日本轧制技术的发展历程
日本钢铁企业考察学习报告(无头技术)

5、君津制铁所线材车间
长信工业集团
线材产品尺寸精度的提高 螺栓等汽车用小型精密零件一般是用冷锻方法制成。螺栓 原料是线材。要求螺栓冷锻用线材具有高尺寸精度。 过去君津制铁所线材车间产品的尺寸公差是±0.34mm(产品 直径 15mm),不能满足对尺寸有严格要求用户的需求。由于 粗轧至 No.1 中间轧机的 4 线轧制,轧材条数变化,使轧材 尺寸波动很大,达到±0.74mm,并且通过 No.2 中间轧机至 精轧机组轧制不能降低这个尺寸波动。设备改造后,新 3 辊 轧机投产,通过 No.2 中间轧机轧制使轧材尺寸波动大幅度 下降,直径 15mm 的线材产品尺寸公差控制在±0.15mm。 2.5 线材生产效率提高 由于新配置的 3 辊轧机展宽小,可以利用同一孔型生产多 种规格的产品。利用新轧机的这个特点,可以对 No.1 中间 轧机的孔型系列进行整合。过去 No.1 中间轧机的孔型系列 有 3 种孔型,使不同钢种、不同规格轧材的轧制受到限制, 新配置了 3 辊轧机后,No.1 中间轧机的孔型变为 2 系列, 放宽了对不同钢种、不同规格轧材轧制的限制,大大提高了 生产效率。 君津制铁所线材车间导入新型的 No.2 中间轧机,提高了 产品的尺寸精度,自 2008 年投产以来一直运行到现业集团
2.2PFB 轧机 新的中间轧机是 3 辊轧机。3 辊轧机利用 3 个孔型的轧辊对轧材全 周进行轧制,展宽小于传统的 2 辊轧机,可以抑制轧材尺寸的波动。 2.3 设备布局 在配置新中间轧机时,为了在狭窄的空间安装 4 架 3 辊轧机,对原 有的 No.1 中间轧机和精轧机之间的所有设备布局进行调整(图 1 和图 2)。轧材从原有的 No.1 中间轧机到 No.2 中间轧机时转动 90°,在轧 材转动处设置活套挑以消解轧材速度的变化。在 No.2 中间轧机后面, 是中间水冷区,对轧材氧化铁皮性状进行控制。然后轧材再次转动 90° 进入精轧机组。在 No.2 中间轧机和精轧机组之间也设置了活套挑。由 于活套挑设置在生产线的直线部位,所以采用了侧活套型的活套挑。
JFE不锈钢产业发展历程介绍
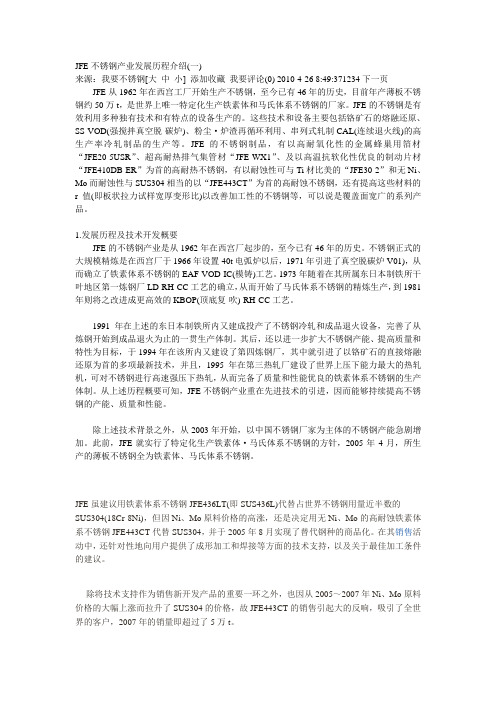
JFE不锈钢产业发展历程介绍(一)来源:我要不锈钢[大中小] 添加收藏我要评论(0) 2010-4-26 8:49:371234下一页JFE从1962年在西宫工厂开始生产不锈钢,至今已有46年的历史,目前年产薄板不锈钢约50万t,是世界上唯一特定化生产铁素体和马氏体系不锈钢的厂家。
JFE的不锈钢是有效利用多种独有技术和有特点的设备生产的。
这些技术和设备主要包括铬矿石的熔融还原、SS-VOD(强搅拌真空脱-碳炉)、粉尘·炉渣再循环利用、串列式轧制CAL(连续退火线)的高生产率冷轧制品的生产等。
JFE的不锈钢制品,有以高耐氧化性的金属蜂巢用箔材“JFE20-5USR”、超高耐热排气集管材“JFE-WX1”、及以高温抗软化性优良的制动片材“JFE410DB-ER”为首的高耐热不锈钢,有以耐蚀性可与Ti材比美的“JFE30-2”和无Ni、Mo而耐蚀性与SUS304相当的以“JFE443CT”为首的高耐蚀不锈钢,还有提高这些材料的r值(即板状拉力试样宽厚变形比)以改善加工性的不锈钢等,可以说是覆盖面宽广的系列产品。
1.发展历程及技术开发概要JFE的不锈钢产业是从1962年在西宫厂起步的,至今已有46年的历史。
不锈钢正式的大规模精炼是在西宫厂于1966年设置40t电弧炉以后,1971年引进了真空脱碳炉V01),从而确立了铁素体系不锈钢的EAF-VOD-IC(模铸)工艺。
1973年随着在其所属东日本制铁所干叶地区第一炼钢厂LD-RH-CC工艺的确立,从而开始了马氏体系不锈钢的精炼生产,到1981年则将之改进成更高效的KBOP(顶底复-吹)-RH-CC工艺。
1991年在上述的东日本制铁所内又建成投产了不锈钢冷轧和成品退火设备,完善了从炼钢开始到成品退火为止的一贯生产体制。
其后,还以进一步扩大不锈钢产能、提高质量和特性为目标,于1994年在该所内又建设了第四炼钢厂,其中就引进了以铬矿石的直接熔融还原为首的多项最新技术,并且,1995年在第三热轧厂建设了世界上压下能力最大的热轧机,可对不锈钢进行高速强压下热轧,从而完备了质量和性能优良的铁素体系不锈钢的生产体制。
王丽文库之近10年日本轧钢技术的进步简况

近10年日本轧钢技术的进步简况一、轧钢技术的最近进展和今后展看日本最近10年轧钢生产虽受钢产量起伏的影响而波动,但技术仍在不断进步。
随着计算机的小型化、高速化和有限元法(FEM)的登场,材料三次元的解析得以应用,对以板材为首的各种钢材的加工压力、荷重、扭矩和金属活动等均可计算出。
变形阻抗作为高精度计算荷重和扭矩的物性值,现已进进数据收集和模式化阶段,热变形阻抗已在细晶粒钢开发中广为应用,冷变形阻抗也在高强度钢的开发方面实用化。
现结合由“大生产大消费时代”向资源循环型社会的转变,今后轧钢技术发展的主要方向如下:(1)从主要变形向大幅进步材料性能、且以最小能耗生产易再循环利用产品的新加工技术转变,如复合加工、多轴加工、超精密加工、工具自由化加工等和材质控制技术。
(2)研究开发方面,由利用模拟技术使试验时间和用度大幅下降的追求型向重视手工装置和发挥人才作用的方式转变。
(3)基础技术应重视工具特性的奔腾改进和与环境和谐技术的开发。
二、轧钢基础技术的开发1.变形的理论解析轧钢方面的理论数值解析已在各种钢材生产上应用。
如对产品尺寸精度和外形的猜测,对被轧材的材料活动、荷重、形变、温度分布等的解析,对轧钢变形和对产品影响的说明,产品材质、组织、残留应力等的猜测以及轧制条件的最佳化和轧钢设备的公道设计等方面的应用。
由于三次元FEM应用的快速发展,日本在轧钢技术理论方面已居世界领先地位。
上世纪80年代后期,在轧板解析方面以三次元FEM为主,结合轧辊弹性变形解析,可测出钢板宽边变形的具体情况后加以控制,对板材控制的高度化和轧机设备的高效设计作出了多方贡献,迄今已经基本实用化。
