气相沉积技术制备TiN类硬质膜
TiN薄膜制备方法_性能及其应用的研究进展_季鑫
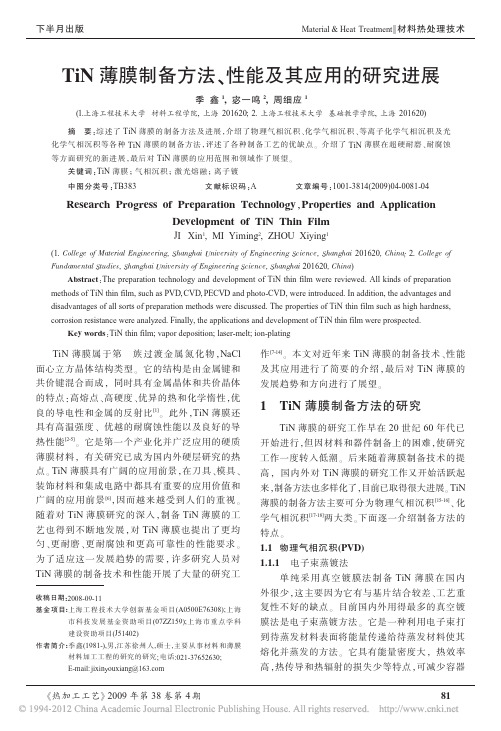
等离子体浸没式离子注入技术(PIII)制备 TiN 薄膜方法最早由 Conrad 教授发明,他发现 PIII 技 术 能 同 时 对 一 批 工件进行注入处理,因此这种方法 的工艺和设备非常简单, 能较大幅度地降低生产成 本,在制备 TiN 薄膜方面有很好的应用价值。等离子 体浸没式离子注入(PIII,有些 文献中 也 称 为 PSII) 是在 PIII 过程中, 等离子体中的被注元素在强电 场力作用下, 全方位地垂直注入到所有表面内的 一种沉积方法。 目前国内对 PIII 技术制备 TiN 膜
磁控溅射制备 TiN 薄膜技术主要有直流磁控 溅射和射频(RF)磁控溅 射(使 用陶瓷 TiN 靶材)两 种 , 最 近 又 出 现 了 非 平 衡 磁 控 溅 射 和 反 应 溅 射 [21]。 其中反应溅射方法因其独特的优点最早和最多地 使用在 TiN 薄膜制备上[22]。 国外 Vaz 等[8]第一次 应用反应溅射方法制备 TiN 薄膜,另外非平衡磁 控溅射方法也是一种国内外常用的溅射方法, Hsieh 等[23]利用非平衡磁控溅射方法,通过闸板控 制、功率控制和旋转基体控制等方法,得到了多元 TiN/TiAlN 多层膜。 磁控溅射制备 TiN 薄膜具有 溅射率高、基片温升低、膜基结合力好、装置性能 稳定、操作控制方便等优点[24]。 同时它也有一些缺 点,例如它的沉积速率较底, 效率较差, 对降低沉 积成本不利,因此磁控溅射方法仅应用于光学、微 电子学等对 TiN 涂层要求较高的领域[22]。 1.1.3 电弧离子镀(Arc Ion Plating AIP)
化学气相沉积层技术的优点及其应用

化学气相沉积层技术的优点及其应用化学气相沉积层的优点是:膜层致密,与基体结合牢固,沉积性好,膜厚且比较均匀,膜层质量比较稳定,易于实现大批量生产等。
近几年来,CVD技术已广泛应用于机械和仪表零件、刀具和模具等的表面强化,以改善其服役性能及寿命。
1.在切削工具上的应用用CVD涂覆刀具,能有效地减少在车、铣钻孔过程中出现的磨损,在这里应用了硬质合金刀具和高速钢刀具,特别是车床的转位刀片、铣刀、刮刀和整体钻头等。
使用高耐磨性的碳化物、氮化物、碳氮化物、氧化物和硼化物等涂层。
TiN 与金属的亲和力小,抗粘附力和抗月牙形磨损性能比Tin涂层高。
因此,刀具上广泛使用的是TiN涂层。
目前,国外先进工业国家加工齿轮广泛使用涂层刀具,估计约有80%的齿轮滚刀和40%的插刀使用了’FiN涂层。
这些刀具的寿命增加了4-8倍,并且提高了进给量和切削速度,刀具的抗月牙形磨损性能也显着提高。
为了进一步提高涂层刀具的使用性能,除了单涂层外,近年来还发展了双涂层、三涂层及多层的复合涂层刀片。
常用的双涂层有Tic—TiN、Tic—A120,等涂层。
三涂层的组合方式很多,例如:Tic.Ti(c、N)一’riN、Tic—Ti(c、N).A170,等涂层,还有多层如Tic-Ti-TiN-A1203等。
这些相互结合的涂层改善了涂层的结合强度和韧性,提高了耐磨性。
美国最新的涂层铣刀片使用了A1203—7FiN—Tic复合涂层,基体为专用的抗塑性变形硬质合金。
因为该硬质合金有很好的切削性能,Tic涂层和外层的越203结合,抗磨损性能优于si,N4,能显着减少月牙形磨损。
经生产实践证明,刀具、冷加工模具等经沉积覆层,其使用寿命提高3~6倍,经济效益非常显着。
化学气相沉积层降低刀具磨损的主要原因为:在切削开始时,切削与基体的直接接触减小,这样刀具和工件之间的扩散过程降低,因此降低了月牙形磨损。
即使破坏了表面涂层,仍然能阻挡进一步的磨损,保留的涂层仍然能支持切削工作。
气相沉积技术制备TiN类硬质膜
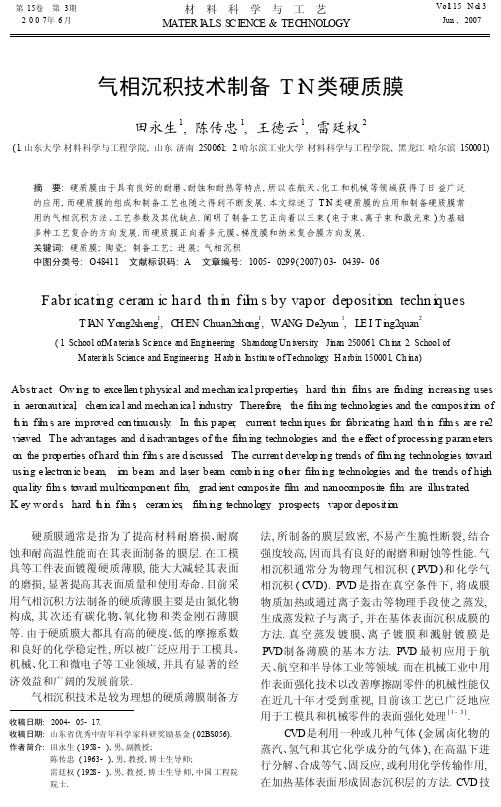
子束等加热蒸发容器中成膜的原材料, 使其表面 原子或分子气化, 形成蒸气流并射到基体表面沉 积为固态薄膜的方法. 真空蒸镀是发展较早、应用 也较广泛的一种薄膜制备技术, 制备的膜层细密、 光滑, 不含颗粒和杂质等, 适合大规模生产. 基体 的镀膜温度一般在 200 ~ 600e , 受热影响小. 但 沉积过程中通常只使用一种材料的靶材, 绕射性 较差. 另外, 基体的表面状况对沉积层的附着性较 为敏感, 故沉积前应严格清洗基体表面. 蒸发源是 蒸发装置的关键部件, 根据蒸发源不同, 真空蒸镀 又可以分为电子束蒸镀、电阻蒸镀、高频感应蒸镀 等, 其中电子束蒸镀较适宜沉积硬质膜.
