设备确认操作规程(英文)
设备的维护维修及设备确认

18
1、企业应当对新的或改造的厂房、设施、设备按 照预定用途和本规范及相关法律法规要求制定用户 需求,并经审核、批准。
2、设计确认应当证明设计符合用户需求,并有相 应的文件。
19
基本工艺描述 容量或产量 设计原则 各部分结构设计 各部分材质选择 各部分功能设计 对公用介质的要求 技术参数 安全联锁、健康、环保措施 各部分自控功能 在线检测、自动剔废功能 工艺流程PID图、设备平面布局图、机械、电气原理图 关键部件清单核查 技术标准与方案、报告
照明、暖通、给排水、公用工程、人净、物净、、 防虫鼠等设施。附着在厂房建筑物上(或内)不可 分割的部分。 设备:由金属或其他材料组成,由若干零部件装配 起来,在一种或几种动力驱动下,能够完成生产、; 加工、运行等功能或效用的装置。 系统:若干设备与设施的功能组合。
10
11
概念: 硬件的确认:用于证明公用系统及各个设备适合于
修改;C 安全联锁与保护测试;D 程序运行、手动测试; E 空载运行;F 负载运行;G 更换不同品种规格的测试。 5、不符合项清单,缺陷整改。 6、再检查、再测试。 7、清洁、涂油、装箱检查
因为药厂的机械加工条件的限制,所以:必须把任 何微小缺陷消灭在出厂之前。
实验室操作规程英文翻译

实验室操作规程英文翻译Laboratory Operating ProceduresIntroduction:Laboratory safety is of paramount importance to ensure the well-being of laboratory personnel and to prevent accidents or incidents that may compromise experimental results. These laboratory operating procedures aim to provide guidelines for safe and efficient laboratory practices. All personnel working in the laboratory are expected to adhere to these procedures at all times.1. General Safety Guidelines:1.1. Personal Protective Equipment (PPE): All laboratory personnel must wear appropriate PPE, including lab coats, gloves, and safety glasses, when working in the laboratory.1.2. Personal Hygiene: Maintain good personal hygiene by washing hands thoroughly before and after any laboratory activity.1.3. Fire Safety: Know the location of fire exits, fire extinguishers, and emergency showers. In the eventof a fire, immediately evacuate the laboratory and follow the designated emergency procedures.1.4. Chemical Safety: Properly handle chemicals and follow the Material Safety Data Sheet (MSDS) guidelines provided for each chemical. Avoid direct contact with skin, eyes, and inhalation of chemical fumes.1.5. Electrical Safety: Inspect electrical equipment regularly for frayed wires or damaged plugs. Only authorized personnel should make repairs or adjustments to electrical equipment.1.6. Equipment Safety: Follow manufacturer instructions for the operation, maintenance, and disposal of laboratory equipment. Do not use equipment without proper training or authorization.2. Laboratory Procedures:2.1. Experiment Planning: Before conducting any experiment, thoroughly read and understand the experimental procedures. Identify potential hazards and plan accordingly to mitigate risks.2.2. Workspaces: Keep workspaces clean, organized, and free from unnecessary clutter. Maintain clear pathways to avoid accidents and spills.2.3. Handling Glassware: Handle glassware with caution to prevent breakage and injuries. Dispose of broken glassware in designated sharps containers.2.4. Chemical Storage: Store chemicals in appropriate containers and cabinets, following chemical compatibility guidelines. Clearly label all chemical containers with their contents and expiration dates.2.5. Waste Disposal: Dispose of laboratory waste in designated waste containers. Separate hazardous waste from non-hazardous waste and ensure proper disposal according to regulatory requirements.2.6. Spill Procedures: Promptly report and clean up any spills, following the appropriate spill containment and cleanup procedures. Use suitable absorbent materials and dispose of them as hazardous waste.2.7. Laboratory Instruments: Use laboratory instruments, such as balances, pipettes, and centrifuges, according to manufacturer instructions. Calibrate and maintain instruments regularly to ensure accurate results.3. Emergency Procedures:3.1. First Aid: Familiarize yourself with the location of first aid kits and emergency eyewash stations. Report all injuries, accidents, or near misses to the laboratory supervisor immediately.3.2. Chemical Spills: In the event of a chemical spill, immediately notify the laboratory supervisor and follow the spill procedures. Evacuate the affected area if necessary.3.3. Fire Emergencies: In the event of a fire, activate the fire alarm, evacuate the laboratory, and follow the designated emergency procedures. Do not use elevators during a fire emergency.3.4. Gas Leaks: In the event of a gas leak, immediately evacuate the laboratory and inform the laboratory supervisor. Do not use any electrical devices or create any sources of ignition.Conclusion:These laboratory operating procedures provide guidelines for safe laboratory practices. It is the responsibility of all personnel to familiarize themselves with these procedures and adhere to them at all times. Any deviations or unsafe conditions should be reported to the laboratory supervisor immediately. By following these procedures, we canensure a safe and productive laboratory environment for all.。
起重设备安全操作规程(中英文)-百

起重设备安全操作注意事项Precautions for Safe Operation of Lifting Equipment (Crane)1. 正常作业时,严禁使用强制释放开关;During normal operation, the forced release switch is strictly prohibited to press;2. 换挡时注意要逐档增加或减少,不要从一档越过二档,直接换到三档,反之亦然;When shifting gears, pay attention to increasing or decreasing gear by gear.Don't go over from the first gear and directly shift to the third gear, skipping the second gear, and vice versa;3. 车辆行驶时,气压表指示气压应不低于0.7MPa;When the vehicle is running, the air pressure indicated by the barometer should not be lower than 0.7MPa;4. 任何时候发动机都不应长时间在无负荷的情况下高速运转;At no time should the engine run at high speed without load for a long time;5. 行驶时,上车操作室严禁坐人;When driving, it is strictly forbidden to sit in the operating room of the vehicle;6. 起重机进入工作场地,驾驶员要特别注意场地环境,避免轮胎被坚硬的尖锐物刺破或刺伤;When the crane enters the work site, the driver must pay special attention to the site environment to avoid the tires from being punctured by hard sharp objects;7. 作业前必须先打开支腿使轮胎离地,作业当中不准起动轮胎;Before operation, the outriggers must be opened to lift the tire off the ground, and it is not allowed to start the tire rotation during the operation;8. 起重工作时,当风力大于6级(14m/s)或雷雨天气时应停止工作,并将吊臂缩回成行驶状态;When lifting , stop working when the wind is greater than force 6 strong breeze (14m/s) or there are thunderstorms, and retract the crane arm intodriving state;9. 工作时,起重臂下严禁站人;When working, it is strictly forbidden to stand under the crane arm;10. 起重作业时,转台上不得站人;During lifting operations, no one is allowed to stand on the turntable;11. 回转半径内注意安全;Pay attention to safety within the radius of gyration;12. 不准在重物上有人的情况下起吊重物;Do not lift heavy objects with people on them;13. 不准斜拉斜吊物品;It is not allowed to pull items diagonally;13. 严禁在不使用支腿的情况下进行作业,且应选择平坦坚实的场地,如遇地基松软或凹凸不平,应将枕木垫于支脚板下,使起重机保持平稳状态;It is strictly forbidden to work without using outriggers, and a flat and solid site should be selected. In case of soft or uneven foundation, the crossties should be cushioned under the supporting leg to keep the crane in a stable state;15. 严禁帯载行车;Driving with load is strictly prohibited;16. 严禁帯载伸缩吊臂;It is strictly forbidden to extend and retract the arm when carrying a heavy load;17. 重物在空中作较长时间停留时,司机不得离开操纵室;When heavy objects stay in the air for a long time, the driver shall not leave the control room;18. 操作应平稳、缓和,严禁猛拉、猛推操纵手柄;The operation should be smooth and gentle, and it is strictly forbidden to pull or push the handle;19. 操作时应经常注意对起重机进行检查,发现异常,应查明原因,及时排除;Always pay attention to checking the crane during operation. If abnormalities are found, the cause should be found out and eliminated in time;20. 操作人员在身体不适或精神不佳时,不应操纵起重机,严禁司机酒后操纵起重机;Operators should not operate the crane when they are unwell or in poor state. Drivers are strictly prohibited from operating the crane after drinking;21. 操作支腿时应注意周围留有足够的空间,以免碰伤人或起重;When operating the outriggers, pay attention to leaving enough space around to avoid hurting people or the crane;22. 在支腿水平油缸未完全伸出的情况下严禁伸出垂直油缸,在支脚板未完全离开地面之前,严禁操作支腿的水平油缸;It is strictly forbidden to extend the vertical oil cylinder when the horizontal oil cylinder of the outrigger is not fully extended, and it is strictly prohibited to operate the horizontal oil cylinder of the outrigger before the supporting leg is completely off the ground;23. 起重机作业过程中,严禁操纵支腿手柄;During crane operation, it is strictly forbidden to manipulate the outrigger handle;24. 只能垂直起吊载荷,不许拖拽尚未离地的载荷;The load can only be lifted vertically, and the load that has not been lifted off the ground is not allowed to be dragged;25. 起重机作业时,主、副卷扬上严禁站人;When the crane is operating, it is strictly forbidden to stand on the main and auxiliary hoists;26. 操作时应十分平稳,在起吊重物时,急剧的操作会给起重机带来很大的冲击;The operation should be very stable. When lifting heavy objects, the abrupt operation will bring great impact to the crane;27. 回转运动时,驾驶员后方和两侧视野受到很大限制,因此,必须十分谨慎操作,在确认起重机回转半径范围内没有人和其他障碍物后方可操作;During the rotary movement, the driver’s r ear and both sides of the field of vision are greatly restricted. Therefore, the operator must be very cautious and can only operate after confirming that there are no people and other obstacles within the radius of gyration of the crane;28. 必须确保足够的作业空间;Sufficient working space must be ensured;29. 随着使用时间的增加,钢丝绳会产生疲劳现象,应引起足够的重视。
设备确认操作规程(英文)

PURPOSE:To provide a formal methodology to be followed during qualification of equipment.SCOPE:Applicable to qualification of new equipment, re-qualification of equipment, which has undergone major modification, relocation of equipment and Periodic Qualification as per schedule in Pharma manufacturing department.RESPONSIBILITY:Production, Engineering, Safety, Quality Control and Quality Assurance staff. DEFINITION:Qualification: Documented verification that the environment and equipment are appropriate for the designated function.User Requirement Specification (URS): A Requirement specification that describes what the equipment or system is suppose to do, thus containing at least set of criteriaor conditions that have to be met.Functional Design Specification (FDS): Functional design specification is a document that specifies in a complete, precise, variable manner, the requirement design, behaviour or other characteristics of a system or component and often the procedures for determining whether these provisions have been satisfied.Specification that is offered by manufacturing based on URS and are agreed mutually. Design Qualification (DQ): Formal and systematic verification that the requirements defined in the specification phase are completely covered by the succeeding specification or implementation phase.Factory Acceptance Test (FAT): Testing conducted at the suppliers factory to determine whether or not a system specifies it’s acceptance criteria and to enable the user to determine whether or not to accept the system.Installation Qualification (IQ): Documented verification that a system is installed according to written and pre-approved specifications.Site Acceptance Test (SAT): An acceptance test at the users site, usually involve the supplier.Operation Qualification (OQ): Documented verification that a system operates according to written and pre-approved specification throughout all specified operating ranges..PLC Validation: Documented verification that PLC Hardware are as per original drawing, Digital and Analog Input and Output are connected as per PLC Architecture and functioning according to written and pre-approved specification throughout all specified operating ranges.Performance Qualification (PQ): Documented verification that a system is capable of performing or controlling the activities of the processes, it is required to perform or control, according to written and pre-approved specifications, while operating in its specified operating environment.User (s): The person, or persons, who operate or interact directly with the system. Supplier: Any organisation or individual contacted directly by the user to supply a product or service.Critical Equipment: The machine within a system where the malfunctioning or failure of equipment will have direct impact on product quality. Where product is in direct contact with machine body parts.Non-critical Equipment: The machine within a system where the malfunctioning or failure of equipment will not have direct impact on product quality. Where product is not in direct contact with machine body parts.1.0 HEALTH, SAFETY AND ENVIRONMENT: (对验证实施人员的HES要求)1.1 Personnel involved in qualification / re-qualification / periodic qualificationshould use appropriate personal protective equipment.1.2 Do not touch the moving parts.1.3 Electrical isolation should be done before any electric control panelverification.1.4 Read the safety instructions specified in the operation Manual of themachine to be qualified.2.0 PROCEDURE:2.1 Equipment qualification should be based on the following documents2.1.1 User Requirement Specification (URS)2.1.2 Functional Design Specification (FDS)2.1.3 Design Qualification (DQ)2.1.4 Factory Acceptance Test (FAT)2.1.5 Checklist on Receipt2.1.6 Installation Qualification (IQ).2.1.7 Operation Qualification (OQ)2.1.8 PLC Validation ( If applicable)2.1.9 Provisional Handover Certificate2.1.10 Performance Qualification (PQ)2.1.11 Handover CertificateThe flow of the equipment qualification is as followsURS → FDS → DQ → FAT → IQ → OQ → PLC Validation (if applicable)SAT→ PQ2.1.1 User Requirement Specification (URS):2.1.1.1 URS protocol should be approved by the project team(Users) members and Quality Assurance with Name, Signand Date.2.1.1.2 Following points should be considered during thedevelopment of URS.➢Introduction➢Over view➢Operation requirements➢Constraints➢Life cycle➢Glossary➢References➢Approval2.1.1.3 Each URS protocol should be allotted with a protocol no. inthe format specified below“URS/P”Where,“URS” stands for User requirement specification.“P” sta nds for equipment / instrument / balance / areaabbreviated code.2.1.1.4 The protocol should also identify with a Version No. Wherethe version no. changes with every change in the URS.2.1.1.5 The URS protocol header should consist of the following detailsas mentioned below:➢Title of the URS➢Protocol No.➢Version No.➢Date➢Cipla Patalganga➢Unit➢Page No..精品文档.A specimen of the header is given below:2.1.2 Functional Design Specification (FDS):2.1.2.1 The FDS should be the manufacturer interpretation ofURS. FDS should include basic functioning of theequipment with focus on control and critical componentsspecifications and functions.2.1.2.2 The FDS should be in the form of separate documentand should include equipment specification, P&IDdiagrams.2.1.2.3 The FDS protocol / report should be mutually approvedby the user and supplier with sufficient technical detailsbased on the techno commercial offer.2.1.2.4 The supplier is finally selected and CER is raised.2.1.2.5 Any changes made after finalisation of DQ should undergo change control procedure as per SOP CQA 06.2.1.3 Design Qualification (DQ):2.1.3.1 Design qualification should be based on the discussionbetween the supplier and the user with reference toURS / FDS.2.1.3.2 Following points should be considered during thedevelopment of design qualification.➢ Purpose➢ Scope➢ Responsibility➢ Project requirement➢ Critical variables to be met➢ Process/ Product parameters e.g. Capacity etc.