supplier_audit_form
汽车类供应商准入审核报告 中英文双语版

Supplier Approval Audit Report 供应商准入审核报告Table instructions:表格使用说明:SUPPLIER SELF ASSESSMENT 供应商自评• The supplier shall use this tool to complete a Self Assessment in advance of the CATL on-site audit.• 供应商需要在CATL现场审核以前,用此评审标准进行自审。
• By completing the Self Assessment, the supplier will be able to prepare for the audit and seek advance help and guidance from CATL SQE to be best positioned for success. The supplier should use this opportunity to ask questions to clarify or better• 在进行自审时,供应商可向SQE就审核具体内容进一步澄清并准备现场审核,以达到审核的最佳效果。
• The Self Assessment should be submitted to the responsible CATL SQE one week in advance of the on-site audit which will signal the Supplier's readiness for the formal audit.• 供应商在CATL SQE发出正式审核要求一个星期以前,将自审结果报给CATL SQE。
CATL ON-SITE AUDIT & AUDIT SUMMARY CATL现场审核• The CATL auditor usually includes the SRC, design , SQE. The SRC staff audit business ; design staff audit technical; SQE audit quality.• CATL审核员通常包括采购人员、设计人员、供应商质量管理人员。
供应商管理程序中英文版
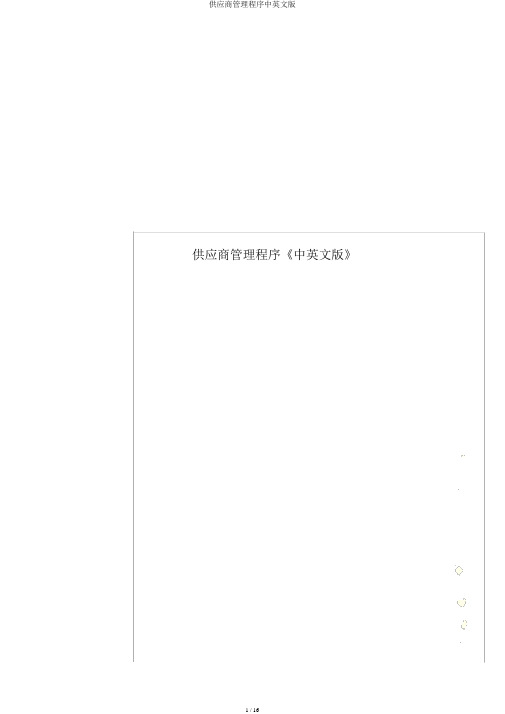
供应商管理程序《中英文版》Title 标题 :Doc No. 文件编号 :BZQP-7-07Supplier Quality Management Procedure Revision 版本 :4供货商质量管理程序Page 页码 :Page 2 of 16Rev.版本1 23 4Revision History 版本記录Change Description改正内容New releaseOriginated By Date编写日期KS Yang Sep.1,2006KS Yang July.1,2007KS Yang Oct.9,2007Frank Peng Nov.19,2009Approval & Distribution审批&散发APP Dept.Signature/Date APP Dept.Signature/ Date 審批部門簽署/日期審批部門簽署/日期生产部 PRD人力资源部HR品保部 QA财务部FIN资材部 Sourcing仓储部WH工程部 Engineering管理者代表MR生产及物料管控PMC厂长Plant ManagerOther Distribution Location :Checked by (Doc. Con.) :_______________Effective Date :___________________________________________________________________________________________________________________ Form No. 表格編號﹕Title 标题 :Doc No. 文件编号 :BZQP-7-07Supplier Quality Management Procedure Revision 版本 :4供货商质量管理程序Page 页码 :Page 3 of 16 Confidential & Proprietary Information of XXX (ZhongShan). XXX(中山)机密及专利文件1.PURPOSE 目的 :To establish a guideline to control and monitor supplier quality performance, manage supplier to improvequality system and product quality to meet XXX (ZhongShan) expectations.成立监控供货商质量绩效的目标,管理供货商改良质量系统及产质量量以达到XXX( 中山 )的希望目标 .2. SCOPE 范围 :This procedure applies to all suppliers that provides production material products to XXX (ZhongShan).此程序合适于XXX( 中山 )供应生产性物料的全部供货商.This procedure is applicable for QA to manage supplier quality and related issue only.此文件仅合用于QA 管理供货商质量及有关问题.3. DEFINITIONS定义:Key Supplier :The supplier provides the material that is either valuable and / or critical impact to product ’ s characteristics重点供货商 : 供应对产品价值或性能有重点影响物料的供货商.SRS: Supplier Rating System .SRS: 供货商评估系统 .FAI: First Article Inspection.FAI: 首件查验 .LAR: Lot Accept Rate from incoming inspection.LAR: 来料检查批接收率 .4.REFERENCE DOCUMENT 参照文件 :BZQP-7-06Supplier Rating System Procedure供货商评估系统程序.BZQP-8-07Corrective and preventive actions procedure纠正及预防举措程序.______________________________________________________________________________________________________Form No. 表格編號﹕Title 标题 :Doc No. 文件编号 :BZQP-7-07Supplier Quality Management Procedure Revision 版本 :4供货商质量管理程序Page 页码 :Page 4 of 165.RESPONSIBILITY 职责 :Purchasing staff采买Arrange consolidation of the overall material supplier performance and distribute to related parties.整理供货商质量绩效并公布给有关部门Review the supplier performance and enhance supplier improvement management.评估供货商绩效增强供货商改良管理.’ s support both for ongoing & future if necessary.Coordinate and plan supplier协调解规划供货商此刻及未来的支持5.2 QA 质量工程师.Follow supplier corrective action in line complaint.跟进产线投诉问题和供货商的改良行动.Define key supplier for evaluation or assessment with purchasing staff.与采买定义重点供货商以便评估.Review the assessment result for further improvement or supplier quality related matters..审察供货商质量有关的事项的评估结果,达到连续改良.5.3 ME 制造工程If necessary, ME will support QA to perform supplier process audit and technology evaluation.必需时 ,ME 将辅助QA 履行供货商制程审察及技朮评估.程序:Supplier Rating System供货商级别评估系统.Purchasing and QA shall select the key supplier and perform SRS. Refer to Supplier RatingSystem Procedure(BZQP-7-6).采买和 QA 选择重点供货商进行评估, 参照供货商评估系统程序(BZQP-7-6)Material qualification物料资格认证 .Under selection of a potential supplier, Sourcing or purchasing sends the specification ordrawing component requirements to supplier andEngineer instruct supplier to submitsample and related document (Attachment 1.)______________________________________________________________________________________________________ Form No. 表格編號﹕供应商管理程序中英文版Quality Procedure质量程序Title 标题 :Doc No. 文件编号 :BZQP-7-07Supplier Quality Management Procedure Revision 版本 :4供货商质量管理程序Page 页码 :Page 5 of 16选定部分供货商后,资材部或采买将零件规格要求或图纸转交给供货商﹐工程部工程师指导供货商依照提交样品和有关档(附檔1)Engineer will cooperate to complete FAI, detail operation process refer toInspection Instruction (BZQAWI-003) ”.工程师将达成物料的FAI 检查 ,详细作业方法请参照“来料首件检查指示“ Incoming First Arti(BZWIQA- 003) ”After the internal inspection completed, QA submit the passed part and FAI documents to customerfor make final approve if need. After customer approve the sample, QA distribute the approvedsample and relative files to IQC and buyer as the proof of approved by XXX (ZhongShan).内部检查达成后, 如客户要求, QA 将零件同意的数据(零件样板 ) 和同意 . 客户检查并同意后, QA 将客户最后认可的样板及有关文件散发至FAI报告送与客户IQC 和采买 ,作为样板被XXX( 中山 )认可的依照 .If material is rejected by customer, the original copy of material approval should return back to QA.如零件认可被客户反对, 则认可零件退回给QA.重复步骤 6.2.1 至 6.2.4.6.2.4.1 For the critical to quality indirect material and not customer specified ,new developed suppliermaterial needs to pass Engineer ’ s approval, and send to customer for appas required.roval对于客户未指定的间接物料,在其对产质量量有重要影响的状况下,新物料需要经过工程师同意 ,假如客户要求将送给客户进行同意.Material disqualification procedure.物料资格撤消程序6.2.5.1 In the below cases, IQC or buyer has the authority to request and disqualify suppliersupply, and IQC rise a material disqualification request.( BZQP-7-07F01.1 )’ s pa当发现以下状况时, IQC或采买有权对供货商提出撤消其生产件供应资格的申请,而且该申请将以物料供应资格撤消申请书形式提出( BZQP-7-07F01.1 )6.2.5.1.1 Serious quality issue from supplier (example: safety issue, use bannedmaterial, or seriously impact production in XXX etc).部品发现重要质量问题(如安全问题,使用禁用物料,或对 XXX造成重要生产影______________________________________________________________________________________________________Form No. 表格編號﹕Title 标题 :Doc No. 文件编号 :BZQP-7-07Supplier Quality Management Procedure Revision 版本 :4供货商质量管理程序Page 页码 :Page 6 of 16响等 ).6.2.5.1.2More than 3 times claims for material quality from IQC or production line within onemonth and there is no effective action to improve the quality after IQC warn or QAperform factory audit.在一个月内IQC 拒收三批以上的物料或生产线对该物料有三次以上的质量投诉而且在IQC 通知供货商或对供货商进行审察后供货商在质量方面没有有效改良.6.2.5.1.3 Continual twice get red card in supplier rating system (for single sourcing supplier,materialis disqualified except customer approval)在供货商级别评定中连续两次评定为不合格(对于单调货源供货商 ,除非客户同意 ,不然将撤消其资格 ).Customer requirement 客户要求 .Others 其余 .Supplier Qualification & disqualification供货商资格认证及撤消6.3.1 For new supplier (or second source) who is opened by XXX (ZhongShan), QA needs to qualifynew supplier. For the current suppliers, purchasing can list them directly in the A VL list.对于 XXX( 中山 )开发的新供货商 (或许第二供货商), QA 需要进行新供货商的资格认证.对于现有的供货商 ,可直接进入AVL 表 .6.3.2There are 5classifications of“ supplier qualification” process will be applied:将有 5 个不一样级其他文件被引用到供货商认证中去:NDA (Non-disclosure agreement):保密协议This is a non-disclosed agreement for supplier with XXX (ZhongShan)before business. Supplier must obey XXX (ZhongShan) businessrequirements, can not disclose any XXX (ZhongShan) businessinformation, drawing, technical information, pricing information toany other 3rd party under this agreement withoutXXX(ZhongShan)permissions.