涡扇发动机叶片高效切削基础研究
航空发动机精锻叶片数字化数控加工技术
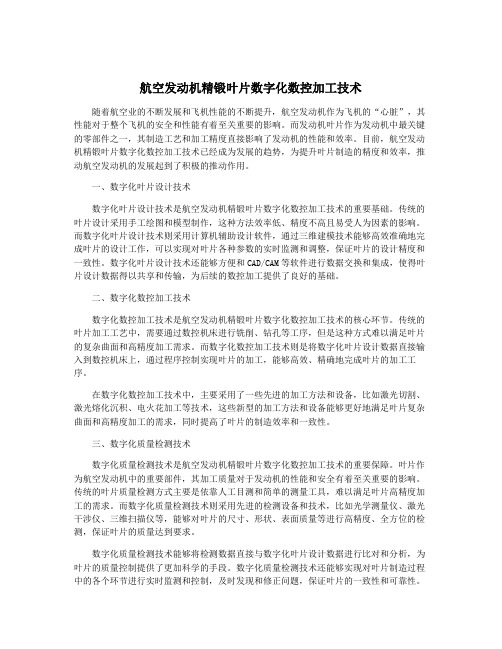
航空发动机精锻叶片数字化数控加工技术随着航空业的不断发展和飞机性能的不断提升,航空发动机作为飞机的“心脏”,其性能对于整个飞机的安全和性能有着至关重要的影响。
而发动机叶片作为发动机中最关键的零部件之一,其制造工艺和加工精度直接影响了发动机的性能和效率。
目前,航空发动机精锻叶片数字化数控加工技术已经成为发展的趋势,为提升叶片制造的精度和效率,推动航空发动机的发展起到了积极的推动作用。
一、数字化叶片设计技术数字化叶片设计技术是航空发动机精锻叶片数字化数控加工技术的重要基础。
传统的叶片设计采用手工绘图和模型制作,这种方法效率低、精度不高且易受人为因素的影响。
而数字化叶片设计技术则采用计算机辅助设计软件,通过三维建模技术能够高效准确地完成叶片的设计工作,可以实现对叶片各种参数的实时监测和调整,保证叶片的设计精度和一致性。
数字化叶片设计技术还能够方便和CAD/CAM等软件进行数据交换和集成,使得叶片设计数据得以共享和传输,为后续的数控加工提供了良好的基础。
二、数字化数控加工技术数字化数控加工技术是航空发动机精锻叶片数字化数控加工技术的核心环节。
传统的叶片加工工艺中,需要通过数控机床进行铣削、钻孔等工序,但是这种方式难以满足叶片的复杂曲面和高精度加工需求。
而数字化数控加工技术则是将数字化叶片设计数据直接输入到数控机床上,通过程序控制实现叶片的加工,能够高效、精确地完成叶片的加工工序。
在数字化数控加工技术中,主要采用了一些先进的加工方法和设备,比如激光切割、激光熔化沉积、电火花加工等技术,这些新型的加工方法和设备能够更好地满足叶片复杂曲面和高精度加工的需求,同时提高了叶片的制造效率和一致性。
三、数字化质量检测技术数字化质量检测技术是航空发动机精锻叶片数字化数控加工技术的重要保障。
叶片作为航空发动机中的重要部件,其加工质量对于发动机的性能和安全有着至关重要的影响。
传统的叶片质量检测方式主要是依靠人工目测和简单的测量工具,难以满足叶片高精度加工的需求。
航空发动机叶片高效切削技术研究
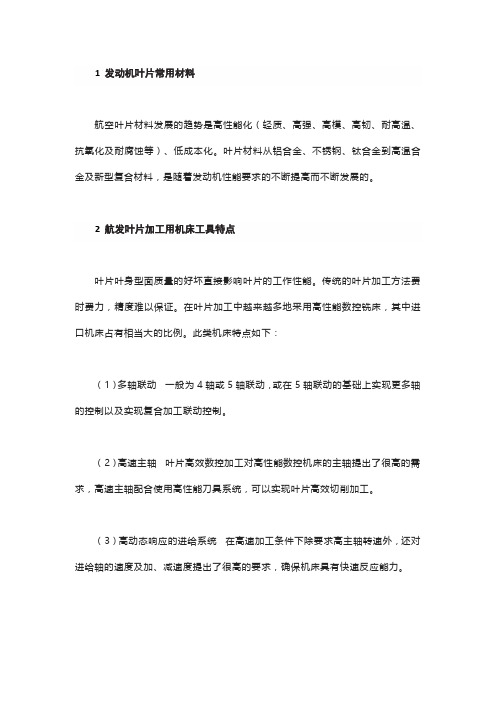
1 发动机叶片常用材料航空叶片材料发展的趋势是高性能化(轻质、高强、高模、高韧、耐高温、抗氧化及耐腐蚀等)、低成本化。
叶片材料从铝合金、不锈钢、钛合金到高温合金及新型复合材料,是随着发动机性能要求的不断提高而不断发展的。
2 航发叶片加工用机床工具特点叶片叶身型面质量的好坏直接影响叶片的工作性能。
传统的叶片加工方法费时费力,精度难以保证。
在叶片加工中越来越多地采用高性能数控铣床,其中进口机床占有相当大的比例。
此类机床特点如下:(1)多轴联动一般为4轴或5轴联动,或在5轴联动的基础上实现更多轴的控制以及实现复合加工联动控制。
(2)高速主轴叶片高效数控加工对高性能数控机床的主轴提出了很高的需求,高速主轴配合使用高性能刀具系统,可以实现叶片高效切削加工。
(3)高动态响应的进给系统在高速加工条件下除要求高主轴转速外,还对进给轴的速度及加、减速度提出了很高的要求,确保机床具有快速反应能力。
(4)高刚度、高精度主轴系统、进给系统和机床结构应具有良好的静态刚度和动态刚度以及热稳定性。
(5)智能化机床控制智能化和加工过程智能化。
目前,叶片加工用刀具以硬质合金刀具为主。
