某异型威力件压制成型优化工艺参数的三次设计
超硬材料异形零件数控加工工艺改进方案

针对超硬材料异形零件结构复杂、装夹困难、材料硬度高、刀具磨损严重、传统装夹方式易产生变形以及关键特征几何精度难以保证等工艺难题,设计拉紧定位工装,解决装夹问题。
采用平面特征底齿轴向微量渐进铣削和应力释放防变形技术,有效解决切削力、夹紧力、切削热和材料应力释放等综合因素对零件加工精度造成的影响,确保了加工质量稳定可靠。
1序言随着航天技术的不断发展进步,航天产品结构也越来越复杂。
超硬材料异形零件的加工尺寸精度、表面粗糙度以及几何公差直接影响机构传动的性能指标。
由于这类零件具有结构复杂、尺寸精度高和几何公差要求严的特性,所以加工过程中零件易变形,刀具磨损严重,关键特征几何精度难以保证,其加工方法一直是困扰科研和生产的难题。
本文将详述通过设计拉紧定位工装来解决装夹问题,采用平面特征底齿轴向微量渐进铣削和应力释放防变形技术,有效解决各种因素对精度造成的影响,确保了加工质量稳定可靠。
2零件结构分析超硬材料异形零件(见图1)材料为自由锻件,精加工前经淬火处理后,硬度高达40~45HRC,属于难加工材料。
零件具有结构复杂、尺寸精度高和几何公差要求严的特性,整体为不规则异形结构,各个空间位置分布筋、槽、孔、阶台、圆弧和角度特征,其关键控制部分槽底相对于基准孔距尺寸为103mm,零件总长为127mm,最薄筋厚度为10mm。
各方向结构特征相对于基准孔和基准轴线的尺寸精度和几何公差具有严格的要求。
热处理后零件变形较大,零件孔与槽之间、孔与面之间以及面与面之间的几何精度要求极严。
3加工难点分析零件目前是在五轴机床上采用通用夹具(平口钳)装夹其平整部位两侧(零件夹持部位底部留夹持余量),采用圆柱铣刀径向切削模式加工。
由于受切削力、夹紧力、切削热和材料应力释放等综合因素影响,因而加工质量难以保证。
分析该零件的加工难点,有以下几方面。
1)零件装夹过程中,工件被夹持部位需要平口钳夹紧力作用进行定位,各空间位置特征相对于基准要素保持相对平衡状态,零件在装夹后产生微小变形的情况下,完成切削加工并达到精度要求。
三次设计
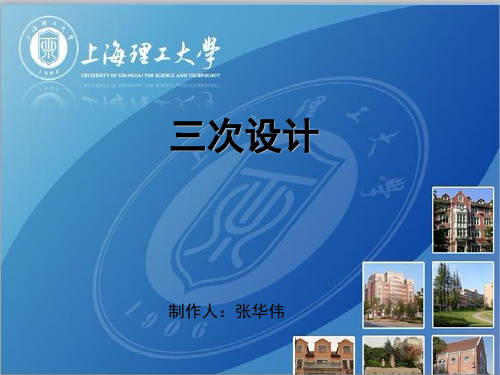
水平
c)
水平
1
2
3
d)
水平
面向质量的设计—参数设计
参数设计案例
平均牵引力
21.0 20.0 19.0 18.0 1 2 3
平均牵引力
21.0 20.0 19.0 18.0
a) 平均牵引力
21.0 20.0 19.0 18.0 1 2 3
水平 平均牵引力
21.0 20.0 19.0 18.0
1
2
3
b)
主导思想不同 传统设计方式是被动应付式的,只有当产品的 问题暴露出来后才着手解决。而三次设计方式 则通过采取各种手段,把可能出现的问题消灭 在“萌芽”状态,从根本上提高了产品的质量 和可靠性。 产生的经济效益和社会效益不同
参数设计
在产品质量的形成过程中,由于受到很多 因素(如人员、机器、材料、方法、环境 等)的影响而发生波动,在设计过程中就 需要考虑这些因素的影响,并尽量减小其 影响,使产品的质量特性对这些因素的变 化不敏感,即提高产品质量特性的健壮性 。 参数设计从设计质量工程的角度保证产品 的质量性能,同时提高产品质量对外界干 扰的抵抗力,使得所设计的产品(或工艺 )无论在制造和使用中当结构参数产生偏 差,或是在规定寿命内结构发生老化和变 质时都能保持产品性能稳定。
面向质量的设计—容差设计
容差设计 质量波动损失 异常波动损失,质量特性值的波动超出容差范 围而造成不合格品流入市场或报废给用户和社 会带来的损失。 正常波动损失,质量特性值的波动未超出容差 范围生产出合格品出厂供应市场给用户和社会 带来的损失
质,产品不满足规范要求会造 成损失,产品满足规范要求也会造成损失,只有 当产品质量特性严格处在目标值时的产品损失为 零。 随产品质量特性偏离,损失呈二次函数增长。
三次设计法
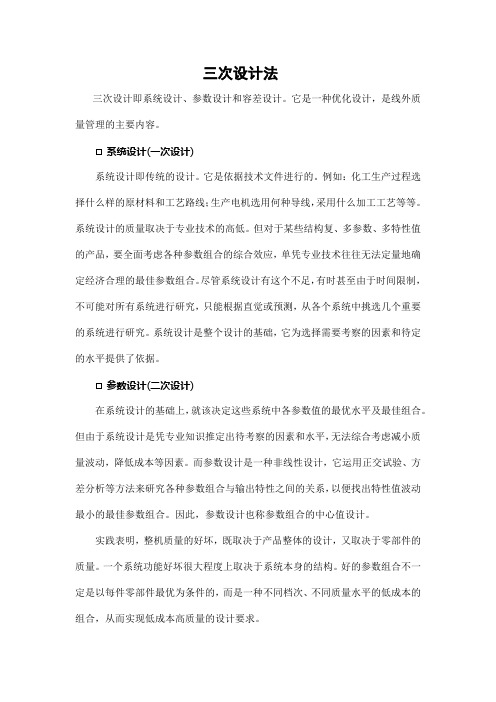
三次设计法三次设计即系统设计、参数设计和容差设计。
它是一种优化设计,是线外质量管理的主要内容。
□系统设计(一次设计)系统设计即传统的设计。
它是依据技术文件进行的。
例如:化工生产过程选择什么样的原材料和工艺路线;生产电机选用何种导线,采用什么加工工艺等等。
系统设计的质量取决于专业技术的高低。
但对于某些结构复、多参数、多特性值的产品,要全面考虑各种参数组合的综合效应,单凭专业技术往往无法定量地确定经济合理的最佳参数组合。
尽管系统设计有这个不足,有时甚至由于时间限制,不可能对所有系统进行研究,只能根据直觉或预测,从各个系统中挑选几个重要的系统进行研究。
系统设计是整个设计的基础,它为选择需要考察的因素和待定的水平提供了依据。
□参数设计(二次设计)在系统设计的基础上,就该决定这些系统中各参数值的最优水平及最佳组合。
但由于系统设计是凭专业知识推定出待考察的因素和水平,无法综合考虑减小质量波动,降低成本等因素。
