纤维的应用
纤维知识小常识

纤维知识小常识
纤维是人们日常生活中不可或缺的一部分,它存在于我们的衣物、家居用品、食品等多个领域。
了解纤维的基本知识,对于我们更好地选择和使用纤维制品具有重要意义。
一、纤维的分类
纤维主要分为天然纤维和合成纤维两大类。
天然纤维包括棉、麻、丝、毛等,它们具有吸湿性好、透气性好、弹性好等优点。
合成纤维则是由石油化工原料经过聚合反应制成的,常见的有涤纶、尼龙、腈纶等。
二、纤维的特性
1.吸湿性:纤维的吸湿性是指纤维吸收空气中水蒸气的能力。
吸湿性好的纤
维能够保持皮肤的干爽,减少过敏和皮肤疾病的发生。
2.透气性:纤维的透气性是指纤维让空气通过的能力。
透气性好的纤维能够
保持皮肤的呼吸畅通,避免汗液滞留在皮肤上。
3.弹性:纤维的弹性是指纤维在受到外力作用后恢复原状的能力。
弹性好的
纤维能够提供更好的穿着舒适度和耐用性。
三、纤维的应用
1.纺织品:纤维是纺织品的主要原料,包括衣物、床品、家纺等。
不同的纤
维具有不同的特性,因此适用于不同的纺织品。
2.建筑材料:纤维可以用于制造建筑材料,如玻璃纤维增强混凝土、碳纤维
增强塑料等,具有轻质、高强、耐久等优点。
3.食品加工:纤维可以用于制作食品,如膳食纤维、可溶性膳食纤维等,具
有改善肠道健康、降低胆固醇等作用。
4.医疗卫生:纤维在医疗卫生领域也有广泛应用,如用于制造医疗器械、药
物载体等。
总之,了解纤维的基本知识对于我们更好地选择和使用纤维制品具有重要意义。
高功能纤维的定义及其应用范围
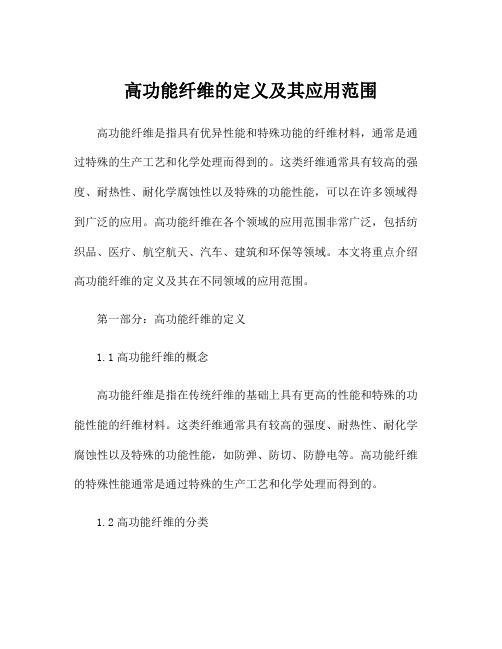
高功能纤维的定义及其应用范围高功能纤维是指具有优异性能和特殊功能的纤维材料,通常是通过特殊的生产工艺和化学处理而得到的。
这类纤维通常具有较高的强度、耐热性、耐化学腐蚀性以及特殊的功能性能,可以在许多领域得到广泛的应用。
高功能纤维在各个领域的应用范围非常广泛,包括纺织品、医疗、航空航天、汽车、建筑和环保等领域。
本文将重点介绍高功能纤维的定义及其在不同领域的应用范围。
第一部分:高功能纤维的定义1.1高功能纤维的概念高功能纤维是指在传统纤维的基础上具有更高的性能和特殊的功能性能的纤维材料。
这类纤维通常具有较高的强度、耐热性、耐化学腐蚀性以及特殊的功能性能,如防弹、防切、防静电等。
高功能纤维的特殊性能通常是通过特殊的生产工艺和化学处理而得到的。
1.2高功能纤维的分类高功能纤维根据其性能和功能可分为多种不同的类型,如高强度纤维、耐热纤维、防弹纤维、防切纤维、防静电纤维等。
每种类型的高功能纤维都具有特殊的性能和应用特点。
1.3高功能纤维的生产工艺高功能纤维的生产需要经过特殊的工艺流程和化学处理。
通常包括原料的挑选、纤维的拉丝、纺纱、织造、化学处理等多个环节。
这些工艺环节都需要精密的设备和工艺技术支持。
第二部分:高功能纤维在纺织品领域的应用2.1功能性纤维的材料和特点在纺织品领域,功能性纤维的应用颇为广泛,例如超级吸湿纤维的应用可以降低体温,排湿纳凉,抑菌防臭等。
它采用精细的工艺,通过其内部结构的改变,使得它成为了超级纳米纤维材料,表示纤维的单纤度能最终降低到200—300纳米大小,结构的多孔性、阳离子等其特殊性能。
2.2防弹纤维的应用高功能纤维在纺织品领域的一个重要应用是在防弹服和防弹材料中。
高强度和耐热性是防弹纤维的主要特点,它可以提供卓越的抗弹和抗切能力,保护穿戴者的安全。
2.3抗菌纤维的应用另一种功能性纤维的应用,是在医疗纺织品上。
抗菌纤维被广泛应用于医用纺织品,如医用口罩、医用衣物、医用手套等,它可以有效地杀灭细菌,减少交叉感染的风险,保护医护人员和患者的健康。
碳纤维在生活中的应用
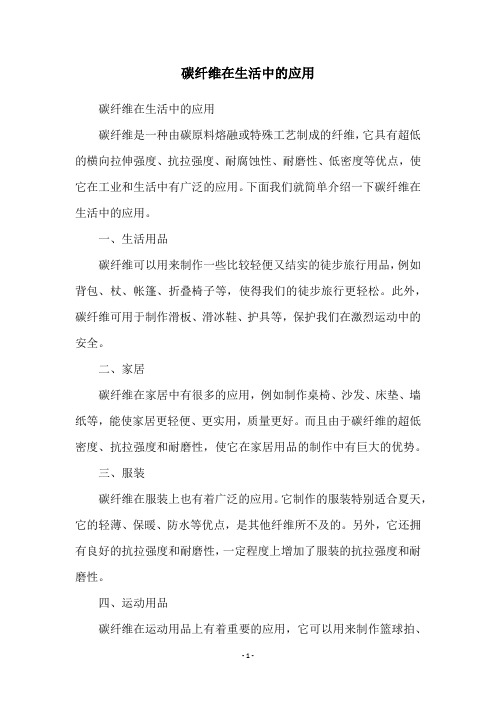
碳纤维在生活中的应用
碳纤维在生活中的应用
碳纤维是一种由碳原料熔融或特殊工艺制成的纤维,它具有超低的横向拉伸强度、抗拉强度、耐腐蚀性、耐磨性、低密度等优点,使它在工业和生活中有广泛的应用。
下面我们就简单介绍一下碳纤维在生活中的应用。
一、生活用品
碳纤维可以用来制作一些比较轻便又结实的徒步旅行用品,例如背包、杖、帐篷、折叠椅子等,使得我们的徒步旅行更轻松。
此外,碳纤维可用于制作滑板、滑冰鞋、护具等,保护我们在激烈运动中的安全。
二、家居
碳纤维在家居中有很多的应用,例如制作桌椅、沙发、床垫、墙纸等,能使家居更轻便、更实用,质量更好。
而且由于碳纤维的超低密度、抗拉强度和耐磨性,使它在家居用品的制作中有巨大的优势。
三、服装
碳纤维在服装上也有着广泛的应用。
它制作的服装特别适合夏天,它的轻薄、保暖、防水等优点,是其他纤维所不及的。
另外,它还拥有良好的抗拉强度和耐磨性,一定程度上增加了服装的抗拉强度和耐磨性。
四、运动用品
碳纤维在运动用品上有着重要的应用,它可以用来制作篮球拍、
排球拍、网球拍以及乒乓球拍等运动用品,使运动用品更轻便、更结实,提升比赛水平。
总之,碳纤维在生活中有着多种应用,它的出现给我们的生活带来了极大的方便。
纤维的再生利用范文

纤维的再生利用范文
摘要:纤维的再生利用是近年来崭露头角的环保和可持续发展技术。
随着全球资源日益短缺,纤维再生利用已经成为一种重要的方式来缓解资源限制和环境污染。
本文将详细介绍纤维再生利用的原理、方法和应用,并探讨其在可持续发展中的潜力和前景。
第一章:纤维再生利用的原理
1.1纤维再生利用的定义和意义
1.2纤维再生利用的分类
1.3纤维再生利用的原理
第二章:纤维再生利用的方法
2.1机械再生方法
2.2化学再生方法
2.3物理再生方法
第三章:纤维再生利用的应用
3.1纤维再生利用在纺织工业中的应用
3.2纤维再生利用在建筑材料中的应用
3.3纤维再生利用在环境保护中的应用
第四章:纤维再生利用的优势和挑战
4.1纤维再生利用的优势
4.2纤维再生利用面临的挑战
第五章:纤维再生利用的潜力和前景
5.1纤维再生利用的潜力
5.2纤维再生利用的前景
第六章:结论
通过对纤维再生利用的研究,可以看出它对于资源限制和环境污染问题具有重要的意义。
纤维再生利用不仅可以节约有限的资源和能源,还可以减少废弃物的产生。
然而,纤维再生利用在技术上还面临一些挑战,如材料的再生率和再生后材料的性能等。
随着科技的发展和创新,相信这些问题将会逐渐得到解决,纤维再生利用的潜力和前景将会更加广阔。
服装纤维知识点总结图

服装纤维知识点总结图一、纤维的分类1.1 植物纤维植物纤维是指从植物中提取的纤维,主要包括棉、麻、竹、木质纤维等。
其中,棉纤维是最常见的植物纤维,具有柔软、吸湿性好、透气性好等特点,适合用于制作夏季服装。
麻纤维具有耐磨损、透气性好、吸湿性强等特点,适合用于制作夏季服装。
竹纤维具有抗菌、防臭、吸湿性强等特点,适合用于制作内衣等服装。
木质纤维具有光滑、柔软、透气性好等特点,适合用于制作贴身服装。
1.2 动物纤维动物纤维是指从动物身上提取的纤维,主要包括羊毛、丝绸、羊绒等。
其中,羊毛具有保暖性好、弹性好、吸湿性强等特点,适合用于制作冬季服装。
丝绸具有光滑、柔软、透气性好等特点,适合用于制作高档礼服等服装。
羊绒具有保暖性好、柔软、舒适性好等特点,适合用于制作冬季外套等服装。
1.3 化学纤维化学纤维是通过化学方法合成的纤维,主要包括涤纶、锦纶、腈纶等。
其中,涤纶具有耐磨损、易清洗、抗皱性好等特点,适合用于制作运动服、工作服等服装。
锦纶具有弹性好、耐磨损、不易变形等特点,适合用于制作内衣、泳衣等紧身服装。
腈纶具有保暖性好、弹性好、耐磨损等特点,适合用于制作冬季外套等服装。
1.4 矿物纤维矿物纤维是由矿物质加工而成的纤维,主要包括玻璃纤维、石棉纤维等。
其中,玻璃纤维具有耐高温、耐腐蚀、绝缘性好等特点,适合用于制作防护服等特种服装。
石棉纤维具有耐高温、耐磨损、防火性能好等特点,适合用于制作特种防护服等服装。
二、纤维的性能2.1 强度纤维的强度是指纤维在拉伸时承受的力量大小。
通常情况下,纤维的强度越高,其耐磨损性和耐拉伸性就越好,适合用于制作耐磨损、耐拉伸的服装。
2.2 弹性纤维的弹性是指纤维在拉伸后能否恢复原状的能力。
通常情况下,纤维的弹性越好,其服装在使用过程中不易变形,给人穿着舒适的感觉。
2.3 吸湿性纤维的吸湿性是指纤维吸取水分的能力。
通常情况下,纤维的吸湿性越好,其服装在夏季穿着时不易粘身,给人带来凉爽的感觉。
纤维材料在工程领域的应用与研究进展
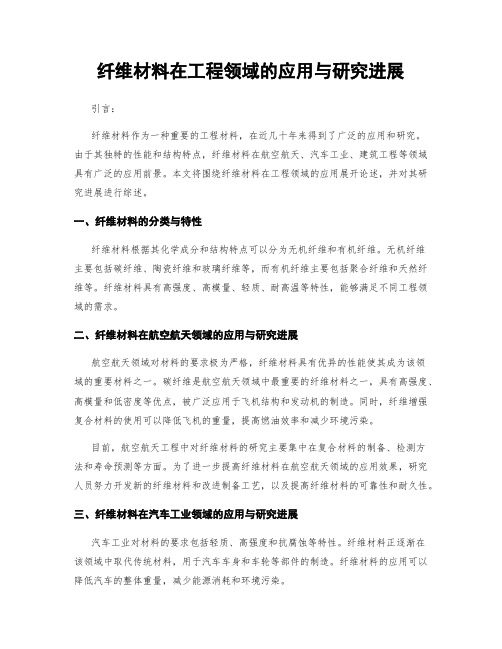
纤维材料在工程领域的应用与研究进展引言:纤维材料作为一种重要的工程材料,在近几十年来得到了广泛的应用和研究。
由于其独特的性能和结构特点,纤维材料在航空航天、汽车工业、建筑工程等领域具有广泛的应用前景。
本文将围绕纤维材料在工程领域的应用展开论述,并对其研究进展进行综述。
一、纤维材料的分类与特性纤维材料根据其化学成分和结构特点可以分为无机纤维和有机纤维。
无机纤维主要包括碳纤维、陶瓷纤维和玻璃纤维等,而有机纤维主要包括聚合纤维和天然纤维等。
纤维材料具有高强度、高模量、轻质、耐高温等特性,能够满足不同工程领域的需求。
二、纤维材料在航空航天领域的应用与研究进展航空航天领域对材料的要求极为严格,纤维材料具有优异的性能使其成为该领域的重要材料之一。
碳纤维是航空航天领域中最重要的纤维材料之一,具有高强度、高模量和低密度等优点,被广泛应用于飞机结构和发动机的制造。
同时,纤维增强复合材料的使用可以降低飞机的重量,提高燃油效率和减少环境污染。
目前,航空航天工程中对纤维材料的研究主要集中在复合材料的制备、检测方法和寿命预测等方面。
为了进一步提高纤维材料在航空航天领域的应用效果,研究人员努力开发新的纤维材料和改进制备工艺,以及提高纤维材料的可靠性和耐久性。
三、纤维材料在汽车工业领域的应用与研究进展汽车工业对材料的要求包括轻质、高强度和抗腐蚀等特性。
纤维材料正逐渐在该领域中取代传统材料,用于汽车车身和车轮等部件的制造。
纤维材料的应用可以降低汽车的整体重量,减少能源消耗和环境污染。
在汽车工业中,碳纤维和玻璃纤维是最常用的纤维材料。
碳纤维由于其高强度和高刚度的特点,被广泛应用于赛车以及高端豪华汽车的制造。
而玻璃纤维则具有良好的抗腐蚀性能和低成本,适用于大量生产以及安全性要求不高的汽车。
