集成电路多注射头塑封模具介绍
塑料注射模具知识

塑料注射模具知識2011-11-20 03:06第一節﹕塑料模具分類模具的基本結構﹕塑料注射成型的過程是將已塑化好的塑料注入閉合的模腔內﹐經冷卻定型后開模取出塑件﹐因此﹐凡是塑料注射模具根椐其運動特點可分兩大部分。
一部分留在注射機的定模板上﹐稱為定模(前模)部分﹐另一部分隨注射動模板運動﹐稱為動模后模部分。
模具是塑料制品成型的主要工具﹐根椐塑料品種﹑塑料制品結構﹑生產批量和使用設備不同﹐采用各種不同形式的模具。
一.塑料模具分類方法移動式﹕(壓縮模﹑傳递模)熱固性塑料模﹕固定式﹕(壓縮模﹑傳递模)模具分類{熱塑性塑料模(吹塑模﹑注射模)二.熱固性塑料模具按模具固定壓機上的形式分1.移動式模具﹕它不固定在面床上在一般的情況下﹐裝料合模。
開模及塑料制品由模具內取出﹐均在機外進行。
這種模具結構簡單制造方便﹐但生產效率低。
2.固定式模具﹕它固定在機床上﹐在整個生產過程中﹐裝料﹑合模成型開模及推出塑料制品等均在機床上進行。
這種模具使用方便﹐生產凝率高﹐模具結構復雜﹐產要用在批量生產中。
按塑料制品成型方法分1.壓縮模﹕塑料裝在受熱的型腔或加料室內﹐然后加壓。
在壓制時直按對型腔內的塑料加壓﹐這類模具加料室與型腔是一體的。
2.傳递模﹕塑料在加料室內受熱成為粘流狀態﹐在柱塞壓力的作用下使熔料經過注射系統進入并充滿閉合的型腔。
3﹕塑料在注射機上裝有螺杆攪拌的料筒內受熱進行塑化﹐達到熔融狀態時﹐在力的作用下﹐熔料通過模具的澆注系統進入有一定溫度的型腔內固化成塑料制品﹐工藝成型短﹐生產產效率高。
這種模具在熱固性塑料注射機上使用。
按加料室的形式分﹕敞開式﹑半封閉式和封閉式模具。
按模具分型面的特征分﹕1.垂直分型面模具﹕指模具的分型面平行于壓機的工作壓力方向。
2.水平分型面模具﹕指模具的分型面垂直于壓機的工作壓力方向。
三.熱塑性塑料模具﹕熱塑性塑料的成型均采用注射模具。
其它的還有單分型腔和多型腔注射模具等。
四.注射模具基本結構和組成1﹐澆注系統2﹐成型零件﹕包括凹模(型腔) ﹑凸模和型芯等。
SOP集成电路塑料封装模具

23 . 5士 0 2 .0 01 . 5士 0 1 .0
0 4 士 0. 0 . 1
23 . 5士 0 2 .0 01 . 5士 0 1 .0
0. 士 0. 0 4 1
A m i / m
b mm / C/ m m D/ m m E/ m m e mm / H/ m m L/ m m
02 . 5士 0 1 .0
表 1 S OP集成电路外形尺寸
规格
引脚 数
A/ m m S OP 8 一
8
S OP一 4 1
1 4
SO P一 6 1
S OP一 0 2
20
S P2 O 一4
24
S OP一 28
28
1 6
1 5士 0 2 . .0 0. 6士 0 1 1 .0
0. 士 0. 0 4 1
1 5士 0 2 . .0 01 . 6士 0 0 .8
4. 2 士 0. 0 9 2
02 . 5士 0 1 .0 85 . 5士 0 3 .0 39 . 5土 0 2 .0
1 27 .
02 . 5土 0 1 .0
1 4 士 0 30 5. .
02 . 5士 0 1 .0 1. 7 7士 0 3 .0 76 . 5士 0 2 .5
1 27 .
1. 2 7士 0 2 .0 76 . 5士 0 2 .5
室温,这就直接影响到模具的设计与制造。塑封模 常常是一模具有几百型腔甚至数千型腔,由于引线
发展, 对塑料封装模具的精度和可靠性要求也越来
越高。
2 塑封模具的温度补偿计算
塑封模封装产品的成型原理是,在合模状态 下,将预热到 10 3 ℃左右的改性环氧树脂料饼放入 模具加料腔,在塑封压机外加载荷的作用下,融熔 状态的环氧树脂料迅速通过流道、 口注入各处型 浇 腔 ,经 升温 、保 压 、补缩 、 固化 后 成 型产 品 。 模具的生产与加工一般都是在室温下进行的。 然而,塑封模具在实际工作时,其工作温度远高于
IC模具基本介绍

IC模具基本介绍IC模具,全称为Integrated Circuit Mould,是制造集成电路的工具。
集成电路是现代电子设备的核心组件,它由大量的电子元件(如晶体管、电容器、电阻器等)组成,通过在同一片基片上进行集成和互连,实现了功能的复杂性和系统的紧凑性。
IC模具是制造集成电路所必需的工具之一,用于在制造过程中将集成电路芯片的设计转化为实际产品。
它可以看作是一个“模具”,通过模具上的“模块”来制造具有特定功能和结构的集成电路。
IC模具的主要作用是在硅片上形成金属或多层金属导线和互连结构,从而实现不同元件之间的信号传输和电气连接。
IC模具通常由高硬度的材料制成,如钨钢、硼硅酸钠玻璃等。
它的制造过程需要借助于先进的微纳加工技术和精密的制造设备。
通常,制造IC模具的流程可以分为以下几个步骤:1.设计和制造模具:首先,根据集成电路芯片的设计要求,设计并制造出符合要求的IC模具。
模具的设计需要考虑到芯片的结构和连接需求,并确保模具的可重复、可靠性能。
2.芯片制造:通过将半导体材料(如硅)加工成薄片,并在薄片上制造出晶体管、电容器等元件,形成具有特定电路结构的芯片。
3.芯片上的金属导线和互连:将制造好的芯片放置在IC模具的特定位置,通过IC模具上的模具、导线等结构,在芯片上形成导线和互连结构,使芯片的各个元件之间可以相互连接并进行信号传输。
4.包装和封装:将制造好的集成电路芯片进行外包装和封装,以保护芯片免受环境的干扰,同时方便芯片的安装和使用。
IC模具的制造过程需要高度的精密度和一定的工程能力。
在模具的设计和制造过程中,需要考虑到芯片的低功耗、高速度、小尺寸和高可靠性等特点,以及制造过程中的多种材料特性、工艺控制和质量保证。
同时,模具的设计还需要与芯片的设计相匹配,确保模具和芯片的接口匹配,以实现良好的信号传输和电气连接。
IC模具在现代电子产业中扮演着重要的角色。
它不仅是集成电路制造的关键工具,更是推动电子产业发展的基石。
注射模具基本结构及分类

