. 物料进料:将粉状物料通过给料装置加入到造粒机械中。
2. 压缩:利用造粒机械的挤压作用,使物料颗粒间形成紧密接触。
3. 成形:物料受到机械力的作用,使其逐渐形成一定形状和大小的颗粒。
4. 散热:由于机械加工和压缩过程会引起能量的转化,物料会发热,需要通过散热来降低温度。
5. 固化:通过物料中的湿分或其他添加剂的作用,使颗粒表面形成一定的硬度,确保颗粒的稳定性。
6. 收集:将造粒后的颗粒进行收集、分级和包装等后续处理。
三、干粉造粒工艺流程干粉造粒工艺流程可以按照不同的工艺要求进行调整,但基本流程包括以下几个步骤:1. 原料准备原料准备是干粉造粒的第一步,主要包括原料的筛选、研磨和混合等操作。
筛选可以去除粗大颗粒和杂质,研磨可以使原料粒度均匀,混合可以将不同成分的原料均匀分布。
2. 干粉造粒机选择根据原料的特性和要求,选择合适的干粉造粒机型号。
常见的干粉造粒机有压力型造粒机、摩擦型造粒机、滚筒造粒机等。
3. 控制操作参数根据干粉造粒机的不同,需要控制适当的操作参数,如进料速度、转速、压力和温度等。
合理的操作参数可以保证造粒效果和产品质量。
4. 干粉造粒过程将经过预处理的原料加入到造粒机中,通过机械力和压力的作用下,经过压缩、成形、散热和固化等过程,形成一定大小和形状的颗粒。
5. 产品处理造粒后的产品需要进行处理,如冷却、筛分、干燥和包装等。
冷却可以降低产品温度,筛分可以去除不规则颗粒,干燥可以降低湿分含量,包装可以保护产品质量。
四、干粉造粒工艺的影响因素干粉造粒工艺的效果和产品质量受到许多因素的影响,主要包括以下几个方面:1. 原料特性原料的粒度、湿分、粉性和流动性等特性会直接影响干粉造粒的效果。
蒸汽造粒的原理和应用实例
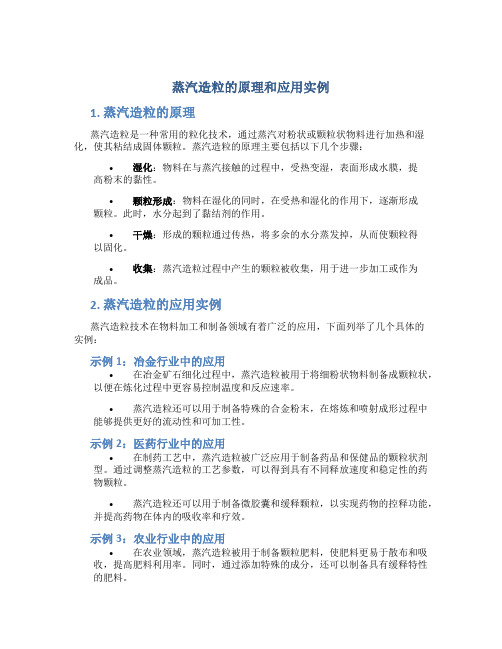
蒸汽造粒的原理和应用实例1. 蒸汽造粒的原理蒸汽造粒是一种常用的粒化技术,通过蒸汽对粉状或颗粒状物料进行加热和湿化,使其粘结成固体颗粒。
蒸汽造粒的原理主要包括以下几个步骤:•湿化:物料在与蒸汽接触的过程中,受热变湿,表面形成水膜,提高粉末的黏性。
•颗粒形成:物料在湿化的同时,在受热和湿化的作用下,逐渐形成颗粒。
此时,水分起到了黏结剂的作用。
•干燥:形成的颗粒通过传热,将多余的水分蒸发掉,从而使颗粒得以固化。
•收集:蒸汽造粒过程中产生的颗粒被收集,用于进一步加工或作为成品。
2. 蒸汽造粒的应用实例蒸汽造粒技术在物料加工和制备领域有着广泛的应用,下面列举了几个具体的实例:示例1:冶金行业中的应用•在冶金矿石细化过程中,蒸汽造粒被用于将细粉状物料制备成颗粒状,以便在炼化过程中更容易控制温度和反应速率。
•蒸汽造粒还可以用于制备特殊的合金粉末,在熔炼和喷射成形过程中能够提供更好的流动性和可加工性。
示例2:医药行业中的应用•在制药工艺中,蒸汽造粒被广泛应用于制备药品和保健品的颗粒状剂型。
通过调整蒸汽造粒的工艺参数,可以得到具有不同释放速度和稳定性的药物颗粒。
•蒸汽造粒还可以用于制备微胶囊和缓释颗粒,以实现药物的控释功能,并提高药物在体内的吸收率和疗效。
示例3:农业行业中的应用•在农业领域,蒸汽造粒被用于制备颗粒肥料,使肥料更易于散布和吸收,提高肥料利用率。
同时,通过添加特殊的成分,还可以制备具有缓释特性的肥料。