目前,研究人员还致力于开发新型的纤维材料,以满足汽车工业对更轻、更强材料的需求。
此外,纤维材料的回收与再利用也成为研究的重点,以减少资源消耗和环境负荷。
纤维材料的力学性能与应用研究

纤维材料的力学性能与应用研究随着科学技术的不断进步,纤维材料在现代工程领域中得到广泛应用。
纤维材料的力学性能对其应用性能起着至关重要的作用。
本文将介绍纤维材料的力学性能以及其在不同领域的应用研究。
一、纤维材料的力学性能1. 强度:纤维材料的强度是指材料能够承受的最大外力。
常见的纤维材料如碳纤维、玻璃纤维等具有较高的强度,能够在应力作用下保持较好的稳定性。
2. 刚度:纤维材料的刚度是指材料对变形的抵抗能力。
刚度较高的材料具有较低的变形能力,适用于需要保持形状稳定的结构和设备。
3. 韧性:纤维材料的韧性是指材料在受力后能够发展出的塑性变形能力。
相比于脆性材料,具有较高韧性的纤维材料更能够抵抗外界冲击和振动。
4. 耐磨性:纤维材料的耐磨性是指材料表面抵抗磨损的能力。
一些纤维材料具有较好的耐磨性,适用于摩擦和磨损较为频繁的场合。
二、纤维材料的应用研究1. 汽车工业:汽车制造行业对材料的强度和刚度要求较高。
纤维材料的高强度和轻质特性使其成为汽车制造的重要材料。
例如,碳纤维复合材料被广泛应用于汽车车身和零部件的制造,提高了汽车的整体性能和燃油经济性。
2. 航空航天工业:航空航天领域对材料的强度、刚度和轻量化要求极高。
纤维材料的独特性能使其成为航空航天工业的研究热点。
例如,玻璃纤维增强塑料在航空航天结构中的应用有助于提高飞机的安全性和飞行效率。
3. 建筑领域:纤维材料在建筑领域中具有广泛的应用前景。
纤维增强混凝土和玻璃纤维增强塑料等材料被用于加固和增强建筑结构,提高其抗震性能和使用寿命。
4. 医疗领域:纤维材料在医疗领域也有重要的应用。
例如,某些生物可降解的纤维材料被用于制造缝合线和植入物,具有良好的生物相容性和组织再生能力。
5. 环境工程:纤维材料在环境工程中的应用主要体现在过滤材料和污水处理等方面。
纤维材料的高表面积和过滤效率使其成为处理废水和废气的有效材料。
三、结论纤维材料的力学性能是其在不同领域应用研究的基础。
纤维的分类及发展PPT课件

20世纪初,合成纤维开始出现并逐渐取代天然纤维。随着科技的进步,合成纤 维的性能不断优化,如强度、耐磨性、耐热性等方面的提升,使其在纺织、工 程、航空航天等领域得到广泛应用。
高性能纤维的研发和应用
高性能纤维
是指具有高强度、高模量、耐高温、耐化学腐蚀、低密度等一系列优异性能的纤 维。常见的有碳纤维、玻璃纤维、芳纶等。
天然纤维发展
随着人们对自然环境的日益关注,天然纤维因其环保、可持续的 特点而受到重视。植物纤维如亚麻、大麻等逐渐被更多人认识和 应用,动物纤维如羊毛、蚕丝等也因其独特的性能而受到研究和 开发。
合成纤维的发明和发展
合成纤维
是指用天然的或人工合成的高分子物质为原料、经过化学加工和纺丝而制得的 纤维。常见的合成纤维有涤纶、锦纶、腈纶、维纶、丙纶、氯纶等。
05
未来纤维的发展趋势和挑战
高性能纤维的进一步研发和应用
高性能纤维是指具有优异力学性能、 耐高温、耐腐蚀等特性的纤维,如碳 纤维、芳纶纤维等。随着科技的进步 和应用领域的拓展,高性能纤维的需 求量不断增长,未来将有更多的高性 能纤维被研发出来,应用于航空航天、 汽车、体育器材等领域。
VS
碳纤维是一种高性能纤维,具有高强 度、高模量、轻质等优点,广泛应用 于航空航天、汽车、体育器材等领域。 未来,随着碳纤维生产技术的不断改 进和成本的不断降低,碳纤维的应用 领域将进一步拓展。
THANK YOU
感谢聆听
02
纤维的分类
天然纤维
定义
天然纤维是从自然界中获取的纤维,如棉花、羊毛 、亚麻等。
特点
天然纤维具有良好的透气性、保暖性和舒适性,对 人体无害,且易于生物降解。
应用
天然纤维广泛应用于纺织、服装、家居用品等领域 。
- 1、下载文档前请自行甄别文档内容的完整性,平台不提供额外的编辑、内容补充、找答案等附加服务。
- 2、"仅部分预览"的文档,不可在线预览部分如存在完整性等问题,可反馈申请退款(可完整预览的文档不适用该条件!)。
- 3、如文档侵犯您的权益,请联系客服反馈,我们会尽快为您处理(人工客服工作时间:9:00-18:30)。
Fibers and Polymers 2011, Vol.12, No.1, 95-10395Modification of Natural Bamboo Fibers for Textile ApplicationsLifang Liu 1,2, Qianli Wang 1,2, Longdi Cheng 1,2, Jingfang Qian 1,2, and Jianyong Yu 1,3*1The Key Lab of Textile Science & Technology, Ministry of Education, Donghua University, Shanghai 201620, China2College of Textiles, Donghua University, Shanghai 201620, China 3Modern Textile Institute, Donghua University, Shanghai 200051, China(Received March 5, 2010; Revised August 6, 2010; Accepted September 25, 2010)Abstract: Natural bamboo fibers have excellent properties suggesting that there is a good potential for them to be used in tex-tiles; however, they have not received the attention that they deserve owing to their coarse and stiff quality. Therefore, a chemical method for extraction and modification of natural bamboo fibers for textile end uses were developed and optimized in this paper. The quality of natural bamboo fibers were characterized by their chemical composition, linear density, and tenacity. Experimental results show that the modified bamboo fibers are finer, with significant lower content of noncellulosic substances. The processing parameters are optimized as: 20 g/l NaOH, 3 g/l Na 5P 3O 10, 5 g/l Na 2SO 3, 3 g/l penetrating agent,with a fiber to liquid ratio of 1:10, at 100o C for 2 h, and the bamboo fiber thus produced has cellulose amount of 73.25%,fineness of 3.26 tex, average length of 44.5 mm, breaking elongation of 2.8% and tenacity of 2.41 cN/dtex. The result of this study may offer a possibility of developing natural bamboo fibers into practical applications in textiles.Keywords: Natural bamboo fiber, Chemical modification, Chemical composition, Linear density, TenacityIntroductionNatural cellulose fibers have received increasing attention because of their biodegradability and renewable resources in comparison to synthetic fibers [1-3]. Cotton and bast fibers,especially cotton fibers, are important textile materials,primarily because of their more cost-efficient production and nearly universal product possibilities [1]. However, regarding another abundant renewable biomass material, the natural bamboo fibers, they have not received the attention that they deserve owing to their coarse and stiff quality, although bamboo pulp viscose fibers, also called bamboo fibers sometimes, have already been used for textiles products [4].Natural bamboo fibers are extracted from bamboos which have long been widely used for constructional purpose, for