而参数设计是一种非线性设计,它运用正交试验、方差分析等方法来研究各种参数组合与输出特性之间的关系,以便找出特性值波动最小的最佳参数组合。
因此,参数设计也称参数组合的中心值设计。
实践表明,整机质量的好坏,既取决于产品整体的设计,又取决于零部件的质量。
一个系统功能好坏很大程度上取决于系统本身的结构。
好的参数组合不一定是以每件零部件最优为条件的,而是一种不同档次、不同质量水平的低成本的组合,从而实现低成本高质量的设计要求。
产品设计中的波动情况是复杂的,很多产品的输出特性与因素组合之间并不是线性关系。
例如:某特性值y与因素组合(或各种零件参数组合)为X的产品之间存在着非线性关系。
当因素组合处于X1时,因素波动为△X1;输出特性为Y1,输出特性的波动幅度为△Y1。
如果通过正交试验找到参数组合X2,输出特性为Y2当因素波动△X2与△X1相同时,输出特性的波动△Y2△Y1。
可见选择合理的因素组合可以减小输出功能的波动幅度。
三次设计
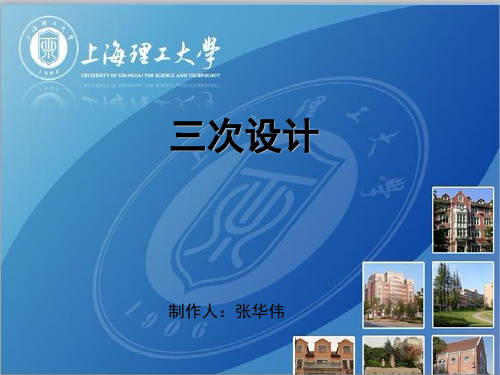
1 S Ve S / N 10Lg [ ( m )] n Ve
2
Ve [ yi ( yi ) 2 / n] /(n 1)
望小特性的信噪比计算式
1 2 S / N 10Lg[ ( y i )] n
望大特性的信噪比计算式
1 2 S / N 10Lg[ ( y i )] n
面向质量的设计—容差设计
质量损失函数
当质量特性目标值为某一确定值时
L K y T
2
当质量特性目标值不是确定值,而是越大越好
1 L K y2
当质量特性是越小越好
L Ky 2
质量损失函数
一、成本相同的假定 组装某种电源电路,需要一些原材料(如焊接材料等)、元器 件。譬如需要某种型号的三级品电阻,质量仍有好坏。按质论价,价 值应该不同。但通常买进的价格是样的。利用这些原材料、元器 件,加工成电源电路,每部的加工费(管理费、工资、能源的损耗、 机器与厂房的磨损折旧、参观招待费等等)也不尽相同。因此,仔细 追究起来,每部电源电路的成本是不全相同的。 我们近似地假定它们的成本是相同的,是用了平均成本去作 为每一部电源电路的成本。 平均成本=(6000部的材料费+6000部的加工费)/6000 =(233000+7000)/6000=40元/部 损失函数=质量损失函数+成本损失函数。 既然成本被假定为相同,故总损失大小取决于质量损失函数 的高低。
产品设计活动的分配
产品研制过程的工作量分配
三次设计理论和传统设计的区别
在工程更改的次数和分布上有明显差别 传统设计在产品研制后期有大量的工程更改。 按三次设计方式,大部分工程更改都出现在产 品研制早期,而且在图样上进行,从而大大降 低了成本,缩短了研制周期。
超硬材料异形零件的数控加工改进研究

超硬材料异形零件的数控加工改进研究发布时间:2022-11-02T09:12:28.726Z 来源:《科学与技术》2022年7月13期作者:汤业超[导读] 超硬材料异形零件的特点为结构复杂、尺寸精度高、几何公差要求严、硬度高等汤业超中航西安飞机工业集团股份有限公司陕西省西安市 710089摘要:超硬材料异形零件的特点为结构复杂、尺寸精度高、几何公差要求严、硬度高等,采用传统方式进行加工易出现零件变形、刀具严重磨损等问题。
因此,相关工作人员需将超硬材料异形零件的数控加工改进重视起来,基于实际情况解决当前存在的问题,提高超硬材料异形零件加工质量。
鉴于其涉及较多内容,所以本文就超硬材料异形零件的数控加工改进进行研究,旨在提高加工效率及质量,为相关行业的发展奠定良好基础。
关键词:超硬材料;异形零件;数控加工;改进策略1.超硬材料异形零件结构分析超硬材料异形零件为自由锻件。
由于其硬度可高达40HRC~45HRC,且其结构复压、尺寸精度高、几何公差要求严,所以隶属于难加工材料。
以下图超硬材料零件结构为例,其整体属于不规则异形结构,各空间位置分布有槽、阶台、孔、筋、圆弧等,关键控制部分槽底相对于基准孔距尺寸为103mm,总长度为127mm,最薄筋厚度为10mm。
经热处理后,零件会发生较大变形,而设计针对零件孔与槽、孔与面、面与面之间的几何精度提出了较高要求。
图1 超硬材料异形零件2.超硬材料异形零件结构的加工难点在进行超硬材料硬性零件结构加工时,需选择五轴机床,借助平口钳装夹平整部位的两侧、采用铣刀(圆柱)以径向切削的模式进行加工。
在加工过程中,很容易受零件装夹、零件材料硬度大、刀具受力、应力释放、材料去除率较高等因素的影响,导致超硬材料异形零件结构的加工质量与理想不符。
2.1零件装夹零件装夹时,需利用平口钳装夹平整部位两侧。
平口钳具有夹紧力,使得零件各空间特征处于相对平衡的状态,但零件的装夹部分会出现一定变形。
三次设计
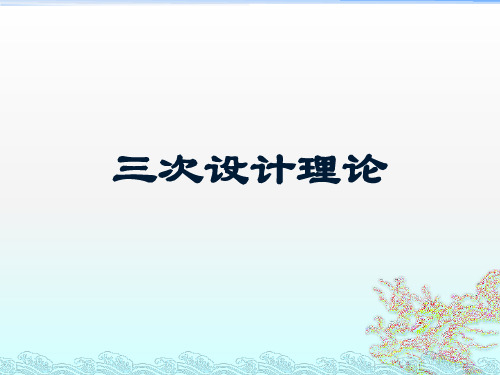
Ly K1y m2,其中K1
n件产品的平均质量损失为:
L' ' m
2!
