各类脱硫工艺流程图
醇胺法脱硫工艺流程图
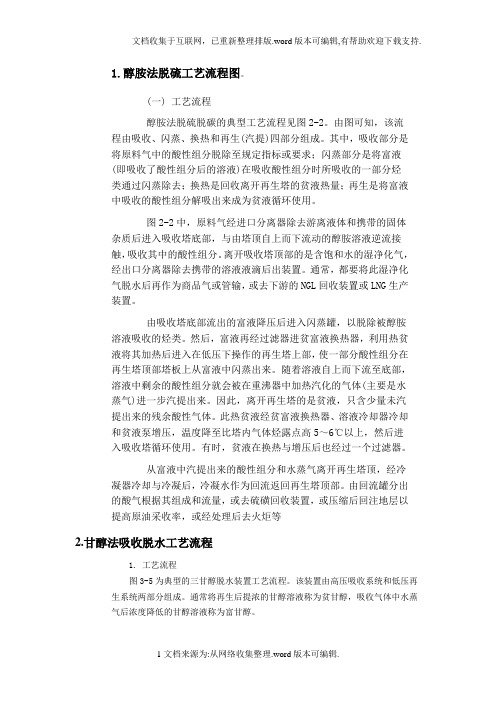
1.醇胺法脱硫工艺流程图。
(一) 工艺流程醇胺法脱硫脱碳的典型工艺流程见图2-2。
由图可知,该流程由吸收、闪蒸、换热和再生(汽提)四部分组成。
其中,吸收部分是将原料气中的酸性组分脱除至规定指标或要求;闪蒸部分是将富液(即吸收了酸性组分后的溶液)在吸收酸性组分时所吸收的一部分烃类通过闪蒸除去;换热是回收离开再生塔的贫液热量;再生是将富液中吸收的酸性组分解吸出来成为贫液循环使用。
图2-2中,原料气经进口分离器除去游离液体和携带的固体杂质后进入吸收塔底部,与由塔顶自上而下流动的醇胺溶液逆流接触,吸收其中的酸性组分。
离开吸收塔顶部的是含饱和水的湿净化气,经出口分离器除去携带的溶液液滴后出装置。
通常,都要将此湿净化气脱水后再作为商品气或管输,或去下游的NGL回收装置或LNG生产装置。
由吸收塔底部流出的富液降压后进入闪蒸罐,以脱除被醇胺溶液吸收的烃类。
然后,富液再经过滤器进贫富液换热器,利用热贫液将其加热后进入在低压下操作的再生塔上部,使一部分酸性组分在再生塔顶部塔板上从富液中闪蒸出来。
随着溶液自上而下流至底部,溶液中剩余的酸性组分就会被在重沸器中加热汽化的气体(主要是水蒸气)进一步汽提出来。
因此,离开再生塔的是贫液,只含少量未汽提出来的残余酸性气体。
此热贫液经贫富液换热器、溶液冷却器冷却和贫液泵增压,温度降至比塔内气体烃露点高5~6℃以上,然后进入吸收塔循环使用。
有时,贫液在换热与增压后也经过一个过滤器。
从富液中汽提出来的酸性组分和水蒸气离开再生塔顶,经冷凝器冷却与冷凝后,冷凝水作为回流返回再生塔顶部。
由回流罐分出的酸气根据其组成和流量,或去硫磺回收装置,或压缩后回注地层以提高原油采收率,或经处理后去火炬等2.甘醇法吸收脱水工艺流程1. 工艺流程图3-5为典型的三甘醇脱水装置工艺流程。
该装置由高压吸收系统和低压再生系统两部分组成。
通常将再生后提浓的甘醇溶液称为贫甘醇,吸收气体中水蒸气后浓度降低的甘醇溶液称为富甘醇。
锅炉脱硫脱硝工艺流程图
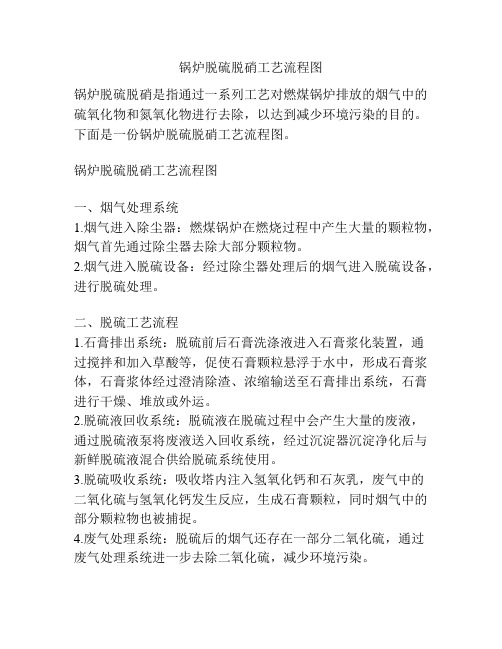
锅炉脱硫脱硝工艺流程图锅炉脱硫脱硝是指通过一系列工艺对燃煤锅炉排放的烟气中的硫氧化物和氮氧化物进行去除,以达到减少环境污染的目的。
下面是一份锅炉脱硫脱硝工艺流程图。
锅炉脱硫脱硝工艺流程图一、烟气处理系统1.烟气进入除尘器:燃煤锅炉在燃烧过程中产生大量的颗粒物,烟气首先通过除尘器去除大部分颗粒物。
2.烟气进入脱硫设备:经过除尘器处理后的烟气进入脱硫设备,进行脱硫处理。
二、脱硫工艺流程1.石膏排出系统:脱硫前后石膏洗涤液进入石膏浆化装置,通过搅拌和加入草酸等,促使石膏颗粒悬浮于水中,形成石膏浆体,石膏浆体经过澄清除渣、浓缩输送至石膏排出系统,石膏进行干燥、堆放或外运。
2.脱硫液回收系统:脱硫液在脱硫过程中会产生大量的废液,通过脱硫液泵将废液送入回收系统,经过沉淀器沉淀净化后与新鲜脱硫液混合供给脱硫系统使用。
3.脱硫吸收系统:吸收塔内注入氢氧化钙和石灰乳,废气中的二氧化硫与氢氧化钙发生反应,生成石膏颗粒,同时烟气中的部分颗粒物也被捕捉。
4.废气处理系统:脱硫后的烟气还存在一部分二氧化硫,通过废气处理系统进一步去除二氧化硫,减少环境污染。
三、脱硝工艺流程1.脱硝催化剂:适量装载于催化剂催化层中,通过催化剂对废气中的氮氧化物进行还原反应,使氮氧化物转化为氮气和水。
2.脱硝反应器:烟气进入脱硝反应器,在催化剂的作用下,氮氧化物发生还原反应,生成无害的氮气和水。
3.脱硝副产品处理:通过处理副产物,如废水中的亚硝酸盐,实现对副产物的无害化处理。
四、废气排放系统1.烟气经过去除二氧化硫和氮氧化物的处理,达到国家排放标准要求的废气,然后经过排放系统排放到大气中。