the pulp and paper in industry, and also for the natural fibers reinforced composites [5,6]. Like bast fibers, such as flax,hemp, jute, and ramie, natural bamboo fibers morphologically exist as technical fibers consisted of elementary fibers (usually with length of 1.9mm and width of 15.3µm)concreted together by noncellulosic substances (lignin,hemicellulose, pectin, and so on) [1,5,7-11]. Although the noncellulosic substances are contributed to hold those very short elementary fibers together, they are also responsible for the coarse and stiff quality of natural bamboo fibers. The main task in producing natural bamboo fibers for textile applications is to partially remove noncellulosic substances without damage to the fiber cellulose. It should be remarked that the natural bamboo fibers have not been successfully applied for textile products until now; however, there is a good potential for their application in textiles regarding their excellent properties, such as aseptic properties, high absorbencyand hygroscopicity, good electrostatic, and ultraviolet resistant properties [1,3,12]. Therefore, it is very interesting to investigate the extraction and modification of natural bamboo fibers for textile end uses.Chemical, biological, mechanical methods, or their combin-ation are usually used to modify bast fibers, among which chemical method is used most commonly [10,13-17].Chemical method is based on the mechanism that the cellulosic fibrils and noncellulosic substances have different stability in alkaline solution. It is a rapid and efficient process compared to that of biological or mechanical method, which usually involves the soaking of bast fibers in aqueous alkaline solutions, such as the solution of sodium hydroxide (NaOH), potassium hydroxide (KOH), and sodium carbonate (Na 2CO 3) [16]. Experiments showed the cheap and commercial available NaOH can dissolve and remove non-cellulosic substances by a swelling reaction without observable decomposition of cellulosic fibrils, so as to make the fiber finer, softer, and more suitable for textile processing [16,17].As for natural bamboo fibers, chemical method is also used most commonly. Kushwaha and Kumar [18] treated bamboo strips with NaOH solution with different concen-tration of 1~25% for 30 min at room temperature (20o C),and found that the composites have better mechanical properties at 5% of NaOH. Das et al. [19-21] conducted alkali treatments on bamboo strips with caustic soda solution with varying concentration (10, 15, 20, and 50%) for 1 h at ambient temperature. However, all of those researches were conducted on bamboo strips for the enhancement of composites; regarding the extraction of natural bamboo fibers for textiles end uses, there are little relative reports.Therefore, the chemical method is applied in this paper to extract and modify natural bamboo fibers. NaOH is also*Corresponding author: yu_jianyong@DOI 10.1007/s12221-011-0095-396Fibers and Polymers 2011, Vol.12, No.1Lifang Liu et al.selected to extract finer fibers, and its concentration is optimized in terms of fiber characteristics. Moreover, three additives, Na 5P 3O 10, Na 2SiO 3, and penetrating agent are also introduced to enhance the effects of NaOH, and their concentrations are optimized by orthogonal design method.Furthermore, the optimum treating temperature and time are also discussed to produce natural bamboo fibers with improved quality. The present study aims at offering a possibility of developing natural bamboo fibers into practical applications in textiles.ExperimentalMaterialsThe bamboo strips used to extract fibers in this study were split from the stems of natural bamboo produced in China.This bamboo as shown in Figure 1, which belongs to Phyllostachys Pubescens , was dried for more than 1 year in ambient conditions, and cut to 60 mm before use. All the chemicals used here were reagent grade and used without further purification.MethodsPretreatmentThe bamboo strips were firstly pretreated by soaking into 2 g/l H 2SO 4 solution with a strip to liquid ratio of 1:30 at 20±2o C for 24 h, followed by heating at 50o C for 1h,washed and vacuum-dried at 60o C for 8 h; then they were immersed into 100 g/l NaOH solution with a strip to liquid ratio of 1:20 at 20±2o C for 24 h, followed by heating at 60o C for 2 h, washed, and vacuum-dried at 60o C for 8 h.Chemical TreatmentAll the experiments were conducted on a high temperature laboratory dying machine (RY -1261, Shanghai Longling laboratory Instruments Co. Ltd., China). (1) Optimization of NaOH concentrationThe pretreated bamboo fibers were soaked into NaOH solution with different concentration (5, 10, 15, 20, 25, and 30 g/l ), with a fiber to liquid ratio of 1:10, at 90o C for 2 h.