L
Y
k
1 n
n i 1
yi
m2
kV
系数k的确定方法:
(1)功能界限0 和相应的损失A0确定k。
A0
k 0 2
k
A0 02
(2)容差 和相应的损失A确定k。
A k2 k A 2
功能界限 0与容差 之间的关系:
k
A0 02
A 2
A A0
0
例:有一彩电的电源电路,其功能是将220V交流变为110V 直流输出;彩电功能界限为0 25V (即当输出直流电为 110V±25V时,彩电丧失功能),丧失功能的损失为 A0=2000元,彩电不合格时返修费为A=20元。
所以要解决第二个问题即偏离值
m f ( A0 A, B0 B, C0 C,...) min
参数设计是在系统设计的基础上,运用正交试 验、方差分析、信噪比等方法,研究各种参数 组合与输出特性的关系,从而找出经济合理、 特性值波动最小的最佳参数组合。
参数设计的经验表明,全部采用优质元器件的产品,其质 量也未必能达到最优,即使达到优质产品,经济上也未必 合理,质量特性也未必稳定。产品质量不仅取决于元器件 的质量还取决于其参数水平的组合。
假定该稳压电源电路的输出电压目标值为m, 则参数设计需要解决的问题有以下两方面:
(1)寻找一组参数A0,B0,C0,…使得: f(A0,B0,C0,…)=m
(2)各元件都有波动 A,B,C,..., 所以
第十二章 三次设计
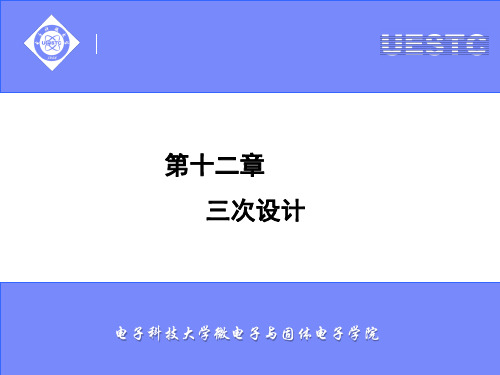
12.2 通过试验设计容差(华达呢染色)
前面讨论的试验项目,一般都是参数设计的项目。有时候,找到了 优良参数组合以后,在怎样的精度下使用这种好参数条件,就需要进行 容差设计。容差设计告诉我们:对哪些因素应严格控制和掌握?对哪些 因素可放宽限制?“严”则提高质量、效果,“宽”则降低成本简化操作。 例如,北京化工厂的“铬酸钡工艺改进”试验后,发现PH值为重 要因素,应严格控制在PH3-PH4之间才行,这样用PH试纸就不 合适了,化工厂用工业酸度计代替了试纸,实现了PH值自动控制,结果 不仅产品质量大为改进,而且提高了生产效率。 下面介绍的“华达呢染色”中的(三)是一个通过试验进行容差设 计的实例。纯毛华达呢6707色号(蓝色), 过去由于操作水平不统一, 同样的染料配方,染出的产品色差却很大。原来作试验的主要目的是 为了找出对上色号的辅料配比及方便易行的操作方法。试验后不仅达 到了目的,而且还节约了染料。
2.参数设计:系统设计之后,就是要决定系统因素的好参数组合. 在试验项目中,指的是要找到综合效果较好的生产条件。对于可计算 性项目,什么叫做好参数组合呢?它主要分成两类: 第一类是“直接择优”项目,优良的参数组合使得产品的性能指标达 到优良的状态。
第二类是:稳定性择优”项目,通过优良的参数组合,来提高产品指标 的稳定性。
表 12-4 因素
试验号
1 2 3 4 K1 K2 R
矾前沸 1 1大沸 2 小沸 1 2 180 185 5
矾后沸 2 1小沸 1 2大沸 2 185 180 5
矾前留液 3 1界限之间 2低于下限 2 1 200 165 35
评分 100 85 80 100 总和=365
四、效果
1.通过参数设计(前两批正交试验)找到了好的搭配条件,染色效果显著 提高。通过参数设计能得到好的生产条件,通过容差设计知道,如何实 现好条件。要想生产稳步上升,条件掌握该粗则粗,该细则细。 2. 用三次设计得到的好条件投产,批批对上色号。在不增加人力、物 力、财力的条件下,做到节约成本(节约染料15%),提高质量(批批对上 色号)、减少三废(减少了红矾用量,又取消了矾前放液。使染料与红矾 充分络合。减少了留入地沟的红矾),又减少了染色时间,真是一举四得。
三次设计
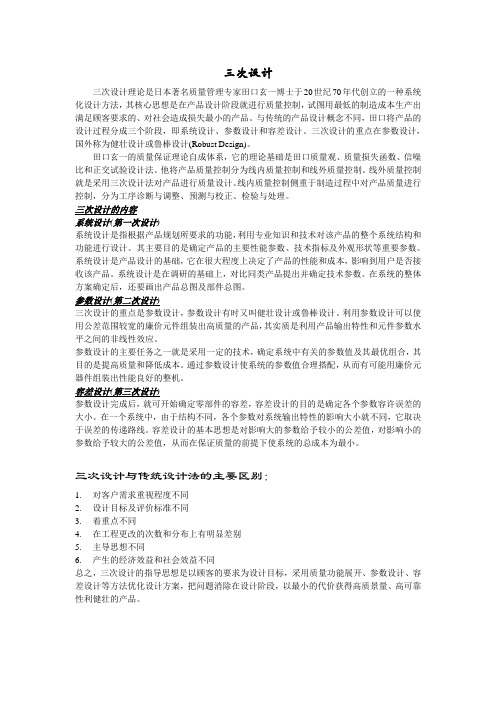
三次设计三次设计理论是日本著名质量管理专家田口玄一博士于20世纪70年代创立的一种系统化设计方法,其核心思想是在产品设计阶段就进行质量控制,试图用最低的制造成本生产出满足顾客要求的、对社会造成损失最小的产品。
与传统的产品设计概念不同,田口将产品的设计过程分成三个阶段,即系统设计、参数设计和容差设计。
三次设计的重点在参数设计,国外称为健壮设计或鲁棒设计(Robust Design)。