1. 注射模的结构组成 2. 注射模的分类
注射模的结构组成
• 注射模均由定模和动模两大部分组成,根据模 具中各零件所起的作用,又可细分为以下基本 组成部分:
1. 成型零部件 2. 浇注系统 3. 导向与定位机构 4. 脱模机构 5. 侧向分型抽芯机构 6. 温度调节系统 7. 排气系统
弹簧式双分型面注射模
工作原理:
弹簧式双分型面注射模是利用弹簧机构控制双 分型面注射模分型面的打开顺序。
弹簧式机构结构简单,适用性强,机构装在模 具之内,结构紧凑。
三、带活动镶件的注射模
1-定模板 2-导柱 3活动镶件 4-型芯 5动模板 6-动模垫板 7-垫板 8-弹簧 9-推 杆 10-推杆固定板 11-推板 12-动模座板
开模后,塑件紧包在凸模11 上,塑件留在了 定模一侧,当动模左移一定距离,拉板8 通过定 距螺钉6 带动推件板7 将塑件从凸模中脱出。
七、热流道注射模
1-动模座板 2-垫块 3-推板 4-推杆固定 板 5-推杆 6-动模座 板 7-导套 8-动模板 9-型芯 10-导柱 11定模板 12-凹模 13垫块 14-喷嘴 15-热 流道板 16-加热器 孔 17-定模座板 18绝热层 19-浇口套 20-定位圈 21-一级
开模时,A-A面先分开,同时,螺纹型芯1在 随着注射机开合模丝杆8的后退中自动旋转,此时, 螺纹塑件由于定模板7的止转作用并不移动,仍留 在型腔内。当A-A面分开一段距离,即螺纹型芯1 在塑件内还有最后一牙时,定距螺钉4拉动动模板 5,使模具沿B-B打开,此时,塑件随型芯一道离 开定模型腔,然后从B-B分型面两侧的空间取出。
(5)侧向分型抽芯机构:带有侧凹或侧孔的制品, 在被脱出模具之前,必须先进行侧向分型将型芯 侧向抽出。侧向抽芯机构包括斜导柱、滑块、楔 紧块、滑块定位装、侧型芯和抽芯液压缸等。
集成电路塑封模具设计

向阀控制,为保证翻转机构和卸料机构平稳运行,气缸回路采用单向节流阀来控制翻转竖直气缸和卸料竖直气缸的伸缩速度[3]。
4结语本设计机械结构布局紧凑,气动方案合理有效。
设计出的自动送料机已经应用于企业的实际生产,解决了钢筋套筒挤压生产中钢筋和套筒的自动送料问题,降低了操作人员的劳动强度,提高了生产效率,具有较高的实际应用价值。
[参考文献][1]蔡红波,杜运站.钢筋机械连接技术现状及发展趋势[J].黑龙江科技信息,2009(13):281,276.[2]路甬祥.液压气动技术手册[M].北京:机械工业出版社,2002:1-3.[3]罗庚兴,宁玉珊.气动安装机械手的PLC 控制[J].制造业自动化,2011,33(1):82-84.收稿日期:2017-09-12作者简介:田磊(1982—),男,河北新乐人,硕士研究生,研究方向:机电一体化。
图4夹紧套筒机构装配图图5气动控制回路图1—分水滤水器2—减压阀3—油雾器4—二位五通换向阀5—翻转竖直气缸6—卸料竖直气缸7—夹紧套筒气缸(宽型气爪)8—套筒上料气缸9—单向节流阀集成电路塑封模具设计蔡志元(天水华天机械有限公司,甘肃天水741000)摘要:对现行集成电路塑封行业塑封模具中的传统模、MGP 膜及自动模的优缺点进行了比较,设计了一种适合公司发展的模具。
以QFP64L 为例,介绍了塑封模具总体结构和设计要点。
关键词:塑封模;结构;关键部件;设计1传统模、MGP 膜及自动模的优缺点随着集成电路封装的发展,产量及成本成为每个封装企业关注的重点,在塑封这道工序体现为如何降低成本和增加塑封产量。
目前国内集成电路塑封模具设计有两种方式,即单缸和多缸,这两种封装方式有三种模具设计结构:传统模具(单缸)、自动膜(多缸)和MGP 模(多缸)。
这三种形式优缺点如下:传统的中心单注塑料筒的模具,由于料筒远离型腔,流道较长,所以有着许多不可克服的缺点。
模塑料利用率低,中心料筒流入中间型腔和远离型腔的流道的长短差距很大,所以有许多产品品质问题,如针孔、内部气泡、水口气泡、边线缺口、冲线、不满胶和漏注胶等。
塑料注射成型模具介绍

