4、转炉炼钢工艺制度(下)共45页
炼钢工艺管理制度

炼钢工艺管理制度第一章总则第一条为规范和管理炼钢工艺,保证生产质量,提高工作效率,制定本制度。
第二条本制度适用于钢铁生产企业的炼钢工艺管理。
第三条炼钢工艺管理应遵循安全生产、环保、质量控制和节能减排的原则,保证生产过程安全稳定、高效持续。
第四条炼钢工艺管理应根据生产工艺特点和技术要求,合理制定和落实各项管理制度。
第五条炼钢工艺管理应强化标准化管理,健全质量控制体系,提高产品质量水平。
第六条炼钢工艺管理应加强环保意识,严格执行国家和地方环保法规政策,积极推进节能减排工作。
第二章组织机构第七条炼钢工艺管理应设立专门的工艺管理部门,负责炼钢生产工艺流程的规划、监控和改进。
第八条工艺管理部门应设立生产工艺组、技术研发组和质量控制组等专门机构。
第九条生产工艺组负责炼钢生产工艺的设计、调整和检测,确保生产工艺稳定可靠。
第十条技术研发组负责对新工艺、新技术进行研究和试验,提高产品质量和工艺水平。
第十一条质量控制组负责制定产品质量标准、检测方法和质量控制方案,确保产品合格率。
第三章工艺设计第十二条炼钢工艺设计应综合考虑原材料、设备、炼钢工艺流程和成品质量等因素,合理优化工艺。
第十三条炼钢工艺设计应符合国家标准和行业规范,确保生产安全和产品质量。
第十四条炼钢工艺设计应充分考虑环保要求,精简工艺流程,减少污染排放。
第十五条炼钢工艺设计应使用先进的技术和设备,提高生产效率和产品品质。
第十六条炼钢工艺设计应注重节能减排,合理利用资源,降低生产成本。
第四章工艺控制第十七条炼钢工艺控制应建立健全的监控体系,及时发现和处理工艺异常。
第十八条炼钢工艺控制应加强生产过程中的参数调节和检测,确保生产质量。
第十九条炼钢工艺控制应对关键环节实施严格的监督和管理,杜绝安全事故和产品质量问题。
第二十条炼钢工艺控制应加强信息化管理,利用先进的信息技术手段对工艺过程进行监控和分析。
第二十一条炼钢工艺控制应加强对人员的培训和管理,提高员工的技术素质和安全意识。
转炉炼钢工艺课件
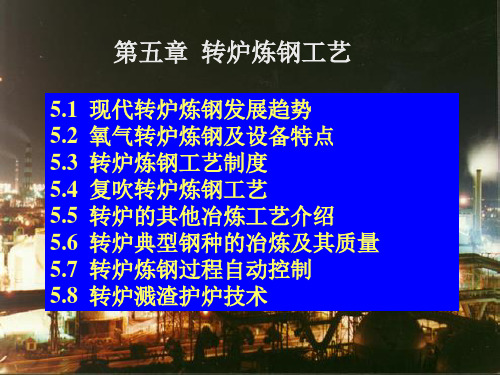
5.3.1 原料装入制度
不同的转炉,以及同一转炉在不同的生产条件 下,都有其不同的合理的金属装入量。
装入量过大,喷溅增加,熔池搅拌不好,造渣 困难,炉衬特别是炉帽寿命缩短,供氧强度也 因喷溅大而被迫降低。
装入量过小,炉产量减少。因熔池过浅,炉底 容易受来自氧气射流区的高温和高氧化铁的循 环流冲击,甚至损坏炉底。
回收→三通阀→水封逆止阀→V形水封→煤气柜 风机
放散→旁通阀→放散烟囱
LT法净化、回收系统工艺流程
LT法净化、回收系统工艺流程
未燃烟气(800~1000 ℃ )→活动罩裙→冷却烟道(或余热锅炉)→蒸发冷却器
(蒸发冷却塔)→煤气冷却(150~200℃) 、干燥(水雾蒸发)、除粗尘→
干粗尘
回收→三通阀→冷却塔→煤气柜
补炉长瓢 (与炉前共用);
补炉短瓢 (与炉前共用); 撬捧(与炉前共用); 长撬捧;泥塞棒;
氧气皮管, 氧气管
(与炉前共用); 铁锹;鎯头
(与炉前共用); 出钢口塞; 挡渣球。
炉后用具示意图
炉后操作用具
•转炉简介 •转炉解剖 •现场转炉炉内演示 •补炉操作程序
请单击画面
转炉是炼钢 的反应容器, 它由炉帽、 炉身和炉底 组成。在炉 帽和炉身的 连接处安置 一个出钢口
现 场 转 炉
兑铁水 加废钢
操 作
请单击画面
5.3.1 原料装入制度
装料工艺对转炉炼钢的技术经济指标有明显的 影响。
对使用废钢的转炉,如先装废钢后兑铁水,为 了保护炉衬不被废钢击伤,应先加洁净的轻废 钢,再加中型和重型废钢。过重的废钢,最好 在兑铁水后加入。
为了防止炉衬过分急冷,装完废钢后应立即兑 入铁水。
转炉炼钢的工艺流程

转炉炼钢的工艺流程
《转炉炼钢的工艺流程》
转炉炼钢是一种常用的钢铁冶炼方法,其工艺流程主要包括原料准备、炉前处理、炼钢过程和成品出炉等环节。
首先是原料准备。
在转炉炼钢生产线上,主要使用的原料通常包括生铁、废钢和废铁。
这些原料需要经过预处理、配料等环节,以确保其化学成分符合生产要求。
接下来是炉前处理。
在转炉炼钢的炉前处理环节,主要包括抛丸清理、喷吹脱硫等工序,以确保进入转炉的原料具有良好的熔化性能和清洁度。
然后是炼钢过程。
炼钢过程主要包括炉前倒料、保护渣层、吹炼、控制成分等环节。
在这一过程中,通过向转炉中吹入氧气和喷吹其他合金添加剂,将原料中的杂质和不良元素得以去除,从而得到合格的熔池成品。
最后是成品出炉。