田口玄一的质量保证理论自成体系,它的理论基础是田口质量观、质量损失函数、信噪比和正交试验设计法。
他将产品质量控制分为线内质量控制和线外质量控制。
线外质量控制就是采用三次设计法对产品进行质量设计。
线内质量控制侧重于制造过程中对产品质量进行控制,分为工序诊断与调整、预测与校正、检验与处理。
三次设计的内容系统设计(第一次设计)系统设计是指根据产品规划所要求的功能,利用专业知识和技术对该产品的整个系统结构和功能进行设计。
其主要目的是确定产品的主要性能参数、技术指标及外观形状等重要参数。
系统设计是产品设计的基础,它在很大程度上决定了产品的性能和成本,影响到用户是否接收该产品。
系统设计是在调研的基础上,对比同类产品提出并确定技术参数。
在系统的整体方案确定后,还要画出产品总图及部件总图。
参数设计(第二次设计)三次设计的重点是参数设计,参数设计有时又叫健壮设计或鲁棒设计。
利用参数设计可以使用公差范围较宽的廉价元件组装出高质量的产品,其实质是利用产品输出特性和元件参数水平之间的非线性效应。
参数设计的主要任务之一就是采用一定的技术,确定系统中有关的参数值及其最优组合,其目的是提高质量和降低成本。
通过参数设计使系统的参数值合理搭配,从而有可能用廉价元器件组装出性能良好的整机。
容差设计(第三次设计)参数设计完成后,就可开始确定零部件的容差,容差设计的目的是确定各个参数容许误差的大小。
在一个系统中,由于结构不同,各个参数对系统输出特性的影响大小就不同,它取决于误差的传递路线。
试析异形零件加工工艺及变形控制方案
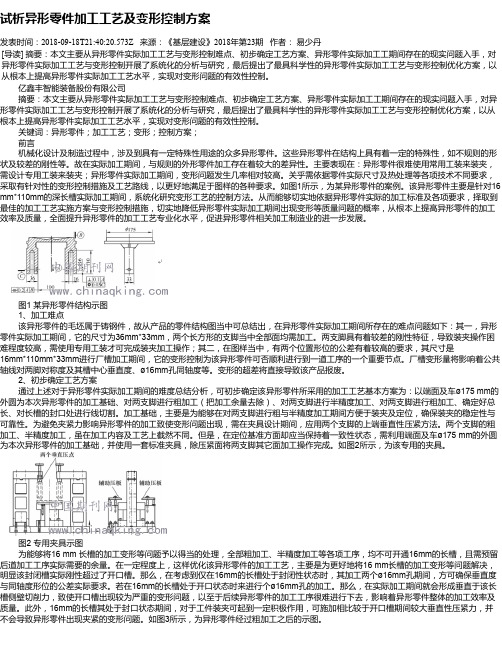
试析异形零件加工工艺及变形控制方案发表时间:2018-09-18T21:40:20.573Z 来源:《基层建设》2018年第23期作者:易少丹[导读] 摘要:本文主要从异形零件实际加工工艺与变形控制难点、初步确定工艺方案、异形零件实际加工工期间存在的现实问题入手,对异形零件实际加工工艺与变形控制开展了系统化的分析与研究,最后提出了最具科学性的异形零件实际加工工艺与变形控制优化方案,以从根本上提高异形零件实际加工工艺水平,实现对变形问题的有效性控制。
亿鑫丰智能装备股份有限公司摘要:本文主要从异形零件实际加工工艺与变形控制难点、初步确定工艺方案、异形零件实际加工工期间存在的现实问题入手,对异形零件实际加工工艺与变形控制开展了系统化的分析与研究,最后提出了最具科学性的异形零件实际加工工艺与变形控制优化方案,以从根本上提高异形零件实际加工工艺水平,实现对变形问题的有效性控制。
关键词:异形零件;加工工艺;变形;控制方案;前言机械化设计及制造过程中,涉及到具有一定特殊性用途的众多异形零件。
这些异形零件在结构上具有着一定的特殊性,如不规则的形状及较差的刚性等。
故在实际加工期间,与规则的外形零件加工存在着较大的差异性。
主要表现在:异形零件很难使用常用工装来装夹,需设计专用工装来装夹;异形零件实际加工期间,变形问题发生几率相对较高。
关乎需依据零件实际尺寸及热处理等各项技术不同要求,采取有针对性的变形控制措施及工艺路线,以更好地满足于图样的各种要求。
如图1所示,为某异形零件的案例。
该异形零件主要是针对16 mm*110mm的深长槽实际加工期间,系统化研究变形工艺的控制方法。
从而能够切实地依据异形零件实际的加工标准及各项要求,择取到最佳的加工工艺实施方案与变形控制措施,切实地降低异形零件实际加工期间出现变形等质量问题的概率,从根本上提高异形零件的加工效率及质量,全面提升异形零件的加工工艺专业化水平,促进异形零件相关加工制造业的进一步发展。
铝合金壳体异形件温挤压成形工艺优化的开题报告

铝合金壳体异形件温挤压成形工艺优化的开题报告开题报告:铝合金壳体异形件温挤压成形工艺优化1.课题背景铝合金作为轻量、强度高的材料,在现代工业领域中应用较广。
其中,铝合金壳体异形件应用较广泛,应用于各种机械设备和电器设备中。
为了满足不同的使用要求,需要对铝合金壳体异形件的成形工艺进行优化,以实现更好的性能和高质量的制造。
2.研究目的本研究目的是对铝合金壳体异形件的温挤压成形工艺进行优化,旨在探究最佳的成形参数和工艺路线,从而得到高质量、高效率、经济性的生产过程。