(2) Optimization of additives concentrationThe pretreated bamboo fibers were immersed into a mixed solution with NaOH at optimum concentration and the three additives, Na 5P 3O 10, Na 2SiO 3, and penetrating agent at different concentration, as shown in Table 1. The experiments were conducted with a fiber to liquid ratio of 1:10 at 90o C for 2 h.(3) Optimization of temperatureThe pretreated bamboo fibers were treated with NaOH and three additives with their optimum concentration at different temperature (80, 90, 100, 110, and 120o C), with a fiber to liquid ratio of 1:10 for 2 h.(4) Optimization of timeThe pretreated bamboo fibers were treated with NaOH and three additives with their optimum concentration, at optimum temperature, with a fiber to liquid ratio of 1:10 for different periods of time (1, 1.5, 2, 3, and 4 h).Determination of Fiber CharacteristicsFiber Chemical Composition, Characteristics , and Weight LossFiber chemical composition was determined according to the scheme of Soutar and Bryden [1,22] by successively removal of noncellulosic substances, that is, water solubles,wax, pectim, lignin, and hemicellulose. The content of cellulose was obtained by accounting for the amount of noncellulosic substances. Measurements were repeated at three times for each specimen.Fiber fineness in tex was determined as per standard methods [23] by dividing the mass of fibers by their known length [1]. The fineness was determined by averaging the experimental results of three specimens.Fiber average length was expressed as the length by weighted average. A textile fiber should have certain length to reach the requirement of textile processing, usually about 30 mm for cotton spinning machines. Therefore, only the fibers that are longer than 30 mm were counted in fiber length testing. Measurements were repeated at three timesfor each specimen.Figure 1. Strips of natural bamboo.Table 1. The concentration of three additives (g/l )Experimentalno.Na 5P 3O 10Na 2SO 3Penetrating agent 111221333154431453326353751385349552Modification of Natural Bamboo Fibers for Textile Applications Fibers and Polymers 2011, Vol.12, No.197Fiber mechanical properties were determined by a single fiber test conducted on a LLY-06 Tensile Tester (Laizhou Electronic Instrument Co. Ltd, Shandong Province, China) according to GB5886-1986, with clamps spaced at 100 mm and with test speed of 100 mm/min. The tenacity was obtained by averaging the experimental results of sixty fibers.Fiber weight loss was determined by the direct gravimetric method [1,24]. The average value was calculated for the three specimens tested.SEM, FTIR and X-ray AnalysisThe surface properties and FTIR spectra of original bamboo strips and optimally modified bamboo fiber were examined by scanning electron microscope (SEM) (JSM-5600LV, JEOL Ltd., Japan) and Fourier transform infrared spectrophotometer (FTIR) (NEXUS-670, Nicolet Company, US), respectively. FT-IR measurements were conducted at 20±2o C and 65±3 % RH.The crystal structure of bamboo strip and optimally modified fiber were obtained by using D/Max-2550 PC X-ray diffraction with Cu-Kα radiation (40 kV and 300 mA) operated at the scanning rate of 10o/min. X-ray diffraction measurements were also conducted at 20±2o C and 65±3% RH.Results and DiscussionCharacteristics of Pretreated Bamboo StripsA detailed investigation in terms of chemical composition and weight loss is carried out to determine the effects of pretreatment on bamboo strips. Table 2 shows the chemical composition of bamboo strips after different treatments. It can be found that the fraction of noncellulosic substances (56.59%) for the original bamboo strip is quite higher than other bast fibers, such as flax (about 20-30%) and hemp (about 22-33%) [25], implying that separating bamboo fibers for textile end uses is very difficult. After acid treatment and alkaline treatment, parts of noncellulosic substances are dissolved