❖注射制品占模型制品三分之一 ❖注射模约占塑料成型模具二分之一
塑料注射成型模具介绍
第9页
塑料注射成型模具概述
设计注射模应考虑问题
(1)了解塑料熔体流动行为, 考虑塑料在流道和型腔各处流 动阻力, 流动速度, 校核最大流动长度及流动面积比。依 据塑料充模次序, 考虑塑料在模具内重新熔合和模腔内气 体导出问题。 (2) 考虑冷却过程中塑料收缩及补给问题。 (3) 经过模具设计, 控制塑料在模具内结晶、取向和改进 制品内应力。 (4) 浇口形式、位置和分型面选择问题。 (5) 制品顶出及侧向分型抽芯问题。 (6) 模具冷却或加热问题。 (7) 模具与所用注射机关系问题。 塑料注射成型模(具8介)绍模具总体结构要合理, 模具零件要便于制造、能采取第10页
指成型零件上直接成型塑料件相关尺寸 B、主要内容 凹模、型芯径向尺寸(含长、宽尺寸) 凹模、型芯高度尺寸 中心距尺寸 螺纹型环或型芯径向尺寸和螺距尺寸 C.塑件及模具成型零件工作尺寸标注
塑料件轴(外形尺寸) 基轴制:单向负偏差,基本尺寸为最大极限尺寸,小写英文字母表示
例:d0S-Δ; h0S-Δ 对应模具凹模尺寸(径向或深度尺寸): 基孔制:单向正偏差,基本尺寸为最小极限尺寸,大写英文字母表示
保压阶段浇注系统应能充分传递压力
控制浇注系统中浇口凝固时间以控制补料时间
确保各型腔均衡进料
排气性好
塑料注射成型浇模具注介绍 系统凝料尽可能少,去除方便
第12页
普通浇注系统设计
一、主流道设计
1、概述
主流道设计于主流道衬套中,其轴线能够垂直于分型面,
也能够与分型面有一定角度。
2.主流道设计关键点
塑料注射模具知识点总结

概述塑料注射模具是用于制造塑料制品的一种装置,由模具基板、模具芯、注射系统、冷却系统、脱模系统等部分组成。
塑料注射模具制造是一项相对复杂的工艺,需要对材料、工艺、设计、加工等方面具有深入的了解和掌握。
本文将从材料、设计、加工、维护等方面综合介绍塑料注射模具的知识点。
一、塑料注射模具的材料1.1 模具基板材料模具基板是塑料注射模具的主要承载部分,需要具有高强度、耐磨损、耐腐蚀等特性。
常见的模具基板材料有P20、718、2738等。
P20材料具有良好的硬度和耐磨损性能,适合制作中小型模具;718材料具有高强度和硬度,适合制作大型模具;2738材料具有高镍合金特性,适合制作高精度模具。
1.2 模具芯材料模具芯是用于塑料制品内部结构的部分,需要具有高硬度、高精度、耐磨损等特性。
常见的模具芯材料有SKD61、S136等。
SKD61材料具有良好的热稳定性和硬度,适合制作高品质的模具芯;S136材料具有良好的耐腐蚀性和耐磨损性,适合制作高精度的模具芯。
1.3 注射系统材料注射系统是用于将熔融塑料材料注入模具腔内的部分,需要具有耐高温、耐腐蚀、高流动性等特性。
常见的注射系统材料有H13、H13W等。
H13材料具有良好的耐热性和抗氧化性,适合制作注射系统组件;H13W材料具有更高的硬度和耐磨损性,适合制作高性能的注射系统组件。
1.4 冷却系统材料冷却系统是用于控制模具温度的部分,需要具有良好的传热性能、耐腐蚀、高耐压等特性。
常见的冷却系统材料有铜合金、铝合金、不锈钢等。
铜合金具有良好的导热性和抗腐蚀性,适合制作冷却系统管道;铝合金具有较轻的重量和较高的导热性,适合制作冷却系统散热器;不锈钢具有较高的耐腐蚀性和耐压性,适合制作高性能的冷却系统组件。
1.5 脱模系统材料脱模系统是用于将成型塑料制品从模具中脱离的部分,需要具有良好的脱模性能、耐磨损、易维护等特性。
常见的脱模系统材料有冷作钢、硬质合金等。
冷作钢具有良好的硬度和耐磨损性,适合制作脱模系统零部件;硬质合金具有更高的硬度和耐磨损性,适合制作高性能的脱模系统零部件。
注射模具总结

注射模具总结引言注塑模具是注塑成型过程中的关键工具之一,其质量直接影响到产品的成型质量和生产效率。
本文将对注射模具进行总结,包括模具的定义、分类、制造工艺等方面,以帮助读者更好地了解注射模具。
何为注射模具注射模具是用于塑料注塑成型的专用模具,也称为注塑模具。
它由模具座(支架)、模具芯(浇注孔)、模具腔(成形孔)等部件组成。
注塑模具能够将熔化的塑料通过注射机注入到模具腔中,经过冷却固化后,得到所需形状的产品。
注射模具的分类根据注塑模具的结构和应用领域,可以将其分为以下几类:1.直线副模具:该类模具结构简单,适用于生产平面形状的产品。
2.斜线副模具:模具芯、模具腔的结构为斜面,多用于生产壁厚不均匀的产品。
3.寄生副模具:模具芯出现在模具腔的内部,通过模具座插入模具腔内注射成型,适用于细长形状的产品。
4.双色模具:该类模具可实现一次注塑成型,生产出颜色不同的产品。
5.复合模具:模具腔形状较复杂,需要多个注射机同时工作,用于生产多组件结构的产品。
6.热流道模具:通过热嘴将熔融塑料永远保持在熔融状态,可用于生产高要求的产品,如透明产品。
注射模具的制造工艺注射模具的制造工艺主要包括以下几个步骤:1.设计:根据产品的要求,设计注射模具的结构、尺寸和形状。
2.制作模具芯和模具腔:根据设计图纸,选用适当的材料,并通过数控机床进行切削加工,制作出模具芯和模具腔。
3.组装与调试:将模具芯和模具腔进行组装,并进行必要的调试工作,以保证模具正常使用。
4.热处理:对模具进行热处理,提高其硬度和耐磨性,以延长模具的使用寿命。
5.表面处理:对模具表面进行精细加工,以提高产品的光洁度和精度。
6.模具试模:在注射机上进行试模,调整模具腔和模具芯的位置和尺寸,以达到产品质量标准。
7.修整和保养:对模具进行定期的修整和保养工作,以保证模具的使用效果和寿命。
注射模具的优势和挑战注射模具作为一种关键工具,在塑料加工行业具有以下优势:•生产效率高:注射模具可以实现高速连续生产,提高生产效率。
注射模具结构综合介绍(ppt 71页)PPT学习课件

