ST_MTS-M_GIVI_ITA
SGS-THOMSON TODV 640 ---> 1240 数据手册

TODV 640--->1240March 1995ALTERNISTORSSymbol ParameterValue Unit I T(RMS)RMS on-state current (360°conduction angle)Tc =75°C40AI TSMNon repetitive surge peak on-state current (Tj initial =25°C )tp =2.5ms 590Atp =8.3ms 370tp =10ms350I 2t I 2t valuetp =10ms 610A 2s dI/dtCritical rate of rise of on-state currentGate supply :I G =500mA di G /dt =1A/µsRepetitive F =50Hz 20A/µsNon Repetitive100Tstg Tj Storage and operating junction temperature range-40to +150-40to +125°C °C TlMaximum lead temperature for soldering during 10s at 4.5mm from case260°CRD91(Plastic).HIGH COMMUTATION :>142A/ms (400Hz).INSULATING VOLTAGE =2500V (RMS)(UL RECOGNIZED :EB1734).HIGH VOLTAGE CAPABILITY :V DRM =1200VDESCRIPTIONSymbol ParameterTODVUnit64084010401240V DRM V RRMRepetitive peak off-state voltage Tj =125°C60080010001200VABSOLUTE RATINGS (limiting values)FEATURESThe TODV 640--->1240use a high performance passivated glass alternistor technology.Featuring very high commutation levels and high surge cur-rent capability,this family is well adapted to power control on inductive load (motor,transformer...)A 2GA 11/5查询TODV 640 ---> 1240供应商GATE CHARACTERISTICS (maximum values)Symbol ParameterValue Unit Rth (c-h)Contact (case-heatsink)with grease0.1°C/W Rth (j-c)DC Junction to case for DC1.2°C/W Rth (j-c)AC Junction to case for 360°conduction angle (F=50Hz)0.9°C/WSymbol Test ConditionsQuadrant Value Unit I GT V D =12V (DC)R L =33ΩTj=25°C I-II-III MAX 200mA V GT V D =12V(DC)R L =33ΩTj=25°C I-II-III MAX 1.5V V GD V D =V DRM R L =3.3k ΩTj=125°C I-II-III MIN 0.2V tgt V D =V DRM I G =500mA dI G /dt =3A/µs Tj=25°C I-II-III TYP 2.5µs I LI G =1.2I GTTj=25°CI-III TYP100mAII200I H *I T =500mA gate open Tj=25°C TYP 50mA V TM *I TM =60A tp=380µs Tj=25°C MAX 1.8V I DRM I RRM V DRM Rated V RRMRatedTj=25°C MAX 0.02mA Tj=125°C MAX 8dV/dt *Linear slope up to V D =67%V DRM gate open Tj=125°CMIN 500V/µs (dI/dt)c *(dV/dt)c =200V/µs Tj=125°C MIN 35A/ms(dV/dt)c =10V/µs142*For either polarity of electrode A 2voltage with reference to electrode A 1.P G (AV)=1WP GM =40W (tp =20µs)I GM =8A (tp =20µs)V GM =16V (tp =20µs).ELECTRICAL CHARACTERISTICSTHERMAL RESISTANCESTODV 640--->12402/5Fig.1:Maximum RMS power dissipation versus RMS on-state current (F=50Hz).(Curves are cut off by (dI/dt)c limitation)Fig.2:Correlation between maximum RMS power dissipation and maximum allowable temperatures (T amb and T case )for different thermal resistances heatsink +contact.Fig.3:RMS on-state current versus case temperature.tp(s)1E-31E-21E-11E+01E+10.010.11Zth(j-c)/Rth(j-c)Fig.4:Relative variation of thermal impedance junction to case versus pulse duration.Fig.5:Relative variation of gate trigger current and holding current versus junction temperature.Fig.6:Non Repetitive surge peak on-state current versus number of cycles.TODV 640--->12403/5TODV640--->1240Fig.7:Non repetitive surge peak on-state current for aFig.8:On-state characteristics(maximum values). sinusoidal pulse with width:t≤10ms,andcorresponding value of I2t.Fig.9:Safe operating area.4/5PACKAGE MECHANICAL DATA RD91PlasticMarking :type number Weight :20gAa1a2Bd1b2C c1c2EFILIL2N1N2REF.DIMENSIONSMillimetersInches Min.Max.Min.Max.A40.001.575a129.9030.30 1.1771.193a222.000.867B 27.001.063b113.5016.500.5310.650b224.000.945C 14.000.551c1 3.500.138c2 1.95 3.000.0770.118E0.700.900.0270.035F 4.00 4.500.1570.177I 11.2013.600.4410.535L1 3.10 3.500.1220.138L2 1.70 1.900.0670.075N133°43°33°43°N228°38°28°38°Information furnished is believed to be accurate and reliable.However,SGS-THOMSON Microelectronics assumes no responsability for the consequences of use of such information nor for any infringement of patents or other rights of third parties which may result from its use.No license is granted by implication or otherwise under any patent or patent rights of SGS-THOMSON Microelectronics.Specifications mentioned in this publication are subject to change without notice.This publication supersedes and replaces all information previously supplied.SGS-THOMSON Microelectronics products are not authorized for use as critical components in life support devices or systems without express written approval of SGS-THOMSON Microelectronics.©1995SGS-THOMSON Microelectronics -Printed in Italy -All rights reserved.SGS-THOMSON Microelectronics GROUP OF COMPANIESAustralia -Brazil -France -Germany -Hong Kong -Italy -Japan -Korea -Malaysia -Malta -Morocco -The Nether-lands -Singapore -Spain -Sweden -Switzerland -Taiwan -Thailand -United Kingdom -U.S.A.TODV 640--->12405/5。
TEMI S1使用手册说明书

TEMI S1 使用手册该使用手册基于Launcher 系统:16056-chinaTencent ROBOX 系统:127.28 使用目录安全 (4)介绍temi (6)temi是什么? (6)包装箱内有什么? (7)temi的组件 (8)开始使用 (10)temi的开箱 (10)设置充电桩 (11)启动和关闭temi (12)电源管理 (13)temi移动应用程序 (14)同步和邀请联系人 (14)激活temi (15)用户管理 (16)最新活动 (17)我的temi (17)与temi交流 (18)联系人和最近通话 (18)视频电话:手机APP端操作 (19)视频电话:temi机器人操作 (20)跟随模式 (21)托盘 (23)音量控制 (23)基本使用说明 (23)设置菜单 (24)地图功能 (28)在机器人上操作指南 (28)地图菜单功能 (30)在手机APP上操作指南 (32)软件更新 (33)temi的内置技能 (34)正确和错误使用temi的举例 (39)安全为降低伤害或损坏风险,请在安装、使用和维护机器人前阅读以下安全注意事项。
不正确地操作本产品可能会导致人身伤害或物理损伤。
对于因误操作而导致的任何损坏,制造商不承担任何超出本产品使用手册中定义之正常使用范围的责任。
适用环境•请将temi置于室内干燥地面。
•temi的适用工作温度范围为0ºC至40ºC,超出此范围的操作将会导致产品损坏。
•请勿在存有易燃气体或烟雾的情况下操作本产品,在这样的环境中操作任何电子仪器均会构成一定的安全隐患。
使用•请小心使用temi,操作时请勿施加任何物理压力或冲击力。
•避免将手指放在活动部件附近,例如temi的颈部、激光雷达或轮子。
•不适合5岁以下的儿童单独使用。
保养•请勿用湿手接触temi或其底座,也勿溅上任何液体。
•如需清洁temi,请使用干净的无绒布擦拭,切勿使用液体喷洒或冲洗temi,同时避免使用清洁剂。
维亚维解决方案:T-BERD MTS-5800多技术测试手持设备说明书

BrochureVIAVI T-BERD/MTS-5800All-in-one handheld network and fiber testingThe T-BERD®/MTS-5800 handheld network tester is the one tool that network technicians and engineers need to install, turn-up, and maintain their networks. It supports both the legacy and emerging technologies required to handle various network applications including metro/core, mobile backhaul, and business services installations.Key Benefitsy Simplifies multitechnology testing with an all-in-one dual-10 G handheldy Optimized for field use with a multitouch screen, scripted workflows, and clear resultsy Supports efficient best practices with repeatable methods and procedures with Job Manager guided workflows y Speeds fiber characterization, Ethernet service activation, and troubleshootingKey Featuresy Fully-loaded TDM/PDH to dual 10 G Ethernet, SONET , SDH, Fiber Channel, CPRI/OBSAI, eCPRI, and OTN supporty Automated, enhanced RFC 2544 and SAMComplete testing per ITU-T Y .1564y Integrated burst testing approach per MEF 34 and RFC 6349 TrueSpeed™ TCP throughput testingy Timing/Synchronization testing with PTP , SyncE, and 1 PPS, 2 MHz and 10 MHz Wandery Compatible with VIAVI 4100-Series OTDR, FiberComplete, and COSA modules with Smart Link Mapper™, fiber microscopes, and optical power metersApplicationsy Mobile and backhaul characterization, validation, and troubleshootingy Converged Ethernet/IP network testing and troubleshooting at 10 Mbps to 10 G interfacesy Fiber link characterization and troubleshootingy Installation and maintenance of OTN and legacy SONET/SDH and TDM/PDH networksy Remote radio head (RRH) testing at the wireless basestation, including CPRI 1-9 ratesThe industry’s smallest handheld instrument can test throughout the service life cycle, including fiber characterization, service activation, troubleshooting, and maintenance. Advanced Ethernet test features such as TrueSpeed per RFC 6349, J-Profiler™, Wirespeed capture/decode, and automated J-Mentor, help field technicians test their networks faster and more accurately than ever before.y All test interfaces are readily availabley Compact form factor for easy portability:7 x 9.5 x 3 in (17.8 x 24.1 x 7.62 cm)y Large 7 in multi-touch displayy T ablet-like interface for easy navigation through test informationand advanced workflowsCompatible with VIAVI Solutions Fiber Test ToolsMobility, business services, and metro technicians can now test virtually any interface in their network as well as qualify fiber plant with one ultra-portable instrument. The T-BERD/MTS-5800 is compatible with:y The P5000i fiber microscope for connector end-face inspection and analysisy MP-Series optical power meters for optical power and loss measurementsy OTDR modules for fiber link characterization and fault findingy Smart Link Mapper optical analysis software that displays OTDR results in a simple, icon-based map view for clear diagnostics of detected issuesOptimized for Easy Field Usey Fixed test interfaces eliminate loose pluggable modules y LEDs indicate plug-ins for testsy A streamlined user interface provides simple pass/fail, green/red resultsy Extended battery life enables longer test times y Boots up rapidly from power-on to test starty Dual-port operation runs two tests simultaneously , including10 G/high-speed testsLow-speed electricalT1, PRI, E1External BITS clockinputHigh-speed electrical T3, STS1, E3, E4, STM-1eDual RJ45 ports 10/100/1000 EthernetDual SFP+ ports; 1 and 10 G Ethernet LAN/WAN; 10GE eCPRISTM-1-64, OC3-192; OTN OTU 1, 2 OTU1e, 2eFiber Channel: 1/2/4/8/10/16 G FC CPRI/OBSAI 614 Mbps – 12.2 GbpsTest every interface in your network!Compatible with VIAVI FiberScopeTrueSAM Saves Valuable Service Activation TimeT est better and quicker with automated tests combined into one ultimate installation tool: y J-QuickCheck — a fast, automated test (RFC 2544, Y .1564) for validating end-to-end and auto-negotiation configuration ykey performance indicators (KPIs)/concurrently measuring SLAssuch as throughput, frame delay committed burst size (CBS) — optionalyY .1564 SAMComplete — an automated service verification testthat speeds the installation of multiple classes of services (COS) y TrueSpeed per RFC 6349 — an automated, standards-basedtest that can save up to 25% of operating expenses (OpEx) and reveals the reason for slow file downloads, eliminating finger-pointingy Interoperable with TrueSpeed VNF and QT-600 to speed testingReduce Mean Time to Repair for Network ProblemsReduce CapEx/OpEx while immediately identifying problems with automated tests — without the need for a field expert or a separate analyzer.y Network discovery automatically identifies equipment present on the network y J-Profiler discovers live traffic streams for real-time troubleshooting with in-service top-talkers analysisy Integrated capture/decode offers 10 G line-rate packet capture and analysis in a handheld y J-Mentor provides expert troubleshooting guidance and interprets packet decodesEnhanced RFC 2544 with J-QuickCheck SAMComplete per ITU-T Y .1564TrueSpeed per RFC 6349J-Mentor provides expert troubleshooting guidanceEnables Network Evolution — Today and TomorrowThe 5800 meets leading-edge, carrier-grade Ethernet requirements:y Ensures reliability with link and service OAM (IEEE 802.3ah, 802.1ag, and ITU-T Y .1731)y Validates network scalability with VLAN, Q-in-Q, MAC-in-MAC Ethernet-over-Ethernet, MPLS, and VPLS tunnelling technologies.y Support for ODU multiplexing including ODU1, ODU0, and ODUflexy T est emerging 5G technology with eCPRI specific testing including One-Way-Delay (OWD) y Full-featured VoIP and IP video turn-up and troubleshooting testsy Supports packet transport network (PTN) evolution with MPLS-TP technology y Ethernet Service Disruption with multi-tier triggersy Run Bi-Directional Forwarding Detection (BFD) against switch and router partners while generating traffic to measure KPIsEmpower Cell-Site Technicians - Fiber testing to CPRI and eCPRIT-BERD/MTS-5800 tools let cell-site technicians efficiently install and maintain backhaul and fronthaul networks. They can ensure BBU and RRH connectivity with CPRI and OBSAI tests: y Validate C-RAN connectivity across CWDM networksy T est RRH health from the bottom of the tower or from a C-RAN location by emulating a BBUy Identity PIM and interference issues from an optical test access point including quad spectrum with enhanced markers.(RFoCPRI) y Support 2-T one PIM generation enabling PIM detection without climbing a towery Bit Error Rate T est eCPRI fronthaul circuitsy Validate RJ-45 Ethernet wiring is properly crimped down and wire mapped including end-to-end shield ground connectivity y CPRI Check automates setting Antenna Tilt, detecting PIM and reading VSWRAnd, they can verify network synchronization:y Emulate a 1588v2 master clock/slave recovery for proper point-to-point (PTP) message propagation and packet-delay variation (PDV) verificationy Verify SyncE frequency synchronization accuracy and Ethernet synchronization message channel (ESMC) message propagationTest the RRH herewith CPRIDon’t climb hereCommon Application BaseSame user interface + same results + same methods and proceduresActivate services more quickly and accuratelyReduce mean time to repair (MTTR) on network problems T est the widest range of traditional and emerging telecom interfacesPart of the Leading T-BERD/MTS Test Portfolio StrataSyncEmpower Y our AssetsStrataSync is a hosted, cloud-enabled solution for managing assets, configurations, and test data on VIAVI instruments. It ensures that all instrument software is current and the latest options are installed. StrataSync lets you manage inventory , test results, and performance data anywhere with browser-based ease while it also improves technician and instrument efficiency. StrataSync manages and tracks test instruments, collects andanalyzes results from the entire network, and it informs and trains the workforce.y Measure wander on SyncE, 1PPS, T1, E1, and 2 and 10 MHz signals y T est Floor Packet Percentile per ITU PTP Frequency recommendationsWhen equipped with an OTDR module, the T-BERD/MTS-5800 is the perfect solution for mobile network testing, providing easy fiber link characterization and troubleshooting.© 2020 VIAVI Solutions Inc.Product specifications and descriptions in this document are subject to change without notice.5800-gov-br-tfs-tm-ae 30191085 910 0120Contact Us +1 844 GO VIAVI (+1 844 468 4284)To reach the VIAVI office nearest you, visit /contact.。
VIAVI T-BERD MTS-5800 端到端测试指南说明书
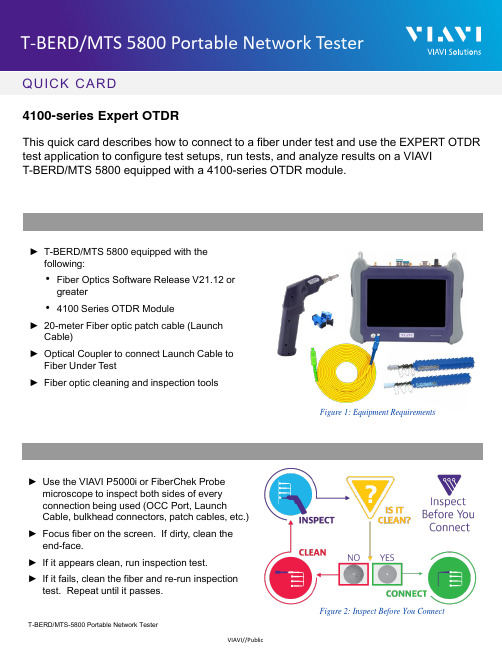
QUICK CARD►Use the VIAVI P5000i or FiberChek Probe microscope to inspect both sides of every connection being used (OCC Port, Launch Cable, bulkhead connectors, patch cables, etc.)►Focus fiber on the screen. If dirty, clean the end-face.►If it appears clean, run inspection test.►If it fails, clean the fiber and re-run inspection test. Repeat until it passes.Figure 2: Inspect Before You ConnectFigure 1: Equipment Requirements4100-series Expert OTDRThis quick card describes how to connect to a fiber under test and use the EXPERT OTDR test application to configure test setups, run tests, and analyze results on a VIAVI T-BERD/MTS 5800 equipped with a 4100-series OTDR module.►T-BERD/MTS 5800 equipped with the following:•Fiber Optics Software Release V21.12 or greater•4100 Series OTDR Module►20-meter Fiber optic patch cable (Launch Cable)►Optical Coupler to connect Launch Cable to Fiber Under Test ►Fiber optic cleaning and inspection toolsQUICK CARDAll fibers and connectors should be inspected and clean prior to connection, as described on page 1. The OTDR may be connected to the FUT via an optical patch panel (OPP) or a coupler:1.Inspect the OTDR port on top of the test set.2.Inspect the fiber end face of the Launch Cable.3.Connect the Launch Cable to the OTDR port.4.If the interface to the FUT is a patch cord, connect the patch cord to an optical coupler.5.Inspect the FUT connected to the coupler or OPP port and the fiber end face of the Launch Cable.6.Connect the Launch Cable to the coupler or OPP port.Figure 5: Connecting to OPP1.Press the Power button to start the test instrument.2.Tap the Fiber Optics iconin the Status Bar at the top of the screen.3.If a purple symbol is displayed on the left screen side, tap it to display the Fiber Optics home screen.4.Tap the EXPERT OTDR icon until it is yellow and highlighted.Figure 6: Fiber Optics Home ScreenFigure 4: Connecting to couplerFigure 3: OTDR Port InspectionQUICK CARD1.Tap the Setup soft key .2.Tap Acquisition and configure the followingbasic settings for the trace:➢Laser:Choose the wavelength(s) to test.➢Acquisition Mode:o Select Manual to manually to enterRange and Pulse width settings.o Select Auto to automatically configure Range, Pulse width, and SmartAcqsettings.o Select SmartAcq to perform anacquisition with a short pulse width,followed by an acquisition with a longerpulse width. The first acquisition allowsevents at the beginning of the fiber to bedetected more precisely.➢Acq. Time:Select Realtime, Auto or the desired time to sample the fiber.➢Launch Cable: Select and enter Length if you are using a Launch Cable.Enter 20 meters or 66 feet for Viavi supplied20-meter launch cables.3.Tap Alarms and configure pass/fail criteria:➢Set Alarm Level to Fail.