飞边
飞边的标准
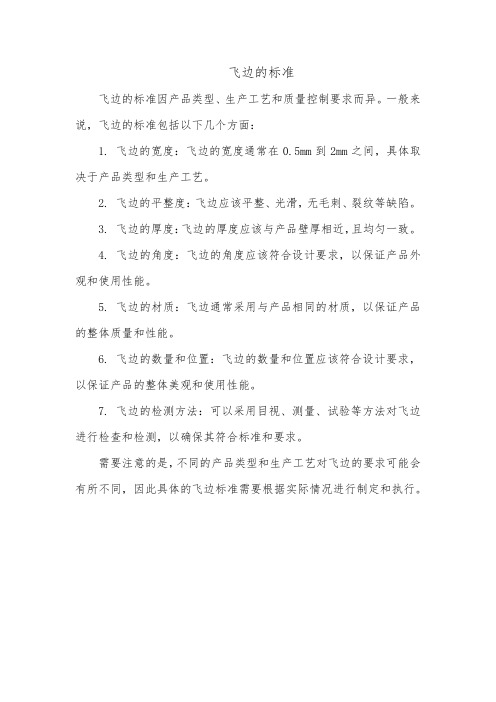
飞边的标准
飞边的标准因产品类型、生产工艺和质量控制要求而异。
一般来说,飞边的标准包括以下几个方面:
1. 飞边的宽度:飞边的宽度通常在0.5mm到2mm之间,具体取决于产品类型和生产工艺。
2. 飞边的平整度:飞边应该平整、光滑,无毛刺、裂纹等缺陷。
3. 飞边的厚度:飞边的厚度应该与产品壁厚相近,且均匀一致。
4. 飞边的角度:飞边的角度应该符合设计要求,以保证产品外观和使用性能。
5. 飞边的材质:飞边通常采用与产品相同的材质,以保证产品的整体质量和性能。
6. 飞边的数量和位置:飞边的数量和位置应该符合设计要求,以保证产品的整体美观和使用性能。
7. 飞边的检测方法:可以采用目视、测量、试验等方法对飞边进行检查和检测,以确保其符合标准和要求。
需要注意的是,不同的产品类型和生产工艺对飞边的要求可能会有所不同,因此具体的飞边标准需要根据实际情况进行制定和执行。
塑料注塑飞边是什么含义

b.模具中活动构件、滑动型芯受力不平衡时会造成飞边。
c.模具排气不良,在模具的分型面上没有开设排气槽,或排气槽太浅或太深过大,或受异物阻塞都将造成飞边。
d.当塑件壁厚不均勻时,应在制品壁厚尺寸较大的部位进料,可以防止一边缺料一边出飞边的情况。
e.当制品中央或其附近有较大成型孔时,习惯上在孔内侧开设侧浇口,在较大的注射压力下,如果合模力不足,模具的这部分支承作用力又不够时,就容易发生轻微翘曲变形造成飞边。
②塑料原料Leabharlann 度大小不均匀时会使加料量变化不定,造成塑件或不满,或飞边。
(3)模具方面
①模具分型面制造精度差活动模板(如中板)变形翘曲;分型面上沾有异物或模框周边有凸出的撬印毛刺;旧模具因早先的飞边挤压而使型腔周边疲劳塌陷等。
②模具设计不合理
a.模具型腔分布不平衡或平行度不好导致受力不平衡而造成局部飞边、局部填充不足!应在不影响塑件完整性的前提下使流道应尽量平衡布置。
飞边又称溢边、披锋、毛刺等,大多发生在模具的分型面、镶件结合面或顶出件和镶件型芯配合面上,飞边在很大程度上是由于模具制造精度差、零件变形或注塑机锁模力不足造成,原因主要有注塑机的原因、塑胶原料的原因、模具的原因以及成型工艺等方面的原因,具体分析如下。
(1)注塑机方面
①注塑机锁模力不足。选择注塑机时,注塑机的额定锁模力不能低于注射时型腔胀型力的1.25倍,否则将造成胀模,出现飞边。
②调机时,锁模机铰未伸直,或开、锁模时调模螺母经常会动而造成锁模力不足出现飞边。
③料筒、喷嘴温度太高或模具温度太髙都会使塑料黏度下降,流动性增大,在高压下进入型腔造成飞边。
④加料量过大造成飞边。值得注意的是,不要为了防止收缩凹陷而注入过多的熔料, 这样凹陷未必能“填平”,而飞边却会出现。这种情况应延长注射时间或保压时间来解决。
铸造飞边处理

铸造飞边处理
铸造飞边处理是指在铸造零件的边缘出现悬步或者其他不满意的缺陷时,采取一些特殊的方法进行修复或者脱除。
常见的铸造飞边处理方法有以下几种:
1.手工修整:采用手工工具对飞边进行切割或者打磨,以达到平整的目的。
2.机械修整:使用机械设备,如切割机、钻床、铣床等进行修整。
3.热处理:适用于大型零件和复杂形状的零件,通过加热零件来软化金属,再进行机械切割。
4.切割焊接:通过将飞边切除,再进行焊接处理,以修整零件。
5.化学除锈:采用化学方法将飞边脱除,再进行涂层等处理。
需要根据具体情况选择合适的处理方法,以保证零件质量和生产效率。
玻璃飞边工艺-概述说明以及解释
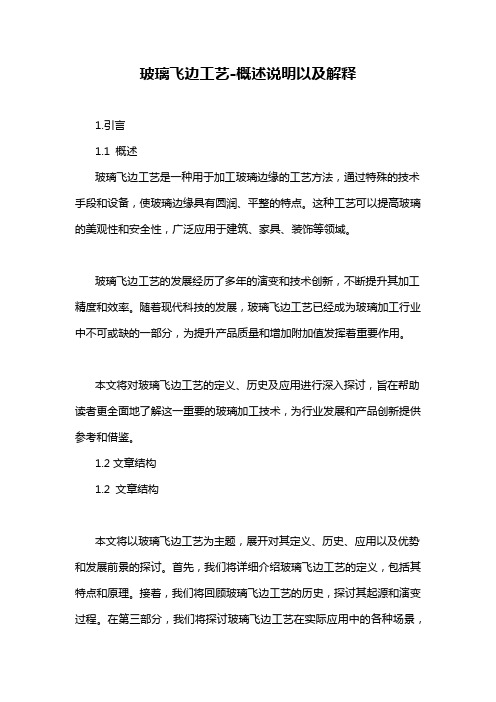
玻璃飞边工艺-概述说明以及解释1.引言1.1 概述玻璃飞边工艺是一种用于加工玻璃边缘的工艺方法,通过特殊的技术手段和设备,使玻璃边缘具有圆润、平整的特点。
这种工艺可以提高玻璃的美观性和安全性,广泛应用于建筑、家具、装饰等领域。
玻璃飞边工艺的发展经历了多年的演变和技术创新,不断提升其加工精度和效率。
随着现代科技的发展,玻璃飞边工艺已经成为玻璃加工行业中不可或缺的一部分,为提升产品质量和增加附加值发挥着重要作用。
本文将对玻璃飞边工艺的定义、历史及应用进行深入探讨,旨在帮助读者更全面地了解这一重要的玻璃加工技术,为行业发展和产品创新提供参考和借鉴。
1.2文章结构1.2 文章结构本文将以玻璃飞边工艺为主题,展开对其定义、历史、应用以及优势和发展前景的探讨。
首先,我们将详细介绍玻璃飞边工艺的定义,包括其特点和原理。
接着,我们将回顾玻璃飞边工艺的历史,探讨其起源和演变过程。
在第三部分,我们将探讨玻璃飞边工艺在实际应用中的各种场景,包括建筑、装饰和工艺品等方面。
最后,我们将分析玻璃飞边工艺的优势和未来发展前景,总结本文的主要观点和结论。
通过对这些方面的深入探讨,读者将能更好地了解和认识玻璃飞边工艺的重要性和价值。
1.3 目的本文旨在深入探讨玻璃飞边工艺这一传统工艺的定义、历史和应用,同时分析其优势和发展前景。
通过对玻璃飞边工艺的全面介绍,旨在增加读者对这一文化传统的了解,促进对这一技艺的传承和发展。
同时,本文也旨在引起读者对玻璃飞边工艺的关注,探讨如何将这一传统工艺与现代生活相结合,促进其在当代的应用和发展,实现传统文化的创新与传承。
2.正文2.1 玻璃飞边工艺的定义玻璃飞边工艺,是一种通过特殊的加工技术,使玻璃的边缘呈现出透明、圆润、无毛刺的效果。
在这种工艺中,玻璃的边缘被加热、切割和打磨,使其具有平滑的触感和优美的外观。
这种技术能够提高玻璃制品的质感和观赏性,同时也增强了其安全性和耐用性。
