TPM讲座 概要(DFLZZ见直し日文) 中文译稿
TPM发言稿
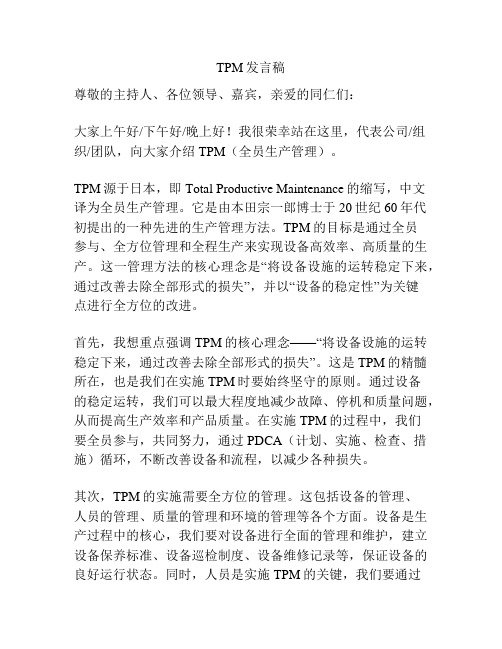
TPM发言稿尊敬的主持人、各位领导、嘉宾,亲爱的同仁们:大家上午好/下午好/晚上好!我很荣幸站在这里,代表公司/组织/团队,向大家介绍TPM(全员生产管理)。
TPM源于日本,即Total Productive Maintenance的缩写,中文译为全员生产管理。
它是由本田宗一郎博士于20世纪60年代初提出的一种先进的生产管理方法。
TPM的目标是通过全员参与、全方位管理和全程生产来实现设备高效率、高质量的生产。
这一管理方法的核心理念是“将设备设施的运转稳定下来,通过改善去除全部形式的损失”,并以“设备的稳定性”为关键点进行全方位的改进。
首先,我想重点强调TPM的核心理念——“将设备设施的运转稳定下来,通过改善去除全部形式的损失”。
这是TPM的精髓所在,也是我们在实施TPM时要始终坚守的原则。
通过设备的稳定运转,我们可以最大程度地减少故障、停机和质量问题,从而提高生产效率和产品质量。
在实施TPM的过程中,我们要全员参与,共同努力,通过PDCA(计划、实施、检查、措施)循环,不断改善设备和流程,以减少各种损失。
其次,TPM的实施需要全方位的管理。
这包括设备的管理、人员的管理、质量的管理和环境的管理等各个方面。
设备是生产过程中的核心,我们要对设备进行全面的管理和维护,建立设备保养标准、设备巡检制度、设备维修记录等,保证设备的良好运行状态。
同时,人员是实施TPM的关键,我们要通过培训和教育,提高员工的技能和意识,让每个员工都成为质量控制和问题解决的能手。
此外,我们还要注重质量管理,不断改进流程和操作方法,提高产品的一致性和客户满意度。
最后,环境的管理是TPM的重要组成部分,我们要注重设备的清洁和管理,减少能源的消耗和废物的生成,实现环境友好型生产。
最后,我想谈一下TPM的好处和挑战。
TPM的好处主要体现在三个方面:首先,它可以提高生产效率和产品质量,减少停机和故障,从而提高生产线的运行稳定性和产能利用率。
TPM全面生产维护讲义

TPM的主要手段——OEE
TPM术语介绍-1
设备部
设备效率:设备效率(Equipment Effectiveness)是指利用设备进行生产施工所产生的附加值(Value-added)的一种测度。附加值是由全部收入减去全部资源成本(材料和劳动力等)而形成的,然后分解为利润、工资和税金。利润归属于投资者,工资归属于劳动者(包括经营者),税金归属于政府,所以附加值体现了投资者、劳动者、政府三者之间的利益。
TPM术语介绍-2
设备部
故障/停机损失(Equipment Failure / Breakdown Losses)故障停机/损失是指故障停机造成时间损失和由于生产缺陷产品导致数量损失。因偶发故障造成的突然的、显著的设备故障通常是明显的并易于纠正;而频繁的、或慢性的微小故障则经常被忽略或遗漏。由于偶发性故障在整个损失中占较大比例,所以许多企业都投入了大量时间努力寻找避免这种故障,然而,要消除这些偶发性故障是很困难的。所以,必须进行提高设备可靠度的研究,要使设备效率最大化,必须使故障减小到零,因此,首先需要改变传统故障维修中放为故障是不可避免的观点。
TPM是一个以制造业领先的创新,强调人的重要性。一个“能做”和“持续改进”理论、生产的重要性和维护员工共同协作。它作为一个全面制造学的关键剖分被阐述出来。实质上说,TPM试图重塑组织以
TPM定义及特点
设备部
定义:TPM是日本现代设备管理维修制度,它是以达到最高的设备综合效率为目标,确立以设备一生为对象的生产维修全系统,涉及设备的计划、使用、维修等所有部门,从最高领导到第一线工人全员参加,依靠开展小组自主活动来推行的生产维修,概括为:T----全员、全系统、全效率,PM---生产维修(包括事后维修、预防维修、改善维修、维修预防)。
全面生产维护(TPM)讲义(改)

❖ 这种以提高生产设备效率达到提高生产能力的生产模式是一种内涵式的 发展模式,较之传统的以增加生产要素提高产能的外延式发展更加符合 可持续发展的战略目标。
❖ 许多世界级企业已经证明,现代设备管理可以在无需增加资源投入的条 件下较大幅度地提高设备的生产能力。
2021/8/5
13
❖ (5)设备管理对可持续发展战略的影响
5
2、什么是机制?