______________________________________________________________________________________________________Form No. 表格編號﹕Title 标题 :Doc No. 文件编号 :BZQP-7-07Supplier Quality Management Procedure Revision 版本 :4供货商质量管理程序Page 页码 :Page 7 of 16此档是供货商与XXX( 中山 )买卖合作以前的保密协议.供货商一定恪守XXX( 中山 )商业要求 , 不可以揭穿任何XXX( 中山 )买卖方面信息、图纸、技术信息、价钱信息等给任何未经XXX( 中山 ) 受权的第三方机构 .6.3.2.2 Supplier reliable investigate report:供货商信用度检查This report is to investigate supplier reliable information in market andensure supplier can show enough capability to support XXX(ZhongShan)此文件用以检查供货商的市场信息以保证供货商有足够能力和XXX( 中山 )配合 .6.3.2.3 Supplier Qualification Summary Report供货商认证总结报告This report is conducted by purchasing for one supplier evaluation summary report &qualification status.此份报告由采买主导用以供货商评估总结及认证状况.6.3.2.4 Supplier audit report, QA is responsible for perform audit ,if it is necessaryand applicable, QA releases the copy of report to purchasing.供货商审察报告,QA 有必需且可实行状态下将对供货商进行审察,QA将复印件散发至采买 .6.3.2.5 Supplier Disqualification Request供货商资格撤消申请 .This report will be requested by purchasing & QA to disqualify a supplier; andthe applicant will fill in the application. It will be effective by theirmanager and Plant Manager approval.此份报告由采买及QA 用以供货商资格撤消申请.由各自部门经理和厂长署名后奏效.6.3.3Primary opportunities for one qualified supplier:供货商认证的首选时机 :A well developed quality management system.优异的质量发展管理系统 .Reasonable price and forwardly to support XXX (ZhongShan) on cost down approach.能够接受的价钱水平并主动配合XXX(中山 )降低成本 .Capability of ensuring stable and punctual material supply chain system.能够保证稳固而准时的供应链系统.Good service can support XXX (ZhongShan) at emergency; provide XXX (ZhongShan) on ______________________________________________________________________________________________________Form No. 表格編號﹕Title 标题 :Doc No. 文件编号 :BZQP-7-07Supplier Quality Management Procedure Revision 版本 :4供货商质量管理程序Page 页码 :Page 8 of 16reliable & acceptable information; quickly respond on claims & remarks; support XXX (ZhongShan) on flexibility;forwardly to provide XXX (ZhongShan) on Information (News, Technical support).优异的服务; 能够在紧迫状况下支持XXX(中山);供应给XXX(中山 )合理的和能够接受的信息; 快速回馈XXX(中山 )的诉苦及有关要求; 弹性地服务XXX( 中山 ); 主动配合XXX( 中山 )实用的信息(新闻、技术支持).Buyer gathering information of supplier: company profiles, brochures; productsinformation (samples, specs), etc. If it matches current business requirments, then willsend “ Supplier Reliable Investigate Report” to supplier-evaluation,forself requestsupplier to submit self-evaluation data to purchasing for evaluation, based on currentcommodity supplier base status, technology, quality, cost, responsiveness, service, delivery,stability &capability, environmental & safety, If recommended supplier matches XXX’ srequirements, purchasing wil l lead the“ Development team” to audit supplier.采买采集供货商信息: 企业资料及手册; 产品信息(样品、规格)等 . 假如供货商切合目前XXX( 中山 )商业需求 , 负责采买将“供货商信用度检查报告”发给供货商进行自我评估; 要求供货商供应自我评估数据并回馈给采买,采买依照XXX现有商品供货商基础、技术、质量、成本、反响速度、服务、交期、稳固性和能力、环境及安全等予以综合评估. 假如介绍的供货商切合XXX( 中山 )要求 ,采买将安排发展团队予以评鉴.Purchasi ng will lead “ development team ” to summarize “ Supplier Qualification Summary Report evaluaterecommended supplier will be qualified supplier. XXX (ZhongShan) qualified supplier must be required:采买将主导“发展团队”总结“供货商认证总结报告”,以评估介绍供货商成为合格供货“BZWIQA-015商 .XXX( 中山 )合格供货商一定同时知足以下要求:Pass XXX (ZhongShan) QA audit if it is applicable. The approval classification will refer tosupplier audit &qualification”.在审察能够进行和需要的条件下,供货商须经过XXX(中山 )QA稽核 .有关认可条件请参照“BZWIQA-015供货商审察和认证指示”.Reasonable price and proactively to support XXX (ZhongShan) on cost reductionapproach.合理的价钱水平易主动配合XXX( 中山 )进行成本降低.Supplier has a capability & stability system to support XXX (ZhongShan);______________________________________________________________________________________________________ Form No. 表格編號﹕Title 标题 :Doc No. 文件编号 :BZQP-7-07Supplier Quality Management Procedure Revision 版本 :4供货商质量管理程序Page 页码 :Page 9 of 16供货商拥有稳固的能力服务XXX(中山).Supplier can provide XXX (ZhongShan) technology solutions proactively.供货商能够主动供应XXX( 中山 )资料技术解决方案.“ Acceptable”and or above classification status approached to“ Cost competitive, Stability Capability, Technology”criterions.“价钱竞争性、稳固性及能力、技术”达到“可接受”或以上标准.“ Supplier reliable investigates report”willXXXbe(ZhongShan)matchedrequirements on supplier reliable survey.“供货商信用度检查”一定切合XXX( 中山 )对于供货商可信度检查要求.The supplier evaluation summarized report will be forwarded to supplier by purchasing. If openednew supplier which pass or conditional pass XXX (ZhongShan) audit, purchasing will create a vendorcode in system and pass to Finance, after the signature of purchasing Manager.采买将供货商评估总结报告转给供货商.假如新开发的供货商经过或条件经过XXX(中山 )的审察,采买将填写供货商朝码并经采买经理署名后,附上供货商评估总结报告交会计部.For customer specified suppliers, or suppliers are specified in customer BOM, QA donqualify supplier except customer request. QA will perform supplier audit when supplierquality performance is not satisfying. If supplier fail audit, customer shall approve qualityrisk assessment form ” if customerstilluse this source.’ t need对于客户指定的供货商必对此类供货商进行认证,或在客户BOM中指明的供货商.当供货商质量表现不好时,,除非客户有要求,不然QAQA 将履行审察。
Supplier Audit Check List供应商审核检查表

Observations and Notes
Supplier Response
Mandatory Key Questions N Y
N/A Explanation
N
N
N
N
N
N
N
N
N
N N N
OSA
2 of 7
Doubleclick cell if N/A
Partia
N
Y
N
Y
N
N
Y
N
N
Y
OSA
1 of 7
Doubleclick cell if N/A
Partial Credit
Full Credit
Assessment Item 12. Is the supplier ISO or TS registered? 13. Is there a formally documented system used to select and manage suppliers through advanced evaluation or by review of quality performance? (Verify if approved suppliers list exists) 14. Is there a formal corrective action program implemented for the Supplier's purchased material? How do they monitor their supplier compliance to this process? 15. Are raw materials / components identified and traceable to test or certification reports? ·Date Codes ·Serial numbers ·Certificates of Analysis ·Bar coding technology 16. Are raw materials / purchased components inspected, tested or otherwise verified prior to use? Do they use in-house testing or external lab tests? 17. If work is subcontracted to external sources, are there controls to assure the quality of the subcontracted work? 18. Is there a system for verification, storage, reporting and maintenance of their customer’s consigned material, equipment, tools, dies, patterns, gages? 19. Are the environmental conditions in the laboratory and work areas adequate for the work performed? Are the work areas organized (using 5S or other methods) for the work performed? Does the work environment appear safe? 20. Is Statistical Process Control being used as the parts are produced or after the fact? 21. Are statistical methods effectively used for assuring parts are produced within control limits (e.g., histograms, X & R charts, P charts, etc.). If yes, indicate the % of parts involved in the Notes field. 22. If control charts are used throughout the production areas are they used effectively? Note how many are attribute vs. variable charts, how many use control limits vs. spec limits, frequency and recency of updates. Check to see if out of control points are identified and acted on. Include comments in the Notes field. 23. Is there evidence of control charts leading to actions? 24. Are process operators and inspectors trained on the work instructions for their area? 25. Are machine operators and inspection personnel sufficiently trained to utilize the statistical process control concepts?
