半成品质量检验标准
PCBA半成品检验规范

PCBA半成品检验规范一、引言PCBA(Printed Circuit Board Assembly)是指将电子元器件焊接在印制电路板(PCB)上形成电路连接的工艺过程。
在生产过程中,对PCBA半成品的质量进行检验是至关重要的,这有助于确保最终产品的性能和可靠性。
本文将介绍PCBA半成品检验的规范和要求。
二、外观检验1. PCB外观检验PCB的外观检验包括检查表面是否平整,焊盘是否存在破损或变形等。
同时也需要检查PCB上的丝印是否清晰可辨,是否有缺陷。
2. 焊接质量检验焊接质量对于PCBA的性能至关重要。
在检验焊接质量时,需要注意以下几个方面:- 焊接质量:检查焊盘是否焊接牢固,是否存在焊虚焊接或焊接不良的情况。
- 焊剂残留:使用显微镜检查焊盘上是否有残留的焊剂,焊剂残留可能导致短路或影响信号传输。
- 焊点距离:检查焊盘上的焊点与焊盘之间的距离,确保符合设计规范。
三、功能性检验1. 电气测试通过电气测试检验PCBA半成品在工作电压下的电气性能。
常用的电气测试方法有:- 电阻测试:检查电路中的电阻值是否符合设计要求,以排除开路或短路现象。
- 绝缘测试:检查电路板之间的绝缘情况,以确保不会发生漏电或电容等问题。
- 高压测试:在一定电压下检查电路是否能正常工作,以验证其耐压能力。
2. 功能性测试根据PCBA半成品的设计要求,在实际工作环境中进行功能性测试。
测试人员需要根据产品规格书和功能说明书,进行各项功能的验证和测试,确保PCBA半成品的性能符合要求。
四、可靠性检验1. 热老化测试通过将PCBA半成品在高温条件下运行一段时间,检验其在长时期高温环境下的可靠性。
通常使用恒温箱进行热老化测试,测试样品应该在规定的温度下运行一定时间,并观察其性能和工作情况。
2. 冷热冲击试验冷热冲击试验用于检验PCBA半成品在温度变化及温度冲击下的可靠性。
将PCBA半成品暴露在高温和低温环境中交替,观察其在温度变化时是否存在问题,如焊接断裂、组件脱落等。
半成品检验标准
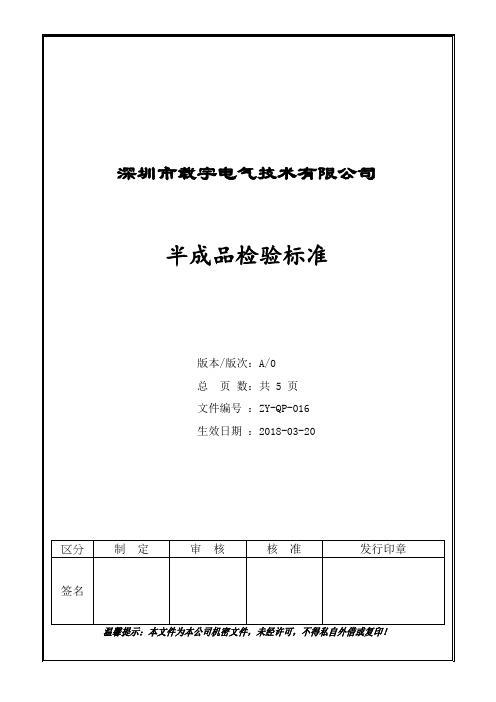
深圳市载宇电气技术有限公司半成品检验标准版本/版次:A/0总页数:共 5 页文件编号:ZY-QP-016生效日期:2018-03-20区分制定审核核准发行印章签名温馨提示:本文件为本公司机密文件,未经许可,不得私自外借或复印!流程性文件生效日期2018-03-20修订记录制定/修订日期修订内容摘要页次版本/版次总页数2018-03-20新制订-- A/0 5流程性文件生效日期2018-03-20 1.0目的对半成品产品制程进行有效的控制,使生产的产品品质符合规定的要求。
2.0适用的范围适用于本公司所有的产品的过程检验。
3.0权责:3.1质检部是本程序的归口管理部门,负责本程序的制定与保持工作;3.2质检部负责对首件进行确认,巡回检验的执行及制程异常的处理;3.3生产部负责自主检验及纠正、预防措施的制定及执行;4.0定义无5.0工作程序5.1检验依据◆客户订单的明示要求(产品的质量特性、外观及参数要求);◆产品图纸要求以及各类作业指导文件中规定的要求。
5.2检验前的准备工作◆生产部、质检部对生产技术文件进行确认,了解其产品特性及检测重点;◆质检部负责策划产品检测所需的测量设备以及正确的检测方法和判定标准。
外观检测:通过目视、手感及参照样板。
质量特性检测:通过利用相关的测量设备进行参数的测量,依据产品图纸及相关检测标准中规定的特性参数进行对比与判定;产品尺寸的检测:通过利用卡尺测量产品的脚排距和脚间距,与图纸进行对比符合图纸要求的为合格。
5.3首件检验的确认5.3.1对于每台机器正式生产前或机台维修、调校、更换易损件及停机4小时以上生产的产品,IPQC 需对生产部送检的首件产品进行检测确认,并将检验结果记录于《IPQC 巡查点检表》上,首件确认合格后方能生产。
5.3.2首件合格产品的样品需挂在相应的工位上,以便生产过程中检测时参照。
必要时IPQC留存样品以便备查。
5.4作业员自主检查5.4.1作业员每小时对所操作工位生产之产品进行自主检测,检测标准按作业指导性文件或首件进行检验,检测判定合格后才可流入下一道工序。
ISO22716半成品检验标准

出料前
200ml
卫生
指标
细菌菌落数,类大肠菌群,绿脓杆菌,金黄色葡萄球菌,按GB7918-87检验,本公司尚没有检测能力的项目,定期向有关部门送检.