在转炉炼钢的成品出炉环节,主要包括连铸、凝固、切割、成品检验等工序,最终得到合格的钢材成品。
总的来说,转炉炼钢的工艺流程包括原料准备、炉前处理、炼钢过程和成品出炉等环节。
通过这一工艺流程,可以将原料中的杂质和不良元素得以去除,从而得到优质的钢材产品。
转炉工艺管理制度

转炉工艺管理制度一、总则为加强转炉工艺管理,规范生产操作,保障生产安全和产品质量,特制定本工艺管理制度。
二、工艺参数设定1. 转炉操作工艺参数由技术部门根据原料成分、生产要求等综合考虑确定,并定期进行优化和调整。
2. 工艺参数包括但不限于转炉氧气流量、气体切换时间、炉料投放方式、炉底排渣时间等。
3. 工艺参数的设定需要进行严格的试验和验证,确保其合理稳定,符合生产要求。
三、操作规程1. 操作岗位设置:每个转炉操作岗位应配备专职操作人员,且需要经过专业培训和考试合格。
2. 操作程序:转炉操作人员需按照工艺参数设定进行操作,严格按照操作规程进行生产操作,严禁擅自调整工艺参数。
3. 数据记录:转炉操作人员需做好生产过程数据的记录,包括但不限于氧气流量、炉料投放量、气体切换时间等,以备日后查阅和分析。
四、设备管理1. 转炉设备的管理需按照相关规定进行,定期进行设备检修和维护,确保设备的正常运转和安全生产。
2. 转炉设备的使用需严格按照操作规程进行,严禁私自操作或使用不合格设备。
3. 对于设备故障或异常情况,需及时报告并采取相应的措施,保障安全生产。
五、安全防护1. 转炉操作人员需严格遵守安全操作规程,正确佩戴相关防护用品,如防护面具、手套等。
2. 转炉操作场所需保持整洁,严禁杂物堆放或燃烧,确保消防通道畅通。
3. 对于有害气体的排放及时进行监测和处理,确保环境安全。
六、品质管理1. 转炉产品的质量需严格按照产品标准要求进行生产,确保产品质量稳定。
2. 转炉操作人员需密切关注产品质量数据,对于异常情况及时报告并采取相应的措施。
3. 转炉产品的质量检测需定期进行,确保产品符合要求。
七、管理责任1. 技术部门需负责转炉工艺参数的设定、优化和调整,确保生产工艺稳定可靠。
2. 生产部门需负责转炉操作规程的制定和执行,确保生产安全和产品质量。
3. 设备部门需负责转炉设备的管理和维护,确保设备的正常运转。
4. 管理部门需负责对转炉工艺管理制度的执行和监督,确保各项规定得到有效执行。
转炉炼钢工艺过程..
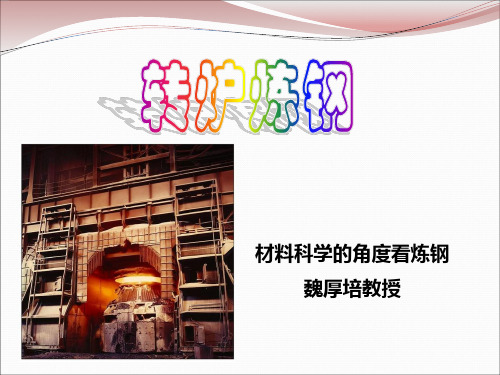
产生的氧化壳层,铁量约占70%-75%。氧化铁皮还 有助于化渣和冷却作用,使用时应加热烘烤,保持 干燥。
铁矿石中铁的氧化物存在形式是Fe2O3、Fe3O4和FeO
其氧含量分别是30.06%,27.64%和22.28%。
三、转炉冶炼五大制度
1. 装料制度
2. 供氧制度
3. 造渣制度 4. 温度制度
LD转炉
• 1970年后,由于发明了用
碳氢化合物保护的双层套 管式底吹氧枪 而出现了底 吹法,各种类型的底吹法 转炉(如OBM,Q-BOP,LSW等) 在实际生产中显示出许多 优于顶吹转炉之处,使一 直居于首位的顶吹法受到 挑战和冲击。
OBM装置
•继奥地利人Dr.Edaurd等 于1973年研究转炉顶底复 吹炼钢之后,世界各国普 遍开展了转炉复吹的研究 工作,出现了各种类型的 复吹转炉,到20世纪80年 代初开始正式用于生产。
(1)成分;
(2)带渣量; (3)温度。
1)硅(Si)
硅是重要的发热元素,铁水中含Si量高,炉内的化学热增加,铁水中Si量增
加0.10%,废钢的加入量可提高1.3%-1.5%。
铁水含Si量高,渣量增加,有利于脱磷、脱硫。
硅含量过高会使渣料和消耗增加,易引起喷溅,金属收得率降低,同时渣中 过量的SiO2,也会加剧对炉衬的侵蚀,影响石灰渣化速度,延长吹炼时间。 通常铁水中的硅含量为0.30%-0.60%为宜。
近几年中国年产钢量
2009
2007 2002 钢产量达到4.89亿t 粗钢产量达到 5.678亿t
2005 年产钢量为1.82亿t 2003 钢产量达到3.5亿t
预计2010年 将突破6亿t
钢产量首次突破2 亿t,达到2.234亿t
转炉炼钢工艺流程

转炉炼钢工艺流程转炉炼钢工艺是一种重要的钢铁生产工艺,常用于中小型钢铁企业。
下面将为大家介绍转炉炼钢工艺的基本流程。
转炉炼钢是一种冶炼方法,它的主要原理是利用高温将生铁中的杂质氧化并脱除,使得铁中含碳量减少,从而生产出合格的钢铁产品。
该工艺主要分为以下几个步骤:首先,将生铁预处理。