•蒸汽造粒还可以用于制备种子包衣剂,提高种子的出芽率和抗逆性,促进农作物的生长。
示例4:化工行业中的应用•在化工工艺中,蒸汽造粒被用于制备颗粒状的催化剂和吸附剂,以增加其表面积和反应速率,并提高催化剂的稳定性。
•蒸汽造粒还可以用于制备颗粒状的陶瓷和复合材料,以提高其力学性能和成型性能。
结论蒸汽造粒是一种常用的粒化技术,通过蒸汽对物料进行加热和湿化,使其形成颗粒。
蒸汽造粒的应用十分广泛,包括冶金、医药、农业和化工等行业,用于制备颗粒状的产品。
- 1、下载文档前请自行甄别文档内容的完整性,平台不提供额外的编辑、内容补充、找答案等附加服务。
- 2、"仅部分预览"的文档,不可在线预览部分如存在完整性等问题,可反馈申请退款(可完整预览的文档不适用该条件!)。
- 3、如文档侵犯您的权益,请联系客服反馈,我们会尽快为您处理(人工客服工作时间:9:00-18:30)。
近年来 , 德国学者在单板液压成 形的基础上 又提出 了 成 对 液压 成 形 技 术 l , 图 3所 示 。成 对 液 压 成 形 就 是 如 在 2块板料之间用一 隔板 把 2块板料相 互隔开 , 过中间 通
隔板 上 的 2 注 油通 道 分 别 向 上 下 2个 型腔 注 入 液 压 油 , 个 这 样 1 就 可成 形 1对零 件 , 次 不但 提 高 了生 产效 率 , 而且 上
中图 分 类号 :H1 T 6 文献标识码: A 文 章 编 号 : 0 0 0 (00 0 o 6 O 1 6~ 7 7 2 1 )4一 o4一 5 0
汽车轻量化是世界 汽车工业发展 的趋势。近几年来 , 国内各汽车企业 开始普 遍采用 高强 度钢板 。但 高强度钢 板在成形时较普通冷轧板更容易 开裂 和起皱 , 随着材料 且 强度 的提高 , 回弹量也 相应增 大。因此 , 这类 高强度 钢板 零 件的成 形对传 统 的板料 成形 方法提 出 了严 峻 的挑 战。 为此 , 研究者们提出了软模 成形技术 。软模成形 是指采用 某种材料代替 剐性 凸模或凹模作 为成形 的传力介质 , 再用
刚性模具作为凹模或 凸模 , 在传力 介质作用下使板材按 刚性模具形状成形的工艺。软模 成形包括 液压成形 、 橡胶
又称为反向压力成 形 ; 采用液体 代替 凸模时 , 液压 力以相
同于凸模作用力 的方 向作用在板料 的上表面 , 板材直接被 压 入 凹 模 , 紧 贴 凹 模 而 成 形 , 又 称 为 正 向 压 力 并 故
邹
强, : 等 固体 颗 粒介质 成 形技 术
6 5
一 屠
a 橡胶 作 为凹 模 ) b 橡 胶 作 为 凸模
1 料 ;2压 边 圈;3刚性 凸模 ;4 胶 ;5刚性 凹模 板 橡
I 边 圈 :2注 液 通 道 ; 3板 料 压 4液 压 油 : 5凹 模
图 4 橡 胶 成形 示意
成 形 一 。
成形 、 粘质成 形等 。这些 工艺 的出现 , 大大提 高 了板料 的
成 形性 能 , 进 了 板 料 成 形 技 术 的 发 展 , 亦 存 在 着 诸 多 促 但
的不足之处。如液压成 形过 程 中液 压油 的密封需 要严格 控制 , 一旦液压油 泄露将 污染环 境 ; 橡胶 的寿命较 短且在 模具 的圆角区域贴膜性差 ; 质介质 同样需要 良好的密封 粘 且成本较高等 …。这些 不足在某 种程度 上 限制 了该技 术