第 3期
田永生, 等: 气相沉积技术制备 T iN类硬质膜
# 441#
以提高工件的耐磨和耐蚀性能.
快的发展. 溅射镀膜的方式很多, 较常用的有直流 二极或多极溅射、磁控溅射、射频溅射、反应溅射、 偏压溅射、非对称交流溅射和离子束溅射等.
图 2 离子镀系统示意图
采用多弧离子镀技术 在高速钢钻头 上沉积 ( T,i A l) N 硬质膜的研究表明 [ 12 ] , 适宜的沉积工 艺参数是制备优质膜的重要保证. 偏压增大, 膜层 变得致密, 附着力增强. 但随偏压的增高, 沉积速 率将显著降低, 当偏压增大到 400V 时, 沉积速率 几乎为零. 氮气压力的大小影响着 T i、A l与 N2 的 反应程度. 气压过低, 反应不完全; 气压过大, 膜层 中的氮含量偏高. 升高温度可改善膜层的组织, 但 易导致基片 (工件 )机械性能降低. 较适宜的镀膜 工艺参数为: 偏压 200V, N2 气压力 15 @l0- 2 Pa, 温度 300e . 在此工艺下对高速钢钻头 ( < 6)镀膜 (时间为 1h)后的耐磨试验表明, 切削能力较未镀 膜钻头大幅度提高, 使用寿命提高了 6~ 7 倍. 在 D6防锈铝的基体上采用多弧离子镀技术沉积 T i ( C, N ) /T iN /T i( C, N ) /T iN /T i( C, N ) /T iN 多层膜 的研究发现 [ 13 ] , 膜与基体之间形成了纳米级厚度
等离子体增强化学气相沉积方法制备类金刚石薄膜实验-PPT文档资料

(9)根据工艺参数沉积类金刚石薄膜20分钟,然后结束镀膜,之后关闭电
源和气体。 (10)薄膜在真空状态下搁置一段时间。待冷却后,关机械泵。打开充气
阀对真空室充气后,打开真空室门,取出薄膜进行观察。
(11)合上真空室门,将真空室内抽到一定真空后,然后关掉机械泵,关 掉总电源,切断冷却水。
六、实验报告要求
四、实验原理
(1)化学气相沉积制备薄膜介绍
(2)直流辉光放电等离子体化学 气相沉积
(3)类金刚石薄膜简介
4.1 化学气相沉积制备薄膜介绍:
化学气相沉积(Chemical Vapor Deposition, CVD):利用气态的先驱反 应物,通过原子、分子间化学反应的途径生成固态薄膜的技术。
化学气相沉积过程中的各个动力学环节:
(3)等离子体增强化学气相沉积( PECVD):
在低压化学气相沉积过程的同时,利用气体放电产生等离子体
并对沉积过程施加影响的薄膜制备技术。
(4)等离子体产生方法:
微波辅助PECVD、 射频辉光放电PECVD、
直流辉光放电PECVD
(5)直流辉光放电PECVD沉积原理:
直流电源
气体 石英玻璃
直流 电源
性能 Density (g/cm3) Atomic Number Density (Mole/cm3) 金刚石 3.51 类金刚石 1.8 – 3.6 石墨 2.26
0.3 10000
0.05 2.42 UV-VIS-IR
0.2 – 0.3 2000 - 8000
0.03 – 0.2 1.8 – 2.6 VIS-IR
(3)将清洗好的基片放入沉积室里面的样品台上,然后关好真空室门。
(4)仔细检查水源、气源和电源正常后,打开冷却循环水。 (5)抽真空。首先用机械泵抽真空,开启真空泵,打开机械泵的真空阀门, 一段时间后(约10分钟)打开热偶真空计测量真空度,待真空室内气压达 到1Pa左右,然后开启分子泵及分子泵的阀门,用分子泵与机械泵一起抽真 空,一段时间后(约30分钟)打开电离真空计测量真 空度,待室内气
Si 和316L 基片上TiN 薄膜微观结构和应力的对比分析

表面技术第51卷 第3期收稿日期:2021-04-21;修订日期:2021-09-07 Received :2021-04-21;Revised :2021-09-07基金项目:深圳职业技术学院重点项目(6020310007K );深圳市基础研究项目(JCYJ20190809150001747)Fund :Supported by the Key Project of Shenzhen Polytechnic (6020310007K); Science and Technology Project of Shenzhen (JCYJ20190809150001747) 作者简介:赵升升(1979—),男,博士,副教授,主要研究方向为硬质薄膜的力学性能。
Biography :ZHAO Sheng-sheng (1979—), Male, Doctor, Associate professor, Research focus: mechanical properties of hard films.引文格式:赵升升,程毓,张小波,等. Si 和316L 基片上TiN 薄膜微观结构和应力的对比分析[J].表面技术, 2022, 51(3): 278-285.ZHAO Sheng-sheng, CHENG Yu, ZHANG Xiao-bo, et al. Comparative Study on Stress and Microstructure of TiN Films on Si and 316L Si 和316L 基片上TiN 薄膜微观结构和应力的对比分析赵升升1,程毓1,张小波2,常正凯2(1.深圳职业技术学院 机电工程学院,广东 深圳 518055;2.深圳市速普仪器有限公司,广东 深圳 518000)摘 要:目的 比较Si 和316L 基片上TiN 薄膜的微观结构和应力,分析基片材料和基片初始曲率对薄膜应力的影响。
铸造Al-Si合金表面气相沉积TiN薄膜的耐磨性能

武汉船舶职业技术学院学报2010年第5期铸造A I—Si合金表面气相沉积T i N薄膜的耐磨性能谭银元(武汉船舶职业技术学院科研处,湖北武汉430050)擒要采用多弧离子镀技术,对铸造A l—si合金表面气相沉积T i N薄膜的耐磨性能进行了研究。