2009_TAPA_FSR_Audit_Form -简体中文版本

Acceptable 合格
Audit Results 审核结果
Facility Classification 仓储设施评级 Total Points 总得分 Possible Points 可能获得分数 Mandatory Items(M) 强制性项目(必选项)
A
0.0
154 Did not meet 1 or more Mandatory Items 未满足一个或多个强制性项目(必选项)要求
Score 得分
2.1 Office Entrances 办公区入口
(M) 2.1.1 – Visitor entry point(s) controlled. (必选项)访客到办公区域的各进入点均有控制措施
(M) 2.1.2 - Employee entry point(s) controlled. (必选项)员工到办公区域的各进入点均有控制措施
仓库评级
"X" if not
Scored 如不计分,
请划"X"
Total Score 总得分
A
0
A
0
A
0
A
0
A
0
A
0
A
0
A
0
A
0
A
0
A
0
COMMENTS 备注
A Facility 2009_TAPA_FSR_Audit_Form - Simplefied Chinese rev1_proofread_FINAL.XLS © TAPA 2000-2009, All Rights Reserved
一至五部分各均达到60% )
Section 1 Score 第一部分得分
供应商审核流程图
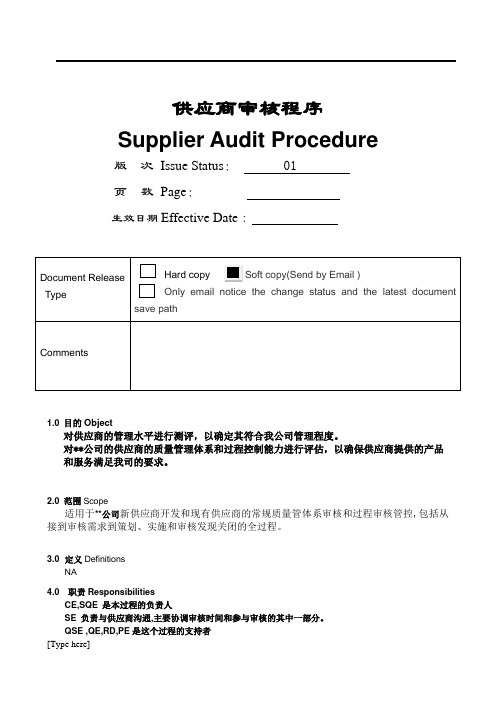
供应商审核程序Supplier Audit Procedure版次Issue Status: 01页数Page:生效日期Effective Date:1.0 目的Object对供应商的管理水平进行测评,以确定其符合我公司管理程度。
对**公司的供应商的质量管理体系和过程控制能力进行评估,以确保供应商提供的产品和服务满足我司的要求。
2.0 范围Scope适用于**公司新供应商开发和现有供应商的常规质量管体系审核和过程审核管控,包括从接到审核需求到策划、实施和审核发现关闭的全过程。
3.0 定义DefinitionsNA4.0 职责ResponsibilitiesCE,SQE 是本过程的负责人SE 负责与供应商沟通,主要协调审核时间和参与审核的其中一部分。
QSE ,QE,RD,PE是这个过程的支持者[Type here]25.0 过程概要 General Process职责 过程概要 接口文件Responsibility General Process connection Doc.6.0 操作流程Operation process职责Responsibility接口文件 Injection Doc.相关部门人员 Relative department person供应商质量工程师 Supplier Quality Engineer Audit Team OR Boss供应商质量工程师 Supplier Quality Engineer战略采购工程师Sourcing Engineer相关记录 N/A 年度审核计划 Annual Audit plan 审核日程表 Audit Agenda审核日程表接口文件职责供应商质量工程师 Supplier Quality Engineer供应商质量工程师 Supplier Quality Engineer 材料工程师 Commodity Engineer供应商质量工程师 Supplier Quality Engineer 材料工程师 Commodity Engineer供应商质量工程师 Supplier Quality Engineer 材料工程师 Commodity EngineerN纠正措施报告 Corrective&Preventive action reportSupplier Capability Assessment Audit **QF352 supplier product/process audit report **QF566 ** eis Electronicpart Supplier evaluateForm备注Comments:1. 审核需求如下:1.1 新项目的导入,Sourcing部门提出新供应商审核要求1.2 年度审核1.3 如果需要的话,特殊产品的过程和产品审核,质量投诉的现场审核。
英文版 supplier-audit-form

Management Responsibility Yes No N/A 1. Does the company have a written quality policy or statement identifying the company’sobjectives and commitment towards quality?2. Is the written statement oriented towards reduction, elimination, and prevention rather thandetection of product defects?3. Is the quality policy effectively communicated so that it is understood and maintainedthroughout the organization?4. Is there evidence that cross functional teams are involved in the quality planning process?5. Is there documented evidence, supported by appropriate records, that upper management isproactively involved in maintaining the quality system?6. Are quality responsibilities clearly defined and adequately staffed with qualified andexperienced personnel to assure effective implementation of quality policies as well as ofthe achievement ofquality objectives?7. Is there a clearly identified supplier representative whose function includes ensuring that theelements of customer standards are implemented and maintained?8. Do records on file indicate that the management of the organization periodically reviews thequality system adopted to assure compliance to the requirements of customer standards?9. Do records indicate a documented and controlled Business Plan which includes short and long termappropriate?10. Are the company level data being used to monitor trends in terms of quality, operational andcustomer performance?Quality System1. Is there a documented comprehensive quality system capable of meeting customerrequirements?2. Are quality procedures aligned such that they are consistent in supporting the written statementof corporate quality policy?Contract Review1. Does the supplier conduct a documented contract review per internal procedure(s) to ensure thatall requirements are thoroughly understood and are within the supplier’s capability prior toorder acceptance?2. Is there documented evidence on file to indicate deployment of customer contract requirementsinto the quality system?Document Control1. Has the supplier established and documented a procedure or procedures for controllingdocuments and data?2. Per the procedure(s) are all documents reviewed and approved for adequacy by authorizedpersonnel prior to release for use?3. Are changes to existing documents reviewed and approved by the functions/organizations thatperformed the original approval?4. Are all changes (revisions) identified on each document and do these revision notes indicatethe purpose/reason for the change?5. Are special characteristic symbols, where applicable, shown on process control plans and otherpertinent documents such as control charts, in-process instructions, etc.?6. Does the supplier formally acknowledge receipt of customer prints with all part number,customer drawing, and purchase order revision level changes?7. Is there a documented procedure to assure that correct revision level customer drawings andspecifications are always available and in use?8. Is there a procedure in use that defines record retention practices, location, and retrievalmethods?9. Is the method of record retention accurate, accessible, and readily retrievable?Purchasing1. Is there a documented procedure for the qualification of sub-suppliers which includes anevaluation of their business practices, policies, and procedures?2. Is an on-site survey or assessment conducted at the sub-supplier's manufacturing location prior to the issuance of a purchase order and does it include a performance evaluation based onquality, delivery cost, and technical support?3. Does the supplier review and approve purchasing documents for their adequacy of clearlyspecified requirements prior to release of the purchasing document, i.e., quality requirements, description of the product or service being ordered, local government safety and environmentalregulations, etc.?Product Identification and Traceability1. Is there a method and a procedure of identifying the product throughout its manufacturing, anddelivery stages?2. Do records indicate that lot identity and disposition are maintained throughout the supplier’smanufacturing and delivery process to assure lot integrity and traceability to materialsused and processes performed?3. Does the method used indicate processing and inspection status of product throughout thesystem, including storage and in-process holding areas?Process Control1. Are individual operations specified by detailed work instructions on the traveler or posted ateach operation per QS-9000 Element 4.9?2. Does the supplier's procedures require approval of the operator, process and equipment afterset-ups, tool changes, etc., prior to actual use?3. Are workmanship standards defined to accept/reject criteria by written specifications,photographs, and/or labeled limit samples for operators?4. Is there a process to identify all applicable government safety and environmental regulations,i.e., handling, recycling, eliminating or disposing of hazardous material?5. Are the supplier's plant operating practices in accordance with these approved governmentsafety and environmental regulations as well as measures that include machine location/operation, uncluttered aisles, slippery or dangerous floor conditions/markings and overhead/forklift or additional methods of material handling?6. Is there a process router/traveler that defines each step of the manufacturing process in useon the production floor?Incoming Materials Control1. Is there a procedure for the control and verification of purchased material prior to release toproduction and is there evidence of adherence to the procedure?2. Are purchased materials traceable to material certifications and used on a first-in, first-out basis?3. Does the supplier track purchased material rejection trends and rejection rates in Parts PerMillion (PPM's) or by any other acceptable means?4. Does the procedure require positive identification of material released to production that is notverified, for the purpose of potential positive recall, should a discrepancy be detected afterward?5. Have established goals been directed towards the reduction of incoming inspection activities,where applicable, by "ship-to-stock" and/or certification programs?1. Is first piece inspection (set-up approval) required after each machine set-up, tool change,or process change per a formal quality plan or documented procedure?2. Does the supplier inspect, test, accept/reject, and identify product as required per a formalquality plan or the documented procedure?3. Are set-up parts identified and segregated from production parts to prevent their inadvertentshipment to the customer?4. Are sample sizes and frequencies of inspections performed and specified per a formal qualityplan adequate as well as a documented procedure, and are they adequately and uniformlydetermined?5. Are adequate records maintained of all inspections and tests?Final Inspection and Testing1. Is final inspection and testing performed in accordance with the quality plan or documentedprocedures to verify conformance of the final product to the specified requirements?2. Is all product held until all activities associated with the quality or documented procedures have been satisfactorily completed and the associated data and documentation is verified andapproved?3. Are adequate records maintained of all inspections and tests?4. Does the supplier have adequate safeguards in place to prevent product from being shippedwithout proper verification, acceptance, and authorization from designated personnel?5. Do records indicate that the supplier tracks outgoing rejection trends and rejection rates inParts Per Million (PPM) or by any other acceptable means?Inspection, Measuring and Test Equipment1. Does the supplier have a program or documented procedures to control, calibrate and maintaininspection, measuring, and test equipment?2. Does the supplier establish, document and maintain calibration procedures, including details ofequipment type, identification number, location, frequency of checks, checking method,acceptance criteria, and the action taken when results are unsatisfactory?3. Are statistical methods (gage R&R and/or ISO-plot) used to determine stability and capability ofinspection, measuring, and test equipment, and are appropriate corrective measures taken whenthis equipment is deemed unsuitable for the specific application?4. Has the supplier determined and specified the required accuracy/precision?5. Does the statistical method(s) used demonstrate that the inspection, measuring, and