相对于国外企业,国产机床工具企业中高端产品在技术水平和产业化方面与国外企业还存在差距。
国内机床工具企业欲在航空航天领域有所突破,还需加强技术创新,提高产品质量稳定性,进一步完善技术服务体系,提升核心竞争力。
3 航发叶片高效切削策略航发叶片的材料、结构和工艺特点,对加工质量、效率、成本等方面提出了更高的要求。
高效切削是要在数控切削加工过程中,通过对“机床-零件-刀具-夹具”工艺系统特性、走刀路径、数控编程、切削用量等做具体分析,对刀具种类、刀具结构、夹紧方案、刀轴倾角等加工方案及切削深度、切削速度、进给量等切削参数进行全面优化,最终实现高质量、高效率、低成本及绿色数控加工。
(1)合理选择刀具高效刀具涉及刀具材料、刀具涂层技术、刀具结构设计与优化、刀具配套技术等多方面。
航空发动机叶片加工新工艺的设想

航空发动机叶片加工新工艺的设想叶片是航空发动机关键零件,它的制造量占整机制造量的三分之一左右。
航空发动机叶片属于薄壁易变形零件,如何控制其变形并高效、高质量地加工是目前叶片制造行业研究的重要课题之一。
随着数控机床的出现,叶片制造工艺发生重大变化,采用精密数控加工技术加工的叶片精度高,制造周期短,一般6-12 个月。
虽然目前我国叶片生产厂已普遍采用数控加工技术,但只限于叶片半精加工,型面留0.3-0.5mm 余量,叶片型面最终精度仍然要靠抛光保证。
1 叶片数控加工传统工艺路线叶片数控加工传统工艺是单个叶片依次加工。
在铣削加工和车削加工前必须合理设计工装,并高精度地制造出来,这样才能保证叶片的精度,工装的精度对叶片的制造精度影响很大。
在叶片铣削加工全部完成后,必须把叶片组合成一周,通过车削来完成内、外橼板的加工。
其工艺路线如图1所示。
图1 叶片数控加工传统工艺路线2 叶片加工新工艺的设想——整体叶盘加工再分割整体叶盘(Blisk—Blade Disk)是第四代战斗机配套推重比10高性能航空发动机的核心技术。
与传统的叶片和轮盘装配结构相比,整体叶盘将叶片和轮盘设计成一个整体,省去了榫头、榫槽和锁紧装置,避免了榫头气流损失、减少了结构重量和零件数量;由于整体叶盘使发动机结构大为简化,推重比可靠性进一步提高,因而在新研制的第四代战斗机所配套的高推比发动机上得到了成功应用。
但整体叶盘在制造过程中一旦某个叶片不符合质量要求,整个叶盘就成为废品,因此良品率较低;同样,发动机在使用过程中, 转子叶片常遇到外物打伤或因振动叶片出现裂纹, 整体叶盘要更换叶片非常困难, 有可能因为一个叶片损坏而报废整个整体叶盘。
因此,在目前的技术条件下,整体叶盘仍然有较大的局限性。
在这一背景下,传统的轮盘、叶片分离结构仍然有用武之地。
但利用整体叶盘这一概念,本文提出了一种加工单个叶片的新的工艺方案:叶片按整体叶盘的方式整体加工,最后再分割成单个叶片。
航空发动机涡轮叶片精密成形技术分析

航空发动机涡轮叶片精密成形技术分析1. 引言1.1 研究背景航空发动机是飞机的心脏,而航空发动机涡轮叶片作为发动机的关键部件,对发动机的性能和效率起着至关重要的作用。
随着航空业的快速发展和飞行器对性能要求的不断提高,涡轮叶片的精密成形技术也日益受到重视。
传统涡轮叶片成形技术存在着一些问题,如成形周期长、成形精度低、材料利用率低等,难以满足现代航空发动机对涡轮叶片性能的要求。
研究和探索先进的涡轮叶片精密成形技术成为当前的热点之一。