2.废气排放系统要确保排放的废气符合国家相关的环保要求,不对周围的环境造成污染。
总结:锅炉脱硫脱硝工艺流程图包括烟气处理系统、脱硫工艺流程、脱硝工艺流程和废气排放系统等几个主要部分。
通过石膏排出系统和脱硫液回收系统对脱硫废弃物进行处理和回收,通过脱硫吸收系统和废气处理系统对烟气中的二氧化硫进行去除,通过脱硝催化剂和脱硝反应器对氮氧化物进行还原反应,最后通过废气排放系统将处理后的无害废气排放到大气中。
氨法脱硫工艺流程图

氨法脱硫工艺流程图氨法脱硫是一种常用的烟气脱硫工艺,适用于煤炭、燃油等含硫燃料的燃烧排放中的硫化物的去除。
下面是一个典型的氨法脱硫工艺流程图。
工艺流程图中包括以下几个步骤:1. 烟气净化塔:烟气从锅炉或其他燃烧设备中产生后,进入烟气净化塔。
此处主要是进行粉尘的去除,通过喷洒水雾或其他净化剂,将烟气中的颗粒物捕集下来。
2. 双碱喷射吸收塔:烟气从烟气净化塔底部进入到双碱喷射吸收塔。
在吸收塔内,喷射进入的溶液与烟气进行充分接触,吸收烟气中的二氧化硫。
溶液一般是由氨水和碱液混合而成,主要成分为氨和氢氧化钠。
3. 溶液处理:吸收塔中的溶液会随着烟气中的硫化物被吸收而变得含有高浓度的硫酸盐和亚硫酸盐。
这些溶液需要经过处理进行脱硫产物的分离和再生。
首先是通过过滤和沉淀等方法,将产生的固体脱硫产物分离出来。
然后,将溶液进行再生处理,通常是经过氧化和还原反应,将硫酸盐还原为硫化物,并与新鲜的溶液混合,构成新的脱硫吸收溶液。
4. 脱硫产物处理:通过上述的溶液处理过程,产生的固体脱硫产物需要进行处理。
一般来说,这些产物中含有一定量的硫酸钙和硫酸钠,可以用于制备化肥或者其他产品;同时,可以通过煅烧工艺将其转化为硫酸盐,再继续加工利用。
5. 精制液处理:脱硫产物处理后的精制液,需要进行再次处理,以达到排放标准。
该处理一般包括过滤、吸附和中和等步骤,以置除残留的硫化物、硫酸盐和废液中的酸。
6. 污水处理:氨法脱硫工艺中,产生的废液属于含有某些浓度硫酸盐的废水,需要进行处理。
废水处理工艺一般包括初沉、生化处理、沉淀等步骤,以绞尽脱硫工艺中产生的滞后固体和溶解物质。
以上即为氨法脱硫工艺流程图的主要内容。
这个流程图展示了氨法脱硫工艺的主要步骤,以及每个步骤中的关键处理过程。
通过该工艺,能够有效地去除烟气中的硫化物,达到减少燃煤燃气排放对环境的污染的目的。
常见的十七种脱硫工艺原理及工艺图
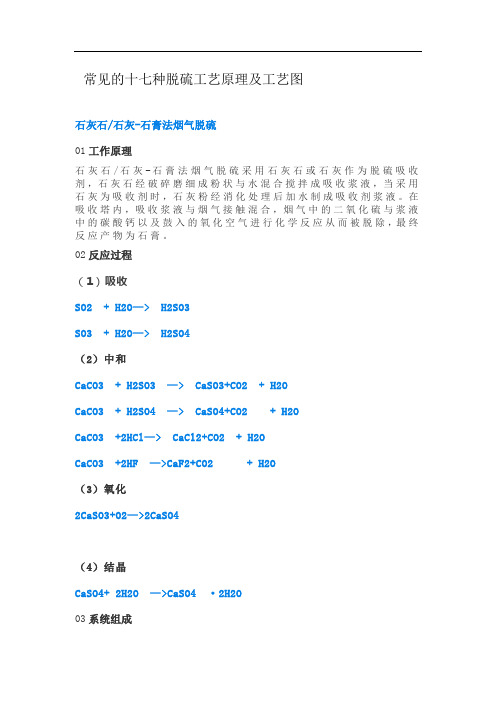
常见的十七种脱硫工艺原理及工艺图石灰石/石灰-石膏法烟气脱硫01工作原理石灰石/石灰-石膏法烟气脱硫采用石灰石或石灰作为脱硫吸收剂,石灰石经破碎磨细成粉状与水混合搅拌成吸收浆液,当采用石灰为吸收剂时,石灰粉经消化处理后加水制成吸收剂浆液。
在吸收塔内,吸收浆液与烟气接触混合,烟气中的二氧化硫与浆液中的碳酸钙以及鼓入的氧化空气进行化学反应从而被脱除,最终反应产物为石膏。
02反应过程(1)吸收SO2 + H2O—> H2SO3SO3 + H2O—> H2SO4(2)中和CaCO3 + H2SO3 —> CaSO3+CO2 + H2OCaCO3 + H2SO4 —> CaSO4+CO2 + H2OCaCO3 +2HCl—> CaCl2+CO2 + H2OCaCO3 +2HF —>CaF2+CO2 + H2O(3)氧化2CaSO3+O2—>2CaSO4(4)结晶CaSO4+ 2H2O —>CaSO4 ·2H2O03系统组成脱硫系统主要由烟气系统、吸收氧化系统、石灰石/石灰浆液制备系统、副产品处理系统、废水处理系统、公用系统(工艺水、压缩空气、事故浆液罐系统等)、电气控制系统等几部分组成。
04工艺流程锅炉/窑炉—>除尘器—>引风机—>吸收塔—>烟囱来自于锅炉或窑炉的烟气经过除尘后在引风机作用下进入吸收塔,吸收塔为逆流喷淋空塔结构,集吸收、氧化功能于一体,上部为吸收区,下部为氧化区,经过除尘后的烟气与吸收塔内的循环浆液逆向接触。