生铁经过预处理之后,可以去除一部分含硫、磷等杂质。
预处理包括短暂的高温还原、碳酸钙煅烧等过程。
然后,将预处理后的生铁装入转炉内。
转炉是一个直立式圆形容器,内壁有耐火材料保护。
生铁装入转炉后,开始吹氧气。
吹氧气的目的是将生铁中的碳氧化为二氧化碳,使得含碳量降低。
接着,通过添加石灰石和硅石等脱硫剂。
这些脱硫剂被放入炉内,与融化的生铁反应,吸附并氧化掉生铁中的硫。
硫气随着炉排出,从而达到去除硫杂质的目的。
然后,再进行除磷。
除磷是利用石灰石、蛋白石等物质进行,它们可以与熔融的生铁反应,将磷杂质转化为更容易被吸附和排出的化合物。
通过这种方式,可以有效降低钢中的磷含量。
接下来,加入适量的合金元素。
根据需要生产的不同钢种,可以加入一些合金元素,如锰、铬、镍等。
这些合金元素的加入可以提升钢的性能和品质。
最后,进行温度调整和取样分析。
钢液需要在一定的温度范围内冷却,然后将一定的钢液放入真空状态下进行取样分析,以确定钢液中主要成分的含量。
根据取样分析结果,可以对转炉炼钢过程进行调整,以获得所需的合格产品。
总而言之,转炉炼钢工艺流程包括生铁预处理、吹氧、脱硫、除磷、加入合金元素、温度调整和取样分析等步骤。
通过这些步骤,可以将生铁中的杂质去除,并得到合格的钢铁产品。
这种工艺流程简单可行,因此被广泛应用于中小型钢铁企业。
转炉炼钢岗位作业规程

转炉炼钢岗位作业规程转炉炼钢岗位作业规程第一章总则第一条为加强转炉炼钢工作的管理,规范操作,确保生产安全和质量,提高工作效率,特制定本作业规程。
第二条本规程适用于转炉炼钢岗位,包括转炉操作、钢水调质、炉口处理、锻炼炉甩废等岗位。
第三条所有从事转炉炼钢工作的人员必须按照本规程进行操作,严格遵守有关安全生产和环保规定。
第二章作业人员要求第四条从事转炉炼钢工作的人员必须经过相应的培训,取得相应的操作证书,并在岗位上熟练操作。
第五条作业人员必须具备良好的身体素质和健康状况,严禁有酗酒、吸烟等不良嗜好。
第六条作业人员必须配备完善的个人防护装备,包括护目镜、防尘口罩、耐高温手套等,并严格按照规定佩戴使用。
第七条作业人员要遵循岗位责任制,做到岗位交接有序,确保工作的连续性。
第三章作业程序第八条作业人员在进行转炉炼钢前,必须对设备进行检查,确保设备运转正常,无故障。
第九条在进行转炉炼钢前,必须对相关设备进行预热,达到操作要求的温度。
第十条操作人员应按照程序,依次进行转炉倒入生铁、碱、浇铸以及喷吹剂等操作,注意操作的顺序和时间。
第十一条操作人员必须经常观察转炉的操作情况,及时调整炉与钢水的比例,保证炼钢质量。
第十二条在转炉炼钢过程中,如出现异常情况,必须立即停止操作,并及时报告上级领导。
第十三条调质人员在进行钢水调质工作前,必须先取样进行化验,确保钢水的成分符合要求。
第十四条钢水调质过程中,调质人员必须按照配方和程序进行操作,严禁随意添加和调整。
第四章安全注意事项第十五条作业人员在操作过程中,必须时刻保持清醒的头脑,保持注意力集中。
第十六条作业人员不得疲劳驾驶,严禁操作过程中打瞌睡。
第十七条作业人员必须严格遵守岗位安全操作规程,杜绝违反操作规程的行为。
第十八条作业人员在操作过程中,必须保持设备和作业现场的清洁,每班结束后进行清理。
第十九条作业人员在进行炉口处理和锻炼炉甩废工作时,必须佩戴特制的耐高温手套,防止烫伤。
炼钢转炉工艺流程

炼钢转炉工艺流程
《炼钢转炉工艺流程》
炼钢转炉是一种常见的钢铁冶炼设备,采用氧气作为原料,通过不断升温、熔化、脱碳和合金化,将生铁或废钢冶炼成高品质的钢材。
其工艺流程主要包括加料、通氧、出渣、出钢四个主要过程。
首先是加料过程,将生铁、废钢、合金等原料按照一定的配比投入转炉中,并在炉内预热至适宜的温度。
加料过程中需要保证稳定的投料速度和均匀的加热,以确保后续工艺的顺利进行。
接着是通氧过程,氧气通过一定的喷嘴直接通入炉内,与炉料进行充分的混合和燃烧,产生高温的炉内环境。
在此过程中需要控制氧气的进气量和温度,使炉内气氛能够达到最佳的燃烧条件,促进炉料的融化和氧化还原反应的进行。
随后是出渣过程,炉脚下部设置有出渣孔,脱碳反应产生的气体和氧化物等杂质会通过这一孔口不断排出。
出渣的效率和质量直接关系到后续的钢液质量和工艺稳定性。
出渣过程需要通过适当的控制和处理,使得炉内的杂质尽可能排出并避免对钢液产生影响。
最后是出钢过程,当炉内的炉料达到设计要求后,将铁水通过转炉底部的出钢孔排出,经过连铸机进行浇铸成型。
出钢过程需要严格控制排钢速度和温度,以确保钢液的质量和成型的规格。