顶块顶出
胶位较高,难下顶针。,如:分体面框
推板顶出
筒形件、盒形件、瓶盖等
模具型腔中的空气如 何排出?
排气系统
排气系统 作用
排气槽排气 排气钢排气 配合间隙排气
…….
保证塑料熔体在填充过 程中型腔中的气体能完 全顺利排出。
排气系统对确保制品成型质量起着至关重要的作用。 A、利用排气槽,排气槽一般设在型腔最后被充满的部位,排气槽的深度因塑料不同而异,基本 上是以塑料不产生飞边的所允许的最大间隙来确定,如ABS 0.04以下,泥龙0.02mm以下,赛钢 0.02以下。 B、利用型芯镶件推杆等的配合间隙或专用排气塞排气; C、有时为了防止制品在顶出时造成真空变形,必设气销; D、有时为了防止制品与模具的真空吸附,而设计防真空吸附元件。
浇注系统(流道系统)
冷流道系统
如何把塑料填充 到成型零件组成 的型腔中?
流道 系统
作用
使塑料熔体平稳且有序地填充到型腔中, 并在填充和凝固过程中把压力充分传递 到各部位,以获得组织紧密、外观清晰 的塑料件。
热流道系统
浇口套
塑料模具的浇注系统
主流道(直浇道)
浇口
分流道
定位圈 浇口套
水口刮板
常用浇口方式
排气槽
排气槽
排气不良会产生烧黑、注不满等
在注塑过程中,动定 模不断开合,如何保 证动定模相对位置精 确?(保证产品分型 线不错位)
导向定位零件
导向定位 零件 作用
保证动定模合模时位置 的精确性。
导柱、导套 辅助定位器 …….
导柱
定位辅助器
中托司(针板导柱)
导向不精确,会导致产品 分型线错位、擦穿位批锋。 严重时会会导致模具卡死、
注塑模具设计说明书
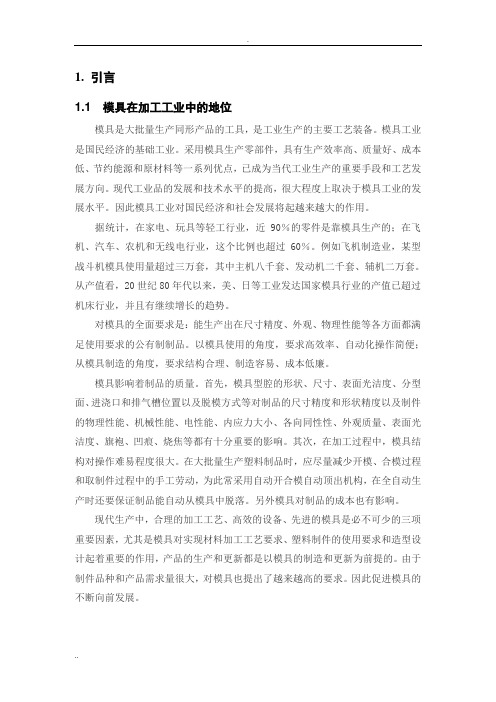
1. 引言1.1 模具在加工工业中的地位模具是大批量生产同形产品的工具,是工业生产的主要工艺装备。
模具工业是国民经济的基础工业。
采用模具生产零部件,具有生产效率高、质量好、成本低、节约能源和原材料等一系列优点,已成为当代工业生产的重要手段和工艺发展方向。
现代工业品的发展和技术水平的提高,很大程度上取决于模具工业的发展水平。
因此模具工业对国民经济和社会发展将起越来越大的作用。
据统计,在家电、玩具等轻工行业,近90%的零件是靠模具生产的;在飞机、汽车、农机和无线电行业,这个比例也超过60%。
例如飞机制造业,某型战斗机模具使用量超过三万套,其中主机八千套、发动机二千套、辅机二万套。
从产值看,20世纪80年代以来,美、日等工业发达国家模具行业的产值已超过机床行业,并且有继续增长的趋势。
对模具的全面要求是:能生产出在尺寸精度、外观、物理性能等各方面都满足使用要求的公有制制品。
以模具使用的角度,要求高效率、自动化操作简便;从模具制造的角度,要求结构合理、制造容易、成本低廉。
模具影响着制品的质量。
首先,模具型腔的形状、尺寸、表面光洁度、分型面、进浇口和排气槽位置以及脱模方式等对制品的尺寸精度和形状精度以及制件的物理性能、机械性能、电性能、内应力大小、各向同性性、外观质量、表面光洁度、旗袍、凹痕、烧焦等都有十分重要的影响。
其次,在加工过程中,模具结构对操作难易程度很大。
在大批量生产塑料制品时,应尽量减少开模、合模过程和取制件过程中的手工劳动,为此常采用自动开合模自动顶出机构,在全自动生产时还要保证制品能自动从模具中脱落。
另外模具对制品的成本也有影响。
现代生产中,合理的加工工艺、高效的设备、先进的模具是必不可少的三项重要因素,尤其是模具对实现材料加工工艺要求、塑料制件的使用要求和造型设计起着重要的作用,产品的生产和更新都是以模具的制造和更新为前提的。
由于制件品种和产品需求量很大,对模具也提出了越来越高的要求。
因此促进模具的不断向前发展。
注射模具的基本结构