通过采用先进的数控加工技术、材料工程技术以及仿真分析技术,可以有效提高涡轮叶片的成形精度和生产效率,从而满足航空发动机对涡轮叶片的高性能要求。
在这样一个背景下,本文旨在对航空发动机涡轮叶片精密成形技术进行深入分析,探讨其作用和重要性,比较传统成形技术和先进成形技术的优缺点,展示精密成形技术在航空发动机涡轮叶片中的应用以及影响成形精度的因素。
通过研究,为航空发动机涡轮叶片的精密成形提供技术支持,并为未来的研究方向提供参考。
1.2 研究目的研究目的是通过分析航空发动机涡轮叶片精密成形技术,探讨其在航空发动机性能提升中的作用和价值。
具体包括了对传统涡轮叶片成形技术和先进涡轮叶片精密成形技术的比较分析,以及精密成形技术在航空发动机涡轮叶片制造中的应用现状和发展趋势。
研究旨在揭示精密成形技术对提高航空发动机涡轮叶片成形精度和性能的影响,以及探讨成形精度的影响因素,为提高航空发动机燃烧效率、降低燃油消耗、延长涡轮叶片使用寿命等方面提供参考和借鉴。
通过深入研究航空发动机涡轮叶片的精密成形技术,旨在促进我国航空发动机产业的发展,并为全球航空工业的进步提供技术支持和保障。
1.3 研究意义航空发动机涡轮叶片精密成形技术的研究意义是非常重要的。
航空发动机是飞机的“心脏”,涡轮叶片是航空发动机的核心部件之一,直接影响着发动机的性能和效率。
提高涡轮叶片的制造工艺和精度可以大大提升航空发动机的整体性能。
航空发动机叶片加工工艺探讨

航空发动机叶片加工工艺探讨摘要:在国家飞机装备的制造加工过程中,航空发动机是十分关键的加工部分,其加工质量至关重要。
发动机叶片的制造问题是飞机零部件制造应用领域一道已知的“瓶颈”问题。
由于发动机叶片具有重量轻、壁薄、变异性大等特征,其制造技术一直是研究的重点。
随着科学技术的进步,数字化和自动化机床的引入都极大地改进了叶片制造工艺,在加工的过程中,保障发动机叶片的质量至关重要。
如何高效稳定地制造发动机叶片依然是一个加工难点。
基于此,阐述航空发动机叶片的主要形状与特征,并对航空发动机叶片的加工工艺做出了详尽的分析具有重要意义。
关键词:航空发动机;发动机叶片加工特征;加工工艺探讨;加工检验引言航空发动机是飞行装备加工制造过程中最重要的零件,其叶片也是发动机中数量最多、工艺最复杂的一部分。
在航空发动机的基本构造中,压气机主要由整流叶片组成,数量最多。
正因如此众多性能优异的叶片,航空发动机可以进行多种用途。
航空发动机可以利用叶片的功能对空气进行挤压与扩张,并从中产生动能,从而驱动飞行器正常工作运行。
叶片作为发动机部件中的重要部分,不但数量庞大,而且造型复杂多变。
也正因为叶片加工工艺的复杂性,在叶片加工生产过程中会出现很多影响叶片品质的问题。
作为发动机叶片研究者,保证发动机叶片质量至关重要,这也是发动机叶片加工工艺的难点。
这就要求研究人员必须在实际处理过程中不断结合经验,不断增加人力与财力的投资,以此保证发动机叶片的加工质量。
一、航空发动机叶片加工的主要特征航空发动机开发中所采用的叶片加工技术,和普通发动机批量生产中所采用的叶片加工技术有较大差别[1]。
专业厂家的叶片生产周期一般为十二至十四个月。
而航空发动机开发的叶片加工周期一般为六个月至十二个月。
在飞机发动机研制过程中,叶片的制造批量往往相当小,而且通常是几个或一个的小批量生产。
在航空发动机的研制过程中,叶片技术应该尽量选择国际通用的高效率加工机床,以减少叶片的加工周期,从而降低生产成本。
某型发动机叶片的数控编程和仿真加工
