SPS-9102AMWG中文资料
TC9102A(电话拔号IC)pdf

TC9102A (文件编号:S&CIC1035) 电话拔号IC一、 概述TC9102A 是音频/脉冲可转换的拔号器,有上次号码重拔(LNB )功能。
它采用CMOS 工艺制造,无论在音频方式还是在脉冲方式下,工作电压范围都很宽。
挂机状态下的保持电流很小。
TC9102A 采用DIP-18封装形式。
二、 特点音频/脉冲可转换的拔号电路 一个32位上次号码重拔存储器脉冲转音频(P→T )键,供PBX 使用 有闪断键最短音频持续时间为100ms 最短音频间隔时间为106ms使用3.579845MHz 晶体或陶瓷谐振器 重拔暂停时间(0ms)提供混合拔号功能有上电复位电路提供多种方式选择:拔号方式(10PPS:20PPS;音源) 续继比(40:60;30:66) 暂停时间(3.6S) 闪断功能(RESET)(P→T )等候时间(3.6S) 闪断时间(600/100ms) 闪断暂停时间(0ms)三、 引脚定义TC9102A(文件编号:S&CIC1035)电话拔号ICTC9102A(文件编号:S&CIC1035)电话拔号ICTC9102A(文件编号:S&CIC1035)电话拔号IC 四、键盘排列2、P:暂停键3、F:闪断键4、RD:重拔键5、*/P:在音频方式下,执行*;在脉冲方式下,执行暂停6、#/RD:在音频方式下,执行#;在脉冲方式下,重拔五、拔号信号选择六、极限参数(除非特殊说明:T amb=25℃,VDD=3.6V,fosc=3.579545MHz)七、电气参数(除非特殊说明,T amb=25℃,VDD=3.6V,fosc=3.579545MHz)TC9102A(文件编号:S&CIC1035)电话拔号IC2、失真(dB)=20Iog{[V12+V22+V32+…Vn2]1/2]/[(V L2+V H2)1/2]}V L,V H:行和列的信号。
V1,V2…,Vn为谐波信号(带宽=300Hz~3500Hz)TC9102A(文件编号:S&CIC1035)电话拔号IC 八、实际频率输出(fosc=3.579545MHz)九、键盘操作符号定义:a) ↑ :摘机或使免提功能工作。
Fluke 9100S和9102S手持干燥井说明书
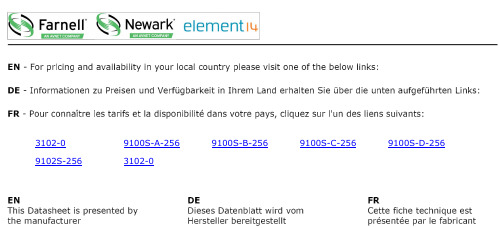
3102-09100S-A-2569100S-B-2569100S-C-2569100S-D-256 9102S-2563102-0Published on Fluke Calibration: Europe9102S Dry-WellFor work in the temperature range of –10°C to 122°C, our Model 9102S dry-well is another first in the industry, featuring stability to ±0.05°C.This dry-well is only four inches high and six inches wide, achieves temperatures as low as –10°C, includes a NIST-traceable calibration, and is stable to ±0.05°C. The Model 9102S is excellent for dial gauges, digital thermometers, bulb switches, and other sensors that need calibration below ambient.The 9102S has two wells so you can use one for a reference thermometer to increase accuracy. Both wells are 1/2 inch in diameter, and each has inserts available for almost any sensor size. The 9102S also has a battery pack option that gives you approximately four hours of field use when AC power is unavailable.SpecificationsSpecifications9100S 9102S Range35 °C to 375 °C (95 °F to 707°F –10 °C to 122 °C (14 °F to 252 °F) at23 °C ambient Accuracy± 0.25 °C at 50 °C; ± 0.25°C at 100 °C; ± 0.5 °C at 375°C ± 0.25 °C Stability± 0.07 °C at 50 °C; ± 0.1 °C at 100 °C; ± 0.3 °C at 375 °C ± 0.05 °C Well-to-Well Uniformity± 0.2 °C with sensors of similar size at equal depths within wells Heating Times35 °C to 375 °C: 9.5 minutes ambient to 100 °C: 10minutes Stabilization5 minutes 7 minutes Cooling Times375 °C to 100 °C: 14 minutes ambient to 0 °C: 10 minutes Well Depth 102 mm (4 in);1.6 mm (1/16in) hole is 89 mm (3.5 in)deep102 mm (4 in)Removable Inserts;N/AAvailable in sizes from 1.6 mm (1/16 in) to 11.1 mm (7/16in) [6.4 mm (1/4 in) and 4.8mm (3/16 in) included]Power 115 V ac (± 10 %), 55–65Hz, 1.5 A or 230 V ac (± 10%), 0.8 A, 45–55 Hz, 175 W94-234 V ac (± 10 %), 50/60Hz, 60 W;or 12 VDC Size (HxWxD)57 x 125 x 150 mm (2.25 x 4.9 x 6.1 in)99 x 140 x 175 mm (3.9 x 5.5x 6.9 in)Weight 1 kg (2 lb 3 oz)1.8 kg (4 lb)Computer InterfaceRS-232 interfaceData at 50 °C, 100 °C, 150Data at –10 °C, 0 °C, 25 °C,9100S Users Guide (Eng) (714.29 KB)9100S Users Guide Supplement (23.76 KB)9100S Users Guide (Ger) (891.75 KB)9100S Users Guide (Rus) (665.18 KB)9102S Users Guide (English) (758.49 KB)9102S Users Guide Supplement (35.15 KB)9102S Kalibriergerät Bedienerhandbuch (German) (752.33 KB) Industrial Temperature Calibrators Workload Matrix (96.74 KB)Power and utilities industry calibration solutions (5.03 MB)Soluciones de calibración de la industria de energía y servicios (Spanish) (6.52 MB)Решения в области калибровки приборов для измерения при производстве электроэнергии иэксплуатации инженерно-технических систем (6.98 MB)Soluções de calibração do setor de serviços públicos e energia (Portuguese) (6.97 MB)Kalibrierungslösungen für die Energie- und Versorgungsindustrie (German) (5.91 MB)Solutions d'étalonnage pour le secteur de la distribution d'énergie (French) (5.9 MB)Temperature Calibration Applications and Solutions (12.87 MB)Etalonnage de la température APPLICATIONS ET SOLUTIONS (9.22 MB)Calibración de temperatura Aplicaciones y soluciones (12.7 MB)Calibração de Temperatura Aplicações e soluções (12.52 MB)Temperaturkalibrierung Anwendungen und Lösungen (12.96 MB)Best Practices for Temperature Calibration (2.13 MB)Bewährte Methoden zur Temperaturkalibrierung (German) (1.81 MB)Meilleures pratiques pour la calibration de la température (French) (1.98 MB)Mejores prácticas para la calibración de la temperatura (Spanish) (1.98 MB)Improving loop calibration temperature accuracy (991.83 KB)Verbesserung der Temperaturgenauigkeit bei der Kalibrierung von Messketten (German) (793.62 KB)Selecting an Industrial Temperature Calibrator (1.6 MB)Auswahl eines Temperaturkalibrators für den Einsatz in der Industrie (German) (1.43 MB)Sélection d'un calibrateur de température industriel (French) (1.42 MB)Selección de un calibrador de temperatura industrial (Spanish) (1.42 MB)Выбор промышленного калибратора температуры (Russian) (1.43 MB)Why calibrate temperature devices? (977.05 KB)The Development of a High-Temperature PRT Calibration Process Based on Dry-Block Calibrators (60.55 KB)Industrial Temperature Calibration Selection Guide (1.83 MB)Industrielle Temperatur-Kalibrierung Produktübersicht (German) (3.49 MB)Guide de sélection d'étalonnage industriel (French) (3.99 MB)Gúia de selección de equipos para calibraciones industriales (Spanish) (3.45 MB)Guide alla selezione di strumenti per calibrazione industriale (Italian) (3.52 MB)Указатель приборов для промышленной калибровки (Russian) (3.59 MB)©1995-2018 Fluke Corporation3102-09100S-A-2569100S-B-2569100S-C-2569100S-D-256 9102S-2563102-0。
莫莎公司 OnCell G2111 G2151I 系列工业四频GSM GPRS模块产品简介说明书

OnCell G2111/G2151I SeriesIndustrial quad-band GSM/GPRS modemsFeatures and Benefits•Quad-band GSM/GPRS850/900/1800/1900MHz•DIN-rail mounting and wall mounting•2.5kV RMS isolation for1min.for all serial signals(G2151I only)•LED indicators for GSM/GPRS and data transmission status•Extended operating temperature from-25to70°C(G2111-T only)CertificationsIntroductionThe OnCell G2111/G2151I Series of industrial quad-band GSM/GPRS modems are designed to transmit data and short messages(SMS)over GSM/ GPRS mobile networks.The modems can be used to increase the efficiency of maintenance and communication,but do not require extensive training.In addition,the modems can be mounted on a DIN rail or wall.The OnCell G2111/G2151I Series modems accept a12to48VDC power input,making them suitable for use with a variety of field power sources.The serial ports feature15kV ESD line protection to protect the products from harmful electrical discharge,and separate RS-232and RS-422/485 interfaces are built into the OnCell G2151I,each with2.5kV RMS isolation protection for one minute.The two serial interfaces on the OnCell G2151I make it ideal for attaching all kinds of devices,such as stand-alone controllers,PC COM ports,and multi-dropped electric meters.In addition,the OnCell G2111-T has an extended operating temperature(-25to70°C)design that makes it suitable for heavy industrial use. SpecificationsCellular InterfaceCellular Standards GSM,GPRSBand Options Quad-band GSM/GPRS850MHz/900MHz/1800MHz/1900MHzGPRS Multi-Slot Class10GPRS Terminal Device Class Class BGPRS Coding Schemes CS1to CS4CSD Data Rates Up to14400bpsCellular Antenna Connectors1SMA femaleNo.of SIMs1SIM Control Voltage3VSerial InterfaceNo.of Ports1Serial Standards All models:RS-232(DB9female connector)OnCell G2151I:RS-232/422/485(5-pin terminal block connector)ESD Protection OnCell G2111:15kVIsolation OnCell G2151I:2kVData Bits8Stop Bits1Parity NoneFlow Control RTS/CTSBaudrate300bps to230.4kbpsSerial SignalsRS-232TxD,RxD,RTS,CTS,DTR,DSR,DCD,RI,GNDRS-422Tx+,Tx-,Rx+,Rx-,GNDRS-485-2w Data+,Data-,GNDRS-485-4w Tx+,Tx-,Rx+,Rx-,GNDPower ParametersInput Voltage12to48VDCPower Connector Terminal blockInput Current0.625A@12VDC,0.16A@48VDCPhysical CharacteristicsHousing ABS+PolycarbonateIP Rating IP30Dimensions27x123x79mm(1.06x4.84x3.11in)Weight155g(0.34lb)Environmental LimitsOperating Temperature OnCell G2111/G2151I:-20to55°C(-4to131°F)OnCell G2111I-T:-25to70°C(-22to158°F)Storage Temperature(package included)-40to75°C(-40to167°F)Ambient Relative Humidity5to95%(non-condensing)Standards and CertificationsSafety UL60950-1EMC EN55032/24EMI CISPR32,FCC Part15B Class AEMS IEC61000-4-2ESD:Contact:4kV;Air:8kVIEC61000-4-3RS:80MHz to1GHz:3V/mIEC61000-4-4EFT:Power:0.5kVIEC61000-4-5Surge:Power:1kVIEC61000-4-6CS:3VIEC61000-4-8PFMFRadio Frequency FCC Part22H,FCC Part24E,EN301489-1,EN301489-7,EN301511MTBFTime OnCell G2111:925,000hrsOnCell G2111-T:925,000hrsOnCell G2151I:864,000hrsStandards Telcordia SR332WarrantyWarranty Period5yearsDetails See /warrantyPackage ContentsDevice1x OnCell G2111/G2151I Series GSM/GPRS modem1Antenna1x GSM/GPRSAccessory1x terminal block for power jack connectorDocumentation1x quick installation guide1x warranty cardDimensionsOrdering InformationModel Name Cellular Standard Band Operating Temp.Serial Isolation Serial StandardsOnCell G2111GSM/GPRS 850/900/1800/1900MHz-20to55°C–RS-232OnCell G2111-T GSM/GPRS 850/900/1800/1900MHz-25to70°C–RS-232OnCell G2151I GSM/GPRS 850/900/1800/1900MHz-20to55°C✓RS-232/422/4851.An activated SIM card(not included)must be provided by a third party Cellular Service Provider.Accessories(sold separately)AntennasANT-CQB-AHSM-00-3m GSM/GPRS/EDGE,omni-directional magnetic base antenna,0dBi,3m cableANT-CQB-AHSM-03-3m GSM/GPRS/EDGE,omni-directional magnetic base antenna,3dBi,3m cableANT-CQB-AHSM-05-3m GSM/GPRS/EDGE,omni-directional magnetic base antenna,5dBi,3m cableANT-CQB-ASM-01GSM/GPRS/EDGE,omni-directional rubber duck antenna,1dBiANT-WCDMA-ANF-00GSM/GPRS/EDGE/UMTS/HSPA,omni-directional outdoor antenna,0dBiANT-WCDMA-ASM-1.5GSM/GPRS/EDGE/UMTS/HSPA,omni-directional rubber duck antenna,1.5dBiANT-WCDMA-AHSM-04-2.5m GSM/GPRS/EDGE/UMTS/HSPA,omni-directional magnetic base antenna,4dBiANT-LTE-ASM-02GPRS/EDGE/UMTS/HSPA/LTE,omni-directional rubber duck antenna,2dBiANT-LTE-ANF-04GSM/GPRS/EDGE/UMTS/HSPA/LTE,omni-directional outdoor antenna,4dBi,IP66AntennasANT-LTEUS-ASM-01GSM/GPRS/EDGE/UMTS/HSPA/LTE,omni-directional rubber duck antenna,1dBiWireless Antenna CableA-CRF-SMSF-R3-100Cellular magnetic-base SMA connector with1-meter RF cable©Moxa Inc.All rights reserved.Updated Nov12,2018.This document and any portion thereof may not be reproduced or used in any manner whatsoever without the express written permission of Moxa Inc.Product specifications subject to change without notice.Visit our website for the most up-to-date product information.。
AS9102Training培训资料
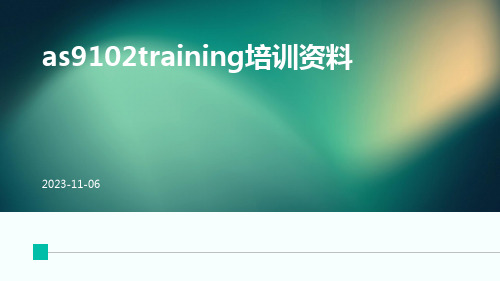
02
AS9102质量管理体系 的构建与实施
Chapter
质量管理体系的基本概念与原理
质量管理体系的定义
质量管理体系的原理
基于PDCA循环、过程方法、持续改进等质量管理 原则,构建一套完整、科学、有效的管理体系。
一个组织为了实现质量目标,建立和实施的 一系列相互关联、相互协调的质量管理活动 的总和。
AS9102的应用范围和实施意义
01
AS9102适用于汽车电子控制单 元的软件开发和维护过程,包 括燃油喷射控制、点火控制、 刹车控制等系统。
02
该标准的实施有助于提高汽车 电子控制单元的可靠性、安全 性和有效性,降低汽车故障率 ,提高汽车性能和安全性。
03
同时,实施AS9102标准还有助 于提高汽车制造商的研发效率 和质量,降低开发成本和风险 。
03
AS9102质量管理体系 的审核与认证
Chapter
审核的概念和基本原理
审核的概念
审核是对某个组织或个人的管理体系、过程或产品进行客观、独立和系统的检查,以确定其是否符合相关标准 或准则的要求。
审核的基本原理
审核的基本原理包括公正性、客观性和系统性。公正性指的是审核必须由有资格的第三方进行,以确保审核的 公正性和独立性;客观性是指审核员必须以事实为依据,不偏不倚地进行审核,不受任何干扰;系统性是指审 核员必须按照规定的程序和步骤进行审核,确保审核的全面性和有效性。
AS9102标准简介
Chapter
AS9102的背景和目的
AS9102是由美国汽车工程师学会(SAE)发布的一款面向汽车电子控制单元( ECU)的软件开发和维护的标准化指导文件。
该标准旨在规定一套统一的软件开发和维护过程,以确保汽车电子控制单元的安 全性、可靠性和有效性。
SPS-9102G中文资料