灌装后成品
1~2支
六
花
露
水
/
收
缩
水
感观
指标
1、色泽:符合规定色泽。
出料前
一
洗
发
水
感观
指标
1、外观:无异物。
出料前
200ml
QB/T1974-2004
2、色泽:符合色泽。
出料前
200ml
3、香气:符合香型、无异味。
出料前
200ml
理化指标
1、PH值(25℃)5.5-7.0。
出料前
200ml
QB/T1974-2004
2、粘度(25℃)≥6000 mPa.s。
出料前
200ml
出料前
200ml
理化
指标
1、PH值:5.5-7.5。
出料前
200ml
QB/T1857-2013
2、粘度:(25℃)>30000mpa.s
出料前
200ml
3、耐热:45℃±1℃,24h恢复室温正常。
灌装后成品
200ml
4、耐寒:-5—15℃,24h恢复室温正常。
灌装后成品
200ml
卫生
指标
细菌总菌,粪大肠菌群,绿脓杆菌,金黄色葡萄菌,按BG7918-87检验。
出料前
200ml
理化
指标
1、PH值:5.5-7.5(果酸类产品除外)。
工程材料半成品质检制度

工程材料半成品质检制度1. 引言工程材料的质量直接影响到工程项目的安全和质量。
为了确保工程材料的质量符合相关标准和要求,制定一个有效的半成品质检制度是非常重要的。
本文将详细介绍工程材料半成品质检制度的建立和执行。
2. 半成品质检的目的半成品质检的目的是确保工程材料在生产过程中的质量符合相关标准和要求。
通过半成品质检,可以:•发现和排除生产过程中的缺陷和问题•提高工程材料的质量和产品的可靠性•检验供应商的产品质量,确保其符合合同要求3. 半成品质检的内容3.1 原材料检验对于工程材料的半成品制造过程,首先需要对原材料进行检验。
3.1.1 材料标识检查原材料标识是否清晰、准确,并与供应合同一致。
3.1.2 材料外观检查检查原材料的外观,包括表面平整度、颜色、变形等。
3.1.3 材料尺寸测量测量原材料的尺寸,确保其符合设计和制造要求。
3.2 半成品制造过程检验在半成品的制造过程中,需要进行以下检验步骤:3.2.1 工艺操作检查检查半成品制造过程中的工艺操作是否规范,包括原材料的加工、搅拌、喷涂等。
3.2.2 半成品外观检查检查半成品外观和表面处理质量,如焊缝、切割面、表面涂装等。
3.2.3 半成品尺寸测量测量半成品的尺寸,包括长度、宽度、厚度等,确保其符合设计和制造要求。
3.3 半成品功能性测试对于特定的工程材料半成品,需要进行功能性测试来确保其具备预期的性能。
3.3.1 功能性测试方法根据工程材料的特点和要求,选择合适的功能性测试方法,如拉力测试、抗压测试、耐磨测试等。
3.3.2 功能性测试结果评估根据功能性测试的结果,评估半成品是否符合相关标准和要求。
4. 半成品质检的执行流程为了确保半成品质检的规范性和有效性,制定了以下执行流程:4.1 质检计划制定制定质检计划,明确质检的对象、标准和方法。
4.2 质检样品采集按照质检计划,采集半成品的样品,确保样品具有代表性。
4.3 质检设备准备准备质检所需的设备和工具,包括测量仪器、试验设备等。
质量部半成品检验规范
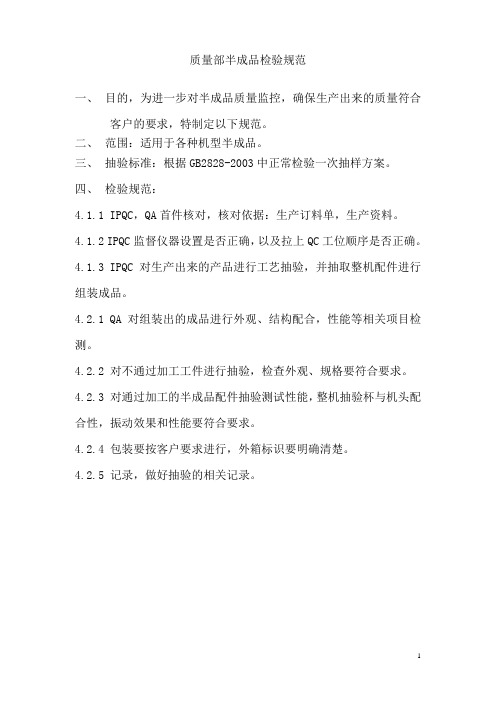
质量部半成品检验规范
一、目的,为进一步对半成品质量监控,确保生产出来的质量符合
客户的要求,特制定以下规范。
二、范围:适用于各种机型半成品。
三、抽验标准:根据GB2828-2003中正常检验一次抽样方案。
四、检验规范:
4.1.1 IPQC,QA首件核对,核对依据:生产订料单,生产资料。
4.1.2 IPQC监督仪器设置是否正确,以及拉上QC工位顺序是否正确。
4.1.3 IPQC对生产出来的产品进行工艺抽验,并抽取整机配件进行组装成品。
4.2.1 QA对组装出的成品进行外观、结构配合,性能等相关项目检测。
4.2.2 对不通过加工工件进行抽验,检查外观、规格要符合要求。
4.2.3 对通过加工的半成品配件抽验测试性能,整机抽验杯与机头配合性,振动效果和性能要符合要求。
4.2.4 包装要按客户要求进行,外箱标识要明确清楚。
4.2.5 记录,做好抽验的相关记录。
1。
半成品成品检验标准

半成品成品检验标准半成品、成品检验标准1.⽬的:对⼯⼚内部的在制品、制成品、成品进⾏检验,以保证符合使⽤及技术要求,防⽌⽣产过程中出现重⼤错误,同时起到及时纠正预防作⽤。