testequipment (including software when appropriate) available is capable of the required accuracyand precision?Inspection and Test Status Yes No N/A1. Is inspection and/or test status appropriately identified throughout the production process?Control of NonConforming Product1. Does the supplier have documented instructions to isolate, identify, and control allnon-conforming material throughout the manufacturing process?2. Are the responsibilities for review and disposition of non-conforming and suspect productclearly defined in a documented procedure?3. Does the supplier have a documented procedure for immediate customer notification in theevent that non-conforming material is suspected of being shipped?4. Are products which have been dispositioned to rework or repair, handled with documentedinstructions that include re-inspection and re-identification (customer returns) prior to returningto the customer?5. Are customer returns subject to the same documented instructions and controls used to handlenon-conforming material from the manufacturing process?6. Does the supplier track the rejection rate of returned goods from customers in Parts Per Million(PPM) or by any other acceptable means?Corrective and Preventive Action Yes No N/A 1. Does the supplier have documented corrective action procedures for all non-conformancesdetected either in their facility or their customer's facility?2. Do records indicate that adequate analysis has been performed to determine and eliminate theroot cause of a nonconformance using appropriate methods of problem solving?3. Do records indicate that the supplier has verified the implementation and effectiveness ofcorrective action measures on subsequent production runs using mistake proofing methodologyas appropriate?4. Is the relevant documentation, i.e., Process Flow Diagram, PFMEA, Control Plan, workinstructions, etc., updated and re-submitted for review and approval?Handling, Storage, Packaging, Preservation, and Delivery1. Does the supplier have a procedure for handling, storage, packaging, and delivery of product?2. Does the supplier's records indicate conformance to the procedure and any additional customerspecifications?3. Do material handling methods prevent product damage and deterioration?4. If delivery performance is not 100% to schedule, are there appropriate analyses to determine rootcauses and corrective actions to prevent recurrence?Quality Records Yes No N/A 1. Does the supplier have a procedure for the retention of quality record, i.e., PPAP approvals,control charts, FMEAs, quality audits, etc., and does the procedure specify the types andlength of time records are to be retained?2. Are all quality records (hard copy or electronic) readily available, legible, and identified to theproduct involved?3. Are quality records stored in a suitable manner to prevent deterioration, damage, or loss?Internal Quality Audits1. Is there a documented procedure for use in conducting internal audits or evaluations todetermine the effectiveness of the supplier’s quality system in achieving stated qualityobjectives?2. Are the auditors or personnel conducting the audit independent of the function(s) beingaudited?3. Are audit findings submitted to the responsible personnel and upper management for reviewand used as a basis for continuous improvement plans?4. Are suitable root causes, corrective actions, and proper follow-ups for effectiveness indicated inthe audit records?Training1. Is there an established and documented procedure for identifying the on-going training needs ofemployees and are the needs being met?2. Are personnel assigned to specific tasks, qualified on the basis of their knowledge, education,training, and/or other skills as required?3. Does the supplier maintain a record of training provided to each employee in an easily accessibleand readily available format for quick reference when making work assignments?Servicing1. Is there evidence that the supplier has adequate procedures established for performing andverifying that the servicing meets the specified requirements related to managing customerStatistical Techniques1. Are statistical techniques being used to control processes, minimize part-to-part variation, andverify the capability of process parameters and product characteristics?2. Are statistical data summarized, reported, and acted upon (if corrections/improvements arerequired) on a regular basis?3. Are short-term capability studies conducted on all new or changed processes prior to runninginitial sample parts?4. Do production personnel possess adequate statistical skills and knowledge to understandControl Plan requirements, analyze data, and make the necessary corrections (if required) to theprocesses which they are monitoring?5. Are production personnel involved in the investigative, decision making, and problem solvingprocess for all activities related to process variability activities in their areas?Advanced Quality Planning1. Is there a documented procedure and/or stated commitment to use advanced quality planningtechniques on all new or changed products/processes?2. Does the supplier prepare a detailed Process Flowchart for each of his new/revised products orprocesses?3. From this flowchart, does the supplier prepare a Process FMEA (Failure Mode and EffectsAnalysis) and a asubsequent Control Plan?4. Do the Process Flowcharts, Process FMEA's, and Control Plans identify all significant activitiesfrom the purchase of raw material through shipment to the customer?5. Is there evidence that the Process Flowcharts, Process FMEA's, and Control Plans are actually Updated when changes occur in design, processes, or when new failure modes are identified bysubsequent rejections and root cause analysis?6. Are all revised Process Flowcharts, Process FMEA's and Control Plans sent for customerconcurrence of proposed changes prior to instituting any action?Continual Improvement1. Is the supplier involved in activities for the purpose of continuously improving the quality,cost, and delivery of products and services provided?2. Does the supplier have records that indicate the supplier has participated in Concurrent product/Process Development with any existing customers?3. Is there evidence in the supplier's records of set-up or cycle-time improvements which directlyimproved quality, capacity, or resulted in a cost reduction?4. Does the supplier use any automation techniques to improve product quality by eliminating thepossibility of operator error?5. Has the supplier developed any specialized inspection equipment to perform 100% checking ofdimensions deemed too critical for conventional inspection or statistical sampling errors?Facilities and Tooling Management Yes No N/A 1. Is the supplier's plant layout clean, efficient, organized, and well lighted with demonstratedevidence of "good housekeeping" being practiced throughout the manufacturing process?2. Is the quantity of equipment, size and physical plant layout capable of handling increasedproduction volumes without serious detriment to overall operations and part quality?3. Can the supplier show examples of Mistake-Proofing on fixtures, operations, or processes toeliminate the possibility of producing a defect?1. Does the supplier have a documented preventative maintenance system to assure thatmachinery, tooling, and equipment are maintained to support quality and production requirements?2. Is there a schedule of planned regular maintenance on all machinery, tooling and equipment usedto produce products including parts cleaning equipment?3. Are records available for all maintenance conducted within the facility (both regularly scheduledand any unscheduled emergencies) whether done by outside contractor or company employees?4. Are modifications or revisions of regular maintenance schedules based on tooling life studiesand previous maintenance histories including emergencies?5. Does the supplier use statistical data to reduce downtime (such as average number of parts runprior to tool sharpening or insert change)?6. Does the supplier monitor uptime/downtime on a real time basis as a measure of maintenanceprogram effectiveness?SURVEY COMPLETED BY:TITLE:DATE:Reference Question Surveyor’s Comments On Item Rating (*) Number。
Supplier Management供应商管理程序(中英文)

1.0 PURPOSE 目的1.1 The procedure standards the general rules for selection, evaluation and management ofsuppliers to ensure all what purchased including products and service aligned with company requirements.规范供应商的选择、评估和管理流程,确保所采购的产品和服务符合公司的要求。
2.0 SCOPE 范围2.1 Apply to all suppliers which provide products and service to company.适用于向公司提供产品和服务的所有供应商。
3.0 DEFINITIONS 定义3.1 Three types Suppliers 三类供应商:Type A: Suppliers which provide finished-goods, raw material in BOM and process subcontractin Routing.A类:提供成品,BOM中的原材料和产品加工工艺路线中的工序外包服务的供应商。
Type B: Suppliers which provide raw material and process subcontract for mould.B类:提供模具材料和模具加工供应商。
Type C: Other suppliers except type A, type B.C类:A、B类以外的其他供应商4.0 REFERENCE DOCUMENTS 参考文件4.1 ISO/TS 16949:2009 Clause 7.4 Purchasing 采购5.0 RECORDS 记录5.1 FN-PU-001 Supplier Audit Form 供应商调杳表5.2 FN-P∪-002 Approved Supplier List 合格供方名录5.3 FN∙PU∙003 Back Up Supplier List 备用供方名录5.4 FNFU-005 Supplier On S让e Audit Form 供应商现场评审我5.5 FN-PU-006 Supplier Performance Evaluation Form 供应商业绩考核表6.0 RESPONSIBILITY 职责6.1 .Purchasing department responsible for organizing the activities of research, selection, evaluate,monitor and control for suppliers of raw material in BOM and process subcontract in Routing, set up and revised "Approved Supplier LisΓ.采购部负责组织采购产品供方、外协加工方的选择、评价和监督控制,供方的审核评估、建立及修订“合格供方名单”;6.2 Quality department responsible for incoming inspection and quality evaluation, establishsuppliers1 quality records, and provide coaching and support for suppliers5 quality improvement when needed.质量部负责物料性能检验及产品品质评价,建立供方质量档案,并对供方的质量方面提供辅导。
Supplier Survey (Audit) Checklist form Rev 06(供应商审核)