总的来说,炼钢转炉工艺流程需要进行一系列严格的操作和控制,确保原料得到充分融化和反应,以得到满足生产要求的高品质钢材。
转炉冶炼的工艺流程

转炉冶炼的工艺流程
转炉冶炼的工艺流程如下:
1.准备阶段:主要原料包括铁水、废钢和铁合金。
根据需求,加入不同的造渣材料,如石灰、白云石、铁皮球、矿石和萤石。
2.吹炼阶段:温度逐渐上升,碳含量逐渐下降。
炉口由浓烟滚滚逐渐变得明亮。
在这一阶段,通过控制枪位位置,可以防止喷溅和返干。
3.脱碳阶段:脱碳速度降低,熔池温度上升。
炉口由烟气明亮逐渐变得稀疏透明。
此时,需要确定冶炼终点,即检查碳、硫、磷和温度是否满足要求。
4.出钢阶段:通过经验法,如炉口明亮度、副枪和吹氧累积量来确定何时结束吹氧并提升氧枪。
副枪系统的使用取消了人工取样和测温,这不仅可以节省时间,而且降低了对操作人员的技能要求。
转炉炼钢原理及工艺

转炉炼钢原理及工艺
转炉炼钢是通过加热合金材料,然后将其在氧气中抽出到转炉,形成一个旋转坩埚里,再使材料在转炉内不断熔化、混合、渣滓沉淀,达到钢的熔化和净化,最后冷却固化,即可获得均匀的高质量的钢的过程。
转炉炼钢的工艺路径主要包括:原料进炉、熔炼、净化、合金添加、出炉等步骤。
1、原料进炉:将碳钢和合金料装入转炉,加热至溶化温度,开始熔融。
2、熔炼:转炉内熔融的温度受多种因素的影响,如加料量、加料温度、炉气系统的平衡性、熔炼时间等。
3、净化:即清洁熔化渣滓,消除杂质,把金属液中的杂质置于渣滓中,让金属液纯度升高。
4、合金添加:将净化后的钢液入合金添加系统,加入合金钢料,使钢液按照要求的成分,营造钢种具有相应的技术性能。
5、出炉:金属液改变形态,冷却成指定的形状和尺寸,经过纯化后形成高质量钢。
转炉炼钢工艺操作规范
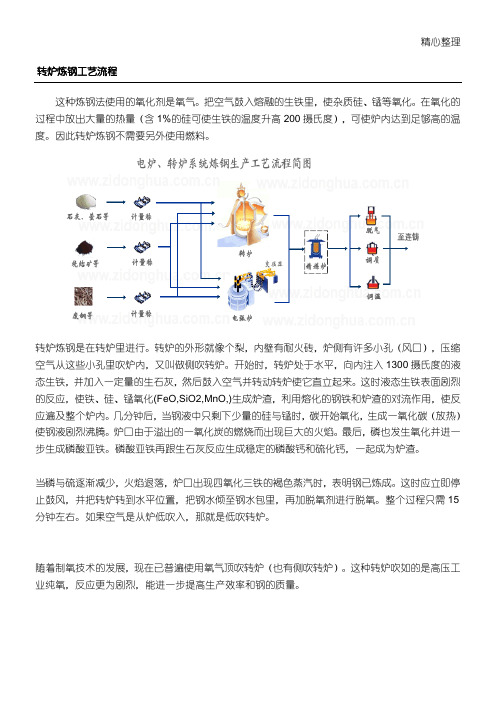
精心整理转炉炼钢工艺流程这种炼钢法使用的氧化剂是氧气。
把空气鼓入熔融的生铁里,使杂质硅、锰等氧化。
在氧化的过程中放出大量的热量(含1%的硅可使生铁的温度升高200摄氏度),可使炉内达到足够高的温度。
因此转炉炼钢不需要另外使用燃料。
摄氏度这时液态生铁表面生成炉渣,利用熔化的钢铁和炉渣的对流作用,碳开始氧化,生成一氧化碳(放热)最后,磷也发生氧化并这时应立再加脱氧剂进行脱氧。
整个过程只需15分钟左右。
如果空气是从炉低吹入,那就是低吹转炉。
随着制氧技术的发展,现在已普遍使用氧气顶吹转炉(也有侧吹转炉)。
这种转炉吹如的是高压工业纯氧,反应更为剧烈,能进一步提高生产效率和钢的质量。
转炉一炉钢的基本冶炼过程。
顶吹转炉冶炼一炉钢的操作过程主要由以下六步组成:(1)上炉出钢、倒渣,检查炉衬和倾动设备等并进行必要的修补和修理;(2(3暗红的火焰;3~5min同时渣料熔化,噪声减弱);(4)3~5min后火焰微(5(63-5分钟后,第一批渣料化小型转炉为2.5-4.5m3/(t·min);120t以上的转炉一般为2.8-3.6m3/(t·min)。
◆开吹时氧枪枪位采用高枪位,目前是为了早化渣,多去磷,保护炉衬;◆在吹炼过程中适当降低枪位的保证炉渣不“返干”,不喷溅,快速脱碳与脱硫,熔池均匀升温为原则;◆在吹炼末期要降枪,主要目的是熔池钢水成分和温度均匀,加强熔池搅拌,稳定火焰,便于判断终点,同时使降低渣中Fe含量,减少铁损,达到溅渣的要求。
◆当吹炼到所炼钢种要求的终点碳范围时,即停吹,倒炉取样,测定钢水温度,取样快速分析[C]、[S]、[P]的含量,当温度和成分符合要求时,就出钢。
◆当钢水流出总量的四分之一时,向钢包中的脱氧合金化剂,进行脱氧,合金化,由此一炉钢冶炼完毕。
炼钢学概述第一节?????概述一、钢与生铁的区别及发展历程:铁的熔点在航天航空、交通运输、农业、国防等许多重要的领域均需要各种类型的大量钢材,我们的日常生活更离不开钢。
转炉炼钢主要工艺介绍(PPT 68页)

6
1.金属料
• 1)铁水:占钢铁料的(75~100%) 主要要求 成分:[Si]、[Mn]、[P]、[S] 温度: T
7
铁水成分及温度影响
• Si影响 • 转炉炼钢重要发热元素,[Si]↑0.1%,废钢比↑1.0%。 • 铁水合适的[Si]0.3-0.5%。 • [Si] >0.6%,渣量增加并引起喷溅;渣中(SiO2)↑。 • 石灰加入量=(2.14×R× [Si] )×1000 /(石灰CaO
• 热来源于:
• 转炉炼钢不需要外来热源;
铁水物理热及元素氧化化学热。 铁水及废钢的合理配比须根据炉子的热平衡计算确定。 • 硅的作用 优点:因发热量大,增大废钢加入量,一般铁水中Si增 加0.1%,废钢比增大1%。 缺点:增大渣量,侵蚀炉衬一般控制在0.3-0.5%。