结果表明,镀有Ti N薄膜的铸造A l—s i合金具有比未镀膜铸造A卜s i合金更优异的耐磨性。
在相同的磨损条件下,未镀膜试样表面由于发生磨粒磨损,在磨损过程中出现严重的微观切削现象}Ti N涂层表面以粘着磨损为主,其磨痕存在剥落,并且随着磨损时间的延长,磨损机制由粘着磨损转为磨粒磨损,未镀膜试样的磨痕宽度几乎是Ti N磨痕的2倍。
关键词A l—S i合金;气相沉积;Ti N薄膜;耐磨性能中图分类号TG l35.6文献标志码A文章编号1671—8100(2010)05—0022一03耐磨性是衡量材料表面耐用性的一项很重要的性能指标,有文献表明,当前材料约有80%失效是由磨损引起的[1引,这给国民经济造成巨大的损失,因此,提高零件表面耐磨性一直是人们致力研究的内容。
采用气相沉积技术在材料表面沉积硬质涂层是提高材料耐磨性的重要途径之一,硬质涂层最显著的特点是具有高硬度和高耐磨性,涂层的耐磨性是评估一种硬质涂层优劣的重要指标,关系着镀膜材料的使用寿命,是硬质薄膜材料设计中必须考虑的问题。
镀层材料本身的特性是决定耐磨性的根本因素,耐磨性也在一定程度上反映了涂层的硬度和结合力,而且仅在零件的表面或特殊部位获得特殊性能涂层,使基体仍保持原有的组织和成分是一种经济、有效的措施。
本文选择ZLl09材料为研究对象,采用多弧离子镀技术,在铸造铝合金表面沉积Ti N薄膜并对膜的耐磨性能进行研究。
1试验过程试验用材料为Z Ll09,试样规格为:20m m×10m m X10m m,其化学成分如表1。
离子镀用靶材为纯度为99.99%的Ti靶,靶直径为100m m,工作气体为工业氮气(纯度为99%)和氩气(纯度为99.99%)。
等离子体增强化学气相沉积方法制备类金刚石薄膜实验

(2)实验设备:
超声清洗器;
直流辉光放电等离子体增强化学气相沉积系统。
直流辉光放电等离子体化学气相沉积类金刚石薄膜是利用高压直流负偏压 (-1~-5kV),使低压碳氢气体发生辉光放电从而产生等离子体,等离子体
在电场作用下沉积到基片上并形成类金刚石薄膜。
直流辉光放电PECVD沉积系统示意图
主要组件:真空室组件、直流电源、基片水冷加热台、窗口及法兰接口 部件、工作气路、抽气机组(机械泵和分子泵)、阀门及管道、真空测量 及电控系统。
0.2 500
0.1 2.15 – 1.8 Opaque
Hardness (Kgf/mm2)
Friction Coeff. Refractive Index Transparency
Resistivity (Wcm)
>1016
1010 - 1013
0.2 – 0.4
应用:
VCR Head Drum
六、实验报告要求
(1)描述实验过程中观察到的各种现象,并给出合理的解释。 (2)实验装置中各主要部分的用途。 (3)阐述等离子体的产生原理。 (4)详细记录实验过程、工艺参数及实验步骤,写出类金刚石薄膜制备 实验报告。
CD/DVD Mold
Spacer Tool
Form Die
Hard Disk & Slider
Wrist Pin
Digital VCR Tape
Razor Blade
五、实验方法和步骤
(1)根据实验目的,设定工艺参数。 (2)用超声波清洗器清洗玻璃基片和单晶硅基片15分钟,清洗时加入丙酮 或酒精,清洗后用氮气吹干。 (3)将清洗好的基片放入沉积室里面的样品台上,然后关好真空室门。 (4)仔细检查水源、气源和电源正常后,打开冷却循环水。 (5)抽真空。首先用机械泵抽真空,开启真空泵,打开机械泵的真空阀门, 一段时间后(约10分钟)打开热偶真空计测量真空度,待真空室内气压达
TiN论文:TiN化学气相沉积正交试验XRDXPS
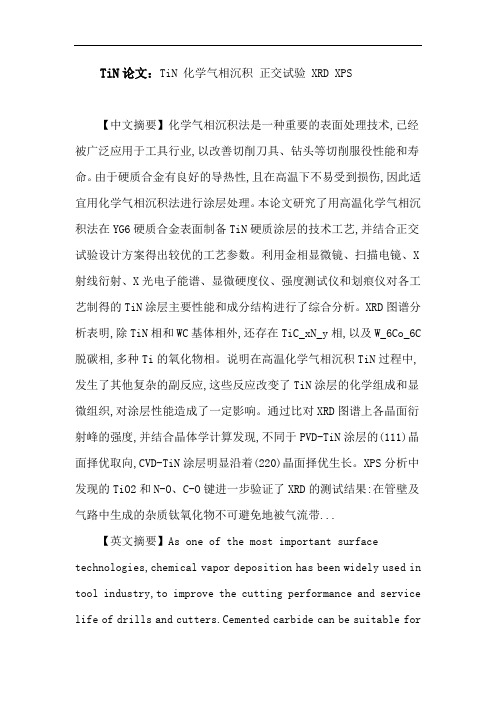
TiN论文:TiN 化学气相沉积正交试验 XRD XPS【中文摘要】化学气相沉积法是一种重要的表面处理技术,已经被广泛应用于工具行业,以改善切削刀具、钻头等切削服役性能和寿命。
由于硬质合金有良好的导热性,且在高温下不易受到损伤,因此适宜用化学气相沉积法进行涂层处理。
本论文研究了用高温化学气相沉积法在YG6硬质合金表面制备TiN硬质涂层的技术工艺,并结合正交试验设计方案得出较优的工艺参数。
利用金相显微镜、扫描电镜、X 射线衍射、X光电子能谱、显微硬度仪、强度测试仪和划痕仪对各工艺制得的TiN涂层主要性能和成分结构进行了综合分析。
XRD图谱分析表明,除TiN相和WC基体相外,还存在TiC_xN_y相,以及W_6Co_6C 脱碳相,多种Ti的氧化物相。
说明在高温化学气相沉积TiN过程中,发生了其他复杂的副反应,这些反应改变了TiN涂层的化学组成和显微组织,对涂层性能造成了一定影响。
通过比对XRD图谱上各晶面衍射峰的强度,并结合晶体学计算发现,不同于PVD-TiN涂层的(111)晶面择优取向,CVD-TiN涂层明显沿着(220)晶面择优生长。
XPS分析中发现的TiO2和N-O、C-O键进一步验证了XRD的测试结果:在管壁及气路中生成的杂质钛氧化物不可避免地被气流带...【英文摘要】As one of the most important surface technologies,chemical vapor deposition has been widely used in tool industry,to improve the cutting performance and service life of drills and cutters.Cemented carbide can be suitable forcoating by CVD,because of its good thermal conductivity and less detriment under high temperature.In this paper, we searched for the technical processes of TiN coating on YG6 cemented carbide by using high-temperature chemical vapor deposition.Then the optimum parameters were obtain...【关键词】TiN 化学气相沉积正交试验 XRD XPS【采买全文】1.3.9.9.38.8.4.8 1.3.8.1.13.7.2.1同时提供论文写作定制和论文发表服务.保过包发.【说明】本文仅为中国学术文献总库合作提供,无涉版权。