对串列轧机、非对称轧制也在试用中。
在钢板变形解析中,还建议采用计算时间短、更易理解的模拟三次元解析法。
在热轧方面,材质、猜测控制均十分重要,最近正在开发利用三次元FEM对其的轧制加工进行的解析模式,拟在超微细粒钢的开发中应用。
影响轧钢产品质量和操纵效率的表面缺陷很早即受到人们的重视。
近10年日本钢管制造技术进展

近10年日本钢管制造技术进展1 钢铁制造技术的变迁从20世纪60年代至70年代,日本的钢铁产量有大幅度的提高,这是由于日本引进和开发了大量高生产率技术所致。
LD转炉、连铸、高炉的大型化、板坯连续冷轧技术、高速轧制和芯棒式无缝管轧制等技术的开发为大幅度提高产量和生产率起了巨大的作用。
这些技术的发展离不开设备、材料和计算机等相关技术的发展。
在轧制和轧制理论发展的同时,如果没有计算机和计算机控制技术的发展,就没有连续轧制技术。
日本的钢铁业在高效、大量生产方面以先进的制造技术为武器,确立了其在国际上的钢铁技术的主导地位。
但是,在国际上对钢铁需求变化的同时,技术的发展方向也开始向重质轻量方向转变,并追求质量的稳定,进一步降低生产成本。
尤其是,随着汽车的迅速普及,对板材挤压成形性和耐蚀性提出了越来越高的要求,为此日本加强技术的主导地位,在IF钢和表面处理材料的开发方面取得了很大的进展。
在降低生产成本方面,开发了大幅度节能、提高产品合格率和提高生产率的技术。
在建筑建设领域,近年来随着超高层建筑和特大型桥梁的建设,开发了高强度、焊接性好的钢板。
在汽车制造业方面,为确保汽车碰撞时的安全性和环保的要求,开发了高强度、轻量化钢材生产技术。
在钢管制造方面,为确保轻量化和碰撞安全及降低生产成本,钢管的高强度化和管材液压成形技术引入关注,汽车生产厂和钢铁企业合作进行了钢管生产技术开发。
另外,在油井管和干线用管方面,进行了高耐蚀性和高强度材料的开发。
日本钢铁技术能够领先世界是由于日本始终以需求为先、认真实施技术开发的结果。
日本所具有的优势就是技术和需求的超前性。
在上述产品和生产技术开发中,一个非常重要的关键词就是技术的融合。
制造技术在吸收相关技术并与上游技术融合的同时不断发展。
另外,支撑加工技术发展的是加工模拟技术。
今后,日本应将制造、加工技术的经验和计算模拟取得的经验技术进行融合,在以需求为先的同时,创造出领先一步的制造技术,如高强度钢的加工技术、高精度稳定的加工技术和钢构功能开发技术等。
多品种高级钢冶炼连铸技术的进步
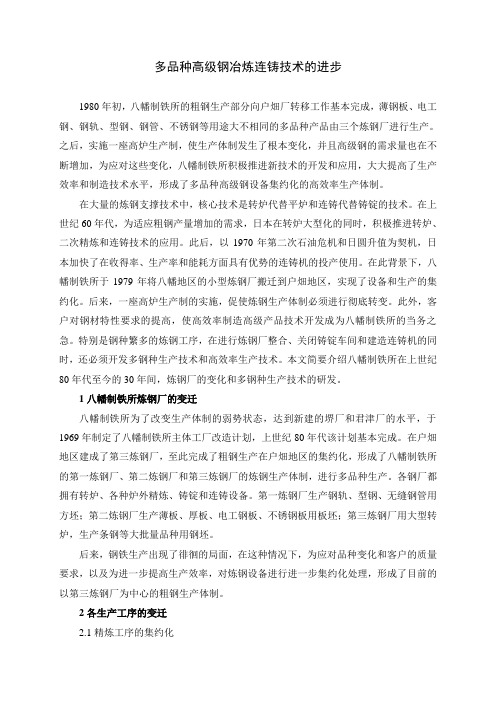
多品种高级钢冶炼连铸技术的进步1980年初,八幡制铁所的粗钢生产部分向户畑厂转移工作基本完成,薄钢板、电工钢、钢轨、型钢、钢管、不锈钢等用途大不相同的多品种产品由三个炼钢厂进行生产。
之后,实施一座高炉生产制,使生产体制发生了根本变化,并且高级钢的需求量也在不断增加,为应对这些变化,八幡制铁所积极推进新技术的开发和应用,大大提高了生产效率和制造技术水平,形成了多品种高级钢设备集约化的高效率生产体制。
在大量的炼钢支撑技术中,核心技术是转炉代替平炉和连铸代替铸锭的技术。
在上世纪60年代,为适应粗钢产量增加的需求,日本在转炉大型化的同时,积极推进转炉、二次精炼和连铸技术的应用。
此后,以1970年第二次石油危机和日圆升值为契机,日本加快了在收得率、生产率和能耗方面具有优势的连铸机的投产使用。
在此背景下,八幡制铁所于1979年将八幡地区的小型炼钢厂搬迁到户畑地区,实现了设备和生产的集约化。
后来,一座高炉生产制的实施,促使炼钢生产体制必须进行彻底转变。
此外,客户对钢材特性要求的提高,使高效率制造高级产品技术开发成为八幡制铁所的当务之急。
特别是钢种繁多的炼钢工序,在进行炼钢厂整合、关闭铸锭车间和建造连铸机的同时,还必须开发多钢种生产技术和高效率生产技术。
本文简要介绍八幡制铁所在上世纪80年代至今的30年间,炼钢厂的变化和多钢种生产技术的研发。
1八幡制铁所炼钢厂的变迁八幡制铁所为了改变生产体制的弱势状态,达到新建的堺厂和君津厂的水平,于1969年制定了八幡制铁所主体工厂改造计划,上世纪80年代该计划基本完成。
在户畑地区建成了第三炼钢厂,至此完成了粗钢生产在户畑地区的集约化,形成了八幡制铁所的第一炼钢厂、第二炼钢厂和第三炼钢厂的炼钢生产体制,进行多品种生产。
各钢厂都拥有转炉、各种炉外精炼、铸锭和连铸设备。
第一炼钢厂生产钢轨、型钢、无缝钢管用方坯;第二炼钢厂生产薄板、厚板、电工钢板、不锈钢板用板坯;第三炼钢厂用大型转炉,生产条钢等大批量品种用钢坯。
2003年日本钢铁生产技术的发展历程

2003年日本钢铁生产技术的发展历程一、日本钢铁业的概况2003年日本经济保持稳定恢复的状况。
虽然公共投资减少,东亚经济在一定程度上受到了“非典”的影响,但经济仍保持高速增长,加之股票价格的上涨等原因,增强了企业家的投资信心,设备投资出现了明显的好转。
不仅个人消费稳步上升,而且出口行市也持续坚挺。
根据日本政府预测,2003年度日本的GDP实际增长率为2.0%,整个经济形势出现了好转。
虽然2003年10月日本全国的消费者物价指数与2002年10月相比已连续5年零6个月上升,但从整体来看,物价继续下降,还无法克服通货紧缩的问题。
即使从就业形势来看,虽然完全失业率在12月份已降到4.9%,但年平均失业率依然很高,达到5.3%,年平均完全失业人数为350万人,连续5年超过300万人,就业形势依然严峻。
根据2003年日本国内钢铁需求订货的统计来看,在建筑方面,民间在非住宅建筑的投资恢复有所增加,但住宅建筑开工户数与2002年相同;在土木工程建设方面,公共土木工程建设陷入严重的不良状况,整个建设呈下降的趋势;在制造业方面,不仅汽车用钢材的需求持续坚挺,而且造船业的开工量也持续保持好的势头,以土木工程建设机械、金属加工机械和机床为主的产业机械的出口也开始出现好转,整个制造业的形势比2002年好。