2.范围:⼯⼚内⽣产的所有半成品、制成品、成品等。
3.检验标准:(⼀)半成品部分(贴防⽕板前):3.1开料检验内容及质量标准:3.1.1对照开料申请单检验开料选材规格、型号,尺⼨是否正确,被开板料的切割⾯是否平直、光滑,且与板⾯成直⾓或特定⾓度,有⽆⿊边、崩边现象;不得有明显双重锯路和凹凸不平现象。
3.1.2开出板材净料1m以内时,误差≤2mm;1m以上时误差≤3mm,对⾓线误差≤1mm。
3.1.3防⽕板、有机板(保护膜不可撕掉)、三聚氰胺板、宝丽板表⾯不得划花、划伤。
3.2框架体验内容及质量标准:3.2.1对照设计原图检验框架的外形尺⼨是否正确,框架稳固结实,正放、侧放、或反放不会摇晃,材料的使⽤是否正确。
3.2.2框架板材内外表⾯⽆破损、⽆断裂、⽆堆胶、⽆露钉等现象。
3.3内部结构的检验内容及质量标准:3.3.1检验部件形状尺⼨、村质是否正确,部件与框架相连接板材边保持在同⼀平⾯上,允许误差±2mm。
3.3.2检验各部件的直⾓、圆⾓或斜⾓的接合处是否紧密、平整光滑,缝隙⼩于1mm。
3.3.3检验在制品在⽣产过程中使⽤的加固⽊、三⾓⽊等是否超出所在板材部件的范围。
3.3.4检验产品在各接合处(如是有胶接合)是否有溢胶,并检验各部分结合强度是否符合要求。
3.3.5检验板材是否枪钉、螺钉等⾦属材料裸露在表⾯(如不贴防⽕板可从宽处理),且板材⽆⼤的沟痕、损坏等缺陷。
3.3.6检验柜台对电器安装预留孔、预留位数量、位置的正确性和要操作性。
3.4柜台其余部分的检验内容及质量标准:3.4.1检验柜台主结构、玻璃、⾦属相互接触的部位的吻合性,要求接合缝隙≤1mm;检验接合处是否在同⼀平⾯上,允许误差±1mm;玻璃翘曲度≤5mm/1m,玻璃(⾦属)表⾯⽆划花、污点,且表⾯清洁⼲净。
西服半成品,成品检验标准

西服半成品,成品检验标准
西服半成品和成品的检验标准包括以下方面:
1. 尺码标准:西服尺码应符合国家或行业标准。
在制作过程中,需要对衣服的尺寸进行检查,确保其准确无误。
2. 型号规格:西服的型号和规格应符合设计要求。
制作完成后,需要进行型号规格的检查,确保每个衣服都符合要求。
3. 环保标准:西服所使用的面料、吸湿内衬、缝纫线等材料应符合国家或行业的环保标准。
制作完成后,需要对西服进行环保检查。
4. 工艺要求:西服应符合制作要求,包括剪裁、缝制、整烫等工艺环节的要求。
制作完成后,需要进行工艺质量检查。
5. 外观质量:西服外观应当整洁美观、无瑕疵,衣领、扣子、袋袋等结构部件位置要准确。
制作完成后,需要进行外观检查。
6. 功能性能:西服应能够满足使用者的要求和期望,如保暖、透气、防水、抗皱等。
制作完成后,需要对西服进行功能测试。
7. 品质持续性:西服制作后应保持品质持续性,这需要对制作过程进行质量控制,确保每件西服都符合相关标准。
以上是西服半成品和成品的一些检验标准,这些标准将确保西服的品质和可靠性,并让消费者购买更加满意。
原材料和半成品质量检验标准

原材料批次的标识: 在原材料的包装上标 明批次号、生产日期 等信息
原材料批次的存储: 根据原材料的种类、 规格、生产日期等信 息进行存储和摆放, 避免混淆和污染
原材料质量异常处理
原材料质量异常分 类:外观缺陷、尺 寸偏差、性能不合 格等
异常处理流程:确 认异常、分析原因、 制定解决方案、实 施整改、验证效果
检验文件培训: 定期对员工进行 检验文件培训, 提高检验质量和 效率
检验文件更改与修订
修订流程:提出申请、审核、 批准、实施
更改原因:生产工艺、设备、 原材料等发生变化
更改内容:检验标准、方法、 频率、记录等
培训与沟通:对相关人员进 行培训,确保理解并执行新
的检验文件
Part 06
质量检验不合格品处理
检验标准:根据国家和 行业标准制定,也可根 据企业实际情况制定
半成品流转检验
目的:确保半成品的质量符合标准 检验项目:外观、尺寸、性能等 检验方法:目测、测量、试验等 检验结果处理:合格品放行,不合格品返修或报废
半成品质量异常处理
异常情况识别:及时发现并识别半成品质量异常情况
异常原因分析:分析异常原因,找出问题根源
原材料和半成
品质量检验标
z
准
XXX,a click to unlimited possibilites