PCVD-TiN,TiAlN及TiSiN涂层的抗高温氧化性能

材料保护MATERIALS PROTECTION1999年 第32卷 第1期 No.1 vol.321999PCVD-TiN,TiAlN及TiSiN涂层的抗高温氧化性能彭红瑞 石玉龙 谢 雁 赵 程 摘 要 研究了用PCVD法所制备的TiN,TiAlN和TiSiN硬质涂层的抗高温氧化性能及TiN 涂层在双氧水介质中的抗氧化性能。
结果表明,TiAlN,TiSiN涂层在空气中的抗高温氧化温度达700 ℃以上,TiN涂层可达600 ℃。
在双氧水介质中,PCVD-TiN涂层仍具有较强的抗氧化能力,且优于PVD-TiN涂层。
关键词 涂层 抗氧化性能 等离子体化学气相沉积 TiN TiAlN TiSiN1 前 言 等离子体化学气相沉积(PCVD)TiN类硬质涂层技术具有沉积温度低(600 ℃)和挠度好等特点。
高速钢工具和模具上沉积TiN类硬质涂层已得到较为广泛的研究及应用[1~6],但这也仅限于用此提高耐磨性及使用寿命,而对它抗高温氧化性能的研究却较少。
国内某精密轴承的工作环境温度为300 ℃,瞬间可达420 ℃,而其高温氧化试验在空气中加热到580 ℃,保温30 min后,要求工件表面涂层无剥落等缺陷[5]。
经过反复试验,我们最后选用了PCVD法沉积TiN涂层,作为轴承内外圈表面的抗氧化涂层,并取得了成功[7]。
为此,我们对PCVD-TiN,TiAlN,TiSiN及PVD-TiN等涂层进行了抗氧化性能的研究,以期了解并掌握这些涂层的抗氧化性能。
2 试验方法 PCVD-TiN,TiAlN,TiSiN涂层的制备在自制的PCVD设备上进行[8],PVD-TiN涂层用多弧离子镀设备制备。
试验材料为W18Cr4V高速钢刀片,加工成16×10×3,再用金相砂纸抛光成镜面。
PCVD-TiN,TiAlN,TiSiN和PVD-TiN涂层厚度为2.5~3.5 μm。
抗高温氧化试验在管式加热炉中进行:将以PCVD法沉积的TiN,TiAlN,TiSiN涂层及用PVD法沉积的TiN涂层高速钢试样放入管式炉中,大气条件下加热到300~700 ℃,保温30 min后取出,空冷至室温,观察分析其表面状态。
tin沉积方式

tin沉积方式摘要:1.Tin 沉积方式的概述2.Tin 沉积方式的种类3.Tin 沉积方式的影响因素4.Tin 沉积方式的应用领域5.Tin 沉积方式的发展前景正文:1.Tin 沉积方式的概述Tin 沉积方式,即锡沉积方法,是指在电子工业中用于制造锡膜或锡球的一系列技术。
这些锡膜或锡球通常用于电子设备的焊接、封装和连接。
锡沉积方式的发展对电子工业的微型化和可靠性有着重要影响。
2.Tin 沉积方式的种类常见的Tin 沉积方式主要有以下几种:(1)化学气相沉积(CVD):通过向工件表面提供含锡化合物的气体,使其在表面形成锡膜。
(2)物理气相沉积(PVD):通过将锡靶材置于真空室中,并施加电压,使锡离子轰击到工件表面形成锡膜。
(3)电化学沉积:通过将工件浸泡在含锡电解液中,施加电流,使锡离子在工件表面还原形成锡膜。
(4)溶胶- 凝胶法:将锡盐添加到溶剂中,形成凝胶,然后将凝胶涂覆到工件表面,通过热处理使其形成锡膜。
3.Tin 沉积方式的影响因素Tin 沉积方式的选择和效果受到多种因素影响,如:(1)沉积温度:不同沉积方式对温度的要求不同,过高或过低的温度会影响锡膜的性能。
(2)沉积时间:沉积时间的长短直接影响到锡膜的厚度和均匀性。
(3)锡源:锡源的纯度和活性会影响到锡膜的质量。
(4)工件表面处理:工件表面的清洁度和粗糙度会影响到锡膜的附着力。
4.Tin 沉积方式的应用领域Tin 沉积方式广泛应用于电子工业,如:(1)半导体制造:用于制造芯片的焊接、封装等过程。
(2)电子器件制造:用于制造电容器、电阻器、晶体管等电子器件。
(3)光电子器件制造:用于制造LED、太阳能电池等光电子器件。
5.Tin 沉积方式的发展前景随着电子工业的不断发展,对Tin 沉积方式的要求也越来越高。
基于TiN类膜制备工艺的研究

基于TiN类膜制备工艺的研究摘要:硬质TiC、TiN、Ti(CN)薄膜因具有相似的性质,故合称为TiN类薄膜。
TiN类薄膜因具有高强度、高硬度、化学稳定性好、耐磨及防腐蚀等一系列优点,其涂层被广泛作用于机械工业中的刀具、模具等表面,成为具有巨大应用前景的涂层材料。
TiN类陶瓷膜由于其独特的性能而成为当前材料表面研究热点之一。
文章简要介绍了利用化学气相沉积(CVD)、物理气相沉积(PVD)、双辉技术及其它表面处理技术制备TiN类膜的研究进展,讨论了各种制备方法的工艺特点。
关键词:表面技术;TiN类膜;制备工艺当前TiN类陶瓷膜制备主要工艺方法之一是气相沉积法,根据各种气相沉积过程的不同特点又可分为化学气相沉积(CVD)和物理气相沉积(PVD)。
气相沉积法的主要特点在于不管原来需镀物料是固体、液体或气体,在输运时都要转化成气相形态进行迁移,最终到达工件表面沉积凝聚成固相薄膜。
气相沉积法是一种干式真空镀膜法,具有膜不受污染,纯度高,膜材与基材选择广泛等特点。
另还可用于制备Ti(CN)陶瓷膜的方法有自蔓延燃烧合成法、固体粉末渗覆法、激光熔覆法、电泳沉积法等。