玻璃飞边工艺在玻璃制品的生产中起着至关重要的作用,广泛应用于玻璃家居用品、建筑玻璃等领域。
去飞边操作规程
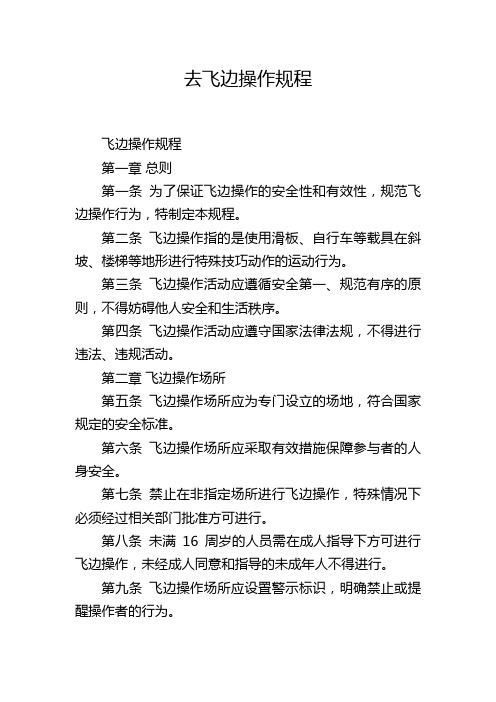
去飞边操作规程飞边操作规程第一章总则第一条为了保证飞边操作的安全性和有效性,规范飞边操作行为,特制定本规程。
第二条飞边操作指的是使用滑板、自行车等载具在斜坡、楼梯等地形进行特殊技巧动作的运动行为。
第三条飞边操作活动应遵循安全第一、规范有序的原则,不得妨碍他人安全和生活秩序。
第四条飞边操作活动应遵守国家法律法规,不得进行违法、违规活动。
第二章飞边操作场所第五条飞边操作场所应为专门设立的场地,符合国家规定的安全标准。
第六条飞边操作场所应采取有效措施保障参与者的人身安全。
第七条禁止在非指定场所进行飞边操作,特殊情况下必须经过相关部门批准方可进行。
第八条未满16周岁的人员需在成人指导下方可进行飞边操作,未经成人同意和指导的未成年人不得进行。
第九条飞边操作场所应设置警示标识,明确禁止或提醒操作者的行为。
第三章飞边操作装备第十条操作者应佩戴适合的防护装备,包括但不限于头盔、护肘、护膝等。
第十一条飞边操作器械应符合国家质量标准,确保使用安全。
第十二条佩戴装备应保持整洁,定期检查装备的使用状况,一旦发现问题应及时更换。
第四章飞边操作行为第十三条操作者应事先了解并熟悉操作场所,清楚地判断场地的安全性和适应性。
第十四条飞边操作时应保持专注,确保自身和他人的安全。
第十五条飞边操作应避免无效操作、无理操作,以免造成人员伤害。
第十六条操作者在进行飞边操作前应做好充分的热身准备,保证身体状态良好。
第十七条飞边操作时应保持速度适中,避免过快或过慢的操作,以免造成摔倒或失控。
第五章飞边操作安全第十八条飞边操作时应注意不要突然停止或急转弯,避免造成失控伤害。
第十九条飞边操作时应注意避让他人,不得与行人或其他操作者发生碰撞。
第二十条飞边操作时应注意并遵守相关信号或指示,确保行动安全。
第二十一条飞边操作者应始终保持清醒状态,不得酒后、疲劳或服用影响操作的药物。
第二十二条飞边操作行为涉及到危险动作时,应经过充分准备、安全测试和相关人员监护。
注塑产品飞边的原因和处理方法
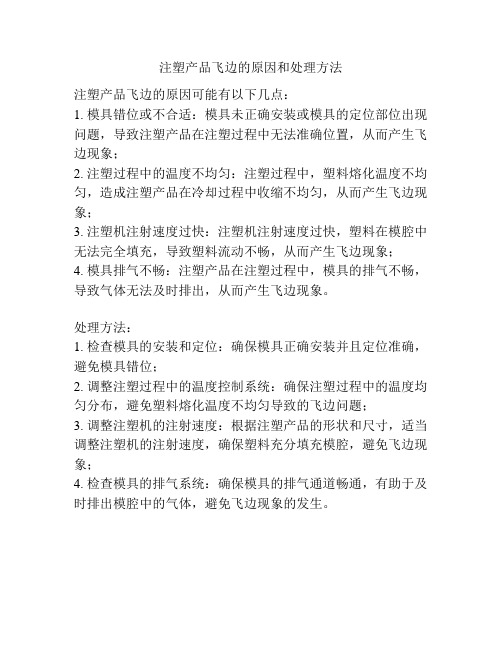
注塑产品飞边的原因和处理方法
注塑产品飞边的原因可能有以下几点:
1. 模具错位或不合适:模具未正确安装或模具的定位部位出现问题,导致注塑产品在注塑过程中无法准确位置,从而产生飞边现象;
2. 注塑过程中的温度不均匀:注塑过程中,塑料熔化温度不均匀,造成注塑产品在冷却过程中收缩不均匀,从而产生飞边现象;
3. 注塑机注射速度过快:注塑机注射速度过快,塑料在模腔中无法完全填充,导致塑料流动不畅,从而产生飞边现象;
4. 模具排气不畅:注塑产品在注塑过程中,模具的排气不畅,导致气体无法及时排出,从而产生飞边现象。
处理方法:
1. 检查模具的安装和定位:确保模具正确安装并且定位准确,避免模具错位;
2. 调整注塑过程中的温度控制系统:确保注塑过程中的温度均匀分布,避免塑料熔化温度不均匀导致的飞边问题;
3. 调整注塑机的注射速度:根据注塑产品的形状和尺寸,适当调整注塑机的注射速度,确保塑料充分填充模腔,避免飞边现象;
4. 检查模具的排气系统:确保模具的排气通道畅通,有助于及时排出模腔中的气体,避免飞边现象的发生。
固体硅胶飞边快速处理方法

固体硅胶飞边快速处理方法嘿,朋友们!今天咱就来聊聊固体硅胶飞边快速处理这档子事儿。
你说这固体硅胶飞边啊,就像那调皮的小孩子,时不时就冒出来捣乱。
那可咋整呢?别急,且听我慢慢道来。
咱可以试试用小刀片呀,就像理发师给人修头发一样,小心翼翼地把那多余的飞边给剃掉。
你想想看,是不是有点像给硅胶做个微型的“理发手术”?不过可得小心着点儿,别一不小心给硅胶弄出个“伤口”来。
或者呢,用砂纸轻轻地打磨呀。
这就好比给硅胶做个温柔的“按摩”,把那些不平整的地方慢慢磨平。
但可别太用力啦,不然把硅胶给磨坏了可就糟糕喽。
还有啊,我们可以借助一些专门的工具,就像是给我们的处理工作配上了一把“秘密武器”。
这些工具就像神奇的魔杖,轻轻一挥,那飞边就乖乖听话啦。
哎呀,你说这处理飞边是不是也挺有讲究的呀!要是处理不好,那可就影响美观和使用啦。
这就好像一件漂亮的衣服上有个显眼的线头,多让人别扭呀!咱可不能小瞧了这固体硅胶飞边的处理,这可是个细致活儿呢。
就跟绣花似的,得一针一线慢慢来。
要是马马虎虎的,那最后出来的效果肯定不咋地。
你想想,要是你精心制作的一个硅胶制品,因为飞边没处理好而变得不完美,那多可惜呀!所以呀,处理飞边的时候咱可得认真点儿,就像对待一件珍贵的宝贝一样。
其实呀,生活中很多事情不都跟这固体硅胶飞边处理一样嘛。
都需要我们细心、耐心,还得掌握好方法。
就像做饭,调料放多放少都会影响味道;又好比画画,一笔一划都得恰到好处。
咱可别嫌麻烦,毕竟只有把这些小细节处理好了,才能让事情变得更加完美呀。
你说是不是这个理儿?所以呀,下次再遇到固体硅胶飞边的问题,就按照我说的这些方法试试吧,保准让你的硅胶制品变得漂漂亮亮的!让那些飞边都乖乖消失不见!。
飞边

飞边(1)何谓飞边(外观)?虽然制作模具时精度很高(μm级),而且成型时采用高压合模,但由于树脂的填充压力也很高,所以实际上留有很小的缝隙。
飞边就是因树脂进入这种缝隙而形成的。
在PL面、套管、滑芯界面和排气口等处都会出现飞边。
飞边就是树脂挤入模具PL面(模具的分型面),并使制品带上了多余的薄膜这样一种现象。
当PL面不敌树脂压力而分开,或PL面有缝隙时就会出现这种情况。