❖ 机制就是制度加方法或者制度化了的方法。 其含 义为“因为这个方法的存在,使得一件事不得不被 完成到最好” 。
❖ (1)机制是经过实践检验证明有效的、较为固定 的方法,不因组织负责人的变动而随意变动,而单 纯的工作方式、方法是可以根据个人主观随意改变 的。
❖ (2)机制本身含有制度的因素,并且要求所有相 关人员遵守,而单纯的工作方式、方法往往体现为 个人做事的一种偏好或经验。
❖
传统的工业生产过程中,生产能力的提高通常是通过增加固定资产
投资或员工的加班加点也就是资源的投入实现的。但是这种资源投入型
的生产方式由于固定成本的增加并不能有效提高企业生产经营的效益,
同时这种粗放型的生产方式也不利于资源的节约和环境保护。
❖ 现代设备管理的理念是通过加强设备管理,提高设备的综合效率以 实现生产能力的提高。因为生产设备综合效率的提高可以减少各种形式 的设备非计划停机时间,从而实现提高设备生产能力的目标。
2021/8/5
25
6. 日本对PM的改进完善
❖ 为了解决设备管理中的诸多问题,日本把美国维护设备的 经验进行了总结:
❖ 将装备出现故障以后采取应急措施的事后处置方法称为 “事后保全(BM)”;
❖ 将装备在出现故障以前就采取对策的事先处置方法称为 “预防保全(PM)”;
TPM经典培训课程(很值得去学习)

维修案例库,为类似故障的排除提供参考。同时鼓励维修人员分享维修
经验和技巧,提高整体维修水平。
03
生产现场改善方法论述
现场环境整治与5S管理
现场环境整治
确保生产现场整洁有序,消除脏乱差现象,提高工作效率和员工士气。
5S管理
通过实施整理(Seiri)、整顿(Seiton)、清扫(Seiso)、清洁(Seiketsu) 和素养(Shitsuke)五个步骤,打造良好的工作环境,提高生产效率和质量。
持续改进文化在组织中落地生根
1 2 3
员工参与 鼓励员工积极参与持续改进活动,提出改进意见 和建议,激发员工的创新精神和主动性。
培训和教育 通过培训和教育活动,提高员工对持续改进文化 的认知和认同度,培养员工的持续改进意识和能 力。
激励机制
建立有效的激励机制,对在持续改进中取得优异 成绩的员工给予表彰和奖励,激发员工的持续改 进热情。
分析提供依据。
故障诊断与排除技巧
01
故障诊断
通过观察、听取、测试等手段,判断设备故障的性质和原因,为故障排
除提供依据。
02
排除技巧
根据故障诊断结果,采取相应的维修措施,如更换零部件、调整设备参
数等,确保设备恢复正常运行。
03
维修记录与经验分享
详细记录设备维修情况,包括故障现象、诊断结果、维修措施等,形成
跨部门协作推进TPM模式构建
跨部门沟通机制 建立有效的跨部门沟通机制,促进不同部门之间的信息交 流和协作,共同推进TPM模式的构建。
目标一致性 强化各部门对TPM目标的认知,确保各部门在推进过程中 目标一致,形成合力。
资源共享 促进不同部门之间的资源共享,包括技术、经验和知识等, 提高资源利用效率,推动TPM模式在组织内的广泛应用。
分かり易いTPM(中国文)
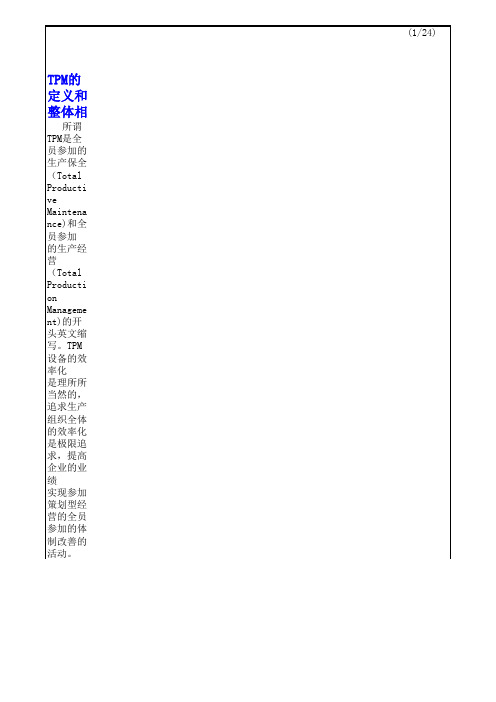
设备的7大损耗和计划的制造成本产生的差就是损失。
按照计划制造的成本,也有制造不出的情况。
例如,因故障稼动速度下降。
偶尔停线后恢复正常作业时,因不良的原因再次使用材料,加班、休息日出勤生产等,这些都是使用计划的材料费、劳务费以外的经费,都是增加制造成本。
浪费的产生是从一点的小问题产生的。
例如,不定期的供油就会导致轴瓦烧蚀,杂乱的夹具保管装态就会延长切换时间。
使用模具变形的夹具在放置时要调整、修正等。
这些都是小问题,发生时几乎都是引起不了注意的微小问题,是因该马上就要修正的,但实际上[这样没关系]被逃脱掉了。
小问题一成长,其结果损失就造成制造成本增加的主要原因。
换句话说就是损失是我们制造的。
生产现场的设备、人、材料、能源、模具、夹具等在现场使用的所有物品都产生了损耗(如下图)。
为了减少损耗,重要的是对损耗要正确地认识。
定量的把握损耗、设定具体的改善目标,明确问题进行改善。
另外,损耗和成本相关,正确的认识是非常重要的。
以生产设备为中心发生的损耗,也就是设备的7大损耗,可细分为①故障、②切换、③刀具更换、④成品、⑤速度低、⑥偶尔停线、⑦修改不良。
设备综合效率是设备的可靠性和稳定性进行评价的重要指标。
设备综合效率=时间稼动率×良品率而算出来的。
(如下图)●微小的问题就会发生损耗●生产现场的损耗存在16个(大的损耗)要点BOX(例)0.87×0.5×0.98×100= 42.6%设备的7大损耗和设备综合效率的关系设备7大损耗负荷时间稼动时间停止损耗净稼动时间性能损耗价值稼动时间不良损耗①故障损耗②切换调整损耗③刀具更换损耗⑤偶尔停线空运损耗⑦不良修正损耗⑥速度低的损耗④完成损耗设备综合效率的计算设备综合效率=时间稼动率×性能稼动率×良品率现场潜在的设备损失稼动率低能源损失质量不良故障不良的日常管理在生产现场按生产计划来进行生产。