and removed, resulting in the increase of cellulosic fibrils from 43.41 to 46.83% and 50.23%, respectively. Table 2 also shows the increase of weight loss resulting from the removal of noncellulosic substances.As shown in Table 2, pretreatment with acid and alkaline seems to only have limited effects on the fibrillation of bamboo strips; however, it actually has essential influence on the modification of natural bamboo fibers. A very thin, but compact skin covering on the surface of bamboo stem can resist the penetration of alkaline solution, but it is easily degraded by H2SO4. Moreover, the acid and alkaline at quite high concentration can softly break off the compact connection between noncellulosic substances (mainly hemicellulose and lignin) and cellulosic fibrils at lower temperature, which can make NaOH solution easier to penetrate into fibers and so efficiently get rid of noncellulosic substances.Optimization of NaOH ConcentrationAlkali treatment can lead to fibrillation which causes the breaking down of the fiber bundle into smaller bundles so as to reduce fiber diameter [26]. Therefore, the pretreated bamboo strips are modified with NaOH solution. The NaOH concentration undoubtedly has important influence on the characteristics of bamboo fibers, as shown in Table 3 and Figure 2, respectively. The fraction of noncellulosic substances in bamboo fibers are gradually decreasing at increasing NaOH concentration from 5 to 25g/l, because the degradation of noncellulosic substances is enhanced with the increase ofTable 2. The chemical compositions and weight loss of differently treated bamboo stripsBamboo strip Hemicellulose (%)Lignin (%)Cellulose (%)Weight loss (%) Without treatment23.96 (2.3 %)a24.25 (2.6 %)43.41 (2.2 %)0 Acid treated22.79 (2.6 %)23.38 (2.4 %)46.83 (2.1 %) 7.3 (5.3 %) Alkaline treated21.85 (2.4 %)22.13 (2.3 %)50.23 (2.2 %)14.1 (4.1 %) a The value in the parenthesis is standard deviation.Table 3. The chemical compositions and weight loss of natural bamboo fibers treated by NaOHNaOH Hemicellulose (%)Lignin (%)Cellulose (%)Weight loss (%)5 g/l19.85 (2.5 %) a20.98 (2.4 %)55.48 (2.3 %)23.5 (3.5 %)10 g/l18.82 (2.8 %)18.87 (2.6 %)60.36 (2.1 %)31.6 (3.4 %)15 g/l15.95 (2.4 %)14.65 (2.1 %)67.75 (2.4 %)42.5 (3.0 %)20 g/l13.63 (3.1 %)13.09 (2.9 %)71.78 (2.2 %)48.1 (2.8 %)25 g/l13.49 (2.9 %)13.84 (3.2 %)71.31 (2.2 %)53.4 (3.3 %)30 g/l15.17 (2.7 %)15.14 (2.8 %)68.37 (2.1 %)64.7 (3.4 %) The value in the parenthesis is standard deviation.98Fibers and Polymers 2011, Vol.12, No.1Lifang Liu et al.NaOH concentration,which is also confirmed by the considerably increased weight loss in Table 3. The reduction of hemicellulose from 23.96 to 13.49% and lignin from 24.25 to 13.84% after treated with 25 g/l NaOH indicates that NaOH is quite effective to modify natural bamboo fibers. Kalia et al. [26] also reported that alkali treatment has the similar effect on flax fibers. Regarding the experimental result at 30g/l NaOH that shows a contrary trend, it is mainly due to the fact that although NaOH at high concentration can degrade more noncellulosic substances, it can also lead to the decomposition of cellulose. The result on weight loss in Table 3 also shows a remarkably increase at 30 g/l NaOH.Figure 2 shows the characteristics of natural bamboo fibers at increasing NaOH concentration in terms of linear density and tenacity. The liberation of fibers is increasing with the increase of NaOH concentration among 5-25g/l ;however, it reduces when NaOH concentration reaches to 30g/l . This phenomenon can be explained that NaOH atlower concentration can efficiently degrade hemicellulose and lignin that are situated between the cellulose regions to release smaller fiber bundles from the other parts of the strips, resulting in a decrease in fiber linear density; however at higher concentration NaOH can also decompose part of cellulose to cause the break of cellulosic fibrils and the destruction of structural integrity of bamboo fibers, resulting in an increase in fiber linear density. Moreover, NaOH at higher concentration can reduce the strength of fiber.Especially when NaOH reaches to 25g/l or above, the tenacity of fiber obviously decrease because of the damage of cellulosic fibrils, indicating that NaOH at too high concentration has no efforts devoted to the extraction of natural