图1. 平板PL面上出现的飞边(2)飞边的生成原因(2-1) 树脂压力偏高树脂压力过高时,模具分开并产生飞边。
相反,模具压力偏低时,同样也容易产生飞边。
树脂压力增高的主要原因如下:(1)注射速度偏快(2)注射压力偏高(3)保压力偏高(4)V-P切换偏慢一般来说,当希望获得良好的外观时,有时会将保压设定的过高,特别是为了防止出现凹痕而采用高于标准的设定。
这样一来有时就会产生飞边。
图2. 树脂压力偏高时容易出现飞边(2-2) 树脂流动性好流动性越好,树脂就越容易进入缝隙,因此飞边也就越大。
一般来说,树脂温度和模具温度越高,飞边也就越大;反之,温度越低,飞边也就越小。
(2-3) 模具的PL面有间隙即使在简单的2块式模具中,模具有时也会因成型品顶出不当而受损,并在损伤处出现飞边。
使用滑芯时,必须特别注意吻合以及滑动面的缝隙。
另外,模具是钢制的,合模压属于高压,而树脂压也是与其相当的高压,所以在几乎所有的注射成型中,模具一般都会发生变形。
特别是在大型成型品的情况下尤为显著。
此时,有无支柱对飞边也有影响(如果没有支柱,变形→缝隙就会增大,飞边也会增多)。
图3. PL面的细微间隙中产生飞边(2-4) Fortron PPS(聚苯硫醚)PSS树脂在低剪切区的流动性很强,因此该树脂就其本身的性质而言就具有容易产生飞边的缺点。
因此,与使用其他材料时相比,使用PPS树脂时必须更加注意防止出现飞边。
此时对模具精度等级的要求也比使用其他材料时更加严格。
(3)飞边的对策(3-1) 降低树脂压力降低树脂压力的方法如下:(1)延缓注射速度(2)降低注射压力(3)降低保压力(4)略微加快V-P切换(3-2) 检查合模力虽说是一件很平常的事,但还是要检查一下是否存在设定错误。
探讨铸造飞边缺陷的成因及对策
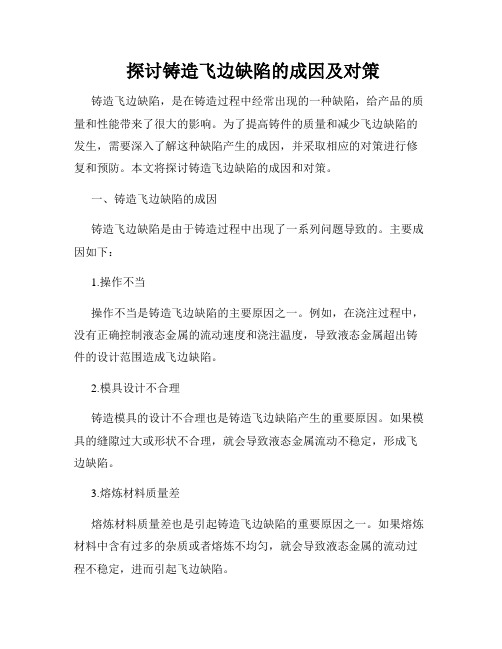
探讨铸造飞边缺陷的成因及对策铸造飞边缺陷,是在铸造过程中经常出现的一种缺陷,给产品的质量和性能带来了很大的影响。
为了提高铸件的质量和减少飞边缺陷的发生,需要深入了解这种缺陷产生的成因,并采取相应的对策进行修复和预防。
本文将探讨铸造飞边缺陷的成因和对策。
一、铸造飞边缺陷的成因铸造飞边缺陷是由于铸造过程中出现了一系列问题导致的。
主要成因如下:1.操作不当操作不当是铸造飞边缺陷的主要原因之一。
例如,在浇注过程中,没有正确控制液态金属的流动速度和浇注温度,导致液态金属超出铸件的设计范围造成飞边缺陷。
2.模具设计不合理铸造模具的设计不合理也是铸造飞边缺陷产生的重要原因。
如果模具的缝隙过大或形状不合理,就会导致液态金属流动不稳定,形成飞边缺陷。
3.熔炼材料质量差熔炼材料质量差也是引起铸造飞边缺陷的重要原因之一。
如果熔炼材料中含有过多的杂质或者熔炼不均匀,就会导致液态金属的流动过程不稳定,进而引起飞边缺陷。
二、铸造飞边缺陷的对策针对铸造飞边缺陷的成因,可以采取以下对策进行修复和预防。
1.优化操作流程通过优化操作流程,改善操作人员的技术水平和操作技巧,减少因操作不当引起的飞边缺陷。
例如,在浇注过程中,严格控制液态金属的流动速度和浇注温度,确保其不超出铸件的设计范围。
2.优化模具设计对于存在飞边缺陷的铸造模具,应该优化模具设计,通过减小模具缝隙或改变模具形状等方式,改善液态金属的流动性,从而减少飞边缺陷的发生。
3.优化熔炼材料通过优化熔炼材料的质量,减少杂质的含量,改善材料的熔炼过程,可以有效降低液态金属的不稳定性,进而减少飞边缺陷的产生。
4.采用预防措施除了以上对策,还可以采取一些预防措施来减少铸造飞边缺陷的发生。
例如,在模具设计阶段,应该尽量避免设计过于复杂的铸造模具;在操作过程中,应该定期检查设备的状态,及时修复设备的故障。
总结:铸造飞边缺陷是铸造过程中常见的一种缺陷,会影响铸件的质量和性能。
通过深入了解铸造飞边缺陷的成因,并采取相应的对策进行修复和预防,可以提高铸件的质量,减少飞边缺陷的发生。
飞边的产生和改良

1.何谓飞边(外观)?飞边就是因树脂进入这种缝隙而形成的。
在PL面、套管、滑芯界面和排气口等处都会出现飞边。
2.飞边的生成原因a.树脂压力偏高:1.注射速度偏快 2.注射压力偏高 3.保压力偏高 4.V-P切换偏慢b.树脂流动性好c.模具的PL面有间隙3.飞边的对策a.降低树脂压力:1.延缓注射速度 2.降低注射压力 3.降低保压力 4.略微加快V-P切换b.检查合模力c.加快树脂固化d.检查模具PL面气泡的产生和改良2.1.何谓气泡(外观)气泡是指成型品表面鼓起的一种现象。
注射成型后从模具取出时,制品表面开始渐渐鼓起和成型品表面因受热膨胀而鼓起时。
2.气泡的生成原因a.卷入空气 :螺杆转速快、背压低并且抽塑量多的时候容易产生气泡b.表层容易剥离c.树脂中产生大量气体3.气泡的对策a.减少空气卷入: 1.降低螺杆转速2.提高背压3.抽塑量设定不要过多b.使层间难以剥离: 1.提高模具温度2.·减慢注射速度 3.·增大浇口4.增加厚度(仅对于过薄的部分)5.避免产生喷射纹c.抑制气体的产生3.1.何谓凹痕(外观)?“凹痕”是指因树脂收缩而产生坑凹的一种现象。
结晶性树脂冷却固化后,体积会大幅度减少。
凹痕便是因此而产生的。
因为收缩比率(收缩率)大致固定,而且厚度越厚收缩量越多,所以凹痕一般是在成型品的较厚部分产生的。
2.凹痕的生成原因a.有效保压偏低:树脂填补偏少=> 1.保压设定值偏低2.保压时间偏短 3.浇口尺寸偏小 4.分流道偏细b. 缓慢冷却:收缩量偏多3.凹痕的对策a.尝试提高保压b.尝试降低模具温度c.减小厚度可以认为施加保压=增加树脂的填补量。