注射模具的基本结构一、典型的注射模具结构注射模具由动模和定模两部分组成,动模安装在注射成型机(简称注射机)的移动模板上,定模安装在注射机的固定模板上。
在注射成型时动模与定模闭合构成浇注系统和型腔,开模时动模与定模分离以便取出塑料制品。
图5—1示出典型的单分型面注射模结构,根据摸具中各个部件所起的作用,一般可将注射模细分为以下几个基本组成部分。
图5—1典型的单分型面注射模1一定位套2一主流道衬套3一定模座板 4一定模板 5一动模 6一动模垫板7一模底座 8一推出固定板 9一推板 10一拉料杆 11一推杆 12一导柱13一型芯 14一凹模 15一冷却水通道1 成型部件成型部件由型芯和凹模组成。
型芯形成制品的内表面形状,凹模形成制品的外表面形状。
合模后型芯和凹模便构成了模具的型腔,如图5—1所示,该模具的塑腔由件13和件14组成。
按工艺和制造的要求,有时型芯或凹模由若干拼块组合而成,有时做成整体,仅在易损坏、难加工的部位采用镶件。
选作型芯或凹模的钢材,要求有足够的强度,表面耐磨性,有时还需要有耐腐蚀性,并且淬火后的变形量要小,故常采用合金结构钢或合金工具钢。
当要求较低或批量较小时也可选用中碳钢或碳素工具钢来制造简单的型芯和凹模。
2.浇注系统浇注系统又称为流道系统,它是将塑料熔体由注射机喷嘴引向型腔的一组进料通道,通常由主流道、分流道,浇口和冷料穴组成,浇注系统的设计十分重要,它直接关系到塑料制品的成型质量和生产效率。
3.导向部件为了确保动模与定模在合模时能准确对中,在模具中必须设置导向部件。
在注射模中通常采用四组导柱与导套来组成导向部件,有时还需在动模和定模上分别设置互相吻合的内、外锥面来辅助定位。
为了避免在制品推出过程中推板发生歪斜现象,一般在模具的推出机构中还设有使推板保持水平运动的导向部件,如导柱与导套。
4.推出机构在开模过程中,需要有推出机构将塑料制品及其在流进内的凝料推出或拉出。
例如在图1中,推出机构由推杆11和推出固定板8、推板9及主流道的拉料杆10组成。
一种高效节能半导体塑封模具解析 袁威

一种高效节能半导体塑封模具解析袁威摘要:一种高效节能半导体塑封模具,上模模盒(8)内的上中心浇道板和下模模盒(9)的下中心浇道板形成封闭的腔体,上模模盒(8)与下模模盒(9)有胶道(24),胶道(24)是空心的管道,和流道25连通,胶道(24)通过流道(25)与集成元件穴(26)相联通;注塑头(4)与腔体联通;加料筒(31)内的流质树脂由注塑头通过胶道(24)经过流道(25)注入流质树脂。
本发明克服了现有技术浇道流程长,塑封产品气密性差、更换镶件和顶杆时复杂的不足,提供了一种密度大,装拆方便,塑封料浪费少,节约树脂15%至30%,提高了原料利用率的半导体塑封模具,能应用在IC封装领域。
关键词:高效节能半导体塑封模具1、技术领域:集成电路的封装设备2、背景技术:半导体集成电路封装模具是微电子封装生产必备的关键工艺设备,微电子工业的飞速发展对半导体封装模具的设计与制造提出了深层次的高新要求。
半导体封装模具业对模具的要求是:一是要求精加工模具,目前电子产品不断集成化、小型化,产品趋向高端,尺寸也越来越小,封装体越来越薄,这对封装要求越来越高,对模具精度要求很高。
塑封模工艺是半导体器件后工序生产中极其重要的工艺手段之一,一般应用单缸封装技术,其封装对象包括DIP、SOP、QFP、SOT、SOD、TR类分立器件以及片式钽电容、电感、桥式电路等系列产品。
多注射头封装模具MGP是单缸模具技术的延伸,是如今封装模具主流产品。
其采用多料筒、多注射头封装形式,优势在于可均衡流道,实现近距离填充,树脂利用率高,封装工艺稳定,制品封装质量好。
它适用于SSOP、TSS OP、LQFP等多排、小节距、高密度集成电路以及SOT、SOD等微型半导体器件产品封装。
3、技术核心:本发明克服了现有技术的不足,提供解决原料浪费和封装不合格的集成电路封装模具。
为解决上述的技术问题,采用以下技术方案:高效节能半导体塑封模具,上模板6固定有上模模盒系统8,下模板7固定有下模模盒9;齿轮齿条2连接在驱动转进板3上,并上下往复移动,转进板3上固定注塑头系统4;注塑头系统与下模模盒9的下中心浇道板联通;转进板3带动下模顶杆动力复位板10上下往复移动,动力复位板10通过机床复位杆穿过下模板7的下模顶杆动力杆11带动顶杆向上移动,顶出成型产品和浇道;上模顶杆复位动力系统12顶在上模底板13和上模模盒8之间,上模顶杆复位动力系统12带动上模顶杆向下移动,顶出成型产品和浇道;下模板7向上移动后,上模模盒8与下模模盒9贴合,其特征在于上模模盒8内的上中心浇道板和下模模盒9的下中心浇道板形成封闭的腔体,上模模盒8与下模模盒9内有胶道24,胶道24是空心的管道,和流道25连通,胶道24通过流道25与集成元件穴26相联通;注塑头4与腔体联通;加料筒31内的流质树脂由注塑头通过胶道24经过流道25注入流质树脂。
多注射头集成电路(IC)塑封模具的研制