关于钢铁出口,各钢铁公司都采取了谨慎的销售态势,虽然与2002年相比,钢铁的出口减少了5.1%,为3446万吨,但对中国等国的出口保持旺盛。
2003年中国的粗钢产量在历史上首次突破2亿吨,中国的钢材需求比2002年度增长了26%,达到了2.66亿吨。
另一方面,2003年日本的钢铁进口比2002年增长了13.3%,达到了596万吨,出现时隔3年的增长。
但是,厚板和热轧宽带钢等钢板的进口量仍很低。
另外,中国台湾已连续11个月减少普通钢材的进口,而中国大陆却连续10个月增加普通钢材的进口。
日本的粗钢产量在随着国内制造业好转的同时,向以中国为主的亚洲国家的出口也出现了良好的势头,2003年累计粗钢产量为l.1051亿吨,比2002年增长2.6%,连续4年超过1亿吨。
日本热轧带钢技术

日本热轧带钢技术由于日本的热轧带钢轧机建设时间早,一般轧机能力较现代轧机弱。
近年建设的轧机,特别是我国建设的轧机,均增大了电机功率和允许轧制力,提高了轧机的刚性,这对于提高产品尺寸精度、轧制高变形抗力的合金钢和HSLA钢是有利的。
但是,日本通过制定合理的轧制规程,利用相对较弱的轧机,再配以先进的轧后冷却系统,也轧制出了各种高强钢种。
这表明,轧机并非是决定产品强度等级的唯一因素。
对于钢铁材料来说,由于在冷却过程中会发生复杂的相变,如果加强对控制冷却系统的控制和优化,可在不提高轧机能力的条件下,利用对冷却过程的控制,来提高钢材的强度,达到生产高强钢的目的。
轧后加速冷却系统的发展情况与国际上大多数热轧带钢轧机相似,日本的热轧带钢厂多数采用管层流系统进行轧后冷却过程的控制。
但少数厂家例外,如住友金属鹿岛厂,在1984年改造时,采用水幕冷却系统;近年,JFE福山厂通过改造,采用超快速冷却系统Super0LACH(SuperOn—LineAcceleratedCoolingforHotStripMill),据介绍,对3mm厚的热轧带钢,其冷却速度可达700℃/s,为目前世界最高冷却速度。
该冷却系统可对钢板实行全面、均匀的快速冷却,其位于精轧机出口处。
对冷却路径的控制是生产汽车用AHSS钢的重要手段。
由于日本热轧带钢轧机均为传统轧机,未采用短流程技术和热卷箱技术,为了消除头尾温差,-必须采用升速轧制。
冷却路径的控制要求温度演变历程(即温度与时间的关系)在升速轧制过程中保持不变。
与传统的以精轧温度、卷取温度为控制目标的控制方式相比,实施冷却路径控制难度很大。
对于生产AHSS钢,日本采用2种冷却控制措施;一是采用带钢分段、冷却系统分区的控制方式,以提高控制系统的控制精度;二是添加一定的合金元素,扩太钢材的工艺控制窗口,减少钢材对冷却路径改变的敏感性,降低冷却控制的难度。
目前,对一些重要的高强钢种,日本各厂均可生产,这表明日本热轧带钢冷却控制的水平是比较高的。
日本JFE公司开发和应用的中厚板制造技术介绍

日本JFE钢铁公司开始开发采用水淬火的热机械控制工艺(TMCP),作为高强度、高韧性,具有优良焊接性能钢板生产技术的核心技术。
下面简单介绍由JFE钢铁公司开发和应用的中厚板制造技术,包括超级-OLAC技术,一种新的中厚板加速冷却技术以及HOP技术(热处理在线工艺),一种加速冷却后的在线热处理工艺。
同时,下面还介绍Easyfab钢板制造技术,即通过应用具有新功能的冷矫直机将中厚板中残余应力降至零。
一、新加速冷却技术——“超级-OLAC”技术的开发与控制轧制技术一起,加速冷却技术是TMCP工艺的核心技术。
JFE钢铁公司是世界上首家开发并成功在中厚板生产中应用在线加速冷却技术的钢铁企业。
在上世纪90年代初,采用加速冷却技术制造的TMCP钢实现了提高钢板强度、改进焊接性能的目的,从而有助于焊接结构建筑用钢使用的合理化和提高建筑的安全性,并开始用于造船业。
然而,最近几年对钢板质量的要求日趋严格,如减少强度下降等。
为了满足新的要求,基于一个全新的概念,JFE钢铁公司进行了大量研究以获得解决与传统冷却技术问题相关的方案,并开发出新一代加速冷却工艺,称之为超级-OLAC工艺,并应用于JFE钢铁公司西日本钢厂。
当中厚板进行水淬火时出现的热传递和沸腾现象可以大致分为两种方式,即核胞沸腾和薄膜沸腾。
在前一种沸腾中,冷却水直接与钢接触,热量通过产生的泡传递。
相比之下,后一种沸腾中在钢与冷却水间形成一个蒸汽薄膜,热量是通过蒸汽薄膜传递。
核胞沸腾的冷却能力比薄膜沸腾更高。
在中厚板冷却开始时,中厚板表面温度较高,薄膜沸腾起主导作用。
然而,随着中厚板表面温度的下降,蒸汽薄膜变得不稳定,冷却水开始局部上直接与中厚板接触,沸腾逐渐转向核胞沸腾。
此外,在瞬时沸腾状态下,当薄膜沸腾和核胞沸腾共存时,随着冷却的继续,冷却能力提高。
采用传统冷却方法,如喷淋冷却和层流冷却时,如果冷却水流量提高以强化冷却,冷却迅速地转换成瞬时沸腾,是核胞沸腾和薄膜沸腾的混合。
日本热轧带钢技术的发展和现状_随中国金属学会代表团访问日本观感之一
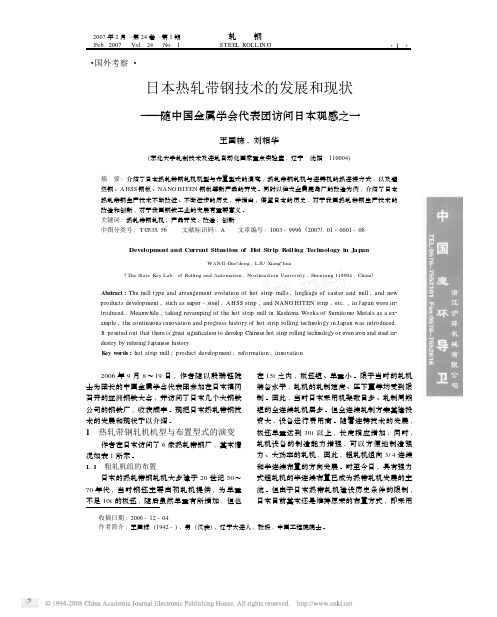
2007年2月・第24卷・第1期Feb.2007 Vol.24 No.1 轧 钢STEEL ROLL IN G ・国外考察・日本热轧带钢技术的发展和现状———随中国金属学会代表团访问日本观感之一王国栋,刘相华(东北大学轧制技术及连轧自动化国家重点实验室,辽宁 沈阳 110004)摘 要:介绍了日本热轧带钢轧机机型与布置型式的演变,热轧带钢轧机与连铸机的热连接方式,以及超级钢、A HSS 钢板、NANO HITEN 钢板等新产品的开发。
同时以住友金属鹿岛厂的改造为例,介绍了日本热轧带钢生产技术不断改进、不断进步的历史,并指出,借鉴日本的历史,对于我国热轧带钢生产技术的改造和创新,对于我国钢铁工业的发展有重要意义。