bamboo fibers. It can be concluded that an optimum results can be obtained using a 20g/l NaOH solution.Therefore, the following experiments for the optimization of additives concentration, treating time and temperature are all implemented with 20g/l NaOH.Optimization of Additives ConcentrationThe effects of three additives, that is, Na 5P 3O 10, Na 2SO 3,and penetrating agent on the characteristics of bamboo fibers are detailed in Table 4. It can be found that the addition of additives even at very low concentration can obviously decrease the linear density of fiber. As shown in Table 4, the linear density of modified fibers remarkably decreases from 6.25 tex to 4.64 tex even at 1 g/l of all the three additives. In addition, it can be observed that the influence of additives concentrations on the fiber linear density seems rather slight,but quite significant on the fiber tenacity, indicating the optimization of their concentration is necessary. The spinnability of a textile fiber is mainly determined by its fineness, length, and tenacity. As for the natural bamboo fiber in this study, the fineness is most important, because its length and tenacity can well satisfy the requirements for textile processing. Therefore, the concentration of three additives is optimized as 3 g/l Na 5P 3O 10, 5 g/l Na 2SO 3, and 3g/l penetrating agent. The bamboo fiber thus obtained hasFigure 2. The linear density and tenacity of bamboo fibers at increasing NaOH concentration.Table 4. The characteristics of fibers treated with additives at different concentrationExperimentalno.Na 5P 3O 10(g/l )Na 2SO 3(g/l )Penetrating agent(g/l )Experimental results a N t (tex)b P dt (cN·dtex -1)1112 4.64 (7.8 %) c 2.80 (6.5 %)2133 4.52 (7.5 %) 2.65 (7.2 %)3154 4.42 (6.4 %) 2.57 (7.7 %)4314 4.45 (7.1 %) 2.60 (5.6 %)5332 4.25 (6.9 %) 2.57 (6.1 %)6353 4.18 (7.5 %) 2.55 (7.5 %)7513 4.42 (5.3 %) 2.50 (6.6 %)8534 4.26 (6.2 %) 2.20 (8.1 %)9552 4.36 (5.8 %) 2.26 (7.8 %)a N tis fiber linear density and b P dt is fiber tenacity; c the value in the parenthesis is standard deviation.Modification of Natural Bamboo Fibers for Textile Applications Fibers and Polymers 2011, Vol.12, No.199fineness of 4.18 tex and tenacity of 2.55 cN/dtex.Optimization of Treating TemperatureTreating temperature is also an important parameterfor the modification of bamboo fibers, so experiments are carried out to optimize it. The experiment are implemented with 20 g/l NaOH, 3 g/l Na 5P 3O 10, 5 g/l Na 2SO 3, and 3 g/l penetrating agent. The characteristics of bamboo fibers at increasing treating temperature are illustrated in Figure 3. It is observed that the linear density is decreasing at 80~110o C, while showing a slight increase at 120o C; otherwise,the tenacity is reducing gradually. Higher temperature is contributed to the separation of cellulosic fibrils from noncellulosic substances by enhance the effect of treating agent; however, too high temperature should also be responsible for the decomposition of cellulosic fibrils,consequently resulting in the decrease in fiber linear density.It seems that the finest fiber can be achieved at 110o C;however, the corresponding fiber tenacity is extremely low,suggesting that the fiber is too weak to spin successfully.Therefore, the optimum treating temperature is determined as 100o C. The natural bamboo fiber thus obtained is 3.26 tex in fineness and 2.41 cN/dtex in tenacity.Optimization of Treating TimeThe penetration of alkaline solution into bamboo fibers strongly depends on the treating time. Longer treating time contributes to the modification; however, too longer time will lead to the decomposition of cellulose molecule and the obvious reduction in fiber tenacity. Therefore, detailed discussion is carried out in present study to obtain an optimum treating time. The experiment are implemented with 20 g/l NaOH, 3 g/l Na 5P 3O 10, 5 g/l Na 2SO 3, and 3 g/l penetrating agent at 100o C. As displayed in Figure 4, it can be found that the increase of treating time from 1 h to 2 hcontributes to the modification of bamboo fibers, but not when the time reaches to 3 or 4 h. Regarding fiber tenacity, it continually reduces with the increase of treating time. This is mainly because that more alkaline solution can penetrate into natural bamboo fibers and act on noncellulosic substances with increasing