FMEA普通版
FMEA 作业指导书
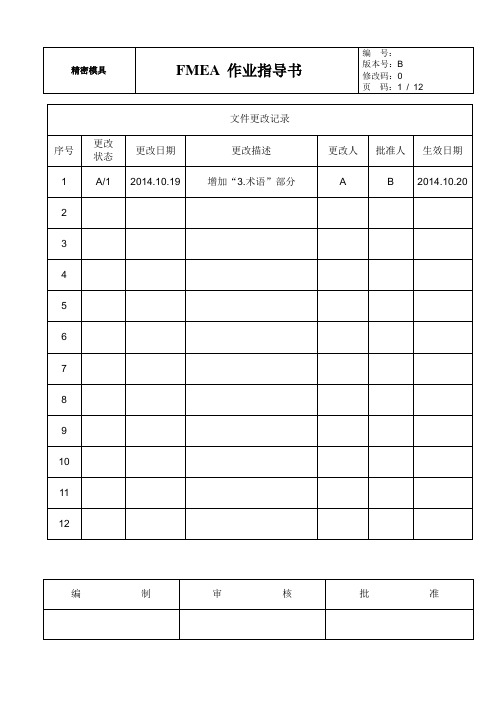
1. 目的:1.1 对新产品进行潜在失效分析,确定可能的失效模式(特别是高风险失效模式),找出可能的失效原因,研究其失效模式对系统产生的影响,为工装设计、制造、品质控制等方面提供依据,并采取相应预防纠正措施;1.2 推动过程改进作为主要目标,重点在防错方法。
2. 范围:2.1 适用于组织开发的所有新产品;2.2 适用于组织所有量产产品,特别是存在高返修费用、召回、不合格和客户抱怨的产品。
3. 术语:3.1 D/P FMEA或PFMEA:Process Potential Failure Mode and Effects Analysis 过程潜在的失效模式及后果分析;3.2 顾客:FMEA中“顾客”的定义通常是指“最终使用者”,然而顾客也可以是随后或下游的制造或装配工序,维修工或政府法规;3.3 防错(POKA-YOKE):是一种消除错误的技术,通常称之为“防止失效”,应作为控制重复性任务或行为的预防性技术,用来消除顾客的忧虑;3.4 变差:由人、设备、材料、方法与环境等原因造成的产品目标值与实际值之间的差异。
变差可分为普通原因变差与特殊原因变差。
普通原因变差是一直在过程中出现的变差,被认为系统是稳定的和可预测的。
特殊原因变差是指过程、产品或服务特性之中那些由“异常”或“外部”事件产生的,在普通原因变差之上或之外的变差,使得过程不可预测。
3.5 过程更改:在过程概念上的更改,是指能够改变过程能力以满足设计要求或产品的耐久性。
4. 职责:4.2 APQP小组负责PFMEA的评审;4.3 生产部技术员负责量产后PFMEA的评审;5. 流程图:(无)6. 内容:6.1 PFMEA的理解:·一种分析技术,用以最大限度地保证从单个部件到总成的所有的制造工序过程中各种潜在的失效模式及其相关起因/机理已得到充分的考虑和论述;·一份动态文件,需要不断的进行修订和评审;·在新产品开发策划阶段,促进对新的或更改的过程进行早期评审和分析,以便预测、解决或监控潜在的过程问题;·D/P FMEA假定所设计的产品能够满足设计要求,因设计的薄弱环节而产生的潜在失效模式可包括在D/P FMEA中,而其后果和避免包括在设计FMEA当中;·D/P FMEA不依靠改变产品设计来克服过程中的薄弱环节,但是他的确要考虑与计划的制造或装配过程有关的产品设计特性,以最大限度的保证产品能够满足顾客的要求和期望;·FMEA信息来源:相关工程技术人员之经验、曾发缺陷经验、顾客抱怨、厂内不良再发防止对策、内部报告、改善报告等。
FMEA手册
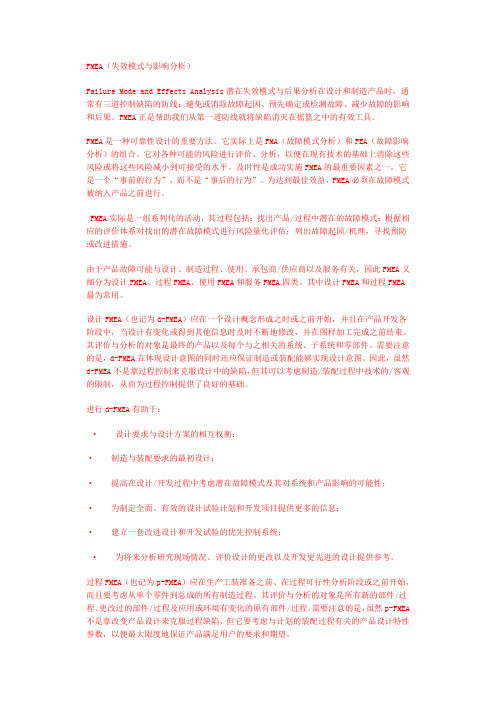
FMEA(失效模式与影响分析)Failure Mode and Effects Analysis潜在失效模式与后果分析在设计和制造产品时,通常有三道控制缺陷的防线:避免或消除故障起因、预先确定或检测故障、减少故障的影响和后果。
FMEA正是帮助我们从第一道防线就将缺陷消灭在摇篮之中的有效工具。
FMEA是一种可靠性设计的重要方法。
它实际上是FMA(故障模式分析)和FEA(故障影响分析)的组合。
它对各种可能的风险进行评价、分析,以便在现有技术的基础上消除这些风险或将这些风险减小到可接受的水平。
及时性是成功实施FMEA的最重要因素之一,它是一个“事前的行为”,而不是“事后的行为”。
为达到最佳效益,FMEA必须在故障模式被纳入产品之前进行。
FMEA实际是一组系列化的活动,其过程包括:找出产品/过程中潜在的故障模式;根据相应的评价体系对找出的潜在故障模式进行风险量化评估;列出故障起因/机理,寻找预防或改进措施。
由于产品故障可能与设计、制造过程、使用、承包商/供应商以及服务有关,因此FMEA又细分为设计FMEA、过程FMEA、使用FMEA和服务FMEA四类。
其中设计FMEA和过程FMEA 最为常用。
设计FMEA(也记为d-FMEA)应在一个设计概念形成之时或之前开始,并且在产品开发各阶段中,当设计有变化或得到其他信息时及时不断地修改,并在图样加工完成之前结束。
其评价与分析的对象是最终的产品以及每个与之相关的系统、子系统和零部件。
需要注意的是,d-FMEA在体现设计意图的同时还应保证制造或装配能够实现设计意图。
因此,虽然d-FMEA不是靠过程控制来克服设计中的缺陷,但其可以考虑制造/装配过程中技术的/客观的限制,从而为过程控制提供了良好的基础。