➢Set Threshold to Default, or select alternate alarm thresholds (TIA-568.3, User, etc.)4.Tap Display and set Distance Unit to yourdesired unit of measure.Figure 7: Acquisition settings Figure 8: Alarm Settings Figure 9: Display settingsQUICK CARD1.Tap the Start soft-key to start the test. After auto-configuration, the OTDR will perform a connection check to ensure that theconnection is Good . If the Connection is Bad , disconnect the launch cable, and reconnect as described on pages 1 and 2, cleaning every fiber end-face that fails the inspection test. 2.After connection checks, the OTDR will perform acquisitions at the configured wavelengths. 3.Tap the SmartLink tab at the left screen top to select SmartLink view.4.Set the toggle switch at the right screen top to Event Line .5.View SmartLink results:►The FUT is displayed as a series of icons representing events (front connector,launch cable, connectors, splices, bends, etc.) and distances. Swipe left or right to view additional icons on spans with more than 4 events.►The center of the display shows summary results for the entire span for eachacquisition or wavelength. Tap any event in the upper display to view detailed results for that specific event.►Events and Acquisitions are marked with a green check or red x based on the Alarms setting.Note:the icon-based view may not beavailable on older T-BERD/MTS 5800s when acquisition Mode = SmartAcq. Rerun the test with Manual or AutoAcquisition or contact VIAVI to upgrade your unit to add this feature.Figure 11: SmartLink View, Summary ResultsFigure 12: SmartLink View, Event ResultsFigure 10: Start TestQUICK CARD6.Tap the Trace tab at the left screen top to select Trace view .7.Set the toggle switch at the screen top to Info .8.Tap the magnifying glass icons to zoom in , zoom out , or auto-zoom the display. You can also pinch and zoom with your fingers.9.View trace results:►Trace information is shown in the upperdisplay. Tap 1 or 2 to select the acquisition (wavelength or pulse width) for results display.►Graphical results (dB versus distance) areshown in the center display.► A color-coded Event table is shown in thelower display. Swipe up and down to view all events. 10.Tap the Table tab to select Table view . 11.Set the toggle switch at the right screen top to the center (off) position.12.View table results:►Distance, Loss, and Reflectance are shownfor each event.►Tap the toggle switch to view All events or Failed events.Figure 13: Trace viewFigure 14: Table viewQUICK CARD© 2021 VIAVI Solutions, Inc,Product specifications and descriptions in this Contact Us+1 844 GO VIAVI(+1 844 468-4284)1.Tap the Fast Report soft key .2.Enter Job Id , Cable ID , Fiber Number , Locations , and Direction .►The Job Id field identifies the Job and creates a folder by the same name. Results are saved to this folder.►The Cable Id, Fiber Id, and Fiber Number fields determine the file name.3.Set Dir. Naming to disk/[Job_Id]. Use the abc/[auto] button to toggle between test entry and field entry,4.Set Save Mode to pdf .5.Tap Save .6.Tap to accept the default filename and save test results.7.Tap the Fast Report soft key again to return to the results display.8.Tap to return to the OTDR Home screen.Figure 17: Fast ReportFigure 16: Directory NamingFigure 15: Report Settings。
罗克韦尔自动化 2198-IM005 安装说明书 基尼克斯5300单轴以太网 IP伺服驱动器

Installation InstructionsOriginal InstructionsKinetix 5300 Single-axis EtherNet/IP Servo DrivesCatalog Numbers 2198-C1004-ERS, 2198-C1007-ERS, 2198-C1015-ERS, 2198-C1020-ERS, 2198-C2030-ERS, 2198-C2055-ERS, 2198-C2075-ERS, 2198-C4004-ERS, 2198-C4007-ERS, 2198-C4015-ERS, 2198-C4020-ERS, 2198-C4030-ERS, 2198-C4055-ERS, 2198-C4075-ERSSummary of ChangesThis publication contains new and updated information as indicated in the following table.About the Kinetix 5300 DrivesKinetix 5300 servo drives provide an Integrated Motion over the EtherNet/IP network solution for applications with continuous 3-phase output power and current requirements in the range of 0.72…14.7 kW and 2.3…67.5A 0-pk, respectively.See the Kinetix 5300 Servo Drives User Manual, publication 2198-UM005, for detailed information on wiring, applying power, troubleshooting, and integration with ControlLogix®5570, ControlLogix 5580, CompactLogix™ 5370, or CompactLogix 5380 controllers, and Studio 5000 Logix Designer® application.TopicPage Summary of Changes 1About the Kinetix 5300 Drives 1Before You Begin 3Mount the Kinetix 5300 Drive 3Connector Data 5Wiring Requirements8Attach the Motor Cable Shield Clamp 10Circuit Breaker/Fuse Selection 12Motor Overload Protection 14Additional Resources14TopicPage Added 140UT circuit breakers12 (14)Kinetix 5300 Single-axis EtherNet/IP Servo Drives Installation InstructionsCatalog Number ExplanationThis publication applies to the following Kinetix 5300 servo drives. Kinetix 5300 Drive Catalog NumbersCat. No.Frame Size Input Voltage(1)(1)Nominal input voltage rating (110, 230, or 480V rms) is required to achieve full power.Continuous Output PowerkWContinuous Output CurrentA (rms)Continuous Output CurrentA (0-pk)2198-C1004-ERS185…132V rms single-phase170…253V rms single-phase170…253V rms three-phase 0.220.460.722.8 4.02198-C1007-ERS10.360.761.184.6 6.52198-C1015-ERS20.671.412.188.512.02198-C1020-ERS20.972.023.1312.217.32198-C2030-ERS2170…253V rms three-phase 5.0219.627.72198-C2055-ERS310.3040.256.9 2198-C2075-ERS312.2247.767.52198-C4004-ERS1342…528V rms three-phase 0.86 1.6 2.32198-C4007-ERS1 1.55 2.9 4.1 2198-C4015-ERS2 2.78 5.27.4 2198-C4020-ERS2 3.907.310.3 2198-C4030-ERS2 6.2511.716.5 2198-C4055-ERS312.0822.632.0 2198-C4075-ERS314.7027.538.92Rockwell Automation Publication 2198-IN021B-EN-P - July 2022Rockwell Automation Publication 2198-IN021B-EN-P - July 20223Kinetix 5300 Single-axis EtherNet/IP Servo Drives Installation InstructionsBefore You BeginRemove all packing material, wedges, and braces from within and around the components. After unpacking, check the item nameplate catalog number against the purchase order.The Kinetix 5300 servo drives include the following:•Wiring-plug connector set for AC input power, 24V control input power, digital inputs/auxiliary feedback, motor power, motor brake, shunt (installed and wired to the internal shunt), and safe torque-off (STO) connector. Spare shunt wiring plug for optional external shunt.•Clamp spacer for motor shield clamp•The frame 3 clamping plate, for cables too large to fit within the standard shield clamp •These installation instructions, publication 2198-IN021Mount the Kinetix 5300 DriveFollow these steps to mount the drive in single-axis configurations.1.Observe these clearance requirements when mounting a single drive to the panel:•Additional clearance is required for cables and wires connected to the top of the drive.•Additional clearance is required if other devices are installed above and/or below the drive and have clearance requirements of their own.•Additional clearance left and right of the drive is required when mounted adjacent to noise sensitive equipment or clean wire ways.•The recommended minimum cabinet depth is 300 mm (11.81 in.).Drives can be spaced by aligning the zero-stack tab and cutout. For the zero-stack feature to engage properly (when more than one frame size exists in the drive system) frame 3 drives must mount left of frame 1 or 2 drives, and frame 2 drives must mount left of frame 1 drives. For additional mounting and 24V shared-bus information, refer to the Kinetix 5300 Servo Drives User Manual, publication 2198-UM005.2.Mount the Kinetix 5300 drive to the cabinet subpanel with M4 (#8-32) steel machine screws torqued to 2.0 N•m (17.7 lb•in) max.Replacement connector sets are also available. See the Kinetix 5700, 5500, 5300, and 5100 Servo Drives Specifications, publication KNX-TD003, for more information.IMPORTANTMount the drive in an upright position as shown to provide proper air flow. Do not mount the drive on its side. Mount drives in descending order, left to right, according to frame size.Clearance left of the drive is not required.40 mm (1.57 in.) clearance belowdrive for airflow40 mm (1.57 in.) clearance abovedrive for airflowTechnical Data, publication KNX-TD003, for Kinetix 5300 drive dimensions.Zero-stack Tab and Cutout AlignedMount drives in descending order, left to right, according to frame size.The optional 24V shared-bus connection system is not shown for clarity.4Rockwell Automation Publication 2198-IN021B-EN-P - July 2022Kinetix 5300 Single-axis EtherNet/IP Servo Drives Installation InstructionsProduct DimensionsIncluded in this figure are the drill hole patterns for standalone drives. Refer to the Kinetix 5300 Servo Drives User Manual, publication 2198-UM005, for multi-axis drill-hole patterns.Kinetix 5300 Drives with 2198-K53CK-D15M Connector KitKinetix 5300 Drives with 2198-K53CK-D15M Connector KitRefer to Kinetix Servo Drives Technical Data, publication KNX-TD003, for motor/actuator compatibility with the 2198-K53CK-D15M connector kit and product dimensions.Kinetix 5300 Drive Cat. No.FrameA mm (in.)B mm (in.)C mm (in.)D mm (in.)E mm (in.)Drill Hole Patterns (1)(1)Hole spacing is measured in millimeters and not converted to inches to avoid errors due to rounding.F mmG mm2198-C1004-ERS 150 (1.97)175 (6.89)204 (8.03)265 (10.43)215 (8.46)193.68 4.512198-C1007-ERS 2198-C4004-ERS 2198-C4007-ERS 2198-C1015-ERS 255 (2.16)225 (8.86)265 (10.43)243.84 5.002198-C1020-ERS 2198-C2030-ERS 2198-C4015-ERS 2198-C4020-ERS 2198-C4030-ERS 2198-C2055-ERS 385.2 (3.35)250 (9.84)294 (11.57)273.700.02198-C2075-ERS 2198-C4055-ERS 2198-C4075-ERSDimensions are in mm2198-C1004-ERS Drive is ShownHole spacing is measured in millimeters and not converted to inches to avoiderrors due to rounding.65.0(2.56)Rockwell Automation Publication 2198-IN021B-EN-P - July 20225Kinetix 5300 Single-axis EtherNet/IP Servo Drives Installation InstructionsConnector DataUse these illustrations to identify the Kinetix 5300 drive features and indicators.Kinetix 5300 Drive Features and IndicatorsThese procedures assume that you have prepared your panel and understand how to bond your system. For installation instructions regarding equipment and accessories not included here, refer to the instructions that came with those products.Kinetix 5300 Drive ConnectorsItem DescriptionItem DescriptionItem Description 1Motor cable shield clamp 7Zero-stack mounting tab/cutout 13Motor brake connector 2Motor feedback (MFB) connector 8Four-character status display 14Ground terminal 3Digital inputs and auxiliary feedback connector9Navigation pushbuttons 15Shunt resistor connector 4Ethernet (PORT1) RJ45 connector 10Link speed status indicators 16AC input power connector 5Ethernet (PORT2) RJ45 connector 11Link/Activity status indicators 1724V control input power connector 6Module and Network status indicators12Motor power connector18Safe torque-off (STO) connectorSHOCK HAZARD: To avoid hazard of electrical shock, perform all mounting and wiring of the Kinetix 5300 drive prior to applying power. Once power is applied, connector terminals can have voltage present even when not in use.ATTENTION: Plan the installation of your system so that you can perform all cutting, drilling, tapping, and welding with the system removed from the enclosure. Because the system is of the open type construction, be careful to keep any metal debris from falling into it. Metal debris or other foreign matter can become lodged in the circuitry and result in damage to components.Description ConnectorDescription Connector AC input power 4-position plug, terminal screws Motor feedback (MFB)15-position plug24V control input power 2-position plug, terminal screws Brake power (MBRK)2-position plug, terminal screwsShunt power 2-position plug, terminal screws Digital inputs / Auxiliary feedback 20-position plug, spring terminalsMotor power4-position plug, terminal screwsSafe torque-off (STO)10-position plugs, spring terminals, 2x (2 rows of 5 pins)Ethernet communication portsRJ45 Ethernet18171615123114567Cooling Fan6Rockwell Automation Publication 2198-IN021B-EN-P - July 2022Kinetix 5300 Single-axis EtherNet/IP Servo Drives Installation Instructions Main Input Power ConnectorShunt Power Connector PinoutControl Input Power Connector PinoutMotor Power Connector PinoutMotor Feedback (MFB) Connector PinoutMotor Brake (MBRK) Connector PinoutPin DescriptionSignal –Shunt connections DC+–SHPin DescriptionSignal 124V power supply, customer-supplied 24V+224V common24V-MFB Pin Description Signal MFB Pin Description Signal1Sine differential input +A differential input +MTR_SIN+MTR_AM+9Reserved–2Sine differential input –A differential input –MTR_SIN–MTR_AM–10Data differential input/output –Index differential input –MTR_DATA–MTR_IM–3Cosine differential input +B differential input +MTR_COS+MTR_BM+11Motor thermostat (normally closed) (1) (1)Not applicable unless motor has integrated thermal protection.MTR_TS 4Cosine differential input –B differential input –MTR_COS–MTR_BM–12Hall commutation S1 input MTR_S15Data differential input/output +Index differential input +MTR_DATA+MTR_IM+13Hall commutation S2 input MTR_S26Encoder common MTR_ECOM 14Encoder 5V power output MTR_EPWR5V (2)(2)Determine which power supply your encoder requires and connect to only the specified supply. Do not make connections to both supplies.7Encoder 9V power output MTR_EPWR9V (2)15Reserved–8Hall commutation S3 inputMTR_S3MBRK PinDescriptionSignal 1Motor brake connections MBRK+2MBRK-L3L2L121U V WPin 11Pin 6Pin 15Pin 1Pin 10Pin 521Rockwell Automation Publication 2198-IN021B-EN-P - July 20227Kinetix 5300 Single-axis EtherNet/IP Servo Drives Installation InstructionsDigital Inputs and Auxiliary Feedback Connector PinoutSafe Torque-off (STO) Connector PinoutThe 2198-C xxxx -ERS drives ship with the safe torque-off function enabled. Connect the safe torque-off inputs to a safety circuit or install bypass wiring to enable motion. Refer to the Kinetix 5300 Servo Drives User Manual, publication 2198-UM005, for more information.Ethernet Communication PORT1 and PORT2 PinoutPin DescriptionSignalPin DescriptionSignal124V current-sinking fast input #1IN11124V current-sinking fast input #3IN32I/O common for customer-supplied 24V supply COM 12I/O common for customer-supplied 24V supply COM 324V current-sinking fast input #2IN21324V current-sinking fast input #4IN44I/O common for customer-supplied 24V supply COM 14I/O common for customer-supplied 24V supply COM 5I/O cable shield termination point SHLD 15I/O cable shield termination point SHLD 6Channel AM Differential Input +AM+16Channel AM Differential Input –AM–7Channel BM Differential Input +BM+17Channel BM Differential Input –BM–8Channel IM Differential Input +IM+18Channel IM Differential Input –IM–9Encoder 5V power outputEPWR_5V 19Auxiliary commonAUX_COM 10Auxiliary feedback cable shield termination pointSHLD 20Auxiliary feedback cable shield termination pointSHLD STO Pin (1)(1)STO is enabled by default, with no terminations. Refer to the Kinetix 5300 Servo Drives User Manual, publication 2198-UM005, to wire safe torque off bypass jumper or to wire to the upstream relay as required.DescriptionSignal 1 / 6Safety bypass plus signal. Connect to both safety inputs to disable the STO function SB+2 / 7Safety bypass minus signal. Connect to safety common to disable the STO function SB-3 / 8STO input 1 (SS_IN_CH0)S14 / 9STO input common (SCOM)SC 5 / 10STO input 2 (SS_IN_CH1)S2Port Pin DescriptionSignal 1Transmit port (+) data terminal TD+ 2Transmit port (–) data terminal TD– 3Receive port (+) data terminal RD+ 4––5––6Receive port (–) data terminal RD– 7––8––1011120156SB+SB-S1SC S210SB+SB-S1SC S2Standard RJ4518Kinetix 5300 Single-axis EtherNet/IP Servo Drives Installation InstructionsWiring RequirementsWire must be copper with 75 ︒C (167 ︒F) minimum rating. Phasing of AC input power is arbitrary and earth ground connection is required for safe and proper operation. Refer to Kinetix 5300 Single-axis EtherNet/IP Servo Drives User Manual, publication 2198-UM005, for interconnect diagrams.IMPORTANTThe National Electrical Code and local electrical codes take precedence over the values and methods provided.ATTENTION: To avoid personal injury and/or equipment damage, observe the following:•Make sure installation complies with specifications regarding wire types, conductor sizes, branch circuit protection, and disconnect devices. The National Electrical Code (NEC) and local codes outline provisions for safely installing electrical equipment.•Use motor power connectors only for connection purposes. Do not use them to turn the unit on and off.