29
转炉兑铁水操作现场图示
一范围 0.75-1.1Mpa。 • 枪位,由冲击深度决定,1/3-1/2。 • 供氧强度(Nm3/t.min) 决定冶炼时间,但太大,喷溅可
能性增大,一般3.0-4.0。
34
氧枪
氧枪是转炉供氧的 主要设备,它是由 喷头、枪身和尾部 结构组成。 喷头是用导热性良 好的紫铜经锻造和 切割加工而成,也 有用压力浇铸而成 的。喷头的形状有 拉瓦尔型、直筒型 和螺旋型等。目前 应用最多的是多孔 的拉瓦尔型喷头。
30
2.2造渣制度
• 造渣制度就是确定合适的造渣方法、渣料加入量和时 间,以及如何快速成渣。
• 炼钢就是炼渣。通过造渣,快速脱P、脱S,减少喷溅, 保护炉衬,降低终点氧含量。
• 石灰的熔解: 加开石始灰后吹,氧由时2渣Fe中O·主Si要O2是→CSaiOO·2F,eOM·nSOi,O2F→eO2,C是aO酸·S性iO渣2 ,, 2CaO·SiO2难熔渣,石灰溶解有些停滞,出现返干。
转炉炼钢工艺操作规程
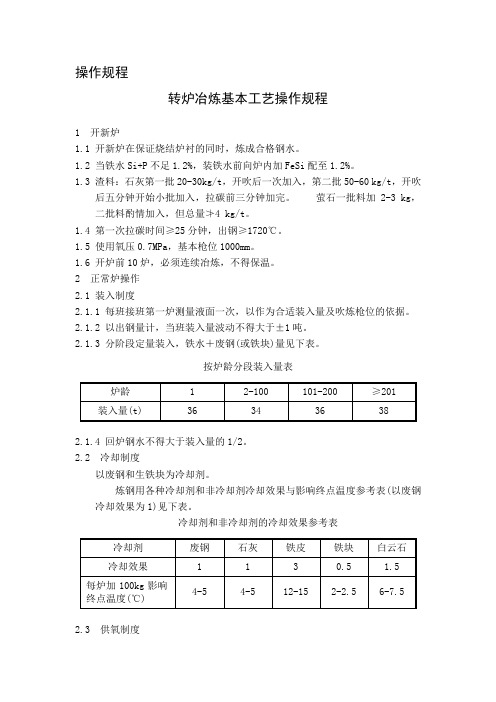
操作规程转炉冶炼基本工艺操作规程1 开新炉1.1 开新炉在保证烧结炉衬的同时,炼成合格钢水。
1.2 当铁水Si+P不足1.2%,装铁水前向炉内加FeSi配至1.2%。
1.3 渣料:石灰第一批20-30kg/t,开吹后一次加入,第二批50-60 kg/t,开吹后五分钟开始小批加入,拉碳前三分钟加完。
萤石一批料加2-3 kg,二批料酌情加入,但总量≯4 kg/t。
1.4 第一次拉碳时间≥25分钟,出钢≥1720℃。
1.5 使用氧压0.7MPa,基本枪位1000mm。
1.6 开炉前10炉,必须连续冶炼,不得保温。
2正常炉操作2.1 装入制度2.1.1 每班接班第一炉测量液面一次,以作为合适装入量及吹炼枪位的依据。
2.1.2 以出钢量计,当班装入量波动不得大于±1吨。
2.1.3 分阶段定量装入,铁水+废钢(或铁块)量见下表。
按炉龄分段装入量表2.1.4 回炉钢水不得大于装入量的1/2。
2.2 冷却制度以废钢和生铁块为冷却剂。
炼钢用各种冷却剂和非冷却剂冷却效果与影响终点温度参考表(以废钢冷却效果为1)见下表。
冷却剂和非冷却剂的冷却效果参考表2.3 供氧制度2.3.1 采用分期定压、恒压变枪位操作。
氧压低于0.4MPa不得吹炼。
各阶段氧压参考表2.3.2 枪位控制基本枪位900-1100mm,波动枪位800-1200mm。
枪位调整要做到勤动少动。
正常情况应控制≯200mm/次。
以基本枪位为主要吹炼枪位,为迅速成渣,在开始吹炼时或炉渣返干时允许适当提高枪位。
严禁过高枪位操作。
冶炼末期要采取低枪位操作,时间最少不少于60秒。
2.3.3 采用三孔喷头吹炼,喷头参数φ27×3-11,氧枪漏水时应及时换枪。
2.4 造渣制度要求吹炼全程化渣2.4.1 除后吹炉次外,均采用留渣操作工艺。
即出完钢后,先向炉内加入石灰、白云石混合物,稠化炉渣,后吹炉次必须倒净炉渣,不得先加石灰,后倒渣。
2.4.2 铁水Si>0.8%时应采用双渣操作。
转炉炼钢5大制度
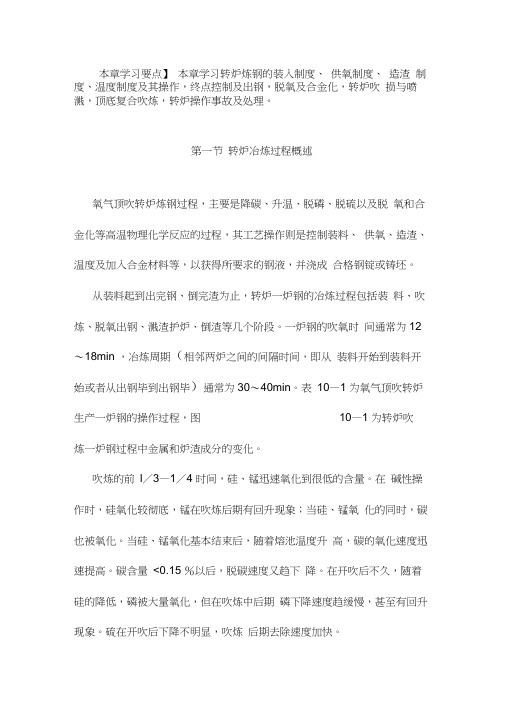
本章学习要点】本章学习转炉炼钢的装入制度、供氧制度、造渣制度、温度制度及其操作,终点控制及出钢,脱氧及合金化,转炉吹损与喷溅,顶底复合吹炼,转炉操作事故及处理。
第一节转炉冶炼过程概述氧气顶吹转炉炼钢过程,主要是降碳、升温、脱磷、脱硫以及脱氧和合金化等高温物理化学反应的过程,其工艺操作则是控制装料、供氧、造渣、温度及加入合金材料等,以获得所要求的钢液,并浇成合格钢锭或铸坯。
从装料起到出完钢、倒完渣为止,转炉一炉钢的冶炼过程包括装料、吹炼、脱氧出钢、溅渣护炉、倒渣等几个阶段。
一炉钢的吹氧时间通常为12〜18min ,冶炼周期(相邻两炉之间的间隔时间,即从装料开始到装料开始或者从出钢毕到出钢毕)通常为30〜40min。
表10—1 为氧气顶吹转炉生产一炉钢的操作过程,图10—1 为转炉吹炼一炉钢过程中金属和炉渣成分的变化。
吹炼的前l/3—1/4 时间,硅、锰迅速氧化到很低的含量。
在碱性操作时,硅氧化较彻底,锰在吹炼后期有回升现象;当硅、锰氧化的同时,碳也被氧化。
当硅、锰氧化基本结束后,随着熔池温度升高,碳的氧化速度迅速提高。
碳含量<0.15 %以后,脱碳速度又趋下降。