关键词:热轧带钢轧机;产品开发;改造;创新中图分类号:T G 335156 文献标识码:A 文章编号:1003-9996(2007)01-0001-06Development and Current Situ ation of H ot Strip R olling T echnology in JapanWAN G Guo 2dong ,L IU Xiang 2hua(The State Key Lab.of Rolling and Automation ,Nort heastern University ,Shenyang 110004,China )Abstract :The mill type and arrangement evolution of hot strip mills ,lingkage of caster and mill ,and new products development ,such as super -steel ,A HSS strip ,and NANO HITEN strip ,etc.,in J apan were in 2troduced.Meanwhile ,taking revamping of the hot strip mill in Kashima Works of Sumitomo Metals as a ex 2ample ,the continuous innovation and progress history of hot strip rolling technology in Japan was introduced.It ponited out that there is great signification to develop Chinese hot strip rolling technology or even iron and steel in 2dustry by refering Japanese history.K ey w ords :hot strip mill ;product development ;reformation ;innovation收稿日期:2006-12-04作者简介:王国栋(1942-),男(汉族),辽宁大连人,教授,中国工程院院士。
日本中厚板生产技术的发展和现状(一)——随中国金属学会代表团访问日本观感之二_轧钢_2007tr
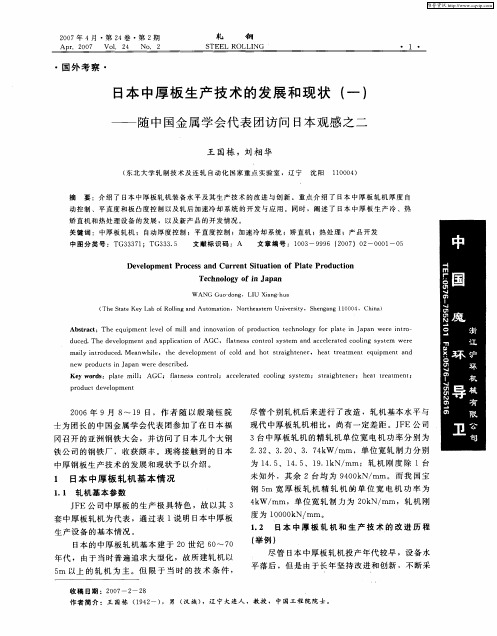
收 稿 日期 :2 0 — 2 8 0 7 —2
尽 管 日本 中厚板 轧机 投产 年代 较早 ,设备 水 平落 后 ,但 是 由于 长年 坚持改 进 和创新 ,不 断采
作 者简 介 : 王 国 栋 (9 2 ) 男 ( 族 ) 14- , 汉 ,辽 宁 大连 人 ,教 授 , 中 国工 程 院 院 士 。
未知 外 ,其余 2台均 为 9 0 k mm。而我 国宝 4 0 N/
钢 5 宽 厚 板 轧 机 精 轧 机 的 单 位 宽 电 机 功 率 为 m 4 W/ k mm,单位 宽轧 制 力 为 2 k mm ,轧 机 刚 0 N/
J E公 司 中厚 板 的生 产 极 具特 色 ,故 以其 3 F
n w r d csi a a r e cie . e p o u t n J p n we ed s r d b
Ke r s: plt m il A GC + fa ne s on r l ac ee at d ooi g s t m ; sr i t ne ; he t r a m e ; y wo d ae l; lt s c t o ; c lr e c ln ys e t agh e r a t e t nt pr duc v l m e o tde eop nt
第2 4卷 ・ 2期 第
王 国 栋 等 :L本 中厚 板 生 产 技 术 的发 展 和 现 状 ( ) t 一
・3 ・
的任 意道 次 可进 行 动 态 立辊 轧 制 。此 外 , 由于 采 圈 圈 嗣目 7 线探 - 射 测器 用液 压 AWC、 短行 程 控制 等 技 术 , 可控 制 钢 板 头 尾部 和全 长 的宽 度精 度 。
日本控制轧制技术的发展
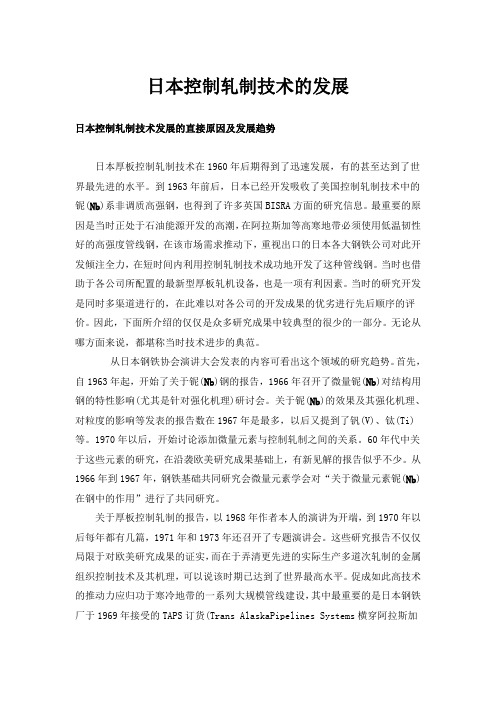
日本控制轧制技术的发展日本控制轧制技术发展的直接原因及发展趋势日本厚板控制轧制技术在1960年后期得到了迅速发展,有的甚至达到了世界最先进的水平。
到1963年前后,日本已经开发吸收了美国控制轧制技术中的铌(Nb)系非调质高强钢,也得到了许多英国BISRA方面的研究信息。
最重要的原因是当时正处于石油能源开发的高潮,在阿拉斯加等高寒地带必须使用低温韧性好的高强度管线钢,在该市场需求推动下,重视出口的日本各大钢铁公司对此开发倾注全力,在短时间内利用控制轧制技术成功地开发了这种管线钢。
当时也借助于各公司所配置的最新型厚板轧机设备,也是一项有利因素。
当时的研究开发是同时多渠道进行的,在此难以对各公司的开发成果的优劣进行先后顺序的评价。
因此,下面所介绍的仅仅是众多研究成果中较典型的很少的一部分。
无论从哪方面来说,都堪称当时技术进步的典范。
从日本钢铁协会演讲大会发表的内容可看出这个领域的研究趋势。
首先,自1963年起,开始了关于铌(Nb)钢的报告,1966年召开了微量铌(Nb)对结构用钢的特性影响(尤其是针对强化机理)研讨会。
关于铌(Nb)的效果及其强化机理、对粒度的影响等发表的报告数在1967年是最多,以后又提到了钒(V)、钛(Ti)等。
1970年以后,开始讨论添加微量元素与控制轧制之间的关系。
60年代中关于这些元素的研究,在沿袭欧美研究成果基础上,有新见解的报告似乎不少。
从1966年到1967年,钢铁基础共同研究会微量元素学会对“关于微量元素铌(Nb)在钢中的作用”进行了共同研究。
关于厚板控制轧制的报告,以1968年作者本人的演讲为开端,到1970年以后每年都有几篇,1971年和1973年还召开了专题演讲会。
这些研究报告不仅仅局限于对欧美研究成果的证实,而在于弄清更先进的实际生产多道次轧制的金属组织控制技术及其机理,可以说该时期已达到了世界最高水平。