生产现场阻碍生产的要因也就是发生事故,使生产不能顺利进行的最大要因就是故障和不良。
TPM培训课程(经典)

3 STEP : 清扫/注油基准书的制定 清扫/注油基准的制定及注油困难地点的改善 学习正确的注油技能
4 STEP : 设备总点检 设备点检point及点检技能的学习 清扫/注油/点检技术的统合及点检困难地点的改善
TPM
(全员生产保全)
1. TPM 概论
TPM定义
TOTAL 全公司的
PRODUCTIVE 生产设备
MAINTENANCE 维护(保全)
由全员参与的生产维护活动
TPM(Total productive maintenance)= 全员生产保全
提高设备效率 提高人的效率 提高管理效率 提升品质 推进无人化
纵向:从高层到一线员工, 横向:所有部门 纵横: 小集团活动
TPM发展
事后保全BM
1950
1960
1970
1980
1990
预防保全PM
改良保全CM
保全预防MP
TPM
时间管理时代
状态管理时代
修理为主
预防故障
改进设备
设计设备
设备的 体质改善
人员的 体质改善
标 准 化
单纯/最佳化
5S, 提案, 小组活动
人员方面目的
设备方面目的
企业方面目的
容易感知异常的现场
定期锻炼,每天30分钟 散步
每天少食多餐胜过 每天两次大餐
每年一次体检,定期 血液和视力检查
我们自己的身体
我们使用的设备
每天对设备的清扫、 润滑、紧固
定期进行适当的润滑 或过滤器等零件更换
每月、季、半年进行 计划性维护
TPM全面生产维护培训讲义
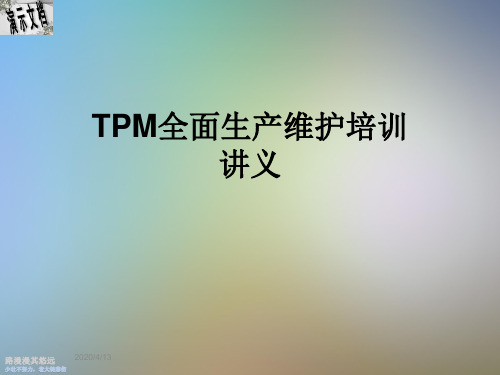
➢ 不良品率降低。
➢ 员工技能水平提高
➢ 生产及管理周期缩短。
健康 诊断
劣化测定
检查
(诊 断)
早期 治疗
劣化复原
预防修理
(提前改善)
路漫漫其悠远
预防保全
陈旧的设备管理观念
我是生产人员,你是维修人员。 设备我操作,维修你负责。 我修理,你设计。 我设计,你操作。 只要稼动率,不要可动率。 只有救火队,没有保养队。 只有单兵作战,没有团队合作。 迷信高速度的设备等。
P
Perfect
Production
M
路漫漫其悠远
Maintenance Management
设备管理的意义
获得过程(设备计划)
调查 研究
①
设计
制作
②
安装
使用过程(设备保全)
运行
保全
③
废弃
广义的含义
广义的设备管理 --- ① ② ③ 狭义的设备管理 --- ③
路漫漫其悠远
预防保全
Preventive Maintenance
立PM奖。 • 1971年,丰田(TOYATA)汽车公司的供应商日本电装,发扬光大了PM
活动,首次推出TPM概念。 • 1982年第一本标准化的TPM专著问世,书名为«TPM活动程序» • 1989年TPM的定义又一次被修改,内容得到进一步充实。
路漫漫其悠远
TPM活动的定义
1. 以最大限度地提高设备效率为目标(综合效率化); 2. 建立以生产设备为对象的预防保全系统; 3. 包括设备的计划、使用、保全等全部部门; 4. 从TOP到第一线工作人员的全体人员参加; 5. 教给员工管理方法,以小组的自主活动推进PM。
◎
TPM培训讲义课件

01
根据生产需求,明确设备应具备的功能、性能参数及技术要求
。
设计方案评估与优化
02
对设备设计方案进行全面评估,确保满足生产需求、降低成本
、提高可靠性。
设备布局与配套设施规划
03
合理规划设备布局,确保设备安全、高效运行;同时考虑配套
设施如电力、气源、排水等。
设备采购、安装及调试流程
01
02
03
设备采购
按照预防性维护计划,对设备进行定期检查、保养、更换易损件等 活动,防止设备故障发生。
建立检查记录与档案
对每次检查、保养、维修等活动进行记录,建立设备档案,方便后 续管理和维护。
03
CATALOGUE
计划保全与故障排除技巧
计划保全策略制定及实施步骤
设备状况评估
定期检查设备运行状态,收集 设备运行数据,评估设备性能
确定团队领导及核心成 员角色定位
建立有效的团队协作与 沟通机制
设定团队目标与工作计 划
培训需求分析和课程体系设计
01
02
03
04
调研分析员工技能现状及培训 需求
制定针对不同岗位和层级的培 训课程
设计符合TPM理念的课程体 系架构
评估课程效果并持续优化更新
内部讲师选拔培养及激励机制
制定内部讲师选拔标准与流程
01
02
03
04
维修流程梳理
对设备维修流程进行全面梳理 ,明确各环节职责及工作要求
。
维修效率提升措施
制定并实施维修效率提升措施 ,如采用快速维修工具、优化
维修步骤等。
维修人员培训
加强维修人员技能培训,提高 维修效率和质量。
维修备件管理
TPM系列讲座课程