与其单纯地提高保压的设定值,倒不如使用多段保压来阶段性地提高保压会更有效。
此外,为了更容易施加保压,还可采取这样一种有效的处理方法,即扩大主流道和分流道,并将浇口移至凹痕附近。
银纹的产生和改良4.1.何谓银纹(外观)?银纹是指成型品表面出现气体或空气的一种现象。
注塑飞边解决方法
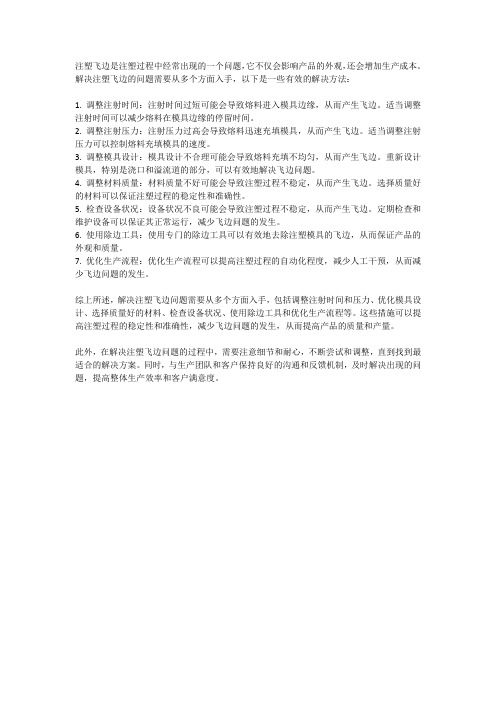
注塑飞边是注塑过程中经常出现的一个问题,它不仅会影响产品的外观,还会增加生产成本。
解决注塑飞边的问题需要从多个方面入手,以下是一些有效的解决方法:1. 调整注射时间:注射时间过短可能会导致熔料进入模具边缘,从而产生飞边。
适当调整注射时间可以减少熔料在模具边缘的停留时间。
2. 调整注射压力:注射压力过高会导致熔料迅速充填模具,从而产生飞边。
适当调整注射压力可以控制熔料充填模具的速度。
3. 调整模具设计:模具设计不合理可能会导致熔料充填不均匀,从而产生飞边。
重新设计模具,特别是浇口和溢流道的部分,可以有效地解决飞边问题。
4. 调整材料质量:材料质量不好可能会导致注塑过程不稳定,从而产生飞边。
选择质量好的材料可以保证注塑过程的稳定性和准确性。
5. 检查设备状况:设备状况不良可能会导致注塑过程不稳定,从而产生飞边。
定期检查和维护设备可以保证其正常运行,减少飞边问题的发生。
6. 使用除边工具:使用专门的除边工具可以有效地去除注塑模具的飞边,从而保证产品的外观和质量。
7. 优化生产流程:优化生产流程可以提高注塑过程的自动化程度,减少人工干预,从而减少飞边问题的发生。
综上所述,解决注塑飞边问题需要从多个方面入手,包括调整注射时间和压力、优化模具设计、选择质量好的材料、检查设备状况、使用除边工具和优化生产流程等。
这些措施可以提高注塑过程的稳定性和准确性,减少飞边问题的发生,从而提高产品的质量和产量。
此外,在解决注塑飞边问题的过程中,需要注意细节和耐心,不断尝试和调整,直到找到最适合的解决方案。
同时,与生产团队和客户保持良好的沟通和反馈机制,及时解决出现的问题,提高整体生产效率和客户满意度。
铝板飞边工艺

铝板飞边工艺我呀,在铝制品加工这个圈子里也混了好些年了。
今天就想和大家唠唠铝板飞边工艺,这可真是个相当有趣又特别重要的工艺呢。
铝板飞边,就像是给铝板做一场精致的边缘整形手术。
你想啊,一块铝板,刚从生产线上下来的时候,边缘往往是粗糙的,就像一个没经过打扮的小姑娘,虽然有着成为美人的潜力,但是还缺那么点精致感。
而飞边工艺就是那把神奇的化妆刷,能把铝板的边缘变得光滑、整齐,还能根据需求做出各种造型。
我有个朋友,老张,他刚开加工厂那会儿,对铝板飞边工艺那是一知半解的。
他就觉得不就是把边缘弄弄整齐嘛,能有多难。
结果呢,他第一批加工出来的铝板,边缘那叫一个参差不齐。
客户看到后,皱着眉头说:“老张啊,你这铝板边缘就像狗啃的一样,这可不行啊。
”老张那叫一个沮丧,就像霜打的茄子。
他这才意识到,铝板飞边工艺可不是闹着玩的。
那铝板飞边到底是怎么个流程呢?首先得有合适的设备。
就像厨师做菜得有好的厨具一样。
这设备得能够精准地对铝板边缘进行操作。
有了设备,操作工人的技术也是关键。
这工人啊,就像是个艺术家,他得根据铝板的厚度、材质以及最终的要求,来调整设备的参数。
你说这是不是像画家根据画布和想要表达的意境来调配颜料一样?我曾经见过一个特别厉害的师傅,老李。
他在进行铝板飞边的时候,那专注的眼神,就像老鹰盯着猎物一样。
他的手稳稳地操作着设备,那铝板的边缘在他手下就像是听话的孩子,一点点变得完美。
我就好奇地问他:“老李啊,你这技术咋练的啊?”他笑着说:“这就和你练书法一样,得多练,还得用心琢磨。
每块铝板都有它自己的脾气,你得摸透了才能做出好的飞边。
”铝板飞边工艺在很多地方都有着至关重要的作用。
比如说在建筑行业,那些铝板幕墙。
如果铝板边缘不经过飞边处理,参差不齐的边缘不仅影响美观,还可能会有安全隐患呢。
想象一下,一栋大楼的铝板幕墙,边缘像锯齿一样,多吓人啊。
这就好比一个人穿着破破烂烂的衣服,还露着线头,怎么能算得上是得体呢?再比如说在一些铝制家具上,精致的飞边能够让家具看起来更加高档,摸起来也不会刮手。
注塑件飞边解决方法

注塑件飞边解决方法英文回答:Injection molding is a widely used manufacturingprocess for producing plastic parts. However, one common issue that can occur during the injection molding processis the occurrence of flash, also known as burrs or flying edges. Flash refers to the excess material that escapesfrom the mold cavity and forms thin, unwanted edges or protrusions on the final plastic part. Flash can negatively affect the appearance, functionality, and quality of the injection molded parts.There are several methods to address the issue of flash in injection molded parts. One effective approach is to optimize