进行d-FMEA有助于:·设计要求与设计方案的相互权衡;·制造与装配要求的最初设计;·提高在设计/开发过程中考虑潜在故障模式及其对系统和产品影响的可能性;·为制定全面、有效的设计试验计划和开发项目提供更多的信息;·建立一套改进设计和开发试验的优先控制系统;·为将来分析研究现场情况、评价设计的更改以及开发更先进的设计提供参考。
FMEA简述

缺陷产品;不需要分拣;需要向供应商提供反馈
触感令人略微感觉不舒服。
1
非常低 没有可觉察到的影响
没有可觉察到的影响或没有影响
没有可觉察到的影响。
注:绿色为公司重点采用的相关评判标准,灰色为不常用标准。
十、第五版FMEA内容——失效原因
· 由小组结合特定的知识和经验来确定 · 失效原因能够直接确定或者通过理解失效的原理来确定
八、第四版FMEA
过程步骤/功能
要求
潜在失效模式
潜在失效影 响
SEV 严重度
分类
潜在失效原因
OCC发生 度
现行过程控制 预防
Plasma清洗
芯片背面 无污染
D/B 焊胶层 芯片背面污染 脱落,电参
失效
8
Plasma能量&时间参 数不恰当 Plasma工艺气压值偏 小或偏大
气体流量偏小
1.限制参数编辑权限,仅工程部负责人有
· 描述失效模式对客户的影响:
- 内部客户(下一个操作/后续操作/操作目标) - 外部客户(下一级/OEM/经销商)政府法律法规
- 产品或产品最终用户/操作者 - 立法机构
要求 四个螺钉
失效模式
影响
最终顾客:座垫松动,有噪音。
少于四个螺钉 制造和装配:由于受影响的部分,因而停止发
运,并进行额外挑选和返工。
1.要求作业员每班检查气罐接口是否漏气 2.气体流量超出范围时,设备自动报警
DET RP 探测度 N
4 64
4 64 2 32
推荐措施 NONE NONE NONE
Action Results/实施结果
职责和目标完 成日期
采取的措施 和有效日期
SE V 严重 度
FMEA培训教材
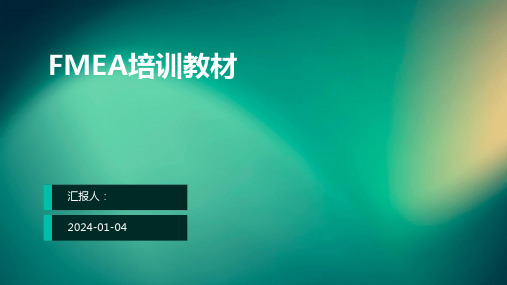
总结词
汽车刹车系统FMEA分析是一个典型的故障模式与影响 分析案例,通过对刹车系统的各个组成部分进行故障 模式分析,评估其对整个系统性能的影响。
详细描述
汽车刹车系统FMEA分析首先识别刹车系统中的各个组 成部分,然后对每个组成部分进行故障模式分析,包括 可能的故障类型、故障发生概率和故障影响程度。接着 ,根据分析结果,评估每个故障模式对刹车系统整体性 能的影响,并确定优先改进顺序。最后,制定相应的改 进措施和预防措施,降低故障发生概率和影响程度。
高级功能
介绍FMEA软件的高级功能,如 影响分析、优先级排序、报告 生成等。
常见问题与解决方案
列举使用FMEA软件过程中可能 遇到的问题,并提供相应的解 决方案。
FMEA软件应用实例
01
汽车刹车系统FMEA分析
通过实际案例,演示如何使用FMEA软件对汽车刹车系统进行故障模式
、影响和优先级分析,并提出相应的改进措施。
FMEA软件应用领域
FMEA软件广泛应用于汽车、航空、电子、医疗等制造业 领域,用于提高产品质量、降低产品风险和优化产品设计 。
FMEA软件操作教程
软件安装与启动
介绍如何下载和安装FMEA软件 ,以及如何启动软件并进入操 作界面。
基础操作
介绍FMEA软件的基本操作,如 创建项目、添加部件、设置故 障模式等。
感谢您的观看
FMEA的应用范围
总结词
FMEA可以应用于各种行业和领域,如汽车 、航空、医疗、电子等,用于评估产品设计 或流程的可靠性和安全性。
详细描述
FMEA是一种通用的质量工具,可以应用于 各种行业和领域。在汽车行业中,FMEA可 以用于评估汽车零部件的可靠性,提高车辆 的安全性能;在航空领域,FMEA可以用于 评估飞机设计和制造过程中的潜在故障模式 ,确保飞行的安全;在医疗领域,FMEA可 以用于评估医疗设备的可靠性和安全性,提 高患者的治疗效果;在电子行业,FMEA可 以用于评估产品的设计和制造流程,提高产 品的质量和可靠性。
FMEA培训教材2024版本课件

FMEA培训教材2024版本课件FMEA培训教材2024版本课件一、FMEA简介故障模式与影响分析(Failure Modes and Effects Analysis,简称FMEA)是一种预防性的质量工具,用于识别、评估和降低潜在的设计缺陷或过程风险。
FMEA的核心目标是找出可能的故障模式,并评估它们对系统和过程的影响,从而在实际发生故障之前采取措施进行改进。