一、化学气相沉积法化学气相沉积(ChemicalVaporDeposition,简称CVD)是现代表面工程技术中的一个重要领域,也是近几十年来发展迅速、应用广泛的表面成膜技术之一,用CVD法在钢材表面沉积TiN类陶瓷膜的应用大多集中在含碳量高的工膜具钢方面。
它是利用气态物质在固体表面上进行化学反应,生成固态沉积物,即在一定温度条件下,混合气体与基材表面相互作用,使混合气体中的某些成分分解并在基材表面形成金属或化合物的固态膜或薄膜镀层。
从沉积化学反应能量激活看,化学气相沉积技术可分为多种,其中可常用于制备TiN类陶瓷膜的有:中温CVD、高温CVD、等离子体增强CVD、激光辅助CVD。
采用化学气相沉积所得TiN类陶瓷膜存在与基体结合不佳的问题,因而还需进行后续热处理。
等离子体氮化与物理气相沉积TiN薄膜复合处理研究进展

等离子体氮化与物理气相沉积复合处理研究进展赵彦辉1,董利民1,杜昊1,于传跃2,肖金泉1,于宝海1(1.中国科学院金属研究所,沈阳 110016;2.沈阳华俄科技发展有限公司,沈阳 110164)摘要:简要综述了等离子体氮化及物理气相沉积复合处理的新进展,主要介绍了复合处理的工艺进展、复合处理的组织结构、力学性能(硬度、耐磨性、结合强度、抗腐蚀性能等)等;指出了复合处理存在的问题及并对其应用前景进行了展望。
关键词:等离子体氮化;物理气相沉积;复合处理;组织结构;性能中图分类号:TG156.8+2, TB43 文献标识码:AThe Recent Research Progress of a Duplex Treatment Consisting of Plasma Nitriding and Physical Vapor Deposition ZHAO Y an-hui1, DONG Li-min1, DU Hao1, YU Chuan-yue2, XIAO Jin-quan1, YU Bao-hai1(1. Institute of Metal Research Chinese Academy of Sciences, Shenyang 110016, China;2. Shenyang Hua-e Science and Technology Development Co., Ltd., Shenyang 110164, China)Abstract:In this article, the progress of the research on a duplex treatment consisting of plasma nitriding and physical vapor deposition (PN/PVD) was reviewed. In accordance with the order of processing development of PN/PVD, the microstructures and mechanical properties (hardness, wear-resistance, adhesion and corrosion-resistance) of the duplex treatment, strengthening mechanism of the duplex treatment were summarized. Then the present problems were pointed out and the application prospect was outlooked.Key words: Plasma nitriding; Physical vapor deposition; Duplex treatment; Microstructure; Mechanical properties0引言氮化处理一般能提高钢材的抗疲劳、抗磨损及抗腐蚀能力。
《稀土掺杂TiN薄膜的制备及性能调控》范文
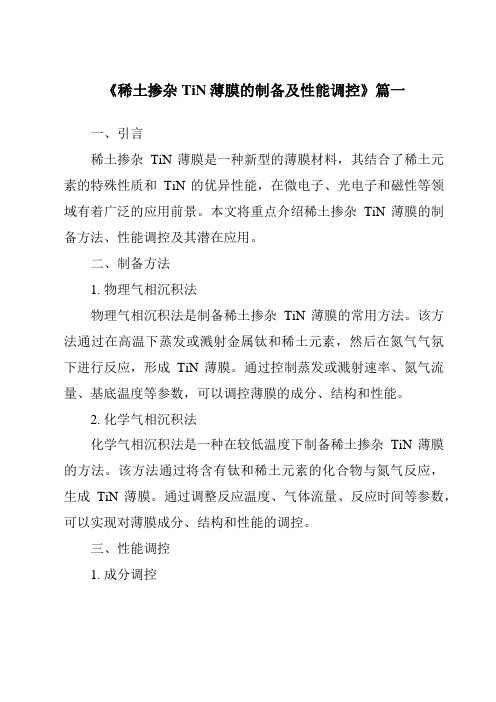
《稀土掺杂TiN薄膜的制备及性能调控》篇一一、引言稀土掺杂TiN薄膜是一种新型的薄膜材料,其结合了稀土元素的特殊性质和TiN的优异性能,在微电子、光电子和磁性等领域有着广泛的应用前景。
本文将重点介绍稀土掺杂TiN薄膜的制备方法、性能调控及其潜在应用。
二、制备方法1. 物理气相沉积法物理气相沉积法是制备稀土掺杂TiN薄膜的常用方法。
该方法通过在高温下蒸发或溅射金属钛和稀土元素,然后在氮气气氛下进行反应,形成TiN薄膜。
通过控制蒸发或溅射速率、氮气流量、基底温度等参数,可以调控薄膜的成分、结构和性能。
2. 化学气相沉积法化学气相沉积法是一种在较低温度下制备稀土掺杂TiN薄膜的方法。
该方法通过将含有钛和稀土元素的化合物与氮气反应,生成TiN薄膜。
通过调整反应温度、气体流量、反应时间等参数,可以实现对薄膜成分、结构和性能的调控。
三、性能调控1. 成分调控通过改变稀土元素的种类和掺杂量,可以调控TiN薄膜的成分,进而影响其性能。
例如,掺杂稀土元素可以改善TiN薄膜的导电性、光学性能和磁性等。
2. 结构调控通过调整制备过程中的参数,如基底温度、氮气流量、反应时间等,可以调控TiN薄膜的结构,如晶粒大小、晶格常数等。
这些结构参数对薄膜的性能有着重要影响。
3. 薄膜厚度调控薄膜厚度是影响其性能的重要因素之一。
通过调整制备过程中的沉积时间或蒸发/溅射速率,可以实现对TiN薄膜厚度的精确控制,从而优化其性能。
四、潜在应用稀土掺杂TiN薄膜具有优异的导电性、光学性能和磁性等,使其在微电子、光电子和磁性等领域具有广泛的应用前景。
例如,可以用于制备高性能的电极材料、光电器件、磁性存储器件等。
此外,由于其优异的耐磨、耐腐蚀性能,还可用于制备防护涂层等。
五、结论本文介绍了稀土掺杂TiN薄膜的制备方法、性能调控及其潜在应用。
通过物理气相沉积法和化学气相沉积法等方法,可以实现对TiN薄膜成分、结构和性能的精确调控。
