物理气相沉积PVD技术
表面处理工艺PVD及其他
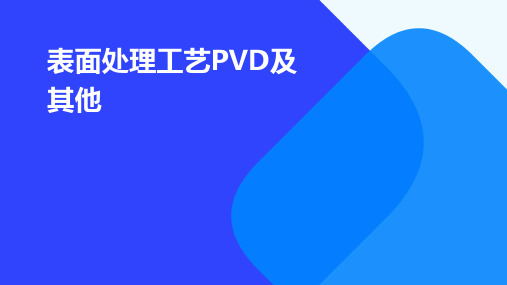
汽车外观件
PVD技术可以用于制造具有高光 泽度和耐候性的汽车外观件,如 车门、车顶和后视镜等。
汽车轻量化
PVD技术可以用于制造轻量化的 汽车零部件,如铝制零件的涂层, 以提高其硬度和耐磨性。
刀具行业
高品质刀具
PVD技术可以用于制造具有高硬度、 高耐磨性和良好抗腐蚀性的高品质刀 具,如铣刀、钻头和车刀等。
喷涂技术主要包括油漆喷涂、 粉末喷涂等,广泛应用于建筑、 机械、汽车等领域的防腐和装 饰。
喷涂技术的优点是工艺简单、 适用范围广,缺点是涂层质量 不稳定,环境污染较大。
激光表面处理
激光表面处理是一种利用高能激光束对材料表 面进行快速加热和熔融处理的表面处理技术。
激光表面处理技术主要包括激光熔覆、激光淬 火等,广泛应用于工具、模具、机械零件等的 表面强化和修复。
降低成本
通过技术创新和规模化生产,降低PVD技术的 成本,提高其市场竞争力。
提高工艺稳定性
加强技术研发和工艺优化,提高PVD技术的稳 定性和可靠性。
拓展应用领域
进一步拓展PVD技术的应用领域,满足更多行业对高性能表面处理的需求。
05
PVD表面处理工艺的实 例分析
汽车发动机活塞的PVD涂层
总结词
提高耐磨性和耐腐蚀性
PVD与电镀的比较
PVD和电镀都是表面处理技术 ,但它们所使用的工艺和材料
有所不同。
PVD技术是一种环保型表面处 理技术,它不需要使用有害的 化学试剂和添加剂,而电镀则 需要使用大量的化学试剂和添
加剂。
PVD技术可以用于制造具有高 硬度、低摩擦系数和优异耐腐 蚀性的涂层,而电镀则可以用 于制造具有高光泽度和镜面效 果的涂层。
激光表面处理技术的优点是处理速度快、精度 高,可实现局部处理,缺点是设备成本高、运 行成本高,可能引起材料变形或开裂。
物理气相沉积(PVD)技术

物理气相沉积(PVD)技术第一节 概述物理气相沉积(Physical Vapor Deposition,PVD)技术表示在真空条件下,采用物理方法,将材料源——固体或液体表面气化成气态原子、分子或部分电离成离子,并通过低压气体(或等离子体)过程,在基体表面沉积具有某种特殊功能的薄膜的技术。
物理气相沉积技术早在20世纪初已有些应用,但在最近30年迅速发展,成为一门极具广阔应用前景的新技术。
物理气相沉积的主要方法有,真空蒸镀、溅射镀膜、电弧等离子体镀、离子镀膜,及分子束外延等。
发展到目前,物理气相沉积技术不仅可沉积金属膜、合金膜、还可以沉积化合物、陶瓷、半导体、聚合物膜等。
真空蒸镀基本原理是在真空条件下,使金属、金属合金或化合物蒸发,然后沉积在基体表面上,蒸发的方法常用电阻加热,高频感应加热,电子柬、激光束、离子束高能轰击镀料,使蒸发成气相,然后沉积在基体表面,历史上,真空蒸镀是PVD法中使用最早的技术。
溅射镀膜基本原理是充氩(Ar)气的真空条件下,使氩气进行辉光放电,这时氩(Ar)原子电离成氩离子(Ar+),氩离子在电场力的作用下,加速轰击以镀料制作的阴极靶材,靶材会被溅射出来而沉积到工件表面。
如果采用直流辉光放电,称直流(Qc)溅射,射频(RF)辉光放电引起的称射频溅射。
磁控(M)辉光放电引起的称磁控溅射。
电弧等离子体镀膜基本原理是在真空条件下,用引弧针引弧,使真空金壁(阳极)和镀材(阴极)之间进行弧光放电,阴极表面快速移动着多个阴极弧斑,不断迅速蒸发甚至“异华”镀料,使之电离成以镀料为主要成分的电弧等离子体,并能迅速将镀料沉积于基体。
因为有多弧斑,所以也称多弧蒸发离化过程。
离子镀基本原理是在真空条件下,采用某种等离子体电离技术,使镀料原子部分电离成离子,同时产生许多高能量的中性原子,在被镀基体上加负偏压。
这样在深度负偏压的作用下,离子沉积于基体表面形成薄膜。
物理气相沉积技术基本原理可分三个工艺步骤:(1)镀料的气化:即使镀料蒸发,异华或被溅射,也就是通过镀料的气化源。
PVD简介

真空镀膜(PVD)简介真空镀膜(PVD)简介2009年04月27日星期一 20:16PVD(Physical Vapor Deposition),指利用物理过程实现物质转移,将原子或分子由源转移到基材表面上的过程。
它的作用是可以是某些有特殊性能(强度高、耐磨性、散热性、耐腐性等)的微粒喷涂在性能较低的母体上,使得母体具有更好的性能!PVD基本方法:真空蒸发、溅射1. PVD简介PVD是英文Physical Vapor Deposition(物理气相沉积)的缩写,是指在真空条件下,采用低电压、大电流的电弧放电技术,利用气体放电使靶材蒸发并使被蒸发物质与气体都发生电离,利用电场的加速作用,使被蒸发物质及其反应产物沉积在工件上。
2. PVD技术的发展PVD技术出现于二十世纪七十年代末,制备的薄膜具有高硬度、低摩擦系数、很好的耐磨性和化学稳定性等优点。
最初在高速钢刀具领域的成功应用引起了世界各国制造业的高度重视,人们在开发高性能、高可靠性涂层设备的同时,也在硬质合金、陶瓷类刀具中进行了更加深入的涂层应用研究。
与CVD工艺相比,PVD工艺处理温度低,在600℃以下时对刀具材料的抗弯强度无影响;薄膜内部应力状态为压应力,更适于对硬质合金精密复杂刀具的涂层;PVD工艺对环境无不利影响,符合现代绿色制造的发展方向。
目前PVD涂层技术已普遍应用于硬质合金立铣刀、钻头、阶梯钻、油孔钻、铰刀、丝锥、可转位铣刀片、异形刀具、焊接刀具等的涂层处理。
PVD技术不仅提高了薄膜与刀具基体材料的结合强度,涂层成分也由第一代的TiN发展为TiC、TiCN、ZrN、CrN、MoS2、TiAlN、TiAlCN、TiN-AlN、CNx、DLC和ta-C等多元复合涂层。
3. 涂层的PVD技术增强型磁控阴极弧:阴极弧技术是在真空条件下,通过低电压和高电流将靶材离化成离子状态,从而完成薄膜材料的沉积。
增强型磁控阴极弧利用电磁场的共同作用,将靶材表面的电弧加以有效地控制,使材料的离化率更高,薄膜性能更加优异。
是pvd处理工艺_概述说明
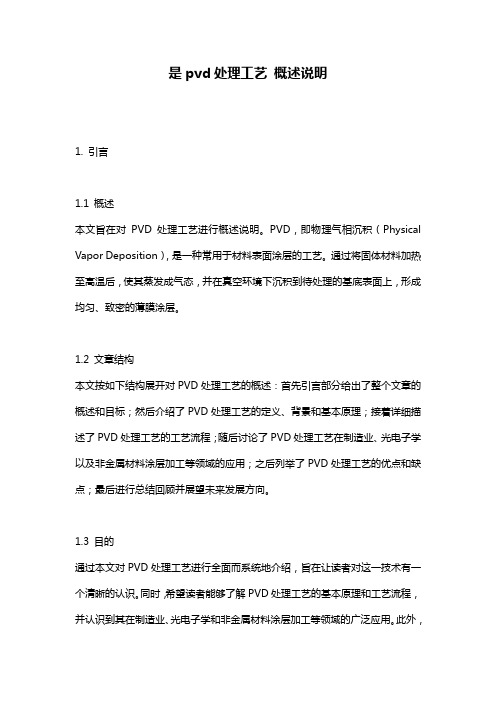
是pvd处理工艺概述说明1. 引言1.1 概述本文旨在对PVD处理工艺进行概述说明。
PVD,即物理气相沉积(Physical Vapor Deposition),是一种常用于材料表面涂层的工艺。