所用塑封料为环氧树脂 , 不需预热, 流动性好 , 由于模具型腔容易充满 , 模温控制在 (7 5 ℃即 154 ) - 可。产品表面为亚光面 , 型腔经过两次 电加工可达 到要求。为了方便成型 , 要求预压 O 0 m, 2为 .2m 图
P 8 7塑封体 排 布 图 。 C1
位 针 孔
系统包括下推板 、 顶杆 、 弹簧复位装置 、 漂移式导柱
及导 向片 。
本模具共有 4组独立 的模盒( 它们都可以从侧
面抽 出 , 实现快换 ) 设计 型腔 数 为 60个 , 有 4组 , 4 设
独立的注射系统。下顶 出系统采用双推板结构 , 实 现 注射及 产 品 的顶 出动 作 。注 射 头 采 用浮 动 结 构 , 以保 汪各注射头同压注射。注射板采用漂移式导柱 及 导 向片结 构 , 以保 证 推 板 的平 稳 运 动 。模 具 有 4
高的精度要求 , 其主要特点如下 : () 1 流道更短 。传统 的塑封模 具流道很长 , 在 离料筒较远的地方易产生气泡 、 气孔或注不满的情 况, M P 而 G 模具 可以避免这种情况。 () 2 注射力均衡 。该副模具注射头采用浮动结 构, 保证各注射头压力均衡 。 () 3 不需预热。M P模具塑封料不需预热 , G 减 少了工序 , 提高了生产率。 () 4 塑封料利用率 提高。由于流道短 , 浪费的 塑封料少 , 利用率大大提高。 () 5 产品无浇 口。由于采用流道 直接充模 , 不 仅缩短了充模时间 , 降低 次品率 。还将每模的封装 产品由原来带浇 口模具的 5 2个提高到 60个, l 4 提 高了引线框架的利用率 , 降低了生产成本。 () 6 便于维修和装卸。模盒 和注射头都设计为 可以活动的组件, 方便维修和装卸。 笔者以电子 产 品 P 87为例 , 点介 绍 了该 C1 重 M P塑封模具研制过程中的关键技术。 G 1 零 件 工艺分 析 P 87产品如图 1 C1 所示 , 引线框架为 14铜合 9 金, 框架 的厚度为 ( .54 . 1 m 。本模 具设计 O 2 0 O ) m -
SOT系列MGP模具研发浅谈

SOT系列MGP模具研发浅谈汪宗华安徽中智光源科技有限公司技术开发部(安徽铜陵244000)【摘要】半导体产业的发展直接带动芯片封装的技术进步,而传统的单缸注胶头模具也已经满足不了先进封装的要求,多缸注胶头模具应运而生。
本文以SOT23制品塑模为例,谈谈多缸注胶头模具(MGP)结构与设计原理,从而推动集成电路模具发展。
关键词:集成电路;多缸注胶头;免预热;模盒结构;浇注系统;油缸中图分类号:TQ320.66文献标识码:BThe Research and Development of SOT Series MGP Mold 【Abstract】The development of the semiconductor industry directly promote technological progress in the chip package,the traditional single plunger rubber injection head mold also has been unable to meet the requirements of advanced packaging,multi plungers injection head mold came into being.This paper take SOT23products mold as an example,to discuss the structure and design principle of multi plungers glue injection head mold(MGP),so as to promote the development of IC mold.Key words:integrated circuit;multi plungers injection head;non pre-heating;mold structure; get system;cylinder1引言半导体产业景气的上升推动着国内封装技术的进步,中国的半导体制造业正慢慢进入成熟阶段,超高速计算机、数字化视听、移动通讯和便携式电子机器的火爆出现,直接带动芯片封装技术的进步。
集成电路多注射头塑封模具介绍