二、FMEA的应用范围FMEA广泛应用于各个行业,包括汽车、航空、电子、医疗和化工等领域。
它主要用于产品设计和制造过程,也可用于服务行业的风险评估。
三、FMEA的基本步骤1、确定分析范围:明确需要分析的对象和系统,确定分析的边界和条件。
2、确定故障模式:列出所有可能的故障模式,包括硬件故障、软件错误、人为因素和环境因素等。
3、评估故障影响:分析每个故障模式对系统性能和安全的影响,包括功能丧失、性能下降、对人员和环境的影响等。
4、评估风险优先级:根据故障模式的频率、影响程度和可检测性等指标,计算风险优先级(RPN)。
5、制定改进措施:根据RPN值,制定并实施针对高风险故障模式的改进措施。
6、监控和审查:跟踪实施效果,定期进行FMEA分析,以确保持续改进。
四、FMEA的表格FMEA分析过程中需要使用多种表格,以下是常用的几种表格:1、FMEA计划表:用于列出分析的范围、对象、分析人员和进度等信息。
2、FMEA故障模式表:用于列出所有可能的故障模式,包括故障类型、位置、影响和频率等信息。
3、FMEA故障影响表:用于分析每个故障模式对系统性能和安全的影响。
4、FMEA风险优先级表:用于根据故障模式的频率、影响程度和可检测性等指标,计算风险优先级(RPN)。
5、FMEA改进措施表:用于列出针对高风险故障模式的改进措施,包括措施内容、责任人、进度和效果跟踪等信息。
五、FMEA的注意事项1、全面分析可能的故障模式,包括硬件、软件、人为因素和环境因素等。
FMEA手册中文正式
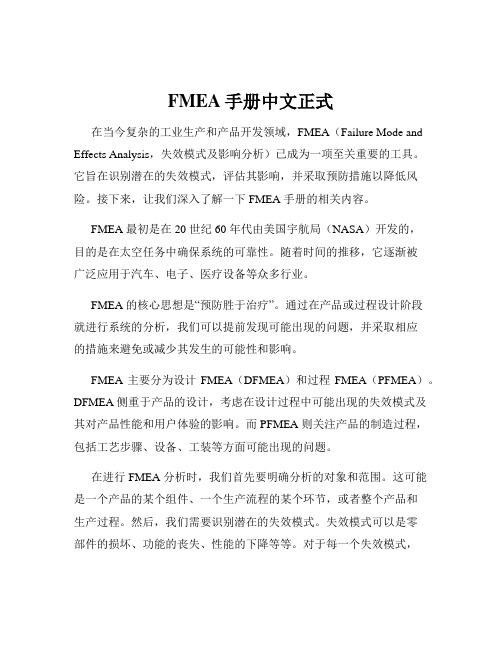
FMEA手册中文正式在当今复杂的工业生产和产品开发领域,FMEA(Failure Mode and Effects Analysis,失效模式及影响分析)已成为一项至关重要的工具。
它旨在识别潜在的失效模式,评估其影响,并采取预防措施以降低风险。
接下来,让我们深入了解一下 FMEA 手册的相关内容。
FMEA 最初是在 20 世纪 60 年代由美国宇航局(NASA)开发的,目的是在太空任务中确保系统的可靠性。
随着时间的推移,它逐渐被广泛应用于汽车、电子、医疗设备等众多行业。
FMEA 的核心思想是“预防胜于治疗”。
通过在产品或过程设计阶段就进行系统的分析,我们可以提前发现可能出现的问题,并采取相应的措施来避免或减少其发生的可能性和影响。
FMEA 主要分为设计FMEA(DFMEA)和过程FMEA(PFMEA)。
DFMEA 侧重于产品的设计,考虑在设计过程中可能出现的失效模式及其对产品性能和用户体验的影响。
而 PFMEA 则关注产品的制造过程,包括工艺步骤、设备、工装等方面可能出现的问题。
在进行 FMEA 分析时,我们首先要明确分析的对象和范围。
这可能是一个产品的某个组件、一个生产流程的某个环节,或者整个产品和生产过程。
然后,我们需要识别潜在的失效模式。
失效模式可以是零部件的损坏、功能的丧失、性能的下降等等。
对于每一个失效模式,我们要评估其可能产生的影响。
影响可能包括对产品质量、安全性、可靠性、客户满意度等方面的影响。
接下来,我们要确定失效的原因。
这些原因可能是设计缺陷、材料问题、加工误差、操作不当等等。
然后,我们根据失效模式的严重程度(S)、发生频率(O)和探测难度(D)来计算风险优先数(RPN)。
RPN 是一个用于衡量风险大小的指标,其计算公式为 RPN= S × O × D。
根据 RPN 的值,我们可以确定需要采取的措施。
对于高 RPN 值的失效模式,我们需要优先采取措施来降低风险。
FMEA普通版公开课获奖课件

辨认产品或过程失效模式 估计涉及特殊原因旳风险 减小风险旳措施优先排序 评价产品旳设计验证计划 拟制目前旳过程控制计划
2024/10/2
37
10 FMEA 旳类别
System-FMEA Design-FMEA Process-FMEA
2024/10/2
38
FMEA旳作用
2024/10/2
39
FMEA 旳作用
则2024完/10/毕2 这个事件总旳措施有 N = P1 X P2 X P3 X P4,…. 7
B
A
2024/10/2
1+1+1=3 8
A
2024/10/2
B
2
3x2=6
3
C
9
3
B
D
2
3x2x3=18
A
2024/10/2
3
C
10
回忆二个定理
加法定理: 假如要完毕一种事件,有若干种措施n1,n2,n3,n4,…. 则完毕这个事件总旳措施有 N = n1+n2+n3+n4+ ….