treating time, and so the linear density and tenacity of fibers undoubtedly reduces with the removal of hemicellulose and lignin that act as cement to connect cellulose region. However, the cellulosic fibrils will be degraded if being exposed to caustic solution for too long time (more than 2 h in this study), leading to a remarkable increase in fiber linear density and significant decrease in fiber tenacity. The treating time is optimized as 2 h by taking into account of fiber characteristics, energy loss, and production cost.In general, the optimum parameters for modification of natural bamboo fibers can be obtained as: 20 g/l NaOH, 3 g/l Na 5P 3O 10, 5 g/l Na 2SO 3, 3 g/l penetrating agent, with a fiber to liquid ratio of 1:10, at 100o C for 2 h. The fiber thus obtained has linear density of 3.26 tex and tenacity of 2.41cN/dtex.Microstructure Analysis on Optimally Treated Bamboo FiberThe main characteristics of the optimally treated bamboo fibers are investigated, as shown in Table 5. It can be found that the amount of cellulose component in bamboo fiber rises remarkably because of the removal of noncellulosic substances. The average length, breaking elongation, and modulus of natural bamboo fibers after different treatments were illustrated in Table 6. With the increase in treatment intensity, the average length and modulus decrease, but breaking elongation increases. This is also due to the removal of non-cellulosic substances that act as cementing material in natural bamboo fibers. However, as shown in Table 5,Figure 3. The effects of treating temperature on the characteristics of bamboo fibers.Figure 4. The effects of treating time on the characteristics of bamboo fibers.100Fibers and Polymers 2011, Vol.12, No.1Lifang Liu et al.high amount of hemicellulose and lignin that are 12.45 and 12.86%, respectively, still remain in optimally treated fiber, because of the considerable stable hemicellulose hydrogen bonding to cellulosic fibrils and the strong C-C linkages and other chemical groups in lignin [1].Figure 5 and Figure 6 are the surface pictures and cross-section pictures of bamboo strip and differently treated bamboo fibers, respectively. A large quantity of gum in theTable 5. The characteristics of optimally treated bamboo fiberLinear density (tex)Tenacity (cN/dtex)Hemicellulose (%)Lignin (%)Cellulose (%)3.26 (5.5 %)a 2.41 (7.3 %)12.45 (3.2 %)12.86 (2.9 %)73.25 (2.4 %) The value in the parenthesis is standard deviation.Table 6. The characteristics of differently treated bamboo fibersFiber Average length (mm)Breaking elongation (%)Modulus (GPa) Bamboo strip60 //Treated with 20 g/l NaOH53.7 (3.8 %) a 1.9 (8.8 %)23.8 (8.5 %)Treated with optimal additives48.1 (3.6 %) 2.5 (7.6 %)16.7 (8.7 %)Treated with optimal parameters44.5 (4.0 %) 2.8 (7.1 %)14.1 (8.1 %)aThe value in the parenthesis is standard deviation.Figure 5. Fracture surface (1500×) of (a) bamboo strip and bamboo fibers treated with (b) 20 g/l NaOH; (c) 20 g/l NaOH, 3 g/l Na5P3O10, 5g/l Na2SO3, and 3 g/l penetrating agent, and (d) optimal parameters.Modification of Natural Bamboo Fibers for Textile Applications Fibers and Polymers 2011, Vol.12, No.1101bamboo strip can be observed in Figure 5(a). After treatedwith 20 g/l NaOH, the bamboo fiber is fiberized, but still with large amount of impurities on surface (Figure 5(b)).With the increase in treatment intensity, the bamboo fibers are getting cleaner and finer (Figure 5(c) and (d), which is also supported by the pictures in Figure 6. As can be found in Figure 6(a),the natural bamboo fiber consists of numerous elementary fibers, and the elementary fiber has an irregular hollow polygonal cross-section. With the increase in treatment intensity (from Figure 6(a) to (b) and (d)), the number of elementary fibers is decreasing, meaning that the technical bamboo fiber is getting finer. Moreover, the inner structure of bamboo fiber becomes looser after treated with additive agents. As shown in Figure 6(c), clear cracks can be observed for thus produced natural bamboo fiber, indicating that the fiber can be easily separated into small bundles. FTIR spectra are also introduced here to illuminate the change in chemical compositions of natural bamboo fibersFigure 6. Cross-section of (a) bamboo strip (500×) and bamboo fibers treated with (b) 20 g/l NaOH (500×); (c) 20 g/l