促成如此高技术的推动力应归功于寒冷地带的一系列大规模管线建设,其中最重要的是日本钢铁厂于1969年接受的TAPS订货(Trans AlaskaPipelines Systems横穿阿拉斯加管线系统),即外径为1219mm的大直径高强度X65管线钢。
日本炼钢技术十年进步概况

日本炼钢技术十年进步概况一、日本近十年钢产量及主要指标的变化从1994年到2003年的10年是钢产量波动较大的时期。
由于泡沫经济的破灭,钢产量由1995年的1.016亿t跌到1998年的9355万t的低谷,后又转为上升,进入21世纪后连续4年超过1亿t。
特别是近年由于高炉大钢的合并和东亚经济快速发展带动钢铁需求兴旺,2004年又超过1.1亿t大关而直追1973年1.1932亿t的历史最高纪录。
其中,电炉钢年产量亦由期初的2842万t上升到3425万t,特殊钢比例基本保持在18.4%~20%的水平。
而铁水预处理比则由44.9%猛升到67.6%。
至于二次精炼比,电炉钢由85%上升到95%,转炉钢由80%上升到86%。
连铸比则由96.9%上升到98.6%,其中特殊钢连铸比由87.2%上升到93.5%,而普碳钢则保持在99.8%的极限状态。
二、十年间有代表性的技术开发成果1.铁水预处理工艺的重组为取代过去在铁水罐车和铁水包内进行的预处理,各厂开发成功各种用转炉的预处理法(H炉法、SRP法、NRP法、MuRc法、LD-ORP 法),大幅提高了脱磷效率,减少了对外排渣。
个别工厂已实现全部铁水预处理。
2.环境友好型精炼工艺由于环保意识的提高,十分重视减少钢渣外排技术的开发,使钢渣外排总量达原来的1/2,突出的如彻底脱硅的零排渣工艺。
还开发成功含碳渣用于烧结矿和铁水脱硫,钢渣制砼用于护岸材,用含铁粉尘制球团矿等再生利用技术。
有的厂已作到了炼钢固体废物为零。
3.电磁力应用技术的革新从初期的电磁搅拌和局部作用的电磁制动发展到后期的可适应钢水的加减速而切换的电磁设备、在铸坯宽度方向均匀磁场的静磁场制动以及结晶器内钢水流动的模拟计算软件。
4.高质量技术不断进行提高产品质量的技术开发,坚持了洁净钢技术开发。
在硬件方面,二次精炼中增加燃烧器后使RH多功能化,开发成功连铸坯防止裂纹缺陷的技术。
在软件方面亦开发成功预测产品质量的技术,使轴承钢中的含氧量由1994年的5ppm降到2001年的4.7ppm,最好时达3ppm左右。
日本中厚板生产技术的发展和现状

日本中厚板生产技术的发展和现状——随中国金属学会代表团访问日本观感之二王国栋刘相华(东北大学轧制技术及连轧自动化国家重点实验室)2006年9月8日-19日,随以殷瑞钰院士为团长的中国金属学会代表团参加在日本福冈召开的亚洲钢铁大会,并访问了日本几个大钢铁公司的钢铁厂。
作者有幸随团访问,收获颇丰。
现就接触到的日本中厚板生产技术的发展和现状予以介绍。
1 中厚板车间的基本情况1.1 基本设备参数JFE中厚板的生产极具特色,故以该公司的3套中厚板轧机为代表,通过表1说明日本中厚板生产设备的基本情况。
表1 JFE的3台中厚板轧机的基本情况日本的中厚板轧机基本上建设于上一世纪60-70年代,由于当时追求大型化的趋势,所以轧机的尺寸基本以5m以上的轧机为主。
但是,限于当时的技术条件,尽管个别轧机进行了改造,轧机基本水平与现代中厚板轧机相比,尚有很大的差距。
这3台轧机的精轧机单位宽电机功率分别为 2.32kW/mm、3.20kW/mm、3.74kW/mm,单位宽轧制力分别为14.5kN/mm、14.5kN/mm、19.1kN/mm,轧机刚度分别为94000kN/mm、94000kN/mm、未知kN/mm。
我国宝钢5m精轧机的单位宽电机功率4 kW/mm、单位宽轧制力20kN/mm、轧机刚度10000kN/mm,在轧机强力化方面有一定的优势。
建设初期,日本的这些轧机自动控制水平不是很高,产品质量也有差距。
当时均没有装设控制冷却装置,所以无法进行控制冷却。
矫直机和其他辅助设备也远未达到强力化的水平。
1.2 日本中厚板轧机和生产技术的改进历程(举例)尽管日本的中厚板轧机投产年代较早,投产初期设备水平与今天相比,还是相当落后的。
但是由于常年坚持改进和创新,不断采用新技术,始终保持日本中厚板轧机和生产技术领先于国际发展,生产出满足新世纪需要的国际领先的高级产品。
下面是JFE的3个中厚板轧机设备和工艺改进的一览表,它真实的记录了日本中厚板轧机的发展和领跑世界中厚板技术的历史轨迹。
日本全球领先顶尖科技(六)-钢铁冶炼技术
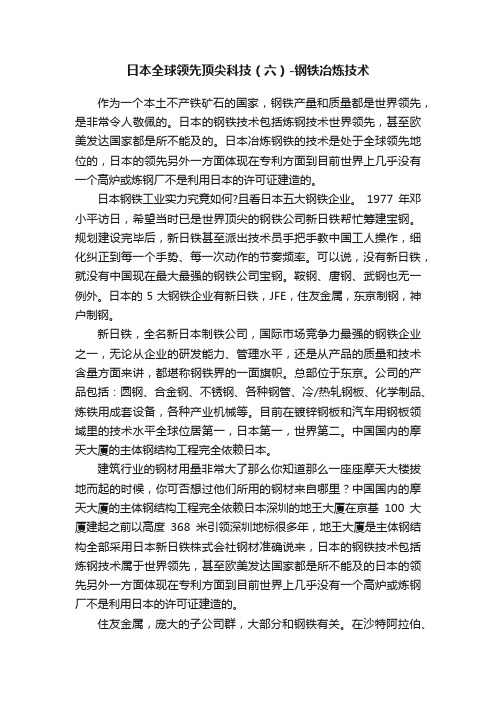
日本全球领先顶尖科技(六)-钢铁冶炼技术作为一个本土不产铁矿石的国家,钢铁产量和质量都是世界领先,是非常令人敬佩的。
日本的钢铁技术包括炼钢技术世界领先,甚至欧美发达国家都是所不能及的。
日本冶炼钢铁的技术是处于全球领先地位的,日本的领先另外一方面体现在专利方面到目前世界上几乎没有一个高炉或炼钢厂不是利用日本的许可证建造的。
日本钢铁工业实力究竟如何?且看日本五大钢铁企业。
1977年邓小平访日,希望当时已是世界顶尖的钢铁公司新日铁帮忙筹建宝钢。
规划建设完毕后,新日铁甚至派出技术员手把手教中国工人操作,细化纠正到每一个手势、每一次动作的节奏频率。
可以说,没有新日铁,就没有中国现在最大最强的钢铁公司宝钢。
鞍钢、唐钢、武钢也无一例外。
日本的5大钢铁企业有新日铁,JFE,住友金属,东京制钢,神户制钢。
新日铁,全名新日本制铁公司,国际市场竞争力最强的钢铁企业之一,无论从企业的研发能力、管理水平,还是从产品的质量和技术含量方面来讲,都堪称钢铁界的一面旗帜。
总部位于东京。
公司的产品包括:圆钢、合金钢、不锈钢、各种钢管、冷/热轧钢板、化学制品、炼铁用成套设备,各种产业机械等。
目前在镀锌钢板和汽车用钢板领域里的技术水平全球位居第一,日本第一,世界第二。
中国国内的摩天大厦的主体钢结构工程完全依赖日本。