Optoway SPS-9102G**********************************************************************************************************************************************************************************************************************************************************************************************************************************************OPTOWAY TECHNOLOGY INC. No .38, Kuang Fu S. Road, Hu Kou, Hsin Chu Industrial Park, Hsin Chu, Taiwan 303Tel: 886-3-5979798 Fax: 886-3-5979737E-mail: sales@ http: // 12/1/2005 V2.01SPS-9102G / SPS-9102AG (RoHS Compliant)3.3V / 1310 nm / 2.5 Gbps SFP LC SINGLE-MODE TRANSCEIVER**********************************************************************************************************************************************************************FEATURESl Hot-Pluggable SFP Footprint LC Optical Transceiver l Small Form-Factor Pluggable (SFP) MSA compatible l Compliant with Intra-Office SONET OC-48 SR / SDH STM-16 (I-16)l Compliant with Fibre Channel 1x/2x SM-LC-L FC-PI l Compliant with IEEE 802.3z 1000BASE-LX l AC/AC Coupling according to MSA l Single +3.3 V Power Supply l RoHS Compliantl -10 to 85o C Operation: SPS-9102G l -40 to 85o C Operation: SPS-9102AGl Class 1 Laser International Safety Standard IEC-60825 CompliantAPPLICATIONSl ATM Switches and Routersl SONET / SDH Switch Infrastructure l XDSL Applications l Metro Edge SwitchingDESCRIPTIONThe SPS-9102G series single mode transceivers is small form factor pluggable module for bi-directional serial optical data communications such as SONET OC-48 / SDH STM-16 (I-16), Gigabit Ethernet 1000BASE-LX and Fibre Channel 1x/2x SM-LC-L FC-PI. It is with the SFP 20-pin connector to allow hot plug capability. This module is designed for single mode fiber and operates at a nominal wavelength of 1310 nm. The transmitter section uses a multiple quantum well laser and is a class 1 laser compliant according to International Safety Standard IEC-60825. The receiver section uses an integrated InGaAs detector preamplifier (IDP) mounted in an optical header and a limiting post-amplifier IC.LASER SAFETYThis single mode transceiver is a Class 1 laser product. It complies with IEC-60825 and FDA 21 CFR 1040.10 and 1040.11. The transceiver must be operated within the specified temperature and voltage limits. The optical ports of the module shall be terminated with an optical connector or with a dust plug.ORDER INFORMATIONP/No.Bit Rate (Gb/s) SONET /SDH Distance (km) Wavelength (nm) Package Temp. (oC) TX Power (dBm) RX Sens. (dBm) RoHSCompliant SPS-9102G 2.488 SR/I-16 2 1310 LC SFP -10 to 85 -3 to -9.5 -18 Yes SPS-9102AG2.488SR/I-162 1310 LC SFP -40 to 85 -3 to -9.5 -18 YesAbsolute Maximum RatingsParameterSymbol Min Max Units NotesStorage TemperatureTstg -40 85 o COperating Case Temperature Topr -10 -40 85 85 o C SPS-9102G SPS-9102AGPower Supply VoltageVcc-0.53.6VRecommended Operating ConditionsParameterSymbol Min Typ Max Units / NotesPower Supply VoltageVcc 3.1 3.3 3.5 V Operating Case Temperature Topr -10 -40 85 85 oC / SPS-9102G oC / SPS-9102AGPower Supply Current I CC (TX+RX)200 300 mA Data Rate62224882670Mb/s / 11. OC-48, Gigabit Ethernet and 1x/2x Fibre Channel compliant.Transmitter Specifications (-10o C < Topr < 85o C, 3.1V < Vcc < 3.5V)Parameter Symbol Min Typ Max Units NotesOpticalOptical Transmit Power Po -9.5 --- -3 dBm 1Output Center Wavelength λ1270 1310 1350 nmOutput Spectrum Width ∆λ--- --- 3 nm RMS (σ)Extinction Ratio E R8.2 --- --- dBOutput Eye Compliant with Telecordia GR-253-GORE and ITU-T Recommendation G.957Optical Rise Time t r150 ps 20 % to 80% Values Optical Fall Time t f150 ps 20 % to 80% Values Relative Intensity Noise RIN -120 dB/HzElectricalData Input Current – Low I IL-350 µAData Input Current – High I IH350 µADifferential Input Voltage V IH - V IL0.5 2.4 V Peak-to-PeakTX Disable Input Voltage – Low T DIS, L0 0.5 V 2TX Disable Input Voltage – High T DIS, H 2.0 Vcc V 2TX Disable Assert Time T ASSERT10 µsTX Disable Deassert Time T DEASSERT 1 msTX Fault Output Voltage -- Low T FaultL0 0.5 V 3TX Fault Output Voltage -- High T FaultH 2.0 Vcc+0.3 V 31. Output power is power coupled into a 9/125 µm single mode fiber.2. There is an internal 4.7K to 10K ohm pull-up resistor to VccTX.3. Open collector compatible,4.7K to 10K ohm pull-up to Vcc (Host Supply Voltage).Receiver Specifications(-10o C < Topr < 85o C, 3.1V < Vcc < 3.5V)Parameter Symbol Min Typ Max Units NotesOpticalSensitivity Sens -18 dBm 4,5 Maximum Input Power Pin -3 dBm 4,5Signal Detect -- Asserted Pa --- -18 dBm Transition: low to high Signal Detect -- Deasserted Pd -30 --- --- dBm Transition: high to low Signal detect -- Hysteresis 1.0 --- dBWavelength of Operation 1100 --- 1600 nmElectricalDifferential Output Voltage V OH– V OL0.6 2.0 VOutput LOS Voltage -- Low V OL0 0.5 V 6Output LOS Voltage -- High V OH 2.0 Vcc+0.3 V 64. Measured at 223-1 PRBS at BER 1E-10 @ 1300 nm.5. Measured at 27-1 PRBS at BER 1E-12 @ 1300 nm for 2.125 Gb/s, 1.25Gb/s, and 1.063 Gb/s.6. Open collector compatible, 4.7K to 10K ohm pull-up to Vcc (Host Supply Voltage).*********************************************************************************************************************************************************************** OPTOWAY TECHNOLOGY INC. No.38, Kuang Fu S. Road, Hu Kou, Hsin Chu Industrial Park, Hsin Chu, Taiwan 303Tel: 886-3-5979798 Fax: 886-3-5979737***********************************************************************************************************************************************************************OPTOWAY TECHNOLOGY INC. No .38, Kuang Fu S. Road, Hu Kou, Hsin Chu Industrial Park, Hsin Chu, Taiwan 303Tel: 886-3-5979798 Fax: 886-3-5979737PINSignal NameDescriptionPINSignal Name Description1 TX GND Transmitter Ground11 RX GND Receiver Ground2 TX Fault Transmitter Fault Indication12 RX DATA OUT- Inverse Receiver Data Out 3 TX Disable Transmitter Disable (Module disables on high or open)13 RX DATA OUT+ Receiver Data Out 4 MOD-DFE2 Modulation Definition 2 – Two wires serial ID Interface14 RX GND Receiver Ground5 MOD-DEF1 Modulation Definition 1 – Two wires serial ID Interface15 Vcc RX Receiver Power – 3.3V ±5% 6 MOD-DEF0 Modulation Definition 0 – Ground in Module16 Vcc TX Transmitter Power – 3.3V ±5% 7 N/C Not Connected 17 TX GNDTransmitter Ground 8 LOS Loss of Signal 18 TX DATA IN+ Transmitter Data In9 RX GND Receiver Ground 19 TX DATA IN- Inverse Transmitter Data In 10RX GNDReceiver Ground20TX GNDTransmitter GroundModule DefinitionModule DefinitionMOD-DEF2 PIN 4 MOD-DEF1 PIN 5 MOD-DEF0 PIN 6 Interpretation by Host 4SDASCLLV-TTL LowSerial module definitionprotocolModule Definition 4 specifies a serial definition protocol. For this definition, upon power up, MOD-DEF(1:2) appear as no connector (NC) and MOD-DEF(0) is TTL LOW. When the host system detects this condition, it activates the serial protocol. The protocol uses the 2-wire serial CMOS E 2PROM protocol of the ATMEL AT24C01A/02/04 family of components.*********************************************************************************************************************************************************************** OPTOWAY TECHNOLOGY INC. No.38, Kuang Fu S. Road, Hu Kou, Hsin Chu Industrial Park, Hsin Chu, Taiwan 303Tel: 886-3-5979798 Fax: 886-3-5979737。
SIWAREX WP231工程说明书