品质系统评鉴 第 1 頁本次评鉴发现缺失Findings项次No.稽核单位Audit DEP 项目Item单项最高分Highest score评鉴结果Result评鉴合格率Qaulified Rate单元目标Target 1品质系统要求 Quality System Requirement484797.9%80%2文件管制与品质记录 Document Control and Qaulity Record484695.8%80%3原物料供应商管理 Supplier Management393897.4%80%4产品识别与追溯 Product Identification and Lot Traceability 515098.0%80%5检检与测试 Inspection and Test 363494.4%80%6仪器校验 Equipment Calibration 2424100.0%80%7客户服务 Customer Services454395.6%80%8资材管理/物管 Material Management 3636100.0%80%9生产排程管制 Production Schedule 272696.3%80%10采购 Purchasing605998.3%80%11Engineering设计管制 Design Control515098.0%80%46545397.4%80%分数Score32Conditionally Approved10有文件,绝大部份确实执行,少部份未执行Document but implemented record is incompeleteQualityMaterial 综合评分 Total有文件,确实执行良好Document and implementation are well done.评分标准 Standard品质系统评鉴结果Quality System Assessment Result供应商名称 北京中石伟业技术有限公司Approved厂址Adress: 北京经济技术开发区东环中路3号评鉴日期Date: 2012.7.31 供应商代表Member from supplier: 贾万明评鉴成员Survey team member:Rejected< 60 %80-100%60-80%注意:原则上每个小项目最多只问三个问题就做评分.Notice: The rule of audit is that three questions for every item.无文件,亦无执行No document and implemented record有文件,少部份执行,绝大部份未执行; 无文件,有执行Document with no implemented record; Implement without document 品质系统要求Quality SystemRequirement文件管制与品质记录Document Control and Qaulity Record原物料供应商管理SupplierManagement产品识别与追溯Product Identificationand Lot Traceability检检与测试Inspection and Test仪器校验Equipment Calibration客户服务Customer Services 资材管理/物管MaterialManagement生产排程管制Production Schedule采购Purchasing设计管制Design ControlForm No.:QM-Form-019Form Rev.:06Effective Date:2009/2/27Total Reteniton Time:3years。
【实用文档】QF-PR-08-01 Supplier audit form
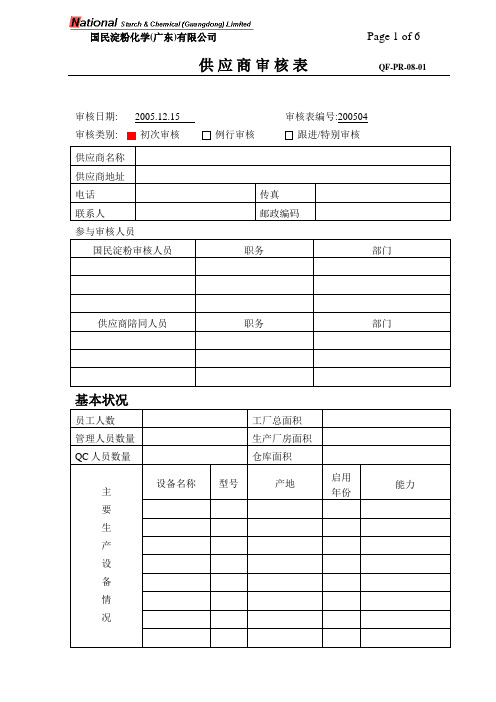
审核日期: 2005.12.15 审核表编号:200504审核类别: 初次审核例行审核跟进/特别审核供应商名称供应商地址电话传真联系人邮政编码国民淀粉审核人员职务部门供应商陪同人员职务部门基本状况员工人数工厂总面积管理人员数量生产厂房面积QC人员数量仓库面积主要生产设备情况设备名称型号产地启用年份能力设备名称型号产地启用年份能力主要检测设备情况材料名称产地等级使用情况原材料采购状况评估内容序号评估要求评估结果符合基本符合不符合说明A.管理职责1所有雇员都经岗位培训才能上岗,培训记录完整。
2有专职的质量负责人和质检人员。
3有明确的安全要求,特别在生产现场和实验室,工作人员都按要求穿戴好相应的防护服饰。
4工厂设计布局合理,环境符合环保要求,卫生状况良好。
B.质量保证 5 建立了文件化的质量管理体系,通过ISO9001质量管理体系的认证。
6 所有涉及质量相关的标准及操作规程都经QA或质量负责人批准。
7 所有原料和产品是由QA批准使用和发放销售。
8 提供分析报告(COA)连同货物一起送往客户,COA内容充分、清晰明了。
9 有清晰的检索批号系统,方便对原材料、半成品和成品进行追溯。
10 确保不合格品得到识别,防止被使用或交付;不合格品应有专人进行控制,采取措施对其进行处理后,应重新进行验证是否符合要求。
相应的记录必须完整。
11 对质量问题能及时进行分析,采取有效的纠正或预防措施。
12 通过内部、外部信息和数据的收集,提出组织改进的机会。
13 定期对质量管理体系进行审查,以发现问题并加以改进。
C.原材料检验14有原材料供应商确认或审核程序,并有记录在案。
15 采用经批准的标准取样程序。
16执行经批准的原材料验收规格标准,检验记录完整。
评估内容序号评估要求评估结果符合基本符合不符合说明D.工艺控制17使用固定的、经评审合格的配方进行生产。
18生产步骤有成文描述并被严格执行。
19制定影响产品质量的重要工序控制点及控制方法,记录完整。
出厂验收测试FAT

Supplier 制造商
嘉华通软
工厂测试方案
二、 确认内容................................................................................................................................................... 6 II. Content of confirmation.................................................................................................................................. 6 (Ⅰ) 文件检查 .................................................................................................................................................... 6 (Ⅰ) Document inspection ................................................................................................................................... 6 (二)配置检查................................................................................................................................................. 8 (Ⅱ)Configuration inspection ......................................................................................................................... 8
供应商审计表 调查表 Supplier Audit Form
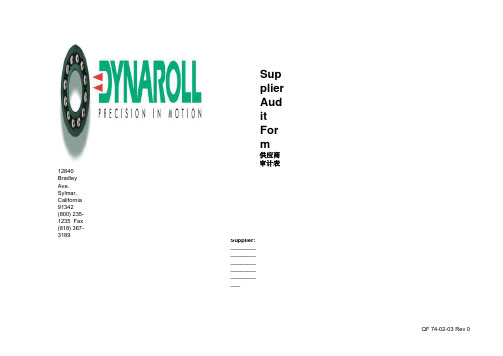
Supplier Audit Form供应商审计表12840 Bradley Ave. Sylmar, California 91342(800) 235-1235 Fax (818) 367-3189Supplier: ___________________________________________General System:一般系统:Auditor:_______________________ Audit Date:___________质量手册何时更新的?供应商是否有最新的组织架构图?供应商是否有客户?对质量作用和责任是否有清晰的定义?Evidence: ____________________________________________________________________________________________________有没有包括客户投诉的原因、纠正和预防措施Evidence: ____________________________________________________________________________________________________供应商是否有内部审核?Evidence: ____________________________________________________________________________________________________对客户有没有保证准时交付的系统?Evidence: ____________________________________________________________________________________________________有没有原材料的材质检验?Evidence: ____________________________________________________________________________________________________供应商是否可以全部追溯?Evidence: ____________________________________________________________________________________________________供应商是否有做首检、过程检验和成品检验?Evidence: ____________________________________________________________________________________________________在制造期间,是否所有阶段处理和充分存贮Evidence: ____________________________________________________________________________________________________有没有书面工作规程、标准操作程序等等?Evidence: ____________________________________________________________________________________________________Calibration:校准:供应商是否有被校准的设备?Evidence: ____________________________________________________________________________________________________对NIST 测量和测试设备的校准是否可以追溯?Evidence: ____________________________________________________________________________________________________12. Are there written work instructions, standard operating procedures, etc.? ___________1. Does the supplier have calibrated equipment? __________2. Is measuring and test equipment calibration traceable to NIST? ___________6. Does the supplier conduct internal audits? _____________7. Is there a system to ensure on-time delivery to the customer? ____________8. Is material awaiting inspection segregated from all other materials? _____________9. Does the supplier have lot traceability? ___________10. Does the supplier perform first article, in-process and final inspections? _________11. Is handling and storage adequate to preserve product quality during all stages of manufacturing? ___________3. Does the supplier have a company mission statement that commits to customer satisfaction? _____________2. Does the supplier have an up to date Organizational Chart? ___________1. When was the Quality Manual last revised? __________4. Are quality functions and responsibilities clearly defined? ____________ 5. Is there a system for customer complaints that include root cause, corrective and preventative actions? _____________Control of Nonconforming Product:不一致产品的管理:供应商是否有任何成绩显著的矫正措施报告?Evidence: ____________________________________________________________________________________________________有没有被核实的先前纠正措施报告预防行动的Evidence: ____________________________________________________________________________________________________是否有隔离被怀疑不一致的材料并做书面记录Evidence: ____________________________________________________________________________________________________有没有被发现的瑕疵工具、测量仪和测试设备Evidence: ____________________________________________________________________________________________________供应商是否有书面Evidence: ____________________________________________________________________________________________________Document Control:文件管理:供应商是否有对Dynaroll 的文件进行适当修正Evidence: ____________________________________________________________________________________________________Evidence: ____________________________________________________________________________________________________Training:培训:1. Does the supplier maintain training records? __________ 供应商是否维护训练记录?Evidence: ____________________________________________________________________________________________________Identification and Traceability:证明和可追溯:Evidence: ____________________________________________________________________________________________________Contract Review:合同复审:供应商如何执行合同复审?Evidence: ____________________________________________________________________________________________________Supplier/Service Control:供应商/服务管理:有没有批准的供应商名单?供应商是否对它的供应商进行审核或审查?Capability Controls:管理能力:供应商是否有执行SPC ?Evidence: ____________________________________________________________________________________________________1. How does the supplier perform contract review?1. Is there an approved supplier list? ________2. Does the supplier conduct audits/surveys of it's suppliers? _____________1. Does the supplier perform SPC? ___________________________________________________________________________1. How does the supplier identify product throughout the manufacturing process and do they perform inspections at specific intervals?Step Corrective Ac2. Are there examples of preventative actions from previous SCARs that can be verified? ____________3. Is suspected nonconforming materials segregated and are there written procedures/training? ___________3. Are there recall procedures for product measured by a discovered defective tool, gage, or test equipment? ____________4. Does the supplier have written re-work procedures and is material re-inspected after re-work? _____________1. Does the supplier have any outstanding SCARs? __________1. Does the supplier have the appropriate revision level on documents for Dynaroll (i.e.: drawings, etc).? __________2. Does the supplier have controls in place to assure the latest drawings, change notices and specifications are in use? __________Auditor's Comments:审核员注释:______________________________________________________________________________________________________________________ ______________________________________________________________________________________________________________________ ______________________________________________________________________________________________________________________ ______________________________________________________________________________________________________________________ ______________________________________________________________________________________________________________________ ______________________________________________________________________________________________________________________ ______________________________________________________________________________________________________________________ ______________________________________________________________________________________________________________________ ______________________________________________________________________________________________________________________ ______________________________________________________________________________________________________________________ ______________________________________________________________________________________________________________________ ______________________________________________________________________________________________________________________ Auditor's Signature: _____________________________ Date: _____________________审核员签字:Director of Quality Audit Approval: ___________________________________ Date: ______________________QA主管批准:Dir. of QA Comments:QA主管注释:______________________________________________________________________________________________________________________ ______________________________________________________________________________________________________________________ ______________________________________________________________________________________________________________________ ______________________________________________________________________________________________________________________ ______________________________________________________________________________________________________________________ ______________________________________________________________________________________________________________________ ______________________________________________________________________________________________________________________ ______________________________________________________________________________________________________________________ ______________________________________________________________________________________________________________________ ______________________________________________________________________________________________________________________ ______________________________________________________________________________________________________________________有客户满意度的公司代表声明?证据:客户投诉的原因、纠正和预防措施的系统?在制造期间,是否所有阶段处理和充分存贮能维护产品质量?、标准操作程序等等?ive Action Reports(SCARs)实的先前纠正措施报告预防行动的例子?是否有隔离被怀疑不一致的材料并做书面记录或训练?有没有被发现的瑕疵工具、测量仪和测试设备产品的回收程序?有书面重做做法,并且材料在重做以后被再检查?有对Dynaroll的文件进行适当修正的水平?供应商在使用中是否保证控制得到最新的图纸、更改通知和说明书?供应商怎么辨认在制造过程中的产品,并且他们是否进行检查在具体间隔时间?有执行SPC?。