建筑行业的钢材用量非常大了那么你知道那么一座座摩天大楼拔地而起的时候,你可否想过他们所用的钢材来自哪里?中国国内的摩天大厦的主体钢结构工程完全依赖日本深圳的地王大厦在京基100大厦建起之前以高度368米引领深圳地标很多年,地王大厦是主体钢结构全部采用日本新日铁株式会社钢材准确说来,日本的钢铁技术包括炼钢技术属于世界领先,甚至欧美发达国家都是所不能及的日本的领先另外一方面体现在专利方面到目前世界上几乎没有一个高炉或炼钢厂不是利用日本的许可证建造的。
住友金属,庞大的子公司群,大部分和钢铁有关。
在沙特阿拉伯、墨西哥、巴西、美国以及东南亚的一些国家和地区设有一批分厂和办事处。
日本轧制技术的发展历程

日本轧制技术的发展历程1、前言自1953年日本钢铁产量超过战前以来,经济高度发展,产量飞越提高。
20世纪70年代初期产量超过了1亿吨,成为了世界屈指可数的钢铁大国。
其后产量一直保持在1亿多吨,并努力使生产技术处于世界领先水平。
日本钢铁业的发展以战后从欧美各国引进技术为基础,通过迅速对其进行改造和创新,开发了具有自主知识产权的技术。
在轧制工艺方面,从20世纪60年代至70年代开发了高速轧制技术,从20世纪70年代至80年代开发了连续轧制技术,自20世纪80年代以后开发了轧制尺寸精度高、产品质量高和不受工艺过程约束的轧制技术及应用这种技术的新型轧机。
最近以适应环保要求为目的的轧制工艺引人注目。
本文主要就20世纪80年代以来日本开发的具有自主知识产权的轧制技术的发展历程进行概述。
2、轧制理论和轧辊的发展2.1 轧制解析众所周知,日本的轧制技术以理论为基础,轧制技术始终领先于世界水平。
为解析板材轧制中的板材形状和中间凸厚的原理,对轧机的弹性变形条件和被轧材的塑性变形条件进行了连立求解。
采用将弯曲和剪切挠曲的材料力学模型进行扩展或校正的方法对各种类型轧机进行解析的方法已基本确立。
另一方面,关于材料的塑性变形,引进了三维解析法,使解析由二维理论向高精度解析发展。
在解析法的发展方面,有采用数值计算法忠实解析变形的所谓三维解析法,有刚性和塑性FEM,有弹性和塑性FEM,尤其是还有为缩短计算时间而将上述方法进行组合的解析法。
在孔型轧制方面,一般说来纯理论处理是极为困难的,作为一种简便的方法,虽然可以采用所谓的矩形换算法把孔型轧制替换为适当的矩形断面材的扁平轧制,但无法获得高的精度。
提高精度用的实验式和半理论式在简单推测随孔型和轧制条件变化时的变形特性和负荷特性方面依然是一种有效的方法,但目前一般是采用FEM解析。
由于FEM的出现,使材料的三维流解析变得可能起来。
它不仅可以用于板材的解析,而且还可以用于型材、棒线材和管材的轧制力、轧制载荷、轧制力矩和宽展的求解。
日本轧钢技术发展概括与展望
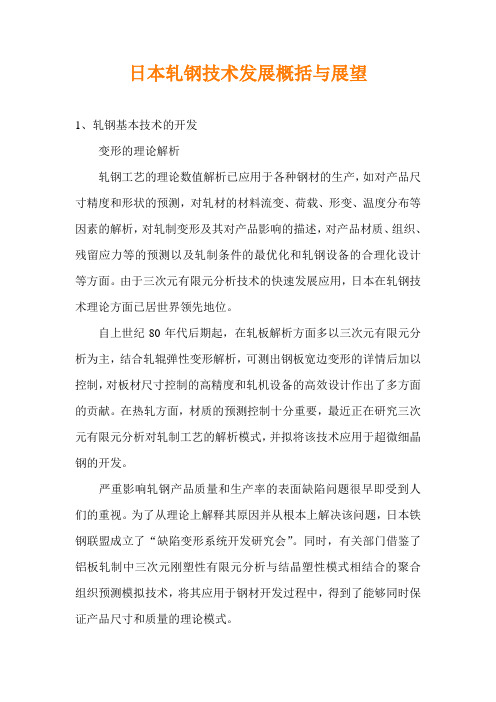
日本轧钢技术发展概括与展望1、轧钢基本技术的开发变形的理论解析轧钢工艺的理论数值解析已应用于各种钢材的生产,如对产品尺寸精度和形状的预测,对轧材的材料流变、荷载、形变、温度分布等因素的解析,对轧制变形及其对产品影响的描述,对产品材质、组织、残留应力等的预测以及轧制条件的最优化和轧钢设备的合理化设计等方面。
由于三次元有限元分析技术的快速发展应用,日本在轧钢技术理论方面已居世界领先地位。
自上世纪80年代后期起,在轧板解析方面多以三次元有限元分析为主,结合轧辊弹性变形解析,可测出钢板宽边变形的详情后加以控制,对板材尺寸控制的高精度和轧机设备的高效设计作出了多方面的贡献。
在热轧方面,材质的预测控制十分重要,最近正在研究三次元有限元分析对轧制工艺的解析模式,并拟将该技术应用于超微细晶钢的开发。
严重影响轧钢产品质量和生产率的表面缺陷问题很早即受到人们的重视。
为了从理论上解释其原因并从根本上解决该问题,日本铁钢联盟成立了“缺陷变形系统开发研究会”。
同时,有关部门借鉴了铝板轧制中三次元刚塑性有限元分析与结晶塑性模式相结合的聚合组织预测模拟技术,将其应用于钢材开发过程中,得到了能够同时保证产品尺寸和质量的理论模式。
为了适应棒线材尺寸的高精度化、规格易变以及低成本和高质量的要求,日本钢铁业目前已经开发出了三辊轧制工艺、2Hi精密轧机和四辊轧机等多变数控制理论。
三次元刚塑性有限元分析亦应用于棒线材的孔型设计,保证了产品的高精度。
棒线材控制轧制技术目前正在研发中,通过增设缓冷、快冷系统可以使工序简化。
三次元刚塑性有限元分析在H型钢轧制领域的应用正在逐步推广,应用于万能轧机预测材料流变和应力分布的研究正在进行中。
今后,随着建筑物的大型化和抗震性要求的提高,H型钢的控轧、控冷技术将被广泛采用。
塑性加工摩擦学理论的发展冷轧中的超高速轧制。
进入上世纪90年代,为了生产厚度在0.2毫米以下的食品包装用薄板,日本成功开发出轧制速度高达2800米/分钟的超高速轧制法,并开发出与之配套的高速润滑油、高耐磨工作辊和轴承防烧坏技术,并为防烧损开发了摩擦学理论。
近二十年日本炼铁技术发展回顾
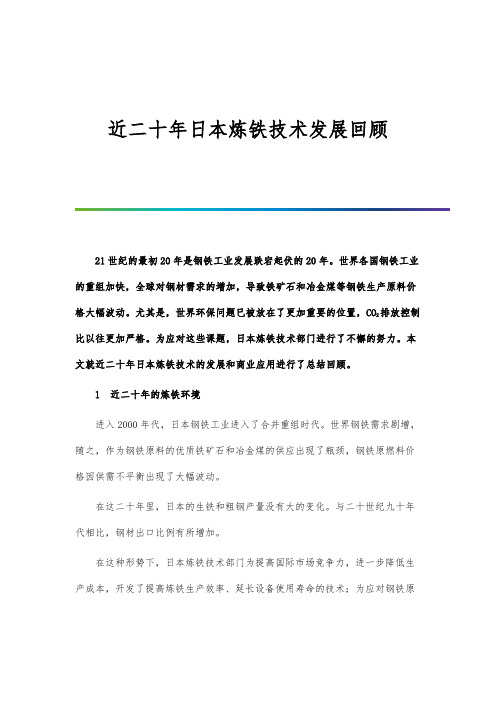
近二十年日本炼铁技术发展回顾21世纪的最初20年是钢铁工业发展跌宕起伏的20年。
世界各国钢铁工业的重组加快,全球对钢材需求的增加,导致铁矿石和冶金煤等钢铁生产原料价格大幅波动。
尤其是,世界环保问题已被放在了更加重要的位置,CO排放控制2比以往更加严格。
为应对这些课题,日本炼铁技术部门进行了不懈的努力。
本文就近二十年日本炼铁技术的发展和商业应用进行了总结回顾。
1 近二十年的炼铁环境进入2000年代,日本钢铁工业进入了合并重组时代。
世界钢铁需求剧增,随之,作为钢铁原料的优质铁矿石和冶金煤的供应出现了瓶颈,钢铁原燃料价格因供需不平衡出现了大幅波动。
在这二十年里,日本的生铁和粗钢产量没有大的变化。
与二十世纪九十年代相比,钢材出口比例有所增加。
在这种形势下,日本炼铁技术部门为提高国际市场竞争力,进一步降低生产成本,开发了提高炼铁生产效率、延长设备使用寿命的技术;为应对钢铁原料价格的高涨,开发了廉价劣质资源利用技术;为应对环保问题,开发了节能技术。