通过调整稀土元素的种类和掺杂量、薄膜结构以及厚度等参数,可以优化TiN薄膜的性能,使其在微电子、光电子和磁性等领域具有广泛的应用价值。
氮化钛纳米粒子的制备及表征

氮化钛纳米粒子的制备及表征
钛氮化物(TiN)作为一种重要的功能性材料,具有优异的导电性、热导
率和磨损韧性,用于制造电子器件和传感器中得到广泛应用。
本文자
讨论了制备TiN纳米粒子的方法以及粒子的表征和表征结果。
1. 钛氮化物纳米粒子的制备
纳米TiN粒子的制备通常是水热法和气相沉积蒸镀法。
在水热法中,
钛酸钠和氨的混合物在高温下反应,可以生成钛氮化物。
在气相沉积
蒸镀法中,TiCl4通过气-相热化学反应生成TiN粉末,粉末放置在衬
底上,施加电压,使粉末气化成TiN薄膜。
2. 钛氮化物纳米粒子表征
主要采用X射线衍射(XRD)和扫描电镜(SEM)来表征钛氮化物纳米粒子。
X射线衍射分析可以提供钛氮化物粒子体系的晶体结构,从而探究TiN 纳米粒子的物相。
SEM可以全面观察TiN粒子的形貌,图像的分辨力
非常细致,甚至可以接近原子尺度,捕捉微小空隙。
3. 钛氮化物纳米粒子表征结果
制备的TiN纳米粒子在XRD检测中,Ni主峰的波峰强度和宽度符合钛氮化物的x射线分析数据,Ni2相的反射模式和波峰位置也与报道的结
果一致。
SEM结果表明,制备的TiN粒子是圆形球形,且表面无明显
缺陷,粒子形貌光滑圆滑,具有均匀的尺寸分布。
综上,本文介绍了TiN纳米粒子的制备方法和表征性质,并得出了积
极的表征结果。
本文研究对研究TiN功能性纳米复合材料有重要意义,也为应用TiN纳米粒子提供了重要参考。
氮化钛膜和纳米陶瓷膜
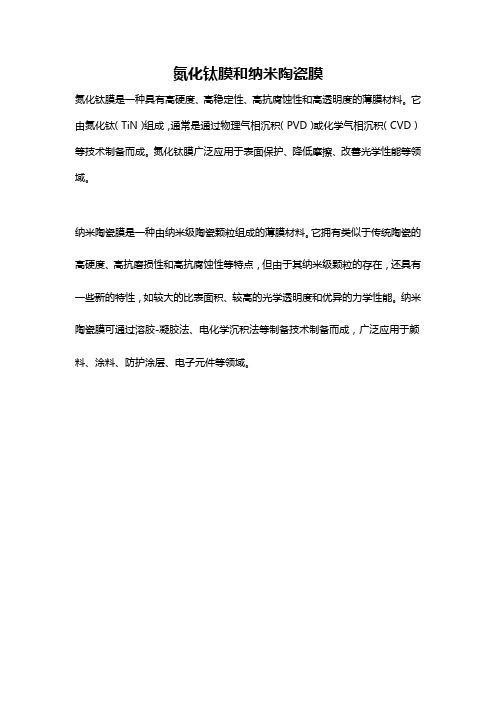
氮化钛膜和纳米陶瓷膜
氮化钛膜是一种具有高硬度、高稳定性、高抗腐蚀性和高透明度的薄膜材料。
它由氮化钛(TiN)组成,通常是通过物理气相沉积(PVD)或化学气相沉积(CVD)等技术制备而成。
氮化钛膜广泛应用于表面保护、降低摩擦、改善光学性能等领域。
纳米陶瓷膜是一种由纳米级陶瓷颗粒组成的薄膜材料。
它拥有类似于传统陶瓷的高硬度、高抗磨损性和高抗腐蚀性等特点,但由于其纳米级颗粒的存在,还具有一些新的特性,如较大的比表面积、较高的光学透明度和优异的力学性能。
纳米陶瓷膜可通过溶胶-凝胶法、电化学沉积法等制备技术制备而成,广泛应用于颜料、涂料、防护涂层、电子元件等领域。
化学气相沉积法制备金属氧化物薄膜的优化研究

化学气相沉积法制备金属氧化物薄膜的优化研究引言随着纳米科技的快速发展,金属氧化物薄膜作为一种重要的纳米材料,广泛应用于光电子器件、电子器件、传感器等领域。
化学气相沉积法(Chemical Vapor Deposition,CVD)作为一种常用的制备薄膜的方法,具有操作简便、薄膜质量高等优点。
本文将重点研究化学气相沉积法制备金属氧化物薄膜的优化方法。
第一章金属氧化物薄膜的制备过程1.1 CVD方法的原理1.2 金属氧化物薄膜的结构与性质第二章制备过程中的优化策略2.1 原材料选择2.2 反应温度的控制2.3 气氛和反应压力的控制第三章薄膜结构与性能分析3.1 表面形貌和晶体结构3.2 光学性质和电学性质分析3.3 薄膜的物理性能测试第四章实验研究与结果分析4.1 实验设计与设备介绍4.2 实验条件与操作步骤4.3 结果分析与讨论第五章优化策略的应用5.1 某金属氧化物薄膜的优化研究5.2 优化策略在其他金属氧化物薄膜制备中的应用结论本文通过对化学气相沉积法制备金属氧化物薄膜的优化研究,探索了原材料选择、反应温度和气氛等方面的优化策略,以获得高质量的金属氧化物薄膜。
实验结果表明,优化策略在提升薄膜的表面形貌、结构与性能方面具有重要的作用。
在今后的研究中,可以进一步完善优化策略,以提高金属氧化物薄膜的制备效率和应用范围。
参考文献[1] Smith A.B. et al., Chemical Vapor Deposition of Metal Oxide Thin Films, Thin Solids Films, 2010, 518(10): 2631-2635.[2] Wang C. et al., Optimization of Growth Parameters for Fabrication of Transition Metal Oxide Thin Films by Metal Organic Chemical Vapor Deposition, J. of Materials Science, 2008, 43(7): 2335-2342.[3] Liu D. et al., Investigation of the Effects of Synthesis Parameters on the Morphology and Properties of Zinc Oxide Thin Films Prepared by Metalorganic Chemical Vapor Deposition, Thin Solids Films, 2015, 576: 51-59.。
tin沉积方式

tin沉积方式(原创版)目录1.引言2.Tin 沉积方式的定义和分类3.Tin 沉积方式的影响因素4.Tin 沉积方式的应用实例5.结论正文1.引言锡(Tin)是一种重要的金属元素,具有良好的导电性、延展性和化学稳定性,广泛应用于电子、冶金、化工等行业。
在锡的加工过程中,沉积方式对其性能和应用有着重要影响。
本文将对锡的沉积方式进行介绍,分析其影响因素和应用实例。
2.Tin 沉积方式的定义和分类锡的沉积方式是指在加工过程中,锡如何在基材上形成薄膜或沉积物的过程。
根据沉积方法的不同,锡的沉积方式可以分为以下几类:(1)化学气相沉积(Chemical Vapor Deposition,CVD):通过向加热的基材表面提供锡源气体,使锡在基材表面沉积。