•Ground shielded power cables to prevent potentially high voltages on the shield.Kinetix 5300 Drive Power and I/O Wiring Requirements8Rockwell Automation Publication 2198-IN021B-EN-P - July 2022Rockwell Automation Publication 2198-IN021B-EN-P - July 20229Kinetix 5300 Single-axis EtherNet/IP Servo Drives Installation InstructionsSee Kinetix Rotary and Linear Motion Cable Specifications Technical Data, publication KNX-TD004, for cable specifications.2198-C1004-ERS 2198-C1007-ERS 2198-C1015-ERS 2198-C1020-ERS 2198-C2030-ERS 2198-C2055-ERS 2198-C2075-ERS 2198-C4004-ERS 2198-C4007-ERS 2198-C4015-ERS 2198-C4020-ERS 2198-C4030-ERS 2198-C4055-ERS 2198-C4075-ERSPELV 24V power (2)(single-axis connector)1224V+24V-0.2…2.5(24…12)7.0 (0.28)0.5…0.6(4.4…5.3)Brake power 12MBRK+MBRK-0.14…1.5 (28…16) (3)0.22…0.25(1.9…2.2)Shunt resistor—DC+SH 0.2…2.5(24…12)8.0 (0.31)0.5…0.6(4.4…5.3)Safety ST0-1/6ST0-2/7ST0-3/8ST0-4/9ST0-5/10SB+SB-S1SC S20.2…1.5(24…16)10.0 (0.39)N/A (4)Digital inputs and Auxiliary feedback 1234567891011121314151617181920IN1COM IN2COM SHLD AUX_AM+AUX_BM+AUX_IM+Reserved SHLD IN3COM IN4COM SHLD AUX_AM-AUX_BM-AUX_IM-EPWR_5V SHLD0.2…1.5(24…16)10.0 (0.39)N/A (4)(1)For 10 AWG conductors, use 0.7…0.8 N•m (6.2…7.1 lb•in) of torque.(2)The wire size, strip length, and torque specifications shown here apply to the single-axis connector that ships with the drive. For the shared-bus connector specifications, refer to the Kinetix 5300 Servo Drives User Manual, publication 2198-UM005.(3)Motor brake wires are part of the Kinetix 2090 motor cable.(4)This connector uses spring tension to hold wires in place.Kinetix 5300 Drive Power and I/O Wiring RequirementsKinetix 5300 Drive Cat. No.Description Connects to Terminals Wire Size mm 2 (AWG)Strip Length mm (in.)Torque Value N•m (lb•in)PinSignal10Rockwell Automation Publication 2198-IN021B-EN-P - July 2022Kinetix 5300 Single-axis EtherNet/IP Servo Drives Installation InstructionsAttach the Motor Cable Shield ClampA shield clamp and two screws are supplied with each Kinetix 5300 drive. Use the clamp to bond the motor cable shield-braid to chassis ground.Allen-Bradley Motors and ActuatorsA clamp spacer is included with the drive for motor power/brake cable diameters that are too small for a tight fit within the drive clamp alone. A clamping plate is provided with frame 3 drives for cables too large to fit within the standard shield clamp.Cable Clamp AttachmentRefer to the Kinetix 5300 Servo Drives User Manual, publication 2198-UM005, for detailed information on wiring the 2198-K53CK-D15M feedback connector kit and attaching the motor power/brake shield clamp.IMPORTANT•Loosen the screw, if needed, until you can start threading both clamp screws with the cable shield under the clamp.•Make sure the cable clamp tightens around the cable shield and provides a high-frequency bond between the cable shield and the drive chassis.IMPORTANTIf the power/brake cable shield has a loose fit inside the shield clamp, insert the clamp spacer between the shield clamp and the drive to reduce the clamp diameter. When the clamp screws are tight, 2.0 N•m (17.7 lb•in), the result must be a high-frequency bond between the cable shield and the drive chassis.If the frame 3 cable is too large to fit within the standard shield clamp, substitute the standard clamp for the frame 3 clamping plate. The standard shield clamp screws are reused on the frame 3 clamping plate.Apply two tie-wraps around the cable shield and clamping plate, to provide a high-frequency bond between the cable shield and the drive chassis.Insert the clamp spacer when the cable diameter is smaller than the drive clamp alone.Shield Clamp Clamp Screws 2.0 N•m (17.7 lb•in.)Frame 1Servo DriveFrame 2Servo DriveFrame 3Servo DriveClamp Spacer Added (small diameter cable)Clamping Plate for Large (2)Diameter Cables (applies to frame 3 only)Standard Shield Clamp (frame sizes 1 and 2)Frame 3Servo DriveStandard Shield Clamp(frame 3)xx connector sets with frame 1, 2, and 3 drives.Connector Kit 2198-K53CK-D15MClamp Screws Frame 1 and 2Servo DrivesClamp Spacer (if needed) (1)(if needed)Rockwell Automation Publication 2198-IN021B-EN-P - July 202211Kinetix 5300 Single-axis EtherNet/IP Servo Drives Installation InstructionsGround Your Kinetix 5300 Drive to the SubpanelGround Kinetix 5300 drives to a bonded cabinet ground bus with a braided ground strap. Keep the braided ground strap as short as possible for optimum bonding.Connecting the Braided Ground StrapRefer to the System Design for Control of Electrical Noise Reference Manual, publication GMC-RM001, for more information.Kinetix 5300Kinetix 5300 Single-axis EtherNet/IP Servo Drives Installation InstructionsCircuit Breaker/Fuse SelectionThe Kinetix 5300 drives use internal solid-state motor short-circuit protection and, when protected by suitable branch circuit protection, are rated for use on a circuit capable of delivering up to 200,000 A (fuses, UL applications), 10,000A (miniature circuit breakers), and 65,000A (molded-case circuit breakers).Kinetix 5300 UL/CSA Circuit Protection SpecificationsDrive Cat. No.AC Input Voltage, nom Phase Bussmann FusesCat. No.Molded Case CB Cat. No.2198-C1004-ERS200…240V ACThree phase KTK-R-6140U-D6D3-B40140UT-D7D3-B402198-C1007-ERS KTK-R-10140U-D6D3-B80140UT-D7D3-B802198-C1015-ERS KTK-R-15140U-D6D3-C12140UT-D7D3-C122198-C1020-ERS KTK-R-25140U-D6D3-C20140UT-D7D3-C202198-C2030-ERS KTK-R-30140U-D6D3-C30140UT-D7D3-C302198-C2055-ERS LPJ-50SP140G-G6C3-C502198-C2075-ERS LPJ-60SP140G-G6C3-C602198-C4004-ERS380…480V AC KTK-R-3140U-D6D3-B20140UT-D7D3-B202198-C4007-ERS KTK-R-6140U-D6D3-B40140UT-D7D3-B402198-C4015-ERS KTK-R-12140U-D6D3-B80140UT-D7D3-B802198-C4020-ERS KTK-R-15140U-D6D3-C12140UT-D7D3-C122198-C4030-ERS KTK-R-25140U-D6D3-C15140UT-D7D3-C152198-C4055-ERS LPJ-30SP140U-D6D3-C30140UT-D7D3-C302198-C4075-ERS LPJ-35SP140U-D6D3-C30140UT-D7D3-C302198-C1004-ERS100…120V ACSingle phase KTK-R-6140U-D6D2-B40140UT-D7D2-B402198-C1007-ERS KTK-R-10140U-D6D2-B80140UT-D7D2-B802198-C1015-ERS KTK-R-15140U-D6D2-C12140UT-D7D2-C122198-C1020-ERS KTK-R-25140U-D6D2-C20140UT-D7D2-C202198-C1004-ERS200…240V AC KTK-R-6140U-D6D2-B40140UT-D7D2-B402198-C1007-ERS KTK-R-10140U-D6D2-B80140UT-D7D2-B802198-C1015-ERS KTK-R-15140U-D6D2-C12140UT-D7D2-C122198-C1020-ERS KTK-R-25140U-D6D2-C20140UT-D7D2-C2012Rockwell Automation Publication 2198-IN021B-EN-P - July 2022Kinetix 5300 Single-axis EtherNet/IP Servo Drives Installation Instructions Kinetix 5300 IEC (non-UL/CSA) Circuit Protection SpecificationsDrive Cat. No.AC Input Voltage, nom Phase DIN gG FusesAmps, max Miniature CBCat. No.Molded Case CBCat. No.2198-C1004-ERS200…240V ACThree phase 61489-M3C060140U-D6D3-B40140UT-D7D3-B402198-C1007-ERS101489-M3C100140U-D6D3-B80140UT-D7D3-B802198-C1015-ERS161489-M3C160140U-D6D3-C12140UT-D7D3-C122198-C1020-ERS251489-M3C250140U-D6D3-C20140UT-D7D3-C202198-C2030-ERS321489-M3C400140U-D6D3-C30140UT-D7D3-C302198-C2055-ERS40—140G-G6C3-C502198-C2075-ERS50—140G-G6C3-C602198-C4004-ERS380…480V AC 21489-M3C030140U-D6D3-B20140UT-D7D3-B202198-C4007-ERS61489-M3C060140U-D6D3-B40140UT-D7D3-B402198-C4015-ERS121489-M3C100140U-D6D3-B80140UT-D7D3-B802198-C4020-ERS161489-M3C130140U-D6D3-C12140UT-D7D3-C122198-C4030-ERS251489-M3C200140U-D6D3-C15140UT-D7D3-C152198-C4055-ERS321489-M3C350140U-D6D3-C30140UT-D7D3-C302198-C4075-ERS321489-M3C400140U-D6D3-C30140UT-D7D3-C302198-C1004-ERS100…120V ACSingle phase 61489-M2C060140U-D6D2-B40140UT-D7D2-B402198-C1007-ERS101489-M2C100140U-D6D2-B80140UT-D7D2-B802198-C1015-ERS161489-M2C160140U-D6D2-C12140UT-D7D2-C122198-C1020-ERS251489-M2C250140U-D6D2-C20140UT-D7D2-C202198-C1004-ERS200…240V AC 61489-M2C060140U-D6D2-B40140UT-D7D2-B402198-C1007-ERS101489-M2C100140U-D6D2-B80140UT-D7D2-B802198-C1015-ERS161489-M2C160140U-D6D2-C12140UT-D7D2-C122198-C1020-ERS251489-M2C250140U-D6D2-C20140UT-D7D2-C20Rockwell Automation Publication 2198-IN021B-EN-P - July 20221314Rockwell Automation Publication 2198-IN021B-EN-P - July 2022Kinetix 5300 Single-axis EtherNet/IP Servo Drives Installation InstructionsMotor Overload ProtectionAllen-Bradley servo drives use solid-state motor overload protection that operates in accordance with UL requirements. Motor overload protection is provided by algorithms (thermal memory) that predict actual motor temperature based on operating conditions as long as control power is continuously applied.In addition to thermal memory protection, these drives provide an input for an external temperature sensor/thermistor device, embedded in the motor, to support the UL requirement for motor overload protection.This servo drive meets the following UL requirements for solid-state overload protection.Refer to the Kinetix 5300 Servo Drives User Manual, publication 2198-UM005, for the interconnect diagram that illustrates the wiring between your motor and drive.Additional ResourcesThese documents contain additional information concerning related products from Rockwell Automation. You can view or download publications at rok.auto/literature .Motor Overload Protection Trip Point Value Ultimately 100% overload Within 8 minutes 200% overload Within 20 seconds600% overloadATTENTION: To avoid damage to your motor due to overheating caused by excessive, successive motor overload trips, follow the wiring diagram provided in the user manual for your motor and drive combination.ResourceDescriptionKinetix Rotary Motion Specifications, publication KNX-TD001Product specifications for Kinetix VPL, VPC, VPF, VPH, and VPS; Kinetix MPL, MPM, MPF, and MPS; Kinetix TLY and TL; Kinetix MMA; and Kinetix HPK rotary motors.Kinetix Linear Motion Specifications Technical Data, publication KNX-TD002Product specifications for Kinetix MPAS and MPMA linear stages, Kinetix MPAR and MPAI electric cylinders, and Kinetix LDC and LDL linear motors.Kinetix 5700, 5500, 5300, and 5100 Servo Drives Specifications, publication KNX-TD003Provides product specifications for Kinetix Integrated Motion over the EtherNet/IP network and EtherNet/IP networking servo drive families.Kinetix Rotary and Linear Motion Cable Specifications Technical Data, publication KNX-TD004Product specifications for Kinetix 2090 motor and interface cables.Kinetix 5300 Single-axis EtherNet/IP Servo Drives User Manual, publication 2198-UM005Provides information on how to install, configure, startup, and troubleshoot your Kinetix 5300 servo drive system.Kinetix 5300 Feedback Connector Kit Installation Instructions, publication 2198-IN023Provides information on installing and wiring the 2198-K53CK-D15M motor feedback connector kit.Integrated Motion on the EtherNet/IP Network Reference Manual, publication MOTION-RM003Provides information on the AXIS_CIP_DRIVE attributes, the configuration software control modes, and methods.System Design for Control of Electrical Noise Reference Manual, publication GMC-RM001Use this manual if you are responsible for the circuit design and layout of wiring panels or the installation and mounting of Allen-Bradley products.AC Line Filter Installation Instructions, publication 2198-IN003Provides information on installing and wiring the AC line filters.Kinetix 300 Shunt Resistor Installation Instructions, publication 2097-IN002Provides information on installing and wiring these external shunt resistors for your Kinetix 5300 servo drives.Kinetix 5700 Passive Shunt Modules, publication 2198-IN011Provides information on how to install and wire Kinetix 5700 passive shunts.Industrial Automation Wiring and Grounding Guidelines, publication 1770-4.1Provides general guidelines for installing a Rockwell Automation industrial system.Product Certifications website, http://rok.auto/certificationsProvides declarations of conformity, certificates, and other certification details.Kinetix 5300 Single-axis EtherNet/IP Servo Drives Installation Instructions Notes:Rockwell Automation Publication 2198-IN021B-EN-P - July 202215Publication 2198-IN021B-EN-P - July 2022 | Supersedes Publication 2198-IN021A-EN-P - June 2020Copyright © 2022 Rockwell Automation, Inc. All rights reserved. Printed in the U.S.A.Rockwell Otomasyon Ticaret A.Ş. Kar Plaza İş Merkezi E Blok Kat:6 34752 İçerenkÖy, İstanbul, Tel: +90 (216) 5698400 EEE YÖnetmeliğine UygundurAllen-Bradley, ControlLogix, CompactLogix, expanding human possibility, Kinetix, Rockwell Automation, and Studio 5000 Logix Designer are trademarks of Rockwell Automation, Inc.EtherNet/IP is a trademark of ODVA, Inc.Trademarks not belonging to Rockwell Automation are property of their respective companies.*PN-671714*PN-671714Your comments help us serve your documentation needs better. If you have any suggestions on how to improve our content, complete the form at rok.auto/docfeedback .For technical support, visit rok.auto/support .Waste Electrical and Electronic Equipment (WEEE)Rockwell Automation maintains current product environmental information on its website at rok.auto/pec .At the end of life, this equipment should be collected separately from any unsorted municipal waste.。
MTS4L TETRA LTE混合通信基站说明书

TETRA AND LTE WORKING TOGETHERThe MTS4L TETRA/LTE Base Stationprovides a flexible path for the addition of LTE to complement a TETRA system. By provisioning for the addition of an eNodeB into the TETRA Base Station cabinet, Motorola is offering a highly flexible migration solution for TETRA operators. The MTS4L can be installed as a TETRA only base station, but it can include the services for the eNodeB such as shared backhaul, common power supply and battery backup. These services can be installed at the start or they can be upgraded at a later time when needed by customers. Most importantly the MTS4L footprint is unchanged when the eNodeB is installed and so the upgrade is very simple and fast.MTS4 TETRA BTS IN THE MTS4L CABINET DESIGNED FOR THE FUTUREBuilt and designed for future communications needs, the MTS4 supports TETRA Enhanced Data Services (TEDS) - the platform for secure mission critical high speed data services.Providing support for E1 and IP-over-Ethernet, the MTS4enables operators to utilize the most efficient andcost effective transmission networking technologiesavailable today and in the future.FLEXIBLE CAPACITY AND COVERAGEThe compact MTS4 is a high performance base stationwith state of the art capacity and coverage enhancingcapabilities:• C-SCCH – additional control channels on the maincarrier, quadrupling existing capacity.• B est-in-class transmitter output power and receiversensitivity, together with various diversity options,enabling a reduction in the number of sites requiredto achieve a given level of coverage, and increaseddata performance and enhanced audio quality.•Rx/Tx antenna, easing implementation costs andreducing cycle time.MTS4 ADDITIONAL FEATURES• P rovision for eNode B in the samecabinet as the TETRA BTS• R apid installation of eNobe B asa future upgrade with minimumcost and disruption•frequency and roll-out whenappropriate• I nterference Detection andCorrection• Air Interface Encryption• M ulti-Slot Packet Data (MSPD)for enhanced data services• Hot swapable modules• D ynamic Channel allocationbetween voice and packet data• L ockable door equipped withstandard alarm contacts – aneffective intrusion detectionsystem.MOTOROLA, MOTO, MOTOROLA SOLUTIONS and the Stylized M Logo are trademarks or registered trademarks of Motorola Trademark Holdings, LLC and are used under license.All other trademarks are the property of their respective owner shown are typical.To learn more, visit us on the web at: /TETRAOPTIMISED TOTAL COST OF OWNERSHIPThe running costs of basestation sites typically account for a significant portion of the total cost of ownership of any TETRA network. MTS4 basestations are specifically designed with advanced features that help to minimise operational expenditures. Such features enable:• B etter power consumption through use of high delivering significant operational cost savings over the network’s lifetime.• R educed transmission costs – native support using IP-over-Ethernet capability means that the MTS4 can enable up to 70% savings compared with non-IP based transmission.• R educed battery capacity requirement and low heat dissipation due to excellent power efficiency. With a strong integrated battery charger, power supply costs are kept to an absolute minimum.RELIABLE AND EASY TO MAINTAINThe MTS4 offers supreme reliability plus flexible access for easy servicing. Key features include:• T wo E1 or Ethernet interfaces can be provided with the MTS4 to facilitate implementing link redundancy using ring configurations. Redundant E1 and Ethernet ports can be activated in the event of link failure, ensuring continuous connectivity.• L ocal Site Trunking – in the event of site link failure, the base station is able to operate independent of themobile switching office, maintaining secure talkgroup communications throughout.• N on-GPS operation – supports operation in the absence of a GPS signal, ideally suited to underground applications.• F ull redundancy of site controller and base radio subsystems including support for automatic Main Control Channel switching.TOTALLY SECURE…DAY AND NIGHTWith the MTS4, there is no need to worry about theft or vandalism. The basestation equipment includes the latest security features for total peace of mind:• E xternal alarm interface supports 15 alarm inputs and 2 external control outputs.• T he MTS4L supports site link encryption in release 8.1, and air interface encryption with TEA1, TEA2 and TEA3.© 2014 Motorola Solutions, Inc. All rights reserved.。