通过将固体材料加热至高温后,使其蒸发成气态,并在真空环境下沉积到待处理的基底表面上,形成均匀、致密的薄膜涂层。
1.2 文章结构本文按如下结构展开对PVD处理工艺的概述:首先引言部分给出了整个文章的概述和目标;然后介绍了PVD处理工艺的定义、背景和基本原理;接着详细描述了PVD处理工艺的工艺流程;随后讨论了PVD处理工艺在制造业、光电子学以及非金属材料涂层加工等领域的应用;之后列举了PVD处理工艺的优点和缺点;最后进行总结回顾并展望未来发展方向。
1.3 目的通过本文对PVD处理工艺进行全面而系统地介绍,旨在让读者对这一技术有一个清晰的认识。
同时,希望读者能够了解PVD处理工艺的基本原理和工艺流程,并认识到其在制造业、光电子学和非金属材料涂层加工等领域的广泛应用。
此外,我们也将分析和讨论PVD处理工艺的优点和缺点,以期为相关领域的研究人员和实践者提供参考,促进该技术的进一步发展。
以上是“1. 引言”部分内容的详细清晰撰写。
2. PVD处理工艺:PVD(物理气相沉积)是一种常用的表面涂层加工技术,它通过在真空环境中将固体材料蒸发或溅射成薄膜,将其沉积在待加工物体的表面上。
PVD处理工艺具有广泛的应用领域和重要的实际意义。
2.1 定义与背景:PVD处理工艺是一种以物理方式将材料从源头转移到待加工表面的技术。
其背景可以追溯到20世纪60年代,当时科学家们开始研究如何利用低压下的物理机制来制造具有优异性能和特殊功能的薄膜。
通过高纯度材料的蒸发和溅射过程,在无需化学反应的情况下形成薄膜沉积。
这种技术以其高效、环保等特点越来越受到关注。
2.2 基本原理:PVD处理工艺基于几种主要原理,包括热蒸发、电子束枪石墨棒石雾传输(EB-PVD)、直流磁控溅射(DC Sputtering)和射频磁控溅射(RF Sputtering)。
物理气相沉积(PVD)技术简介

物理气相沉积(PVD)技术简介作者:黄志云来源:《科学与财富》2019年第20期摘要:物理气相沉积技术早在20世纪初已有些应用,但在最近30年迅速发展,成为一门极具广阔应用前景的新技术。
本文主要从真空溅射镀膜、真空蒸发镀膜、行业发展现状三个方面介绍物理气相沉积技术。
关键词:PVD,真空,溅射镀膜,蒸发镀膜物理气相沉积(Physical Vapor Deposition 简称PVD)技术是制备薄膜材料的主要技术之一,指在真空条件下,采用低电压、大电流的电弧放电技术,利用气体放电使靶材蒸发并使被蒸发物质与气体都发生电离,利用电场的加速作用,使被蒸发物质及其反应产物沉积在工件上。
当下主流的两种 PVD 镀膜方式是溅射镀膜和真空蒸发镀膜。
用于制备薄膜材料的物质被称为PVD镀膜材料。
本文将从真空溅射镀膜、真空蒸发镀膜、行业发展现况三个方面介绍PVD镀膜技术。
一、真空溅射镀膜真空溅射镀膜是指在真空条件下,利用获得功能的粒子轰击靶材料表面,使靶材表面原子获得足够的能量而逃逸的过程称为溅射。
被溅射的靶材沉积到基材表面,就称作溅射镀膜。
真空溅射镀膜工艺可重复性好、膜厚可控制,可在大面积基板材料上获得厚度均匀的薄膜,所制备的薄膜具有纯度高、致密性好、与基板材料的结合力强等优点,已成为制备薄膜材料的主要技术之一。
溅射镀膜中的入射离子,一般采用辉光放电获得,在l0-2~10Pa范围,所以溅射出来的粒子在飞向基体过程中,易和真空室中的气体分子发生碰撞,使运动方向随机,沉积的膜易于均匀。
近年发展起来的规模性磁控溅射镀膜,沉积速率较高,工艺重复性好,便于自动化,已适当于进行大型建筑装饰镀膜,及工业材料的功能性镀膜,各种类型的溅射薄膜材料已得到广泛的应用,按使用的原材料材质不同,溅射靶材可分为金属/非金属单质靶材、合金靶材、化合物靶材等。
溅射镀膜工艺可重复性好、膜厚可控制,可在大面积基板材料上获得厚度均匀的薄膜,所制备的薄膜具有纯度高、致密性好、与基板材料的结合力强等优点,已成为制备薄膜材料的主要技术之一[1],各种类型的溅射薄膜材料已得到广泛的应用,因此,对溅射靶材这一具有高附加值的功能材料需求逐年增加,溅射靶材亦已成为目前市场应用量最大的PVD 镀膜材料。
科学11-班——物理气相沉积(PVD)

1、直流溅射
设备简单,操作方便,适合于溅射金属薄膜 但直流溅射中靶材只接收正离子,如果靶材是绝缘材料,阴 极表面聚集的大量正离子无法被电子中和使其电位不断上 升,阴阳两极电势减小,使溅射不能持续进行.
惰性气体
2、射频溅射
射频溅射原理:交变电场使得靶材正半周接收电子,负半周接收 正离子,相互中和,从而使阴阳两极电位的大小保持稳定,使溅射 能够持续进行.
入射粒子引起靶材表面 原子的级联碰撞示意图
在溅射过程中,通过动量传递,95%的离子能量作为热量而被损耗,仅有5%的能量传递 给二次发射的粒子。 溅射的中性粒子:二次电子:二次离子=100:10:1
辉光放电
离子束溅射
工艺昂贵
溅射过程的物理模型
阴极溅射镀膜原理示意图
1-高压屏蔽 2-高压线 3-基片 4-钟罩 5-阴极屏蔽 6-阴极 (靶材)
离子镀的类型:(从离子来源的角度可分为) 蒸发源离子镀和溅射离子镀两大类。
离子镀技术的特征:在基片上施加负偏压, 用来加速离子,增加调节离子的能量。
二极直流放电离子镀示意图
离子镀的主要优点:⑴等离子体的活性有利于降低化合物的合成温度;⑵离子 轰击提高了薄膜的致密度;⑶改善了膜层的组织结构;⑷提高膜/基结合力。
1. 所生长的材料以物理的方式由固体转化为气体 2. 生长材料的蒸汽经过一个低压区域到达衬底 3. 蒸汽在衬底表面上凝结,形成薄膜
Substrate
Substrate Substrate Substrate Substrate
热运动 原子团簇
岛 薄膜
PVD所需实验条件及实验配置
实验条件
高真空 (HV) 高纯材料
PVD
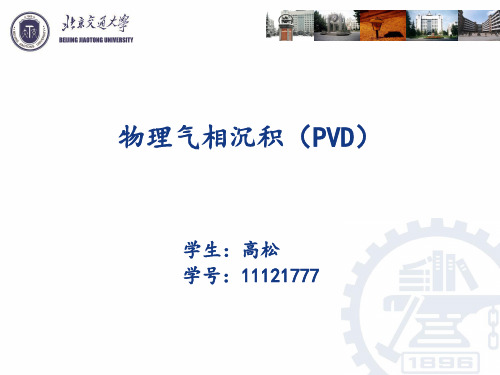
二、真空蒸发镀膜
1.真空的定义
真空:泛指低于一个大气压的气体状态。与普通的大气 状态相比,分子密度较为稀薄,从而气体分子与气体分 子,气体分子与器壁之间的碰撞几率要低些。
2.真空蒸发镀膜定义
真空蒸发镀膜(简称蒸镀)是在真空条件下,用蒸发器 加热蒸发物质使之汽化,蒸发粒子流直接射向基片并在 基片上沉积形成固态薄膜的技术。
(1)镀层附着性能好,膜层不易脱落 (2)绕镀性好,改善了表面的覆盖度 (3)镀层质量好
(4)沉积速率高,成膜速度快
(5)镀膜所适用的基体材料与膜材范围广
谢 谢!