the design of the mold. By carefully designing the mold, engineers can minimize the occurrence of flash. This can be achieved by ensuring proper venting and gating, as well as optimizing the parting line and mold surface finish.A well-designed mold can help control the flow of themolten plastic and prevent excess material from escaping.Another method to address flash is through process optimization. By adjusting the injection molding process parameters, such as the injection speed, pressure, and temperature, engineers can minimize the occurrence of flash. It is important to find the right balance between filling the mold cavity completely and avoiding excessive pressure that can lead to flash. Process optimization requirescareful monitoring and adjustment of the injection molding machine settings.Furthermore, using high-quality materials can also help reduce flash in injection molded parts. Choosing materials with good flow properties and low shrinkage can minimizethe occurrence of flash. Additionally, using additives,such as mold release agents or anti-flash agents, can help prevent flash formation during the injection molding process.Regular maintenance and inspection of the injection molding equipment is also crucial in preventing flash. Anyworn or damaged components, such as the mold, nozzle, or screws, should be promptly repaired or replaced to ensure proper functioning of the machine. Proper maintenance can help prevent material leakage and reduce the occurrence of flash.In conclusion, flash in injection molded parts can be effectively addressed through various methods. These include optimizing the mold design, adjusting the injection molding process parameters, using high-quality materials, and regular equipment maintenance. By implementing these strategies, manufacturers can minimize the occurrence of flash and produce high-quality injection molded parts.中文回答:注塑是一种广泛应用于生产塑料零件的制造工艺。
压飞边工艺

压飞边工艺压飞边工艺,这听起来好像有点神秘,其实就像给一块刚出炉的精美糕点修边儿一样。
你看啊,糕点做出来的时候,周围可能会有些不整齐、多余的部分,这就好比是工件在制造过程中产生的飞边。
咱们得把这些多余的部分处理得干干净净,才能让糕点看起来更精致,让工件达到更好的使用效果。
那什么是压飞边工艺呢?简单说,就是把工件上那些多余的、不规整的飞边给压掉或者修整好。
比如说你看到的那些金属零件,在铸造或者锻造的时候,就像面团发酵膨胀一样,边缘部分可能会多出一些材料,这多出来的材料就是飞边啦。
这飞边要是不管它呀,就好比一个漂亮的新衣服上有好多线头,多影响美观啊,而且还可能影响零件的装配和使用性能呢。
咱先说这压飞边的设备吧。
这设备就像是一个超级大力士,专门负责把飞边给制服。
有各种各样的压力机,它们就像不同性格的人。
有的压力机是那种慢慢用力,稳稳当当的,就像一个经验丰富的老师傅,一点一点地把飞边给压平。
还有的压力机呢,力气特别大,动作也快,就像一个年轻气盛的小伙子,一下子就能把飞边处理得差不多。