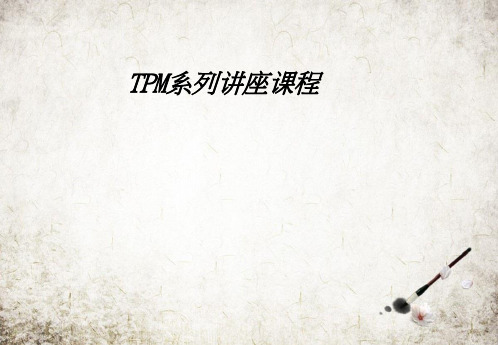
事务改善分科会 研修委员会 安全卫生委员会
TPM 基 本 理 念
1.建立可以赚钱的企业体质 -追求经济性、零灾害、零不良、零故障
2.预防哲学(事前防止) -MP -PM -CM
3.全员参加(参与型管理,尊重人性) -重复小集团组织,操作人员的自主保养
4.现场现物主义 -把设备塑造成“应有的状态”,以目视管理,创造干净明亮的 现场
应有状态的观念
应有状态
发挥并保持设备最高机能 及性能,所应具备的条件
从工学原理原则看,所希 望的状态,或以机能为中 心来考虑新希望的理想状 态
已了解者
未了解者
未遵守
基准 太松
应有状态的八个观点 1. 使用条件的 2. 安装、精度的 3. 组立、精度的 4. 机 能 的 5. 环 境 的 6. 外观形状的 7. 尺寸、精度的 8. 材质、强度的
教育训练
5. 提高技能
设备初期管理
第三章
TPM导入开始到落实— 活动步骤
TPM展开架构--推行TPM的12步骤
导入开始
导入准备阶段
区分
步
骤
1.经营阶层的TPM导入决心宣言
2.TPM导入教育与倡导活动
3.TPM推动组织与建立职制示范
4.TPM的基本方针及目标的设定 5.制作TPM展开的主计划
6.TPM的开始实施(Kick-Off大会)
异常与正常的分界
正常
异常
正常
异常
‧依看法之不同有正常、异常 两种看法
‧此分界领域引起问题的可能 性很大
正常 分界领域
正常
异常 异常
正常的范围变狭小
设定正常与异常的 分界,或将境界领 域缩小
复原的观念
何谓复原
tpm讲义大全[1]
![tpm讲义大全[1]](https://img.taocdn.com/s3/m/17f951c527284b73f342508d.png)
PPT文档演模板
tpm讲义大全[1]
波及世界的TPM
1.亚洲地区(日本以外)
韩国(现代汽车,三星,LG) 台湾(中华映管) 新加坡(纳基工业) 印度尼西亚(尤尼利巴) 马来西亚
2.欧洲国家
比利时(VOLVO EUROPA) 德国(VW) 波兰(SAAB-VALMET) 法国(SOLLAC.FOS、MBK、RENAULT雷诺车) 意大利(FIAT) 瑞典、荷兰 葡萄牙
4- MP保全预防
Maintenance Prevention
5- PM生产保全
Productive maintenance
1950年以前,半自动、手动操作设备多,结构也简 单,常采用的方法。在设备出现故障后再维护。
1950年以后,人们发现设备故障总在某部位出现, 因此在维护时主要去查找薄弱部位并对其改良。
而TPM(Total Productive Maintenance),是“全员生产保 全”的简称,目的是在各个环节上持续不断地进行改善,积小善为
大善,最终达成整体上的创新飞跃;同时通过标准化活动,将创新 取得的成果持久地加以保持。
海信之所以作出这个决定,最直接的诱因源于韩国三星的TPI/ TPM。三星因为推行TPI/TPM之后,整个集团的管理发生了脱胎换 骨的变化。事实上,在三星大力推行TPI/TPM之前,排名韩国前三 个大集团公司之间存在的差距并不大。但是,1997年亚洲金融危机的 爆发,促使三星加大了推行TPI/TPM,并裁减冗员30%。此后,三
Total Perfect Manufacturing
Total Plant Management 全面工厂管理创新
Total Profitable Management
PPT文档演模板
工厂全面改善TPM专业讲座

工厂全面改善TPM专业讲座工厂全面改善TPM专业讲座尊敬的各位领导、各位同事们:大家上午好!今天我给大家做一个关于工厂全面改善TPM (Total Productive Maintenance)的专业讲座。
TPM是一种全新的设备维护管理方法,它的目标是通过全员的参与,实现设备的持续稳定运行,提高生产效率和产品质量。
接下来,我将从TPM的基本概念、实施步骤和重要性三个方面给大家做详细的介绍。
首先,让我们来了解TPM的基本概念。
TPM是通过全员参与,以实现零故障、零事故、零缺陷和零停机为目标的设备维护管理方法。
它主要包括三大支柱:设备保养活动、设备自主管理和员工参与。
其中,设备保养活动的核心是预防保养,通过定期的保养和检查,预防设备故障的发生。
设备自主管理是指将设备的操作和保养工作交给设备操作员,使其成为设备的“专家”,实现设备的稳定运行。
员工参与是TPM的灵魂,通过培养员工的意识、技能和能力,实现员工对设备的积极参与和改进,推动企业的全面发展。
然后,我们来看一下TPM的实施步骤。
TPM的实施分为六个阶段:从事实管理、创始管理、递进管理、综合管理、持续管理和创新管理。
从事实管理是指通过对现有设备运行状况的分析,找出设备故障的原因和改进的方向,为后续的改善工作做好准备。