Automated Precision WeighingSIWAREX WP231E n g i n e e r i n g N o t ePBK9/PFK9-APW Weigh Platformswith SIWAREX WP2312E n g i n e e r i n g N o t eInhaltsverzeichnis1.1 Field of application ....................................................................................... 32.1 Connecting to Siwarex WP231 ...................................................................... 4 2.2 Configuring Siwarex WP231 ......................................................................... 5 2.3Configuring PBK9/PFK9 Weigh Platform ......................................................... 5 2.3.1 Connecting the weighing sensor to a PC ................................................................... 5 2.3.2 RS422/485 interface .............................................................................................. 5 2.3.3 Weight output ........................................................................................................ 6 2.3.4 User mode ............................................................................................................ 6 2.4 Weight transmission with Siwatool ................................................................. 6 4.1 Other Applicable Documents .......................................................................... 8 4.2 Figures . (8)1Introduction1.1Field of applicationPBK9/PFK9-APW weigh platforms from METTLER TOLEDO (hereafter referred to as “weighing sen-sors”)were developed especially for operation in automated plants. The weighing sensors profides an optionfor direct connection to the SIWAREX WP231 weighing system by Siemens (hereafter referred to as "Si-warex"). This document describes the steps for commissioning and optimizing this kind of connection.Figure 1: Connection to Siwarex via RS48534E n g i n e e r i n g N o t e2 CommissioningThis chapter summarizes, in form of a list, the steps required for commissioning PBK9/PFK9-APW weigh platforms at Siwarex.2.1 Connecting to Siwarex WP231The following diagram shows the connection of the PBK9/PFK9-APW weigh platforms to Siwarex WP231.Figure 2: Connection diagrammAssignment of the connections at SIWAREX WP231for the connection with PBK9/PFK9-APW weigh plat-form:2.2Configuring Siwarex WP231The following sections describe the steps required to configure the Siwarex when using Siwatool PCSoftware. Service mode must be activated before the records can be sent from Siwatool to the Siwarex:service commands-> Service Mode ON. When the service mode is activated, the corresponding icon(open-end wrench on red background) appears in the status bar.For SIWAREX WP231 as of firmware V3.0.4, parameters in the data record 3 and 13 must be adjustedas follows:DR3:Weight unit: grLoading cell type: Digital load cell Mettler Toledo PBKMaximum weight: capacity of the weighing sensor (unit: gr)Calibration weight 0: 0Calibration weight 1: capacity of the weighing sensor (unit: gr)Calibration weight 2: 0Calibration digits 0 (measured): 0Calibration digits 1 (measured): (capacity of the weighing sensor (unit: gr)) / (resolution)e.g.: 1 kg / 0.1 g = 1000 gr / 0.1 gr = 10,000Calibration digits 2 (measured): 0DR13:RS485 Protocol: Mettler Toledo PBK/PFK9 (Code 4)RS485 Baudrate: 38400RS485 Parity: evenRS485 Data Bits: 7RS485 Stop Bits: 1Delay: 2000 ms2.3Configuring PBK9/PFK9 Weigh PlatformThe steps are described below to configure the weighing sensor such that it operates with Siwarex.2.3.1Connecting the weighing sensor to a PCThe RS232 interface of the weighing sensor should be connected to a PC (using APW-Link TM - Free Con-figuration Tool – /apw-link) via the SubD9 connector of the ConBlock. The interface pa-rameters are configured in factory settings as follows: 9,600 baud, 8 data bits, no parity and1 stop bit.These settings shall NOT be modified.2.3.2RS422/485 interfaceFor the weighing platform, following parameters need to be configured:Parameter Value DescriptionM103 1 2 Configure the communication interface of the weighing platform as "RS485mode (half-duplex)"COM 1 8 0 0 Configure the communication interface of the weighing platform as follows:▪38400 bits per second▪7 data bits / even parity / 1 stop bit▪No handshakeM68 0 Keep the parameters of the communication interface permanently stored,such that they are not reset to factory defaults after a power cycle56E n g i n e e r i n g N o t e2.3.3 Weight outputFor seamless communication with the Siwarex, the update rate must be configured as follows:Update rate (UPD): UPD 922.3.4 User modeThe weighing sensors are automatically set to zero at power on. This might be undesirable in certain applications, particularly for larger platforms when a weight value shall be recovered after power off. When selecting the mode described below, the weight values refer to a fix reference point (as per pro-duction setting) and the zeroing at start up is disabled.Start-up with fix reference point: M35 12.4 Weight transmission with SiwatoolAfter successfully configuring the Siwarex and the weighing sensor, Siwatool can be used to weigh forcontrol purposes.The "Start Send" command (code 905) is used to send the individual records to the Siwarex. To con-firm, a record with “Receive” can be read out from the Siwarex. The communication can be stopped with the "Stop Send" command (code 906).Below in the picture, you can see the overview of the SIWATOOL:Figure 3: Siwatool(1) Control elements for SIWATOOL and the for the operation of the weighing sensor (2) Parameter list of the SIWATOOL module (3) Offline values of the SIWATOOL module(4) Online values of the connected SIWAREX module3Supported METTLER TOLEDO ProductsFTAV9.5.2WMS/WMSPBK9-APW/PBK9PFK9-APW/PFK9SLF6/SLF67Mettler-Toledo GmbH IndustrialCH-8606 Nänikon, SwitzerlandSubject to technical changes© 03/2017 Mettler-Toledo GmbHPrinted in Switzerland EN181_160407 4 Appendix4.1 Other Applicable Documents[1] METTLER TOLEDO, Reference Manual, Standard Interface Command Set (11781363G)[2] METTLER TOLEDO, Installation Manual PBK9 bench scales (30233012A)[3] METTLER TOLEDO, Installation Manual PFK9 floor scales (30233015A)[4]Siemens, Siwarex WP231, Device Manual, version 06/2014 (or later)4.2 FiguresFigure 1: Connection to Siwarex via RS485.................................. 3 Figure 2: Connection diagramm .................................................. 4 Figure 3: Siwatool (6)。
Transition Networks SISTG1040-2x2-LRT 产品说明书

SISTG1040-2x2-LRT Quick Start GuideIntroductionTransition Networks’ SISTG1040-242-LRT and SISTG1040--282-LRT are Industrial Unmanaged GbESwitches suitable for industrial Ethernet applications. See the SISTG1040-2x2-LRT Install Guide forimportant Cautions, Warnings, Features, Specifications, Front & Back Panel, LEDs, RESET button,Installation, Package Contents, and Troubleshooting, Warranty, Support & Compliance information.Unpack and Install1.Check package contents: verify that you have received the Switch, Quick Start Guide, Terminal Block, and Mountingkit. Two optional Power Supply models are available (sold separately).2.Unpack the contents in install location, and continue with Desktop, DIN Rail, or Wall mounting; see the Install Guide.3.Review the front panel description the Install Guide. Use the front panel grounding screw as required; see chapter 3of the Install Guide.4.Install SFP modules. Refer to the specific SFP manual for cautions and warnings. Note: The SFP ports should use ULListed Optional Transceiver product, Rated 3.3Vdc, Laser Class 1.5.Connect to Network / Devices: the switches provide eight or four 10M/100M/1G RJ45 ports. Use Cat 5e or betterunshielded twisted pair (UTP) cable terminated with an RJ-45 connector.6.Connect to 12-48V DC Power. Caution: Before applying power from an AC outlet, insert terminal connectors into theSISTG1040-2x2-LRT switch and verify all connections. Plugging in power connection after energizing power supply(s) may damage the switch. a) Connect the wires between the +P1 and –P1 terminals on the switch terminal block and the +V and -V terminals on the power supply. Optionally, connect the wires between the +P2 and –P2 terminals on the switch terminal block and the +V and -V terminals on the power supply if redundant power is to be used.b) Use a small Phillips screwdriver to tighten the wire-clamp screws. c) Connect the three wires (e.g., green, black,white) of the power cord to the Ground (), N, and L clamp connections respectively. Use a small Phillipsscrewdriver to tighten the wire-clamp screws. d) Connect the plug end of the power cord into a live AC outlet.e) Verify that the Power Supply front panel DC OK LED is lit. See the Install Guide for more details.7.Check the SYS LED. If it is lit, the power connection is correct. If not, see the Install Guide.LED Descriptions: three front panel LEDs allow switch status checking and monitoring:•Power LEDs indicate if the switch is powered up correctly.•System LED indicates if the system is ready.•Port Status LEDs indicates the current status of each port. Check these LEDs to understand the port status.RESET ButtonPress the RESET button to reboot the switch. The front panel LEDs flash and the switch is reset.Front PanelsSISTG1040-242-LRT SISTG1040-282-LRT LED SummaryLED Color FunctionSYS (System) Green On = the switch is ready. Of = the switch is not ready.P1 (Power 1) Green Input Power source 1 supplying power. P2 (Power 2) Green Input Power source 2 supplying power.Link/Act/Speed Green/AmberLight off: port disconnected or link failed.Green Light on: 1G Link Present, No Activity.Amber Light on: 100M/10M Link Present, No Activity.Green Blinking: 1G Activity. Port is sending or receiving data.Amber Blinking: 100M/10M Activity. Port is sending or receiving data.Link/Act/Speed Green/AmberLNK: Amber/Green (Two Color)Light off: port disconnected or link failedAmber Light on: link-up (100M)Green Light on: link-up (1G)Blinking: activity (receiving or transmitting data)Contact UsFor Transition Networks Drivers, Firmware, etc. go to the Product Support webpage (logon required).For Manuals, Application Notes, Brochures, Data Sheets, Specifications, etc. go to the Support Library (no logon required).Transition Networks | 10900 Red Circle Drive | Minnetonka, MN 55343, U.S.A.Technical Support: Technical support is available 24-hours a day. US and Canada: 1-800-260-1312;International: 00-1-952-941-7600. | tel: +1.952.941.7600 | toll free: 1.800.526.9267 | fax: 952.941.2322 ******************** | ************************** | ******************************。
9102操作说明

安規校正器9102使用手冊版本1.32007年3月料號 A11 000831法律事項聲明本使用手冊內容如有變更,恕不另行通知。
本公司並不對本使用手冊之適售性、適合作某種特殊用途之使用或其他任何事項作任何明示、暗示或其他形式之保證或擔保。
故本公司將不對手冊內容之錯誤,或因增減、展示或以其他方法使用本手冊所造成之直接、間接、突發性或繼續性之損害負任何責任。
致茂電子股份有限公司台灣省桃園縣龜山鄉華亞科技園區華亞一路66號版權聲明:著作人―致茂電子股份有限公司―西元2003-2007年,版權所有,翻印必究。
未經本公司同意或依著作權法之規定准許,不得重製、節錄或翻譯本使用手冊之任何內容。
ii保證書致茂電子股份有限公司秉持〝品質第一是責任,客戶滿意是榮譽〞之信念,對所製造及銷售之產品自交貨日起一年內,保證正常使用下產生故障或損壞,負責免費修復。
保證期間內,對於下列情形之一者,本公司不負免費修復責任,本公司於修復後依維修情況酌收費用:(1) 非本公司或本公司正式授權代理商直接銷售之產品。
(2) 因不可抗拒之災變,或可歸責於使用者未遵照操作手冊規定使用或使用人之過失,如操作不當或其他處置造成故障或損壞。
(3) 非經本公司同意,擅自拆卸修理或自行改裝或加裝附屬品,造成故障或損壞。
保證期間內,故障或損壞之維修品,使用者應負責運送到本公司或本公司指定之地點,其送達之費用由使用者負擔。
修復完畢後運交使用者(限臺灣地區)或其指定地點(限臺灣地區)之費用由本公司負擔。
運送期間之保險由使用者自行向保險公司投保。
致茂電子股份有限公司桃園縣333龜山鄉華亞科技園區華亞一路66號服務專線:(03)327-9999傳真電話:(03)327-2886網址:iii設備及材料污染控制聲明本產品之有毒有害物質或元素表:有毒有害物質或元素部件名稱鉛汞鎘六价鉻多溴聯苯多溴聯苯醚Pb Hg Cd Cr6+ PBB PBDE PCBA °○○○○○機殻°○○○○○標準配件°○○○○○包裝材料○○○○○○○:表示該有毒有害物質在該部件所有均質材料中的含量在SJ/T 11363-2006與EU 2005/618/EC規定的限量要求以下。
FOXBORO I A Series HARDWARE产品规格说明书