这些设备的压力大小得调整好,就跟炒菜放盐一样,放多了太咸,放少了没味道。
压力大了可能会把工件本身弄坏,压力小了飞边又压不掉,多麻烦呐。
再说说这压飞边的模具吧。
模具可重要啦,它就像给工件量身定做的一个小夹子。
这个夹子的形状得和工件边缘特别贴合才行。
要是模具不合适,就好比你穿了一双不合脚的鞋子,走起路来别提多难受了。
模具的材质也有讲究,得又硬又耐磨,不然压几次飞边,模具自己就先坏掉了,那可不成。
就像一个战士上战场,自己的武器都不结实,怎么打胜仗呢?在进行压飞边工艺的时候啊,操作的人也得特别细心。
这就像绣花一样,得一针一线地来。
操作工人得时刻盯着工件和设备,就像妈妈看着自己的小宝贝一样,容不得一点差错。
要是稍微一走神,可能就会把工件压坏了,这多可惜呀。
这就跟你好不容易画了一幅特别漂亮的画,结果一不小心滴了一大滴墨在上面一样,前面的功夫都白费了。
TPR.TPR注塑成型制品易出现缺陷,原因,解决全方案

TPR/TPE注塑成型制品易出现缺陷,原因,解决方案1. TPR/TPE等注塑成型的制品易出现飞边注塑零件飞边又称溢边或者披锋,大多发生在模具上模块相结合的位置。
如:分型面、顶针的孔隙、滑块的配合部位、镶件的缝隙、顶针的孔隙等处。
飞边不及时修正可能会影响产品外观或影响充模过程中的排气;若飞边过大,脱模过程中产生的碎屑可能会残留在模具内部,导致产品出现冷料,严重的还会使模具产生永久性压痕,如果碎屑残留在运动部件,如滑块、顶针等处,还可能导致模具运动不畅。
第一、设备方面(1)成型机合模力不足。
如果成型机的额定合模力小与成型过程中制品从像投影面积上的张力,将会导致分型面间隙,造成飞边。
TPR/TPE注塑缺陷问题解决方案:增大锁模力(2)成型机合模形成不足。
如果成型机合模的最小间隙大于模具的厚度,制品的投影面积超过了注压机的最大注射面积,注压机模板安装调节不正确,模具安装不正确,锁模力不能保持恒定,注压机模板不平行,拉杆变形不均将会导致模具合模不紧密造成飞边。
TPR/TPE注塑缺陷问题解决方案:改进注塑机缺陷第二、模具方面(1)模具本身精度差,如分型面配合不严密;分型面有压痕或疲劳塌陷;分型面间隙过大;TPR/TPE注塑缺陷问题解决方案:改进模具设计(2) 设计不合理,如型腔分布不对称,导致成型时张力不均容易产生分型面飞边;顶出机构不对称,导致顶出时顶针受到扭力,也会产生飞边;排气间隙过大;型腔和型芯对插结构过多;型腔和型芯偏移;模板不平行;模板变形;模子平面落入异物;排气不足;排气孔太大;第三、工艺方面(1) 注射压力过高或速度过快,产生高速高压熔体,导致模具接合部位出现弹性变形,从而产生飞边。
TPR/TPE注塑缺陷问题解决方案:降低注塑速度(2) 温度过高:无论是料筒温度、喷嘴温度还使模具温度过高,都将使塑料熔体黏度下降,流动性增强从而在模块接合部位产生飞边。
TPR/TPE注塑缺陷问题解决方案:降低温度(3)计量过大,会使模具内产生局部高压,如果发生在模块接合部位,将产生飞边。
o型圈去飞边方法

o型圈去飞边方法
O型圈去飞边的常用方法主要包括以下几种:
1.机械去飞边:使用机械工具,如磨石、抛光轮等,对
O型圈进行研磨和抛光,以去除飞边。
这种方法适用于各种材质的O型圈,并且可以获得较好的表面质量。
2.热去飞边:将O型圈加热至一定温度,使其软化并易
于去除飞边。
这种方法适用于热塑性塑料材质的O型圈,但
不适合金属材质的O型圈。
3.化学去飞边:使用化学试剂对O型圈进行腐蚀或溶
解,以去除飞边。
这种方法适用于某些特定材质的O型圈,
如某些塑料或橡胶材质。
4.激光去飞边:使用激光高能束对O型圈表面进行烧蚀
和剥离,以去除飞边。
这种方法具有高精度、高效率和高表面质量等优点,但设备成本较高。
这些方法都可以有效地去除O型圈的飞边,具体选择哪种方法取决于O型圈的材质、尺寸和生产要求等因素。
注塑制品有溢料(飞边)现象
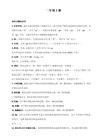
(1)模具分型面精度差。活动模板(如中板)变形翘曲;分型面上沾有异物或模框周边有凸出的橇印毛刺;旧模具因早先的飞边挤压而使型腔周边疲劳塌陷。
(2)模具设计不合理。模具型腔的开设位置过偏,会令注射时模具单边发生张力,引起飞边;塑料流动性太好,如聚乙烯、聚丙烯、尼龙等,在熔融态下黏度很低,容易进入活动的或固定的缝隙,要求模具的制造精度较高;在不影响制品完整性的前提下应尽量安置在质量对称中心上,在制品厚实的部位入料,可以防止一边缺料一边带飞边的情况;当制品中央或其附近有成型孔时,习惯上在孔上开设侧浇口,在较大的注射压力下,如果合模力不足模的这部分 支承作用力不够发生轻微翘曲时造成飞边,如模具侧面带有活动构件时,其侧面的投影面积也受成型压力作用,如果支承力不够也会造成飞边;滑动型芯配合精度不良或固定型芯与型腔安装位置偏移而产生飞边;型腔排气不良,在模的分型面上没有开排气沟或排气沟太浅或过深过大或受异物阻塞都将造成飞边;对多型腔模具应注意各分流道合浇口的合理设计,否则将造成充模受力不均而产生飞边。
(3)机筒、喷嘴温度太高或模具温度太高都会使塑料黏度下降,流动性增大,在流畅进模的情况下造成飞边。
四 原料方面
(1)塑料黏度太高或太低都可能出现飞边。黏度低的塑料如尼龙、聚乙烯、聚丙烯等,则应提高合模力;吸水性强的塑料或对水敏感的塑料在高温下会大幅度的降低流动黏度,增加飞边的可能性,对这些塑料必须彻底干燥;掺入再生料太多的塑料黏度也会下降,必要时要补充滞留成分。塑料黏度太高,则流动阻力增大,产生大的背压使模腔压力提高,造成合模力不足而产生飞边。