通过研究,可以有效提高铝合金壳体异形件的成形质量和生产效率,实现工业制造的自动化和精益化。
3.研究内容和方法(1)分析铝合金壳体异形件的特点和要求,研究温挤压成形的原理和工艺特点。
(2)通过建立数学模型和仿真分析,优化铝合金壳体异形件的温挤压成形工艺。
(3)基于优化结果,进行试验验证,检测异形件的成形质量和工艺效率。
(4)对试验结果进行数据分析,总结出铝合金壳体异形件温挤压成形工艺优化的适用范围和关键技术要点。
4.预期结果和意义(1)通过优化铝合金壳体异形件的温挤压成形工艺,实现高质量、高效率、经济性的生产过程。
(2)提高铝合金壳体异形件的成形质量和生产效率,满足不同客户的需求。
(3)为铝合金强力异形件的制造提供技术支持,促进工业制造的自动化和精益化。
5.研究计划和进度安排(1)文献研究和技术调研:3个月(2)数学模型建立和仿真分析:6个月(3)试验验证和数据分析:6个月(4)论文撰写和答辩准备:3个月6.预算和资源(1)研究费用预算:20万元(2)研究资源:铝合金壳体异形件试验设备、计算机仿真软件、试验室、科研人员等7.参考文献(1)谢积光,王睿. 铝合金异形材在汽车车身上的应用[J]. 金属现代化,2016,45(6):16-23.(2)周晓霞,杨志成. 铝合金板材挤压成形仿真研究[J]. 大学物理,2019,42(6):55-62.(3)刘元甫,徐钦. 铝合金异型件温挤压成形数值模拟[J]. 机械科学与技术,2017,36(3):270-276.。
三次设计理论
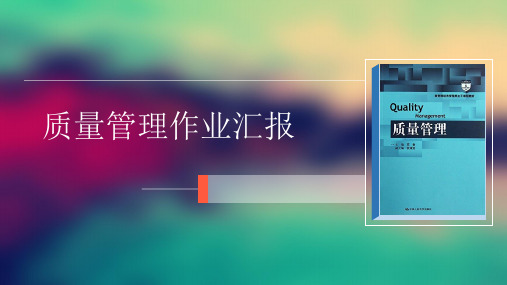
1
试验设计(DOE)
DOE概念及发展历程
design of experiment
试验设计(design of experiment,DOE),也称
为实验设计,它是以概率论和数理统计为理论基础
,经济地、科学地安排试验的一项技术。
20实际20年代问世 早期的单因素和多因素方差分析,传统 的正交试验法和近代的调优设计法。
最佳水平组合后进行,此时各元
件(参数)的质量等级较低,参 数波动范围较宽。
目的
容差设计案例分析
极值分 析法
统计平 模拟法 方公差 极值分析法是目前应用范围最广泛、操作最简便的方法,大 法 多数的设计都基于这个概念。在这种方法中,零部件都设计 为名义值,然后假定容差差完全向一个或另一个方向积累, 最终的结果仍能满足产品的功能要求。 在极值分析法分析中主要考虑的是设计规格的线性极值,它 虽然确保了所有零件的组合,但往往导致最终结果过于保守 ,产生过大或过小的容差。而且严格地说,极值分析法并不 属于统计方法,但它为后面讲到的统计平方公差法提供了比 较的基础,能够帮助我们更好地意识到应用统计方法的好处 。我们通过一个典型的机械系统设计案例来加深理解。
基本思想
根据各参数的波动对产品质量特性贡献(影响
)的大小,从经济性角度考虑有无必要对影响 大的参数给予较小的容差(例如用较高质量等 级的元件替代较低质量等级的元件)。这样做
来确定各参数的最合理的容差,使
总损失(质量与成本之和)达到最佳 (最小)。
,一方面可以进一步减少质量特性的波动,
提高产品的稳定性,减少质量损失;另一方 面,由于提高了元件的质量等级,使产品的 成本有所提高。因此,容差设计阶段既要考 虑进一步减少在参数设计后产品仍存在的质 量损失,又要考虑缩小一些元件的容差将会 增加成本,要权衡两者的利弊得失,采取最 佳决策。
大批量异形产品冲裁模具的优化设计

图 1 膜 片
产品表面平整, 毛刺小于 O l m . m 。但由于该零件原模具 O 设计方面的原因, 凸凹模经常开裂 , 导致该零件的批量上
在2 个定位销 1 上 , 3 实现精确定位, 此时条料恰好往前
送进一个步距 , 第二次冲裁时 , 凸模 1 又冲出 3 0 4 个 4 孔, 凸模 1 仍为空行程。 2 第三次送料时, 此时条料又『好 合 往前送进一个步距,第一次冲出的 3 0 孔准确的位 个 4 于落料凸模 1 之下 , 2 第三次冲裁时, 落料凸模 1 2冲出一 个带孔的完整工件 , 与此同时 , 冲孔凸模 1 又冲出 3 4 个
}
6 (
1
f r 一 _ ∈
【 2 l
/ ∈lf
、
l
/ 厂
∈
●
tቤተ መጻሕፍቲ ባይዱ
3。 一4 难
.