2 2000年代炼铁的主要应用技术在高炉方面,随着计测和计算科学技术的发展,应用了各种传感技术和模拟技术。
为提高高炉的操作精度,开发了各种提高烧结矿质量的技术,同时,采用了各种降低还原剂比的技术,如装入含碳团矿降低高炉热保存带温度和在铁矿石中混合装入大量焦炭,并喷吹城市煤气。
在高炉入炉原料方面,还使用了球团矿和还原铁等。
在高炉风口喷吹技术方面,为提高粉煤喷吹量,推进了粉煤喷吹技术和喷吹设备的开发,还开发了喷吹转炉渣的技术。
尤其是,各种高炉长寿化技术的开发和应用取得进步。
在原料和烧结方面,为提高资源应对能力和生产效率,应用了各种制粒技术和提高装料溜槽功能的技术。
尤其是,作为环保和节能的应对技术,开发和应用了向烧结机喷吹碳氢气体和使用CaO 改质的粉焦减少NOx排放等新技术。
在炼焦方面,SCOPE炉已开始应用,除了进行焦炉的新建和改造外,还开发和应用了各种应对焦炉老化的观察、诊断、修补技术。
- 1、下载文档前请自行甄别文档内容的完整性,平台不提供额外的编辑、内容补充、找答案等附加服务。
- 2、"仅部分预览"的文档,不可在线预览部分如存在完整性等问题,可反馈申请退款(可完整预览的文档不适用该条件!)。
- 3、如文档侵犯您的权益,请联系客服反馈,我们会尽快为您处理(人工客服工作时间:9:00-18:30)。
日本轧制技术的发展历程1、前言自1953年日本钢铁产量超过战前以来,经济高度发展,产量飞越提高。
20世纪70年代初期产量超过了1亿吨,成为了世界屈指可数的钢铁大国。
其后产量一直保持在1亿多吨,并努力使生产技术处于世界领先水平。
日本钢铁业的发展以战后从欧美各国引进技术为基础,通过迅速对其进行改造和创新,开发了具有自主知识产权的技术。
在轧制工艺方面,从20世纪60年代至70年代开发了高速轧制技术,从20世纪70年代至80年代开发了连续轧制技术,自20世纪80年代以后开发了轧制尺寸精度高、产品质量高和不受工艺过程约束的轧制技术及应用这种技术的新型轧机。
最近以适应环保要求为目的的轧制工艺引人注目。
本文主要就20世纪80年代以来日本开发的具有自主知识产权的轧制技术的发展历程进行概述。
2、轧制理论和轧辊的发展2.1 轧制解析众所周知,日本的轧制技术以理论为基础,轧制技术始终领先于世界水平。
为解析板材轧制中的板材形状和中间凸厚的原理,对轧机的弹性变形条件和被轧材的塑性变形条件进行了连立求解。
采用将弯曲和剪切挠曲的材料力学模型进行扩展或校正的方法对各种类型轧机进行解析的方法已基本确立。
另一方面,关于材料的塑性变形,引进了三维解析法,使解析由二维理论向高精度解析发展。
在解析法的发展方面,有采用数值计算法忠实解析变形的所谓三维解析法,有刚性和塑性FEM,有弹性和塑性FEM,尤其是还有为缩短计算时间而将上述方法进行组合的解析法。
在孔型轧制方面,一般说来纯理论处理是极为困难的,作为一种简便的方法,虽然可以采用所谓的矩形换算法把孔型轧制替换为适当的矩形断面材的扁平轧制,但无法获得高的精度。
提高精度用的实验式和半理论式在简单推测随孔型和轧制条件变化时的变形特性和负荷特性方面依然是一种有效的方法,但目前一般是采用FEM解析。
由于FEM的出现,使材料的三维流解析变得可能起来。
它不仅可以用于板材的解析,而且还可以用于型材、棒线材和管材的轧制力、轧制载荷、轧制力矩和宽展的求解。
三维FEM解析作为一种有效的解析工具已得到人们的认可。
人们期待着今后能向轧制温度解析和将轧制加工时的材料组织变化,尤其是将轧制缺陷解析系统组合起来的综合轧制理论方面发展。
2.2 变形阻抗变形阻抗值是计算轧制载荷和轧制力矩时的重要物理特性值。
日本钢铁协会轧制理论研究会已对变形阻抗值的研究数据进行了充实和收集,并采用数学模型进行了研究。
在热变形阻抗方法,采用考虑到多道次高速连续轧制时的累积应变效应的变形阻抗公式进行计算后,显著地提高了热变形阻抗值的预测精度。
为把考虑到材料组织变化的轧制理论进行扩展,希望能建立对材料的硬化、恢复和再结晶等现象同时进行跟踪的理论体系,积累一些与合金成分相对应的能对冶金现象进行定量化的数据。
在冷变形阻抗方面,通常是采用考虑到温度和应变速度相互关系的动态变形阻抗公式进行计算。
最近已开发了在ε=10-2-10-3时能简单获得应力-应变曲线图的高速材料试验机。
2.3 轧制润滑和轧辊随着冷轧速度的高速化(最大2800mpm),为获得摩擦系数的定量值,开发了高速轧制模拟装置和双圆筒滑动试验机,严格计算注入曲膜的厚度,对轴与轴承等的热胶着进行了评价,提出了表面光泽度的推定和控制系统,并对轧制润滑油进行了改进。
作为工作辊材质,一般是将高碳Cr系锻造材进行表面淬火后,使微细碳化物在完全变为马氏体的基质中大量析出,形成硬度高的组织,但由于轧制方面的要求越来越高,因此加快了对镀Cr和喷镀WC-Co来提高耐磨性的研究和高速钢及陶瓷新材质的研究。
轧辊表面的加工也从喷丸清理变为电火花加工,或采用电子束和激光束等进行加工,使轧辊表面加工得更加均匀、轧辊形状更加妥当。
在热轧过程中,确保材料的咬入性能,提高轧辊的耐磨性,防止轴与轴承等的热胶着是重要的课题。
目前轧辊一般是使用高速钢,但希望开发出高载荷轧辊和轧制工具,以适应更大的压下轧制要求。
提高轧辊和轧制工具的耐磨性、抗事故性和耐桔皮状缺陷性是轧制技术飞越发展所不可缺少的重要技术,从减轻环保压力的观点来看,这些技术要素今后也是很重要的。
3、钢板3.1 连续轧制和直接连接轧制日本自1968年开发了森吉米尔式多辊轧机的全连续式串列式冷轧机(TCM)和1970年开发了四辊轧机的全连续式TCM以来,轧机的连续化已取得很大的进展,目前日本国内的主要轧机都实现了完全连续化。
完全连续轧机的技术可以和轧机的上下工序连接,因此1986年开发出了酸洗—TCM—连续退火成套设备。
完全连续化的开发包括了轧制生产计划可以随意变化、稳定焊接技术、带材稳定移动技术、前进方向可变装置等。
在冷轧的连续化之后,1996年首次在世界上开发出了热轧的连续化技术。