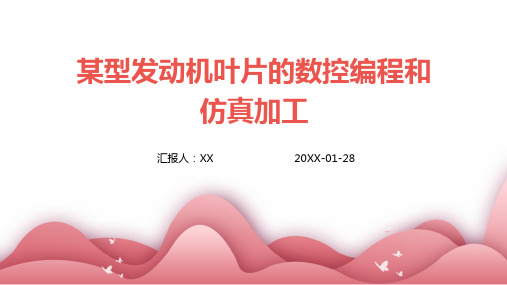
由于叶片的薄壁和复杂曲面特点,加工过程中容 易产生变形。解决方案包括优化装夹方式、采用 小切削力加工、合理安排加工顺序等。
数控编程技术
叶片的复杂曲面形状需要高精度的数控编程技术 。解决方案包括采用专业的CAM软件进行编程、 优化刀具路径、提高编程精度等。
刀具选择与管理
叶片加工需要用到多种刀具,刀具的选择和管理 对加工质量和效率有很大影响。解决方案包括选 用高性能刀具、建立刀具管理系统、定期检查和 更换刀具等。
度、进给量和切削深度等,以提高加工效率和质量。
程序仿真与调试
03
利用仿真软件对程序进行验证和调试,确保程序的正
确性和可行性,减少实际加工中的试切次数和成本。
04
仿真加工技术
仿真软件介绍
01
CATIA
02
UG NX
03
Vericut
一款广泛应用于航空航天领域的三维 CAD/CAM/CAE软件,具有强大的曲 面造型功能和高级数控编程能力,适 用于复杂发动机叶片的设计和仿真。
了加工的成功率和效率。
03
通过本项目的研究,推动了数控编程和仿真加工技术
的发展,为相关领域的技术进步做出了贡献。
未来研究方向展望
01 深入研究更加高效、智能的数控编程算法,进一 步提高发动机叶片的加工精度和效率。
02 将仿真加工技术与实际加工过程更加紧密地结合 ,实现实时仿真和加工过程的优化。
03 探索将本项目的研究成果应用于其他类似零件的 加工,拓展其应用范围和领域。
发展趋势
随着计算机技术和制造技术的不 断发展,数控编程和仿真加工技 术将越来越智能化、自动化和精 细化。
本项目研究目标
研究目标
本项目旨在研究某型发动机叶片的数控编程和仿真加工技术,实现叶片的高精度、高效 率制造。
试论航空发动机叶片数控铣削方法

试论航空发动机叶片数控铣削方法摘要:由于航空发动机叶片空间自由曲面较为复杂,且其几何精度非常高,在加上航空发动机叶片的制作材料多食铝合金或钛合金,在切削方面存在很大苦难,此外,航空发动机叶片是薄壁零件,加工时零件容易产生变形。
这些因素就导致航空发动机叶片铣削难度较大。
本文从航空发动机叶片数控技术现状出发,对数控铣削方法进行浅显的探讨。
关键词:0.引言航空发动机是飞机的核心部分,是飞机的“心脏”,对飞机性能具有决定性作用。
而航空发动机叶片则是航空发动机的最重要部件之一[1]。
由于航空发动机叶片空间自由曲面较为复杂,且其几何精度非常高,在加上航空发动机叶片的制作材料多是铝合金或钛合金,在切削方面存在很大困难,此外,航空发动机叶片是薄壁零件,加工时零件容易产生变形。
这些因素就导致航空发动机叶片铣削难度较大。
1.航空发动机叶片加工制造现状自20世纪90年代以来,美国等发达国家在对航空发动机叶片进行制造时,采用了精密的数控加工技术。
通过精密的数控加工技术的应用,使航空发动机叶片余量不需要人工去除,而且所加工出来的叶片精度高,加工的周期大幅度缩短。
相对于传统的加工制造工艺来说,数控加工技术具有很大的先进性。
随着科学技术的进步,我国的航空发动机叶片精密数控加工工艺逐步发展,但与发达国家相比,我国航空发动机叶片切削效果和制造工艺还有较大差距。
就我国的航空发动机叶片数控加工工艺来说,虽然通过大量数控加工设备的引进,使我国的叶片加工取得了一定程度的发展,但是其发展程度相对有限,多数仍局限在叶片半精加工,叶片最终制造质量仍是依赖人工抛光工艺。