FOXBORO ®The FBM214 HART ® Communication Input Interface Module provides eight input channels, each accepting a 4 to 20mA analog signal or a digital HART signal superimposed on a 4 to 20 mA analog input signal.FEATURESKey features of the FBM214 module are:Eight analog input channels, each accepting oneof the following inputs:•Standard 4 to 20 mA analog sensor signal •Digital HART Frequency Shift Keying (FSK) signal superimposed on a 4 to 20 mA analog input signal.FSK modem dedicated to each input channel forbi-directional digital communications with a HART field deviceAnalog to digital conversion of each of the 4to20mA input signals from the HART devicesSupport for the HART universal commandsnecessary to interface the field device with the I/A Series ® system databaseGalvanic isolation of the group of 8 inputchannels from ground and module logicCompact, rugged design suitable for enclosure inClass G3 (harsh) environmentsHigh accuracy achieved by sigma-delta dataconversions for each channelTermination Assemblies (TAs) for locally orremotely connecting field wiring to the FBM214Termination Assemblies for per channel internallyand/or externally loop powered transmitters.PSS 21H-2Z14 B4 Page 2OVERVIEWThe FBM214 HART Communication Input Interface Module contains eight 4to20mA group isolated analog input channels. The FBM214 supports any mix of standard 4to20mA devices and HART devices.The FBM214 serves as a HART communications field device host, enabling the I/A Series system to request and receive two digital messages per second from the field device. The message pass-through capability can be used to support HART universal, common practice, and device-specific commands, but not the burst communication mode. These commands are implemented using the Intelligent Field Device Configurator (IFDC — refer toPSS 21S-8A3 B3 for details).The FBM214 provides a common isolated power supply to power all eight channels. Optionally, the channels can be powered by an external power supply. However, when a common external power supply is used with two or more channels, a Cable Balun module is required to prevent channel cross talk.COMPACT DESIGNThe FBM214 has a compact design, with a rugged extruded aluminum exterior for physical protection of the circuits. Enclosures specially designed for mounting the FBMs provide various levels of environmental protection, up to harsh environments per ISA Standard S71.04.HIGH ACCURACYFor high accuracy, the module incorporates a Sigma-Delta converter which can provide new analog input values for each channel every 100 milliseconds.VISUAL INDICATORSLight-emitting diodes (LEDs) incorporated into the front of the module provide visual indication of the module’s operational status, and communication activity on the channels.EASY REMOVAL/REPLACEMENTThe module can be removed/replaced without removing field device termination cabling, power, or communications cabling.FIELDBUS COMMUNICATIONA Fieldbus Communication Module or a Control Processor interfaces the redundant 2 Mbps module Fieldbus used by the FBMs. The FBM214 module accepts communication from either path (A or B) of the redundant 2 Mbps fieldbus – should one path fail or be switched at the system level, the module continues communication over the active path.The use of an external power supply common to two or more loops requires a Cable Balun Module to maintain communication signal line balance.MODULAR BASEPLATE MOUNTINGThe module mounts on a modular baseplate which accommodates up to four or eight FBMs. The modular baseplate is either DIN rail mounted or rack mounted, and includes signal connectors for redundant fieldbus, redundant independent dc power, and termination cables.TERMINATION ASSEMBLIESField input signals connect to the FBM subsystem via DIN rail mounted TAs. The TAs used with theFBM214 are described in “TERMINATION ASSEMBLIES AND CABLES” on page8.PSS 21H-2Z14 B4Page 3CABLE BALUN MODULEThe Cable Balun module is used to maintain digital communication line balance for HART Transmitter to FBM loops that are powered from a common external power supply. This powering effectively connects one line of each loop together. Without the Baluns, in each loop so powered, the common connection at the external power supply, would cause near end crosstalk at the system end of the loop wiring cable. Loops using FBM internal power source do not require Baluns.The Cable Balun module contains multiple Baluns. One Balun segment is interconnected in each loop powered from an external power supply per the diagram above. There is one Cable Balun module.Figure 1. Cable Balun Module Cable Balun ModuleModule Model ModulePart No.No. of Balunsin the ModuleCBM-4P0903SV4PSS 21H-2Z14 B4Page 4FUNCTIONAL SPECIFICATIONSField Device ChannelsVERSION SUPPORTEDHART Protocol v6INTERFACE8 group-isolated channelsCOMMUNICATION TO THE DEVICEPoint-to-point, master/slave, asynchronous, half-duplex, at 1200 baud.ERROR CHECKINGParity on each byte, and one CRC check byte.SPEED2 messages per secondFASTEST ALLOWED ECB BLOCK PERIOD500 msecMAXIMUM DISTANCE (FBM214 TO FIELDDEVICE)Meets HART FSK physical layer specificationHCF_SPEC-54, Revision 8.1 [up to 3030 m(10000ft)](1).COMPLIANCE VOLTAGE18 V dc minimum at 20.5 mACURRENT INPUTSSense Resistor61.9 Ω nominalTotal Input Resistance280 Ω minimumAccuracy (Includes Nonlinearity)±0.03% of full scaleTemperature Coefficient50 ppm/ºCResolution15 bitsUpdate Rate100 msIntegration Time500 msCommon Mode Rejection>100 db at 50 or 60 HzNormal Mode Rejection>35 db at 50 or 60 HzMAXIMUM LOOP RESISTANCE280 Ω (not including the field device)(2)LOOP POWER SUPPLY PROTECTIONEach channel is galvanically group isolated,current limited and voltage regulated. All inputsare limited by their design to less than 30 mA. Ifthe current limit circuit shorts out, the current islimited to about 85 mA.FBM INPUT IMPEDANCE280 Ω minimumFBM INTERNAL POWER FOR FIELD DEVICE24 V dc ±10% common power supply for allchannels. Loop load limited to one device perchannel.ISOLATIONThe channels are not galvanically isolated fromeach other, but are galvanically isolated (bothoptical and transformer isolation) as a group from ground and module logic. Inputs use an internal FBM isolated power supply for field power. Themodule withstands, without damage, a potential of 600 V ac applied for one minute between the group-isolated channels and earth (ground).CAUTIONThis does not imply that these channels areintended for permanent connection tovoltages of these levels. Exceeding the limitsfor input voltages, as stated elsewhere in thisspecification, violates electrical safety codesand may expose users to electric shock. Fieldbus CommunicationCommunicates with its associated FCM or FCP via the redundant 2 Mbps module FieldbusHEAT DISSIPATION4 W (maximum)(1)The maximum allowable distance decreases when the loop is operated through an intrinsic safety barrier. The maximum distance ofthe field device from the FBM is a function of compliance voltage, wire gauge and voltage drop at the device.(2)In an intrinsic safety application, if a zener barrier is used between the FBM and the field device, the power supply must be set at24V dc +5%, -1%. There are no specific constraints with the use of galvanic barriers.PSS 21H-2Z14 B4Page 5 FUNCTIONAL SPECIFICATIONS (CONTINUED)Power RequirementsINPUT VOLTAGE RANGE (REDUNDANT)24V dc ±5%CONSUMPTION7 W (maximum)Regulatory ComplianceELECTROMAGNETIC COMPATIBILITY (EMC) European EMC Directive 89/336/EECMeets:EN 50081-2 Emission standardEN 50082-2 Immunity standardEN 61326 Annex A (Industrial Levels) CISPR 11, Industrial Scientific and Medical(ISM) Radio-frequency Equipment -Electromagnetic Disturbance Characteristics- Limits and Methods of MeasurementMeets Class A LimitsIEC 61000-4-2 ESD ImmunityContact 4 kV, air 8 kVIEC 61000-4-3 Radiated Field Immunity10 V/m at 80 to 1000 MHzIEC 61000-4-4 Electrical FastTransient/Burst Immunity2 kV on I/O, dc power and communicationlinesIEC 61000-4-5 Surge Immunity2kV on ac and dc power lines; 1kV on I/Oand communications linesIEC 61000-4-6 Immunity to ConductedDisturbances Induced by Radio frequencyFields10 V (rms) at 150 kHz to 80 MHz on I/O,dc power and communication linesIEC 61000-4-8 Power Frequency MagneticField Immunity30 A/m at 50 and 60 HzPRODUCT SAFETY (FBM AND CABLE BALUN) Underwriters Laboratories (UL) for U.S. andCanadaUL/UL-C listed as suitable for use inUL/UL-C listed Class I, Groups A-D;Division 2; temperature code T4 enclosurebased systems. These modules are also ULand UL-C listed as associated apparatus forsupplying non-incendive communicationcircuits for Class I, Groups A-D hazardouslocations when connected to specifiedI/A Series® processor modules as describedin the I/A Series DIN Rail MountedSubsystem User’s Guide (B0400FA). Wherepower is supplied by the FBM,communications circuits also meet therequirements for Class2 as defined inArticle725 of the National Electrical Code(NFPA No.70) and Section 16 of theCanadian Electrical Code (CSA C22.1).Conditions for use are as specified in theI/A Series DIN Rail Mounted SubsystemUser’s Guide (B0400FA).European Low Voltage Directive 73/23/EECand Explosive Atmospheres (ATEX) directive94/9/ECCENELEC (DEMKO) certified as EEx nA IICT4 for use in CENELEC certified Zone 2enclosure certified as associated apparatusfor supplying non-incendive field circuits forZone 2, Group IIC, potentially explosiveatmospheres when connected to specifiedI/A Series processor modules as describedin the I/A Series DIN Rail MountedSubsystem User’s Guide (B0400FA). Also,see Table1 on page9.Calibration RequirementsCalibration of the module or termination assembly is not required.PSS 21H-2Z14 B4Page 6ENVIRONMENTAL SPECIFICATIONS(3)OperatingTEMPERATUREModule-20 to +70°C (-4 to +158°F)Termination AssemblyPVC-20 to +50°C (-4 to +122°F)PA-20 to +70°C (-4 to +158°F) RELATIVE HUMIDITY5 to 95% (noncondensing)ALTITUDE-300 to +3,000m (-1,000 to +10,000ft)StorageTEMPERATURE-40 to +70°C (-40 to +158°F)RELATIVE HUMIDITY5 to 95% (noncondensing)ALTITUDE-300 to +12,000m (-1,000 to +40,000ft) ContaminationSuitable for use in Class G3 (Harsh) environments as defined in ISA Standard S71.04, based on exposure testing according to EIA Standard 364-65, Class III. Vibration7.5 m/S2 (0.75 g) from 5 to 500 Hz(3)The environmental limits of this module may be enhanced by the type of enclosure containing the module. Refer to the applicableProduct Specification Sheet (PSS) which describes the specific type of enclosure that is to be used.PSS 21H-2Z14 B4Page 7 PHYSICAL SPECIFICATIONSMountingMODULEFBM214 mounts on a modular baseplate. Thebaseplate can be mounted on a DIN rail(horizontally or vertically), or horizontally on a19-inch rack using a mounting kit. Refer toPSS21H-2W6B4 for details.TERMINATION ASSEMBLYThe TA mounts on a DIN rail and accommodates multiple DIN rail styles including 32mm (1.26in) and 35mm 1.38in).MassMODULE284 g (10 oz) approximateTERMINATION ASSEMBLYCompression181 g (0.40 lb) approximateRing Lug249 g (0.55 lb) approximateDimensions – ModuleHEIGHT102 mm (4 in)114 mm (4.5 in) including mounting lugsWIDTH45 mm (1.75 in)DEPTH104 mm (4.11 in)Dimensions – Termination AssemblySee page10.Part NumbersFBM214 MODULEP0922VTTERMINATION ASSEMBLIESSee “FUNCTIONAL SPECIFICATIONS –TERMINATION ASSEMBLIES” on page8. Termination CablesCABLE LENGTHSUp to 30 m (98 ft)CABLE MATERIALSPolyurethane or Hypalon®/XLPTERMINATION CABLE TYPEType 1 – See Table2 on page9.CABLE CONNECTION – TA25-pin male D-subminiatureConstruction – Termination AssemblyMATERIALPolyvinyl Chloride (PVC), compressionPolyamide (PA), compressionPVC, ring lugFAMILY GROUP COLORGreen – communicationTERMINAL BLOCKS3 tiers, 8 positionsField Termination ConnectionsCOMPRESSION-TYPE ACCEPTED WIRINGSIZESSolid/Stranded/AWG0.2 to 4 mm2/0.2 to 2.5 mm2/24 to 12 AWGStranded with Ferrules0.2 to 2.5 mm2 with or without plastic collarRING-LUG TYPE ACCEPTED WIRING SIZES#6 size connectors (0.375 in (9.5 mm))0.5 to 4 mm2/22 AWG to 12 AWGPSS 21H-2Z14 B4Page 8TERMINATION ASSEMBLIES AND CABLESField input signals connect to the FBM subsystem via DIN rail mounted Termination Assemblies, which are electrically passive.TAs for the FBM214 are available in the following forms: Compression screw type using Polyvinyl Chloride(PVC) materialCompression screw type using Polyamide (PA) material Ring lug type using PVC material.See the following “FUNCTIONAL SPECIFICATIONS –TERMINATION ASSEMBLIES” for a list of TAs used with the FBM214.The FBM214 provides sufficient loop resistance to allow use of the HART Hand-Held Terminal, or PC20 Intelligent Field Device Configurator (PSS 2A-1Z3 E).A removable termination cable connects the DIN railmounted TA to the FBM via a field connector on the baseplate in which the FBM is installed. Termination cables are available in the following materials: PolyurethaneHypalon XLP .Termination cables are available in a variety of lengths, up to 30 meters (98feet), allowing the Termination Assembly to be mounted in either theenclosure or in an adjacent enclosure. See Table 2 for a list of termination cables used with the TAs forthe FBM214.FUNCTIONAL SPECIFICATIONS – TERMINATION ASSEMBLIESFBM Type Input SignalTA Part NumberTermination TA Cable TACertification PVC (a)(a)PVC is polyvinyl chloride rated from -20 to +50°C (-4 to +122°F).PA is Polyamide rated from -20 to +70°C (-4 to +158°F).PA (a)Type (b)(b) C = TA with compression terminals; RL = TA with ring lug terminals.Type (c)(c)See Table 2 for cable part numbers and specifications.Type (d)(d)See Table 1 for Termination Assembly certification definitions.FBM2148 input channels, 4 to 20mA analog signal, alone or with HART signal superimposedP0916BX P0926EA P0926TD CRL11, 2PSS 21H-2Z14 B4Page 9Table 1. Certification for Termination AssembliesType Certification (a)(a)All TAs are UL/UL-C listed to comply with applicable ordinary location safety standards for fire and shock hazards. Hazardous locationtypes comply with ATEX directive for II 3 G use. They also comply with the requirements of the European Low Voltage Directive. All listings/certifications require installation and use within the constraints specified in DIN Rail Mounted Subsystem User’s Guide (B0400FA) and the conditions stated in UL and DEMKO reports.Type 1TAs are UL/UL-C listed as suitable for use in Class I; Groups A-D; Division 2 temperature code T4 hazardous locations. They are CENELEC (DEMKO) certified EEx nA IIC T4 for use in Zone 2 potentially explosive atmospheres.Type 2TAs are UL/UL-C listed as associated apparatus for supplying non-incendive field circuits Class I; Groups A-D; Division 2 hazardous locations when connected to specified DIN rail mounted FBMs and field circuits meeting entity parameter constraints specified in DIN Rail Mounted Subsystem User’s Guide (B0400FA). They are also CENELEC (DEMKO) certified as associated apparatus for supplying field circuits for Group IIC, Zone 2 potentially explosive atmospheres. Field circuits are also Class 2 limited energy (60 V dc, 30 V ac, 100 VA or less) if customer-supplied equipment meets Class 2 limits.Table 2. Cables Types and Part NumbersCable Lengthm (ft) Type 1P/PVC (a)Type 1H/XLPE (b)Cable Lengthm (ft) Type 1P/PVC (a)Type 1H/XLPE (b)0.5 (1.6)P0916DA P0916VA 10.0 (32.8) P0916DE P0916VE 1.0 (3.2) P0916DB P0916VB 15.0 (49.2) P0916DF P0916VF 2.0 (6.6)P0931RM P0931RR 20.0 (65.6) P0916DG P0916VG 3.0 (9.8) P0916DC P0916VC 25.0 (82.0) P0916DH P0916VH 5.0 (16.4)P0916DDP0916VD30.0 (98.4)P0916DJP0916VJ(a)P/PVC is polyurethane outer jacket and semi-rigid PVC primary conductor insulation.(b)H/XLPE is Hypalon outer jacket and XLPE (cross-linked polyethylene) primary conductor insulation.PSS 21H-2Z14 B4Page 10DIMENSIONS – NOMINALRELATED PRODUCT SPECIFICATION SHEETSCompression Termination AssemblyRing Lug Termination Assembly(a) Overall width – for determining DIN rail loading.(b) Height above DIN rail (add to DIN rail height for total).PSS NumberDescriptionPSS 21H-2W1 B3DIN Rail Mounted FBM Subsystem OverviewPSS 21H-2W2 B3DIN Rail Mounted FBM Equipment, Agency CertificationsPSS 21H-2Z14 B4Page 11PSS 21H-2Z14 B4 Page 12IPS Corporate Headquarters 5601 Granite Parkway Suite 1000 Plano, TX 75024United States of AmericaFoxboro Global Client Support Inside U.S.: 1-866-746-6477 Outside U.S.: 1-508-549-2424 or contact your local Foxboro representative.Facsimile: 1-508-549-4999Invensys, Foxboro, I/A Series and the IPS Logo are trademarks of Invensys plc, its subsidiaries, and affiliates. All other brand names may be trademarks of their respective owners.Copyright 2002-2010 Invensys Systems, Inc.All rights reservedMB 21A Printed in U.S.A. 0210。
AS9102