系统一般装3-5台浆液循环泵,每台循环泵对应一层雾化喷淋层。
当只有一台机组运行时或负荷较小时,可以停运1-2层喷淋层,此时系统仍保持较高的液气比,从而可达到所需的脱硫效果。
吸收区上部装二级除雾器,除雾器出口烟气中的游离水份不超过75mg/N m3。
吸收SO2后的浆液进入循环氧化区,在循环氧化区中,亚硫酸钙被鼓入的空气氧化成石膏晶体。
石膏法脱硫工艺流程图
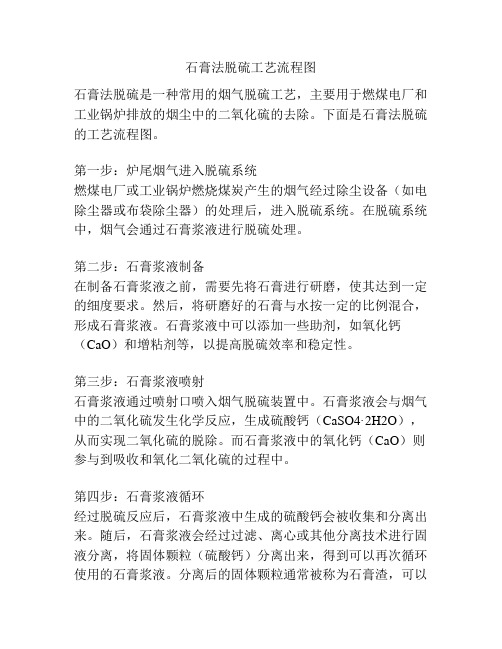
石膏法脱硫工艺流程图石膏法脱硫是一种常用的烟气脱硫工艺,主要用于燃煤电厂和工业锅炉排放的烟尘中的二氧化硫的去除。
下面是石膏法脱硫的工艺流程图。
第一步:炉尾烟气进入脱硫系统燃煤电厂或工业锅炉燃烧煤炭产生的烟气经过除尘设备(如电除尘器或布袋除尘器)的处理后,进入脱硫系统。
在脱硫系统中,烟气会通过石膏浆液进行脱硫处理。
第二步:石膏浆液制备在制备石膏浆液之前,需要先将石膏进行研磨,使其达到一定的细度要求。
然后,将研磨好的石膏与水按一定的比例混合,形成石膏浆液。
石膏浆液中可以添加一些助剂,如氧化钙(CaO)和增粘剂等,以提高脱硫效率和稳定性。
第三步:石膏浆液喷射石膏浆液通过喷射口喷入烟气脱硫装置中。
石膏浆液会与烟气中的二氧化硫发生化学反应,生成硫酸钙(CaSO4·2H2O),从而实现二氧化硫的脱除。
而石膏浆液中的氧化钙(CaO)则参与到吸收和氧化二氧化硫的过程中。
第四步:石膏浆液循环经过脱硫反应后,石膏浆液中生成的硫酸钙会被收集和分离出来。
随后,石膏浆液会经过过滤、离心或其他分离技术进行固液分离,将固体颗粒(硫酸钙)分离出来,得到可以再次循环使用的石膏浆液。
分离后的固体颗粒通常被称为石膏渣,可以用于其他用途,如建材工业等。
第五步:废石膏处理在石膏法脱硫工艺中,除去硫酸钙的石膏浆液中可能还含有其他的杂质和重金属离子。
因此,废石膏需要经过处理才能符合环境保护要求。
常用的处理方法有湿法脱硫石膏综合利用和中间贮存等。
第六步:排放烟气经过脱硫处理后,烟气中的二氧化硫含量已大幅降低。
经过除尘装置的处理,烟气中的颗粒物也被有效地去除,达到了环境排放标准要求。
最后,处理后的烟气可以经过烟囱或烟气处理设施排放到大气中。
以上就是石膏法脱硫的工艺流程图,通过该工艺可以有效地去除燃煤电厂和工业锅炉烟尘中的二氧化硫,降低对环境的污染。
同时,脱硫薄膜的制备方法和脱硫薄膜的应用也在不断进步中,以提高脱硫效率和降低能耗。
石灰脱硫工艺流程图

石灰脱硫工艺流程图
石灰脱硫工艺流程图简介如下:
石灰脱硫工艺是一种常用的烟气脱硫方法,它通过注入石灰来吸收烟气中的二氧化硫。
该工艺流程通常包括石灰搅拌池、石灰浆液循环系统、氧化风机、石灰循环泵和石灰浆液喷嘴等主要设备。
首先,烟气从锅炉或工业炉中产生,并加到石灰脱硫系统中。
烟气中的二氧化硫浓度较高,需要进行脱硫处理。
石灰搅拌池是将石灰与水混合的地方。
石灰与水的比例一般为1:3。
在这个过程中,加入一定的搅拌剂以保证石灰和水充分混合。
混合后的石灰浆液将进入下一个工艺阶段。
石灰浆液循环系统是将石灰浆液从搅拌池中抽出,并通过石灰循环泵输送到烟气处理设备中。
石灰循环泵通常采用离心泵,可以实现石灰浆液的稳定输送。
氧化风机是石灰循环泵之前的设备。
它用于输送氧化风,将湿法石灰循环脱硫工艺中的SO2氧化成SO3。
SO3与石灰浆液中的碱性成分(如Ca(OH)2)反应生成硫酸和水。
石灰浆液喷嘴是将石灰浆液喷洒到烟气中的设备。
石灰浆液喷嘴通常安装在喷洒器上,喷洒器根据烟气流量和SO2浓度的变化来调整喷洒量,以获得较高的脱硫效率。
在石灰浆液喷嘴的作用下,石灰浆液与烟气中的SO2发生反应,SO2被吸收并转化为硫酸盐。