(1)机器真正的合模力不足。选择注塑机时,机器额定合模力必须高于注射成型制品纵向投影面积在注射时形成的张力,否则将造成胀模,出现飞边。
(2)合模装置调节不佳,肘杆机构没有伸直,产生或左右或上下合模不均衡,模具平行度不能达到的现象造成模具单侧一边被合紧而另一边不密贴的情况,注射时将出现飞边。
- 1、下载文档前请自行甄别文档内容的完整性,平台不提供额外的编辑、内容补充、找答案等附加服务。
- 2、"仅部分预览"的文档,不可在线预览部分如存在完整性等问题,可反馈申请退款(可完整预览的文档不适用该条件!)。
- 3、如文档侵犯您的权益,请联系客服反馈,我们会尽快为您处理(人工客服工作时间:9:00-18:30)。
二溢料飞边故障分析及排除方法(1)合模力不足。
当注射压力大于合模力使模具分型面密合不良时容易产生溢料飞边。
对此,应检查增压是否增压过量,同时应检查塑件投影面积与成型压力的乘积是否超出了设备的合模力。
成型压力为模具内的平均压力,常规情况下以40mpa计算。
生产箱形塑件时,聚乙烯,聚丙烯,聚苯乙烯,及ABS的成型压力值约为30mpa;生产形状较深的塑件时,成型压力值约为36mpa;在生产体积小于10cm3的小型塑件时,成型压力值约为60mpa。
如果计算结果为合模力小于塑件投影面积与成型压力的乘积,则表明合模力不足或注塑定位压力太高。
应降低注射压力或减小注料口截面积,也可缩短保压及增压时间,减小注射行程,或考虑减少型腔数及改用合模吨位大的注塑机。
(2)料温太高。
高温熔体的熔体粘度小,流动性能好,熔料能流入模具内很小的缝隙中产生溢料飞边。
因此,出现溢料飞边后,应考虑适当降低料筒,喷嘴及模具温度,缩短注射周期。
对于聚酰胺等粘度较低的熔料,如果仅靠改变成型条件来解决溢料飞边缺陷是很困难的。
应在适当降低料温的同时,尽量精密加工及修研模具,减小模具间隙。
(3)模具缺陷。
模具缺陷是产生溢料飞边的主要原因,在出现较多的溢料飞边时必须认真检查模具,应重新验核分型面,使动模与定模对中,并检查分型面是否密着贴合,型腔及模芯部分的滑动件磨损间隙是否超差。
分型面上有无粘附物或落入异物,模板间是否平行,有无弯曲变形,模板的开距有无按模具厚度调节到正确位置,导合销表面是否损伤,拉杆有无变形不均,排气槽孔是否太大太深。
根据上述逐步检?榈慕峁杂诓奈蟛羁刹捎没导庸さ姆椒ㄓ枰耘懦?BR>(4)工艺条件控制不当。
如果注射速度太快,注射时间过长,注射压力在模腔中分布不均,充模速率不均衡,以及加料量过多,润滑剂使用过量都会导致溢料飞边,操作时应针对具体情况采取相应的措施。
值得重视的是,排除溢料飞边故障必须先从排除模具故障着手,如果因溢料飞边而改变成型条件或原料配方,往往对其他方面产生不良影响,容易引发其他成型故障。
三熔接痕故障分析及排除方法(1)温太低。
低温熔料的分流汇合性能较差,容易形成熔接痕。
如果说塑件的内外表面在同一部位产生熔接细纹时,往往是由于料温太低引起的熔接不良。
对此,可适当提高料筒及喷嘴温度或者延长注射周期,促使料温上升。
同时,应节制模具内冷却水的通过量,适当提高模具温度。
一般情况下,塑件熔接痕处的强度较差,如果说对模具中产生熔接痕的相应部位进行局部加热,提高成型件熔接部位的局部温度,往往可以提高塑件熔接处的强度。
如果由于特殊需要,必须采用低温成型工艺时,可适当提高注射速度极增加注射压力,从而改善熔料的汇合性能。
也可在原料配方中适当增用少量润滑剂,提高熔料的流动性能。
(2)模具缺陷。
模具浇注系统的结构参数对流料的熔接状况有很大的影响,因为熔接不良主要产生于熔料的分流汇合。
因此,应尽量采用分流少的浇口形式并合理选择浇口位置,尽量避免充模速率不一致及充模料流中断。
在可能的条件下,应选用一点式浇口,因为这种浇口不产生多股料流,熔料不会从两个方向汇合,容易避免熔接痕。
如果模具的浇注系统中,浇口太多或太小,多浇口定位不正确或浇口到流料熔接处的间距太大,浇注系统的主流道进口部位及分流道的流道截面太小,导致料流阻力太大都会引起熔接不良,使塑件表面产生较明现的熔接痕。
对此,应尽可能减少浇口数,合理设置浇口位置,加大浇口截面,设置辅助流道,扩大主流道及分流道直径。
为了防止低温熔料注入模腔产生熔接痕,应在提高模具温度的同时在模具内设置冷料穴。
此外,塑件熔接痕的产生部位经常由于高压充模而产生飞边,而且产生这类飞边后熔接痕不会产生缩孔,因此这类飞边往往不作为故障排除,而是在模具上产生飞边的部位开一很浅的小沟槽,将塑件上的熔接痕转移到附加的飞边小翼上,待塑件成型后再将小翼除去,这也是排除熔接痕故障时常用的一种方法。
(3)模具排气不良,当熔料的熔接线与模具的合模线或嵌缝重合时,模腔内多股流料赶压的空气能从合模缝隙或嵌缝处排出;但当熔接线与合模线或嵌缝不重合,且排气孔设置不当时,模腔内被流料赶压的残留空气便无法排出,气泡在高压下被强力挤压,体渐渐变小,最终被压缩成一点,由于被压缩的空气的分子动能在高压下转变为热能,因而导致熔料汇料点处的温度升高,当其温度等于或略高于原料的分解温度时,熔接点处便出现黄点,若其温度远高于原料的分解温度时,熔接点处便出现黑点。
一般情况下,塑件表面熔接痕附近出现的这类斑点总是在同一位置反复出现,而且出现的部位总是规律性地出现在汇料点处,在操作过程中,应不要将这类斑点误认为杂质斑点。
产生这类斑点的主要原因是?捎谀>吲牌涣迹侨哿细呶路纸夂笮纬傻奶蓟恪?BR>出现这类故障后,首先应检查模具排气孔是否被熔料的固化物或其他物体阻塞,浇口处有无异物。
如果阻塞物清除后仍出现碳化点,应在模具汇料点处增加排气孔。
也可通过重新定位浇口或适当降低合械力,增大排气间隙来加速汇料合流。