AEROSPACE STANDARDSAE Technical Standards Board Rules provide that: “This report is published by SAE to advance the state of technical and engineering sciences. The use of this report is entirely voluntary, and its applicability and suitability for any particular use, including any patent infringement arising therefrom, is the sole responsibility of the user.” SAE reviews each technical report at least every five years at which time it may be reaffirmed, revised, or cancelled. SAE invites your written comments and suggestions. Copyright © 2004 SAE InternationalAll rights reserved. No part of this publication may be reproduced, stored in a retrieval system or transmitted, in any form or by any means, electronic, mechanical, photocopying, recording, or otherwise, without the prior written permission of SAE.TO PLACE A DOCUMENT ORDER:Tel: 877-606-7323 (inside USA and Canada)Tel: 724-776-4970 (outside USA) Issued 2000-08 Revise d 2004-01 Supersedes AS90125.5 Documentation (7)5.5.1 Forms (7)Accountability (8)5.5.2 Characteristic5.5.3 Record of Results (8)5.6 Control of Records (8)6. NOTES (9)APPENDIX A FORMS AND GUIDELINES TO COMPLETE THE FORMS (10)1. INTRODUCTION:1.1 Scope:This SAE Aerospace Standard (AS) establishes requirements for performing anddocumenting the First Article Inspection (FAI).1.2 Purpose:The purpose of the First Article Inspection is to give objective evidence that allengineering, design and specification requirements are correctly understood, accounted for, verified, and recorded. The purpose of this standard is to provide a consistentdocumentation requirement for aerospace components FAI.1.3 Convention:The following convention is used in this Standard.• The words “shall” and “must” indicate mandatory requirements.• The word “should” indicates mandatory requirements with some flexibility allowed in compliance methodology. An Organization is permitted to show that its approachmeets the intent of the requirement and this standard.• Words “typical”, “example” or “e.g.” show suggestions given for guidance only.• “Notes” are used for additional clarification.2. REFERENCES:1. International Aerospace Standard 9100 “Quality Systems - Aerospace - Model forQuality Assurance in Design, Development, Production, Installation and Servicing”.2. International Aerospace Standard 9103 “Variation Management in Key Characteristics”.3. International Aerospace Standard 9131 “Quality Systems - NonconformanceDocumentation”.3. DEFINITIONS:ATTRIBUTE DATA: A result from a characteristic or property that is appraised only as to whether it does or does not conform to a given requirement (for example, go/no-go,accept/reject, pass/fail, etc.).DELIVERABLE SOFTWARE: Embedded or loadable airborne, space borne or ground support software components that are part of an aircraft Type Design, weapon system, missile or spacecraft.DESIGN CHARACTERISTICS: Those dimensional, visual, functional, mechanical, and material features or properties, which describe and constitute the design of the article as specified by Drawing Requirements. These characteristics can be measured, inspected, tested, or verified to determine conformance to the design requirements. Dimensionalfeatures include in-process locating features such as target-machined (or forged/cast)dimensions on forgings and castings, and, weld/braze joint preparation necessary foracceptance of finished joint. Material features or properties may include processingvariables and sequences, which are specified by the drawing (e.g., heat treat temperature, fluorescent penetrant class, ultrasonic scans, sequence of welding and heat treat). These provide assurance of intended characteristics that could not be otherwise defined.DRAWING REQUIREMENTS: Requirements of the drawing (including Parts Lists),specification, or purchasing document to which the article is to be made. These include any notes, specifications, and lower-level drawings invoked.FIRST ARTICLE INSPECTION (FAI): A complete, independent, and documented physical and functional inspection process to verify that prescribed production methods haveproduced an acceptable item as specified by engineering drawings, planning, purchase order, engineering specifications, and/or other applicable design documents.FIRST ARTICLE INSPECTION REPORT (FAIR): The forms and package of documentation for a part number or assembly, including FAI results, as per this Standard.FIRST PRODUCTION RUN PARTS: The first group of one or more parts that are the result of a planned process designed to be used for future production of these same parts.Prototype parts, or parts built using methods different from those intended for the normal production process, shall not be considered as part of the first production run.MULTIPLE CHARACTERISTICS: Identical characteristics that occur at more than one location (e.g., “4 Places”) but are established by a single set of drawing requirements (e.g., rivet hole size, dovetail slots, corner radii, chemical milling pocket thickness).PRODUCT: The result of a process, which in the context of this Standard includes finished detailed parts and assemblies. It also includes forgings and castings.3. (Continued):REFERENCE CHARACTERISTICS: The characteristics that are used for “information only”or to show relationship. These are dimensions without tolerances and refer to otherdimensions on the drawing.STANDARD CATALOG HARDWARE: A part or material that conforms to an established industry or national authority published specification, having all characteristics identified by text description, National/Military Standard Drawing, or catalog item.VARIABLES DATA: Quantitative measurements taken on a continuous scale. For example, the diameter of a cylinder or the gap between mating parts.4. APPLICABILITY:This Aerospace Standard applies to assemblies sub-assemblies, and detail parts including castings and forgings. This Standard applies to organizations that are responsible forproducing the design characteristics of the product. The Organization shall flow down the requirements of this Standard to Suppliers who produce Design Characteristics.This Standard does not apply to procured Standard Catalog Hardware or DeliverableSoftware.5. REQUIREMENTS:5.1 Part Requirements:The Organization shall perform FAI on new Product representative of the First Production Run.NOTE: For assemblies, the assembly level FAI shall be performed on thosecharacteristics specified on the assembly drawing.NOTE: The Organization shall not use prototype parts, or parts manufactured using methods different from those intended for the normal production process, for theFAI. This Standard may be used to verify conformance of a prototype part todesign requirements.5.2 Evaluation Activities:The Organization should conduct the following activities in support of FAI.1. Review documentation for the manufacturing process (e.g., routing sheets,manufacturing/quality plans, manufacturing work instructions, etc.) to make sure alloperations are complete as planned.2. Review referenced exhibits supporting the FAI (e.g., inspection data, test data,Acceptance Test Procedures, etc.) for completeness.3. Review nonconformance documentation (if any), for completeness.NOTE: International Aerospace Standard 9131 may be used as a guidance.4. Review material certifications for compliance, as applicable.5. Verify that approved Special Process sources are used (as applicable), and that themanufacturing planning/routing document calls out the correct specification.6. Verify that Key Characteristic requirements have been met, as applicable (seeInternational Aerospace Standard 9103 for guidance).7. Verify part specific gages and/or tooling are qualified and traceable, as applicable.8. Verify that every design characteristic requirement is accounted for, uniquely identifiedand has inspection results traceable to each unique identifier.5.3 Partial or Re-accomplishment of First Article Inspection:The FAI requirement, once invoked, shall continue to apply even after initial compliance.The FAI requirements may be satisfied by a partial FAI that addresses differencesbetween the current configuration and prior approved configurations. When a partial FAI is performed, the Organization shall complete only the affected fields in the FAI forms.FAI requirements may also be satisfied by previously approved FAI performed on identical characteristics of similar parts produced by identical means. When FAI requirements(partial or complete) are satisfied in this manner, identify the approved configuration in the index of part numbers on Form 1.5.3 (Continued):The Organization shall perform a full FAI, or a partial FAI for affected characteristics, when any of the following events occurs:1. A change in the design affecting fit, form or function of the part.2. A change in manufacturing source(s), process(es), inspection method(s), location ofmanufacture, tooling or materials, that can potentially affect fit, form or function.3. A change in numerical control program or translation to another media that canpotentially affect fit, form or function.4. A natural or man-made event, which may adversely affect the manufacturing process.5. A lapse in production for two years or as specified by the Customer.5.4 Nonconformance Handling:The FAI is not complete until the Organization closes all non-conformances affecting the part and implements corrective actions. The Organization shall re-do an FAI for thoseaffected characteristics and shall record the results.5.5 Documentation:5.5.1 Forms: The Appendix of this Standard contains forms that comply with thedocumentation requirements of this Standard. Each field in the forms is designated witha unique reference number. Each field is also identified as:• (R) Required: This is mandatory information.• (CR) Conditionally Required: This field must be completed when applicable (i.e., when there exists a Customer requirement, then this field must be filled in).• (O) Optional: This field is provided for convenience.Forms contained in the Appendix should be used to document the results of the FAI.NOTE: The fields in the forms are color-coded for convenience. Use of black-and-white forms is acceptable.Forms other than those contained in the Appendix may be used, however they mustcontain all “Required” and “Conditionally Required” information and have the same field reference numbers.5.5.1 (Continued):All forms shall be completed either electronically or in permanent ink.All forms shall be completed in English or in a language specified by the Customer.NOTE: Continuation sheets using the same form are acceptable or insert additional rows if completing electronically.5.5.2 Characteristic Accountability: The Organization shall verify every Design Characteristicduring FAI and record the results. Every Design Characteristic shall have its own unique characteristic number.NOTE: Reference characteristics may be omitted from the FAI.NOTE: Use more than one line if needed for any characteristic.NOTE: Characteristics not measurable in the final product shall be verified during the manufacturing process (as long as they are not affected by subsequentoperations) or by destructive means. Characteristics verified at the detail levelmay be referenced in the assembly-level FAIR.5.5.3 Record of Results: Results from inspection of design characteristics shall be expressedin quantitative terms (Variables Data) when a Design Characteristic is expressed bynumerical limits.The Organization shall record the results in the units specified on the drawing orspecification, unless otherwise approved by the Customer.Attribute Data (e.g., go/no-go) may be used if no inspection technique resulting inVariables Data is feasible. Attribute Data is permitted when the Design Characteristicdoes not specify numerical limits (e.g., break all sharp edges). It is also permitted where qualified tooling is consistently used as a check feature and a go/no-go feature has been established for the specific characteristic.5.6 Control of Records:All FAI documentation required by this Standard shall be considered as a quality record and the Organization shall retain it according to Customer or regulatory requirements.6. NOTES:6.1 The change bar ( l ) located in the left margin is for the convenience of the user in locatingareas where technical revisions, not editorial changes, have been made to the previous issue of this document. An (R) symbol to the left of the document title indicates acomplete revision of the document.PREPARED UNDER THE JURISDICTION OFSAE COMMITTEE G-14, AMERICAS AEROSPACE QUALITY GROUP (AAQG)APPENDIX AFORMS AND GUIDELINES TO COMPLETE THE FORMSThis Appendix provides the guidelines to complete the forms. Each input field is identified as:This is mandatory information.This field is shown in Bold font.• (R) Required:• (CR) Conditionally Required: This field must be completed when applicable. This field is shown in Bold Italic font.• (O) Optional: This field is provided for convenience. It is shown in Regular font.The fields are also color coded for visual convenience: (R) as yellow and (CR) as blue. Use of black-and-white forms is acceptable.Instructions to Complete Form 1: Part Number AccountabilityThis form is used to identify the part that is being first-article inspected (FAI part) and associated subassemblies or detail parts.NOTE: Fields 1-4 are repeated on all forms for convenience and traceability.1) (R) P art Number: Number of the part (FAI part).P art Name: Name of the part as shown on the drawing.2) (R)number:Serial number of the part.3) (CR) Serial4) (O) FAI Report Number: Reference number that identifies the FAI. This may be aninternal report number.5) (CR) Part Revision Level: Latest part revision that affects the part being first articleinspected. If there is no revision, indicate as such. Note: The latest drawingrevision (Field 7) does not always affect all parts contained on a drawing.6) (CR)Drawing Number: Drawing number associated with the FAI part.7) (CR) Drawing Revision Level:The revision level of the engineering drawing. If thereis no revision, indicate as such.8) (CR) Additional Changes: Provide reference number(s) of any changes that areincorporated in the product but not reflected in referenced drawing/part revisionlevel (e.g., change in design, engineering changes, manufacturing changes,deviation or exclusion from certain drawing requirement, etc.).9) (R) Manufacturing Process Reference: A reference number that providestraceability to the manufacturing record of the FAI part (e.g., router number,manufacturing plan number, etc.)10) (R) Organization Name: Name of the Organization performing this FAI.11) (O) Supplier Code: Supplier Code is a unique number given by Customer to theOrganization. It is sometimes referred to as Vendor Code, Vendor IdentificationNumber, Supplier Number, etc.12) (O) P.O. Number: Enter Customer Purchase Order number, if applicable or required.13) (R) D etail part or an Assembly FAI: Check as appropriate .14) (R) Full FAI or Partial FAI: Check as appropriate. For a partial FAI, provide thebaseline part number (including revision level) to which this partial FAI is performedand the reason for it. For example, changes in design, process, manufacturinglocation, etc.15, 16, 17 and 18: This section is required only if the part number in Field 1 is an assembly requiring lower level parts to be installed into the assembly.15) (CR) Part Number: Detail or next level sub-assembly part number to be included in theassembly.16) (CR) Part Name , as shown on the drawing.17) (CR) Part Serial Number of the part that is installed in the assembly, when applicable.18) (O) FAI Report Number for detail part.19) (R) Signature: Name and signature of the person who prepared FAI Form 1. Alsocheck appropriate box if this FAI is complete per 5.4.Note: The signature on this form certifies the following two things:1) that all characteristics are accounted for; meet drawing requirements or areproperly documented for disposition.2) if this FAI is complete per 5.4. Check as appropriate.20) (R) Date when this FAI Form 1 was prepared.21) (O) Name of the person from the Organization who approved FAI report22) (O) Date when the FAI report is approved.23) (O) Customer Approval. This field is used by Customer to record approval, if required.24) (O) Date Customer approved this FAI form.Instructions to Complete Form 2: Product Accountability – Raw Material, Specifications and Special process(s), Functional TestingThis form is used if any material, special processes or functional testing are defined as a Design Requirement.NOTE: Fields 1-4 are repeated on all forms for convenience and traceability.1) (R) P art Number: Number of the part (FAI part).2) (R) P art Name: Name of the part as shown on the drawing.3) (CR) Part serial number: Serial number of the part.4) (O) FAI Report Number: Reference number that identifies the FAI. This may be aninternal report number5) (CR) Material or Process:Enter the name of material or process.6) (CR) Specification:Enter material or process specifications number (include permittedalternates, if used), class, and material form (e.g., sheet, bar, etc.). Include all“Make From” materials that are incorporated into the FAI part. For raw materials,include all materials that are incorporated into the FAI part, (e.g., weld/braze fillermaterials, balls for ball brazing, etc.), and Standard Catalog hardware (e.g., AN,MS fasteners); but do not include processing materials such as acid etchants.7) (O) Code: Enter any required code from the Customer for material or process listing,when required.8) (CR) Special Process Supplier Code: Customer given Supplier code of theorganization performing special process(es) or supplying material, as applicable.Also add, Special process supplier name and address.9) (CR) Customer Approval Verification: Indicate if the special process or materialsource is approved by the Customer. Write NA if Customer approval is notrequired.10) (CR) Certificate of Conformance number: Number of the certificate (e.g., specialprocess completion certification, raw material test report number, Standard Cataloghardware compliance report number, traceability number).11) (CR) Functional Test Procedure Number: Functional Test Procedure called out asDesign Requirement.12) (CR) Acceptance Report Number: The functional test certification indicating that testrequirements have been met.13) (O) C omments: As applicable.14) (R) P repared By: Name of the person who prepared this form.15) (R) D ate: Date when this form was completed.Instructions to Complete Form 3: Characteristic Accountability, Verification and Compatibility EvaluationNOTE: Fields 1-4 are repeated on all forms for convenience and traceability.1) (R) P art Number: Number of the part (FAI part).2) (R) P art Name: Name of the part as shown on the drawing.3) (CR) Part serial number: Serial number of part.4) (O) FAI Report Number: Reference number that identifies the FAI. This may be aninternal report number.5) (R) Characteristic Number: Unique assigned number for each Design Characteristic.6) (CR) ReferenceLocation: Location of the Design Characteristic (e.g., drawing zone (page number and section), specification, etc.)7) (CR) Characteristic Designator: If applicable, record characteristic type (e.g., key,flight safety, critical, major, etc.).8) (R) Requirement: Specified requirement for the Design Characteristic (e.g., drawingdimensional characteristics with nominal and tolerances included, drawing notes,specification requirements, etc.).9) (R) Results: List measurement(s) obtained for the Design Characteristics.• For Multiple Characteristics list each characteristic as individual values or list once with the minimum and maximum of measured values attained. If acharacteristic is found to be non-conforming then that characteristic must belisted separately with the measured value noted.• If a Design Requirement requires verification testing, then the actual results will be recorded on the form. If a laboratory report or certificate of test is includedin the FAIR, then these results need not be written on the form, record thereference number in this field. The laboratory report or certificate of test mustshow specific values for requirements and actual results.• For metallurgical characteristics with visual verification requirement that are rated against standard photographs, list the photo number of the closestcomparison. A statement of conformance is acceptable (record the referencenumber in this field).• For processes that require verification per Design Characteristic, include statement of compliance (e.g., certification of compliance, verification indicatorsuch as “accept”, etc.).• For part marking, ensure that marking is legible, correct in content and size and properly located, per applicable specification.10) (CR) Designed Tooling: If a specially designed tooling (including NC programming) isused as a media of inspection, record the tool identification number.11) (CR) Non-Conformance Number: Record a non-conformance document referencenumber if the characteristic is found to be non-conforming.12) (R) P repared By: Name of the person who prepared this form.13) (R) D ate: Date when this form was completed.14) (O) This field area is reserved for optional fields. Add additional columns as requiredby the Organization or Customer.Reason for Partial FAI:。
奥斯汀休斯UM-PPS-01-Q212V9智能远程电源管理说明书