创始管理是指制定设备保养标准和操作规程,建立设备保养体系,为设备的稳定运行提供保障。
递进管理是指通过设备保养的不断改进,提高设备的稳定性和可靠性,实现预防性保养。
综合管理是指将设备的管理与生产计划、质量控制、物料控制等其他管理工作结合起来,推动企业整体绩效的提高。
持续管理是指通过设立全员参与的机制,发挥员工的主观能动性,推动企业的全面发展。
最后,创新管理是指通过技术创新和管理创新,实现企业的持续发展和竞争优势。
最后,我们来谈谈TPM的重要性。
TPM对企业发展具有重要的推动作用。
首先,TPM能够提高设备的可靠性和稳定性,减少设备故障和停机时间,提高生产效率和产品质量。
TPM培训讲义精品课件

TPM培训讲义精品课件一、教学内容本讲义依据TPM(Total Productive Maintenance)培训教材第四章“设备维护与故障排除”进行设计,详细内容包括设备维护的基本原则、常见设备故障诊断方法、预防性维护的实施步骤以及设备故障排除技巧。
二、教学目标1. 理解设备维护的重要性,掌握设备维护的基本原则。
2. 学会诊断常见设备故障,并能提出合理的解决方案。
3. 掌握预防性维护的实施步骤,提高设备运行效率。
三、教学难点与重点1. 教学难点:设备故障诊断方法及故障排除技巧。
2. 教学重点:设备维护基本原则、预防性维护实施步骤。
四、教具与学具准备1. 教具:PPT课件、设备维护与故障排除案例视频、设备模型。
2. 学具:笔记本、教材、笔。
五、教学过程1. 导入:通过展示设备维护与故障排除的实践情景,引发学生对设备维护的关注。
2. 设备维护基本原则讲解:讲解设备维护的基本原则,结合实际案例进行分析。
3. 设备故障诊断方法:介绍常见设备故障诊断方法,如直观诊断、仪器诊断等。
4. 预防性维护实施步骤:详细讲解预防性维护的实施步骤,包括维护计划的制定、实施、检查和改进。
5. 故障排除技巧:通过例题讲解,让学生学会设备故障排除的技巧。
6. 随堂练习:让学生分组讨论,针对给定设备故障案例,提出解决方案。
六、板书设计1. 设备维护基本原则定期维护预防为主随时检查记录分析2. 设备故障诊断方法直观诊断仪器诊断专家系统3. 预防性维护实施步骤制定维护计划实施维护检查维护效果改进维护计划七、作业设计1. 作业题目:请简述设备维护的基本原则。
请列举至少三种设备故障诊断方法,并简要说明其优缺点。
请结合实际案例,说明预防性维护实施步骤。
2. 答案:设备维护的基本原则:定期维护、预防为主、随时检查、记录分析。
设备故障诊断方法:直观诊断:简单易行,但受限于个人经验和技能。
仪器诊断:准确度高,但需要专业设备和培训。
八、课后反思及拓展延伸2. 拓展延伸:推荐学生阅读相关资料,了解设备维护与故障排除的最新技术和发展趋势。
TPM讲座

反复检查变化症状
因清扫不充分而引起的弊害
1.故障的原因
由于回转部,悬接部空压,油压系统,电气装御系统,传感品等被 污染,异物混入经过磨擦,堵塞、阻抗、通电不良等成为精度低 下或误动作等故障的原因.
2.品质不良的原因
异物直接混入制品中,或因设备的误动作而造成
3.强制劣化的原因
灰尘,污染落入缝隙而使检查困难,或加油困难造成中断等,是引起设备 强制劣化的原因.
3. 如果设备事前正常管理,就不会出现故障,若没有故障,自然就能预 防不良、灾害;
4、如果员工技能能够得到保证,就不会出现作业性不良,不会有不良品 流到市场; 4. 由人和设备、产品技术,决定竞争力; 5. 随着企业的发展,我们还会迫切需要能够降低制造成本的TPM活动;
TPM 8大活动支柱 TPM 体系由通常的下述八个支柱构成
的工厂、创造清洁的工厂、创造可视化的工厂。
5S具体内容
整理 整顿
物品分类,除去不必要的物品。 合理放置,方便使用。
清扫
清洁 清心
对角落清扫,清扫时检查。
制订可维持的基准。 养成良好的习惯,自觉遵守规则。
5S活动的5个阶段
通过TPM-消除不合理
不合理的思想概念:300:29:1
◇4-技能教育和设备检查
◇5-整理基准书做综合检查 ◇6-树立品质标准系统 ◇7-自主管理
以人员组装流水线为主的自主保全6STEP活动 ◇1-初期清扫 ◇2-发生源及困难部位的解决 ◇3-鉴定标准设定
通过感官彻底去除灰尘污染 去除,改善发生源/困难场所 标准的可视化管理,流水线效率化 作业条件的检查、操作最易化 均衡化生产 构筑品质均一,生产灵活的线体
对微小缺陷的思考方法
TPM全面生产管理培训讲义
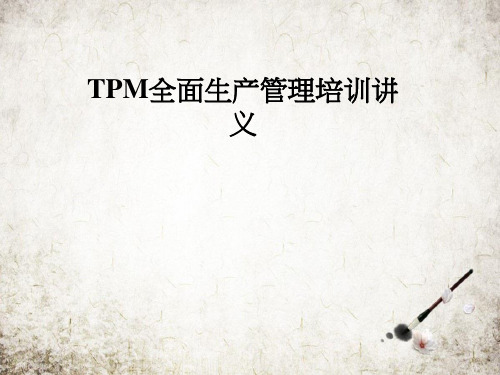
第二章 TPM深層研討
4.TPM活動主要法寶 5S活動 設備MAP 活動看板 小組會議 QC STORY 重點教育(ONE POINT LEESON) 目視管理基準書 自主保養基準書 5 WHY分析 MITBF分析 KYT
第二章 TPM深層研討
5.何謂TPM?