➢ cGMP considerationse.g. MOC of individual parts, finish of contact parts➢ Critical parameters e.g. Instrumentation, limits,➢ Safety➢ Location suitability➢ References➢ Documents to be attached.➢ Any changes made against the formally agreedparameters (Deviation if any).➢ Justification for acceptance (if any deviation)➢ Review (Inclusive of follow up action, if any)➢ Recommendation➢ Signing off2.1.3.3 Any change in DQ should be through a change controlprocedure as per SOP CQA-06 and should bedocumented.2.1.4 Factory Acceptance Test (FAT):2.4.1 The FAT sh ould be conducted at the supplier’s premisesunder the users supervision unless agreed upon.2.4.2 The FAT protocol / report should be prepared by the supplieras per Manufacturers format and should be submitted forapproval of user.2.4.3 The equipment should be shipped to the site only afterapproval by the user.2.4.4 The FAT protocol / report should include details of the URSand FDS.2.4.5 Any modification, changes needs during the FAT should bedocumented and intimated to the user and carried out withmutual consent.2.1.5 Checklist on Receipt:2.1.5.1 All critical parts of equipment should be checked forfinish, any damages on receipt for availability as perpacking list and order details.2.1.6 Installation Qualification (IQ):2.1.6.1 All aspects such as utility connections, location suitability,material of construction of critical parts, installation of allmonitoring, controlling, instruments and gauges includingtheir calibration and certification by supplier should bechecked and verified.2.1.6.2 During the installation qualification Area Lux level, Floordrains, piping connections , machine alignment, levelling,P& ID Diagram, Schematic, circuit diagram, tagging,wiring pheruling, pneumatic connections consideredduring design qualification are checked and verified.2.1.7 Operation Qualification (OQ):2.1.7.1 During Operation qualification the working of themonitoring and controlling instruments, gauges andsystems like PLC, switches, gauges, motors, pumps etc.are checked and certified..2.1.7.2 The parameters considered during design qualificationare checked and certified.2.1.8 PLC Validation2.1.8.1 PLC validation should be carried out by competentexternal approved agency.2.1.8.2 PLC validation should be carried out during SAT orsubsequently within three months based on level ofchecks carried out during SAT. Validation should be doneaccording to pre-approved protocol and report. Allreference instruments being used for validation should becertified by approved agencies like ‘IDEMI’ and ‘ERTL.2.1.8.3 Brief description about equipment operating function andits location should be mentioned in the report. All rawdata should be handwritten at site during actual validation.2.1.8.4 The details of PLC and HMI hardware are checked as percircuit diagram and type of PLC, HMI, its software Versionno. details, details of the available digital/ analogue inputsand outputs. Installed switchgear details should bementioned i.e. SFU, MCB, relays, contactors, pushbuttons, switch, power supply, Surge protection etc.2.1.8.5 Equipment interlocks, alarms and operation logic shouldbe checked. Details of the PLC Battery conditions shouldbe checked and it’s life will be verified appropriately.2.1.8.6 All PLC validation reports should be handed over by thevalidation agency to the engineering department forverification within a week after physical verification of thesystem. Engineering, user department and qualityassurance department will verify submitted reports2.1.8.7 Any deviation observed should be highlighted and broughtup to the notice of Engineering/ User/QA dept.2.1.8.8 No changes should be made in the software or hardwareduring the course of validation.2.1.9 Site acceptance test (SAT) and Provisional HandoverCertificate:2.1.9.1 SAT should be carried out in conjugation with thesupplier and may include checks of critical components,controls based on the detail Fat, IQ and OQ have beensuccessfully performed.2.1.9.2 After the equipment goes through the installation andoperational qualification procedure, it should be reviewedat each stage by a team of Engineering, Production,Quality Assurance, Quality Control, Safety and Unit Head. .2.1.9.3 In few cases the equipment may have to go through aprocess cycle development and stabilisation phase beforesubject to validation trials.2.1.9.4 If any deviation or non conformance to the acceptancecriteria should be recorded and informed to concernedsupplier. A decision should be taken by user team andsupplier to reject or to proceed for PQ.2.1.9.5 If SAT is found to be satisfactory, equipment should beprovisionally handed over to the concerned departmentfor Performance Qualification.2.1.10 Performance Qualification (PQ):2.1.10.1 During the Performance Qualification the working of thesystem as a whole is checked with respect to out put, quality,quantity and any specific requirements as per designqualification.2.1.10.2 Critical equipment should undergo extensive validationstudies to ensure consistent performance depending onapproved validation protocol.2.1.11 Handover Certificate:After successful Performance Qualification, based on reviewby the team of Engineering, Production, Quality Assurance,Quality Control, Safety and Unit Head. The equipment ishanded over to the concerned department for regular use.2.2 Equipment Qualification and Requalification protocol consist of thefollowing sections.➢Covering page➢Table of contents.➢Glossary➢Pre approval➢Design Qualification➢Check list on receipt➢Installation Qualification➢Operation Qualification➢Provisional Handover Certificate➢Performance Qualification➢Hand over Certificate2.3 REQUALIFICATION / PERIODIC QUALIFICATION2.3.1 All Major equipment should be requalified after any majorchange in the equipment or modification.2.3.2 If there are any major changes in critical parameters of equipment .(e.g. RPM of blender, speed of agitator etc.) which has directimpact on the quality, then the revalidation of the process shouldbe done.2.3.3 The requalification need not be performed for any minor changesin the equipment, For example, few blades of multimill arereplaced.NOTE: Minor changes should be recorded in the Machine History Card.2.3.4 If any fixed equipment is shifted from one area to another area.Critical parameters should be checked during requalification.Transfer note should be made for the equipment. It should bekept along with the requalification record. For relocation ofportable equipment requalification is not required.2.3.5 During the transfer of equipment from one unit to another unitrequalification as IO, OQ should be conducted based on criticalparameters. A such copy of original qualification should beforwarded for reference.2.3.6 While transferring the equipment to other area / units, reviewshould be done for any specific requirements of conditions2.3.7 For equipment having no changes requalification time periodshould be decided based on performance of annual review of theequipment. The review of the equipment should be recorded inthe Equipment Review Report (Annexure MT95/A1) Therequalification time period should not exceed five years.2.3.8 Schedule for requalification of the major equipment shouldavailable at unit level and should be recorded in schedule forrequalification Annexure MT95/A2.2.3.9 Schedule for PLC revalidation of the major equipment should beavailable at unit level and should be recorded in AnnexureMT95/A3.2.3.10 Any changes in schedule of equipment qualification should becarried out through deviation.Requalification / Periodic Qualification protocol consist of thefollowing sections:➢Covering page➢Table of contents.➢Glossary➢Pre approval➢Over view➢Pre requisite➢Preventive Maintenance verification➢Major breakdown verification.➢System description➢Physical verification➢Calibration verification of critical components➢Calibration verification of calibration standards used➢Safety features verification➢Control panel verification➢Interlocks/controls verification➢Performance evaluation➢Documentation verification➢Post approval➢Hand over certificate2.4 Protocol Approval:2.4.1 All protocols are approved by Quality Assurance and Unit Headprior to their implementation i.e. after they are compiled by a teamof Production, Engineering, Quality Control and Safety.2.4.2 Each protocol should be allotted with a protocol number in theformat specified bellow“QUALI/X”Where,“QUALI” stands for qualification“X” stands for equipment / instrument / balance / area abbreviatedcode2.4.3 The protocol should also be identified with a Version No., wherethe version no. changes with every change in the Qualification,Requalification and Periodic Qualification of equipment.2.4.4 The Qualification, Requalification and Periodic Qualificationprotocol header should consist of the following details asmentioned below➢Title of the protocol➢Protocol No.➢Version No.➢Department➢Area➢Page No.A specimen of the header is given below:2.4.5 Frequency for Periodic QualificationFor Critical Equipment: Once in 3 years of its previous.qualification (Initial qualification / requalification)For Non Critical Equipment: Once in 5 years of its previousqualification (Initial qualification / requalification)Note: The period of periodic qualification should be determinedbased on review of history of preventive maintenance, breakdown,calibration data and criticality of process.3.0 ABBREVIATIONS:URS User Requirement SpecificationFDS Functional Design SpecificationDQ Design QualificationFAT Factory Acceptance TestIQ Installation QualificationSAT Site Acceptance TestOQ Operation QualificationPQ Performance QualificationNo. NumberP&ID Piping and Instrumentation DiagramCER Capital Expenditure RequisitionCGMP current Goods Manufacturing PracticesPLC Programmable Logic Controller.MOC Material of Construction材质i.e. That ise.g. For exampleIDEMI Institute for Design of Electrical Measuring InstrumentsERTL Electronics Regional Testing LaboratoryPLC Programmable Logic ControllerHMI Human Machine InterfaceSFU Switch Fuse UnitMCB Miniature Circuit Breaker4.0 REFERENCES:CQA-06 Change Control5.0 ANNEXURES:MT95/A1 Equipment Review Report (MT95/F1)MT95/A2 Schedule for Requalification/Periodic (MT95/F2)QualificationMT95/A3 Schedule for PLC Revalidation /Periodic (MT95/F3)Validation .。
OECD GLP Principles No. 1中英文翻译-标准操作规程
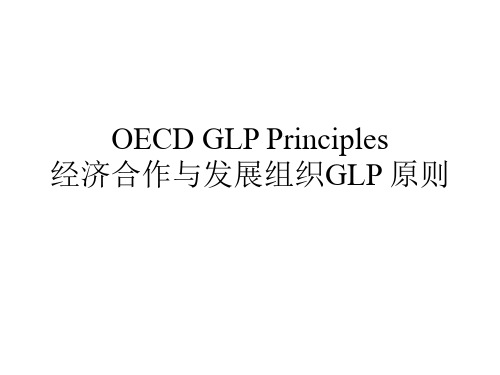
7. Standard Operating Procedures 标准操作规程
7.4Standard Operating Procedures should be available for, but not be limited to, the following categories of test facility activities. The details given under each heading are to be considered as illustrative examples. 7.4机构内的SOP应当涵盖但不局限于以下种类。 标题下的详细内容可以理解为解释性举例。
7. Standard Operating Proeference Items.供试品和对照品。 7.4.1.1Receipt, identification, labelling, handling, sampling and storage. 7.4.1.1 接收、鉴别、贴标签、存放、取样和贮存。
7. Standard Operating Procedures 标准操作规程
7.2Each separate test facility unit or area should have immediately available current Standard Operating Procedures relevant to the activities being performed therein. Published text books, analytical methods, articles and manuals may be used as supplements to these Standard Operating Procedures. 7.2机构独立的单元或区域应当有所执行操作的现 行版SOP。出版的文献、分析方法和手册可以作 为对SOP的补充材料。
离心机操作规程 中英文
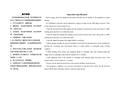
操作规程开机前检查设备有无杂物,有无阻碍运行的状况。
严禁带电时打开控制箱或插拔电缆插件!1、打开总电源开关,接通电源。
2、辅机起动,待达到平稳转速,如无异常声响,可起动主机。
3、主机起动,待达到平稳转速,如无异常声响,可起动供液泵。
4、供液泵起动,向离心机供液。
5、在正常运转时,辅机和主机可分别按加速、减速按钮进行速度调节,以达到理想的使用状态。
6、停机时先停止向离心机供液,起动清洗泵向机内供清水清洗内腔3-5分钟。
7、清洗泵停止向内腔供水,向转鼓外喷水清洗转鼓1-2分钟。
8、停止时先停主机、再停辅机。
9、在紧急状态下可按急停按钮使系统停机,但是由于滚筒自身的惯性,滚筒会带动电机转动一段时间。
Operation SpecificationBefore staring, check the equipment and ensure that there are no sundries or dirt impeded its normal running.It is forbidden to open the control cabinet/box or plug in or plug out the cable plugs on power.1 Turn on the main power switch, and power on.2 Start the electrical motor alter making sure the auxiliary electrical motor stats and reaches to stable rotating speed and there is no abnormal sound.3 Start the liquid feed pump after making sure the main electrical motor starts and reaches to stable rotating speed and there is no abnormal sound.4 Start the liquid feed pump, then supply liquid to centrifuge.5 When running normally, the speed of auxiliary electrical motor and main motor can be regulated by pressing the "accelerate and "deceleration button to realize perfect or reasonable using working condition.6 When shutting down, firstly stop supplying liquid to centrifuge, then start cleaning pump and supply water to centrifuge I and clean the chamber for 3-5 minutes7 Stop supplying water to the chamber of centrifuge with cleaning pump, and spray water to the outside surface of rotary drum for 1-2 minute.8 Firstly stop the main electrical motor. then stop the auxiliary electrical motor.9 In emergency conditions. you can press stop button to shut down the system, but the electrical motor will till rotate with drum, which is caused by drum inertia.。
操作规程英文版

机床操作规程Operating Procedure of Machine工作前穿戴好工作服及防护用品,扎好袖口,不准穿长衫、围围巾和头巾等丝带状物品,以及穿高跟鞋。
The worker shall wear the uniform, dress the protective equipments and fasten the cuff before work. Everyone is forbidden to wear gown, scarf, headband and high heels.女工应戴好工作帽。
高速切削或切削铸铁、铝、铜工件时,必须戴防护眼镜。
The workwoman shall wear helmet. The worker must wear protective glasses when the machine is fly cutting or cutting the iron, aluminum and copper materials接触旋转开关及旋转部位时,不得带手套作业,在夹装工件过程中允许带手套作业。
The worker does not allow wearing gloves when you touch the rotary switch or portions.1.车床技术安全操作规程1. Safety Operating Procedure of Lathe(1) 工作前须检查机床运转情况,检查工件及刀具是否夹紧,清除床面杂物。
(1) Before working, the lathe operator (lathe man) shall confirm the condition of lathe. The operator should check whether the work piece and cutter is tightened or not. The operator need clean the sundries from the platform before working.(2) 卡盘、花盘必须有保险装置,加工畸形和偏心零件时,要加平衡配重,先低俗运转,然后变为所要的速度。
设备确认操作规程(英文)【精选文档】

PURPOSE:To provide a formal methodology to be followed during qualification of equipment.SCOPE:Applicable to qualification of new equipment, re-qualification of equipment, which has undergone major modification, relocation of equipment and Periodic Qualification as per schedule in Pharma manufacturing department。
RESPONSIBILITY:Production, Engineering, Safety, Quality Control and Quality Assurance staff. DEFINITION:Qualification: Documented verification that the environment and equipment are appropriate for the designated function。
User Requirement Specification (URS):A Requirement specification that describes what the equipment or system is suppose to do, thus containing at least set of criteria or conditions that have to be met。
Functional Design Specification (FDS): Functional design specification is a document that specifies in a complete, precise, variable manner, the requirement design, behaviour or other characteristics of a system or component and often the procedures for determining whether these provisions have been satisfied。
操作技术规程 英文