Infoprint 250 導入と計画の手引き 第 7 章ホスト
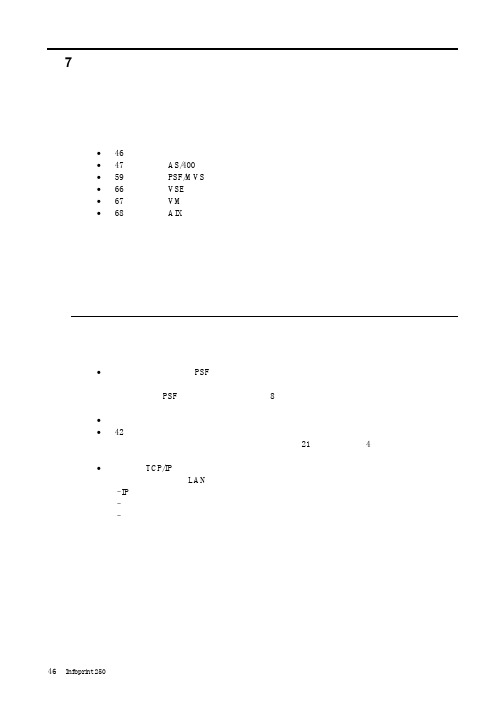
SUBNETMASK
255.255.255.128
Type of service...............: TOS
*NORMAL
Maximum transmission unit.....: MTU
*LIND
Autostart.....................:
AUTOSTART
*YES
: xx.xxx.xxx.xxx
: xx.xxx.xxx.xxx
*
(
)
IEEE802.3
60 1500
: xxxx
48 Infoprint 250
31. AS/400
IP
MTU
1
1
IPDS TCP
CRTPSFCFG (V3R2)
WRKAFP2 (V3R1 & V3R6)
RMTLOCNAME RMTSYS
MODEL
0
Advanced function printing............:
AFP
*YES
AFP attachment........................:
AFPATTACH
*APPC
Online at IPL.........................:
ONLINE
FORMFEED
*CONT
Separator drawer......................:
SEPDRAWER
*FILE
Separator program.....................:
SEPPGM
*NONE
Library.............................:
8175 TX-I O 模块 TXM1.6R TXM1.6R-M 说明书

8175TX-I/O™Relay modules TXM1.6RTXM1.6R-M∙Two fully compatible versions:– TXM1.6R:– 6 volt-free relay outputs– Individual I/O point signaling with green I/O status LED– TXM1.6R-M: As TXM1.6R, but with the following additional features– Three-color I/O status LED (red, yellow or green)– Local override (to ISO 16 484-2)∙ 6 relay outputs, which can be individually configured as:– Maintained contact or pulse, 1 … 3-stage– Three-position control output with stroke algorithm∙Mixed voltages (AC 250 V mains voltage and SELV/PELV 24 V) as well asmixed phases are permitted on adjacent I/O points of the module∙Compact DIN format, small footprint∙ Separate terminal base and plug-in I/O module for convenient handling– Self-establishing bus connection for maximum ease of installation– Terminal isolation function for fast commissioning– I/O module replaceable in seconds, without rewiring and without affectingthe full functioning of the remaining I/O modules∙Terminal strips are required to connect N and PE of the field devices∙Simple strategy for operation and display– I/O status LED for each I/O point– LEDs for fast diagnostics∙Double-sided labels for identification of all I/O pointsCM2N8175en_112/10FunctionsThe modules support the following I/O functions:Signal type (TRA)Signal type DescriptionBO Relay NO 250V BO Relay NC 250V Q250Maintained contact relay, changeover contact N/O, N/C contact BO Pulse On-Off Q250-P Q250A-P On/off pulse Q250-P With self-latching and 2 channels Q250A-PWith dual-winding switchBO Pulse *)PulseMO Steps Q-M1…M4Multistate maintained contact, 1…6-stage mutually exclusive electronic relay interlock MO Pulse Q250-P1…P5Multistate pulse, 1…5-stagemutually exclusive electronic relay interlock BO 3-Pos RelayY250TPulse, control signal, three-position output,internal algorithm for stroke running time*) DESIGO V4, V5: Use MO Q250-P1.For a detailed description of these functions, please refer to document CM110561,"TX-I/O™ functions and operation".∙Q250B Use TXM1.6RL with BO Bistable NO / NCFor switched current <100mA, see CM110563, Replacement of legacy signal types.∙QD Feedback must be implemented using separate digital inputse.g. with TXM1.8D, see CM110563.CompatibilitySupport of signal types and functions in different building automation and control systems: see TX-I/O Engineering and installation manual, CM110562Type summary Relay module TXM1.6RRelay module TXM1.6R-M with local overrideThe terminal base and the plug-in I/O module are interconnected and delivered in the same box.The available accessories include address keys, label sheets, and spare transparent label holders. Refer to data sheet CM2N8170.NotesASNDeliveryAccessories3/10Technical and mechanical designFor a description of the features common to all TX-I/O™ modules, please refer to the TX-I/O™ Engineering and installation manual, document CM110562.Indicators and operator controlsConnection terminals (No. 1 screwdriver for slotted or recessed-head * screws)with test pickup (for 1.8...2 mm pins) and terminal number Signal designationOverride status LEDs (yellow)Address key and module status LEDI/O point numbersOverride button (TXM1.6R-M only)I/O status LEDs (TXM1.6R: green;TXM1.6R-M: colors can be configured, green/yellow/red)* Combined slotted / recessed-head screws from mid-2012∙The I/O status LEDs indicate the status of the relays ∙The LEDs on the TXM1.6R are green.∙In the case of the TXM1.6R-M the LEDs are three-colored. If the I/O function supports it, the module can display Alarm = red and Service = yellow, besides Normal = green∙The LEDs are also used for diagnostics∙The module status LED illuminates the transparent address key∙The (green) LED shows the module status as a whole (as opposed to the I/O points)∙It is also used for diagnostics∙The module operates only with the address key inserted∙The module address is mechanically encoded in the address key∙When replacing the plug-in I/O module, the address key must be swiveled outward. It remains plugged into in the terminal base.∙The relay contacts of the individual I/O points are volt-free, and are notinterconnected. The switched voltage must be provided separately for each I/O point.∙Mixed voltages (AC 250 V mains voltage and SELV/PELV 24 V) as well as mixed phases are permitted on adjacent I/O points of the moduleI/O status LEDsModule status LEDsAddress keyTerminals4/10Local override (TXM1.6R-M only)∙Pressing an override button in the middle enables/disables local override∙Pressing "+" for one of the I/O points activates the relay or switches control to the next stage up (depending on function)Repeated or sustained pressure switches several stages until the function stops at the highest stage.∙Pressing "–" for one of the I/O points deactivates opens the relay or switches control to the next stage down (depending on function)Repeated or sustained pressure switches several stages until the function stops at the lowest stage.∙The yellow "Override" LED indicates that local override is active∙All safety-relevant functions must be implemented with external solutions ∙The local override must not be used for safety shutdown operations∙In compliance with the standard (ISO 16 484-2, Section 3.110), the module executes all local overrides directly, without safety precautions or interlocks.→ Full responsibility lies with the operator.←Module labelingThe plug-in I/O module has a removable transparent cover (the label holder) for insertion of a label.DisposalThe device is classified as waste electronic equipment in terms of the European Direc-tive 2012/19/EU and should not be disposed of as unsorted municipal waste.The relevant national legal rules are to be adhered to.Regarding disposal, use the systems setup for collecting electronic waste.Observe all local and applicable laws.Override buttonOverride status LEDEngineering, mounting, installationPlease refer to the following documentsDocument NumberTX-I/O™ functions and operation CM110561TX-I/O™ Engineering and installation manual CM110562Replacement of legacy modules CM110563 *)*) Login with Siemens account necessary.MountingThe TX-I/O™ devices can be installed in any orientation:It is important to provide adequate ventilation so that the admissible ambienttemperature (max. 50°C) is not exceeded.Technical dataSupply(bus connector on side)Operating voltageExtra low voltage SELV or PELVin accordance with HD384DC 21.5 ... 26 VMax. power consumption TXM1.6R 1.7 WTXM1.6R-M(for the sizing of power supplies, see CM110562)1.9 WProtection Bus connector on side No protection against shortcut andincorrect wiring with AC/DC 24 VSwitching outputs Number of switching outputs 6 (changeover contact)External fuse protection for incoming cable∙Slow blow fusible link Max. 10 A∙Circuit breaker Max. 13 ACircuit breaker tripping characteristic Type B, C or D to EN 60898 Contact data for AC Voltage range min. AC 12V max. AC 250VCurrent,resistive load max. 4ACurrent, inductive load (cos phi≥ 0.6)max. 3ASwitching current min. 1 mA at AC 250 Vmin. 10mA at AC 12VCurrent on make max. 20 A during max. 10 msmax. 10A during max. 1sFor UL applications 3 FLA, 9 LRA, 1/4 HP, 4 (3) A Contact data for DC Voltage range min. DC 12V, max. DC 30VCurrent, resistive load max. 3 A at DC 30 Vmin. 10mA at DC 12VCurrent on make max. 3 AService life of contact With 0.1 A resistive8 million switching operations for AC 250 V With 0.5 A resistive 2 million switching operationsWith 4.0 A resistive(N/O)0.2 million switching operationsReduction factor with inductive load(cos phi≥ 0.6)0.6 (max. 3 A inductive)Insulation resistance Reinforced insulation between relay outputs andsystem electronicsAC 3750 V, to EN 60 730-1Mixed voltages (AC 250 V mains voltage and SELV/PELV 24 V) as well asmixed phases are permitted on adjacent I/O points of the modulePermitted orientation5/10Connection terminals Mechanical designSolid conductorsStranded conductors without connector sleevesStranded conductors with connector sleeves(DIN46228/1)Cage clamp terminals1 x 0.5 mm2to 4mm2or 2 x 0,6 mm∅ to 1.5 mm2 1 x 0.5 mm2 to 2.5 mm2or 2 x 0,6 mm∅ to 1.5 mm2 1 x 0.25 mm2 to 2.5 mm2 or 2 x 0,6 mm∅ to 1.5 mm2Screwdriver No. 1 Screwdriver for slotted orrecessed-head * screwswith shaft diameter ≤ 4.5 mm* Combined slotted / recessed-head screws from mid-2012Max. tightening torque0.6 NmTest pickups (terminals)For pin diameter 1 x 1.8 … 2.0 mmLocal override(TXM1.6R-M only)Local override device ISO 16 484-2, Section 3.11Classification to EN 60730Mode of operation of automatic electrical controlsContamination levelMechanical designType 12Devices are suitable for use in equip-ment with protective class I and IIHousing protection standard Protection standard to EN 65029Front-plate components in DIN cut-outTerminal baseIP30IP20Ambient conditions OperationClimatic conditionsTemperatureHumidityMechanical conditions To IEC 60721-3-3 Class 3K5-5...50 °C5…95 % rh Class 3M2Transport / storageClimatic conditionsTemperatureHumidityMechanical conditions To IEC 60721-3-2 Class 2K3-25…70 °C 5…95 % rh Class 2M2Standards, directives and approvals Product standard EN 60730-1Automatic electrical controls forhousehold and similar use Electromagnetic compatibility (Applications)For use in residential, commercialand industrial environmentsEU conformity (CE)CM1T10870 *)RCM conformity (EMC)T10870en_C1 *)UL approbation UL 916, UL 864Environmental compatibility The product environmental declaration containsdata on RoHS compliance, materials composition,packaging, environmental benefit,disposal)CM2E8175 *)Color Terminal base and plug-in I/O module RAL 7035 (light gray) Dimensions Housing to DIN 43 880, see "Dimensions"Weight Without / with packaging TXM1.6R231 / 252 gTXM1.6R-M241 / 262 g*) The documents can be downloaded from /bt/download.6/107/10Connection diagrams (examples)TXM1.6R, TXM1.6R-M I/O point (1)(2)(3)(4)(5)(6)Supply3915202632N/O contact 2814212733N/C contact41016192531For functions with several I/O points:∙Always use adjacent I/O points∙Each function must be confined to one module only∙The I/O points have a fixed sequence within the function, e.g. the first I/O point is for switch-off.Maintained contact BO Relay NO 250V BO Relay NC 250V8175z 13_01U Relay moduleQ1 Switched load(N/O contact)Q2 Switched load(N/C contact)K3 Step switch /pulse switch /bistable relayOn/off pulseBO Pulse On-Off Self-latching and 2channels (Q250-P)Dual-winding switch (Q250A-P)U Relay moduleK1 Power contactor,self-latchingK2 Dual-winding steppingswitch, bistable relay Pulse on I/O point (2) = K1 ON Pulse on I/O point (1) = K1 OFFPulse on I/O point (4) = K2 ON Pulse on I/O point (3) = K2 OFFPulse control for single-stage load with control from two separate control loops of equal statusBO Pulse On-OffU Relay module K1Power contactor,self-latchingControl circuit 1:Pulse on I/O point (2) = ON Pulse on I/O point (1) = OFF Control circuit 2:Pulse on I/O point (4) = ON Pulse on I/O point (3) = OFFTerminal layout8/10Pulse control for single-stage load with control of equal status from tworemote switching locations BO Pulse On-OffU Relay module K1Power contactor,self-latchingControl circuit 1:Pulse on I/O point (2) = ON Pulse on I/O point (1) = OFF External control location A:S1OFF button S2ON button External control location B:S3OFF button S4ON buttonMaintained contact,3-stage MO Steps81AC / DC 24 ... 230 VU Relay moduleK1, K2, K3Contactors for Stages 1 (3)I/O point (1) ON = Stage 1I/O point (2) ON = Stage 2I/O point (3) ON = Stage 3Pulse, 1-stage DESIGO V4, V5:Use Q250-P1 DESIGO TRAUse BO PulsePulse, 3-stage MO PulseURelay module K1, K2, K3Contactors with self-latching feature for Stages 1 (3)Pulse on I/O point (1) = OFF Pulse on I/O point (2) = Stage 1Pulse on I/O point (3) = Stage 2Pulse on I/O point (4) = Stage 3*)External self-latching is optional**)For other means of control,replace bridge with external circuit9/10Pulse control for a three-stage load with control from two control loops of equal status MO PulseU1, U2Relay modules Control loop 1:U1 Pulse on I/O point (1) = OFF U1 Pulse on I/O point (2) = Stage 1U1 Pulse on I/O point (3) = Stage 2U1Pulse on I/O point (4) = Stage 3K1, K2, K3 Contactors with self-latching feature for Stages 1 … 3*)External self-latching is optionalControl loop 2:U2 Pulse on I/O point (1) = OFF U2 Pulse on I/O point (2) = Stage 1U2 Pulse on I/O point (3) = Stage 2U2 Pulse on I/O point (4) = Stage 3Control signal, three-position output BO 3-Pos Relay8175z 17URelay moduleY1 Control signal OPEN Y2 Control signal CLOSE10/10DimensionsDimensions in mm8172M 01Published by:Siemens Switzerland Ltd.Smart Infrastructure Global Headquarters Theilerstrasse 1a CH-6300 Zug SwitzerlandTel. +41 58 724-2424/buildingtechnologies© Siemens Switzerland Ltd 2007Delivery and technical specifications subject to change。
海尔商业空调中央控制器系统说明书
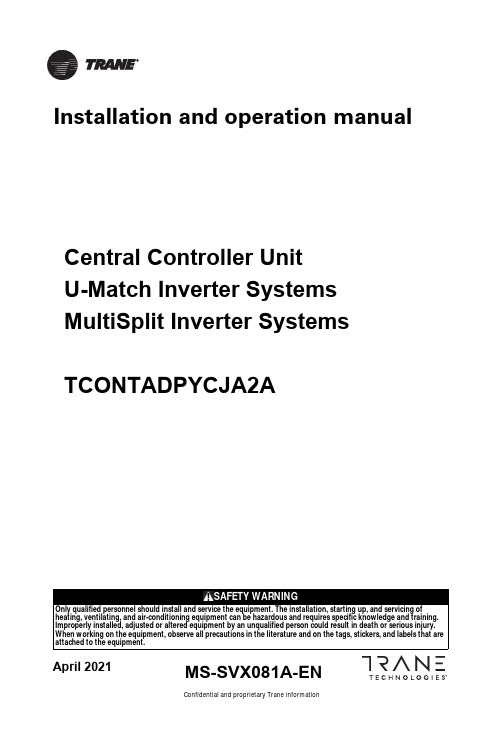
Central Controller U nit UMatch Inverter Systems MultiSplit Inverter SystemsTCONTADPYCJA2AConfidential and proprietary Trane informationA pril 2021Installation and operation manualMS-SVX081A-ENUser manuals and installation manuals for remote control detector TCONTADPYCJA2AFunctions IntroductionRemote control detector(short form:Detector)is essential equipment of remote monitor system of Haier commercial A/C.By connecting the interface in indoot units or outdoor units,this detector can reach functions of remote an central control◆Communication function1.with air conditioning communication:①. YCJ-A002 can at most connect two same model units by six-pin fixed screw. It canrealize double switching function. It can control air conditioning to work in different ways according to the requirement of detector, at the same time query the airconditioner's operation information and fault information.munication with RS-485:①. Communication with the central controllerBM1 dip switch as (1: OFF, 2: OFF)Communicate with the central controller via RS-485 interface bus (A, B). It receives commands from central controller according to the units address what is set by detector dip switch. And to realize internal control or query request, and answer the reception status and air conditioning operation information and fault information.②Communication with the central controllerBM1 dip switch as (1: ON, 2: OFF)Communicate with the central controller by RS-485 bus port. According to the detector within the dip switch setting address, Receive commands from the central controller. Have internal control or query request, and answer the reception status and air conditioning operation informationand fault information.③Communicate with remote devices. Detector has RS-485 port, and the protocol is Modbus RTU, users can use the private network and open protocol to create remote control program, no need other accessories.The BM1 dip switch as (1: OFF, 2: ON).