汇报人:XXX
目录
01 原 材 料 质 量 检 验 标 准 03 质 量 检 验 人 员 要 求 05 质 量 检 验 文 件 管 理
02 半 成 品 质 量 检 验 标 准 04 质 量 检 验 设 备 管 理 06 质 量 检 验 不 合 格 品 处 理
异常处理措施:根据异常原因采取相应的处理措施,如返工、报废等 异常记录与跟踪:记录异常情况及处理结果,并进行跟踪,确保问 题得到解决
化妆品半成品检验标准

化妆品半成品检验标准化妆品半成品是指还未成品化妆品的产品,通常是化妆品生产过程中的中间产品。
对于化妆品半成品的质量和安全性检验至关重要,只有通过严格的检验标准,才能确保最终成品化妆品的质量和安全性。
本文将就化妆品半成品的检验标准进行详细介绍。
一、外观检验。
1. 化妆品半成品的外观应该整洁、无异物、无明显色斑和气泡等缺陷。
2. 化妆品半成品的包装应该完好无损,标签清晰、无误,防伪标识鲜明。
二、pH值检验。
1. 化妆品半成品的pH值应符合国家标准,一般来说,不同类型的化妆品半成品对应的pH值范围是不同的。
2. pH值检验应使用专业的仪器,确保准确性。
三、微生物检验。
1. 化妆品半成品应进行细菌、霉菌、酵母菌等微生物检验,确保产品不受污染。
2. 检验标准应符合国家相关法规,确保产品的微生物指标符合安全要求。
四、活性成分含量检验。
1. 化妆品半成品中的活性成分含量应符合配方要求,确保产品的功效。
2. 活性成分含量检验应使用专业的仪器和方法,确保准确性和可靠性。
五、稳定性检验。
1. 化妆品半成品在不同温度、湿度条件下的稳定性应进行检验,确保产品在储存和使用过程中不会发生变质。
2. 稳定性检验应包括物理稳定性、化学稳定性等多个方面,确保产品的整体稳定性。
六、重金属和有害物质检验。
1. 化妆品半成品中的重金属和有害物质含量应符合国家标准,确保产品对用户的安全。
2. 检验应使用专业的仪器和方法,确保准确性和可靠性。
七、其他特殊检验。
1. 根据具体产品的特点,可能需要进行特殊的检验,如防腐剂、防晒剂、色素等成分的含量检验。
2. 特殊检验应根据产品的特点和要求进行,确保产品的质量和安全性。
综上所述,化妆品半成品的检验标准涉及外观、pH值、微生物、活性成分含量、稳定性、重金属和有害物质等多个方面,只有严格按照相关标准进行检验,才能确保最终成品化妆品的质量和安全性。
化妆品生产企业应严格执行相关标准,确保产品的质量和安全,为消费者提供放心、安全的产品。
食品半成品检验标准
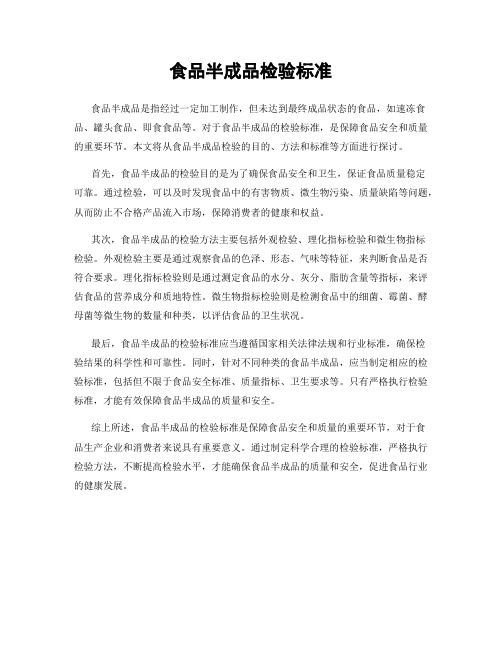
食品半成品检验标准
食品半成品是指经过一定加工制作,但未达到最终成品状态的食品,如速冻食品、罐头食品、即食食品等。
对于食品半成品的检验标准,是保障食品安全和质量的重要环节。
本文将从食品半成品检验的目的、方法和标准等方面进行探讨。
首先,食品半成品的检验目的是为了确保食品安全和卫生,保证食品质量稳定
可靠。
通过检验,可以及时发现食品中的有害物质、微生物污染、质量缺陷等问题,从而防止不合格产品流入市场,保障消费者的健康和权益。
其次,食品半成品的检验方法主要包括外观检验、理化指标检验和微生物指标
检验。
外观检验主要是通过观察食品的色泽、形态、气味等特征,来判断食品是否符合要求。
理化指标检验则是通过测定食品的水分、灰分、脂肪含量等指标,来评估食品的营养成分和质地特性。
微生物指标检验则是检测食品中的细菌、霉菌、酵母菌等微生物的数量和种类,以评估食品的卫生状况。
最后,食品半成品的检验标准应当遵循国家相关法律法规和行业标准,确保检
验结果的科学性和可靠性。
同时,针对不同种类的食品半成品,应当制定相应的检验标准,包括但不限于食品安全标准、质量指标、卫生要求等。
只有严格执行检验标准,才能有效保障食品半成品的质量和安全。
综上所述,食品半成品的检验标准是保障食品安全和质量的重要环节,对于食
品生产企业和消费者来说具有重要意义。
通过制定科学合理的检验标准,严格执行检验方法,不断提高检验水平,才能确保食品半成品的质量和安全,促进食品行业的健康发展。
半成品质量检验标准

半成品质量检验标准编制:审核:批准:受控状态:文件编号:发布日期:生效日期:目的:明确钣金车间各工序所生产的零部件的检验方法和质量要求,确保每件产品合格流入下一道工序。