在工艺操作方面,也可采取降低料温及模具温度,缩短高压注射时间,降低注射压力等辅助措施。
(4)脱模剂使用不当。
脱模剂用量太多或选用的品种不正确都会引起塑件表面产生熔接痕。
在注射成型中,一般只在螺纹等不易脱模的部位才均匀地涂用少量脱模剂,原则上应尽量减少脱模剂的用量。
对于各种脱模剂的选用,必须根据成型条件,塑件外形以及原料品种等条件来确定。
例如,纯硬脂酸锌可用于除聚酰胺及透明塑料外的各种塑料,但与油混合后即可用于聚酰胺和透明塑料。
又如硅油甲苯溶液可用于各种塑料,而且涂刷一次可使用很久,但其涂刷后需加热烘干,用法比较复杂。
(5)塑件结构设计不合理。
如果塑件壁厚设计的太薄可厚薄悬殊以及嵌件太多,都会引起熔接不良。
薄壁件成型时,由于熔料固化太快,容易产生缺陷,而且熔料在充模过程中总是在薄壁处汇合形成熔接痕,一旦薄壁处产生熔接?郏突岬贾滤芗的强度降低,影响使用性能。
因此,在设计塑件形体结构时,应确保塑件的最薄部位必须大于成型时允许的最小壁厚。
此外,应尽量减少嵌件的使用且壁厚尽可能趋于一致?BR>(6)其他原因。
当使用的原料水分或易挥发物含量太高,模具中的油渍末清洗干净,模腔中有冷料或熔料内的纤维填料分布不良,模具冷却系统设计不合理,熔料固化太快,嵌件温度太低,喷嘴孔太小,注塑机塑化能力不够,注塑机料筒中压力损失太大,都会导致不同程度的熔接不良。
对此,在操作过程中,应针对不同情况,分别采取原料预干燥,定期清理模具,改变模具冷却水道设置,控制冷却水的流量,提高嵌件温度,换用较大孔径的喷嘴,改用较大规格的注塑机等措施予以解决。
四波流痕故障分析及排队除方法:(1)熔料流动不良导致塑件表面产生以浇口为中心的年轮状波流痕。
当流动性能较差的低温高粘度熔料在注料口及流道中以半固化波动状态注入型腔后,熔料沿模腔表面流动并被不断注入的后续熔料挤压形成回流及滞流,从而在塑件表面产生以浇口为中心的年轮状波流痕。
针对这一故障产生的原因,可分别采取提高模具及喷嘴温度,提高注射速率和充模速度。
增加注射压力及保压和增加时间。
也可在浇口处设置加热器增加浇口部位的局部温度。
还可适当扩大浇口和流道截面积。
而浇口及流道截面最好采用圆形,这种截面能够获得最佳充模。
但是,如果在塑件的薄弱区域设置浇口,应采用正方形截面。
此外,注料口底部及分流道端部应设置较大的冷料穴,料温对熔料的流动性能影响较大,越要注意冷料穴尺寸的大小,冷料穴的位置必须设置在熔料沿注料口流动方向的端部。
如果产生年轮状波流痕的主要原因是树脂性能较差时,可在条件充许的情况下,选用低粘度的树脂。
(2)熔料在流道中流动不畅导致塑件表面产生螺旋状波流痕。
当熔料从流道狭小的截面流入较大截面的型腔或模具流道狭窄,光洁度很差时,流料很容易形成湍流,导致塑件表面形成螺旋状波流痕。
对此,可适当降低注射速度或对注射速度采取慢,快,慢分级控制。
模具的浇口应设置在厚壁部位或直接在壁侧设置浇口,浇口形式最好采用柄式,扇形或膜片式。
也可适当扩大流道及浇口截面,减少流料的流动阻力。
此外,应节制模具内冷却水的流量,使模具保持较高的温度。
若在工艺操作温度范围内适当提高料筒及喷嘴温度,有利于改善熔料的流动性能。
(3)挥发性气体导致塑件表面产生云雾状波流痕。
当采用ABS或其他共聚树脂原料时,若加工温度较高,树脂及润滑剂产生的挥发性气体会使塑件表面产生云雾状波流痕。
对此,应适当降低模具及机筒温度,改善模具的排气条件,降低料温及充模速率,适当扩大浇口截面,还应考虑更换润滑剂品种或减少数量。
五浇口附近表面混浊及斑纹故障分析及排除方法体破裂。
熔体注入型腔后先在模具腔壁上形成一层薄的表壳,当这层表壳在充模过程中受到后续熔料的挤压时,就会导致熔体破裂。
一旦很薄的表壳被撕破或发生移动,塑件表面即产生搓痕或皱纹。
例如,在熔体指数较小的低密度聚乙烯塑件上,其表面径常可以看到明暗交替的条形区域,其产生的部位一般离浇口有一定距离,并遍布整个表面,尤其是薄壁塑件最容易产生这类故障,这主要是由于熔料在充填小熔腔尚未结束前受到较大的压力,导致熔体破裂,形成表面缺陷。
通常,减慢熔料在充模过程中的冷却速度和表壳层的形成速率是消除这类故障的最好办法,可以通过适当提高模具温度或提高熔体破裂部位的局部温度来排除这一故障。
对于模腔表面的局部加热,可利用安装在浇口附近及熔体破裂部位的小型管式电加热器来实现。
(2)熔料在模腔内产生不规则脉冲流动。
熔料的流动特性与其流变性能有关,还与决定熔料在模具入口处剪切速率的浇口截面积有关。
当浇口尺寸很小而注射速率很高时,熔料是以细而弯曲的射流态注入型腔的,若熔料的冷却速度很快,就会与后续充模的不规则流料熔合不良,导致浇口附近产生表面混浊及斑纹。
有时,少量冷料会沿着模腔表面移动,使表面混浊及斑纹产生在离浇口较远的部位。
通常,结晶型聚合物注射时产生的表面混浊及斑纹较难排除,因为这类树脂的熔融温度相当高,与非结晶型聚合物相比,结晶型聚合物的固化速度快,加工温度区域窄,而且在壁厚急剧变化和熔料突然改变流动方向处产生的不规则流动熔料与其余熔料在型腔中熔合的时间也比较短,很容易产生表面混浊及斑纹。
对于排除这类故障,在工艺操作方面,应适当提高模具,料筒及喷嘴温度,降低注射时螺杆的前进速度。
在模具操作方面,应扩大浇口尺寸,优先选用扇形浇口,如果采用隧道型浇口,其顶部尺寸太小会使浇口处的残料杂质影响充模,加剧流料的不规则流动,应适当加大其顶部尺寸;若模具排气不良,也会影响流料的规则性流动,应予以改进。
此外,应减少润滑剂的用量并选择适宜的品种。
六裂纹及破裂故障分析及排除方法残余应力太高。
当塑件内的残余应力高于树脂的弹性极限时,塑件表面就会产生裂纹及破裂。