④communication with the central control systemD ip switch BM1 (1: ON,2: ON)Communicate with the central control system by RS-485 bus port(A, B). it receives12commands from central controller according to the units address what is set by detector dip switch. And to realize internal control or query request, and answer the reception status and air conditioning operation information and fault information.In order to improve the reliability of air conditioning, the detector has double switching function, set SW1 to single unit mode, detector controls the A unit according to the command from the host equipment. Set SW1 to double switching mode, it can realize double switching function.Double switching function realization: under normal condition, the detector control one unit ON and another unit OFF, when reach the switch time, detector wake up the OFF state unit and the ON state unit will still work half an hour and then OFF.If any air conditioner has failure, switch time will stop, the detector automatically wake up another unit, and let the failure unit OFF, then upload the failure information. After the failure restore, automatically change to the double switching function; if air-conditioner operate for some time and cannot reach setting temperature, switch time will stop, the detector automatically wake up another air conditioner, double units operate until reaching the setting temperature, then automatically turn off that air conditioner, and automatically restore the double switching function. Factory default switch time is 12 hoursDetector has three lights, yellow light is for RS-485 communication , red and green lights are for the air conditioner communication, When the communication is normal, lights in accordance with the frequency of 0.5s flashing, when have failure, lights in according with the frequency of 1s flashing, stop 2s flashingThrough the RS-485 bus to build a central control network, In order to reduce the impact of unified operation of air conditioning on the power grid, the detector set the delay start function, the delay time is automatically generated by the detector【1】【2】BM10:OFF 1:ON numbe485communication mode details00①TCONTCCMYCZG1/TCONTCCMYCZ256 single unit10②/01③Modbus rtu standard protocol 11④BMS system◆Dual switch function◆Address setting function◆Operation status displasy function◆Delay control functionThe detector with 8-bit dip switch (SW1), the highest bit D8 bit, for setting the single mode or double-switch mode,(D7, D6, D5, D4, D3, D2, D1) is used to set the number (central control network or double switch time when select the dual switch mode)◆Double switching function instructions◆use central controller for central control functionSystem OverviewDetector connects with the two same model units through six-pin fixed screw. Set the dip switch to double switching model. Only use the double switching function, the system does not need connect the other components; double switching time can be chosen 8,10,12,14 hours by dip switch setting.the specific settings and the corresponding time see dip switch list12V 、COM 、GND ports of detector connect with air conditioner. Dip switch set to singlemode, the specific settings and the corresponding address see dip switch list, The system also needs to connect withcentral controller, Each detector connect with central Controller by 2-pin fix screw(A,B).DetectorsIndoor Unit Indoor UnitOutdoor Unit Outdoor Unit4◆Status check◆When servicing, be sure to power off the power supplyMaintenanceDimension drawing•When select the single unit mode and control A unit, when A unit failure occurs, the detector will query fault information and upload it, when select double switch mode,detectorcontrolA unit and B unit, if one of air conditioner is faulty, the detector will query the fault information and upload it•Detector operating status and running lamp display: When operation properly, running lamp for 0.5 seconds off 0.5 secondsfor a cycle to indicate,When have the fault to flash 1 second, stop 2 seconds to cycle to indicate, yellow lamp for the central control of communication status indication, red light for the air conditioner A unit communication Status indication, green lamp for air conditioning B unit communication status indication•Wipe clean with a soft cloth and be careful not to touch the electrical parts.•Do not use gasoline, thinner, decontamination powder, chemical wipes, etc. to avoid damage to electrical parts.•Check whether the wiring with the central control and air conditioning is normal, there is no broken wire or the existence of loosening of the connection.Interface Description:1-air conditioning A communication port,three-core shielded communication wire connection, wire length is not more than 10meter2-air conditioning B communication port,three-core shielded communication wire connection, wire length is not more than 10meter3 - dial switch is used for centralized control interface of detector detector Communication Associationand dual switching functionIOS device to achieve remote control.Installation and commissioning◆installation and wiring of the basic requirements:Use a screw driver to install detector, screw spacing see the right figure.Keep the detector on a wall or other reliable location to ensure that there is no water and other creatures that may cause failure to enter.1.Central control network design planning principles:(1) Detector, in order to maintain the appropriate response speed and communication reliability, the number of detectors in one central system should not exceed 64 pieces (2)A/C should be ready for network ,bu sure to be installed and us according to instructions(3) Detector installation position does not leave the air conditioner too far; do not exceed the wiring length(4) Detector address number in strict accordance with the order from small to large allocation(5) Detector power from the indoor unit, 12V, need have distance with the high voltage cable .and the shieldlayer needs earth one side(6) Central control bus wire length limit less than 1000 meters(7) both ends of the bus in the A bus and B bus were connected between the 100 ohm metal film precision resistance (depending on the scene to match)(8) bus shielded wire single point grounding, the proposed layout in the middle of the communication bus location, and centralized controller similar(9) Central controller installation location in principle arranged in the middle of the communication bus position, and the communication bus shield ground similar2.Detector and air conditioning connection: Detector through the air conditioning interface six screws fixed terminal (12V、COM1、GND、12V、COM2、GND) ,andup to two air-conditioning (A, B) for wired communication; detector and air conditioning connection with the uniform wiring, one end of the wiring terminal with plug connect to air conditioning indoor PCB remote control terminal. If the detector does not operation properly during commissioning, it can be check by change the wiring polarity + - . Also can be based on the running lamp show the operation status of the air conditioning and communication interface to determine whether the normal.3.After the communication bus wiring is completed, connect the detector and the communication bus: the connection method of hand by hand type, all A ports in the same Bus, all B ports on another bus, the communication bus shielding line in the communication bus in a single point of grounding, communication bus total length Limited to less than 1000 meters.◆According to the host equipment to select RS-485 interface protocol by dip switch BM1:Detector built a variety of different protocols to correspond to different host equipment, the use of four different protocols corresponding to four different conditions:1.The host equipment is a centralcontroller, central controller can choose to select the device type for single unit, in order to be able to deal with different system structure, the detector has two built-in protocols that communicate with the central controller.5①central controller, select the communication mode for the single unit, then dip switch: BM1: 1: OFF; 2: OFF.The system diagram is as follows:67②the host equipment for the third party communication equipment, the detector provides the standard Modbusrtu protocol, BM1 dip switch: 1: ON; 2: OFF, The communication between the detector and the air conditioner is consistent with the other 3. When the detector is used as a third-party protocol converter, it should be specificAccess to the requirements of third-party host device connection; the basic functions are as follows:The address of the address set by SW1 changes to the slave address in the Modbus RTU communicationSerial port9600,8,n ,1130B modbusrtu query01 control 05/15WORD name Unit Range Remarks 01 function code 0Indoor units on/off Read operation to obtain the current switchunit status 0: off 1: onWrite operation to change the switch state 0: off 1: on03 function code query 03 control 06/16 0I n t e r n a l s e t t i n g temperature ℃16-30Read operation Get current setting temperature, write operationChange set temperature1within the machine running mode 1--5Read operation to obtain the current operating mode: 1 - cooling 2 - heating 3 - dehumidification4 – Fan only5 - automatic Write operation to change the operating mode: 1 - cooling 2 - heating 3 - dehumidification 4 – Fan only 5 - automatic2Fan speed 1--4Read operation to obtain the current fan speed: 1 - low speed 2 – middle speed 3 - high speed4 – Automatic speedWrite operation to change the fan speed: 1 - low speed 2 – middle speed 3 - high speed 4 -Automatic speed3i n d o o r c o n t r o lmode1--4 1 is not locked; 2 empty - query back to 1, issued to write 1; 3 query back to 1,Issued to write 1; 4 - lock 04 function code read only 0indoortemp ℃301℃1Fault code 0-256within the indoor fault code 0-256 value of 0 that no error ,2machine numberThe number of internal indoor This address exists , query back 08◆Power test :◆RS485 interface dip switch instructions1.Power test: After the equipment is connected, the power test①first verify the detector and air conditioner communication status, the red lightshould be light 0.5 seconds off 0.5 seconds as a cycle to indicate, If the indicator does not light or flashes for 1 second and stops for 2 seconds, it should check whether the communication wire of the air conditioner and detector are the connection is correct and the air conditioner is powered up until the indicator flashes normally.②check 485 communication indicator (yellow lamp), should be light 0.5 seconds off 0.5seconds as a cycle to indicate, if the instructions If the lamp does not light or flashes for 1 second and stops for 2 seconds, it should check whether the BM1 protocol is correct; the communication wire is connectedWhether it is correct; whether there is a device with a repeated address, etc., until the indicator flashes normally2.The detector and the host equipment communication, if the host equipment to normal monitoring and control of air conditioners, the completion of debugging.Performance parameters and accessoriesDetector built a variety of different protocols to correspond to different equipment, the use of four different protocols corresponding to four different conditions:1.The host equipment is a centralcontroller, central controller can choose to select the device type for single unit , in order to be able to deal with different the system structure, the detector has two built-in protocols that communicate with the central controller.①central controller, select the communication mode for the unit, then dip switch BM1:1: OFF; 2: OFF.performance parameter DC12VPower consumption Power consumption is less than 3W Detector code number 0151800130BAccessoriesair conditioning communication 3 core shielded wire, special number 0010452854, color white, yellow, and redPerformance parameter9S W 1(1m e a n O N ,0 m e a n O F F )B M 1c o d e1:O F F ;2:O F F1:O N ;2:O F F 1:O F F ;2:O N 1:0N ;2:O N[1][2][3][4][5][6][7][8]D e fi n i t i o n : u n i t a r y a i r c o n d i t i o n e D e fi n i t i o n :V R F D e fi n i t i o n :M o d b u s R T U D e fi n i t i o n :B M S G a t e a d d r U n i t a d d r 1---0000D u a l m o d e a d d r =1D u a l m o d e a d d r =1-1D u a l m o d e s l a v e I D =1D u a l m o d e 3101---0001D u a l m o d e a d d r =2D u a l m o d e a d d r =2-2D u a l m o d e s l a v e I D =2D u a l m o d e 311—— —— —— —— —— —— 1---1110D u a l m o d e a d d r =15D u a l m o d e a d d r =15-15D u a l m o d e s l a v e I D =15D u a l m o d e 31141---1111D u a l m o d e a d d r =16D u a l m o d e a d d r =16-16D u a l m o d e s l a v e I D =16D u a l m o d e 3115-0000000S i n g l e m o d e a d d r =1S i n g l e m o d e a d d r =1-1S i n g l e m o d e s l a v e I D =1S i n g l e m o d e 310-0000001S i n g l e m o d e a d d r =2S i n g l e m o d e a d d r =2-2S i n g l e m o d e s l a v e I D =2S i n g l e m o d e 311—— —— —— —— —— —— -0100110S i n g l e m o d e a d d r =39S i n g l e m o d e a d d r =39-39S i n g l e m o d e s l a v e I D =39S i n g l e m o d e 3138-0100111S i n g l e m o d e a d d r =40S i n g l e m o d e a d d r =40-40S i n g l e m o d e s l a v e I D =40S i n g l e m o d e 3139-0101000S i n g l e m o d e a d d r =41S i n g l e m o d e a d d r =41-41S i n g l e m o d e s l a v e I D =41S i n g l e m o d e 300-0101001S i n g l e m o d e a d d r =42S i n g l e m o d e a d d r =42-42S i n g l e m o d e s l a v e I D =42S i n g l e m o d e 301—— —— —— —— —— —— -1001110S i n g l e m o d e a d d r =79S i n g l e m o d e a d d r =79-79S i n g l e m o d e s l a v e I D =79S i n g l e m o d e 3038-1001111S i n g l e m o d e a d d r =80S i n g l e m o d e a d d r =80-80S i n g l e m o d e s l a v e I D =80S i n g l e m o d e 3039-1010000S i n g l e m o d e a d d r =81S i n g l e m o d e a d d r =81-81S i n g l e m o d e s l a v e I D =81S i n g l e m o d e 290-1010001S i n g l e m o d e a d d r =82S i n g l e m o d e a d d r =82-82S i n g l e m o d e s l a v e I D =82S i n g l e m o d e 291—— —— —— —— —— —— -1110110S i n g l e m o d e a d d r =119S i n g l e m o d e a d d r =119-119S i n g l e m o d e s l a v e I D =119S i n g l e m o d e 2938-1110111S i n g l e m o d e a d d r =120S i n g l e m o d e a d d r =120-120S i n g l e m o d e s l a v e I D =120S i n g l e m o d e 2939-1111000S i n g l e m o d e a d d r =121S i n g l e m o d e a d d r =121-121S i n g l e m o d e s l a v e I D =121S i n g l e m o d e 280-1111001S i n g l e m o d e a d d r =122S i n g l e m o d e a d d r =122-122S i n g l e m o d e s l a v e I D =122S i n g l e m o d e 281—— —— —— —— —— —— -1111110S i n g l e m o d e a d d r =127S i n g l e m o d e a d d r =127-127S i n g l e m o d e s l a v e I D =127S i n g l e m o d e 286-1111111S i n g l e m o d e a d d r =128S i n g l e m o d e a d d r =128-128S i n g l e m o d e s l a v e I D =128S i n g l e m o d e 287◆ Address setting functionSW01Definition[1][2][3][4][5][6][7][8]0———————Single mode 1———————Double Switch mode —00—————Double Switch time 8 hours —01—————Double Switch time 10 hours —10—————Double Switch time 12 hours —11—————Double Switch time 24 hours———0————Dual operation at ambient temperature of 34℃———1————Dual operation at ambient temperature of 32℃1———0000Double Switch mode and ad-dress=11———0001Double Switch mode and ad-dress=2———1———1110Double Switch mode and ad-dress=151———1111Double Switch mode and ad-dress=1600000000Single mode and address=100000001Single mode and address=2———01111110Single mode and address=12701111110Single mode and address=12810Trane - by Trane Technologies (NYSE: TT), a global climate innovator - creates comfortable, energy efficient indoor environments for commercial and residential applications. For more information, please visit or .Trane has a policy of continuous product and product data improvement and reserves the right to change design and specifications without notice. We are committed to using environmentally conscious print practices.©2020 TraneConfidential and proprietary Trane information。
Isomet iMS Studio快速入门指南说明书