适用范围:钣金车间加工的各工序,是对钣金车间加工产品的质量的控制。
职责:1、钣金车间操作技术人员负责对钣金加工过程的产品的自检,互检。
2、综合质检部在钣金车间的质检员负责对钣金生产加工的过程中的产品质量进行抽验、监督、确认。
3、综合质检部负责对不合格品的发现,记录并做标识隔离,组织处理不合格品。
4、生产部钣金车间参与不合格品的处理。
5、采购部对进厂的钣金原料不合格品与供应商进行沟通。
检测工具:5mm卷尺、200\300卡尺、角度尺、目测一、下料组1、内装:⑴先审图后施工,首先对工程项目的料厚,规格,领用数量进行审核后,严格按图纸要求进行下料。
⑵标准件下料5件内的长≤2000m m、宽≤1200m m尺寸公差控制在±0.5m m,5件以上的产品下料尺寸要完全跟图纸一致,≥2000m m公差控制在±0.8m m.⑶非标件下料5件以内的长≤2000m m、≤1200m m宽尺寸公差控制在±0.8m m,5件以上的产品下料尺寸要完全跟图纸一致,≥2000m m公差控制在±1m m。
⑷标准件、非标件的下料毛刺公差控制在±0.3m m。
⑸标准件5件以内的产品对角线公差在±0.5m m。
5件以上的产品对角线要完全跟图纸一致,非标件5件以内的产品角线公差在±1m m,5件以上的产品对角线要完全跟图纸一致,长度≥4000m m,宽度≥1300m m对角线公差±3m m。
⑹表面无划伤、凹凸点、水印、氧化、辊印、波浪、变形等。
划伤、凹凸点宽度>1m m,深度>0.3m m,板面是≤2000m m,划伤、凹凸点宽度>1.5m m、深度>0.5m m,板面是≥2000m m。
⑺标准件每隔半小时对所下之料进行抽检,非标件每隔3-5件须进行抽检。
半成品检验标准
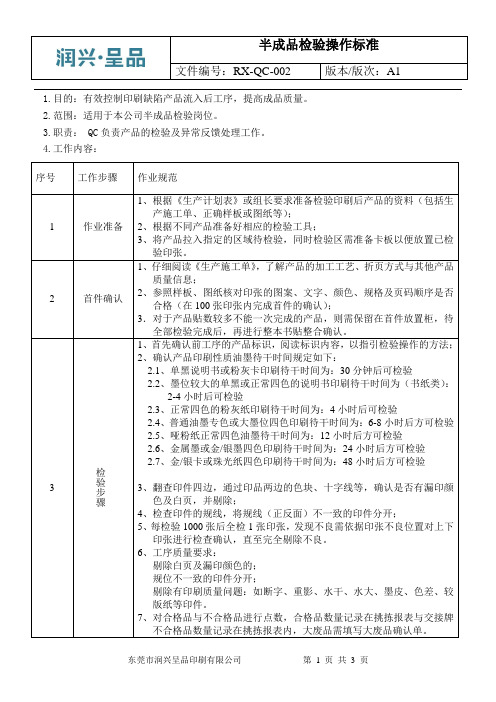
1.目的:有效控制印刷缺陷产品流入后工序,提高成品质量。
2.范围:适用于本公司半成品检验岗位。
3.职责: QC负责产品的检验及异常反馈处理工作。
4.工作内容:序号工作步骤作业规范1 作业准备1、根据《生产计划表》或组长要求准备检验印刷后产品的资料(包括生产施工单、正确样板或图纸等);2、根据不同产品准备好相应的检验工具;3、将产品拉入指定的区域待检验,同时检验区需准备卡板以便放置已检验印张。
2 首件确认1、仔细阅读《生产施工单》,了解产品的加工工艺、折页方式与其他产品质量信息;2、参照样板、图纸核对印张的图案、文字、颜色、规格及页码顺序是否合格(在100张印张内完成首件的确认);3.对于产品贴数较多不能一次完成的产品,则需保留在首件放置柜,待全部检验完成后,再进行整本书贴整合确认。
3 检验步骤1、首先确认前工序的产品标识,阅读标识内容,以指引检验操作的方法;2、确认产品印刷性质油墨待干时间规定如下:2.1、单黑说明书或粉灰卡印刷待干时间为:30分钟后可检验2.2、墨位较大的单黑或正常四色的说明书印刷待干时间为(书纸类):2-4小时后可检验2.3、正常四色的粉灰纸印刷待干时间为:4小时后可检验2.4、普通油墨专色或大墨位四色印刷待干时间为:6-8小时后方可检验2.5、哑粉纸正常四色油墨待干时间为:12小时后方可检验2.6、金属墨或金/银墨四色印刷待干时间为:24小时后方可检验2.7、金/银卡或珠光纸四色印刷待干时间为:48小时后方可检验3、翻查印件四边,通过印品两边的色块、十字线等,确认是否有漏印颜色及白页,并剔除;4、检查印件的规线,将规线(正反面)不一致的印件分开;5、每检验1000张后全检1张印张,发现不良需依据印张不良位置对上下印张进行检查确认,直至完全剔除不良。
6、工序质量要求:剔除白页及漏印颜色的;规位不一致的印件分开;剔除有印刷质量问题:如断字、重影、水干、水大、墨皮、色差、较版纸等印件。
半成品检验管理制度

半成品检验管理制度一、总则为规范半成品检验工作,确保半成品质量,提高生产效率,制定本制度。
二、适用范围本制度适用于公司生产部门半成品的检验工作。
三、责任部门1. 生产部门负责半成品的生产和检验工作。
2. 质量部门负责监督和指导半成品的检验工作。
四、半成品检验标准1. 成品外观应符合相关国家标准。
2. 成品尺寸应在允许范围内。
3. 成品材料应符合相关规定。