它是在粗轧结束后将前后轧材在进入精轧机前面进行焊接,使精轧机在无切头切尾的状态下进行无头轧制的技术,解决了产品前后端部的质量问题,同时使极薄钢板和新材质钢板的生产技术变得有可能。
自1989年将50-100mm厚的薄板坯连铸机和轧机直接连接的紧凑式轧机诞生以来,其建设数量逐年增加,目前在日本以外的国家中至少已建设了50套。
紧凑式轧机的特征是设备投资少、交货期短,它可进行没有水冷滑轧造成黑印的等温轧制,如果采用长的板坯,还能进行半无头轧制,可以预计今后其应用将越来越广,同时能进一步提高产品质量。
另外,将来在带材浇铸机应用的趋势引人关注。
3.2 新型轧机关于轧机辊距的控制,轧辊项弯装置是关键。
众所周知,日本以20世纪70年代后期出现的六辊变速轧机(HC轧机、UC轧机)为契机,开发了交叉辊薄板轧机(PC轧机)、双轴承座顶弯装置(DC-WRB)、在小直径工作辊上装有侧支撑辊的六辊FFC轧机、Z-Hi轧机、多辊型CR轧机、KT轧机、轧辊本身具有可变凸度型的VC轧辊、TP轧辊、NIPCO轧辊,还有采用在线磨削的轧辊磨床(ORC)等,这些新型轧机为世界轧制设备的发展做出了很大的贡献。
另外,还研究开发了采用1机架多道次轧制技术的各种轧机,但其应用仅限于特殊材的轧制。
3.3 板材中心凸厚部分和板材形状的控制板材轧制时的中心凸厚部分和板材开头的控制是对同一现象进行控制的技术。
由于前者的控制精度在数μm~数10μm就可以了,而后者的控制精度应在0.1μm 或小于0.1μm,因此被视为不同的技术。
在对比较厚的钢板进行热轧时要控制板材的中心凸厚部分比率保持一定,在考虑形状后进行薄壁化轧制。
虽然这是常规操作法,但由于板材端部容易产生三维变形,因此开发了控制边缘凸度的技术。
例如,有采用立辊轧机减少边缘损失的方法、在轧机上下辊之间使圆盘状水平辊向板的两边挤压,一面约束宽度一面进行轧制的方法、还有采用带有锥度工作辊的轧机和交叉辊轧机进行轧制的方法。
因此,可以预计今后仍将积极利用三维变形的技术来控制板材中心凸厚部分。
在形状控制方面对板厚(轧辊间隙形状)控制的精度要求非常严,这是因为只要控制精度有一点点的偏差,板材就会出现板厚偏差很大的形状缺陷。
陡度在0.5%以下,就可以视为形状良好,延伸率偏差为6.2*10-5(6.2Iunit),1mm 板厚的压下量偏差为0.06μm。
因此,实现高精度轧制当然离不开轧辊的局部矫直和材料的横向移动所产生张力的缓和稳定作用,但在轧制过程中使轧辊间隙形状和板材的中心凸厚部分一致是控制形状的基础。
轧辊挠曲、热凸度、母材形状、机械试验值的偏差和轧辊耗等会对轧辊间隙形状和板材中心凸厚部分产生影响。
为精确控制形状,必须对从低次函数到高次函数这一大范围内的形状偏差进行修正,因此将新型轧机的形状控制传动装置进行组合,采用多变量控制理论等复杂而又精密的控制方法进行形状控制的趋势将进一步增大。
3.4 板厚控制随着钢板加工自动化程度的提高,为排除加工过程中的故障,用户对钢板制品的板厚精度要求越来越高。
将支撑辊的油膜轴承替换为滚柱轴承,采用高性能油压压下装置消除和控制轧辊偏心已取得很大的发展。
作为轧机用传动装置,所有AC传动装置都形成了标准数字化控制。
AC传动装置的优点是,在结构上已完全采用电刷、单机容量增大,在性能方面已达到高精度、高应答化、可变速度范围扩大。
在以往的板厚控制装置中有自动测量调整装置(AGC)、监视AGC、FFAGC和游标尺AGC。
在最新的串列式轧机中,在此基础上还开发了轧机速度数字化控制、轧辊偏心控制、机架间的无干扰控制和在线板厚变化控制等技术。
尤其是为使连续式轧机能在不停机的情况下对轧机入口侧依次焊接的钢种、板厚、板宽不同的材料进行连续轧制,因此通过抑制张力过度变化,协调式地改变各机架的轧辊位置、轧制速度等在线板厚变化控制技术是很重要的。
由此可大幅度减少板材穿过轧机和切头切尾落料造成的轧辊损伤和板材等外品,同时提高对小批量订货的适应能力。
另外,它也是紧凑式轧机实施无头轧制所不可缺少的技术。
3.5 平面形状和板宽控制在厚板和热轧钢板生产工艺中板宽浇注技术在20世纪80年代就已确立其基本技术。
在厚板生产方面有,大幅度提高合格率的平面形状控制新技术MAS (Mizushima Automatic Plan View Pattern Control System)轧制法和附设的接近水平轧机的立辊轧机设备。
MAS轧制就是对各种钢板在轧制终了后的平面形状控制变化量进行预测,根据预测的变化量,给出轧制过程中板坯厚度形状,最终将平面形状变成矩形的方法。
热轧时实现将连铸机和轧机有效直接连接的板坯宽度定径技术、大幅度提高热轧钢板宽度精度的热轧板宽度控制技术、精轧时利用机架间的立轧机和张力控制来提高尺寸精度的技术、尤其是采用冷轧TCM和冷轧工艺线的板宽控制技术等都是日本开发的领先于世界水平的独有技术。
4、钢管在最近20年的发展中,首先应举出的是无缝钢管用钢坯的连续浇铸技术。
随着圆钢坯质量的提高和制管技术的进步,采用热挤压法生产的13%Cr钢和奥氏体系不锈钢已改变了轧制方式。
最近已开发了圆坯连铸和制管、热处理直接连接的技术。
4.1 穿孔轧制使用方钢坯的PPM(压力辊穿孔机)已被替换为使用圆钢坯的斜辊穿孔机。
在穿孔方法变化中值得注意的是圆锥形穿孔机和被称作交叉穿孔机的交叉辊穿孔机的发展。
圆锥形穿孔机的优点为是具有旋转锻造的效果和抑制圆周方向剪切变形的作用,因此可以抑制钢管内面的缺陷,可用于难加工性材料的穿孔,尤其是可以用于扩孔和薄壁穿孔。
采用普通穿孔机时壁厚/外径比(T/D)的极限为大约6%,而采用圆锥形穿孔机时能进行T/D为3.2%的薄壁管穿孔。
4.2 拉伸轧制芯棒式无缝管轧机已向大型化(最大16-3/4”轧机)和紧凑化方向发展。
在轧制过程中将芯棒速度保持在一定的芯棒前沿技术已确立。
由于能进行上述的扩管和薄壁穿孔,因此芯棒式无缝管轧机实现了紧凑化,即机架数由7-9机架减为4-5机架,穿孔机和芯棒式无缝管轧所需的能源消耗共计可减少20%左右。