預防保養 Preventive Maintenance
和製造時引入P.M.觀念,雖然初期費用會偏高,但將來費 用和老化浪費會較少,長遠眼光來看,依然符合經濟原則.
第二章 TPM深層研討
二、全員生產保養內容 1.TPM方針與全員定義
• 通過參與,使設備效率最大化. • 保持各提高設備的可靠性;保持和創造保養安全、質量
和生產率的能力.
• 保持設備使用幫助最大化. • 提高員工技能,培養員工的專有經驗.
行修理較為經濟的情況,通常適用於不影響生產的設備.
• 糾正保養(Corrective Maintenance-C.M.)即設備本質的改
善,以提高設備的可靠性和可保養性;換句話說,延長設備 壽命,採用無故障、無保養麻煩的材料及備品等改良保 養保養.
• 保養預防(Maintenance Preventive-M.P.)用於新設備設計
C J C-D
G.生產量
=(I*G/C)**良品數/生產數*100%
H.良品率=良品數/生產數 =(I*G)/(A-B)*(良品數/生產數)*100%
I.理論週期時間
=(理論周期時間*生產量) * 良品數
J.實際週期時間
操作時間-計劃損失時間 生產數
F.實際加工時間=J*G T.時間稼動率=E/C M.速度稼動率=I/J N.純稼動率=F/E L.性能稼動率=M*N*100
▪
TPM讲座_东风日产中文译稿

保全预防
保证保全和修理等的便利性 CM・・・・ Corrective Maintenance 改良保全 故障发生前预防其发生 (1951年左右 自美国导入) PM・・・・ Preventive Maintenance
预防保全
事后保全
发生故障后修理 ( PM以前是保全主流方式) BM・・・・ Breakdown Maintenance
何谓自主保全・・・设备的预防 医学
设备的健康诊断
父母(作业员)向医生(保全员)详细说明, 可以早期恢复 身体情况的观察・・・・・身体情况从何时开始变差的? 发热?食欲呢?有没有异常声音?
何谓自主保全・・・设备的预防 医学 自主保全的作用
发现不及时・・・ ・需要做手术 (设备拆解修理)
早期发现设备疾病・・・・家庭常备药即可治疗
同期生产 TQM JIT SQC GK(现场管理) TPM
全部门明确目的和作用,统一活动方向,切实推 动管理循环,以便登上更高层次
JIT・SQC・TPM → 排除浪费的工具
JIT:以物的流动为切入口的综合改善
SQC:专项问题的分析・解析
TPM:以设备可靠性为切入口的综合改善 GK(现场管理) →日产生产方式的基础
目标 手 段 分 类
正常运转
实 老化防止
施 活 老化测定
动 老化复原
分 担 运转 保全 技术
◎ ◎ ◎ ◎ ◎ ◎ ◎ ○
维 持 活 动
日常保全
正确操作 准备、调整 清扫 ·潜在缺陷的找出 ·改善 加油 再紧固 使用条件, 老化的日常检查 小整备 定期点检 定期诊断 定期维修 倾向诊断
定期保全 设 备 综 合 效 率 提 升
Maintenance 全员参加的生产保全
全员生产维修(TPM)概论

全员生产维修(TPM)概论第一节概述全员生产维修(Total Productive Maintenance,TPM)是一种由日本人中岛青一推出的通过企业全体员工积极参与的方式对生产过程进行优化的管理体系。
全员生产维修是日本全面质量管理(Total Quality Control,TQC)及全员参与(Total lmployee lnvolve- ment,TEl)的理念与美国预防维修的实践相结合的产物。
全员生产维修也是一种能够提高维修效率、减少设备故障、员工自主参与的创新体系。
全员生产维修不是以技术,而是以人为中心,充分体现了现代企业以人为本的精神。
全员生产维修也可以被视为涉及范围更为广泛的生产维修。
人们对维修的理解就是确保生产设备的系统功能,维修的必要性在这里是无需讨论的。
较高的设备有效度和生产过程的安全性、产品可靠的质量保证都需要生产设备保持良好的状态。
在这种意义上,维修包括预防维修(维护、检查以及预防性零部件更换)以及各种修理措施。
为了确保生产过程中物流的畅通,及时制(Just h Time,JIT)的应用具有特别重要的意义,物流的组织管理的改善及设备有效度的提高都可以通过及时制实现。
及时制生产意味着:·适宜的零部件;·在适宜的时间;·以适宜的数量;·鲁按照所要求的质量标准。
进行生产而不仅仅是供应。
在及时制生产中,设备的可靠性以及根据质量进行调整的生产过程是绝对必要的。
全员生产维修的理念是基于应用于现代工业生产中高新技术设备的复杂性进行设计的。
对此认识不足的企业经常出现的情况就是时间和金钱的浪费,组织管理效率的低下,材料及零部件积压、周转困难,设备停机时间及故障率居高不下,生产率不稳定等。
在全员生产维修体系中,维修人员不仅要承担设备的维修任务,而且还要对整体工作场所的状态承担责任。
这里所说的工作场所的状态既包括设备本身的状态,也涉及实施维修作业所必须的所有设备、工具、器材等的状态。
全面生产管理TPM培训

全面生产管理(TPM)培训什么是全面生产管理(TPM)?全面生产管理(Total Productive Maintenance,简称TPM)是一种综合性的生产管理方法论,旨在通过提高设备的可靠性、安全性和维护性,实现生产效率的最大化。
TPM是由日本制造业公司所提出,并逐渐在全球范围内推广和应用。
为什么需要进行TPM培训?在现代制造业中,设备的正常运行和高效率是生产过程的关键。