旳过程控制特征
Manufacture
characteristic MC
料 Material
CC Control
机 Machine
KCC (Key)
SCC (Standard)
人 Man
KCC
KCC KCC
2024/10/2
KCC
KCC KCC
环 Environment 测 Measure 法 Method
——美国汽车工业行动集团(AIAG)
VDA6.1质量体系审核
2024/10/2
——德国汽车工业联合会(VDA)
2024年FMEA培训教材(多应用版)
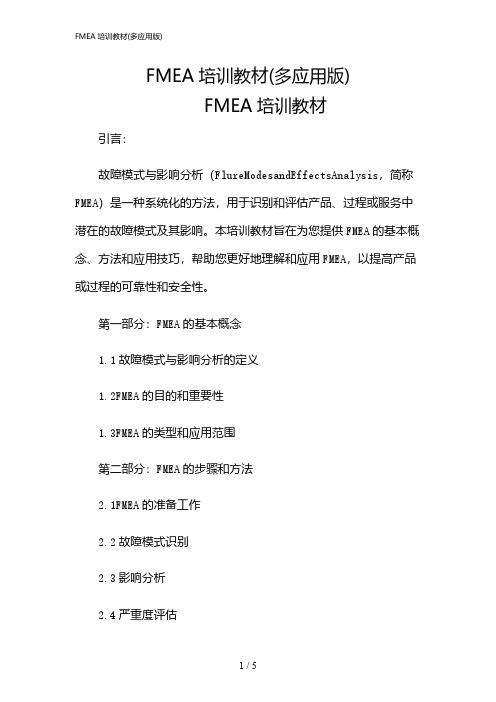
FMEA培训教材(多应用版)FMEA培训教材引言:故障模式与影响分析(FlureModesandEffectsAnalysis,简称FMEA)是一种系统化的方法,用于识别和评估产品、过程或服务中潜在的故障模式及其影响。
本培训教材旨在为您提供FMEA的基本概念、方法和应用技巧,帮助您更好地理解和应用FMEA,以提高产品或过程的可靠性和安全性。
第一部分:FMEA的基本概念1.1故障模式与影响分析的定义1.2FMEA的目的和重要性1.3FMEA的类型和应用范围第二部分:FMEA的步骤和方法2.1FMEA的准备工作2.2故障模式识别2.3影响分析2.4严重度评估2.5发生概率评估2.6检测难度评估2.7风险优先级评估2.8制定改进措施和行动计划第三部分:FMEA的实践应用3.1FMEA团队的组建和培训3.2FMEA实施过程中的常见问题及解决方法3.3FMEA报告的编制和评审3.4FMEA与其他质量管理工具的结合应用第四部分:FMEA的持续改进4.1FMEA的跟踪和监控4.2FMEA的回顾和更新4.3FMEA的最佳实践分享和推广结论:通过本培训教材的学习,您应该能够了解FMEA的基本概念、方法和应用技巧。
FMEA是一种重要的质量管理工具,可以帮助组织识别和评估潜在的故障模式及其影响,从而采取相应的改进措施,提高产品或过程的可靠性和安全性。
希望本教材能够为您在FMEA的实际应用中提供指导和支持。
注意事项:1.本教材的内容仅供参考,具体应用时需结合实际情况进行适当调整。
2.FMEA的实施需要团队合作和专业知识的支持,建议在实施前进行相关培训和能力提升。
3.FMEA是一种持续改进的过程,需要定期回顾和更新,以适应组织的发展和变化。
关键词:FMEA、故障模式、影响分析、风险管理、质量改进、可靠性、安全性重点关注的细节:FMEA的步骤和方法详细补充和说明:1.故障模式识别:故障模式是指产品、过程或服务中可能出现的问题或失效方式。
FMEA培训教材PPT完整版(2024)

产品设计阶段FMEA案例分析
案例一
某型号汽车发动机设计FMEA分 析。针对发动机系统可能出现的 故障模式进行分析,如气缸磨损 、活塞环断裂等,制定相应的改
进措施。
案例二
某型号手机电池设计FMEA分析 。针对电池可能出现的过热、短 路等故障模式进行分析,优化电 池结构和电路设计,提高电池安
全性。
26
过程控制阶段FMEA流程
定义过程范围和功能
01
识别潜在的故障模式
02
评估故障影响的严重度、发生
度和检测度
03
计算风险优先数(RPN)并排 序
04
制定并实施控制措施
2024/1/29
05
跟踪验证控制措施的有效性并
更新FMEA
06
27
过程控制阶段FMEA案例分析
案例一
某汽车制造厂涂装车间过程FMEA分 析
为生产过程FMEA提供支持
产品设计阶段FMEA的输出可以为生产过程 FMEA提供重要的输入和支持。
20
产品设计阶段FMEA流程
组建FMEA团队
由多部门、多学科的专业 人员组成,包括设计、制 造、质量、采购等。
2024/1/29
定义系统和子系统
明确产品的结构和功能, 划分系统和子系统。
识别故障模式
针对每个子系统或部件, 识别所有可能的故障模式 。
9
组建FMEA团队并分配任务
02
01
03
2024/1/29
组建多学科团队
包括设计、制造、质量、采购等相关领域专家。
分配角色与责任
明确团队成员的角色和责任,确保任务有效执行。
提供培训与支持
为团队成员提供FMEA培训,确保掌握相关知识和技 能。
(完整版)FMEA简介

FMEA简介[ 2004年3月5日,阅读人数1024人 ]失效模式和效果分析(Failure Mode and Effect Analysis, FMEA)是一种用来确定潜在失效模式及其原因的分析方法。
具体来说,通过实行FMEA,可在产品设计或生产工艺真正实现之前发现产品的弱点,可在原形样机阶段或在大批量生产之前确定产品缺陷。
FMEA最早是由美国国家宇航局(NASA)形成的一套分析模式,FMEA是一种实用的解决问题的方法,可适用于许多工程领域,目前世界许多汽车生产商和电子制造服务商(EMS)都已经采用这种模式进行设计和生产过程的管理和监控。
FMEA简介FMEA有三种类型,分别是系统FMEA、设计FMEA和工艺FMEA,本文中主要讨论工艺FMEA。
实施FMEA管理的具体步骤见图1。
确定产品需要涉及的技术、能够出现的问题,包括下述各个方面:需要设计的新系统、产品和工艺;对现有设计和工艺的改进;在新的应用中或新的环境下,对以前的设计和工艺的保留使用;形成FMEA团队。
理想的FMEA团队应包括设计、生产、组装、质量控制、可靠性、服务、采购、测试以及供货方等所有有关方面的代表。
记录FMEA的序号、日期和更改内容,保持FMEA始终是一个根据实际情况变化的实时现场记录,需要强调的是,FMEA文件必须包括创建和更新的日期。
创建工艺流程图。
工艺流程图应按照事件的顺序和技术流程的要求而制定,实施FMEA需要工艺流程图,一般情况下工艺流程图不要轻易变动。
列出所有可能的失效模式、效果和原因、以及对于每一项操作的工艺控制手段:1.对于工艺流程中的每一项工艺,应确定可能发生的失效模式,如就表面贴装工艺(SMT)而言,涉及的问题可能包括,基于工程经验的焊球控制、焊膏控制、使用的阻焊剂(soldermask)类型、元器件的焊盘图形设计等。
2.对于每一种失效模式,应列出一种或多种可能的失效影响,例如,焊球可能要影响到产品长期的可靠性,因此在可能的影响方面应该注明。
fmea分析 (4)

FMEA分析什么是FMEAFMEA,即失效模式与影响分析(Failure Mode and Effects Analysis),是一种常用的质量管理工具。