三、真空辉光放电产生离子轰击靶材; 气压过低辉光放电难以维持(<1Pa); 溅射气压高(~10Pa)、沉积速率低; 工艺参数:电源功率、工作气体流量与压 强、基片温度、基片偏压。
四、真空离子镀膜
1、真空离子镀的定义
真空离子镀膜是真空蒸发和真空溅射镀膜结合的一种镀 膜技术。离子镀在真空条件下,利用气体放电使气体或 被蒸发物质部分电离,并在气体离子或被蒸发物质离子 的轰击下,将蒸发物质或其反应物沉积在基片上的方法。
三、真空溅射镀膜
1.真空溅射镀膜定义
真空溅射镀膜是指,在真空室中,利用荷能粒子轰击靶 材表面,使表面原子获得足够大的动能而脱离表面最终 在基片上沉积形成薄膜的技术。
真空溅射示意图
三、真空溅射镀膜
2.真空溅射镀膜优缺点
真空溅射的优缺点 真空溅射镀膜的特点 • 对于任何待镀材料,只有能做成靶材,就能实现溅射 • 溅射所获得的薄膜与基片结合良好 • 溅射所获得的薄膜纯度高,致密性好 • 溅射工艺可重复性好,膜厚可控制,同时可以在大面积基片上获得厚度均匀的 薄膜 真空溅射镀膜的缺点 • 溅射设备复杂 • 溅射淀积的成膜速率低,真空蒸镀淀积速率为0.1~5µ m/min • 基板升温较高和易受杂质气体影响
物理气相沉积技术

物理气相沉积技术1简介物理气相沉积(Physical Vapor Deposition,PVD)是一种表面处理技术,它基于原子、分子或离子在真空条件下从固体源“蒸发”或“剥离”,并在另外一个表面生成薄膜或涂层的过程。
PVD技术广泛应用于半导体、电子、机械、医疗等领域,可以改善材料表面的性能、延长使用寿命,也可以改变物体的颜色和外观。
2工艺流程PVD技术是在真空下完成的,因此主要工具是真空室,其次是沉积源,对于不同的应用场景,沉积源也会有所不同。
例如,如果是进行金属沉积,则沉积源可以是纯净金属,或者是通过将金属块或箔片加热,使其蒸发或溅射而得到的。
如果需要沉积金属氧化物,则需要放置源材料和氧气在沉积室中进行反应。
在PVD过程中,首先需要将材料放入真空室中,制备必要的工艺条件,使得沉积源的物质能够蒸发、溅射并扩散到目标基板上。
其中一个关键参数是真空度,PVD通常在10^-4~10^-8torr的高真空条件下进行。
另一个参数是沉积源与基板的距离,过近会导致过度热量和膜的不均匀厚度,过远影响膜的成形。
3分类根据真空沉积源材料的不同,PVD可分为四种类型:蒸发、离子镀、磁控溅射和分子束外延。
其中,蒸发和离子镀常常被用于制备功能性和装饰性薄膜涂层,磁控溅射则常被用于制备金属、半导体和陶瓷等薄膜,而分子束外延则适用于高质量、高洁净度的材料制备。
4应用PVD技术的应用涵盖了许多领域。
其中,电子和半导体产业是其中的重要应用领域之一。
在芯片制造过程中,PVD技术用于制备镀膜、金属连线等的处理;在随着显示技术的发展,PVD技术也被广泛应用于液晶显示器、有机EL显示器、柔性显示器等各种显示器领域。
此外,在航空航天、汽车、医疗、光学等领域都有PVD技术的应用。
5结论总的来说,PVD技术是一种成熟、广泛应用的表面处理技术。
它可以对各种材料表面进行处理,使其具有功能性和装饰性,可以改善产品的表面性能。
然而,由于技术的复杂性和设备的昂贵性,PVD技术在应用过程中也存在一定的限制性。
pvd与cvd技术适用的薄膜制程
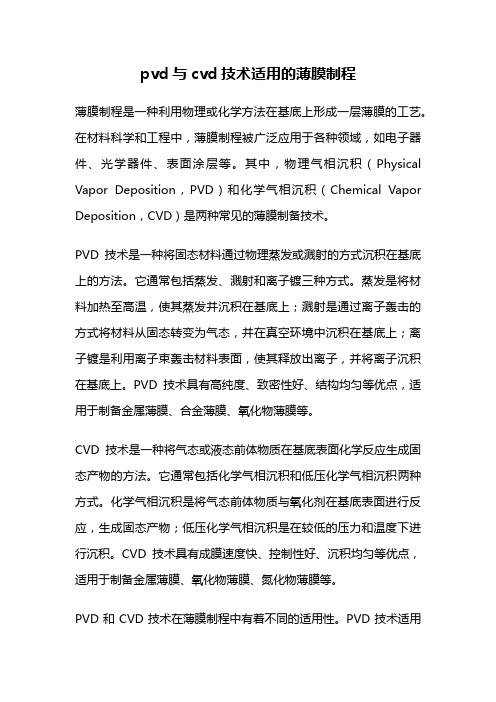
pvd与cvd技术适用的薄膜制程薄膜制程是一种利用物理或化学方法在基底上形成一层薄膜的工艺。
在材料科学和工程中,薄膜制程被广泛应用于各种领域,如电子器件、光学器件、表面涂层等。
其中,物理气相沉积(Physical Vapor Deposition,PVD)和化学气相沉积(Chemical Vapor Deposition,CVD)是两种常见的薄膜制备技术。
PVD技术是一种将固态材料通过物理蒸发或溅射的方式沉积在基底上的方法。
它通常包括蒸发、溅射和离子镀三种方式。
蒸发是将材料加热至高温,使其蒸发并沉积在基底上;溅射是通过离子轰击的方式将材料从固态转变为气态,并在真空环境中沉积在基底上;离子镀是利用离子束轰击材料表面,使其释放出离子,并将离子沉积在基底上。
PVD技术具有高纯度、致密性好、结构均匀等优点,适用于制备金属薄膜、合金薄膜、氧化物薄膜等。
CVD技术是一种将气态或液态前体物质在基底表面化学反应生成固态产物的方法。
它通常包括化学气相沉积和低压化学气相沉积两种方式。
化学气相沉积是将气态前体物质与氧化剂在基底表面进行反应,生成固态产物;低压化学气相沉积是在较低的压力和温度下进行沉积。
CVD技术具有成膜速度快、控制性好、沉积均匀等优点,适用于制备金属薄膜、氧化物薄膜、氮化物薄膜等。
PVD和CVD技术在薄膜制程中有着不同的适用性。
PVD技术适用于制备厚度较薄的薄膜,通常在几纳米到几十微米之间。
由于PVD 技术在沉积过程中,材料以固态形式进行转移,因此PVD制备的薄膜具有较高的致密性和纯度。
此外,PVD技术还可以在复杂的表面结构上进行沉积,如孔洞、凹槽等,适用于制备具有特殊形状要求的薄膜。
相比之下,CVD技术适用于制备较厚的薄膜,通常在几十纳米到几百微米之间。
由于CVD技术是通过化学反应生成固态产物,因此可以在基底表面上形成较为均匀的薄膜。
此外,CVD技术还可以在较低的温度下进行沉积,适用于对基底温度敏感的材料。
PVD(物理气相沉积)简介

书山有路勤为径,学海无涯苦作舟
PVD(物理气相沉积)简介
1. PVD 简介PVD 是英文Physical Vapor Deposition(物理气相沉积)的缩写,是指在真空条件下,采用低电压、大电流的电弧放电技术,利用气体放
电使靶材蒸发并使被蒸发物质与气体都发生电离,利用电场的加速作用,使被
蒸发物质及其反应产物沉积在工件上。
2. PVD 技术的发展PVD 技术出现于二十世纪七十年代末,制备的薄膜具
有高硬度、低摩擦系数、很好的耐磨性和化学稳定性等优点。
最初在高速钢刀
具领域的成功应用引起了世界各国制造业的高度重视,人们在开发高性能、高
可靠性涂层设备的同时,也在硬质合金、陶瓷类刀具中进行了更加深入的涂层
应用研究。
与CVD 工艺相比,PVD 工艺处理温度低,在600℃以下时对刀具材料的抗弯强度无影响;薄膜内部应力状态为压应力,更适于对硬质合金精密复
杂刀具的涂层;PVD 工艺对环境无不利影响,符合现代绿色制造的发展方向。
目前PVD 涂层技术已普遍应用于硬质合金立铣刀、钻头、阶梯钻、油孔钻、铰刀、丝锥、可转位铣刀片、异形刀具、焊接刀具等的涂层处理。
PVD 技术不仅提高了薄膜与刀具基体材料的结合强度,涂层成分也由第
一代的TiN 发展为TiC、TiCN、ZrN、CrN、MoS2、TiAlN、TiAlCN、TiN- AlN、CNx、DLC 和ta-C 等多元复合涂层。
3. 星弧涂层的PVD 技术增强型磁控阴极弧:阴极弧技术是在真空条件下,通过低电压和高电流将靶材离化成离子状态,从而完成薄膜材料的沉积。