在开吹后不久,随着硅的降低,磷被大量氧化,但在吹炼中后期磷下降速度趋缓慢,甚至有回升现象。
硫在开吹后下降不明显,吹炼后期去除速度加快。
熔渣成分与钢中元素氧化、成渣情况有关。
渣中CaO 含量、碱度随冶炼时间延长逐渐提高,中期提高速度稍慢些;渣中氧化铁含量前后期较高,中期随脱碳速度提高而降低;渣中Si0 2,Mn0 ,P205 含量取决于钢中Si,Mn ,P 氧化的数量和熔渣中其他组分含量的变化。
在吹炼过程中金属熔池升温大致分三阶段:第一阶段升温速度很快,第二阶段升温速度趋缓慢,第三阶段升温速度又加快。
熔池中熔渣温度比金属温度约高20-100 0C。
根据熔体成分和温度的变化,吹炼可分为三期:硅锰氧化期(吹炼前期)、碳氧化期(吹炼中期)、碳氧化末期(吹炼末期)氧气顶吹转炉一炉钢的操表10 —1作1(7 6 s 4 i 2 t 0_ 41060 4 60.5f)•电工艺6 2:3OZO1Ou2 密二g*・忑L2F.K3三第二节 装入制度与装入操作一、装入量装入量指炼一炉钢时铁水和废钢的装入数量, 它是决定转炉产量、 炉龄及其他技术经济指标的重要因素之一。
钢铁厂炼钢工艺管理制度
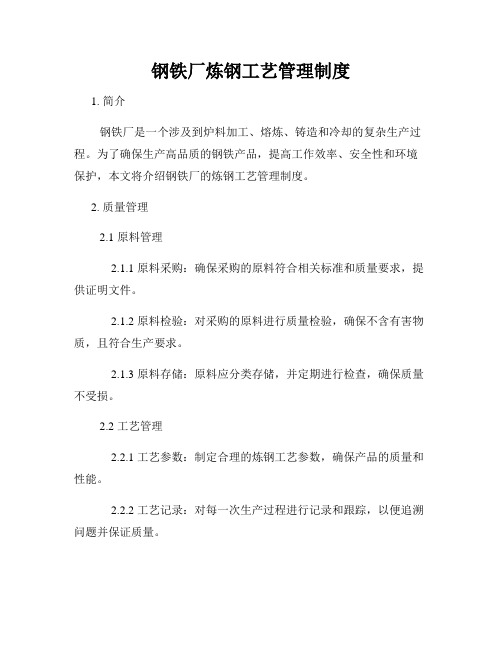
钢铁厂炼钢工艺管理制度1. 简介钢铁厂是一个涉及到炉料加工、熔炼、铸造和冷却的复杂生产过程。
为了确保生产高品质的钢铁产品,提高工作效率、安全性和环境保护,本文将介绍钢铁厂的炼钢工艺管理制度。
2. 质量管理2.1 原料管理2.1.1 原料采购:确保采购的原料符合相关标准和质量要求,提供证明文件。
2.1.2 原料检验:对采购的原料进行质量检验,确保不含有害物质,且符合生产要求。
2.1.3 原料存储:原料应分类存储,并定期进行检查,确保质量不受损。
2.2 工艺管理2.2.1 工艺参数:制定合理的炼钢工艺参数,确保产品的质量和性能。
2.2.2 工艺记录:对每一次生产过程进行记录和跟踪,以便追溯问题并保证质量。
2.2.3 工艺优化:随着技术的发展,持续改进工艺,并进行试验和验证,降低生产成本,提高产品质量。
3. 设备管理3.1 设备维护3.1.1 定期检查:按照设备维护计划,对设备进行定期检查,确保设备运行状态正常。
3.1.2 日常维护:设备操作人员应进行日常维护工作,保持设备的正常运行和安全性。
3.1.3 备用设备:配备备用设备,以便出现故障时能够及时维修或更换。
3.2 设备更新3.2.1 技术更新:随着科技的进步,及时更新设备,使其能够适应新的工艺要求。
3.2.2 性能评估:对新设备进行性能评估,确保其符合工艺要求并提高生产效率。
3.2.3 设备培训:对操作人员进行设备使用培训,提高工作效率和操作安全。
4. 安全管理4.1 安全制度4.1.1 安全规定:制定全面的安全规定,包括安全操作流程、事故预防和应急处置等。
4.1.2 安全培训:对所有员工进行安全培训,提高员工的安全意识和紧急处理能力。
4.1.3 安全检查:定期进行安全检查,发现和整改潜在的安全隐患。
4.2 应急管理4.2.1 应急预案:制定详细的应急预案,包括事故类型、应对措施和责任分工等。
4.2.2 应急演练:定期组织应急演练,提高员工在应急事件中的反应和处理能力。
4、转炉炼钢工艺制度(下)
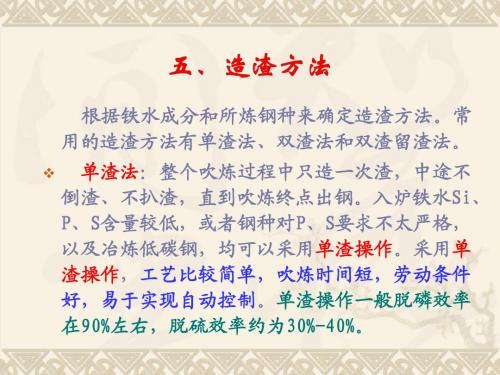
六、温度制度
在吹炼一炉钢的过程中,需要正确控制温度。
温度制度主要是指炼钢过程温度控制和终点温
度控制。
转炉吹炼过程的温度控制相对比较复杂,如 何通过加冷却剂和调整枪位,使钢水的升温和 成分变化协调起来,同时达到吹炼终点的要求, 是温度控制的关键。
热量来源:铁水的物理热和化学热,它 们约各点热量来源的一半。 热量消耗:习惯上转炉的热量消耗可分 为两部分,一部分直接用于炼钢的热量, 即用于加热钢水和炉渣的热量;一部分未 直接用于炼钢的热量,即废气、烟尘带走 的热量,炉口炉壳的散热损失和冷却剂的 吸热等。
双渣留渣法:将双渣法操作的高碱度、高氧 化铁、高温、流动性好的终渣留一部分在炉内, 然后在吹炼第一期结束时倒出,重新造渣。此 法的优点是可加速下炉吹炼前期初期渣的形成, 提高前期的去磷、去硫率和炉子热效率,有利 于保护炉衬,节省石灰用量。采用留渣操作时, 在兑铁水前首先要加废钢稠化冷凝熔渣,当炉 内无液体渣时才可兑入铁水,以避免引发喷溅。
加速渣料的熔化