Quick Start Guide: Isomet iMS StudioIsomet iMS Studio v1.30 is the first release of the Windows graphic user interface for the iMS4- series of 4 channel synthezisers.This guide gives a brief description of the iMS4 functions , how to use this GUI and concludes with a number of examples.[Note: This guide assumes individual file sizes < 1024 frequency data points. The iMS4-P is capable of storing >10 million points however the GUI will react slowly for Image files exceeding ~4000 points. Please contact Isomet for guideance on using the GUI for large image sizes ]The current release does not support the following features:- Diagnostics- Image Play Sequences- Compensation table generator(These features are supported in the SDK for C++ ).Download the appropriate installation program from: /software.html Uninstall any prevous versions of the SDK and/or GUIDepending on your computer select and run one of the followimg :Isomet iMS SDK v 1.30 Win7 32-bit Setup.exeIsomet iMS SDK v 1.30 Win7 64-bit Setup.exeIsomet iMS SDK v 1.30 Win10 32-bit Setup.exeIsomet iMS SDK v 1.30 Win10 64-bit Setup.exeFollow the installation instructions.A full explanation and supporting documentation is found underStart menu > All Programs > Isomet iMS SDKor from the installed folder : >> Program Files / Isomet / iMS_SDK / v1.30 / docRun: Isomet iMS Studio.Overview: GUI Windows and tabsOpening windowCentre window is the main input array. This behaves much like a typical spread sheet.- Copy and paste can be applied to individual cells, cell groups, entire rows or columns.- Rows can be deleted or inserted.The array is used to input the Frequency, Amplitude , Phase, and Synchronous output data.The column data is predefined and differs depending on the selected operating mode:Tone buffer(s) modeOne or more tables of 256 frequencies/amplitude/phase (F/A/P) values.∙Columns display the Frequency, Amplitude and Phase values.This is repeated for each of the 4 channels.∙Rows display the buffer entry. Up to 256 max lines per buffer.Array values can be entered directy into the GUI array or copied from an Excel spread sheet. Image files (s) modeOne or more files containing many frequencies/amplitude/phase/sync data points.∙Columns display the Frequency, Amplitude and Phase values PLUS a 12bit wide digital output register and two synchronous output DACs.The F/A/P data is repeated for each of the 4 channels.∙Rows display the image point entry.Image mode is useful for generating larger more complex frequency scan patterns.Values can be entered directy into the GUI array or data copied from an Excel spread sheet .For both modes, the data in selected cells within a column can be auto filled or interpolated.1: Signal Path tabMain purpose this tab is to set the RF power limits and enable RF power amplifer(s) that are connectedto the control outputs of the iMS4 (connector J5 or J6)Overview: Output Power control1.1: The 10-bit Amplitude values specified for each frequency point in the Image File or Tone Buffer.This value is multiplied by a Array Compensation factor stored in acalibration look up table (LUT).The LUT can be bypassed if required.The LUT is applied by default.1.2: DDS Power Level.8-bit non-volatile digital pot.GUI slider control is providedin the Signal Path tab1.3: Amplitude Control Source for the output RF mixers.Selection and slider optionsare provided under theSignal Path tabA typical selection is Wiper 1,which is a 8-bit non-volatiledigital pot with GUI slider controlThe optimum slider settings will depend on the connected RF power amplifier and AO device. Recommended values will be provided on the AO test data sheet supplied with the iMS4- Sliders values will increment/decrement in steps of 0.1 by using the up-down arrow keysSignal Path tab cont’dIn a typical system, the iMS4- will be the frequency source to a power amplifer(s). This in turn is connected to the AO modulator, frequency shifter , deflector or tuneble filter.Depending on the amplifier model, the iMS4- will provide the enable or Gate signal to the external power amplifier(s).Amplifer Enable controlsToggle Buttons, as shown Turn Green when activeExamples:2: Compensation tabA calibration or compensation look-up-table (LUT) contains frequency specific phase and amplitude data. It may be applied to Image and Tone Buffer frequency points in order to :a: to compensate for amplitude non-linearitiesb: apply a predefined phase shift between adjacent RF channels *.* For beam steered AO deflectors with multiple RF inputs, a frequency dependent phase shift “steers”the acoustic column in crystal. This optimizes the Bragg angle relationship resulting in higher effiency across the scan angle. (see App Note “Beam Steered AO Deflectors”)∙LUT values are AO device specific.∙LUT tables can be generated in Excel and converted to the correct format for the GUI. (The Compensation Functions window of the present GUI release is not active)Step 1: Import the desired LUT tableA graphic representation of the selected LUT data will appear in the panel e.g. phaseStep 2: DOWNLOAD into iMS4Download will not abort if no iMS4 is connected.3: Calibration tab (Single Tone output)This mode does not use the input array.Values are controlled using the sliders.The same frequency , amplitude and phase increment are applied across all channels(Channel 1 is always zero phase)Use this mode to check basic iMS4 operation and/or initial AO device alignment.Click Calibration tab on right side toolbarAdjust sliders to the desired value.Use with caution.The Slider limits are fixed and may exceed the range of any connected power amplifier and AO device. The Compensation LUT values are bypassed.Click the large RED button to activate . This will change to Green (arrowed).Click again to disable. It will toggle back to RED.4: Player Configuration tabThese functions apply to the Image File output.e.g. Choice of Trigger and Clock Source.Select the active edge for external clock and/or trigger.Action at the end of the Image play.Check boxes allow selective disabling of the Image mode LUT compensation.WHEN UNCHECKED:- Image point amplitude value is multiplied by 100%- Phase offset = 0 deg all frequencies, all channels.5: Image Play controlTool bar buttonsTo Start image play(Reserved for future use)Stop at end of current Image playStop immediatelyEmergencey Stop, reducing RF power controls to Zero %and disabling any connected power ampsExample 1: Image Mode10 point image on Channel 1 and Channel 2 only.Linear frequency scan : 60-100MHz100% amplitudeCompensation LUT appliedSynchronous output at mid-scan point, data = 255Internal Clock, No trigger, Repeated continuous outputiMS4 only. No connected power amps.1: Enter Number of Image Points2: Input Channel1 frequency end pointsPoint 0, input 60.00 MHz, Point 9, input 100.00 MHzClick on the column header to highlight the cells and right click to reveal the options window. Choose Interpolate to fill in incrementing values between the start and end point frequencies. 3: Input Channel1 AmplitudeClick on the column header to highlight the amplitude cells.Enter 100. A 100% value will auto fill down all highlighted cells.Navigate away from the amplitude column to complete4: Copy to Channel 2Left click cell: Channel1_Frequency_Row 0 to select and highlightNavigate to cell: Channel1_Amplitude_Row 9. Shift- left click this cell.This will select the Frequency and Amplitude data for Channel 1Copy & Paste into Channel 25: Set Synchronous digital output (outputs through connecter J7)Use the lower slider to navigate to the Sync Data columnsInput ‘FF’ at the desired cell(s)Ensure Digital Sync Output Source field is set to ImageDigital[Note for iMS4-L users. Sync data can only applied using the Compensation LUT . In this case the Digital Sync Output Source is set to LookUpFieldCh1]6: Apply Compensation table ∙Import the desired LUT table∙DOWNLOAD into iMS47: Set Player Configuration Image Clock Source: Internal Image Trigger: No TriggerImage Repeats : Repeat forever8: Set power levelsIn this exampleDDS power to 63%Amplitude Control Source is Wiper 1 Wiper 1 setting = 80%9: Start PlayExample 2: Tone Buffer Mode16 tones only.Channel 1: Linear frequency increments, 150-90MHzChannel 1: Linear amplitude slope : 100 – 70%Channel 2: Static frequency increments, 120MHzChannel 2: Static amplitude : 55%No Compensation LUT appliediMS4 only. No connected power amps.At output, Tones selected though the GUI software (USER)1: Click in the Tone Buffer window . Edit the name if desired.or click “ + ” to add another buffer fileThe input array will fill with 256 rows = 256 x 4 channel F/A/P data pointsNot all 256 need be used.In this example we are not applying compensation table.2: Uncheck Amplitude Compensation box, Phase Compensation box3: In the Control Source, select User ** Other options are External and Extended ExternalThe 256 tone buffer (LTB) locations are arranged in 16 pages.Within each page, the 16 F/A/P Tones may be rapidly addressed using 4x external LTB address lines on connector J8. See IMS4- manual for details4: Channel1 Frequency, enter end point valuesTone 0, enter 150.00 MHz 9 (Start) , Tone 15, enter 90.00 MHz (End) 5: Channel1 Amplitude , enter end point valuesTone 0, enter 100 %, Tone 15, enter 70 %6: Channel2 Frequency, enter end point valuesTone 0, enter 120.00 MHz 15 (Start) , Tone 15, enter 120.00 MHz (End) 7: Channel2 Amplitude, enter end point valuesTone 0, input 55 %, Tone 15, input 55 %Use the Interploate feature to fill the remainimg 14 cellsFor each coloum:- Left click on Start cell- Hold down the shift key- Navigate to the end cell and left click(This should select and highlight all 16 cells)- Right click to open sub window- Select Intepolate8: Set power levelsIn this exampleDDS power to 63%Amplitude Control Source is Wiper 1 Wiper 1 setting = 80%9: Enable output10: Tone SelectionClick on then desired Row to output that frequency set11: To disable outputClick as shownExample 3: Calibration ModeUse internal amplitude control, Wiper 1. Apply cautious power settings for initial use. Set slider of AO centre freq e.g. 80MHz External Amplifier connected to J61: Set power level limitsIn this exampleDDS power 40%Amplitude Control Source is Wiper 1 Wiper 1 setting = 30%2: Enable amplifier3: Select Calibration tabAdjust sliders as requiredClick the large RED button to activate . This will change to Green. Click again to disable. It will toggle back to RED.。
VIAVI T-BERD MTS-5800产品说明书

QUICK CARDEthernet RFC 2544 Layer 2 TrafficThis quick card describes how to configure and run an RFC 2544 Layer 2 Traffic Test for Metro Ethernet service activation.•T-BERD/MTS 5800 equipped with the following:o BERT software release V30.1.0 or greatero C510M1GE test option for 10 Megabit to 1 Gigabit Etherneto C510GELAN test option for 10 Gigabit Etherneto C525GE test option for 25 Gigabit Etherneto C540GE test option for 40 Gigabit Etherneto C550GE test option for 50 Gigabit Etherneto C5100GE test option for 100 Gigabit Ethernet•Optical Transceiver supporting the line rate to be tested(SFP or QSFP)•Cables to match the optical transceiver and the line under test•Fiber optic inspection microscope (P5000i or FiberChek Probe)•Fiber optic cleaning supplies Figure 1: Equipment Requirements1.Press the Power button to turn on theT-BERD.2.Press the Test icon at the top of thescreen to display the Launch Screen.ing the Select Test menu, Quick Launchmenu, or Job Manager, launch the EthernetRFC 2544 Layer 2 Traffic test on Port 1 for the desired rate. For Example:Ethernet►1GigE Optical ►RFC 2544 ►L2 Traffic ►P1 Terminate.4.Tap the button next to “Start a NewConfiguration (reset to defaults)”Figure 2: Launch ScreenQUICK CARD►The following Information is needed to configure the test:•VLAN ID, if VLAN tagging is used.•Maximum Transmission Unit (MTU), if Jumbo Frames are used.•Committed Information Rate (CIR)•Pass/Fail Threshold for Throughput, Frame Loss, Latency and Jitter1.Tap the button to display theL2 Network Settings screen.2.If you are testing a VLAN, setEncapsulation to VLAN and enter yourVLAN ID.3.Tap the button twice to displaythe Select Tests screen.4.Select the Throughput, Latency, FrameLoss, and Packet Jitter tests.5.Tap the button to display theUtilization screen.6.Set Max Bandwidth to the CommittedInformation Rate (CIR).7.Tap the button to display theFrame Lengths screen.Figure 4: Work OrderFigure 6: Select TestsFigure 5: L2 Network SettingsQUICK CARD8.Select the 1st, 4th, and 8th Frame Lengths.9.If the MTU is greater than 1518 (1522 with VLAN tagging), also enter and select the frame length of the MTU.10.Deselect (uncheck) all other frame lengths.11.Tap the button four times to display the Test Thresholds screen.12.Check all boxes for which a Pass/Fail Threshold is known. Enter the Threshold for each selection.13.Tap the button 3 times to display theRun J-QuickCheck screen.Figure 8: Frame LengthsFigure 9: Test ThresholdsFigure 10: J-QuickCheckQUICK CARD►For Optical Interfaces:e the VIAVI P5000i or FiberChek Probemicroscope to inspect both sides of everyconnection being used (SFP, attenuators,patch cables, bulkheads)o Focus the fiber on the screen.o If it appears dirty, clean the fiber end-face and re-inspect.o If it appears clean, run the inspection test.o If it fails, clean the fiber and re-runinspection test. Repeat until it passes.2.Insert desired Optical Transceiver into thePort 1 SFP or QSFP slot on the top of theT-BERD.3.If necessary, insert optical attenuators intothe SFP TX and/or RX ports.4.Connect the SFP to the port under testusing a jumper cable compatible with theline under test.►For Copper 10/100/1000BASE-T interfaces: Connect the 10/100/1000 RJ-45 jack tothe port under test using CAT 5E or bettercable.►Verify that Local Port status UP and Full Duplex (FD)►Tap the button.►Verify that the Remote Loop is recognized, and that Measured Throughput is greater than or equal to the Committed Information Rate.►Tap the button to display the Run RFC 2544Tests screen. Figure 12: Local Port statusFigure 11: Inspect Before You Connect Figure 13: Run J-QuickCheckQUICK CARD© 2022 VIAVI Solutions, Inc,Product specifications and descriptions in this Contact Us+1 844 GO VIAVI(+1 844 468-4284)1.Tap the button three times to display the Report screen.2.Tap .3.Tap buttons three times toclose the report and exit the RFC 2544 test.1.Tap the button.2.Wait for the test to complete and verify that all tests pass or complete as indicated by agreen or blue checkmark.E RE P ORTFigure 14: Run RFC 2544 TestsFigure 15: Create ReportFigure 16: Exit。
VisualATE软件手册

主程序界面
用户界面
测试主程序边 界界面
测试模块编辑 界面
Map分析界面
……
数据分析逻辑
业务逻辑
硬件控制逻辑
界面显示逻辑
界面操作逻辑
……
采集的数 据
控制数据
底层数据
GPIB驱 动
MTS737A 硬件驱动
GPIB驱 动
TTL驱动
软件系统结构图
在本手册中,将分为五个章节来对 VISUALATE 软件系统描述。第一章到第四章 将分别描述系统架构、测试程序的编写、测试语句的可视化编程、Map 分析与数 据保存,在第五章将给出一个 VISUALATE 软件系统得使用实例。
数字测试部分.............................................................................................................................45 其他的测试语句设置.................................................................................................................69
MTS737X VisalATE软件手册
工具栏选项
作用 分别为两个工位载入 tst 文件 弹出测试程序编辑向导 弹出测试程序(tst 文件) 编辑界面 弹出测试模块(dcp 文件) 编辑界面 将当前编辑的 tst 文件保存 测试控制 用户登录界面 进入数据保存设置界面 Map 分析界面 数据清空 打印 系统复位
三.测试语句的可视化编程 ..................................................... 23
VIAVI Solutions T-BERD MTS 8000和6000A产品说明书

T-BERD/MTS 8000 and 6000AFIBER CHARACTERIZATIONATTENUATION PROFILE REFERENCINGPROCEDUREQUICK GUIDEThe following procedure describes how to perform a AP referencing with the use of an MTAU and a AP module into a T-BERD/MTS 8000V2. This measurement is done to ensure that the broadband source is taken into account for an accurate qualification of the fiber to test. This procedure is a two ended testNote 1: Both products must be at the same locationNote 2: it is possible to apply a new reference to an existing CD resultPlease read the entire procedure BEFORE starting.Inspect and clean connectorsBefore connecting a fiber into a test module or fiber panel, inspect and clean the bulkhead and the fiber jumper connectors.1. Connect the P5000i video inspection scope to both units USB port (any)2.3.4.5.Activate the Microscope function on both units by touching twice with your finger or stylus.6. Use the P5000i video inspection scope to verify the connector quality.7. Use appropriate cleaning material (e.g. IBC™ cleaner, cotton swab, dust air sprays, etc...) and re-inspect to confirm. Activating the AP function on the T-BERD/MTS 8000 unit1.2.3. Activate the test functions by touching twice with your finger or stylus. Wait for the tuning process of the1. tab2. SelectConnecting both test sets1. Inspect and clean connectors of the fiber jumpers, the COM port of the T-BERD/MTS 8000 and the OTDR port of theT-BERD/MTS 6000A using the P5000i inspection scope.2. Connect the fiber jumper 1 to the T-BERD/MTS 8000 COM port of the MTAU module and to the mating adapter.3. Connect the fiber jumper 2 to the T-BERD/MTS 6000A OTDR module and to the mating adapter.Patchcord inspection Bulkhead and test port inspectionT-BERD/MTS 8000T-BERD/MTS 6000A1.activate the BBS function 2.3. Touch the soft key to turn the source on4. Touch the softkey to position the test mode as AP1. 2. Touch the tab.3. SelectNote: BBS serial number is displayed on the T-BERD/MTS6000A Results page6. Confirm by pressing YES when the message pops up.Note: A message “valid Reference” is displayed in green. If not, verify proper connector cleanliness and interconnections then restart referencing processSaving a reference file on the T-BERD 80001. Once the reference measurement is done, press key2.Select3.Enter the source serial number under4.Press the key5. Give it a namexxx being the BBS serial number, so that you know itcontains the reference for T-Berd 6000A SN xxx.Note 1: This file (ex: T-BERD6000A CD REF SN xxx.ocd” into your T-BERD 8000 unit.Note 2: Repeat the referencing and saving steps for as many T-BERD 6000A and T-BERD 8000 units Note 3: It’s recommended to save the reference files into a dedicated directory for easy locationLoading a reference file into a T-BERD 80001. Press the “file” hard key2.Select the directory where the reference files are located. For example:3.Highlight the file that has the requested T-BERD/MTS 6000A reference4.Press the soft key5. Select6.Note: You now see 2 reference boxes On says and that shows the current reference loaded into the test unit. Thelower box says and that shows the reference information for the trace that is currently loaded (your new reference). It also shows the filename so you can see if it is “T-BERD6000A CD REF SN xxx.ocd”, for example.7. Under the list, select8. Press the soft key9. The message appears. SelectNote: The date and s/n of the reference appear into the list. You know the new reference is loaded.10. Follow the above steps to change the reference again。