它主要用于预测产品或系统失效的潜在模式,并识别可能的影响,以便在设计或生产过程中采取合适的预防和纠正措施。
通过进行FMEA分析,可以帮助组织减少风险,改善质量,并提高产品和流程的可靠性。
FMEA分析的步骤FMEA分析通常包括以下步骤:1.明确分析的范围:确定要进行FMEA分析的产品或系统的范围。
2.识别失效模式:通过对产品或系统进行全面的分析和评估,识别可能存在的失效模式。
3.评估失效的影响:对每个失效模式进行评估,确定其对产品或系统性能、功能或安全性的可能影响。
4.确定失效的原因:分析每个失效模式的潜在原因,并确定可能的失效机制。
5.评估失效的频率:评估每个失效模式的发生频率,以确定其在实际使用中的相对概率。
6.制定预防措施:为每个失效模式确定适当的预防措施,以降低发生概率或消除失效产生的根本原因。
7.制定纠正措施:为每个失效模式确定适当的纠正措施,以减轻失效可能带来的影响。
8.实施和跟踪措施:制定实施计划,并跟踪预防和纠正措施的执行情况和效果。
FMEA分析的优势FMEA分析具有以下优势:•风险识别:通过具体的分析过程,可以识别潜在的失效模式和其可能带来的影响,有助于组织及时采取措施降低风险。
•质量改进:FMEA分析可以帮助组织发现产品或系统的潜在问题和缺陷,并制定相应的预防和纠正措施,从而改善产品质量。
•效率提升:通过在早期阶段识别和解决问题,FMEA分析可以减少错误和不必要的修复工作,提高生产效率。
•客户满意度提升:通过预测和预防潜在的失效模式,FMEA分析可以提高产品的可靠性和可用性,从而提升客户的满意度。
FMEA分析的应用领域FMEA分析广泛应用于各行业的产品和系统设计、制造和服务过程中。
以下是一些常见的应用领域:•汽车制造业:对汽车零部件和系统进行FMEA分析,以确保安全性和可靠性。
fmea大纲

FMEA大纲通常包括以下几个部分:
1. FMEA简介:介绍FMEA的概念、目的、意义和应用范围。
2. FMEA基本概念:包括失效模式、失效效应、风险优先数等基本概念,帮助理解FMEA的分析方法。
3. FMEA功能:介绍FMEA在产品设计阶段和过程设计阶段的功能,如识别潜在失效模式、分析失效影响、评估风险优先数等。
4. FMEA使用时机:说明在何时使用FMEA,例如在产品设计阶段、过程设计阶段、产品制造阶段等。
5. FMEA运用成功的关键:介绍运用FMEA成功的关键因素,如团队协同合作、有效沟通、数据分析等。
6. FMEA应用流程:详细介绍FMEA的应用流程,包括准备阶段、分析阶段、结果解释阶段等。
7. 失效分析技巧:介绍失效分析的技巧和方法,如因果图分析、故障树分析等。
8. 探究根因方法:介绍探究产品或过程失效根本原因的方法,如实验设计、数据分析等。
9. FMEA案例分析:通过实际案例分析,展示FMEA在产品设计和过程设计中的应用和效果。
10. 总结与展望:总结FMEA的重要性和应用前景,提出未来研究方向和应用建议。
以上是FMEA大纲的一般内容,具体内容和结构可能会因不同的培训课程或教材而有所差异。
FMEA模板及介绍

Prepared by Justin Tao 32
2. 特性分类
按状态分: 产品特性和过程特性
按重要程度分: 1)关键特性: 与安全、法规有关的关键特性(特殊特性) 与功能、装配有关的关键特性(重要特性) 2)普通特性:除关键特性之外的所有特性
4. DFMEA潜在失效后果
潜在失效后果(设计) :
就是失效模式对功能的影响,就如顾客感受的一样。 要根据顾客可能发现或经历的情况来描述失效的后
果。 要清楚地说明该失效模式是否会影响到安全性,或
与法规不符。 不同级别的系统、子系统或零件之间存在着系统层
次上的关系。
Prepared by Justin Tao 19
工程的影响
采取可行的对策
Prepared by Justin Tao 11
5. FMEA分类
依据阶段不同可分为: DFMEA PFMEA
依据作用不同可分为: 系统FMEA 子系统FMEA 零件FMEA
Prepared by Justin Tao 12
二、FMEA关键术语理解
13
1. FMEA失效
SFMEA
来自SFMEA
生的原因
PFMEA 问题产生的原因来自 和DFMEA相同 详细的过程失效
DFMEA
的后果
模式产生的原因
Prepared by Justin Tao 39
3. FMEA的时间顺序
DFMEA PFMEA
概念 初始设计 设计完成 样件制造 设计/过程 生产开始 确认
DFMEA 开始早于过程,完成时间在早期的图样完成但任何工 具的制造开始之前 PFMEA 开始于基本的操作方法讨论完成时,完成时间早于生产 计划制定和生产批准之前
FMEA标准手册(完整资料).doc

FMEA
Potential Failure Mode and Effect Analysis
潜在失效模式与后果分析
概 要
概 述
本手册介绍了潜在失效模式及后果分析(FMEA)的概念,给出了运用FMEA技术的通用指南。FMEA可以描述为一组系统化的活动,其目的是:
1)发现、评价产品/过程中潜在的失效及其后果;
时间性是成功实施FMEA的最重要因素之一,它是一个“事前行为”,而不是“事后练习”。为达到最佳效益,FMEA必须在设计或过程失效模式被无意地纳人设计产品之前进行。事先花时间很好地进行综合的FMEA分析,能够容易、低成本地对产品或过程进行修改,从而减轻事后修改的危机。FMEA能够减少或消除因修改而带采更大损失的机会。适当地加以应用,FMEA是一个相互作用的过程,永无止境。
设计FMEA
简 介
设计FMEA主要是由“负责设计的工程师/小组”采用的一种分析技术,用来保证在可能的范围内已充分地考虑到并指明各种潜在的失效模式及其相关的起因/机理。应评估最终的产品以及每个与之相关的系统、子系统和零部件。FMEA以其最严密的形式总结了设计一个零部件、子系统或系统时,一个工程师和设计组的设计思想(包括根据以往的经验和教训对可能出现问题的项目的分析)。这种系统化的方法体现了一个工程师在任何设计过程中正常经历过程,并使之规范化、文件化。
·为推荐和跟踪降低风险的措施提供一个公开的讨论形式;
·为将来分析研究现场情况、评价设计的更改及开发更先进的设计提供参考。
顾客的定义
设计FMEA中“顾客”的定义,不仅仅是指“最终使用者”,还包括负责车型更高一级装配过程设计的工程师/小组,以及在生产过程中负责制造和售后服务的工程师。