加速石灰溶解的措施 1)适宜的炉渣成分 渣中的(FeO)是石灰溶解的基本熔剂,原因在于: (1)(FeO)可与CaO及2CaO· SiO2作用生成低熔点的盐,能有效 地降低炉渣的粘度,改善石灰溶解的外部传质条件; (2)(FeO)是碱性氧化渣的表面活性物质,可以改善炉渣对石 灰的润湿性,有利于熔渣向石灰表面的孔中渗透,增大二者之间的 接触面积; (3)Fe2+及O2-的半径是同类中最小的,扩散能力最强; (4)有足够的(FeO)存在时,可以避免石灰表面生成C2S而有 利于石灰的溶解。 因此,吹炼操作中应合理地控制枪位,始终保持较高的 (FeO)含量。(MnO)对石灰溶解的影响与(FeO)类似,生产中可 在渣料中配加适量锰矿。
转炉炼钢的六大制度
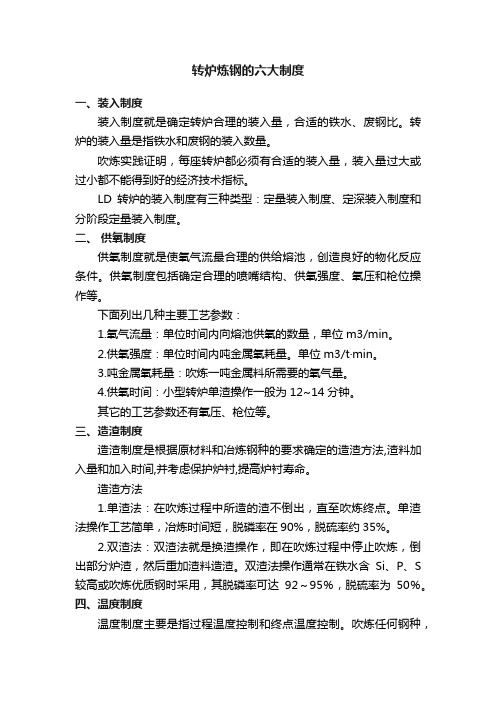
转炉炼钢的六大制度一、装入制度装入制度就是确定转炉合理的装入量,合适的铁水、废钢比。
转炉的装入量是指铁水和废钢的装入数量。
吹炼实践证明,每座转炉都必须有合适的装入量,装入量过大或过小都不能得到好的经济技术指标。
LD转炉的装入制度有三种类型:定量装入制度、定深装入制度和分阶段定量装入制度。
二、供氧制度供氧制度就是使氧气流最合理的供给熔池,创造良好的物化反应条件。
供氧制度包括确定合理的喷嘴结构、供氧强度、氧压和枪位操作等。
下面列出几种主要工艺参数:1.氧气流量:单位时间内向熔池供氧的数量,单位m3/min。
2.供氧强度:单位时间内吨金属氧耗量。
单位m3/t·min。
3.吨金属氧耗量:吹炼一吨金属料所需要的氧气量。
4.供氧时间:小型转炉单渣操作一般为12~14分钟。
其它的工艺参数还有氧压、枪位等。
三、造渣制度造渣制度是根据原材料和冶炼钢种的要求确定的造渣方法,渣料加入量和加入时间,并考虑保护炉衬,提高炉衬寿命。
造渣方法1.单渣法:在吹炼过程中所造的渣不倒出,直至吹炼终点。
单渣法操作工艺简单,冶炼时间短,脱磷率在90%,脱硫率约35%。
2.双渣法:双渣法就是换渣操作,即在吹炼过程中停止吹炼,倒出部分炉渣,然后重加渣料造渣。
双渣法操作通常在铁水含Si、P、S 较高或吹炼优质钢时采用,其脱磷率可达92~95%,脱硫率为50%。
四、温度制度温度制度主要是指过程温度控制和终点温度控制。
吹炼任何钢种,对其出钢温度都有要求。
控制好终点温度是LD转炉吹炼工艺的重要环节之一。
控制好过程温度是确保终点温度合格的关键。
铁水的物理热是指铁水带入的热量,与铁水的温度有直接关系;铁水的化学热就是铁水中各成分氧化、成渣所放出的热量,他与铁水的化学成分有关。
在转炉吹炼中,一般铁水温度为1250~1400℃,而出钢温度通常为1650℃左右。
出钢温度的确定:出钢温度受钢种,锭型和浇注方法的影响,其依据原则是:1).保证浇注温度高于所炼钢种凝固温度50~100℃(小炉子偏上限,大炉子偏下限)。
- 1、下载文档前请自行甄别文档内容的完整性,平台不提供额外的编辑、内容补充、找答案等附加服务。
- 2、"仅部分预览"的文档,不可在线预览部分如存在完整性等问题,可反馈申请退款(可完整预览的文档不适用该条件!)。
- 3、如文档侵犯您的权益,请联系客服反馈,我们会尽快为您处理(人工客服工作时间:9:00-18:30)。
理论用量W(kg/t)=
1000渣量(%MgO) 渣 (%MgO) 白
实际用量W/=W-W灰-W衬
(3) 其他熔剂的用量 萤石用量:尽量少用或不用,要求≤4kg/t。 矿石用量:铁矿石及氧化铁皮也具有较强的化渣能力, 但同时对熔池产生较大的冷却效应,其用量应视炉内温度 的高低,一般为装入量的2~5%。
渣料的加入方法
关于渣料的加入,关键是要注意渣料的分批和 把握加入的时间。
(1) 渣料分批 目的:渣料应分批加入以加速石灰的熔化(否 则,会造成熔池温度下降过多,导致渣料结团且 石灰块表面形成一层金属凝壳而推迟成渣)。 批次:单渣操作时,渣料通常分成两批:1/2~ 2/3及白云石全部(冶炼初期炉衬侵蚀最严重); 1/2~1/3。
(2) 加料时间 1)第一批渣料在开吹的同时加入。 2)第二批渣料,一般是在硅及锰的氧化基本结束、头 批渣料已经化好、碳焰初起的时候(30吨的转炉开吹6 min左右)加入(如果加入过早,炉内温度还低且头批渣 料尚未化好又加冷料,势必造成渣料结团难化;反之, 如果加入过晚,正值碳的激烈氧化时期,渣中的(∑FeO) 较低渣料亦难化。问题的关键是正确判断炉况,头批渣 料化好的标志是:火焰软且稳定,炉内发出柔和的嗡嗡 声,喷出物为片状,落在炉壳上不粘贴;未化好的情况 是:炉口的火焰发散且不稳定,炉内发出尖锐的吱吱声, 喷出物是金属火花和石灰粒)。