当石灰浆液中的石灰浓度降低时,石灰循环泵将石灰浆液重新送回到石灰搅拌池,继续循环使用。
最后,经过脱硫处理后的烟气中的SO2浓度大大降低,达到环境排放标准。
石灰脱硫工艺广泛应用于电力站、钢铁厂、化工厂等工业领域,以实现二氧化硫的减排和环境保护。
石灰石-石膏湿法脱硫技术的工艺流程、反应原理及主要系统
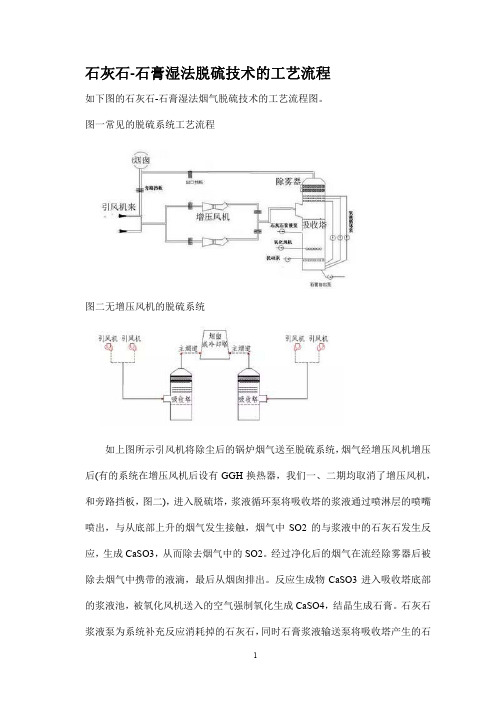
石灰石-石膏湿法脱硫技术的工艺流程如下图的石灰石-石膏湿法烟气脱硫技术的工艺流程图。
图一常见的脱硫系统工艺流程图二无增压风机的脱硫系统如上图所示引风机将除尘后的锅炉烟气送至脱硫系统,烟气经增压风机增压后(有的系统在增压风机后设有GGH换热器,我们一、二期均取消了增压风机,和旁路挡板,图二),进入脱硫塔,浆液循环泵将吸收塔的浆液通过喷淋层的喷嘴喷出,与从底部上升的烟气发生接触,烟气中SO2的与浆液中的石灰石发生反应,生成CaSO3,从而除去烟气中的SO2。
经过净化后的烟气在流经除雾器后被除去烟气中携带的液滴,最后从烟囱排出。
反应生成物CaSO3进入吸收塔底部的浆液池,被氧化风机送入的空气强制氧化生成CaSO4,结晶生成石膏。
石灰石浆液泵为系统补充反应消耗掉的石灰石,同时石膏浆液输送泵将吸收塔产生的石膏外排至石膏脱水系统将石膏脱水或直接抛弃。
同时为了防止吸收塔内浆液沉淀在底部设有浆液搅拌系统,一期采用扰动泵,二期采用搅拌器。
石灰石-石膏湿法脱硫反应原理在烟气脱硫过程中,物理反应和化学反应的过程相对复杂,吸收塔由吸收区、氧化区和结晶区三部分组成,在吸收塔浆池(氧化区和结晶区组成)和吸收区,不同的层存在不同的边界条件,现将最重要的物理和化学过程原理描述如下:(1)SO2溶于液体在吸收区,烟气和液体强烈接触,传质在接触面发生,烟气中的SO2溶解并转化成亚硫酸。
SO2+H2O<===>H2SO3除了SO2外烟气中的其他酸性成份,如HCL和HF也被喷入烟气中的浆液脱除。
装置脱硫效率受如下因素影响,烟气与液体接触程度,液气比、雾滴大小、SO2含量、PH值、在吸收区的相对速度和接触时间。
(2)酸的离解当SO2溶解时,产生亚硫酸,同时根据PH值离解:H2SO3<===>H++HSO3-对低pH值HSO3-<===>H++SO32-对高pH值从烟气中洗涤下来的HCL和HF,也同时离解:HCl<===>H++Cl-F<===>H++F-根据上面反应,在离解过程中,H+离子成为游离态,导致PH值降低。
各种烟气脱硫工艺介绍及其工艺流程图汇总

各种脱硫工艺介绍及其流程图汇总脱硫技术简介通过对国内外脱硫技术以及国内电力行业引进脱硫工艺试点厂情况的分析研究,目前脱硫方法一般可划分为燃烧前脱硫、燃烧中脱硫和燃烧后脱硫等3类。
其中燃烧后脱硫,又称烟气脱硫(Flue gas desulfurization,简称FGD),在FGD技术中,按脱硫剂的种类划分,可分为以下五种方法:以CaCO3(石灰石)为基础的钙法,以MgO为基础的镁法,以Na2SO3为基础的钠法,以NH3为基础的氨法,以有机碱为基础的有机碱法。
世界上普遍使用的商业化技术是钙法,所占比例在90%以上。
按吸收剂及脱硫产物在脱硫过程中的干湿状态又可将脱硫技术分为湿法、干法和半干(半湿)法。
湿法FGD技术是用含有吸收剂的溶液或浆液在湿状态下脱硫和处理脱硫产物,该法具有脱硫反应速度快、设备简单、脱硫效率高等优点,但普遍存在腐蚀严重、运行维护费用高及易造成二次污染等问题。
干法FGD技术的脱硫吸收和产物处理均在干状态下进行,该法具有无污水废酸排出、设备腐蚀程度较轻,烟气在净化过程中无明显降温、净化后烟温高、利于烟囱排气扩散、二次污染少等优点,但存在脱硫效率低,反应速度较慢、设备庞大等问题。
半干法FGD技术是指脱硫剂在干燥状态下脱硫、在湿状态下再生(如水洗活性炭再生流程),或者在湿状态下脱硫、在干状态下处理脱硫产物(如喷雾干燥法)的烟气脱硫技术。