Intelligent Remote Power ManagementUser Manual PPS-01, IP dongle GUI softwareMTS switched PDUMT monitored PDUDesigned and manufactured by Austin HughesLegal InformationFirst English printing, October 2002Information in this document has been carefully checked for accuracy; however, no guarantee is given to the correctness of the contents. The information in this document is subject to change without notice. We are not liable for any injury or loss that results from the use of this equipment.Safety InstructionsPlease read all of these instructions carefully before you use the device. Save this manual for future reference.■ Unplug equipment before cleaning. Don’t use liquid or spray detergent; use a moist cloth.■ Keep equipment away from excessive humidity and heat. Preferably, keep it in an air-conditioned environment with temperatures not exceeding 40º Celsius (104º Fahrenheit).■ When installing, place the equipment on a sturdy, level surface to prevent it from accidentally falling and causing dam age to other equipment or injury to persons nearby.■ When the equipment is in an open position, do not cover, block or in any way obstruct the gap between it and thepower supply. Proper air convection is necessary to keep it from overheating.■ Arrange the equipment’s power cord in such a way that others won’t trip or fall over it.■ If you are using a power cord that didn’t ship with the equipment, ensure that it is rated for the voltage and current labeled on the equipment’s electrical ratings label. The voltage rating on the cord should be higher than the one listed on the equipment’s ratings label.■ Observe all precautions and warnings attached to the equipment.■ If you don’t intend on using the equipment for a long time, disconnect it from the power outlet to prevent being dam aged by transient over-voltage.■ Keep all liquids away from the equipment to minimize the risk of accidental spillage. Liquid spilled on to the power supply or on other hardware may cause damage, fi re or electrical shock.■ Only qualifi ed service personnel should open the chassis. Opening it yourself could damage the equipment and invali date its warranty.■ If any part of the equipment becomes damaged or stops functioning, have it checked by qualifi ed service personnel.What the warranty does not cover■ Any product, on which the serial number has been defaced, modifi ed or removed.■ Damage, deterioration or malfunction resulting from:□ Accident, misuse, neglect, fi re, water, lightning, or other acts of nature, unauthorized product modifi cation, orfailure to follow instructions supplied with the product.□ Repair or attempted repair by anyone not authorized by us.□ Any damage of the product due to shipment.□ Removal or installation of the product.□ Causes external to the product, such as electric power fl uctuation or failure.□ Use of supplies or parts not meeting our specifi cations.□ Normal wear and tear.□ Any other causes which does not relate to a product defect.■ Removal, installation, and set-up service charges.Regulatory Notices Federal Communications Commission (FCC)This equipment has been tested and found to comply with the limits for a Class B digital device, pursuant to Part 15 of the FCC rules. These limits are designed to provide reasonable protection against harmful interference in a residential instal-lation.Any changes or modifi cations made to this equipment may void the user’s authority to operate this equipment. This equipment generates, uses, and can radiate radio frequency energy and, if not installed and used in accordance with the instructions, may cause harmful interference to radio communications.However, there is no guarantee that interference will not occur in a particular installation. If this equipment does cause harmful interference to radio or television reception, which can be determined by turning the equipment off and on, the user is encouraged to try to correct the interference by one or more of the following measures:■ Re-position or relocate the receiving antenna.■ Increase the separation between the equipment and receiver.■ Connect the equipment into an outlet on a circuit different from that to which the receiver is connected.The company reserves the right to modify product specifi cations without prior notice and assumes no responsibility for any error which may appear in this publication.All brand names, logo and registered trademarks are properties of their respective owners.Copyright 2011 Austin Hughes Electronics Ltd. All rights reserved.The equipment comes with the standard parts shown on the package contents. Check and make sure they are included and in good condition. If anything is missing, or damage, contact the supplier immediately.UnpackingPackage contents( 1 ) Vertical MTS / MT PDU x 1- VMS mounting screw, set of 2 or 3 - VMB mounting bracket set2 -3 sets+M4M4 x 2M6 x 2M6 nut x 2 PEGM6 nutBracket x 2( 2 ) Rackmount MTS / MT PDU x 1ORPower ON■ Connect the PDU into an appropriately rated receptacle■ When the PDU is power on, the LED display will light up. That means all outlets are activated■ Keep the equipments in the power off position until it is plugged into the PDUDon’t exceed the outlet, branch or phase limitations< 1.1 > PDU meter setting & cascade< 1.2 > IP dongle installation & connection < 1.3 > IP dongle confi guration< 1.4 > PPS-01 IP dongle GUI Software P. 1 - 2 P. 3 - 4 P. 5 P. 6 - 7ContentUsing the dip switch no. 1, 2, 3, 4 & 8 to setup each PDU level as below :Cascaded PDUs Dip switch no.123481st PDUOn On On On Off 2nd PDU Off On On On Off 3rd PDU On Off On On Off 4th PDU Off Off On On Off 5th PDU On On Off On Off 6th PDU Off On Off On Off 7th PDU On Off Off On Off 8th PDU Off Off Off On Off 9th PDU On On On Off Off 10th PDU Off On On Off Off 11th PDU On Off On Off Off 12th PDU Off Off On Off Off 13th PDU On On Off Off Off 14th PDU Off On Off Off Off 15th PDU On Off Off Off Off 16th PDUOff Off Off OffOffCascaded PDUs setting< 1.1 > PDU meter setting & cascadePDU cascade portDIP Switch <ON>1Current display 2Dip switch3Reset button4■ For rackmount PDU, on the front panel left , on the rear panel2341DIP Switch <OFF>1st level PDU Dip switch setting Dip switch settingDip switch settingTo LINK port of next PDU ( Up to 16 levels )Meter display settingCurrent display Dip switch no.57Circuit A + Circuit B Off Off Circuit A only On Off Circuit B onlyOnOnCAT. 5 / 6cableCAT. 5 / 6cableIP dongle ( refer to P.3 - 9 )Dip switch 6Enable Off DisableOnAudio alarmUp to 20 metersUp to 20 meters■ The PDU can be cascaded up to 16 levels■ For IP PDU access simply connect 1 x IP dongle - IPD-01■ 1 x IP dongle allows access to 16 levelsUsing the dip switch no. 5 & 7 to setup each PDU meter display as below :Using the dip switch no. 6 to setup each PDU audio alarm as below :3rd level PDU2nd level PDU< 1.2 > IP dongle installation & connectionTo remote PDU over IP, users can order IP dongle :I PD-01 IP dongle for vertical PDUVertical IP dongle installation steps :- slide the IP dongle on the plate above the meter- plug the RJ-45 connector of IP dongle into the LINK port of the 1st level PDU meter - use the CAT. 5 / 6 cable to connect IP dongle to network deviceI PD-H01 IP dongle for rackmount PDUHorizontal IP dongle installation steps :- fi x the IP dongle on the rear side of rackmount PDU with 4 screws- plug the RJ-45 connector of IP dongle into the LINK port of the 1st level PDU meter - use the CAT. 5 / 6 cable to connect IP dongle to network deviceCustomer’s network device( router or hub )< 1.3 > IP dongle con fi gurationAfter the completion of IP dongle connection, please take the following steps to con figure the IP dongle :IP dongle on 1st level PDU4. Click Scan to search the connected IP dongles5. Enter the device name ( min. 4 char. / max. 16 char. ) in the device name fi eld. The default is Name.6. Enter the location in the location fi eld ( min. 4 char. / max. 16 char. ). The default is Rack_001.7. Enter the password for security in the password fi eld ( min. 8 char. / max. 16 char. ). The default is 00000000.8. Re-enter the new password in the Con fi rm new password fi eld.9. Change the desired IP address / Subnet mask / Gateway, then click Save to con fi rm the setting to IP dongle.10. The default IP address is as below: IP address : 192.168.0.1 Subnet mask : 255.255.255.0 Gateway :192.168.0.254Reconnect the IP dongle with the network device ( router or hub ), after fi nish IP dongle con fi guration.Ensure the PDU inpower ON status1. Prepare a notebook computer to download the IP setup utilities from the link : /support/utilities/infrapower/IPdongleSetup.msi2. Double click the IPDongleSetup.msi and follow the instruction to complete the installation.3. Go to each fi rst level PDU with the notebook computer & a piece of CAT. 5 / 6 cable to con fi gure the IP dongle by IP setup utilities as below. Please take the procedure for all IP dongles ONE BY ONE .< 1.4 > PPS-01 IP dongle GUI SoftwareEach IP dongle provides a built-in GUI software, PPS-01, which allows user, via an I.E. web browser, to see PDU’s data and remotely manage the PDU over a TCP/IP Ethernet network.Each I.E. supports ONLY one IP dongle. If the user installs more IP dongles, multi windows will be required.< Status >- Data refresh every 10 seconds - Disable Refresh during data inputStatus of all connected PDUs Aggregate current on each PDULatest loading on each circuit of PDU Alarm threshold setup: save the changes: quit without changesPPS-01 is a management software but with very limited features. The user can use advanced software, InfraPower Manager IPM-01.Step 1. Open Internet Explorer ( I.E. ), version 6.0 or above Step 2. Enter the con fi gured IP dongle address into the I.E. address bar ( Refer to set up IP utilities p.5 )Step 3. Enter password ( Refer to set up IP utilities P.5 )< Setup >IP dongle con fi guration settingPassword settingNetwork setting Hardware information provided: save the changes : restart the PDU meter ( outlets are still activated ): reload the PDU information < Details >- Data refresh every 10 seconds - Disable Refresh during data input On / Off status of each outletRemote on / off outlet ( MTS switched PDU only )Rename outlet device, PDU and location Aggregate current on the PDU : reload the IP dongle to factory default( Press Default > Apply ): restart the IP dongle: save the changesThe company reserves the right to modify product specifi cations without prior notice and assumes no responsibility for any error which may appear in this publication.All brand names, logo and registered trademarks are properties of their respective owners.Copyright 2012 Austin Hughes Electronics Ltd. All rights reserved.。
光照度芯片型号-概述说明以及解释