I
●±5 25 } - ● 一 1( R 0. ) 0
…
1± . 2 0) ( 5
I / 。
一
I I
l
+ )1 (
不去, 且毛刺较大。笔者应该厂的要求 , 重新设计了新的
模具 , 实践证明, 该模具有强度好 , 寿命长 , 生产效率高的
优点。
2 设计思想
首先分析该零件原模具容易损坏 的原因: 由于该零
0 孔。 4 以后各次冲裁就重复上述工序连续进行 , 直至条
料全部冲完。
4 模具设计要点
件具有尖角 、 孔壁小的特点, 0 4 原模具设计采用复合模
f 1 一 1-I + 一 . -. 5 . 5
图 3 产品排样 图
f
5 6
一种航空发动机异形封严环3d液压成形方法
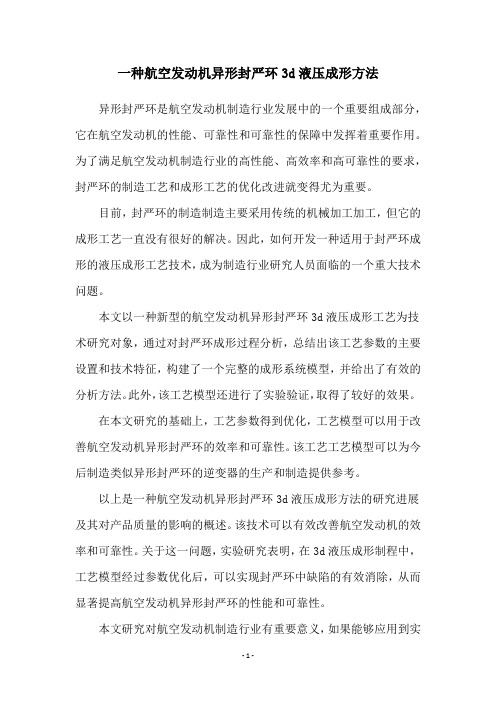
一种航空发动机异形封严环3d液压成形方法异形封严环是航空发动机制造行业发展中的一个重要组成部分,它在航空发动机的性能、可靠性和可靠性的保障中发挥着重要作用。
为了满足航空发动机制造行业的高性能、高效率和高可靠性的要求,封严环的制造工艺和成形工艺的优化改进就变得尤为重要。
目前,封严环的制造制造主要采用传统的机械加工加工,但它的成形工艺一直没有很好的解决。
因此,如何开发一种适用于封严环成形的液压成形工艺技术,成为制造行业研究人员面临的一个重大技术问题。
本文以一种新型的航空发动机异形封严环3d液压成形工艺为技术研究对象,通过对封严环成形过程分析,总结出该工艺参数的主要设置和技术特征,构建了一个完整的成形系统模型,并给出了有效的分析方法。
此外,该工艺模型还进行了实验验证,取得了较好的效果。
在本文研究的基础上,工艺参数得到优化,工艺模型可以用于改善航空发动机异形封严环的效率和可靠性。
该工艺工艺模型可以为今后制造类似异形封严环的逆变器的生产和制造提供参考。
以上是一种航空发动机异形封严环3d液压成形方法的研究进展及其对产品质量的影响的概述。
该技术可以有效改善航空发动机的效率和可靠性。
关于这一问题,实验研究表明,在3d液压成形制程中,工艺模型经过参数优化后,可以实现封严环中缺陷的有效消除,从而显著提高航空发动机异形封严环的性能和可靠性。
本文研究对航空发动机制造行业有重要意义,如果能够应用到实际生产中,那么生产效率将会大大提高,并显著提升航空发动机的可靠性,为客户提供满意的产品。
在本文研究的基础上,今后将继续从工艺分析的角度对航空发动机异形封严环3d液压成形工艺进行深入研究,满足不同行业不断增长的性能和可靠性要求。
综上所述,本文以一种新型的航空发动机异形封严环3d液压成形工艺为技术研究对象,分析了封严环成形过程及其特征,构建了一个完整的成形系统模型,并给出了有效的分析方法。
实验研究表明,经过参数优化后,3d液压成形制程可以消除封严环中缺陷,从而实现航空发动机异形封严环的高性能和高可靠性。
金属成型工艺参数优化与应用考核试卷
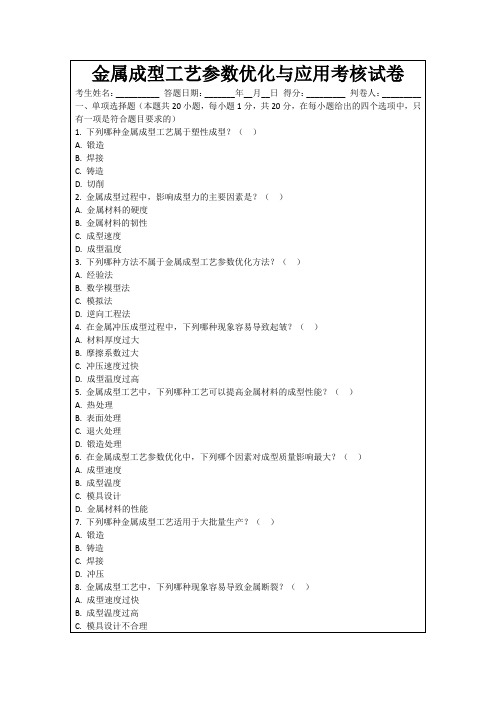
3.金属成型工艺参数优化中,常用的数学模型法包括______模型和______模型。
()
4.成型金属材料的______性能直接影响成型件的精度和质量。
()
5.为了提高金属成型工艺的效率,可以采用______成型和______成型技术。
()
6.在金属成型工艺中,为了止起皱和断裂,需要合理控制______和______。
()
标准答案
一、单项选择题
1. A
2. D
3. D
4. C
5. C
6. D
7. D
8. C
9. B
10. A
11. D
12. C
13. D
14. A
15. A
16. A
17. B
18. D
19. D
20. B
二、多选题
1. AC
2. ABC
3. ABC
4. ABD
5. ABCD
6. ABCD
7. ABC
C.优化模具设计
D.选用合适的金属材料
19.下列哪种金属成型工艺适用于小型零件的制造?()
A.锻造
B.铸造
C.焊接
D.高速冲压
20.在金属成型工艺参数优化过程中,下列哪种方法可以帮助预测成型缺陷?()
A.数学模型法
B.模拟法
C.实验法
D.经验法
二、多选题(本题共20小题,每小题1.5分,共30分,在每小题给出的四个选项中,至少有一项是符合题目要求的)
A.减少材料浪费
B.提高成型速度
C.提高模具寿命
D.减少人工干预
17.在金属成型工艺中,下列哪种现象容易导致金属变形不均匀?()
A.成型速度过快
异形瓶液压胀形数值模拟及工艺参数优化的开题报告

异形瓶液压胀形数值模拟及工艺参数优化的开题报告一、研究背景异形瓶是一种广泛应用于包装、储运等领域的特殊瓶型,其形状独特、复杂,具有高度的装饰性和实用性。
胀形是异形瓶生产过程中的一项重要工艺,通过压力加工将平面薄板材料变形成为异形瓶形,具有成本低、生产效率高等优点。
然而,由于异形瓶形状复杂,胀形过程中易出现突变、曲率变化等问题,导致成品质量不稳定,生产效率低下。
因此,探究异形瓶液压胀形数值模拟及工艺参数优化的方法具有重要的实践意义和科学价值。
二、研究内容本研究旨在通过液压胀形数值模拟和工艺参数优化,实现异形瓶生产工艺的优化与改进。
具体研究内容如下:1. 构建异形瓶液压胀形数值模拟模型,通过有限元方法分析异形瓶胀形过程中的力学特性和变形规律,探究其影响因素。
2. 基于模型分析结果,提出异形瓶胀形工艺的优化方案。
针对异形瓶胀形过程中可能出现的突变、曲率变化等问题,优化工艺参数,使得异形瓶的成型质量更加稳定可靠。
3. 验证优化方案的可行性和有效性。
将优化后的工艺参数应用于异形瓶胀形生产实践中,并对成品进行质量检验和性能测试,探究优化方案的成果。
三、研究意义本研究的意义在于:1. 提高异形瓶生产效率和成品质量。
通过模拟分析和工艺优化,减少异形瓶胀形生产过程中可能出现的错误和浪费,提高生产效率和成品质量。
2. 推动胀形工艺的理论研究。
异形瓶的胀形是一项较为复杂的工艺过程,通过数值模拟和优化研究,推广和发展胀形工艺的理论基础,提高异形瓶生产水平。
3. 为胀形工艺的改进提供参考。
本研究的成果可以为其他异形器件的胀形工艺改进提供参考,拓展异形制件的生产应用领域。
四、研究方法和技术路线1. 建立三维胀形数值模型。
2. 使用有限元软件对胀形过程进行数值模拟。
3. 通过变量单因素分析和正交实验等方法确定主要影响因素,寻找最优方案。
4. 进行生产实验,验证胀形优化的效果。
五、预期成果1. 构建异形瓶胀形数值模拟模型。
2. 确定异形瓶胀形过程中的主要影响因素。