操作技术规程英文Standard Operating Procedure for Operation Technique1. IntroductionThe operation technique is a crucial part of anyindustrial process. It involves the use of specific methods and procedures to ensure the smooth and efficient runningof the equipment and machinery. This standard operating procedure (SOP) outlines the steps and guidelines for the correct operation technique to be followed by the operators.2. PurposeThe purpose of this SOP is to ensure that all operators are familiar with and adhere to the correct operation technique for the equipment and machinery. By following the standard procedure, the risks of accidents and equipment damage can be minimized, and the overall efficiency of the operation can be improved.3. ScopeThis SOP applies to all operators and technicians responsible for the operation of equipment and machinery inthe industrial setting. It covers the general operation technique as well as specific guidelines for individual equipment.4. Responsibilities- Operators are responsible for familiarizing themselves with the correct operation technique outlined in this SOP and adhering to it at all times.- Supervisors are responsible for ensuring that operators are trained in the correct operation technique and for monitoring compliance with the SOP.5. Procedure5.1 Pre-Operation Checks- Before starting the equipment, operators must conduct a thorough inspection to ensure that all components are in good working condition.- Check for any leaks, unusual noises, or signs of wear and tear.- Verify that all safety guards and devices are in place and functioning properly.5.2 Start-Up Procedure- Follow the manufacturer's guidelines for starting up the equipment.- Gradually increase the speed or pressure as per the standard operating parameters.- Monitor the equipment closely for any abnormalities during the start-up process.5.3 During Operation- Operate the equipment according to the recommended settings and parameters.- Keep a close eye on the performance indicators and be alert for any deviations from the norm.- Report any issues or abnormalities to the supervisor immediately.5.4 Shut-Down Procedure- Follow the manufacturer's guidelines for shutting down the equipment.- Allow the equipment to cool down, if necessary, before performing any maintenance tasks.- Ensure that all safety protocols are followed during the shut-down process.6. Safety Precautions- Operators must wear the appropriate personalprotective equipment (PPE) at all times during the operation.- Maintain a clean and organized work area to minimize the risk of tripping or falling hazards.- Follow all safety protocols and guidelines as outlined in the company's safety manual.7. Record-Keeping- Operators must maintain accurate records of the operation and any maintenance tasks performed.- Any deviations from the standard operation technique should be documented and reported to the supervisor.8. Training and Certification- All operators must undergo training in the correct operation technique for the equipment they are responsible for.- Operators must be certified to operate specific equipment and machinery as per the company's standards.中文翻译:操作技术规程1.简介操作技术是任何工业过程中至关重要的一部分。
设备确认操作规程(英文)

PURPOSE:To provide a formal methodology to be followed during qualification of equipment.SCOPE:Applicable to qualification of new equipment, re-qualification of equipment, which has undergone major modification, relocation of equipment and Periodic Qualification as per schedule in Pharma manufacturing department.RESPONSIBILITY:Production, Engineering, Safety, Quality Control and Quality Assurance staff. DEFINITION:Qualification: Documented verification that the environment and equipment are appropriate for the designated function.User Requirement Specification (URS): A Requirement specification that describes what the equipment or system is suppose to do, thus containing at least set of criteriaor conditions that have to be met.Functional Design Specification (FDS): Functional design specification is a document that specifies in a complete, precise, variable manner, the requirement design, behaviour or other characteristics of a system or component and often the procedures for determining whether these provisions have been satisfied.Specification that is offered by manufacturing based on URS and are agreed mutually. Design Qualification (DQ): Formal and systematic verification that the requirements defined in the specification phase are completely covered by the succeeding specification or implementation phase.Factory Acceptance Test (FAT): Testing conducted at the suppliers factory to determine whether or not a system specifies it‟s acceptance criteria and to enable the user to determine whether or not to accept the system.Installation Qualification (IQ): Documented verification that a system is installed according to written and pre-approved specifications.Site Acceptance Test (SAT): An acceptance test at the users site, usually involve the supplier.Operation Qualification (OQ): Documented verification that a system operates according to written and pre-approved specification throughout all specified operating ranges.PLC Validation: Documented verification that PLC Hardware are as per original drawing, Digital and Analog Input and Output are connected as per PLC Architecture and functioning according to written and pre-approved specification throughout all specified operating ranges.Performance Qualification (PQ): Documented verification that a system is capable of performing or controlling the activities of the processes, it is required to perform or control, according to written and pre-approved specifications, while operating in its specified operating environment.User (s): The person, or persons, who operate or interact directly with the system. Supplier: Any organisation or individual contacted directly by the user to supply a product or service.Critical Equipment: The machine within a system where the malfunctioning or failure of equipment will have direct impact on product quality. Where product is in direct contact with machine body parts.Non-critical Equipment: The machine within a system where the malfunctioning or failure of equipment will not have direct impact on product quality. Where product is not in direct contact with machine body parts.1.0 HEALTH, SAFETY AND ENVIRONMENT: (对验证实施人员的HES要求)1.1 Personnel involved in qualification / re-qualification / periodic qualificationshould use appropriate personal protective equipment.1.2 Do not touch the moving parts.1.3 Electrical isolation should be done before any electric control panelverification.1.4 Read the safety instructions specified in the operation Manual of themachine to be qualified.2.0 PROCEDURE:2.1 Equipment qualification should be based on the following documents2.1.1 User Requirement Specification (URS)2.1.2 Functional Design Specification (FDS)2.1.3 Design Qualification (DQ)2.1.4 Factory Acceptance Test (FAT)2.1.5 Checklist on Receipt2.1.6 Installation Qualification (IQ)2.1.7 Operation Qualification (OQ)2.1.8 PLC Validation ( If applicable)2.1.9 Provisional Handover Certificate2.1.10 Performance Qualification (PQ)2.1.11 Handover CertificateThe flow of the equipment qualification is as followsURS → FDS → DQ → FAT → IQ → OQ → PLC Validation (if applicable)SAT→ PQ2.1.1 User Requirement Specification (URS):2.1.1.1 URS protocol should be approved by the project team(Users) members and Quality Assurance with Name, Signand Date.2.1.1.2 Following points should be considered during thedevelopment of URS.IntroductionOver viewOperation requirementsConstraintsLife cycle Glossary References Approval2.1.1.3 Each URS protocol should be allotted with a protocol no. inthe format specified below “URS/P”Where,“URS” stands for User requirement specification.“P” stands for equipment / instrument / balance / area abbreviated code.2.1.1.4 The protocol should also identify with a Version No. Wherethe version no. changes with every change in the URS.2.1.1.5 The URS protocol header should consist of the following detailsas mentioned below:Title of the URSProtocol No. Version No. DateCipla Patalganga UnitPage No.A specimen of the header is given below:2.1.2 Functional Design Specification (FDS):2.1.2.1The FDS should be the manufacturer interpretation of URS. FDS should include basic functioning of the equipment with focus on control and critical components specifications and functions.2.1.2.2 The FDS should be in the form of separate documentand should include equipment specification, P&IDdiagrams.2.1.2.3 The FDS protocol / report should be mutually approvedby the user and supplier with sufficient technical detailsbased on the techno commercial offer.2.1.2.4 The supplier is finally selected and CER is raised.2.1.2.5 Any changes made after finalisation of DQ should undergo change control procedure as per SOP CQA 06.2.1.3 Design Qualification (DQ):2.1.3.1 Design qualification should be based on the discussionbetween the supplier and the user with reference toURS / FDS.2.1.3.2 Following points should be considered during thedevelopment of design qualification.PurposeScopeResponsibilityProject requirementCritical variables to be metProcess/ Product parameters e.g. Capacity etc.cGMP considerationse.g. MOC of individual parts, finish of contact partsCritical parameters e.g. Instrumentation, limits,SafetyLocation suitabilityReferencesDocuments to be attached.Any changes made against the formally agreedparameters (Deviation if any).Justification for acceptance (if any deviation)Review (Inclusive of follow up action, if any)RecommendationSigning off2.1.3.3 Any change in DQ should be through a change controlprocedure as per SOP CQA-06 and should bedocumented.2.1.4 Factory Acceptance Test (FAT):2.4.1 The FAT should be conducted at the supplier‟s premisesunder the users supervision unless agreed upon.2.4.2 The FAT protocol / report should be prepared by the supplieras per Manufacturers format and should be submitted forapproval of user.2.4.3 The equipment should be shipped to the site only afterapproval by the user.2.4.4 The FAT protocol / report should include details of the URSand FDS.2.4.5 Any modification, changes needs during the FAT should bedocumented and intimated to the user and carried out withmutual consent.2.1.5 Checklist on Receipt:2.1.5.1 All critical parts of equipment should be checked forfinish, any damages on receipt for availability as perpacking list and order details.2.1.6 Installation Qualification (IQ):2.1.6.1 All aspects such as utility connections, location suitability,material of construction of critical parts, installation of allmonitoring, controlling, instruments and gauges includingtheir calibration and certification by supplier should bechecked and verified.2.1.6.2 During the installation qualification Area Lux level, Floordrains, piping connections , machine alignment, levelling,P& ID Diagram, Schematic, circuit diagram, tagging,wiring pheruling, pneumatic connections consideredduring design qualification are checked and verified.2.1.7 Operation Qualification (OQ):2.1.7.1 During Operation qualification the working of themonitoring and controlling instruments, gauges andsystems like PLC, switches, gauges, motors, pumps etc.are checked and certified.2.1.7.2 The parameters considered during design qualificationare checked and certified.2.1.8 PLC Validation2.1.8.1 PLC validation should be carried out by competentexternal approved agency.2.1.8.2 PLC validation should be carried out during SAT orsubsequently within three months based on level ofchecks carried out during SAT. Validation should be doneaccording to pre-approved protocol and report. Allreference instruments being used for validation should becertified by approved agencies like …IDEMI‟ and …ERTL.2.1.8.3 Brief description about equipment operating function andits location should be mentioned in the report. All rawdata should be handwritten at site during actual validation.2.1.8.4 The details of PLC and HMI hardware are checked as percircuit diagram and type of PLC, HMI, its software Versionno. details, details of the available digital/ analogue inputsand outputs. Installed switchgear details should bementioned i.e. SFU, MCB, relays, contactors, pushbuttons, switch, power supply, Surge protection etc.2.1.8.5 Equipment interlocks, alarms and operation logic shouldbe checked. Details of the PLC Battery conditions shouldbe checked and it‟s life will be verified appropriately.2.1.8.6 All PLC validation reports should be handed over by thevalidation agency to the engineering department forverification within a week after physical verification of thesystem. Engineering, user department and qualityassurance department will verify submitted reports2.1.8.7 Any deviation observed should be highlighted and broughtup to the notice of Engineering/ User/QA dept.2.1.8.8 No changes should be made in the software or hardwareduring the course of validation.2.1.9 Site acceptance test (SAT) and Provisional HandoverCertificate:2.1.9.1 SAT should be carried out in conjugation with thesupplier and may include checks of critical components,controls based on the detail Fat, IQ and OQ have beensuccessfully performed.2.1.9.2 After the equipment goes through the installation andoperational qualification procedure, it should be reviewedat each stage by a team of Engineering, Production,Quality Assurance, Quality Control, Safety and Unit Head.2.1.9.3 In few cases the equipment may have to go through aprocess cycle development and stabilisation phase beforesubject to validation trials.2.1.9.4 If any deviation or non conformance to the acceptancecriteria should be recorded and informed to concernedsupplier. A decision should be taken by user team andsupplier to reject or to proceed for PQ.2.1.9.5 If SAT is found to be satisfactory, equipment should beprovisionally handed over to the concerned departmentfor Performance Qualification.2.1.10 Performance Qualification (PQ):2.1.10.1 During the Performance Qualification the working of thesystem as a whole is checked with respect to out put, quality,quantity and any specific requirements as per designqualification.2.1.10.2 Critical equipment should undergo extensive validationstudies to ensure consistent performance depending onapproved validation protocol.2.1.11 Handover Certificate:After successful Performance Qualification, based on reviewby the team of Engineering, Production, Quality Assurance,Quality Control, Safety and Unit Head. The equipment ishanded over to the concerned department for regular use. 2.2 Equipment Qualification and Requalification protocol consist of thefollowing sections.Covering pageTable of contents.GlossaryPre approvalDesign QualificationCheck list on receiptInstallation QualificationOperation QualificationProvisional Handover CertificatePerformance QualificationHand over Certificate2.3 REQUALIFICATION / PERIODIC QUALIFICATION2.3.1 All Major equipment should be requalified after any majorchange in the equipment or modification.2.3.2 