光照度芯片型号-概述说明以及解释1.引言1.1 概述概述部分的内容可以包括对光照度芯片型号的简要介绍以及其在实际应用中的重要性和作用。
在现代科技发展的背景下,光照度芯片型号成为了光电技术领域中一项重要的研究内容。
随着科技的不断进步,光照度芯片型号在各个领域都有着广泛的应用,包括照明、建筑、农业、医疗等等。
光照度芯片型号能够测量周围环境中的光照强度,并将其转化为电信号输出,具有灵敏度高、响应速度快、可靠性强等特点。
光照度芯片型号在照明领域中扮演着重要的角色。
通过精确测量室内或室外的光照强度,光照度芯片型号可以用于自动调光系统,实现节能和提高照明效果的目的。
在建筑领域中,光照度芯片型号可以用于监控室内光照情况,通过智能调光系统来提供更舒适和适宜的照明环境。
在农业领域中,光照度芯片型号可以测量光照强度以帮助决定种植的适宜时间和条件,提高农作物的产量和质量。
在医疗领域中,光照度芯片型号可以用于测量手术室、病房等环境中的光照强度,为患者提供更好的照明环境。
因此,光照度芯片型号的研究和应用是十分重要的。
它不仅在提供舒适的照明环境方面起到了关键作用,还在节能、提高生产效率、改善生活质量等方面发挥了积极的影响。
随着技术的不断进步和创新,相信光照度芯片型号在未来的发展前景将更加广阔。
本文将对光照度芯片型号的相关要点进行详细介绍和分析,并展望未来的发展趋势。
1.2 文章结构文章结构部分主要介绍了文章的具体组织和内容安排,以便读者对整个文章有一个清晰的了解。
在本文中,文章结构部分可以参考以下内容:文章结构:本文主要包括引言、正文和结论三个部分。
其中,引言部分提供了对整个文章的概述和目的的介绍;正文部分着重介绍了光照度芯片型号的相关要点;结论部分对正文提到的要点进行总结,并对未来进行展望。
引言(Introduction):引言部分旨在引导读者了解文章的背景和目的。
首先,我们将概述光照度芯片型号的重要性和应用领域。
其次,我们将介绍文章的结构和内容安排,以便读者更好地理解全文内容。
AS9102Training培训资料
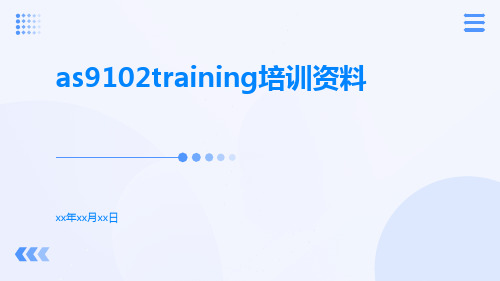
xx年xx月xx日
目录
• AS9102认证概述 • AS9102认证考试内容及考试方法 • AS9102认证培训课程内容和特点 • AS9102认证考试及培训前准备事项 • AS9102认证考试及培训后的跟进工作 • AS9102认证相关问题解答与常见问题处理方法
AS9102认证培训课程不仅介绍理论 知识,还结合实际案例进行讲解,帮 助企业更好地理解和应用AS9102标 准。
03
权威性
AS9102认证培训课程由权威机构进 行管理和认证,通过培训后可以获得 权威的证书,提升个人和企业的竞争 力。
04
AS9102认证考试及培训前准备事项
AS9102认证考试前准备事项
AS9102认证流程与操作规范
AS9102审核技巧与要点
AS9102认证培训课程内容详细介绍
AS9102标准的背景和意义
AS9102标准的框架和特点
AS9102标准的实施和审核要点
AS9102认证的申请流程和要求
AS9102认证培训课程的优势和特点
01
02
系统性
实用性
AS9102认证培训课程系统地介绍了 AS9102标准,帮助企业建立起完整 的质量管理体系,提高产品质量和可 靠性。
AS9102认证的重要性和影响
确保产品质量和安全性
AS9102认证为企业提供了一套完整的质量管理体系规范,可以确保企业在产品设计、制造、检验等环节达到高质量标准, 从而保证产品的安全性和可靠性。
提高企业信誉和品牌价值
获得AS9102认证可以证明企业在质量管理方面达到了国际标准,有助于提高企业的信誉和品牌价值,增加客户的信任度。
01
AS9102认证概述
AS9102Training培训资料

阐述AS9102标准中的质量管理原则,包括领导作用、全员工参与、过程方法等。
AS9102的组织架构和职责
介绍AS9102标准中对于组织架构和职责的具体要求和说明。
AS9102认证详细框架
要点一
AS9102的流程
要点二
AS9102的审核要点
详细介绍AS9102认证的流程,包括 认证申请、审核准备、审核实施、审 核结论、认证决定等环节。
认证范围
AS9102适用于整个航天工业, 包括卫星、火箭、导弹等领域。
认证内容
认证内容主要包括质量管理体系 的策划、实施、监控和改进等方 面。
AS9102认证经验教训
01
经验教训1
经验教训2
02
03
经验教训3
质量管理体系策划不够细致,导 致在实际工作中难以实施。
质量管理体系的监控不够严格, 导致一些问题无法及时发现和解 决。
AS9102认证基本概念
03
认证的机构和体系
AS9102认证基本框架
AS9102认证的框架结构 AS9102认证的流程和步骤 AS9102认证的监督和持续改进
03
AS9102认证详细内容
AS9102认证详细知识
AS9102标准背景与 发展
介绍AS9102标准的起源、发展历程 、主要内容以及适用范围。
航天制造与装配企业质量体系认 证
火箭、导弹、卫星等武器装备研 制企业质量体系认证
原材料采购与供应商质量体系认 证
AS9102认证应用方法
申请认证
审核准备
审核实施
审核判定
认证决定
向认证机构提交申请, 包括企业基本情况、质 量体系文件及申请认证 范围
白色贴片式发光二极管产品名称为1204-T1.0的产品承认书说明书

产品承认书产品名称:1204-T1.0白色贴片式发光二极管产品型号:XL-3210UWC客户名称:客户料号:承认日期:深圳市成兴光电子科技有限公司制定审核核准客户承认栏确认审核核准一、产品描述:●外观尺寸(L/W/H): 3.2x1.5x1.0mm●颜色:高亮度白色●胶体:黄色胶体●EIA规范标准包装●环保产品,符合ROHS要求●适用于自动贴片机●适用于红外线回流焊制程二、外形尺寸及建议焊盘尺寸:备注:1.2.单位公差:毫米(mm):如无特别标注则为±0.10mmA node建议焊盘尺寸C athode三、建议焊接温度曲线:有铅制程无铅制程四、最大绝对额定值(Ta=25℃):参数符号最大额定值单位消耗功率Pd80mW最大脉冲电流(1/10占空比,0.1ms脉宽)I FP100mA正向直流工作电流I F25mA 反向电压V R5V 工作环境温度Topr-30°C~+85°C存储环境温度Tstg-40°C~+90°C焊接条件Tsol 回流焊:260°C,10s 手动焊:300°C,3s五、光电参数(Ta=25℃):参数符号最小值代表值最大值单位测试条件光强IV 160---331mcd IF =5mA 半光强视角2θ1/2---120---deg IF =5mA 正向电压VF 2.6--- 3.0V IF =5mA 反向电流IR------1uAVR=5V亮度分档:代码最小值最大值单位测试条件Q1160192mcdIF=5mAQ2192230Q3230276Q4276331电压分档:代码最小值最大值单位测试条件F7 2.7 2.9VIF=5mAF8 2.9 3.1F93.13.3波长分档:代码最小值最大值单位测试条件2W389349901nmIF=5mA2W51028812152六、光电参数代表值特征曲线:注:如无另外注明,测试环境温度为25+3 Cφ6七、标签标识:CAT:光强(mcd)HUE:波长(nm)REF:电压(V)误差范围a.Luminous Intensity:±15%b.HUE:±0.003c.Forward Voltage:±0.1V八、包装载带与圆盘尺寸:φ13.0AA A-A剖面图U ser Feed D irection备注:1.尺寸单位为毫米(mm);2.尺寸公差如无标注,为±0.15mm;九、圆盘及载带卷出方向及空穴规格:尾端空壳载带的组合开始端空壳载带的组合盖带与空壳载带的组合十、内包装及外包装:内标签圆盘干燥剂防潮防静电袋5cartons/box外标签抽真空、热封10bags/carton 至少160mm盖带和装有零件部分至少160mm盖带和至少160mm独立盖带或十一、信赖性实验:测试项目测试条件测试次数参考标准失效判定标准失效LED 数量(PCS )防潮等级1.回流焊最高温度=260℃,10秒,2次回流焊;2.回流焊之前存储条件:30℃,相对湿度=70%,168H;-JEITAED-4701300.301﹟10/22焊接信赖性(无铅回流焊)回流焊最高温度=245±5℃,5秒(无铅回流焊)-JEITAED-4701303303A ﹟20/22冷热循环-40℃30分钟~25℃5分钟~100℃30分钟~25℃5分钟300个循环JESD22-A104﹟10/22冷热冲击-35℃15分钟转换时间3分钟85℃15分钟300个循环JESD22-A106﹟10/22高温存储Ta=100℃1000小时JESD22-A103﹟10/22低温存储Ta=-40℃1000小时JESD22-A119﹟10/22常温老化Ta=25℃IF=20mA1000小时JESD22-A108﹟10/22(2)失效标准★U.S.L :规格上限L.S.L :规格下限标准﹟项目测试条件失效标准﹟1正向电压(V F )I F =20mA >U.S.L*1.1光强(IV )I F =20mA <L.S.L*0.7反向电流(I R )V R =5V >U.S.L*2.0﹟2焊接可靠性/锡膏覆盖焊盘比例小于95%十二、使用注意事项:◆使用:1.过高的温度会影响LED的亮度以及其他性能,所以为使LED有较好的性能表现,应将LED远离热源。
AS9102
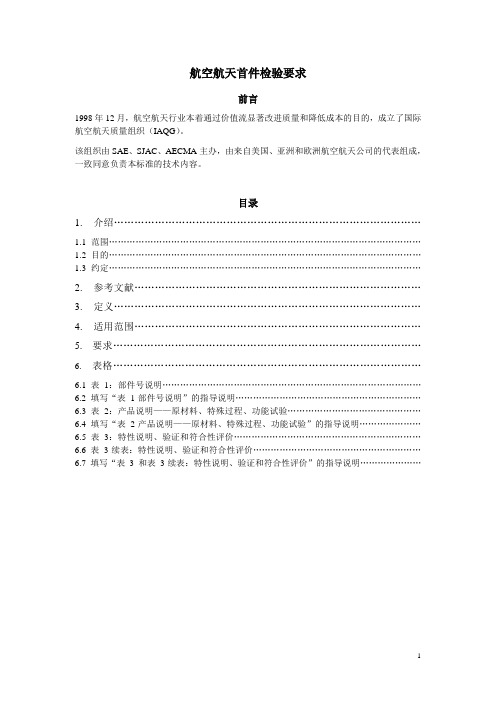
航空航天首件检验要求前言1998年12月,航空航天行业本着通过价值流显著改进质量和降低成本的目的,成立了国际航空航天质量组织(IAQG)。
该组织由SAE、SJAC、AECMA主办,由来自美国、亚洲和欧洲航空航天公司的代表组成,一致同意负责本标准的技术内容。
目录1. 介绍………………………………………………………………………………1.1 范围……………………………………………………………………………………………1.2 目的……………………………………………………………………………………………1.3 约定……………………………………………………………………………………………2. 参考文献…………………………………………………………………………3. 定义………………………………………………………………………………4. 适用范围…………………………………………………………………………5.要求………………………………………………………………………………6.表格………………………………………………………………………………6.1 表1:部件号说明……………………………………………………………………………6.2 填写“表1-部件号说明”的指导说明………………………………………………………6.3 表2:产品说明——原材料、特殊过程、功能试验………………………………………6.4 填写“表2-产品说明——原材料、特殊过程、功能试验”的指导说明…………………6.5 表3:特性说明、验证和符合性评价………………………………………………………6.6 表3-续表:特性说明、验证和符合性评价…………………………………………………6.7 填写“表3和表3-续表:特性说明、验证和符合性评价”的指导说明…………………1. 介绍:1.1 范围:本SAE航空航天标准(AS)规定了进行首件检验(FAI)的文件要求。
1.2 目的:首件检验的目的是为正确理解、说明、验证和文件化所有工程设计和规范的要求提供客观证据。
SA9102H资料

n
Adaptable to different types of current sensors Operates over a wide temperature range Precision voltage reference on-chip Two output signal formats available
FUNCTIONAL DESCRIPTION The SA9102F/SA9102H are CMOS mixed signal Analog/Digital integrated circuits, which perform bidirectional power/energy calculations across a power range of 1000:1, to an overall accurancy of better than Class 1. These integrated circuits includes all the required functions such as two oversampling A/D converters for the voltage and current sense inputs, power calculation and energy integration. Internal offsets are eliminated through the use of cancellation procedures. These devices generate pulses, the frequency of which is proportional to the power consumption. The pulse rate follows the instataneous power measured. Direction information is also provided.
三技术被动红外 微波防盗探测器安装手册说明书