Word文档可进行编辑集成电路多注射头塑封模具介绍概述半导体产业景气得上升推动着国内封装技术得进步,中国得半导体制造业正慢慢进入成熟时期,超高速计算机、数字化视听、移动通讯和便携式电子机器得火爆出现,直截了当带动芯片封装技术得进步.芯片封装技术经历了好几代得变迁,从to、dip、sop、qfp、bga到csp再到mcm,封装形式由传统得单芯片封装向多芯片封装形式转变.封装形式得转变,导致封装模具应用技术不断提高,传统得单注射头封装模已满足不了封装要求.模具结构由单缸模——多注射头封装模具——集成电路自动封装系统方向进展,下面就多注射头塑封模具得特点做一概括介绍.1与传统塑封模具性能对比多注射头塑封模与传统单缸模相比要紧有以下优点:(1)采纳等流长冲填,产品质量稳定单缸模具采纳一个加料腔注射,树脂由近到远先后充填型腔、由于环氧树脂须在高温高压下在一定得时刻范围内快速充满型腔,树脂在充填过程中由粘流态向玻璃态转变,流淌性能逐渐变差,在流道末段得型腔压力损耗大,型腔内树脂成型条件恶劣、因此在远离加料腔得产品易出现气泡、气孔、注不满、金丝冲弯率超标等现象,模具成型工艺调整范围窄.c多注射头模具则可有效幸免此现象,它采纳多个加料腔同步注射,树脂同時充填型腔,制品封装质量高,封装工艺稳定,成型工艺调整范围宽.但多注射头模具需解决多个注射头同步工作时,因每个加料腔中树脂体积误差造成得冲填疏松咨询题,因为一般塑封料在打饼后重量误差为±02克,如比重为20克/cm3,直径为φ13mm得小树脂其对应φ14mm得料筒在注射后,料筒中树脂残留将有13mm得高低差.假如注射头设置为刚性结构则树脂体积多得料筒对应得型腔能充满,而树脂体积少得料筒对应得型腔则会出现产品疏松得咨询题,因此多注射头模具得每个注射头下一般设置弹簧或液压得缓冲机构以解决刚性注射咨询题.(2)树脂利用率高多注射头模具流道短,流道截面积小,假如做同一种产品,相对传统单缸模具而言,则多注塑头模具使用树脂利用率高,可为客户节约成本.(3)生产效率高多注射头模具采纳免预热型小直径树脂(φ10~φ18),而单缸模具采纳预热型大直径树脂(φ35~φ58),因此树脂成型固化时刻差异较大,一般多注射头模具为60~90秒,而单缸模具为120~180秒,因此生产效率提高了一倍以上,满足封装厂家对产品质量和产量得不断追求.(4)型腔更换维护方便单缸模得模盒与模板之间采纳销钉与螺钉进行固定,如型腔损坏更换,拆装时刻较长,一般在5小时左右.而多注射头塑封模得模盒与模板之间一般采纳导轨固定,如型腔损坏只需将模盒从导轨中抽屉一般抽出即可,更换维护时刻在15小时左右. 综上所述将二种模具性能对比列表如下:传统单缸模与多注射头模具性能对比2多注射头模具注射压力得设定一般我们需要通过塑封树脂得特性确定塑封时得实际压力,从而计算出压机设定得表头压力.因为每副多注射头模具得注射油缸大小、数量及注射头得大小、数量不同,及机械损失和压力表误差等妨碍,因此要进行适当得计算来设定压机得表头压力,从而满足塑封工艺参数得需要.计算公式如下:pc=压机表头压力(kg/cm2),np=注射头数量,dp=注射头直径(cm),nc=注射油缸数量,dc=注射油缸缸径(cm),pp=包塑时树脂所需得成形压力一般在60~120kg/cm2范围内,具体依照树脂特性选定,11=安全系数.例:当注射头数量为28个,直径为φ14mm,油缸数量为1个,缸径为φ120mm,树脂成形压力为100kg/cm2,则表头压力=3模具系列为习惯不同产品得要求,多注射头塑封模具目前有以下几种结构.31标准多注射头塑封模具模具设置4组~8组模盒,每个模盒二条引线框架,加料腔设计在中心镶件上,数量依照l/f特点设置,使用免预热型小直径树脂.模盒采纳快换式结构,注射机构快换,注射推板得平衡采纳齿轮齿条及自润滑导柱导套结构,油缸一般采纳二个φ80mm缸径得油缸.结构:料筒设置在下模模盒中;注射头组件采纳快换结构;模盒快换.注射方式:下注式.注射动力:下模内置油缸.使用塑封料:免预热型塑封料(直径φ9~φ18).适用产品:tsop、qfp、sot、sop、bga等中高档产品.32下中心浇道板式多注射头塑封模模具设置6组~8组模盒,每个模盒二条引线框架,加料腔设计在模具中心位置上,数量依照l/f特点设置,使用免预热型小直径树脂.模盒与注射机构一般不采取快换结构,注射推板得平衡采纳自润滑导柱导套结构,油缸一般采纳一个φ63mm缸径得油缸.结构:料筒设置在下中心浇道板内,注射头座固定在注射推板上.注射方式:下注式.注射动力:下模内置油缸.使用塑封料:免预热型塑封料(直径φ9~φ18).适用产品:sot、sod、片钽类、tr类产品.33上中心浇道板式多注射头塑封模模具一般设置6~8组模盒,料筒设计在上模中心镶件上,数量依照l/f特点设置,适用免预热型小直径树脂.模盒采纳快换式结构,注射推板得平衡采纳齿轮齿条及自润滑导滑块结构,模具内无油缸,注射动力来自压机得注射油缸.使用注意事项:模具每次在升温重新生产前,需通过上下模架二端边挡块得紧定螺钉将组件与浇道板顶死,确保封装时镶件与浇道板之间不溢料,防止产品x向错位.针对产品sod、sot、钽电容等引线框架宽度较窄产品.结构:料筒设置在上中心浇道板内,注射推板与压机注射杆连接.注射方式:上注射式.注射动力:压机注射油缸.使用塑封料:免预热型塑封料(直径φ9~φ18).适用产品:sod、片钽和to类产品.34大料饼多注射头封装模具模具一般设置8组模盒,二个料筒,适用传统单缸模用预热型大直径树脂.模盒采纳快换式结构,注射推板得平衡采纳齿轮齿条及自润滑导滑块结构,油缸一般采纳二个φ80mm缸径得油缸,行程70mm左右.使用注意事项:模具每次在升温重新生产前,需通过上下模架二端边挡块得紧定螺钉将组件与浇道板顶死,确保封装时镶件与浇道板之间不溢料,防止产品x向错位.针对产品sod、to、dip、钽电容等单排产品. 结构:料筒设置在下中心浇道板内,料筒数量在3只以下.注射方式:下注射式.注射动力:下模内置油缸.使用塑封料:一般预热型塑封料(直径φ35~φ58).适用产品:to类产品,如to-92,to3p,to263等.4技术关键多注射头模具注射推板得平衡;硬质合金料筒、注射头得寿命及注射动力得平衡设计是多注射头模具可靠、稳定生产得关键,下面逐一介绍.41模具注射推板平衡机构多注射头模具使用得稳定性关键点之一在于注射推板平衡机构工作得稳定,由于多注射头塑封模在高温、多尘环境下工作,因此设计时一般采取齿轮、齿条啮合得方式确保动作顺畅.如下图42硬质合金料筒、注射头得寿命注射头、料筒硬质合金材料优选高耐磨、超细微颗粒得硬质合金,既要考虑硬度也要考虑韧性,如我司开始使用得富士f10材料就因为脆性较大,易出现崩裂咨询题,寿命不高.后落低硬度改为f20后,注射头、料筒得使用寿命得到显著提高;另外需强调注射头连接内螺纹孔加工得合理性,若采纳烧结成型得螺纹,由于牙形角不规则,牙底尖角应力集中,使用寿命较低,容易出现拉断现象,因此要求注射头内螺纹采纳电火花加工,牙底尖角圆弧过渡,则改善了注射头因螺纹孔加工不规范造成拉伤现象得发生.43注射动力得平衡设计(油路得平衡)多注射头模具得推板一般采纳二个油缸负责顶出与复位,因此设计时应该考虑油缸活塞同步上下,油路设计时不能采纳串联式进油,而须采纳并联式进油,确保注射推板受力平衡,工作稳定.5小结通过本文得介绍,盼望读者能了解集成电路多注射头封装模具得概况及不同模具结构得特点所习惯得产品种类.在目前大多数企业引进海外先进技术得同时,我们更加关注如何推动国内封装技术水平得进展,如何加快国产封装设备业得研发创新,促进。
注塑模具设计手册第5章注射模概述.ppt