If there are any major changes in critical parameters of equipment(e.g. RPM of blender, speed of agitator etc.) which has directimpact on the quality, then the revalidation of the process should be done.2.3.3 The requalification need not be performed for any minor changesin the equipment, For example, few blades of multimill arereplaced.NOTE: Minor changes should be recorded in the Machine History Card.2.3.4 If any fixed equipment is shifted from one area to another area.Critical parameters should be checked during requalification.Transfer note should be made for the equipment. It should bekept along with the requalification record. For relocation ofportable equipment requalification is not required.2.3.5 During the transfer of equipment from one unit to another unitrequalification as IO, OQ should be conducted based on criticalparameters. A such copy of original qualification should beforwarded for reference.2.3.6 While transferring the equipment to other area / units, reviewshould be done for any specific requirements of conditions2.3.7 For equipment having no changes requalification time periodshould be decided based on performance of annual review of theequipment. The review of the equipment should be recorded inthe Equipment Review Report (Annexure MT95/A1) Therequalification time period should not exceed five years.2.3.8 Schedule for requalification of the major equipment shouldavailable at unit level and should be recorded in schedule forrequalification Annexure MT95/A2.2.3.9 Schedule for PLC revalidation of the major equipment should beavailable at unit level and should be recorded in AnnexureMT95/A3.2.3.10 Any changes in schedule of equipment qualification should becarried out through deviation.Requalification / Periodic Qualification protocol consist of the following sections:Covering pageTable of contents.GlossaryPre approvalOver viewPre requisitePreventive Maintenance verificationMajor breakdown verificationSystem descriptionPhysical verificationCalibration verification of critical componentsCalibration verification of calibration standards usedSafety features verificationControl panel verificationInterlocks/controls verificationPerformance evaluation Documentation verification Post approvalHand over certificate2.4 Protocol Approval:2.4.1 All protocols are approved by Quality Assurance and Unit Headprior to their implementation i.e. after they are compiled by a team of Production, Engineering, Quality Control and Safety.2.4.2 Each protocol should be allotted with a protocol number in theformat specified bellow“QUALI/X” Where,“QUALI” stands for qualification“X” stands for equipment / instrument / balance / area abbreviated code2.4.3 The protocol should also be identified with a Version No., wherethe version no. changes with every change in the Qualification, Requalification and Periodic Qualification of equipment.2.4.4The Qualification, Requalification and Periodic Qualificationprotocol header should consist of the following details as mentioned below Title of the protocol Protocol No. Version No. Department Area Page No.A specimen of the header is given below:2.4.5 Frequency for Periodic QualificationFor Critical Equipment: Once in 3 years of its previousqualification (Initial qualification / requalification)For Non Critical Equipment: Once in 5 years of its previousqualification (Initial qualification / requalification)Note: The period of periodic qualification should be determinedbased on review of history of preventive maintenance, breakdown,calibration data and criticality of process.3.0 ABBREVIATIONS:URS User Requirement SpecificationFDS Functional Design SpecificationDQ Design QualificationFAT Factory Acceptance TestIQ Installation QualificationSAT Site Acceptance TestOQ Operation QualificationPQ Performance QualificationNo. NumberP&ID Piping and Instrumentation DiagramCER Capital Expenditure RequisitionCGMP current Goods Manufacturing PracticesPLC Programmable Logic Controller.MOC Material of Construction材质i.e. That ise.g. For exampleIDEMI Institute for Design of Electrical Measuring InstrumentsERTL Electronics Regional Testing LaboratoryPLC Programmable Logic ControllerHMI Human Machine InterfaceSFU Switch Fuse UnitMCB Miniature Circuit Breaker4.0 REFERENCES:CQA-06 Change Control5.0 ANNEXURES:MT95/A1 Equipment Review Report (MT95/F1)MT95/A2 Schedule for Requalification/Periodic (MT95/F2)QualificationMT95/A3 Schedule for PLC Revalidation /Periodic (MT95/F3)Validation。
设备管理英文术语大全

概率(几率)probability·方差 variance·分散维修 decentralized maintenance·动态试验 dynamic test·动力设备设施管理 power facilities management·除尘、防护设备管理 duct-proof and protective equipment managemen t·抽样调查 sampling investigation·备件国产化管理 domestic production management of imported spare parts ·标准偏差 standard deviation·安装预算 budget of installation·包机制 machine contracting system·班前检查与润滑制度 regulation of check and lubrication before on shift ·[设备]交接班制度 shift relief system·《设备管理条例》(《条例》)《Equipment Management Regulation》·[设备]修理 repair·[设备]维修 maintenance (and repair)·重点调查 key-point investigation·重点设备管理 management of key-point equipment·重点设备 key-point equipment·责任事故 liability accident·指数分布 exponential distribution·直方图 histogram·预付与托收承付 prepayment and collection·预防性试验 prophylactic test·预防为主 prevention first·正交设计法(正交试验法) orthogonal design·正态分布 normal distribution·运输车辆管理制度 transportation vehicle management system·质量“三包” three guarantees of quality·质量事故 accident due to quality·压力容器管理制度 management regulation of pressure vessel·无故障运行时间 mean time to failure·威布尔分布 Weibull distribution·闲置设备管理制度 idle equipment management·闲置设备 idle plant·统计分析 statistical analysis·维修性 maintainability·维修信息管理 maintenance information management·维护与计划检修相结合 combination of service and planned maintenance·随机事件 random event·数控设备管理 numerical control (NC) equipment management·三级保养制 three-level service system·数学期望 mathematical expectation·数学模型 mathematical model·数理统计 mathematical statistics·生产技术装备 technical facilities in production·生产设备 production equipment·寿命周期费用 life cycle cost (LCC)·润滑油库管理制度 mangement regulation of lubricant warehouse·商检(商品检验) commodity inspection·设计、制造与使用相结合 combination of design, manufacturing and operation·设备调研 investigation on plant·设备的可靠性与可靠度 reliability reliability theory·设备的节能性 energy saving property of plant·设备的检查评比 facility inspection and appraise through comparison for plant·设备点检制度 plant check system·设备的成套性 complete set of plant·设备的安全性 safety of plant·设备的生产率 productivity of plant设备的耐用性 durability of plant·设备的灵活性 flexibility of plant·设备状态监测与诊断技术管理 equipment condition monitoring and diagnostic technology manage·设备状态管理制度 equipment condition management systen·设备综合管理 total plant management·设备资产动态管理制度 dynamic management system of plant assets·设备租赁 plant leasing·设备修前准备制度 preparation system before equipment repair·设备修理工时定额 man-hours quota for equipment repair·设备修理费用定额 expense quota for equipment repair·设备修理材料定额 material quota for equipment repair·设备修理质量验收制度 acceptance regulation of equipment repair quality ·设备型号 equipment model·设备型式 type of equipment·设备经济寿命 economical life of equipment·设备经营管理制度 operation and business management system·设备技术档案 technical document of plant·设备技术状况 technical conditions of equipment·设备技术状态管理 technical condition management of plant·设备技术资料管理制度 management system for technical document and plant ·设备技术性能 technical properties of plant·设备技术寿命 technical life of equipment·设备检修专业化协作 specialized cooperation of plant maintenance·设备检修计划管理制度 planning and management regulation of plant maintenance·设备检修计划 plant maintenance plan·设备检修规程 plant maintenance specification·设备检修质量 plant maintenance quality·设备基础设计与施工 design and construction of equipment foundation ·设备合同管理 management of equipment order contract·设备规划可行性分析 feasibility studies of plant project设备规划 investment plan of plant·设备功能(效能) performance of plant·设备工作能力 operational capability of plant·设备管理考核制度 examination and check systems of plant management ·设备管理经济责任制度 economic responsibility regulation of plant management·设备管理岗位标准 post standard of plant management·设备管理制度 plant management systems·设备管理停歇时间定额(停歇天数) downtime quota for equipment repair ·设备管理现代化 plant engineering modernization·设备管理 plant management, plant enginerring·设备固定资产管理制度 fixed plant assets management systems·设备故障 equipment failure·设备更新管理制度 plant renewal management·设备更新 plant renewal·设备更换 plant replacement·设备岗位责任 post responsibility of plant management·设备改造管理制度 equipment modification management system·设备改造 plant reconstruction, plant modernization·设备分级管理 classified management of plant·设备定人定机、凭证操作规定 operation regulation with fixed qualified operator and fixed eq·设备操作的“五项纪律” “five disciplines”of plant operation·设备操作规程 operation specification of equipment·设备备品配件管理制度 management regulation of equipment spare parts ·设备备件库房管理制度 management regulation of equipment spare parts inventory·设备报价 to quote plant price·设备报废 discard of plant·设备安装管理 equipment installation management·设备安装 equipment installation·设备巡回检查制度 tours system to inspect plant·设备询价 to enquire plant price设备选型 plant model selection·设备验收交接制度 acceptance check and reception systems of plant ·设备统计报表制度 statistic-reporting system of plant·设备维修技术资料 technical document and date for plant maintenance ·设备维修技术管理制度 management regulation of plant maintenance technology·设备维修定额 equipment maintenance quota·设备维护规程 equipment service specification·设备台帐 unit account of plant·设备完好标准 equipment perfectness norm·设备完好 plant in good condition·设备索赔 claims for equipment·设备使用规程 specifications of usage·设备使用初期信息反馈管理 information feedback management in initial operation period of pl·设备使用与维护管理制度 management regulation for operation and service of equipment·设备全过程管理 life-cycle management of plant·设备寿命 life of equipment·设备润滑管理制度 lubrication management regulation of plant·设备润滑“五定” “five fixation” of lubrication·设备事故管理制度 accident management regulation of plant·设备事故“三不放过” three do not let pass of plant accident·设备事故 plant accident·设备区域维修负责制 region responsibility system of plant maintenance ·设备前期管理和后期管理 fore period and later period management of plant ·设备前期管理规定 regulation of fore period management of plant·设备磨损补偿 wear compensation for plant·设备老化 plant ageing·算术平均值(均值) arithmetic mean·强制保养制 coercionary service system· 投资效果系数 effect coefficient of investment· 设备经济管理制度 economic management system of plant设备管理评优活动 excellence selection activity in plant management· 排列图(帕累托图) Pareto chart·负荷试验 load test·故障停机时间 breakdown time·工艺适应性 technological adaptability·工程设备监理 supervision of engineering facilities·工序控制点设备管理 management of proccess-control-point equipment·合同变更与解除 contract change and cancellation·混合维修 combined maintenance·回归分析 regression analysis·检查间隔期 interval between inspections·检修社会化 socialization of maintenance·集中维修 centralized maintenance·技术先进性 technical advancement·技术管理与经济管理相结合 combination of technical management and economic management·计算机辅助设备管理 computer-aided plant management·计划预修制度(ЛЛP) planned preventive maintenance system·进口设备离岸价 FOB of imported equipment·进口设备管理 imported equipment management·进口设备到岸价 CIF of imported equipment·精、大、稀设备 precise,large scale,rare plant·精、大、稀设备管理 management of precise,large scale,rare equipment ·精、大、稀、关键设备的“五定” “five fixed” of precise,largescale,rare,critical equipme·经济性 economy·静态试验 static test·开箱检查 open-case inspection·平均偏差 average deviation·平均等待时间 mean waiting time,MWT·修理周期 repair cycle·修理周期结构 structure of repair cycle修理、改造与更新相结合 combination of repair, modernization and renewal ·修理复杂系数 complexity coefficient of repair·修理间隔期 time between repairs·租赁设备管理制度 leased equipment management system·资金的时间价值 time value of fund·自然事故 natural accident·自制设备 self-made equipment·自制设备管理制度 management system for selfmade equipment·自制备件管理制度 self-made spare parts management system·专业管理与群众管理相结合 combination of professional management and mass management·转让设备(设备调剂) transfer of facility·典型调查 typical investigation·地区(部门)修理中心 areal (departmental) repair center·废油回收率 recovery ratio of used oil·动力设备完好率 perfectness ratio of power plant·定期保养完成率 fulfillment ratio of periodic service·大修理平均停歇天数 mean downtime(days) due to overhaul·重点设备完好率 perfectness ratio of key-point equipments·一次交验合格率 qualification ratio under first acceptance check·在用设备可利用率 availability of plant in use·已安装设备利用率 utilization ratio of installed equipments·万元固定资产年创利润率 annual profit ratio per 10000 yuan fixed assets ·万元产值占用维修费用 maintenance expense for 1000 yuan production value ·实有设备安装率 installation ratio of owned equipments·设备综合利用率 comprehensive utilization ratio of plant·设备资产增值率 added value rate of plant assets·设备资产投资回收期 capital investment recovery period of plant·设备新度 newness degree of plant·设备净资产创利润率 profit ratio vs net book value of plant·设备计划台时利用率 utilization ratio of planned time of plant设备构成比 constitution ratio of plant·设备负荷率 load rate of plant·设备返修率 back repair rate·设备制度台时利用率 utilization ratio of institutional time of plant ·设备闲置率 idelness ratio of plant·设备投资回收报率 plant capital investment recovery ratio·设备投资产出比 capital investment recovery period of plant·设备完好率 perfectness ratio of plant·设备日常保养完成率 plant daily service fulfillment ratio·设备事故频率 incident frequency·设备利用率 utilization ratio·事故[故障]停机率 down time ratio to accident (failure)·清洗换油计划完成率 fulfillment ratio of cleaning and oil change plan ·每个修理复杂系数平均大修理成本 mean repair cost per complexity coefficient of repair·每个复杂系数占用维修费用 maintenance expense per repair complexity coefficient·每万元固定资产创工业增加值率 industrial increase value ratio per 10000 yuan fixed assets·故障强度 failure intensity·故障频率 failure frequency·关键设备完好率 perfectness ratio of critical equipments·精大稀设备完好率 perfectness raito of precise,large scale and rare equipments·可利用率(有效利用率) availability·平均停机时间 mean down time,MDT·平均故障间隔期,平均无故障工作时间 mean time between failture·修理计划完成率 fulfillment ratio of repair plan废润滑油再生(废油再生) regeneration of waste lubricating oil·防泄漏管理 leak prevention management·二级保养 second level service·定期精度调整 periodic accuracy adjustment·定人定机制度 system of fixed machine and operator·额定载荷 rated load·超负荷试运行 commissioning under overload·初步试运行 preliminary commissioning·操作工人的“四会” four basic skills for operator·参数故障 parametric failure·保养计划完成率 fulfilment ratio of service plan·保养规程 service specification·保养“十字”作业法“ten words” method for service·保养 service·安全性故障 safety failure·安全规程 safety procedure·[设备性能]劣化 degradation (of equipment performance)·PM小组 PM group·隐蔽故障 hidden failure·有效性 availability·有效度 avaliability·有效寿命 effective life·制度时间 institutional time·一级保养 first level service·原发故障 primary failure·原始记录 original record·正常负荷 normal load·正常超载 normal overload·治漏“八字”法“eight words” method for leakage control·运行时间 operating time仪表“三率” “three rate”of meter·早(初)期故障期 early failure period·永久性故障(持续性故障) permanent failure·验收试运行 final commissioning·无泄露[区]标准 leakless(area) standard·突发性(偶发)故障 random failure·维护费 service cost·危险性故障 dangerous failure·误操作故障 failure by misoperation·完好设备 perfect facility·生产维修 productive maintenance(PM)·润滑工作岗位责任制 post responsibility of lubrication work·润滑管理制度 lubrication management system·润滑“五定” “five fixation” of lubrication·润滑“三过滤” three-step filtration of