【实用文档】supplier audit list-english version
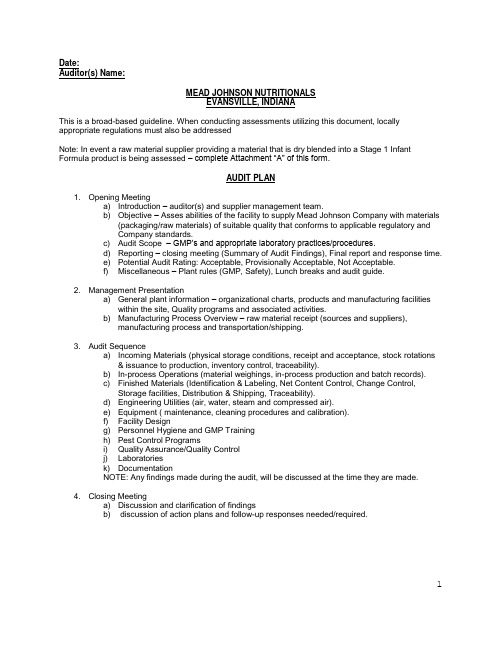
Date:Auditor(s) Name:MEAD JOHNSON NUTRITIONALSEVANSVILLE, INDIANAThis is a broad-based guideline. When conducting assessments utilizing this document, locally appropriate regulations must also be addressedNote: In event a raw material supplier providing a material that is dry blended into a Stage 1 Infant Formula product is being assessed –complete Attachment “A” of this form.AUDIT PLAN1. Opening Meetinga) Introduction – auditor(s) and supplier management team.b) Objective – Asses abilities of the facility to supply Mead Johnson Company with materials(packaging/raw materials) of suitable quality that conforms to applicable regulatory andCompany standards.c) Audit Scope –GMP’s and appropriate laboratory practices/procedures.d) Reporting – closing meeting (Summary of Audit Findings), Final report and response time.e) Potential Audit Rating: Acceptable, Provisionally Acceptable, Not Acceptable.f) Miscellaneous – Plant rules (GMP, Safety), Lunch breaks and audit guide.2. Management Presentationa) General plant information – organizational charts, products and manufacturing facilitieswithin the site, Quality programs and associated activities.b) Manufacturing Process Overview – raw material receipt (sources and suppliers),manufacturing process and transportation/shipping.3. Audit Sequencea) Incoming Materials (physical storage conditions, receipt and acceptance, stock rotations& issuance to production, inventory control, traceability).b) In-process Operations (material weighings, in-process production and batch records).c) Finished Materials (Identification & Labeling, Net Content Control, Change Control,Storage facilities, Distribution & Shipping, Traceability).d) Engineering Utilities (air, water, steam and compressed air).e) Equipment ( maintenance, cleaning procedures and calibration).f) Facility Designg) Personnel Hygiene and GMP Trainingh) Pest Control Programsi) Quality Assurance/Quality Controlj) Laboratoriesk) DocumentationNOTE: Any findings made during the audit, will be discussed at the time they are made.4. Closing Meetinga) Discussion and clarification of findingsb) discussion of action plans and follow-up responses needed/required.1GENERAL INFORMATIONA. Name of firm:B. Plant location:Address:Phone:Fax:Contact Person:E-mail:C. Quality Compliance audit ratings:1. Current:2. Previous:3. Is a follow-up audit necessary? If so, what is the recommended time frame?NOTE: STANDARDIZED AUDIT RATINGSAcceptable - No observations. Or, if observations are noted, they can be corrected within a reasonable periodof time (90 days), and none are deemed to present significant regulatory risk. No follow up audit is required,although monthly action plan updates must be received from the supplier.Provisional– Numerous observations noted, enough to pose a moderate regulatory risk to the product and/orMJ operations. Immediate attention should be given to addressing these concerns. A follow up audit must bescheduled, unless the auditor feels that sufficient evidence of corrective action has been provided within areasonable period of time.Unacceptable - Critical observation(s) noted. An immediate focused effort is required to correct deficiencies.Global Quality Assurance must be contacted immediately to determine the approval status of a supplier receivingan unacceptable rating. A recommendation to Global Procurement to cease operations or not to establish abusiness relationship with a firm may result.Definitions:Observations - those findings that pose a low or moderate regulatory risk with no immediate impact on MJoperations or consumer safety. An example would be a supplier that has quality systems in place, but fails tocomply completely with them, or lacks sufficient documentation of such.Critical Observations- those findings that would place the supplier and/or MJ at high regulatory risk. This alsoapplies to any finding that places consumer safety at risk due to product adulteration. An example would be asupplier that lacks a key quality system, such as GMP training, equipment calibration, or HACCP plan.D. Materials supplied to Mead Johnson Nutritionals:1. Product usage:2. Summary of Production Process:3. Lot coding system:4. Lot or Batch Size:E. Facility Information:1. Are steroids, antibiotics, pesticides, herbicides, fungicides or other high-risk, toxic materialshandled or manufactured at this facility?2. List other types of products manufactured at this location:3. List other products manufactured in the same facility as Mead Johnson Nutritionalproducts/materials:24. In general does the firm have a system of procedures and/or work instructions?5. Are they properly maintained?6. Facility maintenance:a. Raw Material Warehouse:b. Finished Product Warehouse:c. Processing/Packaging areas:Recommendation: One plastic piece in the foot of changing cabinet of pouch line hadbeen found , suggest to repair it and keep well7. Pest Control Programs:a. Raw Material Warehouse:Observation: Positions of No# 6,7 insectocutors in warehouse are wrong, their heightis low 5 ft.Observation: The insectocutor near door in packing workshop of pouch line isineffective.b. Finished Product Warehouse:c. Processing/Packaging areas:F. Personnel:1. Number of employees at this site:2. Quality Control/Assurance employees at this site:3. Technical Training and Documentation:4. GMP Training and Documentation:5. Uniforms:6. Key Personnel:G. Regulatory Inspections:1. Last Plant Inspection:a. USDA:b. FDA:2. Number and Nature of Observations:33. Action Taken in Response to Observations:4. Awareness of GMP requirements:H. Significant Changes Since Last Audit:1. Personnel:2. Facility/Equipment:3. Process:I. Is this facility Kosher Certified? If so, which Rabbinical council? Is D.O.U. a factor to beconsidered with this operation?J. Are there any carriers that may be allergens?K. Does the facility manufacture any items that represent a potential contaminant issue?L. Changes planned for the future?M. Other important information:RAW MATERIALSA. Raw Material Receiving, Identification and Storage:1. General cleanliness of warehouse:2. Bulk Storage Systems:3. Status Segregation Systems:4. Item Number Assignment:5. Lot Number Assignment:6. Receiving Log:Recommendation: When checking one inspection report of sucrose provided by Ruiliand compared its COA, found the supplier’s Lot No. is different. It is 0408021168 in MJreport, but it is 0408021168-HQ in supplier’s COA. Suggest MI to keep it consistent fortraceability.7. How are raw materials protected:Observation: One temperature record(Aug. 2004) of cool house showed almost all dataare above 8 dec. C.8. Separate reject area:B. Raw Material Sampling:1. Separate Room:2. Written Sampling Procedures:Bags/drums:Bulk Liquids:4Recovered Solvents:3. What precautions are taken to prevent/minimize contamination:4. Other pertinent information:PRODUCTION OPERATIONSA. Raw materials and Utilities:1. Where are raw materials weighed out for production:2. Precautions to prevent contamination:Recommendation: One vitamin premix label was reserved on the surface of dust binin weighing room though it was identified on the over cap, suggest to peel itthoroughly.3. Production Scale/Balance suitability:Observation: The suitability of N0.1# and No.2# balance in weighing room is notmatched, and No.1# balance can not detect 0.006 kg weight.Calibrated on a regular basis:4. Weighed-out materials identified:Observation: Workers in dumping room can not make sure the validity to dumpraw materials because they check major raw materials and minor raw materialsseparately .5. Bulk Ingredients:6. Utilities (water, steam, air, compressed gases, etc.) Source, quality, additives, andmeans of protection from contamination:7. Recovered solvents or other raw materials:8. Other pertinent information:Observation: On the checking table for leaking test in pouch line, found that someineffective documents (QA working instruction-6/27 and testing protocol ofSouthern laminates ) have been filed with effective quality records.Recommendation: The unit(mmH2O) of pressure meter of sampling room inweighing room is different from its record(Pa), suggest to integrate it.B. Processing - Equipment and Cleaning:1. Production Area Housekeeping.2. Equipment Identified:3. Dedication to the production of BMS materials:4. Equipment usage logs:5. Run in campaigns/series of batches:6. What constitutes a lot:7. Are batch records utilized:8. Batch records near equipment:9. Batch record documentation:10. Equipment Cleaning Frequency:a. Written procedures: -b. Types of Cleaning Compounds and Approvals:C. Packaging1. Is finished product or intermediate stored between steps, or is process continuous:Observation: Regarding the High/ middle/ low filter in hopper room 0f the 2nd room,there is no any evidence to show the filtrating efficiency was validate2. Are drums reused:3. Product filled in final containers or repackaged:4. Net contents of packaged product determined immediately after filling:5. Partial Drum/Packages:6. Labeling Systems:7. Final