增强型磁控阴极弧利用电磁场的共同作用,将靶材表面的电弧加以有效地控
制,使材料的离化率更高,薄膜性能更加优异。
物理气相沉积(PVD)技术物理气相沉积(PVD)技术

真空度介绍1atm=760torr=760mmHg=1.1325*105Pa(N/m2)=1.01325Bar=14.7Psi(lb/m2)粗略真空(rough vacuum):气压从<760torr-1troo中度真空(medium vacuum):气压从1torr-10-3torr高真空(high vaccum):气压从10-3torr-10-7torr超高真空(ultra-high vaccum):气压<10-7torr真空邦浦(一) 定义:凡能将一特定空间内之气体去除,以减低气体分子数目,造成某种程度之真空状态之机件,统称为真空邦浦._(二) 分类:在未介绍各种真空邦浦之结构,原理,功能等特性前,先让我们依照不同性质将真空邦浦加以分类,以得一概括之认识.依抽气型态:______ 排气式:将气体由特定空间内去除并排出至大气.______ 储气式:欲除去之气体不排至大气,而利用物理或化学作用永久或暂时性吸附在系统内.真空邦浦真空帮浦的分类机械帮浦(mechanical pump)回转油垫帮浦(rotary oil-sealed pump)此种帮浦的简单构造如图所示.机械帮浦(mechanical pump)* 工作压力范围:粗略真空中度真空~ 10-2 Torr~ 10-3 Torr (two stage)* 抽气速率:转子之转速约120 ~ 2000 l/min* 用途:低真空抽气作为Diffusion Pump,Roots Pump,Turbomolecular Pump之前置邦浦.冷冻帮浦(cryo pump)冷冻帮浦低温抽气主体构造如图所示.分为两个不同温度的低温面,第一级 (first stage)温度为50~80.K,第二级 (second stage )温度为10~20.K,在设计上,为防止辐射热对第二级的影响,第一级要将第二级完全罩住,且不可透光,同时第一级要有足够的间隙使气体能进入第二级,因此第一级通常设计成百叶窗式的45.挡片;第二级设计成倒悬的杯状,杯内部贴附有活性炭吸附材料.冷冻帮浦(cryo pump)冷冻帮浦(cryo pump)抽气时气体由系统经高真空阀而进入帮浦主体,首先碰到温度为70.K的第一级,这时水气 (H2O)和部份约二氧化碳 (C02)将丧失动能脱离气态而凝结在此低温面上,其余的气体则丧失部份动能而进入第二级,在10.K的低温下除He,H,和Ne外所有气体都将冷凝而附著在此低温面上,这种因冷却而丧失动能脱离气态的现象称之为低温冷凝作用(Cryocondensation ),至於He,Ne,H,等气体再次丧失动能后进入第二级之内部而被低温的活性炭吸附住,这种抽气现象称之为低温吸附作用(Cryosorption) .如前所示,冷冻帮浦只靠冷凝,吸附是不够的.不过在低温时有另一优点可以协助捕获不易冷凝的气体分子,此即为低温捕获.低温邦浦主要靠这三种原理来达到抽气的目的.冷冻帮浦(cryo pump)Cyropump若长期使用或是吸入大量气体,其抽气量将会降低,此时必须要对Cyropump 作再生的动作,那就是将Cyropump内部温度回升到室温,然后通以氮气来回数次,藉此将原本吸附的气体带出,如此Cyropump将可恢复原状,不过若因操作不当有油气进入Cyropump污染了内部的活性炭,则必须全部更换活性炭才有办法恢复原抽气量.冷冻帮浦-再生冷冻帮浦(cryo pump)* 工作压力范围:中度真空高度真空1.压力范围:10-3~10-10.torr2.抽气速率大小:(对空气)500~10000 l / sec3.用途:高真空或超高真空抽气使用4.特点:乾净,无油气污染反应性溅镀反应性溅镀物气相沉积(PVD)处 ,又可分为真空蒸镀( Vacuum Evaporation),溅射(Sputtering), 子蒸镀(Ion Plating) 等三种型态.溅镀法是在辉光放电的环境下, 用动传递的方式,以子轰击置於阴极的靶材,将靶原子溅射出并积於基板上.在溅镀化合物薄膜时, 直接以化合物做为靶材,溅镀出的薄膜成份会与靶材成份相差很大,故一般在溅镀化合物薄膜时,通常将反应气体混合於放电气体中,以控制化合物薄膜的组成与性质,此种溅镀方法称为反应性溅镀法.在反应性溅射中,所通入的反应气体可能被消耗的途径包含在靶材表面被吸附(adsorbed),(包括腔体内部其它表面含基板表面) , 与溅射原子发生化学吸附(chemisorption).反应性溅镀脉冲直溅镀脉冲直溅镀脉冲直反应式磁控溅镀系统所采用的电源系统为脉冲式电源供应系统,有别於传统的直式电源与射频式电源,脉冲式电源供应系统可提供五种同的电压输出模式,如图所示,分别为(1)DC+,(2)DC-,(3)UP+,(4)UP-以及(5)BIPOLAR.可依照同的制程需求而采用同的模式,且可调整脉冲频 ,脉冲宽及工作周期以达到制程的最佳化.脉冲直溅镀脉冲直溅镀脉冲式电源系统除上述功能外,还可藉由被动抑弧方式解决电弧放电的问题.如图所示,Ton+/-分别表示为正放电时间及负放电时间,Toff即表示为中断放电时间,Imax为脉冲式电源的最大输出电 ,Arc level表示当电值超过此范围时进入电弧放电区.被动抑弧的工作方式为当制程中发生常放电现象时 ,系统中的电值会发生遽增的现象,此时脉冲电源供应器将延缓电源输出,以抑制常放电现象持续进 ,即图中的arc avoidance. 常放电现象再发生时,则电压及电又将恢正常供输.脉冲直溅镀物理气相沉积(PVD)技术第一节概述物理气相沉积技术早在20世纪初已有些应用,但在最近30年迅速发展,成为一门极具广阔应用前景的新技术。
8.2 物理汽相沉积(PVD)

图8.2.10 辉光放电
3. 溅射机理——两种假说 (1)Hippel理论(1926提出) 离子轰击靶产生的局部高温使靶材料(阴 极材料)的局部蒸发,在阳极上沉积制膜。
(2)动能转移机理 (Stark,1909,Langmuir, Henschk)
(I) 溅射出的原子能量比热蒸发原子能量高一个数量级; (II)轰击离子存在一个临界能量,低于这个能量,不能产生溅 射; (Ⅲ)溅射系数=溅射原子数/轰击离子数,既与轰击离子的能量 1 mv 2 有关,也与轰击离子的质量有关 ( ,动能转移 ); 2 (Ⅳ)离子能量过高,溅射系数反而下降,可能是因为离子深入 到靶材内部,能量没有交给表面附近原子的缘故; (Ⅴ)溅射原子出射的角分布,对于单晶靶材,粒子主要沿几个 方向出射。 最强的出射方向对应于晶格中原子最密集排列的方向,这 种现象可用“聚焦碰撞”解释。
(g/cm2· s)
(4)
② 凝结速Na:
——蒸发源对基片单位面积的沉积速率。 Na与系统的几何形状、源与基片的相对位置、蒸发速率有关
设:a. 忽略碰撞,直线运动;
点源,球面发射: N AN e cos a 2
b.