FMEA的全面实施要求对所有新的部件、更改的部件以及应用或环境有变化的沿用零件进行设计FMEA。FMEA始于负责设计工作的工程师,但对有专有权的设计来说,可能始于其供方。
FMEA培训教材(PPT14)
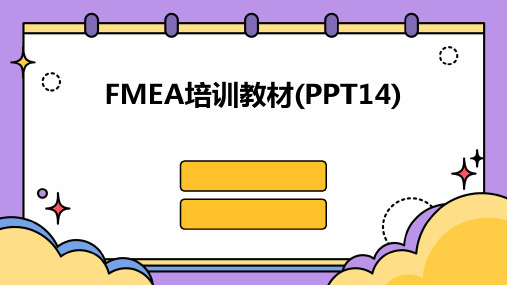
某电子厂在生产手机主板时,通过FMEA分析发现某道工序 存在潜在的静电影响,及时改进了生产工艺和防静电措施, 提高了产品质量和生产效率。
生产过程FMEA优化建议
完善数据收集机制
建立生产过程的数据收集和分析机制,为 FMEA分析提供全面、准确的数据支持。
A 加强团队培训
提高FMEA团队成员的专业技能和分 析能力,确保FMEA分析的准确性和
用的质量工具。
标准化
为了规范FMEA的实施过程,国 际标准化组织(ISO)和美国汽 车工程师学会(SAE)等机构制 定了相关的FMEA标准和指南。
FMEA核心思想
预防性
结构化
FMEA强调在产品设计或过程设计阶段进行 预防性的分析,识别并消除潜在的失效模 式。
FMEA采用结构化的分析方法,通过系统的 、有条理的分析过程,确保所有潜在的失 效模式都被充分考虑。
设定分析目标
明确FMEA分析的目的和预期结 果,例如降低故障率、提高可靠 性等。
组建FMEA团队
确定团队成员
包括具有专业背景和实际经验的跨职 能团队成员,如设计、制造、质量、 维修等。
明确团队职责
分配各成员在FMEA分析中的具体职 责和任务。
收集相关资料
01
02
03
收集历史数据
收集与分析对象相关的历 史故障数据、维修记录等 。
案例二
某医院医疗设备保养FMEA分析。医院对重 要医疗设备进行定期保养,但保养过程中经 常出现漏检、误检等问题。通过FMEA分析 ,发现保养流程不规范、人员技能不足是导 致问题的主要原因。医院采取了优化保养流 程、加强人员培训等措施,提高了医疗设备
保养的质量和效率。
THANKS
感谢观看
FMEA介绍(绝对经典版)
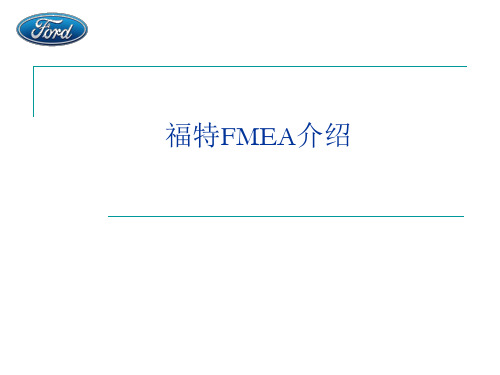
PFMEA:
流程图分析; 特性矩阵;
PFMEA的S/O/D 判定原则。
Change Point Approach 变化点的处理
FMEAs are living documents, and are updated when ... FMEA是动态文件,在以下情况下进行更新…
New design or process is planned 有新的设计或过程的变化 Modification to a component, process or system is planned, including those due to Global 8D 有部件,过程或系统的更改,包括由于G8D带来的更改 Component is to be used in new environment, location, or application 部件将要用于新的环境,位置或用途。
*Headdlamp Housing to Attachment
Attachment
Hood *Hood adjuster depth to Housing
GOP Align.
Tabs *Align tabs to Screws
Adjustment Screws (2) *Snap fit to Hdlm *Snap fit to Hdlm
*Elect Sys. to connector. Electrical System.
Environmental -Road salt *Elect Sys. location to Housing
Environmental -Road Material
* Denotes Relationship between hardware that goes on Interface Matrix
FMEA(失效模式与影响分析)

失效模式与影响分析即“潜在失效模式及后果分析”。
FMEA是在产品设计阶段和过程设计阶段,对构成产品的子系统、零件,对构成过程的各个工序逐一进行分析,找出所有潜在的失效模式,并分析其可能的后果,从而预先采取必要的措施,以提高产品的质量和可靠性的一种系统化的活动。
FMEA又根据产品故障可能产生的环节:设计、制造过程、使用、承包商(供应商)以及服务可细分为:1. DFMEA:设计FMEA2. PFMEA:过程FMEA3. EFMEA:设备FMEA4. SFMEA:体系FMEA一、概念潜在的失效模式及后果分析(Failure Mode and Effects Analysis,简记为FMEA),是“事前的预防措施”,并“由下至上。
关键词:潜在的—失效还没有发生,它可能会发生,但不一定会发生。
“核心”集中于:预防—处理预计的失效,其原因及后果/影响。
主要工作:风险评估—潜在失效模式的后果影响。
FMEA 开始于产品设计和制造过程开发活动之前,并指导贯穿实施于整个产品周期。
进行分析系统中每一产品所有可能产生的故障模式及其对系统造成的所有可能影响,并按每一个故障模式的严重程度,检测难易程度以及发生频度予以分类的一种归纳分析方法。
二、目的·能够容易、低成本地对产品或过程进行修改,从而减轻事后危机的修改。
·找到能够避免或减少这些潜在失效发生的措施;三、RPN的评价准则1.1 设计FMEA严重性(Severity :S)1)评分原则a)衡量是小的影响程度b)失效影响:产品或制程的某一失效对产品外观,结构,功能,性能稳定性,可靠性影响c)或对下一制程,使用者或设备的影响d)或对最终客户、政府法规、安全、环保的违及e)划分标准——主观判定2)设计:FMEA风险评估标准说明严重性(Severity :S):严重性是对下一个制程、系统或客户所发生的潜在失效模式效果的严重性进行评估,严重性仅适用于效果,严重性等级指数的减低只能透过设计变更才能够生效,严重性应该在1~10的等级上评估。
质量管理的五大工具(标准版)
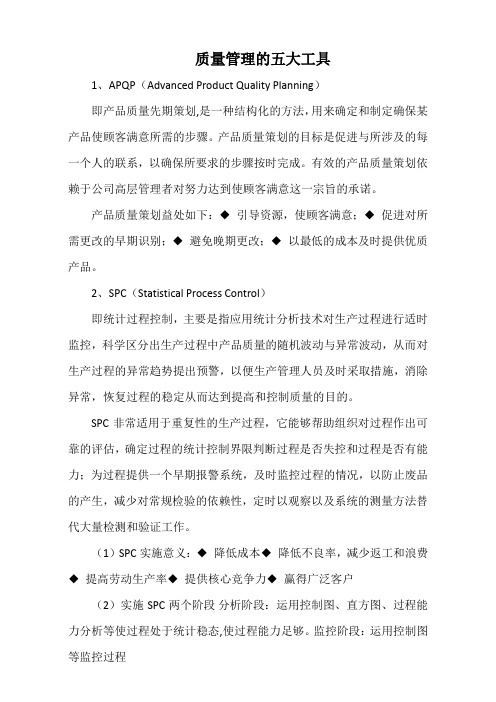
质量管理的五大工具1、APQP(Advanced Product Quality Planning)即产品质量先期策划,是一种结构化的方法,用来确定和制定确保某产品使顾客满意所需的步骤。
产品质量策划的目标是促进与所涉及的每一个人的联系,以确保所要求的步骤按时完成。
有效的产品质量策划依赖于公司高层管理者对努力达到使顾客满意这一宗旨的承诺。