NaOH, 3 g/l Na 5P 3O 10,5 g/l Na 2SO 3, and 3 g/l penetrating agent (2000×), and (d) optimal parameters (500×).Figure 7. Partial FTIR spectra of natural bamboo fibers (a) without treatment and (b) after optimum treatment.102Fibers and Polymers 2011, Vol.12, No.1Lifang Liu et al.before and after treatment, as shown in Figure 7. The bandsappearance at about 1160, 1320, and 1370 cm -1 are characteristic for one of more possible positions of hemicellulose, and the bands at 1430 and 1640 cm -1 are for lignin, respectively. It can be observed that all the bands mentioned above are remarkable weaker for the fiber after treatment, indicating that a great amount of hemicellulose and lignin are removed from the fiber.Figure 8 shows the X-ray diffraction pattern for bamboo strips and optimally treated bamboo fiber. It found that they have the similar diffraction peaks, but with different intensity. Furthermore, their crystallinity degree are calculated by dividing the crystalline area by the total area formed by the curve in Figure 8, which are 67.5 and 70.3% for bamboo strip and optimally treated bamboo fiber, respectively.Swelling in NaOH introduces considerable changes in crystallinity of natural bamboo fiber, which is mainly due to the removal of the non-cellulosic material that leads to a better packing of cellulose chains [19].ConclusionNatural bamboo fibers were chemically extracted and modified in this paper, and the processing parameters were optimized to improve fiber quality. Reduced contents of noncellulosic substances and improved fiber fineness benefiting from the chemical modification can be observed from experimental results. The processing parameters are optimized as: 20g/l NaOH, 3g/l Na 5P 3O 10, 5g/l Na 2SO 3, 3g/l penetrating agent, with a fiber to liquid ratio of 1:10, at 100o C for 2h, and the natural bamboo fiber thus obtained has cellulose amount of 73.25%, fineness of 3.26tex,average length of 44.5 mm, breaking elongation of 2.8%and tenacity of 2.41 cN/dtex. The chemical modification in this study may offer a possibility of developing naturalbamboo fibers into practical applications in textiles.AcknowledgementsThe supports of the Fujian Provincial Science and Technology Agency (Project 2008HZ0001-3), National Natural Science Foundation of China (Project 50809016 and Project 10872048), and the Fundamental Research Funds for the Central Universities (Project 2009C01-1-01) are gratefully acknowledged. We also thank anonymous referees and editors for useful and constructive suggestions which have resulted in significant improvement of the original manuscript.References1.M. Kostic, B. Pejic, and P . Skundric, Bioresource Technol.,99, 94 (2008).2.K. M. M. Rao, K. M. Rao, and A. V . R. Prasad, Mater .Design , 31, 508 (2010).3.A. P . Deshpande, M. B. Rao, and C. L. Rao, J. Appl.Polym. Sci ., 76, 83 (2000).4.Y . Liu and H. Hu, Fiber. Polym., 9, 735 (2008).5.L. Zou, H. Jin, W. Lu, and X. Li, Mater. Sci. Eng ., 29, 1375(2009).6.K. Okubo, T. Fujii, and Y . Yamamoto, Compos. Part A-Appl. S ., 35, 377 (2004).7.M. K. Basak, S. Chanda, S. K. Bhaduri, S. B. Mondal, and R. Nandi, Ind. Crop. Prod ., 5, 173 (1996).8.C. A. Hill, H. A. Khalil, and M. D. Hale, Ind. Crop. Prod .,8, 53 (1998).9.F. Khan and S. R. Ahmad, Polym. Degrad. Stabil ., 52, 335(1996).10.L. Liu, Q. Wang, Z. Xia, J. Y u, and L. Cheng, Ind. Crop.Prod ., 31, 43 (2010).11.Y . Wang, X. Xu, and X. Zhang, Surf. Interface Anal ., 38,1211 (2006).12.J. M. O. Scurlock, D. C. Dayton, and B. Hames, BiomassBioenerg ., 19, 229 (2000).13.F. Brulmann, M. Leupin, and K. H. Erismann, J.Biotechnol ., 76, 43 (2000).14.E. Joko, S. Tokuda, N. Kikumoto, J. Sugai, T. Hayashi, andM. Arai, Sen’I Gakkaishi , 58, 22 (2002).15.H. K. Sreenath, A. Shah, V . Yang, M. M. Gharia, and T. W.Jeffries, J. Ferment Bioeng ., 81, 18 (1996).16.B. Beltran, C. J. Hurren, A. Kaynak, and X. Wang, Fiber .Polym ., 3, 129 (2002).17.I. V . Weyenberg, T. C. Truong, B. V angrimde, and I.V erpoest, Compos. Part A-Appl. S ., 37, 1368 (2006).18.P . Kushwaha and R. Kumar, J. Reinf. Plast. Comp ., 28,2851 (2009).19.M. Das and D. Chakraborty, J. Appl. Polym. Sci., 102,5050 (2006).20.M. Das, A. Pal, and D. Chakraborty, J. Appl. Polym. Sci .,100, 238 (2006).Figure 8. X-ray diffractograms of natural bamboo fibers (a)without treatment and (b) after optimum treatment.。