一
刚性的凹模或 凸模 , 使坯料在传 力介质 的压力作 用下贴合
凸模 或凹模成 形的工 艺 。板 材液压成 形按 照液体介 质 取代对象 的不 同又 可分 为 2类 : 液体 介质代 替 凹模 ( 称 又
反向压力成形 , 图 1 和液体 介质代替 凸模 ( 见 ) 又称正 向压 力成形 , 图 2 。采用液体代 替凹模时 , 见 ) 刚性 凸模 下行将 板材压人液压室 , 液压力以相对 于凸模作 用力方 向的反 向 压力作用在板料 的下表 面 , 使板料 紧贴 凸模而成 形 , 迫 故
下 2个零件 也不会发生干扰 , 特别适合 于摩 托车油箱等 型
腔 类 零 件 的成 形 。
能等 , 而且也克服 了液 压成形 、 粘质成 形过程 中要 求严格 密封和橡胶成形贴膜性差等缺 点。所 以, 固体颗粒 介质成
形 工 艺 在航 空 、 天 、 车 、 工 和机 械 等 板 料 冲压 方 面 有 航 汽 化
第3 1卷
第 4期
四 川 兵 工 学 报
21 O0年 4月
【 制造技术 】
固体 颗 粒 介 质 成 形 技 术 半
邹 强 , 彭成 允 , 平 , 田 李世 明
( 庆理 工 大 学 材料 科 学 与 工 程 学 院 , 庆 重 重 40 5 ) 0 00
摘要 : 介绍了传统软模成形工艺 , 为适应板料成形技术 的进一步发展 , 出了一种 固体颗 粒介 质成形技术。介绍 提 了其成形原理 、 成形特点 、 工艺参数对成形的影响 、 国内外 的研究现状 以及数值模拟方式等。 关键词: 软模成形 ; 固体颗粒介质成形 ; 数值模拟
l
作为压力传递介质 ( 作粘介质 ) 将其作用在板料 的 1 称 , 侧 时作用下成形的新技术 , 图 5所示 。 如
2
3 ห้องสมุดไป่ตู้
l板 料 A:2隔 板 :3板 料 B
图 3 板 料 成 对 液 压 成 形
与 传 统 刚性 模 相 比 , 压 成 形 有 如 下 特 点 : 因 板 液 ①
固体颗粒介质 成形是 在传统 软模成 形的基 础上提 出 的一种采用 固体颗粒介质代替刚性 凸模 ( 弹性体 、 或 液体 ) 的作用 , 而 实 现对 板 料进 行 成形 的新 型板 料 成 形 工 从
艺 j 。其不但继承 了软模 成形 的一 些优点 , 如能达到 比传
统板 料 成 形 方 法更 大 的成 形 极 限 , 分 发 掘板 料 的 成 形 性 充
l 2
3 t
着广泛的应用前景。
1 传统软模成形工艺
1 1 液 压 成 形 .
5 l凸模 ; 2压 边 圈 ; 3板 料 . 4液 压 室 :5凹 模 体
图 l 液 体代 替 凹模
液压成形是指 采用液 态 的水 、 油等作传 力介 质 , 替 代
收 稿 日期 :00一 1 0 21 O — 2 作者简介 : 邹强( 95 )男 , 18 一 , 硕士 , 主要从事板料成形工艺及模具研究。
图 2 液 压 代 替 凸模
13 粘 质 成 形 . 粘 性 介 质 压 力 成 形 ( i o spesr r n , P ) v cu rsuef mi V F 是 s o g
一
种采用半固态 、 具有一定粘 度和应 变速率敏感 性的物质 ( 一般为 凹模侧 ) 2侧 , 或 使板料在正 向压力 和反 向压力 同