iMX Developer’s Kit s 使用摄像头的指南说明书

Copyright 2021 © Embedded Artists ABUsing a Cameraoni MX Developer’s Kit sEmbedded Artists ABRundelsgatan 14SE-211 36 MalmöSwedenCopyright 2021 © Embedded Artists AB. All rights reserved.No part of this publication may be reproduced, transmitted, transcribed, stored in a retrieval system, or translated into any language or computer language, in any form or by any means, electronic, mechanical, magnetic, optical, chemical, manual or otherwise, without the prior written permission of Embedded Artists AB.DisclaimerEmbedded Artists AB makes no representation or warranties with respect to the contents hereof and specifically disclaim any implied warranties or merchantability or fitness for any particular purpose. Information in this publication is subject to change without notice and does not represent a commitment on the part of Embedded Artists AB.FeedbackWe appreciate any feedback you may have for improvements on this document. Send your comments by using the contact form: /contact.TrademarksAll brand and product names mentioned herein are trademarks, services marks, registered trademarks, or registered service marks of their respective owners and should be treated as such.Table of Contents1Document Revision History (4)2Introduction (5)2.1Conventions (5)3Before getting started (6)3.1Linux distributions (6)3.2Yocto configuration (6)4USB interface (7)4.1Camera (7)4.2Supported boards (7)4.3Instructions (7)5MIPI/CSI-2 interface (10)5.1Camera (10)5.2Supported boards (10)5.3Instructions (10)6Parallel interface (13)6.1Camera (13)6.2Supported boards (13)6.3Instructions (13)1 Document Revision History2 IntroductionThis document describes how to connect a camera to Embedded Artists i.MX 6/7/8 based Develop er’s Kits. Three different interfaces are described: MIPI/CSI-2, Parallel, and USB. Not all boards support all interfaces.Additional documentation you might need is.•The Getting Started document for the board you are using.•The Adding Displays to iMX Developer's Kits document about displays and how to use them2.1 ConventionsA number of conventions have been used throughout to help the reader better understand the content of the document.Constant width text– is used for file system paths and command, utility and tool names.3 Before getting started3.1 Linux distributionsThe instructions in this document have been tested on Embedded Artists 4.9.11 distribution and later.3.2 Yocto configurationGStreamer will be used to capture video feed from a camera and v4l-utils will be used to query a camera interface.From the 4.14.78 distribution and when using the ea-image-base image all packages are already included. If you are using an earlier version or different image you have to add the below packages to your conf/local.conf file.4 USB interface4.1 CameraA Logitech QuickCam Pro 9000 camera was used when testing a camera via the USB interface.Figure 1 - Logitech QuickCam Pro 90004.2 Supported boardsThe following boards support USB based cameras.•iMX6 SoloX COM•iMX6 Quad COM•iMX6 DualLite COM•iMX6 UltraLite COM•iMX7 Dual COM•iMX7 Dual uCOM•iMX7ULP uCOM•iMX8M Mini uCOM•iMX8M Nano uCOM•iMX8M Quad COM4.3 Instructions1. Connect the camera to the USB host port on the carrier board as shown in Figure2.Figure 2 - USB Host connector2. The camera will be detected and you will see output in the console similar to below.usb 1-1.1: USB disconnect, device number 3usb 1-1.3: new high-speed USB device number 4 using ci_hdrcuvcvideo: Found UVC 1.00 device <unnamed> (046d:0990)input: UVC Camera (046d:0990) as /devices/soc0/soc/2100000.aips-bus/b/ci_hdrc.1/usb1/1-1/1-1.3/1-1.3:1.0/input/input1 usbcore: registered new interface driver uvcvideoUSB Video Class driver (1.1.1)usb 1-1.3: Warning! Unlikely big volume range (=3072), cval->res is probably wrong.usb 1-1.3: [5] FU [Mic Capture Volume] ch = 1, val = 4608/7680/1 usbcore: registered new interface driver snd-usb-audio3. Use v4l2-ctl to find out on which video interface the camera is attached. In this example four interfaces are available and the USB camera (UVC Camera) is attached to /dev/video3.# v4l2-ctl --list-devicesi.MX6S_CSI (platform:2214000.csi):/dev/video1i.MX6S_CSI (platform:221c000.csi):/dev/video2pxp (pxp_v4l2_out):/dev/video0UVC Camera (046d:0990) (usb-ci_hdrc.1-1.3):/dev/video34. Use the command below to start capturing a video stream and show it on a display. If you don’t havea display, go to step 5 and take a snapshot instead.For all iMX6 and iMX7 based boards:For iMX8M based boards:5. Use the command below to take a snapshot from the camera. The snapshot is stored as a jpeg file. For all iMX6 and iMX7 based boards:For iMX8M based boards:6. In the above examples a resolution of 640x480 and frame rate of 30 fps was used. You can query the camera to see which resolutions and frame rates it supports for different pixel formats. Only a portion of the output from the command is shown below.Using a Camera on i MX Developer’s Kit s Page 105 MIPI/CSI-2 interface5.1 CameraThe Pcam 5C camera from Digilent was used when testing a camera with MIPI interface. This camera is using the Omnivision OV5640 image sensor. Two data lanes are connected. The camera comeswith a (about) 200 mm long, 20-pos, 1 mm pitch flat cable.Do not extend the cable length more than this. The total length of the MIPI/CSI-2 trace lengthshould be kept less than 200 mm. This is due to the high frequency signals on the MIPI/CSI-2 interface.Figure 3 - Digilent Pcam 5C (OV5640)5.2 Supported boardsThe following boards support cameras with MIPI/CSI-2 interface.•iMX6 Quad COM•iMX6 DualLite COM•iMX7 Dual COM•iMX7 Dual uCOM•iMX8M Mini uCOM•iMX8M Nano uCOM•iMX8M Quad COM5.3 Instructions1. Connect the camera to the J20 connector if you are using COM Carrier Board V1 or to the J32connector if you are using COM Carrier Board V2. Figure 4 and Figure 5 below are for COM CarrierBoard V1, but it looks similar for COM Carrier Board V2. The exposed pads on the cable shall bemounted towards the nearby PCB edge. Figure 4 illustrates the exposed pads. Figure 5 illustrates the side of the cable without exposed pads.Using a Camera on i MX Developer’s Kit s Page 11Figure 4 - Cable inserted into J20 (back)Figure 5 - Cable inserted into J20 (front)2. Boot into the u-boot. We need to change to a different dtb (device tree) file before booting into Linux.This new dtb file enables the MIPI/CSI-2 interface and adds the ov5640 camera to the I2C bus. In this example we are using an iMX6 Quad COM board. For other boards the name of the dtb file will bedifferent. C hange “imx6qea-com-kit” to the name of the board you are using, for example, “imx7dea-com-kit” if you are using the iMX7 Dual COM board.=> setenv fdt_file imx6qea-com-kit-ov5640.dtb=> saveenvIf you want to see how the device file looks like you can find it on our GitHub repository.https:///embeddedartists/linux-imx/blob/ea_4.9.11_1.0.0/arch/arm/boot/dts/imx6qea-com-kit-ov5640.dts3. Reset the board and boot into Linux. When you have logged into Linux run the command below to see if the camera has been found. You should see the m essage “camera ov5640_mipi is found”.4. Use v4l2-ctl to list available video interfaces. In this example three interfaces are listed, but no detailed information about each interface. The camera is in this case available on /dev/video0.5. Use the command below to start capturing a video stream and show it on a display. If you do n’t havea display, go to step 6 and take a snapshot instead.For all iMX6 and iMX7 based boards:For iMX8M based boards:6. Use the command below to take a snapshot from the camera. The snapshot is stored as a jpeg file. For all iMX6 and iMX7 based boards:For iMX8M based boards:6 Parallel interface6.1 CameraThe Waveshare OV5640 Camera Board was used when testing a camera with parallel interface. This camera is using the Omnivision OV5640 image sensor. This sensor supports both the MIPI/CSI-2 and parallel camera interface. On the Waveshare board, the parallel interface is connected.Figure 6 – Waveshare OV5640 Camera BoardPlease note that this board cannot be connected directly to the connector on EmbeddedArtists COM Carrier board. You need to make an adapter between the camera board and the COM Carrier board.Also note that the camera must be supplied with a 24 MHz clock with 2.8V voltage level. A3.3V logic level clock will create disturbances in the camera. A local 24 MHz oscillator,powered by 2.8V, can be placed on the adapter between the Waveshare module and COMCarrier board.Note that the parallel camera interface cannot be extended more than 100 mm from theMXM3 connector. Depending on pixel clock frequency, it can even be shorter than this. Ingeneral, Embedded Artists recommend using the MIPI/CSI-2 interface when connecting acamera.6.2 Supported boardsThe following boards support cameras with parallel interface.•iMX6 SoloX COM•iMX6 Quad COM•iMX6 DualLite COM•iMX6 UltraLite COMiMX7 Dual COM and iMX7 Dual uCOM boards also support parallel interface, but not in combination with the Embedded Artists' COM Carrier Board.6.3 InstructionsNOTE: If you are using iMX6 Quad COM or iMX6 DualLite COM you cannot have thecamera inserted into the J21/J34 during a reset / power-cycle. The board will enter USB boot mode and not boot from eMMC. You can boot into u-boot, insert the camera and thencontinue and boot into Linux.Contact Embedded Artists for more details.1. Connect the camera to the J21 connector if you are using COM Carrier Board V1 or to the J34 connector if you are using COM Carrier Board V2. Figure 7 and Figure 8 below are for COM Carrier Board V1, but it looks similar for COM Carrier Board V2.Figure 7 - Cable inserted into J21 (back)Figure 8 - Cable inserted into J20 (front)2. Boot into the u-boot. We need to change to a different dtb (device tree) file before booting into Linux. This new dtb file enables the parallel interface and adds the ov5640 camera to the I2C bus. In this example we are using an iMX6 SoloX COM board. For other boards the name of the dtb file will bedif ferent. Change “imx6sxea-com-kit” to the name of the board you are using, for example, “imx6qea-com-kit” if you are using the iMX6 Quad COM board.If you want to see how the device file looks like you can find it on our GitHub repository.https:///embeddedartists/linux-imx/blob/ea_4.9.11_1.0.0/arch/arm/boot/dts/imx6sxea-com-kit-ov5640-pl.dts3. Reset the board and boot into Linux. When you have logged into Linux run the command below to see if the camera has been found. You should see the message “camera ov5640, is found”.4. Use v4l2-ctl to list available video interfaces. In this example three interfaces are listed, but no detailed information about each interface. The camera is in this case available on /dev/video1.5. Use the command below to start capturing a video stream and show it on a disp lay. If you don’t havea display, go to step 6 and take a snapshot instead.6. Use the command below to take a snapshot from the camera. The snapshot is stored as a jpeg file.。
VIAVI Fusion JMEP智能SFP千兆以太网收发器手册说明书

手册VIAVIFusion JMEP 智能 SFP用于测试、开通和性能监控的千兆以太网收发器优点y 简单易用,可轻松部署在现有网络 SFP 端口中 y 可将网络端口变为服务保障工具,针对任何千兆以太网实现以太网操作、管理和维护 (OAM) y 可简化测试和故障排查程序,减少设备升级、上门服务次数,并缩短平均维修时间 (MTTR) y 与 VIAVI MTS 测试产品组合和屡获殊荣的 Fusion EtherASSURE ™ 集中式测试解决方案兼容 y 无需使用额外的仪器即可跨移动回传网络进行监控特性y 与 RFC 2544 和 Y .1564 测试方法完全兼容 y 可激活测试环回 (L2/L3)y 可使用 Y .1731/TWAMP-Light (RFC 5357) 监控内联性能 y 可测量吞吐量、可用性、帧丢失、帧延迟和帧延迟变化 y 可启用 OAM 802.1ag 以实现故障隔离应用y 3G 、4G 、L TE 和小型基站以太网移动回传的服务激活与保障 y 以太网商业服务 SLA 验证和保障 y 同步以太网 (SyncE) 端点VIAVI JMEP 智能 SFP 是一款第三代一千兆以太网智能 SFP 收发器,减少了额外的网络检测需求。
第三代(或 JMEP3)收发器可以无缝地部署到现有的网络设备中。
它们为网络运营商和服务提供商提供了远程可测试性点,可实现性能有保障的业务交付,并提高现有网络基础设施的价值。
JMEP3 设备提供了额外的远端测试和监控功能。
它们还可通过 Y .1564 流量生成模拟网络上多个同时出现的负载,以及对吞吐量一天中随着时间变化的情况进行突发流监测,突发流Microburst 的时间颗粒度支持到 1 毫秒。
微突发检测JMEP3 的一项关键功能是微突发检测。
在 TCP 网络中,可能会出现短时间内的流量突发(例如,路由器上多个端口的超额订阅)。
这些突发可能会导致重传/重设/丢包,所有这些都会对应用性能产生巨大影响,例如,VoL TE 语音质量不良。
泰登TMX-0404SDI2 4×4高清数字视频追踪矩阵切换器说明书
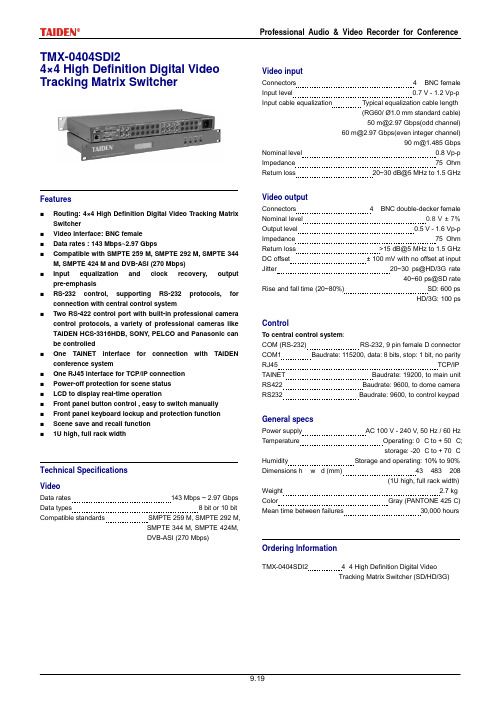
Professional Audio & Video Recorder for Conference TMX-0404SDI24×4 High Definition Digital VideoTracking Matrix SwitcherFeatures■Routing: 4×4 High Definition Digital Video Tracking Matrix Switcher■Video interface: BNC female■Data rates : 143 Mbps~2.97 Gbps■Compatible with SMPTE 259 M, SMPTE 292 M, SMPTE 344 M, SMPTE 424 M and DVB-ASI (270 Mbps)■Input equalization and clock recovery, output pre-emphasis■RS-232 control, supporting RS-232 protocols, for connection with central control system■Two RS-422 control port with built-in professional camera control protocols, a variety of professional cameras like TAIDEN HCS-3316HDB, SONY, PELCO and Panasonic can be controlled■One TAINET interface for connection with TAIDEN conference system■One RJ45 interface for TCP/IP connection■Power-off protection for scene status■LCD to display real-time operation■Front panel button control , easy to switch manually■Front panel keyboard lockup and protection function■Scene save and recall function■1U high, full rack widthTechnical SpecificationsVideoData rates 143 Mbps ~ 2.97 Gbps Data types 8 bit or 10 bit Compatible standards SMPTE 259 M, SMPTE 292 M,SMPTE 344 M, SMPTE 424M,DVB-ASI (270 Mbps) Video inputConnectors 4 × BNC female Input level 0.7 V - 1.2 Vp-p Input cable equalization Typical equalization cable length(RG60/ Ø1.0 mm standard cable)************(oddchannel)************(evenintegerchannel)************* Nominal level 0.8 Vp-p Impedance 75 Ohm Return loss 20~*****************Video outputConnectors 4 × BNC double-decker female Nominal level 0.8 V ± 7% Output level 0.5 V - 1.6 Vp-p Impedance 75 Ohm Return loss >***************** DC offset ± 100 mV with no offset at input Jitter 20~30 ps@HD/3G rate40~60 ps@SD rate Rise and fall time (20~80%) SD: 600 psHD/3G: 100 psControlTo central control system:COM (RS-232) RS-232, 9 pin female D connector COM1 Baudrate: 115200, data: 8 bits, stop: 1 bit, no parity RJ45 TCP/IP TAINET Baudrate: 19200, to main unit RS422 Baudrate: 9600, to dome camera RS232 Baudrate: 9600, to control keypadGeneral specsPower supply AC 100 V - 240 V, 50 Hz / 60 Hz Temperature Operating: 0 °C to + 50 °C;storage: -20 °C to + 70 °C Humidity Storage and operating: 10% to 90% Dimensions h × w ×d (mm) 43 × 483 × 208(1U high, full rack width) Weight 2.7 kg Color Gray (PANTONE 425 C) Mean time between failures 30,000 hoursOrdering InformationTMX-0404SDI2 4×4 High Definition Digital VideoTracking Matrix Switcher (SD/HD/3G)Tracking Matrix SwitcherFeatures■Routing: 8×4 High Definition Digital Video Tracking Matrix Switcher■Video interface: BNC female■Data rates : 143 Mbps~2.97 Gbps■Compatible with SMPTE 259 M, SMPTE 292 M, SMPTE 344 M, SMPTE 424 M and DVB-ASI (270 Mbps)■Input equalization and clock recovery, output pre-emphasis■RS-232 control, supporting RS-232 protocols, for connection with central control system■Two RS-422 control port with built-in professional camera control protocols, a variety of professional cameras like TAIDEN HCS-3316HDB, SONY, PELCO and Panasonic canbe controlled■One TAINET interface for connection with TAIDEN conference system■One RJ45 interface for TCP/IP connection■Power-off protection for scene status■LCD to display real-time operation■Front panel button control , easy to switch manually■Front panel keyboard lockup and protection function■Scene save and recall function■1U high, full rack widthTechnical SpecificationsVideoData rates 143 Mbps ~ 2.97 Gbps Data types 8 bit or 10 bit Compatible standards SMPTE 259 M, SMPTE 292 M,SMPTE 344 M, SMPTE 424M,DVB-ASI (270 Mbps) Connectors 8 × BNC female Input level 0.7 V ~ 1.2 Vp-p Input cable equalization Typical equalization cable length(RG60/ Ø1.0 mm standard cable)************(oddchannel)************(evenintegerchannel)************* Nominal level 0.8 Vp-p Impedance 75 Ohm Returnloss20~*****************Video outputConnectors 4 × BNC double-decker female Nominal level 0.8 V ± 7% Output level 0.5 V ~ 1.6 Vp-p Impedance 75 Ohm Return loss >***************** DC offset ± 100 mV with no offset at input Jitter 20~30 ps@HD/3G rate40~60 ps@SD rate Rise and fall time (20~80%) SD: 600 psHD/3G: 100 psControlTo central control system:COM (RS-232) RS-232, 9 pin female D connector COM1 Baudrate: 115200, data: 8 bits, stop: 1 bit, no parity RJ45 TCP/IP TAINET Baudrate: 19200, to main unit RS422 Baudrate: 9600, to dome camera RS232 Baudrate: 9600, to control keypadGeneral specsPower supply AC 100 V - 240 V, 50 Hz / 60 Hz Temperature Operating: 0 °C to + 50 °C;storage: -20 °C to + 70 °C Humidity Storage and operating: 10% to 90% Dimensions h × w ×d (mm) 43 × 483 × 208(1U high, full rack width) Weight 2.8 kg Color Gray (PANTONE 425 C) Mean time between failures 30,000 hoursOrdering InformationTMX-0804SDI2 8×4 High