特别是在湿状态下脱硫、在干状态下处理脱硫产物的半干法,以其既有湿法脱硫反应速度快、脱硫效率高的优点,又有干法无污水废酸排出、脱硫后产物易于处理的优势而受到人们广泛的关注。
按脱硫产物的用途,可分为抛弃法和回收法两种。
烧结烟气脱硫工艺海水脱硫技术烟气脱硫-脱硫工艺石灰石石膏湿法烟气脱硫技术氧化镁法烟气脱硫工艺典型双碱法脱硫技术石膏湿法烟气脱硫工艺流程图半干法工艺流程图脱硫脱硝除尘一体化设备半干法脱硫工艺流程带炉内煅烧的烟气循环流化床脱硫技术半干法烟气脱硫系统工艺流程图氢氧化镁浆液制备系统-镁法脱硫工艺流程Ⅳ湿法粗粉脱硫生产流程图石灰石/石灰石膏法烟气脱硫工艺1脱硫工艺流程图烟气脱硫工艺流程石灰石-石膏湿法脱硫工艺流程图循环流化床脱硫技术工艺流程图-工艺流程-双碱法脱硫系统烧结脱硫工程。
锅炉脱硫工艺

针对于大中型锅炉的湿法烟气脱硫技术,是采用德国Babcock Borsig Power公司授权的石灰石--石膏湿法烟气脱硫工艺技术,完成了多项4×500MW机组烟气脱硫工程业绩。
该技术具有以下特点:脱硫效率高节省吸附剂/能耗低性能可靠,使用方便生成稳定的商用石膏在整个工程期间公司提供全方位的服务包括供货,安装,工程管理,现场调试和投产服务石灰石--石膏湿法烟气脱硫工艺流程图1、吸收剂槽2、吸收带3、除雾器4、氧化鼓风机5、吸附剂仓6、新配制的洗涤悬吊槽7、石膏浆旋流器站8、真空皮带过滤器9、真空泵10、废水旋流器站11、循环水槽1、石灰石-石膏法脱硫工艺(Gypsum Recovery Process)石灰石-石膏法脱硫工艺流程图工艺特点:有机酸隔离,SO2吸收率高,在烟气流量及SO2容量变化范围大的情况下也能稳定运行;能够在低PH值(4-5)条件下吸收,在吸收塔里很易氧化,所以不要强制的氧化槽也不要强制的氧化硫酸,吸收剂利用率高;制造商业用石膏(用于石膏、木板、水泥等)2、放流法脱硫工艺(MgSO4 Purge Process)放流法脱硫工艺流程图工艺特点:SO2吸收率高;操作适应性高;吸收塔压力损失小;避免结垢系统;运转低成本;使排放的废水量达到最小。
3、半干法脱硫工艺(Semi-dry Process)半干法脱硫工艺流程图工艺特点:运转低成本;无废液产生;操作及维护简便;无须白烟气防止系统。
4、干法脱硫工艺(Dry Process)5、芒硝法脱硫工艺(Na2SO4 Recovery System)干法脱硫工艺流程图工艺特点:运转低成本;无废液产生;操作及维护简便;无须白烟气防止系统。
芒硝法脱硫工艺流程图工艺特点:SO2吸收率高;制成高纯度芒硝;结晶器采用了MVR系统,所以能量消耗低;结晶器避免结垢故障。
6、亚硫酸钠法脱硫工艺(Na2SO3 Recovery System)亚硫酸钠法脱硫工艺流程图工艺特点:SO2吸收率高;运转低成本;操作适应性高;吸收塔压力损失小;通过增加结晶系统可得到Na2SO4结晶。
《双碱法脱硫工艺图》

常见的十七种脱硫工艺原理及工艺图
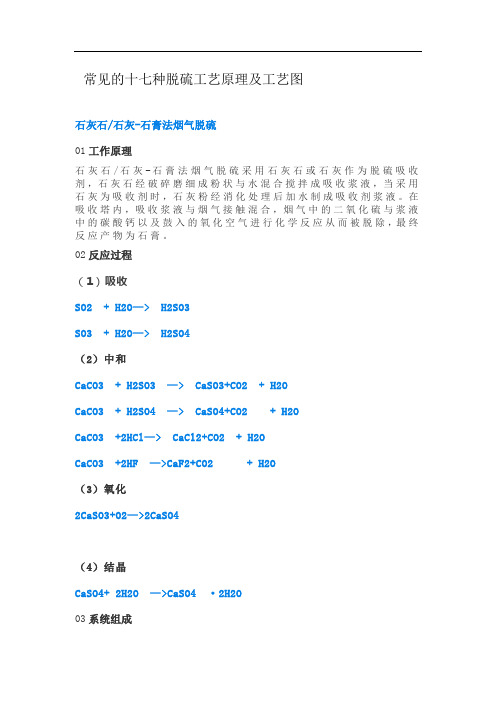
常见的十七种脱硫工艺原理及工艺图石灰石/石灰-石膏法烟气脱硫01工作原理石灰石/石灰-石膏法烟气脱硫采用石灰石或石灰作为脱硫吸收剂,石灰石经破碎磨细成粉状与水混合搅拌成吸收浆液,当采用石灰为吸收剂时,石灰粉经消化处理后加水制成吸收剂浆液。
在吸收塔内,吸收浆液与烟气接触混合,烟气中的二氧化硫与浆液中的碳酸钙以及鼓入的氧化空气进行化学反应从而被脱除,最终反应产物为石膏。