田口参数实验设计
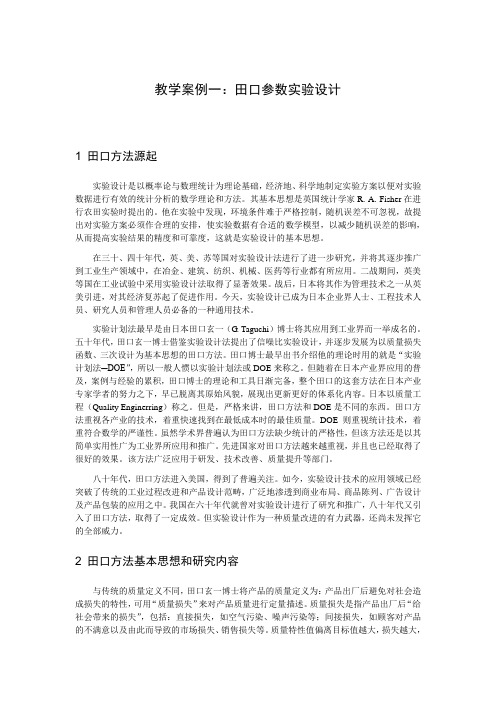
教学案例一:田口参数实验设计1 田口方法源起实验设计是以概率论与数理统计为理论基础,经济地、科学地制定实验方案以便对实验数据进行有效的统计分析的数学理论和方法。
其基本思想是英国统计学家R. A. Fisher在进行农田实验时提出的。
他在实验中发现,环境条件难于严格控制,随机误差不可忽视,故提出对实验方案必须作合理的安排,使实验数据有合适的数学模型,以减少随机误差的影响,从而提高实验结果的精度和可靠度,这就是实验设计的基本思想。
在三十、四十年代,英、美、苏等国对实验设计法进行了进一步研究,并将其逐步推广到工业生产领域中,在冶金、建筑、纺织、机械、医药等行业都有所应用。
二战期间,英美等国在工业试验中采用实验设计法取得了显著效果。
战后,日本将其作为管理技术之一从英美引进,对其经济复苏起了促进作用。
今天,实验设计已成为日本企业界人士、工程技术人员、研究人员和管理人员必备的一种通用技术。
实验计划法最早是由日本田口玄一(G. Taguchi)博士将其应用到工业界而一举成名的。
五十年代,田口玄一博士借鉴实验设计法提出了信噪比实验设计,并逐步发展为以质量损失函数、三次设计为基本思想的田口方法。
田口博士最早出书介绍他的理论时用的就是“实验计划法─DOE”,所以一般人惯以实验计划法或DOE来称之。
但随着在日本产业界应用的普及,案例与经验的累积,田口博士的理论和工具日渐完备,整个田口的这套方法在日本产业专家学者的努力之下,早已脱离其原始风貌,展现出更新更好的体系化内容。
日本以质量工程(Quality Enginerring)称之。
但是,严格来讲,田口方法和DOE是不同的东西。
田口方法重视各产业的技术,着重快速找到在最低成本时的最佳质量。
DOE则重视统计技术,着重符合数学的严谨性。
虽然学术界普遍认为田口方法缺少统计的严格性,但该方法还是以其简单实用性广为工业界所应用和推广。
先进国家对田口方法越来越重视,并且也已经取得了很好的效果。
- 1、下载文档前请自行甄别文档内容的完整性,平台不提供额外的编辑、内容补充、找答案等附加服务。
- 2、"仅部分预览"的文档,不可在线预览部分如存在完整性等问题,可反馈申请退款(可完整预览的文档不适用该条件!)。
- 3、如文档侵犯您的权益,请联系客服反馈,我们会尽快为您处理(人工客服工作时间:9:00-18:30)。
某异型威力件压制成型优化工艺参数的三次设计乔广文 胡焕性(中国兵器工业第204研究所,西安 710065)摘要 叙述了用三次设计方法对某异型件压制成型工艺进行的优化组合。
以最大密度差作为望小输出特性,各工艺参数作为可控因素,采用L 18(21×37)不完备正交表进行内设计。
通过方差分析,确定高度显著、显著的工艺参数和优化工艺。
对优化工艺进行了工程平均估计,计算了优化工艺的质量水平及收益。
最后做了验证实验。
关键词 异型威力件 压制成型 工艺参数 设计Threefold D esign of Pressed For m Opti m iz i ng Technology Param eter for a Spec i a l -shaped ChargeQi ao Guangwen Hu Huanx i ng(T he R esearch Institute N o 1204of Ch ina O rdnance Industry Co rpo rati on ,X i’an 710065)Abstract T h is paper relates the op ti m ized com binati on used in the fo rm ing p rocessing techno logy of a special 2shaped charge by m eans of th reefo ld design m ethod .T he incomp lete o rthogonal layout L 18(21×37)is used to the design of entraits .T he great significant and significant techno logy param eters and the op ti m ized techno logy are defined by analysis of variance ,A n engineering average esti m ati on is m ade fo r the op ti m ized techno logy ,and the quatily level and gains of the op ti m ized techno l 2ogy are calculated .L ast the results are verified be the tests . Keywords Special 2shaped charge ,P rocessing fo rm ing techno logy ,T hehno logy param eter ,T hereefo ld design .引 言预测2000年时装甲防护技术的发展和装甲类型的改进,要求反坦克导弹战斗部必须具有大炸高下大穿深的能力,有效地击毁主动装甲、重型三层间隔靶及其他靶板的主战坦克。
作为战斗部的能源威力部件是保证战斗部上述性能的最重要的一种影响因素。
因此,其质量水平和质量波动直接影响战斗部威力性能和威力的稳定性。
对此,我们采用田口三次设计方法,对工艺参数进行优化,确定优化工艺条件,成功地提出了一种优化生产工艺。
该工艺不但使产品质量稳定和满足技术指标要求,同时还缩短了研制周期并节省了研制经费。
1 系统设计我们承担一项压制某产品威力零件的任务,该任务对部件的各种密度差指标提出了严格的要求,把一个零件分解成四十九块15mm ×15mm ×15mm 的样块,测试密度后,计算出四十一个密度差数据,这些数据都要满足对其周向、径向、轴向、最大等规定的密度差要求。
要满足对压制件提出的密度差要求,必须研究出相应的成型工艺参数。
目前尚未有计算1第3期 1996年9月 火 炸 药各成型工艺参数的成熟数学模型,不能用计算方法来确定压制成型工艺的各参数值,只有通过实验方法加以实现。
由过去研究经验可知,压制件的最大密度差不能发发满足要求。