lubricating oil·润滑站 lubricating station·润滑图表 lubricating diagram·试车 commissioning·日常保养费 daily service expenses·日常保养(日保) daily service·日历时间利用率 utilzation ratio of calender time·设备的可靠性和可靠度 reliability·设备的区域维护 regional service of equipment·设备技术状态 technical conditions of equipment·设备故障率曲线(浴盆曲线) failure rate curve of equipment,tub curve ·设备操作合格证 operation licence·设备“5S”活动“5S” activity of equipment·设备隐患 hidden trouble of equipment·设备运行记录 operation record of equipment·设备维护的“四项要求” four requirements for plant service设备维护标准 service standard of equipment·设备维护 equipment service·设备使用的“三好” three well doing for use of facility·设备使用过程 process of machine operation·设备三级保养 three-level service system for equipment·设备日常点检 routine inspection·设备清洗(清扫) cleaning of plant·设备漏油标准 oil leakage standard·设备利用系数 utilization factor of equipment·人身保护装置personal safety device·强制保养 mandatory service·潜在故障 latent filure·偶发故障期 accidental failure period·磨损性故障 wearout failure·例行保养(例保) routine service·密封点 sealed point·劣化趋向管理 degradation trend control· 随机故障 random failure· 设备的定期维护 periodic service of equipment·负荷试运行 commissoning under load·故障类型 failure type·故障率(失效率) failure rate·故障率基本类型 basic forms of failure rate·故障模式 failure mode·故障模型 failure model·故障弱化 failure weakening·故障树分析 FTA,fault tree analysis·故障物理学 physics of failure·故障停机率 breakdown rate·故障征兆 failure symptom·故障安全 safety protection against failure·故障分析方法 failure analysis method·故障机理 failure mechanism·功能故障 functional failure·关键设备使用维护“四定” four stipulations for operation a nd maintenance of critical equip·耗损(劣化)故障期 exhaustion failure period·红旗设备 red-flag equipment·基本故障 basic failure·间断性故障 intermittent failure·继发故障 secondary failure·计划时间利用率 utilization ratio of planned time·渐衰失效性故障 local and gradual failure·渐发性(磨损)故障 gradual(wear-out) failure·精、大、稀、关键设备的使用维护 operation and service of precise,large scale,rare and criti·净开动时间 net operating time·可使用时间 up time·可用性(可利用率) availability·可靠性为中心的维修 reliability centered maintenance,RCM·平均故障间隔期(平均无故障工作时间) mean time between failures,MTBF ·破坏性故障 catastrophic failure·起重机安全保护 safety protection of crane·最大允许寿命(宣称寿命) maximum permitted life (declared life)·自显故障 self-displayed failure·综合试运行 total commissioning·专群结合 combination of specialists and masses·调整 adjustment·跟踪检查 trail checkout·法定检查 lawful inspection·动特性试验 dynamic performance test·动态精度 dynamic accuracy动态检验 dynamic test·定期点检 periodic fixed point inspection·定期检查 periodic inspection·定期参数检查 periodic parameter examination·定期润滑检查 periodic lubrication check·“三位一体”点检制“three in one” fixed point inspetion system·主观(五官)判断故障 subjective(sensible) failure deciding·一般目视检查 general visual inspection·影响设备效率的六大损失 six major losses affecting running efficiency ·正常检查 normal inspection·巡回检查 patrol inspection·巡回检测 patrol test·无损检查 non-destructive test·停机时间 down time·微观组织检查 examination of microscopic structure·损坏 break down·缺陷 defect·失效(故障) failure·容许故障率 allowable failure rate·日常检查 daily inspection·日常润滑检查 daily lubrication check·设备点检 fixed point inspection of equipment·设备检查 facilities inspection·设备监测 equipment monitoring·设备故障频率 equipment failure frequency·设备故障管理效果评价 result evaluation of plant failure management ·设备诊断技术 equipment diagnostic technique·设备诊断 equipment diagnosis·酸洗检查 inspection with pickling·敲打检查 hammering test磨损检查 wearing inspection·内表面检查 inner surface inspection·故障强度率 failure intensity rate·故障趋于零的“四个阶段” “four steps” to zero failure·故障危害程度 harm extent of failure·故障为零的五项措施 five measures to zero failure·故障(停机)损失 breakdown loss·故障管理程序 program of railure management·故障管理信息 information of failure management·故障修理 troubleshooting·功能检查(功能测试)function inspection,function test·宏观组织检查 examination of macroscopic structure·检定周期 cycle of verification·技术维护 technical service·季节性技术维护 seasonal technical service·计划保全管理 planned maintenance management·解体检查 inspection under disassembled condition·精度检查 accuracy inspection·静态精度 static accurary·可靠性试验 reliability test·可靠性分析 reliability analysis·平均寿命时间(MTTF) mean time to failure·状态监测 condition monitoring·状态检查 condition inspection·点检的主要环节 main items of fixed point inspection改善修理 corrective maintenance·返修率 back repair rate·分级修理 stepped(sizing) repair·分散修理制 decentralized maintenance system·废次品及返修损失 waste and ungraded product and back repair loss ·非预定维修时间 unscheduled maintenance time·定期修理作业 periodic repair task·定期维修法 periodic repair·定位精度 location accuracy·传动精度 transmission accuracy·大修计划修改 revision of overhaul plan·大修计划考核 assesment of overhaul plan·大修计划编制 overhaul planning·大修计划依据 basis of overhaul plan·大修计划完成率 fulfilment rate of overhaul plan·大修计划实施 implementation of overhaul plan·大修费用 overhaul cost·大修成本构成 overhaul cost·大修成本分析 overhaul cost analysis·大修成本完成率 fulfilment rate of overhaul cost·大修保修 overhaul guarantee·大修周期 interval between overhauls, overhaul cycle·大修质量保证体系 guarantee system of overhaul quality·大修理质量评定 overhaul quality evaluation·大修理质量控制 overhaul quality control·大修 overhaul,capital repair·部件修理法 assembly repair·部分修理法 partial repair·补偿法 compensation method·备件生产计划 production program of spqre parts备份或冗余系统 stand-by or redundancy system·标准尺寸修理法 standard-size repair method·八步法“eight steps”method·重复定位精度 repeat location accuracy·中修 middle repair·有可维修备份的系统 system with maintainable standby parts·远距离维修 remote maintenance·预防维修 preventive maintenance·预定维修时间 scheduled maintenance time·预知维修(状态监测维修) predictive maintenance·质量体系 quality system·质量 quality·逾期维修 deferred maintenance·网络计划 network planning·维修技术培训 maintenance skill training·维修间隔(正常运行时间) maintenance interval, uptime·维修活动的经济分析 economic analysis of maintenance activities ·维修工人 maintenance worker·维修防护 maintenance protection·维修车间 maintenance shop·维修预防 maintenance prevention·维修周期 maintenance cycle·维修时间 maintenance time·同步修理法 synchronous repair·停修时间 repair downtime·项修(项目修理) item repair·外委修理 repair on commission·全员参加的生产维修制(TPM) total production maintenance system ·受控维修 controlled maintenance·寿命周期维修 life cycle maintenance热修 hot repair·设备修理计划 repair schedule of equipment·设备修理验收 acceptance check for equipment repair·设备季度修理计划 quarterly repair schedule of equipment·设备技术考核 technical check of equipment·设备大修计划 equipment overhaul plan·设备月度修理计划 monthly repair schedule of equipment·设备维修计划 equipment maintenance plan·设备维修三要素 three essential factors of equipment maintenance ·设备项修计划 item repair plan of equipment·设备年度修理计划 annual repair schedule of equipment·事后修理 breakdown maintenance·抢修 first-aid repair· 大修机床精度 accuracy of machine tool after overhaul·滚动计划 rolling (circulation) plan·管理信息系统维修 MIS maintenance·工程能力指数 process capacity index·工作精度 working accuracy·恢复性修理 recovery repair·机床旋转精度 rotational accuracy of machine tool·机修车间(分厂) machine repair shop·机修技工 maintenance mechanic·机械修复法 mechanical repair method·机械的瞬时效率 instantaneous efficiency of machinery·互换法 interchange method·检验 inspection·集中修理制 centralized maintenance system·几何精度 geometric accuracy·季节性修理 seasonal repair·计划外修理 repair out of plan计划维修 scheduled maintenance·计划预修制(ППP) planned preventive maintenance system·计划修理 planned repair·接触精度 contact accuracy·紧急修理作业 emergency repair task·就地加工修配法 machining and fitting method on the spot·精度指数 precision index·精度标准 accuracy standard·精度保持性 precision retaining ability·精度储备 precision reserve·精修 fine repair·精修技工 fine repair mechanic·经济精度 economic accuracy·平衡精度等级 balancing precision grade·平均修理时间 mean time to repair(MTTR), mean repair time·小修 minor repair·修配法 fitting method·修配环 repair link·修理任务书 repair specification·修理施工调度 repair rasks dispatch·修理时间 repair time, shutdown time·修理停歇时间定额 downtime quota for equipment repair·修理用设备 repair facilities·修理质量 repair quality·修理质量指标 repair quality index·修理质量计划 repair quality plan·修理质量考核 repair quality assessment·修理标识 repair symbols·修理成本考核 repair cost assessment·修理尺寸 repair size修理定额 repair quota·修理费用定额 repair cost quota·修理方案 repair scheme·修理工时定额repair manhour quota·修理工时考核 repair manhours assessment·修理工艺 repair technology·修理工程车 maintenance engineering truck·修理工具 maintenance tool·修理工期考核 repair time limit assessment·修理考核 repair assessment·修前预检 inspection before repair·修前测绘 measuring and drawing before repair·修前访问 inquiry before repair·修后服务 service after repair·最优修理周期 optimum repair cycle·装配精度 assembly accuracy·电修车间(分厂) electric repair shop·电修技工 maintenance electrician·单台设备修理费用核算 repair cost accounting for single equipment ·调整法 adjustment method·调整环 adjusting link覆盖件 covering parts·返修品 back repaired products·分散(混合)储备 decentralized storage·分散生产方式 decentralized production mode·分散生产分散储备 decentralized production and decentralized storage ·废品损失 rejection loss·废品率 rejection rate·废品 waste products·存放合理化 storage rationalization·储备形式 storage form·储备恢复周期(订货间隔期) interval between orders·储备限额 storage limit·大型铸锻件 large-sized casting and forging·次品 substandard products·超差品 over-tolerance products·常备备件 runing spare parts·成品 finished products·成品储备 storage of finished products·成对储备 conjugated storage·成对(套)件 conjugated parts·部件储备 storage of assembles·部件 assembly·仓库面积利用率 utilization ratio of storehouse area·备件的“五清” “five clear”for spare parts·备件自给率 self - sufficiency rate of spare parts·备件自然失效 natural failure of spare parts·备件资金的核算法 accounting method of spare parts fund·备件资金占用率 occupation rate of spare parts fund·备件资金周转期 turnover period of spare parts fund·备件资金周转率 turnover rate of spare parts fund备件考核指标 assessment criteria of spare parts managment·备件卡基础资料 elementary data of spare parts cards·备件卡(帐) cards of spare parts·备件库的“五五码放” “five - five tiering”for storehouse of spare parts ·备件库的“三一致” “three coincidence”for storehouse of spare parts ·备件库的“三清” “three clear”for storehouse of spare parts·备件库的“两齐” “two neatness”for storehouse of spare parts·备件库管理工作 management of spare parts storehouse·备件库存供应率 supply rate of spare parts inventory·备件库保管员职责 responsibility of spare parts storehouse manager·备件库职责 responsibilities for storehouses of spare parts·备件库 storehouse for spare parts·备件经济管理 economic management of spare parts·备件经常储备定额 regular storage quota of spare parts·备件计划员 planner responsible for spare parts·备件计算机管理 computer - aided management of spare parts·备件技术员 technician responsible for spare parts·备件技术失效 technical failure of spare parts·备件汇总 collection of spare parts·备件合用率 suitability of spare parts·备件供应率 supply rate of spare parts·备件管理计划工作 planning work of sapre parts management·备件管理技术工作 technical work of spare parts management·备件管理职责 responsibility of spare parts management·备件管理 spare parts management·备件范围 range of spare parts·备件分类工作 classifying work of spare parts·备件订货点法 ordering point method of spare parts·备件订货点 ordering point of spare parts·备件订货量 ordering quantity of spare parts·备件定期订货法 periodic ordering method of spare parts·备件定量订货法 fixed - quantity ordering method of spare parts·备件定量保持法(维持定量法)fixed - quantity keeping method of spare parts ·备件储备的“三点制” “three point system”of spare parts storage·备件储备资金限额 limit of funds for reserve spare parts·备件储备资金 funds for reserve spare parts·备件储备定额 storage quota of spare parts·备件储备失效寿命 storage life of spare parts to failure·备件成本价格 cost price of spare parts·备件采购(供应)周期 delivery cycle of spare parts·备件包装法 packing method of spare parts·备件拥有量 possessed amount of spare parts·备件周转加速率 turnover acceleration rate of spare parts·备件周转率 turnover rate of spare parts·备件质量检验 quality inspection of spare parts·备件图册基本内容 main contents of spare parts album·备件图册质量 quality of spare parts album·备件图册 spare parts album·备件统计分析法 statistical analysis method of spare parts·备件统计 statistic of spare parts·备件消耗量 consumption of spare parts·备件退库率 return rate of spare parts·备件使用寿命 service life of spare parts·备件双箱法(双储备法) double case method of spare parts·备件生产方式 production mode of spare parts·备件寿命 life of spare parts·备件名目卡(帐) item cards of spare parts·备件年平均库存金额 annual average stock sum of spare parts·备件ABC管理法 A,B,C management method of spare parts·备件ABC分类法 A,B,C classifying method of spare parts备件 spare parts·标准件 standard parts·半成品储备 storage of semifinished porducts·半成品 semi-finished products·易损件 vulnerable parts·中心备件库 central storehouse of spare parts·一般备件 running spare parts·液压件 hydraulic parts·在制品 articles being processed·循环性备件 repairable spare parts·限寿机件 life-limited item·特殊储备 special storage·橡胶件 rubber parts·替代品 substitute products·维修用外购物资 outsourcing materials used for maintenance·通用配件商品化 commercialization of general-purpose spare parts·微电子器件 micro-electronic parts of appliances·消耗性备件 consumptive spare parts·消耗定额 consume quota·外协件 outsourcing manufactured parts·外购备件储备定额公式 storage quota formula of outsourcing spare parts ·外购备件 outsourcing spare parts·确定备件的结构分析法 structural analysis method for determining spare parts·润滑件 lubricating parts·设备备件综合卡(帐) integrated cards of equipment spare parts·设备备件卡(帐) cards of equipment spare parts·强制更换件 mandatory replacement item·每个复杂系数备件资金 fund of spare parts per complexity coefficient ·毛坯库 storehouse for stocks·毛坯件 stock毛坯储备 storage of stock·密封件 sealing parts·配件 fittings· 通用(共用)件 general-purpose parts·光学系统备件 parts of optical system·贵重备件 valuable spare parts。
设备管理英文术语大全