02反应过程(1)吸收SO2 + H2O—> H2SO3SO3 + H2O—> H2SO4(2)中和CaCO3 + H2SO3 —> CaSO3+CO2 + H2OCaCO3 + H2SO4 —> CaSO4+CO2 + H2OCaCO3 +2HCl—> CaCl2+CO2 + H2OCaCO3 +2HF —>CaF2+CO2 + H2O(3)氧化2CaSO3+O2—>2CaSO4(4)结晶CaSO4+ 2H2O —>CaSO4 ·2H2O03系统组成脱硫系统主要由烟气系统、吸收氧化系统、石灰石/石灰浆液制备系统、副产品处理系统、废水处理系统、公用系统(工艺水、压缩空气、事故浆液罐系统等)、电气控制系统等几部分组成。
04工艺流程锅炉/窑炉—>除尘器—>引风机—>吸收塔—>烟囱来自于锅炉或窑炉的烟气经过除尘后在引风机作用下进入吸收塔,吸收塔为逆流喷淋空塔结构,集吸收、氧化功能于一体,上部为吸收区,下部为氧化区,经过除尘后的烟气与吸收塔内的循环浆液逆向接触。
系统一般装3-5台浆液循环泵,每台循环泵对应一层雾化喷淋层。
当只有一台机组运行时或负荷较小时,可以停运1-2层喷淋层,此时系统仍保持较高的液气比,从而可达到所需的脱硫效果。
吸收区上部装二级除雾器,除雾器出口烟气中的游离水份不超过75mg/N m3。
吸收SO2后的浆液进入循环氧化区,在循环氧化区中,亚硫酸钙被鼓入的空气氧化成石膏晶体。
脱硫工段工艺流程图

脱硫工段工艺流程图
脱硫工段是热电厂燃煤发电过程中的重要环节,其主要目的是减少燃煤产生的二氧化硫排放,保护环境。
下面我将详细介绍脱硫工段的工艺流程图。
首先,燃煤进入燃烧室,与空气进行充分的燃烧反应,产生大量的烟尘和废气。
废气中含有二氧化硫,需要进行脱硫处理。
第一步是氧化反应。
废气经过预处理后,进入净化塔顶部分布的喷头区域,与一定比例的含氧气体进行接触。
氧化剂主要有空气和二氧化氯等,能够将二氧化硫氧化为二氧化硫酸。
第二步是吸收反应。
氧化后的废气经过喷头区域,进入喷雾层。
在喷雾层中,废气与喷雾液体进行接触,喷雾液体是一种含有吸收剂的溶液,一般为石灰石浆液。
在此过程中,二氧化硫与液滴中的吸收剂发生吸收反应,生成硫酸。
第三步是分离反应。
经过吸收的废气与喷头层中的液滴一起下沉,进入喷雾塔的下部,此处设有分离装置。
在分离过程中,废气和液滴发生反向冲刷,液滴中的硫酸被回收下来,而废气中的烟尘和其它颗粒物被截留,净化后的废气从塔顶排放。
第四步是脱水处理。
分离后的液滴中含有大量水分,需要进行脱水处理。
液滴进入脱水装置,通过旋流器等装置将水分与液滴分离,脱水后的液滴进入再生系统。
最后,通过再生系统,将脱水后的液滴进行再利用。
具体的再
生方式受到多种因素的影响,一般采用高温回归的方法,将液滴中的硫酸分解为二氧化硫和水,再经过氧化反应转化为硫酸,用于循环再利用。
以上就是脱硫工段的工艺流程图。
通过该流程,热电厂能够有效地减少燃煤产生的二氧化硫排放,保护环境,同时实现废气中的硫酸回收和再利用。
HPF脱硫工艺流程图
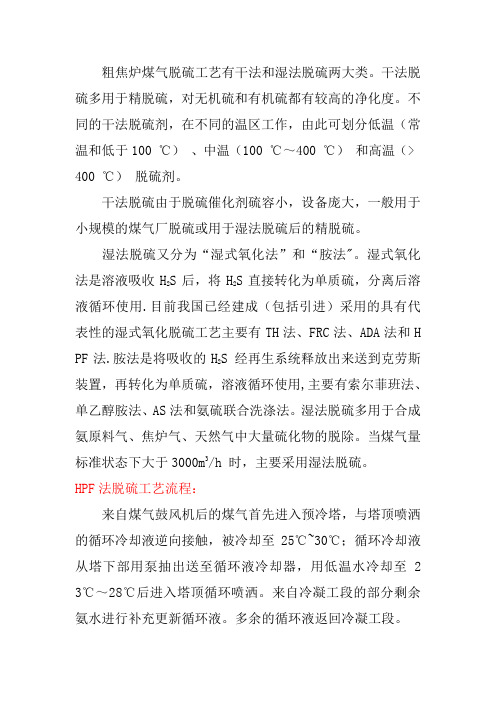
粗焦炉煤气脱硫工艺有干法和湿法脱硫两大类。
干法脱硫多用于精脱硫,对无机硫和有机硫都有较高的净化度。
不同的干法脱硫剂,在不同的温区工作,由此可划分低温(常温和低于100 ℃)、中温(100 ℃~400 ℃)和高温(> 400 ℃)脱硫剂。
干法脱硫由于脱硫催化剂硫容小,设备庞大,一般用于小规模的煤气厂脱硫或用于湿法脱硫后的精脱硫。
湿法脱硫又分为“湿式氧化法”和“胺法"。
湿式氧化法是溶液吸收H2S后,将H2S直接转化为单质硫,分离后溶液循环使用.目前我国已经建成(包括引进)采用的具有代表性的湿式氧化脱硫工艺主要有TH法、FRC法、ADA法和H PF法.胺法是将吸收的H2S 经再生系统释放出来送到克劳斯装置,再转化为单质硫,溶液循环使用,主要有索尔菲班法、单乙醇胺法、AS法和氨硫联合洗涤法。
湿法脱硫多用于合成氨原料气、焦炉气、天然气中大量硫化物的脱除。
当煤气量标准状态下大于3000m3/h 时,主要采用湿法脱硫。