(2)物理气相沉积(Physical Vapor Deposition,PVD):通过将锡靶材加热至高温,使其蒸发并在基材表面沉积。
(3)电化学沉积(Electrochemical Deposition,ECD):通过在基材表面施加电流,使锡离子在基材表面还原并沉积。
(4)溶胶 - 凝胶法(Sol-Gel Method):通过将锡前驱体与溶剂混合,形成凝胶,再通过干燥、煅烧等处理,使锡在基材表面沉积。
3.Tin 沉积方式的影响因素锡的沉积方式受到多种因素的影响,主要包括:(1)基材:不同材质的基材对锡的沉积方式和性能要求不同。
(2)锡源:锡源的性质和纯度会影响锡的沉积速率和膜层质量。
(3)沉积参数:沉积温度、压力、时间等参数会影响锡的沉积速率和膜层性能。
(4)前驱体:不同前驱体的选择会影响锡的沉积方式和性能。
4.Tin 沉积方式的应用实例锡的沉积方式在电子、冶金、化工等行业中都有广泛应用,例如:(1)微电子领域:用于制造集成电路、电容器等电子元器件。
(2)太阳能电池:用于制造电极材料,提高太阳能电池的光电转换效率。
(3)防腐领域:用于涂覆船舶、桥梁、钢结构等,提高其抗腐蚀性能。
- 1、下载文档前请自行甄别文档内容的完整性,平台不提供额外的编辑、内容补充、找答案等附加服务。
- 2、"仅部分预览"的文档,不可在线预览部分如存在完整性等问题,可反馈申请退款(可完整预览的文档不适用该条件!)。
- 3、如文档侵犯您的权益,请联系客服反馈,我们会尽快为您处理(人工客服工作时间:9:00-18:30)。
111 电子束蒸发镀膜 真空蒸发镀膜法是在真空室中采用电阻或电
子束等加热蒸发容器中成膜的原材料, 使其表面 原子或分子气化, 形成蒸气流并射到基体表面沉 积为固态薄膜的方法. 真空蒸镀是发展较早、应用 也较广泛的一种薄膜制备技术, 制备的膜层细密、 光滑, 不含颗粒和杂质等, 适合大规模生产. 基体 的镀膜温度一般在 200 ~ 600e , 受热影响小. 但 沉积过程中通常只使用一种材料的靶材, 绕射性 较差. 另外, 基体的表面状况对沉积层的附着性较 为敏感, 故沉积前应严格清洗基体表面. 蒸发源是 蒸发装置的关键部件, 根据蒸发源不同, 真空蒸镀 又可以分为电子束蒸镀、电阻蒸镀、高频感应蒸镀 等, 其中电子束蒸镀较适宜沉积硬质膜.
Abstr act: Ow ing to exce llen t physical and mechan ica l properties, hard thin films are finding increasing uses in aeronaut ica,l chem ica l and mechan ica l industry. Therefore, the film ing technologies and the composit ion of th in film s are improved con tinuously. In this paper, current techn iques for fabricating hard th in film s are re2 viewed. The advantages and d isadvantages of the film ing technologies and the e ffect of processing param eters on the properties of hard thin film s are d iscussed. The current develop ing trends of film ing technologies toward using e lectron ic beam, ion beam and laser beam comb in ing other film ing technologies and the trends of high qua lity film s toward multicomponent film, grad ient composite film and nanocomposite film are illustrated. K ey w ord s: hard th in film s; ceram ics; film ing technology; prospects; vapor deposit ion
第 15卷 第 3期 2 0 0 7年 6 月
材料科学与工艺 MATER IALS SCIENCE & TECHNOLOGY
Vo l1 15 N o1 3 Jun. , 2007
气相沉积技术制备 T iN类硬质膜
田永生1, 陈传忠 1, 王德云1, 雷廷权 2
( 1. 山东大学 材料科学与工程学院, 山东 济南 250061; 2. 哈尔滨工业大学 材料科学与工程学院, 黑龙江 哈尔滨 150001)
CVD是利用一种或几种气体 (金属卤化物的 蒸汽、氢气和其它化学成分的气体 ), 在高温下进 行分解、合成等气、固反应, 或利用化学传输作用, 在加热基体表面形成固态沉积层的方法. CVD 技
# 440#
材料科学与工艺
第 15卷
术用于表面强化始于 20世纪 60年代, 目前采用 CVD 制备硬质膜已广泛用于各 种工件的表面强 化 [ 4- 6] . 由于 CVD 制备膜层是利用气态物质在热 基体表面进行化学反应, 生成固态沉积物的过程, 整个反应建立在热力学基础上, 所以绕镀性较好, 基体的孔内表面都能成膜. 与 PVD 相比, CVD 法 制备的膜组织细微致密, 与基体的结合强度较高, 并且有沉积多层复合膜层的优势 [ 7 ] . 但普通 CVD 沉积温度较高, 易引起基体的变形和开裂, 因此主 要应用于硬质合金刀具和 模具. PVD 和 CVD 都 要求在一定的真空度下沉积薄膜. 所以, 获得并保 持所需的真空环境是镀膜的必要条件.