产品质量策划益处如下:◆引导资源,使顾客满意;◆促进对所需更改的早期识别;◆避免晚期更改;◆以最低的成本及时提供优质产品。
2、SPC(Statistical Process Control)即统计过程控制,主要是指应用统计分析技术对生产过程进行适时监控,科学区分出生产过程中产品质量的随机波动与异常波动,从而对生产过程的异常趋势提出预警,以便生产管理人员及时采取措施,消除异常,恢复过程的稳定从而达到提高和控制质量的目的。
SPC非常适用于重复性的生产过程,它能够帮助组织对过程作出可靠的评估,确定过程的统计控制界限判断过程是否失控和过程是否有能力;为过程提供一个早期报警系统,及时监控过程的情况,以防止废品的产生,减少对常规检验的依赖性,定时以观察以及系统的测量方法替代大量检测和验证工作。
(1)SPC实施意义:◆降低成本◆降低不良率,减少返工和浪费◆提高劳动生产率◆提供核心竞争力◆赢得广泛客户(2)实施SPC两个阶段分析阶段:运用控制图、直方图、过程能力分析等使过程处于统计稳态,使过程能力足够。
监控阶段:运用控制图等监控过程(3)SPC的产生:工业革命以后,随着生产力的进一步发展,大规模生产的形成,如何控制大批量产品质量成为一个突出问题,单纯依靠事后检验的质量控制方法已不能适应当时经济发展的要求,必须改进质量管理方式。
于是,英、美等国开始着手研究用统计方法代替事后检验的质量控制方法。
1924年,美国的休哈特博士提出将3Sigma原理运用于生产过程当中,并发表了著名的“控制图法”,对过程变量进行控制,为统计质量管理奠定了理论和方法基础。
FMEA普通版-文档资料

每个过程又有若干种方法 P1 : n11,n12,n13,n14,…. P2 : n21,n22,n23,n24,…. P3 : n31,n32,n33,n34,…. P4 : n41,n42,n43,n44,….
1则5.0完3.20成21 这个事件总的方法有 N = P1 X P2 X P3 X P4,…. 8
15.03.2021
26
三种类型
Process-FMEA
P-FMEA
对工艺流程设计输出在验证前的综合评估
识别和消除制造 /服务过程中的潜在隐患
深及制造 /服务过程每一环节的潜在隐患
15.03.2021
27
三种基本情况
新设计,新技术,新过程的开发 对对现现有有设设计计或或过过程程的的重修要改修改
现有的设计或过程有新的应用
改进控制输入变量明显改善输出变量
15.03.2021
17
FMEA的成功应用
50年代初期,美国Grumman公司第一次把FMEA思想用 于一种战斗机的操纵系统的设计分析,取得较好效 果,以后逐渐推广。
60年代中期用于美国航天工业.(阿波罗)
1974年用于美国海军。(1629号军标)
1985年IEC公布了FMEA标准: IEC812, 这个标准被我国等同采用为 GB 7826-87:
功能 失效模式 失效后果 S
别 起因机理 O 控制预防 控制探测 D
R N
的措施 完成日期 采取的措施 S O D PRN
15.03.2021
29
FMEA的一些基本概念
15.03.2021
30
FMEA的一些基本概念
1.失效 3.失效后果 5.顾客 7.KPC 9.FMEA的定义
- 1、下载文档前请自行甄别文档内容的完整性,平台不提供额外的编辑、内容补充、找答案等附加服务。
- 2、"仅部分预览"的文档,不可在线预览部分如存在完整性等问题,可反馈申请退款(可完整预览的文档不适用该条件!)。
- 3、如文档侵犯您的权益,请联系客服反馈,我们会尽快为您处理(人工客服工作时间:9:00-18:30)。
Potential Failure Mode and Effects Analysis
上海质量教育培训中心
2016/12/2 1
潜在失效模式及后果分析 FMEA
Potential Failure Mode and Effects Analysis
2001.07 第三版 2001.07 Third edition
自觉与不自觉 科学法则与自然法则 注意性与随意性 借鉴型与抛弃型
螺旋提高与闭环解决
2016/12/2 6
介绍二个定理
2016/12/2
7
介绍二个定理
加法定理:
如果要完成一个事件,有若干种方法n1,n2,n3,n4,…. 则完成这个事件总的方法有 N =
n 1 + n 2 + n 3 + n4 +
项目 潜在 潜在 严重度 级 潜在失效 频度 现行设计 现行设计 探测度 功能 失效模式 失效后果 S 别 起因机理 O 控制预防 控制探测 D
P R N
采取措施后的结果 建议采取 责任目标 的措施 完成日期 采取的措施 S O D PRN
2016/12/2
29
FMEA的一些基本概念
2016/12/2
KPC
特殊 关注
S/C
பைடு நூலகம்
Safe / Complain
product Characteristic
PC
特殊 关注
F/F Function /F it
一般特性
一般特性
一般 关注
Standard
2016/12/2
Standard
37
7
KPC 重要的产品特性
功能,配合的质量特性
Safe / Complain
2016/12/2 22
执行FMEA程序的基本活动
1. 你所关注的对象 : 特性功能; 工艺过程 6. 对象失效的起因或机理 7.失效的起因或机理出现的频度 O
8.现行的预防控制措施 9.现行预防控制措施的可探测度 D 10.确定风险顺序数( RPN )
2016/12/2
(Occurrence)
(Detection)
使用资源
确定影响输出变量的关键的输入变量 改进控制输入变量明显改善输出变量
2016/12/2 17
FMEA的成功应用
50年代初期,美国Grumman公司第一次把FMEA思想用 于一种战斗机的操纵系统的设计分析,取得较好效 果,以后逐渐推广。
60年代中期用于美国航天工业.(阿波罗)
1974年用于美国海军。(1629号军标) 1985年IEC公布了FMEA标准: IEC812, 这个标准被我国等同采用为 GB 7826-87:
—— 失效给顾客(广义)带来的影响
引起运行系统失调
零, 部件无法装配 加工流程间歇停顿 造成顾客停线停产
典型的失效后果: 噪声
2016/12/2
工作不正常 间歇性工作
不良外观 无法坚固
无法攻丝 无法钻孔
34
粗糙
4 失效的原因(Failure Cause)
——引起失效的原因: 不可预计的 自然的/人为的 物理的/化学的
….