HPF法脱硫工艺流程:来自煤气鼓风机后的煤气首先进入预冷塔,与塔顶喷洒的循环冷却液逆向接触,被冷却至25℃~30℃;循环冷却液从塔下部用泵抽出送至循环液冷却器,用低温水冷却至2 3℃~28℃后进入塔顶循环喷洒。
来自冷凝工段的部分剩余氨水进行补充更新循环液。
多余的循环液返回冷凝工段。
预冷塔后煤气并联进入脱硫塔A、脱硫塔B,与塔顶喷淋下来的脱硫液逆流接触,以吸收煤气中的硫化氢(同时吸收煤气中的氨,以补充脱硫液中的碱源)。
脱硫后煤气进入下道工序进行脱氨脱苯.脱硫基本反应如下:H2S+NH4OH→NH4HS+H2O 2NH4OH+H2S→(NH4)2S+2H2O NH4OH+HCN→NH4CN+H2O NH4OH+CO2→NH4HCO3NH4OH+NH4HCO3→(NH4)2CO3+ H2O吸收了H2S、HCN的脱硫液从脱硫塔A、B下部自流至反应槽,然后用脱硫液循环泵抽送进入再生塔再生.来自空压机站压缩空气与脱硫富液由再生塔下部并流进入再生塔A、B,对脱硫液进行氧化再生,再生后的溶液从塔顶经液位调节器自流回脱硫塔循环使用.再生塔内的基本反应如下:NH4HS+1/2O2→NH4OH+S (NH4)2S+1/2O2+ H2O→ 2NH4OH+S(NH4)2Sx+1/2O2+ H2O→2NH4OH+Sx除上述反应外,还进行以下副反应:2NH4HS+2O2→(NH4)2S2O3+ H2O 2(NH4)2S2O3+O2→2(NH4)2SO4+2S从再生塔A、B顶部浮选出的硫泡沫,自流入硫泡沫槽,在此经搅拌,沉降分离,排出清液返回反应槽,硫泡沫经泡沫泵加压后送压滤机进行脱水,形成硫膏成品。
脱硫技术流程图

电厂脱硫除尘技术研讨会专题七Vattenfall Europe Generation电厂湿法脱硫工艺经验POWERCONSULT07 / 2003 Nass-REA-Verfahren 2内容1. VE-G电厂脱硫设备的介绍2. 系统与工艺3. 运转经验4. 工艺开发07 / 2003 Nass-REA-Verfahren 3新建烟气脱硫设备的工艺原理机械房、蒸气搂、电除尘脱硫装置、冷却塔、燃料坑、LUVO、引风机楼、冷却水泵房,电开关房07 / 2003 Nass-REA-Verfahren 4脱硫装置介绍07 / 2003 Nass-REA-Verfahren 5地点Jänschwalde Boxberg III Boxberg IV Schwarze Pumpe Lippendorf总负荷MW 3000 (6 x 500) 1000 (2 x 500) 900 1600 (2 x 800) 1800 (2 x 900) 冷却塔的数目12 4 2 4 4烟气体积m³/h (i.N.,f.)1,5 x 106 1,5 x 106 1,8 x 106 1,8 x 106 1,75 x 106SO2 进气峰值.mg/m³, i.N.tr. 6 % O2 平均值770044007450410072503935100008100SO2 净化后气峰值.mg/m³, i.N.tr. 6 % O2400 400 400 400脱硫率> 95 % > 95 % > 95 % > 95 %石灰石的需求t/a 700 000 210 00 150 000 290 000 300 000 (Branntk.)产生的石膏量t/a(湿石膏)1.300 000 400 000 285 000 550 000 1.020 000反应塔设备提供商NOELL-KRC L&C Steinmüller NOELL-KRC NOELL-KRC Bischoff反应塔工艺双循环单循环双循环双循环Einkreis塔径大小∅m吸收塔高度m16,5045,70吸气坑23,00吸气塔15,5044,5018,004,7518,0044,7516,0042,50开始运转时间KW/REAs 1981-89/195-96 1978-80/1995 2000 1997-98 