Operations performed in separate rooms:Observation: In packing room of pouch line, found more scoops taken from reworkedproducts, new equipment (not installed temporary) without identification.FINISHED PRODUCT WAREHOUSINGA. General Cleanliness of warehouse:sB. How are products protected from the elements:C. Status Segregation Systems:D. Separate Quarantine area for unreleased finished product:E. Separate reject area:F. Lot Selection System for shipments to Mead Johnson:G. How is returned product handled:H. Other pertinent information:QUALITY CONTROL LABORATORIESA. Laboratory/Analytical:1. Is Production or In-Process Lab separate from QC or finished product/release lab:2. Equipment - general description:3. Equipment calibration:Observation: The buret to test Vc have no validated label and QC person said thatactually they have not sent it for calibration.4. Reagent and Standard Solution Control:5. Are agricultural based raw materials tested for potential contaminants:6. What are the key microbiological and chemical analysis conducted on the finishedproduct:7. Environmental monitoring: -8. Are HACCP programs utilized:❑contamination control program covering chemical,physical, biological ,microbiological and allergens❑active HACCP program❑active, cross-functional HACCP team❑identification of the minimum required prerequisite programs (GMP, Pest control, Environmental control programs,etc)❑7 principles of HACCPequivalent to pasteurization?10. Are validated analytical methods utilized:❑written procedure❑signature of writer❑reference to the development of the analytical procedure❑validation data and evaluation❑applicable instrumentaion must be available.❑or compendia procedure11. What water quality testing is accomplished:❑ routine testing for chemical (pesticides and heavy metals)❑ microbiological testingB. Documentation/General:1. Are contract labs used:a. Name:b. Test performed:2. Incoming materials accepted on C.O.A.'s:3. Is there any verification of COA results:❑quality testing , COA reliance – adequate justification &appropriate identity testing utilized❑qualification program for approved suppliers4. Documentation system for test results for incoming and finished materials:❑electronic records / electric data – should be qualified for such❑back up file of data entered into a computer or related system❑consistent evaluation of test data prior to product release or issuance of COA❑procedures to prevent the release of below standard to unapproved materials/products and providing inaccurate results on COA5. Are reference samples of finished product and raw materials maintained:6. Other pertinent information:DOCUMENTATION SYSTEMSA. "Blank Master" forms approved:B. Specifications system for:1. Raw Materials: FCC,USP/NF etc:2. Finished Product:3. System for handling Mead Johnson Specifications:❑written specification for all materialsC. Testing programs for:1. Raw Materials:❑identity test ( or special reason for not doing the test) specific❑for given compound.❑or three non-specific tests (refractive index, density , boiling❑point, or melting point,optical rotation assay)❑microbiological quality testing❑holding samples of key starting materials original,separate❑sample, not left over material samples2. Finished Product:❑potential chemical contaminants monitoring as per RMAQD. Analytical Method System for:1. Raw Materials:2. Finished Product:❑written procedure : signature of writer , reference to thedevelopment of the analytical procedure, data of procedurevalidation, applicable instrumentaion must be available.❑compendia procedure (USP . NF orr AOAC International , FCC)❑records of analytical data – with signature of analyst and person who verifies calculations❑electronic records / electric data – should be qualified for such use.E. Written Stability Test Program for:1. Raw Materials:2. Finished Product:F. Batch Record System:G. Record Retention:❑retention period in compliance with MJNH. What type of change control programs exist:❑Change Control procedure – should be developed and utilized to communicate design, specification, process, and manufacturinglocation changes to the customer. This notification should bereceived and approved by the customer before the changed isimplemented.I. Other pertinent Information:❑retention period in compliance with MJNATTACHMENT “A”Minimum Microbial Control Expectations for Assessing Suppliers of Raw Materials that are DryBlended into Stage 1 Infant Formula Products.Listed below are minimum expectations for suppliers of dry blended raw materials that are dry blendedinto MJ Stage 1 Infant Formula powder product:ManagementDetermine if facility management (especially the QC manager) understands basic microbiological control practices. If the management staff is weak in this area, the site will need development prior to using the facility.Water ControlMicroorganisms need water to survive. A classic means of controlling microbiology of an area is to eliminate sources of water. When assessing suppliers look for evidence of water in critical dry processing areas.a. Water should not be visible in dry product handling areas.❑no signs of water leaks from roof,walls, or pipes . Common sources of water are hoses, cleaning stations, cleaning programs, pumps,and pipes.b. Management and personnel working in the area should understand the importance of water to themicrobiology of the product. Interview them to assess this know ledge. If the knowledge isn’tpresent, discuss with management and require diffusion of the knowledge throughout theirorganization.❑quality awareness – water and microbiology of productc. Determine if measures are in place to assure equipment is dried out sufficiently after wet cleaning.For example, equipment with gaskets may need to be disassembled to clean and to assure theinner surfaces are dry before the equipment is reassembled.d. Observe facility layout to determine if wet and dry processing areas are adequately separated.Traffic (human or equipment) should not travel from a wet processing area to a dry processingarea. Areas should be physically separated so that aerosol from wet areas does not travel to dryareas.e. Critical zones should be defined for the facility.❑critical hygiene zones are defined (dry powder handling areas)❑facilities to provide greater protection: physical barriers ;positive pressure ; airlock or anteroom ,shoe change area/room ❑dedicated personnel ; restricted entries❑assurance of control practices for maintenance staff and production personnelf. Relative humidity (RH) of dry material handling areas should be controlled to 50% or less.❑temperature and RH (50%) requirements are met.Cleaning ProgramsPrograms must be established for cleaning of interior and exterior of equipment and room surfaces.a. Cleaning programs must be written in sufficient detail to allow employees to know what to clean,how to clean it, what chemicals to use, frequency of cleaning, how the environment should beprotected during cleaning, how equipment is to be dried after cleaning and how/when toreassemble equipment.❑written comprehensive cleaning program.❑what to clean: product; piece of equipment or installation, room❑type of cleaning: dry, wet❑frequency of cleaning❑cleaning tool❑cleaning chemical and sanitiser ; concentration❑procedure for cleaning including protection of environment❑how and when to assemble/disassemble equipment❑drying procedure after wet cleaning❑responsibilityb. Cleaning programs should be established by an individual with sufficient knowledge/experience ofcleaning systems (typically the design is contracted to sanitizer companies). The program should be validated.❑utilitized cleaning specialists❑correct cleaner and disinfectant for specific applicationc. Inquire about equipment that is difficult to clean and assure cleaning programs address these insufficient detail.d. Inquire about the cleaning and maintenance program for hollow body equipmente. Inquire about the presence of equipment that can not be wet cleaned. Assure the cleaningprogram for such equipment is adequate.f. Cleaning programs should address the process to dry out equipment and process area after wetcleaning. If this is not validated, determine how they determine equipment is sufficiently dried.Dust ControlDust control is important to prevent tracking of/transfer of microorganisms into critical processing areas ❑airborne contamination (powder spills)a. A moderate to heavy build up of dust should not be visible during the tour of dry processing areas.b. Equipment that generates dust such as sifters, mills, and dump stations should have a point ofuse dust control system.c. Housekeeping programs should be in place that requires dust be removed from the environmentat sufficient frequency to minimize material buildup.d. Some facilities use vacuum cleaners to assist with dust control. If these are used, they should bededicated to the critical zone and cleaned/emptied in a dedicated area located away from critical zones.e. Vacuums with filtered exhausts should be used.❑accessories are maintained and cleaned as necessaryProduct Contact AirAir that directly contacts powder should be controlled for microbes.a. Compressed air that may contact product or product contact surfaces should have in linebacteriological and particulate filters.b. Air serving fluid beds or powder transport systems should be filtered with HEPA filtersc. Preventative maintenance procedures must be in place for these filter systemsEnvironmental ControlFacility should have an established environmental program to assess microbiology of the environment to assure pathogens have not established themselves in the facility.a. Facilities should test critical locations in dry processing areas for Salmonella at least monthly.b. Monitoring should also be conducted for general microbial and fungal bioburden.c. Assess if the facility is willing to enact an environmental Eb test for cleaning effectiveness.d. Limits and corrective action plans should be in place for environmental findings.trend analysis, evaluation and corrective action。
SQE供应商稽核表
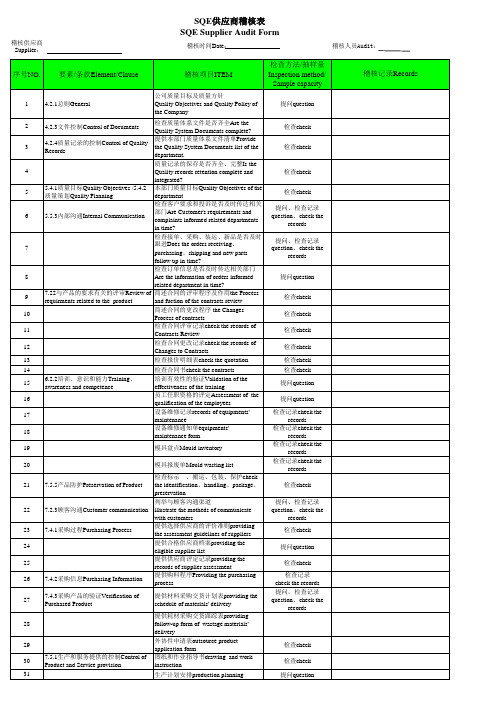
12
检查合同更改记录check the records of Changes to Contracts
检查check 检查check 检查check 检查check
13
检查报价明细表check the quotation
检查check
14
检查合同书check the contracts
检查check
requirments related to the product
and fuction of the contracts review
10
简述合同的更改程序 the Changes
Process of contracts
11
检查合同评审记录check the records of Contracts Review
检查check 检查check 检查check
integrated?