概率〔几率〕probability·方差variance·分散修理decentralized maintenance·动态试验dynamic test·动力设备设施治理power facilities management·除尘、防护设备治理duct-proof and protective equipment managemen t ·抽样调查sampling investigation·备件国产化治理domestic production management of imported spare parts ·标准偏差standard deviation·安装预算budget of installation·包机制machine contracting system·班前检查与润滑制度regulation of check and lubrication before on shift ·[设备]交接班制度shift relief system·?设备治理条例?〔?条例?〕?Equipment Management Regulation?·[设备]修理repair·[设备]修理maintenance (and repair)·重点调查key-point investigation·重点设备治理management of key-point equipment·重点设备key-point equipment·责任事故liability accident·指数分布exponential distribution·直方图histogram·预付与托收承付prepayment and collection·预防性试验prophylactic test·预防为主prevention first·正交设计法〔正交试验法〕orthogonal design·正态分布normal distribution·运输车辆治理制度transportation vehicle management system·质量“三包〞three guarantees of quality·质量事故accident due to quality·压力容器治理制度management regulation of pressure vessel·无故障运行时间mean time to failure·威布尔分布Weibull distribution·闲置设备治理制度idle equipment management·闲置设备idle plant·统计分析statistical analysis·修理性maintainability·修理信息治理maintenance information management·维护与方案检修相结合combination of service and planned maintenance ·随机大事random event·数控设备治理numerical control (NC) equipment management·三级保养制three-level service system·数学期望mathematical expectation·数学模型mathematical model·数理统计mathematical statistics·生产技术装备technical facilities in production·生产设备production equipment·寿命周期费用life cycle cost (LCC)·润滑油库治理制度mangement regulation of lubricant warehouse·商检〔商品检验〕commodity inspection·设计、制造与使用相结合combination of design, manufacturing and operation ·设备调研investigation on plant·设备的牢靠性与牢靠度reliability reliability theory·设备的节能性energy saving property of plant·设备的检查评比facility inspection and appraise through comparison for plant ·设备点检制度plant check system·设备的成套性complete set of plant·设备的平安性safety of plant·设备的生产率productivity of plant设备的耐用性durability of plant·设备的敏捷性flexibility of plant·设备状态监测与诊断技术治理equipment condition monitoring and diagnostic technology manage·设备状态治理制度equipment condition management systen·设备综合治理total plant management·设备资产动态治理制度dynamic management system of plant assets·设备租赁plant leasing·设备修前预备制度preparation system before equipment repair·设备修理工时定额man-hours quota for equipment repair·设备修理费用定额expense quota for equipment repair·设备修理材料定额material quota for equipment repair·设备修理质量验收制度acceptance regulation of equipment repair quality·设备型号equipment model·设备型式type of equipment·设备经济寿命economical life of equipment·设备经营治理制度operation and business management system·设备技术档案technical document of plant·设备技术状况technical conditions of equipment·设备技术状态治理technical condition management of plant·设备技术资料治理制度management system for technical document and plant ·设备技术性能technical properties of plant·设备技术寿命technical life of equipment·设备检修专业化协作specialized cooperation of plant maintenance·设备检修方案治理制度planning and management regulation of plant maintenance·设备检修方案plant maintenance plan·设备检修规程plant maintenance specification·设备检修质量plant maintenance quality·设备根底设计与施工design and construction of equipment foundation·设备合同治理management of equipment order contract·设备规划可行性分析feasibility studies of plant project设备规划investment plan of plant·设备功能〔效能〕performance of plant·设备工作力量operational capability of plant·设备治理考核制度examination and check systems of plant management·设备治理经济责任制度economic responsibility regulation of plant management ·设备治理岗位标准post standard of plant management·设备治理制度plant management systems·设备治理停留时间定额〔停留天数〕downtime quota for equipment repair·设备治理现代化plant engineering modernization·设备治理plant management, plant enginerring·设备固定资产治理制度fixed plant assets management systems·设备故障equipment failure·设备更治理制度plant renewal management·设备更plant renewal·设备更换plant replacement·设备岗位责任post responsibility of plant management·设备改造治理制度equipment modification management system·设备改造plant reconstruction, plant modernization·设备分级治理classified management of plant·设备定人定机、凭证操作规定operation regulation with fixed qualified operator and fixed eq·设备操作的“五项纪律〞“five disciplines〞of plant operation·设备操作规程operation specification of equipment·设备备品配件治理制度management regulation of equipment spare parts·设备备件库房治理制度management regulation of equipment spare parts inventory·设备报价to quote plant price·设备报废discard of plant·设备安装治理equipment installation management·设备安装equipment installation·设备巡回检查制度tours system to inspect plant·设备询价to enquire plant price设备选型plant model selection·设备验收交接制度acceptance check and reception systems of plant·设备统计报表制度statistic-reporting system of plant·设备修理技术资料technical document and date for plant maintenance·设备修理技术治理制度management regulation of plant maintenance technology ·设备修理定额equipment maintenance quota·设备维护规程equipment service specification·设备台帐unit account of plant·设备完好标准equipment perfectness norm·设备完好plant in good condition·设备索赔claims for equipment·设备使用规程specifications of usage·设备使用初期信息反响治理information feedback management in initial operation period of pl·设备使用与维护治理制度management regulation for operation and service of equipment·设备全过程治理life-cycle management of plant·设备寿命life of equipment·设备润滑治理制度lubrication management regulation of plant·设备润滑“五定〞“five fixation〞of lubrication·设备事故治理制度accident management regulation of plant·设备事故“三不放过〞three do not let pass of plant accident·设备事故plant accident·设备区域修理负责制region responsibility system of plant maintenance·设备前期治理和后期治理fore period and later period management of plant·设备前期治理规定regulation of fore period management of plant·设备磨损补偿wear compensation for plant·设备老化plant ageing·算术平均值〔均值〕arithmetic mean·强制保养制coercionary service system·投资效果系数effect coefficient of investment·设备经济治理制度economic management system of plant设备治理评优活动excellence selection activity in plant management·排列图〔帕累托图〕Pareto chart·负荷试验load test·故障停机时间breakdown time·工艺适应性technological adaptability·工程设备监理supervision of engineering facilities·工序掌握点设备治理management of proccess-control-point equipment·合同变更与解除contract change and cancellation·混合修理combined maintenance·回归分析regression analysis·检查间隔期interval between inspections·检修社会化socialization of maintenance·集中修理centralized maintenance·技术先进性technical advancement·技术治理与经济治理相结合combination of technical management and economic management·计算机关心设备治理computer-aided plant management·方案预修制度〔ЛЛP〕planned preventive maintenance system·进口设备离岸价FOB of imported equipment·进口设备治理imported equipment management·进口设备到岸价CIF of imported equipment·精、大、稀设备precise,large scale,rare plant·精、大、稀设备治理management of precise,large scale,rare equipment·精、大、稀、关键设备的“五定〞“five fixed〞of precise,large scale,rare,critical equipme·经济性economy·静态试验static test·开箱检查open-case inspection·平均偏差average deviation·平均等待时间mean waiting time,MWT·修理周期repair cycle·修理周期构造structure of repair cycle修理、改造与更相结合combination of repair, modernization and renewal·修理简单系数complexity coefficient of repair·修理间隔期time between repairs·租赁设备治理制度leased equipment management system·资金的时间价值time value of fund·自然事故natural accident·自制设备self-made equipment·自制设备治理制度management system for selfmade equipment·自制备件治理制度self-made spare parts management system·专业治理与群众治理相结合combination of professional management and mass management·转让设备〔设备调剂〕transfer of facility·典型调查typical investigation·地区〔部门〕修理中心areal (departmental) repair center·废油回收率recovery ratio of used oil·动力设备完好率perfectness ratio of power plant·定期保养完成率fulfillment ratio of periodic service·大修理平均停留天数mean downtime(days) due to overhaul·重点设备完好率perfectness ratio of key-point equipments·一次交验合格率qualification ratio under first acceptance check·在用设备可利用率availability of plant in use·已安装设备利用率utilization ratio of installed equipments·万元固定资产年创利润率annual profit ratio per 10000 yuan fixed assets·万元产值占用修理费用maintenance expense for 1000 yuan production value ·实有设备安装率installation ratio of owned equipments·设备综合利用率comprehensive utilization ratio of plant·设备资产增值率added value rate of plant assets·设备资产投资回收期capital investment recovery period of plant·设备度newness degree of plant·设备净资产创利润率profit ratio vs net book value of plant·设备方案台时利用率utilization ratio of planned time of plant设备构成比constitution ratio of plant·设备负荷率load rate of plant·设备返修率back repair rate·设备制度台时利用率utilization ratio of institutional time of plant·设备闲置率idelness ratio of plant·设备投资回收报率plant capital investment recovery ratio·设备投资产出比capital investment recovery period of plant·设备完好率perfectness ratio of plant·设备日常保养完成率plant daily service fulfillment ratio·设备事故频率incident frequency·设备利用率utilization ratio·事故[故障]停机率down time ratio to accident (failure)·清洗换油方案完成率fulfillment ratio of cleaning and oil change plan·每个修理简单系数平均大修理本钱mean repair cost per complexity coefficient of repair·每个简单系数占用修理费用maintenance expense per repair complexity coefficient·每万元固定资产创工业增加值率industrial increase value ratio per 10000 yuan fixed assets·故障强度failure intensity·故障频率failure frequency·关键设备完好率perfectness ratio of critical equipments·精大稀设备完好率perfectness raito of precise,large scale and rare equipments ·可利用率〔有效利用率〕availability·平均停机时间mean down time,MDT·平均故障间隔期,平均无故障工作时间mean time between failture·修理方案完成率fulfillment ratio of repair plan废润滑油再生〔废油再生〕regeneration of waste lubricating oil·防泄漏治理leak prevention management·二级保养second level service·定期精度调整periodic accuracy adjustment·定人定机制度system of fixed machine and operator·额定载荷rated load·超负荷试运行commissioning under overload·初步试运行preliminary commissioning·操作工人的“四会〞four basic skills for operator·参数故障parametric failure·保养方案完成率fulfilment ratio of service plan·保养规程service specification·保养“十字〞作业法“ten words〞method for service·保养service·平安性故障safety failure·平安规程safety procedure·[设备性能]劣化degradation (of equipment performance)·PM 小组PM group·隐蔽故障hidden failure·有效性availability·有效度avaliability·有效寿命effective life·制度时间institutional time·一级保养first level service·原发故障primary failure·原始记录original record·正常负荷normal load·正常超载normal overload·治漏“八字〞法“eight words〞method for leakage control·运行时间operating time仪表“三率〞“three rate〞of meter·早〔初〕期故障期early failure period·永久性故障〔持续性故障〕permanent failure·验收试运行final commissioning·无泄露[区]标准leakless(area) standard·突发性〔偶发〕故障random failure·维护费service cost·危急性故障dangerous failure·误操作故障failure by misoperation·完好设备perfect facility·生产修理productive maintenance(PM)·润滑工作岗位责任制post responsibility of lubrication work·润滑治理制度lubrication management system·润滑“五定〞“five fixation〞of lubrication·润滑“三过滤〞three-step filtration of lubricating oil·润滑站lubricating station·润滑图表lubricating diagram·试车commissioning·日常保养费daily service expenses·日常保养〔日保〕daily service·日历时间利用率utilzation ratio of calender time·设备的牢靠性和牢靠度reliability·设备的区域维护regional service of equipment·设备技术状态technical conditions of equipment·设备故障率曲线〔浴盆曲线〕failure rate curve of equipment,tub curve ·设备操作合格证operation licence·设备“5S〞活动“5S〞activity of equipment·设备隐患hidden trouble of equipment·设备运行记录operation record of equipment·设备维护的“四项要求〞four requirements for plant service设备维护标准service standard of equipment·设备维护equipment service·设备使用的“三好〞three well doing for use of facility·设备使用过程process of machine operation·设备三级保养three-level service system for equipment·设备日常点检routine inspection·设备清洗〔清扫〕cleaning of plant·设备漏油标准oil leakage standard·设备利用系数utilization factor of equipment·人身保护装置personal safety device·强制保养mandatory service·潜在故障latent filure·偶发故障期accidental failure period·磨损性故障wearout failure·例行保养〔例保〕routine service·密封点sealed point·劣化趋向治理degradation trend control·随机故障random failure·设备的定期维护periodic service of equipment·负荷试运行commissoning under load·故障类型failure type·故障率〔失效率〕failure rate·故障率根本类型basic forms of failure rate·故障模式failure mode·故障模型failure model·故障弱化failure weakening·故障树分析FTA,fault tree analysis·故障物理学physics of failure·故障停机率breakdown rate·故障征兆failure symptom·故障平安safety protection against failure·故障分析方法failure analysis method·故障机理failure mechanism·功能故障functional failure·关键设备使用维护“四定〞four stipulations for operation and maintenance of critical equip·耗损〔劣化〕故障期exhaustion failure period·红旗设备red-flag equipment·根本故障basic failure·连续性故障intermittent failure·继发故障secondary failure·方案时间利用率utilization ratio of planned time·渐衰失效性故障local and gradual failure·渐发性〔磨损〕故障gradual(wear-out) failure·精、大、稀、关键设备的使用维护operation and service of precise,large scale,rare and criti·净开动时间net operating time·可使用时间up time·可用性〔可利用率〕availability·牢靠性为中心的修理reliability centered maintenance,RCM·平均故障间隔期〔平均无故障工作时间〕mean time between failures,MTBF·破坏性故障catastrophic failure·起重机平安保护safety protection of crane·最大允许寿命〔宣称寿命〕maximum permitted life (declared life)·自显故障self-displayed failure·综合试运行total commissioning·专群结合combination of specialists and masses·调整adjustment·跟踪检查trail checkout·法定检查lawful inspection·动特性试验dynamic performance test·动态精度dynamic accuracy动态检验dynamic test·定期点检periodic fixed point inspection·定期检查periodic inspection·定期参数检查periodic parameter examination·定期润滑检查periodic lubrication check·“三位一体〞点检制“three in one〞fixed point inspetion system·主观〔五官〕推断故障subjective(sensible) failure deciding·一般目视检查general visual inspection·影响设备效率的六大损失six major losses affecting running efficiency·正常检查normal inspection·巡回检查patrol inspection·巡回检测patrol test·无损检查non-destructive test·停机时间down time·微观组织检查examination of microscopic structure·损坏break down·缺陷defect·失效〔故障〕failure·容许故障率allowable failure rate·日常检查daily inspection·日常润滑检查daily lubrication check·设备点检fixed point inspection of equipment·设备检查facilities inspection·设备监测equipment monitoring·设备故障频率equipment failure frequency·设备故障治理效果评价result evaluation of plant failure management·设备诊断技术equipment diagnostic technique·设备诊断equipment diagnosis·酸洗检查inspection with pickling·敲打检查hammering test磨损检查wearing inspection·内外表检查inner surface inspection·故障强度率failure intensity rate·故障趋于零的“四个阶段〞“four steps〞to zero failure·故障危害程度harm extent of failure·故障为零的五项措施five measures to zero failure·故障〔停机〕损失breakdown loss·故障治理程序program of railure management·故障治理信息information of failure management·故障修理troubleshooting·功能检查〔功能测试〕function inspection,function test·宏观组织检查examination of macroscopic structure·检定周期cycle of verification·技术维护technical service·季节性技术维护seasonal technical service·方案保全治理planned maintenance management·解体检查inspection under disassembled condition·精度检查accuracy inspection·静态精度static accurary·牢靠性试验reliability test·牢靠性分析reliability analysis·平均寿命时间〔MTTF〕mean time to failure·状态监测condition monitoring·状态检查condition inspection·点检的主要环节main items of fixed point inspection改善修理corrective maintenance·返修率back repair rate·分级修理stepped(sizing) repair·分散修理制decentralized maintenance system·废次品及返修损失waste and ungraded product and back repair loss ·非预定修理时间unscheduled maintenance time·定期修理作业periodic repair task·定期修理法periodic repair·定位精度location accuracy·传动精度transmission accuracy·大修方案修改revision of overhaul plan·大修方案考核assesment of overhaul plan·大修方案编制overhaul planning·大修方案依据basis of overhaul plan·大修方案完成率fulfilment rate of overhaul plan·大修方案实施implementation of overhaul plan·大修费用overhaul cost·大修本钱构成overhaul cost·大修本钱分析overhaul cost analysis·大修本钱完成率fulfilment rate of overhaul cost·大修保修overhaul guarantee·大修周期interval between overhauls, overhaul cycle·大修质量保证体系guarantee system of overhaul quality·大修理质量评定overhaul quality evaluation·大修理质量掌握overhaul quality control·大修overhaul,capital repair·部件修理法assembly repair·局部修理法partial repair·补偿法compensation method·备件生产方案production program of spqre parts备份或冗余系统stand-by or redundancy system·标准尺寸修理法standard-size repair method·八步法“eight ste〞ps method·重复定位精度repeat location accuracy·中修middle repair·有可修理备份的系统system with maintainable standby parts·远距离修理remote maintenance·预防修理preventive maintenance·预定修理时间scheduled maintenance time·预知修理〔状态监测修理〕predictive maintenance·质量体系quality system·质量quality·逾期修理deferred maintenance·网络方案network planning·修理技术培训maintenance skill training·修理间隔〔正常运行时间〕maintenance interval, uptime·修理活动的经济分析economic analysis of maintenance activities ·修理工人maintenance worker·修理防护maintenance protection·修理车间maintenance shop·修理预防maintenance prevention·修理周期maintenance cycle·修理时间maintenance time·同步修理法synchronous repair·停修时间repair downtime·项修〔工程修理〕item repair·外委修理repair on commission·全员参与的生产修理制〔TPM〕total production maintenance system·受控修理controlled maintenance·寿命周期修理life cycle maintenance热修hot repair·设备修理方案repair schedule of equipment·设备修理验收acceptance check for equipment repair·设备季度修理方案quarterly repair schedule of equipment·设备技术考核technical check of equipment·设备大修方案equipment overhaul plan·设备月度修理方案monthly repair schedule of equipment·设备修理方案equipment maintenance plan·设备修理三要素three essential factors of equipment maintenance ·设备项修方案item repair plan of equipment·设备年度修理方案annual repair schedule of equipment·事后修理breakdown maintenance·抢修first-aid repair·大修机床精度accuracy of machine tool after overhaul·滚动方案rolling (circulation) plan·治理信息系统修理MIS maintenance·工程力量指数process capacity index·工作精度working accuracy·恢复性修理recovery repair·机床旋转精度rotational accuracy of machine tool·机修车间〔分厂〕machine repair shop·机修技工maintenance mechanic·机械修复法mechanical repair method·机械的瞬时效率instantaneous efficiency of machinery·互换法interchange method·检验inspection·集中修理制centralized maintenance system·几何精度geometric accuracy·季节性修理seasonal repair·方案外修理repair out of plan方案修理scheduled maintenance·方案预修制〔ППP〕planned preventive maintenance system ·方案修理planned repair·接触精度contact accuracy·紧急修理作业emergency repair task·就地加工修配法machining and fitting method on the spot·精度指数precision index·精度标准accuracy standard·精度保持性precision retaining