为了解决这个问题,采用三次设计方法对压制件成型工艺参数进行优化,以保证压制件最大密度差在满足指标要求的前提下,越小越好,最好为零。
实验结果表明,压制件最大密度差超标是由于第I层样片中的Θ111、Θ112、Θ113、Θ114四个样块密度值偏低和第 层样片中的Θ215、Θ216、Θ217、Θ218四个样块密度值偏高造成的。
为此,对上述八个样块密度差进行计算,其计算原则是,Θ215~Θ218中最大的值减去Θ111~Θ114中的最小的值得出一个密度差值∃Θ1。
依此原则,可逐次算得∃Θ2、∃Θ3、∃Θ4,使得∃Θ1>∃Θ2>∃Θ3>∃Θ4,把∃Θ1~∃Θ4做为输出特性,要求成型工艺能满足制件的∃Θ1~∃Θ4不大于01015g c m3且越小越好。
2 参数设计211 确定可控因素水平表选取的可控因素有:A,B,C,D,E,F,G,H。
因素A取两个水平,因素B~H取三个水平。
三个水平呈等间隔变化。
因素水平见表1。
表1 可控因素水平表因素A B C D E F G H1A1B1C1D1E1F1G1H12A2B2C2D2E2F2G2H23B3C3D3E3F3G3H3212 内设计不考虑各因素间的交互作用,选用L18(21×37)作为内表,来安排可控因素,见表2。
由于压制工艺各参数的误差体现在压制件的 、 层的样块位置上,故由取样方法代替工艺参数的误差,而不对工艺参数误差进行模拟。
213 计算信噪比按望小特性,由Γ=-10lg1n 2ni=1y2j式计算信噪比,其中,y i=∃Θi,n=4,N o11~N o118的Γ值见表2。
2火 炸 药 1996年 表2 内表及密度差试验数据因素列号N o 可 控 因 素A B C D E F G H 12345678111111111211222222311333333412112233512223311612331122713121323813232131913313212102113322111212113321221322113132212313214222312131522312321162313231217232131231823321231T 1347129235144239116217180222189233153230131231193T 2341176212166231170182140229167211171218110221104T 32401952181192881852361492431812401642361083 第3期 某异型威力件压制成型优化工艺参数的三次设计表2 (续)序实 测 密 度 值密度差(输出特性)信噪比号Θ111Θ112Θ113…Θ217Θ218∃Θ1∃Θ2∃Θ3∃Θ4Γ(dB )1118361183711837…118471184501011010080100801007411282118021179811803…118411184301045010410103901038271783118381183911840…118401184101003010010100001000561024118251182611827…118441184201019010180101601015351355118201181611816…118411184201026010250102501021321286118271182711826…118371183701011010110101001008391947118091181011810…118411184201033010210102101020321278118391183911840…118421184201004010030100201001511259118091181111810…1183811837010300102801027010263111210118391183611836…1184211843010070100701005010034418111118231182411824…1183811837010160101501014010133617512118041180311806…1184211841010390103701036010332818013118101181211813…1184111841010310102901027010273018914118351183511836…1183911840010050100501004010034212715118121181211811…1183711837010280102501025010233119316118361183811838…1183911837010030100101000010025415617118311183111831…11840118400100901009010090100741,3718118041*********…11835118340103201031010290102930138现品118201181711817…11844118410103001026010260102131172T =210i =1Γi =41128+27178+…+30138=689105214 对内表进行方差分析先计算总波动平方和,各因素波动平方和及自由度C T =118(218i =1Γi )2=T 218=689105218=26377122S T =218i =1(Γ1)2-C T =1261145 (fT=17)S A =118(T 1-T 2)2=1170 (f A =1)S B =16(T 21+T 22T 23)-C T =74198 (f B =2)4火 炸 药 1996年 再进行方差分析,并计算各因素的纯波动和贡献率,见表3。
表3 方差分析表方差来源波动平方和S 自由度f 方 差V =s f方差比F =V V e纯波动平方和S ′=S -TV e 贡献率Θ(◊)=S ′ TA 11701∃2222B 741982371497105364134511C 37166218183315127102211D 979160218918092107339681967618E 151412∃2222F 891562441788142378192613G 42143221122319931179215H201112∃2222(e )(37122)(7)(5132)(90142)(712)T1261145171261145100注:F 27(0105)=1174;F 27(0101)=9155经方差分析得出因素D 为高度显著因素,因素F 、B 为显著因素。