5
5.4.1质量目标Quality Objectives /5.4.2 本部门质量目标Quality Objectives of the
质量策划Quality Planning
department
检查check
6
5.5.3内部沟通Internal Communication
提问,检查记录 question、check the
records
提供耗材采购交货跟踪表providing
28
follow-up form of wastage materials'
delivery
检查客户要求和投诉是否及时传达相关 部门Are Customer's requirements and complaints informed related departments
供应商审核报告表中英文对照版
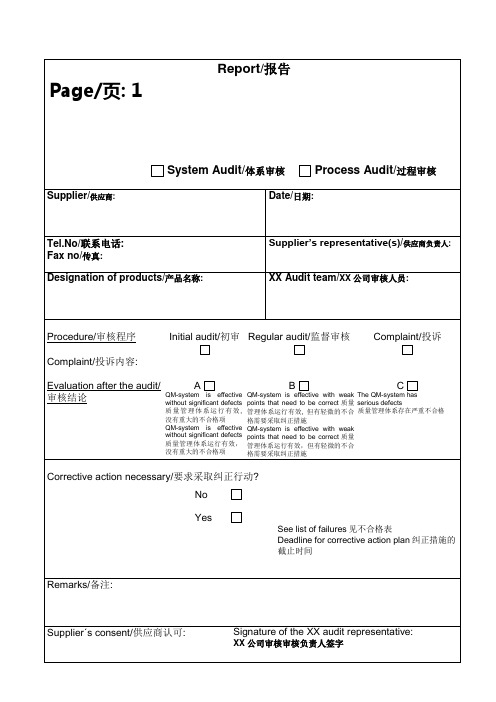
表格编号form code:A-PQEO-15/1-5/03Page页: 2Supplier/供应商: Date日期: QM audit/体系审核a = Requirements are fully satisfied/完全满意*) Please enclose copy附上复印件b = Requirements are satisfied with deviations/基本满意,但稍有偏差c = Requirements are not satisfied/不满意n.a. = Not applicable/不适用a = Requirements are fully satisfied/完全满意*) Please enclose copy附上复印件b = Requirements are satisfied with deviations/基本满意, 但稍有偏差c = Requirements are not satisfied/不满意n. a. = Not applicable/不适用a = Requirements are fully satisfied/完全满意*) Please enclose copy附上复印件b = Requirements are satisfied with deviations/基本满意,但稍有偏差c = Requirements are not satisfied/不满意n. a. = Not applicable/不适用Page页: 3Supplier供应商: Date日期:表格编号form code:A-PQEO-15/1-5/03a = Requirements are fully satisfied完全满意b = Requirements are satisfied with deviations/基本满意,但稍有偏差c = Requirements are not satisfied/不满意n.a. = Not applicable/不适用b = Requirements are satisfied with deviations/基本满意, 但稍有偏差c = Requirements are not satisfied/不满意n. a. = Not applicable/不适用b = Requirements are satisfied with deviations/基本满意,但稍有偏差c = Requirements are not satisfied/不满意n. a. = Not applicable/不适用Page页: 5Supplier/供应商: Date日期:EHS audit/环境健康安全审核表格编号form code:A-PQEO-15/1-5/03a = Requirements are fully satisfied/完全满意*) Please enclose copy附上复印件b = Requirements are satisfied with deviations/基本满意, 但稍有偏差c = Requirements are not satisfied/不满意n.a. = Not applicable/不适用Action plan Enclosure for audit conducted on:Signature Supplier (corrective actions started): ___________________表格编号form code:A-PQEO-15/1-5/03。
供应商审核表(英文版)Supplier Audit Form-List
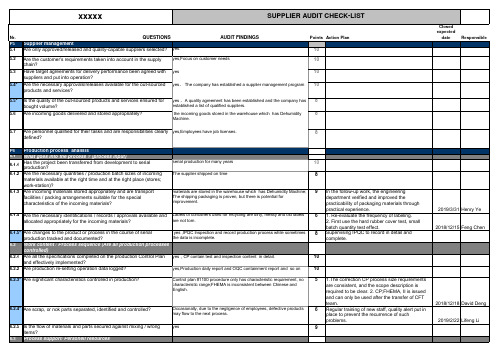
department verified and improved the
improvement.
practicability of packaging materials through
practical experience.
6.1.4 Are the necessary identifications / records / approvals available and Labels of containers used for recycling are dirty, messy and old labels
work-station)?
6.1.3 Are incoming materials stored appropriately and are transport facilities / packing arrangements suitable for the special characteristics of the incoming materials?
materials are stored in the warehouse which has Dehumidity Machine; 9 In the follow-up work, the engineering
The shipping packaging is proven, but there is potential for
P6 Production process analisis
6.1 What goes into the process ? (process input)
6.1.1
Has the project been transferred from development to serial production?
Supplier_Assessment_Report__供应商评估表
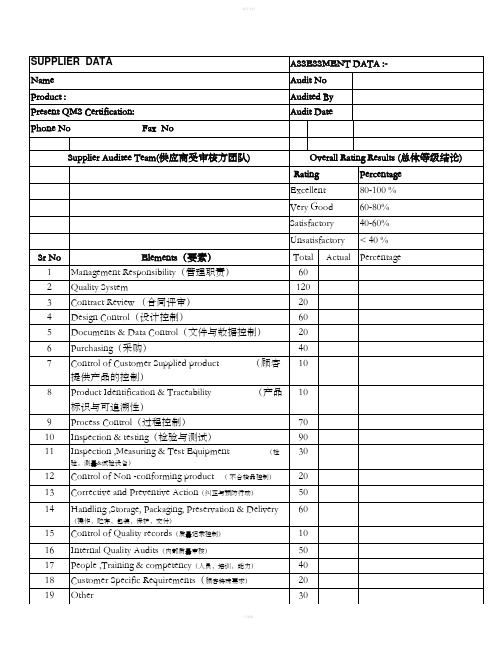
Total :-8101. KEY TO ASSESSMENT RATINGThe subcontractor quality assurance measures are rated with points from 0 to 10 on the basis of the following. Only those areas of the subcontractor that bear relevance to the product/service offered by the subcontractor to ‘TACO’ need b e assured.(分供方质量保证方法被从0~10分进行分级。
NTACO分供方的与产品/服务相关的方面必须得到保证)ELEMENTS NOT APPLICABLE TO A PARTICULAR SUBCONTRACTOR(不适合特殊分供方的条款)Certain elements such as 4.7 (Control of Customer Supplied Product) and 4.19 (Servicing) will not apply to every supplier. In such cases, ‘N/A’ is entered in place of the score.REPORTING OF ASSESSMENT FINDINGS(审核结果的报告)The supplier assessment report shall be filed along with this assessment form for reporting and recommendation on supplier selection and approval.(供应商评估报告应连同此评估表格作为报告、建议新供方的选择以及批准)MINIMUM CRITERIA FOR ACCEPTANCE(新供方接受的最小准则)The supplier (including Specially designated small supplier(包括指定的特别小供方)) should score minimum 40-60% & score minimum 5 points on the following elements individually for acceptance as approved supplier.(至少得分在40-60%以及至少分别在下面条款中得到5分,方可批准为供方)1. Product identification and traceability.(产品标识与可追溯性)2. Control plan.(控制计划)3. Contract review.(合同评审)4. Control of customer supplied products.(顾客财产保护)5. Process monitoring operation instructions.(过程监控作业指导书)6. Control of non confirming products.(不合格品控制)7. Inspection status.(检验状况)8. Calibration status.(校验状况)9. Corrective action on customer complaints.(客户抱怨纠正行动)10. Compliance with customer's standards/requirements.(遵守客户标准与要求)11. Control of quality records(质量记录控制)2. CHECKLISTS(检查清单)--▪------------------ASSESSMENT DONE BY: Signature:Name:Date:。
供应商BSR审核表

Supplier供应商
Factory Location地址
Audit Date: 审核日期
XXX Auditor XXX审核员
Item/项目 1.质量管理体系Quality Management System
Supplier Self Audit
FM-MSP-16-D01-004PLM-04A
Qualified Limit %
36
34
94%
36
0
0%
70%
2 企业社会责任Corporate-Social-Responsibility
72
669Βιβλιοθήκη %7200%
70%
3.设计与开发Design and Development
21
20
95%
21
0
4.供应商开发和管理Supplier development and management
21
19
90%
21
0
5.物料管控Material management
48
46
96%
48
0
6.生产控制Production control
48
46
96%
48
0
7.检测与计量(MSA)Measurement System Analysis
24
22
92%
24
0
8.销售与客户服务Sales and customer service
XXX Audit
Total Score for Related
Item
Score of supplier self audit
- 1、下载文档前请自行甄别文档内容的完整性,平台不提供额外的编辑、内容补充、找答案等附加服务。
- 2、"仅部分预览"的文档,不可在线预览部分如存在完整性等问题,可反馈申请退款(可完整预览的文档不适用该条件!)。
- 3、如文档侵犯您的权益,请联系客服反馈,我们会尽快为您处理(人工客服工作时间:9:00-18:30)。
电子邮件E-mБайду номын сангаасil
能力评估Production Capacity
公司主要产品Main Products
公司雇员数Number of Employees
设计、技术人员数No. of designers/engineers
质检控制人员数No. of QC
月生产量Production Capacity
Supplier Audit Report
请填写如下表格:Please complete the form as follows.
基本信息Information
供应商名称Supplier Name
公司成立日期Foundation date of your company
法人或业务负责人Legal Representative /Owner
供应商确认信息Confirmation and Signature
填表人Prepared By
填表日期Date
年销售额Turn-over
产品是否已获取第三方认证(如ISO、CE或者其他)?如有,请列出。Have you got any certificates from third party, such as ISO, CE and so on. If so, please list them in the right blank.
合作评估Cooperation issues
是否已有自创品牌?如有,请列出。Have you got any patent brands? If so, please list them on the right balnk.
是否提供OEM服务?(是否可以贴牌生产?)
OEM Service Offeredor not?