第 3期
田永生, 等: 气相沉积技术制备 T iN类硬质膜
# 441#
以提高工件的耐磨和耐蚀性能.
快的发展. 溅射镀膜的方式很多, 较常用的有直流 二极或多极溅射、磁控溅射、射频溅射、反应溅射、 偏压溅射、非对称交流溅射和离子束溅射等.
图 2 离子镀系统示意图
采用多弧离子镀技术 在高速钢钻头 上沉积 ( T,i A l) N 硬质膜的研究表明 [ 12 ] , 适宜的沉积工 艺参数是制备优质膜的重要保证. 偏压增大, 膜层 变得致密, 附着力增强. 但随偏压的增高, 沉积速 率将显著降低, 当偏压增大到 400V 时, 沉积速率 几乎为零. 氮气压力的大小影响着 T i、A l与 N2 的 反应程度. 气压过低, 反应不完全; 气压过大, 膜层 中的氮含量偏高. 升高温度可改善膜层的组织, 但 易导致基片 (工件 )机械性能降低. 较适宜的镀膜 工艺参数为: 偏压 200V, N2 气压力 15 @l0- 2 Pa, 温度 300e . 在此工艺下对高速钢钻头 ( < 6)镀膜 (时间为 1h)后的耐磨试验表明, 切削能力较未镀 膜钻头大幅度提高, 使用寿命提高了 6~ 7 倍. 在 D6防锈铝的基体上采用多弧离子镀技术沉积 T i ( C, N ) /T iN /T i( C, N ) /T iN /T i( C, N ) /T iN 多层膜 的研究发现 [ 13 ] , 膜与基体之间形成了纳米级厚度
摘 要: 硬质膜由于具有良好的耐磨、耐蚀和耐热等特点, 所以 在航天、化工 和机械 等领域获 得了日 益广泛 的应用, 而硬质膜的组成和制备工艺也随之得到不断发展. 本文综述了 T iN 类硬质膜的应用和制备硬质膜常 用的气相沉积方法、工艺参数及其优缺点. 阐明了制备工艺正向着以三束 ( 电子束、离子束 和激光束 )为基础 多种工艺复合的方向 发展. 而硬质膜正向着多元膜、梯度膜和纳米复合膜方向发展. 关键词: 硬质膜; 陶瓷; 制备工艺; 进 展; 气相沉积 中图分类号: O48411 文献标识码: A 文章编号: 1005- 0299( 2007) 03- 0439- 06
CrA .l 而且, 在 N i基体上离子辅助电子束沉积 Cr 的膜层 显 微 硬 度 高 于 无 离 子 束 辅 助 的, 这 在 Sch iller等在沉积 A l2O3 薄膜研究中也得 到了证 实 [ 10] . 由于电子束的能量较高, 所以电子束气相 沉积的速率较高. Arezzo等 [ 11] 采用磁溅射镀、离 子镀和电子束蒸镀等方法制备 T iN 薄膜时发现, 电子束蒸镀与前两者相比具有沉积率高且膜层与 基体结合力强等优点. 文献 [ 10]的试验表明, 采 用等离子辅助电子束在钢基体上沉积 A l2 O3 膜的 速率可达 50~ 100 nm s- 1, 而沉积 T i膜的速率高 达 1000 nm s- 1.
法, 所制备的膜层致密, 不易产生脆性断裂, 结合 强度较高, 因而具有良好的耐磨和耐蚀等性能. 气 相沉积通常分为物理气相沉积 ( PVD )和 化学气 相沉积 ( CVD). PVD 是指在真空条件下, 将成膜 物质加热或通过离子轰击等物理手段使之蒸发, 生成蒸发粒子与离子, 并在基体表面沉积成膜的 方法. 真 空 蒸发 镀 膜、离 子 镀 膜 和 溅射 镀 膜 是 PVD制备薄膜 的基 本方 法. PVD 最初 应用于 航 天、航空和半导体工业等领域. 而在机械工业中用 作表面强化技术以改善摩擦副零件的机械性能仅 在近几十年才受到重视, 目前该工艺已广泛地应 用于工模具和机械零件的表面强化处理 [ 1 - 3 ] .
电子束蒸镀是利用电子束加热, 使蒸发材料 气化后沉积在基体表面成膜 (见图 1). 其优点是 沉积率高, 特别适合制作高熔点薄膜. 然而, 电子 束蒸镀所用的靶材需具有良好的导电性能, 这使 它的应用范围受到一定的限制. 电子束斑的能量 密度是由束流和电压决定的. 林翠等 [ 8] 利用电子 束反应蒸镀技术在普通碳钢上蒸镀铝 - 铬合金膜 层的研究表明, 束流和电压的改变影响着沉积速 度和膜层的外观. 当 采用高电压 ( 10 kV ) 和低束 流 ( 30~ 50 mA )时, 膜层的外观较好, 膜层较厚, 但沉积速度较快而导致内应力过大, 易造成膜层 的爆裂; 采 用低 电压 ( 6 kV ) 和低 束流 ( 30 ~ 50 mA)时, 膜层外观差, 沉积速度过慢; 采用低电压 ( 6 kV )和高束流 ( 80 ~ 120 mA ) 时, 沉积 速度适 中, 所得的膜层较为美观, 且内应力较小, 无开裂 现象. 在 ( C /C- S iC)复合材料上采用离子辅助电 子束沉积 C r和 ( C r- A l)复 合膜的试验发现 [ 9] , 复合 层 内 原 位 形 成 了 金 属 间 化 合 物 Cr3 S i 和
硬质膜通常是指为了提高材料耐磨损、耐腐 蚀和耐高温性能而在其表面制备的膜层. 在工模 具等工件表面镀覆硬质薄膜, 能大大减轻其表面 的磨损, 显著提高其表面质量和使用寿命. 目前采 用气相沉积方法制备的硬质薄膜主要是由氮化物 构成, 其 次还有碳化物、氧化物 和类金刚石薄膜 等. 由于硬质膜大都具有高的硬度、低的摩擦系数 和良好的化学稳定性, 所以被广泛应用于工模具、 机械、化工和微电子等工业领域, 并具有显著的经 济效益和广阔的发展前景.
Fabr icating ceram ic hard th in film s by vapor deposition techn iques
T IAN Yong2sheng1, CH EN Chuan2zhong1, WANG De2yun 1, LE I T ing2quan2