4. 成品性能应符合相关国家标准。
五、半成品检验程序1. 半成品检验由生产部门工人负责进行。
2. 根据检验标准,制定检验计划。
3. 对半成品进行外观、尺寸、材料、性能等方面进行检验。
4. 发现问题及时处理,合格的半成品进行下一步生产,不合格的半成品应及时处理和返修。
5. 检验记录应当详细,包括检验的时间、地点、人员、结果等。
六、半成品检验设备1. 公司应配备相应的检验设备。
2. 检验设备的维护保养工作由相关人员负责。
3. 检验设备的使用应按照操作规程进行,保证设备正常使用。
七、半成品检验人员培训1. 公司应定期对半成品检验人员进行技术培训。
2. 培训内容包括半成品检验标准、检验设备的使用和维护等。
3. 培训后应进行考核,确保员工掌握相关知识和技能。
八、半成品检验记录管理1. 检验记录应当完整、准确、真实,不得随意篡改或删除。
2. 检验记录应保存至少两年,以备查验。
3. 检验记录应按规定进行归档,便于管理和查询。
九、半成品检验结果处理1. 合格的半成品可以进入下一步生产环节。
2. 不合格的半成品应及时返工或报废,不得随意流入下一步生产环节。
3. 不合格的半成品应及时处理并分析原因,防止类似问题再次发生。
十、半成品检验不合格处理1. 不合格的半成品应在专人监督下进行返工处理。
2. 返工后的半成品应再次进行检验,确保质量符合标准。
3. 经过返工处理为合格的半成品,应加强质量管理,防止再次出现问题。
十一、其他其他事项按照公司相关管理规定执行。
十二、制度的解释权本制度的解释权归公司质量部门负责。
原辅材料、半成品质量检验标准及流程
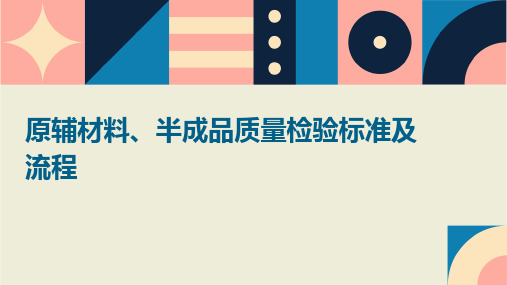
抽样计划
根据产品特性和质检标准,制定合理的抽样计划,确定抽样数量、抽样频率和抽样 方法。
对原辅材料和半成品进行外观、尺寸、重量、色泽等直观检验,确保产品符合要求 。
根据生产批次和产品特性,对原辅材料和半成品进行随机抽样,确保样品具有代表 性。
检验操作流程
01 按照质检标准和产品要求,对原辅材料和半成品 进行各项指标的检验。
原辅材料、半成品质量检验标准及 流程
• 引言 • 原辅材料质量检验标准 • 半成品质量检验标准 • 质量检验流程 • 质量检验工具和技术 • 不合格品处理及改进措施 • 质量检验培训和意识培养 • 附录:质量检验相关文件和记录
01
引言
目的和背景
确保原辅材料、半成 品的质量符合规定要 求,提高产品质量和 稳定性。
提高生产效率和成本 控制水平,实现企业 可持续发展。
降低生产过程中的不 良品率,避免因质量 问题导致的生产中断 或退货。
定义与术语
原辅材料
指用于生产过程中的各种原材料和辅助材料,如化工原料、面料 、辅料等。
半成品
指经过一定加工处理但尚未完成全部加工过程的中间产品,如完成 部分工序的纺织品、电子产品等。
将检验报告及时上报相关部门和领导,以便及时 采取相应措施解决问题。
05
质量检验工具和技术
常规检测设备
电子秤
游标卡尺
计时器
测温仪
用于称量原辅材料的重 量。
用于测量原辅材料的尺 寸。
用于测量加工过程的时 间。
用于测量加工过程的温 度。
精密检测设备
01
02
03
04
显微镜
用于观察原辅材料的微观结构 。
02 对各项指标进行详细记录,包括但不限于成分、 密度、含水量、粒度、硬度等。
半成品检验标准
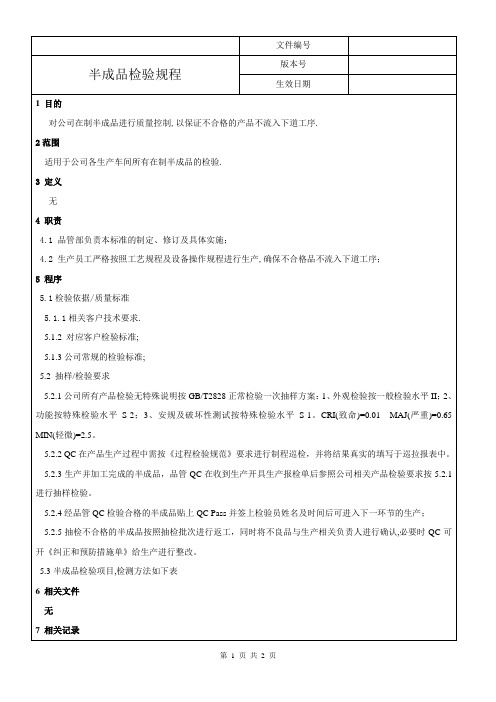
半成品检验规程
版本号
生效日期
1目的
对公司在制半成品进行质量控制,以保证不合格的产品不流入下道工序.
2范围
适用于公司各生产车间所有在制半成品的检验.
3定义
无
4职责
4.1品管部负责本标准的制定、修订及具体实施;
4.2生产员工严格按照工艺规程及设备操作规程进行生产,确保不合格品不流入下道工序;
5程序
5.2.2QC在产品生产过程中需按《过程检验规范》要求进行制程巡检,并将结果真实的填写于巡拉报表中。
5.2.3生产并加工完成的半成品,品管QC在收到生产开具生产报检单后参照公司相关产品检验要求按5.2.1进行抽样检验。
5.2.4经品管QC检验合格的半成品贴上QC Pass并签上检验员姓名及时间后可进入下一环节的生产;
5.1检验依据/质量标准
5.1.1相关客户技术要求.