目前,我国航空发动机叶片加工来看,主要存在叶片加工变形、加工效率低下、加工精度不高、叶片表面质量较低等问题,这些问题严重制约了我国航空发动机叶片制造发展。
随着数控编程软件和空间自由曲面CAD/CAM集成中,刀具轨迹生成和干涉处理成为国内外研究的热点。
在生成刀具轨迹时,要解决刀具路径拓扑问题,从而控制叶片粗糙度;要解决走刀步距问题,从而减少叶片加工的误差产生;要解决切削行距,从而使叶片残留高度得到控制。
航空发动机叶片自动化磨削加工质量分析

2024 NO.1(上) 中国新技术新产品
航空发动机叶片自动化磨削加工质量分析
孙雨婷 昂给拉玛 赵 明 吴志新 (中国航发沈阳黎明航空发动机有限责任公司,辽宁 沈阳 110000)
摘 要 :为了提升航空发动机叶片的加工质量,本文采取自动化磨削的加工方法,从仿真加工的角度分析了自
动化磨削的加工过程,对磨具和被加工叶片的接触情况和磨削工具进行了可视化展示,从理论上证实了磨削加
1 航空发动机叶片磨削加工的机械特性
航空发动机叶片的加工难点包括 2 个方面。第一个方 面,叶片的形状不规则、起伏变化大,从而导致加工过程 中余量分布极不均匀。第二个方面,叶片的选用材料一般 都比较特殊,属于刚度较低的材料,因此常规加工效果不 理想。叶片的加工经常出现削边误差、缩边误差、平头误 差和尖头误差等,如图 1 所示。
90
70
弹簧拉伸量(mm)
50
30
10 5
10
15
20
25
磨削压力(N)
图 4 磨削加工中磨削压力 - 弹簧拉伸量的关系曲线
18 静态磨削压力
动态磨削压力 14
磨削压力(N)
10
6
2 10
20
30
40
50
磨头垂直方向位移量(mm)
图 5 磨头垂直方向上位移量 - 磨削压力的关系曲线
- 29 -
- 27 -
中国新技术新产品 2024 NO.1(上)
高新技术
运用砂带执行磨削加工的效果包括 2 个方面。第一
是达到切除余量、塑造叶片形状的效果。第二是一边加工
一边降低叶片表面粗糙度并提升叶片表面质量。磨削加工
中,叶片余量被去除的模型如公式(1)所示。
航空发动机涡轮叶片精密成形技术分析
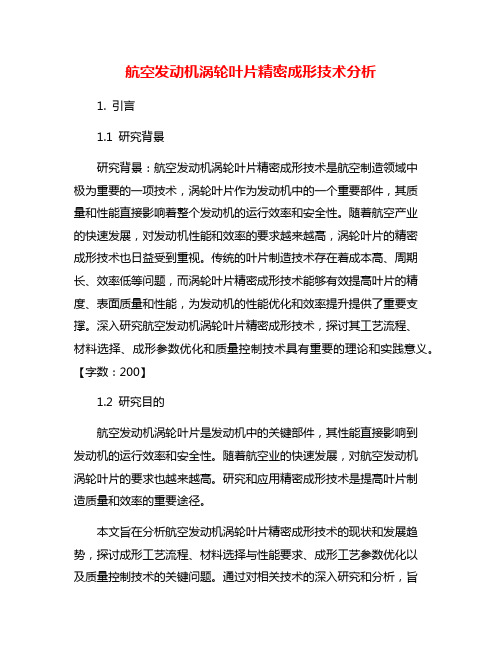
航空发动机涡轮叶片精密成形技术分析1. 引言1.1 研究背景研究背景:航空发动机涡轮叶片精密成形技术是航空制造领域中极为重要的一项技术,涡轮叶片作为发动机中的一个重要部件,其质量和性能直接影响着整个发动机的运行效率和安全性。
随着航空产业的快速发展,对发动机性能和效率的要求越来越高,涡轮叶片的精密成形技术也日益受到重视。
传统的叶片制造技术存在着成本高、周期长、效率低等问题,而涡轮叶片精密成形技术能够有效提高叶片的精度、表面质量和性能,为发动机的性能优化和效率提升提供了重要支撑。
深入研究航空发动机涡轮叶片精密成形技术,探讨其工艺流程、材料选择、成形参数优化和质量控制技术具有重要的理论和实践意义。
【字数:200】1.2 研究目的航空发动机涡轮叶片是发动机中的关键部件,其性能直接影响到发动机的运行效率和安全性。
随着航空业的快速发展,对航空发动机涡轮叶片的要求也越来越高。
研究和应用精密成形技术是提高叶片制造质量和效率的重要途径。
本文旨在分析航空发动机涡轮叶片精密成形技术的现状和发展趋势,探讨成形工艺流程、材料选择与性能要求、成形工艺参数优化以及质量控制技术的关键问题。