通过进行TPM 培训,企业可以教育和培养员工掌握全面生产管理的理念和方法,激发员工的积极性和责任感,提高设备的稳定性、可靠性和维护效率,从而实现生产效率的提升和资源的最大化利用。
TPM培训的目标和意义TPM培训的目标是让员工了解和理解TPM的核心概念和方法,培养和提高员工的TPM意识和技能,使其能够积极参与到设备维护和改善工作中来。
通过TPM 培训,企业可以实现以下目标:1.提高设备的可靠性和稳定性:通过有效的设备维护和保养,减少设备故障和停机时间,提高生产线的稳定性和连续性。
2.提高设备的维护效率:培养员工的维护技能和方法,提高维修任务的执行效率,降低维修成本。
3.提高生产效率:通过减少停机时间和缺陷品率,提高生产效率和产品质量,降低生产成本。
4.让员工发挥更大的潜力:通过培训,让员工了解并参与到设备管理和改善工作中,发挥自己的创造性和主动性,提高工作满意度和归属感。
TPM培训的内容TPM培训的内容包括但不限于以下几个方面:1.TPM的基本概念和原理:介绍TPM的核心概念和原理,包括维修保养(Maintenance)、设备保持(Equipment Management)、过程控制(Process Control)等。
2.TPM的实施步骤和方法:详细介绍TPM的实施步骤和方法,包括设备状态评估、保养计划制定、维护标准化、设备故障分析等。
3.TPM的工具和技术:介绍TPM中常用的工具和技术,如设备维护记录表、故障模式与影响分析(FMEA)、维修作业标准(SOP)等。
- 1、下载文档前请自行甄别文档内容的完整性,平台不提供额外的编辑、内容补充、找答案等附加服务。
- 2、"仅部分预览"的文档,不可在线预览部分如存在完整性等问题,可反馈申请退款(可完整预览的文档不适用该条件!)。
- 3、如文档侵犯您的权益,请联系客服反馈,我们会尽快为您处理(人工客服工作时间:9:00-18:30)。
何谓TPM・・・・・
设备保全方式
生产保全 保全预防
全员参加TPM
TPM的5本柱 TPM ・・・全员参加的生产保全 MP活动
专项改善
改良保全
预防保全
自主保全 计划保全
人材培养
事后保全
最大的特点是 ・“操作员的自主保全”(自己的设备自己维护) ・全员参加(所有关联部门、从领导到一线)的活动
何谓TPM・・・ 设备保全的分工
这是自主保全!
何谓TPM・・・ 减少故障→生产 效率化
时间
<人的高效化> <设备的高效化> 投入时间
就业工时
除外工时
(支援其他部门)
工作时间 负荷时间
计划 停止
计划停止 (8) 停机损失 (1) 故障损失
负荷时间
阻 碍 人 的 效 率 化 的 5 大 损 失
等待指示的损失 等待材料损失 设备停止损失 设备性能损失 方法顺序损失 技能/士气损失
生产保全时代 生産保全時代 Productive Maintenance
TPM时代 TPM時代
Total Productive Maintenance
何谓TPM・・・・・
TPM的定义
①打造极限追求生产体系效率化(综合效率化)的 企业体质 ②以生产体系整个生命周期为对象, 在现场利用现物建立 “灾害0、不良0、故障0”等预防 所有损失的机制, ③现场、技术、管理等所有部门, ④从高层领导到一线员工的全体人员参加, ⑤以重复小集团的形式实现损失零。
TPM讲座
TPM概要
TOTAL Procuctive Maintenance
Agenda
1、何谓TPM 2、NPW的推进
何谓TPM・・・・・
TPM的历史
1950 事後保全 事后保全 Breakdown Maintenance
1960
1970
1980
预防保全时代 予防保全時代 Preventive Manitenance
Maintenance 全员参加的生产保全
TPM ・・・・TOTAL Procuctive
何谓TPM・・・・・ TPM5大支柱
自主保全 ・・・・ 计划保全 ・・・・ 专项改善 ・・・・ 制造主导的故障防止活动 保全主导的故障防止活动 制造・保全・技术・品保・其他部门 合力开展的损失改善活动
人材培养 ・・・・ 设备精通人员的培养 (异常发现力・修理复原力・改善力・维持管理力) MP活动 ・・・・反馈到新一代免维护设备
纳入处 关系会社 (KICK OFF) 协力会社
导入 开始
10. 组成间接管理部分的 效率化体制 11. 组成安全, 卫生和 环境管理体制的 稳定 阶段 12. TPM完全设备和
领导的集合教育 成员的教育传达 开发容易制造的制品 开发容易使用的设备 非发生不良的 条件设定和维持管理 生产支援,本部属的效率化 和设备的效率化 组成灾害 ZERO, 公害ZERO体制 挑战比PM奖的受奖 更高的目标 LEVEL UP
TPM主计划的编制
DNEC的事例
2006
准备阶段 TPM导入宣言 推进体制准备(组织・方针・目标) 导入培训准备 TPM导入培训(分层) TPM启动 自主保全模范设备活动准备 高层领导体验实习 自主保全模范设备活动 自主保全STEP 1~3(全线) 自主保全STEP 4~5(全线) 损失改善活动 制造技能员 保全技能培训 5 S
良品数量 良品重量
不良损失 暖机损失 头尾料损失
(15)能源损失
有效能源
(16)模具/治工具损失
(14)成品率损失
损耗损失 多余的损失
单位成本的效率化------------阻碍[物料效率化]得3大损失
TPM的推动方法
TPM展开进程(12阶段)
区分 S T E P 要 点