A r
4r
(1/cm2· s)
(5)
小型圆平面源:
AN e cos cos Nd r 2
∴ 连续加料,保证熔池料为 A1B25, 从而膜料成分为A4B1;
在蒸镀过程中,还应注意使熔池温度和体积保持恒定。
(2)蒸镀难熔化合物膜——多数会分解
例如:A12O3 Al、AlO、(AlO)2、Al2O、O和O2 等, 解决对策——适当通氧 (15)
(3)反应镀膜 2Ti C2 H 2 2TiC H 2 6.蒸镀的特点和用途
PVD简介(物理气相沉积)

PVD简介(物理气相沉积)PVD简介PVD是英文Physical Vapor Deposition的缩写,中文意思是“物理气相沉积”,是指在真空条件下,用物理的方法使材料沉积在被镀工件上的薄膜制备技术。
2. PVD镀膜和PVD镀膜机—PVD(物理气相沉积)镀膜技术主要分为三类,真空蒸发镀膜、真空溅射镀和真空离子镀膜。
对应于PVD技术的三个分类,相应的真空镀膜设备也就有真空蒸发镀膜机、真空溅射镀膜机和真空离子镀膜机这三种。
近十多年来,真空离子镀膜技术的发展是最快的,它已经成为当今最先进的表面处理方式之一。
我们通常所说的PVD镀膜,指的就是真空离子镀膜;通常所说的PVD镀膜机,指的也就是真空离子镀膜机。
3. PVD镀膜技术的原理—PVD镀膜(离子镀膜)技术,其具体原理是在真空条件下,采用低电压、大电流的电弧放电技术,利用气体放电使靶材蒸发并使被蒸发物质与气体都发生电离,利用电场的加速作用,使被蒸发物质及其反应产物沉积在工件上。
4. PVD镀膜膜层的特点—采用PVD镀膜技术镀出的膜层,具有高硬度、高耐磨性(低摩擦系数)、很好的耐腐蚀性和化学稳定性等特点,膜层的寿命更长;同时膜层能够大幅度提高工件的外观装饰性能。
5. PVD镀膜能够镀出的膜层种类—PVD镀膜技术是一种能够真正获得微米级镀层且无污染的环保型表面处理方法,它能够制备各种单一金属膜(如铝、钛、锆、铬等),氮化物膜(TiN、ZrN、CrN、TiAlN)和碳化物膜(TiC、TiCN),以及氧化物膜(如TiO等)。
6. PVD镀膜膜层的厚度—PVD镀膜膜层的厚度为微米级,厚度较薄,一般为0.3μm ~5μm,其中装饰镀膜膜层的厚度一般为0.3μm ~1μm ,因此可以在几乎不影响工件原来尺寸的情况下提高工件表面的各种物理性能和化学性能,镀后不须再加工。
7. PVD镀膜能够镀出的膜层的颜色种类—PVD镀膜目前能够做出的膜层的颜色有深金黄色,浅金黄色,咖啡色,古铜色,灰色,黑色,灰黑色,七彩色等。
PVD(物理气相沉积)
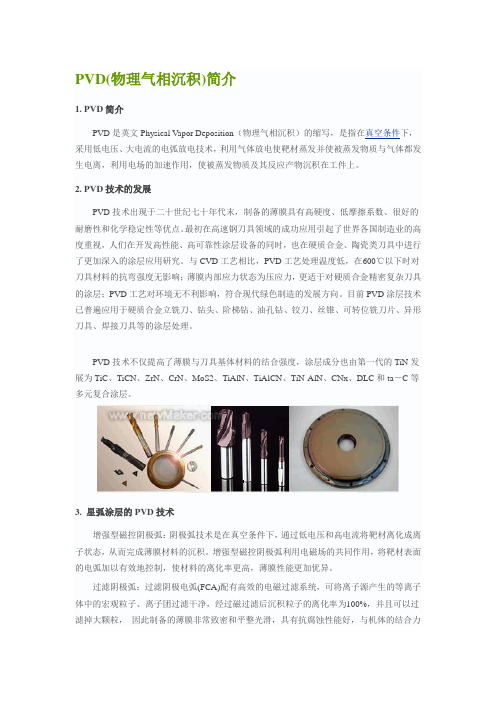
PVD(物理气相沉积)简介1. PVD简介PVD是英文Physical Vapor Deposition(物理气相沉积)的缩写,是指在真空条件下,采用低电压、大电流的电弧放电技术,利用气体放电使靶材蒸发并使被蒸发物质与气体都发生电离,利用电场的加速作用,使被蒸发物质及其反应产物沉积在工件上。
2. PVD技术的发展PVD技术出现于二十世纪七十年代末,制备的薄膜具有高硬度、低摩擦系数、很好的耐磨性和化学稳定性等优点。
最初在高速钢刀具领域的成功应用引起了世界各国制造业的高度重视,人们在开发高性能、高可靠性涂层设备的同时,也在硬质合金、陶瓷类刀具中进行了更加深入的涂层应用研究。
与CVD工艺相比,PVD工艺处理温度低,在600℃以下时对刀具材料的抗弯强度无影响;薄膜内部应力状态为压应力,更适于对硬质合金精密复杂刀具的涂层;PVD工艺对环境无不利影响,符合现代绿色制造的发展方向。
目前PVD涂层技术已普遍应用于硬质合金立铣刀、钻头、阶梯钻、油孔钻、铰刀、丝锥、可转位铣刀片、异形刀具、焊接刀具等的涂层处理。
PVD技术不仅提高了薄膜与刀具基体材料的结合强度,涂层成分也由第一代的TiN发展为TiC、TiCN、ZrN、CrN、MoS2、TiAlN、TiAlCN、TiN-AlN、CNx、DLC和ta-C等多元复合涂层。
3. 星弧涂层的PVD技术增强型磁控阴极弧:阴极弧技术是在真空条件下,通过低电压和高电流将靶材离化成离子状态,从而完成薄膜材料的沉积。
增强型磁控阴极弧利用电磁场的共同作用,将靶材表面的电弧加以有效地控制,使材料的离化率更高,薄膜性能更加优异。
过滤阴极弧:过滤阴极电弧(FCA)配有高效的电磁过滤系统,可将离子源产生的等离子体中的宏观粒子、离子团过滤干净,经过磁过滤后沉积粒子的离化率为100%,并且可以过滤掉大颗粒,因此制备的薄膜非常致密和平整光滑,具有抗腐蚀性能好,与机体的结合力很强。
磁控溅射:在真空环境下,通过电压和磁场的共同作用,以被离化的惰性气体离子对靶材进行轰击,致使靶材以离子、原子或分子的形式被弹出并沉积在基件上形成薄膜。
物理气相沉积 相场法
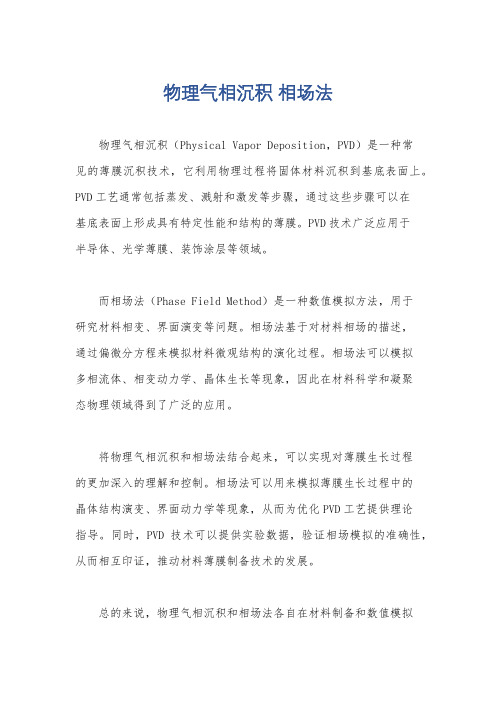
物理气相沉积相场法
物理气相沉积(Physical Vapor Deposition,PVD)是一种常
见的薄膜沉积技术,它利用物理过程将固体材料沉积到基底表面上。
PVD工艺通常包括蒸发、溅射和激发等步骤,通过这些步骤可以在
基底表面上形成具有特定性能和结构的薄膜。
PVD技术广泛应用于
半导体、光学薄膜、装饰涂层等领域。
而相场法(Phase Field Method)是一种数值模拟方法,用于
研究材料相变、界面演变等问题。
相场法基于对材料相场的描述,
通过偏微分方程来模拟材料微观结构的演化过程。
相场法可以模拟
多相流体、相变动力学、晶体生长等现象,因此在材料科学和凝聚
态物理领域得到了广泛的应用。