通过对相关技术的深入研究和分析,旨在揭示精密成形技术在航空发动机涡轮叶片制造领域的重要性,并为未来的发展提供参考和借鉴。
在探讨研究目的的过程中,希望能够全面了解航空发动机涡轮叶片精密成形技术的关键问题,为提高叶片制造质量、减少生产成本和优化生产效率提供理论指导和技术支持。
通过该研究,为航空发动机涡轮叶片制造技术的进一步发展和提升质量水平提供理论基础和实践经验。
2. 正文2.1 叶片精密成形技术概述叶片精密成形技术是航空发动机制造中关键的工艺之一,它直接影响着发动机的性能和可靠性。
叶片是发动机中的重要部件,起着承受高温、高压气流的作用。
叶片的精密成形技术至关重要。
叶片精密成形技术是指利用精密模具和高精度设备对叶片进行成形加工的技术。
这种技术可以确保叶片的几何形状和表面质量达到设计要求,从而提高发动机的性能和寿命。
航空发动机叶片抗疲劳磨削加工工艺研究
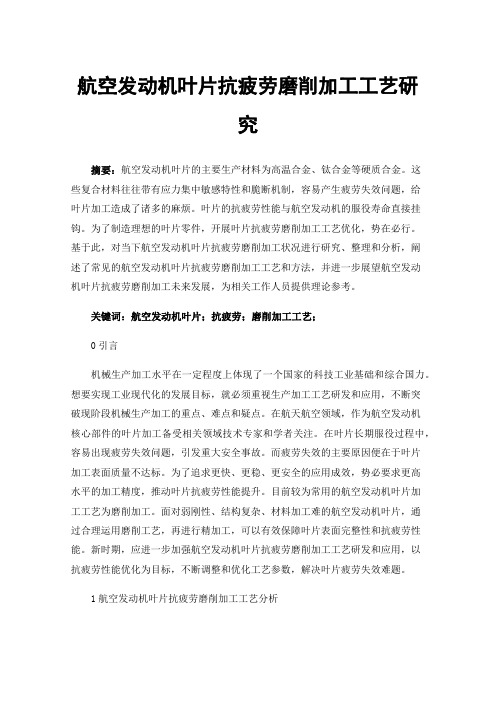
航空发动机叶片抗疲劳磨削加工工艺研究摘要:航空发动机叶片的主要生产材料为高温合金、钛合金等硬质合金。
这些复合材料往往带有应力集中敏感特性和脆断机制,容易产生疲劳失效问题,给叶片加工造成了诸多的麻烦。
叶片的抗疲劳性能与航空发动机的服役寿命直接挂钩。
为了制造理想的叶片零件,开展叶片抗疲劳磨削加工工艺优化,势在必行。
基于此,对当下航空发动机叶片抗疲劳磨削加工状况进行研究、整理和分析,阐述了常见的航空发动机叶片抗疲劳磨削加工工艺和方法,并进一步展望航空发动机叶片抗疲劳磨削加工未来发展,为相关工作人员提供理论参考。
关键词:航空发动机叶片;抗疲劳;磨削加工工艺;0引言机械生产加工水平在一定程度上体现了一个国家的科技工业基础和综合国力。
想要实现工业现代化的发展目标,就必须重视生产加工工艺研发和应用,不断突破现阶段机械生产加工的重点、难点和疑点。
在航天航空领域,作为航空发动机核心部件的叶片加工备受相关领域技术专家和学者关注。
在叶片长期服役过程中,容易出现疲劳失效问题,引发重大安全事故。
而疲劳失效的主要原因便在于叶片加工表面质量不达标。
为了追求更快、更稳、更安全的应用成效,势必要求更高水平的加工精度,推动叶片抗疲劳性能提升。
目前较为常用的航空发动机叶片加工工艺为磨削加工。
面对弱刚性、结构复杂、材料加工难的航空发动机叶片,通过合理运用磨削工艺,再进行精加工,可以有效保障叶片表面完整性和抗疲劳性能。
新时期,应进一步加强航空发动机叶片抗疲劳磨削加工工艺研发和应用,以抗疲劳性能优化为目标,不断调整和优化工艺参数,解决叶片疲劳失效难题。
1航空发动机叶片抗疲劳磨削加工工艺分析航空发动机叶片结构弱刚性,型面复杂,在加工过程中倘若加工工艺选用不恰当,就容易出现受力不均、表面烧伤等问题,严重损害叶片加工精度和表面质量。
目前较为适用的叶片磨削加工工艺为磨粒流加工技术。
区别于传统的磨削工艺,运用磨粒流加工技术,向半固体磨料介质施加模具模芯的约束和挤推压力,使半固体磨料通过叶片表面,可以高效、高质地完成复杂曲面叶片表面的去毛刺、倒圆、抛光等作业。
涡扇发动机叶片高效切削基础研究
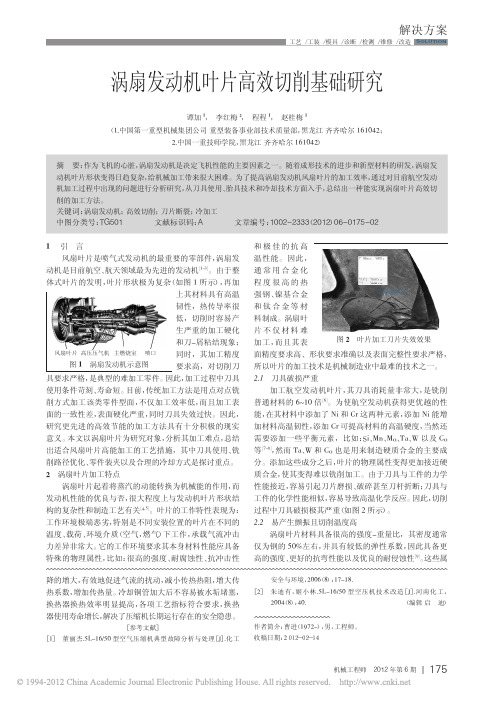
(3):141-142.
[7] 关玉璞,等.航空发动机叶片外物损伤研究现状[J].航空学报,
2007,28(4):852-853.
[8] 颜鸣皋,等.航空材料技术的发展现状与展望[J].航空制造技术,
2003(12):19-20.