区分 S T E P 要 点 追求生产效率化的极限 PROJECT TEAM 活动 工作岗位小集团活动 STEP 方式, 诊断和合格证
同期生产 TQM JIT SQC GK(现场管理) TPM
全部门明确目的和作用,统一活动方向,切实推 动管理循环,以便登上更高层次
JIT・SQC・TPM → 排除浪费的工具
JIT:以物的流动为切入口的综合改善
SQC:专项问题的分析・解析
TPM:以设备可靠性为切入口的综合改善 GK(现场管理) →日产生产方式的基础
2、维持管理 ・计划保全・自主保全的定期点检 ・追求自主保全点检的效率化 3、人的培养 (培养精通设备的人才) ・异常发现技能 ・修理复原技能 ・改善技能
何谓TPM・・・・TPM的目的
4、 “0挑战”
“0”挑战
故障0
不良0
灾害0
何谓TPM・・・・ TPM的效果
有形效果 S Q C T :停工、非停工灾害零 :减少工程不良率 :降低制造成本 : 提升OEE、JPMH ・减少突发故障件数 ・提升设备稼动率 ・削减库存 :增加改善件数
成本 コスト (C)
何谓TPM・・・・ TPM的目的
3、生产性提升和维持管理
1、生产性和设备可靠性提升 结果系・・・ OEE・JPMH・JPH的提升 要因系・・・ ①设备可靠性提升・・・故障防止・早期复原 ②自主保全日常活动・・・利用5感发现异常 ③减少自主保全故障的活动・・・STEP1~4 ④6大损失的改善(故障损失为MUST)
预知保全
○ 不定期维修
◎ ◎ ◎ ◎ ◎ ○ ◎ ◎ ○ ◎ ○ ◎ ◎ ◎ ◎ ○ ◎ ◎ ◎ ○
事后保全
不具合的早期发现和迅速联络
突发修理
◎ ○ ◎ ○ ◎
改 善 活 动
改良保全 信頼性
强度提升 负荷的减轻 提高精度 在线监控的开发 点检作业的改善
◎
○ ○ ○ ○ ◎
改良保全 保全性
整备作业的改善 整备品质的提升
综合总结了“工作的标准化和改善”、“人财的 培养” 维持・提升制造现场QCT水准的的机制
TPM的推进 同期生产的实现 NPW
TQM
Q、C、T 提升 SQC 接头(JIT) IFA 自主保全
追求NPW “两个无限” 无限同期于顾客 无限的课题表面化和改革 自主保全 层次提升活动 计划保全体制诊断 降低6大损失 提升OEE的活动
5S活动
进度 2007
已实施 2008
开展中 2009
6 7 8 9 10 11 12 1 2 3 4 5 6 7 8 9 10 11 12 1 2 3 4 5 6 7 8 9 10 11 12 1 2 3 4 5 6 7 8 9 10 11 12
STEP 1
STEP 2
STEP 3 STEP 1
STEP2
何谓自主保全・・・设备的预防 医学
设备的健康诊断
父母(作业员)向医生(保全员)详细说明, 可以早期恢复 身体情况的观察・・・・・身体情况从何时开始变差的? 发热?食欲呢?有没有异常声音?
何谓自主保全・・・设备的预防 医学 自主保全的作用
发现不及时・・・ ・需要做手术 (设备拆解修理)
早期发现设备疾病・・・・家庭常备药即可治疗
目标 手 段 分 类
正常运转
实 老化防止
施 活 老化测定
动 老化复原
分 担 运转 保全 技术
◎ ◎ ◎ ◎ ◎ ◎ ◎ ○
维 持 活 动
日常保全
正确操作 准备、调整 清扫 ·潜在缺陷的找出 ·改善 加油 再紧固 使用条件, 老化的日常检查 小整备 定期点检 定期诊断 定期维修 倾向诊断
定期保全 设 备 综 合 效 率 提 升
6. TPM 决议宣言
赋予意识
TPM推进组织的设定
DFL PV HD的事例
TPM推进负责人 技术担当 推进干事
TPM总负责人
NML: TPM协调:
自主保全分科会
计划保全分科会
会长:科长 推进干事
安全环保分科会
会长:科长 推进干事
品质保全分科会
会长:科长
推进干事
会长:科长
推进干事
个别改善分科会
会长:科长 推进干事
初期管理分科会
会长:科长 推进干事
间接事务分科会
会长:科长 推进干事
教育训练分科会
会长:科长 推进干事
TPM的目标设定
提升生产效率
目
OEE JPMH JPH 加工不良
标
FY08
FY09
FY10
STAR
劳动灾害
降低成本
年度
单台成本 (元/台)
FY08
FY09
FY10
人材培养
年度 FY08 FY09 FY10 达成水平 能够正确实施自主保全点检 的水平 能够更换消耗件、定期更换 部品的水平 能够修理轻微故障的水平 100% 40% 20% 目标人员
何谓TPM・・・・・
TPM的定义 (狭义)
①以达到最高设备效率(综合效率化)为目标, ②确立针对设备全寿命周期的PM综合体系, ③设备的规划部门・使用部门・保全部门等所有部门,
④从高层领导到一线员工全体人员参加, ⑤通过士气管理、即小集团自主活动推进PM。
何谓TPM・・・・・ 何谓保全
通过综合活动提高生产性,实现盈利的保全 (当前的主流) PM・・・・ Procuctive Maintenance 生产保全 从设计阶段即确保可维护性优良的设备 MP・・・・ Maintenance Prevention
改良保全,计划保全,预防保全
1. TOP的
社内报上记载 TPM导入决议宣言TPM社内讲习会宣言 干部 : 阶层别合宿研修 Champion 一般 : 页面上映会 委员会, 专门分会 推进事务局 Bench Mark(水准点)和目标 目标设定 效果预测 导 入 实 施 阶 段
7. 组成生产效率化体质 7.1 个别改善