ability·精度贮存precision reserve·精修fine repair·精修技工fine repair mechanic·经济精度economic accuracy·平衡精度等级balancing precision grade·平均修理时间mean time to repair(MTTR), mean repair time·小修minor repair·修配法fitting method·修配环repair link·修理任务书repair specification·修理施工调度repair rasks dispatch·修理时间repair time, shutdown time·修理停留时间定额downtime quota for equipment repair·修理用设备repair facilities·修理质量repair quality·修理质量指标repair quality index·修理质量方案repair quality plan·修理质量考核repair quality assessment·修理标识repair symbols·修理本钱考核repair cost assessment·修理尺寸repair size修理定额repair quota·修理费用定额repair cost quota·修理方案repair scheme·修理工时定额repair manhour quota·修理工时考核repair manhours assessment·修理工艺repair technology·修理工程车maintenance engineering truck·修理工具maintenance tool·修理工期考核repair time limit assessment·修理考核repair assessment·修前预检inspection before repair·修前测绘measuring and drawing before repair·修前访问inquiry before repair·修后效劳service after repair·最优修理周期optimum repair cycle·装配精度assembly accuracy·电修车间〔分厂〕electric repair shop·电修技工maintenance electrician·单台设备修理费用核算repair cost accounting for single equipment ·调整法adjustment method·调整环adjusting link掩盖件covering parts·返修品back repaired products·分散〔混合〕贮存decentralized storage·分散生产方式decentralized production mode·分散生产分散贮存decentralized production and decentralized storage ·废品损失rejection loss·废品率rejection rate·废品waste products·存放合理化storage rationalization·贮存形式storage form·贮存恢复周期〔订货间隔期〕interval between orders·贮存限额storage limit·大型铸锻件large-sized casting and forging·次品substandard products·超差品over-tolerance products·常备备件runing spare parts·成品finished products·成品贮存storage of finished products·成对贮存conjugated storage·成对〔套〕件conjugated parts·部件贮存storage of assembles·部件assembly·仓库面积利用率utilization ratio of storehouse area·备件的“五清〞“five clear〞for spare parts·备件自给率self - sufficiency rate of spare parts·备件自然失效natural failure of spare parts·备件资金的核算法accounting method of spare parts fund·备件资金占用率occupation rate of spare parts fund·备件资金周转期turnover period of spare parts fund·备件资金周转率turnover rate of spare parts fund备件考核指标assessment criteria of spare parts managment·备件卡根底资料elementary data of spare parts cards·备件卡〔帐〕cards of spare parts·备件库的“五五码放〞“five- five tiering〞for storehouse of spare parts ·备件库的“三全都〞“three coincidence〞for storehouse of spare parts ·备件库的“三清〞“three clear〞for storehouse of spare parts·备件库的“两齐〞“two neatness〞for storehouse of spare parts·备件库治理工作management of spare parts storehouse·备件库存供给率supply rate of spare parts inventory·备件库保管员职责responsibility of spare parts storehouse manager ·备件库职责responsibilities for storehouses of spare parts·备件库storehouse for spare parts·备件经济治理economic management of spare parts·备件常常贮存定额regular storage quota of spare parts·备件方案员planner responsible for spare parts·备件计算机治理computer - aided management of spare parts·备件技术员technician responsible for spare parts·备件技术失效technical failure of spare parts·备件汇总collection of spare parts·备件合用率suitability of spare parts·备件供给率supply rate of spare parts·备件治理方案工作planning work of sapre parts management·备件治理技术工作technical work of spare parts management·备件治理职责responsibility of spare parts management·备件治理spare parts management·备件范围range of spare parts·备件分类工作classifying work of spare parts·备件订货点法ordering point method of spare parts·备件订货点ordering point of spare parts·备件订货量ordering quantity of spare parts·备件定期订货法periodic ordering method of spare parts·备件定量订货法fixed - quantity ordering method of spare parts·备件定量保持法〔维持定量法〕fixed - quantity keeping method of spare parts ·备件贮存的“三点制〞“three point system〞of spare parts storage·备件贮存资金限额limit of funds for reserve spare parts·备件贮存资金funds for reserve spare parts·备件贮存定额storage quota of spare parts·备件贮存失效寿命storage life of spare parts to failure·备件本钱价格cost price of spare parts·备件选购〔供给〕周期delivery cycle of spare parts·备件包装法packing method of spare parts·备件拥有量possessed amount of spare parts·备件周转加速率turnover acceleration rate of spare parts·备件周转率turnover rate of spare parts·备件质量检验quality inspection of spare parts·备件图册根本内容main contents of spare parts album·备件图册质量quality of spare parts album·备件图册spare parts album·备件统计分析法statistical analysis method of spare parts·备件统计statistic of spare parts·备件消耗量consumption of spare parts·备件退库率return rate of spare parts·备件使用寿命service life of spare parts·备件双箱法〔双贮存法〕double case method of spare parts·备件生产方式production mode of spare parts·备件寿命life of spare parts·备件名目卡〔帐〕item cards of spare parts·备件年平均库存金额annual average stock sum of spare parts·备件ABC 治理法A,B,C management method of spare parts·备件ABC 分类法A,B,C classifying method of spare parts备件spare parts·标准件standard parts·半成品贮存storage of semifinished porducts·半成品semi-finished products·易损件vulnerable parts·中心备件库central storehouse of spare parts·一般备件running spare parts·液压件hydraulic parts·在制品articles being processed·循环性备件repairable spare parts·限寿机件life-limited item·特别贮存special storage·橡胶件rubber parts·替代品substitute products·修理用外购物资outsourcing materials used for maintenance·通用配件商品化commercialization of general-purpose spare parts·微电子器件micro-electronic parts of appliances·消耗性备件consumptive spare parts·消耗定额consume quota·外协件outsourcing manufactured parts·外购备件贮存定额公式storage quota formula of outsourcing spare parts ·外购备件outsourcing spare parts·确定备件的构造分析法structural analysis method for determining spare parts ·润滑件lubricating parts·设备备件综合卡〔帐〕integrated cards of equipment spare parts·设备备件卡〔帐〕cards of equipment spare parts·强制更换件mandatory replacement item·每个简单系数备件资金fund of spare parts per complexity coefficient·毛坯库storehouse for stocks·毛坯件stock毛坯贮存storage of stock·密封件sealing parts·配件fittings·通用〔共用〕件general-purpose parts·光学系统备件parts of optical system·贵重备件valuable spare parts·管路备件spare parts for pipes·工程塑料件engineering plastic parts·关键备件critical spare parts·机械零件machine parts·机械备件mechanical spare parts·连续贮存discontinued storage。
设备标牌中英文对照

设备标牌中英文对照一、前言设备标牌是工业生产中常见的一种标识方式,通过标牌可以清晰地了解设备的基本信息和操作规程。
在国际化的今天,越来越多的企业希望将设备标牌同时标注中英文,以便吸引更多的国际客户或便于外籍员工使用设备。
本文将介绍一些常见的设备标牌中英文对照,方便读者参考和使用。
二、设备名称中文英文设备名称Equipment Name机床Machine Tool液压机Hydraulic Press起重机Crane电焊机Welding Machine搅拌机Mixer压力机Press注塑机Injection Molding Machine磨床Grinder车床Lathe三、设备参数中文英文设备参数Equipment Parameters长度Length宽度Width高度Height重量Weight电压Voltage电流Current功率Power频率Frequency温度Temperature湿度Humidity四、安全警示语中文英文安全警示语Safety Warning Message高压危险High Voltage Danger警告Warning停止Stop危险区域Danger Zone非作业人员禁止入内No Entry for Unauthorized Personnel 注意触电风险Beware of Electric Shock使用前请阅读说明书Read Instruction Manual before Use五、操作指南中文英文操作指南Operation Guide启动Start停止Stop调整Adjust清理Clean维修Repair更换零件Replace Parts保养Maintenance检修Overhaul紧固螺丝Tighten Screws注油Oil Injection六、注意事项中文英文注意事项Precautions请戴安全帽Wear Safety Helmet禁止吸烟No Smoking禁止接打电话No Phone穿戴防护服Wear Protective Clothing注意摔落物Beware of Falling Objects禁止拆卸No Disassembly禁止闲人停留No Loitering警示标志Warning Sign紧急停车Emergency Stop请勿触摸Do Not Touch七、总结设备标牌中英文对照在工业生产中具有重要的作用,它能够帮助用户更好地理解和使用设备,并提供必要的安全保障。
操作规程的英文简称是什么

操作规程的英文简称是什么《Operation Procedure (OP)》In any organization, the smooth operation and management of various tasks and processes are crucial for efficient and effective performance. To ensure that all activities are carried out in a standardized and systematic manner, many companies and institutions have established Operation Procedures (OPs) as a set of guidelines governing various tasks.An OP is a document that outlines the step-by-step instructions for performing a specific task or adhering to a specific process. It provides a framework for employees to follow, ensuring that tasks are completed in a consistent and reliable manner. OPs are often created based on best practices and industry standards, and they may be updated regularly to reflect changes in technology, regulations, or organizational needs.The content of an OP typically includes the purpose of the task or process, the necessary equipment and resources, the sequence of steps to be followed, and any safety or quality control considerations. It may also include troubleshooting tips, best practices, and references to related documents or resources.By following OPs, employees can ensure that they are meeting the requirements of their role, adhering to safety and quality standards, and contributing to the overall success of the organization. OPs also provide a valuable training resource for new employees, as they can be used to learn how to perform tasks correctly and efficiently.In summary, Operation Procedures (OPs) are an important tool for organizations to standardize and optimize their operations. By providing clear and detailed instructions for tasks and processes, OPs help ensure that work is carried out in a consistent and reliable manner, ultimately contributing to the success of the organization.。
流程泵操作规程
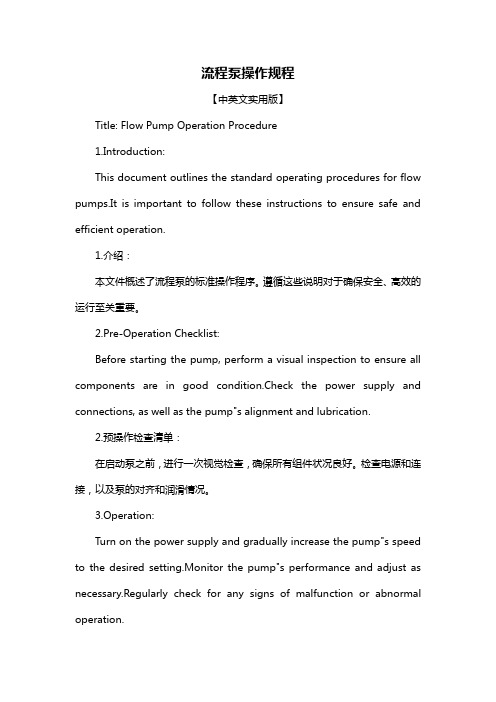
流程泵操作规程【中英文实用版】Title: Flow Pump Operation Procedure1.Introduction:This document outlines the standard operating procedures for flow pumps.It is important to follow these instructions to ensure safe and efficient operation.1.介绍:本文件概述了流程泵的标准操作程序。
遵循这些说明对于确保安全、高效的运行至关重要。
2.Pre-Operation Checklist:Before starting the pump, perform a visual inspection to ensure all components are in good condition.Check the power supply and connections, as well as the pump"s alignment and lubrication.2.预操作检查清单:在启动泵之前,进行一次视觉检查,确保所有组件状况良好。
检查电源和连接,以及泵的对齐和润滑情况。
3.Operation:Turn on the power supply and gradually increase the pump"s speed to the desired setting.Monitor the pump"s performance and adjust as necessary.Regularly check for any signs of malfunction or abnormal operation.3.操作:开启电源,逐渐将泵的速度增加到所需设置。
监控泵的性能,如有必要进行调整。
运输车辆和设备操作规程及交通安全管理制度(中英文)-百
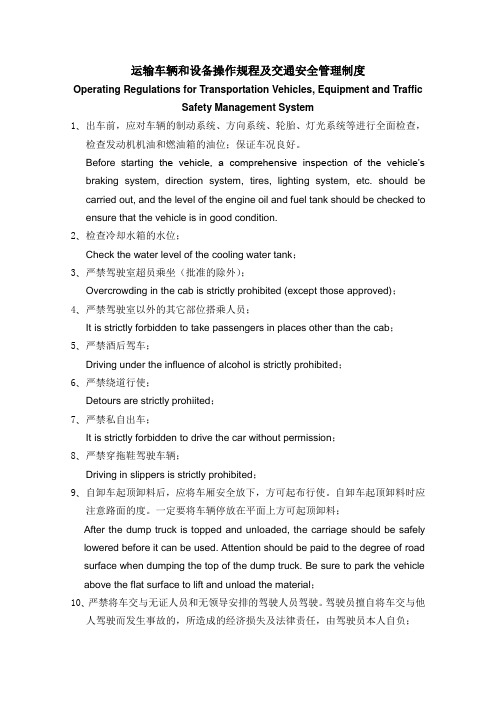
运输车辆和设备操作规程及交通安全管理制度Operating Regulations for Transportation Vehicles, Equipment and TrafficSafety Management System1、出车前,应对车辆的制动系统、方向系统、轮胎、灯光系统等进行全面检查,检查发动机机油和燃油箱的油位;保证车况良好。
Before starting the vehicle, a comprehensive inspection of the vehicle’s braking system, direction system, tires, lighting system, etc. should be carried out, and the level of the engine oil and fuel tank should be checked to ensure that the vehicle is in good condition.2、检查冷却水箱的水位;Check the water level of the cooling water tank;3、严禁驾驶室超员乘坐(批准的除外);Overcrowding in the cab is strictly prohibited (except those approved);4、严禁驾驶室以外的其它部位搭乘人员;It is strictly forbidden to take passengers in places other than the cab;5、严禁酒后驾车;Driving under the influence of alcohol is strictly prohibited;6、严禁绕道行使;Detours are strictly prohiited;7、严禁私自出车;It is strictly forbidden to drive the car without permission;8、严禁穿拖鞋驾驶车辆;Driving in slippers is strictly prohibited;9、自卸车起顶卸料后,应将车厢安全放下,方可起布行使。
切割机安全操作规程(中英文)-百
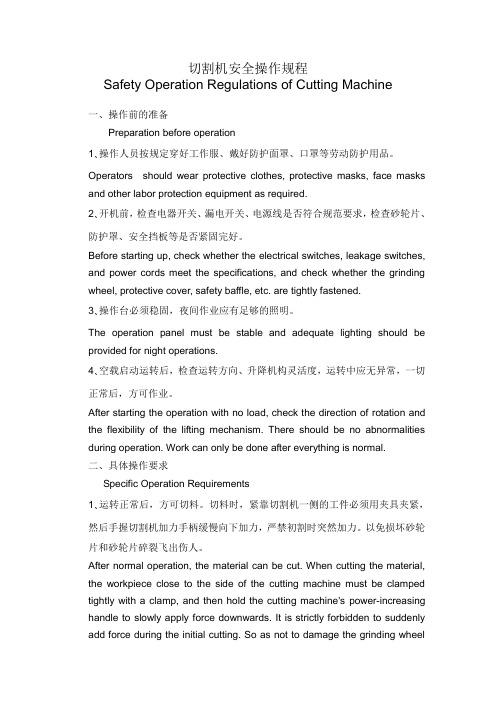
切割机安全操作规程Safety Operation Regulations of Cutting Machine一、操作前的准备Preparation before operation1、操作人员按规定穿好工作服、戴好防护面罩、口罩等劳动防护用品。
Operators should wear protective clothes, protective masks, face masks and other labor protection equipment as required.2、开机前,检查电器开关、漏电开关、电源线是否符合规范要求,检查砂轮片、防护罩、安全挡板等是否紧固完好。
Before starting up, check whether the electrical switches, leakage switches, and power cords meet the specifications, and check whether the grinding wheel, protective cover, safety baffle, etc. are tightly fastened.3、操作台必须稳固,夜间作业应有足够的照明。
The operation panel must be stable and adequate lighting should be provided for night operations.4、空载启动运转后,检查运转方向、升降机构灵活度,运转中应无异常,一切正常后,方可作业。
After starting the operation with no load, check the direction of rotation and the flexibility of the lifting mechanism. There should be no abnormalities during operation. Work can only be done after everything is normal.二、具体操作要求Specific Operation Requirements1、运转正常后,方可切料。
- 1、下载文档前请自行甄别文档内容的完整性,平台不提供额外的编辑、内容补充、找答案等附加服务。
- 2、"仅部分预览"的文档,不可在线预览部分如存在完整性等问题,可反馈申请退款(可完整预览的文档不适用该条件!)。
- 3、如文档侵犯您的权益,请联系客服反馈,我们会尽快为您处理(人工客服工作时间:9:00-18:30)。
Patalganga STANDARD OPERATING PROCEDURENo.: MT95EQUIPMENT QUALIFICATIONDate of Issue盛年不重来,一日难再晨。
及时宜自勉,岁月不待人。
PURPOSE:To provide a formal methodology to be followed during qualification of equipment.SCOPE:Applicable to qualification of new equipment, re-qualification of equipment, which has undergone major modification, relocation of equipment and Periodic Qualification as per schedule in Pharma manufacturing department.RESPONSIBILITY:Production, Engineering, Safety, Quality Control and Quality Assurance staff. DEFINITION:Qualification: Documented verification that the environment and equipment are appropriate for the designated function.User Requirement Specification (URS): A Requirement specification that describes what the equipment or system is suppose to do, thus containing at least set of criteriaor conditions that have to be met.Patalganga STANDARD OPERATING PROCEDURENo.: MT95EQUIPMENT QUALIFICATIONDate of Issue Functional Design Specification (FDS): Functional design specification is a document that specifies in a complete, precise, variable manner, the requirement design, behaviour or other characteristics of a system or component and often the procedures for determining whether these provisions have been satisfied.Specification that is offered by manufacturing based on URS and are agreed mutually.Design Qualification (DQ): Formal and systematic verification that the requirements defined in the specification phase are completely covered by the succeeding specification or implementation phase.Factory Acceptance Test (FAT): Testing conducted at the suppliers factory to determine whether or not a system specifies it’s acceptance criteria and to enable the user to determine whether or not to accept the system.Installation Qualification (IQ): Documented verification that a system is installed according to written and pre-approved specifications.Patalganga STANDARD OPERATING PROCEDURENo.: MT95EQUIPMENT QUALIFICATIONDate of Issue Site Acceptance Test (SAT): An acceptance test at the users site, usually involve the supplier.Operation Qualification (OQ): Documented verification that a system operates according to written and pre-approved specification throughout all specified operating ranges.PLC Validation: Documented verification that PLC Hardware are as per original drawing, Digital and Analog Input and Output are connected as per PLC Architecture and functioning according to written and pre-approved specification throughout all specified operating ranges.Performance Qualification (PQ): Documented verification that a system is capable of performing or controlling the activities of the processes, it is required to perform or control, according to written and pre-approved specifications, while operating in its specified operating environment.User (s): The person, or persons, who operate or interact directly with the system. Supplier: Any organisation or individual contacted directly by the user to supply a product or service.Patalganga STANDARD OPERATING PROCEDURENo.: MT95EQUIPMENT QUALIFICATIONDate of Issue Critical Equipment: The machine within a system where the malfunctioning or failureof equipment will have direct impact on product quality. Where product is in direct contact with machine body parts.Non-critical Equipment: The machine within a system where the malfunctioning or failure of equipment will not have direct impact on product quality. Where product is not in direct contact with machine body parts.1.0 HEALTH, SAFETY AND ENVIRONMENT: (对验证实施人员的HES要求)1.1 Personnel involved in qualification / re-qualification / periodic qualificationshould use appropriate personal protective equipment.1.2 Do not touch the moving parts.1.3 Electrical isolation should be done before any electric control panelverification.1.4 Read the safety instructions specified in the operation Manual of themachine to be qualified.Patalganga STANDARD OPERATING PROCEDURENo.: MT95EQUIPMENT QUALIFICATIONDate of Issue2.0 PROCEDURE:2.1 Equipment qualification should be based on the following documents2.1.1 User Requirement Specification (URS)2.1.2 Functional Design Specification (FDS)2.1.3 Design Qualification (DQ)2.1.4 Factory Acceptance Test (FAT)2.1.5 Checklist on Receipt2.1.6 Installation Qualification (IQ)2.1.7 Operation Qualification (OQ)2.1.8 PLC Validation ( If applicable)2.1.9 Provisional Handover Certificate2.1.10 Performance Qualification (PQ)2.1.11 Handover CertificateThe flow of the equipment qualification is as followsURS → FDS → DQ → FAT → IQ → OQ → PLC Validation (if applicable)SAT→ PQPatalganga STANDARD OPERATING PROCEDURENo.: MT95 EQUIPMENT QUALIFICATIONDate of Issue2.1.1 User Requirement Specification (URS):2.1.1.1 URS protocol should be approved by the project team(Users) members and Quality Assurance with Name, Signand Date.2.1.1.2 Following points should be considered during thedevelopment of URS.