5.1.2对应客户检验标准;
5.1.3公司常规的检验标准;
5.2抽样/检验要求
5.2.1公司所有产品检验无特殊说明按GB/T2828正常检验一次抽样方案:1、外观检验按一般检验水平II;2、功能按特殊检验水平S-2;3、安规及破坏性测试按特殊检验水平S-1。CRI(致命)=0.01 MAJ(严重)=0.65 MIN(轻微)=2.5。
5.2.5抽检不合格的半成品按照抽检批次进行返工,同时将不良品与生产相关负责人进行确认,必要时QC可开《纠正和预防措施单》给生产进行整改。
5.3半成品检验项目,检测方法源自下表6相关文件无7相关记录
7.1《QC巡检登记表》
7.2《半成品/成品检验报告》
7.3《生产报检单》
7.4《纠正和预防措施单》
- 1、下载文档前请自行甄别文档内容的完整性,平台不提供额外的编辑、内容补充、找答案等附加服务。
- 2、"仅部分预览"的文档,不可在线预览部分如存在完整性等问题,可反馈申请退款(可完整预览的文档不适用该条件!)。
- 3、如文档侵犯您的权益,请联系客服反馈,我们会尽快为您处理(人工客服工作时间:9:00-18:30)。
半成品质量检验标准 Document serial number【LGGKGB-LGG98YT-LGGT8CB-LGUT-半成品质量检验标准编制:审核:批准:受控状态:文件编号:发布日期:生效日期:目的:明确钣金车间各工序所生产的零部件的检验方法和质量要求,确保每件产品合格流入下一道工序。
适用范围:钣金车间加工的各工序,是对钣金车间加工产品的质量的控制。
职责:1、钣金车间操作技术人员负责对钣金加工过程的产品的自检,互检。
2、综合质检部在钣金车间的质检员负责对钣金生产加工的过程中的产品质量进行抽验、监督、确认。
3、综合质检部负责对不合格品的发现,记录并做标识隔离,组织处理不合格品。
4、生产部钣金车间参与不合格品的处理。
5、采购部对进厂的钣金原料不合格品与供应商进行沟通。
检测工具:5mm卷尺、200\300卡尺、角度尺、目测一、下料组1、内装:⑴先审图后施工,首先对工程项目的料厚,规格,领用数量进行审核后,严格按图纸要求进行下料。
⑵标准件下料5件内的长≤2000m m、宽≤1200m m尺寸公差控制在±,5件以上的产品下料尺寸要完全跟图纸一致,≥2000m m公差控制在±.⑶非标件下料5件以内的长≤2000m m、≤1200m m宽尺寸公差控制在±,5件以上的产品下料尺寸要完全跟图纸一致,≥2000m m公差控制在±1m m。
⑷标准件、非标件的下料毛刺公差控制在±。
⑸标准件5件以内的产品对角线公差在±。
5件以上的产品对角线要完全跟图纸一致,非标件5件以内的产品角线公差在±1m m,5件以上的产品对角线要完全跟图纸一致,长度≥4000m m,宽度≥1300m m对角线公差±3m m。
⑹表面无划伤、凹凸点、水印、氧化、辊印、波浪、变形等。
划伤、凹凸点宽度>1m m,深度>,板面是≤2000m m,划伤、凹凸点宽度>、深度>,板面是≥2000m m。
⑺标准件每隔半小时对所下之料进行抽检,非标件每隔3-5件须进行抽检。
⑻每份订单编号的贴法由所生产的板的实际情况下贴在同一位置。
⑼同一批次、同一编号、同一料厚度的下料时放置在一起。
⑽在原材料不够的特殊情况下用其它料代替的时候需在板面上做好详细的标注。
⑾下好的半成品材料要轻拿轻放。
⑿样品的下料宽度、长度、对角线尺寸公差要跟图纸要求的一致。
2、外装;⑴先审图后施工,首先对工程项目的料厚,规格,领用数量进行审核后,严格按图纸要求进行下料。
⑵标准件5件以内的下料的≤2000m m长、宽≤1200m m尺寸公差控制在±,5件以上的产品下料尺寸要完全跟图纸一致,≥2000m m公差控制在±1m m。
⑶非标件5件以内的下料长≤2000m m、宽≤1200m m尺寸公差控制在±1m m,5件以上的产品下料尺寸要完全跟图纸一致,≥2000m m公差控制在±m m。
⑷标准件、非标件的下料毛刺公差控制在±。
⑸标准件5件以内的产品对角线公差在±1m m。
5件以上的产品对角线要完全跟图纸一致,非标件5件以内的产品角线公差在±,5件以上的产品对角线要完全跟图纸一致。
≥2000m m的对角线公差在±2-3m m。
⑹表面无划伤、凹凸点、水印、氧化、辊印、波浪、变形等。
划伤、凹凸点宽度>1m m,深度>,板面是≤2000m m,划伤、凹凸点宽度>、深度>,板面是≥2000m m。
⑺每隔半小时对所下之料进行抽检。
⑻每份订单编号的贴法由所生产的板的实际情况下贴在同一位置。
⑼同一批次、同一编号、同一料厚度的下料时放置在一起。
⑽在原材料不购的特殊情况下用其它料代替的时候需在板面上做好详细的标注。
⑾下好的半成品料要轻拿轻放。
⑿样品的下料宽度、长度、对角线尺寸公差要跟图纸要求的一致。
三、切角(数控冲,普冲,雕刻,内装,外装通用)1先审图后施工,在切角前对上工序工件的表面质量,下料尺寸做出最后的复检。
2严格按图纸要求进行冲,切,雕、并错位冲角码孔,冲角码时间距偏差±5m m。
3冲,切,雕的长、宽尺寸公差控制在±。
4表面无划伤、毛刺宽度>1m m,深度>,板面是≤2000m m,划伤、毛刺宽度>、深度>,板面是≥2000m m。
5冲,切,雕时注意内装、外装的包角工艺处理。
6在生产密拼的勾搭板时应采用长包短或短包长的工艺处理。
7非标件要全检、标准件要进行三检的标准,(三检是,首检、过程检验、最终检验)。
8冲切样板的制作要专人负责生产。