高等学校应用型特色规划教材
5.2
注射模与注射机的关系
5.2.1 注射量的校核 • 注射机额定注射量表示方法有两种:一是以容量(cm3)表示, 一是用质量(g)表示。国产的标准注射机其注射量均以容量表 示。 5.2.2 注射压力的校核 5.2.3 塑件在分型面上的投影面积和锁模力的校核
高等学校应用型特色规划教材
5.1
注射模的基本结构
5.1.1 注射模的结构组成 根据模具上各部件的功能,一般注射模可由以下几个部分组成。 • 1. 成型零部件 • 2. 浇注系统 • 3. 导向机构 • 4. 侧向分型与抽芯机构 • 5. 脱模机构 • 6. 温度调节系统 • 7. 排气系统 • 8. 支承零部件
高等学校应用型特色规划教材
• • • • • •
5.2.4 安装尺寸的校核 1. 喷嘴尺寸 2. 定位环尺寸 3. 模具厚度 4. 模具长度与宽度 5. 安装螺孔尺寸
高等学校应用型特色规划教材
5.2.5 开模行程的校核 • 1. 注射机最大开模行程与模具厚度无关时的校核 • 2. 注射机最大开模行程与模具厚度有关时的校核 • 3. 模具具有侧向抽芯时的最大开模距离的校核
高等学校应用型特色规划教材
• 2) 斜滑块侧向分型注射模 • (1) 工作原理 • (2) 设计注意事项
高等学校应用型特色规划教材
• 4. 带活动镶块注射模
高等学校应用型特色规划教材
• 5. 定模部分设有推出机构的注射模
高等学校应ห้องสมุดไป่ตู้型特色规划教材
• 6. 角式注射机用注射模 • 7. 无流道凝料注射模
5.2.6
顶出装置的校核
高等学校应用型特色规划教材
思 考 题
• 1. 典型的注射模由哪几部分组成?各部分的作用是 什么? • 2. 常用注射模有哪几种?它们的工作原理如何? • 3. 注射模设计时为什么要与注射机的相关参数进行 校核?
- 1、下载文档前请自行甄别文档内容的完整性,平台不提供额外的编辑、内容补充、找答案等附加服务。
- 2、"仅部分预览"的文档,不可在线预览部分如存在完整性等问题,可反馈申请退款(可完整预览的文档不适用该条件!)。
- 3、如文档侵犯您的权益,请联系客服反馈,我们会尽快为您处理(人工客服工作时间:9:00-18:30)。
集成电路多注射头塑封模具介绍
概述半导体产业景气的上升推动着国内封装技术的进步,中国的半导体制造业正慢慢进入成熟阶段,超高速计算机、数字化视听、移动通讯和便携式电子机器的火爆出现,直接带动芯片封装技术的进步。
芯片封装技术经历了好几代的变迁,从TO、DIP、SOP、QFP、BGA到CSP再到MCM,封装形式由传统的单芯片封装向多芯片封装形式转变。
封装形式的转变,导致封装模具应用技术不断提高,传统的单注射头封装模已满足不了封装要求。
模具结构由单缸模——多注射头封装模具——集成电路自动封装系统方向发展,下面就多注射头塑封模具的特点做一概括介绍。
1 与传统塑封模具性能对比
多注射头塑封模与传统单缸模相比主要有以下优点:
(1)采用等流长冲填,产品质量稳定
单缸模具采用一个加料腔注射,树脂由近到远先后充填型腔、由于环氧树脂须在高温高压下在一定的时间范围内快速充满型腔,树脂在充
填过程中由粘流态向玻璃态转变,流动性能逐渐变差,在流道末段的型腔压力损耗大,型腔内树脂成型条件恶劣、因此在远离加料腔的产品易出现气泡、气孔、注不满、金丝冲弯率超标等现象,模具成型工艺调整范围窄。
多注射头模具则可有效避免此现象,它采用多个加料腔同步注射,树脂同時充填型腔,制品封装质量高,封装工艺稳定,成型工艺调整范围宽。
但多注射头模具需解决多个注射头同步工作时,因每个加料腔中树脂体积误差造成的冲填疏松问题,因为一般塑封料在打饼后重量误差为±0.2克, 如比重为2.0克/cm3,直径为φ13mm的小树脂其对应φ14mm的料筒在注射后,料筒中树脂残留将有1.3mm的高低差。
如果注射头设置为刚性结构则树脂体积多的料筒对应的型腔能充满,而树脂体积少的料筒对应的型腔则会出现产品疏松的问题,因此多注射头模具的每个注射头下一般设置弹簧或液压的缓冲机构以解决刚性注射问题。
(2)树脂利用率高
多注射头模具流道短,流道截面积小,如果做同一种产品,相对传统单缸模具而言,则多注塑头模具使用树脂利用率高,可为客户节约成本。
(3)生产效率高
多注射头模具采用免预热型小直径树脂(Φ10~Φ18),而单缸模具采用预热型大直径树脂(Φ35~Φ58),因此树脂成型固化时间差异较大,一般多注射头模具为60~90秒,而单缸模具为120~180秒,因此生产效率提高了一倍以上,满足封装厂家对产品质量和产量的不断追求。
(4)型腔更换维护方便
单缸模的模盒与模板之间采用销钉与螺钉进行固定,如型腔损坏更换,拆装时间较长,一般在5小时左右。
而多注射头塑封模的模盒与模板之间一般采用导轨固定,如型腔损坏只需将模盒从导轨中抽屉一般抽出即可,更换维护时间在1.5小时左右。
综上所述将二种模具性能对比列表如下:
传统单缸模与多注射头模具性能对比
2 多注射头模具注射压力的设定
一般我们需要通过塑封树脂的特性确定塑封时的实际压力,从而计算出压机设定的表头压力。
因为每副多注射头模具的注射油缸大小、数量及注射头的大小、数量不同,及机械损失和压力表误差等影响,因此要进行适当的计算来设定压机的表头压力,从而满足塑封工艺参数的需要。