1999-200007 / 2003 Nass-REA-Verfahren 5脱硫装置的介绍脱硫装置改建与新建的原理:- 全金属的洗涤塔- 避免烟气旁路- GfK(玻璃纤维增强型塑料)导管将烟气导入冷却塔07 / 2003 Nass-REA-Verfahren 6VE-G方案选择• 脱硫湿法工艺-高的脱硫率> 95 %-大烟气流-副产品的利用价值• 材料的选择采用不锈钢代替橡胶(Nickel-Basis-Legierungen)-较高的使用率-取消旁路/并轨开关-费用(针对使用年限与采用新橡胶做经济对比) • 烟气通过冷却塔的排放(GfK)-不需要通过烟囱的重新加热-没有腐蚀的问题07 / 2003 Nass-REA-Verfahren 7VE-G的方案选择• 吸收材料的选择与准备(与地理位置运转费用运输费用相关)- 石灰石粉- 石灰石块- 生石灰• 污水处理(与排放许可相关证的规定相关) -无水排放方案(在VE-G-褐煤电厂)-其他的污水处理设施07 / 2003 Nass-REA-Verfahren 83000 MW生产能力的电厂的供应与生产平衡/日值07 / 2003 Nass-REA-Verfahren 9远程供热/ 8.300 MWh therm./天60.000 住户电能/ 72.000 MWh/天6.850.000 住户石膏/ 4.100 t/天75 车皮灰/ 7.800 t/天195 车皮/天水/ 140.000 m3/天以气体形式释放给水/ 182.000 m3/天湿物/ 2.100 m3/天湿的灰份与湿石膏________________石灰石2.300 t/天43 车皮/天水260.000 m3/天煤82.000 t/天1.400 车皮/天07 / 2003 Nass-REA-Verfahren 9(KRC-湿法)烟气脱硫工艺流程图07 / 2003 N_ss-REA-Verf_hren 10干净气体水石灰吸收池吸收塔空气烟气石膏过滤器水旋风除尘过滤液用来湿润灰分Jänschw_lde电厂反应器NOELL-KRC-石灰石-双循环-湿法脱硫12 蒸气锅炉/12个吸收系统(单循环)反应塔: 每踏烟气1.420.000 Nm3/h i.F.m_x. SO2 进气7.700 mg/Nm3tr. bez.6%O2zul.净化后含SOx <5%, m_x.400 mg/Nm3tr. bez.6%O2 07 / 2003 N_ss-REA-Verf_hren 10系统与工艺脱硫装置反应原理有以下几点:- 石灰石的准备, 石膏脱水,- 成型的喷淋塔系统除了喷淋层和除雾器以外(单循环系统), - 喷淋塔带收集漏斗(中断循环), 喷淋层有或没有接触室和除雾器(双循环).07 / 2003 N_ss-REA-Verf_hren 11系统与工艺单循环与双循环净化后气生产水进气净化后气生产水吸收塔给浆池进气石膏浆空气石灰石浆石膏浆空气材料材料石灰石浆59合金涂料板/固态(c-276涂料板/固态) 07 / 2003 N_ss-REA-Verf_hren 12系统与工艺07 / 2003 N_ss-REA-Verf_hren 13单循环系统的能耗优化极限值每个吸收塔的平均能耗值SEG平均值程序化运转参数非程序化运转参数SEG平均值07 / 2003 N_ss-REA-Verf_hren 13系统与工艺07 / 2003 N_ss-REA-Verf_hren 14脱硫率与能耗优化12341997 1998 1999 1H_lbj_hr 2000[%]10203040[t/GWh]Schw efelemissionsgr_d % elektr. Eigenbed_rf REA % K_lkverbr_uch spezifisch脱硫率% 电除尘的能耗%石灰的需要量07 / 2003 N_ss-REA-Verf_hren 14。