乘法定理:
如果要完成一个事件,有若干个过程P1,P2,P3,P4,…. 每个过程又有若干种方法 P1 : P2 : P3 :
P4 : 2016/12/2 则完成这个事件总的方法有 N = P1 X P2 X P3 X P4,….12
n11,n12,n13,n14,…. n21,n22,n23,n24,…. n31,n32,n33,n34,…. n41,n42,n43,n44,….
2016/12/2
潜在?
32
2 失效模式(Failure Mode)
—— 失效的表现形式 •系统,子,分系统,未达到设计策划的意图 •产品,零件的技术参数未达到设计的要求 •制造工艺过程,不能满足工艺设计的要求
常见的失效模式:
裂纹、变形、松动、泄漏 粘结、短路、氧化、断裂
2016/12/2 33
3 失效后果(Failure Effect)
2016/12/2
KCC
环 Environment 测 Measure
KCC
KCC
39
法 Method
9 FMEA 定义
Potential Failure Mode and Effects Analysis
潜在失效模式及后果分析
是一种系统化的可靠性定性分析方法 通过对系统各组成部分进行事前分析,发现, 评 价产品 /过程中潜在的失效模式,查明其对系统的 影响程度,针对性的采取措施进行预防的分析方法
8
B
A
2016/12/2
1+1+1=3
9
B
2
3x2=6
A
2016/12/2
3
10
C
3
D
B
2
3x2x3=18
A
2016/12/2
3
11
C
回顾二个定理
加法定理:
如果要完成一个事件,有若干种方法n1,n2,n3,n4,…. 则完成这个事件总的方法有 N =
n 1 + n 2 + n 3 + n4 +
管理的基本逻辑方法
图例
开始 结束
开始 过程 活动 判断
记录
过程
活动 判断
记录
人流物流
2016/12/2
信息流
结束
15
管理的基本思维方法
控制方法
输入
输出
确定关键输入
简单 低成本 易操作 共性强 2016/12/2
使用资源
明显改善输出
复杂 高产出 难操作 特性强
16
管理的基本思维方法
控制方法
输入
输出
2016/12/2 26
三种类型
Process-FMEA P-FMEA
对工艺流程设计输出在验证前的综合评估
识别和消除制造 /服务过程中的潜在隐患
深及制造 /服务过程每一环节的潜在隐患
2016/12/2 27
三种基本情况
新设计,新技术,新过程的开发 对现有设计或过程的修改 对现有设计或过程的重要修改 现有的设计或过程有新的应用
是一种系统化的结构性相关分析方法
识别产品或过程失效模式 估计涉及特殊原因的风险 减小风险的措施优先排序 评价产品的设计验证计划 拟制当前的过程控制计划
2016/12/2 41
10 FMEA 的类别
System-FMEA Design-FMEA Process-FMEA
2016/12/2 42
FMEA的作用
Manufacture characteristic
KCC MC CC
Control characteristic
Key Control
characteristic
SCC
人 Man
Standard Control characteristic
料 Material
机 Machine
KCC
KCC
KCC KPC
___________部件 ________________ 设计责任__________ 编制人__________ 车型年 / 车辆类型___________________ 关键日期__________ FMEA 日期(编制)________(修订)_________ 核心小组_________________________________________________________________________________________
很明显:
过程的简化与优化是事件成功的
关键
2016/12/2 13
过程的改进与优化
价值流分析(VALUE STREAM) 精益生产(LEAN PLAN) 六西格玛控制(SIX SIGMA CONTROL) 质量功能分配(QUALITY FUNCTION DEPLOYMENT)
2016/12/2 14
2016/12/2 28
这是一张典型的FMEA的表格
如果你是用于QS9000,那么就必须完全使用它!!
如果你是用于其他场合,完全可以由你自己设计
___________系统 ___________子系统
潜在失效模式及后果分析 FMEA
FMEA 编号 ___________ 共______页, 第______页
——影响安全,国家法律法规
S/C
Key product Characteristic
KPC 重要特性
Product characteristic
F/F
Function /F it
PC
Standard
一般特性
2016/12/2 38
8 KCC 重要的过程控制特性
——影响重要产品特性(KPC)
的过程控制特性(CC)
30
FMEA的一些基本概念
1.失效 3.失效后果 2.失效模式 4.失效原因
5.顾客
7.KPC 9.FMEA的定义
2016/12/2
6.KCDS(特殊特性标识系统)
8.KCC 10.FMEA的类型
31
1 失效 (Failure)
—— 实体失去了完成其功能的能力
实体?
S-FMEA 系统 D-FMEA 产品 P-FMEA 过程 失效=不合格吗? 失效=事故吗?
后经发展,对可能造成特别严重后果的失效模式 进行单独分析,称危害度分析. 简称 FMECA。 (CA: Criticality Analysis )
2016/12/2 40