[9] Xu L,et al. Research on the High-Efficiency and Energy-Saving
工作环境极端恶劣,特别是不同安装位置的叶片在不同的 2.2 易产生颤振且切削温度高
温度、载荷、环境介质(空气,燃气)下工作,承载气流冲击
涡扇叶片材料具备很高的强度-重量比,其密度通常
力差异非常大。它的工作环境要求其本身材料性能应具备 仅为钢的 50%左右,并具有较低的弹性系数,因此具备更
特殊的物理属性,比如:很高的强度、耐腐蚀性、抗冲击性 高的强度、更好的抗弯性能以及优良的耐侵蚀性[9]。这些属
换热器换热效率明显提高编辑 启 迪)
器使用寿命增长,解决了压缩机长期运行存在的安全隐患。
[参考文献]
!!!!!!!!!! 作者简介:曹进(1972-),男,工程师。
[1] 董丽杰.5L-16/50 型空气压缩机典型故障分析与处理[J].化工 收稿日期:2012- 02- 14
不合理的胎具和刀柄都会影响刀具寿命。当夹紧力不 足时,切削时工件产生位移,可能会引起刀杆和刀片的断 裂,如切削刃断裂、刀刃崩碎及刀片塑性变形等。当然,刀 片崩碎也可能是因为硬质合金太硬或切削载荷太大所致, 这时应考虑采用其它种类的刀具进行加工,以减少崩刃的 发生。而选用的刀片应能像硬质合金那样承受较高的切削 温度。因此,应当根据实际情况来选择加工刀具,在加工开 始前,设法加强夹具的刚性。这样不仅延长了刀具的使用 寿命,而且还提高了工件表面质量,减少了加工误差。 3.2 正确的装夹方式是高效切削的前提
航空发动机高压涡轮工作叶片加工工艺改进论述
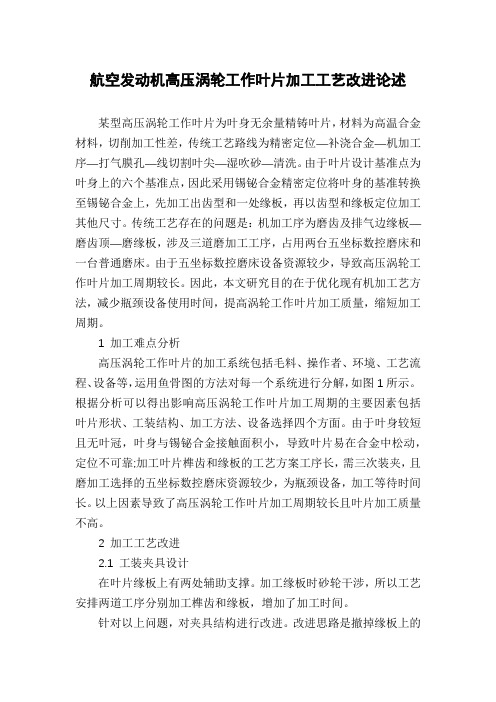
航空发动机高压涡轮工作叶片加工工艺改进论述某型高压涡轮工作叶片为叶身无余量精铸叶片,材料为高温合金材料,切削加工性差,传统工艺路线为精密定位—补浇合金—机加工序—打气膜孔—线切割叶尖—湿吹砂—清洗。
由于叶片设计基准点为叶身上的六个基准点,因此采用锡铋合金精密定位将叶身的基准转换至锡铋合金上,先加工出齿型和一处缘板,再以齿型和缘板定位加工其他尺寸。
传统工艺存在的问题是:机加工序为磨齿及排气边缘板—磨齿顶—磨缘板,涉及三道磨加工工序,占用两台五坐标数控磨床和一台普通磨床。
由于五坐标数控磨床设备资源较少,导致高压涡轮工作叶片加工周期较长。
因此,本文研究目的在于优化现有机加工艺方法,减少瓶颈设备使用时间,提高涡轮工作叶片加工质量,缩短加工周期。
1 加工难点分析高压涡轮工作叶片的加工系统包括毛料、操作者、环境、工艺流程、设备等,运用鱼骨图的方法对每一个系统进行分解,如图1所示。
根据分析可以得出影响高压涡轮工作叶片加工周期的主要因素包括叶片形状、工装结构、加工方法、设备选择四个方面。
由于叶身较短且无叶冠,叶身与锡铋合金接触面积小,导致叶片易在合金中松动,定位不可靠;加工叶片榫齿和缘板的工艺方案工序长,需三次装夹,且磨加工选择的五坐标数控磨床资源较少,为瓶颈设备,加工等待时间长。
以上因素导致了高压涡轮工作叶片加工周期较长且叶片加工质量不高。
2 加工工艺改进2.1 工装夹具设计在叶片缘板上有两处辅助支撑。
加工缘板时砂轮干涉,所以工艺安排两道工序分别加工榫齿和缘板,增加了加工时间。
针对以上问题,对夹具结构进行改进。
改进思路是撤掉缘板上的辅助支撑,在零件测量用的预留方孔增加压紧防松动机构,直接压紧至叶身,以防止叶身装夹松动。
工装改进后定位可靠,使用中未出现零件定位松动,因此补浇合金工序也不必进行。
且夹具改进后即避免了砂轮干涉又实现了榫齿、缘板、齿顶一次装夹完成,提高了加工效率。
2.2 设备选用涡轮工作叶片的工作环境为高温、高压、高转速,因此设计上一般采用强度高、耐高温的铸造高温合金材料,高温合金切削加工性很差,因此加工榫齿、缘板时采用强力緩进给磨削。
叶片切削加工技术发展浅析