Definition Digital VideoTracking Matrix Switcher (SD/HD/3G)Tracking Matrix SwitcherFeatures■Routing: 8×8 High Definition Digital Video Tracking Matrix Switcher■Video interface: BNC female■Data rates : 143 Mbps~2.97 Gbps■Compatible with SMPTE 259 M, SMPTE 292 M, SMPTE 344 M, SMPTE 424 M and DVB-ASI (270 Mbps)■Input equalization and clock recovery, output pre-emphasis■RS-232 control, supporting RS-232 protocols, for connection with central control system■Two RS-422 control port with built-in professional camera control protocols, a variety of professional cameras like TAIDEN HCS-3316HDB, SONY, PELCO and Panasonic canbe controlled■One TAINET interface for connection with TAIDEN conference system■One RJ45 interface for TCP/IP connection■Power-off protection for scene status■LCD to display real-time operation■Front panel button control , easy to switch manually■Front panel keyboard lockup and protection function■Scene save and recall function■1U high, full rack widthTechnical SpecificationsVideoData rates 143 Mbps ~ 2.97 Gbps Data types 8 bit or 10 bit Compatible standards SMPTE 259 M, SMPTE 292 M,SMPTE 344 M, SMPTE 424M,DVB-ASI (270 Mbps) Connectors 8 × BNC female Input level 0.7 V ~ 1.2 Vp-p Input cable equalization Typical equalization cable length(RG60/ Ø1.0 mm standard cable)************(oddchannel)************(evenintegerchannel)************* Nominal level 0.8 Vp-p Impedance 75 Ohm Returnloss20~*****************Video outputConnectors 8 × BNC double-decker female Nominal level 0.8 V ± 7% Output level 0.5 V ~ 1.6 Vp-p Impedance 75 Ohm Return loss >***************** DC offset ± 100 mV with no offset at input Jitter 20~30 ps@HD/3G rate40~60 ps@SD rate Rise and fall time (20~80%) SD: 600 psHD/3G: 100 psControlTo central control system:COM (RS-232) RS-232, 9 pin female D connector COM1 Baudrate: 115200, data: 8 bits, stop: 1 bit, no parity RJ45 TCP/IP TAINET Baudrate: 19200, to main unit RS422 Baudrate: 9600, to dome camera RS232 Baudrate: 9600, to control keypadGeneral specsPower supply AC 100 V - 240 V, 50 Hz / 60 Hz Temperature Operating: 0 °C to + 50 °C;storage: -20 °C to + 70 °C Humidity Storage and operating: 10% to 90% Dimensions h × w ×d (mm) 43 × 483 × 208(1U high, full rack width) Weight 3.0 kg Color Gray (PANTONE 425 C) Mean time between failures 30,000 hoursOrdering InformationTMX-0808SDI2 8×8 High Definition Digital VideoTracking Matrix Switcher (SD/HD/3G)TMX-1604SDI216×4 High Definition Digital Video Tracking Matrix SwitcherFeatures■Routing: 16×4 High Definition Digital Video Tracking Matrix Switcher■Video interface: BNC female■Data rates : 143 Mbps~2.97 Gbps■Compatible with SMPTE 259 M, SMPTE 292 M, SMPTE 344 M, SMPTE 424 M and DVB-ASI (270 Mbps)■Input equalization and clock recovery, output pre-emphasis■RS-232 control, supporting RS-232 protocols, for connection with central control system■Two RS-422 control port with built-in professional camera control protocols, a variety of professional cameras like TAIDEN HCS-3316HDB, SONY, PELCO and Panasonic canbe controlled■One TAINET interface for connection with TAIDEN conference system■One RJ45 interface for TCP/IP connection■Power-off protection for scene status■LCD to display real-time operation■Front panel button control , easy to switch manually■Front panel keyboard lockup and protection function■Scene save and recall function■1U high, full rack widthTechnical SpecificationsVideoData rates 143 Mbps ~ 2.97 Gbps Data types 8 bit or 10 bit Compatible standards SMPTE 259 M, SMPTE 292 M,SMPTE 344 M, SMPTE 424M,DVB-ASI (270 Mbps) Video inputConnectors 4 × BNC female Input level 0.7 V - 1.2 Vp-p Input cable equalization Typical equalization cable length(RG60/ Ø1.0 mm standard cable)************(oddchannel)************(evenintegerchannel)************* Nominal level 0.8 Vp-p Impedance 75 Ohm Returnloss20~*****************Video outputConnectors 4 × BNC double-decker female Nominal level 0.8 V ± 7% Output level 0.5 V - 1.6 Vp-p Impedance 75 Ohm Return loss >***************** DC offset ± 100 mV with no offset at input Jitter 20~30 ps@HD/3G rate40~60 ps@SD rate Rise and fall time (20~80%) SD: 600 psHD/3G: 100 psControlTo central control system:COM (RS-232) RS-232, 9 pin female D connector COM1 Baudrate: 115200, data: 8 bits, stop: 1 bit, no parity RJ45 TCP/IP TAINET Baudrate: 19200, to main unit RS422 Baudrate: 9600, to dome camera RS232 Baudrate: 9600, to control cameraGeneral specsPower supply AC 100 V - 240 V, 50 Hz / 60 Hz Temperature Operating: 0 °C to + 50 °C;storage: -20 °C to + 70 °C Humidity Storage and operating: 10% to 90% Dimensions h × w ×d (mm) 43 × 483 × 208(1U high, full rack width) Weight 3.0 kg Color Gray (PANTONE 425 C) Mean time between failures 30,000 hoursOrdering InformationTMX-0404SDI2 16×4 High Definition Digital VideoTracking Matrix Switcher (SD/HD/3G)TMX-1608SDI216×8 High Definition Digital Video Tracking Matrix SwitcherFeatures■Routing: 16×8 High Definition Digital Video Tracking Matrix Switcher■Video interface: BNC female■Data rates : 143 Mbps~2.97 Gbps■Compatible with SMPTE 259 M, SMPTE 292 M, SMPTE 344 M, SMPTE 424 M and DVB-ASI (270 Mbps)■Input equalization and clock recovery, output pre-emphasis■RS-232 control, supporting RS-232 protocols, for connection with central control system■Two RS-422 control port with built-in professional camera control protocols, a variety of professional cameras like TAIDEN HCS-3316HDB, SONY, PELCO and Panasonic canbe controlled■One TAINET interface for connection with TAIDEN conference system■One RJ45 interface for TCP/IP connection■Power-off protection for scene status■LCD to display real-time operation■Front panel button control , easy to switch manually■Front panel keyboard lockup and protection function■Scene save and recall function■1U high, full rack widthTechnical SpecificationsVideoData rates 143 Mbps ~ 2.97 Gbps Data types 8 bit or 10 bit Compatible standards SMPTE 259 M, SMPTE 292 M,SMPTE 344 M, SMPTE 424M,DVB-ASI (270 Mbps) Video inputConnectors 16 × BNC female Input level 0.7 V ~ 1.2 Vp-p Input cable equalization Typical equalization cable length(RG60/ Ø1.0 mm standard cable)************(oddchannel)************(evenintegerchannel)************* Nominal level 0.8 Vp-p Impedance 75 Ohm Returnloss20~*****************Video outputConnectors 8 × BNC double-decker female Nominal level 0.8 V ± 7% Output level 0.5 V ~ 1.6 Vp-p Impedance 75 Ohm Return loss >***************** DC offset ± 100 mV with no offset at input Jitter 20~30 ps@HD/3G rate40~60 ps@SD rate Rise and fall time (20~80%) SD: 600 psHD/3G: 100 psControlTo central control system:COM (RS-232) RS-232, 9 pin female D connector COM1 Baudrate: 115200, data: 8 bits, stop: 1 bit, no parity RJ45 TCP/IP TAINET Baudrate: 19200, to main unit RS422 Baudrate: 9600, to dome camera RS232 Baudrate: 9600, to control keypadGeneral specsPower supply AC 100 V - 240 V, 50 Hz / 60 Hz Temperature Operating: 0 °C to + 50 °C;storage: -20 °C to + 70 °C Humidity Storage and operating: 10% to 90% Dimensions h × w ×d (mm) 43 × 483 × 208(1U high, full rack width) Weight 3.2 kg Color Gray (PANTONE 425 C) Mean time between failures 30,000 hoursOrdering InformationTMX-1608SDI2 16×8 High Definition Digital VideoTracking Matrix Switcher (SD/HD/3G)System Connection。
AW00136801000_Getting_Started_with_pylon5_and_OpenCV
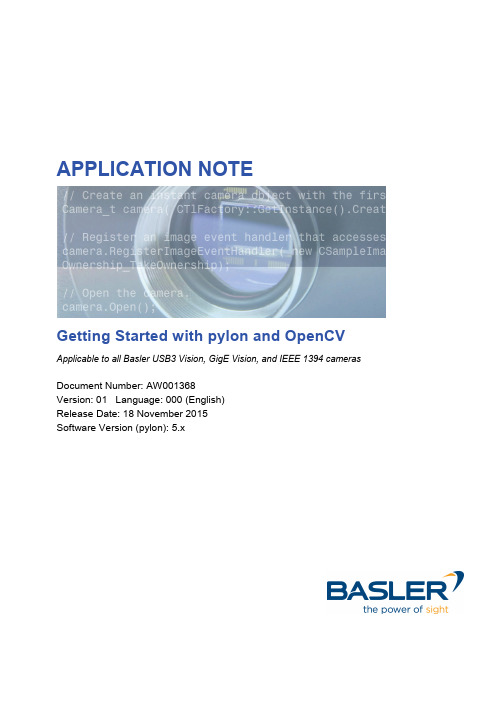
GetenCV
1
AW00136801000
Basler Application Note
1 Introduction
OpenCV is an open-source computer vision library that allows you to perform image processing on Basler Machine Vision cameras. This application note provides information on how to install and use OpenCV in combination with Basler’s pylon Camera Software Suite in Microsoft Visual Studio on Windows operating systems. OpenCV does not support Machine Vision standards such as USB3 Vision, GigE Vision, or IEEE 1394 (FireWire). Therefore, it is not recommended to grab images using OpenCV API functions. Instead, Basler recommends using the pylon Camera Software Suite SDK to grab images and convert them to OpenCV images. This document provides further information on the integration of OpenCV functions for image display, image saving, and video recording into your pylon source code.
维亚维技术 Viavi MTS T-BERD 5800v1 软件更新指南说明书
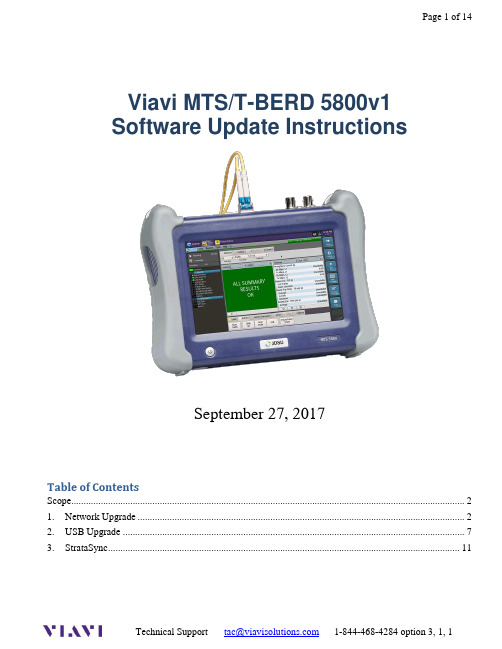
Viavi MTS/T-BERD 5800v1Software Update InstructionsSeptember 27, 2017Table of ContentsScope (2)work Upgrade (2)B Upgrade (7)3.StrataSync (11)ScopeThere are three methods to update T-BERD 5800v1 software:work upgrade - Use this method to update your T-BERD via an Internet connection.B upgrade - Use this method to update your T-BERD with a USB thumb drive.3.StrataSync upgrade - Use this method if your T-BERD 5800v1 is managed using Viavi’s StrataSyncAsset Management system.The T-BERD must be connected to AC Power, regardless of update method.work UpgradeStep Action Details1.Power On Press and hold the ON/OFF button o turn on the T-BERD 5800v1.2.AC Power Connect the AC power adapter to thepower connector on the top of theT-BERD 5800v1.N Connection Connect the Ethernet ManagementPort on the side of T-BERD 5800v1to a network connection with internetaccess, using CAT 5E or better cable.4.System Press the System icon, , at the top of the start-up screen, to display theSystem Menu.work Settings Press the Network icon,, to display LAN Settings. Set IP Mode to“DHCP” for automatic IP address assignment or “Static” for manual input.After configuring LAN settings, press the System icon, , to redisplaythe System Menu.6. Upgrade Press the Upgrade icon,, to display upgrade methods.Page 4 of 14Page 5 of 14 work Upgrade Press to display upgradesettings. Ensure that Server Address= “”8.Connect Press to showthe upgrade versions available at .9.Start Upgrade Press , and press to initiate the upgrade.Page 6 of 14B UpgradeStep Action Details Using an internet browser on your PC or laptop, go to /2.5800v2 Click on theto display the T-BERD 5800v1 upgrade portal.3.Download Click on the US/Canadian Flag, , and click to downloadthe current software revision from the North American download server.Save it to your desktop.B Stick Insert a USB thumb drive into the USB port on your PC or laptop.5.Extract Open and run the downloaded file, enter the path of the USB stick, and pressto extract files.6.Eject Safely eject the USB drive from your PC or Laptop7.Power on T-BERD Press and hold the ON/OFF button to turn on the T-BERD 5800v1.8.AC Power Connect the AC power adapter to thepower connector on the top of theT-BERD 5800v1.B Connect the USB Thumb Drive to oneof the USB ports on the side of theT-BERD 5800v1. An 8GB or smallerdrive is recommended.Page 9 of 14 10.System Press the System icon, , at the top of the start-up screen, to display theSystem Menu.11.Upgrade Press the Upgrade icon,, to display upgrade methods.Page 10 of 14 B Upgrade Press to display upgrade versionsavailable on the USB stick.13.Start Upgrade Press . Press to initiate the upgrade.3.StrataSyncStep Action Details1.Power On Press and hold the ON/OFF button to turn on the T-BERD 5800v1.2.AC Power Connect the AC power adapter to thepower connector on the top of theT-BERD 5800v1.N Connection Connect the Ethernet ManagementPort on the side of T-BERD 5800v1to a network connection with internetaccess, using CAT 5E or better cable.4.System Press the System icon, , at the top of the start-up screen, to display theSystem Menu.work Settings Press the Network icon,, to display LAN Settings. Set IP Mode to“DHCP”for automatic IP address assignment or “Static” for manual input.After configuring LAN settings, press the System icon, , to redisplaythe System Menu.6.StrataSync Press the StrataSync icon,, to display StrataSync Settings. Ensurethat Account ID and Technician ID match those of your StrataSync account.7.Sync Press to sync your T-BERD 5800v1 and initiate upgradesauthorized by your StrataSync System Administrator. If an upgrade has beenassigned you will receive a message box telling you that an upgrade isavailable and prompting you to OK or Cancel. If you were expecting anupgrade notification and did not receive one during your sync to Stratasync,contact your company’s St ratasync Admin.。
- 1、下载文档前请自行甄别文档内容的完整性,平台不提供额外的编辑、内容补充、找答案等附加服务。
- 2、"仅部分预览"的文档,不可在线预览部分如存在完整性等问题,可反馈申请退款(可完整预览的文档不适用该条件!)。
- 3、如文档侵犯您的权益,请联系客服反馈,我们会尽快为您处理(人工客服工作时间:9:00-18:30)。
Cod. MTS M
Impulso di zero Passo polare Risoluzione Precisione** Ripetibilità Cavo Tipo di uscita Frequenza max. Distanza sensore Tensione di alimentazione Assorbimento senza carico passo costante ogni 2 mm*** (C) esterno (E) posizionato su banda magnetica (Z) 2+2 mm 1000 - 500 - 100 - 50 - 25 - 10 - 5 - 1 μm ± 15 μm ± 1 incremento 8 poli LINE DRIVER / PUSH-PULL 300 kHz vedi disegni 5 ÷ 28 Vdc ± 5% 60mAMAX 140 mAMAX (con 5 V e Zo = 120 Ω) 115 mAMAX (con 12 V e Zo = 1.2 kΩ) 90 mAMAX (con 28 V e Zo = 1.2 kΩ) 90° ± 5° elettrici 1.2 m/s (MTS M1) / 12 m/s (MTS M10) 300 m/s
Codice
Progetto
Revisione
Titolo
ST01
A25-B
LINE DRIVER
F
SCHEDA TECNICA
PUSH-PULL
SCHEMA SEGNALI DI USCITA
DIMENSIONI SENSORE
S(mm)
MP200Z 1.3
MP200Z+CV103 1.6 0.7MAX
* Prolunga con sezione dei conduttori di alimentazione di 0.5 mm2. ** Il valore dichiarato è subordinato al rispetto delle tolleranze di allineamento e può essere migliorato riducendo la distanza tra il sensore e la banda magnetica. *** Fatta eccezione per il modello 1K (risoluzione 1000 μm), avente passo costante ogni 4 mm.
CARATTERISTICHE MECCANICHE ED ELETTRICHE
MECCANICHE • Corpo sensore magnetico in materiale pressofuso. • Possibilità di fissaggio del sensore magnetico mediante due soluzioni, con viti M4 o viti passanti M3. • Ampie tolleranze di allineamento. • Impulsi di zero in posizioni a richiesta (solo con MP200Z). ELETTRICHE • Cavo di alimentazione molto flessibile. • Notevole stabilità dei segnali. • Per applicazioni dove la velocità massima è superiore a 1 m/s, è indispensabile l’uso di un cavo speciale.
2
CAVO (lunghezza standard 2 m)
Raggio minimo di curvatura 60 mm 8 POLI Ø 5.3 mm
LINE DRIVER PUSH-PULL
CONNESSIONE
VERDE ARANCIO BIANCO AZZURRO MARRONE GIALLO ROSSO BLU SCHERMO
Mod.GQ051_P02 (C) ST
Pag. 2/2
Il sensore di serie è fornito con un cavo di lunghezza standard 2 m. Si possono richiedere cavi di lunghezza superiore, tenendo conto delle seguenti lunghezze massime possibili: LMAX= 10 m (cavo sensore); LMAX= 100 m (2 m cavo sensore + prolunga*).
GIVI MISURE s.r.l. Via Assunta 57 - 20054 NOVA MILANESE (MI) ITALY TEL.+39 0362.36.61.26 FAX +39 0362.36.68.76 www.givimisure.it sales@givimisure.it
Codice
Senza obbligo di preavviso, i prodotti potrebbero essere soggetti a modifiche che la Casa Costruttrice si riserva di apportare perché ritenute necessarie al miglioramento degli stessi.
Mod.GQ051_P02 (C) ST Pag. 1/2
GIVI MISURE s.r.l. Via Assunta 57 - 20054 NOVA MILANESE (MI) ITALY TEL.+39 0362.36.61.26 FAX +39 0362.36.68.76 www.givimisure.it sales@givimisure.it
Progetto
Revisione
Titolo
ST01
A25-B
F
SCHEDA TECNICA
SENSORE MAGNETICO MTS M
CARATTERISTICHE GENERALI
• • SENSORE MAGNETICO MTS, di dimensioni contenute. BANDA MAGNETICA MP200 (o MP200Z con impulsi di zero in posizioni a richiesta) costituita da un nastro di plastoferrite magnetizzata, con passo polare 2+2 mm, supportata da un nastro di acciaio inossidabile già provvisto di parte adesiva, per una facile applicazione alla macchina.
[55 ÷ 2000 Hz]
2
1000 m/s
(11 ms)
IP 67 DIN 40050/IEC 529 0° ÷ 50°C -20° ÷ 80°C 100% (non condensata) 40 g inversione di polarità della alimentazione e cortocircuiti delle uscite
MP200Z+SP202 2.1 0.2MAX
d(mm) 0.35÷0.9
S(mm) d(mm) d
MP200 1.3 0.3÷1.5
MP200+00+SP202 2.1 0.7MAX
distanza tra sensore e lato superiore di S
A A B B Z Z V+ V-
A B Z V+ V-
Assorbimento con carico
Sfasamento Velocità max. Resistenza alle vibrazioni Resistenza agli urti Grado di protezione Temperatura di esercizio Temperatura di stoccaggio Umidità relativa Peso Protezioni elettriche
528V
528V = 5÷28V
L
L = LINE DRIVER
M02/N
M01/N = 1m M02/N = 2m M10/N = 10m C3 = C3 C4 = C4
SC
SC = senza conn.
1K = 1000μm
Esempio
SENS.MAGNETICO MTS M10C 528VL M02/N SC
CODICE DI ORDINAZIONE
MODELLO PASSO RISOLUZIONE ZERO ALIMENTAZIONE USCITA CAVO CONNESSIONE
MTS
MTS
M
M = 2+2mm 1= 5= 10 =
10
1μm 5μm 10μm E = esterno
C
C = passo costante Z = posizionato su banda magnetica
TOLLERANZE DI ALLINEAMENTO SENSORE
MTS MxxxC MTS MxxxE MTS MxxxZ 1MAX
a a
a(mm)
3MAX
FISSAGGIO E MANIPOLAZIONE
MODALITA’ DI APPLICAZIONE 1. Sgrassare la superficie di appoggio con alcool e ripassare con straccio asciutto. 2. Stendere il nastro di plastoferrite allineato con la testina. 3. Stendere sopra la plastoferrite il nastro protettivo. Il massimo dell’adesione si raggiungerà dopo 48 ore dall’applicazione. SONO DA EVITARE 1. Lavorazioni meccaniche di qualsiasi tipo (taglio, foratura, fresatura, spianatura, ecc.), 2. Modifiche in genere del corpo del sensore. 3. Maltrattamenti di ogni genere. 4. Urti e sollecitazioni esterne. 5. Vicinanza di fonti magnetiche.