石灰用量(kg/t)= 1000[%Si]6028B
%CaO有效
式中 [%Si]——炉料中硅的质量分数; 60/28——表示1kgSi氧化后可生成60/28
(=2.14)kg的SiO2。
(2) 白云石用量的确定 白云石的加入量应根据炉渣要求的饱和MgO含量
来确定。通常渣中MgO含量控制在8%~10%,除了加入的 白云石含有外,石灰和炉衬也会带入一部分。
双渣留渣法:将双渣法操作的高碱度、高氧 化铁、高温、流动性好的终渣留一部分在炉内, 然后在吹炼第一期结束时倒出,重新造渣。此 法的优点是可加速下炉吹炼前期初期渣的形成, 提高前期的去磷、去硫率和炉子热效率,有利 于保护炉衬,节省石灰用量。采用留渣操作时, 在兑铁水前首先要加废钢稠化冷凝熔渣,当炉 内无液体渣时才可兑入铁水,以避免引发喷溅。
泡沫渣的控制
转炉吹炼的初期和末期,因脱碳速度小而炉渣的泡末 化程度较低,因而控制的重点是防止吹炼中期出现严重的 泡沫化现象。通常是因枪位过高,炉内的碳氧反应被抑制, 渣中聚集的(FeO)越来越多(内部条件具备),温度一旦 上来便会发生激烈的碳氧反应,过量的CO气体充入炉渣 (外部条件具备),使渣面上涨并从炉口溢出或喷出,形 成所谓的喷溅。为此,生产中应是在满足化渣的条件下尽 量低些,切忌化渣枪位过高和较高枪位下长时间化渣,以 免渣中(FeO)过高。
五、造渣方法
根据铁水成分和所炼钢种来确定造渣方法。常 用的造渣方法有单渣法、双渣法和双渣留渣法。 单渣法:整个吹炼过程中只造一次渣,中途不 倒渣、不扒渣,直到吹炼终点出钢。入炉铁水Si、 P、S含量较低,或者钢种对P、S要求不太严格, 以及冶炼低碳钢,均可以采用单渣操作。采用单 渣操作,工艺比较简单,吹炼时间短,劳动条件 好,易于实现自动控制。单渣操作一般脱磷效率 在90%左右,脱硫效率约为30%-40%。
出钢前压枪降低渣中的(FeO),破坏泡沫渣,以减少 金属损失。
渣料的用量
加入炉内的渣料主要是石灰和白云石,还有少量的萤 石或氧化铁皮等熔剂。
(1) 石灰用量的确定 首先根据铁水的硅、磷含量和炉渣碱度计算
铁水含磷<0.3%时,炉渣的碱度B=(%CaO)/(%SiO2) =2.8~3.2,所以每吨铁水的石灰加入量按下式计算:
吹炼后期,脱碳速度降低,产生的CO减少,碱度进 一步提高,∑(FeO)较高,但[C]较低,产生的CO少, 表面活性物质的活度比中期进一步降低,因此,泡沫 稳定的因素大大减弱,泡沫渣趋向消除。
影响熔渣泡沫化的因素:
⑴进入熔渣的气体量 这是熔渣泡沫化的外部条件,单位时间内进入炉渣 的气体越多,炉渣的泡沫化程度越高,例如吹炼中期 脱碳速度快,产生气体量大,容易出现炉渣严重泡沫 化现象。 ⑵ 熔渣本身的发泡性即气体在渣中的存留时间 这是熔渣泡沫化的内部条件,它取决于熔渣的粘度 和表面张力。炉渣的表面张力愈小,其表面积就愈易 增大即小气泡愈易进入而使之发泡;增大炉渣的粘度, 将增加气泡合并长大及从渣中逸出的阻力,渣中气泡 的稳定性增加。
双渣法:整个吹炼过程中需要倒出或扒出约 1/2-2/3炉渣,然后加入渣料重新造渣。根据铁水 成分和所炼钢种的要求,也可以多次倒渣造新渣。 在铁水含磷高且吹炼高碳钢,铁水硅含量高,为 防止喷溅,或者在吹炼低锰钢种时,为防止回锰 等均可采用双渣操作。双渣操作脱磷效率可达95% 以上,脱硫效率约60%左右。双渣操作会延长吹炼 时间,增加热量损失,降低金属收得率,也不利 于过程自动控制。其操作的关键是决定合适的放 渣时间。
大量的研究表明,气泡少而小,炉渣表面 张力低,炉渣粘度大,温度低,泡沫容易形 成并稳定地存在于渣中,生成泡沫渣。
吹炼前期,脱碳速度小,泡沫小而无力,易停留在 渣中,炉渣碱度低,∑(FeO)较高,有利于渣中铁滴 生成CO气泡,并含有一定量的SiO2、P2O5等表面活性 物质,因此易起泡沫。
吹炼中期,脱碳速度大,大量的CO气泡能冲破渣层 而排出,炉渣碱度高,∑(FeO)较低,SiO2、P2O5表面 活性物质的活度降低,因此引起泡沫渣的条件不如吹 炼初期,但如能控制得当,避免或减轻熔渣返干现象, 就能得到合适的泡沫渣。
泡沫渣
在吹炼过程中,由于氧射流与熔池的相 互作用,形成了气—熔渣—金属液密切混 合的三相乳化液。分散在炉渣中的小气泡 的总体积往往超过熔渣本身体积的数倍甚 至数十倍。熔渣成为液膜,将气泡包住, 引起熔渣发泡膨胀,形成泡沫渣。
由于炉内的乳化现象,大大发展了气—熔 渣—金属液的界面,加快了炉内化学反应速 度,从而达到良好的吹炼效果。当然若控制 不当,严重的泡沫渣也会引发事故。