➢Introduction➢Over view➢Operation requirements➢Constraints➢Life cycle➢Glossary➢References➢Approval2.1.1.3 Each URS protocol should be allotted with a protocol no. inthe format specified below“URS/P”Where,Patalganga STANDARD OPERATING PROCEDURENo.: MT95 EQUIPMENT QUALIFICATIONDate of Issue “URS” stands for Use r requirement specification.“P” stands for equipment / instrument / balance / areaabbreviated code.2.1.1.4 The protocol should also identify with a Version No. Wherethe version no. changes with every change in the URS.2.1.1.5 The URS protocol header should consist of the following detailsas mentioned below:➢Title of the URS➢Protocol No.➢Version No.➢Date➢Cipla Patalganga➢Unit➢Page No.A specimen of the header is given below:Patalganga STANDARD OPERATING PROCEDURENo.: MT95 EQUIPMENT QUALIFICATIONDate of Issue2.1.2 Functional Design Specification (FDS):2.1.2.1 The FDS should be the manufacturer interpretation ofURS. FDS should include basic functioning of theequipment with focus on control and critical componentsspecifications and functions.2.1.2.2 The FDS should be in the form of separate documentand should include equipment specification, P&IDdiagrams.2.1.2.3 The FDS protocol / report should be mutually approvedby the user and supplier with sufficient technical detailsbased on the techno commercial offer.2.1.2.4 The supplier is finally selected and CER is raised.2.1.2.5 Any changes made after finalisation of DQ should undergo change control procedure as per SOP CQA 06.2.1.3 Design Qualification (DQ):Patalganga STANDARD OPERATING PROCEDURENo.: MT95 EQUIPMENT QUALIFICATIONDate of Issue2.1.3.1 Design qualification should be based on the discussionbetween the supplier and the user with reference toURS / FDS.2.1.3.2 Following points should be considered during thedevelopment of design qualification.➢ Purpose➢ Scope➢ Responsibility➢ Project requirement➢ Critical variables to be met➢ Process/ Product parameters e.g. Capacity etc.➢ cGMP considerationse.g. MOC of individual parts, finish of contact parts➢ Critical parameters e.g. Instrumentation, limits,➢ Safety➢ Location suitability➢ References➢ Documents to be attached.➢ Any changes made against the formally agreedparameters (Deviation if any).➢ Justification for acceptance (if any deviation)➢ Review (Inclusive of follow up action, if any)➢ RecommendationPatalganga STANDARD OPERATING PROCEDURENo.: MT95 EQUIPMENT QUALIFICATIONDate of Issue➢ Signing off2.1.3.3 Any change in DQ should be through a change controlprocedure as per SOP CQA-06 and should bedocumented.2.1.4 Factory Acceptance Test (FAT):2.4.1 The FAT should be conducted at the supplier’s premisesunder the users supervision unless agreed upon.2.4.2 The FAT protocol / report should be prepared by the supplieras per Manufacturers format and should be submitted forapproval of user.2.4.3 The equipment should be shipped to the site only afterapproval by the user.2.4.4 The FAT protocol / report should include details of the URSand FDS.2.4.5 Any modification, changes needs during the FAT should bedocumented and intimated to the user and carried out withmutual consent.Patalganga STANDARD OPERATING PROCEDURENo.: MT95 EQUIPMENT QUALIFICATIONDate of Issue2.1.5 Checklist on Receipt:2.1.5.1 All critical parts of equipment should be checked forfinish, any damages on receipt for availability as perpacking list and order details.2.1.6 Installation Qualification (IQ):2.1.6.1 All aspects such as utility connections, location suitability,material of construction of critical parts, installation of allmonitoring, controlling, instruments and gauges includingtheir calibration and certification by supplier should bechecked and verified.2.1.6.2 During the installation qualification Area Lux level, Floordrains, piping connections , machine alignment, levelling,P& ID Diagram, Schematic, circuit diagram, tagging,wiring pheruling, pneumatic connections consideredduring design qualification are checked and verified.Patalganga STANDARD OPERATING PROCEDURENo.: MT95 EQUIPMENT QUALIFICATIONDate of Issue2.1.7 Operation Qualification (OQ):2.1.7.1 During Operation qualification the working of themonitoring and controlling instruments, gauges andsystems like PLC, switches, gauges, motors, pumps etc.are checked and certified.2.1.7.2 The parameters considered during design qualificationare checked and certified.2.1.8 PLC Validation2.1.8.1 PLC validation should be carried out by competentexternal approved agency.2.1.8.2 PLC validation should be carried out during SAT orsubsequently within three months based on level ofchecks carried out during SAT. Validation should be doneaccording to pre-approved protocol and report. Allreference instruments being used for validation should becertified by approved agencies like ‘IDEMI’ and ‘ERTL.Patalganga STANDARD OPERATING PROCEDURENo.: MT95 EQUIPMENT QUALIFICATIONDate of Issue2.1.8.3 Brief description about equipment operating function andits location should be mentioned in the report. All rawdata should be handwritten at site during actual validation.2.1.8.4 The details of PLC and HMI hardware are checked as percircuit diagram and type of PLC, HMI, its software Versionno. details, details of the available digital/ analogue inputsand outputs. Installed switchgear details should bementioned i.e. SFU, MCB, relays, contactors, pushbuttons, switch, power supply, Surge protection etc.2.1.8.5 Equipment interlocks, alarms and operation logic shouldbe checked. Details of the PLC Battery conditions shouldbe checked and it’s life will be verified appropriately.2.1.8.6 All PLC validation reports should be handed over by thevalidation agency to the engineering department forverification within a week after physical verification of thesystem. Engineering, user department and qualityassurance department will verify submitted reports2.1.8.7 Any deviation observed should be highlighted and broughtup to the notice of Engineering/ User/QA dept.Patalganga STANDARD OPERATING PROCEDURENo.: MT95 EQUIPMENT QUALIFICATIONDate of Issue2.1.8.8 No changes should be made in the software or hardwareduring the course of validation.2.1.9 Site acceptance test (SAT) and Provisional HandoverCertificate:2.1.9.1 SAT should be carried out in conjugation with thesupplier and may include checks of critical components,controls based on the detail Fat, IQ and OQ have beensuccessfully performed.2.1.9.2 After the equipment goes through the installation andoperational qualification procedure, it should be reviewedat each stage by a team of Engineering, Production,Quality Assurance, Quality Control, Safety and Unit Head.2.1.9.3 In few cases the equipment may have to go through aprocess cycle development and stabilisation phase beforesubject to validation trials.2.1.9.4 If any deviation or non conformance to the acceptancecriteria should be recorded and informed to concernedsupplier. A decision should be taken by user team andsupplier to reject or to proceed for PQ.Patalganga STANDARD OPERATING PROCEDURENo.: MT95 EQUIPMENT QUALIFICATIONDate of Issue2.1.9.5 If SAT is found to be satisfactory, equipment should beprovisionally handed over to the concerned departmentfor Performance Qualification.2.1.10 Performance Qualification (PQ):2.1.10.1 During the Performance Qualification the working of thesystem as a whole is checked with respect to out put, quality,quantity and any specific requirements as per designqualification.2.1.10.2 Critical equipment should undergo extensive validationstudies to ensure consistent performance depending onapproved validation protocol.2.1.11 Handover Certificate:After successful Performance Qualification, based on reviewby the team of Engineering, Production, Quality Assurance,Quality Control, Safety and Unit Head. The equipment ishanded over to the concerned department for regular use.Patalganga STANDARD OPERATING PROCEDURENo.: MT95EQUIPMENT QUALIFICATIONDate of Issue 2.2 Equipment Qualification and Requalification protocol consist of thefollowing sections.➢Covering page➢Table of contents.➢Glossary➢Pre approval➢Design Qualification➢Check list on receipt➢Installation Qualification➢Operation Qualification➢Provisional Handover Certificate➢Performance Qualification➢Hand over Certificate2.3 REQUALIFICATION / PERIODIC QUALIFICATION2.3.1 All Major equipment should be requalified after any majorchange in the equipment or modification.2.3.2 If there are any major changes in critical parameters of equipment(e.g. RPM of blender, speed of agitator etc.) which has directimpact on the quality, then the revalidation of the process should be done.Patalganga STANDARD OPERATING PROCEDURENo.: MT95 EQUIPMENT QUALIFICATIONDate of Issue 2.3.3 The requalification need not be performed for any minor changes in the equipment, For example, few blades of multimill arereplaced.NOTE: Minor changes should be recorded in the Machine History Card.2.3.4 If any fixed equipment is shifted from one area to another area.Critical parameters should be checked during requalification.Transfer note should be made for the equipment. It should bekept along with the requalification record. For relocation ofportable equipment requalification is not required.2.3.5 During the transfer of equipment from one unit to another unitrequalification as IO, OQ should be conducted based on criticalparameters. A such copy of original qualification should beforwarded for reference.2.3.6 While transferring the equipment to other area / units, reviewshould be done for any specific requirements of conditions2.3.7 For equipment having no changes requalification time periodshould be decided based on performance of annual review of theequipment. The review of the equipment should be recorded inPatalganga STANDARD OPERATING PROCEDURENo.: MT95 EQUIPMENT QUALIFICATIONDate of Issue the Equipment Review Report (Annexure MT95/A1) Therequalification time period should not exceed five years.2.3.8 Schedule for requalification of the major equipment shouldavailable at unit level and should be recorded in schedule forrequalification Annexure MT95/A2.2.3.9 Schedule for PLC revalidation of the major equipment should beavailable at unit level and should be recorded in AnnexureMT95/A3.2.3.10 Any changes in schedule of equipment qualification should becarried out through deviation.Requalification / Periodic Qualification protocol consist of the following sections:➢Covering page➢Table of contents.➢Glossary➢Pre approval➢Over view➢Pre requisite➢Preventive Maintenance verificationPatalganga STANDARD OPERATING PROCEDURENo.: MT95EQUIPMENT QUALIFICATIONDate of Issue ➢Major breakdown verification➢System description➢Physical verification➢Calibration verification of critical components➢Calibration verification of calibration standards used➢Safety features verification➢Control panel verification➢Interlocks/controls verification➢Performance evaluation➢Documentation verification➢Post approval➢Hand over certificate2.4 Protocol Approval:2.4.1 All protocols are approved by Quality Assurance and Unit Headprior to their implementation i.e. after they are compiled by a teamof Production, Engineering, Quality Control and Safety.2.4.2 Each protocol should be allotted with a protocol number in theformat specified bellow“QUALI/X”Where,Patalganga STANDARD OPERATING PROCEDURENo.: MT95 EQUIPMENT QUALIFICATIONDate of Issue “QUALI” stands for qualification“X” stands for equipment / instrument / balance / area abbreviatedcode2.4.3 The protocol should also be identified with a Version No., wherethe version no. changes with every change in the Qualification,Requalification and Periodic Qualification of equipment.2.4.4 The Qualification, Requalification and Periodic Qualificationprotocol header should consist of the following details asmentioned below➢Title of the protocol➢Protocol No.➢Version No.➢Department➢Area➢Page No.A specimen of the header is given below:Patalganga STANDARD OPERATING PROCEDURENo.: MT95EQUIPMENT QUALIFICATIONDate of Issue2.4.5 Frequency for Periodic QualificationFor Critical Equipment: Once in 3 years of its previousqualification (Initial qualification / requalification)For Non Critical Equipment: Once in 5 years of its previousqualification (Initial qualification / requalification)Note: The period of periodic qualification should be determinedbased on review of history of preventive maintenance, breakdown,calibration data and criticality of process.3.0 ABBREVIATIONS:URS User Requirement SpecificationFDS Functional Design SpecificationDQ Design QualificationFAT Factory Acceptance TestIQ Installation QualificationSAT Site Acceptance TestPatalganga STANDARD OPERATING PROCEDURENo.: MT95EQUIPMENT QUALIFICATIONDate of Issue OQ Operation QualificationPQ Performance QualificationNo. NumberP&ID Piping and Instrumentation DiagramCER Capital Expenditure RequisitionCGMP current Goods Manufacturing PracticesPLC Programmable Logic Controller.MOC Material of Construction材质i.e. That ise.g. For exampleIDEMI Institute for Design of Electrical Measuring InstrumentsERTL Electronics Regional Testing LaboratoryPLC Programmable Logic ControllerHMI Human Machine InterfaceSFU Switch Fuse UnitMCB Miniature Circuit Breaker4.0 REFERENCES:CQA-06 Change ControlPatalganga STANDARD OPERATING PROCEDURENo.: MT95EQUIPMENT QUALIFICATIONDate of Issue5.0 ANNEXURES:MT95/A1 Equipment Review Report (MT95/F1)MT95/A2 Schedule for Requalification/Periodic (MT95/F2)QualificationMT95/A3 Schedule for PLC Revalidation /Periodic (MT95/F3)Validation。