将物理气相沉积和相场法结合起来,可以实现对薄膜生长过程
的更加深入的理解和控制。
相场法可以用来模拟薄膜生长过程中的
晶体结构演变、界面动力学等现象,从而为优化PVD工艺提供理论
指导。
同时,PVD技术可以提供实验数据,验证相场模拟的准确性,从而相互印证,推动材料薄膜制备技术的发展。
总的来说,物理气相沉积和相场法各自在材料制备和数值模拟
领域有着重要的应用,结合起来可以为材料薄膜制备过程提供更深入的理论基础和技术支持。
这种多角度的结合有助于推动材料科学和工程领域的发展,促进新材料的研发和应用。
PVD(Sputter)介绍
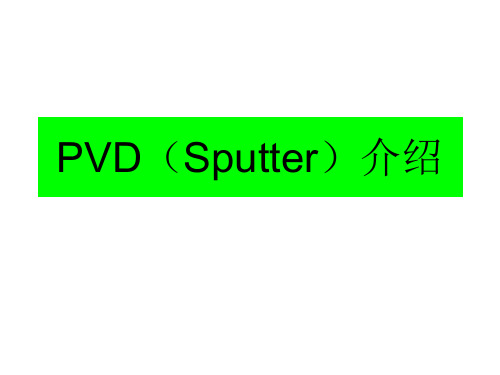
PVD(Sputter)介绍
3、Sputter Coating成膜过程:溅射过程 是以动量传递的离子轰击为基础的动力学过 程。具有高能量的入射离子与靶原子产生碰 撞,通过能量传递,使靶原子获得一定动能 之后脱离靶材表面飞溅出来。 从溅射靶中出来的沉积粒子入射基体表 面之后,在基体表面上形成吸附原子后,它 便失去了在表面法线方向的动能,只具有与 表面水平方向相平行运动的动能。依靠这种 动能,吸附原子在表面上作不同方向的表面 扩散运动.在表面扩散过程中,单个吸附原子 间相互碰撞形成原子对之后才能产生凝结。 经过吸附、凝结、表面扩散迁移、碰撞结合 形成稳定晶核。然后再通过吸附使晶核长大 成小岛,岛长大后互相联结聚结,最后形成 连续状薄膜。
PVD(Sputter)介绍
2、电浆放电系统种类:电浆放电系统可分为以下几种— —热电阻式、电子束式、直流溅射、射频溅射、离子溅射、 镭射剥镀、分子束磊晶系统、冷阴极电弧电浆沉积; 3、溅镀的模型:图2中的母球代表被电离后的气体分子, 而红色各球则代表将被溅镀之靶材(Si、ITO&Ti等),图3则 代表溅镀后被溅射出的原子、分子等的运动情形;即当被加 速的离子与表面撞击后,通过能量与动量转移过程(如图4), 低能离子碰撞靶时,不能从固体表面直接溅射出原子,而是 把动量转移给被碰撞的原子,引起晶格点阵上原子的链锁式 碰撞。这种碰撞将沿着晶体点阵的各个方向进行。同时,碰 撞因在原子最紧密排列的点阵方向上最为有效,结果晶体表 面的原子从邻近原子那里得到愈来愈大的能量,如果这个能 量大于原子的结合能,原子就从固体表面从各个方向溅射出 来;
PVD(Sputter)介绍
PVD(Sputter)介绍
1:PVD:即物理气相沉积(Physicql Vapor Deposition)的简称,包括真空蒸发镀膜,溅 射镀膜,离子束和离子助,外延膜沉积技术 等四大类. 2:PECVD:即等离子增强化学气相沉积 (Plasma-Enhanced Chmical vapor Deposition),其他还有LPCVD ,MOCVD, 等. APCVD
气相沉积CVD、PVD简介
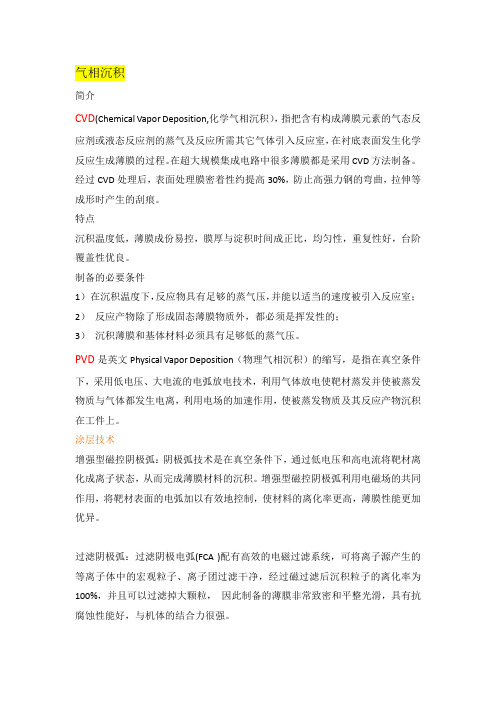
气相沉积简介CVD(Chemical Vapor Deposition,化学气相沉积),指把含有构成薄膜元素的气态反应剂或液态反应剂的蒸气及反应所需其它气体引入反应室,在衬底表面发生化学反应生成薄膜的过程。
在超大规模集成电路中很多薄膜都是采用CVD方法制备。
经过CVD处理后,表面处理膜密着性约提高30%,防止高强力钢的弯曲,拉伸等成形时产生的刮痕。
特点沉积温度低,薄膜成份易控,膜厚与淀积时间成正比,均匀性,重复性好,台阶覆盖性优良。
制备的必要条件1)在沉积温度下,反应物具有足够的蒸气压,并能以适当的速度被引入反应室;2)反应产物除了形成固态薄膜物质外,都必须是挥发性的;3)沉积薄膜和基体材料必须具有足够低的蒸气压。
PVD是英文Physical Vapor Deposition(物理气相沉积)的缩写,是指在真空条件下,采用低电压、大电流的电弧放电技术,利用气体放电使靶材蒸发并使被蒸发物质与气体都发生电离,利用电场的加速作用,使被蒸发物质及其反应产物沉积在工件上。
涂层技术增强型磁控阴极弧:阴极弧技术是在真空条件下,通过低电压和高电流将靶材离化成离子状态,从而完成薄膜材料的沉积。
增强型磁控阴极弧利用电磁场的共同作用,将靶材表面的电弧加以有效地控制,使材料的离化率更高,薄膜性能更加优异。
过滤阴极弧:过滤阴极电弧(FCA )配有高效的电磁过滤系统,可将离子源产生的等离子体中的宏观粒子、离子团过滤干净,经过磁过滤后沉积粒子的离化率为100%,并且可以过滤掉大颗粒,因此制备的薄膜非常致密和平整光滑,具有抗腐蚀性能好,与机体的结合力很强。
磁控溅射:在真空环境下,通过电压和磁场的共同作用,以被离化的惰性气体离子对靶材进行轰击,致使靶材以离子、原子或分子的形式被弹出并沉积在基件上形成薄膜。
根据使用的电离电源的不同,导体和非导体材料均可作为靶材被溅射。
离子束DLC:碳氢气体在离子源中被离化成等离子体,在电磁场的共同作用下,离子源释放出碳离子。
PVD制程介绍范文
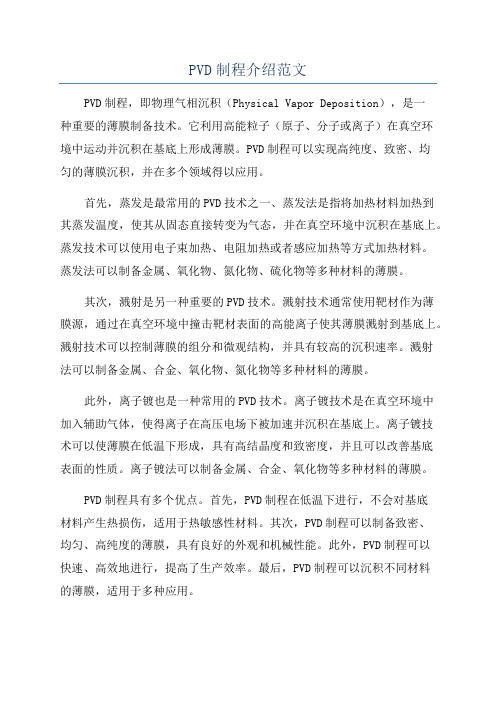
PVD制程介绍范文PVD制程,即物理气相沉积(Physical Vapor Deposition),是一种重要的薄膜制备技术。
它利用高能粒子(原子、分子或离子)在真空环境中运动并沉积在基底上形成薄膜。
PVD制程可以实现高纯度、致密、均匀的薄膜沉积,并在多个领域得以应用。
首先,蒸发是最常用的PVD技术之一、蒸发法是指将加热材料加热到其蒸发温度,使其从固态直接转变为气态,并在真空环境中沉积在基底上。
蒸发技术可以使用电子束加热、电阻加热或者感应加热等方式加热材料。