DS825-CHI/DS825T-CHI/DS840-CHI/DS840T-CHI 安装手册 P/N :4998122944-01第1页DS825-CHI ,DS825T-CHI ,DS840-CHI ,DS840T-CHI三技术被动红外/微波防盗探测器1.0 概述DS825-CHI 和DS840-CHI 系列是以微波处理器为基础的三技术被动红外/微波防盗探测器。
它使用了先进的信号处理技术,提供了超高的探测和防误报性能,不会对一只重27公斤的狗或10猫,昆虫和飞鸟的活动而引起误报。
2.0 技术指标 • 输入电源:6—15伏直流,标准耗电电流为15毫安直流(在步测或故障状态下,耗电电流可至35毫安直流)。
• 待机电源:无内部待机电池。
与直流电源连接可提供待机电源。
每小时待机耗电为15毫安时。
在UL 认可的安装条件下,至少可待机4小时(60毫安时)。
• 报警继电器:静音操作常闭舌簧继电器。
直流抗阻负载时,接点间最大为28伏直流,3瓦特,125毫安。
并由继电器公共"C"脚上的4.7欧姆,0.5瓦特的电阻保护。
不可使用电容性或电感性负载。
• 工作温度: -40℃—+49℃。
UL 认可的安装条件下,工作温度为0℃—+49℃。
• 微波频率:DS825(T)-CHI/DS840(T)-CHI:10.525 Ghz (UL 认证) DS825TA-CHI/DS840A-CHI:10.687 Ghz DS825TB-CHI/DS840TB-CHI:9.9 Ghz • 探测范围:DS825-CHI 系列:8米×8米; DS840-CHI 系列:12米×12米 • 内部偏转:垂直+1°—8° • 可选防拆:DS825T-CHI ,DS825TA-CHI ,DS825TB-CHI ,DS840T-CHI ,DS840TA-CHI ,DS840TB-CHI 有一常闭防拆开关。
LR9102 LR9102A 友顺UTC 电子元器件芯片

BLOCK DIAGRAM
UNISONIC TECHNOLOGIES CO., LTD
3 of 5
QW-R502-923.R
LR9102/A
CMOS IC
ABSOLUTE MAXIMUM RATING
PARAMETER
SYMBOL
RATINGS
UNIT
Input Voltage
VIN
6
V
Input Voltage (CE Pin) Output Voltage
±50
70
MAX UNIT
×1.01 V
+20 mV
DFN2020-6
Copyright © 2022 Unisonic Technologies Co., Ltd
1 of 5
QW-R502-923.R
LR9102/A
ORDERING INFORMATION
Ordering Number
Lead Free
Halogen Free
LR9102L-xx-AE2-R
VCE VOUT
6
V
VIN+0.3
V
Output Current
IOUT SOT-23-3/SOT-23
400
mA
280
mW
Power Dissipation
SOT-23-5/SOT-25
SOT-353 DFN1616-6
PD
300
mW
850 (Note 2)
mW
DFN1820-6
1000 (Note 2)
* Ripple Rejection:
75dB (Typ.)
* Temperature-Drift Coefficient
- 1、下载文档前请自行甄别文档内容的完整性,平台不提供额外的编辑、内容补充、找答案等附加服务。
- 2、"仅部分预览"的文档,不可在线预览部分如存在完整性等问题,可反馈申请退款(可完整预览的文档不适用该条件!)。
- 3、如文档侵犯您的权益,请联系客服反馈,我们会尽快为您处理(人工客服工作时间:9:00-18:30)。
Optoway SPS-9102MWG**********************************************************************************************************************************************************************************************************************************************************************************************************************************************OPTOWAY TECHNOLOGY INC. No .38, Kuang Fu S. Road, Hu Kou, Hsin Chu Industrial Park, Hsin Chu, Taiwan 303Tel: 886-3-5979798 Fax: 886-3-597973712/1/2005 V2.0 1SPS-9102MWG / SPS-9102AMWG (RoHS Compliant)3.3V / 1310 nm / Multirate Digital Diagnostic SFP LC SINGLE-MODE TRANSCEIVER **********************************************************************************************************************************************************************FEATURESl Hot-Pluggable SFP Footprint LC Optical Transceiver l Small Form-Factor Pluggable (SFP) MSA compatible l Up to 2.67 Gb/s bi-directional data linksl Compliant with Intra-Office SONET OC-48 SR / SDH STM-16 (I-16)l Compliant with Fibre Channel 1X/2X SM-LC-L FC-PI l Compliant with IEEE 802.3z 1000BASE-LX l SFF-8472 Digital Diagnostic Function l AC/AC Coupling according to MSA l Single +3.3 V Power Supply l RoHS Compliantl -10 to 85o C Operation: SPS-9102MWG l -40 to 85o C Operation: SPS-9102AMWGl Class 1 Laser International Safety Standard IEC-60825 CompliantAPPLICATIONSl SONET OC-48 SR / SDH STM-16 I-16 l SONET OC-12 / SDH STM-4 l SONET OC-3 / SDH STM-1l Gigabit Ethernet / 1X/2X Fibre ChannelDESCRIPTIONThe SPS-9102MWG series single mode transceivers is small form factor pluggable module for bi-directional serial optical data communications such as SONET OC-48 / SDH STM-16 (I-16), Gigabit Ethernet 1000BASE-LX and Fibre Channel 1x/2x SM-LC-L FC-PI. It is with the SFP 20-pin connector to allow hot plug capability. Digital diagnostic functions are available via an I 2C. This module is designed for single mode fiber and operates at a nominal wavelength of 1310 nm. The transmitter section uses a multiple quantum well laser and is a class 1 laser compliant according to International Safety Standard IEC-60825. The receiver section uses an integrated InGaAs detector preamplifier (IDP) mounted in an optical header and a limiting post-amplifier IC.LASER SAFETYThis single mode transceiver is a Class 1 laser product. It complies with IEC-60825 and FDA 21 CFR 1040.10 and 1040.11. The transceiver must be operated within the specified temperature and voltage limits. The optical ports of the module shall be terminated with an optical connector or with a dust plug.ORDER INFORMATIONP/No.Bit Rate(Mb/s)SONET /SDHDistance (km) Wavelength (nm)PackageTemp. (o C) TX Power (dBm) RX Sens. (dBm) RoHS CompliantSPS-9102MWGMultirate*SR / I-16 2 1310 LC SFP with DMI -10 to 85 -3 to -9.5 -18 Yes SPS-9102AMWG Multirate*SR / I-1621310LC SFP with DMI -40 to 85-3 to -9.5-18YesMultirate*: 2.67 Gb/s / OC-48 / 2X FC / GbE / 1X FC / OC-12 / OC-3Absolute Maximum RatingsParameterSymbol Min Max Units NotesStorage TemperatureTstg -40 85 o COperating Case Temperature Topr -10 -40 85 85 o C SPS-9102MWG SPS-9102AMWG Power Supply VoltageVcc-0.53.6VRecommended Operating ConditionsParameterSymbol Min Typ Max Units / NotesPower Supply VoltageVcc 3.1 3.3 3.5 VOperating Case Temperature Topr -10 -40 85 85 oC / SPS-9102MWG oC / SPS-9102AMWGPower Supply Current I CC (TX+RX)200 300 mA Data Rate12524882670Mb/sTransmitter Specifications (-10o C < Topr < 85o C, 3.1V < Vcc < 3.5V)Parameter Symbol Min Typ Max Units NotesOpticalOptical Transmit Power Po -9.5 --- -3 dBm 1Output Center Wavelength λ1270 1310 1350 nmOutput Spectrum Width ∆λ--- --- 3 nm RMS (σ)Extinction Ratio E R8.2 --- --- dBOutput Eye Compliant with Telecordia GR-253-GORE and ITU-T Recommendation G.957Optical Rise Time t r150 ps 20 % to 80% Values Optical Fall Time t f150 ps 20 % to 80% Values Relative Intensity Noise RIN -120 dB/HzElectricalData Input Current – Low I IL-350 µAData Input Current – High I IH350 µADifferential Input Voltage V IH - V IL0.5 2.4 V Peak-to-PeakTX Disable Input Voltage – Low T DIS, L0 0.5 V 2TX Disable Input Voltage – High T DIS, H 2.0 Vcc V 2TX Disable Assert Time T_off10 µsTX Disable Negate Time T_on 1 msTX Fault Output Voltage -- Low T FaultL0 0.5 V 3TX Fault Output Voltage -- High T FaultH 2.0 Vcc+0.3 V 31. Output power is power coupled into a 9/125 µm single mode fiber.2. There is an internal 4.7K to 10K ohm pull-up resistor to VccTX.3. Open collector compatible,4.7K to 10K ohm pull-up to Vcc (Host Supply Voltage).Receiver Specifications(-10o C < Topr < 85o C, 3.1V < Vcc < 3.5V)Parameter Symbol Min Typ Max Units NotesOpticalSensitivity @ OC-48Sens1 -3 -18 dBm 4 Sensitivity @2X Fibre Channal Sens2 -3 -19 dBm 5 Sensitivity @Gigabit Ethernet Sens3 -3 -20 dBm 5 Sensitivity @OC-12 Sens4 -3 -22 dBm 4 Sensitivity @OC-3 Sens5 -10 -22 dBm 4Signal Detect -- Asserted Pa --- -18 dBm Transition: low to high Signal Detect -- Deasserted Pd -33 --- --- dBm Transition: high to low Signal detect -- Hysteresis 1.0 --- dBWavelength of Operation 1100 --- 1600 nmElectricalDifferential Output Voltage V OH– V OL0.6 2.0 VOutput LOS Voltage -- Low V OL0 0.5 V 6Output LOS Voltage -- High V OH 2.0 Vcc+0.3 V 6LOS Assert Time T_loss_on100 µsLOS Deassert Time T_loss_off100 µs4. Measured at 2-1 PRBS at BER 1E-10 @ 1300 nm.5. Measured at 27-1 PRBS at BER 1E-12 @1300nm.6. Open collector compatible, 4.7K to 10K ohm pull-up to Vcc (Host Supply Voltage).*********************************************************************************************************************************************************************** OPTOWAY TECHNOLOGY INC. No.38, Kuang Fu S. Road, Hu Kou, Hsin Chu Industrial Park, Hsin Chu, Taiwan 303***********************************************************************************************************************************************************************OPTOWAY TECHNOLOGY INC. No .38, Kuang Fu S. Road, Hu Kou, Hsin Chu Industrial Park, Hsin Chu, Taiwan 303PINSignal NameDescriptionPINSignal Name Description1 TX GND Transmitter Ground11 RX GND Receiver Ground2 TX Fault Transmitter Fault Indication12 RX DATA OUT- Inverse Receiver Data Out 3 TX Disable Transmitter Disable (Module disables on high or open)13 RX DATA OUT+ Receiver Data Out 4 MOD-DFE2 Modulation Definition 2 – Two wires serial ID Interface14 RX GND Receiver Ground5 MOD-DEF1 Modulation Definition 1 – Two wires serial ID Interface15 Vcc RX Receiver Power – 3.3V ±5% 6 MOD-DEF0 Modulation Definition 0 – Ground in Module16 Vcc TX Transmitter Power – 3.3V ±5% 7 N/C Not Connected 17 TX GNDTransmitter Ground 8 LOS Loss of Signal 18 TX DATA IN+ Transmitter Data In9 RX GND Receiver Ground 19 TX DATA IN- Inverse Transmitter Data In 10RX GNDReceiver Ground20TX GNDTransmitter GroundModule DefinitionModule DefinitionMOD-DEF2 PIN 4 MOD-DEF1 PIN 5 MOD-DEF0 PIN 6 Interpretation by Host 4SDASCLLV-TTL LowSerial module definitionprotocolModule Definition 4 specifies a serial definition protocol. For this definition, upon power up, MOD-DEF(1:2) appear as no connector (NC) and MOD-DEF(0) is TTL LOW. When the host system detects this condition, it activates the serial protocol. The protocol uses the 2-wire serial CMOS E 2PROM protocol of the ATMEL AT24C01A/02/04 family of components.*********************************************************************************************************************************************************************** OPTOWAY TECHNOLOGY INC. No.38, Kuang Fu S. Road, Hu Kou, Hsin Chu Industrial Park, Hsin Chu, Taiwan 303。