9标准产品上数控冲时应注意检查编程的图形跟生产图是否一致,夹钳应夹尺寸,对冲好后的第一件产品进行检查后确认不无误后方可批量生产。
10非标产品上数控冲时应注意冲的正反方向及编号是否被冲掉,如编号冲掉应及时用彩笔写上后补标签.而后检查所冲的每件产品是否符合技术要求。
11雕刻机在雕产品时应检查技术部提供的展开图是否跟生产图的尺寸方向一致后方可生产。
在雕刻时的边应无毛刺,雕好后的须检查尺寸,并注意方向,标签的贴法要统一。
四、冲孔(外协冲孔,本公司冲孔)1先审图后施工,严格按图纸要求进行冲孔作业。
2不能有多冲,少冲,冲变形等现象。
3因铝的拉伸性冲好后的板面长、宽公差允许在﹢。
4冲好后的板面要求无毛刺,并进行平直处理达到板面平整的最佳程度。
5冲孔后的板面油污要进行简单的处理。
6冲孔板冲好后板面无压痕。
五、辊弧(内装、外装通用)1严格按图纸要求的半径进行滚弧。
2辊弧时注意正反滚的方向。
3滚出来的弧一定要顺,不能有直线段,滚出来的半径与实际半径小10m m为宜。
4滚弧前要对滚铜上的杂质进行清理。
5滚弧时要从大的半径逐步下调到图纸所要半径为止,并做到是从大件到小件或小件到大件的方式进行。
6滚弧好的板面不能有滚铜印,并要对半径进行初娇,到烧焊,粗磨后进行所要半径样板的娇直处理。
六、折弯1、内装:⑴首先检查上工序冲切好的产品与图纸是否一致,在做好工作前的准备时严格按图纸进行调机折弯。
⑵做到无图纸不施工、不审图不施工、无上岗证不施工的三无原则。
⑶成型好的板面平整度公差2m m,≤2000m m,≥2000m m的公差在3m m-4m m。
⑷成型好的板5件以内的板面长≤2000m m、宽≤1200m m公差控制在±,5件以上的公差要与图纸相符,≥2000m m的公差在±1m m。
⑸密拼板的角度控制在88-89°为宜,除特殊情况下(包柱最佳角度为88°)。
⑹成型好的板对角线公差在±1m m。
⑺成型好的板非标件要全检、标准件要进行三检的标准,(三检是,首检、过程检验、最终检验)。
⑻对有特殊技术要求的板成型好后要进行拼装检验。
⑼对以加工的产品数量要做上记录以方便查阅数量。
⑽小角度5件以上的板要用折弯机折压而成。
⑾大小角度的公差控制在±1°⑿对成型好的产品要轻拿轻放并放到指定位置。
⒀样板的制作要专人负责生产,尺寸公差应与图纸尺寸公差一致,表面要美观。
2、外装:⑴首先检查上工序冲切好的产品与图纸是否一致,在做好工作前的准备时严格按图纸进行调机折弯。
⑵做到无图纸不施工、不审图不施工、无上岗证不施工的三无原则。
⑶成型好的板面平整度公差2-3m m,长度≤2000m m,宽度≤1200m m,≥2000m m的平整度公差在3m m-4m m。
⑷成型好的板5件以内的板面长、宽公差控制在±1m m,≤2000m m,5件以上的公差要与图纸相符≥2000m m的公差在±2m m。
⑸外装板的角度控制在90°为宜,除特殊情况下(包柱最佳角度为88°)。
⑹成型好的板对角线公差在±2m m。
⑺成型好的非标件要全检、标准件要进行三检的标准,(三检是,首检、过程检验、最终检验)。
⑻对有特殊技术要求的板成型好后要进行拼装检验。
⑼对以加工的产品要做上记录以方便查阅数量。
⑽小角度5件以上的板要用折弯机折压而成。
⑾大小角度的公差控制在±2°⑿对成型好的产品要轻拿轻放并放到指定位置。
⒀样板的制作要专人负责生产,尺寸公差应与图纸尺寸公差一致,表面要美观。
七、烧焊1先审图后施工,严格按图纸进行焊接。
2焊接前要对成型好的角度进行初矫,在焊接时要牢固、不得漏焊、少焊、脱焊、裂缝、而且满焊要平整光滑。
3焊接后不管是大角度还是小角度还是90°都要进行角度娇正。
4图纸要求特殊焊接的要特殊焊接并确保质量。
5焊接的配件公差不得超过±2m m。
6样品要专人负责焊接并作满焊处理。
7超大板组焊焊接时内须做点焊处理。
8刨槽后的板在焊接时不管长与短均做点焊处理。
八、打磨1先审图后施工,严格按图纸要求对焊接好了的进行打磨处理。
2要重点对焊接焊缝、满焊、表面有划伤、擦伤、凹凸不平等进行打磨光滑平整。
3满焊后的R角大小要打磨一致,密拼板满焊后的打成直角,外装板打成圆角。
4不焊接的勾搭板要进行措角处理。
5内外装板打磨时要重点处理棱角或较难打磨到的死点。
6打磨后的产品要外观完美,在放置产品时要轻拿轻放。
7样品要专人负责打磨、抛光处理。
九、组装1先审图后施工,严格按图纸要求角码高计划进行角码的安装,角码安装的高度公差±1m m,角码位置的误差在5m m内,殊角码要保证其要求的高度。
2角码采用的材料厚度要一样。
3加强筋的安装要按图纸要求,位置和尺寸公差在5m m内,背筋的力度不够时要增加并且保证板面平整面不变形。
4加强筋的长度,腰行孔的打法,种钉的个数同一批板要一致。
5加强筋的分布要均匀并在加筋时要注意避开编号。
6根据种钉的实际材料厚度在种钉时对电流大小进行调节,注意加筋后板面有无种钉印。
7角码安装好后检测板的平整度,平整度公差1000≤2m m,但不允许起波浪状。
8娇正、拼装、检验后的板方可进入下工序作业。
十、抛光1先审图后施工,严格按图纸要求进行抛光处理。
2在组装接过也做好的产品进行抛光时应轻拿轻放。
3抛光后的产品表面用手检验无划手就现象,抛光时做到主次分明,重点抛光有划伤、种钉印、波浪、辊印、凹凸点的。
4抛光好的产品放置移交区时要分清批次、编号、颜色、放置要整洁规范。
5放置做好的成品要轻拿轻放,正反合并。
6样品抛光出来后板面平整、光滑、美观、棱角分明,公司钢印清晰,角码无毛利,背面同样是光滑、美观。
7抛光时应抛无标签那面。
拟稿人:。