蒸发法可以制备金属、氧化物、氮化物、硫化物等多种材料的薄膜。
其次,溅射是另一种重要的PVD技术。
溅射技术通常使用靶材作为薄膜源,通过在真空环境中撞击靶材表面的高能离子使其薄膜溅射到基底上。
溅射技术可以控制薄膜的组分和微观结构,并具有较高的沉积速率。
溅射法可以制备金属、合金、氧化物、氮化物等多种材料的薄膜。
此外,离子镀也是一种常用的PVD技术。
离子镀技术是在真空环境中加入辅助气体,使得离子在高压电场下被加速并沉积在基底上。
离子镀技术可以使薄膜在低温下形成,具有高结晶度和致密度,并且可以改善基底表面的性质。
离子镀法可以制备金属、合金、氧化物等多种材料的薄膜。
PVD制程具有多个优点。
首先,PVD制程在低温下进行,不会对基底材料产生热损伤,适用于热敏感性材料。
其次,PVD制程可以制备致密、均匀、高纯度的薄膜,具有良好的外观和机械性能。
此外,PVD制程可以快速、高效地进行,提高了生产效率。
最后,PVD制程可以沉积不同材料的薄膜,适用于多种应用。
PVD技术在许多领域得到了广泛应用。
在半导体工业中,PVD制程广泛应用于制备金属薄膜,如铝、铜等,以作为导线、电极等。
在光学薄膜领域,PVD制程用于制备反射膜、透明电极等。
在显示器生产中,PVD技术被用于制备透明导电膜。
PVD制程还被应用于表面涂层、摩擦材料等领域。
总之,PVD制程是一种重要的薄膜制备技术,通过高能粒子在真空环境中沉积在基底上形成薄膜。
pvd方法

PVD方法是一种物理气相沉积方法,全称为物理气相沉积(Physical Vapor Deposition)。
它是一种将固态材料转化为蒸汽或气体形式,然后通过凝结在基底表面上形成薄膜的方法。
PVD方法通常包括以下步骤:
1. 准备基底:将需要镀膜的基底进行清洗和处理,以确保表面干净和平整。
2. 加热源:使用电阻加热、电子束加热或激光加热等方式,将固态材料加热至其蒸汽或气体形式。
3. 蒸发:加热后的固态材料开始蒸发,形成蒸汽或气体。
4. 沉积:蒸汽或气体通过真空环境,沉积在基底表面上,形成薄膜。
5. 控制:通过控制沉积速率、温度和压力等参数,调节薄膜的厚度和性质。
6. 冷却:薄膜沉积完成后,将基底冷却至室温,使薄膜固化。
PVD方法具有以下优点:
1. 薄膜均匀性好:PVD方法可以在基底表面均匀沉积薄膜,薄膜的厚度和性质可以通过控制参数进行调节。
2. 薄膜结构致密:PVD方法沉积的薄膜结构致密,具有较高的密度和较好的附着力。
3. 可用于多种材料:PVD方法可以用于沉积多种材料的薄膜,包括金属、合金、氧化物等。
4. 无需溶剂:PVD方法是一种无溶剂的沉积方法,对环境友好。
PVD方法在许多领域都有广泛应用,包括电子器件、光学薄膜、防腐蚀涂层等。
- 1、下载文档前请自行甄别文档内容的完整性,平台不提供额外的编辑、内容补充、找答案等附加服务。
- 2、"仅部分预览"的文档,不可在线预览部分如存在完整性等问题,可反馈申请退款(可完整预览的文档不适用该条件!)。
- 3、如文档侵犯您的权益,请联系客服反馈,我们会尽快为您处理(人工客服工作时间:9:00-18:30)。
物理气相沉积(PVD)技术
第一节 概述
物理气相沉积技术早在20世纪初已有些应用,但在最近30年迅速发展,成为一门极具广阔应用前景的新技术。
,并向着环保型、清洁型趋势发展。
20世纪90年代初至今,在钟表行业,尤其是高档手表金属外观件的表面处理方面达到越来越为广泛的应用。
物理气相沉积(Physical Vapor Deposition,PVD)技术表示在真空条件下,采用物理方法,将材料源——固体或液体表面气化成气态原子、分子或部分电离成离子,并通过低压气体(或等离子体)过程,在基体表面沉积具有某种特殊功能的薄膜的技术。
物理气相沉积的主要方法有,真空蒸镀、溅射镀膜、电弧等离子体镀、离子镀膜,及分子束外延等。
发展到目前,物理气相沉积技术不仅可沉积金属膜、合金膜、还可以沉积化合物、陶瓷、半导体、聚合物膜等。
真空蒸镀基本原理是在真空条件下,使金属、金属合金或化合物蒸发,然后沉积在基体表面上,蒸发的方法常用电阻加热,高频感应加热,电子柬、激光束、离子束高能轰击镀料,使蒸发成气相,然后沉积在基体表面,历史上,真空蒸镀是PVD法中使用最早的技术。
溅射镀膜基本原理是充氩(Ar)气的真空条件下,使氩气进行辉光放电,这时氩(Ar)原子电离成氩离子(Ar+),氩离子在电场力的作用下,加速轰击以镀料制作的阴极靶材,靶材会被溅射出来而沉积到工件表面。
如果采用直流辉光放电,称直流(Qc)溅射,射频(RF)辉光放电引起的称射频溅射。
磁控(M)辉光放电引起的称磁控溅射。
电弧等离子体镀膜基本原理是在真空条件下,用引弧针引弧,使真空金壁(阳极)和镀材(阴极)之间进行弧光放电,阴极表面快速移动着多个阴极弧斑,不断迅速蒸发甚至“异华”镀料,使之电离成以镀料为主要成分的电弧等离子体,并能迅速将镀料沉积于基体。
因为有多弧斑,所以也称多弧蒸发离化过程。
离子镀基本原理是在真空条件下,采用某种等离子体电离技术,使镀料原子部分电离成离子,同时产生许多高能量的中性原子,在被镀基体上加负偏压。
这样在深度负偏压的作用下,离子沉积于基体表面形成薄膜。
物理气相沉积技术基本原理可分三个工艺步骤:
(1)镀料的气化:即使镀料蒸发,异华或被溅射,也就是通过镀料的气化源。
(2)镀料原子、分子或离子的迁移:由气化源供出原子、分子或离子经过碰撞后,产生多种反应。
(3)镀料原子、分子或离子在基体上沉积。
物理气相沉积技术工艺过程简单,对环境改善,无污染,耗材少,成膜均匀致密,与基体的结合力强。