叶片切削加工技术发展浅析刘随建;江剑;高见【摘要】文章介绍了切削加工设备、刀具对叶片制造技术发展的促进作用,阐述了切削加工技术在叶片制造方面能够成为主要加工手段的原因.最后,对先进切削加工技术在叶片加工中的应用前景进行了展望.【期刊名称】《金属加工:冷加工》【年(卷),期】2017(000)007【总页数】4页(P前插1,1-3)【作者】刘随建;江剑;高见【作者单位】沈阳黎明航空发动机(集团)有限责任公司辽宁 110043;沈阳黎明航空发动机(集团)有限责任公司辽宁 110043;沈阳黎明航空发动机(集团)有限责任公司辽宁 110043【正文语种】中文航空发动机叶片的种类主要分为压气机叶片和涡轮叶片两种,其中压气机叶片基本在室温和中高温环境工作,涡轮叶片在高温状态工作。
因此,从材料性质而言,压气机叶片基本是采用合金化程度较低的变形合金制造,而涡轮叶片采用合金化程度较高的铸造高温合金制造,由于两种叶片材料性质的不同,压气机叶片基本采用以铣削与车削加工为主的加工方式,涡轮叶片基本采用以磨削加工为主的加工方式。
由于叶片在结构上存在三维空间曲面的叶身型面,采用切削的轨迹方式加工效率较低,造成叶片生产常常成为发动机配套生产的瓶颈环节。
为此,叶片生产的加工手段逐步引入了特种加工方式,压气机叶片的型面加工出现了精锻、辊轧(见图1)及电解等高效加工方式,涡轮叶片目前已经全部发展为型面无余量的精密铸造方式。
因此,就切削加工的比重而言,叶片制造已经由当初基本全部依靠切削加工而转变为目前的70%~80%左右。
尽管叶片制造的切削加工比重有所下降,但是切削加工仍然是叶片加工的主体手段,其主要原因在于,切削加工的制造精度保证能力最高,最容易,最环保,具有系列化的实现形式,加工成熟度最高,技术复杂性相对较低,设备、刀具发展迅猛,不但推动了切削加工作为零件制造的主体地位,而且也随着产品发展特点,而拓宽了其应用领域,其最为有代表性发展是数控加工设备的发展,刀具材料与磨料、磨具的发展以及切削加工新技术的发展。
GH696叶片型面高效加工技术

GH696叶片型面高效加工技术摘要:针对GH696叶片切削性能差、加工过程中零件变形大、型面波纹度大、一致性差、零件抛光易烧伤等问题,制定出合理的分段加工工艺方案,通过工艺试验,选取合适的加工刀具,确定最优的铣削加工工艺参数,能够有效提高零件加工效率和质量。
关键词:GH696;分段加工;叶片型面0 引言高温合金具有优异的热强性能,热稳定性能及热疲劳性能。
现已广泛应用于航空发动机和燃气轮机。
本文通过对GH696材料性能及某型燃气轮机零级可转静叶叶身结构的研究和试验,确定出合理的数控加工方法和数控加工程序,减少零件加工中的变形量,选择适用于高温合金材料加工的刀具,提高零件的加工效率,同时降低刀具的损耗。
1零件结构及工艺难点1.1 零件结构以某型燃气轮机零级可转静叶为例,该类叶片由上轴颈、下轴颈和叶身组成。
其叶片叶型为复杂空间曲面,叶型最大厚度为4.3mm、长度为390.5 mm,最大弦宽为118.328mm,属于薄壁零件,进排气边由多段变化曲率较大的空间曲线组成,毛料为大余量模锻件,叶身余量为3mm~4.5mm之间,轴颈单边余量为2.5mm~3.5mm之间。
某型燃气轮机零级可转静叶三维模型见图1。
叶身型面是气流流经表面,位置尺寸及表面粗糙度要求很高。
装配时,由叶片上轴颈的定位扁确定叶型角向,通过调整曲柄的位置来调整气流大小和方向,叶片几何形状复杂,型面扭曲度大,叶型弦宽长,尺寸精度要求高,其主要结构尺寸和精度见表1。
表1结构尺寸和精度表最大长度/mm最大弦宽/mm缘板公差/mm轮廓度公差/mm前后缘R公差要求/mm扭转公差两端6mm内其余3 42.5111.3±0.1-0.04~0.16~-0.24Rq +0.04 -0.08 Rh+0.04 -0.08±0°12′1.2 GH696机械加工性能零件材料牌号为GH696,该材料在常温下的抗拉强度为900 MPa。
在加工时,有以下几个特点:1)高温强度高,加工硬化倾向大,切削塑性变形抗力大,切削负荷大;2)导热性差,为45钢的1/2~1/5,切削温度高,热量不易散出;3)强化元素含量高,形成金属化合物硬点,对刀具摩损强烈。