该技术广泛应用于航空航天、电子、光学、机械、建筑、轻工、冶金、材料等领域,可制备具有耐磨、耐腐饰、装饰、导电、绝缘、光导、压电、磁性、润滑、超导等特性的膜层。
随着高科技及新兴工业发展,物理气相沉积技术出现了不少新的先进的亮点,如多弧离子镀与磁控溅射兼容技术,大型矩形长弧靶和溅射靶,非平衡磁控溅射靶,孪生靶技术,带状泡沫多弧沉积卷绕镀层技术,条状纤维织物卷绕镀层技术等,使用的镀层成套设备,向计算机全自动,大型化工业规模方向发展。
第二节 真空蒸镀
(一)真空蒸镀原理
(1)真空蒸镀是在真空条件下,将镀料加热并蒸发,使大量的原子、分子气化并离开液体镀料或离开固
体镀料表面(升华)。
(2)气态的原子、分子在真空中经过很少的碰撞迁移到基体。
(3)镀料原子、分子沉积在基体表面形成薄膜。
(二)蒸发源
将镀料加热到蒸发温度并使之气化,这种加热装置称为蒸发源。
最常用的蒸发源是电阻蒸发源和电子束蒸发源,特殊用途的蒸发源有高频感应加热、电弧加热、辐射加热、激光加热蒸发源等。
(三)真空蒸镀工艺实例
以塑料金属化为例。
真空蒸镀工艺包括:镀前处理、镀膜及后处理。
真空蒸镀的基本工艺过程如下:
(1)镀前处理,包括清洗镀件和预处理。
具体清洗方法有清洗剂清洗、化学溶剂清洗、超声波清洗和离子轰击清洗等。
具体预处理有除静电,涂底漆等。
(2)装炉,包括真空室清理及镀件挂具的清洗,蒸发源安装、调试、镀件褂卡。
(3)抽真空,一般先粗抽至6.6Pa以上,更早打开扩散泵的前级维持真空泵,加热扩散泵,待预热足够后,打开高阀,用扩散泵抽至6×10 -3Pa半底真空度。
(4)烘烤,将镀件烘烤加热到所需温度。
(5)离子轰击,真空度一般在10Pa~10-1Pa,离子轰击电压200V~1kV负高压,离击时间为5min~30min
(6)预熔,调整电流使镀料预熔,调整电流使镀料预熔,除气1min~2min。
(7)蒸发沉积,根据要求调整蒸发电流,直到所需沉积时间结束。
(8)冷却,镀件在真空室内冷却到一定温度。
(9)出炉,.取件后,关闭真空室,抽真空至l × l0-1Pa,扩散泵冷却到允许温度,才可关闭维持泵和冷却水。
(10)后处理,涂面漆。
第三节 溅射镀膜
溅射镀膜是指在真空条件下,利用获得功能的粒子轰击靶材料表面,使靶材表面原子获得足够的能量而逃逸的过程称为溅射。
被溅射的靶材沉积到基材表面,就称作溅射镀膜。
溅射镀膜中的入射离子,一般采用辉光放电获得,在l0-2Pa~10Pa范围,所以溅射出来的粒子在飞向基体过程中,易和真空室中的气体分子发生碰撞,使运动方向随机,沉积的膜易于均匀。
近年发展起来的规模性磁控溅射镀膜,沉积速率较高,工艺重复性好,便于自动化,已适当于进行大型建筑装饰镀膜,及工业材料的功能性镀膜,及TGN-JR型用多弧或磁控溅射在卷材的泡沫塑料及纤维织物表面镀镍Ni及银Ag。
第四节 电弧蒸发和电弧等离子体镀膜
这里指的是PVD领域通常采用的冷阴极电弧蒸发,以固体镀料作为阴极,采用水冷、使冷阴极表面形成许多亮斑,即阴极弧斑。
弧斑就是电弧在阴极附近的弧根。
在极小空间的电流密度极高,弧斑尺寸极小,估计约为1μm~100μm,电流密度高达l05A/cm2~107A/cm2。
每个弧斑存在极短时间,爆发性地蒸发离化阴极改正点处的镀料,蒸发离化后的金属离子,在阴极表面也会产生新的弧斑,许多弧斑不断产生和消失,所以又称多弧蒸发。
最早设计的等离子体加速器型多弧蒸发离化源,是在阴极背后配置磁场,使蒸发后的离子获得霍尔(hall)加速效应,有利于离子增大能量轰击量体,采用这种电弧蒸发离化源镀膜,离化率较高,所以又称为电弧等离子体镀膜。
由于镀料的蒸发离化靠电弧,所以属于区别于第二节,第三节所述的蒸发手段。
第五节 离子镀
离子镀技术最早在1963年由D.M.Mattox提出,1972年,Bunshah &Juntz推出活性反应蒸发离子镀(AREIP),沉积TiN,TiC等超硬膜,1972年Moley&Smith发展完善了空心热阴极离子镀,l973年又发展出射频离子镀(RFIP)。
20世纪80年代,又发展出磁控溅射离子镀(MSIP)和多弧离子镀(MAIP)。
(一)离子镀
离子镀的基本特点是采用某种方法(如电子束蒸发磁控溅射,或多弧蒸发离化等)使中性粒子电离成离子和电子,在基体上必须施加负偏压,从而使离子对基体产生轰击,适当降低负偏压后,使离子进而沉积于基体成膜。
离子镀的优点如下:①膜层和基体结合力强。
②膜层均匀,致密。
③在负偏压作用下绕镀性好。
④无污染。
⑤多种基体材料均适合于离子镀。
(二)反应性离子镀
如果采用电子束蒸发源蒸发,在坩埚上方加20V~100V的正偏压。
在真空室中导人反应性气体。
如N2、02、C2H2、CH4等代替Ar,或混入Ar,电子束中的高能电子(几千至几万电子伏特),不仅使镀料熔化蒸发,而且能在熔化的镀料表面激励出二次电子,这些二次电子在上方正偏压作用下加速,与镀料蒸发中性粒子发生碰撞而电离成离子,在工件表面发生离化反应,从而获得氧化物(如Te02:Si02、Al203、Zn0、Sn02、Cr203、Zr02、In02等)。
其特点是沉积率高,工艺温度低。
(三)多弧离子镀
多弧离子镀又称作电弧离子镀,由于在阴极上有多个弧斑持续呈现,故称作“多弧”。
多弧离子镀的主要特点如下:
(1)阴极电弧蒸发离化源可从固体阴极直接产生等离子体,而不产生熔池,所以可以任意方位布置,也可采用多个蒸发离化源。
(2)镀料的离化率高,一般达60%~90%,显著提高与基体的结合力改善膜层的性能。
(3)沉积速率高,改善镀膜的效率。
(4)设备结构简单,弧电源工作在低电压大电流工况,工作较为安全。